Технология работы станции с зерном с разработкой КМАПРР
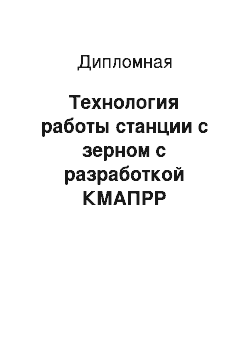
Проблема утилизации отходов существует и в нашей стране. Различные отрасли хозяйства, в том числе и железнодорожный транспорт, ежегодно утилизируют сотни миллионов тонн вторичного сырья. Комплексный характер функционирования железнодорожного транспорта и транспортного строительства обусловливает получение широкой номенклатуры отходов, которые подлежат переработке. Каждый вид отходов имеет… Читать ещё >
Технология работы станции с зерном с разработкой КМАПРР (реферат, курсовая, диплом, контрольная)
МИНИСТЕРСТВО ОБРАЗОВАНИЯ И НАУКИ РЕСПУБЛИКИ КАЗАХСТАН
Костанайский социально-технический университет имени академика Зулхарнай Алдамжар
Кафедра «Организация перевозок и транспорт»
ДИПЛОМНЫЙ ПРОЕКТ
на тему: Технология работы станции с зерном с разработкой КМАПРР
Специальность 50 901 «Организация перевозок, движения и эксплуатация транспорта»
Выполнил: Нурманова И.П.
Костанай 2009
Содержание Введение
1. Характеристика зерновых грузов
2. Перевозки зерновых грузов
2.1 Условия перевозок зерновых грузов
2.2 Погрузка и выгрузка зерновых грузов
3. Определение расчетных объемов работы грузовых пунктов
3.1 Расчет суточных грузопотоков
3.2 Расчет суточных вагонопотоков
4. Выбор схемы комплексной механизации погрузочно-разгрузочных работ
4.1 Выбор типа склада и средств механизации погрузочно-разгрузочных работ для расчета
4.2 Технология погрузочно-разгрузочных работ
4.2.1 Технология погрузочно-разгрузочных работ на местах общего и не общего пользования
4.2.2 Выбор грузозахватных приспособлений
5. Расчет размеров складских сооружений
5.1 Выбор склада
5.2 Определение площади и линейных размеров складов
6. Расчет потребного количества погрузочно-разгрузочных машин
6.1 Потребность в погрузочно-разгрузочных машинах на основе детерминированных грузопотоков
6.2 Потребность в погрузочно-разгрузочных машинах на основе технологии переработки грузопотоков
6.3 Техническое обслуживание и ремонт погрузочно-разгрузочных машин
7. Использование крупнотоннажных контейнеров для перевозки зерна
7.1 Перевозки сыпучих грузов с использованием мягких большегрузных контейнеров (до 14тн)
8. Выполнение расчетов по сравнению вариантов технологических схем доставки зерна
9. Технологический график работы средств механизации погрузки и выгрузки грузов
10. Мероприятия по обеспечению безопасности труда и экологической безопасности
10.1 Утилизация твердых и жидких отходов Заключение
Введение
В полном и своевременном удовлетворении потребностей населения и предприятий в перевозках, повышении эффективности и качества работы транспортной системы страны важное значение имеет повышение уровня комплексной механизации погрузочно-разгрузочных и складских работ, прежде всего переход от использования отдельных машин к разработке, производству и массовому применению высокоэффективных машин и оборудования на всем пути перемещения груза от места добычи сырья до места потребления готовой продукции.
Повышение производительности труда на предприятиях железнодорожного транспорта и совершенствование технологического процесса зависят от уровня механизации и автоматизации этого процесса. Ликвидация ручных погрузочно-разгрузочных работ и исключение тяжелого ручного труда при выполнении основных и вспомогательных операций за счет внедрения комплексной механизации и автоматизации производственных процессов обеспечивает сокращение простоев транспортных средств под грузовыми операциями, сокращает затраты труда и себестоимость переработки грузов, в конечном счете увеличивает доходность и прибыльность грузовых объектов и подразделений железнодорожного транспорта Ежегодная потребность Казахстана составляет 6−8 миллионов тонн зерна. Урожай зерна в 2007 году — 20,1 миллионов. Остальные 12 миллионов зерна Казахстану выгодно экспортировать. Поэтому основной объем погрузки и приходится на экспорт. Для организации перевозок зерна создан специальный зерновой круг, в котором посменно работают диспетчеры, инженеры, которые днем и ночью собирают информацию по погрузке, выгрузке, продвижению составов с зерновозами как в груженом, так и в порожнем состоянии.
Общий казахстанский парк зерновозов составляет 5249 вагонов, а этого недостаточно, чтобы удовлетворить потребности грузоотправителей. Поэтому работа каждого зерновоза — под особым контролем.
Каждый из зерновозов держится под контролем. В Казахстане зерно грузится на более чем ста станциях более чем двумястами грузоотправителями.
Зерно грузят маршрутным способом, т.к. когда поезд идет одним маршрутом, не останавливаясь на сортировку и разбор состава, оборот вагонов не снижается и теряется меньше времени.
В постперестроечные годы многие предприятия сельскохозяйственной и пищевой промышленности остались за пределами государства, а те, что остались, вынуждены были остановить свое производство. Одной из самых главных причин такого положения, было вырождение сельского хозяйства в Казахстане.
Являясь одним из приоритетных направлений развития экономики республики, сельское хозяйство располагает огромным потенциалом и большими резервами.
Разнообразные климатические условия Казахстана позволяют выращивать почти все культуры умеренного теплового пояса и развивать животноводство.
Костанайская область специализируется в перевозках зерновых грузов. Согласно экономической политике Республики Казахстан, огромное значение придается развитию сельского хозяйства: животноводству и растениеводству. Развитие любой отрасли зависит от транспортной составляющей: произведенную продукцию необходимо доставлять от производителя до потребителя.
За последние годы положение настолько улучшилось, что возникла потребность не только в возобновлении работы «старых» предприятий, но и в реконструкции их и создании новых. С целью подъема экономики села за последние десять лет были приняты государственные и отраслевые программы по развитию и поддержке АПК и села, подкрепленные солидными финансовыми ресурсами.
В связи с этим и согласно посланию президента Республики Казахстан Назарбаева Н. А. народу от 2008 года, целью дипломного проектирования является разработка схемы комплексной механизации и автоматизации погрузочно-разгрузочных работ с зерновыми грузами на специализированных пунктах.
1. Характеристика зерновых грузов В нашей стране установлены стандарты на качество зерна каждой культуры и наименования, которые в свою очередь разделяются на виды в зависимости от ботанических и других признаков (например, пшеница — яровая и озимая, белозерная или краснозерная и др.; рожь — озимая северная, озимая южная и т. д.). По некоторым культурам виды разделяются еще на подвиды, классы и сорта в зависимости от их свойств и качественных показателей.
Качественные показатели зерна — натура, влажность и степень чистоты. Натурой зерна называется масса известного объема зерна. Степень чистоты зерна характеризует наличие в нем посторонних примесей. Влажность определяется высушиванием зерна в специальных шкафах. Смешивать зерно различных видов и сортов не разрешается. Перевозят и хранят раздельно.
Физиологические свойства зерна определяют особые условия его хранения. Зерно следует предохранять от атмосферных влияний, так как оно обладает гигроскопичностью. При повышенной влажности в зерновой массе возможен процесс самосогревания, который вызывает порчу зерна. Большие потери зерна создаются также при заражении его хлебными вредителями. В связи с указанными особенностями зерновых грузов к складам, а также хранению и перевозке зерна предъявляют особые требования.
Зерно хлебных культур при содержании влажности до 14% и масленичных культур до 11% считается сухим. При более высоком проценте влажности зерновые культуры считаются влажными и сырыми и не подлежат ни хранению, ни перевозке. Зерно поступает в склады иногда влажностью до 30% и более при дождливой погоде в период уборки урожая. В этих случаях зерно подлежит сушке в специальных передвижных или стационарных сушилках с доведением до нормальной влажности, позволяющей обеспечить сохранность при перевозке и длительном хранении.
Предъявляя к перевозке зерно отправитель обязан представить сертификаты Государственной хлебной инспекции или удостоверения о качестве.
Физические свойства зерновой массы
Сыпучесть и самосортирование относят к физическим свойствам зерна. Зерновая масса состоит из множества отдельных твердых частиц, различных по размеру и плотности, поэтому обладает большой подвижностью — сыпучестью.
С сыпучестью связана способность зерновой массы к самосортированию. При любом перемещении или встряхивании зерновая масса «расслаивается». Тяжелые компоненты — минеральная примесь, крупные зерна как бы «тонут», опускаются вниз, а легкие — органический сор, семена сорняков и щуплые зерна «всплывают».
Это может оказать отрицательное влияние на сохранность, так как обычно семена сорных трав и щуплое зерно имеют повышенную энергию дыхания, что может привести к порче зерна при хранении.
Скважистость — заполненные воздухом промежутки между зернами в насыпи. Обычно скважистость выражают в процентах к общему объему данной насыпи. Плотность укладки зерновой массы в объеме хранилища и, следовательно, ее скважистость зависят от формы, размеров и состояния поверхности зерен, от количества и характера примесей, от массы и влажности зерновой насыпи, формы и размеров хранилища. Однородное по крупности зерно, а также зерно с шероховатой поверхностью имеют скважистость большую, чем зерна разной крупности и округлой формы.
Запас воздуха в межзерновых пространствах имеет большое значение для сохранения жизнеспособности семян. Большая газопроницаемость зерновых масс позволяет проводить активное вентилирование, регулировать состав газовой среды в межзерновых пространствах, вводить пары ядохимикатов для борьбы с амбарными вредителями. Однако наличие межзерновых пространств и кислорода в них благоприятствует развитию амбарных вредителей.
Сорбционные свойства зерна также относят к физическим. Зерно всех культур и зерновые массы в целом обладают сорбционной емкостью, т. е. способностью поглощать газы и пары различных веществ. Эта способность зерна обусловлена его капиллярно-пористой структурой, что делает активную поверхность зерновки в 200 — 220 раз больше истинной. При изменении условий окружающей среды зерно может частично отдавать поглощенные им вещества — десорбировать их. Однако полностью десорбция не происходит.
Явления сорбции принято подразделять на две группы: сорбция и десорбция различных газов и паров, кроме воды; гигроскопичность — сорбция и десорбция паров воды.
Способность зерна и продуктов его переработки активно сорбировать газы и пары различных веществ обязывает руководителей заботиться о чистоте транспорта и хранилищ, иначе продукты по вкусу и запаху могут стать непригодными для пищевых целей. При борьбе с амбарными вредителями можно применять лишь такие пестициды, которые менее вредны для теплокровных и более полно десорбируются.
Гигроскопичность зерновой массы оказывает наибольшее влияние на стойкость зерна при хранении. Хорошо сохраняет свои исходные свойства только то зерно, в котором вся влага находится в связанном коллоидами состоянии. Между относительной влажностью воздуха в хранилище и влажностью зерна через определенное время устанавливается динамическое равновесие. Каждому значению относительной влажности воздуха и его температуры соответствует определенная равновесная влажность продукта.
Влажность продукта, при которой в нем появляется свободная вода, носит название критической. Для большинства культур критическая влажность лежит в интервале 14, 5 — 16%. Зерно, достигшее ее, может заплесневеть.
Гигроскопичность зерна и продуктов его переработки зависит от содержания в них белков и высококомолекулярных пентозанов, способных поглощать влаги больше, чем другие вещества.
Теплопроводность и температуропроводность зерна также относят к физическим свойствам. Тепло в зерновой массе распространяется двумя способами: от зерна к зерну при их соприкосновении — теплопроводность зерна и перемещением воздуха в межзерновых пространствах — конвекция. Зерно имеет теплопроводность, близкую к древесине, т. е. обладает низкой теплопроводностью. Воздух также характеризуется небольшой теплопроводностью. Поэтому суммарный показатель теплопроводности зерновой массы в целом невелик и колеблется в пределах от 0, 12 до 0, 2 ккал.
