Судовые вспомогательные механизмы и устройства
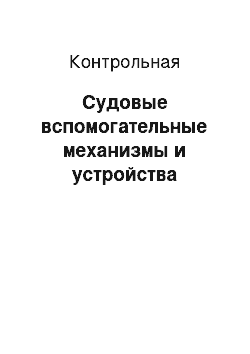
При заполнении системы каждый баллон взвешивают до и после использования для определения действительного количества вводимого в систему хладона. Удобно следить за массой баллона и ходом зарядки системы, если баллон подвешивать к динамометру 7. Для того чтобы полностью исключить попадание влаги в систему, несмотря на наличие стационарного фильтра-осушителя 15, между баллоном и наполнительным… Читать ещё >
Судовые вспомогательные механизмы и устройства (реферат, курсовая, диплом, контрольная)
Контрольная работа Судовые вспомогательные механизмы и устройства
- 1. Назначение и типы судовых вспомогательных механизмов и устройств
- 2. Судовые насосы
- 2.1 Классификация судовых насосов. Основные параметры насосов
- 2.2 Поршневые насосы
- 2.3 Шестеренные насосы
- 2.4 Винтовые насосы
- 2.5 Пластинчатые насосы
- 2.6 Водокольцевые насосы
- 2.7 Радиально — и аксиально-поршневые насосы переменной производительности
- 2.8 Центробежные насосы.
- 2.9 Вихревые насосы
- 2.10 Осевые насосы
- 2.11 Струйные насосы
- 2.12 Мембранные насосы
- 2.13 Подготовка к пуску, обслуживание во время работы и остановка судовых насосов
- 3. Судовые вентиляторы
- 4. Судовые компрессоры
- 5. Механизмы рулевых устройств
- 6. Механизмы якорных и швартовных устройств
- 7. Грузоподъемные механизмы
- 8. Топливные и масляные сепараторы
- 9. Судовые холодильные установки
- 9.1 Назначение и типы холодильных установок
- 9.2 Режимы холодильной обработки и хранения продуктов
- 9.3 Холодильные агенты и их свойства
- 9.4 Эксплуатация судовых холодильных установок
- 10. Опреснительные установки
- 11. Установки по предотвращению загрязнения морской среды
- 11.1 Установки очистки нефтесодержащих вод
- 11.2 Установки очистки сточных вод
- 11.3 Установки переработки мусора
- 11.4 Установки очистки выхлопных газов судовых дизелей (Скрубберы)
- Литература
1. Назначение и типы судовых вспомогательных механизмов и устройств
Судовые вспомогательные механизмы и устройства являются важной частью судовой энергетической установки. Вспомогательным механизмам принадлежит значительная доля в общем комплексе механического оборудования судна. Ввиду большого количества вспомогательных механизмов на судах, на них приходится значительная доля трудоёмкости по техническому обслуживанию и ремонтных затрат. Они потребляют значительное количество энергии, топлива, масла. От надёжности работы некоторых вспомогательных механизмов (якорного и рулевого) непосредственно зависит живучесть, безопасность плавания и непотопляемость судов. В создании хороших санитарно-гигиенических и бытовых условий на судах морского флота, решающая роль принадлежит вспомогательным устройствам (холодильным, водоопреснительным и кондиционным).
Судовые вспомогательные механизмы должны быть надёжны, экономичны в работе, удобны в эксплуатации, устойчивы в работе на переменных режимах, должны иметь возможность плавного регулирования производительности и мощности, обладать ограниченными шумностью и вибрацией в работе, иметь малые габаритные размеры, массу, построечную стоимость.
К судовым вспомогательным механизмам и системам относятся:
1. Насосы, компрессоры, вентиляторы, сепараторы;
2. Палубные механизмы: рулевые, якорные, швартовные, грузовые, шлюпочные, буксирные, траповые, спасательные, подруливающее.
3. Холодильные и кондиционные — служат для получения и поддержания определенной температуры в помещениях или устройствах.
4. Водоопреснительные — служат для получения пресной воды.
судовой насос вентилятор компрессор
5. Установки по предотвращению загрязнения морской среды — установки по обработке и очистке льяльных вод, сточных вод, обработка мусора, очистка выхлопных газов (скрубберы).
2. Судовые насосы
2.1 Классификация судовых насосов. Основные параметры насосов
Насосы — это гидравлические механизмы, предназначенные для перемещения на судне различных веществ.
По назначению насосы делятся на:
общесудовые — обслуживают общесудовые системы (осущительные, балластные, питьевой воды, пожарные, фекальные и т. д.);
специальные — установлены в специальных системах (креновые, дифферентные, грузовые, зачистные и т. д.);
насосы СЭУ (охлаждения двигателя, топливные насосы высокого давления ТНВД, топливоподкачивающие, масляные, питательные и т. д.)
По виду перекачиваемого вещества насосы бывают: водяные, топливные, масляные, конденсатные, рассольные, воздушные и т. д.
Различают автономные и неавтономные (навесные) насосы. Неавтономные насосы не имеют своего двигателя и навешиваются на обслуживаемое устройство. Автономные насосы по типу двигателя бывают: электрические, мотопомпы (привод от ДВС), турбонасосы и гидроприводные. Наибольшее применение на судах получили электрические насосы, мотопомпы применяют как аварийные насосы. Турбонасосы встречаются на танкерах старой постройки в качестве грузовых насосов, где необходима большая производительность.
По конструкции (принципу действия) насосы подразделяются на:
объемные — поршневые, ротационные (шестеренные, пластинчатые, винтовые, водокольцевые, аксиальнои радиально-поршневые)
лопастные (центробежные, осевые и вихревые);
струйные.
мембранные;
Каждый насос характеризуется основными параметрами:
объёмная производительность — объём жидкости, перекачиваемый насосом в единицу времени и измеряемый в мі/ч или л/сек.
напор - это давление, создаваемое насосом, выражается в метрах водяного столба или в кг/смІ (давление).
вакуумметрическая высота всасывания — способность насоса поднимать жидкость по всасывающему трубопроводу, выражается также в метрах водяного столба или в кг/смІ. Характеризует сумму высоты столба воды и потерь напора на преодоление сопротивления во всасывающей магистрали.
мощность — энергия, отдаваемая насосу приводным двигателем, выражается в киловаттах или лошадиных силах.
коэффициент полезного действия (к. п. д.) — представляет собой отношение полезной мощности к мощности насоса
К. п. д. учитывает все виды потерь.
З =Nп / N
к. п. д. учитывает все виды потерь:
з= з0 зг зм
з0 — объёмный к. п. д. — учитывает потери от утечек жидкой среды через неплотности (перетекание жидкости из полости нагнетания в полость всасывания и т. д.)
зг - гидравлический к. п. д. — учитывает потери энергии, затраченной на преодоление гидравлических сопротивлений в насосе.
зм - механический к. п. д. — учитывает механические потери в насосе.
число оборотов в минуту или число ходов поршня — параметр, от которого зависит производительность, напор и мощность.
2.2 Поршневые насосы
Судовые поршневые насосы классифицируются:
по кратности действия: простого, двойного и многократного действия
по конструктивному выполнению: одинарные, сдвоенные, многоцилиндровые, вертикальные и горизонтальные;
по способу соединения с двигателем: приводные через мотылёвый механизм и прямодействующие;
Поршневые насосы могут иметь привод от электродвигателя, через редуктор, с мотылевым механизмом и от паровой машины. Поршневые насосы обслуживают как водяные системы, так и системы перекачки нефтепродуктов; могут создавать высокие давления и имеют широкий диапазон производительности. Если насос за один двойной ход делает одно всасывание и одно нагнетание — это насос простого действия. Насосы простого действия с приводом от электродвигателя применяются в качестве осушительных.
Схема поршневого насоса двойного действия показана на рисунке 1.
Рис. 1. Схема поршневого насоса двойного действия: 1 — поршень; 2 — нагнетательный патрубок; 3 — клапанная коробка; 4, 9 — нагнетательные клапаны; 5, 8 — полости; 6, 7 — всасывающие клапаны.
Насос имеет две рабочие полости 8 и 5. Каждая полость имеет два клапана: всасывающий и нагнетательный. При движении поршня 1 вправо в полости 8 создаётся разряжение (вакуум), вследствие чего автоматически открывается клапан 7 и начинается ход всасывания жидкости. Когда поршень займёт правое крайнее положение и остановится для перемены направления движения, всасывание прекратится и всасывающий клапан закроется. При движении поршня влево, под давлением жидкости откроется нагнетательный клапан 9 и жидкость будет выталкиваться в полость клапанной коробки 3 и в нагнетательный патрубок 2. Обратная картина происходит в полости 5: при движении поршня влево открывается всасывающий клапан 6, а нагнетательный 4 будет закрыт под действием пружины и давления жидкости со стороны нагнетательной полости 3, а при перемене хода открыт нагнетательный и закрыт всасывающий клапан.
При одних и тех же размерах и скорости движения поршня насос двойного действия имеет производительность почти в два раза выше, чем насос простого действия.
Насосы трёхкратного, четырёхкратного и любого многократного действия представляют собой комбинацию двух типов этих насосов. Например, насос трёхкратного действия — это трёхцилиндровый насос простого
действия; четырёхкратного действия — двухцилиндровый насос двойного действия и т. д.
Прямодействующие паровые поршневые насосы, как правило, выполняются двухцилиндровыми в связи с простотой привода золотников парораспределения, когда поршень одного цилиндра приводит в движение золотник другого. Одноцилиндровым поршневым прямодействующим насосам нужен сложный по устройству цилиндрический золотник плавающего типа.
Преимущества поршневых насосов: способность к «сухому» всасыванию, т. е. при наличии воздуха в приёмном трубопроводе насос откачивает воздух без дополнительного устройства; могут создавать высокие давления.
Недостатки поршневых насосов: большой вес и габариты, поэтому они не применимы для перекачки больших объёмов жидкости; пульсирующая подача жидкости в трубопроводе; наличие клапанов усложняет конструкцию и является частой причиной ненормальной работы насоса; сложность привода; быстрый износ поршневых колец и необходимость их замены; большие затраты времени на обслуживание и ремонт.
2.3 Шестеренные насосы
Шестерённые масляные насосы имеют привод от электродвигателя или через систему зубчатых колёс от коленчатого вала двигателя. Привод от коленчатого вала имеют новейшие насосы вспомогательных дизелей и главных двигателей малой мощности (во втором случае насосы выполняются реверсивного типа).
Рис. 2. Устройство и схема работы шестеренного насоса с редукционным клапаном: 1 — корпус; 2,4 — зубчатые колеса (шестерни), 3 — приемный патрубок; 5 — перепускная полость; 6 — клапан; 7 — пружина; 8 — корпус клапана; 9 — регулировочный болт; 10 — контргайка; 11 — нагнетательный патрубок.
На Рис. 2 показаны устройство и схема работы шестерённого насоса.
Масло всасывается из приёмного патрубка 3, подхватывается зубьями колёс (шестерён) 2 и 4, которые вращаются в разные стороны, переноситься определенными объемами во впадинах и затем при зацеплении шестерен выдавливается в нагнетательный патрубок 11. Вал, приводимый от двигателя, является ведущим, а другой — ведомым и свободно проворачивается в подшипниках скольжения. Рабочее давление в масляной системе, составляет 2−6 кг/смІ. Для регулировки давления имеется редукционный клапан 6. Тарелка клапана 6 прижимается пружиной 7, натяжение которой регулируется болтом 9 с контргайкой 10, клапан автоматически открывается при повышении давления выше установленного и перепускает часть масла обратно во всасывающий патрубок через перепускную полость 5.
Современные дизели большой мощности обслуживаются масляными насосами с автономным приводом от электродвигателя и выполняются нереверсивными. Преимуществом их является возможность поддержания постоянного давления в системе, возможность ремонта резервного насоса, простота устройства. У навесных насосов давление зависит от числа оборотов дизеля. С увеличением производительности заметно проявляются недостатки шестерёнчатых насосов: уменьшение к. п. д., чрезмерный шум, пульсирующий поток, влияние на производительность зазоров между зубьями и торцами шестерён и корпуса.
В современных дизелях шестерённые насосы применяют в качестве масляных и топливных насосов.
2.4 Винтовые насосы
Рабочим органом насоса служит винт червячного типа. Число винтов может быть от 1 до 5. Двухвинтовой насос изображен на рис. 3. Насос состоит из двух червячных винтов. Один винт является ведущим, другой — ведомым. Винты размещены в съёмном корпусе. Шейки винтов обычно вращаются в бронзовых опорно-упорных подшипниках. Масло поступает из всасывающей полости корпуса насоса, заполняет впадины и вытесняется винтами в нагнетательную полость. Между всасывающей и нагнетательными полостями обычно ставят предохранительно-редукционный клапан.
Винтовые насосы отличаются высокой производительностью, хорошими всасывающими качествами, бесшумностью работы и равномерностью подачи масла. Недостатками винтовых насосов является высокая стоимость насоса (требуется высокая точность изготовления винтов) и требовательность к чистоте перекачиваемой жидкости. На судах насосы применяют как масляные — в гидравлических системах и маслоперекачивающие.
Рис. 3 Схема двухвинтового насоса: 1,5 — опорно-упорные подшипники; 2,4 — ведомые винты; 3 — корпус; 6 — центральный ведущий винт.
2.5 Пластинчатые насосы
Устройство пластинчатого насоса показано на Рис. 4.
Рис. 4. Пластинчатый насос: 1 — корпус; 2 — лопасти; 3 — ротор; 4 — нагнетательный патрубок; 5 — пружина; 6 — всасывающий (приемный) патрубок.
Пластины 2 помещены в прорезях ротора 3, который вращается в корпусе 1. При вращении ротора пластины под действием центробежных сил выходят из пазов и прижимаются к внутренней цилиндрической поверхности корпуса. Для создания дополнительной выдвигающей силы устанавливают пружины 5. Пройдя всасывающий патрубок 6, пластина создаёт разрежение, жидкость всасывается и заполняет полость между корпусом и ротором. Всасывание продолжается до горизонтального положения пластины, после чего вторая пластина начнёт вытеснять жидкость из объёма между ротором и корпусом. Ротор может иметь от двух до двенадцати пластин, а также от одной до трёх полостей и несколько секций. Это даёт возможность создавать насосы высокой производительности и большого напора.
Многопластинчатые насосы (Рис 5) создают более равномерный поток жидкости без пульсаций.
Рис. 5. Многопластинчатые насосы: 1 — пластина; 2 — ротор.
Пластинчатые насосы создают давление до 30 кг/смІ и широко применяются для привода гидравлических палубных механизмов: лебёдок, брашпилей, кранов, а также для перекачки масла и топлива.
2.6 Водокольцевые насосы
Водокольцевые насосы получили широкое применение благодаря способности создавать глубокий вакуум. Устройство насоса показано на Рис. 6. Корпус цилиндрический. Ротор состоит из вала и насаженного на него барабана с рабочими лопастями. Лопасти прямые или изогнутые, изготовлены заодно с барабаном. Ротор размещен в корпусе со смещением (эксцентрично). Корпус насоса закрыт с торцов крышками. На одной крышке установлены всасывающий и нагнетательный патрубки.
Рис. 6 Водокольцевой насос: 1-крышка; 2-корпус; 3-всасывающее отверстие; 4-ротор; 5-нагнетательное отверстие; 6 — водяное кольцо.
Внутри насоса находиться вода, заливаемая перед пуском. При вращении ротора лопасти воздействуют на воду, отбрасывая ее к поверхности корпуса. В результате этого образуется водяное кольцо и серповидное пространство, являющееся рабочей полостью насоса.
На первой половине оборота ротора жидкость наподобие поршня отходит от ротора, образуя разрежение (правая часть рисунка), и перекачиваемая жидкость или газ засасывается в насос. Эта половина оборота ротора называется всасывающей.
На второй половине оборота ротора кольцо приближается к нему, сжимая и выталкивая засосанную жидкость или газ в нагнетательное отверстие и патрубок. Эта половина оборота ротора нагнетательная.
Очень важно, чтобы при работе насоса не было утечек воды из него и толщина водяного кольца оставалась постоянной. В противном случае внутренний диаметр водяного кольца увеличивается, оно отойдет от поверхности ротора в верхней части и перекачиваемый газ будет просачиваться из нагнетательной полости во всасывающую. Работа насоса резко ухудшиться.
Водокольцевые насосы применяются на судах в качестве вакуумных устройств в самовсасывающих центробежных насосах, в конденсаторах испарительных установок.
Основное достоинство насосов — простота работы и обслуживания. Насосы не имеют специальной системы смазки. Все зазоры между вращающимся ротором и неподвижным корпусом уплотнены рабочей жидкостью. Простота конструкции, отсутствие трущихся пар в проточной части обеспечивают надежность и долговечность работы насоса.
2.7 Радиальнои аксиально-поршневые насосы переменной производительности
Различают роторные радиально-поршневые насосы с радиальным расположением цилиндров относительно оси вращения ротора и аксиально-поршневые насосы с аксиальным расположением цилиндров относительно оси вращения цилиндрового блока. В первых насосах движение поршней (плунжеров) происходит в одной плоскости, во вторых — в пространстве.
Радиально-поршневые насосы
В этих насосах (Рис.7) цилиндры располагают звездообразно, причем оси их находятся в общей плоскости и пересекаются в одной точке. Ротор 4 насоса, представляющий собой блок из нескольких цилиндров, вращается в постоянном направлении. Вместе с блоком вращаются находящиеся внутри его цилиндров плунжеры 5 и шарнирно связанные с ними ползуны 6. Опорные части ползунов прижимаются под действием центробежной силы к внутренней поверхности окружающего их направляющего кольца 7 и скользят по этой поверхности. Направляющее кольцо при помощи цапф 8 подвешивается к неподвижно укрепленному корпусу 9 насоса так, что может смещаться вправо или влево внутри корпуса, не теряя с ним связи. Окруженная звездообразным ротором центральная неподвижная часть (цапфа) насоса имеет перемычку 1, отделяющую верхнюю 3 внутреннюю полость насоса от нижней 2. В положении, показанном на Рис. 2, а, когда центр направляющего кольца 7 совпадает с центром звездообразного ротора 4, вращение последнего не вызывает подачи жидкости, заполняющей внутренние полости насоса. Плунжеры 5 вращаются вместе с ротором, но никакого движения внутри его цилиндров не получают.
Рис. 7. Схема радиально-поршневого насоса: 1 — перемычка; 2,3 — нижняя и верхняя полость насоса; 4 — ротор; 5 — плунжеры; 6 — ползуны; 7 — направляющие кольца; 8 — цапфы; 9 — корпус насоса
Сдвиг направляющего кольца вправо вызывает перемещение плунжеров в цилиндрах (Рис. 7, б), в результате чего плунжеры, продолжая вращаться вместе с ротором, одновременно получают возвратно-поступательное движение внутри цилиндров. При указанном направлении вращения ротора (против часовой стрелки) в нижнюю внутреннюю полость 2 жидкость будет всасываться, а в верхнюю полость 3 - нагнетаться. Если направляющее кольцо сместить влево, плунжеры также получат возвратно-поступательное движение в цилиндрах, но верхняя полость насоса окажется тогда всасывающей, а нижняя — нагнетательной. В присоединенных к этим полостям трубах направление движения жидкости изменится на обратное. Изменяя смещение кольца, т. е. получаемый им эксцентриситет по отношению к ротору, можно увеличивать или уменьшать ход плунжеров в цилиндрах, что будет изменять подачу, развиваемую насосом.
Применяют также схемы, в которых плунжеры опираются на кольцо при помощи роликов. Цилиндры располагают в один или несколько рядов (5−13 цилиндров в каждом ряду). Уплотнение плунжеров цилиндров достигается путем обеспечения минимального диаметрального зазора (0,03−0,04 мм). Радиально-поршневые насосы имеют большой срок службы. Они находят применение в мощных гидроприводах морских судов.
Аксиально-поршневые насосы.
Рис. 8. Схема аксиально-поршневого насоса: 1-крышка блока цилиндров; 2 блок цилиндров; 3-поршни; 4-шатуны; 5-регулировочный диск (шайба); 6-кардан; 7-ведущий вал; 8-отверстия.
Насос (Рис. 8) состоит из цилиндрового блока 2 с поршнями 3, связанными при помощи шатунов 4 с наклонным диском (шайбой) 5. Цилиндровый блок получает вращение от ведущего вала 7 с помощью кардана 6. Распределение жидкости происходит через окна а и b золотника и отверстия 8 в цилиндровом блоке. Если ведущий вал 7 и цилиндровый блок 2 расположить на одной оси (угол у = 0), то подача насоса также будет равна нулю, так как поршни 3, вращаясь вместе с блоком, не будут иметь осевых перемещений относительно своих цилиндров. При отклонении оси вала 7 от оси цилиндрового блока 2 на некоторый угол у, как это показано на схеме, поршни 3 получат наряду с вращательным движением совместно с блоком еще возвратно-поступательное движение внутри цилиндров, поэтому насос будет давать подачу рабочей жидкости определенного направления. Например, для указанных на схеме направления вращения и угла у верхнее окно а будет всасывающим, а нижнее В-нагнетательным. Если при неизменном направлении вращения отклонить ось вала 7 на угол V в противоположном направлении от оси блока 2, то окно а станет нагнетательным, а b - всасывающим. Изменение направления вращения приводного вала также изменило бы направление потока рабочей жидкости, но этого никогда не делают, так как выгоднее иметь приводной электродвигатель постоянного направления вращения. Таким образом, изменяя размер и знак угла у, регулируют значение и направление подачи насоса. Обычно наибольший угол у составляет 30°, а количество цилиндров в блоке 7-9. Поршень (плунжер) сажают в цилиндр с диаметральным зазором в пределах 0,01−0,02 мм, который обычно обеспечивают притиркой. Помещенный в смазанный вертикально расположенный цилиндр поршень должен медленно опускаться под действием собственного веса.
Одним из основных требований при обработке пары «поршень — цилиндр» является обеспечение цилиндричности их рабочих поверхностей; овальность и конусность их не должны превышать соответственно 0,002 и 0,005 мм.
