Дегидрирование пропана с использованием каталитически-активных неорганических мембран
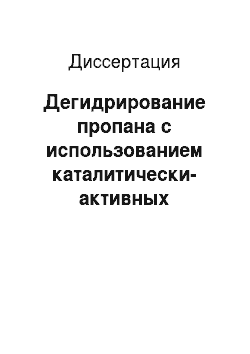
Диссертация
Однако и требования к таким мембранам достаточно жесткие — помимо своей каталитической активности в отношении одной или нескольких реакций, эти мембраны должны обладать химической, термической стойкостью, механической прочностью, и желательно быть доступными для серийного производства, с относительно низкой себестоимостью. В настоящее время уже существуют несколько видов каталитических мембран… Читать ещё >
Содержание
- Глава1. Обзор литературы
- 1. 1. Мембраны и методы их получения. Общие положения
- 1. 2. Классификация мембран
- 1. 3. Методы получения композиционных неорганических мембран
- 1. 3. 1. Пористые подложки композиционных неорганических мембран
- 1. 3. 2. Методы получения селективных слоев композиционных неорганических мембран
- 1. 3. 2. 1. Методы осаждения тонких дисперсий
- 1. 3. 2. 2. Методы осаждения тонких пленок и покрытий
- 1. 4. Массоперенос на неорганических мембранах
- 1. 2. 1. Массоперенос в пористых мембранах
- 1. 2. 2. Массоперенос в непористых мембранах
- 1. 3. Композиционные неорганические мембраны и химическая реакция
- 1. 3. 1. Мембранный катализ — метод, открывающий новые перспективы
- 1. 3. 2. Классификация и конструкции мембранных реакторов
- 1. 3. 3. Дегидрирование пропана в промышленности
- 1. 3. 4. Дегидрирование пропана в мембранных реакторах
- 1. 4. Выводы из литературного обзора
- 2. 1. Характеристики исходных материалов
- 2. 2. Методика осаждения молибдена на пористые подложки CVD методом
- 2. 3. Методика хроматографического анализа газов
- 2. 4. Методика определения открытой пористости
- 2. 5. Методика исследования подложек и мембран с селективным слоем на основе молибдена сканирующей электронной микроскопией
- 2. 6. Методика проведение рентгеновского микроанализа
- 2. 7. Методика определения однородности слоя Мо
- 2. 8. Методика определения удельной поверхности мембран
- 2. 9. Методика исследования распределения пор мембран по размерам методом ртутной порометрии
- 2. 10. Методика экспериментального определения проницаемости, фактора разделения и каталитических свойств мембран
- 2. 10. 1. Методика определения газопроницаемости мембран
- 2. 10. 2. Методика определения фактора разделения мембран
- 2. 10. 3. Методика определения каталитической активности мембран и Мо катализатора
- 2. 11. Методика определения термической стабильности мембран
- 3. 1. О каталитических мембранах
- 3. 2. О методе химического осаждения из газовой фазы
- 3. 3. Выбор условий осаждения Мо в CVD-реакторе с нагревом подложки
- 3. 3. 1. Выбор давления
- 3. 3. 2. Выбор температуры осаждения
- 3. 3. 3. Выбор температуры возгонки гексакарбонила молибдена
- 3. 3. 4. Выбор линейной скорости газа-носителя на накопление Мо
- 3. 3. 5. Влияние продолжительности осаждения на накопление Мо
- 3. 3. 6. Влияние продолжительности осаждения на однородность слоя Мо
- 3. 4. Анализ структуры селективного слоя молибден — керамических мембран, полученных в реакторе с нагревом подложки
- 3. 4. 1. Влияние температуры подложки на морфологию молибденового слоя
- 3. 4. 2. Влияние времени осаждения на морфологию молибденового слоя
- 3. 4. 3. Влияние газовой среды и высокотемпературной обработки образцов мембран на структуру Мо-слоя
- 3. 5. Получение Мо-углеродных мембран
- 3. 6. Поровые характеристики, полученных композиционных мембран с селективным слоем на основе Мо
- 3. 7. Оценка возможности создания пилотной установки для получения молибден-керамических мембран
- 3. 8. Выводы
- 4. 1. Обоснование выбора рабочих условий и газов для определения разделительных характеристик мембран
- 4. 2. Определение проницаемости подложек и мембран по индивидуальным газам
- 4. 3. Определение фактора разделения мембран
- 4. 4. Определение термической стабильности мембран
- 5. 1. Обоснование выбора рабочих условий для проведения реакции дегидрирования пропана
- 5. 2. Термодинамический анализ процесса дегидрирования пропана в выбранных рабочих условиях
- 5. 3. Оценка влияния материала подложки и молибденового слоя мембраны на степень превращения и селективность по пропилену
- 5. 4. Дегидрирование пропана в мембранно-каталитическом реакторе и использованием Мо-керамических мембран
- 5. 5. Дегидрирование пропана в мембранно-каталитическом реакторе и использованием Мо-углеродных мембран
- 5. 6. Основные рабочие характеристики Мо-керамической и Мо-углеродной мембран
Список литературы
- Решение IV Всесоюзной конференции по мембранным методам разделения смесей, Москва, 1978 21с.
