Ящичная солодовня
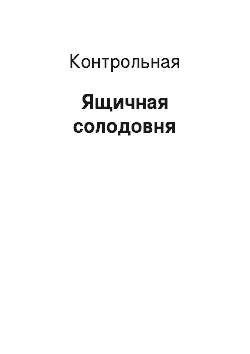
Солодорастильные аппараты барабанного типа. Представляют собой горизонтальный стальной цилиндрический корпус, установленный на двух парах опорных роликов. Проращиваемое зерно продувают кондиционированным воздухом, а перемешивают в результате медленного вращения барабана. Барабанные солодовни бывают закрытые и открытые. Особенностью закрытых барабанов — полная изолированность проращиваемого зерна… Читать ещё >
Ящичная солодовня (реферат, курсовая, диплом, контрольная)
Контрольная работа № 1
по технологическому оборудованию отрасли Оглавление
1. Введение
2. Исходные данные
2.1 Каковы преимущества и недостатки существующих солодовен?
2.2 Найти площадь сит ящичной пневматической солодовни
2.3 Рассчитать расход кондиционированного воздуха на проветривание солода
2.4 Определить тип варочного агрегата непрерывного действия, привести техническую характеристику агрегата и схему разваривания
2.5. Рассчитать вместимость и геометрические размеры разварника непрерывного действия
2.6 Рассчитать расход пара на разваривание крахмалосодержащего сырья
2.7 Каковы устройство и работа аппаратов полунепрерывного разваривания?
Описание, схема, принцип действия оборудования
3. Список литературы
1.
Введение
Бродильная промышленность — одна из старейших отраслей промышленности в России. Анализ современного технического уровня предприятий бродильной промышленности показывает, что его совершенствование осуществляется в направлении повышения единичной мощности, сокращения вспомогательных операций, снижения материалои энергоемкости, повышения уровня механизации и автоматизации, улучшения санитарной обработки.
Модернизация предприятий бродильной промышленности, строительство наряду с крупными предприятиями мини заводов ведет к расширению заводов и выпускаемому ассортименту бродильной промышленности и требует гибкой организации проектировочных работ с учетом достижений мировой практики, внедрения новых технологических процессов и оборудования, ликвидации диспропорций в цехах, повышения уровня механизации транспортно-складских работ. На солодовенных и пивоваренных заводах устанавливаются поточные механизированные линии.
В последнее время широкое распространение получили прогрессивно развивающиеся мини пивоварни и мини пивзаводы, на которых применяются новые методы замачивания и сусловарения сырья. Успешно эксплуатируются цилиндрические бродильные аппараты для ускоренного брожения и дображивания пива, диатомные фильтры и гидроциклонные аппараты для осветления горячего сусла и пива. Появился целый ряд дополнительных операций: карбонизация, стабилизация пива, а также утилизация вторичных материальных ресурсов.
В том числе появились новые разработки по технологическому оборудованию, совмещение функций и конструкций некоторых аппаратов, повышению их производительности, уменьшение энергозатрат на проводимые процессы, сокращение производственных площадей на единицу занимаемого оборудования, вырабатываются усовершенствованные пути повышения эффективности обработки сырья.
Перед всей пивоваренной промышленностью, в частности, минипивоваренной промышленностью стоят задачи по внедрению новой, более прогрессивной техники и технологии, обеспечивающих полное и комплексное использование сырья, высокоэффективных машин и аппаратов непрерывного действия, создающих возможность интенсифицировать и автоматизировать процессы и внедрять АСУТП. При этом в условиях рыночной экономики важно обеспечить их конкурентоспособность при борьбе за рынок с зарубежными партнерами.
Особой задачей, стоящей перед минипивоварнями и минипивзаводами, является проблема утилизации отходов производства, в частности, лагерного осадка, представляющего собой остающиеся в лагерном танке дрожжи. Решение проблемы утилизации отходов позволит улучшить экологическую обстановку, а также позволит добиться определённого экономического эффекта, так как утилизируемые дрожжи содержат определённую долю товарного продукта, т. е. позволит сократить потери продукта.
2. Исходные данные Мощность спирт — завода, дал/ сут. 1600
Температура развариваемой массы, °С 143
Плотность развариваемой массы, кг/ 1220
2.1 Каковы преимущества и недостатки существующих солодовен?
Ответ.
Зерно проращивают в специальных помещениях называемых солодовнями. Солодоращение можно осуществлять в солодовнях следующего типа:
Токовая солодовня. Представляет собой помещение, в котором расположен пол «ток», на котором располагают зерно. Проращивание ведут 7−8 суток. Большим минусом таких солодовен является использование ручного труда и отсутствие механизации.
