Эксплуатация и ремонт оборудования компрессорных станций
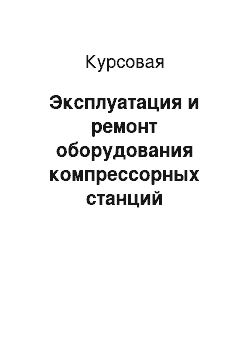
СИСТЕМА ПОДАЧИ ОХЛАЖДАЮЩЕЙ ЖИДКОСТИ Система, подачи охлаждающей жидкости предназначена для отвода тепла из системы смазки агрегата и рассчитана на круглогодичную работу на 60%-ном растворе этиленгликоля в воде. Системам подачи охлаждающей жидкости представляет собой замкнутую систему, в которую входят: маслоохладители; клапан VTR-1 для регулирования температуры смазочного масла; расширительный… Читать ещё >
Эксплуатация и ремонт оборудования компрессорных станций (реферат, курсовая, диплом, контрольная)
В непростом для мировой экономики 2009 году «Газпром» уверенно продолжил развитие по всем направлениям деятельности — разведка, добыча, транспортировка нефти, диверсификация видов продукции, маршрутов, регионов поставки. Стратегические проекты продвигаются на Север, Юг, Запад и Восток, преодолевая границы и континенты, укрепляя позиции «Газпрома» как глобальной энергетической компании.
На севере идет активная реализация мегапроекта «Ямал». В 2009 году «Газпром» ввел в эксплуатацию уникальный мостовой переход железной дороги «Обская — Бованенково» через реку Юрибей. Это самый длинный в мире мост за Полярным кругом. Продолжена первая нитка подводного перехода через Байдарацкую губу — наиболее сложного участка системы магистральных газопроводов «Бованенково — Ухта». Ведется обустройство Бованенковского месторождения.
На Юге «Газпром» построил подводный газопровод «Джубга — Лазаревское — Сочи». Этот объект — весомый вклад компании в обеспечение энергией XXII зимних Олимпийских игр 2014 года. Не менее значимым событием стал ввод в эксплуатацию самого высокогорного в мире газопровода «Дзуарикау — Цхинвал», жизненно необходимой энергетической артерии, которая соединила Южную Осетию и Россию. На Востоке в 2009 году был сварен первый стык магистрали «Сахалин — Хабаровск — Владивосток», положивший начало созданию газотранспортной системы в этом регионе. А в рамках проекта «Сахалин-2» впервые в истории России начат экспорт отечественного сжиженного природного газа на новые для компании рынки сбыта — в страны Азиатско-Тихоокеанского региона. Полным ходом идет выполнение масштабной Восточной газовой программы, координатором которой правительство Российской Федерации назначило «Газпром».
На Западе «Газпром» уверенно продвигается к намеченной цели — обеспечению сверхнадежных и бесперебойных поставок газа на европейский рынок. В 2009 году были получены все разрешения, необходимые для начала строительства газопровода «Северный поток». Сейчас идет прокладка газопровода по дну Балтийского моря. Значительно продвинулись и работы по проекту «Южный поток». Уже заключены все необходимые межправительственные соглашения по этому проекту с зарубежными партнерами. Кроме того, были достигнуты договоренности об увеличении вдвое производительности морского участка «Южного потока» — с 31 до 63 млрд куб. м.
Укрепляя свои позиции на глобальном энергетическом рынке, «Газпром» не менее активно реализует и социально значимые проекты, прежде всего выполняя Программу газификации регионов России. Уровень газификации нашей страны к концу 2009 года достиг 63,2%. Эта работа компанией будет продолжена.
Разработка газовых и газоконденсатных месторождений в системе ОАО «Газпром» должна обеспечить добычу газа к 2015 году около 820 миллиардов метров кубических, а конденсата в 2015 и 2030 годах приблизительно 19,4 миллионов тонн.
Учитывая моральное и физическое старение парка газотурбинных установок, их реконструкция и обновление являются приоритетными проблемами транспорта газа. Всего имеется более 20 типов газотурбинных установок мощностью от 2,5 до 25 мегаватт с коэффициентом полезного действия от 23 до 34% (среднее значение 27,6%). Прогнозируется совершенствование газовых турбин газоперекачивающих агрегатов, как правило, силами конверсионных мероприятий обеспечивающих повышение коэффициента полезного действия каждого из существующих типов газотурбинных установок максимально до 46%.
К работам по созданию некоторых видов новой газоперекачивающей техники привлечены ведущие зарубежные компании. Так АО «Люлька-Сатурн» в кооперации с фирмой «Нуово-Пиньюони» создает новые агрегаты мощностью 16 мегаватт с использованием Российского газогенератора. Совместно с фирмой «Купер-Роллс» ведутся работы по модернизации камеры сгорания двигателя АЛ-31СТ с целью снижения выбросов окислов азота. Пермские предприятия «Авиадвигатель» и «Пермские моторы» планируют проведение работ совместно с фирмой «Пратт энд Уитни» по увеличению ресурса надежности и экологической безопасности двигателей мощностью 12 416 МВт.
Применение газоперекачивающих агрегатов нового поколения позволит на 25−30% сократить потребление газа на технологические нужды, снизить выброс окислов азота, повысить надежность транспортировки газа.
1. ОБЩАЯ ЧАСТЬ
1.1 Характеристика компрессорного цеха В курсовом проекте рассматривается эксплуатация компрессорного цеха № 4 Антиповского ЛПУМГ, оборудованного ГПА ГТК-10И.
Антиповское линейное производственное управление магистральных газопроводов — один из 14 газотранспортных филиалов «Волгоградтрансгаз».
В Антиповское ЛПУМГ входит — Антиповская КС с сетью магистральных газопроводов и ГРС на с. Антиповка, автомобильная газонаполнительная компрессорная странция г. Камышина, Коробковская и Жирновская промплощадки с сетью магистральных газопроводов и ГРС.
Основная задача Антиповского ЛПУМГ — транспортирование газа с заданными параметрами по магистральным газопроводам «Средняя Азия — Центр III» (САЦ — III), «Средняя Азия — Центр IV-I» (САЦ — IV-I), «Средняя Азия — Центр IV-II» (САЦ — IV-I), «Оренбург — Новопсков», «Союз» с целью бесперебойной поставки газа потребителям в соответствии с утвержденным планом.
Общая протяженность газопроводов в однониточном исчислении в зоне ответственности КС Антиповка — 429,7 км. Прокладка газопроводов — подземная, глубина заложения газопроводов с условным диаметром до 800 мм включительно — 0,8 м, с условным диаметром 1400 мм — 1,0 м до верха трубы. Количество компрессорных станций — 1. Количество газораспределительных станций — 1. Автомобильных газонаполнительных компрессорных станций — 1.
Антиповская КС расположена на 251-м км по трассе газопровода САЦ-III, в 3,6 км к югу от села Антиповка, в 500 м от уреза воды на правом берегу реки Волга. Основная территория КС (т.е. месторасположение 4-х компрессорных цехов) имеет форму правильного прямоугольника, вытянутого в направлении с востока на запад. К северу от основной территории КС расположены 4 узла подключения станции к магистральным газопроводам, причем на различных расстояниях о границы станции. На минимальном (250 м) находится узел подключения к САЦ-III, на максимальном (500 м) — узел подключения газопровода «Союз». Территории узлов подключения, огорожены заборами из металлической сетки на бетонных столбах, являющимися границами узлов.
Коридор магистральных газопроводов, находящихся в ведении Антиповского ЛПУМГ, проходит в направлении с востока на запад от левого берега реки Волга до правого берега реки Иловля. Протяженность коридора магистральных газопроводов составляет 76 км (от 245-го до 321-го км по трассе магистрального газопровода САЦ-III). Из них 69 км относится к сухопутным участкам и 7 км — к крупным подводным переходам через реки Волга и Иловля. Ширина коридора из пяти ниток магистральных газопроводов с учетом расстояний между ними (между нитками САЦ — по 13 м, между САЦ-IV-II и «Оренбург — Новопсков» — 13 м, между газопроводами «Оренбург — Новопсков» и «Союз» — 15 м) и охранной зоны на землях сельскохозяйственного назначения (100 м) составляет на сухопутных участках 154 м. С учетом этого площадь занимаемых земель под главный коридор на суше — 10,63 км².
Общая протяженность газопроводов-отводов — 30,8 км при ширине охранной зоны 100 м. Площадь занимаемых земель — 3,1 км².
Ширина створа подводного 9-ниточного перехода через р. Волга составляет 700 м при протяженности 5,2 км. Ширина створа подводного 6-ниточного перехода через р. Иловля — 350 м при протяженности 2 км. Занимаемая площадь — 4,4 км².
Объекты обслуживания Антиповского ЛПУМГ располагаются на Приволжской возвышенности (высота промплощадки Антиповской КС над уровнем моря 162 м), к западу от правого берега р. Волга. В районе расположения КС и коридора магистральных газопроводов преобладает степной микрорельеф — покрытая травой равнина, пересекаемая отдельными балками и реками. Территория КС — незатопляемая.
Коридор газопроводов пересекает 4 основных водных преграды:
р. Волга: ширина зеркала воды — 4 км, глубина до 29 м, скорость течения до 0,5 м/с;
р. Балыклейка: ширина зеркала воды — 200 м;
р. Зензеватка: ширина зеркала воды — 70 м;
р. Иловля: ширина зеркала воды — 130 м, глубина до 3 м, скорость течения до 0,5 м/с.
Основные типы грунтов на трассе газопроводов — суглинок (252−364, 267−303 км трассы газопровода САЦ), известняк (264−267 км), пески (303−317 км). Заболоченные участки, карсты, подземные выработки отсутствуют. На обоих берегах р. Волга имеется вероятность размыва грунта и оголения трубопроводов. Аналогичные проблемы характерны для переходов газопроводов через р. Иловля, балку Венцы, Пеньковскую балку.
Характер застройки площадки КС «Антиповская» — промышленные, малоэтажные здания и сооружения. В северной части территории КС на открытых площадках расположено оборудование (пылеуловители, аппараты воздушного охлаждения газа, краны пускового контура, блок-контейнеры ГПА, компрессорные цеха № 1 и № 2). В южной части территории КС расположены служебно-эксплуатационного и ремонтного блоков, производственно-энергетического блока, прочие строения.
Территория зоны ответственности Антиповского ЛПУМГ включает площадь земель Волгоградской области, отведенных под трассы магистральных газопроводов КС «Антиповская» с узлами подключения КС к магистральным трубопроводам и промплощадки Антиповского ЛПУМГ.
Общая протяженность линейной части газопроводов Антиповского ЛПУМГ: 429,7 м.
В зоне ответственности Антиповского ЛПУМГ расположено 25 подземных переходов через автомобильные дороги, 5 подземных переходов через железные дороги, 5 воздушных переходов, 23 пересечения с инженерными коммуникациями. Переходы являются участками с повышенной вероятностью возникновения ущерба от возможных аварий на газопроводах.
КС «Антиповская» состоит из 4 цехов.
Цех № 1 подключен к магистральному газопроводу САЦ-IV-I, САЦ-IV-II Ду=1200 мм, Рраб=55 кгс/см2. Цех № 2 подключен к магистральному газопроводу САЦ-III Ду=1200 мм, Рраб=55 кгс/см2. Цех № 3 подключен к магистральному газопроводу «Оренбург — Новопсков» Ду=1200 мм, Рраб=75 кгс/см2.
