Вагонное пассажирское депо с отделением по ремонту букс с роликовыми подшипниками
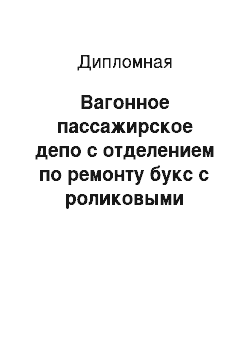
При ревизии, выполняемой по подпунктам «в» и «г» и при удовлетворительном состоянии подшипника остукиванием контролируют болты стопорной планки или тарельчатой шайбы. Ослабшие болты М12 подтягивают, неисправные заменяют. Неисправную проволоку болтов стопорной планки заменяют, под болты стопорной планки ставят пружинные шайбы. Надежность крепления торцевой гайки проверяют ударами слесарного… Читать ещё >
Вагонное пассажирское депо с отделением по ремонту букс с роликовыми подшипниками (реферат, курсовая, диплом, контрольная)
Введение
Важное значение в совершенствовании перевозочного процесса принадлежит вагонному хозяйству, которое объединяет вагоны и материально — техническую базу для их ремонта. Вагонное хозяйство сформировалось как самостоятельная под отрасль железнодорожного транспорта в 1933 г. Основные фонды этого хозяйства составляют пятую часть основных фондов железнодорожного транспорта. Создана необходимая материально — техническая база вагонного хозяйства.
В последнее время растет объем перевозочной работы, и вагоны на дорогах используются все более интенсивно.
Ежегодно на ремонт и техническое обслуживание вагонного парка расходуется более 2,3 млрд руб. На долю вагонного хозяйства приходится около 12% эксплуатационных расходов, почти 7% контингента рабочих железной дороги.
Восстановление работоспособности вагонного парка и поддержание его в технически исправном состоянии осуществляют вагоноремонтные заводы и вагонные депо в ходе планово — предупредительного и текущего ремонта.
Таким образом, от четкой, сложенной работы подразделений вагонного хозяйства во многом зависят бесперебойность и безопасность движения поездов, своевременное обеспечение перевозок технически исправным подвижным составом, эффективность использования транспортных средств.
Поэтому вагонное хозяйство железных дорог, развивая современную техническую базу для обслуживания и ремонта вагонов, приобретает прочную индустриальную основу для обеспечения высокого уровня работоспособности вагонного парка в современных и перспективных условиях его эксплуатации.
Пассажирское вагонное депо является структурным подразделением ОАО «Российские железные дороги». Оно входит в состав региональной пассажирской дирекции дальнего следования, которая подчиняется Федеральной пассажирской компании (ФПК) — дочернему акционерному обществу «РЖД».
Вагонное депо станции Хабаровск, предназначено для деповского ремонта пассажирских и почтово-багажных вагонов, обеспечения запасными деталями и материалами приписанные пункты технического обслуживания вагонов.
Вагонное депо имеет право капитального ремонта.
Для выполнения плана деповского и капитального ремонтов вагонов и обеспечения ПТО всеми необходимыми материалами и запасными частями вагонное депо имеет производственные участки:
— Участок деповского ремонта тележек;
— Малярное отделение;
— Участок ремонта внутреннего оборудования;
— Колесно-роликовый участок;
— участок ремонта автосцепки;
— ремонтно-механический участок с кузнечным и станочным отделениями;
— инструментально-раздаточная;
— подразделение неразрушающего контроля;
Производственные участки имеют технологическое подъемно-транспортное оборудование. Мостовые краны грузоподъемностью 10 тонн, кран-балки грузоподъемностью 0,5−3 тонн, козловые краны — от 3 до 5 тонн.
Производственная структура вагонного депо определяется составом производственных подразделений, их взаимным расположением и формами технологической взаимосвязи. Тип вагонов, по которым специализировано депо, определяет состав производственных участков и отделений, необходимых для ремонта узлов и деталей. В проектируемом депо все участки и ремонтные отделения связаны общей технологией и объединены в главном корпусе.
Увеличение выпуска вагонов из ремонта одновременно с повышением его качества одна из важных задач, обеспечивающих улучшение использования вагонов. На вагоноремонтных предприятиях совершенствуется система планирования и материального стимулирования с широким внедрением научной организации труда, специализации с прогрессивной технологии ремонта на основе широкого использования передовых достижений науки и практики.
Одной из главных деталей вагона является буксовый узел. Надежность работы букс вагонов в значительной мере зависит от исправности подшипников. Особое внимание уделено изучению характера и признаков повреждений деталей подшипников в буксах пассажирских и грузовых вагонов.
Для ремонта букс с роликовыми подшипниками в вагонном депо созданы специализированные производственные участки. Качество ремонта буксового узла определяется совершенством организации производства, квалификации работников уровнем механизации и автоматизации производственных процессов, наличие специального измерительного инструмента.
1. Организационная часть
1.1 Назначение и производственная характеристика пассажирского вагоноремонтного депо Под производственной структурой депо понимают состав производственных участков, вспомогательных и обслуживающих подразделений с указанием связей между ними.
Производственным участком называют объединенную по тем или иным признакам группу рабочих мест, выделенную в самостоятельную административную единицу и возглавляемую мастером. В состав производственного участка могут входить несколько отделений.
Производственная структура вагонного депо определяется составом производственных подразделений, их взаимным расположением, а также формами технологической взаимосвязи. Производственная структура обеспечивает реализацию принципов специализации, пропорциональности и прямоточности.
Состав производственных подразделений определяют типы вагонов, на ремонте которых специализировано депо, а программу — целесообразное разделение производственного процесса на стадии, закрепление за каждым рабочим местом технологических операций.
Основной структурной единицей вагонного депо является производственный участок.
Различают основные, вспомогательные и обслуживающие участки и отделения.
На основных участках выполняются производственные операции по ремонту вагонов и его частей. К таким участкам относят: вагоносборочный, ремонта тележек и колесных пар, роликовых подшипников, ремонтно — комплектовочный, электрооборудования пассажирских вагонов, холодильных установок и кондиционеров.
Вспомогательные участки и отделения предназначены для обеспечения работы депо. К вспомогательным участкам относят ремонтно-механический, ремонта электросилового оборудования, деревообделочный, а к вспомогательным отделениям — инструментальное и ремонтно-строительное.
К обслуживающим, относится ремонтно-хозяйственный участок, который обеспечивает работу котельной, компрессорной станции, трансформаторной подстанции, сетей водоснабжения и канализации, трансформаторного и складского хозяйства. Поддержание в чистоте и ремонт спецодежды, текущий ремонт зданий и сооружений депо.
Управление вагонным депо построено по бесцеховой структуре. Это положительно отражается на организации производства, приближает техническое и административно — хозяйственное руководство подразделения рабочим местам, улучшает оперативность руководства, увеличивает ответственность и повышает роль мастера.
1.2 Вспомогательные участки и отделения депо Ремонтно-механический участок предназначен для выполнения работ по техническому обслуживанию и ремонту технологического подъемно-транспортного оборудования депо и ПТО. Для производства работ на участке установлены станки токарно-винторезные, горизонтальнои вертикально-фрезерные, сверлильные, шлифовальные, строгальные и заточные.
Участок ремонта электросилового оборудования депо служит для обеспечения бесперебойной работы электрооборудования, его технического обслуживания и ремонта. В нем размещены слесарные верстаки, настольный сверлильный станок, столы-стеллажи, стенд для испытания электрооборудования, кран консольный поворотный с электроталью грузоподъемностью 250 кг. В помещении стоянки электрокаров и погрузчиков размещены устройства контроля и зарядки аккумуляторных батарей, трансформатор, селеновый выпрямитель, шкафы.
Деревообделочный участок предназначен для изготовления несъемного оборудования, сушки и обработки пиломатериалов для нужд депо и ПТО. Этот участок создается в крупных пассажирских депо, а также в грузовых, которые специализируются на ремонте платформ и покрытых вагонов. Для сушки пиломатериалов применяются высокотемпературные камеры. Пиломатериал обрабатывают на станках: четырехстороннем строгальном, фуговочном, рейсмусовом.
Инструментально-раздаточное отделение служит для хранения, ремонта, учета и выдачи режущего, слесарного, измерительного и другого инструмента, а также для их частичного изготовления. В помещении раздаточной установлены шкафы и стеллажи, а для ремонта размещены станки: токарно-винторезный, вертикально-сверлильный, универсально-заточный, точильный, а также испытательный стенд для наждачных кругов, верстаки и столы.
Ремонтно-строительное отделение обеспечивает ремонт всех зданий и сооружений, ремонтирует строительные детали зданий, а также хозяйственный инвентарь.
Кладовая депо предназначена для хранения и выдачи материалов и запасных частей. В ней установлены стеллажи, весы сотенные до 500 кг и настольные до 30 кг, шкафы и другое оборудование. Она должна располагаться с учетом удобства транспортировки материалов и запасных частей как в нее со складов, так и из нее к ремонтируемым вагонам и их деталям.
Компрессорная депо служит для обеспечения сжатым воздухом сборочного и других участков и отделений. Здесь устанавливаются два компрессора производительностью 10 / мин.
1.3 Назначение и характеристика колёсно-роликового цеха Отделение ремонта роликовых подшипников предназначено для осмотра, определения необходимого вида ремонта, проведения ремонта, комплектования и хранения подшипников. Отделение размещено в чистом, сухом, светлом и изолированном помещении на 3 этаже участка ремонта колесных пар, рядом с демонтажным и монтажным отделениями. Отделение оборудовано столами, обитыми листовой сталью для осмотра подшипников, стеллажа для хранения подшипников и других деталей, необходимой технологической оснасткой (приспособления для зачистки роликов, колец подшипников, ультразвуковыми моечными машинами), а также шкафами для хранения приборов, инструмента и приспособлений.
Температура в помещении отделения ремонта роликовых подшипников должна быть не ниже +10 градусов.
Колёсный парк Он предназначен для:
— хранения отремонтированных колёсных пар, колёсных пар ожидающих ремонта или отправки на завод для смены элементов
— разгрузки, осмотра и предварительного определения объёма ремонта неисправных колёсных пар поступивших с линии; оформление приходного листка ВУ-51
— погрузки неисправных колёсных пар для отправки в заводы и исправных на линию
Колёсный парк состоит из рабочего парка и парка готовой продукции. Парк готовой продукции служит для хранения отремонтированных и исправных колёсных пар, а рабочий парк предназначен для хранения ожидающих ремонта колёсных пар рассортированных по типам осей.
Участок по ремонту подшипников предназначен для протирки и хранения подшипников, поступивших после обмывки по лотку через окно из колёсно-токарного отделения, дефектоскопирования роликов, ремонта и подбора роликов, передачи промытых подшипников по лотку через окно в комплектовочное отделение. Он размещён в изолированном помещении, имеет смежное помещение с комплектовочным участком.
Комплектовочный участок предназначен для осмотра, измерения осевых зазоров подшипников, измерения диаметров внутренних колец подшипников на горячей посадке, дефектоскопии полиамидных сепараторов, смазывания блоков подшипников, передачи скомплектованных подшипников по лотку в монтажное отделение, хранение неснижаемого запаса подшипников. Он размещён в изолированном помещении, имеет смежные помещения с участком по ремонту подшипников и отделения монтажа колёсных пар.
Монтажное отделение предназначено для монтажа букс с роликовыми подшипниками на шейку оси колёсной пары. Смазывания маслом внутренней поверхности корпуса буксы, подбора парных подшипников, контроля радиального зазора и подбора парных подшипников, укладки подшипников в буксу. Смазывание маслом внутренних колец на шейке оси и в блоке подшипников, нанесения смазки Л3 ЦНИИ на лабиринтные кольца и в блок подшипников. Монтажа букс в комплекте с блоком подшипников на шейку оси, крепления гайки или болтов торцевой шайбы, обвязки проволокой болтов М12. Крепления стопорной планки, клеймения оси, монтажа крепительной и смотровой крышек, проверки лёгкости проворачивания буксы.
