Проектирование капитального ремонта бесстыкового пути
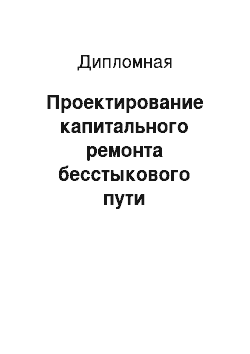
При регулировке ширины колеи за счет поправки перекошенных железобетонных шпал отдельные операции выполняются в следующей последовательности: — отрывка шпальных ящиков у перекошенных шпал;— смазка на них клеммных болтов;— установка стяжного прибора, ослабление гаек клеммных болтов на 2—3 оборота;— передвижка перекошенных шпал в нормальное положение и постановка рельсовой нити при помощи стяжного… Читать ещё >
Проектирование капитального ремонта бесстыкового пути (реферат, курсовая, диплом, контрольная)
Исходные данные ремонт путевой рельса Участок ремонта находится на Хилокской дистанции пути Забайкальской железной дороги.
Направление: Петровский Завод — Чита.
Границы ремонтируемого участка: перегон Хохотуй — Бада, путь № 2.
5871 км — 5880 км (протяженность 10 км).
Участок двухпутный, электрифицированный.
Род тока — переменный.
Двухсторонняя автоблокировка.
Средний вес поезда:
грузового — 6300 т;
пассажирского — 1150 т.
Существующая грузонапряженность — 136,9 млн. т. брутто/на 1 км в год, Пропущенный тоннаж — 1241,7 (1304,3) млн. т. брутто.
Скорость движения поездов:
грузовых — 80 км/час;
пассажирских — 90 км/час.
Локомотивы: ЭП-1, ВЛ-65, ВЛ-80р, 1,5ВЛ-80р, ВЛ-85, ЭР-9.
Класс, группа, категория пути 1А3.
Год последнего капитального ремонта — 2008.
На участках уложены плети бесстыкового пути, рельсы типа Р-65, шпалы железобетонные, промежуточное скрепление — КБ.
Эпюра шпал: 2000 шт/км.
Число замененных в одиночном порядке дефектных и о/дефектных рельсов, шт. за год/с начала укладки — 74/510.
Количество негодных шпал — 908 шт.
Балласт щебеночный, толщиной — 25 — 34 см.
Потребность в ремонте — 2015 год.
Кривые.
Участок. | Расстояние L, м. | Радиус, R, м. | Возвышение, мм. | Наружный рельс. | Боковой износ, мм. | |
5871 км ПК-4 — 5871 км ПК-7. | правый. | |||||
5878 км ПК-6 — 5878 км ПК-9. | левый. | |||||
Доля прямых участков — 94,38%, кривых — 5,62%, из них:
0 м — 0% от всех кривых.
— 291 м — 51,78%.
271 м — 18,22%.
Введение
Железнодорожный транспорт является важнейшей составной частью экономической системы России.
Обеспечение перевозок, безопасность пассажиров и сохранность перевозимых на железнодорожном транспорте грузов гарантируется единым производственно-технологическим комплексом с вертикальной системой управления, охватывающий 17 железных дорог, 64 отделения дорог, около 6000 железнодорожных станций, 400 дистанций пути, 220 локомотивов и 200 вагонных депо, 200 дистанций электроснабжения, почти 100 заводов различного профиля.
Протяженность Российских железных дорог составляет 86 тыс. км, в том числе двухпутный или многопутный линий — 37,3 тыс. км, оборудованных устройствами автоблокировки и диспетчерской централизации — 62,7 тыс.км. По протяженности электрифицированных линий Российские железные дороги занимают первое место в мире.
По эксплуатационной длине железных дорог Россия занимает второе (после России) место в мире, по перевозкам грузов — третье (после США и Китая), по перевозкам пассажиров — третье (после Японии и Индии). Железные дороги России перевозят 88% угля, 94% руды, 88% черных металлов, 79% %удобрений, 66% лесных грузов и т. д. Доля перевозок железнодорожным транспортом страны в общем объеме грузооборота превысила 82%.
В многоотраслевой системе железнодорожного транспорта одно из важнейших мест занимает путевое хозяйство, основные фонды которого составляют свыше 52% основных фондов путевого хозяйства более 26% приходится на земляное полотно, почти 46% - на верхнее строение пути, около 22% - на искусственные сооружения.
Развитие и совершенствование сложного комплекса путевого хозяйства основывается на внедрении современных достижений науки и техники, передового опыта лучших путейских коллективов, разумном использовании зарубежного опыта.
Мощный и долговечный железнодорожный путь, высокоэффективная система его технического обслуживания, включающая надежный мониторинг состояния пути и систему информационного обеспечения путевого хозяйства, не могут качественно функционировать без профессионально подготовительных, знающих и думающих специалистов — бригадиров, мастеров, руководителей путейских предприятий.
Мероприятия по текущему содержанию верхнего строения пути направлены на создание лучших условий взаимодействия пути и подвижного состава. Неровности пути, вызывающие вертикальные и горизонтальные толчки, значительно увеличивают силы воздействия подвижного состава на путь, ускоряют процесс накопления остаточных деформаций: Отсюда вытекают необходимость систематических работ по выправке направления пути в плане и продольном профиле.
Дальнейшие развитие и укрепление отрасли непосредственно связанно и зависит от уровня подготовки путейских кадров.
Современный специалист путеец должен в совершенстве знать и понимать суть процессов, происходящих в железнодорожном пути, закономерности и правила технического обслуживания и ремонта.
Главная цель дипломного проекта — разработать технологические процессы капитального ремонта пути с глубокой очисткой щебня и заменой путевой решетки и капитального ремонта пути с глубокой вырезкой балласта и заменой путевой решетки.
Для решения этого в работе решаются следующие задачи:
ѕ выбор типа верхнего строения пути;
ѕ расчеты верхнего строения пути на прочность;
ѕ организация работ по капитальному ремонту пути;
ѕ провести технико-экономическое обоснование;
ѕ рассмотреть мероприятия по обеспечению безопасности движения поездов и при производстве путевых работ;
ѕ разработать мероприятия по технике безопасности, охране труда и жизнедеятельности;
ѕ разработать мероприятия по охране окружающей среды.
Все разработанные процессы, расчеты выполнены в соответствии с местными условиями региона.
1. Техническая часть.
1.1 Характеристика ремонтируемого участка пути Природно-климатические условия Климат резко-континентальный с жарким коротким летом и продолжительной холодной зимой. Весна и начало лета в основном засушливы, весной часты пыльные бури. Средняя температура в июле +18 +20 °C (максимальная +38 °C), в январе -22 -26 °C (абсолютный минимум -47 °C). Годовое количество осадков не превышает 200−300 мм. Устойчивый снежный покров устанавливается в первой декаде декабря и сходит в первой декаде апреля. Среднее число дней в году со снежным покровом — 121. Высота снежного покрова составляет 45−50 см, глубина промерзания грунта составляет порядка 1 м. 45 см.
Участок, подлежащий ремонту: Хохотуй — Бада, путь № 2 5871 км ПК1- 5880 км ПК10 (протяженность 10 км), он относится к Петровск-Заводской дистанции пути Забайкальской железной дороги.
Ремонтируемый участок двухпутный, электрифицированный, оборудованный двухсторонней автоблокировкой, капитальный ремонт будет производиться на четном пути № 2, грузонапряженность линии 136,9 млн.т. брутто/км в год, пропущенный тоннаж составляет 772 млн. т.
В границах ремонта расположено 2 кривые:
Таблица 1.1. Кривые.
Участок. | Расстояние L, м. | Радиус, R, м. | Возвышение, мм. | Наружный рельс. | Боковой износ, мм. | |
5871 км ПК-4 — 5871 км ПК-7. | правый. | |||||
5878 км ПК-6 — 5878 км ПК-9. | левый. | |||||
Верхнее строение пути: бесстыковой путь, рельсы типа Р-65 длиной 1100 м, накладки двухголовые шестидырные, шпалы железобетонные, эпюра шпал 2000 шт/км, балласт — щебень, толщина балластного слоя под шпалой: 25 — 34 см. Щебень фракций 25−60 мм, только твердых пород с прочностью И20 и У75 по ГОСТ 7392–85 «Щебень из природного камня для балластного слоя железнодорожного пути».
Тип обращающихся единиц: пассажирские локомотивы ЭП-1, ЭР-9, грузовые ВЛ-65, ВЛ-80р, 1,5ВЛ-80р, ВЛ-85.
Максимальная скорость движения поездов: грузовых — 80 км/ч., пассажирских — 90 км/ч.
Данный участок относится к 1 классу, группе, А и категории 3.
Загрязненность балласта ниже подошвы шпал более 30%.
Число замененных в одиночном порядке дефектных рельсов 74 шт. за год и 510 шт. с начала укладки, количество негодных шпал — 908 шт.
Обочины требуют срезки, кюветы очистки.
Год последнего капитального ремонта — 2008 г.
Год последнего промежуточного ремонта — не проводился Таким образом, участок пути Хохотуй — Бада 5871 км ПК1- 5880 км ПК10 не отвечает техническим условиям и требованиям, предъявляемых к конструкциям и элементам верхнего строения пути при следующих критериях для путей класса 1А3 (Технические указания по устройству, укладке, содержанию и ремонту бесстыкового пути и Положение о системе ведения путевого хозяйства ОАО «РЖД» (2012 г.)): минимальная ширина обочины — не менее 50 см; ширина плеча балластной призмы — 45 см; крутизна откосов 1:1,5; На путях 1-го классов должен применяться щебеночный балласт с толщиной слоя под железобетонными шпалами не менее 40 см. (у нас 25 — 34 см);
Периодичность проведения капитального ремонта бесстыкового пути (ППР94) — после наработки тоннажа 700 млн. т.
Таблица 1.2. — Критерии выбора участков, подлежащих усиленному капитальному и капитальному ремонту на новых материалах при текущем планировании.
Класс пути. | Основные критерии. | Дополнительные критерии. | Критерии УРРАН. | |||||
Пропущенный тоннаж, срок службы в годах, % от нормативного1). | Одиночный выход рельсов (в сумме за срок службы — в среднем на участке ремонта), шт/км2). | Количество негодных и дефектных элементов на 1 км верхнего строения пути, % и более. | Частота отказов, шт в год/км. | Затраты на текущее содержание пути, доля от амортизации. | ||||
Негодные деревянные шпалы,%. | Негодные скрепления3), %. | Число шпал с выплесками, %. | ||||||
1 класс. | Не менее 100%. | 4 и более. | 0,2…0,8. | 0,5…0,7. | ||||
1) По таблице 6.1. или 6.2 определяется нормативный срок службы в пропущенном тоннаже с учетом понижающих и повышающих коэффициентов или срок службы в годах.
2) При определении одиночного выхода рельсов учитываются дефекты, образование и развитие которых зависит и возрастает по мере наработки тоннажа (дефекты: 10; 11.1−2; 17; 20; 21.1−2; 41), дефекты 30 В, 30 Г, 69, дефекты пятой группы (кроме дефектов 55; 56.3; 59), дефекты седьмой группы. Выход уравнительных рельсов не учитывается.
3) На пути с железобетонными шпалами со скреплениями КБ подсчитывается суммарный процент подкладок и закладных болтов, при бесподкладочных скреплениях — клемм и прикрепителей (болтов, шурупов, анкеров), на пути с деревянными шпалами — подкладок и костылей.
Назначается капитальный ремонт на новых материалах .
Капитальный ремонт железнодорожного пути на новых материалах предназначен для полной замены выработавшей ресурс рельсошпальной решетки на путях 1 и 2 классов (стрелочных переводов на путях 1−3 классов) и восстановления несущей способности балластной призмы, и в отличие от реконструкции (модернизации) железнодорожного пути включает в себя только работы по верхнему строению пути, а также восстановлению водопропускной способности водоотводов. Критерии назначения капитального ремонта на новых материалах приведены в таблице 1.2.
Капитальный ремонт пути на новых материалах назначается с учетом его фактического состояния при нормативной наработке пути после проведения реконструкции или предыдущего капитального ремонта на новых материалах.
Капитальный ремонт пути на новых материалах проводится в соответствии с проектной документацией, учитывающей местные условия, состояние пути до ремонта, результаты обследований, требования к пути после ремонта и др.
В состав капитального ремонта на новых материалах входят следующие основные виды работ:
замена рельсошпальной решетки на новую решетку, в том числе с элементами более высокого технического уровня (железобетонные шпалы, упругие скрепления и др.);
замена стрелочных переводов на новые переводы того же типа, в том числе с элементами более высокого технического уровня;
очистка щебеночной балластной призмы на глубину в соответствии с проектом, но не ниже 40 см под подошвой шпал на путях с железобетонными.
шпалами, с устройством (при необходимости) разделительного покрытия между очищенным щебнем и поверхностью среза основной площадки земляного полотна;
срезка обочин земляного полотна;
выправка, подбивка и стабилизация пути с постановкой на проектные отметки в профиле;
доведение балластной призмы до требуемых размеров;
постановка пути на ось в плане и приведение длин переходных кривых и прямых вставок между смежными кривыми в соответствие со скоростями движения поездов, предусмотренными проектной документацией на капитальный ремонт;
ликвидация, образовавшейся в процессе эксплуатации многорадиусности кривых, если это не требует дополнительного завоза грунта и замены или.
перестановки опор контактной сети;
очистка и планировка водоотводов;
срезка и уборка накопленных балластных материалов в нижней части откосов выемок и в нулевых местах;
ремонт пешеходных переходов;
ремонт железнодорожных переездов (объем работ по ремонту каждого.
переезда на участке капитального ремонта пути определяется с учетом местных условий с составлением калькуляций, а при необходимости чертежей);
приведение полосы отвода в соответствие с нормативными требованиями;
сварка плетей до длины блок-участка или перегона, включая стрелочные переводы;
шлифование поверхности катания рельсов, стрелочных переводов и другие работы, предусмотренные проектом;
послеосадочная выправка пути (через 10−30 млн. т брутто).
В состав капитального ремонта пути на новых материалах могут быть включены следующие дополнительные работы:
полная вырезка балластной призмы, сложенной из асбестового балласта, щебня слабых пород или их комбинации, на глубину не менее 40 см ниже подошвы шпал с укладкой разделительного покрытия на основной площадке земляного полотна (поверхности среза при вырезке);
частичное уположение кривых, удлинение переходных кривых и прямых вставок, если это не требует дополнительного завоза грунта и замены или перестановки опор контактной сети в объеме более 5%;
другие работы, предусмотренные проектом.
Дополнительные виды работ, включаемые в состав капитального ремонта пути на новых материалах, предусматриваются проектом в случаях:
если ремонтируемый участок пути ранее не подвергался реконструкции, при которой эти работы выполняются;
если фактическое состояние пути по результатам обследования и условия эксплуатации требуют выполнения указанных работ, а реконструкция железнодорожного пути на этом участке не предусмотрена;
наличия пучин, просадок пути, интенсивных расстройств рельсовой колеи по уровню и в продольном профиле, которые устраняют укладкой покрытий;
недостаточной ширины земляного полотна поверху и завышенной крутизны откосов.
2. Проектирование продольного профиля и плана линии.
2.1 Проектирование продольного профиля ремонтируемого участка Проектирование продольного профиля и плана пути выполняется в соответствии с требованиями «Технические условия на работы по реконструкции (модернизации) и ремонту железнодорожного пути», утвержденных ОАО «РЖД№ 18.01.2013 г., «Положение о системе ведения путевого хозяйства ОАО «РЖД», утвержденных 31.03.2000 г. и дополненных 01.02.2009 г. и «Технические указания по устройству, укладке, содержанию и ремонту бесстыкового пути», утвержденных 31.03.2000 г. и дополненных в 2010 г.
Алгебраическая разность уклонов смежных элементов профиля не превышает значений 9,6 ‰ (13‰).
Минимальная длина элементов профиля составляет 200 м.
При алгебраической разности уклонов смежных элементов профиля менее 2,8‰ вертикальные кривые не предусматриваются.
При алгебраической разности уклонов смежных элементов профиля более 2,8‰ устраиваются вертикальные кривые радиусом 15 000 м. вертикальные кривые размещены вне проходной кривой. Тангенс вертикальной кривой находится по формуле:
Тв = Дi (2.1.1).
где RB — радиус вертикальной кривой;
Дi — алгебраическая разность уклонов смежных элементов профиля.
Величина изменения проектной отметки, м, за счет устройства вертикальной кривой определяется.
Дh = (2.1.2).
Значение исправленной проектной отметки находится по формуле :
= Нпр Дh (2.1.3).
Пикектажное положение вертикальных кривых, их тангенс и величина изменения проектной отметки сведены в таблицу 1.
Таблица1.
№, п/п. | Пикет. | ТВ, м. | Дh, м. | |
5871 км 3ПК. | 37,00. | 0,11. | ||
5871 км 6ПК. | 51,00. | 0,12. | ||
5872 км 8ПК. | 35,25. | 0,04. | ||
5873 км 3ПК. | 36,75. | 0,06. | ||
5873 км 6ПК. | 36,25. | 0,05. | ||
5874 км 4ПК. | 24,00. | 0,02. | ||
5875 км 1ПК. | 50,00. | 0,15. | ||
5875 км 3ПК. | 49,00. | 0,09. | ||
5875 км 7ПК. | 42,60. | 0,06. | ||
5877 км 6ПК. | 28,50. | 0,03. | ||
5877 км 9ПК. | 63,00. | 0,13. | ||
5878 км 3ПК. | 56,00. | 0,15. | ||
В процессе проектирования уровень проектной головки рельса нечетного пути приводится к таким отметкам, чтобы разница уровней с соседним существующим путем не превышал 25 см. на железобетонных мостах, на подходах к переездам и остановочным пунктам уровень проектной головки рельса приводился к отметкам уже существующего пути.
Исправление продольного профиля предусматривается за счет подъемки пути на балласт при условии соблюдения размеров обочины земляного полотна, за счет подрезок, которые проводятся в пределах насыпи при наличии в пути слоя балласта сверхнормативной величины.
Продольный профиль ремонтируемого участка выполняется на миллиметровой бумаге в масштабе 1:100 (вертикальный) и 1:1000 (горизонтальный). На профиле показаны отметки земли, отметки уровня существующей головки рельса четного пути, отметки низа балластного слоя и запроектированные отметки пути после ремонта.
Разница отметок путей после ремонта определяется по формуле:
ДН = ПГРII — СГРI (2.1.4).
где ПГРII — отметка проектной головки рельса четного пути, м;
СГРI — отметка существующей головки рельса нечетного пути, м.
Толщина балластного слоя находится:
hб = ПГРII — hр — hподкл — hш — НБС — hпрокл (2.1.5).
где hр — высота рельса Р65, м; hр = 0,18 м;
hподкл — толщина подкладки при скреплении КБ, м; hподкл = 0,022 м;
hш — толщина железобетонной шпалы hш = 0,193 м;
НБС — отметка низа балластного слоя (она же отметка бровки земли), м.
hпрокл — толщина подрельсовой прокладки, hпрокл = 0,008 м.
расстояние от постели шпалы до головки рельса 605,5 мм Величина подъема определяется по формуле:
h = ПГРI — СГРII (2.1.6).
СГРII — отметка существующей головки рельса ремонтируемого пути.
При проектировании пути многорадиусность кривых не устраивалась, так как в противном случае понадобилось бы существенное переустройство земляного полотна и искусственных сооружений.
3. Расчет устойчивости бесстыкового пути Определим интервал закрепления рельсовых плетей для заданных условий эксплуатации и допускаемую температурную продольную силу по условию устойчивости пути против выброса.
Возможность укладки бесстыкового пути в конкретных условиях, устанавливается сравнением допускаемой температурной амплитуды Т для этих условий, с фактически наблюдающейся в данной местности годовой амплитудой колебаний температур рельсов ТА.
Значения ТА определяется как алгебраическая разность наивысшей t max max и наименьшей tmin min температур рельса, наблюдавшейся в данной местности (при этом учитывается, что наибольшая температура рельса на открытых участках превышает на 20 °C наибольшую температуру воздуха) ТА= tmax max — tmin min, (3.1).
Если ТА Т, то бесстыковой путь можно укладывать.
Амплитуда допускаемых изменений температур рельсов определяется по формуле:
Т = Дty + Дtp — Дt3 (3.2).
где [Дtу] - допускаемое повышение температур рельсов по сравнению с температурой их закрепления, определяемое устойчивостью пути против выброса при действии сжимающих продольных сил;
[Дtр] - допускаемое понижение температуры рельсовых плетей по сравнению с температурой закрепления, определяемое их прочностью при действии растягивающих сил;
[Дtз] - минимальный интервал температур, в котором окончательно закрепляется плети, по условиям производства работ; для расчётов он обычно принимается равным 10 °C, но при необходимости его можно уменьшить до 5 °C, если предусматривать закрепление плетей осенью, в пасмурную погоду, когда температура в процессе закрепления изменяется медленно.
Наличие в плетях больших сжимающих (в летний период) и больших растягивающих (в зимний период) сил предъявляет повышенные требования как к конструкции, так и к нормам укладки, содержания и ремонта бесстыкового пути. Основными из них являются: в летний период эксплуатации — обеспечение устойчивости бесстыкового пути, в зимний период — обеспечение прочности пути, под которым подразумевается прежде всего прочность рельсов, исключение, в случае излома плети, образования большого зазора, опасного для прохода поезда и исключение разрывов стыков в уравнительных пролетах. Выполнение приведенных требований должно обеспечиваться при соблюдении действующих норм укладки, содержания и ремонта существующей конструкции бесстыкового пути.
Устойчивость бесстыкового пути обеспечивается (гарантируется) на.
участках, где температура закрепления плетей (t3) соответствует оптимальной температуре из закрепления (tопт ± 5оС), приведенной в таблице 1, прикрепление рельсов к шпалам, состояние балластной призмы соответствует требованиям Инструкции по устройству, укладке, содержанию и ремонту бесстыкового пути, а максимально возможное повышение температуры рельсовых плетей относительно их температуры закрепления не превышает допускаемого повышения по устойчивости пути, т. е.
(tmaxmax — t3)? [?tу],.
где tmaxmax — максимальная температура рельсов для рассматриваемой местности,.
[?tу] - повышение температуры рельсовой плети относительно ее температуры закрепления, допускаемое по условию обеспечения устойчивости бесстыкового пути.
3.1 Расчет «зимних» напряжений В средней части плети возникают температурные напряжения и силы Nt, максимальное значение которых ограничивается условиями прочности или устойчивости. Прочность рельсовых плетей рассчитывают при условии, что суммарное воздействие на путь подвижного состава и изменений температуры рельсов не должно создавать в них напряжений, превосходящих допускаемые.
(3.1.1).
где — растягивающее напряжение в кромках подошвы рельсовых плетей от изгиба и кручения при проходе подвижного состава, определяется расчетом пути на прочность для зимних условий эксплуатации;
— коэффициент запаса прочности рельсов на растяжение: для новых рельсов нВ главных путях; для старогодных; для второстепенных путей .
— напряжение в поперечном сечении рельса от действия температурных сил;
— допускаемое нормальное напряжение [] = 350 и 400 МПа соответственно для новых «сырых» и термоупроченных рельсов.