Цех № 4 подключен к магистральному газопроводу «Союз» Ду=1400 мм, Рраб=75 кгс/см2. Газ высокого давления из магистрали через входной шаровой кран № 7 узла подключения по всасывающему газопроводу-шлейфу (Ду=1400 мм) поступает через входной коллектор (Ду=1400 мм) системы очистки газа на батарею из 6-ти масляных пылеуловителей. После очистки газ попадает во всасывающий коллектор (Ду=1000 мм) и далее — во всасывающие газопроводы (Ду=600 мм) семи полнонапорных ГПА, работающих параллельно, в которых сжимается до проектного давления (75 кгс/см2).
Сжатый газ через нагнетательные газопроводы (Ду=600 мм) ГПА поступает в нагнетательных коллектор (Ду=1000 мм) и далее — в коллектора двух групп аппаратов воздушного охлаждения газа (АВО). После охлаждения в АВО до плюс 39−43 оС газ через выходные коллектора (Ду=1000 мм) АВО попадает в нагнетательный шлейф (Ду=1400 мм), по которому направляется к узлу подключения КС, попадая через кран № 8 в магистраль. Перемычки между нагнетательными газопроводами ГПА и всасывающими кранами №№ 6−6а образуют пусковые контура ГПА.
Сжатие газа осуществляется с помощью газотурбинных ГПА ГТК-10И, для пуска и работы которых требуются топливный и пусковой газ. Для их подготовки предусмотрен блок подготовки топливного и пускового газа, в состав которого кроме устройств редуцирования входят скруббер (пылеуловитель мультициклонного типа), уравнительные резервуары, сухие фильтры и газгольдеры. В качестве подсистемы в БПТПГ входит блок осушки для подготовки импульсного газа, состоящий из 4-х адсорберов.
Маслоснабжение цеха обеспечивается с помощью подземного склада масел, регенераторной и насосной склада масел. Для охлаждения масла служат маслоохладители типа 06−10.
1.2 Характеристика газоперекачивающего агрегата ГТК-10И Основным оборудованием на КС являются ГПА. В компрессорном цехе № 4 Антиповского ЛПУМГ установлено 7 ГПА ГТК-10И. В состав газоперекачивающего агрегата ГТК-10И входит газотурбинный двигатель (газотурбинная установка) модели MS-3000, который служит для привода центробежных нагнетателей, предназначенных для сжатия природного газа в магистральных газопроводах.
Газотурбинный двигатель Антиповского ЛПУМГ расположен в специальном боксе, который разделен на три отсека: вспомогательного оборудования, турбинный и выхлопной, изолированные друг от друга для обеспечения тепловой и акустической изоляции. Изнутри отсеки покрыты теплоизолирующими панелями.
В каждом отсеке поддерживается повышенное давление и осуществляется вентиляция, т. е. отвод тепла из отсеков для поддержания в них температуры ниже определенного значения.
Дифференциальные реле давления 63PF-1, 63PF-2 и 53PF-3 предохраняют отсеки от чрезмерного повышения давления. Тепловые реле 26ВА-1, 26ВА-2 и 26ВА-3, установленные в отсеках турбинном и вспомогательного оборудования сигнализируют о повышении температуры выше заданной величины вследствие неисправной работы вентиляционной системы.
На приточных воздуховодах в отсеках вспомогательного оборудования и турбинном установлены подогреватели, которые поддерживают температуру в пределах от -7 до +10° С. Подогреватели управляются термостатом 26ИА в отсеке вспомогательного оборудования и регулятором температуры 26НТ в турбинном отсеке.
Воздуходувки, имеющие условные обозначения 88НА и 88НТ, подают подогретый воздух, когда подогреватели находятся в действии. Отсеки оборудованы углекислотной системой пожаротушения. Для предотвращения выхода углекислоты во всех входных линиях воздуховода и на вентиляционных щелях отсеков установлены заслонки, которые автоматически закрываются при пожаре, когда повышается давление в отсеке от поступления углекислоты. Открывают заслонки вручную.
Газотурбинный двигатель и его вспомогательное оборудование смонтированы на стальной раме. В переднем конце рамы расположен выполненный за одно целое с ней маслобак. Внутри рамы расположены коллекторы подачи смазочного масла и сливные коллекторы.
Над маслобаком во вспомогательном отсеке смонтировано следующее оборудование: вспомогательный редуктор для привода главного насоса смазочного масла и электрогенератора, вспомогательный и аварийный насосы смазочного масла, главный и вспомогательный насосы гидропитания, главный щит манометров, главные фильтры смазочного масла, оборудование пусковой системы, блок регулирующего и стопорного клапанов топливного газа.
Газотурбинный двигатель опирается на основание двумя упругими пластинами, одна из которых находится под корпусом осевого компрессора, а другая под корпусом выхлопного устройства.
Эти опорные пластины исключают возможность боковых и вращательных движений двигателя, но в то же время допускают осевое перемещение в результате теплового расширения двигателя во время его работы. Осевое перемещение происходит вперед и назад от точки, зафиксированной шпонкой и расположенной под корпусом турбины.
Газотурбинный двигатель представляет собой двухвальную газовую турбину простого цикла. Он состоит из пятнадцатиступенчатого осевого компрессора, шести камер сгорания (расположенных под углом 90° к оси газовой турбины), одноступенчатой турбины высокого давления (первая ступень) для привода осевого компрессора и одноступенчатой турбины низкого давления (вторая ступень) для привода центробежного нагнетателя.
Эксплуатационные характеристики агрегата Агрегат ГТК-10И, находящийся в Антиповском ЛПУМГ, характеризуется быстрым запуском: время до выхода на режим холостого хода 3−3,5 мин, время до принятия полной нагрузки 7−8 мин.
Турбина высокого давления выводится на максимальную частоту вращения в течение 3−3,5 мин. Столь быстрое ускорение вала турбокомпрессора при пуске возможно благодаря поворотному направляющему аппарату силовой турбины, который увеличивает проходное сечение и распределяет большую часть энергии на ТВД. Только после достижения ТВД 99- 100% полной частоты вращения закрываются сопловые лопатки и начинается загрузка силовой турбины. Быстрое нарастание температуры отходящих газов, соответствующее еще большей скорости подъема температуры газов перед турбиной, сопряжено с применением точной и быстродействующей системы регулирования. В противном случае температура может оказаться выше предельного ее значения 540 °C.
Помимо различий в геометрии проточной части и газодинамических характеристик каждая турбина имеет свою индивидуальную настроечную характеристику, которая связывает степень сжатия и температуру на выходе при определенной температуре наружного воздуха, температуре перед турбиной и частоте вращения роторов ТВД и ТНД. Однако для всех турбин существует предельная температура на выходе 540 °C, которая не дает возможность поддерживать расчетную мощность при температурах выше +30° С.
Повышение температуры наружного воздуха приводит к снижению его плотности, а значит и к уменьшению расхода циклового воздуха и степени сжатия. Это, в свою очередь, приводит к еще более резкому падению мощности ГТУ и сопровождается снижением к.п.д. и увеличением удельного расхода топлива. Повышение температуры наружного воздуха на 1 °C сопряжено с падением мощности на 0,7% и к.п.д. на 0,2%. При понижении температуры наружного воздуха до -20 °С установка может развивать предельную мощность 120% (дальнейшее увеличение мощности не допускается по условиям прочности деталей, передающих крутящий момент).
Для более полного удовлетворения требований производительности и степени сжатия компрессорных станций, установленных на разных участках газопроводов, необходимо устанавливать центробежные нагнетатели, отличающиеся в первую очередь диаметром колес и числом ступеней.
Так, нагнетатели фирмы «Нуово-Пиньоне» марки PCL поставляют с тремя модификациями 500, 800 и 1000, указывающими диаметр рабочих колес (в мм).
Центробежный нагнетатель типа PCL 802/24 фирмы «Нуово-Пиньоне» предназначен для сжатия природного газа в магистральных газопроводах. Нагнетатель состоит из корпуса, торцовой крышки, диафрагмы, ротора с рабочими колесами, думмисом и полумуфтой, уплотнений и подшипников.
Корпус нагнетателя бочкообразный и открывается с одного торца. Корпус и торцовая крышка корпуса изготовлены из кованой стали. Всасывающий и нагнетательный патрубки приварены к корпусу. Корпус опирается на две продольные опорные лапы. Корпуса подшипников и гнезда торцовых уплотнений расположены на корпусе нагнетателя и на торцовой крышке. Подшипники и уплотнения при необходимости могут быть заменены без демонтажа корпуса нагнетателя.
На торцах вала установлены датчики для измерения вибрации. На торце вала со стороны упорного подшипника установлен датчик осевого сдвига. Датчики соединены с мониторами вибрации и осевого сдвига. Внутри корпуса компрессора имеется пакет Диафрагм, легко извлекаемый со стороны торцовой крышки при помощи специального приспособления. Диафрагмы предназначены для того, чтобы с наименьшими потерями энергии подвести и отвести газ от ступеней нагнетателя, обеспечивая максимально возможную равномерность параметров газа по сечению. Диафрагмы имеют горизонтальный и вертикальный разъемы, соединены между собой винтами и собраны в пакет набором осевых тяг. Пакет диафрагм, собранный в таком виде с ротором, вводят в корпус нагнетателя с помощью двух роликов, расположенных внизу диафрагмы. Пакет диафрагм фиксируется внутри корпуса буртиком, выполненным в корпусе.
На пакете диафрагм выполнен паз для О-образного уплотнительного кольца, которое предотвращает перетечку газа от нагнетательного патрубка к всасывающему. На торцовой крышке также установлены О-образные уплотнительные кольца. Для предотвращения перетечек между нагнетательными и всасывающими сторонами рабочих колес и между ступенями в пакете диафрагм установлены лабиринтные уплотнения. Во избежание повреждений вала и рабочих колес при случайном соприкосновении уплотнительные кольца изготовлены из легкого сплава. Уплотнительные кольца имеют горизонтальные разъемы: верхняя половина каждого кольца прикреплена к соответствующей диафрагме потайными винтами, нижние половины заведены в пазы и легко могут быть извлечены повертыванием на 180°.
Торцовые лабиринтные уплотнения вала неразъемные и прикреплены осевыми винтами к днищу корпуса и торцовой крышке. Перед первой ступенью установлен конфузор, который подводит по оси поток газа к всасывающей стороне первого рабочего колеса. Конфузор состоит из разъемной по горизонтали части, установленной в диафрагме, и наружной части, прикрепленной к торцовой крышке корпуса. На этом конфузоре предусмотрен штуцер, который выходит наружу через торцовую крышку. Этот штуцер присоединен к прибору, который по перепаду давлений на конфузоре определяет расход газа.
Перед вторым рабочим колесом также установлен конфузор.
Ротор нагнетателя состоит из вала, рабочих колес, думмиса, распорных втулок, упорного диска и соединительной полумуфты.
Вал изготовлен из кованой стали. Поверхности вала, свободные от рабочих колес, защищены распорными втулками из нержавеющей стали.