Предмонтажное отделение примыкает с одной стороны к колёсно-токарному отделению, а с другой стороны к монтажному отделению. Предназначено для осмотра букс, осмотра осевых гаек, стопорных планок, осмотра, зачистки и замера шеек колёсных пар, демонтажа лабиринтных и внутренних колец (если необходимо), окраски средней части оси, дисков, нанесения контрольных полос, отстоя колёсных пар перед монтажом и после ремонта.
Колёсно-токарное отделение предназначено для предварительного осмотра и определения необходимого ремонта, обмера, оформления приходного листа ВУ-51, демонтажа букс с роликовыми подшипниками, обмывки колёсных пар в моечной машине, обмывки корпусов букс, обмывки роликовых подшипников в автоматической установке, обмывки деталей букс, обточки поверхности катания колёсных пар, дефектоскопии колёсных пар, промежуточной ревизии букс колёсным парам, выкаченных из — под вагонов деповского ремонта (пригодных для подкатки под вагоны текущего ремонта), окраски.
1.4 Определение режимов работы участка Режим работы отделения — односменный.
Принимаю Дк = 365 дней, Дп = 14 дней, tc = 8 часов, mсм = 1 смена Фонд времени работы оборудования — это количество часов его работы в течение определенного периода времени (год, квартал, месяц). Различают номинальный и действительный годовой фонд времени работы.
Номинальный фонд времени работы оборудования рассчитывается по формуле:
Fноб =[ (Дк — Дп)х tc]x mсм, (1.4.1)
где Дк — количество календарных дней в году, дни;
Дп — количество праздничных дней и выходных, дни;
Дпредпраздн — количество предпраздничных дней в году, с сокращением продолжительности рабочего дня на 1 час, дни;
tc — продолжительность рабочей смены, час;
mсм — количество смен, смена.
Fноб = [(365 — 14) х 8] x 1 = 2808 часов Действительный фонд времени работы оборудования определяется по формуле:
Fgоб = Fноб х об, (1.4.2)
где Fноб — номинальный фонд времени работы оборудования;
об — коэффициент, учитывающий простой оборудования по технической неисправности и в ремонте. Принимаю об = 0,95 0,98.
Fдоб = 2808×0,95 = 2667,6 часов Фонд времени работы одного рабочего определяется при условии, что среднемесячная норма часов, принятая на железнодорожном транспорте равна 164,17 часа
Fр = 164,17×8 = 1313 часов Вывод: Произведя расчёты установлено, что действительный фонд времени работы оборудования составляет 4001,4 часа, фонд времени одного рабочего 1970 часов в год.
Явочное рабочее время определяется по формуле:
Фяв = Ч1 (1.4.3)
где Дк — количество календарных дней в году;
Дпраздн — количество праздничных дней в году;
tсм — продолжительность смены;
Дпредпраздн — количество предпраздничных дней в году;
Фяв = (365−14)/2Ч12−14Ч1=2092 часа.
Списочное рабочее время определяется по формуле:
Фсп= ФявЧ ((100-Е)/100) (1.4.4)
Фсп = 2092Ч ((100−7)/100) = 2092Ч0,93=1945,5 часа.
1.5 Выбор оборудования к планировкам отделения по ремонту роликовых подшипников Согласно технологического процесса на ремонт буксовых узлов с роликовыми подшипниками в отделении по ремонту этих узлов устанавливается следующее оборудование.
Таблица 1 — Оборудование колесно-роликового отделения
Поз. | Наименование | Обозначение | Коли-чество | |
Рельсовый путь из колёсного парка на участок (позиция предварительного осмотра) | ||||
Рельсовый путь к позиции обкатки редукторов | ||||
Лоток для перемещения подшипников из отделения ремонта роликовых подшипников на позицию монтажа буксовых узлов | собств. изготов. | |||
Подъёмно-поворотное устройство на 1800 | ММ 173 | |||
Подъёмник подшипников | ММ 273 | |||
Моечная машина подшипников | МОП | |||
Позиция сушки окрашенных колесных пар | ||||
Комплекс устройств для демонтажа буксовых узлов | ММ 083 | |||
Моечная машина букс | МЗБ 143А | |||
Кран-балка Q=2т | ||||
Опускатель колёсных пар с повышенного пути | ММ 217 | |||
Позиция окраски колёсных пар | ||||
Стенд контроля буксовых узлов с приспособлением для установки колесных пар с буксовыми узлами грузовых вагонов | ОМСД-02 | |||
Позиция монтажа буксовых узлов (повышенный рельсовый путь) | собств. изготов. | |||
Подъёмник колёсных пар на повышенный путь | ММ 216 | |||
Подъёмно-поворотный стол | ММ 021 | |||
Пост неразрушающего контроля № 3 — позиция комплексного автоматизированного ультразвукового контроля колёсных пар | ПЕЛЕНГ — АВТОМАТ | |||
Пост неразрушающего контроля № 3 | УД4-Т, ВД-213.1 | |||
Колёсотокарный станок | UBC-150 | |||
Позиция хранение эталонных образцов колесных пар | ||||
Пост неразрушающего контроля № 1 | УД2−102 МДУ-КПВ РУ 8617 | |||
Колёсотокарный станок | UBB-112 | |||
Комната бригадиров | ||||
Рельсовый путь на участок ремонта тележек | ||||
Позиция входного контроля | ||||
Моечная машина колёсных пар (старая) | собств. изготов. | |||
Установка индукционного нагрева | УИН 303−10/Т-001 | |||
Позиция монтажа буксового узла | ММ 160 | |||
Моечная машина колёсных пар | МЗБ 333 | |||
Роликовый приводной конвейер | ММ 263 | |||
Пульт управления стенда вибродиагностики | ОМСД-02 | |||
Позиция ремонта деталей буксового узла | MM-01.216-G5015G | |||
Позиция дефектации и подбора деталей буксового узла (позиция входного контроля) | ИКР-1 (УКБ-01, УПП-01, УПЛК-01, УПК-01) Или приборы БВ | |||
Позиция ручной очистки деталей буксового узла | ||||
Гайковёрт для откручивания гайки М110 | ММ 029 | |||
Подъёмно-поворотный стол | ММ 021 | |||
Установка сухой абразивной очистки | САО-3 | |||
Таблица 2 — Оборудование отделения ремонта роликовых подшипников
Поз. | Наименование | Обозначение | Коли-чество | |
Подъёмник подшипников | ММ 273 | |||
Накопитель неисправных подшипников | собств. изготов. | |||
Верстак двухтумбовый для разборки и осмотра подшипников (позиция входного контроля подшипников) | ММ-01.216-G5015G | |||
Шкаф для хранения инструмента, средств измерения и расходных материалов (наждачная бумага, масло) | ММ-03.124-G5015G | |||
Верстак двухтумбовый (позиция ремонта подшипников) | ММ-01.216-G5015G | |||
Приспособление для зачистки торцов роликов | собств. изготов. | |||
Приспособление для зачистки цилиндрических поверхностей роликов | собств. изготов. | |||
Машина для мойки роликов ультразвуковая | СТ 100 | |||
Верстак двухтумбовый (позиция накопления подшипников прошедших дефектоскопию) | ММ-01.216-G5015G | |||
Автомат для зачистки внутренних колец | АЗВК-1 | |||
Автомат для зачистки рабочей поверхности упорного кольца | АЗУК-1 | |||
Автомат для зачистки рабочей поверхности наружного кольца | АЗНК-1 | |||
Машина для мойки колец ультразвуковая | УМП 250 | |||
Накопитель колец подшипника, прошедших ультразвуковую очистку | собств. изготов. | |||
Автоматизированный вихретоковый дефектоскоп | ВД-211.5 | |||
Автоматизированная установка для подбора роликов | УПР-01 | |||
Установка для магнитного контроля колец подшипников | УМДП-01 | |||
Накопитель исправных роликов, подобранных по группам | собств. изготов. | |||
Шкаф для исправных деталей подшипников | ММ-03.124-G5015G | |||
Шкаф для забракованных деталей (изолятор брака) | ММ-03.124-G5015G | |||
Лоток для транспортировки подшипников к УКПП-01 | собств. изготов. | |||
Измерительный блок УКПП-01 | УКПП-01 | |||
Автоматизированная установка для контроля параметров подшипников | УКПП-01 | |||
Автоматизированная установка сбора данных | УСД | |||
Стенд вибродиагностики подшипников | СВП-01В | |||
Верстак двухтумбовый для смазки исправных подшипников | ММ-01.216-G5015G | |||
Опускатель подшипников | ММ 273 | |||
Тележка инструментальная | MM-2 113Н | |||
1.6 Определение габаритных размеров участка К габаритным размерам участка относятся длина, ширина, высота и площадь. Площадь участка складывается из площадей демонтажного, ремонтного, комплектовочного и монтажного отделений. Площади этих отделений определяются из условия, что на одну ремонтируемую колесную пару в смену необходимо для демонтажного отделения 5 м2, а остальных -10 м2, поэтому площадь участка определим по формуле
Sу= (5+10+10+10) * Nyсм
S = 35*5= 175? 180 м Длина участка определяется по формуле:
L= S/B
L= 180/18 =10м Объем участка определяется по формуле:
V=SЧH
V = 180*10,8= 1944 м³
1.7 Определение численности работников с указанием специальности и квалификации Расчет численности основных производственных рабочих ведется исходя из программы депо и трудоемкости ремонтных работ. На основании задания на проектирование годовая программа ремонта колесных пар составляет: 8000 тыс. вагонов Явочная численность рабочих — это число рабочих, фактически явившихся на работу, определяется по формуле:
Rяв=(Nгу ЧNт)/(ФявЧКн)
где, Nгу — годовая программа ремонта вагонов;
Nт — трудоемкость работ в участке (отделении), чел/час Фяв — явочный фонд рабочего времени.
Кн — коэффициент выработки нормы, =1,14 — 1,20.
К — коэффициент замещения законно отсутствующий. К= 1,09 — 1,12
Rяв= 4800Ч4, 1 /1976Ч1, 1= 9 чел.
Списочная численность рабочих определяется по формуле:
Rсп= RявЧK
Rсп = 9Ч1,09 = 9,8? 10 чел.
Из этого количества работников рассчитаем, оперативно-производственный персонал и вспомогательных работников:
Количество вспомогательных (подсобных) рабочих определяется по формуле:
Rвсп= (6 — 8%)Rсп
Rвсп = 6%Ч6 = 0,6Ч1,6? 1 чел.
Таблица № 1.7 — Штатная ведомость
Наименование должности, профессии | Разряд | Количество человек на смену | Условия труда | ||
Руководители | |||||
Мастер | ; | Нормальные | |||
Продолжение таблицы 1.7.1 | |||||
Бригадир | ; | Нормальные | |||
Специалисты | |||||
Слесарь | Нормальные | ||||
Слесарь | |||||
Слесарь | |||||
слесарь | |||||
Рабочие | |||||
Уборщик тех. помещений | ; | Нормальные | |||
Всего: | ; | ; | ; | ||
2. Технологическая часть
2.1 Назначение особенностей конструкции и условия работы букс с роликовыми подшипниками Одной из главных деталей вагона является буксовый узел. От исправного состояния буксового узла в большей степени зависит безопасность движения поездов, являясь неподрессоренной частью вагона, буксовый узел испытывает в пути следования значительные статистические и динамические нагрузки, которые особенно велики при наличии на колесных парах ползунов, выщербин, «наваров», а так же при проходе вагона по стыкам и дефектам рельсов. При проходе кривых участков железнодорожного пути, буксы испытывают большие осевые нагрузки. Буксовый узел требует высокой квалификации в точность выполнения работ по ремонту деталей и монтажу.
В буксах пассажирских и грузовых вагонов применяются роликовые подшипники:
а) с короткими цилиндрическими роликами однорядные с однобортовым внутренним кольцом (рис. 2 а);
б) с короткими цилиндрическими роликами однорядные с безбортовым внутренним кольцом и плоским упорным кольцом (рис. 2 б).
