Технологический расчет магистрального нефтепровода
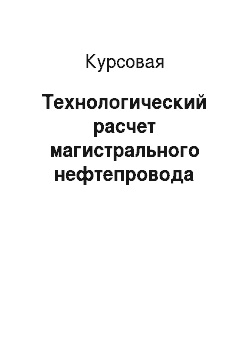
В отдельных случаях, например, при прохождении в одном коридоре нескольких нефтепроводов, на НПС параллельно уложенных магистралей помимо последовательного соединения насосов предусматривается возможность перехода к смешанной параллельно-последовательно схеме соединения всех четырёх агрегатов, включая резервный, а также переход к параллельной схеме работы насосов. Такие возможности… Читать ещё >
Технологический расчет магистрального нефтепровода (реферат, курсовая, диплом, контрольная)
Курсовой проект
Тема: Технологический расчет магистрального нефтепровода
Задание на курсовую работу
Рассчитать магистральный трубопровод по заданным параметрам:
Производительность в год 3,6 млн. т/год.
Температура грунта на глубине заложения трубопровода, +70С.
Плотность нефти 868 кг/м3 приТ=293 К.
Вязкость 16сСт.
Коэффициент неравномерности перекачки, Кнп=1,1.
Х, км | ||||||||||||||||
Z, м | ||||||||||||||||
Трубопроводный транспорт — прогрессивный, экономически выгодный вид транспорта, ему присущи: универсальность, отсутствие потерь грузов в процессе транспортировки при полной механизации и автоматизации трудоёмких погрузочно-разгрузочных работ, возврата тары и др. В результате этого снижается себестоимость транспортировки (например, для жидких грузов в 3 раза ниже по сравнению с перевозкой их по железным дорогам). Стоит также отметить высокую экологичность и безопасность перевозок. При помощи магистральных газонефтепроводов ежегодно перемещается миллионы тонн нефти и миллиарды кубических метров газа. 1]
Все эти преимущества транспорта газа, нефти и нефтепродуктов при помощи магистральных трубопроводов перед остальными видами транспорта создают отличные предпосылки для возрастания значения магистральных трубопроводов, их строительства и эксплуатации в больших объемах. [3]
1. Классификация нефтепроводов
Нефтепродуктопроводы протяженностью более 50 км и диаметром более 219 мм. называются магистральными. Магистральные трубопроводы в зависимости от перекачиваемой жидкости соответственно называются: нефтепроводами — при перекачке нефти; нефтепродуктопроводамипри перекачке жидких нефтепродуктов, например, бензина, керосина, дизельного топлива, мазута.
Магистральные нефтеи нефтепродуктопроводы и ответвления от них в соответствии со Строительными нормами и правилами (СНиП II-45−75) сооружают диаметром до 1620 мм с избыточным давлением не выше 10МПа (100 атм.). Они предназначаются для транспортировки нефти и нефтепродуктов из районов их добычи, производства или хранения до мест потребления — нефтебаз, пунктов налива и отдельных промышленных предприятий.
Магистральные нефте и нефтепродуктопроводы в зависимости от диаметра трубопровода подразделяются на четыре класса:
К I классу относятся трубопроводы диаметром 1620−1000 мм.;
ко II классу — трубопроводы диаметром 1000−500 мм.;
к III классу — трубопроводы диаметром 500−300 мм.;
к IV классу — трубопроводы диаметром менее 300 мм.
Нефтепроводы и нефтепродуктопроводы по устройству в принципе одинаковы и состоят из трубопровода и насосных станций, располагаемых вдоль трассы трубопровода. Различаются они только отдельными элементами технологических схем магистрального трубопровода.