Рабочие колеса с лопатками закрытого типа. Каждое рабочее колесо перед посадкой на вал подвергается динамической балансировке и испытывается на прочность при скорости на 15% выше максимальной рабочей скорости. Рабочие колеса насажены на вал по горячей посадке и зафиксированы шпонками. Распорные втулки, установленные между колесами, насажены на вал также по горячей посадке и определяют точное положение рабочих колес на валу.
Два блокировочных кольца фиксируют на валу ротора рабочие колеса, распорные втулки и думмис. Блокировочные кольца в свою очередь зафиксированы стопорными радиальными винтами.
Ротор нагнетателя подвергается осевому усилию с направлением в сторону всасывания в результате разности давлений, имеющихся с двух сторон ротора. Это усилие частично уравновешивается при помощи думмиса, установленного за рабочим колесом второй ступени. Это уравновешивание достигается соединением полости за думмисом с всасывающей полостью нагнетателя. Осевое усилие, действующее при этом на думмис, направлено противоположно усилию, действующему на рабочие колеса нагнетателя, и следовательно, частично уравновешивает последнее. Остаточное осевое давление воспринимает упорный подшипник. Таким образом, обеспечивается устойчивость ротора в осевом направлении. Думмис изготовлен из кованой стали, насажен на вал по горячей посадке и закреплен на нем шпонкой.
Полумуфта, насаженная на вал ротора, представляет собой стальную кованую деталь и рассчитана на передачу максимальной мощности, вырабатываемой газовой турбиной.
Узел ротора, состоящий из вала, рабочих колес, распорных втулок, думмиса, блокировочных колец и полумуфты подвергается динамической балансировке.
Ротор опирается на два опорных подшипника и на двойной упорный подшипник.
Опорные подшипники скольжения эллиптического типа с принудительной смазкой. Подшипники стальные, внутри покрыты баббитом, состоят из двух половин с горизонтальным разъемом. Проворачивание подшипников по направлению вращения предотвращается штифтом, который выступает в верхней части. Масло под давлением подводится к подшипникам радиально и отводится по оси по бокам каждого подшипника.
Упорный подшипник, установленный на торце вала со стороны всасывания, состоит из двух самоустанавливающихся подшипников с шестью рабочими колодками. Упорная нагрузка равномерно распределяется на все рабочие колодки.
Температура упорного и опорных подшипников контролируется термопарами, установленными на каждом подшипнике.
1.3 Характеристика агрегатных систем ГТК-10И
1.3.1 СИСТЕМА СМАЗКИ Смазка газотурбинного агрегата ГТК-10И представляет собой замкнутую систему, состоящую из следующих элементов: маслобака, маслоохладителей, фильтров, клапанов и различных контрольных и защитных устройств.
Система смазки обеспечивает необходимую подачу масла к подшипникам газотурбинного двигателя, нагнетателя, а также к вспомогательным механизмам.
Весь поток смазочного масла фильтруется пятимикронными фильтрами. Масляный фильтр состоит из двух работающих поочерёдно фильтров с перепускным клапаном между ними, что позволяет производить осмотры корпусов и заменять фильтрующие элементы на работающем агрегате. Дифференциальный манометр, установленный на щите манометров в блоке вспомогательных механизмов, показывает перепад давлений на фильтре. Если перепад давления достигнет 1,5 кгс/см2, надо перейти на второй фильтр следующим образом:
открыть заполнительный клапан;
когда масло покажется в смотровом стекле дренажной линии, переставить перепускной клапан;
закрыть заполнительный клапан.
Чтобы сменить элементы на неработающем фильтре, необходимо открыть выпускной клапан и слить масло из корпуса.
Масло для смазки муфты фильтруется сдвоенным фильтром с размером ячеек 0,5 мкм. Манометр дифференциального давления, установленный на щите манометров в блоке вспомогательных механизмов, показывает перепад давления на фильтре. Когда перепад давления на фильтре достигнет 1 кгс/см2, надо перейти на второй фильтр, переключив перепускной клапан.
Для смены элементов на неработающем фильтре необходимо открыть выпускной кран и слить масло из корпуса в какую-нибудь емкость.
Весь поток смазочного масла охлаждается в маслоохладителе, прежде чем он поступит в коллектор подшипников. Два маслоохладителя с перепускные клапаном между ними установлены горизонтально на боковой стенке маслобака. Перепускной клапан направляет поток масла в любой маслоохладитель, что позволяет отключать любой из них для проверки или ухода, не прерывая подачу масла в систему смазки и не останавливая турбину.
1.3.2 ГИДРАВЛИЧЕСКАЯ СИСТЕМА Основная функция гидравлической системы — подача масла под давлением для привода регулирующих клапанов топливного таза, муфты сцепления турбодетандера и узла управления поворотными соплами второй ступени газовой турбины.
Источником масла для гидравлической системы служит система смазки газовой турбины.
Условно, с целью описания, гидравлическая система разделена на гидравлическую систему питания и на гидравлическую систему управления.
Гидравлическая система питания состоит из главного насоса с приводом от вала редуктора, вспомогательного насоса с приводом от электродвигателя переменного тока, двух фильтров с перепускным клапаном, реле давления и коллектора.
Гидравлический коллектор системы питания обеспечивает удобное соединение различных узлов, входящих в эту часть системы. Он находится в камере, смонтированной над маслобаком в отсеке вспомогательных механизмов.
Гидравлическая система управления осуществляет управление соплами второй ступени турбины, приводит в действие регулирующий и стопорный клапаны системы топливного газа и участвует в работе узла гидравлического выключения.
1.3.3 СИСТЕМА ПОДАЧИ ОХЛАЖДАЮЩЕЙ ЖИДКОСТИ Система, подачи охлаждающей жидкости предназначена для отвода тепла из системы смазки агрегата и рассчитана на круглогодичную работу на 60%-ном растворе этиленгликоля в воде. Системам подачи охлаждающей жидкости представляет собой замкнутую систему, в которую входят: маслоохладители; клапан VTR-1 для регулирования температуры смазочного масла; расширительный бак с датчиком уровня 71WL, срабатывающим при низком уровне охлаждающей жидкости; воздушно-водяные теплообменники (водоохладители) с оребренными трубами; два вентилятора 88СТ-1 и 88СТ-2 с приводом от электродвигателей переменного тока; два выключателя 39СТ-1 и 39СТ-2, срабатывающие от датчиков вибрации вентиляторов; два температурных датчика 26WC-1 и 26WC-2 для контроля температуры охлаждающей жидкости; фильтр; два центробежных насоса охлаждающей жидкости, приводимые в действие от электродвигателей переменного тока 88WC-1 и 88WC-2 датчик давления 63WC, срабатывающий при низком давлении жидкости в системе; отопительное устройство 23СК с термостатом 26СК, установленное в блоке электродвигателей; вентилятор для циркуляции воздуха 88СК с приводом от электродвигателя переменного тока.
Система действует следующим образом. Циркуляция охладителя осуществляется при помощи одного из двух центробежных насосов, смонтированных на основании блока охлаждающего и насосного агрегатов. Проходя через маслоохладитель, жидкость отбирает тепло, охлаждая тем самым масло системы смазки турбины. Расход охлаждающей жидкости, которая поступает в маслоохладитель, регулируется при помощи клапана регулятора VTR-1.
Маслоохладители установлены в маслобаке агрегата под блоком вспомогательных механизмов, а запорные краны — во впускном и выпускном трубопроводах маслоохладителей. Во время работы турбоагрегата включают только один маслоохладитель, а второй отключают путем закрытия запорных кранов во впускном и выпускном трубопроводах.
После маслоохладителя охлаждающая жидкость поступает в теплообменник (водоохладитель), где отдает тепло воздуху продуваемому через теплообменную поверхность двумя вентиляторами 88СТ-1 и 88СТ-2, установленными непосредственна под теплообменником.
Затем охлаждающая жидкость через фильтр вновь поступает во всасывающий коллектор насосов. Подпитывается система из расширительного бака, заполненного охлаждающей жидкостью.
1.3.4 ПУСКОВАЯ СИСТЕМА Пусковым устройством для ГТК-10И служит турбодетандер со ступенями давления, который через кулачковую муфту приводит в действие вспомогательный вал турбины и вал турбины высокого давления.
Пусковая система включает в себя следующие узлы: клапан-регулятор давления VPR-15, турбодетандер, предохранительный клапан VR-6, соленоидные клапаны 20SV и 20SG, редуктор давления VPR-40, аварийный дроссельный клапан и автомат безопасности от превышения частоты вращения турбодетандера.
Давление пускового газа, поступающего на вход турбо-детандера, регулируется при помощи клапана-регулятора давления VPR-15 с двойной точкой регулирования. Чтобы сдвинуть с места вал турбины высокого давления, требуется повышенный крутящий момент, развиваемый турбодетандером, а значит и повышенное давление пускового газа (первая точка задания давления клапана VPR-15). После того как вал турбины начинает вращаться, необходимо более низкое давление пускового газа на входе в турбодетандер (вторая точка задания давления), чтобы не превысить требуемое ускорение турбины.
1.3.5 СИСТЕМА ВОЗДУШНОГО ОХЛАЖДЕНИЯ И УПЛОТНЕНИЯ Система воздушного охлаждения и уплотнения предназначена для охлаждения различных частей турбины и для уплотнения подшипников газовой турбины и осевого компрессора. Воздух для охлаждения, и уплотнения поступает из осевого компрессора, а также из атмосферы.
Предусмотрено воздушное охлаждение следующих узлов газовой турбины дисков турбин первой и второй ступеней, сопловых лопаток и обойм этих лопаток турбины первой ступени; корпуса турбины, выхлопного устройства и опор внутреннего корпуса турбины.
Жаровые трубы и остальные детали камер сгорания охлаждаются цикловым воздухом.
Охлаждающий и уплотняющий воздух, поступающий от осевого компрессора, состоит из воздуха, отбираемого за десятой и пятнадцатой ступенями осевого компрессора и воздуха, прошедшего через уплотнения за пятнадцатой ступенью осевого компрессорам Воздух, отбираемый за пятнадцатой ступенью осевого компрессора через радиальные отверстия в диске пятнадцатой ступени, используется для охлаждения внутренней полости ротора турбокомпрессора и диска турбины первой ступени. Этот воздух через радиальные отверстия поступает в полый вал, проходит через диафрагму в рабочем колесе турбины в полость за рабочим колесом, а затем проходит через уплотнения рабочего колеса и смешивается с рабочим воздухом.
Воздух, прошедший через уплотнения за пятнадцатой ступенью осевого компрессора, используется для уплотнения подшипника № 2 для охлаждения диска первой ступени турбины.
Через отверстия в стенках сальника подшипника № 2 уплотняющий воздух выводится по наружным трубам, смешивается о воздухом, отбираемым за десятой ступенью компрессора, и используется для охлаждения диска второй ступени турбины.
Цикловой воздух после осевого компрессора поступает в воздухораспределительные кожухи камеры сгорания и охлаждает узлы камер сгорания, обойму сопловых лопаток первой ступени и сегменты статора над рабочим колесом первой ступени. Часть воздуха, обтекающего удерживающее кольцо соплового аппарата, входит внутрь сопловых лопаток и охлаждает их.
Сопловые лопатки первой ступени полые, внутри них установлены дефлекторы, которые направляют поток воздуха вдоль внутренних стенок лопаток для повышения эффективности их охлаждения. Далее этот воздух выходит через отверстия около задних кромок лопаток и смешивается с рабочим газом.