Скорость нагревания зерновой массы — температуропроводность зависит от теплопроводности и также невелика. Таким образом, зерновая масса характеризуется большой тепловой инерцией, изменение температуры зерна в средних слоях насыпи происходит очень медленно. Поэтому зерно в зимние месяцы можно охладить, проведя активное вентилирование насыпи холодным сухим воздухом. Низкая температура его сохраняется в течение большей части лета, в результате чего замедляются биохимические процессы, протекающие в нем, и прекращается размножение амбарных вредителей. Если же на хранение засыпано теплое зерно, то в нем долго сохраняются благоприятные условия для: активной жизнедеятельности самого зерна, амбарных вредителей и микроорганизмов. В весенне-летний период, а также в осенне-зимний наблюдается большая амплитуда колебаний температуры между отдельными слоями зерновой массы, что может привести к конденсации влаги на отдельных ее участках, увлажнению зерна.
Биохимические процессы, происходящие в зерновой массе
Зерно — живой организм, находящийся в покое и, следовательно, как и в любом живом организме, в нем совершается постоянный, хотя и медленный, обмен веществ, поддерживающий жизнь зародышевой клетки. Характер и интенсивность физиологических процессов, протекающих в зерновой массе при хранении, зависят не только от активности ферментативного комплекса зерна, но и от условий окружающей среды. Основным, важнейшим физиологическим процессом, протекающим в зерне, является дыхание.
Дыхание обеспечивает энергией клетки семян за счет окисления органических веществ, главным образом сахаров, под действием окислительно-восстановительных ферментов.
При недостатке кислорода полного окисления органических веществ не происходит, в зерне идет процесс анаэробного (интрамолекулярного) дыхания (спиртового брожения). При анаэробном дыхании параллельно со спиртовым брожением частично может идти и молочно-кислое, что приводит к медленному нарастанию титруемой кислотности продукта. Анаэробное дыхание зерновой массы нежелательно, так как накопление этилового спирта и других промежуточных продуктов дыхания может привести к гибели зародыша, т. е. потере всхожести семян.
Интенсивность дыхания зависит от влажности, температуры и качества зерна.
Сухое зерно имеет невысокую интенсивность дыхания.
Температура хранения оказывает существенное влияние на интенсивность дыхания. Зерно, хранящееся при температуре, близкой к 0єС, дышит с исчезающе малой интенсивностью. По мере повышения температуры интенсивность дыхания возрастает, достигая максимума при 50 — 55єС, после чего начинает резко падать. Падение совпадает с началом гибели зерна.
Качество зерна оказывает существенное влияние на энергию его дыхания.
Чем хуже качество зерна, тем труднее его хранить.
Следствия дыхания зерна при хранении. Каким бы способом ни дышало зерно, этот процесс вызывает:
— потерю сухого вещества (убыль массы) зерна. Расходуемая, при дыхании глюкоза постоянно пополняется за счет ферментативного гидролиза крахмала; изменение состава воздуха межзерновых пространств за счет выделения диоксида углерода и расходования кислорода, что в конечном итоге может вызвать анаэробное дыхание;
— увеличение количества гигроскопической влаги в зерне и повышение относительной влажности воздуха в межзерновых пространствах. Образующаяся при аэробном дыхании вода остается в зерновой массе и при высокой интенсивности дыхания может существенно увлажнить ее, приводя тем самым к еще большему увеличению интенсивности дыхания;
— образование тепла в зерновой массе особенно при высокой интенсивности аэробного дыхания мотает быть весьма существенным. Известно, что зерновая масса обладает низкой теплопроводностью, поэтому образующееся тепло вызывает повышение температуры и, следовательно, интенсивности дыхания. Два последних названных следствия дыхания являются причинами возникновения самосогревания зерновой массы, приводящего ее к порче, а иногда и к полной гибели.
Самосогревание — результат высокой интенсивности дыхания зерновой массы, развития в ней плесеней, а иногда и амбарных вредителей. В начальной стадии самосогревания (повышение температуры до 30єС) зерно приобретает солодовый запах и сладковатый вкус, свойственные прорастающему зерну. Поверхность зерна сначала обесцвечивается, затем приобретает красноватый оттенок, а эндосперм — сероватый. Объемный выход хлеба снижается, мякиш получается более темным, чем из нормального зерна. При переработке пшеницы с солодовым запахом ее смешивают с нормальным зерном.
При развитии самосогревания и повышении температуры до 40 — 50єС и выше поверхность зерна темнеет вплоть до полного почернения, иногда полностью покрывается мицелием плесеней. Темнеет, а затем чернеет эндосперм. Запах становится плесневым, а потом гнилостно-затхлым, изменяется соответственно и вкус, увеличиваются титруемая кислотность (в болтушке), кислотное число жира, растет содержание аммиака.
Интенсивность дыхания достигает максимума и начинает падать, снижается всхожесть зерна вплоть до полной ее утраты. Содержание клейковины в пшенице резко снижается, а ее качество ухудшается. Эти изменения говорят о распаде в греющемся зерне углеводов, белков и липидов под действием собственных и плесневых ферментов, а также длительным воздействием повышенных температур. Если самосогревание возникает в поверхностном слое насыпи (до 0, 7 м от поверхности), то главной причиной порчи зерна является его плесневение.
При возникновении самосогревания в глубинных слоях бурное развитие плесеней задерживается недостатком там кислорода, поэтому основной причиной порчи являются деятельность собственных ферментов и высокая температура. Мука из зерна поверхностных очагов самосогревания дает хлеб плоский, почти без пор, с очень темным заминающимся мякишем, а из глубинных очагов самосогревания — высоким, с рваными корками. Зерно, подвергшееся самосогреванию больше, чем в первой стадии, на пищевые (иногда и кормовые) цели не используется.
В период хранения постоянно проводят наблюдения за зерном. Температура хранящейся зерновой массы должна находиться под повседневным контролем. При небольшом повышении температуры (на 1 — 3єС) проводят активное вентилирование сухим холодным воздухом. Если зерно после этого продолжает греться, то его приходится перемещать в резервный силос, пропуская при этом через зерносушилку и зерноочистительную машину (для охлаждения).
Поверхностный слой зерна не реже одного раза в неделю осматривается для определения присутствия (или отсутствия) признаков появления амбарных вредителей. При их обнаружении принимаются срочные меры по обеззараживанию зерновой массы и предупреждению их перехода в другие силосы.
Изменение пищевой ценности зерна при хранении связано с постепенным, хотя и очень медленно протекающим, старением коллоидов. Начало процесса старения коллоидов практически совпадает с завершением послеуборочного дозревания зерна. Известно, что уборка зерна производится в стадии технической спелости, когда влажность его может достигать 18 — 25% и синтез питательных веществ еще не завершен. Оно обычно имеет пониженные всхожесть и технологические достоинства. Полная физиологическая зрелость зерна, при которой наиболее полно выявляются технологические и семенные качества, наступает для ржи и овса через 15 — 20 дней, пшеницы — 1 — 1, 5 мес., ячменя — 6 — 8 мес. после уборки.
Послеуборочное дозревание — комплекс биохимических процессов синтеза высокомолекулярных органических соединений из низкомолекулярных, накопленных в зерне в ходе фотосинтеза растения и налива зерна. При дозревании заканчиваются процессы образования полисахаридов, белков и жиров.
Уменьшается доля растворимых углеводов и небелкового азота. Белки клейковины уплотняются, качество ее улучшается.
Послеуборочное дозревание наиболее быстро завершается в сухом зерне (до 14%) при положительной температуре в хранилище (15 — 20 `С), достаточном доступе кислорода. Более низкая температура или недостаток кислорода растягивают время дозревания, а повышенная влажность зерна может привести к его плесневению. Необходимо подчеркнуть, что процессы синтеза протекают с выделением влаги, связанной низкомолекулярными соединениями. Поэтому наблюдение за изменением влажности зерна в первый период хранения имеет особенно большое значение.
Завершение послеуборочного дозревания и вступление зерна в состоянии покоя фактически являются началом процесса старения.
Биохимические изменения веществ, входящих в состав зерна, постепенно приводят к снижению активности ферментов, всхожести, потере присущего живому организму активного иммунитета и существенному снижению технологических свойств и пищевых достоинств. Зерно становится более хрупким, легко дробится при — переработке с образованием повышенного количества отходов, снижаются выход продукции и ее качество. Полученные продукты значительно легче обсеменяются микроорганизмами и быстрее портятся.
Долговечность зерна зависит от его исходного качества и условий хранения. Хлебные злаки сохраняют жизнеспособность (всхожесть) от 5 до 15 лет. Наиболее долговечными являются овес, пшеница и ячмень, быстрее всех теряет всхожесть просо. Мукомольно-крупяные и пищевые достоинства сохраняются 10 — 12 лет, а кормовые — еще дольше. Однако столь длительное хранение запасов нецелесообразно, их следует обновлять через 3 — 5 лет.
перевозка груз контейнер
2. Перевозки зерновых грузов
2.1 Условия перевозок зерновых грузов К зерновым грузам относят злаковые культуры: пшеница, рожь, ячмень, овес, просо, гречиха, кукуруза в зерне и др.
Зерновые грузы обладают определенными свойствами, которые необходимо учитывать при перевозке и хранении. Прежде всего — это натурная масса, влажность и содержание примесей. Натурная масса, т. е. масса определенного объема груза, зависит от влажности, формы, величины и компактности зерна. Принимают к перевозке (в прямом железнодорожном и прямом смешанном железнодорожно-водном сообщении) зерновые грузы влажностью до 16% (просо до 15%). Зараженное зерно можно перевозить на предприятия, специально выделенные для его переработки, после чего вагоны и хлебные щиты дезинфицируют средствами и за счет грузовладельцев.
Предъявляя к перевозке зерновые грузы, отправитель обязан представить сертификаты Государственной хлебной инспекции или удостоверения о качестве.
Массу всех зерновых грузов, перевозимых насыпью, определяет на весах отправитель, что удостоверяет подписью в накладной; при отсутствии вагонных или элеваторных весов у отправителя массу определяют на вагонных весах станции отправления приемосдатчики дороги совместно с отправителем, что также удостоверяется их подписями в накладной.
За взвешивание груза дорога взыскивает с отправителя сбор. Вагоны под погрузку зерна подают с исправным кузовом, очищенные и в необходимых случаях промытые. Представитель отправителя, ответственный за погрузку, обязан до начала ее убедиться в том, что вагоны исправны, очищены, не заражены вредителями и не имеют отверстий и щелей, через которые может произойти утечка зерна.
Одна из особенностей перевозок зерна: большинство станций (до 80%) отправляют в год не более 10 тыс. т, остальные — от 10 тыс. до 50 тыс. т и только 3% станций — более 50 тыс. т.
Из наиболее крупных пунктов зерновые грузы отправляют в одногруппных маршрутах (отправительских), а основной вид перевозок зерна — ступенчатая маршрутизация с погрузкой на нескольких станциях (двух—четырех) одного (как правило) участка назначением в один пункт выгрузки. Это обеспечивает минимальные простои вагонов. В большинстве случаев наиболее целесообразны ступенчатые маршруты кольцевого типа с постоянными составами. Определяя их эффективность, необходимо учитывать увеличение порожнего пробега вагонов при возвращении из пунктов выгрузки в пункты погрузки, а также сокращение расходов на очистку, промывку вагонов и оборудование щитами.
Число станций, участвующих в погрузке маршрута, зависит от размеров погрузки на каждой из них, времени стоянок поездов, продолжительности грузовых операций с каждой группой вагонов (частью маршрута) и особенно на последней (по направлению движения порожних) станции.
2.2 Погрузка и выгрузка зерновых грузов Грузят, выгружают и хранят зерно на специальных складах. Наиболее совершенные склады-зернохранилища, обеспечивающие наилучшие эксплуатационные и экономические условия переработки зерна, — элеваторы. Принимаемое в них зерно поступает из кузовов автомобилей в лари приемного амбара, откуда подается в рабочую башню и с помощью ленточных конвейеров направляется в зерносушилку или к механизмам, которые поднимают его в весовые бункера для взвешивания. Отсюда зерно попадает на очистительные машины или на надсилосные ленточные конвейеры, при помощи которых его распределяют по силосным бункерам. Для погрузки в железнодорожные вагоны зерно из них поступает на ленту подсилосного конвейера, затем с помощью ковшового элеватора или нории его передают на весы, а оттуда самотеком по трубе направляют в вагон или в отпускные бункера-силосы для последующей погрузки в вагоны.
Рисунок 2.1. Линия погрузки железнодорожных вагонов Линия погрузки железнодорожных вагонов, модели GS-LLR, предназначены для высокопроизводительной погрузки зерна в вагоны зерновозы.