Ящичная солодовня. Ящичная солодовня состоит из нескольких длинных открытых солодорастильных ящиков, разделенных между собой стенкой. Солодорастильный ящик в плане имеет прямоугольную форму. Основное дно сделано с небольшим уклоном для стока воды. На второе (ситчатое) дно, укладывают замоченное зерно. Через подситовое пространство в слой зерна подают кондиционированный воздух. На стенках ящика установлен передвижной солодоворошитель с вертикальными шнеками. Замоченное зерно вместе с водой подают из замочного аппарата в ящик и с помощью ворошителя распределяют на сите ровным слоем высотой 0,6−0,85 м. Продолжительность проращивания составляет 7−8 суток. В отличие от токовых солодовен ящичные механизированы, что облегчает работу. Свежепроросший солод, выращиваемый в ящичной солодовне, по своему химическому составу близок к токовому. В результате уменьшение потерь на дыхание и развитие ростков выход солода и его экстрактивность примерно на 1 процент выше, чем выход солода, приготовленного в токовой солодовне.
Этот тип солодовни в последние десятилетия приобретает наибольшее распространение. Современные солодовни — типа «передвижная грядка» и башенного типа — основаны на принципе ящичной солодовни, которая получила название по имени ее изобретателя — Saladin. Работа таких установок такая же, как и в простых ящичных солодовнях. Аэрация в старых установках осуществлялась с помощью вытяжных вентиляторов, которые с перерывами подавали воздух в материал через общую увлажнительную установку. В современных солодорастильных барабанах ящичного типа системы Saladin каждая грядка оснащается своим напорным вентилятором с агрегатом для увлажнения и охлаждения, причем аэрация осуществляется непрерывно. В аппаратах системы Saladin грядки легкодоступны для осмотра и контроля. В них благодаря равномерности слоя материала обеспечивается и равномерная вентиляция.
Солодовня передвижная грядка. В солодовне с передвижной грядкой, отличающейся от обычной ящичной солодовни только наличием ковшового ворошителя вместо шнекового, проращиваемое зерно постепенно перебрасывается ковшовым ворошителем вдоль ящика от места загрузки зерна до места выгрузки солода. Солодовня с передвижной грядкой представляет собой длинный ящик, в котором подситовое пространство разделено перегородками на секции, число которых равно числу суток ращения солода. Замоченное зерно из чанов выгружается на площадь сита. Перемещение зерна на сита последующих секций и его ворошение проводятся через каждые 12 часов при помощи ковшового ворошителя, установленного по ширине ящика передвижной грядки. На освободившуюся площадь сита вновь загружается замоченное зерно. Масса готового свежепроросшего солода выгружается в бункер, а из него подаётся на сушку.
К солодовням передвижная грядка можно отнести установку с солодорастильными аппаратами «Lausmann». Аппарат для проращивания Lausmann предусматривает ежедневное перемещение проращиваемого зерна в следующий ящик.
Ящики квадратного или прямоугольного сечения располагают в ряд, непосредственно друг около друга. Поднимают и опускают их с помощью подъемного устройства обычной конструкции, регулируя высоту пространства под ящиками. При максимальном подъеме сито достигает края ящика для проращивания, чем обеспечивается его полная очистка. Ворошение осуществляется при подъеме сита, в результате чего часть проращиваемого материала пересыпается через разделительную стенку двух ящиков и перемещается с помощью ворошителя особой конструкции в следующую секцию ящика или в сушилку. Ворошитель состоит из системы скребков и возвышается над двумя ящиками, благодаря чему можно полностью разровнять солод в следующем ящике. За последним ящиком располагается либо встроенная сушилка, либо бункер для транспортирования свежепроросшего солода. Поскольку сушилка требует большой площади, ворошитель должен исполнять и функцию по выгрузке из нее солода.
Солодорастильные аппараты барабанного типа. Представляют собой горизонтальный стальной цилиндрический корпус, установленный на двух парах опорных роликов. Проращиваемое зерно продувают кондиционированным воздухом, а перемешивают в результате медленного вращения барабана. Барабанные солодовни бывают закрытые и открытые. Особенностью закрытых барабанов — полная изолированность проращиваемого зерна от внешних условий. Существует два типа закрытых барабанов: с плоским ситом и с ситчатыми трубами. Барабанные солодовни с плоским ситом представляют собой горизонтальный цилиндрический корпус, внутри аппарата закреплено плоское сито, на котором равномерно загружают замоченное зерно. Высота слоя зерна на ситчатом днище может достигать 1 м. Ворошение два раза в сутки, при этом барабан осуществляет 1 об. /45'. Барабанные солодовни с ситчатыми трубами во многом устроены идентично вышеописанному аппарату, но в центре барабана закреплена ситчатая труба. Кондиционированный воздух нагнетается или в подситовое пространство или в ситчатую трубу, в зависимости от типа солодовни. Качество солода, выращенного в такой солодовне, хорошее. Он достаточно растворен и имеет свежий вид и чистый солодовый запах.