Атмосферный воздух используется для охлаждения задней части корпуса турбины и опор внутреннего корпуса турбины. Этот воздух засасывается через отверстия, просверленные в заднем вертикальном фланце корпуса турбины, благодаря разрежению, создаваемому эжекторами.
1.3.6 СИСТЕМА КОНТРОЛЯ ЗАГАЗОВАННОСТИ ВОЗДУХА Система контроля загазованности воздуха предназначена для определения и сигнализации об опасных концентрациях газа в индивидуальном укрытии турбоагрегата.
Система состоит из трех датчиков диффузионного типа, установленных в отсеках турбины и у нагнетателя, соединенных с модульными блоками типа 1400, установленными на пульте управления турбиной. Соответствие каждого блока установленному датчику определяется в период пуско-наладочных работ и идентифицируется надписью на блоке. Перестановка блоков запрещена.
1.3.7 СИСТЕМА ПОДОГРЕВА ВОЗДУХА НА ВХОДЕ В СЕВОЙ КОМПРЕССОР Система подогрева воздуха предназначена для поддержания постоянной положительной температуры воздуха на входе в осевой компрессор с целью предотвращения образования льда осенью и зимой. Условиями возможного образования льда считается температура наружного воздуха +3°С и ниже при относительной влажности свыше 80%. Входной воздух подогревают до температуры +4±1° С подачей горячих выхлопных газов в воздухо-заборную камеру (ВЗК), в которой они смешиваются с входящим воздухом. В систему подогрева входят следующие элементы:
источник горячих газов — выхлоп газовой турбины;
система трубопроводов, которая подает выхлопные газы на вход в ВЗК;
четыре термопары AT-ID для контроля средней температуры входного воздуха, установленные в ВЗК;
датчики перепада давления на впуске 63CS-1 и 63CS-2;
датчики давления на выхлопе 63ЕА и 63ЕТ;
температурные датчики 26ТР-1 и 26ТР-2 для защиты осевого компрессора от чрезмерно высокой температуры на входе;
заслонки ВВ, BV-1, BV-2 с приводом от электродвигателей и концевыми выключателями.
Система срабатывает в ответ на усредненные сигналы от термопар AT-1D. При температуре воздуха на входе свыше + 3 °C заслонки BV-1 и BV-2 находятся в закрытом положении, а заслонка ВВ полностью открыта. При уменьшении температуры на входе ниже +3°С система подогрева начнет регулировать положение заслонок только при соблюдении определенного соотношения между температурой воздуха на выходе и температурой наружного воздуха; т. е. система не будет действовать до тех пор, пока температура на выходе турбины не достигнет минимального допустимого уровня, обеспечивающего удовлетворительный нагрев.
Во время эксплуатации системы все заслонки открываются поочередно и работают в импульсном режиме. Первой начинает открываться заслонка BV-1 (работа 4 или 6 с, пауза 6 с), подавая выхлопные газы на вход в ВЗК, и будет открываться до тех пор, пока температура на входе в осевой компрессор не поднимется до +3°С или пока не сработает концевой выключатель 33BV-1, т. е. заслонка открывается полностью. Если полное открытие заслонки BV-1 окажется недостаточным для поддержания заданной температуры на входе, система выдает сигнал на прикрытие заслонки выхлопной трубы ВВ. Заслонка ВВ будет закрываться до тех пор, пока температура на входе не установится в заданном пределе или пока не сработает концевой выключатель заслонки ЗЗВВ-2. Концевой выключатель настроен таким образом, чтобы избыточное давление в выхлопной трубе не превышало 336 мм вод.ст. при максимальной нагрузке турбины.
В случае увеличения давления свыше 356 мм вод.ст. сработает датчик 63ЕА и загорится табло предупредительной сигнализации. При увеличении давления свыше 456 мм вод.ст. реле давления 63ЕТ остановит турбину. Если закрытие заслонки выхлопной трубы окажется недостаточным для повышения температуры до 3 °C на входе в осевой компрессор, то система выдает сигнал на открытие заслонки BV-2. Рабочий цикл заслонки BV-2 тот же, что и заслонки BV-1. Заслонка BV-2 будет открываться до тех пор, пока температура на входе не достигнет заданного значения или пока не сработает концевой выключатель 33BV-2.
Если при полностью открытых заслонках BV-1 и BV-2 и при закрытой заслонке выхлопной трубы ВВ температура на входе будет оставаться ниже + 3 °C, то через 12 мин после начала работы система вернется в первоначальное положение и включит сигнал тревоги на световом табло щита управления турбиной «Неисправность системы подогрева».
Если температура на входе станет более +5 °С, то система начнет выдавать сигналы на закрытие заслонок BV-1 и BV-2 или на открытие заслонки ВВ. В зависимости от того, какая заслонка работала последней на повышение температуры, она же начнет работать первой на понижение этой температуры.
Когда перепад давления на входе в осевой компрессор достигнет 254 мм вод.ст., сработает датчик 63CS-1 и включит сигнал тревоги на световом табло щита управления турбиной. Если перепад давления продолжает возрастать и становится: равным 381 мм вод.ст., срабатывает датчик 63CS-2 и аварийно отключает турбину.
Температурные датчики 26ТР-1 и 26ТР-2 защищают осевой компрессор от чрезмерно высоких температур на входе. При повышении температуры свыше +52°С датчик 26ТР-1 включает сигнал тревоги и выдает сигнал в систему подогрева на «Понижение».
Следует заметить, что если имеются два сигнала тревоги как по перепаду давления, так и по температуре, то сигнал перепада давления принимается в первую очередь, и система работает на «Повышение».
Если температура на входе в осевой компрессор повысится более +66°С, то датчик 26ТР-2 аварийно остановит турбину.
Система подогрева воздуха на входе может работать как
в ручном, так и в автоматическом режиме. Выбор режима осуществляется лампами (кнопками) «Автоматическое» и «Ручное», на главном щите управления турбиной.
Работа при ручном режиме допускается в случае, если необходим быстрый выход на рабочий диапазон температур. Однако пользоваться им надо только в крайних случаях, так как электропривод заслонок не рассчитан на непрерывный режим работы, а работает в импульсном режиме, и поэтому возможна перегрузка и перегрев электродвигателей.
1.3.8 ПРОТИВОПОЖАРНАЯ СИСТЕМА Противопожарная система с использованием углекислоты предназначена для тушения пожаров, возникших в отсеках турбины и вспомогательного оборудования, путем понижения концентрации кислорода в воздухе до пределов, недостаточных для горения (с 21 до 15%) и поддержания этой концентрации в течение длительного времени путем подачи углекислоты через систему трубопроводов и распылителей в отсеки турбины и вспомогательного оборудования. Следует помнить, что система не защищает нагнетатель от пожара.
Противопожарная система состоит из пятнадцати баллонов с СО2, соединенных между собой и находящихся в специальном отсеке. Из отсека по системе трубопроводов углекислота подается на десять распылителей, из которых семь расположены в отсеках турбины, а три — в отсеке вспомогательного оборудования. Все баллоны с СО2 в отсеке разделены на две группы. Углекислота из шести баллонов первой группы поступает в первичный трубопровод и служит для быстрого понижения концентрации кислорода в отсеках турбины и вспомогательного оборудования. А углекислота из девяти баллонов второй группы поступает во вторичный трубопровод и служит для поддержания низкой концентрации кислорода в течение длительного времени. Разница во времени подачи СО2 из двух групп баллонов достигается использованием различных размеров выпускных сопел распылителей на трубопроводах первичной и вторичной систем. Выпускные сопла распылителей первичной системы имеют большие размеры и поэтому обеспечивают быструю подачу СО2 для понижения концентрации кислорода, а выходные сопла распылителей вторичной системы имеют небольшие размеры.
1.3.9 СИСТЕМА УПЛОТНЯЮЩЕГО МАСЛА Масло для смазки подшипников нагнетателя отбирается из системы смазки турбины. Масло со степенью фильтрации 5 мкм, с температурой 50−60° С и давлением 1,4−1,75 кгс/см2 поступает в коллектор, от которого ответвляются трубопроводы к подшипникам. На каждом трубопроводе подвода масла к подшипникам установлены калибровочные шайбы, которые редуцируют давление масла до требуемой величины. Давление масла в каждом трубопроводе контролируется манометрами, установленными на щите. При работающем нагнетателе давление масла к опорным подшипникам должно быть равно 1,0−1,3 кгс/см2 и давление к упорному подшипнику 0,6−0,8 кгс/см2. Регулируют давление масла на подшипники при помощи регулировочных винтов. На сливных трубопроводах установлены смотровые стекла для контроля циркуляции масла и термопары для контроля температуры масла на сливе из подшипников.
Сливные трубопроводы соединены в общий коллектор, по которому масло отводится в главный масляный бак турбины.
Система смазочного масла нагнетателя защищена следующими приборами:
термодатчиками ТЕ 3−4 и ТЕ 3−5, включающими сигнал тревоги при высокой температуре масла на сливе из подшипников;
датчиком давления PS3−53, дающим разрешение на запуск насосов уплотняющего масла при нормальном давлении масла на входе насосов и настроенным на 1,1 кгс/см2;
датчиком давления PS3−51, вызывающим остановку насосов уплотняющего масла при падении давления масла на входе насосов и настроенном на 0,35 кгс/см2.
1.3.10 СИСТЕМА СМАЗОЧНОГО МАСЛА Для предотвращения выхода газа из корпуса нагнетателя с двух сторон ротора установлены комбинированные лабиринтные и масляные уплотнения, которые входят в систему уплотняющего масла. Эта система обеспечивает постоянный поток масла под кольцами масляных уплотнений к внутренней части корпуса нагнетателя, чтобы создать преграду находящемуся там газу.
Если принять давление уплотнительного масла с учетом более высокого из этих двух давлений, то расход масла будет слишком высоким для другого уплотнения. Поэтому необходимо выровнять давление газа перед уплотнениями, чтобы они работали в одинаковых условиях. Это достигается установкой лабиринтных уплотнений, в которых выполнены камеры, соединенные между собой линией выравнивающего газа.
Из камер выравнивающего газа газ проходит во внутрь корпуса нагнетателя и наружу в камеры эталонного или контрольного газа. Камеры контрольного газа соединены между собой, чтобы обеспечить (дополнительно) одинаковые величины давления газа перед масляными уплотнениями.
Масляное уплотнение состоит из двух стальных колец с внутренним баббитовым покрытием, насаженным на вал с минимальным зазором. Кольца плавающего типа в своем гнезде свободно перемещаются в радиальном направлении вследствие радиальных перемещений вала, всегда оставаясь концентричными по отношению к валу. Проворачивание колец предотвращается стопорным штифтом. Внутренние торцовые поверхности колец поддерживаются на расстоянии набором пружин. В кольцевое пространство, существующее между двумя кольцами, подается масло, давление которого на 1 кгс/см2 всегда выше давления газа, находящегося в полости, образованной непосредственно перед внутренним кольцом масляного уплотнения (полость контрольного газа). Масляная пленка, образующаяся между внутренним уплотнительным кольцом и валом, предотвращает протечку газа вдоль вала. Масло, которое протекает между наружным уплотнительным кольцом и валом (уплотнение низкого давления), смешивается со смазочным маслом на сливе из подшипников и возвращается в главный масляный бак. А масло, протекающее между внутренним уплотнительным кольцом и валом (уплотнение высокого давления), смешивается с газом, прошедшим через лабиринтное уплотнение и сливается в две поплавковые камеры, откуда попадает в бак дегазации, где освобождается от газа и затем возвращается в главный масляный бак.