Радиально и аксиально-поршневые насосы должны работать на определенном сорте рабочей жидкости (масле), так как от физико-химических свойств этой жидкости во многом зависит работоспособность насоса. Масло следует заливать в насос (гидросистему) через заливной фильтр, обеспечивающий надежную фильтрацию масла. Перед заливкой масло проверяют на соответствие государственному стандарту или техническим условиям. При заливке масла должен быть обеспечен выход воздуха из насоса (гидросистемы) через соответствующие отверстия, закрываемые пробками.
Во время эксплуатации насоса необходимо поддерживать требуемую чистоту рабочего масла путем своевременной очистки фильтров, спуска отстоя и замены отработавшего масла. Периодически следует производить анализ рабочего масла. Насос и всю гидросистему следует содержать в чистоте.
На работу насосов гидроприводов оказывает влияние также колебание температуры рабочего масла. При обслуживании насосов необходимо наблюдать за температурой рабочего масла и поддерживать его в пределах, указанных в инструкции по эксплуатации. При подготовке к действию насос необходимо осмотреть снаружи и убедиться в его исправности. При обнаружении ослабления болтов, крепящих гидронасос в установке, их следует подтянуть. Если гидронасос и его трубопровод не полностью заполнены маслом, то масло следует добавить. Насос запускают лишь после того, как подготовлен к работе гидропривод в целом. Во время работы насоса необходимо наблюдать за показаниями контрольно-измерительных приборов, которые должны соответствовать паспортным данным насоса. При подтекании масла из-под фланцев, мест разъемов крышек и подсоединений трубопроводов необходимо подтягивать крепежные детали. Нельзя допускать подсосы воздуха в гидросистему. При появлении ударов и стуков, свидетельствующих о ненормальной работе или поломке деталей насоса, его следует остановить и устранить причины неисправности. Пуск любого насоса без наличия в нем масла не допускается.
2.8 Центробежные насосы
Основным рабочим органом насоса является колесо 2 с лопастями (крылатка), насаженное на вал 3. Применяются колеса с лопастями загнутыми вперед, загнутыми назад или прямыми (радиальными).
Для пояснения работы центробежного насоса приведен Рис. 9
Рис. 9. Схема центробежного насоса: 1 — корпус; 2 — рабочее колесо; 3 — вал; 4 — всасывающий трубопровод; 5 — нагнетательный трубопровод.
Колесо вращается с большой скоростью в корпусе насоса и вода, находящаяся между лопастями колеса, отбрасывается от центра на периферию под действием центробежных сил в спиральный клапан — «улитку», переходящую в нагнетательный трубопровод 5. Так как вода отбрасывается из каналов рабочего колеса на периферию, то в его центральной части образуется вакуум, под действием которого всасывается вода из трубопровода 4. Насосы, в большинстве своём, располагаются в нижней части машинного отделения, поэтому находятся всегда под напором столба воды, что обеспечивает лучшее всасывание воды насосом. Для экономии места в машинном отделении насосы устанавливают вертикально. Для удобства производства ремонтов и осмотров насосы большого размера делаются с разъёмным корпусом.
На (Рис. 10, а) показана схема работы многоступенчатого центробежного насоса. На одном валу укреплено несколько колёс. Всасываемая жидкость подводится к первому колесу (первая ступень), а нагнетаемая им жидкость подводится на всасывание ко второму колесу (вторая ступень) и т. д.
Рис. 10 Схема действия центробежных насосов: а) с последовательным соединением колес; б) с параллельным
При последовательным подключением колес производительность насоса равна производительности одного колеса, а общий напор насоса будет равен сумме напоров отдельных ступеней.
Многоступенчатые насосы применяются в качестве питательных насосов с высокими параметрами.
В многопоточном насосе (Рис. 10, б) колёса насоса работают параллельно. Нагнетаемая ими жидкость идёт в одну общую трубу. При параллельной схеме подключения в работу нескольких колёс напор насоса будет равен напору одного колеса, а производительность насоса будет равна сумме производительности отдельных колёс. Многопоточные насосы применяются в качестве водоотливных, пожарных насосов на крупнотоннажных судах, грузовых насосов танкеров, т. е. там, где требуется большая производительность.
По конструкции эти насосы бывают самовсасывающие или несамовсасывающие, с горизонтальным или вертикальным расположением вала.
Центробежные насосы распространены на судах наиболее широко: устанавливают для перекачки воды и нефтепродуктов, что способствует следующие достоинства насосов:
равномерная подача жидкости;
простота устройства. Что повышает надежность работы насоса;
возможность перекачки сильно загрязненных жидкостей;
прямое соединение с быстроходны двигателем.
Основным недостатком центробежных насосов является отсутствие сухого всасывания. Поэтому их проектируют для работы с подпором. (ниже уровня перекачиваемой жидкости). В последние годы применяют самовсасывающие центробежные насосы, имеющие вакуумное устройство — на вал навешен водокольцевой насос.
2.9 Вихревые насосы
Вихревые насосы применяются на судах в системах санитарной воды, в системах охлаждениях ДВС, в качестве питательных насосов в паровых котлах и т. п.
Вихревые насосы изготавливаются с закрытыми и открытыми колесами, в одно и многоступенчатом исполнении.
Рис. 11. Схема вихревого насоса
Принцип действия одноступенчатого насоса (Рис.11): жидкость из всасывающего отверстия поступает к лопастям. Под действием центробежной силы жидкость отбрасывается в боковые каналы, при этом завихряется. Лопасти придают жидкости вихревое движение в кольцевом канале, заставляя ее перемещаться к нагнетательному отверстию. Одна и та же частица жидкости несколько раз попадает на лопасти и сбрасывается с них на своем пути, получая постоянное приращение энергии. В этом работа насоса сходна с действием многоступенчатого центробежного насоса. Благодаря многократному приращению энергии жидкости вихревой насос создает в 3−4 раза больший напор, чем центробежный при одинаковых оборотах. В этом состоит одно из преимуществ вихревого насоса.
Высокими эксплуатационными показателями отличаются центробежно-вихревые насосы, в которых удачно использованы достоинства центробежных и вихревых. (Рис.12)
Рис. 12. Центробежно-вихревой насос: 1-вал; 2-крышка; 3-корпус насоса; 4−8-корпус подшипников; 5-вихревое колесо; 6-центробежное колесо; 7-уплотнение; 9 — шариковый подшипник;
Центробежно-вихревой насос представляет собой блок из двух насосов — центробежного и вихревого, собранных на общем валу и соединенных между собой последовательно по ходу перекачиваемой жидкости. Насос имеет осевой подвод воды; на всасывающее линии его устанавливают центробежное колесо, обеспечивающее высоту всасывания до 5−7 м. Затем вода попадает в камеру вихревого колеса, где ей сообщается высокий напор. Таким образом в одном насосе удается объединить три важных качества: обеспечение большой высоты всасывания, присущей центробежным насосам, обеспечение большого напора, присущего вихревым насосам, и самовсасывание, также присущее вихревым насосам.
Отечественные насосы типа ЦВ изготавливаются с подачей 14−36 м3/ч и напором до 280 м ст. жидкости. Выпускаются также самовсасывающие центробежно-вихревые насосы ЦВС, имеющие воздушный колпак. Насосы типа ЦВ имеют к. п. д. порядка 0,45−0,48. Маркируют их следующим образом: ЦВ — центробежно-вихревой; первая цифра — подача в л/с; вторая цифра — напор в м вод. ст.
2.10 Осевые насосы
Осевые насосы применяются на судах в качестве аварийно-осушительных, для прокачки конденсаторов и других целей, где требуется большая производительность при невысоких напорах. Имея небольшие размеры, осевые насосы могут устанавливаться вертикально и горизонтально. Приводом насоса служит электродвигатель. Насосы могут быть одно — и многоколёсными, когда на одном валу последовательно насажено несколько колёс для увеличения напора насоса. Судовой осевой насос показан на Рис. 13.
Рис. 13. Схема осевого насоса: 1 — вал; 2,5 — обтекатели; 3 — направляющие лопасти; 4 — корпус; 6 — лопасти пропеллера.
2.11 Струйные насосы
Принципиальным отличием струйных насосов от остальных насосов является отсутствие движущихся деталей, что повышает их надежность работы и соответственно срок службы.
Рабочим органом струйных насосов служит струя жидкости или газа (обычно вода — водоструйные, пар — пароструйные или сжатый воздух — воздухоструйные.)
По назначению и устройству они делятся на эжекторы и инжекторы.
Эжекторы — это струйные насосы, предназначенные для всасывания, т. е. для удаления жидкости или газа из помещения или какого-либо устройства.
Рис. 14 Схема работы эжектора: 1 — сопло; 2 — всасывающая труба; 3 — нагнетательная труба.
Работа эжектора (Рис. 14):
к рабочему соплу 1 (диффузору) подводиться под давлением рабочее тело (вода, пар или сжатый воздух). За счет сужения сопла увеличивается скорость движения струи. Быстродвижущаяся струя в трубе 2 создает разрежение. Жидкость засасывается в трубу 2, а оттуда идёт по трубопроводу 3, где она смешивается с рабочим телом. Недостатком струйных насосов, является низкий к. п. д и неавтономность работы. К положительным качествам относятся: простота конструкций, высокая надёжность и долговечность, способность к самовсасыванию, возможность перекачивать сильно загрязненные жидкости, равномерная подача жидкости без пульсаций в трубопроводе. возможность работы в затопленном помещении. Эжекторы применяю на судах для создания вакуума в конденсаторах паровых установок, в вакуумных опреснителях, в качестве водоотливных насосов — для откачки аварийной воды из отсеков, при мойке трюмов судов после перевозки руды и угля, в качестве фекальных насосов, для зачистки грузовых и балластных танков на танкерах и др. целей. Инжекторные струйные насосы на судах не получили применения.
2.12 Мембранные насосы
Мембранный (диафрагменный) насос — объёмный насос, рабочий орган которого — гибкая пластина (диафрагма, мембрана), закреплённая по краям. (рис.15) Пластина изгибается под действием рычажного механизма (механический привод) или в результате изменения давления воздуха (пневматический привод) или жидкости (гидравлический привод), выполняя функцию, эквивалентную функции поршня в поршневом насосе.
Такие насосы встречаются на морских судах для окраски, осушения трюмов, для очистки днищ, кессонов для подводных работ, систем пожаротушения, резервуаров, содержащих сточные воды.
Рис. 15 Мембранный насос
1. Шаровые клапана забора/выпуска.
2. Диафрагма (мембрана).
3. Корпус головки дозирующего насоса.
4. Защита головки.
Достоинства насосов:
надёжная простая конструкция — отсутствие двигателя и редуктора, нет вращающихся деталей;
в качестве привода — энергия сжатого воздуха, отсутствие искрообразования, абсолютная безопасность при работе с горючими жидкостями;
компактные размеры и малый вес;
универсальность применения насосов — перекачка воды, вязких жидкостей, жидкостей с твердыми включениями до 12−15 мм в диаметре;
в насосах нет уплотнений и подшипников — гарантия отсутствия утечек и износа основных деталей;
простота регулирования производительности от нуля до максимума посредством изменения количества подаваемого воздуха;
для работы насоса не требуется смазка механизмов и обслуживание;
Недостатки мембранных насосов:
мембрана при работе значительно изгибается, что приводит к её быстрому разрушению;
конструкция мембранного насоса предполагает использование клапанов, которые могут выйти из строя при их загрязнении.
2.13 Подготовка к пуску, обслуживание во время работы и остановка судовых насосов
Перед пуском насоса необходимо произвести наружный осмотр и убедиться в том, что пуску насоса ни что не препятствует, т. е. что на корпусе насоса, на движущихся частях соприкасающихся с ним деталей нет посторонних предметов. Убедиться в исправном состоянии арматуры, в наличии и исправности всех штатных контрольно — измерительных приборов; проверить, открыты ли краны к манометрам и мановакууметрам; убедиться в исправном действии аварийно-предупредительной сигнализации и защиты; произведен замер сопротивления изоляции обмоток электромотора, которое должно быть не менее 1 МоМ.
Убедившись в том, что насос исправен и пуску его ничего не препятствует, запускают насос согласно инструкции по его обслуживанию.
Поршневые насосы пускают в ход при открытых всасывающем и напорном клапанах. Центробежные насосы пускают в ход при открытом всасывающем клапане и закрытом (либо чуть приоткрытом) нагнетательном клапане, а после запуска насоса нагнетательный клапан постепенно открывают. Перед пуском насоса, если нужно, заливают всасывающую магистраль и корпус насоса перекачиваемой жидкостью (если насос не имеет самовсасывающей приставки). Во время работы насоса наблюдают за показаниями контрольно-измерительных приборов, работой сальников, плотностью соединений насоса и звуком, издаваемым работающим насосом. При появлении ненормального шума или стуков насос следует остановить для выявления и устранения причины неисправности. Для вывода поршневого насоса из действия нужно остановить электродвигатель, закрыть клапаны на напорном и всасывающем трубопроводах и краны к манометру и мановакууметру.
Для вывода из действия центробежного насоса нужно закрыть нагнетательный клапан, остановить электродвигатель, затем закрыть всасывающий клапан и краны к манометру и мановакууметру.
3. Судовые вентиляторы
По конструкции судовые вентиляторы делятся на центробежные и осевые, а по назначению — вдувные (приточные), вытяжные и ветрогоны. Устройство и принцип действия центробежного и осевого вентилятора аналогично центробежному и осевому насосу.
На Рис. 16 Изображен центробежный вентилятор
Рис. 16 Вентилятор центробежный: 1-корпус; 2 — рабочее колесо; 3-приемный патрубок; 4-вал; 5-электродвигатель.
Осевые вентиляторы более просты по устройству и более компактны, но по создаваемому напору они уступают центробежным. (рис. 17)
Рис. 17. Осевой вентилятор для охлаждения компьютера
4. Судовые компрессоры
По конструкции судовые компрессоры бывают поршневые, осевые, центробежные, ротационные и спиральные. Наибольшее применение получили поршневые компрессоры, которые применяют в системах сжатого воздуха МКО, в холодильных установках, в качестве палубных для производства палубных работ.
Поршневые компрессоры
Поршневые воздушные компрессоры бывают одно-, двух-, или трехступенчатые. Количество ступеней зависит от конечного давления сжатого воздуха: для получения давления до 35 бар компрессоры выполняют двухступенчатыми, для более высокого давления — трехступенчатыми. Необходимость применения многоступенчатых компрессоров объясняется тем, что степень сжатия воздуха в одной ступени не должна превышать 8. При более высоких степенях сжатия температура в цилиндре может повыситься настолько, что произойдет самовоспламенение паров масла, поступающего на смазку цилиндров компрессора, а это может привести к взрыву и разрушению компрессора.
Для привода компрессора применяют электродвигатели (электрокомпрессоры) и дизели (мотокомпрессоры). Последние применяют как аварийные. По Правилам Регистра Украины суда с неограниченным районом плавания должны иметь не менее двух компрессоров (допускается применять в качестве резервного компрессор с приводом от главного двигателя)
В зависимости от расположения ступеней компрессоры бывают последовательного сжатия — тандем и дифференциальные (Рис. 18)
Трущиеся детали компрессора смазываются разбрызгиванием. Уровень масла в картере контролируют по маслоуказателю. Компрессор может охлаждаться как пресной, так и забортной водой. Каждая ступень имеет предохранительный клапан, который ежегодно осматривается и пломбируется Регистром. После каждой ступени установлены сепараторы-водомаслоотделители инерционного типа.
Рис. 18. Схемы трехступенчатых компрессоров сжатого воздуха: а — Тандем; б — дифференциального типа
Рис. 19. Поршневой компрессор с дифференциальным поршнем.
Перед пуском поршневого компрессора необходимо проверить наличие масла в картере и масленках, открыть продувочные краны сепараторов-водомаслоотделителей. Провернуть коленчатый вал компрессора на 2−3 оборота, открыть запорный клапан воздухохранителя. После набора полных оборотов закрыть краны продувания. Проверить отсутствие посторонних шумов и температуру холодильников и компрессоров.
Винтовые компрессоры
Основным элементом винтового компрессора является винтовая пара, состоящая из нескольких роторов (ведущего и ведомых, которые вращаются навстречу друг другу. Число роторов от одного дотрех. Сжатие воздуха осуществляется за счет вращения роторов винтовой пары навстречу друг другу. Конструктивные особенности винтовых компрессоров позволяют добиться большей производительности при меньшей мощности двигателя (по сравнению с поршневым компрессором). Этот факт обуславливает не только большую длительность ресурса, но и значительную экономию электроэнергии — до 40−50%. Кроме того, винтовые компрессоры имею меньшие массогабаритные параметры, обладают гораздо более низким уровнем шума и значительно проще в эксплуатации и обслуживании, долговечны (до 10 лет постоянной работы);
легкость монтажа, не имеют пульсации воздушного давления при запуске, длительная устойчивая работа (способны работать 24 часа в сутки), высокий КПД 92%.
Недостатки — относительно высокая стоимость компрессора ввиду технологической сложности его изготовления.
Рис. 20 Устройство двухвинтового компрессора
Ротационные компрессоры
Особенностью ротационных компрессоров по сравнению с поршневыми является отсутствие кривошипно-шатунного механизма и возвратно-поступательно движущегося поршня. Поэтому ротационные компрессоры имеют хорошую уравновешенность, сравнительно малую массу, меньшее количество движущихся частей, подвергающихся износу, а также отсутствие всасывающих, а в некоторых конструкциях и нагнетательных клапанов. Они проще в обслуживании и более надежны в работе. К недостаткам ротационных компрессоров можно отнести сложность их изготовления и ремонта, большой износ движущихся частей.
Все многообразие конструкций ротационных компрессоров можно свести к двум основным типам:
компрессоры с вращающимся ротором, ось которого фиксируется относительно оси цилиндра (пластинчатые ротационные компрессоры);
компрессоры с катящимся ротором, ось которого вращается вокруг оси цилиндра, и ротор при этом обкатывает цилиндр.
Ниже описаны ротационные компрессоры с катящимся ротором фирмы «Rotasco» (Япония). Удачное решение схемы смазки компрессора и подбор пары трения позволили получить ротационный компрессор одноступенчатого сжатия, который успешно эксплуатируют в холдильных установках.
" Rotasco" относится к группе компрессоров с катящимся ротором.
На рис. 21 показана принципиальная схема работы компрессора «Rotasco». В цилиндрическом корпусе 1 на валу 3 эксцентрично насажен поршень 4. Диаметр и эксцентриситет поршня подобраны так, что он касается поверхности цилиндра по линии, разделяющей рабочий объем цилиндра от полости всасывания и нагнетания.
Шибер (пластина) 2, прижимающийся к поршню в верхней части цилиндра, делит рабочий объем его на две рабочие полости. Шибер может совершать колебательное движение. В целях лучшего уплотнения шибера с ротирующим поршнем и уменьшения трения в рабочую поверхность шибера вложена специальная уплотняющая полоска, прижимающаяся к поверхности поршня с помощью пружины. Для лучшего соприкосновения катящегося поршня со стенками цилиндра поршень обтянут тонкостенной эластичной втулкой из высококачественной специальной стали.
Рис. 21. Последовательность процессов всасывания, сжатия и нагнетания в ротационном компрессоре: 1-корпус; 2 — шибер (пластина); 3-вал; 4-поршень
К недостаткам пластинчатых ротационных компрессоров относится большой износ неметаллических пластин и значительные потери мощности на трение пластин в пазах и при скольжении по цилиндру. Кроме того, существуют значительные трудности по обеспечению высоких требований к качеству пластин. Энергетическая эффективность пластинчатых компрессоров ниже, чем у поршневых компрессоров, как вследствие указанных причин, так и из-за значительных перетечек газа.
Ротационные компрессоры нашли применение в холодильных установках холодопроизводительностью до 1000 кВт при работе на аммиаке и хладонах.
Спиральные компрессоры
Спиральные компрессоры с каждым годом находят все большее применение в технике и прежде всего в холодильной. Это обусловлено тем, что они более надежны в эксплуатации, содержат на 40% меньше деталей, чем поршневые, производят меньше шума и имеют больший ресурс эксплуатации.
В 1905 г. французский инженер Леон Круа разработал конструкцию спирального компрессора и получил на нее патент. Однако в то время эта технология не могла быть реализована в жизнь, т.к. отсутствовала необходимая производственная база. Поэтому конструкцию работающего прототипа пришлось ждать до второй половины двадцатого века, т.к. для эффективного функционирования, в спиральном компрессоре необходимо обеспечение малого конструктивного зазора в сопрягаемых деталях (спиралях). Такая точность стала возможной только при прецизионной машинной обработке, разработанной в течение второй половины двадцатого века, чем и объясняется относительно недавнее появление спирального компрессора на рынке высокотехнологического оборудования. Последние несколько лет объем производства спиральных компрессоров быстро увеличивается, и к январю 2000 г. было произведено свыше 20 млн. компрессоров.
Спиральные компрессоры нашли применение во всех основных системах воздушного кондиционирования, включая сплит и мультисплит модели, напольные версии и в чиллерах, руфтопах (крышных кондиционерах) и тепловых насосах. Типичным применением является кондиционирование воздуха в квартирах, на кораблях, фабриках и больших зданиях, также на АТС, в процессах охлаждения и на транспорте. Холодильные спиральные компрессоры широко используются в компрессорно-конденсаторных агрегатах, в системах «выносного холода» супермаркетов, в промышленном холоде и в транспортных установках, включая контейнеры. Границы холодопроизводительности для спиральных компрессоров постоянно увеличиваются и в настоящее время приближаются к 200 кВт при использовании многокомпрессорной станции.
Рабочими органами спирального компрессора является две спиральные пластины. Вставленные в друг друга.
(Рис. 22, б) Спираль НС неподвижна. Центр спирали движется по окружности радиусом R. Вращение осуществляется валом с эксцентриком, который шарнирно соединен с противоповоротным устройством. Подвижная спираль ПС не вращается вокруг своей оси. Она совершает движение только по определенной орбите радиусом R вокруг оси неподвижной спирали, совпадающей с осью вала. Повороту вращающейся спирали вокруг своей оси препятствуют противоповоротное устройство.