Основными сооружениями магистрального нефтепровода являются: головная перекачивающая станция, которую размещают на начальном участке трубопровода (в районе нефтепромыслов), она служит для приема нефти с последующей подачей ее в трубопровод; промежуточные перекачивающие станции, которые обеспечивают дальнейшее передвижение нефти по трубопроводу; нефтебаза, где осуществляется прием нефти из трубопровода для дальнейшей отправки потребителю, и трубопровод с ответвлениями и линейными сооружениями, к которым относятся дома линейных ремонтников и аварийно-ремонтные пункты, устройства линейной и станционной связи, установки коррозионной защиты и др. В состав перекачивающих станций входят: резервуарный парк, устройства для пуска скребков или разделителей, установки для фильтров, а также отдельные емкости для сброса утечек и приема жидкости из предохранительных систем защиты. 1]
2. Принципы перекачки
По принципу перекачки на практике применяют две системы, постанционную и транзитную.
Постанционная перекачка характеризуется тем, что нефть поступает в резервуар промежуточной перекачивающей станции до его заполнения, а затем из него откачивают нефть для подачи на следующую станцию.
Для обеспечения непрерывности работы трубопровода на станциях предусматривается не менее двух резервуаров. Причем в один резервуар производится закачка, а из другого одновременно осуществляется откачка для подачи в трубопровод. По этой схеме требуется большее число резервуаров, что связано с усложнением условий эксплуатации и дополнительными затратами. Постанционная перекачка применяется в отдельных случаях: при накладке нефтепровода; выявлении пропускной способности отдельных его перегонов и др.
В основном применяют транзитную перекачку. При такой перекачке поступающий в резервуар продукт немедленно всасывается насосами и перекачивается на следующую станцию. Резервуар одновременно включен и на прием предыдущей станции, и на всасывание насосов для дальнейшей его перекачки.
В зависимости от способа включения самого резервуара различают следующие системы транзитной перекачки:
а) через резервуар;
б) с подключенным резервуаром;
в) из насоса в насос.
При перекачке «из насоса в насос» является наиболее совершенной в отношении предотвращения потерь продукта от испарения.
В качестве перекачивающих агрегатов наиболее эффективны центробежные насосы, так как они легко поддаются синхронизации и автоматическому регулированию. Кроме того, в отличие от поршневых они не дают опасного повышения давления даже при полном закрытии задвижки на нагнетании. Использование поршневых насосов может привести к тяжелой аварии вследствие недопустимого давления на выкиде насосов предыдущей станции. В этом случае обязательна установка предохранительных клапанов на приеме и выкиде, отрегулированных на допустимый избыток давления. Для приема избытка продукта из предохранительных клапанов предусматривают специальные резервуары.
Вообще все трубопроводные сети составляются из следующих основных элементов:
труб разного назначения;
соединительных частей (фланцев, соединительных муфт, колен, угольников, отводов, тройников, крестовин, гребенок и др.);
арматуры (чугунной, стальной, специальной);
компенсаторов.
Виды труб Для выбора размеров сечений элементов трубопроводов пользуются системой условных проходов, установленных ГОСТ 356–80 «Арматура и детали трубопроводов. Давления условные, пробные, рабочие. Ряды».
Для перекачки корродирующих нефтепродуктов применяются трубы из легированной стали (ГОСТ 550−75 «Трубы стальные бесшовные для нефтеперерабатывающей и нефтехимической промышленности. Технические условия»). Для трубопроводов наружным диаметром до 426 мм. используют стальные бесшовные горячекатаные трубы из углеродистых и легированных сталей.
Для магистральных трубопроводов диаметром более 426 мм. применяют электросварные прямошовные или спирально-сварные из низколегированных сталей с более высокими механическими свойствами по сравнению с углеродистыми сталями. Это позволяет изготавливать трубы со стенками уменьшенной толщины.
Существует два метода изготовления труб из стальных болванок:
1) непосредственное вытягивание нагретой до пластического состояния болванки с постепенным приданием ей формы трубы;
2) прокатка горячей болванки в пластину (штрипс) нужной толщины, которую затем сворачивают в трубу, а получающийся при этом продольный шов сваривают.
Трубы, изготовленные первым способом, называют цельнотянутыми, а вторым — сварными.