- Ю.И. Дытнерский, В. П. Брыков, Г. Г. Каграманов «Мембранное разделение газов», Москва, «Химия», 1991 — 344 с.
- М. Мулдер «Введение в мембранную технологию», Мсква, «Мир», 1999 -513 с.
- Назаров В.В. «Коллоидно-химические принципы золь-гель методов получения материалов на основе гидрозолей Z1O2, ТЮ2 и S1O2″, диссертация на соискание степени д.х.н., РХТУ им. Д. И. Менделеева, Москва, 1995−471 с.
- А.С.М. Franken „Membrane distillation: a new approach using composite membrane“, Thesis, Twente, 1998−181p.
- H.A. Платэ „Мембранные технологии авангардное направление развития науки и техники XXI века“, „Мембраны. Критические технологии“, 2001, № 1,ВИНИТИ, Москва, с. 3−8.
- Н.И. Николаев „Диффузия в мембранах“, Москва, „Химия“, 1980 232с.
- Брык М.Т. и др. Мембранная технология в промышленности, Киев, „Техника“, 1990 247с.
- Ю.Каграманов Г. Г., „Научные основы технологии и применениякерамических мембран“, автореферат диссертации на соискание ученой степени д.т.н., РХТУ им. Менделеева, Москва, 2002,36с.
- Hinich О.М., Kirchanov А.А. and others. „Novel macroporous inorganic membranes: Futures of preparation and use.“ 6th International Conference on Inorganic Membranes, Montpellier, June 26−30, 2000, Program and Book of Abstracts, p.106.
- Каграманов Г. Г., Назаров B.B., Лукин E.C., Першикова Е. М., „Микрофильтрационные мембраны с селективным слоем на основе диоксида циркония“, Стекло и керамика, М., 2001, № 7, с. 16−19.
- Antonova А.А., Zhilina O.V., Kagramanov G.G., Nazarov V.V. „Catalytic active membranes on cerium dioxide.“ 6th International Conference on Inorganic Membranes, Montpellier, June 26−30, Program and Book of Abstracts, 2000-p. 102.
- Хванг C.T., Каммермейер К. Мембранные процессы разделения, Москва, „Химия“, 1981 464 с.
- Герасимов Я.И. Курс физической химии. Москва, „Химия“, 1966 — Т 1. 624с.
- Гадалова О.Е. Тзработка основ CVD -технологии композиционных молибден-керамических мембран», диссертация на соискание ученой степени кандидата технических наук, РХТУ им. Д. И. Менделеева, Москва, 2002 155 с.
- Jae-Hyun So and others, Preparation of silica-alumina composite membranes for hydrogen separation by multi-step pore modifications, Journal of Membrane Science, 147,1998, p.147−158
- A.K. Prabhu and others, Modeling of the methane reforming reaction in hydrogen selective membrane reactors, Journal of Membrane science, 177, 2000, p. 83−95.
- Фоглер И. Золь гель процесс и возможности его использования для производства материалов, Берлин, 1989 — 284 с.
- Дытнерский Ю.И. «Обратный осмос и ультрафильтрация», Москва, «Химия» 1978−352 с.
- Сыркин В.Г. «CVD метод. Химическое парофазное осаждение», Москва, «Наука», 2000−496 с.
- Alary J. A., Bauer J.M. and Boudier G. «Synthesis of inorganic membrane by electrocoating processs». Proceed. International Congress on Membranes and Membrane Processes, Chicago, USA, 1990, p.555−558.
- К.Пауэлл, Дж. Оксли, Дж. Блочер «Осаждение из газовой фазы», Москва, Атомиздат, 1970−472 с.