В ценре неподвижной пластины расположено нагнетательное отверстие Подвижная и неподвижная пластины имеют одинаковые размеры, но противоположное направление закрутки спиралей. Если спирали вставлены одна в другую, стенками спиралей образуются ячейки. некоторые из их замкнуты. Объем замкнутых ячеек при движении подвижной спирали изменяется. Газ, находящийся в замкнутом объеме. Сжимается и направляется в нагнетательное отверстие.
Рис. 22 Спиральный компрессор: а — конструкция: б — взаимное положение спиралей по углу поворота
I-положение 0°
1-неподвижная спираль; II-положение 90°
2-подвижная спираль; III-положение 180°
3-эксценрик; IV-положение 270°
4-противоповоротное устройство;
5-опрный подшипник;
6-нижний подшипник;
7-всасывающий патрубок;
8 — масляный поддон.
На Рис. 22 б показаны взаимные положения спиралей при перемещении подвижной спирали по кривой орбите через 90°. Цикл всасывания совершается за 1 оборот вала компрессора. Цикл сжатия и нагнетания длиться от 2 до 2,5 оборотов в зависимости от угла закрутки спирали и размера окна нагнетания. Все три фазы — всасывание, сжатие и нагнетание происходят одновременно.
Центробежные и осевые компрессоры
Центробежный компрессор, часто называемый в технике турбокомпрессором, изображен на рис. 23. В нем установлен вал 1 в подшипниках скольжения 2. На валу напрессованы колеса 3, оснащенные по окружности лопатками 4. При вращении колес центробежная сила выбрасывает массу газа или паров из межлопаточных каналов, сжимает их и перемещает из всасывающего патрубка 5 в нагнетательный патрубок 6. Этот компрессор трехступенчатого сжатия. Для предотвращения выхода сжатой среды в атмосферу установлено уплотнение вала 7.
Рис. 23. З-х ступенчатый центробежный компрессор
Меньшее применение получили осевые компрессоры. На Рис. 24 изображен многоступенчатый осевой компрессор.
Рис. 24 Осевой компрессор
Компрессор имеет ротор 4, состоящий обычно из нескольких рядов рабочих лопаток 6. На внутренней стенке корпуса 2 располагаются ряды направляющих лопаток 5. Всасывание газа происходит через канал 3, а нагнетание через канал 1. Одну ступень осевого компрессора составляет ряд рабочих и ряд направляющих лопаток. При работе осевого компрессора вращающиеся рабочие лопатки оказывают на находящиеся между ними частицы газа силовое воздействие, заставляя их сжиматься, а также перемещаться параллельно оси К. (откуда его название) и вращаться. Решётка из неподвижных направляющих лопаток обеспечивает главным образом изменение направления скорости частиц газа, необходимое для эффективного действия следующей ступени. В некоторых конструкциях осевых компрессоров между направляющими лопатками происходит и дополнительное повышение давления за счёт уменьшения скорости газа.
Основные недостатки центробежных и осевых компрессоров проявляются при небольших производительностях, поэтому КПД небольших компрессоров существенно ниже, чем поршневых или винтовых, что связано с малыми геометрическими размерами их проточной части.
5. Механизмы рулевых устройств
Рулевое устройство предназначено для обеспечения управляемости судна, т. е. ведения его по заданному курсу и поворота в нужном направлении. От его надёжной работы зависит безопасность плавания судна.
По требованиям Морского Регистра Украины главный рулевой привод и баллер должны обеспечивать перекладку руля с 350 одного борта на 350 другого борта при максимальных эксплуатационных осадке и скорости переднего хода судна и, при тех же самых условиях, с 350 одного борта на 300 другого борта не более чем за 28 секунд;
Вспомогательный рулевой привод должен:
1. иметь надлежащую прочность и быть в состоянии управлять судном при скорости, обеспечивающей его управляемость, и быстро приводиться в действие в экстренных случаях;
2. обеспечивать перекладку руля с 34 одного борта на 34 другого борта не более чем за 60 секунд при максимальной эксплуатационной осадке судна и скорости, равной половине максимальной эксплуатационной скорости переднего хода или 7 узлам, смотря по тому, что больше.
Силовые агрегаты главного и вспомогательного рулевых приводов должны:
запускаться автоматически при восстановлении питания энергией после его потери;
приводиться в действие с поста на ходовом мостике. В случае потери питания энергией любого из силовых агрегатов рулевого привода на ходовом мостике должны подаваться звуковой и световой сигналы.
Рулевое устройство состоит из следующих основных узлов:
пера руля с баллером — непосредственно обеспечивает управляемость судна;
рулевого привода — для передачи усилия от рулевой машины к баллеру руля и тем самым перекладки пера руля;
рулевой машины — является силовой частью рулевого устройства и предназначена для приведения в движение рулевого привода;
системы дистанционного управления (телемотора) — для управления рулевого устройства с мостика. Телемоторы бывают механические, электрические и гидравлические.
Рулевые приводы
Назначение рулевого привода — передать усилие от рулевой машины на баллер руля.
Рулевые приводы бывают механические и гидравлические.
Современные морские суда оборудованы гидравлическими рулевыми приводами. Преимущество гидравлических приводов — плавность и точность перекладки руля, возможность получения больших мощностей при относительно малых размерах, экономичность, а также возможность автоматизации всего рулевого комплекса.
По конструкции гидравлические рулевые приводы бывают плунжерные (Рис. 25) и лопастные (Рис. 26).
Рис. 25 Схема плунжерного гидравлического привода: 1-баллер руля; 2-румпель; 3-муфта; 4-цапфы; 5-плунжер; 6-гидроцилиндры; 7 — трубопроводы; 8-рулевой насос; 9-электродвигатель; 10 — предохранительно-перепускной клапан
На баллер руля 1 жестко насажен румпель 2, который может двигаться в шарнирной муфте 3 с цапфами 4. С муфтой соединены два плунжера 5 гидравлических цилиндров 6. Если при помощи плунжеров передвигать шарнирную муфту с борта на борт, то румпель, скользя в муфте, также будет поворачиваться на соответствующий угол. Передвижение плунжеров осуществляется нагнетание гидравлической жидкости под большим давлением в один цилиндр и отсасыванием жидкости из другого цилиндра. Гидравлические цилиндры трубопроводом 7 соединены с насосом 8, имеющим привод от электродвигателя 9. Если насос отсасывает жидкость из правого цилиндра и нагнетает в левый, то румпель повернется на правый борт, а руль на левый борт, т. е. произойдет поворот судна влево. При нагнетании жидкости в правый цилиндр произойдет поворот руля и судна на правый борт. Предохранительно-перепускной клапан 10 служит для смягчения ударов волн, перепуская часть жидкости из одной полости в другую.
На Рис. 26 изображен более современный — лопастной рулевой привод.
Рис. 26 Схема гидравлического лопастного привода: 1-лопастной привод; 2-баллер; 3-гидроцилиндр; 4-радиальные перегородки; 5 — предохранительно-перепускной клапан; 6,9 — трубопроводы; 7 — масляный насос; 8 — электродвигатель.
На баллер руля 2 жёстко насажен лопастный привод, состоящий из двух лопастей 1 и цилиндра 3. С одной стороны лопасти приварены к цилиндрической втулке, которая жёстко насажена на вал привода, соединённый с баллером руля. С другой стороны, лопасти плотно прилегают к поверхности цилиндра 3. Цилиндр имеет две радиальные перегородки 4, прилегающие к цилиндрической втулке. Лопасти и радиальные перегородки разделяют цилиндр на четыре полости, объём которых изменяется в зависимости от положения лопастей. Чтобы жидкость не перетекала из одной полости в другую, торцы лопастей и радиальных перегородок имеют уплотнения из маслостойкой резины или нейлона. Полости рулевого привода сообщаются трубопроводами 6 и 9 с масляным насосом 7, приводимым электродвигателем 8. По команде из рулевой рубки, при помощи дистанционного привода управления, насос 7 отсасывает жидкость из одной пары полостей гидроцилиндра и нагнетает во вторую пару полостей. Лопасти под давлением жидкости будут поворачивать баллер с рулём.
Предохранительно-перепускной клапан 5 служит для смягчения ударов волн, предохраняет гидравлическую систему от чрезмерного повышения давления в ней, перепуская жидкость из одной полости в другую.
Рулевые машины.
К рулевым машинам предъявляют следующие требования:
безотказность в работе и пуск из любого положения с развитием полной мощности;
обеспечение перекладки руля с борта на борт на полном ходу не более чем за 30 секунд;
рулевая машина должна быть реверсивной, т. е. одна машина должна перекладывать руль на левый и правый борт;
при остановке штурвала рулевая машина должна остановиться, а руль при этом должен находиться на заданном углу перекладки;
руль должен перекладываться на тот борт, в какую сторону рулевой вращает штурвал;
рулевая машина должна автоматически останавливаться, когда руль достигнет своего крайнего левого или правого положения.
Для питания гидравлических цилиндров рулевого привода рабочей жидкостью устанавливается насос с приводом от электродвигателя. Гидравлические насосы по своей конструкции бывают переменной и постоянной производительности.
Насосы переменной производительности при вращении в одну сторону с постоянной скоростью могут изменять величину производительности и направление потока жидкости. Эти насосы выполняются поршневого типа, с радиальным и осевым расположением цилиндров.
Насосы постоянной производительности также широко применяются в гидравлических рулевых устройствах. Это насосы с постоянной скоростью вращения, производительностью и направлением потока гидравлической жидкости. Количество жидкости, поступающей в гидравлические цилиндры рулевого привода, направление всасывания и нагнетания регулирует электрогидравлический золотник, управляемый из ходовой рубки.
В качестве насосов постоянной производительности могут служить винтовые насосы. В качестве рабочей жидкости в системе гидравлической рулевой машины применяется гидравлические масла разных марок.
При подготовке рулевой машины к действию следует произвести внешний осмотр, проверить положение клапанов, пробок, золотников и установить их положение согласно требований инструкций. Следует проверить также фланцевые соединения трубопроводов и арматуры гидравлической системы. Проверить исправность предохранительных и перепускных клапанов, основных и резервных насосов, а также запасного рулевого привода, согласовать правильность перекладки руля с мостиком.
Во время работы рулевой машины необходимо периодически её осматривать, обращая внимание на давление рабочей жидкости в системе, уровень масла в расходной цистерне; следить за отсутствием пропусков масла в гидравлической системе и бесшумностью работы.
Для дистанционного управления рулевыми машинами из рулевой рубки служат приводы управления.
Приводы управления рулевой машиной (телемоторы)
Приводы управления (телемоторы) бывают электрическими, гидравлическими и механическими. Наибольшее распространение получил электрический привод управления.
При якорных операциях необходимо строго соблюдать правила техники безопасности.
Запрещается:
отдавать палубные стопоры якорной цепи и разобщать брашпиль, не убедившись в надежности крепления цепного барабана ленточным тормозом;
включать брашпиль на холостой ход, не удостоверившись в том, что цепные барабаны разобщены с валом;
сообщать цепные барабаны с валом без предварительного проворачивания брашпиля на холостом ходу;
отдавать якорь, не убедившись в отсутствии людей или посторонних предметов в цепном ящике и плавсредств под носовым подзором судна;
находиться на линии движения якорной цепи впереди или позади брашпиля и вблизи движущейся якорной цепи;
применять для остановки якорной цепи при ее вытравливании винтовые и другие палубные стопоры;
оставлять без надзора работающий брашпиль;
укладывать якорную цепь путем ее растаскивания в цепном ящике, находясь внутри ящика. Растаскивать якорную цепь можно только абгалдырями. Которые после окончания укладки цепи нельзя оставлять в цепном ящике;
отдавать якорь от грунта ходом судна и втягивать якорь в клюз в присутствии людей в цепном ящике;
посылать людей в цепной ящик для очистки якорной цепи, не включив брашпиль и не взяв якорную цепь на палубные стопоры;
работать брашпилем во время проведения забортных работ по очистке якоря;
оставлять в клюзах якоря закрепленными только на ленточных стопорах при стоянке судна у причала или на палубе производят какие-либо работы с якорной цепью. В этих случаях якорные цепи должны быть закреплены дополнительно палубными стопорами;
Все действия при отдаче и подъема якоря должны производиться только по команде руководителя работ — помощника капитана.
6. Механизмы якорных и швартовных устройств
Якорные устройства обеспечивают постановку судна на якорь, а швартовные — подтягивание и крепление судна к стационарным и подвижным объектам (причалам, другим судам и др.)
Якорное устройство состоит из якоря, который создаёт силу, удерживающую судно при стоянке на открытой воде; якорной цепи для связи судна с якорем (цепи создают также значительную дополнительную держащую силу; стопора — приспособления для закрепления якорного каната и удержания якоря в походном положении; якорных клюзов — наклонных стальных труб для прохода якорной цепи через корпус судна и втягивания в них якорей при закреплении последних по-походному; якорных механизмов для подъёма якорей; цепного ящика для хранения якорных цепей в походном положении.
Швартовное устройство включает в себя следующие элементы: швартовные канаты, вьюшки для наматывания и хранения канатов на судне; швартовные механизмы для создания необходимых усилий на швартовых канатах при подтягивании судна к причалу; кнехты и другие приспособления для закрепления на судне швартовных канатов, киповые планки и швартовные клюзы для изменения направления швартовных канатов, поданных с судна на причал; кранцев (мягких, жёстких или пружинных) для защиты корпуса и надстроек от повреждений при наваливании судна на причал во время швартовки.
Якорно-швартовная лебёдка, обычно, выполняется одним механизмом, который имеет звёздочку для обслуживания якорной цепи и швартовный барабан для швартовных канатов.
Механизмы разделяются на шпили и брашпили. Шпили имеют вертикальную ось вращения тяговых узлов, брашпили — горизонтальную. Шпиль — компактный и простой механизм. Он устанавливается как в носовой, так и в кормовой частях судна.
Суда, не имеющие кормовых якорей, оборудуются кормовыми шпилями без звёздочек, которые в этом случае называются швартовными.
На Рис. 27 Показаны конструктивные типы шпилей.
Рис. 27. Схемы расположения шпилей: а) двухпалубное; б) надпалубное; в) подпалубное; 1-турачка; 2-электродвигатель; 3-редуктор
Брашпили устанавливаются на баке (в носовой части судна), где, по условиям эксплуатации судна, необходимо одновременно обслуживать два носовых якоря. (Рис 28)
По роду используемой энергии якорно-швартовные механизмы подразделяются на паровые, электрические и электрогидравлические.
Широкое применение получили также якорно-швартовные и швартовные лебёдки. Эти устройства имеют специальный барабан для укладки швартовных концов, что исключает необходимость ручного труда при проведении швартовных операций и сокращает их продолжительность.
Швартовные лебёдки в зависимости от типа, назначения и размеров судна могут устанавливаться на баке, на грузовой и кормовой палубах. Швартовные лебёдки, предназначенные для выполнения только швартовных операций, бывают простые и автоматические.
Простые лебёдки подтягивают судно во время швартовки, а автоматические, кроме этого, поддерживают определенное, заранее заданное, тяговое усилие. Это освобождает обслуживающий персонал от необходимости наблюдения за натяжением или провисанием швартовных канатов.
Рис. 28. Устройство электрического брашпиля: 1,10 — швартовные турачки; 2 — грузовой вал; 3,9 — ленточные тормоза; 4,8 — цепные звездочки; 5,7 — кулачковые муфты; 6,13 — цилиндрические шестерни; 11,12 — червячная передача; 14 — брашпиль; 15 — цепной стопор; 16 — клюз; 17 — цепной ящик; 18 — жвакагалс.
При якорных операциях необходимо строго соблюдать правила техники безопасности.
Запрещается:
отдавать палубные стопоры якорной цепи и разобщать брашпиль, не убедившись в надежности крепления цепного барабана ленточным тормозом;
включать брашпиль на холостой ход, не удостоверившись в том, что цепные барабаны разобщены с валом;
сообщать цепные барабаны с валом без предварительного проворачивания брашпиля на холостом ходу;
отдавать якорь, не убедившись в отсутствии людей или посторонних предметов в цепном ящике и плавсредств под носовым подзором судна;
находиться на линии движения якорной цепи впереди или позади брашпиля и вблизи движущейся якорной цепи;
применять для остановки якорной цепи при ее вытравливании винтовые и другие палубные стопоры;
оставлять без надзора работающий брашпиль;
укладывать якорную цепь путем ее растаскивания в цепном ящике, находясь внутри ящика. Растаскивать якорную цепь можно только абгалдырями. Которые после окончания укладки цепи нельзя оставлять в цепном ящике;
отдавать якорь от грунта ходом судна и втягивать якорь в клюз в присутствии людей в цепном ящике;
посылать людей в цепной ящик для очистки якорной цепи, не включив брашпиль и не взяв якорную цепь на палубные стопоры;
работать брашпилем во время проведения забортных работ по очистке якоря;
оставлять в клюзах якоря закрепленными только на ленточных стопорах при стоянке судна у причала или на палубе производят какие-либо работы с якорной цепью. В этих случаях якорные цепи должны быть закреплены дополнительно палубными стопорами;
Все действия при отдаче и подъема якоря должны производиться только по команде руководителя работ — помощника капитана.
При швартовных работах необходимо соблюдать правила техники безопасности.
Запрещается:
присутствовать посторонним лицам в местах производства швартовных работ;
применять для швартовных работ жесткие стальные тросы;
подавать, выбирать, вытравливать, закреплять и отдавать швартовный трос, а также пускать в действие швартовный механизм без команды лица, руководящего швартовными операциями;
подавать бросательный конец без предварительного окрика: «Берегись!» ;
работать внутри шлагов троса, разнесенного по палубе;
подавать швартовные тросы, имеющие калышки и необрубленные концы оборванных проволок;
крепить тросы на швартовных барабанах даже на непродолжительное время;
накладывать, снимать или перетравливать шлаги троса на вращающихся швартовных барабанах;
выбирать или стравливать тросы во время работы с ними у кипов и роульсов;
подбирать швартовные тросы до получения подтверждения с берега, что трос закреплен и «чист» О начале работ необходимо предупреждать работающих на берегу;
применять цепные стопоры для стопорения растительных и синтетических тросов;
находиться на линии натяжения троса и стопора и ближе 2 м. от места его наложения;
работать со стальными тросами без рукавиц;
находиться и держать руки ближе 1 м. от барабанов, кнехтов, блоков и т. п., а при работе со швартовами из синтетических материалов — ближе 2 м.
поправлять или удерживать шлаги на барабанах лебедок во время их работы.
7. Грузоподъемные механизмы
На судах применяют два основных типа грузовых устройств: со стрелами и с кранами, которые дают возможность перемещать груз в вертикальном и горизонтальном направлениях.
Рис. 29. Вариант грузового устройства судна:
1 — перекидная тяжеловесная стрела; 2 — легкая стрела; 3 — грузовой кран.
Грузовое устройство со стрелами состоит из грузовых стрел, лебедок и соответствующего такелажа. Грузовые стрелы подразделяют на легкие грузоподъемностью до 10 т (Рис. 30) и тяжеловесные (Рис. 31) грузоподъемностью 10 т и более.
Рис. 30. Легкая грузовая стрела
Рис. 31. Стрела-тяжеловес
Рис. 32 Поворотные краны
Грузовое устройство с кранами состоит из палубных кранов, которые могут быть полноповоротными — кран поворачивается на 360° (Рис. 32), неподвижными и перемещающимися по подкрановым путям вдоль или поперек судна — козловые и мостовые краны (Рис. 33)
Рис. 33. Козловой кран контейнеровоза: 1-колона; 2-консоль; 3 — тележка с контейнером.
Появление транспортных судов с горизонтальной грузообработкой связано с различными видами колесной техники. Перемещение груза на таких судах в процессе грузовых работ осуществляется с помощью аппарелей. На паромных судах носовая и кормовая аппарели обеспечивают сквозной проезд автомобилей. Багаж и почта грузятся вилочными автопогрузчиками, которые въезжают внутрь судна по бортовым аппарелям.
На ролкерах используются более производительные аппарели, обычно — угловые. Передвижение колесной техники с палубы на палубу производится по внутренним подъемным аппарелям или постоянно закрепленным наклонным площадкам — пандусам. (Рис. 34)
Рис. 34. Возможные схемы устройств для горизонтальной обработки судов: а) — на паромах; б) — на ролкерах; 1-обтекатель; 2 — носовая аппарель; 3-подъемник: 4-бортовая аппарель; 5-бортовой лацпорт; 6-закрытие комового проема; 7-кормовая аппарель; 8-угловая аппарель; 9-закрытие кормового проема; 10-пандус; 11-закрытие проема; 12-герметизированные закрытия пандусов; 13-лацпорты; 14-люки; 15-закрытие носового проема.
При грузовых работах необходимо строго соблюдать правила техники безопасности.
Запрещается при работе лебедок и кранов:
поднимать грузы, масса которых больше грузоподъемности стрелы или крана;
поднимать груз с находящимися на нем людьми или незакрепленными предметами, а также груз, находящийся в неустойчивом положении или заложенный другими грузами;
оттягивать, разворачивать и останавливать раскачивающийся груз во время подъема, перемещения или опускания без применения специальных оттяжек;
подавать груз в трюм без предупредительного окрика или сигнала, если в нем находятся люди;
подавать груз в трюм до того, как с просвета люка будет убран ранее поданный груз и люди отойдут в безопасное место;
проносить груз на высоте менее 0,5 м. от конструкций судна или предметов, находящихся на пути перемещения груза;
оставлять по окончании работ или во время перерыва груз на весу;
оставлять без присмотра механизмы, находящихся под напряжением;
поправлять шкентель рукой, сматывать или наматывать его на барабан лебедки одному во время ее работы;
находиться на линии перемещения груза, под грузом или стрелой, в просвете люка. А также спускаться в трюм или подниматься из него при подъеме или опускании груза.