Погрузочное устройство станции на один вагон представляет собой специальные емкости с коническим дном вместимостью 40 тонн каждая, установленные на прочной металлической конструкции непосредственно над вагоном. В фермерских элеваторах возможна прямая погрузка с конвейера в вагон, без буферных емкостей. Для коммерческих элеваторов обязательно устанавливается одна, две и более емкостей, в зависимости от норм погрузки. Каждая емкость оборудована двумя самотечными трубами и электрической задвижкой.
Для подачи зерна с элеватора на линию погрузки применяется герметичный скребковый конвейер.
Количество одновременно разгружаемых вагонов — 1, 2 или 3 на одной ЖД линии. Линий погрузки может одна, две, три. Общая производительность конвейерной линии — 300 т/ч. Загрузка осуществляется из двух емкостей с коническим дном вместимостью по 40 т. каждый самотеком непосредственно в вагон-зерновоз. Преимуществом данного вида загрузки является то, что вагон загружается одновременно в четыре загрузочных люка вагона, тем самым сокращая время простоя вагона под погрузкой.
После погрузки рекомендуется взвешивание вагона с грузом на вагонных весах, расположенных на путях разгрузки или на ж/д станции.
Для взвешивания зерно сначала поступает в питающий бункер автоматических элеваторных весов, а оттуда через выпускное отверстие с клапаном в ковш, соединенный с весовым механизмом. При заполнении ковша точно установленной порцией груза клапан выпускного отверстия бункера автоматически закрывается, ковш опрокидывается, и зерно высыпается в приемник подводящей системы. Освободившийся ковш возвращается в прежнее положение, клапан питающего бункера открывается и процесс повторяется. Массу зерна определяет особый механизм — счетчик, учитывающий груз, прошедший через ковш, по количеству отвесов. Элеваторные весы позволяют взвесить в один прием зерно для целого вагона.
Определяя массу зерна не на элеваторных, а на вагонных весах, сначала взвешивают порожние вагоны, а затем груженые с отцепкой от состава и дозировкой, что требует много времени. Поэтому при загрузке группы вагонов рекомендуется разделить ее на две подачи и совмещать загрузку первой с взвешиванием второй, а загрузку второй — с взвешиванием и дозировкой первой.
Для загрузки вагонов зерном применяют специальные приспособления — разбрасыватели (крыльчатки), которыми оборудуют ленточные конвейеры. Зерно лентой конвейера подается в приемное устройство разбрасывателя, откуда поступает на вращающуюся крыльчатку, которая направляет его к торцовым стенам и разравнивает внутри вагона. Производительность разбрасывателей 68—73 т/ч; применение их позволяет повысить загрузку вагона на 3—5 т.
Для определения качества зерна берут пробы: при механизированной погрузке — с транспортерной ленты, в остальных случаях — из вагона вагонным щупом после погрузки.
Погрузка в специальные вагоны бункерного типа для перевозки грузов насыпью выполняется на пунктах, оборудованных устройствами для подачи грузов сверху с помощью погрузочных приспособлений (специальных лотков, отпускных труб).
В расчетную технологическую норму на погрузку вагонов бункерного типа включаются затраты времени на следующие операции:
— подготовительные операции tподг — открывание двух-трех крышек загрузочных люков с выходом на крышу вагона и отмыканием запоров и фиксаторов, заправка в люки концов отпускных труб, установка желобов, лотков. Как правило, с этими операциями должны совмещаться операции закрепления троса маневровой лебедки;
— заключительные операции tзакл — выход на крышу вагона, уборка отпускных труб, желобов, лотков, очистка крыши вагона от просыпавшегося груза, закрывание загрузочных люков, замыкание затворов и фиксаторов, навешивание запорно-пломбировочных устройств. С этими операциями должны совмещаться операции отцепки троса маневровой лебедки, очистки последнего вагона снаружи;
— основные операции погрузки груза в вагон t груз.
При погрузке группы вагонов в затраты времени на основные операции погрузки включается также время на передвижения вагонов маневровыми средствами. Время на дозировочные операции должно совмещаться с основными операциями погрузки, для чего места погрузки должны быть оснащены весоизмерительными и дозирующими устройствами, обеспечивающими загрузку массы груза, соответствующей технической норме загрузки вагона.
Выгружают зерно на элеваторах с приемными ларями (бункерами), а также на мельничных комбинатах и механизированных складах.
Производственные элеваторы на мельничных комбинатах одновременно принимают под выгрузку целый маршрут.
На станции назначения вагоны с зерновыми грузами взвешивают, а затем после подачи под выгрузку осматривают в коммерческом отношении (исправность вагонов и пломб) представитель местной организации хлебопродуктов и приемосдатчик дороги, в присутствии которого вскрывают вагоны и разгружают их. При взвешивании учитывают норму естественной убыли, которая зависит от расстояния перевозки.
Погрузка происходит через отпускную трубу элеватора из погрузочного бункера с выходным горизонтальным отверстием диаметром 350 мм. Насыпная масса зерна 0,75 т/м3, в вагон в среднем загружается Qв = 65 т. В процессе загрузки вагоны последовательно передвигают на длину вагона и не менее трех раз перестанавливают отпускную трубу. Длина вагонов по осям автосцепок Lв = 14,7 м. Скорость движения троса маневровой лебедки Vл = 0,18 м/с.
Закрепление троса маневровой лебедки согласно хронометражным данным занимает 1,5 мин и совмещается с операциями подъема рабочих на верхнюю площадку, выхода их на крышу вагона, открывания двух загрузочных люков и заправки отпускной трубы в первый люк вагона. На подготовительные операции требуется 3 мин, на операцию открывания (закрывания) бункерного затвора — 5с, продолжительность заключительных операций по уборке отпускной трубы, закрыванию люков на последнем вагоне группы, приведение в действие фиксаторов, а также по освобождению троса маневровой лебедки составляет 3 мин.
При выгрузке зерна на элеваторах вагоны разгружают в приемные бункера только после полного освобождения их от ранее выгруженного зерна. Разгружать вагоны необходимо без простоев в ожидании освобождения приемных бункеров и так, чтобы конвейеры и ковшовые нории не работали вхолостую. Поэтому при массовом поступлении зерна на элеваторы время на разгрузку и перестановку вагонов должно быть равно необходимому на полное освобождение приемных бункеров или больше его.
Особенность выгрузки зерна в склады мельничных комбинатов заключается в том, что в большинстве случаев часть освобожденных вагонов используется без особой очистки для погрузки муки. Продукты переработки зерна, перевозимые в таре (мука, крупа), принимают к перевозке и сдают грузополучателям по числу мест и по весу, устанавливаемому взвешиванием на вагонных весах, а при отсутствии их в пункте погрузки — на товарных весах.
Кроме того, возможна непосредственная перегрузка зерна из вагоназерновоза в автомобиль.
Комплекс для разгрузки вагонов-хопперов предназначен для выгрузки зерна, комбикормов и других сыпучих продуктов из железнодорожных вагонов типа «Хоппер» с последующей перегрузкой в транспортные средства.
Комплекс состоит из шнекового разгрузчика ШРВ-50 и шнекового конвейера передвижного ШКП-50.
Рисунок 2.2 Комплекс для разгрузки вагонов-хопперов.
Таблица 1 Технические характеристики комплекса
ШРВ-50 | ШКП-50 | ||
Производительность, т/час | |||
Установленная мощность, кВт | 5,2 | 5,5 | |
Диаметр шнеков, мм | 130; 250 | ||
Габаритные размеры, мм | 4600×930×1950 | 5780×1610×3800 | |
Масса, кг | |||
3. Определение расчетных объемов работы грузовых пунктов Объем работы грузовых пунктов исчисляется в суточных грузопотоках и в суточных вагонопотоках. Перевод годовых грузопотоков по каждому роду груза в суточные вагонопотоки выполняется в следующей последовательности.
3.1 Расчет суточных грузопотоков На основе данных годового грузооборота по отправлению в тоннах переводится в расчетный грузопоток по формуле:
тонн/сутки (3.1.1)
Где — годовое прибытие или отправление, т;
365 — дней в году;
— коэффициент неравномерности перевозок Расчет:
Зерно:
3.2 Расчет суточных вагонопотоков Тип вагонов для каждого груза принимается на основании перечней грузов, разрешенных к перевозке на открытом подвижном составе, в цистернах и в крытых вагонах.
Выбор типов вагонов должен производиться с учетом возможности использования под погрузку вагонов из-под выгрузки.
Суточные вагонопотоки рассчитываем исходя из суточного грузопотока для всех грузов, кроме контейнеров, по формуле:
ваг/сутки (3.2.1)
где Рт — техническая норма загрузки вагона, т.
Расчет:
Зерно:
4. Выбор схемы комплексной механизации погрузочно-разгрузочных работ
4.1 Выбор типа склада и средств механизации погрузочно-разгрузочных работ для расчета Схемой механизации погрузочно-разгрузочных работ (ПРР) и складских операций называется комплекс машин, устройств и оборудования, обеспечивающий переработку груза по определенному технологическому процессу.
Для заданного груза выбираем наиболее эффективную схему комплексной механизации погрузочно-разгрузочных работ с учетом заданных объемов работы грузового пункта на основе типовых схем.
При выборе наиболее эффективной схемы учитываем следующие положения:
— выбираемые погрузочно-разгрузочные машины (ПРМ) и устройства должны обеспечивать полную сохранность грузов, надежность в эксплуатации и безопасность для обслуживающего персонала, иметь минимальную массу, соответствовать своему основному назначению, роду и свойствам перерабатываемых грузов;
— техническая производительность и производственная норма выработки ПРМ должны соответствовать объему грузопереработки;
— грузоподъемность ПРМ выбирается в зависимости от количества груза, поднимаемого механизмом за цикл и массы грузозахватного приспособления;
— операции по застропке и отстропке грузов должны быть с минимальными затратами ручного труда и с применением автоматических (полуавтоматических) грузозахватов.
При выборе вариантов механизации и типов ПРМ учитываем расстояние и направление перемещения грузов, способы их хранения, типы складов (закрытое помещение или открытая площадка), размеры и форму площади складов, условия охраны труда обслуживающего персонала.
4.2 Технология погрузочно-разгрузочных работ
4.2.1 Технология погрузочно-разгрузочных работ на местах общего и не общего пользования К навалочным и сыпучим относят грузы, не требующие упаковки при хранении и транспортировке. Зерно относится к группе навалочных грузов перевозимых в крытом подвижном составе и хранимых в крытых складах. В данном случае — в элеваторах.
Характеристики зерна как груза: объемная масса — 0,7−0,8 т/м3, угол естественного откоса в покое — 35. Зерно необходимо предохранять от атмосферного влияния, так как оно обладает гигроскопичностью. В связи с указанными особенностями к складам, хранению и перевозке зерна предъявляются особые требования.
После того, как сборка нового урожая зерна завершена, самый важный вопрос: как сохранить его, чтобы избежать потерь и излишних затрат. Зерно подлежит хранению в течение длительного времени. Для этой цели используются зернохранилища или элеваторы. Потребность в услугах качественного хранения зерновых есть у всех производителей и потребителей данного вида продукции: агрофирм, фермеров, частных предпринимателей и их ассоциаций, промышленных комбинатов, заводов.
Элеваторы представляют собой комплекс оборудования для хранения зерна (емкости, хопперы) и транспортного оборудования (нории, конвейеры), благодаря которому зерно движется по заданным маршрутам.
По своему назначению зерновые склады подразделяют на заготовительные, перевалочные, производственные и базисные. Часто зерновые склады имеют несколько из указанных назначений. Например, они могут быть одновременно перевалочными и базисными или перевалочными и производственными и т. д.