компрессорный газотурбинный воздушный подшипник
1.3.11 БЛОК ПОДОГРЕВАТЕЛЯ ГАЗА Для предотвращения обмерзания запорной и регулирующей арматуры в блоке подготовки газа, вызванного охлаждением газа при расширении, часть газа отводится и подогревается в блоке подогревателя газа, а затем вновь подается в блок подготовки, где смешивается с остальным газом и охлаждается до температуры 44 °C, при помощи терморегулирующего клапана.
Температура газа на входе в подогреватель может быть любой, но на выходе из подогревателя поддерживается автоматически в пределах 46,5−49° С.
Подогреватель газа представляет собой горизонтальный цилиндрический резервуар длиной 4000 мм и диаметром 1200 мм, оборудованный расширительным баком и камерой сгорания с дымовой трубой.
В резервуаре установлено два теплообменника.
Двухходовая топочная камера передает тепло, выделившееся за счет сжигания части подогретого газа, теплоносителю, который заполняет резервуар и омывает трубный пучок высокого давления. В качестве теплоносителя используется 60%-ный раствор диэтиленгликоля в воде.
Двухходовая топочная камера состоит из жаропрочной трубы, направляющего устройства, возвратного пучка труб и трубной доски. К трубной доске крепятся камера сгорания с установленными в ней двумя рабочими и одной пилотной горелками и сборник дымовых газов с дымовой трубой.
Теплообменник подогреваемого газа также двухходовой и состоит из пучка труб, трубной доски и направляющего устройства. Газ из распределительной камеры по трубкам поступает в направляющее устройство и возвращается в распределительную камеру, разделенную глухой перегородкой на две полости. Каждая полость оборудована штуцером для входа и выхода газа. Кроме того, в выходной полости распределительной камеры имеется штуцер для подачи газа на горелки подогревателя и штуцер для регулятора температуры газа на выходе из подогревателя.
1.3.12 БЛОК ОСУШКИ ГАЗА Блок осушки газа предназначен для очистки и осушки импульсного газа, идущего на питание пневмокранов обвязки КС.
Блок осушки газа помимо оборудования для очистки и осушки импульсного газа в своем составе имеет регуляторы давления отопительного газа, а также пускового и топливного газа вспомогательного турбогенератора «Солар».
1.3.13 СИСТЕМА ЗАЩИТЫ НАГНЕТАТЕЛЯ ОТ ПОМПАЖА Явление помпажа в центробежных нагнетателях наблюдается, когда расход газа снижается до такой величины, что нагнетатель при данной частоте вращения не может создать необходимый напор. В этот момент на мгновение происходит перемена направления потока, сопровождающаяся потерей напора. Затем величина степени сжатия восстанавливается, и цикл повторяется. Такое явление вызывает пульсацию и удары в системе и может привести к разрушению установки. Во избежание этого на газоперекачивающем агрегате ГТК-10И предусмотрена система защиты от помпажа.
Система защиты от помпажа, или антипомпажная система агрегата ГТК-10И, состоит из следующих элементов:
датчиков дифференциального давления типа ВО фирмы «Бейли»;
скалярного блока типа 751;
первичного регулятора типа 701;
электропневматического преобразователя типа 546;
пневматического регулятора типа 3570;
рециркуляционного крана № 6.
1.4 Особенности обслуживания газоперекачивающего агрегата ГТК-10И
1.4.1 Предпусковые операции Перед пуском агрегата необходимо убедиться в готовности вспомогательного оборудования и следующих систем:
пусковой системы;
системы охлаждения масла;
системы технологического газа;
системы пожаротушения;
системы контроля загазованности;
системы подогрева воздуха на входе в осевой компрессор;
системы управления «Спидтроник»;
блоков подготовки пускового и топливного газа (БППТГ);
блока подогревателя газа;
блока осушки газа.
1.4.2 Прокрутка агрегатов от турбодетандера Перед прокруткой агрегата необходимо:
убедиться в отсутствии посторонних предметов в ВЗК и во всасывающем воздуховоде компрессора, закрыть двери ВЗК на ключ и снять покрывающую ленту со входа в компрессор;
убедиться, что заслонка в выхлопной трубе полностью открыта и в трубе нет посторонних предметов;
застопорить вал силовой турбины, используя болты от промвала (при этом следует быть осторожным, чтобы не повредить стопорные пружины в отверстиях. Вытаскивать их нельзя!);
убедиться, что БППТГ налажен и может поддерживать в коллекторе пускового газа заданное давление. Чтобы исключить подачу топливного газа, необходимо перекрыть ручные задвижки в БППТГ до трехходового крана;
все ключи в Центре управления двигателями (МСС) поставить в положение «Авто»;
отсоединить высоковольтные кабели от свеч зажигания;
отсоединить импульсный газ от кранов 1, 2, 4, 5, 6 и обесточить кран 6а (при этом краны 1, 2, 4, 6 и 6а должны быть закрыты, а кран 5 — открыт);
обеспечить непрерывную связь между ГЩУ, МСС и агрегатом (иметь минимум трех наблюдателей на агрегате);
установить манометр за клапаном-регулятором VPR-15.
Для включения режима «Прокрутка» главный селекторный переключатель на щите управления турбиной доставить в положение «Прокрутка». Дать сигнал «Пуск». Если ротор ТВД не стронется с места при заданном давлении пускового газа (15 кгс/см2), допускается непосредственно во время пуска при возбужденных соленоидных клапанах 20SV и 20SG с помощью клапана VPR-15 увеличить давление перед турбодетандером до 17 кгс/см2. После того как ротор начнет вращаться, дать сигнал «Остановка», а затем надо:
прослушать агрегат на наличие посторонних шумов;
записать значение реле нулевой скорости 14SR и 14HR;
контролировать включение соленоидных клапанов 20SV и 20SG и выключение 20SG при срабатывании реле 14HR;
убедиться в достаточном сливе масла из подшипников;
при остановке агрегата проверить перестановку трехходовых кранов в БППТГ.
После остановки ротора и появления сигналов «Готовность» и «Проверка», если первый пуск прошел нормально, снова дать сигнал «Пуск». При этом необходимо:
проверить последовательность включения всех двигателей от реле 2АМ;
при наборе оборотов прослушать турбину и контролировать вибрацию;
контролировать давление масла смазочного и гидропитания и предельной защиты;
записать частоту вращения, при которой срабатывают реле скорости 14SR, 14HR и 14НМ;
следить за правильностью зажигания: табло и лампочек на щите управления турбиной.
В режиме «прокрутки» ТВД может достичь ~1400 об/мин. Если прокрутка прошла нормально, можно переходить к следующему этапу — зажиганию.
1.4.3 Зажигание камеры сгорания Перед зажиганием агрегата необходимо:
все ключи в МСС поставить в положение «Авто»;
подсоединить высоковольтные кабели к свечам зажигания;
проверить коллектор топливного газа и убедиться, что конические пробки на месте и соединительные фланцы обтянуты;
настроить регуляторы в БППТГ и включить подогреватель газа (газ можно отбирать от основной или от аварийной линии, а в случае питания от аварийной линии регуляторы давления в блоке осушки необходимо открыть полностью);
сделать изменения в системе управления «Спидтроник» такие же, как и при «прокрутке».
Для включения режима «Зажигание» главный селекторный переключатель установить в положение «Зажигание». Дать сигнал «Пуск». После этого надо:
проконтролировать последовательность прохождения сигналов пуска;
проверить включение насосов, вентиляторов и другого вспомогательного оборудования;
проконтролировать величину давления пускового и топливного газа;
записать значение двухминутного таймера продувки 2TV (IL3J) и при необходимости отрегулировать впоследствии потенциометром;
записать величину VCE при зажигании и после установления пламени;
записать значение давления топливного газа между стопорным и регулирующим клапанами в момент зажигания (должно быть 1,02 кгс/см2).
После зажигания необходимо проверить спектр пламени: на малом газе оно должно быть голубого цвета, а при увеличении нагрузки — оранжевого. Отклонение от этого сигнализирует о неисправности топливной системы.
Следует осмотреть агрегат, прослушать подшипники (перепад температур на подшипниках не должен превышать 33°С), а также проверить топливный коллектор на утечки, которые при необходимости устранить.
Если зажигание прошло успешно и нет никаких отклонений в работе агрегата, можно перейти к выходу на холостой ход по ТВД. Для этого необходимо поставить главный селекторный переключатель в положение «Ручное» или «Автоматическое». При этом должен происходить автоматический набор оборотов ТВД.
После этого необходимо проконтролировать:
частоту вращения, при которой сливается масло из гидроцилиндров пусковой муфты;
частоту вращения, при которой происходит обесточивание соленоидного клапана 20SV и, следовательно, перекрытие пускового газа (если это произойдет на частоте вращения ниже, чем 4200 об/мин, возможно зависание ТВД и, как следствие, рост температуры);
работу контуров регулирования по соответствующим индикационным лампочкам;
срабатывание реле 14HS и 14LS и, как следствие, выключение вспомогательных насосов смазки и гидропитания, выключение в табло «Вспомогательные устройства в работе»;
переход на питание от собственного электрогенератора и загорание красной лампочки «Завершение последовательности пуска».
Пуск окончен. После этого необходимо дать турбине прогреться и проверить следующие параметры:
давление смазочного масла и температуру на сливе из подшипников. Особое внимание обратить на подшипник № 2, как наиболее теплонапряженный. Температура масла на сливе не должна превышать 75° С. Регулировать ее надо регулятором VTR-1, причем данная в инструкции фирмы температура масла в коллекторе (+ 55°С) может быть для разных агрегатов разной, т. е. определяющей следует считать не температуру масла в коллекторе, а температуру слива 75° С и перепад 33° С. Работать при температуре слива масла из подшипников более 90 °C не разрешается;
давление масла в системе гидропитания (при необходимости регулятором VR-21 установить давление 95±1,76 кгс/см2);
среднюю температуру и распределение температур на выходе, т. е. tРАБ=10−20°С (при t >30°С необходимо остановить агрегат);
включение вспомогательного и аварийного насосов при помощи пробных клапанов;
нагрев пламяперекидных труб;
выдвижение свечей из камер сгорания;
перепад давления на фильтрах;
вибрацию по подшипнику Ml.
Если при работе агрегата не были замечены неисправности, можно переходить к испытанию защиты по превышению скорости ТВД как электронной, так и механической.
1.4.4 Пуск агрегата под нагрузку Перед пуском агрегата под нагрузку необходимо:
установить промвал между турбиной и нагнетателем;
собрать линию смазки муфт и установить правильное направление подачи масла;
наладить систему уплотняющего масла нагнетателя;
удалить все перемычки в системе управления «Спидтро-бик»;
проверить правильность перестановки кранов, для чего надо подготовить агрегат к пуску по нормальной схеме, перекрыть в БППТГ ручные задвижки пускового и топливного газа, подать сигнал «Пуск» и проследить правильность перестановки кранов и поставить ручные задвижки в БППТГ в исходное положение;
предварительно настроить систему противопомпажного регулирования;
установить позиционер крана № 6 в положение «Ручное»;
установить все ключи в МСС в положение «Авто»;
за 4 ч до пуска включить подогреватель газа, а также подогреватели в БППТГ, блоке осушки и обогрев скруббера;
проверить линию слива конденсата от скруббера и БППТГ;
проверить наличие в скрубберах жидкости и, если она есть, слить ее.
