Повышение эффективности вентиляции корпусов электролизного производства алюминия путем совершенствования системы газоотсоса
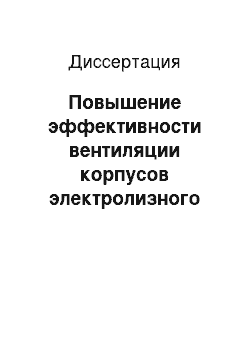
Диссертация
Разработана конструкция газосборного колокола, исключающая образование отложений в подколокольном пространстве. Исключение отложений более, чем в 20 раз сокращает частоту выполнения технологических операций, связанных с разрушением корки. Кроме этого, увеличенные наружные габариты газосборного колокола на 12 -19% сокращают площадь поверхности расплава, находящуюся вне укрытия, что сокращает… Читать ещё >
Содержание
- ОСНОВНЫЕ ОБОЗНАЧЕНИЯ
- 1. СОВРЕМЕННОЕ СОСТОЯНИЕ СИСТЕМЫ 14 ВЕНТИЛЯЦИИ, ПЫЛЕУЛАВЛИВАНИЯ И ОБЕЗВРЕЖИВАНИЯ АНОДНЫХ ГАЗОВ В КОРПУСАХ ПРОИЗВОДСТВА АЛЮМИНИЯ
- 1. 1. Вентиляция в корпусах и вторичные укрытия рабочего 15 пространства электролизера
- 1. 2. Газосборный колокол электролизера
- 1. 3. Горелочные устройства электролизера
- 1. 4. Газоходные сети корпуса электролиза
- 1. 4. 1. Отложения в газоходах. Анализ причин образования 38 отложений
- 1. 4. 2. Удаление отложений. Анализ эффективности очистки 41 газоходов от пылевых отложений
- 1. 4. 3. Электроизоляционные разрывы газохода. Анализ 45 эффективности герметизации узла
- 1. 5. Выводы по главе и формирование задачи исследования
- 2. ТЕОРЕТИЧЕСКИЕ ОСНОВЫ ПОВЫШЕНИЯ 49 ЭФФЕКТИВНОСТИ СБОРА И ОБЕЗВРЕЖИВАНИЯ АНОДНЫХ ГАЗОВ
- 2. 1. Новая конструкция газосборного колокола
- 2. 2. Расчет оптимальных параметров щелевых горелочных 55 устройств
- 2. 3. Система автоматической очистки полостей горелочных 64 устройств от отложений
- 2. 4. Газоходная сеть корпуса электролиза. Повышение 66 эффективности работы системы газоотсоса
- 2. 4. 1. Теоретическое определение условий уноса твердых 68 пылевидных частиц со дна горизонтального воздуховода закрученным газовым потоком
- 2. 4. 2. Расчет аэродинамических сопротивлений узлов 73 газоходной сети корпуса электролиза
- 2. 5. Теоретические основы построения сетевых моделей 82 газоходных трактов корпусов электролиза
- 2. 6. Описание программного комплекса аЫе1, 84 предназначенного для расчета сильноразветвленных сетей
- 2. 7. Математическая модель сильноразветвленной газоходной 87 сети
- 2. 7. 1. Представление гидравлической сети на основе 87 ориентированного графа
- 2. 7. 2. Диффузионная и конвенктивная задачи распределения 88 несущего потока в сети
- 2. 7. 3. Тепломассообмен потока с окружающей средой
- 2. 8. Алгоритм расчета газоходной сети
- 2. 9. Определение значений коэффициентов местных 91 сопротивлений узлов сети из экспериментальных данных
- 2.