Основным типом зерновых складов являются элеваторы, но находят применение и склады напольного хранения. Элеваторы разделяют на заготовительные (линейные), которые служат для приема зерна непосредственно от совхозов (колхозов) и отгрузки его потребителям (рис. 4.2.1) на мельничные производственные или перевалочные (портовые, базисные) элеваторы для перевалки с одного вида транспорта на другой или для длительного хранения. На рис. 4.2.2, а показан план и разрез башни заготовительного элеватора. Для приема зерна из автомобилей, предварительно взвешенных на автомобильных весах, предназначены бункера, расположенные на уровне пола в здании. Каждый из этих бункеров вмещает 50 т зерна. Зерно высыпается в бункер через открытый задний борт автомобиля, стоящего на наклонной платформе автомобилеподъемника. Под бункерами смонтированы ленточные конвейеры, перемещающие зерно к элеваторной башне. Здесь при необходимости зерно подвергают очистке, сушке или сразу же поднимают его нориями наверх башни, взвешивают на автоматических ковшовых весах и передают на ленточные надсилосные конвейеры. С этих конвейеров зерно попадает в силосы корпусов (показаны только два силосных корпуса, прилегающих к башне, но могут быть и четыре, тогда вместимость элеватора увеличивается в 2 раза).
Из силосов зерно ссыпают на подсилосные конвейеры, которые и доставляют его к нории. Затем его поднимают наверх и после взвешивания по отпускным трубам загружают в вагоны.
Технологическая схема движения зерна через силосы и башню элеватора показана на рис. 4.2.2, б. Зерно в вагоны поступает из отпускных бункеров из-под весов или через трубы, присоединенные непосредственно к сбрасывающим тележкам надсилосных ленточных конвейеров.
Рисунок 4.2.1. Приемный пункт и заготовительные склады для зерна: 1 — автомобильные весы; 2, 3 — здания с автомобиле разгружателями; 4 — приемные бункера в тоннеле; 5 — башня элеватора; 6 — силосы для зерна; 7 — конвейер; 8 — железнодорожные пути для загрузки зерна в вагоны; 9 — склад топлива; 10 — конвейерная галерея; 11 — механизированные склады; 12 — башня с перегрузочными устройствами; 13 — мельница; 14 — цех отходов; 15 — склад комбикормов.
Вдоль отпускных устройств элеватора укладывают один или два железнодорожных пути. Вагоны на них передвигают маневровыми лебедками или локомотивами.
Силосные корпуса элеватора изготовляют из монолитного или сборного и предварительно напряженного железобетона (пространственные элементы в виде коробов, плит, колец). В плане силосы имеют квадратную или круглую форму. Квадратные силосы (в плане 3×3 и 4×4 м и высотой 30 м) обычно строят на заготовительных элеваторах. Собирают их из объемных блоков или плит толщиной 25 см. Диаметр круглых силосов обычно 6 м, высота — 30 м, толщина стен 20—25 см. Вместимость типовых сдвоенных круглых силосных корпусов (в тыс. т): 2×11, 2×25, 2×50. Вместимость, образующаяся при соединении круглых силосов в виде звездочки в плане, также используют для хранения зерна. Условные обозначения элеватора Л2×100 или Л3×175. Буква Л показывает, что элеватор линейный; первая цифра после буквы соответствует числу норий, вторая — часовой производительности каждой из них: ЛВ означает элеватор линейный для восточных районов (хотя строят их во всех районах страны); ЛМ — линейный монолитный; ЛС — линейный из сборного железобетона и т. д.
Среднесуточная перерабатывающая способность линейного элеватора составляет по приему с автомобильного транспорта 1,5- 5,0 тыс. т, по погрузке в вагоны — 1,5−2,5 тыс. т, по очистке — 1,5−5,0 тыс. т и сушке — 175−2500 т.
Производительность конвейеров соответствует производительности норий, расположенных в башне элеватора. Для обработки влажного и сырого зерна склады оснащают сушилками и установками активного вентилирования.
Рисунок 4.2.2. Заготовительный элеватор для зерна: а) план и разрез башни, б) технологическая схема движения зерна через силосы и башню, 1 — приемные бункера, 2 — элеваторная башня, 3 — силосные корпуса, 4 — надсилосный конвейер, 5 — подсилосный конвейер, 6 — вагон, 7 — зерносушилка.
Производственные (мельничные) элеваторы получают зерно, как правило, железнодорожными маршрутами. Имеется несколько типов таких элеваторов. Башни мельничных элеваторов М2×100, М3×100, М2×75 и М3×175 оборудованы двумя или тремя ковшовыми элеваторами производительностью 100 или 175 т/ч, одним или двумя сепараторами производительностью 100 т/ч, двумя или тремя ковшовыми 20-тонными весами.
Силосные корпуса элеваторов М2×100 и М3×100 вмещают 8—16 тыс. т зерна, М2×175— 16 тыс. т и М3×175 — 33,4 тыс. т.
Суточная приемная способность по выгрузке зерна из вагонов составляет для указанных четырех типов элеваторов соответственно 1,5; 2,0; 3,0 тыс. т.
Для приема зерна из вагонов на элеваторах служат приемные лари (бункера). Ковшовые элеваторы производительностью 100т/ч имеют два поперечно расположенных ларя по отношению к железнодорожным путям, производительностью 175 т/ч — четыре ларя с продольным расположением. Под приемными ларями находятся ленточные конвейеры, подающие зерно в башмаки ковшовых элеваторов. Вагоны следующей постановки могут быть разгружены в те же самые лари только после полного освобождения их от ранее выгруженного зерна. Если ленточные конвейеры под приемными бункерами расположены вдоль железнодорожных путей, то число путей над ларями должно быть равно числу ковшовых элеваторов. При поперечном расположении приемных конвейеров число путей должно соответствовать числу ларей, обслуживаемых одним ковшовым элеватором.
Выгрузку вагонов необходимо организовать так, чтобы они не простаивали в ожидании освобождения ларей, а приемные конвейеры и ковшовые элеваторы не работали вхолостую во время заполнения ларей. Для этого период освобождения ларей должен быть равен периоду разгрузки и перестановки вагонов.
Продолжительность выгрузки зерна из четырехосного крытого вагона инерционной машиной ЦНИИ МПС составляет 10 мин. Ее выгодно применять при суточной выгрузке пяти вагонов и более. Наиболее эффективны для перевозки зерна специализированные вагоны — зерновозы.
Перевалочные элеваторы в отличие от заготовительных принимают зерно, уже прошедшее первичную обработку. Однако при подготовке зерна к длительному хранению на этих элеваторах выполняют работы по дальнейшему улучшению его качества. Производительность этих элеваторов 350, 500 т/ч и более. Вместимость элеваторов 50—150 тыс. т.
Элеваторы для семенного груза устраивают с вентилируемыми силосами.
Для хранения зерна применяются также напольные зерновые склады. Зерновые склады в настоящее время сооружают из сборного железобетона на 5,5 тыс. т зерна. Продольные стены складов состоят из ребристых панелей. Помимо сборного железобетона, стены такого склада могут быть выложены из кирпича, крупных шлакобетонных или бетонных блоков и других строительных стеновых материалов. Для восприятия сдвигающих усилий от давления зерна, передающегося на стены, предусмотрены анкерные (разгрузочные) плиты.
Плиты закладывают в грунт на глубине подошвы наружного фундамента. Полы применяют асфальтовые по бетонному основанию. Асбестоцементная кровля склада наклонена к горизонту под углом 25°, равным углу естественного откоса зерна. Это дает возможность лучше использовать объем склада и установить между верхним поясом и затяжкой фермы ленточный конвейер со сбрасывающей тележкой.
Для выдачи зерна из склада служит конвейер, размещенный в подземной траншее. Конвейер связан с рабочей башней, которая расположена у торца склада и служит для приема зерна с автотранспорта и погрузки в железнодорожные вагоны. Нижний траншейный конвейер может быть как ленточным, так и скребковым (с погруженными скребками). Зерно поступает на нижний конвейер через затворы с отверстиями 300×200 мм, размещенными с шагом 5 м. Нижний конвейер доставляет зерно в башню для отгрузки в вагоны.
В ряде случаев может возникнуть срочная необходимость в складском помещении для хранения зерна. Тогда целесообразно использовать склад в виде пневмонадувных оболочек. Положительные качества этих складов: предельная легкость, компактность, хорошая транспортабельность в свернутом виде, возможность быстрого возведения и разборки без специальных приспособлений.
На рис. 4.2.3 показана технологическая схема движения зерна при загрузке в склад и выдаче со склада. Зерно, поступающее с транспортных средств в приемные бункера, поднимается ковшовым элеватором (норией) на приемно-очистительные устройства, после которых ковшовым элеватором подается на конвейер для заполнения склада, где оно хранится. Со склада зерно выдается через отверстия или питатели на нижний конвейер, с которого поступает в норию и далее может опять поступать в приемно-очистительные устройства (проветривание, охлаждение, сушка и т. п.) или на транспортные средства.
Оборудование башни механизированных складов составляют два ковшовых элеватора, сепаратор производительностью 100 т/ч, двое весов с нагрузкой 10 т, автомобилеподъемник для выгрузки зерна из автомобилей и прицепов, отгрузочный ленточный конвейер с вагонозагрузчиком, сушильный агрегат производительностью 50 т/ч.
В условиях интенсивной уборки урожая зерна, кроме складов со стационарной механизацией, используют павильонные склады с передвижными средствами механизации, хотя они менее эффективны, чем первые.
Исследования объемно-планировочных и конструктивных решений зернохранилищ, проведенные в Центральном научно-исследовательском институте имени Кучеренко, и зарубежный опыт показали, что весьма эффективными для хранения зерна в сельском хозяйстве являются зернохранилища силосного типа.
Наряду с совершенствованием силосных железобетонных зерновых складов для сельского хозяйства заслуживает внимания использование облегченных металлических силосов. Опыт латвийских специалистов хранения семенного зерна был использован при разработке типового проекта семенохранилища № 813−127 со сблокированными бункерами С-50 производства Латсельхозтехника. Другим примером использования металлических емкостей в сельском хозяйстве являются отдельно стоящие силосы, возводимые из волнистых стальных или алюминиевых листов на болтах.
Современные металлические элеваторы комплектуются оборудованием по уходу за зерном, таким как системы температурного контроля, системы аэрации, системы обнаружения насекомых. В состав элеватора обязательно входят лаборатория и весовое оборудование для контроля над количеством и качеством поступающего зерна. В зернохранилищах также улучшается качество зерна, просушиваясь и очищаясь от мелких и крупных примесей.
Высокотехнологичное оборудование оптимально отвечает требованиям по энергосбережению, экологической и производственной безопасности и потребует минимального технического обслуживания в процессе эксплуатации. Все элеваторное оборудование имеет оцинкованное покрытие, что уменьшает риск коррозии металла, позволяет устанавливать его на открытом пространстве и эксплуатировать при любых погодных условиях без необходимости строительства дополнительных защитных конструкций. Все процессы на элеваторах автоматизированы, что означает минимальное использование рабочей силы. В отличие от элеваторов старой конструкции, современные металлические элеваторы обеспечивают надежную защиту зерна от промокания и от порчи насекомыми-вредителями, грызунами и птицами, позволяют сохранить качественные и количественные показатели зерна в течение более одного года. И самое главное: благодаря высокотехнологичным средствам мониторинга имеется возможность наблюдать и контролировать работу всего элеватора с одного компьютера из офиса.
Вместимость силосов различная — от 98 до 187 м3. Отношение высоты силоса к его диаметру 1 — 1,4. Днище силоса выполнено в двух вариантах: плоские и конические, в последнем случае силосы опираются на металлические колонны высотой 3,2 м. Силосы расположены в ряд и объединены верхней транспортерной галереей.
Институтом ЦНИИ проект сталь конструкция разработаны металлические гладкостенчатые зернохранилища цилиндрической формы с плоским днищем вместимостью от 50 до 2000 м3.
В этих силосах применен при их изготовлении и монтаже метод рулонирования.
Рисунок 4.2.3. Технологическая схема перемещения зерна в механизированном складе: 1 — приемный бункер; 2, 4 — ковшовые элеваторы; 3 — бункер; 5 — загрузочный конвейер; 6 — зернохранилище; 7 — затворы для выдачи зерна; 8 — выгрузочный конвейер.
Рулонируемое полотнище стенки силоса имеет переменную толщину по ярусам. Такие силосы применяются при строительстве промышленных зернохранилищ вместимостью 3000 м3.
При проектировании зернохранилищ в целях экономии металла предложено заменить панель зернохранилища на тонколистовую обшивку — мембрану. Для ускорения сборности конструкции зернохранилища, стены которого выполнены из крупноразмерных панелей, ЦНИИСКом имени Кучеренко разработано зернохранилище, каждая панель которого выполняется в виде плоского листа, прикрепленного к горизонтальным и вертикальным элементам каркаса. Смежные панели соединены тяжами, позволяющими уменьшить длину горизонтальных ригелей. В качестве обшивки панели используется оцинкованная рулонная сталь, что позволяет снизить трудоемкость изготовления панели и повысить антикоррозионную стойкость хранилища.