Увеличение скоростей движения и осевых нагрузок требует постоянного повышения эксплуатационной надежности буксовых узлов. Повышение эксплуатационной надежности буксовых узлов ведется исследователями и конструкторами по следующим направлениям: повышение надежности и долговечности торцевого крепления подшипников; уменьшение динамических нагрузок, действующих на подшипники; контроль над состоянием подшипников перед монтажом, строгое соблюдение требований монтажа; контроль над состоянием букс в поездах.
2.2 Установление неисправностей буксового узла, и причины их возникновения в процессе эксплуатации Таблица № 2.1 — Допускаемые величины повреждения буксового узла
Наименование измерений и норм | Допускаемые размеры, мм | Примечание | ||
при новом изготовлении | при ремонте | |||
1. Корпус буксы | ||||
1. Диаметр внутренней цилиндрической части буксы из стального литья | 250+0,01 +0,015 | 250+0,2 +0,015 | Проверяют в двух взаимно перпендикулярных направлениях | |
2. Овальность внутренней цилиндрической части для букс из стального литья | 0,024 | 0,20 | Проверяют в двух взаимно перпендикулярных направлениях и в двух местах по длине корпуса | |
3 Конусообразность внутренней цилиндрической части буксы, мм | 0,024 | 0.1 | Проверяют по всей длине корпуса | |
4 Ширина корпуса буксы по направляющим | 328+3-2 | Не менее 328±2 | Проверяют при ремонте букс | |
5 Высота опорных поверхностей | 173±1 | 173+1-4 | ||
6 Ширина челюстного проема | 168+1-2 | 168+1-2 | ||
2. Роликовые подшипники | ||||
1. Радиальный зазор подшипников в свободном состоянии | 0,115−0,170 | 0,09−0,25 | Определяют как среднее арифметическое трех измерений при повороте наружного кольца на 120о вокруг оси. Минимальное значение одного из трех измерений допускается до 0,08 мм | |
2. Радиальный зазор непосредственно на шейке оси, менее, мм: | 0,04 | 0,04 | Измеряют непосредственно на шейке оси при ревизиях букс | |
3. Разность радиальных зазоров парных подшипников в свободном состоянии, мм | 0,02 или 0,01 | 0,02 или 0,01 | Определяют по результатам измерений радиальных зазоров 0,02 мм при измерении радиального зазора со своими внутренними кольцами; 0,01 мм при измерении с применением эталонного кольца | |
2. Зазор между торцевыми поверхностями внутренних колец, а также бортом внутреннего кольца заднего подшипника и лабиринтным кольцом, не более | 0,04 | 0,04 | Щуп толщиной не более 0,04 мм может войти в зазор между этими деталями на участке длиной 1/3 окружности | |
3. Натяг на посадку лабиринтного кольца | 0,08−0,15 | 0,02−0,15 | Определяют как разность диаметров предподступичной части оси и лабиринтного кольца | |
4. Натяг на посадку внутренних колец | 0,040−0,065 | 0,030−0,065 | Определяют как разность диаметров оси и внутренних колец подшипников | |
5. Количество смазки ЛЗ-ЦНИИ, закладываемое в буксу, кг | 0,9−1,0 | 0,8−0,9 | Можно дозировать мерной емкостью вместо взвешивания | |
2.3 Обоснование методов и способов устранения неисправностей Таблица 22- Методы и способы устранения неисправностей
Признаки неисправности буксового узла | Возможные неисправности | |
При встрече поезда с хода | ||
Наличие дыма, специфического запаха горелой смазки, пощелкивание | Разрушение подшипника | |
Движение юзом одной из колесных пар при отжатых колодках | Заклинивание разрушенного подшипника | |
Дребезжащий стук колеса о рельс, наличие на колесной паре нескольких ползунов | Разрушен подшипник, ролики периодически заклиниваются | |
Выброс искр со стороны лабиринтной части | Проворот внутреннего кольца или разрушение заднего подшипника | |
Корпус буксы грузовой тележки имеет наклон; боковая рама опирается на буксу одним краем | Проворот внутреннего кольца переднего подшипника | |
Перемещение буксы вместе с рамой тележки вдоль оси, смещение вдоль шейки боковой рамы тележки, черный цвет крышки в зимнее время, наличие на смотровой крышке вмятин, цвета побежалости. | Повреждение торцевого крепления подшипников на шейке. Оборваны болты М20 или излом стопорной планки, гайки М110 сошла с резьбы, разрушен подшипник. | |
Резкий стук рычажной передачи, вертикальные перемещения буксы | Разрушение сепаратора | |
Наличие искр между колесной парой и буксой, а так же между колесной парой и рамой тележки, слышен скрежет | Излом шейки | |
При осмотре буксового узла во время стоянки поезда | ||
Выброс смазки через лабиринтное уплотнение на детали тележки кузовов. Наличие в смазке металл. | Разрушение подшипника, обводнение смазки, поворот внутреннего кольца, заклинивание роликов | |
Повышенный нагрев корпуса буксы в сравнении с другими буксами | Излишнее количество смазки, начало разрушения буксы | |
Двойные удары или дребезжащие звуки при обстукивании смотровой крышки ниже её середины | Повреждение торцевого крепления подшипников | |
Наличие на смотровой крышке пробоин, выпуклостей, протертостей | Повреждение торцевого крепления подшипников | |
Задняя часть корпуса нагрета больше передней | Разрушение заднего подшипника или нет зазора между лабиринтной частью корпуса буксы и лабиринтным кольцом | |
Передняя часть корпуса буксы нагрета больше задней | Разрушен задний подшипник | |
Разность зазоров между корпусом буксы и лабиринтным кольцом в верхней и нижней частях буксы более 1 мм при измерении специальным шаблонами | Поворот внутреннего кольца на шейке оси | |
Смещение корпуса буксы относительно лабиринтного кольца более 1,4 мм | Повреждение торцевого крепления | |
Разработка отверстия в кронштейне для валика подвески башмака, отсутствие валика, срез шлинтонов его крепления, излом надбуксовой пружины, наличие ржавчины на пружинах буксового и центрального подвешивания пассажирской тележки | Разрушение одного или обоих подшипников | |
Демонтаж букс с роликовыми подшипниками типа 232 726 и 42 726 может осуществляться на механизированной или полуавтоматической поточных линиях или ручным способом в соответствии с технологическим процессом демонтажа и монтажа вагонных букс на роликовых подшипниках, разработанным применительно к местным условиям.
При демонтаже буксы не допускается сбрасывать ее с шейки оси. Категорически запрещается использовать любой ударный инструмент для удаления подшипников из корпуса. Подшипники из корпуса буксы необходимо удалять только при помощи специальных прессов или устройств.
При демонтаже букс работы с помощью стендов или ручным способом выполняются в следующем порядке:
а) отвернуть болты крепительной крышки, а затем снять крепительную крышку вместе со смотровой;
б) удалить смазку из крышки и передней части буксы;
в) отвернуть и снять болты стопорной планки или тарельчатой шайбы. Планку или шайбу снять;
г) отвернуть и снять торцевую гайку, а также упорное кольцо переднего подшипника;
д) снять корпус буксы вместе с блоками подшипников (наружное кольцо с сепаратором и роликами) с внутренних колец, насаженных на шейку оси;
е) при помощи пресса вынуть из корпуса буксы блоки подшипников;
ж) снять при необходимости внутренние кольца с шейки оси при помощи индукционного нагревателя, покачивая нагреватель относительно оси колесной пары. При ослаблении кольца нагреватель снять вместе с кольцом, предварительно отключив нагреватель, кольцо удалить из нагревателя. При снятии с шейки оси неисправного кольца переднего подшипника исправное кольцо заднего подшипника можно не снимать с шейки оси. Кольца нагревать до температуры 100°-120°C — это достигается примерно за тридцать пять — сорок пять секунд при напряжении в сети 220 В.
Категорически запрещается нагревать кольца более 1 мин.
Запрещается делать перерыв в питании нагревателя током до полного ослабления и снятия кольца, так как в этом случае происходит нагрев шейки оси. Если время для нагрева истекло (1 мин.), а кольцо с шейки снять не удалось, необходимо работу по съему кольца прекратить и возобновить ее после остывания внутреннего кольца подшипника и шейки оси до температуры окружающей среды. После этого снимать последовательно кольца переднего и заднего подшипников;
з) при необходимости снять лабиринтное кольцо с предподступичной части оси при помощи индукционного нагревателя;
и) операции, указанные в подпунктах «ж» и «з», производить в случае, если полная ревизия выполнялась со снятием внутренних колец.
Блоки подшипников поступают в отделение ремонта роликовых подшипников из демонтажного отделения через подъемник подшипников высотой 7100 мм. С подъемника блоки подшипников через лотки накопителя неисправных подшипников поступают на верстак разборки и осмотра подшипников для определения необходимого вида ремонта. В соответствии с указанием Зам ЦЛД Фетисова № 1343 от 10.10.04 г. при поступлении на участок новых буксовых подшипников в сборе и полиамидных сепараторов в отдельности производить 100% входной контроль. Входной контроль заключается в проверке качества упаковки, качества обработки колец, роликов, сепараторов, соответствия геометрии отверстий внутренних колец требованиям ТУ, радиальных и осевых зазоров, разности длин и диаметров роликов, наличия трещин и других видимых дефектов в кольцах, роликах и сепараторах. При монтаже буксовых узлов разрешается использование новых подшипников и полиамидных сепараторов, поступивших только через организации с наличием сертификата качества. Результаты входного контроля заносят в журнал учета результатов входного контроля. Данные об осмотре новых подшипников заносятся в журнал формы ВУ-91.
После проведения входного контроля блоки подшипников по лотку транспортируются на позицию неразрушающего контроля. Дефектоскопист проводит вихретоковый контроль роликов при помощи дефектоскопа ВД-211.5, магнитопорошковый контроль свободных колец подшипников, визуальный контроль полиамидных сепараторов, забракованные детали укладывает в изолятор брака, по мере заполнения изолятора брака сдает детали в металлолом. Забракованные внутренние и наружные кольца, сепараторы и ролики заменяют новыми или исправными бывшими в эксплуатации. Детали, устанавливаемые взамен забракованных, в обязательном порядке подвергаются неразрушающему контролю. Неразрушающий контроль деталей подшипников проводится в соответствии с главой 6 данного технологического процесса. Результаты контроля заносят в журнал установленной формы. Ответственность за проведение и оформление результатов неразрушающего контроля возлагается на дефектоскописта по магнитному и ультразвуковому контролю. Подшипники, признанные по результатам контроля годными, дефектоскопист транспортирует на верстак позиции накопления подшипников прошедших дефектоскопию.
Слесарь разбирает прошедший дефектоскопию блок подшипников на составляющие (наружное кольцо, комплект роликов и сепаратор), проводит визуальный входной контроль деталей, детали требующие шлифовки (ролики, кольца подшипников) направляет на позицию зачистки, оснащенную установками: автомат зачистки внутренних колец АЗВК-1, автомат зачистки наружных колец АЗНК-1, приспособлениями для зачистки торцов и цилиндрических поверхностей роликов. После проведения зачистки слесарь транспортирует ролики в ультразвуковую установку промывки роликов, кольца подшипников в установку мойки колец. Очищенные ролики слесарь транспортирует к автоматизированной установке подбора роликов УПР-01, комплекты роликов размещает в накопителе исправных роликов.
Забракованные при проведении дефектации и ремонта детали роликовых подшипников слесарь маркирует словом «Брак» или двумя перекрещенными полосами «Х», укладывает детали в изолятор брака, по мере заполнения изолятора брака сдает детали в металлолом.
В металлолом разрешается сдавать кольца и ролики, забракованные в соответствии с требованиями 3-ЦВРК, с составлением акта комиссией и утверждением акта главным инженером депо.