8. Топливные и масляные сепараторы
Судовые сепараторы очищают топливо и масло от механических примесей и воды. Отделение механических примесей и воды, как более тяжёлых частиц, происходит в центробежных сепараторах под действием центробежных сил, возникающих при вращательном движении топлива или масла. На морских судах устанавливают центробежные сепараторы тарельчатого (дискового) типа самоочищающиеся или с ручной очисткой. Отделение грязи и механических примесей от топлива называется кларификацией (осветлением), отделение воды — пурификацией (очищением).
Обводнённое и загрязнённое топливо очищают, применяя комбинированную очистку. Для этой цели на судах устанавливают два сепаратора, один из которых работает в режиме кларификации, другой — в режиме пурификации. Сепарирование масла и сепараторы для него ничем не отличаются от топливных сепараторов и, при наличии соединительной системы, могут быть взаимозаменяемы. На морских судах устанавливают дисковые сепараторы типа СЦС, «Лаваль», «Титан», «Вестфалия» и других зарубежных фирм.
Сборка барабанов на кларификацию и сборка на пурификацию отличаются друг от друга.
Во вращающийся барабан сепаратора, собранный как кларификатор (Рис. 35, а), топливо поступает по центральному каналу в нижнюю часть барабана, отбрасывается к стенкам, проходит по зазорам между тарелками и отводится через кларификационные отверстия (на рисунке показано стрелками). Механические примеси и грязь осаждаются на стенках барабана и на поверхностях тарелок под действием центробежных сил. Осадок со стенок барабана и с тарелок удаляют вручную при разборке сепаратора.
Рис. 35. Настройка барабана сепаратора: а — на кларификацию, б — на пурификацию; 1 — тарелка без отверстия, 2 — грязевое пространство; 3 — тарелка с отверстиями.
Методом кларификации пользуются при наличии в топливе значительного количества механических примесей и незначительного количества воды. Вода, отбрасываемая вместе с механическими примесями, заполняет всё грязевое пространство 2 и образует гидравлический затвор, который перекроет путь поступления топлива в межтарелочные зазоры. Топливо, поступающее в барабан непрерывным потоком, начнёт выливаться из патрубка переполнения. В этом случае сепаратор останавливают и очищают барабан. При кларификации, сепаратор запускают с сухим барабаном и, когда он разовьёт необходимые обороты (8−10 тыс. об/мин), постепенно наполняют топливом Для сепарирования обводнённого (до 3% и более воды) топлива, барабан сепаратора собирают, как пурификатор Для этого устанавливают нижнюю тарелку 3 с отверстиями. При работе сепаратора по методу пурификации барабан заполняют тёплой водой, температура которой должна быть одинакова с температурой сепарируемого топлива. Вода образует водяной затвор, а топливо проходит по отверстиям тарелках. Вода и механические примеси отделяются от топлива в межтарелочных зазорах и устремляются к стенкам барабана. Отделившаяся вода непрерывно отводится от барабана (на рисунке показано стрелками). Самоочищающиеся сепараторы отличаются от несамоотчищающихся конструкцией барабана, очистка которого происходит без остановки сепаратора.
В момент пуска сепаратора разгрузочные отверстия открыты и поршень находится в нижнем положении. Движением поршня управляет специальная гидравлическая система, рабочей жидкостью в которой является вода. Когда барабан наберёт необходимое число оборотов, воду подают в камеру 8, откуда она через отверстия 7 и 9 идёт, соответственно, в полости 6 и 3. Из полости 6 вода сливается наружу к отверстию 10, а из полости 3 — по отверстию 4, каналу 11 в теле поршня к кольцевому пазу 12 в стенке барабана и каналу 5. Подача воды прекращается после заполнения системы полостей и каналов. Из полости 6 вытекает часть воды, которая находится между отверстием 10 и стержнем барабана, в то время, как из полости 3 вода сливается полностью. В результате действия центробежных сил, оставшаяся в полости 6 вода создаёт давление на запирающий поршень, который поднимается и перекрывает разгрузочные отверстия. После этого, в сепаратор подают топливо и работа по очистке топлива происходит, как описано выше.
Рис. 36. Устройство барабана самоочищающегося сепаратора СЦС-3: 1 — разгрузочное отверстие; 2 — запирающий поршень; 3,6 — водяные полости; 4,7,9,10 — отверстия, 5 — сливной канал, 8 — камера; 11 — канал; 12 — кольцевой паз.
Для очистки барабана вновь подают воду в камеру 8, из которой по отверстию 7 и восьми отверстиями 9 вода начинает поступать в полости 6 и 3. В полости 3 вода накапливается гораздо быстрее, т.к. подаётся через восемь отверстий. Накопившаяся вода в полости 3 опускает поршень. Для очистки сепаратора прекращают подачу топлива в барабан и подают в большом количестве подогретую воду. Скопившаяся грязь под действием центробежных сил выбрасывается из барабана через разгрузочные отверстия. После остановки сепаратора вода из полости 6 стекает и поршень под действием силы тяжести опускается в нижнее положение.
9. Судовые холодильные установки
9.1 Назначение и типы холодильных установок
На флоте впервые «машинное» охлаждение было применено на пароходе «Фригорифин» в 1876 г. для перевозки мяса из Аргентины (Буэнос-Айрес) во Францию (Руан). Эта дата считается общепризнанным началом применения холодильной техники на судах.
В настоящее время холодильные установки устанавливают практически на всех судах. На транспортных (сухогрузных и наливных) и пассажирских судах холодильные машины используют для охлаждения провизионных кладовых. На судах с горизонтальным способом грузообработки и других, имеющих большие трюмы, холодильные установки применяют также для охлаждения емкости с жидкой углекислотой, предназначенной для тушения пожара. На рефрижераторных судах и судах комбинированного типа холодильные машины используют для охлаждения рефрижераторных трюмов, на газовозах — для охлаждения танков со сжиженным газом, на судах рыбопромыслового флота — для охлаждения и замораживания добытой морепродукции и приготовления искусственного льда.
Кроме того, морские суда являются местом постоянной работы и жительства экипажей и продолжительного пребывания пассажиров. Поэтому в жилых, служебных, общественных и пассажирских помещениях в любых районах плавания, в любое время года и при любых метеорологических условиях должен поддерживаться благоприятный для людей микроклимат, т. е. совокупность состава и параметров состояния воздуха, а также тепловых излучений в ограниченных пространствах помещений.
Микроклимат в судовых помещениях обеспечивается с помощью систем искусственного микроклимата, которые служат для очистки и тепловлажностной обработки воздуха, подаваемого в помещения.
Стальное судно, разделенное на отсеки поперечными и продольными переборками и промежуточными палубами, представляет собой разветвленную теплопроводную систему, внутри которой находятся помещения с высокой температурой и источниками тепла (машинные и котельные отделения, электростанции, аккумуляторные и т. д.). Очевидно, что охлаждаемые помещения независимо от их назначения необходимо располагать дальше от этих источников тепла.
Другой особенностью судовой холодильной установки в отличие от береговой являются повышенные требования к надежности и безопасности ее работы, которые определяются международными конвенциями, а также Правилами Морского Регистра Украины, Правилами классификационных обществ других стран.
Конструкция отдельных механизмов, аппаратов и других элементов судовой холодильной установки, их размещение и крепление должны обеспечивать надежную и бесперебойную работу установки в условиях шторма, крена и дифферента. Это требование важно еще и потому, что к некоторым элементам установки нет доступа для осмотра и ремонта в случае их выхода из строя во время рейса (например, к охлаждающим батареям и воздухопроводам, расположенным в трюмах). В связи с этим Правила Регистра Украины предусматривают повышенные пробные давления при испытании отдельных элементов установки и трубопроводов на прочность и плотность.
Наиболее распространенным способом непрерывного получения холода в большом количестве является машинное охлаждение. Холодильные установки машинного типа подразделяются на:
1. Воздушные;
2. Абсорбционные;
3. Пароэжекторные.
4. Парокомпрессорные
Воздушные холодильные установки (ВХУ)
На Рис. 37 показана простейшая ВХУ.
Рис. 37 Схема простейшей ВХУ.
Воздух из помещения П, где поддерживается температура Т1, засасывается компрессором К и сжимается от давления Р0 до Р. При этом его температура возрастает до Т2. Горячий воздух охлаждается забортной водой в холодильнике ПО и выходит в помещение. Расширяясь воздух охлаждается и сТ1 снова засасывается компрессором. Цикл повторяется.
Достоинством ВХМ является то, что роль хладагента выполняет бесплатный безвредный воздух.
Однако, большого практического применения ВХМ не нашли. Их используют в системах кондиционирования воздуха в самолетах, автомобилях, термобарокамерах.
Термоэлектрические холодильные установки.
Термоэлектрическое охлаждение основано на эффекте Пельте, заключающемся в том, что в процессе прохождения постоянного тока определенного направления по цепи, составленной из разнородных проводников или полупроводников, в местах контактов (спаях) появляются разные температуры. Если температура холодного спая окажется ниже температуры окружающей среды, то он может быть использован как охладитель. Термоэлектрические охлаждающие устройства (ТОУ) сейчас применяют в медицине, радиотехнике и др. областях.
В технике широко известен эффект возникновения термо ЭДС в спаянных проводниках, контакты (места спаев) между которыми поддерживаются при различных температурах (эффект Зеебека). В том случае, когда через цепь двух разнородных материалов пропускается постоянный ток, один из спаев начинает нагреваться, а другой — охлаждаться. Это явление носит название термоэлектрического эффекта или эффекта Пельтье.
Рис.38 Схема термоэлемента
На рис. 33 показана схема термоэлемента. Два полупроводника n и m составляют контур, по которому проходит постоянный ток от источника питания С, при этом температура холодных спаев X становится ниже, а температура горячих спаев Г становится выше температуры окружающей среды, т. е. термоэлемент начинает выполнять функции холодильной машины. Температура спая снижается вследствие того, что под воздействием электрического поля электроны, двигаясь из одной ветви термоэлемента (m) в другую (n), переходят в новое состояние с более высокой энергией. Энергия электронов повышается за счет кинетической энергии, отбираемой от атомов ветвей термоэлемента в местах их сопряжений, в результате чего этот спай (X) охлаждается. При переходе с более высокого энергетического уровня (ветвь п) на низкий энергетический уровень (ветвь т) электроны отдают часть своей энергии атомам спая Г термоэлемента, который начинает нагреваться.
Энергетическая эффективность термоэлектрических холодильных машин значительно ниже эффективности других типов холодильных машин, однако простота, надежность и отсутствие шума делают использование термоэлектрического охлаждения весьма перспективным.
К недостаткам термоохлаждающих устройств следует отнести их низкую экономичность и повышенную стоимость. Примерами устройств этого класса могут служить охладители питьевой воды, воздушные кондиционеры, охладители реактивов в химическом производстве и др. Для таких холодильных машин образцовым циклом будет треугольный цикл Лоренца. Приближение к образцовому циклу достигается простым путем, так как для этого требуется только видоизменить электрическую схему коммутации, что не вызывает конструктивных трудностей. Это позволяет существенно, в некоторых случаях более чем вдвое, повысить эффективность термоэлектрических холодильных машин. Для реализации этого принципа в паровой холодильной машине пришлось бы применять сложную схему многоступенчатого сжатия.
Широкое внедрение термоэлектрического охлаждения будет зависеть от прогресса в создании совершенных полупроводниковых материалов, а также от серийного производства эффективных в экономическом отношении термобатарей
Абсорбционные холодильные установки
Первая абсорбционная холодильная машина была создана во Франции в 1859 году и запатентована в 1860 Фердинандом Карре (Ferdinand Carre). В качестве рабочего тела использовалась смесь аммиака и воды. Из-за высокой токсичности аммиака такие холодильные машины в то время не получили широкого распространения для домашнего применения и использовались для промышленного производства льда.
В установках кондиционирования воздуха абсорбционный холодильный цикл начал использоваться более пятидесяти лет назад.
В производственных процессах, в которых требовалось поддержание низких температур, стали применяться аммиачно-водяные АБХМ.
В конце 1950;х годов была создана первая двухступенчатая бромистолитиевая абсорбционная холодильная машина. Позже бромистолитиевые АБХМ стали использоваться не только для охлаждения помещений, но и в качестве источника горячей воды.
Совершенствование компрессоров, повышение эффективности электродвигателей, устройств управления позволили повысить эффективность компрессорных холодильных машин и снизить стоимость их эксплуатации. Кроме того, свою роль в замедлении распространения АБХМ на природном газе сыграл энергетический кризис 1970;х годов.
Ограничение применения озоноразрушающих фреонов и непрерывное возрастание стоимости электрической энергии способствовали очередному повышению интереса потребителей к АБХМ. (Стоимость природного газа остается достаточно стабильной, а сама технология абсорбционного охлаждения совершенствуется).
АБХМ включает в себя генератор, конденсатор, испаритель и абсорбер с хладагентом и бромидом лития в качестве рабочих растворов.
В генераторе под действием источника тепла (горелка, дымовые газы, пар или горячая вода) из разбавленного раствора бромида лития выделяются пары хладагента (воды), которые затем переносятся в конденсатор. Здесь они конденсируются в жидкость, отдавая в процессе конденсации тепло охлаждающей воде. После этого жидкий хладагент попадает на трубки испарителя, унося тепло от охлаждаемой воды и испаряясь при этом. Концентрированный раствор бромида лития из генератора переходит в абсорбер, поглощая пары хладагента из испарителя и разбавляясь ими. Разбавленный раствор бромида лития перекачивается в генератор, где цикл начинается снова. Чиллеры с подобным циклом называются одноконтурными чиллерами (Single effect type).
Более высокой эффективностью по сравнению с одноступенчатыми отличаются двухступенчатые АБХМ (Рис.39)
Рис. 39. Схема двухступенчатой абсорбционной холодильной машины.
В двухступенчатых чиллерах (Double effect type) генераторная секция разделена на две части — высокотемпературный и низкотемпературный генераторы. Пары хладагента, образующиеся в высокотемпературном генераторе, используются для подогрева раствора бромида лития в низкотемпературном генераторе, в котором давление, а, следовательно, и точка кипения, ниже. Как и в одноконтурных чиллерах, пары хладагента, создаваемые в низкотемпературном генераторе, поступают в конденсатор, чтобы там превратиться в жидкость. С другой стороны, пары хладагента, создаваемые в высокотемпературном генераторе, превращаются в жидкость по мере того, как высвобождается тепло из раствора бромида лития. Это происходит в трубках теплообменника в низкотемпературном генераторе. Пары хладагента из высоко — и из низкотемпературного генератора превращаются в жидкость и смешиваются в конденсаторе перед тем, как вернуться в испаритель. Таким образом, на этом этапе разбавленный раствор нагревается тепловым источником в высокотемпературном генераторе, а в теплообменнике низкотемпературного генератора — скрытым теплом паров хладагента, которое в другом случае должно было бы высвободиться в охлаждающую жидкость. Это означает, что затраты энергии источника тепла меньше. Более того, чем меньше количество тепла, сбрасываемое в охлаждающую жидкость, тем меньше может быть градирня. Например, в то время как существующий тип одноконтурного чиллера требует градирню с номинальной емкостью 200 USRT при 100 USRT нагрузки, для двухконтурного чиллера достаточно всего 34 USRT при той же нагрузке. Благодаря исследованиям и инновациям производители АБХМ достигли значительных успехов в технологии абсорбционного охлаждения и КПД абсорбционных холодильных машин в настоящее время составляет 0,64−0,66.
Пароэжекторные холодильные установки
Принцип работы установки сводиться к созданию сильного разрежения в испарителе с помощью эжектора. В состав такой установки, помимо указанных аппаратов, входят сжимающее устройство, обеспечивающее повышение давления паров, отсасываемых из испарителя, до давления конденсации, конденсатор и регулирующее устройство, в котором жидкость дросселируется (давление понижается до давления в испарителе).
В пароэжекторных ХУ в качестве агента используют воду, которая охлаждается за счет частичного перехода ее в парообразное состояние при вакууме 3−8 мм. рт. ст., что соответствует температуре испарения — 5—+8°С. Вода безвредна и, кроме того, обладает большой теплотой парообразования.
Высокие удельные объемы водяных паров при низких температурах кипения (например — 5 °C удельный объем водяных паров равен 307 м3/кг) требуют применения эжектора — пароструйного компрессора, который сжимает холодные пары, поступающие из испарителя, до давления в конденсаторе и преобразует тепловую. Энергию рабочего пара в кинетическую энергию движения струи. Эжектор состоит из сопла, камеры смещения и диффузора. Принципиальная схема пароэжекторной ХУ представлена на Рис 40.
Рис. 40 Принципиальная схема пароэжекторной пароводяной ХУ: 1-сопло; 2-камера смешения; 3-испаритель; 4-диффузор; 5-конденсатор; 6-воздушный эжектор; 7,8 — насосы; 9-охлаждающая батарея;
РВ — регулирующий вентиль.
Рабочий пар при давлении 1−7кг/см2 из котла поступает в эжектор. Здесь пар расширяется в сопле соответствующего профиля, приобретая сверхзвуковую скорость. В камере смешения 2 этот поток пара подхватывает холодные пары, поступающие из испарителя 3, затрачивая при этом часть кинетической энергии. Далее смесь паров с давлением кипения (р) поступает в диффузор 4, где в расширяющейся его части происходит увеличение ее давления (сжатие) до давления конденсации (р)
Тепло конденсации паров отводиться из конденсатора 5 охлаждающей водой. По выходе из аппарата конденсат разделяется на два потока: один поступает через регулирующее устройство в испаритель, другой насосом 7 перекачивается в паровой котел. Пар из испарителя постоянно отсасывается эжектором. Конденсатор должен быть оборудован воздушным эжектором 6 для откачки воздуха, который может попасть в систему (например, через неплотности). Холодная вода из испарителя насосом 8 перекачивается в охлаждающую батарею 9.
При охлаждении воды до +5°С вследствие несложной конструкции аппаратов и отсутствия движущихся частей эжекторные ХУ экономичны, поэтому их широко применяют в установках кондиционирования воздуха.
Недостатком этих установок является то, что они пригодны для работы при температуре кипения от 10 до 0 °C.
Рабочим телом в пароэжекторных холодильных установках могут быть и другие вещества.
Эффективность пароэжекторной холодильной машины так же, как и абсорбционной, повышается, если для приготовления пара используются источники бросовой теплоты (выпускные газы двигателей и т. п.).
Парокомпрессорные холодильные установки.
Из машинных способов охлаждения наибольшее применение получили парокомпрессорные холодильные установки, в которых применяют следующие системы охлаждения: непосредственная; рассольная; воздушная.
При непосредственном охлаждении испаритель установлен непосредственно в охлаждаемом помещении и хладагент, испаряясь в нём, отбирает тепло сам. Непосредственное охлаждение применяется для охлаждения небольших провизионных камер.
На Рис. 41 изображена схема парокомпрессорной холодильной установки с непосредственным охлаждением.
Рис. 41 Парокомпрессорная холодильная установка с непосредственной системой охлаждения: 1 — всасывающий клапан; 2 — нагнетательный клапан; 3 — маслоотделитель; 4 — конденсатор; 5 — ресивер; 6 — осушитель; 7 — фильтр; 8 — терморегулирующий вентиль; 9 — холодильная камера; 10 — испаритель; 11 — компрессор.
Компрессор 11 отсасывает из испарителя 10 пар холодильного агента, имеющий низкое давление и соответственно низкую температуру, и сжимает его до давления конденсации. Далее горячий пар агента направляется в конденсатор 4, где пар полностью конденсируется, отдавая тепло забортной воде, прокачиваемой через конденсатор. Из конденсатора жидкость поступает к терморегулирующему вентилю. В терморегулирующем вентиле происходит дросселирование жидкого холодильного агента, т. е. снижения его давления до давления кипения, которое сопровождается частичным вскипанием агента (примерно15%) и понижением его температуры. Процесс происходит мгновенно, без поглощения тепла из окружающей среды — только за счет тепла жидкого хладагента. Поэтому за терморегулирующем вентилем холодильного эффекта не происходит. Двигаясь дальше по испарителю, жидкий хладагент продолжает кипеть, отбирая тепло, необходимое для парообразования, от охлаждаемой среды. В той точке испарителя, где выкипает последняя капля хладагента холодильный эффект практически прекращается. Дальнейшее незначительное поглощение тепла происходит в испарителе за счет осушения (перегрева) влажного пара хладагента. Перегретый, но еще влажный пар поступает в теплообменник, где он встречается с теплым жидким хладагентом, отчего его перегрев увеличивается. Сухие пары хладагента отсасываются компрессором из испарителя и под давлением конденсации снова подаются через маслоотделитель 3 в конденсатор. Цикл повторяется.
Рассольное и воздушное охлаждение часто называют «охлаждением с помощью хладоносителей». Рассол или воздух непосредственно охлаждают помещение, а затем в свою очередь охлаждаются хладагентом в испарителе.
Хладоносители должны иметь следующие свойства:
низкую температуру замерзания;
высокие теплоемкость и теплопроводность;
небольшие вязкость и плотность;
быть безопасными и химически нейтральными по отношению к металлам и прокладочным материалам;
быть безвредными для человека;
иметь невысокую стоимость.
Самый дешевый, доступный и безвредный хладоноситель — вода, но из-за высокой температуры замерзания ее применение ограничено. Вода как хладоноситель используется в основном в установках кондиционирования воздуха.
Для получения более низких температур в судовых холодильных установках в качестве хладоносителей применяют водные растворы солей СаС22 и NаС1, называемые рассолами: водный раствор NaCl применяется в установках с температурой не ниже — 10 оС. Используется также раствор Рейнхартин — смесь хлористого магния и хлористого кальция с присадками, который позволяет получить до-18 оС.
На рис. 42 изображена принципиальная схема рассольной системы охлаждения.
Рис. 42. Схема парокомпрессорной установки с рассольной системой охлаждения: 1 — компрессор; 2 — конденсатор; 3 — терморегулирующий вентиль; 4 — испаритель; 5 — рассольный насос; 6 — рассольные батареи; 7 — рефрижераторный трюм.