Панели хранилища полной заводской готовности с монтажными соединениями на болтах доставляются к месту монтажа зернохранилища.
Исследования объемно-планировочных и конструктивных решений по применению зернохранилищ из мембранно-каркасных панелей, выполненные Г. А. Давлетовой (МИИТ), показали высокую эффективность таких зернохранилищ при сохранении качественных показателей зерна.
Требования к объемно-планировочным и конструктивным решениям элеваторов и производственным зданиям для обработки зерновых продуктов изложены в СН 261−77. Установлено, что наружные диаметры круглых силосов должны приниматься 6; 9; 12; 18; 24 м, а высота стен силосов, подсилосных и надсилосных этажей — кратными 0,6.
При этом высота Н должна быть больше чем 1,5vF (F — площадь горизонтального сечения силоса) при диаметре 12 м и более — не меньше 15 м.
Сборные железобетонные стены силосов, как правило, следует предусматривать из предварительно напряженных конструкций, а для квадратных силосов следует предусматривать применение объемных блоков. В силосах следует предусматривать мероприятия по снижению горизонтального давления зерна при выпуске с помощью установки в круглых силосах разгрузочных центральных перфорированных труб или выпуска зерна из силосов через отверстия в стенах межсилосных емкостей (звездочек) и др.
Здания зерноскладов сооружаются одноэтажными, без перепадов высот, с унифицированными объемно-планировочными параметрами: пролеты 6 и 12 м, шаг опор 6 м и высота помещения у стен 3,6 м.
Склады с наклонными полами должны иметь уклон не менее 36°. При длине тоннеля боле 120 м следует предусматривать промежуточные выходы не реже чем через 100 м в виде каналов высотой 1,5 м и шириной 0,7 м.
Вынос кровли (за наружную поверхность стен) должен быть не менее 0,7 м. Полы должны быть асфальтобетонными, не допускается применение дегтей и дегтевых мастик.
Принимаем основной тип зерновых складов — мельничный элеватор. Производственный (мельничный) элеватор получает зерно железнодорожными маршрутами. Башни мельничного элеватора оборудованы ковшовыми элеваторами производительностью 100 т/ч.
Для приема зерна из вагонов на элеваторах служат приемные лари (бункера). Ковшовые элеваторы производительностью 100 т/ч имеют два поперечно расположенных ларя по отношению к железнодорожным путям. Под приемными ларями находятся ленточные конвейеры, подающие зерно в башмаки ковшовых элеваторов.
Выгрузку вагонов организовываем так, чтобы они не простаивали в ожидании освобождения ларей, а приемные конвейеры и ковшовые элеваторы не работали вхолостую во время заполнения ларей.
Станции разгрузки железнодорожных вагонов, модели GS-SAR, предназначены для высокопроизводительной выгрузки зерна из вагонов зерновозов.
Приемное устройство станции на один вагон представляет собой траншею шириной 1,1 м и глубиной до 1,5 м каждая. В траншее установлен скребковый конвейер производительностью 150 т/ч со специальными приемными воронками.
Количество одновременно разгружаемых вагонов может доходить до 8 на одной линии разгрузки. Линий разгрузки может одна, две, три.
Общая производительность конвейерной линии 150 — 900 т/ч.
Рисунок 4.2.4. Станции разгрузки железнодорожных вагонов Вагонные операции включают в себя надвиг и установку вагонов с помощью маневрового тепловоза над приемными устройствами СРВ. Специальный транспортер обеспечивает прием потока груза из кузова четырехосного саморазгружающегося вагона-зерновоза бункерного типа. До начала разгрузки рекомендуется взвешивание вагона с грузом на вагонных весах, расположенных на путях разгрузки или на ж/д станции. Над станцией разгрузки предусмотрен навес с галереей для обслуживающего персонала.
4.2.2 Выбор грузозахватных приспособлений
Производительность ПРМ находится в прямой зависимости от конструктивных качеств захватных устройств, правильного подбора их к конкретному грузу и условий работы с ним. Простой вагонов под грузовыми операциями зависит от производительности ПРМ. При выборе грузозахватных устройств руководствуемся справочными данными.
Для зерна примем за основу ковшовый элеватор (норию), в которой груз перемещается в ковшах, закрепленных на тяговом органе. В качестве тягового органа используется хлопчатобумажную прорезиненную ленту типа конвейерной или цепи.
Нория применяется в качестве подъемно-транспортного оборудования для транспортировки зерна и других мелких сухих материалов в вертикальном направлении. Транспортируемый материал поступает через загрузочный носок в ковши или выбирается ковшами со дна башмака и перемещается транспортируемым органом к верхней головке, где происходит разгрузка ковшей в разгрузочный патрубок.
Работа норий контролируется с помощью амперметров, указывающих на любую опасность перегрузок или перебоев в работе, при этом нория отключается до того, как может произойти серьезное повреждение. Для движения норий используются низкоскоростные приводы, что позволяет наблюдать за работой норий и состоянием ковшей (их износом или повреждением).
Конструкция может быть изготовлена из низкоуглеродистой или нержавеющей стали, гальванизированная или окрашенная.
На рис. 4.2.5. приведен ковшовый двухцепной элеватор. Две его замкнутые цепи 3 и 9 обегают вверху приводные звездочки 6, а внизу — натяжные 1.
Цепи элеватора вместе с закрепленными на них ковшами 4 заключены в кожух 8, что улучшает работу ковшей, исключает распыливание груза и способствует безопасности при эксплуатации машины. Кожух состоит из секций длиной 2 — 2,5 м. Нижняя часть кожуха называется башмаком.
Она снабжена загрузочным отверстием 2 для заполнения ковшей 4 грузом, здесь же размещена натяжная станция. Верхняя съемная часть 5 кожуха называется головкой элеватора. Она имеет выгрузочное отверстие 7. Головка выполняется съемной для удобства осмотра и ремонта наиболее ответственной части элеватора — привода.
Ковши элеватора, проходя через башмак мимо загрузочного, отверстия, заполняются грузом, перемещаются вверх и при опрокидывании на ведущих звездочках освобождаются от груза.
На сегодняшний день наиболее популярны ковши из полимерных материалов. Они имеют более легкий вес и исключают искрение, которое характерно для стальных ковшей.
В элеваторах ленточных вместо приводных и натяжных звездочек вверху монтируется приводной барабан, а внизу — натяжной. Элеватор для зерна — до 1000 тс/ч и высоту подъема груза до 50 — 60 м.
Рисунок 4.2.5. Ковшовый двухцепной элеватор (НОРИЯ).
Рисунок 4.2.6. Схема ковшового элеватора: 1 — рама элеватора; 2 — приводной барабан; 3 — храповый механизм; 4 — замкнутая цепь или лента; 5 — натяжное устройство; 6 — ковш; 7 — башмак; 8 — головка
5. Расчет размеров складских сооружений
5.1 Выбор склада Из существующих типов складов по данным 2 раздела выбирается наиболее экономичный.
Зерно перевозится насыпью в специализированных вагонах — зерновозах и требует защиты от атмосферных осадков. Для хранения зерна применяем крытый силосного типа склад.
5.2 Определение площади и линейных размеров складов Площадь склада и его линейные размеры зависят от типов принятых складов, размещения в них грузов и технологии их переработки.
Емкость элеваторного склада определяем по формуле:
(5.2.1)
Полученные значения емкости следует принять близкими к типовым. Число элеваторных башен рассчитывается по формуле
(5.2.2)
где ес — емкость одной элеваторной башни, т.
Емкость силосного корпуса круглой формы определяется:
(5.2.3)
где D — диаметр силоса, D = 6 м;
Нс — полезная высота силоса, Нс = 30 м;
г — объемный масса груза, т/м3 (прил.3 [14]);
ц — коэффициент заполнения силоса, ц = 0,95ч0,98.
Для зерновых грузов выгрузка вагонов должна быть организована так, чтобы они не простаивали в ожидании освобождения ларей, а приемные конвейеры и ковшовые элеваторы работали вхолостую во время заполнения ларей. Продолжительность освобождения ларей от зерна
(5.2.4)
где n — число ларей (бункеров) приема зерна;
tл — время освобождения от зерна одного ларя, мин.
(5.2.5)
где t1 — чистое время освобождения ларя, мин;
(5.2.6)
где t2 — время истечения остатков зерна до полного освобождения ларя, t2 = 1 мин;
t3 — период между концом выпуска зерна из одного ларя и началом выпуска зерна из другого ларя, t3 = 0,5ч1,0 мин;
Птех — часовая производительность ковшового элеватора т/ч;
Рт — количество груза в ларе (нагрузка вагона), т.
Часовая производительность ковшового элеватора определяется по формуле
(5.2.7)
где Ек — емкость ковша, Ек = 4,2 м3;
lк — шаг ковшей, lк = 0,5 м;
ш — коэффициент заполнения ковша, ш = 0,75ч0,9;
г — объемная масса груза (прил.3 [14), т/м3;
Vк — скорость перемещения ковша, Vк = 2,0 м/с.
Необходимое число ларей
(5.2.8)
где tр — продолжительность разгрузки вагона, tр = 96 мин (по[8]);
tуб — продолжительность уборки и постановки вагонов под разгрузку, tуб = 10 мин.
Определение площади поперечного сечения потока зерна, проходящего через выпускное отверстие бункера, рассчитывается по формуле:
(5.2.9)
Определение гидравлического радиуса поперечного сечения потока из выпускных отверстий круглой формы:
(5.2.10)
Скорость истечения зерна определяется по формуле:
(5.2.11)
Определение средней производительности бункерного погрузочного устройства по пропускной способности бункера:
Пб = 3600· г·F·v, т/ч. (5.2.12)
Число линий приемных устройств (ларей, конвейеров и ковшовых элеваторов) для разгрузки суточного вагонопотока
(5.2.13)
где nв — количество вагонов, разгружаемых одним приемным конвейером и элеватором.
(5.2.14)
где Nпод -число подач вагонов за сутки.
На передвижение вагона маневровой лебедкой в процессе погрузки и выполнение промежуточных вспомогательных операций затрачивается:
где t т — время перестановки отпускной трубы, принимается равным 1 мин на вагон.
Определение среднего времени загрузки одного вагона:
Технологическая норма на погрузку вагонов-зерновозов составит:
Расчет:
Элеваторного склада:
Принимаем элеватор мельничный емкостью 16 тыс. тонн
— принимаем 26 башен Площадь поперечного сечения потока зерна, проходящего через выпускное отверстие бункера, принимая размер зерна, а = 6 мм = 0,006 м:
Гидравлический радиус поперечного сечения потока из выпускных отверстий круглой формы:
Определение средней производительности бункерного погрузочного устройства по пропускной способности бункера при значении коэффициента истечения для зерна л = 0,6:
Пб = 3600 · 0,75 · 0,0928 · 1,04 = 260 т/ч.
Скорость истечения зерна определяется по формуле:
V = 5,9 · 0,6 v0,086 = 1,04 м/с.
На передвижение вагона маневровой лебедкой в процессе погрузки и выполнение промежуточных вспомогательных операций затрачивается:
где t т — время перестановки отпускной трубы.
Определение среднего времени загрузки одного вагона:
Технологическая норма на погрузку трех вагонов-зерновозов составит:
6. Расчет потребного количества погрузочно-разгрузочных машин Потребность в погрузочно-разгрузочных машинах рассчитывается на основе детерминированных грузопотоков и технологии их переработки.
Детерминированный режим работы грузового пункта характеризуется регулярным входящим потоком транспортных средств (вагонов, автомобилей) или поступлением их на грузовой фронт по расписанию, примерно через одинаковые интервалы, при этом количество вагонов в подаче и время выполнения грузовых операций практически не отклоняется от своего среднего значения.
6.1 Потребность в погрузочно-разгрузочных машинах на основе детерминированных грузопотоков При детерминированном режиме работы вагоны и автомобили обслуживаются без задержки, исключается время ожидания грузовых операций и вероятность образования очереди у грузового фронта.