- Bryden K.J. and others. «Pulsed elecrtrosition synthesis and hydrogen absorption. properties of nanostructured palladium-iron alloy films.», Electrochem Soc., 1998,145, № 10, p.3339−3346.
- Wu L.-Q. et others, Preparation of a palladium composite membrane by an improved electroless plating technique, Ind. and Engeneering Chemistry Reviw, 2000, 39, № 2, p.342−348.
- Иванов В.E., Нечипоренко Е. П. «Кристаллизация тугоплавких металлов их газовой фазы», Москва, «Атомиздат», 1974, 264.27.11ias S. and Govind R. «Development of high temperature membranes for membrane reactor» AlChE Symp. Ser., 85(268):18. 1989.
- L.Cot, C. Guizard and others «Preparation and Application of Inorganic Membranes» («Inorganic membranes: 1С1М-91″, Process of the 2nd International Conference on Inorganic Membranes, Montpellier, July 1−4, 1991).
- J.N. Armor.» Membrane Catalysis", Catalysis today, 25 (1995), p. 1−25
- Грязнов B.M. «Системы мембрана катализатор», Москва ,"Наука", 1999-с. 5.
- Грязнов В.М., Серебрянникова О. С., Серов IO.M.,"Pd membranes obtaining", Applied Catalysis, vol. 96,1993 p. 15.
- Раков Э.Г., Тесленко B.B. «Химическое осаждение из газовой фазы», Москва, 1983.
- Владыко М.Н., Масалов В. М., «Осаждение поликристаллических материалов методом CVD», Ин-т физической химии твердого тела, Черноголовка, 1986−80 с.
- Tchouprakov Пуа, The Internet Research Project «MOCVD of Metals with New Precursors and Deposition of Magnetic Materials», (www.MOCVD2.htmn 1998.
- Боресков Г. К., «Катализ. Вопросы теории и практики», «Наука», Сибирское отделение, 1987 481с.
- Каграманов Г. Г., Овсянников A.C., Дытнерский Ю. И., Тазработка керамических микро- и ультрафильтрационных мембран", вестник МГТУ им. Н. Э. Баумана, сер. «Машиностроение», 1992, № 4, с. 25−30.
- Kagramanov G.G., Nazarov V.V., Dytnersky Y.I., Ovsiannikov A.S. 'Development des membranes ceramiques pourmicro et ultгafiltration, Inorganic membranes, Montpellier, France, July, 1−4,1991,p. 456−460.
- Томилина E.M., Пронина B.B., Лукин E.C., Каграманов Г. Г. «Пористая керамика на основе оксида алюминия», «Стекло и керамика», 2000, № 6, с. 23−24.
- Jae-Hyun So and others, Preparation of silica-alumina composite membranes for hydrogen separation by multi-step pore modifications, Journal of Membrane Science, 147, 1998, p. 147−158.
- S. Kitao and M. Asaeda, Gas separation performance of thin porous silica membrane prepared by sol-gel and CVD methods, Key Engineering Materials, Vol. 61−62″ 1991, pp. 267−272.
- A.K. Prabhu and others, Modeling of the methane reforming reaction in hydrogen selective membrane reactors, Journal of Membrane science, 177, 2000, p. 83−95.
- Хванг C.T., Каммермейер К. Мембранные процессы разделения, М., Химия, 1981,464 с.
- Лыков А.В., Тепломассообмен: справочник, М., Энергия, 1972, 560 с.
- Macelroy J.M.D., Kelly J.J., American Institute of Chemical Engineers Journal, 1985, V.31, № 1, p. 35−43.
- Zhang W. L., Jiang B. Q., Sun Y. S., Lin F., Gu L. Study on preparation of supported alumina membrane using sol-gel method. Acta Met. Sin. 12.1999. N5, p. 1082−1085.
- R. M. de Vos, Verweij H. Improved performance of silica membranes for gas separation. Journal Membrane Science, 1998. 143, N 1−2, p. 37−51.
- Asaeda Masashi, Yamazaki Shin. Separation of inorganic gas mixtures by porous silica membranes. 6th International Conference on Inorganic
- Membranes, Montpellier, June 26−30, 2000: ICIM6 2000: Program and Book of Abstracts. Montpellier. 2000, p. 38.
- Белоусов В. M., Кагановский В. А., Литвин В. И. Особенности разделения газовых смесей на композиционной мембране AlOOH-AI2O3, синтезированной золь-гель-методом. Высокочистые вещества. 1996, N5, с. 59−63.