Цельнотянутые трубы, которые также называют бесшовными, изготавливают двумя способами: способом специальной прокатки и способом последовательного расширения. В обоих случаях процесс изготовления трубы начинается с придания болванке строго цилиндрической формы и превращения ее путем «прошивки» сердечником в гильзу со сквозным продольным отверстием небольшого диаметра.
Процесс изготовления сварной трубы начинают с заготовки длинной и узкой стальной полосы (штрипса) путем резки стальных листов на специальном стане. Затем на другом стане, имеющем ряд валков, штрипс последовательными этапами изгибается до придания ему формы трубы. Для сварки трубы применяют электродуговую сварку под слоем флюса на специальных станах.
Спирально сваренные трубы являются разновидностью сварных труб. Штрипс для них изготовляют в виде узкой стальной ленты, которая, проходя через специальный стан-автомат, изгибается в спираль по форме трубы. Спиральный шов сваривается автоматической сваркой. Такой шов увеличивает прочность трубы, повышая жесткость и не ослабляя продольного сечения.
Сварные трубы, кроме простоты изготовления и удешевления, имеют перед цельнотянутыми то преимущество, что их можно изготовлять большого диаметра с малой толщиной стенок.
Алюминиевые трубы конкурируют со стальными при сооружении низконапорных газои нефтепроводов и промысловых сборных коллекторов. Наибольший диаметр алюминиевых труб составляет 300 мм. Низкои среднепрочные сплавы алюминия легко свариваются. Применения алюминия делает ненужным антикоррозионные покрытия. [1]
3. Насосы НПС нефтепроводов
На НПС магистральных нефтепроводов используется два вида технологических насосов — подпорные и основные.
Основными насосами оборудуются основные НС: ГНПС и ПНПС. Данные насосы предназначены для непосредственного транспорта нефти. Подпорные насосы используются только на ГНПС (на их подпорных станциях) и играют вспомогательную роль. Они служат для отбора нефти из резервуарного парка и подачи ее на вход основным насосам с требуемым давлением (подпором), предотвращающим кавитацию в основных насосных агрегатах.
Современным типом основных насосов являются насосы НМ, которые выпускаются на подачу от 125 до 10 000 м3/ч. Данные насосы имеют две конструктивные разновидности.
Насосы на подачу от 125 до 710 м3/ч называются секционными, трёхступенчатыми.
Насосы НМ производительностью от 1250 м3/ч до 10 000 м3/ч спиральные одноступенчатые. Корпус их имеет улиткообразную форму с разъёмом в горизонтальной плоскости по оси ротора. Ротор состоит из вала и центробежного колеса двухстороннего входа, обеспечивающего ротору, благодаря своей конструкции, гидравлическую разгрузку от осевых сил. Опорами ротора служат подшипники — скольжения с принудительной смазкой (под давлением). Неуравновешенные остаточные осевые силы воспринимает радиально-упорный сдвоенный шарикоподшипник.
В подобных насосах используются торцевые уплотнения, которые монтируются в корпусе в месте выхода из него вала.
Конструкция спиральных насосов типа НМ рассчитана на давление 7,4 МПа, что допускает последовательное соединение не более трёх насосов данного вида.
Для повышения экономичности нефтепроводного транспорта при изменении производительности перекачки у спиральных насосов предусмотрено применение сменных роторов с рабочими колёсами на подачу 0,5 и 0,7 от номинальной (насос на подачу 1250 м3/ч имеет один сменный ротор на 0,7 номинальной подачи, а насос на подачу 10 000 м3/ч — дополнительный ротор на подачу 1,25 от номинальной).
Полная маркировка насосов типа НМ содержит группу буквенных обозначений, например: НМ 7000 — 210, где НМ обозначает нефтяной магистральный, 7000 — подачу в м3/ч, 210 — напор в метрах столба перекачиваемой жидкости.