Количество погрузочно-разгрузочных машин Z1, необходимое для выполнения суточного расчетного объема грузопереработки, рассчитывается по формуле:
шт (6.1.1)
где Qр — расчетный суточный грузопоток с учетом «прямого» варианта переработки груза, т;
сут (6.1.2)
где nто-1, nто-2 — периодичность технического обслуживания соответственно ТО-1, ТО-2, сут.;
nр — периодичность текущего ремонта, мес.;
tто-1, tто-2, tр — продолжительность технического обслуживания соответственно ТО-1, ТО-2 и текущего ремонта, сут.
Tпр — продолжительность выходных и праздничных дней в течение года, Tпр = 60;
Пэкс — эксплуатационная производительность погрузочно-разгрузочной машины.
Эксплуатационная производительность — это количество груза, перерабатываемого ПРМ за один час с учетом внутрисменных технологических перерывов (прием-сдача смены, обед, перестановка вагонов, техническое обслуживание механизма и др.).
Эксплуатационная производительность ПРМ может быть принята по ЕНВ или рассчитана по формуле:
т/ч (6.1.3)
где Квр — коэффициент использования ПРМ по времени в течение 1часа, можно принять равным 0,7ч0,8;
Птех — техническая производительность погрузочно-разгрузочной машины.
Под технической производительностью понимают количество груза в тоннах, кубометрах, штуках и других единицах, которое может переработать ПРМ за один час непрерывной работы в условиях максимальной загрузки.
6.2 Потребность в погрузочно-разгрузочных машинах на основе технологии переработки грузопотоков
Поскольку продолжительность простоя подвижного состава под операциями выгрузки строго регламентируется, поэтому число ПРР машин на обработку в заданные сроки количества одновременно подаваемых вагонов определяется по формуле:
шт (6.2.1)
где Qп — количество груза в одной подаче, т;
т (6.2.2)
tгр — продолжительность погрузки или выгрузки одной подачи, ч;
ч (6.2.3)
где tпу — время, затрачиваемое на подачу и уборку вагонов одной подачи на перегрузочном фронте, ч. В работе принимаем tпу = 0,7ч1,0 ч;
tпер — время на обед, прием-сдачу смены и прочие технологические перерывы, tпер = 4ч5 ч.
Расчетное число ПРМ Zр, используемое в дальнейших расчетах, принять как максимальное из Z1 и Z2.
Расчет:
Для ковшовых элеваторов при переработке зерна техническая производительность была определена ранее:
принимаем 7 элеваторов Определим число ППР машин на обработку в заданные сроки количества одновременно подаваемых вагонов по прибытию и отправлению.
принимаем 7 элеваторов Для загрузочных бункеров при переработке зерна техническая производительность была определена ранее:
принимаем 1 загрузочный бункер Определим число ППР машин на обработку в заданные сроки количества одновременно подаваемых вагонов по прибытию и отправлению.
принимаем 2 загрузочных бункера
6.3 Техническое обслуживание и ремонт погрузочно-разгрузочных машин На железнодорожном транспорте для погрузочно-разгрузочных машин установлена система планово-предупредительного ремонта и технического обслуживания. Она представляет собой комплекс мероприятий предупредительного характера, проводимых периодически в плановом порядке и направленных на содержание машины в работоспособном состоянии.
Основным звеном в планово-предупредительной системе является техническое обслуживание, направленное на снижение интенсивности изнашивания деталей, выявление и предупреждение отказов и неисправностей путем своевременного выполнения контрольных, смазочных, крепежных, регулировочных и других работ.
Планово-предупредительной системой предусматривается ежесменное ЕО и периодическое технические обслуживания ТО-1 и ТО-2. Кроме того, два раза в год проводится сезонное техническое обслуживание СО с целью подготовки машины к эксплуатации в холодное и теплое время года.
Ремонт ПРМ предусматривает устранение всех неисправностей, возникших в процессе эксплуатации машины, и по объему разделяется на текущий ТР и капитальный КР.
Время работы машины в часах от момента ввода ее в эксплуатацию до первого капитального ремонта или между двумя капитальными ремонтами называется ремонтным циклом.
Структура ремонтного цикла — число периодических ремонтов в цикле, их вид и чередование.
Межремонтный период — время работы машины в часах между двумя очередными одноименными ремонтами или техническими обслуживаниями.
В данном разделе разрабатываем структуру ремонтного цикла для всех погрузочно-разгрузочных устройств элеватора — норий и отпускных бункеров с конвейерами. Периодичность и продолжительность ремонтов и технических обслуживаний приведена в прил. 5. Для конвейеров проводятся только ТО-2 и ТР.
График технических обслуживаний и ремонта ПРМ представлен на рис. 6.3.1.
Периодичность:
Элеватор (нория) nТО2 = 90 сут Отпускной бункер nТО2 = 90 сут
nТР = 12 мес с конвейерами nТР = 12 мес
Наименование груза и тип ПРМ | Прибытие, отправление | Номер ПРМ | Месяца и недели | Плановое выполнение | Фактическое выполнение | Экономия | |||||||||||||||||||||||
Январь Февраль Март … Декабрь | |||||||||||||||||||||||||||||
… | ТО1 | ТО2 | ТР | ТО1 | ТО2 | ТР | ТО1 | ТО2 | ТР | ||||||||||||||||||||
Элеватор (нория) | Отправление | ^ | ^ | … | ; | ; | ; | ; | |||||||||||||||||||||
^ | ^ | … | ^ | ; | ; | ; | ; | ||||||||||||||||||||||
^ | ^ | … | ; | ; | ; | ; | |||||||||||||||||||||||
^ | … | ; | ; | ; | ; | ||||||||||||||||||||||||
^ | … | ; | ; | ; | ; | ||||||||||||||||||||||||
^ | … | ; | ; | ; | ; | ||||||||||||||||||||||||
^ | ^ | … | ; | ; | ; | ; | |||||||||||||||||||||||
отпуск | прибытие | ^ | ^ | … | ^ | ; | ; | ; | ; | ||||||||||||||||||||
^ | ^ | … | ; | ; | ; | ; | |||||||||||||||||||||||
Рисунок 6.3.1. График технических обслуживаний и ремонта ПРМ: — ТО1; - ТО2; - ТР.
7. использование крупнотоннажных контейнеров для перевозки зерна В рамках правительственной программы по увеличению экспорта казахстанского зерна в страны ближнего и дальнего зарубежья железнодорожные перевозки приобретают все большую актуальность. Между тем существующий парк зерновозов сокращается из-за изношенности, наши возможности позволяют перевозить до трехсот тысяч тонн зерна в месяц, что не соответствует потребностям. Дефицит восполняем за счет вагонов из России и Украины, но зерновозы они предоставляют с опозданием.
Казалось, лучшим выходом из такой ситуации было бы приобретение новых вагонов для перевозки сыпучих грузов. Но так ли необходима покупка большего количества зерновозов и выгодны ли эти затраты государству?
Начнем с того, что вагоны-хопперы по три-четыре месяца в году находятся на путях отстоя, занимая станционные пути общей протяженностью 54 километра, проходят деповские и капитальные ремонты.
Средние затраты на деповский ремонт одного вагона-хоппера составляют от ста до двухсот тысяч тенге, со сменой колесных пар — 500 тысяч тенге, а стоимость капитального ремонта колеблется от 400 до 650 тысяч тенге. Периодичность деповского ремонта зерновозов в среднем — через два-два с половиной года, и годовые расходы только на него составляют около четырехсот миллионов тенге.
Потому, необходимо искать альтернативные способы перевозки зерна, муки и других сыпучих грузов, и таковым может стать использование крупнотоннажных контейнеров общего назначения. Они перевозятся на специальных платформах.
Крупнотоннажные контейнеры заводского изготовления не приспособлены для перевозки сыпучих грузов и жидкостей, но при соответствующем конструктивном добавлении и изменении вполне возможно выйти из положения.
Это стало бы эффективным шагом в обеспечении сельских товаропроизводителей железнодорожным транспортом, в снижении тарифов перевозки сельхозпродукции и тем самым дало новый импульс в развитии фермерских хозяйств. Прежде всего, потому что периодичность капитального ремонта контейнеров 2—2,3 года, причем ориентировочная стоимость капитального ремонта составляет 50 тысяч тенге, а расходы на текущий ремонт около трех тысяч тенге.
К тому же такие контейнеры-зерновозы не занимают станционных путей, и их можно складировать в несколько рядов-этажей на предназначенных для этой цели площадках.
Но для перевозки зерна необходимо произвести конструктивные изменения контейнеров, в частности сконструировать раму с соответствующим днищем для вилочных и клещевых захватов.
В пределах высоты рамы в днище контейнера врезаются выгрузочные люки. По такому же принципу на крыше контейнеров устраиваются загрузочные люки.
Контейнеры-зерновозы будут подъемно-переставными и могут перевозиться автомобильным, железнодорожным и морским транспортом. В период реализации зерна контейнер автотранспортом доставляется к месту загрузки, а затем — на станцию отправления для транспортировки по железной дороге. Такая операция позволяет максимально эффективно использовать железнодорожный подвижной состав, в данном случае платформы под контейнеры, так как они в очень короткое время высвобождаются под другие процессы, и простой вагонов сводится к минимуму.
Предварительный экономический анализ перевозки сыпучих грузов, в частности зерна, различными видами подвижных составов доказывает эффективность использования крупнотоннажных контейнеров. По результатам расчетов экономический эффект на один вагон при применении двадцатифутового контейнера-зерновоза вместо вагона-хоппера составляет шесть миллионов 863 тысячи тенге.
Если учесть, что по АО «НК «КТЖ» задействованы 5249 единицы вагонов-хопперов под зерно, то дополнение их контейнерами-зерновозами дает экономический эффект около четырех миллиардов 470 миллионов тенге.
Благодаря простоте обращения с контейнерами-зерновозами погрузку и выгрузку зерна иногда можно осуществлять силами грузополучателей и грузоотправителей непосредственно на их предприятиях. Упрощается также доставка от двери до двери в тех случаях, когда традиционные способы перевозки вагонами-хопперами для перевозки зерна требуют наличия подъездных путей, хранилищ, грузоподъемных устройств.
Контейнеры-зерновозы оптимальны для смешанных перевозок, так как их легко перегружать с одних транспортных средств на другие. Клиенты имеют возможность покупать или арендовать контейнеры-зерновозы с целью их одноразового или многоразового использования для погрузки, хранения (не занимая железнодорожных путей) или перевозки зерна.
Рисунок 7.1. Контейнер специализированный под перевозку сыпучих грузов Таблица 7.1. Технико-эксплуатационные характеристики контейнеров
Масса: | ||
максимальная масса брутто | 24 000 кг | |
масса тары | 2 720 кг | |
Размеры внутренние: | ||
длина | 5 838 мм | |
ширина | 2 340 мм | |
высота | 2 314 мм | |
внутренний объем (номинальный) | 31,7 м³ | |
Размеры габаритные: | ||
длина | 6 058 мм | |
ширина | 2 438 мм | |
высота | 2 591 мм | |
Размеры дверного проема: | ||
ширина | 2 318 мм | |
высота | 2 282 мм | |
Размеры загрузочного люка: | ||
ширина | 506 мм | |
высота | 506 мм | |
Размеры разгрузочного люка: | ||
ширина | 1 954 мм | |
высота | 600 мм | |
Материал: | ||
каркасных элементов | сталь 09Г2С | |
панелей боковых, торцевых стенок | сталь 09Г2 | |
панелей крыши | сталь 08ПС | |
Прочее: | ||
диапазон предельных температур эксплуатации | от -50оС до +70оС | |
максимальная нагрузка на одну стойку при штабелировании | 848 кН | |
вентиляционное устройство | лабиринтного типа | |
настил пола | стальной плоский или рифленый лист толщиной 4 мм (многослойная фанера) | |
Конструкция контейнера обеспечивает его светои водонепроницаемость | ||
Дверь: торцевая двухстворчатая с резиновым уплотнением по периметру | ||
Люки: три загрузочных и разгрузочный с резиновым уплотнением по периметру | ||
7.1 Перевозки сыпучих грузов с использованием мягких большегрузных контейнеров (до 14тн) В 2008 году ГК «САННА-ЛИТЕР» внедрила уникальную технологию перевозки сыпучих и навальных грузов в мягких большегрузных контейнерах (МК). Контейнер МК удовлетворяет всем требованиям перевозок автомобильным, железнодорожным и водным транспортом. Он удобен для перевозки всех видов сыпучих грузов, в частности, зерна. Хранение грузов в МК сохраняет их физико-химические свойства.