- Выводы по главе
- 3. МОДЕЛИРОВАНИЕ ГАЗОХОДНЫХ СЕТЕЙ ПРИМЕНИТЕЛЬНО К ЭЛЕКТРОЛИЗНОМУ ПРОИЗВОДСТВУ АЛЮМИНИЯ И ПРАКТИЧЕСКАЯ РЕАЛИЗАЦИЯ
- 3. 1. Экспериментальное обоснование решения задачи
- 3. 2. Расчет газоходных сетей корпуса электролиза
- 3. 2. 1. Расчет газоходной сети, эксплуатируемой в корпусе 93 электролиза
- 3. 2. 2. Расчет газоходной сети при условии равномерности углов 97 ввода спусков в подкорпусной газоход
- 3. 2. 3. Расчет газоходной сети при условии отсутствия 99 пылеосадительных камер горелочных устройств
- 3. 2. 4. Расчет газоходной сети при условии исключения 102 несанкционированных подсосов воздуха по длине газоходного тракта
- 3. 2. 5. Расчет газоходной сети, включающей в себя технические 104 решения, рассмотренные в гл. 3.2
- 3. 2. 6. Выравнивание объемов газоотсоса в газоходной сети 106 включающей в себя технические решения, рассмотренные в гл. 3.2
- 3. 2. 7. Расчет «скоростной» газоходной сети корпуса электролиза
- 3. 2. 8. Выравнивание объемов газоотсоса в «скоростной» 112 газоходной сети корпуса электролиза
- 3. 3. Экологоэкономическая эффективность внедрения 116 результатов работы в масштабах Красноярского алюминиевого завода
- 3. 4. Выводы по главе
Список литературы
- П., Истомин С. П. Переработка отходов алюминиевого производства. — Красноярск: 2004.- 480 с.
- ГОСТ 12.1.007−76. Вредные вещества. Классификация и общие требования безопасности.
- Гигиенические нормативы ГН 2.2.5.1313−03. Предельно допустимые концентрации (ПДК) вредных веществ в воздухе рабочей зоны
- Санитарные правила и нормы СанПиН 2.2.4.548−96. Гигиенические требования к микроклимату производственных помещений.
- ГОСТ 12.1.005−88, Общие санитарно гигиенические требования к воздуху рабочей зоны.
- OSPAR Convention for the Protection of the Marine Environment of the North East Atlantic. Ministerial Meeting of the OSPAR Commission./ Sintra: 22 — 23 July 1998.
- Зиганшин М.Г., Колесник A.A., Посохин В. Н. Проектирование аппаратов пылегазоочистки. М.: «Экопресс —ЗМ», 1988, 505 с.
- Санитарные правила и нормы СанПиН 2.2.4.548−96. Гигиенические требования к микроклимату производственных помещений.
- Бегунов А.И.- Гринберг И.С.- Громов Б.С.- Деревягин В.Н.- Кульков В.Н.- Пак Р. В. Устройство для укрытия алюминиевого электролизера и подачи глинозема в криолит. Патент на изобретение № RU 2 083 727. — опубл. 10.07.1997.
- Сухоплечев И.П. Укрытие алюминиевого электролизера с обожженными анодами. Патент на изобретение № RU 2 009 266. -опубл. 15.03.1994.
- Попченков И.Н., Абугов Я. М., Строгов B.C. и Колосов Ю.Н. Укрытие электролизера для получения алюминия. Авт. свид. № SU 1 388 463. — опубл. в БИ № 14, 1988.
- Евменов В.А., Аюшин Б. И., Косыгин В. К., Дерягин В. Н. и Михайлов В.А. Укрытие алюминиевого электролизера. Авт. свид. на изобретение № SU 1 571 106. — опубл. в БИ № 22, 1990.
- Шемет Ю.В., Косыгин В. К., Хороших Б. А. и Рохальский В.А. Укрытие алюминиевого электролизера. Авт. свид. на изобретение № SU 1 252 392. — опубл. в БИ № 31, 1986.
- Грибанов Г. А. Укрытие электролизера с обожженными анодами. Авт. свид. на изобретение № SU 1 258 881. — опубл. в БИ № 35, 1986.
- Рыбкин К.К. Укрытие электролизера с обожженными анодами.-Авт. свид. на изобретение № SU 1 381 201. опубл. в БИ № 10, 1988.