Слесарь собирает блок подшипников из деталей, признанных годными по результатам дефектоскопирования и дефектации, транспортирует блоки подшипников при помощи тележки на позицию автоматизированной установки контроля параметров подшипников УКПП-01 предназначенной для контроля осевого зазора подшипника и радиального зазора подшипника по роликам. Данные установка работает в комплекте с 4 другими установками (УКБ-01, УПП-01, УПК-01,УПЛК-01) измерительного комплекса ИКР-1, расположенными на позиции монтажа в отделении монтажа буксовых узлов и 2 установками (УПР-01,УСД) измерительного комплекса ИКР-1, расположенными в роликовом отделении. Установки связаны между собой линией электрической связи.
На подшипник проверенный на установке УКПП-01 и признанным годным, слесарь маркером наносит присвоенный служебный номер и устанавливает его на установку вибродиагностики подшипников СПВ-01 В. Блок подшипников признанный по результатам вибродиагностики годным к эксплуатации слесарь отправляет в накопитель исправных подшипников. При неисправности установки вибродиагностики подшипников СПВ-01 В допускается проводить вибродиагностику подшипников на стенде вибродиагностики буксовых узлов на базе системы ОМСД-02
Блок подшипников, забракованный по результатам испытаний на установке вибродиагностики или установке УКПП-01, слесарь транспортирует на позицию входного контроля, где производит его переукомплектование с последующим повторным испытанием на установках УКПП-01 и СПВ-01 В.
Отремонтированные блоки подшипников слесарь транспортирует при помощи тележки на верстак где проводит их смазку, смазанные блоки подшипников устанавливает на накопитель исправных подшипников. По требованию бригадира, проводящего монтаж буксовых узлов на колесные пары, слесарь транспортирует блоки подшипников при помощи опускателя подшипников ММ 273 на позицию монтажа буксовых узлов.
Корпуса букс, смотровые и крепительные крышки, лабиринтные кольца, гайки, стопорные планки, болты промываются в моечных машинах автоматического, конвейерного или камерного типа двумя моющими жидкостями при температуре не ниже 90 °C. Первая моющая жидкость содержит 2−5% каустической соды, а вторая -8−10% отработанной смазки ЛЗ-ЦНИИ от объема воды в ваннах. При отсутствии в моечной машине второй ванны допускается промывка деталей вручную перед производством монтажа.
После промывки колесных пар вместе с внутренними и лабиринтными кольцами непосредственно после выкатки колесных пар из моечной машины производить протирку колец обтирочным хлопчатобумажным материалом и покрытие их жидким маслом. Промывка деталей буксовых узлов и колесных пар допускается другими способами, согласованными с Департаментом вагонного хозяйства МПС РФ.
Осмотр, неразрушающий контроль и комплектовка подшипников Подшипники после промывки и просушки осматривать визуально с помощью лупы при рассеянном свете для определения их пригодности к дальнейшему использованию. Неисправные подшипники направить в ремонт. При выпадании отдельных роликов из гнезд сепаратора направлять их в ремонт для измерения диаметра и длины всех роликов. Сведения о каждом осмотренном подшипнике с указанием его состояния (в том числе и упорном кольце) занести в журнал осмотра формы ВУ-91 (Приложение 2), при этом в графу 4, кроме даты изготовления подшипника, заносят также и завод-изготовитель (16ГПЗ, 8ГПЗ и т. д). На основании данных этого журнала ежегодно составляют справку работы роликовых подшипников по соответствующей форме. Эти справки, обобщенные службой вагонного хозяйства или вагоноремонтными заводами, по итогам за год представляют в железнодорожные администрации.
У цилиндрических подшипников осматривают отдельно внутренние, наружные и упорные кольца, а также ролики и сепараторы.
Подшипники с заусенцами направляются в ремонт для их удаления.
Подшипники, имеющие на бортах наружных колец и торцах роликов задиры и повреждения типа «елочка», ремонтируют зачисткой.
Латунные сепараторы и ролики перед дефектоскопированием осматривают визуально.
Подшипники новые и бывшие в эксплуатации после промывки, просушки, остывания осмотра или ремонта комплектуются по радиальным и осевым зазорам, по диаметрам отверстии внутренних колец.
Измерения подшипников производить после выдержки их в комплектовочном отделении не менее 8 часов. При этом эталонные кольца и измерительные средства должны храниться в комплектовочном отделении. Эталонные кольца аттестуют не реже одного раза в год.
Новые подшипники дополнительно к указанному выше осмотру в соответствии с п. 2.6. ТУ 37 006 048−73 подвергаются входному контролю на их соответствие требованиям ГОСТ 520–92. Контроль заключается в проверке качества обработки колец, роликов и сепараторов; соответствия геометрии отверстий внутренних колец требованиям ТУ; радиальных и осевых зазоров, разности длин и диаметров роликов; наличия трещин и других видимых дефектов в кольцах роликах и сепараторах; качества упаковки.
Контрольной проверке подвергается один процент от полученной партии, но не менее трех и не более двадцати подшипников. Если отобранные подшипники не удовлетворяют требованиям, указанным выше то производится проверка удвоенного количества подшипников. При неудовлетворительных результатах повторной проверки всю партию возвращают заводу для обмена на годные.
На роликовые подшипники изготовленные с нарушением требований ГОСТ, ТУ и чертежей, составляют рекламационные акты; копии актов направлять в железнодорожные администрации.
Измерение радиальных зазоров Радиальные зазоры в свободном состоянии цилиндрических подшипников следует определять на приспособлении, как это показано на рис. 9. Для этой цели на приспособлении укрепляют эталонное внутреннее кольцо 2 с бортом. Для удобства установки подшипников к внутреннему кольцу устанавливают специальную конусную оправку 1.
Эталонное кольцо подбирается из имеющихся внутренних колец подшипников.
Радиальный зазор подшипника можно измерять с тем же внутренним кольцом, с которым блок подшипника будет устанавливаться на шейку оси. При этом зазор измеряется щупом в нижней части подшипника.
При установке двух цилиндрических подшипников после демонтажа со снятием и без снятия внутренних колец или установке новых подшипников допускается производить контроль значений и разности радиальных зазоров парных подшипников непосредственно на шейке оси. Тогда в графу 13 журнала формы ВУ-90 заносят радиальные зазоры, измеренные непосредственно на шейке оси.
Радиальный зазор непосредственно на шейке оси определяют щупом в нижней части подшипника или специальным приспособлением с индикатором часового типа. Допускается производить контроль разности радиальных зазоров непосредственно на шейке оси, кроме щупа и приспособления, и с помощью седлообразного приспособления (рис. 10). В этом случае седлообразное приспособление устанавливается на эталонное кольцо, по которому определяется радиальный зазор подшипника в свободном состоянии, и индикатор седлообразного приспособления настраивается на ноль. После настройки седлообразное приспособление поочередно устанавливается на внутренние кольца, насаженные на шейку оси, и фактическое отклонение стрелки индикатора со знаком «плюс» или «минус» записывается на диске цельнокатаного колеса. При установке блока подшипника в буксу в зависимости от того, куда отклонилась стрелка индикатора — в «плюс» или «минус» это отклонение удвоить и добавить (или отнять) от радиального зазора, написанного цветным карандашом на наружной или торцевой поверхности наружного кольца подшипника, измеренного в свободном состоянии на эталонном кольце. Например, радиальный зазор подшипника в свободном состоянии на эталонном кольце составляет 0,07 мм, а отклонение индикатора седлообразного приспособления при установке его на внутреннее кольцо на шейке оси составило «минус» 0 02 мм, тогда фактический зазор подшипника составит 0,11 мм (0,07+0 02×2). При использовании седлообразного приспособления для измерения радиальных зазоров ножку индикатора необходимо удлинить на 20 мм. Удлинитель изготавливают из стали марки СтЗсп.
Рисунок 1 — Приспособление для измерения осевого зазора
Приспособление для измерения осевого зазора между торцами роликов и бортами наружного кольца (1 — рычаг; 2 — плита; 3 — основание; 4 — стоика; 5 — стоика штатива; 6 — гайка;7 — индикатор; 8 — направляющий конус; 9 — прижимное кольцо; 10 — внутреннее кольцо измеряемого подшипника.)
Осевой зазор в подшипнике, как правило измеряют щупом, который вставляют между торцом одного из роликов и бортом наружного кольца после разборки блока подшипника. Измерения производят в трех местах при повороте наружного кольца вокруг оси. За осевой зазор принимают его минимальное значение. Осевой зазор в подшипнике можно определять в собранном виде на приборе или на приспособлении (при его наличии, рис 2.). Для этой цели на плиту прибора устанавливают бортовое внутреннее кольцо 10 (бортом вниз). На кольцо устанавливают блок измеряемого подшипника, а на его ролики — прижимное кольцо 9, закрепляемое гайкой 6.
При помощи рычага 1 поднимают и опускают наружное кольцо; штифт индикатора, упираемый в конец наружного кольца, определяет осевой зазор. В этом случае за осевой зазор в подшипнике принимают наименьшее значение из трех измерений при повороте наружного кольца на 120° вокруг оси.
Первый вид ремонта При первом виде ремонта подшипники ремонтируют без измерения роликов по диаметру и длине, при замене и расточке сепаратора, зачистке бортов колец, замене наружного или внутреннего колец, зачистке дорожек качения колец.
Слесарь осматривает отдельно полученные с позиций неразрушающего контроля наружное кольцо, ролики и сепаратор, упорное и внутреннее кольцо (в случае снятия внутренних колец с шейки оси). Ролики и кольца подшипников имеющие не браковочные дефекты, шлифует шлифовальной шкуркой № 6 на тканевой основе с маслом или притиркой пасты ГОИ.
После шлифовки ролики и кольца должны быть очищены в ультразвуковых моечных машинах. После очистки слесарь производит сборку блока подшипников.
В соответствии с телеграфным указанием МПС № 48 от 05.05.03. при монтаже буксовых узлов пассажирских колесных пар разрешается устанавливать в роликовые подшипники полиамидные сепараторы, изготовленных по чертежу. На сепараторах заводов в обязательном порядке должны стоять клейма предприятия изготовителя и год их изготовления. Запрещается устанавливать в роликовые подшипники пассажирских колесных пар полиамидные сепараторы, изготовленные по чертежу. При сборке подшипников необходимо следить за тем, чтобы маркировка на сепараторе была обращена в ту же сторону, должны быть обращены торцы роликов со следующим условным обозначением: «+» или маркировкой в виде цифр, или с меньшей по диаметру выточкой сферической формы. В собранном состоянии подшипник должен провертываться легко, без заедания и торможения. Не рекомендуется долго вращать его без смазки.
После сборки блок подшипников поступает на установку УКПП-01 измерительного комплекса ИКР-1 для контроля (измерений) осевого зазора подшипника и радиального зазора подшипника по роликам. Действительный радиальный зазор определяется на УПП. Выходной контроль подшипников на установке УКПП-01 проводит бригадир участка ремонта колесных пар. Для обеспечения нормальной работы установки предназначен настроечный подшипник с измеренным осевым и радиальным зазорами. Данные осевой и радиальный зазоры вводятся в качестве поправок. В качестве настроечного подшипника используется подшипник, у которого диаметры роликов отличаются друг от друга не более, чем на 1−2 мкм, а длины не более, чем на 3−5 мкм. Измеритель зазоров УКПП-01 бригадир вставляет в контролируемый подшипник, установленный на поворотном столе, таким образом, чтобы ручка измерителя зазоров находилась за стопорным стержнем.