Примером такой солодовни можно представить солодовню барабанного типа фирмы «Galland». Проращивание в ней ведется при местной аэрации и кондиционировании, а также с применением рециркуляционного воздуха.
Шахтные солодорастильные установки. Применяют в солодовнях непрерывного действия. Основу способа составляют оросительное замачивание ячменя и непрерывное проращивание ячменя в газовой среде с повышенным содержанием СО2. Такой способ орошения ячменя дает возможность вымывать диоксид углерода из межзернового пространства и поддерживать одинаковые условия замачивания по всему объему замочной камеры. После непрерывного замачивания ячмень перекачивают гидротранспортом в аппарат для удаления поверхностной влаги, где оно содержится около 4 часов, после чего его направляют в верхнюю растильную камеру шахты. Общая продолжительность проращивания составляет 135 часов. Свежепроросший солод выгружают из нижней части растильной камеры в приемный бункер, из которого конвейером и норией транспортируют на сушку.
Солодорастильные аппараты круглого сечения. Конструктивные особенности солодорастильных аппаратов круглого сечения делают их наиболее предпочтительными при использовании в современных солодовнях башенного типа, где их размещают по вертикали один под другим. Но в последнее время такие аппараты можно встретить и в традиционной компоновке солодовни, где все солодорастильные аппараты размещены на одном уровне. Изготавливают два вида таких аппаратов: со стационарным и вращающимся днищем. Их оснащают шнековыми ворошителями, поэтому принцип их работы (за исключением загрузки и выгрузки) аналогичен ящичным солодовням. Ситчатое днище аппарата имеет кольцевую форму, поскольку в его центре расположен поворотный бункер, через который осуществляют выгрузку солода. Над ситчатым днищем расположен ворошитель карусельного типа, который может вращаться вокруг центральной оси в разных направлениях. Помимо ворошения с его помощью осуществляют выгрузку свежепроросшего солода и увлажнение зерна в процессе проращивания. Для увлажнения зерна над вертикальным шнеком установлены распылительные форсунки, к которым подведена вода. В процессе солодоращения зерно продувают кондиционированным воздухом, нагнетаемым вентилятором в подситовое пространство.
Солодорастильные аппараты с подвижным днищем применяют в солодовнях повышенной мощности. Единовременная загрузка в них может достигать 700 тонн. В этом случае аппарат оснащают конструкцией, внутри которой обычно монтируют трубы для самотечного перемещения зерна сверху вниз. Такие солодорастильные аппараты применяют реже, так как они сложнее по конструкции и дороже в изготовление, более металлоемки.
Непрерывные системы солодоращения. Система Domalt. Солодовни типа передвижная грячка и башенного типа являются установками полунепрерывного действия. Ячмень замачивается в одном месте далее поступает в солодорастильную установку, а затем направляется в солодосушилку, обычно непосредственно примыкающую к ней. Продолжительность пребывания в отдельных аппаратах или на участках ситовой поверхности составляет в зависимости от особенностей технологии 9,12 или 24 ч. В качестве примера непрерывнодействующей солодовни можно рассмотреть систему Domalt. Ячмень смешивается с водой на входе с помощью поднимающегося моющего шнека. После прохода через шнек (в течение около 100 мин) зерно поступает на подвижную ситовую поверхность, выполненную из сит или пластмассовых полотен, разделяется и распределяется по высоте. Скорость перемещения ситовой поверхности 0,7 м/ч, высота слоя солода около 0,9 м. Во время прохода через первый участок ситовой поверхности ячмень орошается и достигает влажности, оптимальной для проращивания. На определенных расстояниях установлены простые ворошители, обеспечивающие достаточное разрыхление слоя прорастающего зерна. По достижении максимальной влажности лишнюю воду из зерна удаляют. Температуру проращивания регулируют на каждом участке подачей влажного воздуха с регулируемой температурой. На заключительном участке за солодорастильным отделением располагается солодосушилка непрерывного действия. Высушенный солод охлаждают и направляют в росткоотбойную машину.
Непрерывно действующая установка позволяет увязать продолжительность проращивания с характеристиками той или иной партии ячменя. Так, период замачивания и проращивания двухрядных ячменей длится около 100−110 ч, а у многорядных — 70−80 ч. По сравнению с обычными такая установка обеспечивает существенное сокращение продолжительности солодоращения за счет ускоренного проращивания при более низкой влажности и непрерывного перехода от одной стадии проращивания к другой, однако максимальная влажность здесь, как правило, выше, чем, например, в обычной ящичной солодовне. Все эти факторы ускоряют прохождение цитолиза и активизируют действие других групп ферментов, что проявляется также в увеличении объема зерна после сушки.