- Репко А.П., Герасимов A.M., Бабич В. Я., Кузнецов С. Ф. и Тепляков Ф.К. Укрытие для непрерывного питания алюминиевого электролизера. Авт. свид. СССР на изобретение № 962 336. — опубл. в БИ № 36, 1982.
- Калужский H.A., Яблоков В. Г., Никифоров В. П., Кузнецов В. А., Попченков И. Н. и Гольдин Е.Л. Укрытие алюминиевого электролизера с обожженными анодами. Авт. свид. СССР на изобретение № 333 215. -опубл. в БИ № 11, 1972.
- Гусев В.М., Конокоткин В. В., Щанкин Б. Д. и Этингова В.А. Укрытие алюминиевого электролизера. Авт. свид. СССР на изобретение № 439 544. — опубл. в БИ № 30, 1974.
- Павлюченко Г. А., Климова Л. Л. и Хороших Б.А. Укрытие алюминиевого электролизера. Авт. свид. СССР № 449 989. — опубл. в БИ № 42, 1973.
- Хижинский Э.Л., Величко Г. Г. и Костров H.A. Укрытие для алюминиевых электролизеров. Авт. свид. СССР на изобретение № 134 429. — опубл. в БИ № 24, 1960.
- Калужский H.A., Спиридонов А. П., Хомяков B.C., Зайцев В. Н., Беляев A.C., Деркач A.C. и Попченков И.Н. Укрытие алюминиевого электролизера с обожженными анодами. Авт. свид. СССР на изобретение № 546 667. — опубл. в БИ № 6, 1977.
- Хомяков B.C. и Михайлов В.П. Укрытие для укрытия алюминиевого электролизера с верхним подводом тока. — Авт. свид. СССР на изобретение № 185 075. ~ опубл. в БИ № 16, 1966.
- Карпов Г. М., Шентяков В. В., Лукишов Г. И., Иванов Ю. В., Челюк O.A., Королева H.A. и Иванов С.С. Герметичный электролизер. -Авт. свид. СССР на изобретение № 239 057. опубл. в БИ № 5, 1971.
- Юдин Д.И., Попченков И. Н. и Гольдин Е.Л. Устройство для открывания крышек укрытия алюминиевого электролизера с обожженными анодами. Авт. свид. СССР на изобретение № 246 074. -опубл. в БИ № 20, 1969.
- Александров Д.П. Газосборник алюминиевого электролизера. -Авт. свид. СССР на изобретение № 429 133. опубл. в БИ № 19, 1975.
- Яблоков В.Г., Калужский H.A., Никифоров В. П., Кузнецов В. А., Попченков И.Н и Гольдин Е. Л. Верхнее укрытие алюминиевого электролизера. Авт. свид. СССР на изобретение № 293 055. — опубл. в БИ № 5, 1971.
- Чернявский М.А. Приспособление для удаления вредных испарений из травильных и тому подобных ванн. Авт. свид. СССР на изобретение № 58 906. — опубл. 31.01.1941.
- Саакян П.С. и Агабабян М.М. Устройство для непрерывной или полунепрерывной подачи глинозема в электролизер. Авт. свид. СССР на изобретение № 124 627. — опубл. в 1959 г.
- Червинский A.A., Пирогова Л. В., Пугачева Н. П., Суровцева О. В., Коленчиц П. В., Сафонюк A.JI. и Федоре Д.Н. Устройство для удаления газа от алюминиевого электролизера с боковым токоподводом.- Авт. свид. СССР на изобретение № 193 084. опубл. 01.01.1967.
- Александров Д.П. Газоотсос алюминиевого электролизера. -Авт. свид. СССР на изобретение № 302 390. опубл. в БИ № 15, 1971.
- Кайдалов И.В., Минченко A.A. и Семенов B.C. Укрытие алюминиевого электролизера с самообжигающимся анодом. Авт. свид. СССР на изобретение № 360 398. — опубл. в БИ № 36, 1972.