Рисунок 7.2. Мягкий сельскохозяйственный контейнер Доставка/возврат пустых контейнеров к месту погрузки производится в стандартных ж/д контейнерах:
в 20-ти тонный входит 125 шт, в 40-ка тонный входит 270 шт, в авто/полуприцеп (86м3) входит 285 шт.
Транспортировка груженых контейнеров МК с грузом легко размещается в полувагоне (5шт.), в грузовой автомашине в зависимости от веса МК (1−5шт.), и не требует специального крепления.
В автомобильном грузовом транспорте перевозятся без какого-либо специального крепления.
В железнодорожных полувагонах, во избежание порывов от соприкосновения МК с неровностями и выступающими частями стенок полувагона, на МК рекомендуется нашивать листы (1,5 м х 1,5м) обрезиненной ткани или прокладывать места соприкосновения, например, транспортерной лентой.
Время погрузки-выгрузки 1-го вагона составляет 15−20 минут. Зачистки полувагонов не требуется.
Для перевозки МК могут использоваться вагоны из-под любых грузов, в том числе и отбракованные другими грузоотправителями, например с дырами в стенках и полувагона.
Хранение на складских площадках.
Складирование МК допускается на открытых площадках в 5 ярусов (высота хранения составляет в этом случае около 14м). При этом нагрузка на площадку составляет 15,5−16 т/м2. При высоте в 4 яруса нагрузка на 1 м2 составляет 12,4 т. Площадь, которую занимает МК-14−10 на площадке складирования, составляет — 4,52 м2, высота при 100% загрузке — 2,8 м. Допускается складирование в 6 ярусов при высоте в 17 м.
В случае складирования в 6 ярусов, на 1 м2 возможно складирование до 24 м3 сыпучих грузов или до 30 т. При складировании в 2 яруса на 1 м2 складируется 24 м3 груза до 8 т.
Складская площадка (бетон, асфальт, гравий, земля) должны быть ровной, не засоренной острыми предметами.
Загрузка контейнера производится на элеваторе у отправителя.
Если на элеваторе предусмотрена загрузка в ж/д вагон, то монтируется дополнительное грузоподъемное устройство (14 т) под одним из накопительных загрузочных бункеров.
Выгрузка груза из МК производится через разгрузочный узел. Разгрузочный узел состоит из двух блоков, цилиндрической формы (D=80см, длина выпускной трубы L-1,3м). Конструкция позволяет выгружать сыпучие грузы в специальные автомобильные цистерны, ж/дорожные вагоны «хопры», в бункеры и т. п. При необходимости остановки высыпания или дозирования груза используется специальное навесное устройство, перекрывающее выгрузную мягкую трубу.
Время раскрытия разгрузочного узла 5−7 секунд.
Описание контейнера:
Грузоподъемность — до 14 т.
Полезный объем — 12−13 м3,
Диаметр — 2400−2450 мм,
Высота при 100% загрузке — 2800 мм, Объем порожнего МК в свернутом (транспортировочном) виде — 0.3 м3,
Вес — 70−75кг.
Время загрузки в 14-ти тонного контейнера с учетом всех операций — около 8−10 минут.
Для сравнения время загрузки 12−14 т сыпучих грузов в 1 биг-бэг (1,5−2 т) — 30−45мин. Время выгрузки сыпучих грузов из МК составляет около 30сек., например, цемента- 28−35 секунд.
Применение МК-14?10 при транспортировке позволяет:
— минимизировать потери при погрузке, выгрузке, перегрузке груза;
— исключить контакт груза с внешней средой, а также предохранять от реакции с влагой, сохранять груз в неизменном состоянии на протяжении всей доставки;
— решить проблему выгрузки практически в любом месте: в технологический транспорт завода, на складе, в технологический процесс и т. д.;
— складировать груз на открытых площадках накопления при температуре от — 50 до + 60єС;
— уменьшить время выгрузки/загрузки груза;
— предохранять транспортные средства от повреждений, вызванных соприкосновением с химически активными веществами;
— на железнодорожном транспорте зерно перевозится в специализированном подвижном составе — вагонах — зерновозах. При перевозках грузов в МК используются универсальные полувагоны (открытые), что значительно дешевле;
— на автомобильном транспорте — часть сыпучих грузов перевозится в специализированных прицепах. При перевозках в МК возможно использование универсальных прицепов, что значительно удешевляет перевозку и открывает рынок универсальных машин.
Основными преимуществами мягких контейнеров перед другими видами тары является:
· Низкая стоимость упаковки;
· Небольшой вес и объем тары относительно единицы продукта;
· Высокая универсальность, позволяющая использовать МКР для транспортирования и хранения, самых различных порошкообразных и гранулированных материалов, включая пищевые продукты;
· Герметичность упаковки. Отсутствие потерь материала или ухудшения качества продукта на всех этапах обращения;
· Упрощение погрузочно-разгрузочных работ при заполнении, хранении, растаривании и транспортировании. Возможность использования неспециализированных транспортных средств и грузоподъемных механизмов;
· Экологическая безопасность, возможность переработки и повторного использования;
· Разнообразные варианты конструкционного исполнения, учитывающие особенность транспортируемого материала.
Однако для того чтобы преимущества мягких контейнеров были реализованы в полном объеме, на предприятии, использующем данный вид упаковки необходимы средства комплексной механизации погрузочно-разгрузочных работ, а также операции по разгрузки тары. И если для транспортирования мягких контейнеров в основном применяется универсальная техника (например, вилочные автопогрузчики, штабелеры и т. д), то для растаривания МКР, должны использоваться специальные устройства, позволяющие быстро и безопасно разгрузить тару, а затем выдать материал в непрерывном, либо цикличном режиме. При этом от того насколько эффективно работает пост растаривания МКР, зависит общая производительность технологической линии, а также условия работы персонала данного предприятия.
Правильно выбранная схема работы с мягкими контейнерами на производстве, включающая в себя: промежуточное хранение, подвоз тары на пост растаривания, разгрузку МКР и непосредственно выдачу материала, позволяет наиболее эффективно распорядиться теми преимуществами, которые предоставляет самая современная технология упаковки и транспортирования порошкообразных, зернистых и кусковых материалов.
Рисунок 7.3. Загрузка мягкого контейнера
На настоящий момент работают несколько схем загрузки мягких специализированных контейнеров МК-14−10.
Узел загрузки МК-14−10 размещен непосредственно в месте отгрузки продукции железнодорожным транспортом.
Загрузка МК-14−10 производится следующим образом:
— порожние МК-14−10 до начала загрузки подаются в полувагон по 5 штук на вагон;
— вагон подается под силос;
— траверса грузоподъемного механизма опускается в вагон;
— МК-14−10 разворачивается и зацепляется за траверсу;
— траверса поднимается вверх к загрузочной горловине силоса. Дно МК-14−10 оторвано от земли;
— загрузочные горловины МК-14−10 и силоса совмещаются;
— начинается погрузка, по мере загрузки МК-14−10 осаживается и ставится по центру вагона;
— по окончанию загрузки загрузочная горловина МК-14−10 отцепляется, траверса отцепляется, вагон перемещается на 1,5 метра для загрузки следующего МК-14−10.
Время загрузки пяти МК-14−10 или одного вагона — 35 -45 минут.
Норма погрузки до 2000 тн в сутки с одного узла.
При перевозках железнодорожным транспортом используются открытые полувагоны. Во избежание порывов от соприкосновения МК с неровностями и выступающими частями кузова вагона, на МК нашиваются листы (1,5 м х 1,5 м) обрезиненной ткани. Максимальное расстояние, на которое были транспортированы МК, составило 2674 км по маршруту Пермь-Красноярск, время в пути — 8 суток. Потери груза (глинозем — текучесть сравнима с текучестью воды) из-за порывов упаковки составили около 0,03%. При железнодорожной перевозке менее текучих продуктов в случае возникновения порывов потери груза свелись бы к «0». Время погрузки вагона с площадки накопления или выгрузки из вагона на складскую площадку — 15 — 20 минут. Зачистки полувагонов не требуется. Для перевозки грузов в МК могут использоваться вагоны из-под любых грузов и отбракованные другими грузоотправителями (с отверстиями в кузове вагона, неисправными люковыми замками и др.)
Рисунок 7.4. Загрузка МК в полувагоны
При перевозке грузов в МК обеспечивается сохранность полувагона, особенно при проведении разгрузочных работ грейфером в портах, нет просыпей (потерь) груза на верхнее строение пути и стрелки (автоматику). За счет быстрого времени разгрузки/погрузки и отсутствия потерь времени на зачистку и сдачу вагонов после выгрузки на железной дороге значительно повышается оборот универсального подвижного состава.
Рисунок 7.5. Хранение МК в штабелях МК имеет разгрузочный узел, состоящий из двух частей. Основная часть имеет форму цилиндра диаметром 800 мм и длинной 1300 мм. Перед выгрузкой груза докер самостоятельно или при помощи крана раскрывает 2 замка (усилие раскрытия — 40 кг).
После раскрытия первого замка из дна контейнера выпадает закрытая выгрузочная труба, после раскрытия второго замка — выгрузочная труба раскрывается и груз начинает высыпаться из МК.
Время раскрытия МК — 5 секунд;
Время высыпания груза из МК — глинозема — 1,5 мин.; - аммофоса — 25с.
Возможна выгрузка груза в специализированный подвижной состав, в вагоны-зерновозы. При необходимости остановки высыпания груза из МК (дозирования) используется специальное навесное устройство, перекрывающее выгрузочную трубу.
Рисунок 7.6. Разгрузка мягких контейнеров Рисунок 7.7. Перегрузка мягких контейнеров в специальный подвижной состав.
8. Выполнение расчетов по сравнению вариантов технологических схем доставки зерна Определим эффективность варианта комплексной механизации погрузочно-разгрузочных работ с зерном при перевозке груза в специальном подвижном составе — зерновозах в сравнении с перевозками в крупнотоннажных контейнерах на платформах и с перевозками в мягких контейнерах в полувагонах.
Требуется:
1. Определить количество подвижного состава (вагонов, контейнеров) необходимого для выполнения суточного объёма перевозки грузов.
2. Определить оборот транспортной единицы (вагона, контейнера).
3. Определить рабочий парк подвижного состава (вагонов, локомотивов) необходимый для выполнения перевозок рассматриваемыми вариантами.
4. Определить затраты в подвижной состав по вариантам перевозки грузов на заданном направлении и на основе сравнения затрат выбрать выгодный вариант с учетом установки необходимого оборудования для загрузки контейнеров.
Количество ежесуточно отправляемых вагонов определяется по формуле:
ваг/сут. (8.1)
где: — годовой объём перевозок грузов, т;
q — грузоподъёмность подвижного состава (автомобилей, вагонов), т;
Кг — коэффициент использования грузоподъёмности.
Количество ежесуточно отправляемых контейнеров определяется по формуле:
конт/сутки (8.2)
где Рт20 — техническая норма загрузки двадцатитонных контейнеров.
Оборот транспортной единицы:
железнодорожного вагона:
сут. (8.3)
где: — расстояние перевозки груза (пробега транспортной единицы), км;
Vуч — участковая скорость движения грузовых поездов, км/ч;
tп, tв — время нахождения подвижного состава (вагонов) в пункте погрузки, выгрузки, ч.
Рабочий парк подвижного состава (вагонов, локомотивов) потребный для выполнения перевозки:
вагонов:
ваг. (8.4)
локомотивов:
лок. (8.5)
где: nв — количество ежесуточно отправленных соответственно вагонов;
mс — количество вагонов в составе поезда.
Количество потребного подвижного состава с учётом резерва:
ваг., лок. (8.6)
где Крез — коэффициент резерва подвижного состава.
Общая стоимость потребного подвижного состава по вариантам перевозок (капитальные вложения в подвижной состав):
железнодорожного подвижного состава:
(8.7)
где Ск, Св, Сл — соответственно стоимость контейнера, вагона, локомотива, тг.
На основании расчётов определяем выгодный вариант по затратам в подвижной состав:
при К3 > К1 < К2 выгодным является использование зерновозов;
при К3 > К1 > К2 выгодным является использование крупнотоннажных контейнеров на специализированных платформах;
при К2 > К1 > К3 выгодным является использование мягких крупнотоннажных контейнеров в полувагонах.