Допускаемые температурные напряжения растяжения ограничиваются прочностью подошвы рельсов и определяются следующими образом:
(3.1.2).
Допускаемое понижение температуры рельсовых плетей по сравнению с температурой закрепления по условию прочности подошвы рельса:
Дtnn = Дtp = (3.1.3).
где б — коэффициент линейного расширения рельсовой стали,.
б = 0,118 град-1.
Е — модуль упругости рельсовой стали, Е = 210 000 000 кН/м2.
Величину Дtnn необходимо определить воспользовавшись расчетом на прочность при условии, что расчет выполняется для железобетонных шпал, в противном случае используют величину Дtp.
Тогда.
(3.1.4).
Наибольшая растягивающая температурная сила, которая может быть допущена для двух рельсовых плетей по условию прочности подошвы будет:
(3.1.5).
где — площадь двух рельсов.
3.2 Расчет «летних» напряжений Допускаемые температурные напряжения сжатия ограничиваются прочностью головки рельсов и определяются по формуле:
— кромочные сжимающие напряжения в головке рельса посчитанные для лета Наибольшая сжимающая сила:
(3.2.1).
Наибольшее допускаемое повышение температуры рельса по сравнению с температурой закрепления по условию прочности головки:
Дtnг = Дtp = (3.3.2).
Рис. 3. 1 — Эпюры температурных продольных сил в плети в летний (NЛ) и в зимний (NЗ) периоды ее эксплуатации.
3.3 Определение критической силы Бесстыковой путь устойчив, если предельная (критическая) величина суммарной продольной силы в обоих рельсовых нитях будет меньше допускаемой:
(3.3.1).
где — допускаемая по условию устойчивости пути продольная сжимающая сила;
— допускаемое повышение температуры рельсовых плетей относительно температуры закрепления по условию устойчивости пути.
Величины принимаются по результатам опытов, в ходе проведения которых были получены значения закритической продольной силы N3, вызывающей выброс пути.
= (3.3.2).
— коэффициент запаса устойчивости, компенсирующий неточность определения закритической силы и влияние ряда неучтенных факторов, = 1,2.
N3 = (k1k2k3) (3.3.3).
где, А и м — параметры зависящие от типа рельса, плана линии;
i — средний уклон начальной неровности, 2- 3‰;
k1 — коэффициент, зависящий от сопротивления балласта смещению шпал;
k2 — коэффициент, значение которого зависит от эпюры шпал k2 = 0,9 при эпюре 1600 шт./км, k2 = 1,0 при эпюре 1840 шт./км., k2 =1,08 при эпюре 2000 шт./км.
k3 — коэффициент, учитывающий влияние сопротивления повороту шпал по подкладкам и шпалам, он определяется.
3.4 Определение интервала температур закрепления плетей Имея экстремумы температур рельсов Тmin, Тmax, а также допуски и можно определить интервал закрепления рельсовых плетей.
Минимальная температура закрепления плети:
min[t3] = Tmax — (3.4.1).
Максимальная температура закрепления рельсовой плети:
max[t3] = Tmin — (3.4.2).
Закрепление плетей любой длины при любой температуре в пределах расчетного интервала гарантирует надежность их работы при условии полного соблюдения требований ТУ, касающихся конструкции и содержания бесстыкового пути. При этом следует учитывать, что закрепление петлей при очень высоких температурах может в отдельных случаях привести к образованию большого зазора при сквозном изломе плети в холодную погоду или к разрыву болтов в стыках уравнительных пролетов с большим расхождением концов рельсов.
3.5 Расчет на устойчивость принятой конструкции верхнего строения пути Требуется проверить возможность укладки бесстыкового пути из старогодных рельсов типа Р65 с железобетонными шпалами, скреплениями КБ и щебеночным балластом на участке длиной 10 000 м Забайкальской железной дороги, на котором имеются кривые с радиусом 550 м, и установить режимы его укладки при обращении электровозов ВЛ-85 с максимальной скоростью 80км/ч на протяжении всего участка.
Наибольшая температура рельсов:
t max max = +58°C;
наименьшая температура:
t min min = - 55 °C;
наибольшая температурная амплитуда:
ТА= 113 °C.
По таблице П. 2.1 и П. 2.2 «Технических указаний по устройству, укладке, содержанию и ремонту бесстыкового пути» определяем допускаемое повышение [Дtу] и понижение [Дtр] температуры рельсов и их амплитуды для каждого из элементов плана:
[Т]=[Дtу]+[Дtр] - 10;
Для прямых участков пути электровоза ВЛ-85 установлена скорость V=80км/ч.
Для балласта из щебня из твердых скальных пород:
Прямой участок.
[Дtр]=101°С;;
[Дtу]=58°С;
[Т]=159°С;
Для кривой радиусом 550 м и электровозами ВЛ-85 при V = 80км/ч:
[Дtр]=97°С.
[Дtу]=53°С;
[Т]=140°С;
Для всех элементов плана [Т] > ТА, т. е. укладка названной выше конструкции бесстыкового пути возможна.
Расчетный интервал закрепления плетей:
t3 =tу+tр — TА.
t = 58 + 101 — 113 = 46 — для прямой.
t = 53 + 97 — 113 = 37 — для кривой.
Границы интервала закрепления для каждого из элементов плана определяются по формулам (3.4.1 и 3.4.2):
Для прямых участков.
min t3 = 58 — 58 = 0 °C.
max t3 = - 55 + 101 = +46°С.
t3 = 46 — 0 = 46 0С.
Расчет на устойчивость прямого участка пути:
= (кгс/см2).
(кгс/см2).
Для кривой радиусом 550 м:
min t3 = 58 — 53 = 5 °C.
max t3 = -55 + 97 = 42 °C.
t3 = 42 + 5 = 470С Расчет на устойчивость кривого участка пути:
= (кгс/см2).
(кгс/см2).
Плеть на всем протяжении должна быть закреплена в одном интервале температур, границы которого определяются наиболее высокой из рассчитанных min t3 и наиболее низкой из рассчитанных max t3.
При определении расчетного интервала для всего блок участка длиной 10 000 м принимается наибольшее значение min tз и наименьшее max tз.
Отсюда tmin = 5 єС.
tmax = 42 єС.
?t3 = 47 єС.
В соответствии с таблицей 3.1 ТУ оптимальный интервал температуры закрепления плетей на Забайкальской железной дороге, на Петровск-заводской дистанции пути составляет 35 ± 5 єС. Он попадает в верхнюю часть расчетного интервала.
Укладка бесстыкового пути на блок участке возможна. Плети должны быть закреплены в интервале от +30 до +40 єС.
Закрепление плетей любой длины при любой температуре в пределах расчетного интервала гарантирует надежность их работы при условии полного соблюдения требований ТУ. При этом необходимо учитывать, что закрепление при очень высоких температурах может привести к образованию зазора более 50 мм, при сквозном изломе плети в холодную погоду или разрыву болтов в стыках уравнительных пролетов с большим расхождением концов рельсов.
Зазор л, мм, образовавшийся при изломе плети, пропорционален квадрату фактического понижения температуры Дtр по сравнению с температурой закрепления и определяется по формуле:
лР65 = 0,24 ДtР / r (3.5.1).
где: r — погонное сопротивление, кН/см, продольному перемещению рельсовых плетей, зимой, при смерзшемся балласте, при нормативном натяжении клеммных и закладных болтов значение r можно принимать равным 25 Н/мм.
При принятой максимальной температуре закрепления +40°C и наименьшей температуре рельсов в Петровск-заводском районе -51°C, фактическое понижение температуры ДtР будет равно:
ДtР=40 — (-55) = 95 °C.
Величина зазора при разнице температур в 91 °C будет равна:
лР65=0,24Ч95І/25 = 86,6 мм Так как при условии лР65? 50 мм не выполняется, то требуется понизить границу интервала закрепления.
Максимально возможную разницу температур, при которой будет выполняться условие лР65? 50 мм можно определить по формуле:
ДtР = Ч л / 0,24.
ДtР = 95 °C.
В данном случае максимально возможная температура закрепления плетей будет равна:
max tz = (-55) + 95 = 40 °C.
с учетом минимально возможной температуры закрепления плетей.
t min= 5 °C возможный интервал закрепления составит Дtz = 40 — 5 = 35 °C. Из всего выше изложенного следует, что укладка бесстыкового пути на участке данного пути возможна, закрепление плетей должно быть произведено в интервале от +30°C до +40°C. Для анализа температурной работы средней части бесстыкового пути целесообразно построить диаграмму его температурной работы (Лист 3).
Лист 3.
3.6 Определение допускаемых скоростей движения поездов по условию прочности пути Определим при заданных условиях эксплуатации напряжения в элементах верхнего строения пути и по ним максимально допустимые скорости движения поездов по условию прочности пути.
Допущения расчета:
1. В расчетах принимается условие, что силы, действующие на путь независимы друг от друга;
2. Горизонтальные поперечные (боковые) силы, а также крутящие моменты из-за экцентриситета приложения вертикальных сил, в расчетах учитываются коэффициентом f..
3. В качестве «маячных» шпал выбираются шпалы, расположенные против пикетных столбиков. Верх концов «маячных» шпал с наружной стороны рельса за пределами скреплений должен быть окрашен яркой несмываемой краской, а шпала и промежуточные рельсовые скрепления на ней должны соответствовать следующим требованиям:
— чтобы «маячная» шпала не смещалась, она должна быть хорошо подбита;
— при скреплениях КБ-65 закладные болты на ней затянуты, а типовые клеммы заменены клеммами с уменьшенной высотой ножек. При отсутствии клемм с уменьшенной высотой ножек допускается в отдельных случаях клеммы на «маячных» шпалах не устанавливать;
В качестве контрольных сечений на «маячных» шпалах принимаются: при скреплениях КБ-65- боковая грань подкладки.
Независимо от конструкции скреплений типовые подрельсовые прокладки-амортизаторы на «маячных» шпалах заменяются полиэтиленовыми или другими с низким коэффициентом трения.
Последовательность расчета:
Все расчетные значения подсчитываем для летних и зимних условий эксплуатации и для пяти значений скоростей движения V1 = 50 км/ч; V2 = 60 км/ч; V3 = 70 км/ч; V4 = 80 км/ч; V5 = 90 км/ч;
Коэффициент относительной жесткости рельсового основания и рельса:
kл.з = (3.6.1).
где — модуль упругости рельсового основания при летних и зимних условиях эксплуатации, кг/см2;
Е — модуль упругости рельсовой стали, кгс/см2;
J — момент инерции рельса относительно его центральной горизонтальной оси, см4.
kлето. = = 0,0139.
kзима. = = 0,0148.
kg = 0.1 + 0.2 (3.6.2).
где — статический прогиб рессорного подвешивания, мм; составляет 156 мм, для полувагона — 48 мм.
Результаты расчета сведены в таблицу 3.1.
Таблица 3.1. — Расчет коэффициента жёсткости.
V1 = 50 км/ч. | V2 = 60 км/ч. | V3 = 70 км/ч. | V4 = 80 км/ч. | V5 = 90 км/ч. | ||
kg(ВЛ85). | 0,164. | 0,177. | 0,190. | 0,203. | 0,215. | |
kg(вагон). | 0,308. | 0,350. | 0,392. | 0,433. | 0,475. | |
Сила инерции, кгс, связанная со строением обрессоренных масс находится по формуле:
Рр = kg (Pcm — q) (3.6.3).
где Pcm — статическая нагрузка от колеса рельс, кг. Для ВЛ85 — 11 500 кг, для вагона — 15 000 кг;
q — относительный к колесу вес необрессоренных частей, кг. Для ВЛ85 — 2 760 кг, для вагона — 995 кг.
Результаты расчета сведем в таблицу Таблица 3.2. Расчет сил инерции.
V1 = 50 км/ч. | V2 = 60 км/ч. | V3 = 70 км/ч. | V4 = 80 км/ч. | V5 = 90 км/ч. | ||
Рр (ВЛ85). | 1434,26. | 1546,31. | 1658,36. | 1770,41. | 1882,46. | |
Рр (вагон). | 4318,21. | 4901,85. | 5485,29. | 6068,83. | 6652,38. | |
Среднее значение силы инерции определяется по формуле:
(3.6.4).
Таблица 3.3. — Расчет среднего значения силы инерции.
V1 = 50 км/ч. | V2 = 60 км/ч. | V3 = 70 км/ч. | V4 = 80 км/ч. | V5 = 90 км/ч. | ||
(ВЛ85). | 1075,69. | 1159,73. | 1243,77. | 1327,81. | 1411,85. | |
(вагон). | 3238,66. | 3676,31. | 4113,97. | 4554,63. | 4989,28. | |
Средняя динамическая нагрузка колеса на рельс, кгс:
Рср = Рст + (3.6.5.).
Результаты расчета сведем в таблицу Таблица 3.4. — Средняя динамическая нагрузка.
V1 = 50 км/ч. | V2 = 60 км/ч. | V3 = 70 км/ч. | V4 = 80 км/ч. | V5 = 90 км/ч. | ||
Рср (ВЛ85). | 12 575,69. | 12 659,73. | 12 743,77. | 12 827,81. | 12 911,85. | |
Р ср (вагон). | 18 238,66. | 18 676,31. | 19 113,97. | 19 551,63. | 19 989,28. | |
Среднее квадратическое отклонение сил инерции, возникающих за счет колебаний кузова на рессорах, кгс, определяем как:
Sp = 0.08Pp (3.6.6).
Результаты расчета сведем в таблицу.
Таблица 3.5. — Среднee квадратическое отклонение сил инерции.
V1 = 50 км/ч. | V2 = 60 км/ч. | V3 = 70 км/ч. | V4 = 80 км/ч. | V5 = 90 км/ч. | ||
Sр (ВЛ85). | 114.74. | 123.70. | 132.67. | 141.63. | 150.60. | |
Sр (вагон). | 345.46. | 392.14. | 438.82. | 485.51. | 532.19. | |
Сила инерции, связанная с колебанием не рессорных масс:
Рип = (3.6.7).
где — коэффициент, учитывающий изменение величины колеблющейся массы пути на железобетонных шпалах по сравнению с путем на деревянных шпалах;
— коэффициент, учитывающий влияние жёсткости пути на уклон динамической неровности;
в — коэффициент, учитывающий влияние типа рельса на образование динамической неровности на пути;
г — коэффициент, учитывающий влияние рода балласта на образование динамической неровности на пути;
l — расстояние между осями шпал, 51 см.
= L = 0.261.
Результаты расчета сведем в таблицу Таблица 3.6. — Колебание необрессоренных масс.
V1 = 50 км/ч. | V2 = 60 км/ч. | V3 = 70 км/ч. | V4 = 80 км/ч. | V5 = 90 км/ч. | ||
(ВЛ85). | 989,57. | 1195,42. | 1403,91. | 1615,05. | 1828,84. | |
(ВЛ85). | 1093,44. | 1320,89. | 1551,27. | 1784,57. | 2020,80. | |
(вагон). | 861,72. | 1058,87. | 1264,30. | 1478,00. | 1699,97. | |
(вагон). | 952,17. | 1170,02. | 1397,01. | 1633,14. | 1878,40. | |
Среднее квадратическое отклонение от силы инерции, возникающей при прохождении колесом неровности на пути, кгс:
Sип = 0,707Рип (3.6.8).
Результаты расчета сведем в таблицу Таблица 3.7. — Отклонение от силы инерции при прохождении колесом неровностей.
V1 = 50 км/ч. | V2 = 60 км/ч. | V3 = 70 км/ч. | V4 = 80 км/ч. | V5 = 90 км/ч. | ||
(ВЛ85). | 699.63. | 845.16. | 992.57. | 1141.84. | 1292.99. | |
(ВЛ85). | 773.06. | 933.87. | 1096.75. | 1261.69. | 1428.71. | |
(вагон). | 609.23. | 748.62. | 893.86. | 1044.94. | 1201.88. | |
(вагон). | 673.18. | 827.20. | 987.68. | 1154.63. | 1328.03. | |
Сила инерции, связанная с наличием изолированной неровности на колесе, кгс:
= ymax (3.6.9).
где ymax — максимальный дополнительный прогиб рельса при прохождении колесом косинусоидальной неровности, 1,47;
— коэффициент, учитывающий отношение необрессоренной массы колеса и массы пути, 0,403;
е0 — наибольшая расчетная глубина изолированной неровности на колесе. для ВЛ85 — 0,047, для вагона — 0,067.
Результаты расчета сведем в таблицу Таблица 3.8 — Сила инерции, связанная с наличием изолированной неровности на колесе.
V1 = 50 км/ч. | V2 = 60 км/ч. | V3 = 70 км/ч. | V4 = 80 км/ч. | V5 = 90 км/ч. | ||
(ВЛ85). | 6282,10. | 6282,10. | 6282,10. | 6282,10. | 6282,10. | |
(ВЛ85). | 7670,11. | 7670,11. | 7670,11. | 7670,11. | 7670,11. | |
(вагон). | 6282,10. | 6282,10. | 6282,10. | 6282,10. | 6282,10. | |
(вагон). | 7670,11. | 7670,11. | 7670,11. | 7670,11. | 7670,11. | |
Среднее квадратическое отклонение от силы инерции, возникающей при качении колес, имеющих изолированные неровности, кгс:
= (3.6.10).
Результаты расчета сведем в таблицу Таблица 3.9 — Среднее квадратическое отклонение, возникающее при качении колес.
V1 = 50 км/ч. | V2 = 60 км/ч. | V3 = 70 км/ч. | V4 = 80 км/ч. | V5 = 90 км/ч. | ||
(ВЛ85). | 1570,53. | 1570,53. | 1570,53. | 1570,53. | 1570,53. | |
(ВЛ85). | 1917,53. | 1917,53. | 1917,53. | 1917,53. | 1917,53. | |
(вагон). | 1570,53. | 1570,53. | 1570,53. | 1570,53. | 1570,53. | |
(вагон). | 1917,53. | 1917,53. | 1917,53. | 1917,53. | 1917,53. | |
Сила инерции, возникающая при движении колеса, имеющего непрерывную неровность, кгс:
Рннк = (3.6.11).
где К1 — коэффициент, характеризующий степень неравномерности образования проката поверхности колес, 0,23;
d — диаметр колеса по кругу катания. Для ВЛ85 — 125 мм, для вагона — 95 мм.
Результаты расчета сведем в таблицу Таблица 3.10 — Сила инерции, возникающая при движении колеса, имеющего непрерывную неровность.
V1 = 50 км/ч. | V2 = 60 км/ч. | V3 = 70 км/ч. | V4 = 80 км/ч. | V5 = 90 км/ч. | ||
(ВЛ85). | 232,81. | 335,25. | 456,31. | 596,00. | 754,31. | |
(ВЛ85). | 294,53. | 424,13. | 577,29. | 754,01. | 954,29. | |
(вагон). | 232,66. | 335,02. | 456,01. | 595,60. | 753,81. | |
(вагон). | 293,52. | 422,67. | 575,30. | 751,41. | 951,00. | |
Среднее квадратическое отклонение, которое учитывает силы инерции возникающие при движении колеса, имеющего непрерывную неровность.
= (3.6.12).
Результаты расчета сведем в таблицу Таблица 3.11 — Среднее квадратическое отклонение, возникающее при при движении колеса, имеющего непрерывную неровность.
V1 = 50 км/ч. | V2 = 60 км/ч. | V3 = 70 км/ч. | V4 = 80 км/ч. | V5 = 90 км/ч. | ||
(ВЛ85). | 52,38. | 75,43. | 102,67. | 134,10. | 169,72. | |
(ВЛ85). | 66,27. | 95,43. | 129,89. | 169,65. | 214,72. | |
(вагон). | 52,35. | 75,38. | 102,60. | 134,01. | 169,61. | |
(вагон). | 66,04. | 95,10. | 129,44. | 169,07. | 213,98. | |
Среднее квадратическое отклонение динамической вертикальной нагрузки колеса на рельс, S, кгс, определяется по формуле, в которой учитывается то, что 5% осей имеют изолированную неровность на колесе и 95% - плавную неровность:
S = (3.6.13).
Результаты расчета сведем в таблицу Таблица 3.12 — Динамическая вертикальная нагрузка колеса на рельс.
V1 = 50 км/ч. | V2 = 60 км/ч. | V3 = 70 км/ч. | V4 = 80 км/ч. | V5 = 90 км/ч. | ||
(ВЛ85). | 792,83. | 926,46. | 1065,89. | 1210,07. | 1358,38. | |
(ВЛ85). | 893,76. | 1039,19. | 1191,78. | 1350,23. | 1513,78. | |
(вагон). | 758,13. | 918,12. | 1060,60. | 1211,62. | 1370,54. | |
(вагон). | 872,07. | 1015,12. | 1169,55. | 1334,12. | 1508,06. | |
Максимальная динамическая нагрузка от колеса на рельс, кгс:
(3.6.14).
где л — нормирующий множитель, определяющий вероятность события, л = 0,70.
Результаты расчета сведем в таблицу.
Таблица 3.13 — Максимальная динамическая нагрузка колеса на рельс.
V1 = 50 км/ч. | V2 = 60 км/ч. | V3 = 70 км/ч. | V4 = 80 км/ч. | V5 = 90 км/ч. | ||
(ВЛ85). | 13 130,67. | 13 308,254. | 13 489,895. | 13 674,858. | 13 862,71. | |
(ВЛ85). | 13 201,32. | 13 387,164. | 13 578,014. | 13 772,969. | 13 971,49. | |
(вагон). | 18 788,25. | 19 318,99. | 19 856,39. | 20 399,76. | 20 948,66. | |
(вагон). | 18 849,10. | 19 386,90. | 19 932,65. | 20 485,51. | 21 044,92. | |
Максимальная эквивалентная нагрузка для расчетов напряжений в рельсах от изгиба и кручения, кгс:
(3.6.15).
где — ординаты линии влияния изгибающих моментов рельса в сечениях пути, расположенных под колесными нагрузками от осей экипажа, смежных с расчетной осью,.
Величина м назначается в зависимости от величины kx, где х — расстояние между расчетной осью и соседними осями экипажа. Для локомотива ВЛ85 х = 290 см, для вагона х = 185 см.
Результаты расчета сведены в таблицу 3.15.
Таблица 3.14. — Расчет расстояний.
х. | kx, лето. | kx, зима. | м, лето. | м, зима. | ||
ВЛ65. | 4,03. | 4,29. | 0,0024. | 0,0069. | ||
5,36. | 0,0066. | |||||
вагон. | 2,57. | 2,73. | — 0,1058. | — 0,0859. | ||
Таблица 3.15 — Максимальная эквивалентная нагрузка для расчетов напряжений на рельсах от изгиба и кручения.
V1 = 50 км/ч. | V2 = 60 км/ч. | V3 = 70 км/ч. | V4 = 80 км/ч. | V5 = 90 км/ч. | ||
(ВЛ85). | 13 243.85. | 13 422.192. | 13 604.589. | 13 790.308. | 13 978.917. | |
(ВЛ85). | 13 288.10. | 13 474.516. | 13 665.946. | 13 861.481. | 14 060.582. | |
(вагон). | 16 858.60. | 17 343.04. | 17 834.13. | 18 331.19. | 18.833.80. | |
(вагон). | 17 282.40. | 17 782.60. | 18 290.76. | 18 806.03. | 19 327.84. | |
Максимальная эквивалентная нагрузка для расчетов напряжений и сил в элементах подрельсового основания, кгс:
(3.6.15).