Перед началом измерений при помощи клавиш бригадир вводит данные о производителе подшипника, о типе сепаратора подшипника и данные о виде ремонта. Выделяет красным цветом надпись «Измерение», а затем нажимает клавишу «Enter». Включает тумблер питания на измерителе и вставьте его в подшипник. На индикаторе измерителя появится сообщение «Измерение», а затем «Готов к работе». Нажать клавишу «Пробел». На экране появится сообщение и включится привод вращения измерителя. По истечении некоторого времени привод вращения подшипника выключится и на экране монитора появится сообщение о результатах измерения. На экране монитора может появиться надпись «Подшипник не годится» в случае если осевой зазор не соответствует требованиям 3-ЦВРК. Если была нажата клавиша «Пробел», то данные о подшипнике передаются на установку УПП-01. Введите номер подшипника при помощи клавиатуры и нажмите «Enter». На экране появится сообщение о присвоении подшипнику служебного номера. Бригадир маркером наносит на подшипник присвоенный служебный номер. В случаях неработоспособности установки УКПП-01 осевой зазор в подшипнике бригадир или слесарь измеряет при помощи набора пластинчатых щупов № 2 ГОСТ 882–75, который вставляет между торцом одного из роликов наружного кольца вокруг оси. За осевой зазор принимают наименьшее значение трех измерений.
Второй вид ремонта Ремонт подшипников с переборкой роликов (с измерением роликов по диаметру и длине) производят при замене роликов (независимо от количества сменяемых роликов), выпадении отдельных роликов из гнезд сепаратора вследствие повреждения чеканки, зачистке (шлифовке) образующих роликов и торцов роликов.
При ремонте на заводах производят магнитный и вихретоковый контроль колец и роликов с последующим размагничиванием. Аналогичный контроль производят и в депо по мере поступления дефектоскопных установок. Латунные сепараторы дефектоскопируют на установках ВД-11НФ и ВД-18НФ.
Рисунок 2 — Разборка блока цилиндрического подшипника Разборка блока цилиндрического подшипника а) выдвигание роликов; б) снятие наружного кольца; в) удаление роликов из гнезд сепараторов.
При втором виде ремонта подшипник полностью разбирают. Чтобы разобрать подшипники, у которых расчеканка сепараторов произведена по перемычкам и наружные кольца скомплектованы вместе с роликами, например, у подшипников 42 726 и 232 726, надо ролики выдвинуть из бортов наружного кольца внутрь подшипника (рис. 2 а) и, сняв наружное кольцо (рис. 2 б), вынуть ролики из гнезд сепараторов (рис. 2 в).
При выпадении отдельных роликов из гнезд сепаратора проверяют диаметр и длину всех роликов, и подшипник вновь собирают. При этом разность диаметров роликов в подшипнике должна быть не более 5 мкм, а разность длин роликов — не более 12 мкм.
После разборки все детали осматривают. Особое внимание обращают на состояние сепараторов — на наличие трещин в зоне перехода перемычек к основаниям. При необходимости ролики и кольца шлифуют. Полиамидные сепараторы подвергаются растяжению на специальных установках. У цилиндрических подшипников типа 42 726 и 232 726, не имеющих на торце роликов и сепаратора условного обозначения, необходимо наносить на одном из торцов сепаратора со стороны маркировки букву «Ж», а один из торцов роликов условно обозначать знаком «+», который ставят в лунке или в центре торца. Причем ролики, имеющие на торце лунку, маркируют механическим путем с помощью соответствующего приспособления. У роликов с плоскими торцами маркировку наносят с помощью кислоты, медного купороса или электрографом. Запрещается наносить знак «+» на рабочую часть торца ролика. Этот знак должен быть нанесен только в середине торца ролика.
Годные для комплектования подшипников ролики со скосами сортируют (измеряют) по диаметрам в трех сечениях — в середине и по краям цилиндрической части вблизи скосов на приборах В901 (408М) или РМ101 с измерительной головкой или двухмикронным миниметром.
Устанавливается следующий порядок сортировки роликов:
а) по среднему сечению одного из роликов, принятому за эталон для данной группы роликов, настраивают прибор на нулевое положение измерительной головки;
б) остальные ролики измеряют и сортируют на группы по среднему сечению в пределах 5 мкм.
При комплектовании подшипников ролики в одном подшипнике должны быть одной группы по диаметру. Затем ролики на том же приборе В901 проверяют по длине, при этом ролик располагают маркированным торцом непосредственно под измерительную ножку головки на расстоянии 3−3,5 мм от образующей, для чего на стойке прибора необходимо установить боковой фиксатор, определяющий положение ролика. Маркированные торцы — это торцы, имеющие обозначения знаком"+", или с меньшей по диаметру выточкой, или с выточкой сферической формы, или торцы роликов, имеющие засверловку диаметром 5 мм и глубиной 1 мм. Проворачивая ролик вокруг оси, определяют его максимальную длину.
Сепараторы, применяемые при ремонте подшипника, должны иметь гладкую поверхность без срезов, отколов, трещин и повреждения чеканки. Обточка сепараторов по наружному диаметру категорически запрещается. При комплектовании подшипников необходимо следить за тем, чтобы маркировка на сепараторе (товарный знак завода-изготовителя и условное обозначение года выпуска или буквы «Ж»), торцы роликов, имеющие различные отличительные признаки, были обращены в ту же сторону, что и маркировка на наружном кольце.
Контроль и учет отремонтированных подшипников Отремонтированные подшипники осматривают и проверяют по радиальному зазору: среднее арифметическое значение радиального зазора должно быть 0,09−0,20 мм. Разность крайних значений радиального зазора при трех измерениях щупом не должна превышать 20 мкм у цилиндрического подшипника.
На отремонтированные подшипники наносят следующую надпись: на наружном кольце подшипника после номера ставят букву Р1 или Р11 в зависимости от вида ремонта (месяц римскими цифрами и две последние цифры года) и условный номер вагоноремонтного предприятия, производившего ремонт.
Надпись на кольцах производят электрографом при разобранном подшипнике или кислотой в собранном подшипнике. Состав кислоты: висмут азотнокислый 5 г, никель азотнокислый 95 г, азотная кислота 370 см³, вода 630 см³. Через 3−5 мин. после нанесения надписи для нейтрализации кислоты место надписи протирают мыльной пеной или любым машинным маслом. Вагоноремонтное предприятие, производящее ремонт подшипников, учитывает их в журнале формы ВУ-93. Отремонтированные подшипники, которые после ремонта не сразу устанавливают в буксы колесных пар, подлежат консервации.
Периодичность и объем плановых технических осмотров ремонтов буксового узла.
Полную ревизию букс с роликовыми подшипниками производят при полном освидетельствовании колесных пар:
а) при деповском и текущем отцепочном ремонтах вагонов выкатываемым и подкатываемым колесным парам, проходившим последнее полное освидетельствование четыре и более лет для пассажирских и рефрижераторных вагонов и пять и более лет для грузовых вагонов, а также колесным парам, срок службы которых 15 лет и более, кроме колесных пар, ранее проходивших последнее полное освидетельствование не более 3-х месяцев;
Примечание. Разрешается производить обыкновенное освидетельствование колесным парам, срок службы которых 15 лет и старше, при условии дефектоскопирования осей.
б) при повреждении вагона от динамических ударов при падении груза;
в) через две обточки по предельному прокату или другим неисправностям поверхности катания колес грузовых вагонов и через обточку для колес пассажирских вагонов;
г) при каждой обточке колесных пар, работающих с редуктором, и колесных пар, выкаченных из-под шестиосных вагонов;
д) после схода вагона с рельсов у колесных пар сошедшей тележки;
е) при капитальном ремонте вагона;
ж) при всех видах планового ремонта подкатываемым колесным парам РУ-950 и РУ-1050 в соответствии с Инструктивным Указанием 3-ЦВРК;
з) при формировании и ремонте колесной пары со сменой элементов;
и) при неясности клейм и знаков последнего полного освидетельствования на торце шейки оси;
к) после удаления волосовин, плен, неметаллических включений и др.;
л) у поврежденных вагонов после крушения, аварии, маневровой работы;
м) при наличии на поверхности катания колес колесных пар:
— грузовых вагонов — неравномерного проката 2 мм и более, ползуна и навара 1 мм и более, разности диаметров колес на одной оси 3 мм и более;
— пассажирских вагонов — ползуна 1 мм и более, навара -0,5 мм и неравномерного проката 2 мм и более, а у колесных пар с приводом генераторов всех типов (кроме плоскоременных) — неравномерного проката 1 мм и более;
н) при отсутствии бирки или неясности клейм на ней, обнаруженных при ремонте или подкатке колесной пары;
о) при сварочных работах на вагоне или тележке без соблюдения требований п. 1.7.;
п) при недопустимом нагреве буксы или повреждении буксового узла, требующего демонтажа букс, а также отказе в работе привода редуктора от торца шейки оси, требующего его демонтажа;
р) при обнаружении в буксе пассажирского вагона редукторного масла. При неисправности одной буксы обязательно производить полную ревизию второй буксы колесной пары.
Полную ревизию букс с роликовыми подшипниками производят при полном освидетельствовании колесных пар.
Полную ревизию букс производят под непосредственным руководством и контролем мастера или бригадира, имеющих удостоверение о сдаче испытаний на право полного освидетельствования колесных пар и полной ревизии букс.
При полной ревизии букс производят:
а) демонтаж букс с роликовыми подшипниками со снятием внутренних и лабиринтных колец в соответствии с действующими нормативно-техническими документами (ТУ ОАО «РЖД» № 3/148 от 01.11.05 г.).
б) промывка, осмотр, проверка и дефектоскопирование деталей роликовых подшипников, других деталей буксового узла и колесных пар;
в) ремонт деталей буксового узла и колесных пар;
г) измерение радиальных и осевых зазоров, посадочных отверстий внутренних колец при их установке, посадочных поверхностей корпусов букс;
д) монтаж букс.
После полной ревизии и монтажа букс на нее устанавливают бирку, на которой выбивают:
— индивидуальный номер колесной пары, который включает в себя условный номер предприятия-изготовителя черновой оси, порядковый номер черновой оси и год изготовления черновой оси;
— дату полного освидетельствования (месяц и две последние цифры года);
— условный номер, присвоенный пункту, производившему освидетельствование колесной пары и монтаж букс;
— код Государства-собственника колесной пары (определяется по клейму, нанесенному на боковой поверхности ободьев с наружной стороны колес) У колесных пар с торцевым креплением подшипников тарельчатой шайбой и болтами М20 при новом формировании, ремонте со сменой элементов и полном освидетельствовании колесных пар, кроме маркировки на бирке, на стопорной шайбе правой шейки оси выбивают номер оси, знак формирования, условный номер предприятия, сформировавшего или производившего ремонт со сменой элементов, и дату (месяц и две последние цифры года) производства этих работ.
На стопорной шайбе левой шейки оси выбивают дату последнего полного освидетельствования колесной пары и условный номер предприятия, производившего последнее полное освидетельствование колесной пары и полную ревизию букс При этом месяц на стопорной шайбе выбивают клеймами с арабскими цифрами вместо римских Данные полной ревизии букс записывают в журнал формы ВУ-90.
Промежуточную ревизию производят:
а) при обточке колесных пар без демонтажа букс;
б) при обыкновенном освидетельствовании колесных пар;
в) при единовременной технической ревизии пассажирских вагонов;
г) в качестве профилактической меры по отдельным указаниям (профилактическая ревизия).
Ревизию осуществляет слесарь, имеющий квалификацию не ниже 4-го разряда и соответствующее удостоверение.
Перед промежуточной ревизией у выкаченных колесных пар буксы проворачивают для определения неисправностей (раковин и др.). При вращении буксы с толчками и ненормальным шумом производят полную ревизию.
При промежуточной ревизии снимают крышку. Места прилегания крышки предварительно очищают от грязи и протирают. Снятую крышку укладывают в закрываемый ящик внутренней стороной вверх. Изъятую из передней части буксы смазку использовать запрещается, её заменяют свежей смазкой. При этом необходимо соблюдать условия, исключающие попадание в буксу и крышку различных загрязнений. Загрязнение смазки определяют анализом по методу Московской ж.д. или другим методом, согласованным с ОАО «РЖД», или визуально после растирания небольшой порции смазки на тыльной стороне руки или суконном материале, или зеркале, или другим способом. Букса с загрязненной и обводненной смазкой (стальные, латунные включения, механические и другие примеси) подлежит полной ревизии. При хорошем состоянии смазки (потемнение смазки не является браковочным признаком) производят дальнейший осмотр. Прежде всего, проверяют состояние переднего подшипника. При обнаружении масла от редукторно-карданного привода, излома или износа сепаратора, приставного упорного кольца или других дефектов буксу подвергают полной ревизии.