- Maorong С., Machida М., Eguchi К., 'Ва0-А1203, La203-A1203 sol-gel derived membranes', Journal of Membrane Science, vol. 96, 1994, p. 205 -212.
- Champagne A., Tsotsis Т., 'Inorganic reactor dehydrogenation', 1992, p.713−730
- Zaspalis V.T., Van Praag, Keizer K., Burgraaf A.J., Journal of Applied Catalysis, vol 74, 1991, p. 205.
- Zaspalis V.T., Van Praag, Keizer K., Burgraaf A.J., Journal of Applied Catalysis, vol 74,1991, p. 223.
- Armor J.N. 'Catalysis with permselective inorganic membranes', Journal of Catalysis, vol 49,1989, p. 1−25.
- Koukou M.K., Papayannakos N.C., Performance of ceramic membranes at elevated pressure and temperature, Journal of membrane science, vol. 155, 1999, p. 241−259.
- Koros W.S. 'Membranes opportunities and challenges for large capacity gas and vapor feeds', XX EMS Summer School, Norway, Trondheim, 3−8 August 2003.
- Соорег C. A, Lin Y. S, 'Microstructural and Gas Separation Properties of CVD Modified Mesoporous Gamma-Alumina Membranes', JOURNAL OF MEMBRANE SCIENCE Vol. 195, Iss. 1,2002, pp. 35−50.
- Prabhu A. K, Oyama S. T, 'Highly Hydrogen Selective Ceramic Membranes -Application to the Transformation of Greenhouse Gases', JOURNAL OF MEMBRANE SCIENCE, 2000, Vol 176, Iss 2, pp. 233−248.
- Durand.J, Rouessac. V, 'CVD Techniques for Gas Separation Membranes Synthesis Characterization — Applications', JOURNAL DE PHYSIQUE IV, 2001, Vol 11, Iss PR3, pp. 1053−1063.
- Li Y. Y Nomura T. Sakoda A. Suzuki.M.,' Fabrication of Carbon-Coated Ceramic Membranes by Pyrolysis of Methane Using a Modified Chemical Vapor Deposition Apparatus', JOURNAL OF MEMBRANE SCIENCE, 2002, Vol 197, Iss 1−2, pp. 23−35.
- Liu Paul К. Т., Wu Jeffrey C. «Method for forming metal-oxide-modified porous ceramic membranes» Пат. 5 415 891 США, МПК 6 В 05 D 5/00, С
- С 16/40. Media and Process Technology Inc. N 179 614- Заявл. 10.1.94- Опубл. 16.5.95- НПК 427/243. US.
- Перельман Ф.М., Зворыкин, А .Я. «Молибден и вольфрам», М., Наука, 1968.-144с.
- Saracco G., Neomagus H.W.J.P., Versteeg G.F., van Swaaij W.P.M., High temperature membrane reactors: potential and problems, Chemical Engineering Science, 54 (1999), p. 1997−2017.
- Магсапо J.G., Tsotsis T.T., Catalytic membranes and membrane reactors, Wiley-VCH, Weinheim, 2002
- Zaman J., Chakma A., Inorganic membrane reactors, Journal of membrane science, 92 (1994), 1−28.
- Armor J.N. Membrane catalysis: where is it now, what needs to be done?, Catalysis today, 1995, 25, 199 207.
- Venvik H. Catalytic membrane reactors, XX EMS Summer School, Norway, Trondheim, 3−8 August 2003.
- Статистический анализ потоков патентной и периодической информации по мембранным методам разделения углеводородов, Мембраны, Серия критические технологии, 2001, № 9, с 28−33.
- Miachon S. Catalytic membrane reactors. Why? What for? How?, XX EMS Summer School, Norway, Trondheim, 3−8 August 2003.
- Mejdell T. Membrane reactor modeling, XX EMS Summer School, Norway, Trondheim, 3−8 August 2003.
- Tsotsis T.T., Champagnie A.M., Minet R.G., Yi H.M., Catalytic membrane reactors, Computer aided design of Catalysts, Chapter 12, New York, 1993.
- Saracco G., Veldsink J.W., Versteeg G.F., Role of catalyst loading in a non-permselective membrane reactor, Chemical engineering communication, 1996,147, p. 29−42.
- Dalmon J.A., Catalytic membrane reactors., Weinheim, Germany, VCH, 1997, pp. 1387−1398.