где — ординаты линии влияния в прогибах пути, расположенных под колесными нагрузками от осей экипажа, смежных с расчетной осью,.
Величина м назначается по тому же критерию, что и м.
Результаты расчета сведены в таблицу 3.17.
Таблица 3.16. — Расчет расстояний.
х. | kx, лето. | kx, зима. | м, лето. | м, зима. | ||
ВЛ65. | 4,03. | 4,29. | — 0,0256. | — 0,0185. | ||
вагон. | 2,57. | 2,73. | — 0,0228. | — 0,0337. | ||
Таблица 3.17 — Максимальная эквивалентная нагрузка для расчетов напряжений на рельсах от изгиба и кручения.
V1 = 50 км/ч. | V2 = 60 км/ч. | V3 = 70 км/ч. | V4 = 80 км/ч. | V5 = 90 км/ч. | ||
(ВЛ85). | 12 806.22. | 12 981.633. | 13 161.106. | 13 343.901. | 13 529.585. | |
(ВЛ85). | 12 974.96. | 13 159.289. | 13 348.63. | 13 542.068. | 13 739.08. | |
(вагон). | 18 372.41. | 18 893.17. | 19 420.59. | 19 953.98. | 20 492.91. | |
(вагон). | 18 234.46. | 18 757.51. | 19 288.51. | 19 826.62. | 20 371.28. | |
Максимальное напряжение в подошве рельса от его изгиба под воздействием момента М, кг/см2:
у0 = (3.6.17).
где W — момент сопротивления рельса относительно его подошвы. Для рельсов Р65 W = 436 см3.
Результаты расчета сведем в таблицу Таблица 3.18. — Максимальное напряжение в подошве рельса от его изгиба кг/см2.
V1 = 50 км/ч. | V2 = 60 км/ч. | V3 = 70 км/ч. | V4 = 80 км/ч. | V5 = 90 км/ч. | ||
(ВЛ85). | 546,33. | 553,68. | 561,21. | 568,87. | 576,65. | |
(ВЛ85). | 514,82. | 522,04. | 529,46. | 537,03. | 544,75. | |
(вагон). | 695,44. | 715,42. | 735,68. | 756,19. | 776,92. | |
(вагон). | 669,57. | 688,95. | 728,64. | 738,60. | 748,82. | |
Максимальное напряжение в кромках подошвы рельса, кг/см2 :
укп = f (3.6.18).
где f — коэффициент перехода от осевых напряжений в подошве рельса к кромочным. Он равен для ВЛ85 f = 1.50, для вагона f = 1.48.
Результаты расчета сведем в таблицу Таблица 3.19. — Максимальное напряжение в подошве рельса от его изгиба кг/см2.
V1 = 50 км/ч. | V2 = 60 км/ч. | V3 = 70 км/ч. | V4 = 80 км/ч. | V5 = 90 км/ч. | ||
(ВЛ85). | 819,48. | 830,54. | 841,82. | 853,31. | 864,97. | |
(ВЛ85). | 772,23. | 783,07. | 794,18. | 805,56. | 817,12. | |
(вагон). | 1029,26. | 1058,81. | 1088,82. | 1119,16. | 1149,87. | |
(вагон). | 990,97. | 1019,65. | 1048,79. | 1078,33. | 1108,25. | |
Максимальное напряжение в кромках головки рельса, кг/см2:
укп = (3.6.19).
где zг и zп— расстояния от нейтральной оси до наиболее удаленных волокон соответственно на головке и подошве рельса. zг= 9,87 см и zп= 8,13 см.
Результаты расчета сведем в таблицу Таблица 3.20. — Максимальное напряжение в кромках головки рельса кг/см2.
V1 = 50 км/ч. | V2 = 60 км/ч. | V3 = 70 км/ч. | V4 = 80 км/ч. | V5 = 90 км/ч. | ||
(ВЛ85). | 799,85. | 810,62. | 821,61. | 832,85. | 844,25. | |
(ВЛ85). | 753,71. | 764,28. | 775,16. | 786,25. | 797,53. | |
(вагон). | 1011,20. | 1040,25. | 1069,71. | 1099,51. | 1129,66. | |
(вагон). | 973,57. | 1001,75. | 1030,37. | 1059,41. | 1088,81. | |
Максимальное напряжение в шпале на смятие под подкладкой, кг/см2:
уш = (3.6.20).
где w — площадь подрельсовой подкладки, w = 518 см2; lш — расстояние между шпалами, lш = 51 см.
Результаты расчета сведем в таблицу.
Таблица 3.21. — Максимальное напряжение в шпале на смятие под подкладкой кг/см2.
V1 = 50 км/ч. | V2 = 60 км/ч. | V3 = 70 км/ч. | V4 = 80 км/ч. | V5 = 90 км/ч. | ||
(ВЛ85). | 8,76. | 8,89. | 9,00. | 9,12. | 9,28. | |
(ВЛ85). | 9,45. | 9,59. | 9,73. | 9,87. | 10,00. | |
(вагон). | 12,57. | 12,93. | 13,29. | 13,65. | 14,02. | |
(вагон). | 13,29. | 13,67. | 14,06. | 14,44. | 14,85. | |
Максимальное напряжение в балласте, кг/см2:
уб = (3.6.21).
где — площадь полушпалы с учётом изгиба, = 3092 см2.
Результаты расчета сведем в таблицу Таблица 3.21. — Максимальное напряжение в балласте кг/см2.
V1 = 50 км/ч. | V2 = 60 км/ч. | V3 = 70 км/ч. | V4 = 80 км/ч. | V5 = 90 км/ч. | ||
(ВЛ85). | 1,47. | 1,49. | 1,51. | 1,53. | 1,55. | |
(ВЛ85). | 1,58. | 1,61. | 1,63. | 1,65. | 1,68. | |
(вагон). | 2,11. | 2,17. | 2,23. | 2,29. | 2,35. | |
(вагон). | 2,23. | 2,29. | 2,35. | 2,42. | 2,49. | |
Расчетная формула для определения нормальных напряжений уh, кг/см2, в балласте (в том числе и на основной площадке земляного полотна) на глубине h от подошвы шпал по расчетной вертикали:
уh = уh1 + уh2 + уh3 (3.6.22).
где уh1 и уh3 — напряжения от воздействия соответственно первой и третьей шпалы, лежащих по обе стороны от расчетной шпалы;
уh2 — напряжение от воздействия второй (расчетной, маячной) шпалы в сечении пути под расчетным колесом.
уh2 = убр л (2,55С2 + (0,635С1 — 1,275С2) m) (3.6.23).
где убр — напряжение под расчетной шпалой на балласте, осредненное по ширине шпалы. для расчетной шпалы убр = уб.
m — переходной коэффициент от осредненного по ширине шпалы давления на балласт к давлению под осью шпалы;
С — коэффициенты изгиба шпалы, определяемые в зависимости от глубины балластного слоя h = 55 см (от подошвы шпал) и ширины нижней постели шпалы b, см :
С1 = (3.6.24).
C2 = (3.6.25).
m = (3.6.26).
С1 = = 0,25.
C2 = = 0,12.
Результаты расчета сведем в таблицы Таблица 3.23. — Переходной коэффициент.
V1 = 50 км/ч. | V2 = 60 км/ч. | V3 = 70 км/ч. | V4 = 80 км/ч. | V5 = 90 км/ч. | ||
(ВЛ85). | 1,53. | 1,52. | 1,52. | 1,51. | 1,51. | |
(ВЛ85). | 1,50. | 1,49. | 1,49. | 1,48. | 1,48. | |
(вагон). | 1,38. | 1,37. | 1,35. | 1,34. | 1,33. | |
(вагон). | 1,35. | 1,34. | 1,33. | 1,31. | 1,30. | |
Таблица 3.24 -Напряжение от воздействия второй (расчётной) шпалы в сечении пути под расчётным колесом, кг/см2.
V1 = 50 км/ч. | V2 = 60 км/ч. | V3 = 70 км/ч. | V4 = 80 км/ч. | V5 = 90 км/ч. | ||
(ВЛ85). | 0,318. | 0,322. | 0,327. | 0,331. | 0,336. | |
(ВЛ85). | 0,343. | 0,348. | 0,353. | 0,358. | 0,363. | |
(вагон). | 0,455. | 0,468. | 0,481. | 0,494. | 0,507. | |
(вагон). | 0,480. | 0,494. | 0,508. | 0,522. | 0,536. | |
Напряжения в балласте под соседними с расчетной шпалами определяются из условия максимальной динамической нагрузки расчетного колеса, расположенного под расчетной шпалой, и средних нагрузок от остальных колес, кг/см2:
убс = (3.6.27).
в этом случае для двухосных тележек определяется как:
= под шпалой № 1 (3.6.28).
= под шпалой № 3 (3.6.29).
где l1 — 2 — расстояние между первой и второй осямитележки.
Результаты расчета сведем в таблицы.
Таблица 3.25 -Напряжение в балласте под шпалами, кг/см2.
Шпала № 1. | V1 = 50 км/ч. | V2 = 60 км/ч. | V3 = 70 км/ч. | V4 = 80 км/ч. | V5 = 90 км/ч. | |
(ВЛ85). | 0,98. | 1,00. | 1,01. | 1,03. | 1,04. | |
(ВЛ85). | 1,02. | 1,03. | 1,05. | 1,06. | 1,08. | |
(вагон). | 1,71. | 1,76. | 1,81. | 1,86. | 1,91. | |
(вагон). | 1,70. | 1,74. | 1,79. | 1,84. | 1,89. | |
Таблица 3.26 — Напряжение в балласте под шпалами, кг/см2.
Шпала № 3. | V1 = 50 км/ч. | V2 = 60 км/ч. | V3 = 70 км/ч. | V4 = 80 км/ч. | V5 = 90 км/ч. | |
(ВЛ85). | 1,03. | 1,05. | 1,06. | 1,07. | 1,09. | |
(ВЛ85). | 1,07. | 1,09. | 1,10. | 1,12. | 1,13. | |
(вагон). | 1,40. | 1,44. | 1,49. | 1,53. | 1,57. | |
(вагон). | 1,45. | 1,49. | 1,53. | 1,58. | 1,62. | |
Напряжения от воздействия первой и третьей шпалы, лежащих по обе стороны от расчетной шпалы, кг/см2:
уh1 = 0.25уб, 1 — 2 А (3.6.30).
уh3 = 0.25уб, 2 — 3 А (3.6.30).
где уб, 1 — 2 и уб, 2 — 3 — средние значения напряжений по подошве соседних с расчетной (маячной) шпал.
А — коэффициент, учитывающий расстояние между шпалами lш, ширину шпалы b, глубину h и соответственно углы И между вертикальной осью и направлениями от кромки шпалы до расчетной точки, А = 0,295.
Результаты расчета сведем в таблицы.
Таблица 3.27 -Значение напряжений в первой шпале, кг/см2.
Шпала № 1. | V1 = 50 км/ч. | V2 = 60 км/ч. | V3 = 70 км/ч. | V4 = 80 км/ч. | V5 = 90 км/ч. | |
(ВЛ85). | 0,048. | 0,049. | 0,049. | 0,050. | 0,051. | |
(ВЛ85). | 0,050. | 0,051. | 0,052. | 0,052. | 0,053. | |
(вагон). | 0,080. | 0,082. | 0,084. | 0,087. | 0,089. | |
(вагон). | 0,080. | 0,083. | 0,085. | 0,087. | 0,089. | |
Таблица 3.28 — Значение напряжения в третьей шпале, кг/см2.
Шпала № 3. | V1 = 50 км/ч. | V2 = 60 км/ч. | V3 = 70 км/ч. | V4 = 80 км/ч. | V5 = 90 км/ч. | |
(ВЛ85). | 0,049. | 0,050. | 0,51. | 0,051. | 0,052. | |
(ВЛ85). | 0,052. | 0,053. | 0,053. | 0,054. | 0,055. | |
(вагон). | 0,069. | 0,071. | 0,072. | 0,074. | 0,077. | |
(вагон). | 0,071. | 0,073. | 0,075. | 0,077. | 0,080. | |
Таблица 3.29 — Значение в земляном полотне, кг/см2.
Шпала № 3. | V1 = 50 км/ч. | V2 = 60 км/ч. | V3 = 70 км/ч. | V4 = 80 км/ч. | V5 = 90 км/ч. | |
(ВЛ85). | 0,416. | 0,421. | 0,427. | 0,433. | 0,439. | |
(ВЛ85). | 0,445. | 0,451. | 0,458. | 0,464. | 0,471. | |
(вагон). | 0,603. | 0,620. | 0,637. | 0,655. | 0,672. | |
(вагон). | 0,632. | 0,650. | 0,668. | 0,687. | 0,705. | |
Для наглядности по полученным значениям напряжений в элементах ВСП составляем графики (Лист № 4 и Лист № 5), на которые также наносим предельные значения оценочных критериев прочности пути.
Таблица 3.30. — Оценочные критерии прочности пути:
Критерии. | Вид подвижного состава. | Значения оценочных критериев прочности, кг/см2,. при грузонапряженности в млн. nrv/ брутто на км. в год. | ||||
более 50. | 50 — 25. | 24 — 10. | менее 10. | |||
укп. | локомотивы. | |||||
вагоны. | ||||||
уш. | локомотивы. | |||||
вагоны. | ||||||
уб. | локомотивы. | 4,0. | 4,2. | 4,5. | 5,0. | |
вагоны. | 2,6. | 3,0. | 3,5. | 4,0. | ||
уh. | локомотивы. | 1,0. | 1,0. | 1,1. | 1,2. | |
вагоны. | 0,8. | 0,8. | 0,9. | 1,0. | ||
Выводы:
По результатам оценки воздействия подвижного состава на путь (таблица 3.30), по условию обеспечения прочности пути напряжения в кромке головки рельса, в кромке подошвы рельса, в шпалах, в балласте и в земляном полотне не превышает предельно допустимые значения.
4. Разработка технологических процессов.
4.1 Порядок составления технологического процесса Путевые работы можно выполнять комплексно или раздельно. При комплексном методе все работы, например, сплошную смену рельсов, шпал, балласта на данном участке выполняют одновременно.
Ведущей частью комплекса работ по ремонту пути являются основные работы, выполняемые в «окно» определенной продолжительности. В связи с этим проектирование технологического процесса производства сложного комплекса работ начинаем с основных работ, выполняемых в «окно», и работ.
выполняемых после «окна». Затем приступаем к проектированию подготовительных и отделочных работ с разработкой графика распределения по дням.
Порядок составления технологического процесса:
1. Составление задания на проведение капитального ремонта (Приложение А1).
2. Определяем среднюю ежедневную производительность ПМС, фронт работ в «окно», с учетом периодичности предоставления «окон».
3. Составляем схемы формирования рабочих поездов.
4. Определяем продолжительность «окна».
5. Заполняем ведомость затрат труда по технологическим нормам.
6. Разрабатываем график производства работ в «окно» и после «окна» и график распределения работ по дням.
7. Устанавливаем численный состав производственных рабочих ПМС и разрабатываем организационную структуру ПМС.
8. Составляем пояснительную записку.
4.2 Условия производства работ Капитальный ремонт пути выполняется на перегоне, протяжением 10 000 м в «окна» продолжительностью 10 часов.
Капитальный ремонт пути выполняется в следующей последовательности:
ѕ ремонт водоотводов и уборка лишнего балласта с обочины земляного полотна. В ведомости трудозатрат данные работы не учтены, на графике не показаны;
ѕ замена старой рельсошпальной решетки на новую; смонтированную из новых материалов верхнего строения пути; выправка пути на старом балласте;
ѕ очистка щебеночного балласта машиной СЧ-601 (RМ-80 или RM-76), выправка пути в плане и профиле с пополнением балластной призмы щебеночным балластом, стабилизация и оправка балластной призмы (СЧ-601, ХДВ, ВПР, ДСП, ПБ);
ѕ выгрузка щебеночного балласта в местах нехватки, окончательная выправка пути в плане, профиле и по уровню с постановкой по проектным отметкам, стабилизация балластной призмы, отделка пути (ХДВ, ВПР, ДСП, ПБ);
ѕ шлифовка рельсов.
Работы по удалению асбестового балласта и глубокой очистке щебеночного, производится при различных характеристиках балластной призмы, при этом производительность машинного комплекса устанавливается по расчету с учетом различных условий работы (табл. 4.1).
Работы по уборке лишнего балласта с обочины земляного полотна и ремонту водоотводных сооружений выполняются до начала основных работ по отдельным технологическим процессам, затраты труда не учитываются, на графике работы не показаны.
Для обеспечения бесперебойной работы машин с участка удаляются препятствия, которые могут вызвать повреждение или незапланированную остановку работающей техники, снимаются заземлители опор контактной сети, путевые знаки и обустройства (типа ПОНАБ, ДИСК, УКСПС и т. д.).
При демонтаже рельсошпальная решетка укладывается в пакеты звеньями длиной по 25 м и грузится на платформы с применением путеукладочного крана УК-25/9−18. Все платформы для перевозки пакетов оборудованы съемным оборудованием УСО. Перетяжка пакетов звеньев по составу производится моторными платформами МПД-2.
Перед демонтажем звеньев рельсошпальная решетка вывешивается электробалластером. Спрессовавшийся в шпальных ящиках балласт продавливается под вывешенные шпалы специальным пробивщиком.
Машина щебнеочистительная СЧ-601 предназначена для ремонта и реконструкции балластной призмы пути без съема путевой решетки. При этом возможны следующие режимы работы:
" ПОЛНЫЙ ОТБОР" - вырезка загрязненного балласта и транспортировка в заранее подготовленный подвижной состав либо на откос земляного полотна;
" ОЧИСТКА" - вырезка загрязненного балласта и сортировка на две фракции. При этом мелкая (отходы) — удаляется на откос земляного полотна либо загружается в подвижной состав, крупная — укладывается во вновь формируемую балластную призму.
Таблица 4.1 Производительность машины СЧ-601.
Условия работ. | Технологическая производительность машины СЧ-601, м3/ч. | Протяженность участка, в % к общему фронту работ. | ||
При удалении асбестового балласта. | При глубокой очистке щебеночного балласта с укладкой геотекстиля. | |||
При обычных условиях. | ||||
На участке с уплотненным балластом. | ||||
На участке с сильнозагрязненным и уплотненным балластом. | 210−240. | |||
Очистка щебеночного балласта производится машиной СЧ-601 на глубину 25 см с применением подъемного устройства ПРУ. Вырезанный балласт поступает на очистное устройство для отделения засорителей. Очищенный щебень возвращается в путь, а засорители грузятся в составы для засорителей СЗ-240−6 и вывозятся с перегона.
Выработка машины СЧ-601 по очистке щебеночного балласта составляет 500 м в час.
Выправка пути со сплошной подбивкой шпал производится:
ѕ машиной ВПО-3000 в плане и по уровню сразу после укладки рельсошпальной решетки;
ѕ машиной ВПР-02 после глубокой очистки балласта и досыпки нового щебня;
ѕ машиной ВПР-02 в отделочных работах после пополнения балластной призмы щебнем до нормы.
Щебеночный балласт доставляется на место работ и выгружается из хоппер-дозаторов.
Динамический стабилизатор стабилизирует балластную призму после каждой работы машины ВПР-02.
Отделка пути, планировка междупутья и обочины земляного полотна выполняется планировщиком балласта.
Уборка балласта из-под подошвы рельса осуществляется вручную.
Рельсы после укладки в путь подвергаются профильной шлифовке рельсошлифовальным поездом типа РШП-48. Работу выполняют после завершения отделочных работ.
После выполнения основных работ, устранения выявленных неисправностей участок производства работ открывается для движения первых двух поездов со скоростью 25 км/ч, последующих — согласно состояния пути, но не более 60 км/ч.
4.3 Суточная производительность базы ПМС На Забайкальской железной дороге путевые работы с рельсошпальной решетке на железобетонных шпалах осуществляет (на участке Петровский Завод — Ерофей Павлович) ПЧ-1 (ст. Петровский Завод).
Полуавтоматическая сборочная линия ПЗЛ-100 производства хабаровского опытно-конструкторского бюро «Путевые машины» позволяет собирать до 1000 метров РШР в смену.
Ежедневная производительность ПМС :
S = (4.1).
Q — заданный годовой объем работ по капитальному ремонту;
T — количество рабочих дней в сезон капитальных ремонтов? N = 130 дней;
— число дней резерва на случай не предоставления «окон», несвоевременного завоза материалов ВСП, ливневых дождей и других форс-мажорных причин — обычно берется (0,1…0,2)Т.
S = = 0,4977 км = 497,7 500 м.
4.4 Фронт работ в «окно».
Фронт работ «окон»:
Lфр = S*n (4.2).
n — переодичность предоставления «окон», n = 3.
Lфр = 0,4977*3 = 1,493 км = 1500 м (кратное 25 м).
Общее количество звеньев, укладываемых на фронте работ.
Nзв = (4.3).
где — длина звена, .
Nзв = = 60 звеньев.
4.5 Расчет длин рабочих поездов технологического комплекса Составлению схем формирования рабочих поездов придаётся большое значение. Успешная работа ПМС в «окно» в значительной степени зависит от своевременного и правильного формирования рабочих поездов, как на путевой производственной базе, так и на прилегающих к ремонтируемому перегону станциях. Схемы формирования поездов должны соответствовать типовым, установленным Инструкцией по обеспечению безопасности движения поездов при производстве путевых работ. Длины поездов рассчитывают в соответствии с длинами отдельных единиц подвижного состава. Машины выбираем из типового технологического процесса.
Длина путеразборочного (путеукладочного) поезда определяется как:
Lук (p) = lук + (4.5.1).
где lук — длина укладочного крана УК — 25/9−18, lук = 43,9 м;
- длина одной четырехосной платформы грузоподъемностью 60 т., = 14,6 м;
— длина моторной платформы МПД, = 16,2 м;
— длина платформы прикрытия, = 14,6 м.;
— длина локомотива (тепловоз — 2ТЭ10), = 37 м.;
— количество моторных платформ МПД,.
nпак — количество пакетов РШР;
nпак = = = 12 = 24 платформы где nяр — число звеньев в пакете;
k — число платформ, занятых одним пакетом, так как у нас рельсы длиной 25 м, то k=2.
Lук (p) = 43,9 + = 533,6 м.
Длина хоппёр-дозаторного состава:
Lхд = lлок + (4.5.2).
где — объем очищенного щебня,.
— остаток щебня после очистки 70% балласта Толщина слоя балласта под шпалой составит после очистки:
h = = 0.42 м.
Для обеспечения необходимой толщины балласта под шпалой, необходимо дополнительно произвести подсыпку, толщиной до 20 см, до нормируемой толщины.
— вместимость кузова хоппер-дозатора, ;
— длина одного хоппер-дозатора, = 10,9 м.;
Nхоп = = 32,927 = 33 шт.
Длина ХДВ № 1:
Lхд1 = 37 + 10,9 + 24,5 = 420,5 м.