У букс при торцевом креплении гайкой независимо от состояния крепления снимают стопорную планку, торцевую гайку и упорное кольцо. Стопорные планки и упорные кольца подвергают магнитопорошковому контролю согласно РД 32.159−2000. После неразрушающего контроля на стопорные планки и упорные кольца (на наружную часть кольца неударным способом) наносится клеймо предприятия и дата проведения ревизии. Производят визуальный осмотр резьбы шейки оси и гайки. При исправном состоянии резьбы производят затяжку гайки с последующей установкой стопорной планки. При исправном состоянии резьбы и гайки (необходимо 100% применение гаек с кольцевой выточкой) производят постановку гайки с применением клея герметика «Стопор».
При торцевом креплении тарельчатой шайбой болты М20 освобождают от стопорения и динамометрическим ключом проверяют их затяжку (вращением по часовой стрелке). При наличии хотя бы одного из болтов с крутящим моментом менее 5 кгс/м все болты вывертывают и проверяют визуально состояние резьбы отверстий в торце оси и болтов крепления, а также состояния места перехода стержня болта к головке. При обнаружении задиров в месте перехода стержня болта к головке радиусом менее 0,8 мм и без подголовника или других повреждений болты к дальнейшей эксплуатации в торцевом креплении не допускаются. При изломе головки или стержня болта оставшуюся часть болта вывертывают из оси без повреждения резьбы резьбового отверстия. Поврежденные болты заменяются. При обнаружении срыва более трех ниток резьбы в резьбовых отверстиях оси или затруднений при завертывании болтов крепления допускается резьбовые отверстия исправлять метчиком. При повреждении более шести первых ниток резьбы в резьбовых отверстиях оси колесная пара не допускается к дальнейшей эксплуатации до специального указания. Болты, имеющие затяжку крутящим моментом более 5 кгс/м, подтягивают с усилием 23−25 кгс/м. Затяжка болтов должна быть равномерной. Для этого завинчивание трех болтов производят дважды по периметру, а четырех — по схеме 1−2-3−4-3−4-2−1 с последующим стопорением.
При обточке поверхности катания колес взамен снятой смотровой или крепительной крышки устанавливают специальную временную крышку с отверстием для прохода центра станка.
После обточки колесной пары снимают временную крышку, проверяют состояние смазки, надежность крепления торцевой гайки в соответствии с требованиями п. 9.4. Торцевые гайки снимают и осматривают состояние резьбы шейки оси и гайки. Колесные пары и гайки с поврежденной резьбой к дальнейшей эксплуатации не допускают. При торцевом креплении тарельчатой шайбой и болтами М 20 производят проверку состояния такого крепления после освобождения болтов от стопорения, осмотр резьбовых отверстий в оси и болтов, а также последующую их затяжку.
После обточки с промежуточной ревизией под правый верхний болт М 20 крепительной крышки устанавливают бирку, на которой выбивают 01 или 02, условный номер, присвоенный ремонтному предприятию, производившему обточку, и дату.
Затем смотровую или крепительную крышку устанавливают и закрепляют болтами, под которые устанавливают пружинные шайбы. Между крышками ставят резиновую прокладку, новую или бывшую в употреблении, но исправную. Между фланцевой поверхностью крепительной крышки и корпусом буксы устанавливают резиновое кольцо, а свободное пространство заполняют смазкой ЛЗ-ЦНИИ ГОСТ 19 791 или ЛЗ-ЦНИИ (у) по ТУ 0254 -307−148 820−95.
При промежуточной ревизии в случае необходимости в буксу добавляют свежую (не бывшую в употреблении) смазку до объема 0,2 кг ЛЗ-ЦНИИ, которую укладывают валиком на видимую часть переднего подшипника, уплотняя ее пальцами так, чтобы смазка смогла проникнуть между сепаратором и бортом наружного кольца. Затем устанавливают смотровую или крепительную крышку.
О проведенной промежуточной ревизии букс в журнале формы ВУ-92 делают соответствующие записи, при этом необходимо в графе 4 на каждую колесную пару, подвергавшуюся промежуточной ревизии букс, дополнительно к номеру колесной пары указывать тип оси. В графе 5 фиксировать случаи ослабления гайки или болтов М20 в торцевом креплении тарельчатой шайбой. Сведения о количествах случаев обнаруженных ослаблений гаек или болтов М20 и количествах осмотренных осей типа РУI или РУIШ ежеквартально сообщать в железнодорожные администрации Подшипники после демонтажа промываются в моечной машине мыльной эмульсией, подогретой паром до (90−95) °C, и просушиваются подогретым воздухом, пропускаемым через змеевик, размещенный внутри ванны моечной машины. Новые роликовые подшипники и подшипники, покрытые консервационной смазкой, также промываются в автоматической машине. В том случае, если осмотр подшипников будет производиться не ранее, чем через сутки после промывки, их необходимо смазывать жидким маслом.
Испытание и выдачу удостоверения на право полного освидетельствования и ревизии букс осуществляют в соответствии с п. 3.1.4 «Инструкции по осмотру, освидетельствованию, ремонту и формированию вагонных колесных пар». Лица, выполняющие монтаж, промежуточную ревизию, осмотр и ремонт подшипников, должны сдать также испытания и получить удостоверение на право полной и промежуточной ревизии букс, осмотра и ремонта подшипников.
Выдачу удостоверения на право полной и промежуточной ревизии букс, осмотр и ремонт подшипников осуществляет комиссия в составе главного инженера вагонного депо или завода по ремонту подвижного состава и производства запасных частей (председатель) и начальника или мастера колесного или роликового цеха, имеющих удостоверение на право полного освидетельствования колесных пар и ревизии букс.
Рисунок 3 — Бирки а) для двух болтов; б) для одного болта; в) для промежуточной ревизии с обточкой месяц, год номер пункта, производившего полное освидетельствование колесной пары и монтаж букс.
1 — месяц, год, номер пункта, производившего полное освидетельствование колесной пары и монтаж букс; 2 — номер оси;
3 — знак «О», месяц, год и номер пункта, производившего обточку колесной пары без демонтажа букс.
При ревизии, выполняемой по подпунктам «в» и «г» и при удовлетворительном состоянии подшипника остукиванием контролируют болты стопорной планки или тарельчатой шайбы. Ослабшие болты М12 подтягивают, неисправные заменяют. Неисправную проволоку болтов стопорной планки заменяют, под болты стопорной планки ставят пружинные шайбы. Надежность крепления торцевой гайки проверяют ударами слесарного молотка по оправке, упираемой в одну из граней коронки или в шлиц гайки. Проверку производят в обе стороны вращения гайки. При ослаблении гайки торцевого крепления колесную пару выкатывают и снимают гайку. Колесная пара и гайка с поврежденной резьбой к дальнейшей эксплуатации не допускаются. У букс с подшипниками при торцевом креплении гайкой независимо от состояния крепления снимают стопорную планку для дефектоскопирования и клеймения, торцевую гайку и упорное кольцо — для визуального осмотра резьбы шейки оси и гайки. Колесные пары или гайки с поврежденной резьбой к дальнейшей эксплуатации не допускаются. При исправном состоянии резьбы производят затяжку гайки с последующей установкой стопорной планки в соответствии с требованиями настоящих Инструктивных указаний.
Для предотвращения выпадения роликов из гнезд сепараторов промывку роликовых подшипников в моечных машинах производить со специальными втулками или другими приспособлениями. Допускается промывка вместе с внутренними кольцами.
Примечание. На посадочных поверхностях наружных колец подшипников могут оставаться темные пятна от коррозии.
Моющая жидкость (мыльная эмульсия) автоматической машины должна содержать (8−10)% отработанной смазки ЛЗ-ЦНИИ.
Для промывки новых подшипников допускается применять моющую жидкость с содержанием 1,0−1,5% смазки ЛЗ-ЦНИИ.
Для обмывки подшипников после использования смазки Буксол ТУ 0254−107−1 124 328 необходимо использовать моющее средство РИК или ЦИТОМ.
Корпуса букс, смотровые и крепительные крышки, лабиринтные кольца, гайки, стопорные планки, болты промываются в моечных машинах двумя моющими жидкостями при температуре не ниже 90 °C. Первая моющая жидкость содержит (2−5)% каустической соды, а вторая (8−10)% отработанной смазки ЛЗ-ЦНИИ от объема воды в ваннах. При отсутствии в моечной машине второй ванны допускается промывка деталей вручную перед производством монтажа.
Примечание. Корпуса букс нового изготовления и другие детали буксового узла (кроме роликовых подшипников) вместо промывки можно обдувать сжатым воздухом с последующей тщательной протиркой до полного удаления стружки и других частиц.
После промывки колесных пар вместе с внутренними и лабиринтными кольцами непосредственно после выкатки колесных пар из моечной машины производится протирка колец обтирочным хлопчатобумажным материалом и покрытие их жидким маслом.
Лабиринтные кольца после зачистки и промывки протирают и проверяют. На посадочных поверхностях и в лабиринте не допускаются трещины, вмятины, забоины, заусенцы и другие неисправности. При ремонте колесных пар со снятием лабиринтных колец необходимо производить обточку лабиринтного кольца с диаметра 183 до 182 мм.
Крепительные и смотровые крышки после зачистки и промывки осматривают. Соединенные между собой крепительные и смотровые крышки разъединяют для замены уплотнения и вновь собирают. На крышках не допускаются трещины, вмятины, забоины, задиры, заусеницы, изгибы, перекосы и другие дефекты. Смотровые крышки, деформированные по привалочной поверхности, выравнивают.
Торцевые типовые гайки с переходным радиусом 6−8 мм, гайки с проточкой, гайки с проточкой и выточкой, а также стопорные планки, шайбы и болты после промывки должны быть осмотрены. На них не допускаются забоины, заусенцы и другие неисправности, влияющие на работу узла. Категорически запрещается растачивать резьбу гайки М110. Стопорные планки подлежат обязательному магнитопорошковому контролю с постановкой клейм предприятия и даты производство неразрушающего контроля.
При полных ревизиях букс на торцевых гайках, не имеющих кольцевых проточек, производят кольцевую проточку в соответствии с п. 5.2.9.4. 3-ЦВРК.
Необходимо тщательно осматривать тарельчатые шайбы, шайбы стопорные и болты торцевого крепления подшипников, выполненного при помощи тарельчатых шайб для крепления четырьмя болтами, тарельчатых шайб для крепления тремя болтами, соответствующих шайб стопорных и четырех или трех болтов М20.
Болты М 12×35 для крепления стопорной планки и смотровой крышки, а также болты М 20×60 для крепления крепительной крышки и болты М20×60.4.8 для крепления тарельчатой шайбы изготавливают по ГОСТ 7798–70 и техническим требованиям по ГОСТ 1759–70. Головки болтов М20×60.4.8 изготавливают по варианту с ложной шайбой на опорной ее поверхности. На торце головок болтов ставят размером 6×2,25 мм две последние цифры года монтажа букс, когда болты были впервые использованы при монтаже торцевого крепления. Резьба болтов должна быть изготовлена методом накатки. При несоответствии требованиям стандартов болты необходимо браковать.
2.4 Разработка мероприятий по охране труда и технике безопасности Настоящие требования безопасности труда разработаны на основании «Отраслевых правил по охране труда в пассажирском хозяйстве Федерального железнодорожного транспорта» ПОТ РО — 13 153-ЦЛ-923−02, «Сборника нормативных документов по управлению охраной труда на железнодорожном транспорте» ЦЭУ/4826, «Санитарных правил по организации пассажирских перевозок на железнодорожном транспорте» СП 2.5.1198−03.