- Арне Энгесланд (Норвегия). Устройство для улавливания газов алюминиевого электролизера. — Авт. свид. СССР на изобретение № 575 040. опубл. 30.09.1977.
- Ростовцев В.В.,. Швецов А. Д, Липинский М. П., Соболь И. И., Алакин Г. А., Кальченко B.C. Газосборник алюминиевого электролизера.- Авт. свид. на изобретение № SU 1 023 005. опубл. в БИ № 22, 1981.
- Блюштейн М.Л., Гордеев H.H., Доброхотов В. Б., Друкарев В. А. и Цыплаков A.M. Способ эвакуации газов из алюминиевого электролизера с самообжигающимся анодом и устройство для его осуществления. Авт. свид. на изобретение № 557 122. — опубл. в БИ № 17, 1977.
- Хороших Б.А., Швецов А.Д.,. Соболь И. И, Смирнов Ю. Н., Степанов В. Т., Михалев Б. М., Кальченко B.C. Газосборник алюминиевого электролизера. — Авт. свид. на изобретение № 850 744. -опубл. в БИ № 28, 1981.
- Буркат B.C., Гупало И. П., Друкарев В. А., Калужский H.A., Митрофанов P.A., Фукс А.М.и Цыплаков A.M. Устройство для улавливания газов, выделяющихся при производстве алюминия электролизом. Авт. свид. на изобретение № SU 1 025 756. — опубл. 30.06. 1983.
- Борзых С.Д., Карташев Ю. С. Способ удаления отходящих газов из алюминиевого электролизера. Авт. свид. на изобретение № SU 1 702 717. — опубл. 10.06.1996.
- Колчин П.А., Елсуков К. Н. и Грязнова З.Н. Устройство для улавливания газообразных продуктов, выделяющихся из алюминиевого электролизера. Авт. свид. на изобретение № SU 1 786 196. — опубл. в БИ № 1, 1993.
- Козьмин Г. Д., Кулеш М. К., Фризоргер В. К., Савинов В. И., Брюшинин В. П., Бикмурзин В. Т. Устройство для улавливания анодных газов алюминиевого электролизера с верхним токоподводом. Патент на изобретение № RU 2 037 568. опубл. 19.06.1995.
- Спиридонов А.П., Колосов Ю. Н. и Толкачева Т.Ю. Устройство для сбора и удаления газа алюминиевого электролизера. Патент на изобретение № RU 2 218 453. — опубл. 10.12.2003.
- Степанов В.Т., Аносов В. Ф., Афракова Т. Ф., Лавренчук Е. Е., Гринберг И. Г. и Беляев Л.А. Способ изготовления секции газосборного колокола алюминиевого электролизера. Авт. свид. на изобретение № SU 1 578 234. — опубл. в БИ № 26, 1990.
- Одд Олсен (NO). Элемент конструкции электролизера для производства алюминия, контактирующий с газовой фазой. Патент Норвегии № 2 095 484. — опубл. 10.11.1997.
- Александров Д.П. Газосотсос электролизера для получения алюминия с самообжигающимся анодом. Авт. свид. СССР на изобретение № 583 208. — опубл. в БИ № 45, 1977.
- Нестеров Т.Е. Снижение вредных выбросов в атмосферу при электролизе алюминия (зарубежная практика)./ / Цветная металлургия. 1983. — № 9.
- Расчетная инструкция (методика) по определению состава и количества вредных (загрязняющих) веществ, выбрасываемых в атмосферный воздух при электролитическом производстве алюминия (в ред. Приказа Ростехнадзора от 29.11.2005 № 892).
- Из истории технологии производства алюминия. Карл Вильгельм Содерберг. / / Технико-экономический вестник РУСАЛа. -2005. — № 11 -С. 40 — 42.
- Басов А.И., Ельцев Ф. П. Справочник механика заводов цветной металлургии, М.: Металлургия, 1981.- 495 с.