Система работает следующим образом: рассольный насос 5 забирает рассол из испарителя 4, расположенного за пределами охлаждаемого трюма, и подает его в рассольные батареи 6, находящиеся в рефрижераторном трюме 7. Рассол, проходя внутри змеевиковых рассольных батарей, отбирает тепло от охлаждаемого трюма. Нагретый рассол возвращается в испаритель холодильной установки, где отдает тепло кипящему холодильному агенту. Охлажденный в испарителе рассол снова подается насосом в трюм. Таким образом, рассол выполняет роль переносчика тепла от охлаждаемого трюма к холодильному агенту, кипящему в испарителе. Для уменьшения теплообмена с окружающей средой наружную поверхность испарителя изолируют
При воздушном охлаждении происходит одновременно охлаждение помещения и его вентиляция — вентилятор прогоняет воздух через испаритель, где воздух охлаждается и подаётся в помещения. На Рис. 43 показаны две принципиальные схемы воздушного охлаждения рефрижераторных трюмов: вертикальная с палубным распределительным каналом и типа «Робсон» .
Вертикальная схема с палубным воздухораспределителем (рис. 43, а) предусматривает возможность последовательного вентилирования одного или двух расположенных друг под другом помещений.
В системе типа «Робсон» воздух вентиляторами В (Рис 43, б) нагнетается через воздухоохладители ВО левого и правого борта в два бортовых нагнетательных канала 1, расположенных по всей площади бортов и твиндека. Отсюда воздух поступает в воздухораспределительный канал 2, расположенный между палубой и грузовыми решетками. Бортовые воздуховоды снабжены перегородками, обеспечивающими равномерную подачу воздуха ко всем участкам палубного воздухораспределительного канала. В распределительном канале 2 воздух двигается от обоих бортов к центру трюма, причем по всему пути происходит непрерывное поступление воздуха в трюм через отверстия или специальные щели в палубе. Из трюма нагретый воздух всасывается вентиляторами.
Рис. 43 Воздушные системы охлаждения: а) вертикальная с палубным распределительным каналом; б) типа «Робсон» .
9.2 Режимы холодильной обработки и хранения продуктов
Правильный выбор режима холодильной обработки и хранения продуктов имеет важное значение для сохранения продуктов и уменьшения их потерь. Это прежде всего:
вид продукта и его упаковки,
температура воздуха;
относительная влажность;
скорость движения воздуха;
начальная и конечная температура продукта;
продолжительность холодильной обработки;
время хранения продукта.
Кроме этого, в ряде случаев приходится очищать воздух помещения от механических и бактериальных загрязнений, запаха, а также поддерживать определенный состав газовой среды. Например, снижение температур и увеличение скорости движения воздуха в холодильных камерах позволяют в 2−3 раза ускорить процесс охлаждения и замораживания, а также снизить усушку продуктов на 25 — 35%.
Например, мясо, субпродукты и охлажденная птица хранятся при t = - 2 °C и относительной влажности воздуха 90%, колбасные изделия, копчености при t =0°С и относительной влажности 75−78%.
Рыба пряного посола и холодного копчения храниться при t =-2 ч — 6°С
Для хранения фруктов и овощей приняты следующие температуры (°С):
Цитрусовые 2−6
Картофель 2−4
Лук, чеснок — 1ч-3
Яблоки, груши, виноград 0ч-1
Относительная влажность воздуха, а помещениях хранения фруктов и овощей поддерживается в пределах 85−95%, кроме лука и чеснока, где она должна быть 70−80%.
При перевозке и хранении охлажденной и мороженой рыбопродукции необходимо соблюдать общие основные требования.
Во-первых, мороженая рыба не терпит перепада температур, поэтому нужно поддерживать устойчивую, равномерную температуру и влажность по всей холодильной цепи перевозки и хранения продукции. Если изменяются какие-либо условия, влияющие на температуру и влажность воздуха, то необходимо срочно провести работы, с тем чтобы восстановить необходимый режим. Это наиболее полно достигается в современных транспортных средствах и в холодильниках с совершенной теплоизоляцией при правильном выборе и установке охлаждающих устройств с автоматическим регулированием их работы. Необходимо также прилагать все усилия для сокращения как внешних так и внутренних теплопритоков, которые нарушают температуру и влажность воздуха, вызывают нерегулируемость его конвективного свободного движения, создавая неравномерность поля режимных параметров в камере хранения.
На рефрижераторных судах температура воздуха в трюмах при перевозке и хранении рыбы, охлажденной льдом, поддерживается в пределах 0…2°С. Чаще всего, охлажденная рыба перевозится на рефрижераторных судах и температура тела рыбы не должна превышать 5 С. При превышении температуры или обильного таяния льда, рыбу необходимо засыпать дополнительным количеством льда.
Время, на которое охлажденная рыба сохранит свое качество зависит от ее вида, состояния, способа и скорости охлаждения, санитарно-гигиенических условий. Например, сроки хранения и транспортировки охлажденной льдом хамсы при температуре в трюме от 0 до 5 °C не должен превышать 12 ч. Салака и корюшка во льду сохраняются 1 сут, скумбрия и ставрида — 3 — 4, потрошеные треска и окунь — до 10−12 сут.
Мелкая охлажденная рыба сохраняется хуже, чем крупная того же вида. Так, крупная треска, выловленная в Баренцевом море в I квартале, своевременно разделанная и охлажденная льдом, сохраняет свое качество до 12 сут, а мелкая — только 8−9 сут. Сроки хранения охлажденной рыбы зависят также от района промысла и времени вылова.
Предельные сроки хранения и транспортирования отдельных видов рыб устанавливаются на местах с учетом особенностей свойств рыбы, предполагаемых способов использования и конкретных условий перевозки и хранения.
9.3 Холодильные агенты и их свойства
Хладагентом (сокращение от слов «холодильный агент») принято называть рабочее вещество с низкой температурой кипения (испарения), с помощью которого осуществляется процесс охлаждения в холодильных камерах. В парокомпрессорных холодильных машинах применяют разные марки хладагентов.
В 1931 году американская фирма «Дюпон» синтезировала безвредный для человека хладагент — фреон. Впоследствии было синтезировано более 4-х десятков различных фреонов, отличающихся друг от друга по своим свойствам и химическому составу. Наиболее дешевыми и эффективными оказались фреон-12 и фреон-22, которые долгое время всех устраивали.
В настоящее время действует Международный стандарт (МС): ИСО 817. «Органические хладагенты» . Стандарт предусматривает цифровые обозначения хладагентов в технической документации на холодильное оборудование, характеристики хладагентов, масел, тары для транспортирования хладагентов и масел, приборов автоматики и контроля, терминологию холода.
Стандарт допускает несколько обозначений хладагентов: условное название, торговое название (марка), химическое название, химическая формула. При этом международное условное обозначение хладагентов является предпочтительным и состоит из символа R и определяющего числа. Например, фреон 12 имеет обозначение R12, фреон 22 — R22.
К хладагентам предъявляют термодинамические, физико-химические, физиологические и экономические требования. К термодинамическим требованиям относят минусовую температуру кипения при атмосферном давлении, низкое давление конденсации, высокую объемную холодопроизводительность, высокий коэффициент теплопроводности и теплопередачи. Физико-химическими требованиями к хладагентам являются: малая плотность и вязкость, обеспечивающие незначительное сопротивление хладагента при циркуляции в агрегате; химическая пассивность к металлам, материалам изоляции обмоточных проводов электродвигателя; химическая стойкость; негорючесть; малая способность проникать через неплотности; способность растворять воду и т. д.
Холодильные агенты должны быть безвредными для здоровья человека (физиологическое требование) и низкой стоимости (экономическое требование). При одинаковых температурных условиях размеры компрессора пропорциональны объемной холодопроизводительности хладагентов. Так, если размеры углекислотного компрессора принять за единицу, то размеры компрессора на аммиаке и хладоне R22 будут в 4 раза больше, на хладонах R12 и R18a в 6 раз больше. Объемная холодопроизводительность влияет также и на размеры теплообменной аппаратуры. Так, испаритель холодильной машины, работающей на хладоне R12, в 1,5 раза больше испарителя холодильной машины, работающей на хладоне R22.
Аммиак ядовит, пожарои взрывоопасен, хладон R12 экологически опасен. Углекислотные машины опасны из-за высоких давлений конденсации.
До недавнего времени наибольшее применение в холодильной технике имели:
хладон 12 - R12 (CF2 Cl2) — дифтордихлорметан и
хладон 22 - R22 (CНF2 Cl) — дифтормонохлорметан
R12 — это тяжелый бесцветный газ, не имеет запаха, инертен к металлам; взрывоопасностью не обладает. Однако при высокой концентрации в помещении может вызвать отравление и удушье от недостатка кислорода (более 30% по объему). При температуре выше 330 °C R12 разлагается с образованием фосгена, хлористого и фтористого водорода. Поэтому курить и вносить открытый огонь в помещения с R12 запрещается. Температура кипения при атмосферном давлении — 29,8°С. А это значит, что можно получить температуру охлаждаемого объекта порядка — 19 °C.
Пар R12 тяжелее воздуха в 4,3, а жидкий хладон тяжелее воды. Он хорошо растворяется в масле и плохо в воде, как и все фреоны. Обладает большой проникающей способностью — легко проходит через мельчайшие неплотности.
По своим физико-химические свойствам хладон 22-R22 (CНF2 Cl) — дифтормонохлорметан близок к R12, но имеет лучшие холодильные свойства, поэтому также получил более широкое применение в холодильной технике, чем R12. (Температура его кипения при атмосферном давлении — 40,8°С) Однако хладоны R12 и R22 относятся к группе хлорсодержащих хладагентов, т. е. содержат хлор и являются экологически опасными хладагентами, подлежащими замене на экологически безопасными. На основе решения Венской конвенции об охране озонового слоя применение R12 запрещено, а R22 должен быть постепенно заменен до 2020 года озонобезопасными хладагентами. (Монреальский Протокол по веществам, разрушающим озоновый слой; Принят в сентябре 1987 г.)
К озонобезопасным хладагентам (HFC), которые не содержат хлор (Cl) относятся:
фторуглероды ФУ — международное обозначение FC
гидрофторуглероды ГФУ — международное обозначение HFC
углеводороды (УН) — международное обозначение HC
На замену фреону R22 пришел фреон R410A, а также R407C.
Хладагент R410A представляет собой смешанные в равных массовых долях хладагенты R32 и R9. Смесь характеризуется нулевым значением потенциала разрушения озонового слоя
К этой же группе относится и хладагент R407C — смесь R32, R9 и R18a (массовые доли компонентов соответственно 23/25/52%)
В последние годы в холодильную технику стал широко внедряться хладагент R600а — изобутан (С4Н10). Это устойчивый газ с хорошими холодильными свойствами, срок службы — более 20 лет, температура кипения — 11,7°С. В современном 14 литровом холодильнике используется всего 25 г R 600а. Недостаток R600а — взрывоопасен.
Особого внимания требует проблема, связанная с возвратом в холодильную технику аммиака (NH3) — R717.
Аммиак по сравнению с углеводородами менее опасен. При нулевых потенциалах разрушения озона он:
легкий (легче воздуха, не опускается);
имеет запах (легко обнаруживается при утечке);
обладает высокой теплотой парообразования, и поэтому при утечке из сосуда с жидким аммиаком давление в нем быстро снижается до атмосферного и утечка сокращается;
воспламеняется только при 650 °C, и для его воспламенения требуется подвод значительного количества теплоты.
При этом аммиак как хладагент обеспечивает высокую энергетическую эффективность производства холода. Сейчас аммиак, после того как во второй половине XX века настойчиво вытеснялся фреонами и стал уделом почти только крупных береговых промышленных установок, возвращается. Все более широко применяются малые аммиачные холодильные машины В опубликованном в 2006 г. обзоре проанализирован европейский опыт работы с аммиачными холодильными установками, с использованием современных технических решений (герметичные кожухи, оборудование с малой заправкой хладагента, сигнализация, системы эвакуации аммиака, качество изготовления и эксплуатации) и разумных, обоснованных требований безопасности. Должна быть создана такая техническая, экономическая и правовая обстановка, чтобы предприятия хотели и практически могли выпускать аммиачные машины высокого технического уровня, а потребители хотели и могли их применять.
Диоксиду углерода (СО2) — (R744) как и рабочему веществу холодильных машин и тепловых насосов, а также как к вторичному теплоносителю в низкотемпературных холодильных установках, в мире уделяется пристальное внимание. Основной стимул — абсолютная безопасность этого вещества (если не учитывать высокие рабочие давления в системах). Исследовательские и конструкторские работы ряда последних лет перешли в стадию практического применения. Уникальность этих машин состоит в том, что для них не может быть использовано существующее базовое холодильное оборудование — компрессоры, теплообменные аппараты и другое —, а должно быть создано новое. Основная проблема состоит в обеспечении достаточной энергетической эффективности. В цикле холодильной машины на R744 чрезвычайно трудно компенсировать перерасход затрачиваемой работы, связанной с надкритическим протеканием процесса охлаждения сжатого газа. Тем не менее, с учетом безвредности эмиссии R744 в атмосферу начато его применение в таком массовом оборудовании, как автомобильные кондиционеры. Можно ожидать широкого применения диоксида углерода в тепловых насосах. В цикле теплового насоса (ТН) высокая энергетическая эффективность, более высокая чем у фреоновых (углеводородных) ТН, может быть обеспечена при соответствующем выборе параметров нагреваемой среды и оптимизации других параметров цикла
9.4 Эксплуатация судовых холодильных установок
Основной задачей технического обслуживания и эксплуатации судовых холодильных установок является обеспечение надежной и безопасной её работы при минимальных затратах труда и материальных средств. Судовая холодильная установка действует безотказно, если она правильно смонтирована, испытана и обслуживается в точном соответствии с действующими Правилами технического обслуживания и эксплуатации судовых холодильных установок и Инструкциями завода-изготовителя.
Техническая документация любой судовой холодильной установки включает:
документацию завода-изготовителя: паспорта, техническое описание и инструкцию по техническому обслуживанию и эксплуатации установки и обслуживающих её вспомогательных механизмов, аппаратов, приборов, а также комплекты чертежей, схем и др.;
формуляр текущего технического состояния холодильной установки, содержащий акты испытаний, акты отказов и перечень выполненных работ по её техническому обслуживанию;
кодовые книги для заказа запасных частей;
общие правила технической эксплуатации судовых холодильных установок и др.
На транспортных судах обслуживание холодильных установок осуществляет машинная вахта. Для этого старший механик организует подготовку вахтенного персонала (механиков и особенно мотористов) по грамотному техническому обслуживанию конкретной холодильной установки; обращает внимание на особенности установки и какие параметры работающей установки следует контролировать особенно внимательно. При этом машинной вахтой ведется Температурный журнал, в который записываются значения температуры в охлаждаемых помещениях и параметры наружного воздуха.
На крупных пассажирских, транспортных и рефрижераторных судах холодильные установки располагаются в отдельном рефрижераторном отделении и обслуживаются специальными вахтами рефрижераторных машинистов, руководимых рефрижераторными механиками. В этом случае ведется Суточный журнал работы холодильной установки.
Подготовка холодильной установки к работе. Испытание холодильной установки давлением.
Надежность работы холодильной установки в значительной степени зависит от прочности и плотности как ее отдельных узлов, так и установки в целом. Поэтому после окончания монтажа холодильной установки на судне или ремонте, при котором из системы был полностью удален холодильный агент, перед заполнением установки хладоном испытывают систему холодильного агента на герметичность, используя для этого сухой азот, углекислоту или тщательно осушенный воздух (последнее в судовых условиях обеспечить сложно). Все фреоновые холодильные установки испытывают при избыточном давлении: на стороне нагнетания для R12−1,4 МПа (14,0 кгс/см2), для R22−2,0 МПа (21,0 кгс/см2); на стороне низкого давления дляR12−1,0 МПа (10,5 кгс/ом2), для R22−1,6МПа (16,0 кгс/см2). Для испытания системы холодильного агента чаще всего используют инертный газ — азот или углекислоту, поставляемые на суда в баллонах.
Для испытания на герметичность фреоновой холодильной установки с непосредственным охлаждением через наполнительный вентиль, служащий для заполнения холодильной установки хладоном, баллон с газом при помощи зарядной трубки подсоединяют к системе. Испытывают систему давлением при отключенных автоматических приборах и заглушённых предохранительных клапанах. Если автоматический прибор имеет обводной трубопровод, для его отключения закрывают запорные вентили по обе стороны прибора. В противном случае іприбор демонтируют и на его место устанавливают перемычку. Для проверки герметичности трубных решеток снимают крышки конденсаторов и кожухотрубных испарителей. Перед наполнением системы газом необходимо сделать следующее: открыть все запорные вентили, кроме воздухоспускных и вентилей, отсекающих автоматические приборы; заменить манометры и мановакуумметры, рассчитанные на измерение давлений меньших, чем давление испытания, манометрами с соответствующими шкалами. Газ находится в баллоне под высоким давлением порядка 12 — 14 МПа (4 — 24 кгс/см2), поэтому систему наполняют через редукционный вентиль. Наполнение ведут постепенно до давления 1,0 МПа (10,5 кгс/см2) для R12 и 1,6 МПа (16,0 кгс/см2) для R22. Затем вентиль на баллоне и наполнительный вентиль 16 закрывают и делают перерыв на 25−30 мин, необходимый для выравнивания давления во всех частях системы. Одновременно проверяют, нет ли в системе сильных утечек. Если в течение этого времени давление в системе не понижается, закрывают всасывающий 1 и нагнетательный 20 вентили компрессора и разобщают нагнетательные и всасывающие трубопроводы системы холодильного агента. Для этого закрывают вентили на жидкостном коллекторе 6 или (если они предусмотрены) запорные вентили перед каждым камерным ТРВ. Затем, открыв вентиль 16 и вентиль на баллоне, повышают давление только на стороне нагнетания до 1,4 МПа (14,0 кгс/см2) для R12 и 2,0 МПа (21,0 кгс/см2) для R22. После этого, закрыв вентиль на баллоне и наполнительный вентиль 16, отсоединяют баллон от системы, а к вентилю 16 подключают манометр.
Далее приступают к проверке герметичности системы. Для этого обмыливают все разъемные соединения, а также места пайки и сварки. Особенно тщательно обмыливают трубные решетки кожухотрубных конденсаторов. Для обмыливания приготовляют густую мыльную пену. Чтобы пена быстро не высыхала, в нее добавляют несколько капель глицерина. Перед обмыливанием соединение должно быть снаружи очищено и насухо вытерто. Утечки обнаруживаются по появлению пузырей. Если в течение 1 — 1,5 мин не появится пузырьков, соединение считается плотным. Если фланцевое соединение имеет уплотнительный бурт меньшего диаметра, чем фланцы, вырезают полосу газеты, обильно смазывают ее пеной и наклеивают снаружи по окружности на фланцы, герметизируя соединение труб. Затем прокалывают спичкой отверстие в бумаге между фланцами, обмыливают его и в течение нескольких минут контролируют появление пузырьков. Метод довольно надежный, но он требует определенного навыка. Если утечки из системы нет, фиксируют время, температуру помещения и давление в системе. Под указанными давлениями стороны высокого и низкого давления выдерживают в течение 18 ч. В продолжение этого периода каждый час отмечают давление в системе и температуру окружающего воздуха. За первые 6 ч давление в системе может понизиться, но не более чем на 2%. Это объясняется тем, что при резком повышении давления в системе возрастает температура газа, заполнившего системы. В процессе выравнивания температуры газа с температурой окружающей среды давление в системе несколько понижается. В течение последующих 12 ч давление должно оставаться постоянным при условии постоянства температуры окружающего воздуха.
Если сторона низкого давления может периодически работать в качестве стороны высокого давления (как это предусмотрено в установках, где оттаивание снеговой «шубы» осуществляется горячим паром), при отсутствии предохранительного клапана для стороны низкого давления следует принимать то же расчетное давление, что для стороны высокого давления. Выпуск из системы азота или углекислоты рекомендуется осуществлять таким образом, чтобы одновременно обеспечить продувку системы с целью очистки трубопроводов от грязи и ржавчины. Продувку разветвленных систем производят сначала по частям с выключением аппаратов из продуваемой части трубопроводов (в целях предотвращения оседания в них грязи и окалины). Для того чтобы увеличить эффект продувки, в свободный конец трубы забивается деревянная пробка, при повышении давления она вылетает и газ, выходя из трубы с большой скоростью, лучше очищает ее. В конце испытания и после устранения неплотностей желательно продуть систему целиком.
При получении положительных результатов испытания системы холодильного агента на герметичность под давлением считается законченным, о чем составляется акт с указанием величины давлений, продолжительности испытания, даты и др.
После испытания системы холодильного агента приступают к испытанию других систем: забортной воды и рассола. Трубопровод охлаждающей воды, водяная часть конденсаторов, рассольный трубопровод в сборе с аппаратурой и батареями, включая рассольную часть испарителей, испытывают гидравлическим давлением не менее 1,25 рабочего давления. Для этого системы заполняют водой и поднимают в ней давление с помощью ручного гидравлического насоса. Если в течение 5 мин давление остается постоянным, система считается выдержавшей испытание на герметичность. После испытания необходимо тщательно промыть систему, прокачивая ее рабочим насосом до выхода из нее совершенно чистой воды.
Вакуумирование системы холодильного агента.
Для удаления из системы воздуха и неконденсирующих газов, а также для осушения ее от влаги перед заполнением холодильным агентом производят вакуумирование. При опрессовании системы холодильного агента неплотности в ней могут закупориться окалиной или иными механическими частицами. Во время эксплуатации оставшиеся неплотности будут неизбежно размыты хладоном и появятся утечки. Вакуумирование системы помогает выявить эти скрытые дефекты.
Перед испытанием системы вакуумом устанавливают на место все штатные автоматические приборы, снятые на время испытания системы давлением. Испытание проводят посредством вакуум-насоса. Перед началом вакуумирования системы проверяют, все ли запорные и соленоидные вентили, кроме вентилей, соединяющих систему с наружной средой, открыты Вместо мановакуумметра 2 (рис. 44) устанавливают вакуумметр.