Подобная система дает возможность применить полностью автоматическое управление с небольшими трудозатратами и сокращением расхода воды.
В последнее время среди вновь построенных солодовен преобладают солодовни башенного типа, характеризующиеся более высокой технологической эффективностью и экономичностью.
В солодовнях башенного типа оборудование для замачивания, проращивания и сушки размещают ярусами — одно под другим, в основной производственной башне цилиндрической формы, в которой размещают технологическое оборудование. В башенных солодовнях используют оборудование такое, как замочные аппараты цилиндроконической формы и с плоским днищем, солодорастильные аппараты и солодосушилки круглого сечения.
К основным преимуществам башенных солодовен следует отнести:
ь компактность;
ь снижение строительных затрат;
ь компактность, и, следовательно, меньшая потребность в площади застройки;
ь снижение затрат энергии на охлаждение и обогрев помещений;
ь сокращение тепловых потерь за счёт меньшей площади поверхности стен и крыш;
ь снижение затрат на техническое оснащение солодовни за счёт ненадобности транспортных систем для замоченного и свежепроросшего солода;
ь упрощение транспортировки замоченного ячменя и свежепроросшего солода под собственным весом под собственным весом по центральной вертикальной трубе;
ь возможность герметизации отделения солодоращения, что позволяет управлять солодоращением каждой порции зерна индивидуально, например, в начнльной период проращивания можно работать с большим расходом свежего воздуха, содержащим больше кислорода, а в заключительный период с накоплением углекислого газа способствует снижению потерь сухих растворённых веществ солода.
К преимуществам солодовен из металлоконструкций, по сравнению с солодовнями из монолитного железобетона, относят:
ь меньшая трудоёмкость, благодаря простоте сборки и поставкам на строительную площадку готовых узлов каркаса и обшивки;
ь сокращение сроков строительства;
ь исключение условий для развития микроорганизмов, поскольку на металлических поверхностях в процессе эксплуатации не образуется микротрещин;
ь увеличение сроков эксплуатации солодвен, поскольку металлоконструкции более устойчивы в эксплуатации при повышенной влажности и температурных перепадах.
2.2 Найти площадь сит ящичной пневматической солодовни солод проветривание пар пневматический Ответ.
Для расчета возьмем пневматическую солодовню с передвижной грядкой и ковшовым ворошителем.
Расход зерна на солод согласно технологическим требованиям составляет 16% от массы крахмала в зерне, поступающем на разваривание.
Определим площадь сит пневматической солодовни для спиртового завода производительностью 1600 дал/сут.
Определим общее количество зерна на приготовление солода по формуле:
= * 0,16 = * 0,16 = 3,88 т, где С — суточная производительность завода по спирту, С = 1600 дал/сут;
b — выход спирта из 1 т крахмала в зерне, поступившем на разваривание ,
b = 66 дал/сут.
С учетом возможного поступления на солод зерна с пониженной прорастаемостью принимаем = 3,88 т, из них ячмень составляет
= 0,7 * = 0,7 * 3,88 = 2,72 т/сут Для выращивания ячменного солода выделяем два ящика, следовательно, в каждый ящик ежесуточно поступает 1,36 т ячменя, считая на начальную стадию (до замачивания).
При замачивании объем ячменя увеличивается на 45%, следовательно, объем зерна, поступающего на первую секцию сита:
= * 1,45 = *1,45 = 3,03 ,
где — насыпная масса ячменя, = 0,65 /.
Высоту слоя зерна на первой секции ящика принимаем 0,5 м.
Потребная площадь сит для первого ращения:
F = = = 6,06 .
Для типового ковшового ворошителя ВВС 2,3−75−90 ширина рабочего ящика должна быть 2,3 м, тогда длина ящика, занятого зерном в первые сутки ращения составит:
? = = = 2,63 м.
Ворошитель ВВС 2,3 — 75 — 90 за один может переместить солод на 0,9 м.
Для перемещения солода на 2,63 м ежесуточно ворошитель должен делать 3 подхода, т. е. ворошить зерно 3 раза в сутки.
Для 8 — суточного ращения солода необходимо, чтобы каждый ящик имел общую длину:
L = 2,63 * 8 + 0,9 = 21,94 м.
Площадь сит одного ящика:
= 21,94 * 2.3 = 50,5
Площадь сит пневматической солодовни:
F = 50,5 *2 = 101
2.3 Рассчитать расход кондиционированного воздуха на проветривание солода Расчет.