- Буркат B.C., Друкарев В. А. Сокращение выбросов в атмосферу при производстве алюминия. Санкт — Петербург. — 2005, — 275 с.
- Пак М.А., Мурашкин А. И. Газосборный узел анодного устройства алюминиевого электролизера. Патент РФ на изобретение № 2 010 892. — опубл. 15.04.1994.
- Репко А.П., Матвеев Н. С., Бабич В. Я., Герасимов A.M., Кузнецов С. Ф. Газосборный колокол электролизера для получения алюминия. Авт. свид. СССР на изобретение № 949 021. — опубл. в БИ № 29, 1982.
- Бикмурзин В.Т., Казанцев A.A., Немов В. П., Чурак А. И. Алюминиевый электролизер с самообжигающимся анодом и верхним токоподводом. — Авт. свид. СССР на изобретение № 1 775 502. опубл. в БИ № 42, 1992.
- Светличный Б.Н., Цыплаков В. Б., Доброхотов В. Б., Друкарев В. А., Кайдалов И. В., Репко В. П. Газосборный колокол алюминиевого электролизера. Авт. свид. СССР на изобретение № 418 564. — опубл. в БИ № 21, 1977.
- Сахаров Г. Г., Полутчев В. И., Марченко М. М., Морозов Б. М. Газосборный колокол алюминиевого электролизера. Авт. свид. СССР на изобретение № 611 948. — опубл. в БИ № 23, 1978.
- Репко А.П., Герасимов A.M., Матвеев Н. С., Романов В. П. Газосборный колокол электролизера для получения алюминия. Авт. свид. СССР на изобретение № 565 952. — опубл. в БИ № 27, 1977.
- Громов Б.С., Пак Р.В., Мировщиков М. Д., Ахмедов С. Н., Строгов B.C. Газосборный колокол алюминиевого электролизера. -Патент РФ на изобретение № 2 151 825. 27.06.2000.
- Костюков A.A., Киль И. Г., Никифоров В. П., Вольфсон Г. Е., Рапопорт М. Б., Цыплаков A.M., Гупало И. П., Штерн В. И. Справочник металлурга по цветным металлам. Производство алюминия. М.: «Металлургия». 1971. — 560 с.
- Пак М.А., Дробнис В. Ф., Гефтер С. Ж. Узел подвески газосборного колокола алюминиевого электролизера. — Авт. свид. СССР на изобретение № SU 1 786 195. опубл. в БИ № 1. — 1991.
- Технологическая инструкция ТИ 02.01.01. Производство алюминия на электролизерах с самообжигающимся анодом и верхним токоподводом. Введена в действие распоряжением № 429 от 03.08.2006.
- Доброхотов В.Б., Друкарев В. А., Кайдалов И. В. и др. Газосборный колокол электролизера для получения алюминия. Авт. свид. СССР на изобретение № 618 454. — опубл. в БИ № 29. — 1978.
- Лащинский A.A., Толчинский А. Р. Основы конструирования и расчета химической аппаратуры. Справочник. М. — Л.: Машгиз. — 1963. — 468 с.
- Минцис М.Я., Поляков П. В., Сиразутдинов Г. А. Электрометаллургия алюминия. Новосибирск.: Наука. — 2001. — 368 с.
- Енохович A.C. Краткий справочник по физике. М.: Высшая школа. — 1976 — 288 с.
- Леви О.Э., Пингин В. В., Никандров К. Ф., Куликов Ю. В. Внедрение АПГ точечного типа на электролизерах С-8БМ на КрАЗе / /- Технико экономический вестник БрАЗа. — 2002. — № 6. — С. 34 — 37.
- Козьмин Г. Д., Тепляков Ф. К. Освоение и эксплуатация способа автоматической подачи глинозема в электролизные ванны / / Технико -экономический вестник БрАЗа. 2002. — № 6.- С. И — 16.