Насосы на подачу от 125 до 710 м3/ч называются секционными, трёхступенчатыми. Корпус насоса, а точнее его нагнетателя, ограничен входной крышкой, расположенной над линией всасывания, и напорной крышкой над линией нагнетания. Между крышками установлены нагнетательные секции с основными рабочими колесами насоса. Рабочие колеса и используемое для увеличения всасывающей способности предвключенное шнековое колесо установлены на общем валу, соединенном через зубчатую муфту с электродвигателем. Нефть подается в насос через входной патрубок (находящийся под крышкой) и при содействии предвключенного шнекового колеса попадает в первую ступень нагнетателя, в которой происходит увеличение ее напора на некоторую величину. Затем нефть последовательно попадает в рабочие колеса, прохождение которых приводит к дальнейшему увеличению напора, и, наконец, через выкидной патрубок (находящийся под крышкой) нефть уходит из насоса.
Современным типом подпорных насосов являются насосы НПВ (нефтяные подпорные вертикальные). Они выпускаются четырёх типоразмеров: НПВ 1250−60, НПВ 2500−80, НПВ 3600−90, НПВ 5000−120. Цифры в маркировке указывают на производительность (м3/ч) и напор насоса (м).
Помимо насосов НПВ на ГНПС достаточно широко ещё используются подпорные насосы типа НМП (нефтяные магистральные подпорные). Эти насосы горизонтальные, наземной установки. Ротор их аналогичен ротору насоса НПВ, уплотнения торцевые, подшипники качения с кольцевой смазкой. Корпус спиральный с разъёмом в горизонтальной плоскости — подобен корпусу насосов НМ. Маркировка насосов НМП аналогична маркировке насосов НМ.
Основные насосы на НПС соединяются между собой главным образом последовательно. При этом допускается иметь не более трёх рабочих насосов, исходя из прочности агрегатов. В дополнение к трём рабочим насосам на станциях устанавливается по одному резервному агрегату.
В отдельных случаях, например, при прохождении в одном коридоре нескольких нефтепроводов, на НПС параллельно уложенных магистралей помимо последовательного соединения насосов предусматривается возможность перехода к смешанной параллельно-последовательно схеме соединения всех четырёх агрегатов, включая резервный, а также переход к параллельной схеме работы насосов. Такие возможности предусматриваются на аварийный случай. При выходе из строя какой-либо НПС, соседняя с ней станция на параллельной магистрали переводится на смешанную или параллельную работу насосов.
При этом к станции подключаются сразу два нефтепровода — собственный нефтепровод рассматриваемой станции и нефтепровод аварийной НПС. Отмеченное позволяет не прекращать перекачку по аварийному нефтепроводу и поддерживать его производительность на достаточно удовлетворительном уровне.
Подпорные насосы соединяются между собой только параллельно. В основном на подпорной станции используется один или два рабочих насоса и один резервный. 3]
Технологический расчет магистрального нефтепровода Технологический расчет магистральных трубопроводов предусматривает решение следующих основных задач:
— определение оптимальных параметров нефтепровода. К ним относятся диаметр трубопровода, давление на нефтеперекачивающих станциях, число нефтеперекачивающих станции;
— определение толщины стенки трубопровода;
— расчет на прочность и устойчивость;
— расстановка станций по трассе нефтепровода;
— расчет эксплуатационных режимов нефтепровода.
Основные этапы технологического расчета нефтепровода Расчетная часовая производительность нефтепровода определяется по формуле:
(1)
Где Gг — годовая (массовая) производительность нефтепровода, млн т/год;
с — расчетная плотность нефти, кг/м3;
Np — расчетное число рабочих дней в году, 350 суток;
kнп — коэффициент неравномерности перекачки, 1,1.
Расчетная плотность нефти при T=Tр определяется по формуле:
(2)
где с293 — плотность нефти при 293 К, кг/м3;
о — температурная поправка, кг/(м3· К).
Ориентировочное значение внутреннего диаметра вычисляется по формуле:
(3)
где w0 — рекомендуемая ориентировочная скорость перекачки нефти, 0,9 м/с.
.
Принимаем Dн=426 мм.