Рис. 44. Схема подключения баллона с хладоном при зарядке: I — выход хладона к ТРВ кладовых, II — вход хладона из испарителей кладовых
Приводят в действие вакуум-насос и понижают в системе абсолютное давление В начале испытания тщательно наблюдают за работой и температурой вакуум-насоса. Если она увеличивается выше допустимой (предельная температура указана в заводской инструкции на данный насос), то насос на время останавливают. Перед остановкой обязательно закрывают вентиль на системе агента. При достижении в системе наибольшего разрежения вакуум-насос продолжает работать в течение 4 ч.
Во время работы вакуум-насоса тщательно осушают систему от влаги. Для этого водяные и рассольные полости конденсаторов и испарителей заливают водой с ^=50ч-80°С или подают отработавший пар при избыточном давлении не более 0,12 МПа (1,2 кгс/см2).
Если осушают систему непосредственного охлаждения, в камерах включают электрогрелки для повышения температуры до 45-+ 60 °C Подогрев аппаратов способствует интенсивному испарению влаги в системе, находящейся под вакуумом. Через 5 — 6 ч прекращают нагрев системы, закрывают вентиль 16, останавливают и отсоединяют вакуум-насос.
Установки с бессальниковыми компрессорами должны дополнительно испытывать разрежением в течение 8 ч, так как в этом случае требуется повышенная сухость системы холодильного агента.
После того как температура аппаратов сравняется с температурой окружающей среды, записывают время и разрежение в системе, определяемое по вакуумметру. Испытание системы под вакуумом проводят в течение 12 ч. Величину разрежения в системе записывают через каждые 2 ч. Если в продолжении 12 ч при постоянной температуре окружающей среды остаточное давление в системе не повысится, результаты испытаний считают удовлетворительными. Необходимо знать, что при недостаточном осушении системы от влаги остаточное давление в конце испытания повысится за счет парциального давления испарившейся влаги. В таком случае систему необходимо еще раз испытать под вакуумом и просушить с последующей выдержкой под вакуумом 12 ч.
При отсутствии вакуум-насоса в крайнем случае испытание системы разрежением может быть произведено штатным холодильным компрессором. Для этого полностью закрывают нагнетательный вентиль и открывают установленный перед ним специальный запорный воздушный клапан; при его отсутствии следует ослабить фланцевое соединение запорного клапана на нагнетательной магистрали между клапаном и цилиндром. Положение всех вентилей должно быть таким же, как при испытании системы вакуум-насосом. Компрессор приводят в действие, и отсасываемый из системы газ выбрасывается в атмосферу через воздушный клапан. Разрежение в системе контролируется вакуумметром За работой компрессора ведут постоянное наблюдение, особенно тщательно контролируют уровень масла в картере через смотровое стекло. В случае повышенного уноса масла из картера компрессор останавливают, закрыв предварительно всасывающий вентиль, и добавляют масло в картер. При достижении в системе наименьшего давления компрессор продолжает работать в течение 4 ч, после чего его останавливают. Одновременно с остановкой компрессора закрывают воздушный клапан или затягивают ослабленный фланец. Открывают вентиль 20 и выдерживают систему под вакуумом 12 ч. Результаты испытания системы холодильного агента фиксируют актом, в котором указывают дату, продолжительность испытания и все числовые данные. Система, выдержавшая испытание под вакуумом, считается подготовленной к зарядке холодильным агентом.
Испытание системы на герметичность хладоном. Зарядка системы.
Испытание на герметичность хладоном производят на первом этапе зарядки системы. Для этого баллон с хладоном устанавливают вертикально, головкой вверх. Открывая вентиль на баллоне на 1−2 с, продувают его. При этом из баллона должен выходить газообразный, а не жидкий хладон. Выход жидкого хладона указывает на переполнение баллона, вызывающее его повышенную взрывоопасность, так как давление в баллоне может оказаться в несколько раз выше нормального. В этом случае необходимо несколько раз открыть вентиль на баллоне до появления парообразного хладона. Перед введением в систему агента независимо от надписи краакой на баллоне необходимо убедиться в том, что в баллоне находится хладон требуемой, а не другой марки. Для этого на штуцер вентиля устанавливают манометр, открывают вентиль и измеряют давление в баллоне. Зная температуру хладона в баллоне, равную температуре помещения, в котором длительное время находился баллон, сверяют давление в баллоне с табличным значением давления насыщенных паров хладона при данной температуре
Контроль каждого заряжаемого в систему баллона является обязательным. Для этой цели можно использовать манометр 12. Использование хладона-22 для заполнения системы холодильной установки, предназначенной для работы на хладоне-12, не разрешается ввиду более высоких рабочих давлений. Проверенный баллон 11 с хладоном, установленный вентилем вниз, подсоединяют с помощью зарядной трубки 9 к вентилю 16. Воздух из зарядной трубки продувают хладоном при ослабленной накидной гайке на штуцере вентиля 16. Вентиль 5 на обводном трубопроводе закрывают, чтобы хладон перед поступлением в систему обязательно проходил через фильтр-осушитель 15.
Вентиль 16 и вентиль на баллоне открывают и заполняют систему парообразным хладоном до давления 0,2 МПа (2 кгс/см2). Зарядку временно прекращают для проверки всех соединений на плотность.
Учитывая высокую способность хладона проникать через неплотности, проверке герметичности системы под давление газом, а также при вакуумировании и при зарядке хладоном должно быть уделено большое внимание. Сокращение программы испытаний и недостаточная тщательность проверки каждого соединения могут привести к значительно большим затратам времени, труда и средств в процессе эксплуатации установки, в условиях постоянных вибраций и деформации корпуса судна.
Герметичность системы, заполненной хладоном, проверяют обмыливанием, галоидной лампой или электронным галоидным течеискателем. Принцип действия галоидных ламп (спиртовых, бензиновых и пропановых) основан на изменении цвета пламени, получающегося при сгорании топлива, которым заправлена лампа. При отсутствии в воздухе пара хладона пламя оказывается бесцветным. Если в воздухе, который подсасывается к горелке, имеется хладон, то при температуре 600−700°С происходит разложение хладона и образование хлористого и фтористого водорода, которые в присутствии раскаленной меди увеличивают пламя и окрашивают его в зеленоватый цвет. При более высокой концентрации хладона в воздухе цвет пламени делается темно-зеленым, а затем зелено-синим. При больших концентрациях хладона лампа может погаснуть.
Значительно большей чувствительностью обладают электронные течеискатели. Через платиновые электроды датчика, нагретые до температуры 800-=-900°С, вентилятором прогоняется воздух, всасываемый через шуп и гибкий шланг. При наличии в воздухе пара хладона возрастает ионная эмиссия с поверхности платины, в результате чего возрастает ток, проходящий через электроды. Токовый сигнал датчика увеличивается в усилителе и поступает на индикатор, который обеспечивает подачу световых сигналов посредством неоновой лампы, расположенной в датчике, и подачу звуковых сигналов — щелчки в телефоне, расположенном в регистрирующем блоке. В этом блоке имеется также стрелочный индикатор. Если утечка хладона велика, щелчки в телефоне переходят в непрерывный зумімер одного тона, а стрелка выходит за шкалу прибора. Отечественные приборы ГТИ-2, ГТИ-3 и ГТИ-6 работают по описанному принципу, стоимость их достаточно велика. Посредством приборов можно определить утечку хладона порядка 0,5 г в год.
Применяют электронные течеискатели только в тех случаях, когда не удается определить утечку другими (методами. Помимо описанных методов, неплотности в системе можно также определить по следам и подтекам масла. Ввиду взаимной растворимости хладона и масла появление. масляных пятен указывает на возможную утечку хладона. В этом случае следует обезжирить (бензином, ацетоном, спиртом), вытереть насухо проверяемое соединение и плотно обернуть его белой бумагой. Повторное появление следов масла подтверждает наличие утечки хладона. При работе с галоидными течеискателями всех видов следует иметь в виду, что неплотности во фреоновой установке определяют сверху вниз, так как пар хладона опускается вниз из-за большей, чем у воздуха плотности (1,29 кг/м3 — воздух, 5,7 кг/м3 — R12 и 3,9 кг/м3 — R22).
Систему, заполненную паром хладона, подвергают испытанию на плотность в течение 48 ч. При отсутствии утечек хладона приступают к зарядке системы маслом, а затем и хладагентом. Как правило, холодильные агрегаты поступают на суда с залитым в компрессор и конденсатор маслом. (Например, в конденсатор агрегата МАК-6 заправляют 3 кг масла.)
Во фреоновых холодильных установках с рассольной системой охлаждения для обеспечения нормального возврата масла из испарителя в компрессор маслом заряжают не только картер компрессора, но и кожухотрубный испаритель. Количество масла, заряжаемого в испаритель, составляет 10−15% массы заправляемого в систему хладона, а в систему с непосредственным охлаждением — 24−5%. Масса хладона, вводимого в систему, указана в паспорте установки.
Зарядку агентом продолжают в следующем порядке (рис.44). Вентиль 18 за ресивером 17 или (при отсутствии ресивера) вентиль 19 за конденсатором 4 закрывают. Пускают охлаждающий насос конденсатора и проверяют давление в водяном трубопроводе по манометру. Вводят в действие компрессор. Хладон из баллона поступает через испарители в конденсатор, где и накапливается. При понижении давления в испарительной системе до 0,05 МПа (0,5 кгс/см2) компрессор необходимо остановить. Когда давление повысится до 0,25 МПа (2,5 кгс/см2), компрессор следует снова включить.
При заполнении системы каждый баллон взвешивают до и после использования для определения действительного количества вводимого в систему хладона. Удобно следить за массой баллона и ходом зарядки системы, если баллон подвешивать к динамометру 7. Для того чтобы полностью исключить попадание влаги в систему, несмотря на наличие стационарного фильтра-осушителя 15, между баллоном и наполнительным вентилем устанавливают также переносной фильтр-осушитель 13. В этом случае в процессе зарядки системы хладоном можно без сложных переключений перезарядить этот фильтр новым зарядом адсорбента. Для этого следует закрыть вентиль 8 на баллоне, отсосать хладон из зарядной трубки и переносного фильтра-осушителя 13, закрыть вентили 14 и 10 и снять фильтр-осушитель. После перезарядки фильтра зарядную трубку и фильтр следует продуть агентом из баллона при ослабленной накидной гайке на штуцере наполнительного вентиля 16. Наполнение системы хладоном прекращают при заправке в нее около 70% ориентировочно подсчитанного количества. Впоследствии, когда машина будет работать, хладон добавляют при проявлении признаков недостатка его в системе. А пока компрессор останавливают, закрывают вентиль на баллоне, наполнительный вентиль и отсоединяют зарядную трубку. На смотровом стекле конденсатора (или ресивера) ставят отметку уровня жидкого хладона. Помещение освобождают от фреоновых баллонов и тщательно вентилируют. Обмыливанием и галоидной лампой проверяют на плотность все соединения системы и компрессор. Обнаруженные утечки немедленно устраняют. Составляется акт с указанием даты, номеров баллонов и массы брутто, нетто и тары.
В установках средней и большой холодопроизводительности хладон в жидком виде перекачивают в баллоны через наполнительный вентиль. Для этого необходимо проделать следующее: установить баллон на весы вентилем вверх; присоединить баллон к наполнительному вентилю с помощью красно — медной зарядной трубки, испытанной на соответствующее давление; приоткрыв наполнительный вентиль 16, продуть зарядную трубку, открыть запорный вентиль на баллоне; запустить компрессор; закрыть запорный вентиль перед ТРВ; открыть наполнительный вентиль 16, внимательно контролируя количество жидкого хладона, подаваемого в баллон. Для ускорения наполнения баллона хладоном давление конденсации следует повысить до 0,9 — 0,93 МПа (9−9,5 кгс/см2) для R12 и 0,12−0,14 МПа (12 — 14 кгс/см2) для R22 уменьшением количества — прокачиваемой воды, а баллоны охладить водой или льдом. После наполнения баллона закрыть наполнительный вентиль и запорный вентиль на баллоне, отсоединить зарядную трубку, установить на вентиль баллона заглушку и тщательно завернуть предохранительный колпак.
Пуск и регулирование холодильной установки.
Перед пуском установки необходимо произвести ее внешний осмотр: убедиться в отсутствии посторонних предметов, мешающих пуску, а также проверить по смотровым стеклам наличие в картере компрессора масла. Для компрессоров с принудительным смазыванием уровень масла должен составлять 7 г смотрового стекла. При смазывании разбрызгиванием уровень должен быть несколько выше. Затем по смотровому стеклу проверяют уровень жидкого хладона в конденсаторе (ресивере). Если смотрового стекла нет, определить, достаточно ли в системе хладона можно только во время работы установки.
Перед пуском автоматизированной фреоновой холодильной установки после длительного бездействия необходимы следующие операции: провернуть от руки вал компрессора и убедиться, что он вращается без заеданий; открыть все необходимые запорные вентили водяной и рассольной систем; открыть всасывающий и нагнетательный вентили. компрессора, открыть полностью запорные вентили на паровом (от камерных испарителей) коллекторе. Запорные вентили на жидкостном коллекторе для подключения камерных испарителей открывают сначала на 1/3 оборота и сразу включают компрессор. После пуска компрессора, не допуская снижения давления всасывания ниже 0,02 МПа (0,2 кгс/см2), постепенно открывают запорный вентиль конденсатора или ресивера, а затем постепенно увеличивают до полного открытия запорных вентилей на жидкостном коллекторе. Установку переводят в автоматический режим.
Если есть основания полагать, что в испарителях скопился жидкий хладон, перед пуском компрессора запорные вентили на
Признаки оптимального режима работы фреоновой холодильной установки
Оптимальным называется такой режим работы холодильной установки, который обеспечивает поддержание в охлаждаемых помещениях требуемых температурно-влажностных условий при надежной работе и минимальных затратах энергии. Он характеризуется оптимальными перепадами температур в теплообменных аппаратах, оптимальной величиной перегрева всасываемого пара, нормальной работой компрессора и т. д.
У прямоточных компрессоров температура крышки цилиндра должна быть близка к температуре нагнетательного трубопровода, у непрямоточных — к температуре нагнетательного трубопровода с нагнетательной стороны и температуре всасывающего трубопровода с всасывающей стороны.
Важное значение имеет поддержание оптимальных температурных перепадов Температура, а следовательно, и давление конденсации зависят от температуры забортной воды. Давление конденсации определяют по манометру, установленному на нагнетательной стороне компрессора, а температуру конденсации примерно — по температурной шкале этого манометра, а более точно — по таблице насыщенного пара хладона в зависимости от давления конденсации.
Перепад между температурами забортной воды на входе в конденсатор и выходе из него должен составлять 2−5°С. Перепад между температурой конденсации и температурой воды, выходящей из конденсатора следует поддерживать в пределах 5−6°С, а разность для кожухотрубных конденсаторов — 8−9°С. В процессе эксплуатации в целях экономии энергии необходимо стремиться поддерживать давление конденсации возможно более низким, но не ниже 0,4 МПа (4 кгс/см2) при работе на R22.
При низкой температуре забортной воды температуру и давление конденсации в установках, не имеющих водорегулирующего вентиля, повышают, прикрывая запорный вентиль, установленный на выходе воды из конденсатора. В случае повышения температуры забортной воды выше 32 °C желательно прокачивать конденсаторы холодильной установки водой от насосов, имеющих более высокий напор. При этом необходимо иметь в виду, что увеличивать подачу воды в конденсаторы имеет смысл лишь до тех пор, пока это вызывает снижение давления (и температуры конденсации). Дальнейшее повышение расхода воды приводит только к ускоренному изнашиванию труб и трубных решеток.
При непосредственном охлаждении температура кипения хладона в испарителе должна быть ниже температуры в кладовой на 9−5°С. Температуру кипения хладона в испарителях, не снабженных ПРД «до себя», определяют примерно по температурной шкале мановакуумметра на всасывающей трубе компрессора, а более точно — по таблице насыщенного пара хладона. В установках, не оборудованных теплообменником, перегрев пара на всасывании должен быть 8−10°С. Значения полезного перегрева пара хладона, всасываемого компрессором в установках с теплообменником,. должны быть в определенных пределах В системах с одним испарителем перегрев пара определяют как разность между температурой всасываемого пара (по термометру на всасывающей трубе компрессора) и температурой кипения хладона, соответствующей давлению всасывания.
Проверка настройки ТРВ в этом случае осуществляется просто. В многоиспарительных системах определить перегрев пара в каждом испарителе практически невозможно. В этом случае проверка настройки ТРВ осуществляют следующим образом. Удаляют иней с испарителя, включают компрессор и влажными пальцами определяют, в каком месте испарителя прекращается кипение хладона и начинается перегрев пара. Там, где хладон кипит, влажные пальцы прилипают к трубе испарителя. Перегрев всасываемого компрессора пара в многоиспарительных системах регулируют за счет перераспределения величин перегрева в разных испарителях. При этом минимальный перегрев следует устанавливать у испарителей с затрудненным возвратом масла, увеличивая перегрев у испарителей с облегченным возвратом масла. При наличии перегрева всасываемого пара компрессор работает «сухим» ходом, внешними признаками которого являются: леший стук клапанов; относительно высокая температура крышки цилиндра с нагнетательной стороны и нагнетательного патрубка, которая близка к температуре нагнетательного трубопровода. При температуре в кладовой ниже нуля инеем покрыт весь испаритель и часть всасывающего трубопровода.
Работа компрессора «влажным» ходом характеризуется отсутствием стука клапанов и появлением инея на крышке компрессора при значительном понижении температуры крышки компрессора и нагнетательного трубопровода. На ощупь нагнетательная сторона компрессора холодная. В прямоточных компрессорах покрывается инеем картер.
При необходимости ТРВ перестраивают поворотом его регулировочного винта не более чем на четверть оборота с интервалом 15−20 мин.
Температура в конце сжатия определяется по термометру па нагнетательной трубе компрессора. Она зависит от температур конденсации, кипения и перегрева и колеблется в пределах 40 — 14 °C для R22. Эти и другие значения, характеризующие оптимальные температурные пределы.
Влага и воздух в системе холодильного агента и их удаление
Влага в систему хладагента попадает при:
недостаточном осушении системы после её монтажа;
при неполном удалении воздуха из системы, механизмов и аппаратов после ремонта;
при зарядке системы хладагентом и маслом или при добавлении их в систему;
при длительной работе установки при вакууме на всасывании.
Ввиду ограниченной растворимости воды в хладагентах, вода самостоятельно циркулирует в системе. Поэтому при дросселировании холодильных агентов до отрицательных температур, образуются ледовые пробки, частично или полностью закупоривающие дроссельное отверстие ТРВ.
Внешними признаками наличия влаги в системе являются:
повышение температуры в охлаждаемых помещениях;
оттаивание инея с поверхности испарительных батарей;
понижение давления кипения;
значительное увеличение перегрева всасываемого пара.
Перенастройка ТРВ в этом случае на большее открытие не приводит к увеличению давления кипения, так как компрессор быстро отсасывает образовавшийся пар и РНД отключает компрессор по давлению всасывания.
При замерзании влаги в ТРВ, в отличие от его засорения, прохождение жидкого агента возобновляется после его прогрева горячей водой. При наличии в системе значительного количества влаги возможно образование ледовых пробок даже в трубах испарительных батарей.
Наличие влаги в системе приводит к следующим последствиям:
вода в системе вызывает коррозию металлов;
ржавчина, смываемая хладагентом, забивает дроссельные отверстия ТРВ;
в присутствии воды хладагент вступает в химическую реакцию с медью, которая выпадает в виде тонкого слоя на поверхностях и узлах компрессора (омеднение поверхностей), что нарушает работу компрессора.
Поэтому к обезвоживанию фреоновых систем предъявляются высокие требования. Перед заполнением системы хладагентом и маслом ее тщательно вакууммируют и осушают.
В процессе эксплуатации холодильной установки применяют меры, предупреждающие проникновение влаги в систему, а проникшую влагу удаляют с помощью силикагеля или цеолита. Причем фильтр-осушитель включают в работу сразу же при появлении признаков наличия влаги в системе, а выключают не ранее чем через 4 часа после полного исчезновения этих признаков. (Использовать спирт для устранения замерзания ТРВ фреоновых холодильных установок запрещено!)
Одной из тяжелейших аварий холодильной установки является потеря холодильного агента из системы вследствие его утечки в воду конденсатора. В тоже время при снижении давления хладагента в системе ниже давления охлаждающей воды, забортная вода может заполнить систему холодильного агента. В последнем случае после устранения причины, вызывающей серьезнейшую аварию холодильной установки, систему сушат, продувают ее азотом или углекислотой, и неоднократно вакууммируют.
Воздух в системе может оказаться из-за: недостаточно тщательного вакууммирования системы перед первоначальным ее заполнением хладагентом; при вскрытии компрессоров, аппаратов, вспомогательного оборудования и отдельных участков системы для ремонта или профилактических осмотров; при работе установки на вакууме.
Наличие воздуха в системе приводит к увеличению давления конденсации, в результате чего холодопроизводительность установки уменьшается, а потребляемая мощность увеличивается.
Внешними признаками наличия воздуха в системе являются увеличение амплитуды колебаний стрелки манометра со стороны нагнетания компрессора (дрожание корпуса)
Характерные неисправности и неполадки в работе фреоновых холодильных установок и способы их устранения.
Небольшие отклонения, которые лишь снижают экономичность работы, обычно устраняются при профилактическом ремонте. Существенные отклонения от оптимального режима — отказы, при которых установка уже не обеспечивает заданного технологического режима или становится опасной, устраняются в аварийном порядке.
1. Резкое снижение температуры после ТРВ на жидкостной линии
Причина | Принимаемые меры | |
Засорение или неполное открытие ТРВ | Несколько раз полностью закрыть и открыть клапан. При повторных признаках засорения разобрать и прочистить клапан | |
2. Прекращается поступление хладона через ТРВ. Фильтр чист. Подогрев ТРВ и его термочувствительного патрона не приводит к восстановлению подачи хладона
Причина | Принимаемые меры | |
Силовой элемент ТРВ вышел из строя | Сменить ТРВ | |
3. Хладон проходит через ТРВ со свистящим звуком; ТРВ и фильтры исправны.