- Hsieh H.P., Inorganic membranes for separation and reaction, Amsterdam, Elsevier, 1996,610 pp.
- Kapteijn F., Bakker W.J.W., van de Graaf J., Zheng G., Poppe J., Moulijn J.A., Permeation and separation behaviour of silicalite-1 membranes, Catalysis Today, 1995, vol. 25, p. 213−218.
- Verweij H., private comm., Twente University, 1998.
- Shu J., Grandjean B.P.A., Kaliaguine S. and со, Gas permeation and isobutene dehydrogenation over very thin Pd ceramic membranes, Can. Journal of Chemical Engng., 1997, vol. 75, p. 712−720.
- Yeung K.L., Aravind A., Zawada R.J.X., and со, Nonuniform catalyst distribution for inorganic membrane reactors: theoretical considerations andpreparation techniques, Chemical Engineering Science, 1994, vol. 49, p. 4823−4838.
- Vitulli G., Verrazzani A., Pitzalis E., and со, Pt- A1203 catalytic membranes vs. Pt on A1203 powders in the selective hydrogenation of p-chloronitrobenzene, Catalysis letters, 1997, vol. 44, p. 205−210.
- Krishna R., van de Broeke L.J.P., The Maxwell-Stefan description of mass transfer across zeolite membranes, Chemical Engineering Journal, 1995, vol. 57, p. 155−164.
- Sanchez J., Tsotsis Т., Current developments and future research in catalytic membrane reactors, in: Fundamentals of Inorganic Membrane Science and Technology, Burgraaf A.J., and Cot L., Elsevier Science B.V., Amsterdam, 1996, p. 96−98.
- Бондаренко А.Г., Британ И. М., Голубев И. Ф. и др., Мембраны для выделения водорода из газовых смесей, Вып. 3. М. ВНИИГАЗПРОМ, 19 816 С. 44.
- Dixon A., Innovations in catalytic inorganic membrane reactors, Catalysis, vol. 14, The Royal Society of Chemistry, Cambridge, 1999, p. 3 4.
- Zaman J., Chakma A., Inorganic membrane reactors, Journal of membrane science, 1994, vol. 2, p 1−28.
- Itoh N., Haraya, Catalysis Today, 2002, vol 56, p. 103
- Strano M.S., Foley H.C. American Institute of Chemical Engineers Journal, 2001, vol. 47, p. 66.
- Kameyama J. Japan Patent # JP-A-59−59 223,1988
- Itoh N., AIChE Journal, 1987, vol. 33, p. 1576.
- Мир химии, www.chemistrv.narod.ru
- Буянов P.A., Пахомов Н. А., Катализаторы и процессы дегидрирования парафинов и олефинов, Кинетика и катализ, 2001, том 42, № 1, С. 72−85.
- The Energy Daily, New energy new conceptions, August, 2000, #28.
- Информация о научно-практической конференции «Мембранные беседы — 2000», Мембраны, Серия Критические технологии, 2001, № 8, С. 33−34.
- Всероссийское совещание «Водород и топливные элементы», Мембраны, Серия Критические технологии, 2000, № 3, С. 10.
- Quicker P., Hollein V., Dittmeyer R., Catalytic dehydrogenation of hydrocarbons in palladium composite membrane reactors, Catalysis today, 2000, № 56, p. 21−34.
- Лебедев H.H., Химия и технология основного органического и нефтехимического синтеза, Москва, Химия, 1981, 608 с.
- Жоров Ю.М., Кинетика промышленных органических реакций, Москва, Химия, 1989, 384 с.
- Котельников Г. Р., Струнникова Л. В., Патанов В. А., Арапова И. П., Катализаторы дегидрирования низших парафиновых, олефиновых и алкил-ароматических углеводородов, Москва, ЦНИИТЭНЕФТЕХИМ, 1978, С.81.
- Gryaznov V.M., Platinum Metals Review, 1986, № 30, p. 68.
- Gryaznov V.M., Platinum Metals Review, 1992, № 36, p. 70.
- Yildirim Y., Gobina E., Hughes R., An experimental evaluation of high-temperature composite membrane systems for propane dehydrogenation, 1997, № 135, p. 107−115.
- Wu C.S., Flowers P.K.T., and со., Journal of membrane science, 1993, № 77, p. 85−98.
- H. Weyten, K. Keizer, A. Kinoo, J. Luyten: «Dehydrogenation of propane using a packed-bed catalytic membrane reactor" — AIChE Journal: Vol. 43,(7), (1997), p. 1819.