Расчет:
1 вариант Расстояние перевозки — 2025 километров.
2 вариант
3 вариант Принимая во внимание, что для загрузки мягких контейнеров на элеваторе необходимо монтировать дополнительное грузоподъемное устройство (14 т) под одним из накопительных загрузочных бункеров, стоимость устройства принимается равной 100 000 тенге.
Тогда
В результате получили:
К1 = 1315,6 млн. тенге К2 = 1382,76 млн. тенге К3 = 1107,2 млн. тенге К2 > К1 > К3, следовательно, выгодным является использование мягких крупнотоннажных контейнеров в полувагонах.
9. Технологический график работы средств механизации погрузки и выгрузки грузов Основными исходными данными для составления графика являются:
— выбранное время подачи вагонов к грузовым фронтам (желательно время подачи к началу смены и в обеденный перерыв);
— продолжительность работы автотранспорта по завозу и вывозу грузов со станции (как правило, в дневное время на протяжении 8−12 ч.);
— количество ПРМ и их часовая производительность Птех;
— число смен работы грузового пункта (в зависимости от грузооборота может работать в одну, две или три смены);
— объем перегрузки по «прямому» варианту (вагон — автомобиль, автомобиль — вагон).
Расчет:
1. Суточное отправление контейнеров = 291 конт.
2. Погрузка осуществляется из отпускных бункеров в количестве Zр=2.
3. Часовая производительность отпускного бункера составляет Птех=10 конт/ч.
4. Число подач е =2 принимается по заданию.
Построение графика начинается с определения количества контейнеров в одной подаче. Разобьем суточный контейнерооборот по отправлению равномерно на две подачи: 291=145+146 контейнеров.
Время работы бункера tпрм показывается на графике в отдельной горизонтальной строке. Все погрузочно-разгрузочные машины могут работать, как на одной, так и на разных операциях. Время работы отпускного бункера при погрузке со склада tпрм=145/10=14,5ч. Результаты расчетов для удобства сведем в табл. 9.1.
Таблица 9.1
Номер подачи | Количество контейнеров в одной подаче | Время работы отпускного бункера, ч | |
14,5 | |||
14,6 | |||
Рис. 9.1
10. Мероприятия по обеспечению безопасности труда и экологической безопасности
10.1 Утилизация твердых и жидких отходов Под утилизацией понимается использование отходов в качестве вторичного сырья, топлива, удобрений и других целей. При различных видах деятельности общества образуются отходы производства и отходы потребления.
Отходы производства-остатки сырья, материалов, полуфабрикатов, образующиеся при изготовлении продукции, выполнении работ и частично или полностью утратившие первоначальные потребительские свойства.
Отходы потребления — изделия и материалы, утратившие свои потребительские свойства в результате физического и морального износа.
Отходы производства и потребления называют вторичными материальными ресурсами. Вторичные ресурсы могут использоваться для производства новых видов продукции или для получения энергии.
Во всех случаях вторичные ресурсы подлежат утилизации, т. е. удалению из мест образования и накопления с целью последующего использования или захоронения. Чем больше отходов, тем выше себестоимость готовых изделий, тем больше вероятность загрязнения окружающей среды.
Проблема утилизации отходов существует и в нашей стране. Различные отрасли хозяйства, в том числе и железнодорожный транспорт, ежегодно утилизируют сотни миллионов тонн вторичного сырья. Комплексный характер функционирования железнодорожного транспорта и транспортного строительства обусловливает получение широкой номенклатуры отходов, которые подлежат переработке. Каждый вид отходов имеет специфические особенности, которые следует учитывать при разработке технологии и оборудования для их переработки. Каждое предприятие железнодорожного транспорта должно иметь классификаторы отходов. К классификационным признакам следует отнести место получения отходов, их фазовое состояние, номенклатуру, санитарно — гигиенические характеристики, накопление во времени. Отходы образуются на всех стадиях процесса изготовления готовой продукции — получение заготовок, их обработка, дефекация, комплектование, сборка, испытание, окраска и др. большое количество отходов образуется от вспомогательных и обслуживающих процессов и хозяйственно — бытовой деятельности предприятий. Учет отходов должен включать в себя следующие данные: место образования отходов; их количество и номенклатуру; пути движения; пункты складирования. Каждое предприятие обязано вести паспорт формирования отходов.
По фазовому состоянию отходы классифицируются на твердые, жидкие, газообразные и энергетические.
По санитарно — гигиеническим признакам отходы подразделяются на инертные, слаботоксичные растворимые в воде, слаботоксичные летучие, токсичные растворимые в воде, токсичные летучие, содержащие нефть (масло), органические легко разлагающиеся, фекалии, хозяйственно — бытовой мусор. Токсичные отходы имеют свою классификацию.
Номенклатура отходов зависит от вида сырья и готовой продукции. Твердые отходы включают в себя отходы черных и цветных металлов, резину, пластмассы, древесину, абразивы, шлак и золу, минеральные и органические вещества, хозяйственно — бытовой мусор. Жидкие отходы состоят из электролитов, охлаждающих, обезжиривающих и моющих растворов и др. газовые выбросы образуются от котельных, плавильного оборудования, вентиляционных систем. Энергетическими отходами следует считать тепло и различные виды излучений (шум, вибрация, магнитные и электрические поля, радиация).
Сбор вторичного сырья — очень трудоемкая операция. На сбор и вывоз отходов предприятия тратят до 8% стоимости готовой продукции. Эти расходы можно уменьшить, если наладить их переработку, которая позволяет получить большое количество ценных веществ, удобрений, топлива, металла, что экономит природные ресурсы. Использование отходов — одно из важнейших направлений повышения эффективности производства, снижения загрязнения окружающей среды, уменьшения расхода природных ресурсов на единицу выпускаемой продукции.
Доля металлических отходов в общем потреблении черных металлов составляет 21%, а доля вторичных ресурсов в производстве продукции — около 9%.
Важным направлением использования металлических отходов является изготовление из них не основной продукции и товаров широкого потребления. Средняя стоимость продукции, изготовленной из металлических отходов на предприятиях в десятки раз ниже, чем при изготовлении ее из стандартизированных металлов. На изготовление товаров народного потребления идет не более 15% отходов стального проката.
Основным способом переработки металлических отходов является их переплавка. Так, использование 1 т металлолома сберегает 2,5 т железной руды, 1 т кокса и 0,5 т известняка. При выплавке стали из металлолома на 40% снижается расход воды, на 70%расход электроэнергии, в 3 — 4 раза уменьшается загрязнение атмосферы. Стоимость выплавки 1 т металла из отходов производства в 15 — 25 раз ниже, чем из природного сырья.
Большие резервы по экономии природных ресурсов заложены в использовании деталей списанного подвижного состава и производственного оборудования. Списанное оборудование и подвижной состав подлежат разборке. Негодные данные идут в металлолом, годные поступают в оборотный фонд для ремонта подвижного состава и производственного оборудования.
Утилизация древесины. Обрезки, опилки, стружка древесины служат сырьем для изготовления фанеры, картона, оргалита.
Рисунок 9.1. способы утилизации отходов Использование древесных отходов позволяет экономить при изготовлении 1 м3 древесностружечных плит 3,6 м3. в последние время из отходов древесины изготовляются различные детали.
Технологический процесс изготовления изделий из отходов древесины включает в себя операции по сортировке отходов, их измельчению, приготовлению исходного сырья из древесной крошки, смолы и отвердителя. Утилизация отработанных масел. На предприятиях железнодорожного транспорта используется большое количество моторных, индустриальных, компрессорных и других масел, изготавливаемых из нефти. Важнейшим направлением снижения расхода масел на предприятиях железнодорожного транспорта является регенерация отработанных масел.
При регенерации производится отчистка отработанных масел от механических примесей отстаиванием, сепарированием, способами коагуляции, адсорбции, химической обработки, восстановление свойств путем введения различных добавок.
Утилизация смазывающе-охлаждающих жидкостей. Экономия расходов СОЖ обеспечивает сбережение ценных материалов. В составе СОЖ содержится до 5% минеральных масел. Одним из главных направлений экономии СОЖ является создание пунктов централизованного обеспечения СОЖ и оборудования для их очистки и регенерации. Очистка СОЖ от металлической стружки производится с помощью магнитных фильтров типа ФМ, а от абразивных частиц отстаиванием и фильтрованием. Восстановление первоначальных свойств СОЖ достигается регенерацией, которая включает их отчистку от механических примесей, восстановление свойств добавкой израсходованных компонентов.
Заключение
В результате выполненных расчетов в проекте:
— дана характеристика зерновых грузов;
— определены условия перевозки, погрузки выгрузки зерновых грузов;
— определены расчетные объемы работы грузовых пунктов;
— произведен выбор комплексной механизации погрузочно-разгрузочных работ грузовых пунктов;
— произведен расчет размеров складских сооружений и потребного количества погрузочно-разгрузочных механизмов;
— рассмотрены альтернативные способы погрузки и перевозки зерна с использованием крупнотоннажных контейнеров;
— определена эффективность варианта комплексной механизации погрузочно-разгрузочных работ с зерном при перевозке груза в специальном подвижном составе — зерновозах в сравнении с перевозками в крупнотоннажных контейнерах на платформах и с перевозками в мягких контейнерах в полувагонах и выбран оптимальный вариант, которым оказался вариант с использованием мягких крупнотоннажных контейнеров в полувагонах;
По завершении расчетов выполнен технологический график работы средств механизации погрузки и выгрузки зерна на элеваторе, что подтвердило эффективность выбранной схемы комплексной механизации погрузочно-разгрузочных работ контейнерного пункта.
По завершению всех расчетов проанализированы и предложены способы утилизации твердых и жидких отходов.
1. Антонеевич Э. Ф. Погрузо-разгрузочные работы. Справочник. М. Транспорт. 1972.-288 с.
2. Атамкулов Е. Д., Жангаскин К. К. Железнодорожный транспорт Казахстана: реструктуризация и пути интеграции в мировую экономику / Под ред. Р. К. Сатовой — Алматы: Экономика, 2003, 741 с.
3. Гриневич Г. П. Комплексная механизация и автоматизация погрузочно-разгрузочных работ на железнодорожном транспорте: Учебник для вузов ж. — д. транспорта — М: Транспорт, 1981 — 343 с.
4. Грузоведение, сохранность и крепление грузов. Под ред. А. А. Смехова М. Транспорт. 1987.-239 с.
5. Лощинин А. В. Охрана труда на железнодорожном транспорте: Справочная книга — М: Транспорт, 1977 — 448 с.
6. Мачульский И. И., Киреев В. С. Подъемно-транспортные и погрузочно-разгрузочные машины на железнодорожном транспорте: Учебник для вузов — М: Транспорт, 1989 — 319 с.
7. Падня В. А. Погрузочно-разгрузочные машины: Справочник — М: Транспорт, 1981 — 448 с.
8. Сибаров А. В. Охрана труда на железнодорожном транспорте: Учебник для вузов ж. — д. транспорта — М: Транспорт, 1981 — 287 с.
9. Смехов А. А., Управление грузовой и коммерческой работы на железно дорожном транспорте. М. Транспорт. 1990.
10. Методические указания к выполнению курсового проекта по дисциплине «Комплексная механизация и автоматизация погрузочно-разгрузочных, транспортных и складских работ», Кушукпаев Х. К., Алмата, 1987
11. Организация грузовой и коммерческой работы на железнодорожном транспорте. А. Т. Дерибас и др. М. Транспорт. 1980.-328 с.
12. Пакетные перевозки грузов. Под ред. П. К. Лемещука., М. Транспорт. 1972.-288 с.
13. Правила перевозок грузов, М: Транспорт, 1985 — 384 с
14. Правила перевозки грузов. Ч. 1. С изменениями и дополнениями по состоянию на 01.01.83 г.
15. Правила перевозок грузов. М. Транспорт. 1985.
16. Тарифное руководство № 1 часть 1, 2.
17. Тарифное руководство № 4 кн. 1, 2, 3.
18. Экономика железнодорожного транспорта: Учебник для ВУЗов И. В. Белов, В. Г. Галамбурда и др.; Под ред. И. В. Белова. — М.: Транспорт, 1989. — 351 с.
19. Яловой Ю. Г., Катляров А. М. Организация перевозок на промышленном транспорте: — Минск: Выш. школа, 1982 — 248 с.