Для пуска агрегата установить главный селекторный переключатель в положение «Ручное» и подать команду «Пуск». После чего надо:
проверить прохождение последовательности пуска (приведена ниже);
записать частоту вращения, при которой начинает вращаться ротор ТНД;
тщательно прослушать нагнетатель и проконтролировать слив масла из подшипников, а также осевой сдвиг и вибрацию;
проследить за величиной перепада «масло — газ»;
проконтролировать все параметры работы агрегата (температуру и распределение температур на выходе, температуру смазочного и уплотнительного масла, перепад давлений на всех масляных фильтрах и температуру у дисков ТВД и ТНД).
Достижение 99% частоты вращения ТВД и наименьшей частоты вращения регулирования ТНД при открытом кране № б считается холостым ходом агрегата.
Снять и записать в сдаточный протокол параметры работы агрегата на холостом ходу.
1.4.5 Обслуживание агрегата под нагрузкой Во время работы следует постоянно контролировать загрузку агрегата, производительность и степень сжатия, а с помощью характеристики нагнетателя определять удаленность рабочей точки от границы помпажа. Удаленность рабочей точки от границы помпажа должна составлять не менее 10% производительности.
При работе нескольких агрегатов параллельно наиболее рациональным является режим с одинаковой частотой вращения ТНД. При включении агрегата параллельно к работающим агрегатам необходимо:
проанализировать режим до включения агрегата и рассчитать ожидаемые параметры — давление входа и выхода, степень сжатия после подключения;
непосредственно перед пуском включаемого агрегата вывести все работающие агрегаты на «Кольцо» открытием вручную кранов № 6, после чего надо завершить пуск включаемого агрегата на «Кольцо» и загрузить агрегаты закрытием кранов № 6 вручную.
При перегрузке с одного агрегата на другой необходимо:
непосредственно перед завершением пуска включаемого агрегата вывести все работающие агрегаты на «Кольцо» открытием вручную кранов М 6;
завершить пуск включаемого агрегата на «Кольцо»;
загрузить агрегаты, оставив на «Кольце» намеченный к остановке агрегат;
убедившись в нормальной работе агрегатов под нагрузкой, нормально остановить работающий на «Кольце» агрегат.
При работе на «Кольце» следует внимательно следить за температурой газа на выходе из нагнетателей, не допуская ее увеличения выше 80 °C. При каких-либо задержках, требующих работу агрегатов на «Кольце», следует полностью включить охладители газа и снизить обороты ГПА до минимально допустимых. При появлении признаков помпажа и отказа антипомпажной системы нагнетателя (специфический звук, колебание стрелки прибора для измерения, перемещение стрелки блока типа 701 на антипомпажной системе и колебание прибора индикатора перепада «масло — газ») немедленно вывести агрегат на «Кольцо» или его остановить.
Во время работы агрегата обслуживающий персонал обязан следить за показаниями приборов и сигнализаторов на щите управления. Причина любого ненормального отклонения в показаниях приборов при сигнализации должна немедленно выясняться для принятия соответствующих мер. Эксплуатационные параметры, подвергаемые контролю и регистрации, необходимо заносить в суточную ведомость работы агрегата и сравнивать с нормальными, установленными инструкцией и при наладке агрегата.
Перепад температуры масла на подшипниках должен быть не выше 33 °C. Быстрое возрастание этого параметра на одном из подшипников свидетельствует об аварийном состоянии (в этом случае агрегат необходимо немедленно остановить). При контроле показаний термопар на выходе ТНД необходимо особое внимание обращать на разброс показаний, который не должен превышать 30 °C. При увеличении разброса сверх 30 °C агрегат следует остановить и выяснить причину разброса показаний. При выходе из строя двух и более термопар защиты агрегат надо остановить. Не менее чем в 2 раза в смену необходимо производить визуальный осмотр оборудования. При этом следует обращать особое внимание на:
возникновение необычного шума и вибрации;
утечки масла через соединительные детали трубопроводов и узлов систем маслоснабжения, регулирования и уплотнения;
утечки газа, воздуха и продуктов сгорания;
перепады давлений масла на фильтрах (при достижении перепадов на фильтрах смазки полумуфт 1,0 кгс/см2, основных фильтрах масла смазки 1,5 кгс/см2 и фильтрах масла гидропитания 3,5 кгс/см2 необходимо перейти на резервный фильтр, а отключенный фильтр разобрать и заменить в нем фильтрующие элементы);
величину давления масла предельной защиты (OLT);
показания указателей уровня масла в маслобаках;
перепад «масло — газ».
При температуре наружного воздуха ниже +4°С система подогрева воздуха на входе в осевой компрессор должна работать в автоматическом режиме. В случае отказа автоматики следует перейти на ручное управление, поддерживая температуру на входе +4°С, и выяснить причину отказа. Работать с отключенной системой подогрева на входе при температуре всасывания ниже +4°С запрещается.
Один раз в сутки необходимо производить анализ масла на содержание механических примесей и воды. Полный анализ масла производить один раз в неделю. Один раз в смену необходимо проверять включение аварийного и вспомогательного маслонасосов.
1.4.6 Нормальная остановка агрегата При нормальной остановке агрегата необходимо:
дать сигнал «Стоп» и проследить, происходит ли опустошение счетчика системы регулирования частоты вращения ТНД и снижение оборотов ТНД, а при достижении минимальной частоты вращения регулирования ТНД произойдет ли правильная перестановка кранов (краны 1, 2 и 6а закрываются, а кран 5 открывается) и закроются стопорный и регулирующий клапаны;
проследить, что при снижении давления за главным масляным насосом включится вспомогательный насос;
определить время остановки роторов;
после полной остановки агрегата выключить вспомогательный маслонасос (при этом должен включиться аварийный насос);
проверить цикличность включения и выключения (2 мин работает, 13 мин не работает) аварийного насоса смазки;
включить ВМН.
1.4.7 Аварийная остановка агрегата При аварийной остановке агрегата необходимо:
произвести аварийную остановку, воздействуя на любую защиту или на кнопку АО, а также проследить, что закрываются краны 1, 2 и 6а, а открывается кран 5;
проследить наличие сигнализации, закрытие стопорного и регулирующего клапанов, а также слив масла OLT.
При нажатии кнопки «Авария» или прохождении аварийного сигнала главные защитные реле 4 (IRODA, DB, GC, СВ, СА) отпадают и обесточивается 20НД, после чего закрывается клапан соотношения, запускаются вспомогательные насосы, а электропитание переводится с собственного генератора на внешнюю сеть.
1.5 Техника безопасности при обслуживании ГТК-10И Вредными для организма человека являются повышенная температура, вибрация оборудования и шумы в компрессорных цехах, поэтому при выполнении любых работ в производственных помещениях, внутри аппаратов, сосудов и на других коммуникациях КС от персонала требуются строгое соблюдение правил безопасности и организация безопасных условий труда.
К работе на КС допускаются лица не моложе 18 лет, твердо усвоившие правила техники безопасности и технической эксплуатации магистральных газопроводов, правила внутреннего распорядка на КС, производственные инструкции, и конструкцию обслуживаемых (ремонтируемых) агрегатов, их оборудования и правила противопожарной безопасности на КС.
К оборудованию КС предъявляют определенные требования, выполнение которых в значительной степени повышает надежность работы КС в целом.
Компрессорные цеха должны быть оборудованы установками автоматического пенного и углекислотного пожаротушения с датчиками, установленными на каждом агрегате и внутри помещения ГПА на КС в блочно-комплектном исполнении. Во всех цехах и помещениях ГПА должна быть установлена автоматическая система контроля загазованности, сблокированная с аварийной вентиляцией.
Все соединения газопроводов должны быть сварными. Фланцевые и другие разъемные соединения допускается применять только в местах присоединения арматуры, аппаратов и в местах разъемов, необходимых для монтажа и демонтажа газопроводов при ремонтных работах.
Каждый ГПА должен отключаться от сборных газовых коллекторов при помощи стальной запорной арматуры с автоматическим, дистанционным и местным видами управления. Между запорной арматурой и нагнетателем вне цеха и укрытия агрегата должны быть расположены на всасывающей и нагнетательной линиях люки-лазы (Dy=500 мм). На всасывающей линии между нагнетателем и люком-лазом необходимо устанавливать защитные решетки.
Воздухозаборные устройства следует устанавливать со стороны, противоположной местонахождению технологических газовых коллекторов газоперекачивающих агрегатов.
Трубы для вывода отработавших газов, а также свечи обвязки газоперекачивающих агрегатов и газомотокомпрессоров должны быть выведены на 2 м выше конька крыши здания, где расположен компрессорный цех, и на 1 м выше дефлектора. Расстояние по горизонтали между этими трубами и дефлекторами должно быть не менее 6 м.
В соответствии с действующими правилами и нормами газоперекачивающие агрегаты должны иметь необходимую сигнализацию отклонения основных параметров от нормального режима работы. Все автоматические устройства следует регулярно проверять, а результаты проверок записывать в специальный журнал.
Компрессоры и их приводы следует устанавливать на фундаменты, не связанные со стенами зданий, так как на них под воздействием вибрационных нагрузок могут появиться трещины. При наличии вибрации на ГПА возможно разрушение здания.
Каждый агрегат необходимо оснащать устройствами аварийной защиты в объеме, позволяющем автоматически подавать команды на аварийную остановку агрегата при любом аварийном режиме его и неисправности вспомогательного механизма или узла агрегата.
Содержание горючих газов и паров в воздухе при эксплуатации не должно превышать 5% их НПВ. Помещения, где установлены нагнетатели газа, а также газомотокомпрессоры, должны быть оборудованы сигнализаторами довзрывоопасных концентраций, сблокированными с автоматикой включения аварийной вентиляции. Первый сигнал (звуковой) подается от сигнализатора при достижении содержания горючих газов в воздухе помещения (в одном из возможных мест их скопления), равной 10% их НПВ (около 0,5% (по объему) при перекачке природного газа, состоящего в основном из метана). По этому сигналу необходимо принимать меры к обнаружению места утечки газа и к ее ликвидации. Люди, не имеющие непосредственного отношения к эксплуатации ГПА, должны быть немедленно удалены из цеха. Аварийная вытяжная вентиляция должна включаться автоматически при содержании горючих газов в помещении, равном 15% их НПВ (0,75% по метану). При содержании горючих газов в помещении сверх 20% их НПВ (1% по метану) эксплуатация оборудования должна быть прекращена автоматически. Пуск оборудования вновь может быть произведен только при содержании горючих газов в компрессорном цехе менее 10% от НПВ. Запрещается эксплуатировать компрессорный цех с выключенной или неисправной системой контроля и сигнализации содержания горючих газов в воздухе помещения. Работоспособность автоматической сигнализации и автоматическое включение аварийной вентиляции должны проверяться дежурным персоналом каждую смену. Настройка сигнализатора довзрывоопасных концентраций горючих газов в воздухе помещения должна осуществляться с помощью калибровочной смеси газа с воздухом не реже 1 раза в месяц.