- J.S. Chang, H.S. Roh, M.S. Park, S.E. Park, Propane dehydrogenation over a hydrogen permselective membrane reactor, Bull. Korean Chem. Soc., vol. 23, #5, 2002, p. 674 678.
- K. Hou, R. Hughes, A comparative simulation analysis of propane dehydrogenation in composite and microporous membrane reactors, Journal of Chemical Technology and Biotechnology, vol. 78,2002, p. 35−41.
- Wolfrath O., Kiwi-Minsker L., Renken A., Proc. AIChE Annual meeting, Los Angeles, CA, November 2000.
- Bitter J.G.A., Processes and Apparatus for the dehydrogenation of organic compounds, Brit. Patent, GB 2.201.159, August, 24, 1988.
- Z.D. Ziaka, R.G. Minet, T.T. Tsotsis, Propane dehydrogenation in a packed-bed membrane reactor, AIChE Journal, vol. 39, № 3,1993, 526−529
- Z.D. Ziaka, R.G. Minet, T.T. Tsotsis, A high temperature catalytic membrane reactor for propane dehydrogenation, Journal of Membrane Science, vol. 77, 1993, p. 221
- Late L., Blekkan E.A., Kinetics of the oxidative dehydrogenation of propane over a VmgO catalyst, Journal of natural gas chemistry, 2002, № 11, p. 33−42.
- M. Шингляр. Газовая хроматография в практике. Изд. Химия 1964. стр. 105.
- Крауш Т., Роцше X., Хофман М., Экнич В., Хабиш Д. Руководство по газовой хроматографии. Часть 2. Москва, „Мир“, 1988, стр. 34.
- Сыркин В.Г., Газофазная металлизация через карбонилы, Москва, Металлургия, 1985,284 с.
- Shindo Y., Hakuta Т., Yoshitome Н., Permeability correlation modeling, Journal of Chemical Engineering of Japan, 1983, vol.16, № 2, p. 120−126.
- Розанов B.B., Цао Ямин, Крылов О.В., Эффект спилловера водорода в системах Со и Мо/АЬОз, Тезисы докладов пятой
- Всесоюзной конференции по механизму каталитических реакций, 1418 мая, 1990, Москва, С. 166−168.
- Розанов В.В., Цао Ямин, Крылов О.В., Адсорбция и спилловер водорода в системах Со и Мо/АЬОз, Кинетика и катализ, 1993, 34, № 1, С. 132−136.
- Семилетов С.А., Имамаов P.M. и др., О структуре пленок вольфрама и молибдена, осаждаемых из газовой фазы при низкотемпературном пиролизе карбонилов, Кристаллография, 1977, том 22, Вып. 5, С. 1056−1059.
- Гадалова O.E., Скудин B.B. „Получение композиционных молибден-керамических мембран CVD методом: изучение структуры селективного Мо-слоя.“ // Тезисы докладов Всероссийской научной конференции „Мембраны-2001″. Москва. 2−5 октября. 2001. С. 216.
- Lee J.S., Oyama S.T., Boudart М., Molybdenum Carbide Catalysts, Journal of Catalysis, № 106,1987, p. 125−133.
- Solymosi F., Nemeth R., Ovari L., Egri L., Reactions of propane on supported M02C catalysts, Journal of Catalysis, № 195, 2000, p. 316−325.
- Бухаркина T.B., Дигуров Н. Г., Химия природных энергоносителей и углеродных материалов, РХТУ им. Менделеева, Москва, 1999, С. 27.
- Тепляков В.В., Нетрусов А. И., Гасанова Л. Г., Слепова Е. В., Мембранные контакторы, интегрированные с биореакторами, для производства метана и водорода, VI Московская международная телекоммуникационная конференция молодых ученых и студентов, 2002.
- L. Volpe, М. Boudart, Compounds of Мо and W with high specific surface area, 1985, vol. 59, p. 348 356.
- Расчет эквивалентного диаметра пор селективного Мо-слоя для Мо-углеродной мембраны (прирост массы Мо 0,0192 г Мо/ г подложки)
- Эквивалентный диаметр пор мембраны может быть вычислен по формуле 86.:э=4ПуМо-слоя /SvMo-1)где nVMo-cjioH=Vnop/ Vmo-слоя объемная пористость Мо-слоя- (2)
- SvMo= 8удмо*Шмо/ Vmo-слоя ~ объемная поверхность пор в единице объема Мо-слоя, м2/м3- (3)
- Vn0p ~ объем пор в Мо-слое, м3- Vmo-слоя ~ объем селективного молибденового слоя, м3- SyflMo ~ удельная поверхность Мо-слоя, м2/г- Шмо масса молибдена, составляющего селективный слой мембраны, г.