ХДВ № 2 предназначен для досыпки в шпальные ящики и отделку. Считается объем засыпной балластной шпалы:
2,7.
Тогда все шпалы на = 1500 м займут объем в слое балласта: 0,087*2*1500 = 261 м3.
— объем балласта, необходимого на досыпку.
Количество хоппер-дозаторов:
Nхоп = = 18,33 = 19 хоппер-дозаторов.
Длина ХДВ № 2:
Lхд2 = 37 + 10,9 + 24,5 = 261,3 м.
Длина состава выправочно-подбивочной машиной ВПО-3−3000.
LВПО = lвм + lm + lлок (4.5.3).
где lвм — длина ВПО-3−3000, lвм = 27,87 м.
LВПО = 27,87 + 24,5 + 17 = 69 м Длина состава электробалластера ЭЛБ:
LЭЛБ = lЭЛБ + lm + lлок (4.5.4).
где lЭЛБ = 16,97 м., длина машины ЭЛБ.
lЭЛБ = 16,97 + 24,5 + 17 = 57,97 58 м.
Длина машины ПБ-01.
LПБ-01 = 13,31 м.
Длина машины ДСП-С:
LДСП-П = 18,20 м.
Длина щебнеочистительного поезда с машиной СЧ-601.
LСЧ-601 = lСЧ + lm + lсост.зас (4.5.5).
lсост.зас =.
где lсост.зас — длина состава для засорителей, м;
— длина вагона для засорителей, = 14,6 м.;
— количество вагонов для засорителей,.
— длина конечного вагона,.
lСЧ — длина щебеноочистительной машины, lСЧ-601 = 39,24 м.;
lсост.зас =.
LСЧ-601 = 39,24 + 160,6 + 24,5 = 224,34 225 м.
4.6 Разработка технологического процесса капитального ремонта пути с глубокой очисткой щебня и заменой путевой решетки (вариант 1).
Основные работы в «окно» ведутся производственным составом ПМС с применением двух машин СЧ-601. Продолжительность «окна» 14 часов, фронт работ — 1500 м.
Необходимо выполнить:
ѕ закрытие перегона;
ѕ снятие напряжения;
ѕ очистка щебня двумя щебнеочистительными машинами СЧ-601;
ѕ резка плетей длиной 25,5 м.;
ѕ демонтаж рельсошпальной решетки путеукладочным краном.
УК25/9−18;
ѕ планировка балласта автотранспортной техникой — грейдерами и бульдозерами;
ѕ укладка рельсошпальной решетки путеукладочным краном.
УК25/9−18;
ѕ сборка и сболчивание стыков;
ѕ регулировка рельсошпальной решетки в плане с постановкой на ось;
ѕ выгрузка ХДВ № 1;
ѕ работа электробалластера ЭЛБ;
ѕ выгрузка ХДВ № 2;
ѕ выгрправка пути машиной ВПО-3−3000;
ѕ планировка балласта машиной ПБ-1;
ѕ стабилизация пути машиной ДСП;
ѕ приварка соединенителей;
ѕ регулировка контактной сети;
ѕ открытие перегонов.
Определение времени развертывания работ.
«Окна» для ремонтных и строительных работ предоставляются в светлое время суток. В целях сокращения задержек поездов в период предоставления «окон» должны повсеместно следующее организационно-технические мероприятия, позволяющие повысить использование пропускной и провозной способности:
а) организация обращения соединенных поездов;
б) применение устройств, позволяющих обеспечивать движение в противоположном направлении (по неправильному пути) по сигналам локомотивных светофоров;
в) организация двустороннего пакетного движения поездов в период «окна» на временно однопутном перегоне";
г) открытие временных постов;
д) укладка съездов между главными путями на перегоне для установления однопутного движения только на части перегона;
е) использование передвижных тяговых подстанций на электрифицированных линиях;
ж) концентрация работ различного вида на закрытом перегоне;
з) выделение наиболее квалифицированных поездных диспетчеров для дежурства в дни предоставления «окон»;
и) создание в отделениях и управлениях дорог оперативных штабов для разработки составления технологии работы участка в период «окна»;
к) тщательное изучение всеми причастными работниками порядка пропуска поездов в дни «окон»;
л) составление именных графиков для машинистов, которые обучены вождению соединенных поездов;
м) сгущение вариантных; графиков движения поездов до начала и после окончания «окна».
Необходимую продолжительность «окна» устанавливают в зависимости от вида и объема ремонтно-путевых работ, конструкции и числа используемых машин и механизмов, применяемой технологии работ, а также конкретных условий каждого участка, на котором они выполняются. В целях сокращения общей продолжительности закрытия перегонов и повышения эффективности использования машин и механизмов «окна» для капитального среднего ремонтов цуга, как правило, должны предоставляться продолжительностью 6−8 часов.
Началом «окна» для ремонтных и строительных работ считается:
— на не электрифицированных участках время издания приказа дежурным поездным диспетчером о фактически состоявшимся закрытии перегона после освобождения его от всех поездов, кроме хозяйственных;
— на электрифицированных участках — время снятия напряжения в контактной сети, указанное в приказе энергодиспетчера после фактически состоявшегося закрытия перегона для движения всех поездов, кроме хозяйственных.
Окончанием «окна» считается:
— на электрифицированных участках, оборудованных автоблокировкой — время подачи напряжения в контактную сеть, указанное в приказе энергодиспетчера, после получения дежурным поездным диспетчером от ответственного представителя дистанции пути уведомления об окончании работ и отправлении с перегона всех хозяйственных поездов;
— на не электрифицированных участках, оборудованных автоблокировкой — время получения дежурным поездным диспетчером от ответственного представителя дистанции пути уведомления об окончании и отправлении с перегона всех хозяйственных поездов;
— на участке, не оборудованных автоблокировкой, — время получения дежурным поездным диспетчером от ответственного представителяч дистанции пути уведомления об окончании работ после прибытия с закрытого перегона всех хозяйственных поездов.
Предварительно определимся с поправочными коэффициентами, учитывающих сколько пар поездов проходит через участок в сутки, которые будут необходимы в дальнейших расчетах:
Таблица 4.1. — Поправочные коэффициенты.
Поправочные коэффициенты. | Поправочные коэффициенты. | ||||||||
Число пар поездов. в сутки Виды работ. | До12. | 13 — 18. | 19−25. | 26−33. | 34−42. | 43−52. | 53−63. | ||
k1. | Подготовительные работы. | 1,15. | 1,20. | 1,25. | 1,30. | 1,35. | 1,40. | 1,45. | |
k2. | Основные работы в «окно». | 1,10. | 1,11. | 1,13. | 1,15. | 1,17. | 1,19. | 1,21. | |
k3. | Основные работы после «окна». | 1,15. | 1,20. | 1,25. | 1,30. | 1,35. | 1,40. | 1,45. | |
k4. | Отделочные работы. | 1,08. | 1,08. | 1,08. | 1,08. | 1,08. | 1,08. | 1,08. | |
k5. | Работы на звеносборочной базе. | 1,08. | 1,08. | 1,08. | 1,08. | 1,08. | 1,08. | 1,08. | |
Продолжительность «окна» определяется:
Токно = Тразв + Тосновн + Тсв (4.6.1).
где Тразв — время развертывания работ, мин.:
Тразв. = t1 + t2 + t3 + t4 + t5 (4.6.2).
где t1 — - интервал времени, складывающийся из времени на оформление закрытия перегона, на пробег первой машины к месту работ (расчетная величина), к тому же на электрифицированных дорогах добавляется дополнительно 8 мин. на снятие напряжения в контактной сети;
При расстоянии от станции до места работ равной 2 км. при скорости движения 50 км/ч и времени на закрытие перегона в 7 мин.:
t1 = tоф + (4.6.3).
где l — расстояние до станции, 2 км.;
V — скорость следования на перегон двух машин СЧ-601; tоф — время закрытия перегона.
t1 = 7 + = 9,4 мин.
Окончательно: t1 = 8 + = 17,4 мин.
t2 — время, необходимое на зарядку щебнеочистительных машин.
Перед резкой плетей, направляются работники техотдела для разбивки плетей на звенья, также направляется бригада из 2 монтёров пути. При затратах на один рез 2,0 чел.-мин. необходимо произвести 52 реза. При затратах труда с учетом коэффициента на добавочное время и пропуск поездов — 1,25, продолжительность работ составит 130 мин — 2 ч. 10 мин.
t3 — интервал времени между началом работ по очистке щебня машиной СЧ-601, разрядки и началом работ по резке стыков:
t3 = k m lщ (4.6.4).
где lщ — длина участка на котором должен быть очищен щебень машиной СЧ-601, мин.;
m — техническая норма машинного времени на очистку 1 км пути, мин;
k — коэффициент, учитывающий время на отдых и пропуск поездов по соседнему пути k = 1,19.
lщ = LCЧ-601 + lТБ (4.6.5).
где lТБ — интервал по технике безопасности, 50 м.
lщ = 225 + 50 = 275 м.
t3 = 16.12.
Время работы щебеноочистительной машины СЧ-601:
ТСЧ-601. = tоч.щ + tзар+ tукл. ГТ + tразр (4.6.6).
где tоч.щ — время на очистку щебня машиной СЧ-601;
tукл. ГТ — время на укладку геотекстиля для СЧ-601;
tзар, tразр — время на зарядку и разрядку машины СЧ-601, 30 мин.
Производительность щебнеочистительной машины СЧ-601 — 500 м3/час, тогда при фронте работ 1,5 км, Wоч.щ = 4050 м3:
tоч.щ = = 8,1 час = 486 мин.
в нашем случае (при среднем расчете: при фронте работ 1,5 км, Wоч.щ = 4050 м3) задействовано два комплекса машин СЧ-601, первый будет производить работы по фронту работ — 750 м (Wоч.щ = 2025 м3), второй — 750 м (Wоч.щ = 2025 м3).
При подсчете времени принимаем расчет по первой машине:
t 1 оч.щ = = 4,05 ч. = 243 мин.
Укладка геотекстиля первой машиной СЧ-601:
t 1 yкл.ГТ = (4.6.7).
где Q — количество остановок для зарядки рулонов геотекстиля:
Q = = 10 остановок.
tзар — время на зарядку одного рулона геотекстиля, 15 мин.;
t 1 укл.ГТ = 10*15 = 150 мин.
Аналогичны расчеты и для второй машины.
Тогда, ТСЧ-601. = 243 + 30 + 150 + 30 = 453 мин.
t4 — интервал времени между началом резки стыков и началом разборки пути путеразборочным поездом:
t4 = Nщ б (4.6.8).
где Nщ — техническая норма времени очистки 1 км пути щебнеочистительной машиной СЧ-601;
t4 = = 13,17 = 13 мин.
t5 — интервал времени между началом разборки пути и началом укладки пути путеукладчиком, он определяется временем разборки первых 100 м пути (тем самым, обеспечивается дальнейшая работа бульдозера и планировщика):
t5 = Nразб б (4.6.9).
где Nразб — техническая норма времени на разборку одного звена.
t5 = = 16,5 мин.
В итоге получаем время развертывания работ:
Тразв. = 17,5 + 30 + 453 + 13 + 16,5 = 517 мин.
Определение времени на укладку пути Время на укладку — это время работы ведущей машины.
Тосновн = Тук (4.6.10).
Тук = (4.6.11).
где — техническая норма времени на укладку одного звена (2,604 мин). — число укладываемых звеньев (60 шт).
Тук =.
Определение времени свертывания работ Время после укладки последнего звена состоит из следующих интервалов:
Тсв = (4.6.12).
— интервал времени между началом работ по укладке рельсошпальной решетки и началом работ бригады, выполняющей постановку накладок и сболчивание стыков:
= (4.6.13).
где — техническая норма времени на укладку одного звена (2,604);
= = 72 мин.
— интервал времени между окончанием постановки накладок со сбалчиванием стыков и окончанием работы бригады, выполняющей рихтовку пути:
= (4.6.14).
— фронт работ бригады, выполняющей сбалчивание стыков, 50 — 100 м.;
— технологический разрыв между бригадой по рихтовке пути и предыдущей бригадой — 50 м.
= = 12,3 мин.
— интервал времени между окончанием рихтовки пути и окончанием выгрузки щебня из ХДВ № 2:
= (4.6.15).
— расстояние от хвоста первого хоппер-дозатора до конца фронта работ;
— рабочая скорость хоппер-дозатора при выгрузке щебня: 2 …5 км/ч.;
L1 = lбрр + lб + Lук + lбп + L1хд (4.6.16).
lбп - безопасное расстояние между второй частью (питающей) путеукладчика и хоппер-дозатором (lбп = 100 м);
lбрр — фронт работ проводящих рихтовку пути (lбрр = 50 м);
L1 = 50 +50 + 533,6 + 100 + 420,5 = 1154,1 м.
= = 16,4 мин.
— интервал времени между окончанием работ по выгрузке щебня из хоппер-дозаторного состава и окончанием работ по подъемке РШР электробалластером ЭЛБ, мин.:
= *60 (4.6.17).
— длина ЭЛБ с локомотивом, (58 м);
= *60 = 7,6 мин.
— интервал времени между окончанием работ по подъемке РШП электробалластером и выгрузкой щебня из ХДВ № 2, мин.:
= *60 (4.6.18).
= *60 = 5,3мин.
— интервал времени между окончанием работ по выгрузке ХДВ № 2 и окончанием работ по выправке пути машиной ВПО-3−3000, мин:
= *60 + tзар. ВПО (4.6.19).
tзар. ВПО — время на зарядку ВПО-3−3000: 15 мин.;
— рабочая скорость машины ВПО, км/ч.
— интервал по технике безопасности, 100 м.
= *60 + 15 = 16,8 мин.
— интервал времени между окончанием работ ВПО-3−3000 и окончанием работ машины ПБ-01, мин.:
= *60 (4.6.20).
= *60 = 2,7 мин.
— интервал времени между окончанием работ машины ПБ-01 и окончанием работ машины ДСП-С, мин.:
= *60 (4.6.21).
= *60 = 4,6 мин.
— интервал времени между окончанием работ машины ДСП-С и по окончании работ по приварке рельсовых соединений, мин.:
= (4.6.22).
фронт работ по приварке соединений, 25 м;
— интервал по технике безопасности, 50 м.
= = 9,3 мин.
— интервал времени на у окончание работ по регулировке контактной сети, мин.:
= *60 (4.6.23).
— производительность машины ДГку (1,5 км/ч).
= *60 = 3 мин.
— открытие перегона (5 мин.), выезд путевых машин (8 мин.).
tcв = 72 + 12,3 + 16,4 + 7,6 + 5,3 + 16,8 + 2,7 + 4,6 + 9,3 + 3 + 5 + 10 = 165 мин.
Таким образом, полное время окна составит:
Т0 = 517 + 156 + 165 = 838 мин. = 14 часов После проверки пути делается запись в книге ПУ-28 и отправление рабочих поездов нВ станцию, представителями «XR и ПЧ даются уведомления о подаче напряжения и об открытии перегона, после чего поездной диспетчер (LYW) открывает перегон для дальнейшего движения поездов.
Скорость после открытия перегона первым одному — двум составам в 25 км/ч, далее не более 60 км/ч.
Производственный состав Капитальный ремонт пути выполняется работниками пути в следующем составе Руководящий и обслуживающий персонал.
Заместитель начальника (производитель, руководитель работ) — 1 чел.
Старший дорожный мастер — 1 чел.
Дорожный мастер — 3 чел.
Бригадиры пути (не освобожденные входят в состав монтеров пути) — 3.
Сигналисты — 4 чел Телефонист — 1 чел.
Итого: (без не освобожденных бригадиров пути) — 13 чел.
Колонна подготовительных, основных и отделочных работ состоит из 7-ми бригад численностью 76 монтеров пути:
Состав бригад монтеров пути бригада № 1 — 16 чел; бригада № 2 — 12 чел; бригада № 3 — 6 чел; бригада № 4 — 16чел; бригада № 5 — 14 чел; бригада № 6 — 4 чел; бригада № 7 — 8 чел Таблица 4.2. — Состав машинистов.
№ пп. | Наименование машин. | Количество машин (составов). | Количество машинистов. | |
Путеукладочный кран УК-25/9−18 с МПД. | ||||
Моторные платформы. | ||||
Четырехосные платформы УСО. | ; | |||
Автогрейдер ДЗ-98. | ||||
Бульдозер Т-170. | ||||
Щебнеочистительная машина СЧ-601. | ||||
Машина ВПО-3000. | ||||
Динамический стабилизатор пути ДСП. | ||||
Электробалластер ЭЛБ. | ||||
Планировщик балласта ПБ. | ||||
Хопперная вертушка. | ||||
Сварочная установка. | ||||
Электростанции. | ||||
Итого: | ||||
Всего: 131 чел.
Кроме того, бригада машинистов рельсошлифовального поезда типа РШП-48 — 12 чел. Примечание: если по условиям производства работ по дням для монтеров пути возникают технологические перерыва, то в эти дни рабочие используются на других видах работ, вне данного технологического процесса. Потребность материалов на ремонт 1 км. пути Рассчитаем количество км. приходящихся на прямые участки и кривые.
Протяженность кривых участков — 34,8%.
Протяженность прямых участков — 63,2%.
Всего 10 км — 100%.
Рассчитаем протяженность прямых участков.
(10 • 63,2) /100 = 6,32 км — прямых Всего кривые составят: 10 — 6,32 = 3,48 км На 1 км. кривых R< 1200 м эпюра равна 2000 шпал, на всех остальных кривых и прямых эпюра равна 1840 шпал на 1 км.
Определим количество шпал на участках:
0,348 • 10 • 2000 = 6 960 шпал.
0,632 • 10 • 1840 = 11 630 шпалы.
(11 630 + 6 960) /100 = 1859 шпал Определим количество шпал на 1,5 км.: 1859• 1,45 = 2 696 шпалы Потребность материалов для ремонта 1,45 км. пути занесём в таблицу.
Таблица 4.3. — Материалы.
№. | Наименование материалов. | Единицы измерения. | Кол-во на 1,5 км., шт. | |
Рельсы новые Р-65. | Погонные м. | 3 000. | ||
Шпалы железобетонные. | шт. | 2 700. | ||
Накладки шестидырные. | шт. | |||
Болты Р-65 с гайками. | шт. | |||
Шайбы пружинные. | шт. | |||
Подкладки. | шт. | 5 655. | ||
Клеммы. | шт. | 11 310. | ||
Болты клеммные. | шт. | 11 310. | ||
Шайбы двух витковые. | шт. | 22 620. | ||
Болты закладные. | шт. | 11 310. | ||
Плоские шайбы. | шт. | 11 310. | ||
Прокладки под рельс. | шт. | 5 655. | ||
Прокладки под подкладку. | шт. | 5 655. | ||
Втулки изолирующие. | шт. | 11 310. | ||
Гайки закладных болтов. | шт. | 11 310. | ||
Щебень. | м3. | 1 350. | ||
4.7 Разработка технологического процесса капитального ремонта пути с глубокой вырезкой балласта и заменой путевой решетки (вариант 2).
Основные работы в «окно» ведутся производственным составом ПМС с применением машины СЧУ-800 для глубокой вырезки балластной призмы под рельсовой решеткой, укладки геотекстиля на поверхность среза. Продолжительность «окна» 10 часов, фронт работ — 1500 м.
Необходимо выполнить:
ѕ закрытие перегона;
ѕ снятие напряжения;
ѕ резка рельс;
ѕ демонтаж рельсошпальной решетки путеукладочным краном УК25/9;
ѕ планировка балластной призмы автогрейдером;
ѕ укладка рельсошпальной решетки путеукладочным краном УК25/9;
ѕ сборка и сболчивание стыков;
ѕ регулировка рельсошпальной решетки в плане с постановкой на ось;
ѕ глубокая вырезка щебня под РШР машиной СЧУ-800;
ѕ выгрузка из ХДВ — 70%;
ѕ вырправка пути машиной ВПО-3−3000;
ѕ выгрузка из ХДВ 30%;
ѕ планировка балласта машиной ПБ-1;
ѕ стабилизация пути машиной ДСП;
ѕ приварка рельсовых соединенителей;
ѕ регулировка контактной сети;
ѕ открытие перегонов.
Продолжительность «окна» определяется:
Токно = tразв + tведущ + tсв (4.7.).
где tразв — время развертывания работ, мин.:
tведущ — время работы ведущей машины;
tсв — время, необходимое для свёртывания работ и открытия перегона для пропуска поездов.
Определение времени развертывания работ.
tразв. = t1 + t2 + t3 (4.7.1).
где t1 — - интервал времени, складывающийся из времени на оформление закрытия перегона, на пробег первой машины к месту работ (расчетная величина), к тому же на электрифицированных дорогах добавляется дополнительно 8 мин. на снятие напряжения в контактной сети;
При расстоянии от станции до места работ равной 2 км. при скорости движения 50 км/ч и времени на закрытие перегона в 7 мин.:
t1 = tоф + (4.6.3).
где l — расстояние до станции, 2 км.;
V — скорость следования на перегон машины СЧУ-800; tоф — время закрытия перегона.
t1 = 7 + = 9,4 мин.
Окончательно: t1 = 8 + = 17,4 мин.
t2 — интервал времени между началом работ по резке рельс и началом работ по разборке РШР, мин.
t2 = (4.7.3).
— длина первого путеразборочного поезда, м;
— интервал по ТБ, 100 м.;
— длина звена, 25,5 м.;
— норма времени на 1 рез, = 2 мин.;
— количество резов на звене,.
— количество монтеров пути, занятых резкой рельс,.
t2 = = 59 мин.
Время, затрачиваемое на разборку РШР краном УК25/9 — 18, мин.
tразб = Nразб (4.7.4).
Nразб — норма времени на разборку 10 звеньев, Nразб = 29,34 мин.
Nзв — количество звеньев на всем фронте работ, Nзв = 60.
tразб = 29,34* = 209,5 мин.
t3— интервал времени между началом работ по снятию РШР и укладки новой РШР, мин.:
t3 = Nразб (4.7.5).
t3 = 29,34* = 21 мин.
Время, затрачиваемое на укладку новой РШР краном УК25/9 — 18, мин.
tукл = Nукл (4.7.6).
Nукл — норма времени на укладку 10 звеньев, Nукл = 26,04мин.
tукл = 26.04* = 186 мин.
tразв. = 17,4 + 59 + 21 = 97.4 мин.
Определение времени основных работ.
tосн. = t1 + t2 + t3 + tвырез.б (4.7.7).
t1 — интервал времени между началом работ по укладке РШР и началом работ по сбалчиванию стыков, мин:
t1 = Nукл (4.7.8).
t1 = 26,04 = 72,5 мин.
t2 — интервал времени между началом работ по сбалчиванию стыков и началом работ по рихтовке пути:
t2 = Nукл (4.7.9).
— фронт работ по сбалчиванию стыков, = 25 м.;
t2 = 26,04 = 7,8 мин.
t3 — интервал времени безопасности между началом работ по рихтовке пути и началом работ по зарядке машины для глубокой вырезки балласта:
= (4.7.10).
— длина укладочного крана, = 34,9 м.
t3 = 26,04 = 6,8 мин.
Определение времени глубокой вырезки и очистки балласта:
tвырез.б . = tСЧУ-800 = tзарядка+ tвырез + tразрядка (4.7.11).