Двери производственных и бытовых помещений должны открываться наружу. С наружной стороны на входных дверях компрессорного цеха должна быть вывешена предупредительная надпись: «Вход посторонним воспрещен».
Обслуживающий персонал должен иметь таблицы предельно допустимых значений и основных показателей работы каждого ГПА при различных нагрузках. Предельно допустимые значения показателей работы ГПА должны быть ясно обозначены на соответствующих контрольно-измерительных приборах.
Работоспособность обратных клапанов, установленных на линиях подачи масла в системы смазки цилиндров и сальников ГПА, подачи воды в холодильники газа и на линиях нагнетания газа последней ступени, должна периодически проверяться. Работа указанного оборудования при неисправных обратных клапанах недопустима. Масла, применяемые для смазки отдельных ГПА, должны соответствовать требованиям заводов — изготовителей оборудования. При утечках масла из системы смазки или отдельных узлов ГПА должны быть приняты меры к их ликвидации и установлены металлические поддоны для сбора масла.
Во избежание хлопков и взрывов в выхлопном тракте двигателя перед включением его зажигания и подачей топливного газа в двигатель выхлопной тракт должен быть продут сжатым воздухом.
Эксплуатация ГТК-10И должна быть прекращена в случаях, оговоренных техническими инструкциями по эксплуатации отдельных видов агрегатов, в том числе при неисправности запорной и регулирующей аппаратуры, контрольных приборов, кнопок управления и сигнализации на щите управления, масло-насосов или масляных фильтров; снижении уровня масла в маслобаке или давления масла в системе ниже допустимой нормы; значительных утечках газа или масла из агрегата или системы; отключенных автоматических защитах; перегреве подшипников. Обнаруженные неисправности нельзя устранять на работающем ГПА. Остановка агрегата в таких случаях производится с ведома начальника КС или старшего инженера смены.
Во время работы агрегата ГТК-10И обслуживающий персонал обязан следить за показаниями приборов и сигнализаторов на щите управления. Причина любого ненормального отклонения в показаниях приборов при сигнализации должна немедленно выясняться для принятия соответствующих мер. Эксплуатационные параметры, подвергаемые контролю и регистрации, необходимо заносить в суточную ведомость работы агрегата и сравнивать с нормальными, установленными инструкцией и при наладке агрегата.
Перепад температуры масла на подшипниках должен быть не выше 33 °C. Быстрое возрастание этого параметра на одном из подшипников свидетельствует об аварийном состоянии (в этом случае агрегат необходимо немедленно остановить). При контроле показаний термопар на выходе ТНД необходимо особое внимание обращать на разброс показаний, который не должен превышать 30 °C. При увеличении разброса сверх 30 °C агрегат следует остановить и выяснить причину разброса показаний. При выходе из строя двух и более термопар защиты агрегат надо остановить. Не менее чем в 2 раза в смену необходимо производить визуальный осмотр оборудования. При этом следует обращать особое внимание на:
возникновение необычного шума и вибрации;
утечки масла через соединительные детали трубопроводов и узлов систем маслоснабжения, регулирования и уплотнения;
утечки газа, воздуха и продуктов сгорания;
перепады давлений масла на фильтрах (при достижении перепадов на фильтрах смазки полумуфт 1,0 кгс/см2, основных фильтрах масла смазки 1,5 кгс/см2 и фильтрах масла гидропитания 3,5 кгс/см2 необходимо перейти на резервный фильтр, а отключенный фильтр разобрать и заменить в нем фильтрующие элементы);
величину давления масла предельной защиты (OLT);
показания указателей уровня масла в маслобаках;
перепад «масло — газ».
При температуре наружного воздуха ниже +4 °С система подогрева воздуха на входе в осевой компрессор должна работать в автоматическом режиме. В случае отказа автоматики следует перейти на ручное управление, поддерживая температуру на входе +4 °С, и выяснить причину отказа. Работать с отключенной системой подогрева на входе при температуре всасывания ниже +4 °С запрещается.
Один раз в сутки необходимо производить анализ масла на содержание механических примесей и воды. Полный анализ масла производить один раз в неделю. Один раз в смену необходимо проверять включение аварийного и вспомогательного маслонасосов.
Аварийную остановку ГПА должен осуществлять самостоятельно дежурный персонал при поломках агрегата или в других случаях, когда возникает опасность для обслуживающего персонала; появлении металлического звука или шума внутри агрегата; значительной утечке газа или масла; начавшемся в помещении пожаре; неработающем аварийном освещении цеха. Информация об аварийной остановке ГПА должна быть незамедлительно передана руководителю (старшему по смене) КС, на соседние КС и диспетчеру ЛПУ МГ (объединения). Повторный запуск остановленного ГПА может быть произведен только после устранения неполадок.
Газоперекачивающий агрегат, отключенный в резерв или для ремонта, необходимо сразу же отсоединить от технологических, пусковых и топливных газопроводов. При грозе запрещается пуск ГПА и проведение переключений на технологической обвязке и силовом электрооборудовании.
Дежурный персонал КС при приеме смены обязан проверить действующие или подготовленные к пуску установки с целью обнаружения возможных неисправностей или дефектов; получить информацию от сдающих смену о технологических особенностях работы оборудования и режимах работы, а также сведения об исправности защитных устройств и приспособлений; немедленно сообщить вышестоящему руководителю или диспетчеру ЛПУ МГ о всех замеченных нарушениях или необычных условиях работы КС или ГПА при приеме смены.
Не допускается работа ГПА при отсутствии оборудования для улавливания воды, конденсата, пыли и грязи, которые могут попасть во всасывающую линию компрессоров вместе с транспортируемым газом. Надлежащая очистка газа должна обеспечиваться также при отключении одного из этих аппаратов для очистки или ремонта. Пылеуловители, холодильники, влагомаслоотделители и другие узлы компрессорных установок, в которых могут скапливаться конденсат или масло, должны продуваться только в специальные продувочные емкости.
2. РАСЧЕТНАЯ ЧАСТЬ
2.1 Расчет режима работы компрессорного цеха Цель расчета: Определение параметров режима работы ЦБН PCL-802/24: приведенной объемной производительности, приведенной частоты вращения ротора, мощности на валу привода, степени сжатия, политропического КПД и проверка удаленности режима работы от границ помпажа.
Исходные данные:
Пропускная способность компрессорного цеха Qкц, млн. м3/сут. 82
Тип нагнетателя центробежный PCL-802/24
Тип ГПА ГТК-10И Номинальная частота вращения силового вала н, об/мин. 6500
Механические потери Nмех, кВт 100
Потери газа в объвязке пылеуловителей Р, МПа 0,12
Относительная плотность газа по воздуху в 0,63
Конечное давление газа на участке газопровода Рвх, МПа 5,3
Фактическая частота вращения ротора, об/мин. 6300
Показатель политропы К 1,31
Количество работающих нагнетателей m 5
Температура газа на входе в ЦБН Т, К 299
Определяем газовую постоянную R/, Дж/кг К:
(2.1)
где R — газовая постоянная воздуха, Дж/кг К;
R = 286,8 Дж/кг К
?В — относительная плотность газа по воздуху.
R/ = 286,8 / 0,63 = 455,24 Дж/кг К Определяем по номограмме коэффициент сжимаемости Z природного газа по приведенному давлению Рвх, температуре Твх и относительной плотности в: Zср = 0,98
Определяем плотность газа при стандартных условиях 20 0С и 0,1013МПа, кг/м3:
сн =, (2.2)
где 1,205 кг/м3 — плотность воздуха при стандартных условиях.
сн =
Давление газа на всасывании в центробежный нагнетатель с учетом потерь газа в обвязке пылеуловителей, Рвс, МПа:
Рвс = Рвх — ?Р, (2.3)
где Рвх — давление газа на входе в КЦ, МПа;
?Р — потери газа в обвязке пылеуловителей, МПа.
Рвс = 5,4 — 0,12 = 5,28 МПа Определяем плотность газа при всасывании:
= (2.4)
=
Определяем фактическую подачу группы нагнетателей, Qк, млн. м3/сут.:
Qк =QКЦ / m, (2.5)
где QКЦ — пропускная способность КЦ, оборудованного однотипными агрегатами, млн. м3/сут.;
m — число параллельно работающих групп.
Qк = 82 000 000 / 5 = 16 400 000 м3/сут.
Определяем объемную подачу нагнетателя первой ступени, Qоб, м3/мин.:
Qоб = (2.6)
Qоб =
Определяем приведенную объемную подачу, м3/мин.:
(2.7)
где nн — номинальная частота вращения ротора нагнетателя, об./мин.
n — фактическая частота вращения ротора, об./мин.
Qоб — объемная подача нагнетателя, м3/мин.
Определяем приведенную частоту вращения ротора нагнетателя:
(2.8)
где Zпр, Rпр, Тпр — параметры газа, для которых составлена характеристика нагнетателя.
Определяем степень сжатия и приведенную относительную мощность нагнетателя по номограмме:
= 1,41; = 0,81;
Определяем внутреннюю мощность, потребляемую нагнетателем, Ni, кВт:
пр, (2.9)
Ni =
Определяем мощность на муфте привода, N, кВт:
N = Ni +N мех, (2.10)
где N мех — механические потери для газотурбинного привода.
N = 9280,2 + 100 = 9380,2 кВт
Определяем давление газа на выходе нагнетателя, Рвых, МПа:
Рвых= (2.11)
Рвых=
Определяем температуру газа на выходе нагнетателя, Твых, К:
(2.12)
где k — показатель политропы;
— политропический КПД нагнетателя, находится по номограмме.
tвых = 57,7 0С
Удаленность работы центробежного нагнетателя от границы помпажа определяется по величине:
(2.13)
где Qпрmin — минимальное значение приведенной объемной подачи ЦБН.
Вывод: полученные параметры давления Рвых=7,4МПа, температуры Твых=329,75К, мощности N=9380,2кВт — соответствуют для эксплуатации компрессорного цеха № 4 Антиповского ЛПУМГ и обеспечивают безпомпажную работу ЦБН PCL-802/24 ГТК-10И.
2.2 Расчет цикла ГТУ ГТК-10И
Цель расчета: расчет параметров цикла ГТУ ГТК-10И: удельной полезной работы, расхода воздуха через осевой компрессор, расхода рабочего тела турбины внутреннего КПД ГТУ; расхода топливного газа в камере сгорания.
Исходные данные:
Эффективная мощность N, кВт 9700
Температура воздуха на входе в осевой компрессор t1°C 15
Номинальное давление окружающего воздуха P1, кгм/см2 1,033
Температура газа на входе в турбину t3 ,°C 925
Степень сжатия воздуха в осевом компрессоре е 7,2
Показатель адиабаты k 1,4
К.П.Д. камеры сгорания зкс 0,98
К.ПД. осевого компрессора (индикаторный) зок 0,86
Газовая постоянная R кгс. м/кг.град 29,3
Низшая теплота сгорания топлива Q нр, ккал/кг 11 660
К.П.Д. турбины (индикаторный) зт 0,86
К.П.Д. механический турбины змех 0,96
Отношение расхода воздуха к расходу рабочего тела турбины, Gв / Gт 0,98
Задается коэффициент потерь в воздушном и газовом тракте, о
о = 1,05ч 1,1=1,05
Давление газа на выходе из турбины Р4, кгс/см2
Р4 = P1 · о, (2.14)
где P1 — номинальное давление окружающего воздуха, кгс/см2;
о — коэффициент потерь в воздушном и газовом тракте.