Рассчитаем оптимальный расход воздуха для проветривания солода в ящичной пневматической солодовне, состоящей из 2 — х ящиков, если продолжительность проветривания ячменя = 6,5 сут, продолжительность ращения солода = 8 сут, а в каждый ящик загружается = 1360 кг очищенного ячменя.
Площадь поверхности сита в ящике F= 50,5
Параметры воздуха следующие:
Кондиционированный воздух при = 12 = 98%; = 0,0089 кг/кг Отработанный воздух при = 16; = 86%; = 0,1 159 кг/кг Потери сухих веществ при солодоращении на 1 кг очищенного ячменя S = 0,045 кг.
Причем при влажности замоченного зерна = 45%, = 1,5*, а при влажности свежепроросшего солода = 43%, = 1,42* Gяч.
Удельные теплоемкости влажных продуктов рассчитывают как средневзвешенную величину удельных теплоемкостей сухих веществ и воды ;
СИ:
=1,423 кДж/(кг * К), = 1423 Дж/(кг * К);
=4,19 кДж/(кг * К), = 4190 Дж/(кг * К)
= ((100 —)+) / 100 = 78 265 + 188 550 / 100 = 2 668 Дж/(кг * К);
= ((100 —) +) / 100 = (1423 (100 — 43) + 4190 * 43) / 100 = 81 111 + 180 170 / 100 = 2 613 Дж/ (кг * К) Принимаем температуру замоченного ячменя при загрузке = 11,
а свежепроросшего солода при выгрузке = 16 и находим соответствующие количества теплоты:
= 1,51 * * * t = 1,51 * 1360 * 2 668 * 11 = 60 269 052 Дж;
= 1,42 * * * t = 1,42 * 1360 * 2 613 * 16 = 80 739 609 Дж;
= * qS = 1360 * 17 982 000 * 0,045 = 1 100 498 400 Дж, где q — удельное количество теплоты, выделяемой при проращивании зерна на 1 кг потерь сухих веществ, и равное 17 982 000 Дж/кг.
Из потерь теплоты в окружающую среду учитываются только потери с поверхности солода, т.к. потери теплоты через стенки ящика из-за малого перепада температур очень незначительны. Среднюю температуру солода в ящике за все время проращивания принимаем равной =15, а в помещении солодовни =13, тогда потери теплоты:
= Ft= -) = 25 120 * 50,5 * (15 — 13) * 192= 487 127 040 Дж, где = 24 * 8 = 192 ч,
— коэффициент теплоотдачи от поверхности солода окружающему воздуху,
= 25 120 Дж/ (* ч * К).
Удельная энтальпия кондиционированного воздуха:
= + + = 1005 * 12 + 1880 * 12 * 0,0089 * 0,98 +2 500 000 * 0,0089 * 0,98 = 12 060 + 196,77 + 21 805 = 34 062 Дж/кг, где — удельная теплоемкость абсолютно сухого воздуха, = 1 005 Дж/(кг * К);
— удельная теплоемкость водяного пара, = 1 880 Дж/(кг * К);
— удельная теплоемкость парообразования при 0, = 2 500 000 Дж/кг Удельная энтальпия отработанного воздуха:
= + + = 1005 * 16 + 1880 * 16 * 0,1 159 * 0,86 + 2 500 000 * 0,1 159 * 0,86 = 16 080 + 299,82 + 24 918,5 = 41 298,3 Дж/кг Поскольку разность энтальпий в основном оказывает наибольшее влияние на расход воздуха, принимаем, что для оптимального расхода воздуха
— = ,
где = 6,5 кДж/кг. Если —, то температуру кондиционированного воздуха снижают и расчет повторяют.
Массовый расход воздуха за весь цикл ращения солода:
G = (+ - -) / (-) = (60 269 052 + 1 100 498 400 — 80 739 609 — 487 127 040) / (41 298,3 — 34 062) = 592 900 803 / 7 236,3 = 81 934 кг Объемный часовой расход воздуха определяем по формуле:
=GK / (* 24) = 81 934 * 1,1 / 6,5 * 24 * 1,29 = 90 127 / 201,24 = 447,86 /кг, где K — коэффициент неравномерности, при индивидуальной установке вентилятора К = 1,1;
— плотность кондиционированного воздуха, = 1,29 кг/ при = 12 .
Удельный расход кондиционированного воздуха на 1 кг перерабатываемого солода определяем по формуле:
= / = 447,86 / 1360 = 0,329 /(кг * ч)
2.4 Определить тип варочного агрегата непрерывного действия, привести техническую характеристику агрегата и схему разваривания Ответ.
В зависимости от температуры разваривания выбирается тип варочного агрегата непрерывного действия.
Процесс разваривания состоит из двух стадий:
— нагрев замеса до температуры варки;
— выдержка замеса при этой температуре.