Причина | Принимаемые меры | |
.1. Хладон находится в неработающем аппарате (конденсаторе, испарителе, ресивере), что приводит к недостатку хладона в работающей части системы | Принять меры по возвращению хладона в работающую часть системы | |
.2. Недостаток хладона в системе | Дозарядить систему хладоном | |
4. Давление кипения ниже нормального. Разность температур кипения и рассола более 5°С
Причина | Принимаемые меры | |
.1. Закупорка трубок испарителя со стороны рассола кристаллами льда и соли | Проверить концентрацию рассола, при необходимости довести ее до нормы | |
.2. Недостаточное поступление рассола в испаритель вследствие: | ||
малого открытия рассольных задвижек; | Увеличить открытие задвижек | |
неисправности насоса | Осмотреть насос, устранить неисправности | |
5. Давление кипения и конденсации ниже нормального. Увеличение открытия ТРВ приводит к незначительному повышению давления испарения. Температура в охлаждаемых помещениях повышается и снизить ее не удается.
Причина | Принимаемые меры | |
Затруднен проход хладона через ТРВ вследствие малого давления конденсации | Уменьшить поступление охлаждающей воды на конденсатор. Поддерживать давление конденсации не менее 0,4 МПа (4 кгс/см2), а для установок, работающих на систему кондиционирования воздуха, — не менее 0,6 МПа (6 кгс/см2) (избыточных). Временно допускается увеличение открытия ручного регулирующего клапана на обводной линии ТРВ | |
6. Давление кипения выше нормального, запорный клапан на всасывающей стороне компрессора покрыт инеем. Покрыта инеем часть блока компрессора. Нагнетательный трубопровод холодный
Причина | Принимаемые меры | |
.1. Чрезмерно открыт ТРВ или ручной регулирующий клапан | Прикрыть ТРВ или ручной регулирующий клапан | |
.2. Плохой контакт термочувствительного патрона ТРВ с трубой | Зачистить место контакта трубы с термочувствительным патроном. Плотно прижать термочувствительный патрон к трубе | |
.3. Выскочила игла ТРВ из седла | Заменить ТРВ | |
7. Давление в испарителе выше нормального, мало понижается даже при полном закрытии ТРВ. Давление всасывания у компрессора значительно ниже давления кипения
Причина | Принимаемые меры | |
Засорена сетка грязеуловителя (газового фильтра) перед компрессором | Снять грязеуловитель (фильтрующий элемент) и очистить сетку | |
8. Давление в испарителе, температура рассола и воздуха в охлаждаемых помещениях ниже требуемых
Причина | Принимаемые меры | |
Холодопроизводительность работающей установки больше требуемой | Уменьшить холодопроизводительность установки | |
Правила техники безопасности при обслуживании фреоновых холодильных установок
Персонал, обслуживающий холодильную установку, обязан знать и строго соблюдать правила безопасности труда.
Движущиеся части компрессоров, насосов и других механизмов должны иметь ограждения. Запрещается эксплуатация холодильного оборудования, движущиеся части которого имеют неисправные приводные ремни. К движущимся частям машин запрещается прикасаться как во время работы, так и после остановки до тех пор, пока не будет исключена возможность автоматического пуска.
Баллоны с хладоном хранят на судне в специальном помещении, а при его отсутствии — в рефрижераторном отделении или другом месте, по возможности недалеко от холодильного агрегата. Баллоны должны быть надежно закреплены. Каждый баллон должен иметь заглушку на вентиле и предохранительный колпак. В местах хранения баллонов температура не должна превышать 35 °C.
При содержании в воздухе более 30% хладона (по объему) появляются признаки удушья. Однако в связи с тем, что хладон почти не имеет запаха, обслуживающий персонал не всегда может почувствовать опасную концентрацию хладона в воздухе. Это вынуждает принимать ряд специальных мер предосторожности. Помещения, где установлены агрегаты, должны быть оборудованы вентиляцией. Все ремонтные работы должны производиться на обесточенном агрегате. При работах, связанных с опасностью поражения электрическим током, необходимо применять защитные средства: инструмент с изолированными ручками, диэлектрические коврики, галоши, перчатки и т. д. Жидкий хладон, попадая на кожу, может вызвать обмораживание, а попадая в глаза, привести к тяжелому поражению, вплоть до потери зрения Поэтому вскрывать фреоновые компрессоры, аппараты и трубопроводы можно только в защитных очках и лишь после того, как давление хладона в них путем неоднократного отсасывания снижена до атмосферного и остается (постоянным в течение 30 мин. В тех случаях, когда в процессе вскрытия установки полностью не исключается опасность попадания жидкого хладона на кожу, следует пользоваться резиновыми перчатками.
Перед вскрытием системы необходимо запустить в работу нагнетательный и вытяжной вентиляторы, если они были остановлены. Сразу после вскрытия фреоновых компрессоров, аппаратов и трубопроводов обслуживающий персонал должен на время покинуть помещение, которое необходимо тщательно проветрить. Иногда фреоновую систему приходится вскрывать в рефрижераторных кладовых или в других помещениях, не имеющих искусственной вентиляции. В этом случае следует, вскрыв систему, сначала убедиться в том, что запорные вентили, отсекающие вскрываемое соединение труб, полностью герметичны, затем в открытые концы труб плотно вставить заранее подготовленные деревянные или резиновые пробки, произвести тщательное проветривание помещений с помощью переносных вентиляторов. При соблюдении всех этих условий входить в кладовую, в которой в течение 30 мин и более были разобраны трубы, следует, не закрывая за собой двери, а лучше под наблюдением другого лица и после повторного проветривания помещения. Несчастные случаи, имевшие место на судах с фреоновыми установками из-за невнимания к этим требованиям, вынуждают настаивать на их неукоснительном выполнении.
При осмотре внутренних полостей и аппаратов можно пользоваться только переносными лампами напряжения не выше 12 В или электрическими карманными фонарями. Рефрижераторное отделение должны систематически проветривать.
В связи с тем что при температуре выше 400 °C хладон разлагается с выделением фосгена, курить в рефрижераторном отделении запрещается. Использовать галоидную лампу необходимо наиболее короткое время. Перед тем «как пользоваться лампой, помещение тщательно проветривают.
В рефрижераторном отделении на видном месте должны быть вывешены плакаты с правилами оказания первой помощи при обмораживании, удушье, попадании холодильного агента в глаза. Противогаз, защитные очки, резиновые перчатки и аптечка также должны находиться в удобном месте, желательно в застекленном шкафу на входе в рефрижераторное отделение. Рефрижераторные механики и мотористы должны уметь оказать помощь пострадавшему при удушье, обмораживании, попадании хладона в глаза.
При удушье, вызванном недостатком кислорода в помещении, заполненном газообразным хладоном, необходимо немедленно вынести пострадавшего на свежий воздух. Желательно дать ему кислород. При общей слабости пострадавшего напоить крепким чаем или кофе. В случае прекращения дыхания до прихода врача пострадавшему сделать искусственное дыхание. При попадании жидкого хладона на кожу во избежание обмораживания следует сразу окунуть пораженный участок в воду, имеющую температуру 35−40°С на 5−10 мин, затем, не растирая, осушить кожу полотенцем, смазать мазью Вишневского или пенициллиновой и наложить повязку. Если на коже образовались пузыри, следует, не вскрывая их, наложить мазьевую повязку и направить пострадавшего к врачу. При попадании хладона в глаза необходимо промыть их струей воды комнатной температуры, 2°/оным раствором поваренной соли и 2−4% -ным раствором борной кислоты. Затем закапать в глаза стерильное вазелиновое масло и немедленно обратиться к врачу.
Следует особо подчеркнуть, что ошибочное мнение об относительной безвредности хладона и пренебрежение в связи с этим правилами безопасности труда может привести к трагическим последствиям.
Требования охраны труда в аварийных ситуациях Основные аварийные ситуации, которые могут возникнуть в ходе эксплуатации холодильных установок:
выброс хладагента (вследствие внезапной неисправности оборудования или в ходе ремонтных работ);
разрушение элементов оборудования и трубопроводов (из-за повышенных давлений, некачественного монтажа, физического износа, несрабатывания приборов защиты);
возгорание (в ходе сварки, пайки);
незапланированное отключение электроэнергии;
выход параметров оборудования за нормативные пределы.
В случае нарушения герметичности холодильной установки нужно немедленно ее остановить, перекрыть запорными вентилями нарушенный участок, включить общую и аварийную вентиляции, вывести людей из помещения, в котором происходит утечка хладагента. В необходимых случаях следует использовать соответствующие фильтрующие и изолирующие противогазы, дыхательные аппараты.
. В случае возникновения пожара следует применить имеющиеся местные средства пожаротушения и сообщить в противопожарную службу (организации или территориальную).
При отклонении параметров режима холодильной установки (давление, температура) от нормативных значений, определяемых документами организации-изготовителя и окружающей средой, до предельно допустимых величин следует немедленно остановить холодильную установку и выявить причины.
При внезапном отключении электроэнергии следует в условиях аварийного освещения перевести холодильную установку в нерабочее состояние (переключением соответствующих приборов, арматуры, рубильников, кнопок).
При любых аварийных ситуациях и пожарах необходимо поставить в известность своего непосредственного руководителя и администрацию организации, оказать первую (доврачебную) медицинскую помощь пострадавшим (при удушьи, травмировании, отравлении и т. д.).
Устранение аварийной ситуации производить только после выявления ее причин.
10. Опреснительные установки
Назначение и типы установок.
На современных морских судах пресная вода, необходимая для технических и хозяйственных нужд, вырабатывается путём опреснения забортной воды специальными опреснительными установками. В первом случае опресненная вода используется для охлаждения отдельных механизмов, питания паровых котлов, доливки аккумуляторных батарей; во втором случае — для умывания и мытья экипажа и пассажиров, стирки. а после специального приготовления — для мытья посуды, питья и приготовления пищи.
Известны химические, физические и термические методы опреснения морской воды.
Химический метод применяют при опреснении небольшого количества воды и на флоте используются только в аварийной ситуации. (аварийное снабжение коллективных спасательных средств).
В основу физического метода (обратного осмоса или гиперфильтрации) положено фильтрация воды под большим давлением (около 100−34 кг/см2) через специальные мембраны. При этом происходит задержание ионов растворимых в воде солей на мембранах. Мембраны выполнены в виде пучка полых волокон из триацетата целлюлозы с внутренним диаметром 40 мкм и наружным 85−100 мкм или из металлической фольги облученной тяжелыми ионными пучками в ускорителях этих частиц. Установки конструктивно просты и надежны в работе и поэтому находят все большее применение. Недостатком метода обратного осмоса является относительно быстрая замена мембран или их специальная промывка от солей.
К термическим методам опреснения относят дистилляцию (выпаривание) морской воды.
Если воду довести до кипения, удалять выделяющиеся пары и конденсировать их, то будет вырабатываться дистиллят. Установки, в которых происходит такой процесс, называются испарительными, и они делятся на два типа.
В установке первого типа вода кипит при температуре насыщения, соответствующей давлению внутри испарителя. Такой испаритель называется кипящим.
В установке второго типа вода подогревается в одной секции, а затем подаётся в другую, где давление значительно ниже, вследствие чего она начинает кипеть и превращаться в пар. Такой испаритель называется ваккумным. Процесс испарения при давлении ниже атмосферного имеет много положительных сторон: улучшается теплопередача от греющего пара (воды) к подаваемой забортной воде, уменьшается образование накипи, снижаются потери тепла, увеличивается производительность на единицу массы и объёма испарителя. Испарители этого типа отличаются компактностью и простотой конструкции.
Поэтому в настоящее время на судах с дизельной установкой — теплоходах, наибольшее применение получили вакуумные одноступенчатые утилизационные водоопреснительные установки, использующие тепло охлаждающей пресной воды из ситемы охлаждения главного дизеля.
Широкое применение на судах морского флота нашли опреснительные фирм «АТЛАС», «НИРЕКС»
Рассмотрим устройство и работу установки фирмы «АТЛАС» (Рис45):
конденсатор 6. Греющей средой, как сказано было выше, служит горячая пресная вода из системы охлаждения двигателя. Часть воды с температурой 65−700С пропускается через испаритель 11. В испарителе греющая вода, омывая трубки снаружи отдает часть теплоты для испарения забортной морской воды. Морская вода насосом 8 подается в нижнюю часть испарителя 11 и поступает внутрь трубок. Процесс испарения морской воды происходит при температуре 65−700С вследствие создаваемого в корпусе испарителя вакуума (порядка 93%) с помощью эжектора 7. образовавшийся пар проходит через отбойный щит сепаратора и достигает горизонтального конденсатора. В конденсаторе пар конденсируется и в виде дистиллята отводиться дистиллятным насосом 12 через соленомер 13 и расходомер 15 в танки пресной воды. При превышении солесодержания в дистилляте выше допустимого соленомер через электромагнитный клапан 14 возвращает дистиллят на повторное испарение. Неиспарившаяся морская вода с повышенным содержанием солей (рассол) постоянно откачивается рассольным насосом 9 за борт. Насос забортной воды 8 одновременно подает морскую воду в испаритель и обеспечивает работу вакуумного эжектора 7.
Рис. 45 Схема водоопреснительной установки типа " АТЛАС" : 1 — главный двигатель; 2 — терморегулятор; 3 — охладитель пресной воды; 4 — маслоохладитель; 5 — охладитель воздуха; 6 — конденсатор; 7 — эжектор; 8 — насос забортной воды; 9 — рассольный насос; 1 — ротаметр; 11 — испаритель; 12 — дистиллятный насос; 13 — соленомер; 14 — электромагнитный клапан; 15 — расходомер; 16 — насос забортной воды; 17 — насос пресной воды
В одном корпусе установки удачно скомпонованы испаритель 11 и При включении в работу такой установки необходимо учесть, что она начинает работать как охладитель пресного контура системы охлаждения дизеля.
В последние годы получили применение водоопреснительные установки с использованием принципа обратного осмоса — гиперфильтрации. Как было сказано выше он основан на разделении растворов фильтрованием через полупроницаемые мембраны, поры которых пропускают молекулы воды, но не пропускают гидратированные соли или молекулы недиссоциированных соединений. Если в сосуде между пресной и соленой водой поместить полупроницаемую перегородку, способную пропускать воду и задерживать гидратированные ионы растворимых в воде солей, то можно наблюдать, как пресная вода начинает поступать в отсек с соленой водой. Переток чистой воды происходит вследствие разницы концентрации жидкости по обеим сторонам перегородки. Через некоторое время уровень пресной воды станет заметно ниже уровня соленого раствора. Разница уровней после установившегося равновесия характеризует осмотическое давление растворенного вещества. Если создать в соленом растворе давление, превышающее осмотическое, то возникает перетекание молекул пресной воды в направлении, обратном ее естественному движению, т. е. вода из раствора начинает перетекать через перегородку в пресную воду. Такой процесс известен под названием обратного осмоса. Опреснение соленой воды методом обратного осмоса основывается как раз на процессе перетекания молекул чистой воды из раствора при создании давления, превышающего осмотическое, в направлении от раствора к пресной воде через полупроницаемую перегородку. Полупроницаемая перегородка выбирается с таким расчетом, чтобы через ее поры могли проходить молекулы воды, но не могли проходить ионы солей, растворенных в соленой воде. Поскольку ионы солей, в размере примерно в 1,5 раза больше, чем молекулы воды, то это осуществить (в техническом смысле) вполне возможно.
Метод обратного осмоса по сравнению с традиционными методами обладает существенными преимуществами: затраты энергии на процесс относительно невелики, установки конструктивно просты и компактны, их работа мало зависит от колебаний качества исходной воды, для эксплуатации не требуется высококвалифицированного персонала, работа установок может быть легко автоматизирована. Основной особенностью обратного осмоса является практическое отсутствие расхода каких-либо химических реагентов для обработки воды (кислоты, щелочи и др.), если не считать небольших затрат для корректировки рН, ингибирования солеотложений и периодической промывки мембран.
11. Установки по предотвращению загрязнения морской среды
Каждое морское судно является источником загрязнения окружающей среды нефтепродуктами, сточными водами. мусором, пищевыми отходами, выхлопными газами. конвенцией МАРПОЛ 73/78 установлены правовые, организационные и нормативно-технические требования, направленные на предотвращение загрязнения моря с судов.
11.1 Установки очистки нефтесодержащих вод
Из всего разнообразия конструкций сепараторов очистки нефтесодержащих вод «ФРАМ», «ПП МАТИК», «ГИДРОПУР», «САРЕКС», «СОФРАНС», «АКВАМАРИН» ," ПЕТРИЛИМИНАТОР", «РWО», «ТУРБО» и др. можно выделить общие принципы работы: многоступенчатость очистки; автоматическая работа сепараторов. (По требованию Конвенции МАРПОЛ 73/78 если концентрация нефтепродуктов в очищенной воде превысит 15 мл/л происходит прекращение сброса воды за борт и ее перпуск на повторную очистку.) В настоящее время применяют следующие способы очистки нефтесодержащих вод: остой, коалесценция. коагуляция, флотация, биологические методы. Рассмотрим работу установки «СОФРАНС» (Франция), в которой очистка осуществляется способом отстоя и коалесценции. (Рис.46)
Рис. 46 Схема установки " СОФРАНС"
Насосом 1 НВ подается в установку 2 через приемный патрубок 3. В верхней полости 6 установки происходит отстой НВ, в процессе которого пленочные и капельные нефтепродукты всплывают вверх. Частично очищенная вода проходит через полипропиленовые пластины 8, которые, и являются коалесцирующим материалом.
Внутри пластин мелкие частицы нефтепродуктов укрупняются, и всплывают. Из полипропиленовых пластин вода поступает по трубе 9 в патронный фильтр 7. В нем происходит окончательная очистка. Накопление в верхней части установки нефтепродуктов контролируется датчиками 5, которые через систему управления открывают клапана 4 для сброса нефтепродуктов в шламовую цистерну. В установке используется насос объемного типа с низкой частотой вращения. Применение такого насоса позволяет исключить дополнительное эмульгирование НВ при перекачивании её насосом.
11.2 Установки очистки сточных вод
Хорошо себя зарекомендовали конструкции судовых установок очистки сточных вод:
— Установка типа «БИО-КОМПАКТ»
— Установка типа «Нептуматик»
— Установка типа «Юнекс-Био»
Установки типа " БИО КОМПАКТ"
Установки типа «Био Компакт» фирмы «Дойче Герэтэтау Зальц-коттен» (Германия) работают по технологической схеме продленной аэрации (рис.47). Фекальные и хозяйственно-бытовые воды по трубопроводу 6 поступают в аэротанк первой ступени 15, где перемешиваются и обрабатываются воздухом с помощью аэратора 2. Аэратор 2 расположен в аэротанке асимметрично, чем обеспечивается естественная циркуляция стоков. Воздух на аэраторы подается компрессором 8. Частично окисленные стоки поступают по трубопроводу 3 для последующей обработки в аэротанк второй ступени 1. Избыточный воздух и продукты окисления удаляются по вентиляционной трубе 5
Рис. 47. Принципиальная схема установки " Био Компакт" : 1 — аэротанк второй ступени; 2 — аэратор; 3,4 — трубопровод; 5 — вентиляционная труба; 6-трубопровод; 7,14 — аэролифт; 8 — компрессор; 9 — шкафу управления;; 10 — датчики; 11 — насос-дозатор; 12 — камера дезинфекции; 13 — отстойник; 15 — аэротанк первой ступени
Окисленные стоки по трубопроводу 4 подаются в отстойник 13 для осветления. Осевший активный ил возвращается аэролифтом 14 в аэротанк первой ступени 1. Туда же аэролифтом 7 откачиваются всплывшие частицы,
Осветленная вода из отстойника 13 направляется в камеру дезинфекции 12, где обрабатывается хлорсодержащими реагентами. Ввод реагентов в камеру 12 ведется насосом-дозатором 11. Периодическая работа насоса-дозатора 11, откачивающего насоса-измельчителя 16 обеспечивается автоматически. Регулирование уровня в камере 12 осуществляется датчиками 10. Вся система автоматики смонтирована в шкафу управления 9.
11.3 Установки переработки мусора
В соответствии с требованиями Приложения V конвенции МАРПОЛ 73/78 на судне должен быть предусмотрен один из перечисленных видов оборудования по предотвращению загрязнения моря мусором:
Устройства для сбора мусора.
Устройства для обработки мусора.
Установка для сжигания мусора.
Поэтому можно выделить два способа утилизации: сбор и обработка мусора на судне.
Сбор мусора на судах
Количество мусора может быть уменьшено путем повторного использования упаковки. В случаях, когда существует возможность выбора, судовое снабжение следует поставлять в упаковке из материалов иных, чем утилизируемый пластик. Следует рационально использовать расходные материалы с учетом срока их хранения после вскрытия упаковки. Необходимо сводить к минимуму прием на борт судна потенциального мусора, а также образование мусора на борту.
На каждом судне длиной более 12 м должны вывешиваться плакаты, извещающие экипаж судна и пассажиров о требованиях по сбору мусора. Плакаты должны быть написаны на официальном языке государства, под флагом которого плавает судно, и на английском или французском языке, если суда заняты в рейсе к портам или морским терминалам других сторон Конвенции.
Каждое судно валовой вместимостью более 400 и каждое судно, сертифицированное для перевозки более 15 человек, должно иметь и выполнять план операций с мусором. План операций с мусором разрабатывается в соответствии с Руководством, принятым резолюцией МЕРС 70/38 от 10.07.1996 г. В плане должны быть отражены следующие вопросы:
процедуры сбора, хранения, обработки и удаления мусора;
состав судового оборудования для операций с мусором;
мероприятия по уменьшению количества мусора на судне;
ответственное лицо за выполнение плана.