Фактическая скорость перекачки определяется по формуле:
(4)
Определение толщины стенки Расчетную толщину стенки трубопровода определяют по формуле:
(5)
где р — рабочее давление (избыточное); Dн — наружный диаметр трубы;
n1 -коэффициент надежности по нагрузке: n1 = 1,15 для нефте и нефтепродуктопроводов, работающих по системе из «насоса в насос»;
n1=1,1 — во всех остальных случаях;
R1 — расчетное сопротивление металла трубы и сварных соединений.
(6)
где RH1- нормативное сопротивление растяжению (сжатию) металла труб и сварных соединений, определяемое из условия работы на разрыв, равное минимальному пределу прочности увр;
m0- коэффициент условий работы трубопровода (m0 = 0,9 для трубопроводов III и IV категорий, m0 = 0,75 для трубопроводов I и II категорий и m0 = 0,6 для трубопроводов категории В);
К1 — коэффициент надежности по материалу (К1=1,47);
Кн — коэффициент надежности по назначению трубопровода, зависящий от его диаметра (для Dн<1000 мм Кн = 1, для Dн = 1200 мм Кн = 1,05).
Полученное расчетное значение толщины стенки округляем до ближайшего большего по сортаменту равного дН = 0,007 м. Так как округление произведено до наименьшего стандартного значения с запасом, то рассматривать применение стали 09ГБЮ нет необходимости.
Абсолютные значения максимального положительного и максимального отрицательного температурных перепадов по формулам:
(7)
где м=0,3- коэффициент Пуассона.
К дальнейшему расчету принимаем большую из величин = 88,41 град.
Находим величину продольных осевых сжи-мающих напряжений
(8)
Знак «минус» указывает на наличие осевых сжимающих напряжений. Вычисляем коэффициент, учитывающий двухосное напряженное состояние металла,
(9)
Пересчитываем толщину стенки нефтепродуктопровода:
Таким образом, ранее принятая толщина стенки равная дН=0,007 м может быть принята как окончательный результат.
4. Расчет на прочность и устойчивость
1.Вычисляем кольцевые напряжения от расчетного внутреннего давления:
2.Так как нефтепродуктопровод испытывает сжимающие напряжения, вычисляем коэффициент, учитывающий двухосное напряженное состояние металла труб:
(10)
Следовательно,
Так как,, то условие прочности трубопровода выполняется.
3. Вычисляем комплекс
4. Рассчитываем коэффициент, учитывающий двухосное напряженное состояние металла:
(11)
5. Вычисляем величины:
6. Находим максимальные суммарные продольные напряжения в трубопроводе:
(12)
Так как, и, следовательно, недопустимые пластические деформации трубопровода отсутствуют.
Теперь выполним проверку общей устойчивости нефтепродуктопровода.
7. Для глинистого грунта принимаем Cгр=20 кПа, цгр=16°.
8. Находим внутренний диаметр, площадь поперечного сечения металла трубы и осевой момент инерции:
9. Нагрузка от собственного веса металла трубы:
(13)
Нагрузку от собственного веса изоляции принимаем 10% от, т. е.
Нагрузка от веса нефтепродукта, находящегося в трубопроводе единичной длины:
(14)
То есть нагрузка от собственного веса заизолированного трубопровода с перекачиваемым нефтепродуктом:
(15)
10. Среднее удельное давление на единицу поверхности контакта трубопровода с грунтом:
(16)
11. Сопротивление грунта продольным перемещениям отрезка трубопровода единичной длины:
(17)
12. Сопротивление вертикальным перемещениям отрезка трубопровода единичной длины:
(18)
13. Продольное критическое усилие для прямолинейных участков в случае пластической связи трубы с грунтом находим:
(19)
Следовательно
14. Продольное критическое усилие для прямолинейных участков в случае упругой связи с грунтом:
(20)
Следовательно
15. Фактическое же эквивалентное продольное усилие в сечении трубы:
(21)
Так как, 2,04<4,21 и 2,04<37,89, то общая устойчивость прямолинейных участков нефтепродуктопровода обеспечена.