Требования безопасности труда распространяются на работников Пассажирского вагонного депо Хабаровск, занятых на ремонте пассажирских вагонов. Персонал, выполняющий ремонт вагонов, должен быть обучен и испытан в знаниях техники безопасности в соответствии с основными положениями «Организации обучения и проверки знаний по охране труда работников железнодорожного транспорта» ЦСР-325 от 04.05.1995 г.
Уровни шума и вибрации на рабочих местах не должны превышать значений ГОСТ 12.1.003, ГОСТ 12.1.012, СН 2.2.4/21.8.562, СН 2.2.4/2.1.8.566 и «Санитарных правил», регламентирующих физические и химические факторы среды на подвижном составе ж.д. транспорта на уровнях, обеспечивающих безопасность работающих и пассажиров.
Освещенность рабочих мест в помещениях должна соответствовать требованиям СНиП 23−05, «Нормам искусственного освещения объектов ж.д. транспорта» РД 32.15, ОСТ 32.120 и «Отраслевым нормам естественного и совмещенного освещения производственных предприятий ж.д. транспорта».
Производственные, вспомогательные и складские помещения должны быть оборудованы отоплением и вентиляцией в соответствии с ГОСТ 12.1.005 и СНиП 2.04.05.
При ремонте вагонов должны выполняться требования «Правил пожарной безопасности на железнодорожном транспорте» ЦУО/112, «Ведомственных норм пожарной безопасности. Вагоны пассажирские. Требования пожарной безопасности» ВНПБ-03, «Инструкции по обеспечению пожарной безопасности в вагонах пассажирских поездов» ЦЛ/ЦУО-448, «Правил пожарной безопасности при проведении сварочных и других огневых работ на объектах народного хозяйства» ГУПО МВД СССР, «Правил пожарной безопасности в РФ» ППБ-01−93, «Межотраслевых правил по охране труда (правила безопасности) при эксплуатации электроустановок» ПОТРМ-016−2001 РД 153−34.0−03.150−00, «Правил технической эксплуатации электроустановок потребителей».
Средства пожарной сигнализации и средства пожаротушения для различных помещений должны соответствовать определенной категории и требованиям «Норм оснащения объектов и подвижного состава федерального железнодорожного транспорта первичными средствами пожаротушения» № Г-822у.
Использование пожарного оборудования и инвентаря для хозяйственных нужд не допускается.
Погрузочно-разгрузочные работы должны осуществляться в соответствии с требованиями ГОСТ 12.3.009, ГОСТ 12.3.020. В местах производства погрузочно-разгрузочных работ грузоподъемными кранами должны быть вывешены графические схемы способов обвязки и зацепки узлов, деталей и других грузов. Места производства погрузочно-разгрузочных работ должны иметь освещенность не менее 10 л.к.
При переноске тяжестей допускаемая масса поднимаемого и перемещаемого груза в течении рабочей смены не должна превышать для мужчин — 15 кг, для женщин — 7 кг, а при чередовании с другой работой (до 2-х раз в час) для мужчин — 30 кг, для женщин — 10 кг.
Все работники, осуществляющие ремонт вагонов, должны быть обеспечены спецодеждой и защитными средствами в соответствии с «Типовыми нормами бесплатной выдачи сертифицированных средств индивидуальной защиты», утвержденными распоряжением № 1248р от 16.06.2009 г. Коллективные и индивидуальные средства защиты работающих должны отвечать требованиям ГОСТ 12.4.011−89.
Требования безопасности при подготовке вагонов к ремонту, вводе их в депо и постановке на позицию ремонта Вагоны, подаваемые в депо для ремонта, должны быть тщательно очищены от снега, льда, грязи, мусора, промыты и продезинфицированы. С вагонов должно быть снято съемное оборудование, инвентарь.
Расстановка вагонов в вагоносборочном участке должна производиться с соблюдением следующих требований:
1. Расстояние между торцевой стеной вагоносборочного участка и автосцепками крайних вагонов должно быть не менее 3 м;
2. Расстояние между автосцепками вагонов, ремонтируемых без выкатки тележек, должно быть не менее 1 м;
3. При ремонте вагонов с выкаткой тележек при стационарном методе ремонта расстояние между вагонами устанавливается в зависимости от длины тележек и применительно к местным условиям, чтобы проходы с каждой стороны выкаченной тележки были не менее 1 м;
Маневровая работа на деповских железнодорожных путях должна производиться под руководством диспетчера депо.
Подача неисправных вагонов в депо и выдача отремонтированных вагонов должны производиться по заявке старшего мастера вагоносборочного участка под контролем диспетчера депо.
После выполнения маневровых работ ж.д. пути, ведущие в вагоносборочный цех, должны быть ограждены. Стрелки №№ 320, 324 должны находиться в положении, исключающем въезд маневрового локомотива на позиции, где осуществляются ремонтные работы и закрываться на ключ.
При обнаружении в передвигаемом составе вагонов неисправностей в ходовых частях, создающих угрозу схода вагонов с рельс, переносов кузова или излома его деталей, неисправности автосцепного устройства и тормозного оборудования, составитель поездов должен доложить об этом диспетчеру депо. Диспетчер депо должен на месте определить безопасный способ передвижения вагонов на ремонтные позиции. Такие вагоны должны передвигаться локомотивом одиночно при отсутствии людей на соседних междупутьях, со скоростью не более 3 км/ час по команде составителя поездов и в присутствии диспетчера депо.
Все работы на вагонах во время их перемещения должны быть прекращены, а работники удалены на безопасное расстояние.
Требования безопасности при подъеме и опускании вагонов Подъем вагона разрешается при условии, что нагрузка от вагона на грузоподъемные механизмы не превышают их грузоподъемности. Производство ремонтных работ на крыше вагона, а также нахождение людей под вагоном и в вагоне при его подъеме и опускании не допускается.
На поднятом домкратами вагоне производство работ, вызывающих раскачивание вагона или передачу ударных нагрузок на домкраты, не разрешается.
Подъем и опускание вагона двумя или четырьмя электродомкратами должны производиться одновременно под руководством мастера (или бригадира) участка ремонта тележек. Опережение подъема и опускания одного домкрата по отношению к другим — не допускается.
При случайной остановке одного из домкратов или при перерыве подачи электроэнергии во время подъема или опускании вагона все работы необходимо прекратить, выключить все домкраты и рубильник на распределительном щите.
При подъеме вагона домкрат должен занимать вертикальное положение. Конечный выход винта электродомкрата не должен превышать ¾ его смены. Домкраты должны быть оборудованы автоматическими ограничителями подъема (выключателями-концевиками).
Перед подъемом вагона на опорную поверхность домкрата должна быть положена деревянная прокладка, не имеющая трещин, размером 200×250мм и толщиной не менее 20 мм, изготовленная из твердых пород дерева.
Не допускается выполнять какие-либо работы по ремонту вагонов во время их подъема или опускания. Поднимать вагон неисправным домкратом запрещается. Выкатку (подкатку) тележек производить только после окончания подъема вагона и выключения электрических домкратов под руководством бригадира (мастера) участка.
Приведение домкратов в движение разрешается лишь после команды мастера или бригадира участка ремонта тележек и под его личным руководством. После подъемки вагона два человека осуществляют выкатку тележки из-под вагона, толкая от себя, сопровождая до полной остановки. После установки тележек на путях между вагонами их следует с двух сторон закрепить деревянными клиньями.
Домкраты должны быть заземлены. На хоботах должна быть прокладка. Выкатку (подкатку) тележек производить только после окончания подъема вагона и выключения электрических домкратов.
При поднятом вагоне расстояние между наиболее выступающими частями оборудования рамы и тележкой должно обеспечивать свободную выкатку (подкатку) тележки.
При выкатке (подкатке) тележки работникам запрещается находиться на тележке и на пути ее движения, а также размещать детали с вагона в непосредственной близости от передвигаемой тележки.
Основные требования пожарной безопасности объекта в том числе к содержанию территории, зданий и сооружений, электроустановок, к системам отопления, вентиляции, технологическому оборудованию противопожарному водоснабжению, пожарной техники и средствами связи, изложены в типовых правилах пожарной безопасности для промышленных предприятий и в правилах по пожарной безопасности на железнодорожном транспорте.
В складских помещениях и на территории должны вывешиваться запрещающие и указательные знаки: места нахождения пожарных постов, пожарных кранов, гидрантов, огнетушителей, пунктов извещения о пожаре, места курения и т. д.
В обеспечении пожарной безопасности особое место занимает противопожарная подготовка инженерно-технических работников, служащих и рабочих, которая включает первичный и вторичный пожарные инструктажи, а также занятия по программе пожарно-технического минимума.
Под средствами защиты от пожара понимается огнетушащие составы, пожарные автомобили, пожарные поезда, пожарно-технические сооружения. По назначению средства тушения подразделяются на огнетушащие средства (вещества), прекращающие горение, средства доставки огнетушащих средств, их получения, а также выполнения других работ на пожаре. Углекислый газ чаще всего применяется при тушении легковоспламеняющихся и горючих жидкостей в емкостях, горящего электрооборудования и двигателей внутреннего сгорания, при тушении пожаров в местах, где применять воду или пену нецелесообразно.
К изолирующим и разбавляющим веществам относят химическую и воздушно-механическую пену: азот, порошки общего и специального назначения. Химическую пену применяют для тушения легковоспламеняющихся и горючих жидкостей. Наиболее эффективна воздушно-механическая пена, обладающая хорошим теплоотражающим эффектом, также хорошо используются огнетушители (ОХП-10; ОУ; ОУ-2А; ОУ-2ММ; ОУ-5; ОУ-5ММ; ОУ-8), стационарные (ОСУ-5А; ОСУ — 5), порошковые ОП-10, комбинированные ОХВП-10 и ОК-100. При возникновении пожара необходимо сообщить в пожарную охрану и руководителю работ. Тушить горящие предметы, находящиеся на расстоянии менее двух метров от контактной сети, разрешается только углекислотными, аэрозольными или порошковыми огнетушителями. Тушение горящих предметов, расположенных на расстоянии более семи метров от контактного провода, находящегося под напряжением может быть допущено без снятия напряжения. При этом необходимо следить, чтобы струя воды или пены не касалась контактной сети и других частей, находящихся под напряжением. При тушении пожара струю пены направлять в сторону от людей. При возгорании электроприборов применять только углекислотные или порошковые огнетушители.
Требования техники безопасности при выполнении технологического процесса устанавливаются законом об охране труда РФ и местными инструкциями. Перед началом работы работник должен проверить состояние инструмента находящегося на рабочем месте или получаемого из инструментальной кладовой. Инструмент и приспособления должны отвечать требованиям стандартов и технических условий. Молоток должен иметь:
— ровную, не сбитую, без заусенцев, слегка выпуклую поверхность байка;
— овальное отверстие для ручки с небольшим конусом наружу;
— ручку овального сечения из дерева, гладкую без сучков и трещин, конусную с уширением к свободному концу.
Места обработки деталей зубилом или другим подобным инструментом ограждают щитками из сетки, а исполнители работ обеспечиваются защитными очками.
Напильники применяют только с исправными ручками с металлическими кольцами в местах их насадки. Гаечные ключи должны соответствовать указанным на них размерам и не иметь разошедшихся челюстей. Наращивать гаечные ключи другими ключами и трубами, а также применять прокладки между гайкой и ключом не допускается.
Абразивный инструмент, применяемый в заточных станках и ручных пневматических шлифовальных машинах типа ИП-2002 ТУ 22−166−30, должны эксплуатироваться и испытываться в соответствии с ГОСТ 12.3.028.
Запрещается пользоваться неиспытанными абразивными кругами. Для испытания абразивного инструмента в депо имеется специальный стенд находящийся в цехе оборудования. Верстаки, столы и стеллажи должны быть прочными, устойчивыми и иметь высоту, удобную для работы. Поверхность верстаков необходимо покрывать гладким материалом (листовой сталью).