План оформляется на рабочем языке команды судна.
Администрация судна обязана постоянно следить за санитарным состоянием устройств и оборудования для сбора и обработки мусора и своевременно принимать меры по устранению выявленных недостатков.
Устройства по сбору мусора
Для сбора мусора на судне могут быть предусмотрены съемные устройства (контейнеры), мешки, встроенные в корпус мусоронакопительные емкости (бункеры) или бункеры установок для уплотнения мусора.
Устройства для сбора мусора, в которых он должен собираться и храниться, должны быть надежно закрыты, причем на каждом из них должна быть соответствующая маркировка, указывающая вид мусора. Так же они должны размещаться, как правило, в зоне действия судовых грузоподъемных средств для обеспечения возможности погрузки и выгрузки их с учетом удобства сбора мусора. Съемные устройства для сбора мусора должны надежно крепиться к корпусу судну.
Категорически запрещается смешивать пищевые отходы с бытовыми и нефтесодержащими отходами.
Конвенция по защите морской среды района Балтийского моря рекомендует на судах, построенных после 1 октября 1993 г., иметь следующие минимальные емкости для хранения мусора всех категорий.
Объем емкостей для хранения мусора:
При расчете емкости мусоросборников следует руководствоваться национальными санитарными правилами. При подходе к особым районам и другим районам моря, где сброс мусора запрещен, администрация судна обязана оповестить об этом экипаж и пассажиров. Все средства для сбора периодически сбрасываемого в море мусора должны быть заблаговременно опорожнены и приготовлены для приема мусора. 1
Выбор ёмкостей, включая необходимые объемы судовых накопительных цистерн и контейнеров, а также устройств, сосредоточенных в портах, зависит от многих факторов, но в первую очередь от класса, типа судна и условий эксплуатации (район плавания, длительность рейса между заходами в порты). Естественно, что для судов, совершающих короткие рейсы, существует возможность один раз в 2.3 дня передавать отходы на берег, достаточно простейших накопительных устройств.
Данный способ применяют в том случае, когда необходимое оборудование есть и на судне, и в порту, в который намечено передать отходы. На судне должны быть прежде всего контейнеры, размещенные, как правило, на корме, а в портах — суда-сборщики, специализированные причалы, машины-мусоросборщики, устройства для переработки отходов и т. п.
Обработка мусора на судне
Судно может быть оснащено устройствами для обработки и уничтожения мусора такими, как:
установка для сжигания судовых отходов (инсинераторы);
измельчитель мусора (грохот);
установка для прессования мусора.
Инсинераторы
Значительное развитие и широкое применение в последние годы получил термический способ обработки судовых отходов. Отходы сжигаются в специальных печах-инсинераторах. Данным способом можно уничтожить практически все виды судовых отходов, за исключением металла и стекла, которые следует отделять из общей массы. Производительность инсинератора определяется количеством отходов, которые могут быть сожжены в единицу времени.
Способ термической обработки судовых Отходов имеет следующие преимущества: возможность переработки всех видов мусора и значительное уменьшение его объема, стерильность образующихся остатков, автоматизация процесса.
Установки для сжигания мусора должны иметь сертификат Регистра, подтверждающий фактическую способность сжигать отходы, наименование которых должно быть перечислено в Инструкции по эксплуатации установки для сжигания мусора. Кроме того, все инсинераторы, установленные на судах после 01 января 2000 г., должны иметь Свидетельство о типовом одобрении (СОТО). В инсинераторах, имеющих СОТО, разрешено частичное сжигание пластика (например, бумаги — 30%, картона — 40%, ветоши — 10%, пластика — 20%. Зола, которая образуется в результате сжигания мусора, представляет собой обеззараженный мусор, и он сбрасывается за борт на расстоянии более 12 морских миль от ближайшего берега за пределами особых районах за исключением золы пластмасс, которая может содержать остатки токсичных веществ и тяжелых металлов. Такая зола сохраняется на борту и сдается на береговые или плавучие сооружения3.
При сжигании мусора запрещается загружать в инсинераторы большое количество промасленной ветоши и пластика, так как это может привести к резкому повышению температуры в реакторе и повышенной дымности отходящих газов, поэтому следует обратить внимание на использование инсинераторов в портах. Так, например, в территориальных водах стран — участников Конвенции ХЕЛКОМ 92 в районе Балтийского моря запрещается любое сжигание отходов, образовавшихся на борту судна.
Отсепарированные нефтяные остатки и нефтесодержащая ветошь подлежат уничтожению на судне в установках для сжигания судовых отходов или сдаче на берег, о чем делается соответствующая запись в ЖНО (журнале нефтяных операций), часть 1.
К недостаткам способа можно отнести достаточную пожароопасность на судне, повышеный расход топлива и трудоемкость дополнительного обслуживания.
Принцип работы:
Процесс сжигания мусора в инсинераторе можно условно разделить на два этапа: предварительное высушивание и собственно сжигание.
Высушивание мусора позволяет полнее использовать их теплотворную способность и тем самым экономить топливо. Эффективность высушивания отходов зависит от следующих факторов: распределения влаги в пределах массы отходов, температуры в зоне высушивания (сгорания), наличия устройств для перемешивания отходов с целью повышения скорости переноса тепла, размера частиц отходов (уменьшение размеров частиц способствует не только более быстрому высушиванию, но и более эффективному сжиганию).
В современных инсинераторах предварительное высушивание отходов осуществляется непосредственно в топке. Исключение составляет шлам сточных вод: влажность его значительно превышает допустимый предел, до которого можно сжигать отходы без подачи в топку дополнительного топлива. Иногда шлам предварительно перемешивают с топливом в специальном смесительном устройстве. Подсушке способствуют применяемые для этих целей колосниковые решетки, а также подача в топку воздуха.
Перед сжиганием отходы целесообразно подготовить: отделить предметы, способные при расплавлении залить отверстия колосниковых решеток и тем самым уменьшить подачу воздуха, например предметы из алюминиевых сплавов или стекла (температура плавления их соответственно около 700 и около 1100°С). Процесс подсушивания отходов, а следовательно, и их последующее сжигание значительно улучшаются, если в топке есть устройства для перемешивания отходов.
Топку обычно разогревают до температуры не менее 500 °C и заполняют твердыми отходами. Сжигание отходов осуществляется по принципу пиролиза. При температуре около 300 °C из органических веществ начинается испарение газообразных фракций. Происходит так называемая сухая перегонка твердых отходов. Газы поднимаются в верхнюю часть топки или в смежную камеру сгорания, и там с помощью вспомогательного факела полностью сгорают. При температуре более 750 °C дурно пахнущие газы в течение нескольких секунд распадаются.
Жидкие отходы подают в инсинераторы в распыленном виде через специальные шламовые форсунки. Подготовка жидких отходов к сжиганию заключается в приготовлении смеси, содержащей не менее 50% топлива и предварительно подогретой до 60.80°С. Теоретически для сжигания 1 кг жидких отходов требуется около 4 кг атмосферного воздуха. Для уверенности в полном сгорании отходов рекомендуется обеспечивать 50% избытка воздуха. Следовательно, рекомендуемый расход составляет 6 кг воздуха на 1 кг отходов. 4
Типы судовых инсинераторов
Рассмотрим работу инсинератора GS-500 (Норвежского производства) (Рис.48) Установка состоит из двух камер, образующих так называемую полупиролизную систему. Левая камера 1 предназначена для сжигания мусора, правая 2 — для сжигания шлама. Она оборудована топливной и шламовой форсунками, соединенными в специальное топочное устройство (на рисунке не показано) и газоходом 4. Вентилятор, подсоединяемый к газоходу, создает в камерах необходимое разрежение. Воспламенение отходов осуществляется за счет теплового излучения от топочного устройства.
Твердые отходы загружаются через приемный поворотный люк 3 после того, как температура в печи достигнет заданного значения. Колосниковая решетка 7, на которую попадают отходы, имеет шурующее устройство, обеспечивающее более эффективное их сгорание.
Рис. 48 Инсинератор GS-500
Поток газов, отходящих от сжигаемых отходов, поступает во вторичную камеру, где происходит их дожигание, а также несгоревших частиц отходов. Пройдя зону горелки, поток дымовых газов смешивается с потоком охлаждающего воздуха и затем выбрасывается в дымоход вентилятором рециркуляции. В газоходе между камерой сгорания и вентилятором имеется шибер (заслонка). Процесс горения (количество подаваемого воздуха) регулируется положением заслонки.
Камеры сгорания представляют собой стальные конструкции с обмуровкой из шлакоустойчивых огнеупорных блоков 5. Обмуровка имеет модульную конструкцию, позволяющую менять отдельные блоки. Внутренняя сторона стальных камер покрыта слоем изоляции. Между двойными листами стали находится воздушная охлаждающая рубашка 6. Камеры сгорания имеют круглую форму и соединены между собой отверстием в районе днища.
Емкость приемного пространства около 9 л. На лицевой стороне установки на дверце 9 предусмотрено смотровое стекло, позволяющее механику контролировать количество загруженных в камеру отходов и наблюдать за работой системы. В нижней части расположена дверца 8 для удаления золы и шлака.
Топочное устройство состоит из форсунки с двумя соплами. Производительность 14 — 28 л/ч. Шламовая форсунка также вмонтирована в топочное устройство и состоит из двух труб. Внутренняя труба предназначена для подвода шлама. Диаметр ее канала равен 8 мм. Наружная труба служит для подвода пара, который используется для распыливания и отчасти — для подогрева шлама. Топочное устройство расположено таким образом, чтобы наиболее эффективно использовать факелы горения. В данном инсинераторе завихренные факелы сначала направляются к днищу, откуда поднимаются в центральной зоне камеры сгорания и лишь затем направляются к газоходу.
Охлаждающий воздух, смешиваемый с дымовыми газами на выходе из камеры, засасывается из нижней части кожуха камеры и понижает температуру отходящих газов до уровня не выше 400 °C. Процесс сжигания автоматически контролируется специальной программой. Для контроля горения используется фотоэлектрический датчик.
Измельчители мусора
Также для обработки твердых бытовых отходов используются измельчители — установки, оборудованные специальными режущими приспособлениями, позволяющими размельчать любые виды твердых отходов, включая стеклянные предметы, консервные банки, деревянные ящики и др.
Широкого распространения измельчители не получили, хотя известны случаи их применения на некоторых судах. Это произошло потому, что данное устройство практически не позволяет отказаться от других видов оборудования для обработки отходов, в частности от контейнеров. Дело в том, что наш флот значительную часть времени находится в особых районах, где сброс измельченных твердых отходов, кроме пищевых, запрещен. Кроме того, определенную часть времени суда находятся в прибрежных зонах, на акватории портов, а также во внутренних водоемах, где запрещен сброс любых отходов, даже измельченных.
Представляет интерес способ дробления (измельчения) пищевых отходов, внедренный на некоторых судах и в некоторых портах. На судах пищевые отходы дробятся измельчителем, установленным на камбузе, после чего размельченные пищевые отходы направляются в судовую сборную цистерну (например, в цистерну сбора сточных вод). После выхода судна из порта за 12-мильную зону измельченные отходы вместе с СВ откачиваются за борт.
Прессы
Сложнее обстоит дело в тех случаях, когда передача отходов на берег затруднена или невозможна (например, при эксплуатации судна в необжитых районах, в условиях ледового плавания и т. п.). Бывают случаи, когда порты не оснащены необходимым оборудованием для приема и обработки мусора. Такая ситуация может осложниться, если судно вынуждено задержаться в порту, так как емкости судовых контейнеров может не хватить.
Конвенцией МАРПОЛ 73/78 такая ситуация предусмотрена. В ней указано, что отсутствие оборудования в порту не должно быть основанием для сброса отходов за борт на акватории порта, на рейде и в прибрежных (территориальных) водах. В качестве одного из способов борьбы с отходами, точнее, для уменьшения объема скапливающихся судовых отходов, рекомендуется использовать специальные прессы — устройства, снижающие объем твердых бытовых отходов примерно в 8.10 раз.
Прессование как способ обработки отходов имеет следующие преимущества: возможность обработки любых видов твердых отходов (при этом не обязательна предварительная их сортировка); установки для прессования имеют простую конструкцию и почти не требуют ухода; возможность монтажа в любом месте судна, включая палубу; небольшая потребляемая мощность. К недостаткам этого способа следует отнести то, что для хранения спрессованных отходов требуются помещения и обеззараживание при хранении спрессованных отходов на судне. http://www.bestreferat.ru/referat-194 582.html — sdfootnote8sym#sdfootnote8sym
11.4 Установки очистки выхлопных газов судовых дизелей (Скрубберы)
Скруббер (англ. «scrubber», от англ. scrub — «скрести», «чистить») — устройство, используемое для очистки твёрдых или газообразных сред от примесей в различных химико-технологических процессах. Газоочистка — это улавливания из отводимых с печей газов пыли, возгонов и оксидов селена, телура, свинца и других элементов. Очистка газов от примесей с помощью скрубберов относится к мокрым способам очистки. Этот способ основан на промывке газа жидкостью (обычно водой) при максимально развитой поверхности контакта жидкости с частицами аэрозоля и возможно более интенсивном перемешивании очищаемого газа с жидкостью. Данный метод позволяет удалить из газа частицы пыли, дыма, тумана и аэрозолей (обычно нежелательные или вредные) практически любых размеров.
Выделяют следующие виды скрубберов:
— циклоны (насадочные скрубберы);
— орошаемые циклоны (центробежные скрубберы);
— пенные аппараты;
— скрубберы Вентури.
Аппараты мокрого пылеулавливания
Процесс мокрого пылеулавливания основан на контакте запыленного газового потока с жидкостью, которая захватывает взвешенные частицы и уносит их из аппарата в виде шлама.
Мокрая очистка, промывка газов, скрубберная очистка — все это синонимы, определяющие мокрый способ удаления аэрозолей из газовых потоков, являющийся одним из самых эффективных методов пылеулавливания.
Мокрую очистку газов применяют в тех случаях, когда допустимы охлаждение и увлажнение очищаемых газов и хорошо отработаны технологические мероприятия по предотвращению брызгоуноса и утилизации отработанных стоков. Однако, несмотря на указанные ограничения, мокрое пылеулавливание в ряде случаев может оказаться более целесообразным и оправданным, чем сухое. Аппараты мокрого пылеулавливания проще по конструкции, но при этом обладают эффективностью, присущей наиболее сложным сухим пылеуловителям. Их легко изготовить непосредственно на химическом предприятии; как правило, они не имеют подвижных узлов, которыми часто оснащены сухие пылеуловители (например, узлы встряхивания в рукавных фильтрах).
Достоинства мокрых пылеуловителей, по сравнению с аппаратами сухого типа:
— более высокая эффективность улавливания взвешенных частиц;
— возможность использования для очистки газов от частиц размером крупнее 0,1 мкм;
— допустимость очистки газов при высокой температуре и повышенной влажности, а также при опасности возгораний и взрывов очищенных газов и уловленной пыли;
— возможность наряду с пылью одновременно улавливать парообразные и газообразные компоненты.
Однако метод мокрого обеспыливания имеет и ряд недостатков:
— выделение уловленной пыли в виде шлама, что связано с необходимостью обработки сточных вод, т. е. с удорожанием процесса;
— возможность уноса капель жидкости и осаждения их с пылью в газоходах и дымососах;
— в случае очистки агрессивных газов необходимость защищать аппаратуру и коммуникации антикоррозионными материалами.
В качестве орошающей жидкости в мокрых пылеуловителях чаще всего применяется вода; при одновременном решении вопросов пылеулавливания и химической очистки газов выбор орошающей жидкости (абсорбента) обусловливается процессом абсорбции.
В результате контакта запыленного газового потока с жидкостью в мокрых пылеуловителях образуется межфазная поверхность контакта. В различных аппаратах характер поверхности контакта фаз различный: она может состоять из газовых струек, пузырьков, жидкостных струй, капель, пленок жидкости. Поскольку в пылеуловителях наблюдаются различные виды поверхностей, то пыль улавливается в них по различным механизмам.
Общепринятой классификации мокрых пылеуловителей до настоящего времени не существует. Обычно они подразделяются на группы в зависимости от характера (вида) поверхности контакта фаз (капельные, пленочные, барботажные) или способу действия:
— полые газопромыватели (оросительные промывные камеры; полые форсуночные скрубберы);
— насадочные скрубберы;
— тарельчатые газопромыватели (барботажные и пенные аппараты);
— газопромыватели с подвижной насадкой;
— мокрые аппараты ударно-инерционного действия;
— мокрые аппараты центробежного действия;
— механические газопромыватели (механические скрубберы, динамические скрубберы);
— скоростные газопромыватели (скрубберы Вентури, эжекторные скрубберы).
Иногда мокрые пылеуловители подразделяют по затратам энергии на низконапорные, средненапорные и высоконапорные. К низконапорным аппаратам относятся пылеуловители, гидравлическое сопротивление которых не превышает 340 Па. В эту группу входят форсуночные скрубберы, барботажные аппараты, мокрые центробежные аппараты и другие. К средненапорным мокрым пылеуловителям с гидравлическим сопротивлением от 340 до 3000 Па относятся некоторые динамические скрубберы, газопромыватели ударно-инерционного действия, эжекторные скрубберы. Группа высоконапорных газопромывателей с гидравлическим сопротивлением более 3000 Па включает в основном скрубберы Вентури и аппараты с подвижной насадкой.
Полые газопромыватели
В полых газопромывателях запыленные газы пропускают через завесу распыляемой жидкости. При этом частицы пыли захватываются каплями промывной жидкости и осаждаются в аппарате, а очищенные газы удаляются из него.
Наиболее распространенным аппаратом этого класса является полый форсуночный скруббер.
Полые форсуночные скрубберы представляют собой колонны круглого или прямоугольного сечения, в которых осуществляется контакт между газами и каплями жидкости, распыливаемой форсунками. По направлению движения газов и жидкости полые скрубберы делятся на противоточные, прямоточные и с поперечным подводом жидкости. При мокром обеспыливании обычно применяют аппараты с противонаправленным движением газов и жидкости, реже — с поперечным подводом жидкости. Прямоточные полые скрубберы широко используются при испарительном охлаждении газов.
В противоточном скруббере (рис.49) капли из форсунок падают навстречу запыленному потоку газов. Капли должны быть достаточно крупными, чтобы не быть унесенными газовым потоком, скорость которого обычно составляет vг = 0,6−1,2 м/с. Поэтому в газопромывателях обычно устанавливают форсунки грубого распыления, работающие при давлении 0,3−0,4 МПа. При скоростях газов более 5 м/с после газопромывателя необходима установка каплеуловителя.
Рис. 49 Полый форсуночный скруббер: 1 — корпус; 2 — газораспределительная решетка; 3 — форсунки
Высота аппарата обычно в 2,5 раза превышает его диаметр (Н = 2,5D). Форсунки устанавливают в аппарате в одном или нескольких сечениях: иногда рядами (до 14−16 в сеч.), иногда только по оси аппарата.
Факел распыла форсунок может быть направлен вертикально сверху вниз или под некоторым углом к горизонтальной плоскости. При расположении форсунок в несколько ярусов возможна комбинированная установка распылителей: часть факелов направлена по ходу газов, другая часть — в противоположном направлении. Для лучшего распределения газов по сечению аппарата в нижней части скруббера устанавливают газораспределительную решетку.
Полые форсуночные скрубберы широко используют для улавливания крупной пыли, а также при охлаждении газов и кондиционирования воздуха. Удельный расход жидкости невелик — от 0,5 до 8 л/м3 очищенного газа.
Эффективность очистки в полом противоточном скруббере возрастает с уменьшением размера капель и с увеличением скорости газа. Поскольку эти условия являются взаимоисключающими, при эксплуатации скруббера необходимо придерживаться определенного оптимального гидродинамического режима. Согласно расчетам, максимальная эффективность при инерционном осаждении частиц пыли на каплях наблюдается при dк = 0,8 мм. Капли такого размера могут быть получены при помощи обычных центробежных форсунок грубого распыла, работающих под давлением (3−4) 105 Па. При эксплуатации таких форсунок можно использовать оборотную воду, содержащую взвеси.
Степень улавливания частиц крупнее 10 мкм в полых форсуночных скрубберах составляет 99%, но для частиц меньшего размера она резко снижается. Полые форсуночные скрубберы малоэффективны при улавливании частиц размером менее 5 мкм.
Насадочные газопромыватели
Насадочные газопромыватели представляют собой колонные аппараты с неподвижной насадкой в виде колец, шаров, седел или тел другой формы. В пылеулавливании нашли в основном применение противоточные насадочные скрубберы (рис. 50).
Рис. 50 Схема противоточного насадочного скруббера: 1 — корпус скруббера; 2 — входной патрубок; 3 — насадка; 4 — решетка для насадки; 5 — трубопровод для подачи жидкости; 6 — выходной патрубок; 7 — направляющий конус для жидкости; 8 — штуцер для вывода шлама
Насадка предназначена для увеличения поверхности контакта фаз. Жидкость течет пленкой по насадке, газ проходит противотоком. Такие газопромыватели используют для улавливания хорошо смачиваемой пыли, но при невысокой ее концентрации, поскольку в противном случае происходит частое забивание насадки.
1. Андреенков В. Г. Теория судна (конструкция корпуса судна, судовые устройства и системы): учеб. пособие / В. Г. Андреенков, А. В. Самохвалов; Новороссийская гос. морская акад. — 2-е изд. — Новороссийск: НГМА, 211. — 176 с.
2. Кацман Ф. М. Теория и устройство корабля: учебник для вузов / Ф. М. Кацман, Д. В. Дорогостайский. — СПб: Судостроение, 2009. — 279 с.
3. Правила классификации и постройки морских судов: В 3-х т. Т.1: Морской Регистр Судоходства — М: Транспорт, 2005. — 428 с.
4. Теория и устройство судов: метод. руководство по разработке курсового проекта «Расчет посадки, остойчивости и непотопляемости судна в процессе эксплуатации» / сост. Ю. И. Юдин, А. А. Соловьев. — Мурманск: МГАРФ, 213. — 36 с.