16. Теперь проверим общую устойчивость криволинейных участков трубопроводов, выполненных с упругим изгибом.
(22)
Рисунок 1 — Номограмма для определения коэффициента вn
17. По графику находим, что. Вычисляем критическое усилие для криволинейных участков трубопровода:
(23)
Из двух найденных значений выбираем меньшее. Для него:
18. Так как, 2,16>2,04, то условие устойчивости криволинейных участков выполняется.
5. Потери напора и гидравлический уклон в простом нефтепроводе
При перекачке нефти по магистральному нефтепроводу напор, развиваемый насосами нефтеперекачивающих станций, расходуется на трение hф, преодоление местных сопротивлений hмс, статического сопротивления из-за разности геодезических (нивелирных) отметок? z, а также создания требуемого остаточного напора в конце трубопровода hост. Таким образом, напор, необходимый для ведения перекачки с заданным расходом, равен:
H= hф+ hмс+?z+ hост. (24)
Следует отметить, что по нормам проектирования расстояние между линейными задвижками составляет 15…20 км, а повороты и изгибы трубопровода плавные, поэтому доля потерь на местные сопротивления в общей величине Н невелика. С учетом многолетнего опыта эксплуатации трубопроводов с достаточной для практических расчетов точностью можно принять, что потери напора на местные сопротивления составляют 1…3% (в среднем 2%) от линейных потерь. Тогда выражение (24) примет вид:
H= 1,02hф+?z+ hост. (25)
Под разностью геодезических отметок понимают разность отметок конца и начала трубопровода? z=zк-zн. Величина? z может быть как отрицательной (под уклоном), так и положительной (перекачка на подъем). ?z=120−20=100 м. Потери напора на трение в трубопроводе определяются по формуле Дарси-Вейсбаха:
(26)
где л — коэффициент гидравлического сопротивления;
Lр — расчетная длина нефтепровода.
Значение л в общем случае зависят от числа Рейнольдса и шероховатости внутренней поверхности трубы. Число Рейнольдса, характеризующее соотношение сил инерции и вязкости в потоке, вычисляется по формуле:
(27)
где х — расчетная кинематическая вязкость нефти.
Область турбулентного течения подразделяется на три зоны:
— гидравлически гладких труб | ||
— смешанного трения | Re1 | |
— квадратичного (шероховатого) трения | Re>Re2 | |
Значения переходных чисел РейнольдсаRe1 и Re2определяют по формулам:
(28)
где k — относительная шероховатость трубы, k=kэ/D, kэ — эквивалентная (абсолютная) шероховатость стенки трубы, зависящая от материала и способа изготовления трубы, а также от ее состояния. Для нефтепроводов после нескольких лет эксплуатации можно принять kэ=0,2 мм, k=0,2/426−10=0,0005.
Таким образом, имеет место турбулентный режим в зоне смешанного трения.
Расчет коэффициента гидравлического сопротивления производится по формуле:
(29)
Гидравлическим уклоном называют потери напора на трение, отнесенные к единице длины трубопровода
(30)
Линия гидравлического уклона показывает распределение остаточного напора по длине трубопровода. В любой точке трассы величина напора определяется вертикальным отрезком, отложенным от линии профиля трассы до пересечения с линией гидравлического уклона.
Остаточный напор необходим для преодоления сопротивления технологических коммуникаций и заполнения резервуаров конечного пункта.
(31)
где на 30% больше производительности насосов.
hост=915−705=210м.
Таким образом подбираем насосное оборудование, которое будет обеспечивать необходимый напор:
— 2 магистральных насоса НМ 250−475 и НМ 360−460;
— 2 подпорных насоса НПВ 150−60.
6. Определение перевальной точки и расчетной длины нефтепровода
нефтепровод прочность труба устойчивость Ближайшая к началу трубопровода возвышенность на трассе, от которой нефть с требуемым расходом приходит к конечному пункту самотеком, называется перевальной точкой. Это значит, что напор в месте расположения перевальной точки (разность высотных отметок перевальной точки и конечного пункта больше или равен сумме остаточного напора и потерь напора на участке между ними).