Схемы непрерывного разваривания отличаются друг от друга применяемыми аппаратами, а также машинами для дробления и величиной раздробленных частиц.
Тонкое дробление позволяет проводить разваривание при мягком режиме, крупное дробление требует более жесткого режима. Во всех схемах непрерывного разваривания предусмотрена установка паросепаратора для отделения пара от разваренной массы.
В исходных данных нам дана температура развариваемоц массы равная 143 .
Исходя из этой температуры выберем установку непрерывного разваривания крахмалистого сырья Р3 — ВРА — 2000 .
Техническая характеристика установки непрерывного разваривания
Показатели | Р3 — ВРА — 2000 | |
Производительность, дал/сут | ||
Расход электроэнергии, кВт/ч | 37,5 | |
Расход пара при переработке зерна, кг/ч | ||
Расход воды, /ч | 7 — 9 | |
Коэффициент автоматизации,% | ||
Толщина стенок выдерживателя, мм | ||
Установленный срок службы, лет | ||
Габаритные размеры, мм | 9 8003 000 100 000 | |
Масса, кг | 24 800 | |
Измельченное в молотковой дробилке зерно поступает в бункер, откуда дозируется на весоизмерительное устройство и направляется в смеситель. Одновременно сюда подается вода температурой 40 — 50 в количестве, пропорциональной массе измельченного зерна. Из смесителя замес подается плунжерным насосом в подогреватель, где нагревается вторичным паром, поступающим из паросепаратора, до 40 — 85 и через промежуточную емкость, служащую для стерилизации плунжерного насоса, поступает в последний. Подогретый замес подается в контактную головку, где нагревается до температуры разваривания 130 — 150. Замес и часть несконденсировавшегося пара 1,5 мин выдерживается в трубчатом разварнике, где пар окончательно конденсируется. При прохождении по разварнику вязкость массы снижается под действием температуры и высокой скорости сдвига, развиваемой насосом.
Из разварника масса направляется в выдерживатель, где находится под давлением, соответствующим температуре разваривания 40 — 45 мин, а затем выдувается в паросепаратор, охлаждается в нем до 102 — 108 и идет на вакуум — охлаждение .
Схема установки непрерывного разваривания Р3 — ВРА — 2000 :
1 — дробилка молотковая для зерна; 2 — бункер для дробленого зерна; 3 — высокоизмерительное устройство; 4 — смеситель; 5, 8 — плунжерные насосы; 6 — подогреватель замеса; 7 — промежуточная колонна; 9 — контактная головка острого пара; 10 — трубчатый разварник; 11 — выдерживатель; 12 — паросепаратор; 13 — дробилка молотковая для картофеля.
2.5 Рассчитать вместимость и геометрические размеры разварника непрерывного действия.
Ответ.
Количество замеса, развариваемого в течение часа:
G = m / 24 = = 10,8 кг, где m — количество замеса, m = 0,133 /дал;
— плотность замеса, = 1,22 кг Необходимая вместимость варочного агрегата:
= G / = = = 0,83 ,
где — продолжительность разваривания для трубчатого аппарата, = 0,03 ч;
— коэффициент заполнения для трубчатого аппарата, = 0,32.
Диаметр труб аппарата можно определить из равенства:
= ,
где — расход развариваемой массы, /с;
— скорость движения развариваемой массы в трубчатом аппарате, = 0,13 м/с;
d — диаметр труб аппарата, м.
= = = = 0,0025 /с Преобразуем равенство:
=
и найдем диаметр труб аппарата:
d = = = = = 0,16 м Длина (м) варочного агрегата (длина труб):
= = = = 41,5 м.
2.6 Рассчитать расход пара на разваривание крахмалосодержащего сырья Ответ.
Количество теплоты, необходимой для разваривания массы:
Q = G (-),
где — удельная теплоемкость массы, = 3770 Дж/(кг К);
— начальная температура массы, поступающей на разваривание, = 85 ;
— температура разваривания в аппарате, = 143
Q = 10,8 3770 (143 — 85) = 40 716 58 = 2 361 528 Дж/ч Объемный расход пара:
D = ,
где — удельная энтальпия пара, Дж/кг;
— удельная энтальпия конденсата при 143, Дж/кг
D = = = 1,14 кг/ч
2.7 Каковы устройство и работа аппаратов полунепрерывного разваривания? Описание, схема, принцип действия оборудования Ответ.
При полунепрерывном процессе производства спирта разваривание крахмалсодержащего сырья происходит в трех аппаратах: предразварнике, разварнике и паросепараторе-выдерживателе. При этом первые два аппарата работают периодически, а третий обеспечивает непрерывное поступление разваренной массы на осахаривание.