где tзарядка, tразрядка — время на зарядку/разрядку машины СЧУ-800, tзарядка, tразрядка = 30 мин.;
tвырез — время работы по вырезке балласта.
= *60 (4.7.12).
— объем выбранного щебня;
— производительность машины СЧУ-800, = 600 м3/час.
= *60 = 405 мин.
tвырез.б . = 30 + 405 + 30 = 465 мин.
Вместо укладки геотекстиля будем использовать материал «Криогелит».
Необходимый объем рассчитаем по формуле.
Vкриогелит = lсч * hкриогелит * Lфр (4.7.13).
Где lсч — ширина срезаемого балласта;
hкриогелит — толщина слоя «Криогелит»;
Lфр — фронт, срезаемого и очищаемого балласта.
Vкриогелит = 4,5 * 0,01 * 1500 = 67,5 м3 — это потребность в «Криогелите».
tосн. = 72.5 + 7.8 + 6.8 + 465 = 552 мин = 9 часов 12 мин.
Определение времени свертывания работ Время после укладки последнего звена состоит из следующих интервалов:
Тсв = (4.7.14).
— интервал времени между окончанием работ по разрядке щебнеочистительной машины и окончанием работ по выгрузке щебня из хоппер-дозаторного состава:
= (4.7.15).
где — техническая норма времени на укладку одного звена (2,604);
= = 12,4 мин.
— интервал времени между окончанием работ по выгрузке щебня из хоппра-дозатора и окончанием работ по подъемке РШР электробалластером.
= (4.7.16).
= = 13.8 мин.
— интервал времени между окончанием работ по подъемке РШР электробалластером, и выгрузке щебня из второго хоппер-дозаторного состава:
= (4.7.17).
= = 10 мин.
— интервал времени между окончанием работ по выгрузке ХДВ № 2 и окончанием работ по выправке пути машиной ВПО-3−3000, мин:
= *60 + tзар. ВПО (4.7.18).
tзар. ВПО — время на зарядку ВПО-3−3000: 15 мин.;
— рабочая скорость машины ВПО, км/ч.
— интервал по технике безопасности, 100 м.
= *60 + 15 = 16,8 мин.
— интервал времени между окончанием работ ВПО-3−3000 и окончанием работ машины ПБ-01, мин.:
= *60 (4.7.19).
= *60 = 2,7 мин.
— интервал времени между окончанием работ машины ПБ-01 и окончанием работ машины ДСП-С, мин.:
= *60 (4.7.20).
= *60 = 4,6 мин.
— интервал времени между окончанием работ машины ДСП-С и по окончании работ по приварке рельсовых соединений, мин.:
= (4.7.21).
фронт работ по приварке соединений, 25 м;
— интервал по технике безопасности, 50 м.
= = 9,3 мин.
— интервал времени на у окончание работ по регулировке контактной сети, мин.:
= *60 (4.6.23).
— производительность машины ДГку (1,5 км/ч).
= *60 = 3 мин.
— открытие перегона (5 мин.), выезд путевых машин (8 мин.).
tcв = 12,4 + 13,8 + 10 + 16,8 + 2,7 + 4,6 + 9,3 + 3 + 5 + 8 = 85,6 мин.
Таким образом, полное время окна составит:
Т0 = 97,4 + 552 + 85,6 = 735 мин. = 12 часов 15 мин.
После проверки пути делается запись в книге ПУ-28 и отправление рабочих поездов нВ станцию, представителями «XR и ПЧ даются уведомления о подаче напряжения и об открытии перегона, после чего поездной диспетчер (LYW) открывает перегон для дальнейшего движения поездов.
Скорость после открытия перегона первым одному — двум составам в 25 км/ч, далее не более 60 км/ч.
Производственный состав Капитальный ремонт пути выполняется работниками пути в следующем составе Руководящий и обслуживающий персонал.
Заместитель начальника (производитель, руководитель работ) — 1 чел.
Старший дорожный мастер — 1 чел.
Дорожный мастер — 3 чел.
Бригадиры пути (не освобожденные входят в состав монтеров пути) — 3.
Сигналисты — 4 чел Телефонист — 1 чел.
Итого: (без не освобожденных бригадиров пути) — 13 чел.
Колонна подготовительных, основных и отделочных работ состоит из 7-ми бригад численностью 64 монтеров пути:
Состав бригад монтеров пути бригада № 1 — 6 чел; бригада № 2 — 14 чел; бригада № 3 — 14 чел; бригада № 4 — 4 чел; бригада № 5 — 8 чел; бригада № 6 — 16 чел; бригада № 7 — 2 чел Таблица 4.4. — Состав машинистов.
№ пп. | Наименование машин. | Количество машин (составов). | Количество машинистов. | |
Путеукладочный кран УК-25/9−18 с МПД. | ||||
Моторные платформы. | ||||
Автогрейдер ДЗ-98. | ||||
Бульдозер Т-170. | ||||
Щебнеочистительная машина. СЧУ-800. | ||||
Машина ВПО-3000. | ||||
Динамический стабилизатор пути ДСП. | ||||
Электробалластер ЭЛБ. | ||||
Планировщик балласта ПБ. | ||||
Хопперная вертушка. | ||||
Электростанции. | ||||
Итого: | ||||
Всего: 120 чел.
Кроме того, бригада машинистов рельсошлифовального поезда типа РШП-48 — 12 чел.
Примечание: если по условиям производства работ по дням для монтеров пути возникают технологические перерыва, то в эти дни рабочие используются на других видах работ, вне данного технологического процесса.
Потребность материалов на ремонт 1 км. пути Рассчитаем количество км. приходящихся на прямые участки и кривые.
Протяженность кривых участков — 34,8%.
Протяженность прямых участков — 63,2%.
Всего 10 км — 100%.
Рассчитаем протяженность прямых участков.
(10 • 94,38) /100 = 9,438 км — прямых Всего кривые составят: 10 — 9,438 = 0,562 км На 1 км. кривых R > 1200 м эпюра равна 2000 шпал, на всех остальных кривых и прямых эпюра равна 1840 шпал на 1 км.
Определим количество шпал на участках:
0,348 • 10 • 2000 = 6 960 шпал.
0,632 • 10 • 1840 = 11 630 шпалы.
(11 630 + 6 960) /100 = 1859 шпал Определим количество шпал на 1,5 км.: 1859• 1,45 = 2 696 шпалы Потребность материалов для ремонта 1,45 км. пути занесём в таблицу.
Таблица 4.5. — Материалы.
№. | Наименование материалов. | Единицы измерения. | Кол-во на 1,5 км., шт. | |
Рельсы новые Р-65. | Погонные м. | 3 000. | ||
Шпалы железобетонные. | шт. | 2 700. | ||
Накладки шестидырные. | шт. | |||
Болты Р-65 с гайками. | шт. | |||
Шайбы пружинные. | шт. | |||
Подкладки. | шт. | 5 655. | ||
Клеммы. | шт. | 11 310. | ||
Болты клеммные. | шт. | 11 310. | ||
Шайбы двух витковые. | шт. | 22 620. | ||
Болты закладные. | шт. | 11 310. | ||
Плоские шайбы. | шт. | 11 310. | ||
Прокладки под рельс. | шт. | 5 655. | ||
Прокладки под подкладку. | шт. | 5 655. | ||
Втулки изолирующие. | шт. | 11 310. | ||
Гайки закладных болтов. | шт. | 11 310. | ||
Щебень. | м3. | 1 350. | ||
4.8 Технологический процесс замены инвентарных рельсов на бесстыковые рельсовые плети Характеристика участка пути:
Участок пути двухпутный, электрифицированный, оборудованный автоблокировкой. На участке укладки HIG выполнен капитальный ремонт пути.
Верхнее строение пути до укладки рельсовых плетей:
ѕ инвентарные рельсы типа Р65, длиной 25 м;
ѕ накладки инвентарные четырёхдырные;
ѕ рельсовые скрепления типа КБ65;
ѕ шпалы Ж/Б — 1840 шт на прямых участках и в кривых R 1200 м, 2000 шт в кривых R 1200 м.;
ѕ балласт щебеночный мощностью до 55 мм.;
ѕ изолирующие стыки тип АПАТЭК.
Верхнее строение пути после ремонта:
ѕ конструкция верхнего строения пути не изменяется;
ѕ инвентарные рельсы меняются на бесстыковые рельсовые плети длиной 800 м.
Условия проведения работ:
Замена инвентарных рельсов на РШП производится на пути со скреплениями ЖБР.
Технология производства работ по замене инвентарных рельсов плетями бесстыкового пути.
Рельсовые плети свариваются длиной до 800 м в рельсосварочном поезде (РСП) и транспортируются специальными поездами, оборудованными необходимыми приспособлениями (двухосными платформами в количестве 80 штук, на которых имеются специальные ролики, позволяющие одновременно перевозить 12 плетей). В голове платформ имеется вагон, на котором закрепляются концы плетей с одной стороны. Через этот вагон производится выгрузка плетей на перегоне. При этом длина выгружаемых плетей заранее определена и указана в заказе для рельсосварочного поезда. Выгрузка производится под прикрытием «окна» для капитального ремонта..
Замена инвентарных рельсов сварными плетями производится после пропуска не менее 350 тыс. т брутто груза в «окно» с использованием крана УК-25/9, оборудованного специальным приспособлением. После надвижки плетей производится погрузка снятых инвентарных рельсов тем же краном УК-25/9, оборудованным для перевозки рельсовых пакетов. После укладки сварных плетей необходима частичная выправка пути электрошпалоподбойками (до 10% шпал), рихтовка пути и оправка балластной призмы..
Определение необходимой продолжительности «окна».
Необходимая продолжительность «окна» равна:.
(4.8.1).
где: — время развёртывания работ на фронте до начала основной операции;
— время укладки пути на фронте работ;
— время свёртывания работ после выполнения основной операции по укладке.
(4.8.2).
где: мин — время необходимое на оформление закрытия перегонов, пробег машин к месту работ, снятие напряжения с контактной сети и ограждения места работ по схеме.
Посчитаем длину рельсовозного состава, состоящего из локомотива в голове состава, турного вагона, тележек с роликовыми каналами для плетей, платформами прикрытия и спускной платформой.
(4.8.3).
где: м — длина локомотива;
м — длина турного вагона;
М — длина порожней платформы;
М — длина платформы прикрытия;
— длина спускной платформы.
LР.С = 34 + 25 + 62*12,5 + 2*12,5 + 12,5 = 871,5 м.
Выгрузка одной пары плетей с учетом времени на закрепление концов в междупутье:
(4.8.4).
— скорость выгрузки плетей.
Следовательно, продолжительность всей выгрузки плетей (двух пар плетей) будет равна.
= t1 = 42*2 = 84 мин.
— интервал времени между началом выгрузки первой пары плетей и началом разболчивания закладных болтов гайковертом ПМГ.
мин, (4.8.5).
— длина уложенной плети, на которой начинает работу ПМГ.
Интервал времени между началом разболчивания пути гайковертом ПМГ и выходом бригады болтовщиков:
(4.8.6).
где lзв — длина звена, занимаемого гайковертом ПМГ, lзв= 25 м;
50 — интервал безопасности, м;
lбол — длина участка, занимаемого бригадой болтовщиков, lбол =25 м;
Ппмг — производительность гайковерта ПМГ, км/ч;
(4.8.7).
— техническая норма времени на отвинчивание гайки закладного болта, = 0,096 мин;
— количество гаек закладных болтов скреплений, отвинчиваемых на каждой 2-й шпале на фронте работ машиной ПМГ.
ППМГ = = 700 м/ч = 0.7 км/ч.
Подсчитаем производительность бригады болтовщиков:
(4.8.8).
— техническая норма времени на отвинчивание гайки закладного болта скрепления монтерами пути, = 0,42 мин;
— количество гаек закладных болтов скреплений, отвинчиваемое на каждой 3-й шпале на фронте работ монтерами пути, шт.;
— численность бригады болтовщиков, чел.
150 м/ч = 0,15 км/ч Интервал между началом разболчивания закладных болтов и началом снятия инвентарных рельсов и надвижки плетей.
(4.8.9).
где: — фронт работы бригады по разболчиванию стыков;
б — коэффициент, учитывающий потери времени на пропуск поездов по соседнему пути и на переходы по фронту работ, равен 1,15;
(4.8.10).
где: Сб — общие трудозатраты на фронте работ, чел.-мин:
(4.8.11).
где: — количество снимаемых болтов;
с — норма затрат труда на один снимаемый болт, равный 1,7 чел.-мин.
. (4.8.12).
чел.-мин.
м Посчитаем производительность путеукладочного крана, производящего замену инвентарных рельсов на плети бесстыкового пути:
(4.8.13).
— техническая норма времени на снятие одного звена, = 2,6 мин;
W — погрузка инвентарных рельсов, снятых с пути, и надвижка плети с учетом МКС, звено;
м/час = 0,242 км/ч Подсчитаем время на замену инвентаря на первую пару плетей с учетом зарядки надвижного приспособления:
(4.8.14).
а на всем участке соответственно.
= 2*382 = 764 мин. = 12 часов. 44 мин.
— интервал времени между окончанием смены инвентаря на плети и окончанием работы бригады болтовщиков, мин:
(4.8.15).
lбол — расстояние, занятое болтовщиками, lбол = 100 м;
— длина путеукладочного крана (34 м);
— длина платформы прикрытия (12,5 м).
Интервал времени между окончанием работы бригады болтовщиков и бригадой по введению плетей в температурный диапазон закрепления (натяжение плетей с помощью УНГ), мин:
. (4.8.16).
Подсчитаем производительность бригады по натяжению плетей:
(4.8.17).
— техническая норма времени на натяжение рельсовых плетей гидравлическими приборами УНГ, = 0,065 мин;
W — длина рельсовой плети с учетом МКС, которая растягивается гидравлическими натяжными приборами, м;
— интервал времени между окончанием работ по введению плетей в температурный интервал закрепления и окончанием работ по сплошному закреплению закладных болтов гайковертом ПМГ, мин:
.
— расстояние, занятое бригадой по введению плетей в температурный интервал закрепления, м, =100 м;
— длина участка занимаемого ПМГ, м, = 100 м.
= открытие перегона (5 мин.), выезд путевых машин (8 мин.).
Тогда продолжительность «окна» по замене инвентарных рельсов плетями бесстыкового составит:
. (4.8.18).
Т0 = 84 + 35 + 8,6 + 244,6 + 51,8 + 100 + 15 + 10 + 5 = 554 мин =.
= 9 часов 14 мин.
Организация работ по замене инвентарных рельсов плетями бесстыкового пути со сваркой до длины перегона.
Работы по замене инвентарных рельсов на рельсовые плети на скреплении ЖБР-65 со сваркой плетей в пути и постановкой в оптимальную температуру подразделяется на подготовительные и основные, которые выполняются в следующей последовательности:
Подготовительные работы.
Подготовительные работы выполняются на производственной базе, рельсосварочном предприятии и на перегоне.
На производственной базе производится распиловка деревянных шпал на полушпалки.
На платформу мотовоза грузятся: полушпалки с металлическими скользунами, рельсы с МКС длиной 12,5 м, гидравлические приборы с насосной станцией, электростанцией, станции с комплектом кабельной арматуры, ударные механизмы с клиновым упором.
На рельсосварочном предприятии машиной ПРСМ производится сварка двух контрольных образцов для определения фактического укорочения рельсов в результате оплавления и осадки металла.
Дефектоскопистом проверяется качество сварных стыков.
На перегоне производится выгрузка: рельсов КБС, полушпалок с металлическими скользунами.
На всем протяжении участка работ смазываются и опробуются закладные болты.
На прилегающих к участку работ с каждой стороны длиной по 50 м закладные болты подкрепляются.
Указанные работы в ведомости затрат труда учитываются, на графике производства работ не показаны.
Основные работы.
Работы выполняются на участке длиной 1500 м в «окно» продолжительностью 9 часов 14 мин. часов.
Количество ярусов в пакете звеньев.
Характеристика участка. | Род шпал. | Количество звеньев, укладываемых в пакет кранами. | ||
УК-25/9. | УК-25/9−18. | |||
Электротяга. | Деревянные Железобетонные. | |||
Тепловозная тяга. | Деревянные железобетонные. | |||
После проследования последнего графикового поезда, оформления закрытия перегона, снятия напряжения в контактной сети, ограждения места установленным порядком к месту работ прибывает мотовоз и производит выгрузку натяжных гидравлических приборов с насосной станцией, ударных механизмов, гаечных ключей ЭК-1, электростанции.
6 монтеров пути (бр. № 6) производит расшивку рельсовых плетей, закрепленных на полушпалках, снимают предохранительные башмаки на торцах плетей, подготавливают места для сварки стыков машиной ПРСМ: вырезают балласт в стыковых шпальных ящиках в подрельсовой зоне; укладывают полушпалки с металлическими скользунами на местах изгиба плети, производят обрезку концов плетей с болтовыми отверстиями, зачищают концы под сварку, ключами ЭК-1 отвинчивают гайки стыковых болтов, снимают болты и стыковые накладки.
К месту работ прибывает рабочий поезд состоящий по ходу движения из локомотива, специальной платформы с дизельным гайковертом № 1, моторной платформы МПД, комплекта платформ и путеукладочного крана УК-25/9−18.
На месте работ дизельный гайковерт № 1 съезжает с платформы и выполняет сплошное ослабление гаек закладных болтов на 2-х шпалах из 3-х на всем участке работ.
18 монтеров пути (бр. № 2, 3) торцовыми ключами отвинчивают оставшиеся закладные болты; на каждой 6-й шпале (кроме 3-й шпалы) пружинные клеммы сдвигают в монтажное положение и закрепляют. На каждом звене остаются закрепленными по две шпалы.
На всех остальных шпалах пружинные клеммы сдвигают в монтажные положение.
8 монтеров пути (бр. № 1) и 4 машиниста крана УК-25/9−18 устанавливают устройство для надвижки плетей, снимают уравнительные рельсы со сборным изолирующим стыком и инвентарные рельсы длиной, равной длине 1-й пары плетей.
При движении состава 8 монтеров пути распределяются следующим образом: 4 чел. составляют верхнюю бригаду стропальщиков, они же заняты на перетяжке; 2 чел. отвинчивают торцевыми ключами закладные болты, оставленные для пропуска крана, 2 чел. сдвигают пружинные клеммы в монтажное положение и следят за надвижкой плетей.
6 монтеров пути (бр. № 5) обрезают концы примыкающих плетей. Зачищают их под сварку.
К месту работ прибывает рельсосварочная машина ПРСМ в сцепе со специальной платформой, на которой погружен дизельный гайковерт № 2. На месте работ дизельный гайковерт съезжает с платформы, а машина ПРСМ производит сварку одной пары стыков способом подтягивания (передние концы рельсов КБС с примыкающими плетями).
Шлифовальными станками производится грубая и чистовая обработка сварных стыков, а дефектоскопист — ультразвуковым аппаратом проверяет качество сварки и производит соответствующую запись в журнале.
После укладки 1-й пары плетей работа крана УК-25/9−18 приостанавливается и производится разрядка приспособления для надвижки плетей.
12 монтеров пути (бригада № 4) на уложенных плетях сдвигают пружинные клеммы в проектное положение кроме 6-й шпалы и устанавливают скользящие прокладки.
10 монтеров пути (бр. № 5) снимают закладные сборки на длине 45 м со стороны изгиба плети, изгибают плеть в горизонтальной плоскости до совмещения торцов рельсов.
Сварочная машина ПРСМ переезжает по 2-й паре стыков и производит сварку правой и левой нитей способом предварительного изгиба.
Обработка и проверка стыков производится по вышеуказанному способу.
10 монтеров пути (бр. № 5) на правой и левой нитях выполняют горизонтальное выпрямление оставшейся части изгиба, восстанавливают закладные сборки и засыпают балласт в шпальных ящиках.
8 монтеров пути (бр. № 1) монтируют и устанавливают гидравлические приборы в стыках правой и левой нитей; 8 монтеров пути (бр. № 4) устанавливают на обе рельсовые плети ударные механизмы и монтируют клиновые упоры.
Машина ПРСМ возвращается за пределы 1-й пары сварных стыков и остается до окончания растягивания плетей.
Гидравлическими приборами производится растягивание плетей до расчетной величины.
Во время растягивания ударными механизмами производится простукивание плетей.
Руководитель работ контролирует удлинение плетей по контрольным рискам.
20 монтеров пути (бр. № 5, 6 монтеров пути бр. № 1 и 4 монтера пути бр. № 4) выполняют закрепление участка длиной 50 м со снятием прокладок и установкой клемм на каждой 6-й шпале в проектное положение.
После этого гидравлические приборы отключаются и вместе с ударными механизмами снимаются с пути.
2-я пара рельсовых плетей укладывается, сваривается и растягивается аналогичным порядком.
6 монтеров пути (бр. № 6) возвращаются к началу работ и выполняют вначале завинчивание гаек закладных болтов на каждой 3-й шпале (кроме 6-й шпалы), а затем отвинчивают болты на 6-й шпале и устанавливают клеммы в проектное положение. Затем к ним присоединяются 18 монтеров пути (бр. № 2, 3) и выполняют совместно работу на 1-й и 2-й паре плетей. На конце 2-й пары плетей к ним присоединяются 16 монтеров пути (бр. № 4 и 4 монтера пути бр. № 5).
Дизельный гайковерт № 2 выполняет сплошное закрепление гаек закладных болтов на 1-й и 2-й рельсовой плетях (кроме якорных участков по 50 м).
6 монтеров пути (бр. № 5) после удлинения плетей на расчетную величину на уравнительных рельсах производят обрезку концов до величины 5, 65 м с последующим сверлением болтовых отверстий, установкой накладок и сболчиванием стыков.
Работы по вводу рельсовых плетей бесстыкового пути в расчётный интервал температур закрепления выполняются во всех случаях, когда плети при укладке были закреплены при температуре ниже расчетной.
Ввод рельсовых плетей четного пути в расчетный интервал температур закрепления производится принудительным растяжением гидравлическим натяжителем типа ГНУ (установка ГНУ с двух сторон) с предварительным нагревом нагревательным устройством (НУ) по каждой рельсовой нити с анкерованием участков посередине пути.
Перед НУ группа монтеров из 5 человек (бригада № 6) по обоим ниткам производит встряхивание рельсовых нитей при помощи ударного устройства для постановки «контрольных» меток на расчетное удлинение по точкам.
Требуемая величина удлинения рельсовых плетей определяется по формуле:
Дl = (4.8.19).
где б = 0,118 — коэффициент температурного расширения рельсовой стали;
L — длина пути, м Дt = tрасч. — tукл = 35 — (+20) = +150С Здесь tрасч — расчетная температура закрепления плети на постоянный режим эксплуатации (+350С);
tукл — фактическая температура первичного состояния плети (+200С);
Дl =.
Для контроля за удлинением рельсовых плетей через каждые 50 м, относительно кромок шпал наносятся «контрольные» метки, для контроля нанесения последних, наносятся метки против кромки шпалы.
На подошве рельсовой плети от кромки шпалы, противоположной направлению растягивания, откладывают величину, соответствующую размеру удлинения плети в данном месте и закрепляют её меловой риской, служащей «контрольной» меткой.