- Рягузов В.Н. Способ выведения газов из-под подошвы самообжигающегося анода алюминиевого электролизера. Авт. свид. СССР на изобретение № 313 897. — опубл. в БИ № 27, 1971.
- Саакян П.С., Агабабян М. М. Устройство для непрерывной и полунепрерывной подачи глинозема в электролит. Авт. свид. СССР на изобретение № 124 627.- опубл. в БИ № 23, 1959 г.
- Zhaowen Wang, Bingliang Gao, Haitao Li, Zhongnin Shi, Xiaodong Lu, Zhuxian Qiu. Исследования поведения пузырьков на аноде при электролизе алюминия. / / Сб. докл. XI Международной конференции Алюминий Сибири 2005. Красноярск: 2005. С. 135 — 139. .
- Климова JI.JI., Павлюченко Г. А., Белов Б. А. Сравнительная оценка различных горелочных устройств для алюминиевых электролизеров. / / Цветная металлургия. 1979. — № 19. — С. 54 — 56.
- Деревягин В.Н.- Баранцев А.Г.- Ким JI.C. Способ дожига анодных газов алюминиевого электролизера. Патент на изобретение №RU 2 093 610. — опубл. 20.10.1997.
- Сторожев Ю.И.- Поляков П.В.- Вербицкий А.В.- Баранцев А.Г.- Савинов В. И. Устройство для сжигания газа алюминиевого электролизера с двойным аэродинамическим эффектом. Патент на изобретение № RU 2 203 985. — опубл. 10.05.2003.
- Куликов Б.П., Поляков П. В., Сторожев Ю. И. Устройство для сжигания анодных газов алюминиевого электролизера. Патент на изобретение № RU 2 269 610. — опубл. 10.02.2006.
- Юрьев А.С. Справочник по расчетам гидравлических и вентиляционных систем. Санкт — Петербург.: Мир и семья-. — 2001. -1153 с.
- Идельчик И.Е. Справочник по гидравлическим сопротивлениям.- М.: Госэнергоиздат. 1975. — 560 с.
- Куликов Б.П., Сторожев Ю. И., Железняк В. Е. Устройство для эффективного дожигания анодных газов алюминиевого электролизера. -Патент на изобретение № RU 2 294 406. опубл. 27.02.2007.
- Куликов Б.П., Сторожев Ю. И., Лагунов Д. А. Колокольный газосборник алюминиевого электролизера. Патент на изобретение № RU 2 303 660. — опубл. 27.07.2007.
- Шахрай С.Г., Сугак Е. В., Смола П. В., Белоусов С. В. Методы снижения выбросов при электролитическом производстве алюминия.// Сб. докл. XII Международной конференции Алюминий Сибири 2006. —
- Красноярск. 2006. — С. 267 — 272.
- Правила безопасности при производстве глинозема, алюминия, магния, кристаллического кремния и электротермического силумина. -Утверждены постановлением Федерального горного и промышленного надзора России № 20 от 24 апреля 2003 г.
- Отчет НИР. Промышленные испытания и доработка горелок конструкции ИФ ВАМИ на БрАЗе. //№ Гос. регистрации 73 029 178.-Иркутск.: — 1974. 50 с.
- Кесова A.A., Шиллин Г. В. О гидродинамике пылепроводов тепловых электростанций. / / Теплоэнергетика. 1978. — № 8. -С. 46 -49.
- Гордон Г. М., Пейсахов И. Л. Пылеулавливание и очистка газов в цветной металлургии. М.: Металлургия. — 1977. — 456 с.
- Руководство по эксплуатации. Газоходы подкорпусные. -Введено в действие распоряжением № 132 от 05.03.2005.
- Руководство по эксплуатации. Горелочное устройство электролизера. Введено в действие распоряжением № 305 от 06.06.2005.
- Воронец Д., Козич Д. Влажный воздух. Термодинамические свойства и применение. Перевод с сербохорватского под ред Мотулевича В. П. М.: Энергоатомиздат. — 1984. — 135 с.