- Значение эквивалентного диаметра пор (cb) для мембраны с плотным Мослоем определяли следующим образом:
- Объем пор в Мо-слое может быть найден по формуле:
- Vnop=VMo-ciioH-(niMo/pMo)-4)где Рмо плотность молибдена, кг/м3.
- Зная геометрические размеры подложки и селективного слоя Умо-слоя может быть найден по следующей формуле:
- VMo^, oH=7t (D+25)2L/4-(7cD2L)/4−5)где D наружный диаметр подложки (трубка), м- L — длина мембраны- 5 — толщина селективного Мо-слоя, м.
- Тогда, Ум<�ыУ.оя=гс5Ь (В+5)-6)
- Откуда Vnop=7c5L (D+8)-(mMo/pMo)-7)
- Подставив известные числовые значения в выражение (3), получим:
- Vn0p=3,14*5*10"б*74*10"3*(10*10'3+5*10"6)-(0Д08/10,200*10б)-.31. Vnop=5.688*10 м
- Тогда объемная пористость Мо-слоя (П?мо-сл<�ш)“
- Vnop/ Ум"-слоя=5.688*10"9/1,628*10"8-
- SVMo— SyflMo*mMo/ Vmo-слоя Svmo =14.610*0,108/1,628*10^=0,0969*109 м2/м3-о-слоя
- Эквивалентный диаметр пор плотного Мо-слоя равен:1э=4ПУм"ъслоя /SvMo- d3=4*0,35/(0,0969*109), мd3=14 нм
- Материальные балансы процесса мембранного катализа дегидрирования пропана
- Табл. 1. Мо-углеродная мембрана, Т=580 °С, степень отбора пермеата 0,3, давление в напорном канале 1,8 ат.1. Приход Расходкомпонент С, моль/с Н, моль/с компонент С, моль/с Н, моль/с
- СЗН8 0,302 0,403 СЗН8 0,229 0,305
- Н2 0,23 СЗН6 0,66 0,66
- С2Н6 0,4 0,6 С2Н6 0,4 0,61. С2Н4 0,4 0,41. СН4 0,2 0,41. Н2 0,41итого 0,306 0,432 итого 0,305 0,427ошибка к с | 0,330 132
- Табл. 2. Mo-керамическая мембрана, Т=580 °С, степень отбора пермеата 0,3, давление в напорном канале 1,8 ат.1. Приход Расходкомпонент С, моль/с Н, моль/с компонент С, моль/с Н, моль/с
- СЗН8 0,302 0,403 СЗН8 0,263 0,351
- Н2 0,23 СЗН6 0,27 0,27
- С2Н6 0,4 0,6 С2Н6 0,5 0,71. С2Н4 0,9 0,91. СН4 0,4 0,91. Н2 0,34итого 0,306 0,432 итого 0,308 0,436ошибка f/o с ГГ.-0^52 712 н г -0.8582
- Тепловой баланс CVD реактора с охлаждением стенок.
- Проведем расчет для реактора с охлаждением стенок при различных температурах газовой смеси и различных диаметрах труб. Выберем трубы из углеродистой стали, для теплообменников типа „труба в трубе“.
- Примем, что в кожухе реактора расположено 19 труб по вершинам равносторонних треугольников.
- Проведем расчет для труб диаметром 25×3 мм. Длина труб 1 тр. = 1,2 м.
- Температура газовой смеси на входе в реактор примем tnu = 140 °C, предполагая, что температура газовой смеси на выходе из реактора равна температуре на входе или отличается от нее незначительно.
- Определение количества тепла, передаваемого от керамической подложкигазовой смеси.
- Количество тепла, которое передается газовой смеси от керамической подложки, определим по основному уравнению теплопередачи: Q = kFAt • (6)где
- Q количество тепла, передаваемое керамической подложкой газовой смеси, Вт-к коэффициент теплоотдачи, 1. Вт/м *К-1. F площадь мембран, м2:
- A t = t мемв. t газ — разность температур керамической подложки и газовой смеси, С.