Растяжение плети производится до тех пор, пока «контрольная» метка на рельсе не совместится с кромкой шпалы.
Требуемая величина удлинения плети: 141,6 мм (в одну сторону.
Удлинение плети, приходящееся на каждые 50 м, определяется как:
Дl50 = (4.8.20).
где n — количество меток на рельсовой плети;
Дl50 = = 8,85 мм.
Начиная от середины рельсовой плети (анкерного участка) на расстоянии 50 м, первая контрольная метка должна быть намечена на расстоянии 8,85 мм от кромки шпалы, вторая — на расстоянии 17,7 мм и т. д.
Данный расчет производится отдельно работниками ПМС и ПЧ, с целью контроля расчетов. Результаты расчета сверяются и при их совпадении приступают к работам. При постановке плети в температурный режим ведется ведомость учета подвижек плети относительно «контрольных» рисок.
В подготовительный период для создания анкерных участков уравнительные пролёты должны быть закреплены с усилием закладных болтов не менее — 20 кгс/м2.
С целью уменьшения величины трения между растягиваемой рельсовой плетью и подрельсовыми прокладками на каждой 15-ой шпале укладывают скользящие пары. Места их укладки отмечаются руководителем работ заранее.
Две пары рельсов уравнительного пролета, лежащие за растягиваемой плетью, заменяются на рельсы расчётной длины, которые доставляются к месту работ заранее.
В данной технологии работ предусмотрено растяжение плети с анкерованием по середине плети.
Длина анкерного участка со стороны подвижного конца определяется как:
lанк (4.8.21).
Nt = (4.8.22).
где Nt — необходимое усилие для создания расчётных удлинений в плетях; r — погонное сопротивление рельсов (при замерзшем балласте принимается равным 25 кН/м) или шпалах (при незамерзшем балласте — 7 кН/м; при неуплотненном балласте — 12 кН/м).
Е — модуль упругости рельсовой стали, Е = 2,1*105 МПаА.
F — поперечное сечение рельса Р65 — 82,56 см2.
Nt =.
lанк = 25 м.
после растяжения плеть закрепляется. Закрепление начинается от анкерного участка вслед за НУ, перед бригадой монтёров пути, убирающих сколящие прокладки. На участке 31 метр плеть закрепляется на каждой шпале, а на остальном протяжении — на каждой третьей.
Работа по окончательной выправке пути производится машиной «Duomatic» 09−32 CSM после укладки в пути рельсовых плетей и сбора инвентарных рельсов.
После проверки состояния пути, устранения выявленных неисправностей перегон открывается для движения поездов со скоростью первых двух поездов не более 25 км/ч, последующих — с установленной скоростью.
На этом работы по замене инвентарных рельсов на рельсовые плети на скреплении ЖБР-65 со сваркой их в пути и постановкой в оптимальную температуру закрепления заканчиваются.
Производственный состав Капитальный ремонт пути выполняется работниками пути в следующем составе Руководящий и обслуживающий персонал.
Заместитель начальника (производитель, руководитель работ) — 1 чел.
Старший дорожный мастер — 1 чел.
Дорожный мастер — 3 чел.
Бригадиры пути (не освобожденные входят в состав монтеров пути) — 3.
Сигналисты — 5 чел Телефонист — 1 чел.
Итого: (без не освобожденных бригадиров пути) — 12 чел.
Колонна подготовительных, основных и отделочных работ состоит из 6-т и бригад численностью 54 монтеров пути:
Состав бригад монтеров пути бригада № 1 — 8 чел; бригада № 2 — 9 чел; бригада № 3 — 9 чел; бригада № 4 — 12 чел; бригада № 5 — 10 чел; бригада № 6 — 6 чел;
Таблица 4.2. — Состав машинистов.
№ пп. | Наименование машин. | Количество машин (составов). | Количество машинистов. | |
Мотовоз МПТ. | ||||
Моторные платформы МПД. | ||||
Четырехосные платформы УСО. | ; | |||
Путевой моторный гайковерт ПМГ. | ||||
Платформа прикрытия. | ||||
Локомотив 2ТЭ10. | ||||
Спец.состав для перевозки плетей РС-800. | ||||
Рихтовочная машина «Duomatic» 09−32 CSM. | ||||
Сварочная установка. | ||||
Электростанции АБ-4. | ||||
Итого: | ||||
Всего: 99 чел.
Примечание: если по условиям производства работ по дням для монтеров пути возникают технологические перерыва, то в эти дни рабочие используются на других видах работ, вне данного технологического процесса.
Перечень необходимых машин, механизмов и инструмента:
Путеукладочный кран УК-25/9−18 с платформами, МПД и навесным устройством, компл. — 1.
Рельсосварочная машина ПРСМ, шт. — 1.
Универсальный дизельный гайковерт системы Матвеенко, шт. — 2.
Мотовоз МПТ, шт. -1.
Гидравлический прибор для растягивания плети, шт. — 2.
Ударный механизм с клиновым упором, компл. — 2.
Насосная станция, шт. — 1.
Электростанция АБ-4 с комплектом кабельной арматуры, — 1.
Рельсосверлильный станок, шт. — 1.
Рельсорезный станок, шт. — 1.
Рельсошлифовальный станок, шт. — 1.
Рельсошлифовальный станок СЧР, шт. — 1.
Путевые ключи ЭК-1, шт. — 4.
Ультразвуковой дефектоскоп, шт. — 1.
Ключ торцовый, шт — 44.
Ключ гаечный, шт — 4.
Вилы щебеночные, шт. — 4.
Рулетка мерная, шт. — 1.
Лом остроконечный, шт. — 4.
Лом лапчатый, шт. — 4.
Термостат рельсовый, шт. — 1.
Бородок, шт. — 1.
Телефон, шт. — 1.
Аппаратура радиосвязи и оповещения, компл. — 1.
4.9 Технико-экономическое обоснование Выбор варианта технологии производства работ производится исходя из возможности выполнения конкретной задачи, поставленной перед ремонтным подразделением, и является средством достижения цели. В основном решаются три задачи:
очистка существующего щебня от загрязнителей;
укладка железобетонной решетки с инвентарными рельсами;
замена инвентарных рельсов на бесстыковые рельсовые плети со сваркой их ПРСМ на длину блок-участка.
Осуществляем подбор комплекса путевых машин, для каждого из вариантов, способных по своим техническим характеристикам выполнить данный объём работ, предусмотренный проектом капитального проекта пути. При этом рассматривается два варианта:
ѕ при возможности предоставления «окон» большой продолжительности (12 — 16 часов) весь комплекс работ (очистка щебня и смена РШР с сопутствующими работами) выполняется в одно «окно»;
ѕ при отсутствии таких возможностей, как правило, смена РШР и очистка щебня производится последовательно в разные дни.
В первом варианте (очистка щебня и смена РШР с сопутствующими работами) трудозатраты составляют 27 268,01чел. минут при продолжительности «окна» 14 часов 00 минуты.
При производстве работ по второму варианту ((вырезка щебня и смене РШР с сопутствующими работами) трудозатраты составляют 28 015,86 при продолжительности «окна» 12 часов 15 минуты.
Для составления графиков производства работ по дням на 10 км пути при занятости монтеров пути первого варианта — 131 человек, для второго варианта — 120 человек.
Для обоих вариантов разработан график производства работ по дням на 37 календарных дней.
С экономической точки зрения, по показателям сводной калькуляции стоимости затрат на 1000 м пути по глубокой очистке щебня и смене РШР для первого варианта составляет — 3 950 403,64 руб., для второго варианта — 5 483 846,27 руб.
Больша стоимость второго варианта обусловлена использованием материала «Криогелит» вместо геотекстиля, при этом используется одна машина СЧУ-800 и сокращается время «окна» в сравнении с первым вариантом, где используются 2 машины СЧ-601. Поэтому экономически целесообразно использовать в работе специализированные машины по очистке щебня (такие как СЧ-600, СЧ-601, СЧ-16−200, ЩЩМ и т. п.) и укладки геотекстиля.
Поэтому при возможности предоставления «окон» большой продолжительности, для капитального ремонта пути на участке Хохотуй — Бада 5861 пк1 — 5870 пк10 четного пути предпочтительней выбрать технологический процесс производства работ, разработанный по первому варианту.
5. Безопасность движения поездов и охрана труда при производстве путевых работ Безопасность движения поездов О предстоящем закрытии перегона на одном участке, на двухи многопутном участке одного или нескольких путей начальник отделения при отсутствии отделения — заместитель начальника железной дороги) не позже чем за сутки уведомляют соответствующих руководителей работ.
В разрешении начальника отделения (при отсутствии отделения — начальника железной дороги) на производство работ с закрытием перегона должны быть указано время, на которое согласовано закрытие перегона или отдельного пути и фамилия лица, осуществляющего единое руководство этими работами. Фамилию и должность руководителя работ поездной диспетчер обязан сообщить дежурным по станциям, ограничивающим перегон. При наличии соответствующего разрешения закрытие и открытие перегона (пути) до начала работ и после их окончания оформляются приказом поездного диспетчера.
Отмена предоставленного «окна» для производства ремонтно-путевых работ сокращение его продолжительности могут быть допущены только в исключительных случаях и лицом, по распоряжению которого разрешено «окно». Уведомление об этом руководителю работ должно быть дано не позднее, чем за 12 ч до начала «окна» .
На время производства работ, вызывающих перерыв движения, а также для производства которых в графике движения предусмотрены «окна», дистанция сигнализации и связи — по заявке дистанции пути совместно с руководителем работ обязаны установить постоянную связь (телефонную или по радио) с поездным диспетчером.
Руководство работами в «окно» осуществляет:
При работе путевой машинной станции (ПМС):
при замене рельсошпальной решетки — начальник (заместитель начальник ПМС;
при глубокой очистке щебня, с сопутствующими работами в объеме среднего или подъемочного ремонта, и создании слоя чистого балласта не менее 31—40 мм ниже постели шпал — заместитель начальника ПМС;
при очистке щебня на глубину 16−30 см ниже постели шпал с сопутствующими работами в объеме среднего или подъемочного ремонта — производитель работ;
при очистке щебня на глубину 15 см ниже постели шпал с сопутствующими работами в объеме среднего или подъемочного ремонта — дорожный мастер. При работе путевой машинной станции, на весь период ремонта дистанция пути прикрепляет к путевой машинной станции своего работника по квалификации не ниже дорожного мастера для контроля за качеством работ и соблюдением требований по безопасности движения поездов; данный специалист дистанции пути определяет безопасное состояние пути и передает установленным порядком поездному диспетчеру разрешение на открытие перегона, а также выдачу и отмену предупреждений об ограничении скоростей движения поездов по месту работ.
Заявки на предупреждение на работы, выдаваемые в «окно», выдаются по форме 3 приложения 8 ЦП-485 «Инструкция по обеспечению безопасности движения поездов при производстве путевых работ», если после открытия перегона требуется снижение скорости движения поездов.
Перед закрытием перегона руководитель работ обязан дать дежурному по станции, ограничивающей перегон, и поездному диспетчеру заявку о последовательности отправления на закрытый перегон хозяйственных (в дальнейшем — рабочих) поездов, машин и агрегатов с указанием для каждого поезда и машины километра первоначальной остановки на закрытом перегоне (или на пути перегона) и станции, куда они должны возвращаться по окончании работ.
При наступлении срока начала работ с закрытием перегона поездной диспетчер устанавливает его свободность или свободность соответствующего пути на двухи многопутном участках, после чего дает дежурным по станциям, ограничивающим перегон, и руководителю работ приказ о закрытии перегона или пути. В исключительных случаях при отсутствии на месте работ телефонной или радиосвязи с поездным диспетчером приказ о состоявшемся фактическом закрытии перегона или пути передается руководителю работ дежурным ближайшей станции (по телефону или через нарочного, командируемого с места работ).
Запрещается приступать к работам до получения руководителем работ приказа поездного диспетчера (письменного, по телефону или радиосвязи), и до ограждения места работ сигналами остановки, а на электрифицированных участках приказа энергодиспетчера о снятии напряжения в контактной сети и последующей установки заземляющих штанг.
Отправление рабочих поездов (дрезин), машин и агрегатов на перегон, закрытый для ремонта пути, сооружений и устройств, производится по разрешению на бланке белого цвета с красной полосой по диагонали. В соответствии с заявкой руководителя работ в разрешении указывается место (километр) первоначальной остановки каждого поезда и машины на перегоне.
На закрытом перегоне (пути) может работать одновременно несколько рабочих поездов (дрезин) и путевых машин, в том числе и принадлежащих различным организациям, но находящихся под руководством одного работника, указываемого в разрешении начальника отделения (при отсутствии отделения — начальника железной дороги).
Машинист локомотива каждого рабочего поезда, дрезины и агрегата должен следовать до места, указанного в разрешении на бланке белого цвета с красной полосой по диагонали. Первый поезд следует с установленной скоростью, последующие — не более-20 км/ч. При этом расстояние между поездами должно быть не менее 1 км. У места остановки рабочего поезда, идущего вслед, должен быть сигналист с красным сигналом.
Рабочие поезда, отправляемые на закрытый перегон с различных раздельных пунктов навстречу один другому, должны следовать также только до места, указанного в разрешении на бланке белого цвета с красной полосой по диагонали, где по указанию руководителя работ выставляется сигнал остановки. Расстояние между пунктами остановки встречных поездов должно быть не менее 1 км.
В темное время суток и при плохой видимости сигналов (туман, метель, кривые и др.), а также при неблагоприятных условиях сигналист в местах рабочих поездов и путевых машин должен укладывать петарды.
После остановки дальнейшие передвижения рабочих поездов, машин и агрегатов по перегону осуществляются по указанию руководителя работ.
Если работы производятся на перегоне, оборудованном автоблокировкой, то по согласованию с поездным диспетчером разрешается отправлять рабочие поезда, машины и агрегаты к месту производства работ по сигналам автоблокировки, не ожидая закрытия перегона. Машинисту каждого поезда выдается предупреждение об остановке на перегоне в месте, указанном в заявке руководителя работ. Разрешение на бланке белого цвета с красной полосой по диагонали при отправлении таких поездов на перегон, подлежащий закрытию, вручается руководителю работ или уполномоченному им работнику, который передает его машинисту локомотива или самоходной путевой машины после остановки поезда на перегоне в обусловленном месте и получения приказа поездного диспетчера о закрытии перегона. Перегон или соответствующий путь перегона закрывается для производства работ приказом поездного диспетчера после освобождения от поездов, отправленных на этот перегон впереди рабочих поездов, машин и агрегатов.
Отправляемые со станции в одном поезде для одновременной работы на перегоне рабочие поезда, машины и агрегаты могут расцепляться или соединяться на перегоне по указанию руководителя работ. Порядок формирования рабочих поездов для производства работ по усиленному капитальному, капитальному, усиленному среднему, среднему ремонтам пути указан в приложении 9 ЦП-485 «Инструкции по обеспечению безопасности движения поездов при производстве путевых работ» .
Если при выполнении путевых работ необходимо иное размещение комплекта машин Ь поезде, то расстановка и соединение их в один поезд для отправки на перегон устанавливаются руководителем работ.
При отправлении со станции нескольких рабочих поездов, соединенных друг с другом для последую их работы на перегоне по указанию руководителя, машинисту каждого из них должно выдаваться отдельное разрешение на бланке белого цвета с красной полосой по диагонали.
Основные требования по обеспечению безопасности движения поездов при транспортировке путевых машин тяжелого типа и допускаемые скорости движения указаны в приложении 10 ЦП-485 «Инструкция по обеспечению безопасности движения поездов при производстве путевых работ» .
Рабочие поезда, машины и агрегаты при производстве работ на перегоне или в пределах станции должны сопровождаться руководителем работ или уполномоченным им работником. По указанию начальника отделения (при отсутствии отделения — начальника железной дороги) на рабочие поезда в необходимых случаях могут назначаться главные кондукторы.
Ко времени окончания установленного перерыва в движении поездов для производства работ последние должны быть полностью закончены, путь, сооружения и устройства приведены в состояние, обеспечивающее безопасное движение поездов, сигналы остановки сняты с оставлением, если необходимо сигналов уменьшения скорости и соответствующих сигнальных знаков.
По окончании работы поездов, машин и агрегатов руководитель работ обязан лично или через подчиненных работников осмотреть путь и другие монтируемые устройства на всем протяжении участка работы, обеспечить немедленное устранение обнаруженных недостатков, препятствующих нормальному движению, а также проверить, не нарушают ли установленных габаритов находящиеся на участке материалы и механизмы Отправление рабочих поездов (дрезин), машин и агрегатов с перегона производится по указанию руководителя работ, согласованному предварительно с поездным диспетчером. О намеченном порядке возвращения рабочих поездов с перегона диспетчер ставит в известность дежурных по станциям, ограничивающим перегон.
Открытие перегона (пути) производится приказом поездного диспетчера только после получения уведомления (письменного, по телефону или радио связи) от начальника дистанции пути или уполномоченного им работника (по должности не ниже дорожного мастера) об окончании путевых работ или работ на искусственных сооружениях, об отсутствии на перегоне рабочих поездов, машин и агрегатов или об отправлении по правильному пути двухпутного перегона, а также об отсутствии других препятствий для безопасного движения поездов независимо от того, какая организация выполняла работы.
Указанное уведомление передается поездному диспетчеру непосредственно или через дежурного по ближайшей станции. Полученное по телефону или радиосвязи уведомление поездной диспетчер записывает в Журнал диспетчерских распоряжений.
Восстановление действия существующих устройств СЦБ и связи или электроснабжения (если работа их нарушалась) производится после установки и подключения работниками пути всех перемычек и соединителей к рельсам и по получении уведомления соответственно от электромеханика (старшего электромеханика) СЦБ и связи или энергодиспетчера.
Скорость следования возвращаемых после работы на перегоне рабочих поездов, машин, агрегатов (кроме первого) должна быть не более 20 км/ч, а расстояние между ними — не менее 1 км.
Скорость движения рабочего поезда вагонами вперед при наличии радиосвязи между локомотивом и путевой машиной в голове поезда в зависимости конструкции путевых машин допускается не более 40 км/ч.
Охрана труда при производстве работ Железнодорожный путь является опасной зоной из-за угрозы наезда подвижного состава на людей. Находясь на путях, необходимо проявлять постоянную бдительность, осторожность и осмотрительность. Требуется внимательно следить за движением поездов, локомотивов, маневровых составов, а также за окружающей обстановкой и принимать решительные меры к устранению возникающей угрозы для жизни людей или безопасности движения поездов.
При работах на железнодорожных путях для обеспечения безопасности движения поездов и труда рабочих место производства работ предварительно ограждают соответствующими сигналами. В зависимости от вида, объёма и степени опасности различают работы, места производства которых ограждаются сигналами остановки, сигналами уменьшения скорости, сигнальными знаками «С» (о подаче звукового сигнала локомотивами).
Всякое препятствие для движения поездов на перегоне, по станционным путям и стрелочным переводам ограждают сигналами остановки независимо от того, ожидается поезд, маневровый состав или нет. В соответствии с правилами техники безопасности и производственной санитарии при производстве работ в путевом хозяйстве особая ответственность возлагается на руководителя работ.
Перед выходом на работу руководитель обязан проверить исправность инструмента, механизмов, сигнальных принадлежностей, наличие и состояние спецодежды, убедиться в том, что заявка о выдаче предупреждений на поезда принята к исполнению. Кроме того, он должен провести инструктаж рабочих о маршруте безопасного прохода к месту работы и обратно, о правилах безопасного выполнения работ, о порядке ограждения места работы, необходимости наблюдения за движением поездов и маневровых составов, о своевременном прекращении работы и сходе с пути.
До начала работ выставляют сигналы остановки, сигнальные знаки «С» и сигналистов. Для предупреждения работающих о приближении поезда по соседнему пути при работах на одном из путей двупутного участка независимо от того, какими сигналами ограждено место работ, по соседнему пути устанавливают знаки «С» .
Места работ, не ограждаемые сигналами остановки или уменьшения скорости, для предупреждения рабочих о приближении поезда ограждают с обеих сторон знаками «С». Знаки «С» устанавливают на расстоянии 500 — 1500 м от границы участка производства работ.
В случае использования электрического и пневматического инструмента, ухудшающего слышимость, руководитель работ даёт заявку на выдачу предупреждений на поезда об особой бдительности и подаче оповестительных сигналов при приближении к месту работ.
В случаях когда работы выполняются на расстоянии более 2 км от места расположения хозяйственного подразделения, предусматривается организованная доставка рабочих к месту работ и обратно. На участках, где обращаются местные или пригородные пассажирские поезда, рабочих доставляют этими поездами, а путевой и другой инструмент — автомобилями. Могут быть организованы и специальные рабочие поезда, состоящие из пассажирских вагонов пригородного сообщения для доставки рабочих и одной платформы для перевозки инструмента, материалов и надёжно затаренного горючего.
Перевозка горючего на любых транспортных средствах вместе с людьми категорически запрещается. Если нет пассажирских вагонов, то рабочие поезда формируют из специально оборудованных крытых грузовых вагонов.
На каждый вагон выделяют ответственного по должности не ниже бригадира. Онобязан обеспечить безопасное размещение рабочих, порядок в пути следования, при посадке в вагон и высадке из него, выгрузку инструмента и материалов, а также пожарную безопасность. Посадку и высадку рабочих на двухи многопутных перегонах производят только с полевой стороны, двери с противоположной стороны вагонов должны быть закрыты. Поезд сопровождает работник по должности не ниже производителя работ или дорожного мастера, ответственный за безопасность перевозки рабочих. Сопровождающий находится на локомотиве поезда. Запрещается движение рабочих поездов вагонами вперёд.
Монтеры пути должны пользоваться исправным ручным инструментом и регулярно проверять надежность насадки ударных инструментов.
Ручки инструмента должны быть изготовлены из прочного дерева, чисто остроганы, без заусенцев; на ударных инструментах поверхность бойка должна быть чистой и не иметь зазубрин и наплывов метала. При завинчивании гаек вручную надо пользоваться типовым ключом. Запрещается бить чем-либо по ключу, увеличивать его длину, наращивая другим ключом, а такжеприменять неисправный ключ, вставлять прокладки между гайкой и губками ключа. При срубании гайки зубилом необходимо надевать защитные очки.
Проверку совпадений отверстий в накладках и рельсах можно производить только бородком или болтом.
Запрещается садиться на рельсы, концы шпал, балластную призму, внутри рельсовой колеи и на междупутье, а также на стеллажи покилометрового запаса рельсов.
Во время производства работ необходимо постоянно следить за тем, чтобы инструмент не мешал передвижению и не находился под ногами, а новые и старые материалы — рельсы, шпалы, скрепления — были аккуратно сложены вне габарита подвижного состава.
Монтеры пути, при работе на участках бесстыкового пути, до начала работ должны быть обучены особенностям производства работ на этих участках.
Во избежание поражения молнией нужно с приближением грозы принять необходимые меры для обеспечения безопасного пропуска поездов по месту работ, после чего уйти с пути. Нельзя прятаться под деревьями, прислоняться к ним, а также подходить к молниеотводам или высоким одиночным предметам (столбам, деревьям) на расстояние менее 10 м. Опасно находиться во время грозы на возвышенных местах, открытых равнинах. Рекомендуется укрываться в закрытых помещениях, а при удаленности от них — в небольших углублениях на склонах холмов или откосах насыпей или выемок.