- Лащинский A.A., Толчинский А. Р. Основы конструирования и расчета химической аппаратуры. Справочник. М. Л.: Машгиз. — 1963.468 с.
- Афанасенков А.Н., Гостинцев Ю. А., Успенский O.A. Квазиодномерная теория сопла для винтового потока газа. / / Изв. АН СССР. Механика жидкости и газа. 1977. — № 5. — С. 186 — 191.
- Ахмедов Р.Б. Аэродинамика закрученной струи. — М.: Энергия.- 1977. -240 с.
- Ахмедов Р.Б., Балагула Т. Б. К расчету аэродинамических характеристик закрученной струи. //В кн.: Теория и практика сжигания газа. Л.: Недра. — 1972. — т.5. — С. 15 — 27.
- Алимов Р.З. Гидравлическое сопротивление и тепломассообмен в закрученном потоке. ИФЖ. — 1968. — т. 10. № 4.
- Сугак Е.В., Войнов H.A., Николаев H.A. Очистка газовых выбросов в аппаратах с интенсивными гидродинамическими режимами.- Казань: «Школа». 1999, — 224 с.
- Шахрай С.Г., Сугак Е. В. Образование отложений в газоходах и пути их сокращения.//в сб. Современные технологии освоения минеральных ресурсов.- Красноярск. 2006. — Вып. 4. — С. 412 — 418.
- Кузьмин В.В., Пустовойт Ю. А., Фафурин A.B. Экспериментальное определение пристеночного трения при движениизакрученного потока в цилиндрическом канале. Вихревой эффект и его применение в технике. Куйбышев. — 1976. — С. 183 — 186.
- Отчет НИР. Изучение и экспериментальная проверка возможности применения сухого способа очистки фторсодержащих газов. № Гос. регистрации 74 022 163. Красноярск. — 1975. — 99 с.
- Коробов М.А., Дмитриев A.A. Самообжигающиеся аноды алюминиевых электролизеров.- М.: Металлургия. 1972.- 208 с.
- Крюковский В.А. Исследование циркуляции электролита и анодных газов в междуполюсном зазоре мощных алюминиевых электролизеров: Автореферат дисс. канд. техн. наук / Ленинград: Всесоюзный институт алюминиевой и магниевой провышленности (ВАМИ), 1974. 20 с.
- Климова JI.JI., Павлюченко Г. А. Устройство для сжигания анодных газов. Авт. свид. СССР на изобретение № 466 296. — опубл. 05.04.1975.
- Шахрай С.Г., Куликов Б. П., Петров A.M., Сугак Е. В., Кучкин А. Г., Фризоргер В. К. Газосборное устройство алюминиевого электролизера (варианты). Патент РФ на изобретение № 2 324 012. -опубл. БИ№ 13. — 10.05. 2008.
- Гурвич С.М. Справочник химика энергетика. Том третий. Энергетическое топливо. (Характеристика и контроль качества). — М.: Энергия. — 1972. — 215 с.
- Кононенко В.Д., Лопухов В. В., Мальчевская Н. Ф. К расчету параметров закрученного потока в горизонтальном трубопроводе.// в сб. Инженерные методы решения практических задач в санитарной технике. Выпуск IX. Волгоград. — 1977. — С. 3 — 8.
- Биргер М.И., Вальдберг А. Ю., Мягков Б. И. и др. Справочник по пыле и золоулавливанию. Под общ. ред. A.A. Русанова. М.: Энергоатомиздат. — 1983. -312 с.
- Бэкшелл А.К., Лэндис П. К. Распределение скорости в пограничном слое для турбулентного закрученного потока в трубе. Теоретические основы инженерных расчетов. — 1969. № 4. -С. 174 -179.
- Гостинцев Ю.А. Тепломассообмен и гидравлическое сопротивление при течении по трубе вращающейся жидкости. // Изв. АН СССР. Механика жидкости и газа. 1968.- № 5. — С. 115 — 119.