- Так как теплоотдачу от нагревателя к подложке мы не рассматриваем, то а.мемб. — 0. Также принимаем, что загрязнений нет иГг = 0.
- Тогда к ~ агаз. Коэффициент теплоотдачи от подложки к газовой смеси вычисляется по формуле: Nu •X7— (8)где
- Nu критерий Нуссельта- d3 — эквивалентный диаметр, м-
- А коэффициент теплопроводности газовой смеси, Вт/м-К.
- Критерий Нуссельта для развитого турбулентного течения равен: Nu = 0,018 ¦ Re °-89)где
- Re критерий Рейнольдса. Nu = 0,018 • 10 000 °'8 = 28,528
- Подставляя найденные значения критерия Нуссельта и эквивалентного диаметра в формулу (8) вычисляем коэффициент теплоотдачи:
- Тогда количество тепла, получаемое газовой смесью от подложки, будет равно:
- Q = 88,696 • 0,477 • (250−140) = 4653,899 Вт
- Определение количества тепла, передаваемого от газовой смеси воде.
- А, = 46,5 Вт/м2-К коэффициент теплопроводности стали.
- Коэффициент теплоотдачи газовой смеси вычисляем по формуле (8).Критерий Нуссельта при развитом турбулентном движении в данном случае определяется по уравнению:
- Nu = 0,021 • Re °'8 • Рг °'43 • (Рг / Рг^)0−25 (13)где
- Рг / Рг erf-15 = 1 для газа-
- Рг / Рг ст)0,25 = 0,93 для воды-
- Рг — критерий Прандтля для газа или воды, который определяется по формуле:1. Рг=^- (14)Ягде
- С р средняя массовая теплоемкость среды, Дж/кг -К- ц — вязкость среды, Па с- X — коэффициент теплопроводности среды, 1. Вт/м • К.
- По формуле (14), зная физические свойства газовой смеси, вычислимкритерий Прандтля для газовой смеси: рг= 1051,429.0,0223-ИГ* 0,0342
- Подставляя в формулу (13) все известные значения вычислим критерий Нуссельта для газовой смеси: Nu = 0,021 • 10 000 0,8 • 0,692 °'43 • 1 = 28,405
- Тогда по формуле (8) коэффициент теплоотдачи для газовой смеси будет равен:28,405−0,0342 3^/Vir0,011
- Проведем аналогичный расчет для воды. По формуле (14) критерий Прандтля равен:4190−0,3565−10-' з 0,675
- Критерий Нуссельта по формуле (13): Nu = 0,021 • 10 000 °'8 ¦ 2,213 °'43 • 1 = 43,555
- В соответствии с таблицей 25.2 1. формула (15) преобразуется: Dan. 1=6 1,3 ¦ dmp. ен. = 7,8 ¦ dmp. вн. (16)
- По формуле (16) диаметр кожуха будет равен: Dan. 1 = 7,8−0,025 = 0,195 м
- Эквивалентный диаметр можно определить по формуле:4f (17)где
- S- площадь поперечного сечения потока, м — Я смоченный периметр, м.
- Площадь поперечного сечения потока определяется по формуле: S = (iz/4) — (D2an.l-d2H.-n) (18)
- Смоченный периметр: n = n-(Dan.1 + dH. -п) (19)
- Подставляя выражения (18) и (19) в формулу (17) получим, что эквивалентный диаметр равен:= 4 • Ц) — (Pj, ~ dlPHa, • *) Р2тЛ djpMap.» Э л• (А,-1 + ««» п) Dmy+dmnum,-nоя.1 тр. нар / апЛ тр. нар
- Поставляя все известные данные в формулу (20) определим эквивалентный диаметр: iy*/10,195 + 19−0,025
- Тогда по формуле (8) коэффициент теплоотдачи равен:
- По формуле (12) определим коэффициент теплопередачи: к =
- Площадь поверхности труб вычисляется по формуле:1. F = %• dmp. ¦ Imp. -П21)гдеdmp.Hap. наружный диаметр труб, м- 1тр. — длина труб, м- п — число труб в кожухе, шт. F = 3,14 • 0,025 • 1,2 • 19 = 1,790 м²
- Количество тепла, передаваемое воде по формуле (6) равно: Q = 78,784 • 1,79 • (140−80) = 8460,456 Вт
- Аналогичный расчет проведем для других диаметров труб и других средних температур газовой смеси. Полученные данные сведем в таблицу 1.