При грозе нельзя держать при себе или нести инструмент и другие металлические предметы.
При переноске петард следует использовать специальные коробки.
Запрещается:
производить припайку к петардам оторвавшихся пружин и лапок;
подвергать петарды ударам и нагреву, вскрывать;
стоять ближе 20 м от петард, положенных на рельсы, в момент наезда на них подвижного состава;
хранить петарды возле огня или отопительных приборов;
пользоваться петардами, если срок их годности истек.
При производстве работ развернутым фронтом (более 200 м) места работ ограждаются порядком, указанным на рис. 1. Устанавливаемые на расстоянии 50 м от границ участка, требующего ограждения, переносные красные сигналы должны находиться под охраной стоящих около них сигналистов с ручными красными сигналами.
Рисунок № 1.
Места производства работ на перегонах, требующие следования поездов с уменьшенной скоростью, ограждаются с обеих сторон на расстоянии 50 м от границ участка работы переносными сигнальными знаками «Начало опасного места» и «Конец опасного места». От этих сигнальных знаков на расстоянии, А (рис. 2) устанавливаются переносные сигналы уменьшения скорости.
Рисунок № 2.
5.1 Охрана окружающей среды Деятельность железнодорожного транспорта в наибольшей степени отражается на атмосфере в районах, где в качестве локомотивов эксплуатируются тепловозы с дизельными силовыми установками. Так, основным источником загрязнения атмосферы при работе подвижного состава являются отработавшие газы тепловозов. Во всех развитых странах конструкторы новых локомотивов (дизелей) стали строже относится к экологическим требованиям, а работники транспорта, эксплуатирующие локомотивы, тщательнее следят за состоянием и работой двигателей и локомотивов с целью не только снижения токсичности отработавших газов, но и экономии жидкого топлива.
Основное внимание конструкторов направлено на совершенствование процесса горения топлива в цилиндрах с целью образования в них возможного минимума вредных отходов. В первую очередь разрабатываются меры, направленные на сокращение выброса дизелями окислов азота, как в части конструкции (например, применение форкамерных типов), так и в отношении надлежащей эксплуатации тепловозов.
Современные мощные тепловозы оборудуются четырёхтактными дизелями, где рабочий процесс протекает при пониженной температуре и одновременно обеспечивается более полное сгорание топлива. Существенно снижает объём окислов азота рециркуляция отработавших газов, т. е. частичное направление их вместе с очередной порцией горючей смеси в цилиндры.
Для уменьшения дымности дизелей применяются специальные антидымные присадки к топливу.
Другой аспект проблемы заключается в том, что дымление дизелей не только загрязняет атмосферу, но и неблагоприятно влияет на работу самого транспорта. Особенно это проявляется на элекрофицируемых линиях, где часть поездов следует с тепловозами, а также в железнодорожных узлах с большим числом маневровых тепловозов. Из-за оседания копоти на изоляторах может произойти нарушение работы контактной сети и высоковольтных линий передач, которое сопровождается перерывом движения.
В целях снижения ущерба от загрязнения изоляторов изыскиваются новые материалы для изоляторов, новые формы изоляторов (с пазами особой конфигурации), исследуются условия взаимодействия комплекса «проводникизолятор» с тем, чтобы снизить расходы и вероятность аварий. Опыт, однако, показывает, что наиболее эффективные результаты достигаются снижением уровня загрязнения самого воздуха в местах нахождения контактных сетей и высоковольтных линий. Отсюда возникает необходимость более тщательного содержания топливной аппаратуры.
На общую эмиссию сажи существенно влияет и режим движения поездов. Если поезд следует с частными остановками, то выброс в атмосферу сажи возрастает, поскольку удельный вес её в отработавших газах в период разгона поезда выше по сравнению со стадией относительно равномерного движения. Одновременно увеличивается и расход топлива. Таким образом, задача улучшения режима следования возможно большему числу поездов имеет и экологическое, и экономическое значение.
В настоящее время ведётся большая работа по экономии энергии и топлива во всех службах железнодорожного транспорта. Наибольшее влияние на результат экономии оказывают службы локомотивная и движения, которые в первую очередь ответственны за соблюдение весовых составов, а также за обеспечение возможности следования поездов с нормальными графиковыми скоростями с минимальным числом остановок, а лучше безостановочного в пределах тяговых участков.
В некотором отношении железные дороги ответственны за загрязнение среды обитания металлической пылью в результате довольно интенсивного истирания чугунных тормозных колодок. С этой точки зрения лучшими тормозами являются электрои гидродинамические, в особенности если они связаны с маховиками или другими устройствами, аккумулирующими энергию торможения для последующего использования на тяжёлых режимах разгона поездов и преодоления крутых подъёмов.
В отдельных районах возникла проблема загрязнения пути и прилегающих к нему почв угольной и рудной пылью, а также некоторыми другими веществами.
Помимо ужесточения требований к соответствующим службам по исправному содержанию вагонов, необходимы технические меры и, в частности, расширение парка полувагонов со сплошным дном, применение различных вяжущих веществ для образования корки на поверхности насыпного (навалочного) груза, использование укрывающих грузов плёнок, создания новых специальных видов подвижного состава, приспособленных для сохранной перевозки отдельных грузов Известную проблему создаёт масло, вытекающее через неплотности из разных агрегатов локомотивов и узлов вагонов, которое вымывается с пути поверхностными водами и затем переносится в водоёмы, загрязняя их. Устранение этих недостатков связано в основном с совершенствованием конструкций подвижного состава и, в частности, с быстрейшим переводом вагонов на роликоподшипники.
За последнее время в связи с долгосрочной задачей экономии жидкого топлива железные дороги как один из самых экономичных и экологически чистых видов транспорта получают новый импульс для ускоренного и преимущественного развития во многих странах.
Принцип — не нарушать экологического равновесия и не наносить больших ран природе — является руководящим для проектировщиков и строителей железных дорог будущего, а время и дальнейшие научные исследования покажут, насколько реализованные меры были удачными.
6. Инженерная деталь В качестве детали рассматриваем стяжной прибор, применяемый для исправления ширины колеи с железобетонными шпалами.
Исправление ширины колеи Исправление (регулировку) ширины колеи выполняют на пути с железобетонными шпалами — за счет зазоров между подошвой рельса и ребордами прокладок (в том числе устранением перекошенности шпал) либо исправлением переуклонки рельсов, являющейся следствием неодинакового износа резиновых прокладок с внутренней и наружной стороны рельсовых путей. На прямом участке пути перешивку (регулировку) колеи выполняют по нерихтовочной нити, в кривых — по внутренней нити.
Перешивку рихтовочной нити осуществляют в исключительных случаях, например, в зимнее время при смерзшемся балласте, когда исправление положения пути в плане, устранение «отбоев» наружной нити в кривых возможно только со смещением подкладок и отжимом костылей. Поэтому по условиям производства работ по регулировке ширины колеи путь должен быть отрихтован и бригадиром пути заранее отмечены мелом на шейке рельсов места и величины сдвижки рельсовой нити. Постановка сдвигаемой рельсовой нити в требуемое положение производится стяжным прибором (рис. 6.1) либо с помощью лома, заглубленного в балласт. В таблице 8.54 приведены технологический состав групп монтеров пути и нормы времени по перешивке колеи.
Рис. 6.1. Стяжной прибор для перешивки нити.
1 — захват; 2 — запорная втулка; 3, 5, 8 — стержни; 4 — изоляционная втулка; 6 — стягивающая втулка; 7 — храповое устройство.
Работы по регулировке рельсовой колеи ограждаются сигнальными знаками «С» (свисток) при расшивке не более трех (шести при работе со стяжным прибором) смежных концов шпал, а при раздельном скреплении — с одновременным ослаблением закладных болтов не более, чем на трех концах шпал. При необходимости расшивки рельсовой нити более чем на трех смежных концах шпал подряд (более шести при использовании стяжного прибора), место работы ограждается сигналами остановки поезда.
Таблица 6.1. — Состав групп и норм времени по регулировке ширины колеи.
Регулировка ширины колеи. | Состав группы монтеров пути (чел), разряд. | Норм времени на 10 концов шпал, (чел.ч/чел.мин.). | |
При скреплении: · смешанном костыльном. · раздельном КБ на железобетонных шпалах. | 2 мп, 3-го разряда. 2 мп, 4-го разряда. | 1,2 — 1,35/79 — 81. 0,481/28,87. | |
Работа по перешивке колеи при смешанном костыльном скреплении включает в себя следующие последовательные операции. Подготовительные операции: — очистка концов шпал и костылей у регулируемой рельсовой нити от балласта и грязи;— выдергивание дополнительных и третьих основных костылей на концах смежных шпал;— установка стяжного прибора. Основные операции: — выдергивание оставшихся двух основных костылей на концах шпал регулируемой нити;— антисептирование костыльных отверстий и постановку в них пластинок-закрепителей размером 5×15×110 мм, также пропитанных антисептиком;— постановка рельсовой нити в требуемое положение стяжным прибором (или ломом);— забивка двух основных костылей на каждом конце шпалы;— снятие стяжного прибора Заключительные операции: — забивка дополнительных и третьих основных костылей на каждом конце шпалы. При выполнении работ «под поездами» перед пропуском поезда во время перешивки колеи рельсы должны быть пришиты не менее чем двумя костылями, при этом отвод ширины колеи должен быть не более 1 мм на 1 м пути.
При регулировке ширины колеи за счет поправки перекошенных железобетонных шпал отдельные операции выполняются в следующей последовательности: — отрывка шпальных ящиков у перекошенных шпал;— смазка на них клеммных болтов;— установка стяжного прибора, ослабление гаек клеммных болтов на 2—3 оборота;— передвижка перекошенных шпал в нормальное положение и постановка рельсовой нити при помощи стяжного прибора;— закрепление клеммных болтов и заполнение шпальных ящиков балластом. Регулировку ширины колеи за счет устранения переуклонки рельсов производят в следующей последовательности: — ослабляют закладные болты на шпалах с изношенными прокладками;— на трех концах смежных шпал снимают закладные болты;— домкратом, установленным внутри колеи, вывешивают рельс;— изношенные резиновые нашпальные прокладки заменяют на новые;— снимают домкрат;— устанавливают закладные болты, завинчивают на них гайки с крутящим моментом 150 Нм (15 кгс-м). Затем эти же рабочие операции выполняют на следующих трех шпалах и т. д. в пределах границ регулировки ширины колеи. После пропуска поезда производят дозатяжку закладных болтов сначала с наружной стороны рельса, а потом — с внутренней.
Работы по исправлению рельсовой колеи ограждаются: при работе со стяжным прибором — не более шести шпал подряд — сигнальными знаками «Свисток»; при расшивке более шести шпал подряд — сигналами остановки поезда с выдачей предупреждений машинистам поездов о подаче оповестительных сигналов.
ТЕХНОЛОГО-НОРМИРОВОЧНАЯ КАРТА № 69.
Наименование работы — регулировка ширины рельсовой колеи при раздельном скреплении с применением стяжного прибора Условия работы.
1. Ширина колеи регулируется за счет зазоров между подошвой рельса и ребордой подкладки..
2. Места регулировки определены заранее и отмечены мелом на шейке рельса.
3. Гайки клеммных болтов ослабляются не более, чем на шести концах шпал подряд на одной рельсовой нити.
4. Регулировка производится с применением одного стяжного прибора.
5. Рельсы типов Р65 и Р50, скрепление КБ на железобетонных шпалах и КД (К-4) на деревянных, балласт щебеночный.
Состав группы. | Количество исполнителей, чел. | ||
шпалы. | |||
железобетонные. | деревянные. | ||
Монтер пути 4-го разряда. | |||
Монтер пути 3-го разряда. | ; | ||
Итого. | |||
Тарифный разряд работ, выполняемых монтерами пути. | 3,50. | ||
Измеритель работы- 10 концов шпал. | |||
Норма времени, нормо-ч. | 0,482. | 0,723. | |
№ п/п. | Содержание работы. | Единица измерения. | Количество исполнителей, чел. | Применяемые машины, механизмы, инструменты и приспособления. | Учтенный объем работы. | Оперативное время, нормо-мин. | ||
на единицу измерения. | всего. | |||||||
Смазка клеммных болтов. | болт. | Кисть. | 1,66. | 3,32. | ||||
Устройство канавки для установки стяжного прибора на пути с деревянными шпалами. | канавка. | Когти для щебня. | 3,76. | 7,52. | ||||
Установка стяжного прибора. | установка. | ; | 1,70. | 3,40. | ||||
Ослабление гаек клеммных болтов на 2−3 оборота. | гайка. | Ключи путевые. | 0,230. | 4,60. | ||||
Постановка рельсовой нити в требуемое положение при помощи стяжного прибора. | постановка. | Шаблон рабочий путевой, стяжной прибор | 1,97. | 3,94. | ||||
Закрепление гаек клеммных болтов. | гайка. | Ключи путевые. | 0,410. | 8,20. | ||||
Снятие стяжного прибора. | снятие. | ; | 1,10. | 2,20. | ||||
Заравнивание канавки балластом после снятия стяжного прибора с деревянными шпалами. | канавка. | Когти для щебня. | 2,70. | 5,40. | ||||
Итого: шпалы: железобетонные 25,7. деревянные 38,6. | ||||||||
Расчет нормы времени.
Индекс. | нормо-мин. | % к Топ. | ||
шпалы. | ||||
железобетонные. | деревянные. | |||
Топ. Тпз. Тоб. Тпотл. | 25,7. 1,00. 0,257. 1,95. | 38,6. 1,51. 0,386. 2,93. | ; 3,9. 1,0. 7,6. | |
Т. | 28,9 или. 0,482 нормо-ч. | 43,4 или. 0,723 нормо-ч. | ; | |
7. Безопасность и экологичность проекта.
7.1 Безопасность проведения погрузочно-разгрузочных работ Общие положения Погрузка и выгрузка материалов и запасных частей должна производиться согласно ГОСТ 12.3.009−76 «Работы погрузочно-разгрузочные..
Общие требования безопасности", в соответствии с «Правилами техники безопасности и производственной санитарии при производстве погрузочно-разгрузочных работ на железнодорожном транспорте». Грузоподъемные краны и устройства должны содержаться в соответствии с отраслевыми «Правилами устройства и безопасной эксплуатации грузоподъемных кранов» ..
В темное время суток погрузка и выгрузка материалов верхнего строения пути разрешается при освещенности места работ не менее 20 лк, замеренной в горизонтальной плоскости на уровне земли работниками санитарно-эпидемиологической станции (СЭС)..
Поднимать груз без проверки надежности строповки и подтаскивать груз косым натяжением троса запрещается..
Стропальщики во время работы должны быть одеты в защитные каски..
Меры безопасности при погрузке и выгрузке рельсов, стрелок, крестовин и уравнительных приборов Погрузка и выгрузка рельсов, стрелок, крестовин и уравнительных приборов должны производиться с применением грузоподъемных механизмов и приспособлений..
При погрузке и выгрузке рельсов, стрелок, крестовин и уравнительных приборов руководитель работ должен следить, чтобы рабочие соблюдали меры предосторожности, все операции должны производиться только по команде руководителя работ..
Работа без расчалок запрещается..
Выгрузка рельсов с платформ и дрезин на ходу, если нет специальных для этого приспособлений, запрещается..
Строповка рельсов при выгрузке и погрузке производится с помощью рельсовых захватов, не менее как в двух местах..
Меры безопасности при погрузке и выгрузке шпал и брусьев Погрузка и выгрузка шпал, переводных, мостовых и охранных брусьев, пропитанных масляными антисептиками, должна производиться грузоподъемными механизмами, кранами или заменяющими их приспособлениями..
Погрузка, выгрузка и переноска железобетонных шпал должны производиться только с применением машин, механизмов и специальных приспособлений..
Выгрузка шпал и брусьев на ходу поезда запрещается..
Запрещается производить погрузку и выгрузку шпал и брусьев, пропитанных масляными антисептиками, без специальной одежды, установленной действующими нормами. Перед началом работ руководитель работ должен выдать рабочим защитную пасту для смазывания лица, рук, шеи и других открытых частей тела, а по окончании работы обеспечить возможность мытья теплой водой с мылом..
Перемещение шпал и брусьев, пропитанных масляными антисептиками, должно производиться только с помощью специальных шпалоносок..
На платформах, во избежание обрушения, шпалы и брусья во время погрузки должны укладываться ступенчатыми рядами..
7Укладка и крепление шпал, брусьев при погрузке на платформы и в полувагоны должны производиться в соответствии с Техническими условиями погрузки и крепления грузов, глава I «Общие требования к размещению и креплению грузов в вагонах», утвержденными 15 августа 1981 г..
Меры безопасности при выполнении работ по выгрузке балластных материалов Выгрузка балласта должна производиться под руководством дорожного мастера или производителя работ, который обязан обеспечить безопасное производство работ, следить за соблюдением габарита при выгрузке и безопасностью передвижения балластного поезда по фронту работ..
Руководитель работ несет ответственность за приведение подвижного состава в транспортное положение после выгрузки балласта..
Выгрузка балласта на перегоне может производиться при движении поезда со скоростью не свыше 5 км/час..
О разгрузке балласта при движении руководитель должен заблаговременно предупредить рабочих, машиниста и обслуживающий персонал поезда и идти рядом с поездом, с той стороны и на таком расстоянии от поезда, чтобы он был хорошо виден локомотивной бригаде и имел возможность дать распоряжение об остановке поезда в случае надобности..
Требования безопасности при транспортировке и выгрузке балласта из отходов асбестового производства необходимо выполнять по ГОСТ 24 580–81 «Балласт из отходов асбестового производства. Технические условия», а также согласно «Техническим указаниям на применение асбестового балласта для железнодорожного пути действующей сети «..
Меры безопасности при работе с применением съемных кранов для погрузки рельсов на железнодорожные платформы К эксплуатации допускаются краны, имеющие в паспорте отметку о прохождении освидетельствования и испытаний..
Допускаемая грузоподъемность должна быть указана на кране..
Испытание кранов по грузоподъемности производится ежегодно..
Работа крана ведется под руководством лица по должности не ниже бригадира пути, который является ответственным за соблюдение правил техники безопасности..
Захватные приспособления крана должны устанавливаться вертикально над рельсом, подлежащим подъему..
Стойки кранов должны прочно и устойчиво стоять в гнездах платформы..
После перемещения лебедки на конец стрелы она должна надежно закрепляться..
Меры безопасности при работе с применением козловых и стреловых кранов, а также съемных портальных кранов для перевозки рельсов по фронту работ Краны допускаются к работе при наличии отметки в паспорте о прохождении освидетельствования и испытания..
Перед началом работы краны и палочные приспособления должны тщательно осматриваться, при этом необходимо следить, чтобы крепящие гайки движущихся частей были плотно затянуты и зашплинтованы..
Захватные приспособления крана устанавливаются вертикально над грузом, подлежащим подъему..
Работники, связанные с эксплуатацией крана, при погрузочно-разгрузочных работах должны знать и точно выполнять установленную сигнализацию..
Магнитные захваты, не имеющие предохранительных приспособлений (на случай прекращения тока), могут использоваться только при ограждении рабочей зоны..
Поднимать груз без проверки надежности его зацепления запрещается. В случаях погрузки и выгрузки рельсов захват их осуществляется не менее как в двух местах..
При окончании погрузки, выгрузки или при перерыве в работе оставлять груз в подвешенном состоянии запрещается..
Допускается спаренная работа двух стреловых кранов с одинаковым режимом под руководством одного лица, ответственного за безопасность работ по перемещению грузов кранами..
Спаренная работа козловых кранов допускается при условии единого командования и наличия устройства синхронной работы электрической части крана и механического соединения кранов между собой..
Горизонтальное перемещение груза кранами производится на высоте не менее 0,5 м от всех встречающихся на пути предметов..
Перемещение груза над людьми запрещается..
Установка и работа крана ближе 30 м от крайнего провода воздушной линии электропередачи напряжением более 36 кВ допускается при наличии письменного разрешения на производство работ (наряда-допуска) и согласования порядка их ведения с организацией, эксплуатирующей эти линии..
Работа грузоподъемных машин и механизмов в охранной зоне контактной сети и линий электропередачи без снятия напряжения допускается с разрешения предприятия — владельца линий при соблюдении расстояния от подъемной и выдвижной части в любом ее положении до вертикальной плоскости, образуемой проекцией на землю ближайшего провода, находящегося под напряжением не менее указанного в табл. 7.1..
Таблица 7.1.
Напряжение воздушной линии, кВ. | Наименьшее расстояние, м. | |
до 1. | 1,5. | |
от 1 до 25 включительно. | 2,0. | |
от 35 до 110. | 4,0. | |
от 150 до 220. | 5,0. | |
6,0. | ||
от 500 до 4750. | 9,0. | |
800 (постоянного тока). | 9,0. | |
Работать на стреловых кранах и устанавливать их непосредственно под проводами контактной сети, ДПР, ВЛ напряжением 0,4 — 35 кВ, находящихся под напряжением, запрещается..
Грузоподъемные машины и механизмы (кроме машин на гусеничном ходу) при работах в пределах охранной зоны линий электропередачи вдали от электрифицированных железнодорожных путей должны быть заземлены при помощи переносного заземлителя (изготовленного по ГОСТ 16 556–71) и заглубленного в грунт на глубину не менее 1,0 м..
При работе грузоподъемных машин и механизмов на резиновом ходу в охранной зоне контактной сети постоянного и переменного тока, ДПР и воздушных линий электропередачи напряжением 6, 10, 35 кВ, расположенных на опорах контактной сети или самостоятельных опорах, заземление корпусов указанных машин и механизмов, в том числе и при наличии автономных источников электропитания, должно выполняться на рельсы, на которые заземлены опоры контактной сети, или к средней точке дроссель-трансформаторов..
При работе нескольких грузоподъемных машин в районе одной рельсовой цепи их заземление должно подключаться к одному месту рельсовой цепи..
Грузоподъемные машины и механизмы, питающиеся от внешней электрической сети, запрещается заземлять на среднюю точку дроссель-трансформатора и на рельсовые нити как на электрифицированных, так и на неэлектрифицированных участках При работах в охранной зоне воздушных линий электропередачи 6 — 35 кВ вблизи распределительных подстанций напряжением 6 — 35 кВ заземление грузоподъемных машин и механизмов может выполняться на контур заземления подстанции..
Грузоподъемные машины и механизмы на гусеничном ходу, работающие в охранной зоне контактной сети постоянного и переменного тока, ДПР, должны заземляться на рельсы, на которые заземлены опоры контактной сети, или к средней точке дроссель-трансформаторов через искровой промежуток..
Строительно-монтажные и погрузочно-разгрузочные работы в охранной зоне контактной сети и линий электропередачи следует производить под непосредственным руководством инженерно-технического работника предприятия, выполняющего работы, — ответственного за безопасность производства работ, при наличии письменного разрешения предприятия — владельца линии и наряда-допуска..
Не допускается работа грузоподъемных машин при ветре, вызывающем отклонение на опасное расстояние свободных (без груза) тросов и канатов, с помощью которых поднимается груз..