Предразварник предназначен для предварительного нагрева сырья до 60—90 °С отработавшим паром из паросепаратора, что способствует более полному развариванию зерна и позволяет провести последующее разваривание при более низком давлении.
Предразварник представляет собой стальной сосуд с конической крышкой и днищем. Сырье, подлежащее запариванию, загружается через люк 4, находящийся в центре крышки аппарата. Под крышкой находится камера 2, в которую по трубе 5 поступает отработавший пар из выдерживателя или сборника вторичного пара. Из паровой камеры пар по четырем трубам 6 поступает в толщу загруженного сырья. На некоторых заводах в связи с тем, что трубы часто забиваются, они демонтированы, и пар подводится в нижнюю коническую часть аппарата.
На крышке имеется патрубок 3 для отвода воздуха и избыточного пара в бак для подогрева воды. Вода подается в предразварник через патрубок 1.
Сырье выгружается через задвижку 8, которая должна обеспечивать герметичность затвора и возможность регулирования выгрузки сырья из предразварника. В случае слеживания сырья для облегчения его выгрузки имеется шарнирно укрепленный рычаг (ворошитель) 7.
Для разваривания добавляют теплую воду в количестве (в кг): на 1 кг картофеля 0,2—0,5, на 1 кг зерна 2,5—3,5.
Воду задают в предразварник при разваривании зерна и в разварник при разваривании картофеля.
Разварник предназначен для разваривания крахмалсодержащего сырья под давлением до 0,6 МПа (6 кгс/см2), применяется при периодической и полунепрерывной схемах производства спирта. Разварник изготовляют из листовой стали Ст. 3 клепаной или сварной конструкции конической или цилиндроконической формы.
Техническая характеристика разварников СП-1163 СП — 1164
Масса загружаемого картофеля, кг 3000—3500 2500—2600
Масса загружаемого зерна, кг 1300—1500 900—1100
Объем, м3 5,3 4
Диаметр, мм 1500 1500
Высота, мм 5405 5106
Масса, т 2299 1652
Разварник состоит из корпуса 14, загрузочного люка 9 и прикрепленной на фланце выдувной коробки 17. Для предохранения стенок от быстрого износа в нижнюю часть конуса внутри разварника вставляют сменную предохранительную гильзу 4 из стали толщиной 3—4 мм.
В выдувной коробке имеется решетка 18 для удержания посторонних предметов и дополнительного диспергирования сырья в процессе выдувания. Непосредственно над решеткой находится лючок 2, через который очищают решетку и выдувную коробку. В верхней конической части коробки расположены два патрубка, по одному из них 3 подается пар, а другой 16 предназначен для отвода конденсата, но во избежание потери крахмала им пользуются редко. Выходное отверстие над решеткой закрывается коническим клапаном 1.
Поступление пара в разварник регулируется вентилем 6. Обратный клапан 5 препятствует попаданию сырья в вентиль и коммуникации в случае снижения давления в паровой магистрали. Через вентиль 7 подают пар при выдувании разваренной массы.
На крышке разварника к патрубку 13, защищенному сеткой, присоединен тройник с двумя вентилями 11 и 12. Вентиль 12 служит для отвода вытесняемого воздуха в атмосферу при загрузке аппарата и пропаривании сырья, а также для окончательного снятия давления в аппарате перед открытием крышки люка. Вентилем 11 пользуются при циркуляции (перемешивании) сырья паром, избыток пара отводят в выдерживатель.
На крышке разварника имеются патрубок 10 для установки предохранительного клапана и патрубок для манометра 8, выведенного на рабочее место. На высоте 700—800 мм от нижнего фланца располагается пробоотборник 15.
На трубопроводе, подводящем пар к разварникам, устанавливается редукционный вентиль, отрегулированный на рабочее давление аппаратов. Поверхность разварника с внешней стороны теплоизолируют. Верхний люк разварщика для безопасности эксплуатации делается внутренним. Внутреннее давление давит на люк, прижимая его к горловине. Разварник опирается четырьмя лапами на каркас.
Разварники являются сосудами, работающими под давлением. Изготовление и эксплуатация их должны осуществляться в соответствии с требованиями правил Госгортехнадзора.
При эксплуатации разварников необходимо следить за состоянием предохранительной гильзы (при износе на 50% толщины ее необходимо заменить), исправностью предохранительного клапана и редукционного вентиля, которые должны быть отрегулированы на давление, не превышающее разрешенное рабочее давление; исправностью манометра. На стекле манометра (с внутренней стороны) должна быть нанесена красная черта, соответствующая разрешенному давлению.