- Кинни Р.Б. Универсальное подобие скоростей в полностью турбулентных вращающихся потоках.// Прикладная механика. — 1967. № 2. — С. 199 — 206.
- Рочино A.A., Лэвэн З. П. Аналитическое исследование несжимаемого турбулентного закрученного потока в неподвижных трубах.// Прикладная механика. 1969. — № 2. — С. 7 — 16.
- Глебов Г. А., Матвеев В. Б. Использование полиномиальной аппроксимации при расчете закрученного течения в трубе. Пристенные струйные потоки. Новосибирск. — 1984. — С. 81 — 86.
- Леончик Б.И., Маякин В. П. Измерения в дисперсных потоках. М.: Энергия. 1971. — 248 с.
- Мартыненко О.Г., Байрашевский Б. А., Гармизе Л. Х., Сенчцк Л. А. Затухание вращательного движения потока вдоль круглой трубы в условиях постоянной закрутки его на входе. Исследование термогидродинамических световодов. Минск. — 1970. — С. 123 — 132.
- Скоробогатова Н.В. Исследование закрученных потоков при транспортировании твердых частиц в трубах систем аспирации. Свердловск.: Изд-во УПИ. — 1979. — 193 с.
- Хабиб М.С., Уайтлоу Дж. П. Характеристики ограниченных коаксиальных струй с закруткой и без закрутки потока. //Теорет. основы инж. расчетов. — 1980. 102, № 1. — С. 163 — 171.
- Щукин В.К., Халатов A.A. Теплообмен, массообмен и гидродинамика закрученных потоков в осесимметричных каналах. М.: Машиностроение. 1982. — 200 с.
- Щукин В.К., Халатов A.A., Кожевников A.B. Структура закрученного потока в цилиндрическом канале при однородном вдуве.// ИФЖ. 1979. — 37, № 2. — С. 245 — 253.
- Булгакова Н.Г., Петербургская E.H. Измерение дисперсного состава промышленных пылей./ / Обзорная информация ХМ 14. — М.: ЦИНТИнефтехиммаш. — 1982. — С. 13 — 16.
- Сестрин Л.Е. Основы газовой динамики. М.: Изд-во МАИ. -1995. -332 с.
- Stephen Lindsey. Fluoride emissions control. лекция на Международных курсах TMS. — США, г. Эвансвиль. — 20.09.2007.
- Michael Sahling, Elmar Sturm. Improvement of pots gas collection efficiency by implementation of impuls duct system. Light Metals — 2004.- p. 351 — 356
- Хасилев В.Я., Меренков А. П., Каганович Б. М. и др. Методы и алгоритмы расчета тепловых сетей. М., «Энергия». 1978. — 270с.
- Меренков А.П., Хасилев В. Я., Теория гидравлических цепей. М&bdquo- «Наука». 1985. — 175 с.
- Дектерев A.A., Елгин Б. А., Поздяев В. Н. Использование программы для сетевого моделирования при оптимизации работыгазоходных трасс. / / Сб. материалов конф. Использование математического моделирования в котельной технике. — Красноярск -1996. С.48−53.
- Богословский В.Н. Отопление и вентиляция. Часть II. Вентиляция. М.: Стройиздат. — 1976. — 441 с.
- Способ очистки внутренних полостей горелочных устройств от отложений
- Рис. Интенсивность работы горелочных устройств а) горелочные устройства «свидетели», б) испытуемые горелочные устройства
- Рис. 2 Содержание углерода в пыли а) после горелочного устройства «свидетеля" — б) после испытуемого горелочного устройства с автоматической очисткой от отложений
- Считаем целесообразным использование в промышленном масштабе системыавтоматической очистки от отложений внутре электролизеров с верхним токоподводом.
- Директор ДТ ИТЦ Менеджер ОПТ ИТЦ Специалист ОПТ ИТЦг о г? полостей горелочных устройств1. B.В. Пингин1. C.Г. Шахрай Е. В. Кузнецов