Прежде чем приступить к расстановке перекачивающих станций по трассе нефтепровода, необходимо исследовать ее на наличие перевальной точки (рисунок 1). Для этого сначала на сжатом профиле трассы в конечном пункте нефтепровода откладывают величину остаточного напора, а затем из полученной точки проводят линию гидравлического уклона.
Рисунок 2 — Профиль нефтепровода Так как линия гидравлического уклона не пересекает профиль трассы, то перевальной точки не существует.
Характеристика нефтепровода Характеристикой нефтепровода называется зависимость напора, необходимого для ведения перекачки, от расхода. Для трубопровода постоянного диаметра уравнение его характеристики имеет вид:
H= 1,02i· Lр+?z+Nэhост, (32)
где Nэ — число эксплуатационных участков.
При аналитическом решении задач трубопроводного транспорта удобно представлять величину гидравлического уклона в виде:
(33)
где f — гидравлический уклон при единичном расходе,
(34)
Тогда выражение (32) можно представить в виде:
(35)
Графически характеристика нефтепровода представлена на рисунке 3.
Рисунок 3 — Характеристика нефтепровода Уравнение баланса нефтепровода Из курса гидравлики известно уравнение Бернулли для установившегося течения несжимаемой жидкости:
(36)
где z1, P1, w1 — соответственно нивелирная высота, давление и средняя скорость потока в начале трубопровода,
z2, P2, w2 — то же для конечного сечения трубопровода,
h1−2 — потери напора на трение между начальным и конечным сечениями.
При перекачке нефти по трубопроводу постоянного диаметра с одной лишь головной перекачивающей станцией:
— скорость потока неизменна (w1=w2),
— удельная потенциальная энергия давления в начале трубопровода P1/(с· g) складывается из напора hП, создаваемого подпорным насосом, и напора НСТ, создаваемого магистральными насосами, то есть P1/(с· g)=hП+НСТ;
— удельная потенциальная энергия давления в конце трубопровода P2/(с· g) равна остаточному напору hОСТ;
— потери напора между начальным и конечным сечениями трубопровода складываются из потерь напора по длине и на местных сопротивлениях;
— разность нивелирных высот z2-z1=?z.
С учетом сказанного уравнение (36) можно переписать в виде:
(37)
1055=1041,5
Уравнение (37) называется уравнением баланса напоров. Оно читается так: расход в трубопроводе устанавливается сам собой (автоматически) таким образом, чтобы суммарный напор, развиваемый всеми работающими насосами, был равен напору, необходимому для ведения перекачки. По своей сути уравнение Бернулли (16) является математической записью закона сохранения энергии в трубопроводном транспорте нефти.
7. Определение числа перекачивающих станций
На этапе проектирования нефтепроводов, когда требуемая (плановая) производительность нефтепровода QПЛ задана, уравнение баланса напоров используется для определения расчетного числа нефтеперекачивающих станций n0:
(38)
Принимаем число станций n0=1.
Заключение
В данной курсовой работе произведен технологический расчет магистрального трубопровода по заданным параметрам. Определены размеры трубопровода, толщина стенки, произведен расчет на прочность и устойчивость, определены потери напора и гидравлический уклон, найдено число перекачивающих станций, произведена их расстановка, а также построено уравнение баланса нефтепровода.
Список использованных источников
1. Оборудование транспорта и хранения нефти и газа: учебное пособие для вузов / Г. В. Коннова. — 2-е издание. — Ростов н/Д.: Феникс, 2007.-128с.
2. Транспорт и хранение нефти, нефтепродуктов и газа. Бунчук В. А., М., «Недра», 1977, 366 с.
3. ОСТ 153−39.4−010−2002 Методика определения остаточного ресурса нефтегазопромысловых трубопроводов и трубопроводов головных сооружений. Утвержден и введен в действие приказом минэнергороссии от «5» августа 2002 г., № 255. Москва 2002, 24с.