Недостатки разварника следующие: периодичность процесса, значительные затраты времени на загрузку и выгрузку, на прогрев аппарата после каждой новой загрузки, неравномерность процесса варки в каждом аппарате из-за неодинаковых условий разваривания на разных уровнях в разварнике и в результате этого потери крахмала (недоваривание и переваривание сырья). Большим недостатком также является неравномерность потребления пара во времени, что отрицательно сказывается на работе котельной; разварники являются металлоемкими аппаратами; при обслуживании их затрачивается ручной труд, при эксплуатации требуется постоянное повышенное внимание персонала.
Выдерживатель используют при полунепрерывном и непрерывном процессах разваривания сырья. В нем происходит снижение температуры массы после разварника в результате образования вторичного пара, создается запас разваренной массы, обеспечивающий непрерывность процесса осахаривания, доваривается масса, может осуществляться смешивание разваренной массы из разных видов сырья.
В верхней части аппарата, являющейся паровой зоной, происходит сепарирование — отделение вторичного пара от разваренной массы. Она выполняет также роль крахмалоловушки, задерживая частицы массы, увлекаемые паром из разварников при циркуляции.
Наличие выдерживателя значительно выравнивает цикличность работы разварников. Выдерживатель изготовляют цилиндрической формы из листовой стали толщиной цилиндрической части 6—8 мм и днища 7—9 мм, он рассчитан на давление не выше 70 кПа (0,7 кгс/см2).
Разваренная масса и циркуляционный пар подводятся в верхнюю цилиндрическую часть аппарата по тангенциально расположенным патрубкам, что способствует лучшему отделению (сепарированию) пара. В том месте, где выдуваемая масса скользит по стенке, вставлен стальной отражатель 10, препятствующий выбросу массы в паровое пространство выдерживателя. Выдерживатель заполняют разваренной массой на 2/з объема, а 7з приходится на паровое пространство.
Ниже воротника расположены два поплавковых указателя уровня 5, верхний из них показывает предельно допустимый уровень массы, нижняя часть аппарата от днища до первого поплавка служит для выдерживания массы. Объем между поплавками предназначен для массы при очередном выдувании разварника.
По поперечному сечению аппарата расположена решетка 12 для задержания посторонних крупных примесей, которая выполняется разборной из стальных полос. Ширина зазоров между полосами 20 мм. Решетку чистят через люк 13, а на ходу при необходимости путем подвода пара через патрубок 4. При непрерывных схемах разваривания с хорошей подработкой сырья необходимость в решетке отпадает.
Уклон конусного днища составляет 60°, что обеспечивает хороший сток и полный выход массы.
Помимо предохранительного клапана к выдерживателю присоединяют гидравлический затвор 9, представляющий собой У-образную трубу диаметром 100—150 мм и высотой 7 м. Уровень воды в гидравлическом затворе контролируется краном 11. Высота столба воды при отсутствии давления в аппарате 3,5 м. В верхней части трубы гидравлического затвора имеется ловушка 8 для задержания воды, вытесняемой из затвора при повышении давления свыше 70 кПа (0,7 кгс/см2), и в то же время она должна обеспечивать выпуск избыточного пара через отверстия в верхней части ловушки. На трубе, отводящей пар из выдерживателя, устанавливают регулятор давления 7, при помощи которого в выдерживателе поддерживается давление в пределах 0,03—0,05 МПа (0,3— 0,5 кгс/см2).
В случае снижения температуры при длительных простоях массу можно подогревать паром через барботер 15. Давление в аппарате контролируют по манометру 3, который устанавливается в месте, удобном для контроля. Манометрическая трубка 6 заполняется водой. При определении истинного давления в выдерживателе из показаний манометра следует вычесть давление, создаваемое столбом воды в трубе. Загрязнившуюся воду из манометрической трубки периодически спускают через трехходовой кран 2. Наружную поверхность выдерживателя покрывают теплоизоляцией.
1. Кретов И. Т., Антипов С. Т. Технологическое оборудование предприятий бродильной промышленности: Учебник. — Воронеж: Издательство государственного университета, 1997. — 624 с.
2. Кретов И. Т., Антипов С. Т., Шахов С. В. Инженерные расчеты технологического оборудования предприятий бродильной промышленности. — М.: КолосС, 2004. — 391 с.
3. Ковалевский К. А. Технология бродильных производств: учебное пособие. — Киев: Фирма «ИНКОС», 2004. — 340 с.
4. Сорокопуд А. Ф. Технологическое оборудование. Традиционное и специальное технологическое оборудование предприятий пищевых производств: учебное пособие, Кемеровский технологический институт пищевой промышленности, 2009. — 202 с.
5. Бачурин П. Я., Устинников Б. А. Оборудование для производства спирта и спиртопродуктов. — М.: Агропромпромиздат, 1985. -343с