По окончании работ кран ставится на место, предназначенное для стоянки, затормаживается, стрела и крюк поднимаются в верхнее положение, при этом стрела устанавливается вдоль рельсового пути..
Проволочные канаты необходимо периодически очищать от грязи, осматривать наружные проволоки и производить отбраковку изношенных канатов (тросов)..
Работа кранов на железнодорожном ходу на неисправных путях запрещается..
Меры безопасности при выполнении работ с применением крана на дрезинах АГМу, ДГКу, ПРЛ, МПТ и АГМС К работам по погрузке и выгрузке материалов верхнего строения пути кранами на дрезинах АГМу, ДГКу, ПРЛ, МПТ и АГМС допускаются лица, имеющие право к управлению краном..
Приступать к работе с краном на дрезинах АГМу, ДГКу, ПРЛ, МПТ и АГМС разрешается после их постановки на тормоза..
Руководитель работ должен проследить, чтобы машинист перед началом движения, каретки с краном, а также перед началом грузовых операций крана предупредил об этом рабочих звуковым сигналом..
Работой по погрузке и выгрузке краном на дрезинах ПРЛ, МПТ, АГМС должен руководить работник по должности не ниже бригадира пути, который обязан следить, чтобы во время работы крана никто не находился под стрелой и поднятым грузом..
Перед пропуском поезда по соседнему пути поднятый груз должен быть опущен и работа крана прекращена..
При погрузке и выгрузке рельсов и стрелочных переводов для удержания груза должны применяться гибкие чалочные приспособления..
При погрузке и выгрузке шпал и брусьев краном необходимо соблюдать следующие меры предосторожности:.
ѕ строповку пакетов шпал и брусьев производить исправными и испытанными тросами;.
ѕ захватывать пакет так, чтобы исключить смещение и развал пакета;.
ѕ рабочие-стропальщики должны поддерживать и направлять пакет специальными оттяжками, находясь от поднимаемого груза на расстоянии неближе 2 м..
Передвижение дрезин ПРЛ, МПТ и АГМС с грузом на крюке крана разрешается при скорости не более 5 км/ч..
Общие требования к погрузке, выгрузке опасных грузов.
Погрузка, выгрузка опасных грузов должны производиться в соответствии с требованиями Устава железных дорог, Правил перевозок грузов, другой нормативно-технической документации..
Грузоотправители (грузополучатели) обязаны иметь лицензию на погрузочно-разгрузочную деятельность.
Грузоотправители — владельцы собственных или арендованных специализированных вагонов для перевозки опасных грузов перед каждой погрузкой должны предъявлять работникам станции и вагонного депо свидетельство (по форме) о технической исправности вагонов, включая его рабочее и конструктивное оборудование, гарантирующее безопасность перевозок конкретного опасного груза. Номер свидетельства работники вагонного хозяйства проставляют в специальной книге формы ВУ-14, а ответственный представитель грузоотправителя на обратной стороне накладной в графе 4 должен произвести запись: «Вагон в техническом и коммерческом отношении исправен, пригоден для перевозки конкретного опасного груза, его рабочее и конструктивное оборудование соответствует установленным требованиям» и заверить ее своей подписью.
Налив вагонов-цистерн опасными грузами разрешается производить только после осмотра вагонов-цистерн персоналом наливного пункта и записи о пригодности их для перевозки указанного продукта в журнале установленной формы.
Перед началом погрузки и выгрузки опасных грузов на сливо-наливной эстакаде вагоны-цистерны должны быть надежно закреплены с обеих сторон тормозными башмаками, а стрелки переведены в положение, исключающее возможность попадания на путь погрузки (выгрузки) вагонов другого подвижного состава.
При невозможности перевода стрелок в положение, исключающее попадание подвижного состава на путь погрузки (выгрузки), должны предусматриваться другие технические меры, исключающие такую возможность.
Грузоотправитель обязан загружать вагоны, контейнеры опасными грузами не выше норм, установленных стандартами или техническими условиями на данную продукцию.
Погрузка и выгрузка на станциях легковоспламеняющихся грузов, перевозимых мелкими отправками или в контейнерах, должны производиться на неэлектрифицированных путях. В исключительных случаях, когда выделение таких путей не представляется возможным, по разрешению начальника отделения дороги для этих целей могут использоваться электрифицированные пути, контактная сеть которых должна быть выделена в самостоятельную группу с электропитанием через отдельный секционный разъединитель, оборудованный дополнительным заземляющим ножом. Напряжение с контактной сети должно быть снято.
Размещение и крепление опасных грузов в вагонах (кроме вагонов-цистерн) и контейнерах, а также специализированных контейнеров на открытом подвижном составе должны производиться в соответствии с «Техническими условиями погрузки и крепления грузов». Способы размещения и крепления опасных грузов в контейнерах разрабатывает и утверждает грузоотправитель по согласованию с отделением железной дороги. Эти способы должны соответствовать требованиям главы I «Технических условий погрузки и крепления грузов», утвержденных МПС России.
Материал, используемый для крепления грузов в вагонах и контейнерах, должен быть инертным по отношению к перевозимому опасному грузу.
Опасные грузы должны иметь тару и упаковку в соответствии с ГОСТ 26 319–84 и Правилами перевозок грузов. Опасные грузы, следующие в районы Крайнего Севера и отдаленные районы с резкими колебаниями температур, должны иметь тару и упаковку повышенной прочности в соответствии с ГОСТ 15 846–2002 «Продукция, отправляемая в районы Крайнего Севера и приравненные к ним местности. Упаковка, маркировка, транспортирование и хранение».
Перевозка мелкими отправками опасных грузов в стеклянной таре (кроме грузов в мелкой расфасовке массой до 1 кг, но объемом не более 1 л).
Перевозка опасных грузов в мелкой расфасовке массой нетто не более 1 кг, но объемом не более 1 л осуществляется в соответствии с Правилами перевозок грузов.
При отгрузке грузов мелкими отправками тара должна быть испытана по требованиям, предусмотренным для I группы упаковки по ГОСТ 26 319–84.
Работа с взрывчатыми веществами (ВВ) и материалами (ВМ) По железным дорогам разрешается перевозить ВВ только в крытых вагонах, как целыми поездами, так и отдельными вагонами, а также ручной кладью. Поезда или отдельные вагоны должны сопровождаться вооруженной охраной.
При погрузке или выгрузке на общих станционных путях, одновременно подаются для погрузки или выгрузки лишь два вагона. Загруженные вагоны отводятся в места, установленные для стоянки грузов ВВ, на расстояние не менее 100 м до погрузочного пункта.
Такой порядок соблюдается до окончания всей погрузки или выгрузки.
Лица, сопровождающие вагоны с ВВ, должны находиться в одном из ближайших к ним вагонов поезда, но не ближе, чем через шесть вагонов с неопасными грузами, и следить за состоянием вагонов с грузом в пути.
Вагоны с ВВ вне поезда должны быть сцеплены, заторможены, подклинены и ограждены переносными сигналами (красными дисками, фонарями с красным светом). Сигналы устанавливаются по обоим концам группы вагонов с грузами ВВ у внутренней грани правого рельса на расстоянии 50 м от стоянки вагонов. Если состав занимает весь путь или стоит к предельному столбику ближе 50 м, то сигналы ставятся также у грани рельса против предельного столбика.
Станционные пути для погрузки или выгрузки вагонов с ВВ изолируются от других путей, для чего, стрелки, ведущие на эти пути, запираются на замки.
После пломбирования вагонов, на двери каждого из них с обеих сторон наклеиваются белые плакаты с надписью черными буквами «Опасно». Размеры плакатов 60×60 см.
При формировании поездов, вагоны с грузами ВВ должны ставиться в середине с соблюдением установленных норм (по весу и длине поезда), технического состояния и правильности размещения всех вагонов в составе.
Вагоны с детонаторами должны быть отдельны не менее чем шестью вагонами от вагонов с ВВ. Вагоны для людей отделяются от груза ВВ не менее чем шестью вагонами с неопасными грузами.
Маневры поезда с ВВ должны производиться с особой осторожностью, без толчков и резких остановок. Запрещается свободный спуск с горок вагонов с ВМ. Скорость движения при маневрах не должна превышать 10 км/ч.
Перекатка вагонов с ВВ вручную запрещается. При рельефе полотна без уклона, ручная перекатка допускается только в пределах длины погрузочно-разгрузочной платформы или хранилища под наблюдением лица, ответственного за погрузку или выгрузку.
При наружном осмотре в ночное время вагонов, груженных ВВ, разрешается применять электрические фонари, рудничные аккумуляторные светильники или предохранительные бензиновые лампы, а также полностью остекленные свечные фонари. Запрещается при этом пользоваться открытым огнем.
Запрещается загружать вагоны выше сверхустановленной их грузоподъемности, причем для аммиачно-селитренных ВВ, ОШ и ДШ загрузка разрешается до полной грузоподъемности вагона; для ВМ I и IV групп — не свыше двух третей грузоподъемности вагона.
Вагоны с ВВ не могут ставиться в поезде рядом с холодными локомотивами или платформами, гружеными бревнами, железными балками, рельсами и тому подобными грузами, которые могут сдвигаться при толчках и быстрой остановке.
На новостройках железных дорог и при борьбе со льдом у железнодорожных мостов разрешается перевозка ВВ на платформах рабочих поездов, мотовозов и дрезин при соблюдении правил совместной перевозки ВВ, при обязательном сопровождении ВВ охраной и взрывником и при наличии противопожарных средств (огнетушителей, ящиков с песком, бочек с водой, вёдер, лопат).
На открытых работах допускается использование для перевозки ВВ платформы мотовозов или дрезин при соблюдении указанных требований и устройств между платформами и моторными отделениями сплошных перегородок из несгораемых материалов.
7.2 Расчёт безопасных расстояний при передаче детонации, действию УВВ и ядовитых газов Расчёт безопасных расстояний при передаче детонации Таблица 7.2. — Исходные данные.
Тип ВВ в вагоне. | Масса ВВ в вагоне, т. | Расстояние между вагонами с ВВ, м. | Скорость ветра, м/с. | Направление ветра. | Температура воздуха. | |||
активном. | пассивном. | активном. | пассивном. | |||||
Тротил. | АС ВВ. | Юго-восточное. | отрицательная. | |||||
Расстояние, исключающее возможность передачи детонации от взрыва на земной поверхности одного объекта со взрывчатыми материалами — активного заряда к другому такому объекту — пассивному заряду, определяется по формуле.
(7.1).
где — безопасное расстояние от центра активного до поверхности пассивного заряда, м;
— коэффициент, значение которого зависит от вида взрывчатых материалов зарядов и условий взрыва (см. таблице 7.3);
Q — масса ВВ активного заряда, кг;
b — меньший линейный размер пассивного заряда (ширина штабеля), м.
Определяется безопасное расстояние между двумя объектами (площадками, вагонами) по формуле (7.1), считая поочередно каждый объект за активный заряд. За безопасное расстояние между объектами принимается большее из двух рассчитанных. При размещении ВВ в расположенных по одной оси объектов удлиненной формы безопасное расстояние между ними во всех случаях составляют не менее удвоенной ширины большего (по ширине) объекта.
При любом расположении объектов (вагонов, площадок) безопасное расстояние не менее разрыва, установленного правилами противопожарной защиты.
Если при проектировании площадки сближаются объекты (площадки) на расстояние меньшее, чем определено по формуле (7.1), безопасные расстояния для такого объекта определяется исходя из суммарного запаса ВВ в вагоне.
Если пассивный заряд состоит из разных ВВ (например, аммонита и тротила), при расчете безопасных расстояний значение коэффициента выбирается для того ВВ (из числа входящих в состав заряда), которое обладает наибольшей чувствительностью к детонации.
Таблица 7.3 Значения коэффициента для расчета расстояний, безопасных по передаче детонации.
ВМ. | ВВ с содержанием нитроэфиров 40% и более. | ВВ с содержанием нитроэфиров 40% и более. | Тротил. | Детонаторы. | |
ВВ на основе аммиачной селитры с содержанием нитроэфиров до 40%. | 0,8. | 1,1. | 1,3. | 0,8. | |
ВВ с содержанием. нитроэфиров 40% и более. | 1,6. | 2,3. | 2,5. | 1,6. | |
Тротил. | 1,3. | 1,6. | 1,9. | 1,3. | |
Детонаторы. | 0,4. | 0,75. | 0,7. | 0,4. | |
После определения безопасного расстояния определяется общая масса взорвавшегося заряда ВВ.
Qo = Qa + Qn (7.2).
Qn — масса пассивного заряда.
Qo = 50 000 + 100 000 = 150 000 кг.
Пусть теперь в составе перевозятся совместно с тротилом 500 000 электродетонаторов (капсюлей-детонаторов). Определим безопасное расстояние на передаче детонации между объектами.
Определим массу ВВ (кг), содержащегося в электродетонаторах,.
.
где q =0,0015 кг — масса ВВ в одном ЭД, n — число ЭД.
кг.
За активный заряд принимаем вагон с ЭД. По таблице 7. 3 находим значение = 0,7 для условий передачи детонации от открытого заряда детонаторов к отрытому заряду тротила; b = 1,6 м.
Безопасное расстояние по передаче детонации без учета противопожарного разрыва и размещения вагонов м.
Определение расстояний, безопасных по действию ударной воздушной волны (УВВ) при взрывах.
Расстояния, безопасные по действию ударной воздушной волны на здания и сооружения:.
1) безопасные расстояния по действию ударной воздушной волны при взрыве на земной поверхности для зданий и сооружений рассчитываются по формулам:.
(7.3).
(7.4).
где — безопасное расстояние, м; Q — масса заряда ВВ, кг; , — коэффициенты пропорциональности, значения которых зависят от условий расположения и массы заряда, от степени допускаемых повреждений зданий или сооружений (таблице 7.4).
Формулы (7.3) и (7.4) применяют для определения относительно безопасных расстояний до зданий (сооружений) от мест нахождения ВВ, хранения ВМ на складах (хранилища, площадки и тому подобное), мест погрузки, разгрузки и переработки ВВ, отстоя транспортных средств с ними, от мест взрывов наружных зарядов и зарядов выброса.
Формула (7.3) применяется при допустимости первой — третьей степеней повреждений для открытых (наружных) зарядов массой больше 10 т. Формулу (7.4) применяют при допустимости первой — третьей степеней повреждений для открытых зарядов массой менее 10 т Кроме того, формула (7.4) применима при допустимости четвертой-пятой степеней повреждений независимо от массы и расположения заряда;
2) при пользовании таблице 7.4 руководствоваться следующим:
при выборе степени повреждения и значений коэффициентов учитывается вся совокупность местных условий, причем в сложных случаях в выборе степени безопасности участвует руководитель организации, представители заинтересованных организаций, владеющих объектами.
степень повреждения и значения коэффициентов при выборе местоположения объектов с ВВ устанавливается в зависимости от значимости объектов, расположенных в районе размещения ВВ.
В общих случаях при расчете безопасных расстояний от объектов с ВВ до населенных пунктов, автомагистралей, крупных водных путей, заводов, складов взрывчатых и огнеопасных материалов и сооружений государственного значения принимается третья степень повреждения.
Таблица 7.4 Значения коэффициентов и для расчета расстояний, безопасных по действию УВВ при взрыве.
Степень повреждения. | Возможные повреждения. | n = 3. | ||||
Q, т. | ||||||
Отсутствие повреждений. | <10. | 50−150. | ; | 3−10. | ||
>10. | ; | ; | ||||
Случайные повреждения застекления. | <10. | 10−30. | ; | ; | ||
>10. | ; | 60−100. | 1−2. | |||
Полное разрушение застекления. Частичные повреждения рам, дверей, нарушение штукатурки и внутренних легких перегородок. | <10. | 5−8. | ; | ; | ||
>10. | ; | 30−50. | 0,5−1. | |||
Разрушение внутренних перегородок, рам, дверей, бараков, сараев и т. п. | ; | 2−4. | ; | Разрушение в пределах воронки. | ||
Разрушение малостойких каменных и деревянных зданий, опрокидывание железнодорожных составов. | ; | 1,5−2. | ; | ; | ||
Для отдельно стоящих зданий и других сооружений второстепенного значения, автомобильных и железных дорог с небольшим движением, для особо прочных сооружений (стальные и железобетонные мосты, стальные и железобетонные копры, элеваторы, углемойки и тому подобное), принимается четвертая степень повреждения;
при определении расстояний до линии электропередачи исходят из значений радиуса разлета кусков, поскольку линии электропередачи относятся к категории конструкций, стойких по отношению к действию ударной воздушной волны;
коэффициенты в таблице 7.4 указаны не однозначно. То или иное значение выбирается в зависимости от состояния объекта, для которого устанавливаются безопасные расстояния: чем прочнее этот объект, тем меньшее значение коэффициента принимается при расчете в пределах значений, указанных в таблице 7.4;
свойства ВВ при расчете безопасных расстояний не учитываются.
3) Если защищаемый объект расположен непосредственно за преградой (на опушке густого леса, у подножия холма), стоящей на пути распространения ударной воздушной волны, то безопасное расстояние, определенное по приведенным формулам, уменьшается, но не более чем в 2 раза.
4) Если за местом взрыва в радиусе 1,5 имеются прочные преграды в виде стен, валов и тому подобное, в направлении, противоположном этим преградам, безопасное расстояние увеличивается: при расчете по формуле (7.3) — в 1,3, а по формуле (7.4) — в 1,4 раза.
Расстояние (м), безопасное по действию на человека ударной воздушной волны наружного заряда, определяется по формуле.
(7.5).
где Q — масса взрываемого наружного заряда ВВ, кг.
Формула (7.5) используется только, если по условиям работ допускается максимальное приближение персонала к месту взрыва. В остальных случаях полученное по формуле расстояние увеличивается в 2 — 3 раза.
— при нахождении персонала вблизи места взрыва, для остального населения, например, населенного пункта это расстояние составит:
rmin = (2 — 3)*800 = 1600 — 2400 м.
Безопасное расстояние по действию УВВ при взрыве ВВ на земной поверхности для окружающих зданий находим по формулам 7.3 — 7.4 и таблице 7.4. и учетом отрицательных температур:
Определение расстояний, безопасных по действию ядовитых газов при взрыве зарядов на выброс.
При одновременном взрыве зарядов общей массой более 200 т учитывается газоопасность взрыва и устанавливается безопасное расстояние, за пределами которого содержание ядовитых газов (в пересчете на условную окись углерода) не должно превышать ПДК.
Безопасное по действию ядовитых газов расстояние (м) в условиях отсутствия ветра или в направлении, перпендикулярном к распространению ветра, при взрыве зарядов на выброс определяется по формуле.
(7.5).
где Q — суммарная масса взрываемых зарядов, т.
В направлении, противоположном распространению ветра, радиус газоопасной зоны принимается также равным. По направлению ветра радиус газоопасной зоны определяется по формуле.
м, (7.6).
где — скорость ветра перед взрывом, м/с.
Схема расположения.
1 — населенный пункт; 2 — дачный поселок; 3 — железнодорожный состав; 4 — направление ветра Условные обозначения.
— граница зоны действия УВВ на людей (1600 — 2400 м);
— граница зоны разрушений зданий и сооружений (5180,5 м);
— граница зоны действия УВВ на ближний персонал (800 м);
— граница зоны распространения ядовитых газов с ветром (1700,25 м);
— граница зоны распространения ядовитых газов без ветра (8501,27 м);
Заключение
В дипломном проекте разработаны два варианта производства капитального ремонта пути, с фронтом работ 1500 м. в первом варианте предусмотрены комплексные работы по глубокой очистке щебня с применением двух машин СЧ-601 с укладкой геотекстиля и замене РШР, все работы выполняются в одно «окно». В этом варианте технологического процесса занято 76 монтеров пути и 42 машиниста.
Во втором варианте технологического процесса, рассматривается вариант по глубокой вырезке балласта и укладки материала «Криогелит» с заменой РШР, взамен двух щебеноочистительных машин используется машина СЧУ-800 и автотракторная техника (грейдер и бульдозер). Работы выполняются в одно «окно». В работе задействовано 64 монтера пути и 43 машиниста.
Также в работе разработан технологический процесс по смене инвентарных рельсов на бесстыковые рельсовые плети со сваркой плетей машиной ПРС-4 и принудительным вводом их в температурный режим с применением ГНУ и НУ, фронт работ — 1600 м. в «окно» задействовано 54 монтера пути и 35 машинистов. Сварка плетей, выгруженных во внутрь колеи производится машиной ПРС-4 в начале «окна».
Сборка инвентарных рельсов производится под прикрытием «окна» по укладке рельсовых плетей, на предыдущем участке.
По разработанным данным видно, что наиболее выгодным с экономической точки зрения является первый вариант. Несмотря на то, что первый вариант на производство работ занимает 14 часов, а второй 12 часов минут. В этом случае главную роль сыграл тот фактор, что стоимость материалов (раствор «Криогелит») оказалась значительно большей и в процесс очистки балласта участвует только одна машина СЧУ-800.
График производства работ по дням существенной роли не играет, т. к. он подходит к обоим вариантам и составляет 37 календарных дней.
Также в проекте рассмотрены вопросы по технике безопасности при движении поездов, при проведении путевых работ, ТБ по проведению основных работ и охрана труда.
В разделе 5 по безопасности и экологичности проекта рассмотрена тема по безопасному проведению погрузочно-разгрузочных работ во время проведения путевых работ, а также рассмотрен вопрос о безопасных расстояниях при передаче детонаций, действию УВВ и ядовитых газов при перевозке опасных грузов (взрывчатых и ядовитых веществ). Произведен соответствующий расчёт.
В разделе 6 рассмотрена инженерная деталь — стяжной прибор. Приведена технологическая карта из ТОНВ «РЖД» № 69 по производству работ и нормам времени при регулировке ширины рельсовой колеи при раздельном скреплении с применением стяжного прибора.
Список литературы
ремонт путевой рельса.
1. «Технические условия на работы по реконструкции (модернизации) и ремонту железнодорожного пути», утвержденных ОАО «РЖД№ 18.01.2013 г.,.
2. «Положение о системе ведения путевого хозяйства ОАО «РЖД», утвержденных 31.03.2000 г. и дополненных 01.02.2009 г.
3. «Технические указания по устройству, укладке, содержанию и ремонту бесстыкового пути», утвержденных 31.03.2000 г. и дополненных в 2010 г.
4. З. Л. Крейнис, Н. П. Коршикова «Техническое обслуживание и ремонт железнодорожного пути» .
5. «Технологический процесс усиленного капитального ремонта бесстыкового пути с глубокой очисткой щебёночного балласта от засорителей с выполнением всех работ комплексом основных машин: УМ, ЩОМ-4М, УК — 25/9−18, ВПО-3000, ЭЛБ-Р, ОТ-400, ВПР-02, ДСП, ПБ, шлифовального поезда.
6. «Инструкция по обеспечению безопасности движения поездов при производстве путевых работ» под редакцией А. С. Яновского.
7. В. С. Крутяков «Охрана труда и основы экологии на железнодорожном транспорте и в транспортном строительстве» .
8. Сборник технологических процессов капитального ремонта пути / ОАО «РЖД», 1996;2014.