Мастер и бригадиры должны постоянно, в течение рабочей смены контролировать исправность инструмента, а исполнители — перед началом работы.
Работа неисправным инструментом, неочищенным от грязи и масла и без защитных средств запрещается. Все производственное оборудование должно отвечать требованиям ГОСТ 12.1.003−83, ГОСТ 12.2.003−91, ГОСТ 12.2.022−80. Для обеспечения безопасных условий труда электродвигатели, пусковая аппаратура и все другие части оборудования, которые могут находиться под напряжением, надежно заземляют и перед началом работы проверяются работниками цеха.
Зубчатые и ременные передачи, а также другие вращающиеся части оборудования, расположенные в доступной зоне, должны быть ограждены. Конструкции предохранительных устройств на станках должны быть прочными и надежно закрепленными. Внутренние поверхности защитных ограждений окрашивают в ярко-красный цвет.
Стенды и механизированные приспособления для ремонта автосцепного оборудования, потребляющие при работе электрический ток, должны иметь надежное защитное заземление в соответствии с ГОСТ 12.1.030. Сопротивление заземления должно быть 40 Ом. Сопротивление изоляции стендов должно соответствовать требованиям ГОСТ 1516.1 и быть не менее 0.51 Ом.
Все провода должны прокладываться в металлических трубах или гибких металлорукавах, защищенных асбестовой тканью. Оборудование должно быть установлено на изолирующих фундаментах или основаниях, тщательно выровнено и закреплено.
Все люди, работающие с какой-либо машиной или механизмами должны быть совершеннолетними и иметь специальный допуск к работе, т. е. являться квалифицированными специалистами. Помимо этого каждый рабочий должен знать все нюансы своего дела во избежание издержек в работе, он несет полную ответственность за продукцию, получаемую в результате выполнения им своих трудовых обязанностей. На предприятии в целом, и на участке в частности ведется систематическая работа по воспитанию у каждого члена коллектива чувства высокой ответственности за личную безопасность, безопасность рядом работающих, за выполнение норм и правил охраны труда, соблюдение трудовой и производственной дисциплины.
В соответствии с законодательством, рабочим, если при выполнении своих трудовых обязанностей они подвергаются воздействию отрицательных производственных факторов, бесплатно выдают по установленным нормам спецодежду, спецобувь и другие средства индивидуальной защиты. Выдаваемые средства индивидуальной защиты должны соответствовать характеру и условиям их работы, обеспечивать безопасность труда. При проведении работ под движущимися машинами и механизмами в качестве средства индивидуальной защиты предусмотрена каска. При работе с пневмоинструментом обязательны очки и рукавицы. При проведении сварочно-наплавочных работ пользуются сварочными масками для защиты глаз.
С наступлением холодов предусмотрена выдача теплой спецодежды и обуви с последующим возвратом в летнее время года. Регулярно в соответствии со сроками проводят испытание и проверку исправности средств индивидуальной защиты с занесением результатов проверки в журнал.
Возрастание масштабов вызовов и угроз безопасности в мире посредством террористических актов. В том числе на объектах транспорта, является актуальной проблемой, и необходимость её всестороннего изучения не вызывает сомнения.
Вопрос терроризма на транспорте давно вышел за пределы границ отдельных государств и превратился в серьёзную общемировую проблему. Об этом говорит печальная статистика терактов на транспортных объектах, включая всем известные трагедии в Нью-Йорке, Вашингтоне, Мадриде, Токио, Москве, Бостоне и других городах мира. Специфика транспортного комплекса в плане уязвимости от террористических проявлений заключается в его большой протяженности, наличием большого количества объектов обеспечения перевозочной деятельности и транспортных средств. Учитывая такие характерные факторы для пассажирои грузоперевозок, как массовость, интенсивность движения, доступность посещения пассажиро-образующих объектов.
Принятый в феврале 2007 г. федеральный закон «О транспортной безопасности» № 16-ФЗ предусматривает создание системы обеспечения транспортной безопасности на основе определенного на государственном уровне единого подхода к оценке угроз, планированию и реализации мероприятий по обеспечению безопасности объектов транспортной инфраструктуры и транспортных средств.
Основные понятия и термины Транспортная безопасность — состояние защищенности объектов транспортной инфраструктуры и транспортных средств от актов незаконного вмешательства (п. 10. ст. 1 Федерального закона от 09.02.2007 г. № 16-ФЗ «О транспортной безопасности»).
Террористический акт — совершение взрыва, поджога или иных действий, устрашающих население и создающие опасность гибели человека, причинения значительного имущественного ущерба либо наступления иных тяжких последствий, в целях воздействия на принятие решения органами власти или международными организациями, а так же угроза совершения указанных действий в тех же целях (п. 3 ст. 3 Федерального закона от 06.03.2006 г. № 35-ФЗ «О противодействии терроризму»).
Обеспечение транспортной безопасности — реализация определяемой государством системы правовых, экономических, организационных и иных мер в сфере транспортного комплекса, соответствующих угрозам совершения актов незаконного вмешательства.
Оценка уязвимости объектов транспортной инфраструктуры и транспортных средств — определение степени защищенности объектов транспортной инфраструктуры и транспортных средств от угроз совершения актов незаконного вмешательства.
Перевозчик — юридическое лицо или индивидуальный предприниматель, принявшие на себя по договору перевозки транспортом общего пользования обязанность доставить пассажира, вверенный м отправителем груз. Багаж, грузобагаж из пункта отправления в пункт назначения, а так же выдать груз, багаж, грузобагаж управомоченному на его получение лицу (получателю).
Субъекты транспортной инфраструктуры — юридические и физические лица, являющиеся собственниками объектов транспортной инфраструктуры и транспортных средств или использующие их на ином законном основании.
Транспортные средства — воздушные суда, суда, используемые в целях торгового мореплавания или судоходства, железнодорожный подвижной состав, подвижной состав автомобильного и электрического городского наземного пассажирского транспорта в значениях, устанавливаемых транспортными кодексами и уставами.
Транспортный комплекс — объекты и субъекты транспортной инфраструктуры, транспортные средства.
Уровень безопасности — степень защищенности транспортного комплекса, соответствующая степени угрозы совершения акта незаконного вмешательства.
3. Экономическая часть
3.1 Эксплуатационные расходы Прямые расходы, связанные с производством и реализацией по вагонному хозяйству (статья 6004):
1) Расход на топливо для отопления здания определяется по формуле:
Тт= б ЧТоптЧgотЧ VуЧ (tв — tн) ЧКэкспЧКсутЧЦтЧ10-6, руб. (3.1)
где б — коэффициент, учитывающий вид топлива (б = 0,23);
Топт — число часов отопительного сезона (Топт = 3980 ч.);
gот — часовой расход тепла на м3 (gот = 0,8 Вт/м3Чч);
Vу — объем участка (Vу =720 м3);
tв, tн — внутренняя и наружная температуры воздуха (tв=180С; tн = -160С);
Кэксп — эксплуатационный коэффициент (Кэксп= 1,25);
Ксут — коэффициент сменности (Ксут = 0,85);
Цт — цена 1 т топлива, руб. (мазут = 14 798,00 руб.).
Тт = 0,23Ч3980Ч0,8Ч720Ч (18 — (-16)) Ч1,25Ч0,85Ч14 798Ч10-6 = =281 867 руб.
2)Расходы электрической энергии на горячее водоснабжение определяется по формуле:
=, руб. (3.2)
где — расход тепла на сетку душа (= 1500 Вт/чел);
— количество сеток душа (= = = 0,3);
— расход тепла на одного рабочего, пользующегося столовой (= 1800 Вт/чел);
— расход тепла на одного рабочего, связанный с потреблением горячей воды в течение рабочего дня (= 2250Вт/чел);
— рабочих дней в году (= 247 дней);
— цена 1 кВт/ч электроэнергии, руб.
= = 28 182,7 руб.
3) Расходы на электрическую энергию для освещения определяется по формуле:
=, руб. (3.3)
где — освещаемая площадь участка, ;
— годовое количество часов осветительной нагрузки (для депо — 2250 ч.);
— коэффициент спроса (= 0,8);
— коэффициент, учитывающий экономию электроэнергии за счет использования естественного освещения с 1.04 по 1.10 (= 0,85 — 0,9);
— цена 1 кВт электроэнергии, руб.;
— часовая норма расходов электроэнергии на (= 11 Вт/);
= =8981,3 руб.
4) Расходы на воду для бытовых нужд определяется по формуле:
=, руб. (3.4)
где, а — удельный расход воды на одного рабочего (а = 65л.);
= цена 1 воды, руб.
= =204 460,425руб
5) Расходы на воду для обмывки деталей (узлов) для участка определяется по формуле:
=, рубю (3.5)
Где — расход воды на обмывку 1 тележки- 0,07 м3/ч; на 1 колесную пару — 0,025 м3/ч
— коэффициент спроса воды (= 0,75);
1,1 — коэффициент, учитывающий утечку воды;
— цена 1 воды канализации, руб.
= = 1386,5 руб.
6)Отчисления на социальные нужды определяется от фонда заработной платы производственных рабочих:
Зарплата — 292 545,08
Отчисления на социальные нужды — 852 927 руб:
в пенсионный фонд 20% - 550 275,5 руб.
на обязательные медицинские социальные страхования (ОМС) 3% - 82 541,3 руб.
прочие 5% - 137 569 руб.
3.3 Расчёт себестоимости Плановая себестоимость продукции определяется по формуле:
= З./п. +, руб. (3.3)
= 2 751 377,6 +1 423 344,6 = 4 174 722,2
=, руб (3.3.1)
= = 3558,7
вагонный железнодорожный транспорт
Заключение
В данном дипломном проекте рассмотрена тема: «Вагонного пассажирского депо с разработкой отделения по ремонту букс с роликовыми подшипниками», и состоит из пояснительной записки и графической части.
Пояснительная записка содержит данные по трем разделам: организационному, технологическому и экономическому.
В организационной части рассмотрены темы по назначению и производственной характеристике пассажирского депо, произведены расчеты и пояснения, определена численность работников штата.
В технологической части рассмотрены вопросы по организации работы колесно-роликового цеха, программа ремонта, площадь участка мероприятия по охране труда и технике безопасности.
В экономической части представлены расчеты штатной ведомости с расчетом заработной платы и планом эксплуатационных расходов.
В период выполнения дипломного проекта я посещал пассажирское вагонное депо и ознакамливался с типовыми технологическими процессами депо и отделениями по ремонту буксового узла с роликовыми подшипниками. Учитывая направления развития вагонного хозяйства, основными из которых являются уменьшение объемов и стоимости ремонтов, мною были сделаны расчеты эксплуатационных расходов.
1. А. А. Криворучко, Вагонное хозяйство. — Москва: «Транспорт» 2008 г.
2. Р. П. Стрекалина, «Экономика и организация вагонного хозяйства». Москва. «Транспорт» 2006 г.
3. А. А. Амелина, «Устройство и ремонт вагонных букс с роликовыми подшипниками». Москва «Транспорт» 2006 г.
4. Гридюшко В. И. Вагонное хозяйство / В. И. Гридюшко, В. П. Бугаев, Н. З. Криворучко, и др. — М.: Транспорт, 2006. — 294с.
5. Гридюшко В. И. Экономика, организация и планирование вагонного хозяйства: Учебник для техникумов железнодорожного транспорта / В. И. Гридюшко, В. П. Бугаев, А. Ф. Сузова — М.: Транспорт, 2006 — 279с.
6. Инструкционные указания по эксплуатации и ремонту вагонных букс с роликовыми подшипниками 3 — ЦВРК. — М.: ОАО «Астра семь», 2006
7. Сенько В. И. Техническое обслуживание вагонов. Организация ремонта грузовых вагонов в депо: Учебное пособие / В. И. Сенько, И. Л. Чернин, И.С. БычекГомель.: БелГУТ, 2010; 371с