Р4 = 1,033 · 1,05 = 1,08 кгс/см2
Давление воздуха на выходе из осевого компрессора, Р2, кгс/см2
Р2 = P1 · ек, (2.15)
где P1 — номинальное давление окружающего воздуха, кгс/см2;
ек — степень сжатия воздуха в осевом компрессоре.
Р2 = 1,033 · 7,2 = 7,44 кгс/см2
Давление рабочего тела на входе в турбину, Р3, кгс/см2
Р3 = P2 / о,, (2.16)
где Р2 — давление воздуха на выходе из осевого компрессора, кгс/см2.
Р3 = 7,44 / 1,05 =7,08 кгс/см2
Изоэнтропийный теплоперепад в компрессоре, Нок, ккал/кг
Нок = А · R· к/(к-1) · Т1 (е к-1/ к -1), (2.17)
где, А — температурный эквивалент работы;
R — газовая постоянная, кГм/кг°C;
k — показатель адиабаты;
Т1 — температура воздуха на входе в осевой компрессор, К;
е — степень сжатия воздуха в осевом компрессоре.
Нок = 1/427 · 29,3 · 1,4 / (1,4−1) · 288 · (7,2 1,4−1/1,4 -1) = 51 ккал/кг
Действительный теплоперепад в осевом компрессоре, Нк, ккал/кг
Нк = Нок / зок, (2.18)
где Нок — изоэнтропийный теплоперепад в компрессоре, ккал/кг;
зок — КПД осевого компрессора.
Нк = 51 / 0,86 = 59,3 ккал/кг
Средняя температура воздуха в осевом компрессоре, tокср, °C
(2.19)
где t1 — температура воздуха на входе в осевой компрессор, °C;
Нк — действительный теплоперепад в осевом компрессоре, ккал/кг.
Средняя массовая удельная теплоемкость в зависимости от средней температуры воздуха в осевом компрессоре, (tокср); Сmр, ккал/кг°C, определяется согласно таблицы 2.1.
С163 = 0,2434 ккал/кг°C
С163 = С100+(С200 — С100)· 63 / 100 = 0,2413+(0,2447 — 0,2313)· 63 / 100 = 0,2434 ккал/кг°C
Таблица 2.1 — Значение изобарной теплоемкости и энтальпии
Температура t, 0С | Изобарная теплоемкость С, ккал/кг°C | Удельная энтальпия i, ккал/кг | |
0,2397 | |||
0,2413 | 44,68 | ||
0,2447 | 90,35 | ||
0,2495 | 137,40 | ||
0,2552 | 185,90 | ||
0,2609 | 236,80 | ||
0,2663 | 287,60 | ||
0,2712 | 341,20 | ||
0,2756 | 396,30 | ||
0,2795 | 453,10 | ||
0,2855 | 503,44 | ||
Температура воздуха на выходе из осевого компрессора, t2, °C
(2.20)
где t1 — температура воздуха на входе в осевой компрессор, °C;
Нк — действительный теплоперепад в осевом компрессоре, ккал/кг;
Сmр — средняя массовая удельная теплоемкость в зависимости от средней температуры воздуха в осевом компрессоре, ккал/кг°C.
°C
Изоэнтропийный теплоперепад в турбине, Нот, ккал/кг
Нот = А · R· к/(к-1) · Т3 1- (1 / ут) к-1/к, (2.21)
где Т3 — абсолютная температура газа на входе в турбину, К;
ут — степень расширения рабочего тела в турбине, ут = Р3 / Р4 = 7,08/ 1,08=6,53
Нот = 1/427 · 29,3 · 1,4 / (1,4−1) · 1198 · 1- (1 / 6,53)1,4−1/1,4 = 119,4 ккал/кг
Действительный теплоперепад в турбине, Нт, ккал/кг
(2.22)
где Нот — изоэнтропийный теплоперепад в турбине, ккал/кг;
зт — КПД турбины.
Средняя температура рабочего тела в турбине, tТср,°C
(2.23)
где Нот — изоэнтропийный теплоперепад в турбине, ккал/кг;
t3 — температура газа на входе в турбину, °C.
°C
Средняя удельная теплоемкость в зависимости от средней температуры рабочего тела в турбине, (tТср); Сmр, ккал/кг°C, определяется согласно таблицы 2.1.
С746 = 0,2732 ккал/кг°C
С746 = С700+(С800 — С700)· 46 / 100 = 0,2712+(0,2756 — 0,2712)· 46 / 100 = 0,2732 ккал/кг°C
Температура рабочего тела на выходе из турбины, Т4, К
(2.24)
где Нт — действительный теплоперепад в турбине, ккал/кг;
Сmр — средняя массовая удельная теплоемкость в зависимости от средней температуры воздуха в осевом компрессоре, ккал/кг°C.
Удельная полезная работа ГТУ, lт, ккал/кг
(2.25)
где Нт — внутренний теплоперепад в турбине, ккал/кг;
змех — механический К.П.Д. турбины;
Нк — дейсгвительный теплоперепад в осевом компрессоре, ккал/кг;
Qв /QТ — отношение расхода воздуха к расходу рабочего тела через турбину.
Средняя температура рабочего тела в камере сгорания, tксср, °C
(2.26)
где t2 — температура воздуха на выходе из осевого компрессора, °C;
t3 — температура рабочего тела на входе в турбину, °C.
°C
Средняя удельная теплоемкость рабочего тела в камере сгорания, Сmр (tксср), ккал/кг°C, определяется согласно таблицы 2.1.
С92 = (С600 — С500)· 92 / 100 = (0,2663 — 0,2609)· 92 / 100 = 0,4 968 ккал/кг°C
С592 = С500 + С92 = 0,2609 + 0,4 968 = 0,2659 ккал/кг°C
Теплота, подводимая в камере сгорания (удельная), qкс, ккал/кг
qкс = СmрКС · (t3 — t2), (2.27)
где t2 — температура воздуха на выходе из осевого компрессора, °C;
t3 — температура рабочего тела на входе в турбину, °C;
Сmр — средняя удельная теплоемкость рабочего тела в камере сгорания, ккал/кг°C.
qкс = 0,2659 · (925 — 258,6) = 177,17 ккал/кг
Внутренний К.П.Д. ГТУ, зГТУ, %
(2.28)
где Нт — внутренний теплоперепад в турбине, ккал/кг;
Нк — дейсгвительный теплоперепад в осевом компрессоре, ккал/кг;
qкс — теплота, подводимая в камере сгорания (удельная), ккал/кг.
Расход рабочего тела через турбину, GГТ, кг/с
(2.29)
где lт — удельная полезная работа ГТУ, ккал/кг;
N — эффективная мощность ГТУ, кВт.
Расход воздуха через осевой компрессор, GВОК, кг/с
GВОК = 0,98 · GГТ, (2.30)
где GГТ — расход рабочего тела через турбину, кг/с.
GВОК = 0,98 · 60,84 = 59,63 кг/с
Удельная энтальпия воздуха перед камерой сгорания, i2, ккал/кг
i2 = СmрТ · t2, (2.31)
где Сmр — средняя удельная теплоемкость рабочего тела в камере сгорания, ккал/кг°C;
t2 — температура воздуха на выходе из осевого компрессора, °C.
i 2 = 0,2659 · 258,6 = 68,75 ккал/кг
Удельная энтальпия рабочего тела перед турбиной, i3, ккал/кг
i3 = СmрТ · t3, (2.32)
где Сmр — средняя удельная теплоемкость рабочего тела в турбине, ккал/кг°C;
t3 — температура газа на входе в турбину, °C.
i3 = 0,2732 · 925 = 252,71 ккал/кг
Расход топливного газа в камере сгорания, В, кг / с
(2.33)
где GГТ — расход рабочего тела через турбину, кг/с;
GВОК — расход воздуха через осевой компрессор, кг/с;
QНР — низшая теплота сгорания топлива, ккал/кг;
зКС — К.П.Д. камеры сгорания;
i2 — удельная энтальпия воздуха перед камерой сгорания, ккал/кг;
i3 — удельная энтальпия рабочего тела перед турбиной, ккал/кг.
В результате выполненного расчета получены параметры:
удельная полезная работа ГТУ lт = 38,05 ккал/кг;
расход воздуха через OK GВОК = 59,63 кг/с;
расход рабочего тела через турбину GГТ = 60,84 кг/с;
внутренний К.П.Д. турбины зГТУ = 24,49%;
расход топливного газа в камере сгорания В = 0,987 кг/с.
Заключение
В курсовом проекте рассмотрена эксплуатация газоперекачивающих агрегатов ГТК — 10И компрессорного цеха № 4 Антиповского ЛПУМГ. В общей части проекта представлены:
— характеристика компрессорной станции «Антиповская»;
— техническая и конструктивная характеристика газоперекачивающего агрегата ГТК — 10И с подробным описанием конструкции и устройства отдельных узлов агрегата:
— даны характеристика агрегатных систем с указанием назначения системы и оборудования, которое в нее входит;
— особенности эксплуатации и технического обслуживания агрегата ГТК — 10И. Рассмотрены способы оптимизации ГПА. Обслуживание во время пуска, остановки, во время работы. Особенности обслуживания агрегата в холодное время года, а также агрегата, находящегося в резерве;
— техника безопасности при эксплуатации газоперекачивающего агрегата ГТК — 10И.
В расчетной части проекта выполнены следующие расчеты:
— расчет режима работы компрессорного цеха с целью определения параметров работы агрегата. Результаты расчета соответствуют эксплуатационным показателям (Рвых=4 МПа; Твых=329,75 К; = 1,41; N=9380,2 кВт), а также обеспечены условия беспомпажной работы.
— расчет параметров цикла ГТУ ГТК-10И с целью определения удельной полезной работы, расхода воздуха через осевой компрессор, расхода рабочего тела турбины внутреннего КПД ГТУ; расхода топливного газа в камере сгорания.
В графической части выполнены чертежи:
— индивидуального укрытия ГТК — 10И, его план, разрез;
— тепловая схема ГТУ.
Список использованных источников
1. Вести трансгаза: информационный бюллетень ООО «Газпром трансгаз Волгоград». Июнь, 2010.
2. Правила технической эксплуатации магистральных газопроводов: ВРД 39−1.10−006−2000: утв. Председателем правления ОАО «Газпром» Р. И. Вяхиревым 9. 12. 1999: ввод в действие с 1. 03. 2000. — М.: ИРЦ Газпром, 2000. -218 с.
3. Козаченко, А. Н. Эксплуатация компрессорных станций магистральных газопроводов. М., Недра, 1999. — 463 с.
4. Волков, М. М. Справочник работника газовой промышленности./ М. М Волков, А. Л. Михев, К. А. Конев; - М.: Недра, 1989.-362 с.
5. Янович, А. Н. Техника безопасности при эксплуатации магистральных газопроводов / А. Н. Янович, Л. И. Борщенко. Учебник для профессионального обучения рабочих на производстве. — М.: Недра, 1984.
6. Ермошкин, А. Г. Зарубежные ГПА / А. Г. Ермошкин, И. И. Радчик и др. — М.: Недра, 1979. — 247с.