Организация работы роликового участка пассажирского вагоноремонтного депо по проведению полной ревизии
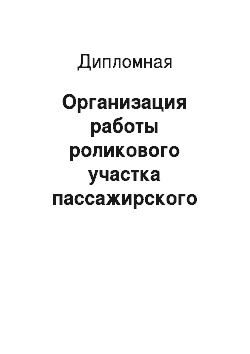
Правильность сборки буксы контролируют по легкости ее вращения на шейке оси, которое должно быть совершенно свободным (букса вращается вручную). Допускается неравномерный зазор по всей окружности, при этом минимально допускаемый зазор 0,3 мм должен находиться в зоне расположения ушков крепительных крышек. Причинами затруднительного вращения может быть чрезмерное заполнение буксы смазкой… Читать ещё >
Организация работы роликового участка пассажирского вагоноремонтного депо по проведению полной ревизии (реферат, курсовая, диплом, контрольная)
Содержание Введение
1. Общая часть
1.1 Назначение и состав производственного участка
1.2 Определение фонда рабочего времени
1.3 Расчет производственной программы участка
1.4 Расчет параметров производственного процесса
2. Технологическая часть
2.1 Расчет и выбор технологического оборудования
2.2 Определение габаритных размеров участка
2.3 Расчет контингента рабочей силы
2.4 Разработка технологического процесса
3. Экономическая часть
3.1 Прямые расходы, связанные с производством и реализацией по вагонному хозяйству
3.2 Расходы, общие для всех мест возникновения затрат и видов работ
3.3 Общехозяйственные расходы
3.4 Расчет себестоимости
4. Охрана труда
4.1 Требования безопасности к технологическому процессу
4.2 Требование пожарной безопасности
4.3 Экологическая безопасность Заключение Список использованных источников
Введение
Железнодорожный транспорт представляет собой единый производственно-технологический орган власти с централизованным управлением. Созданная за большой исторический период сильная система управления позволяет успешно решать все возложенные государством на железнодорожный транспорт задачи.
Огромная общегосударственная и социальная значимость, особенности работы определили законодательное закрепление федерального статуса железнодорожного транспорта, государственное регулирование и контроль за его деятельностью, развитие материально-технической базы и удовлетворение основных потребностей в составе государственных нужд. Железнодорожный транспорт осуществляет свою деятельность в тесном взаимодействии с органами государственной власти и управления субъектов Российской Федерации.
Магистральные железные дороги работают в тесном контакте с подъездными путями, обеспечивающими производственную деятельность десятков тысяч промышленных предприятий, строек и других организаций.
Железнодорожный транспорт — вид транспорта, выполняющий перевозки пассажиров и грузов по рельсовым путям в вагонах с помощью локомотивной или мотор-вагонной тяги.
Среди всех видов транспорта, во многих странах ведущее место занимает железнодорожный транспорт, что объясняется его универсальностью.
Возможностью обслуживать все отрасли экономики и удовлетворять потребности населения в перевозках практически во всех климатических зонах и в любое время года.
Высокой провозной способностью и эффективностью перевозок массовых грузов на большие расстояния, сравнительно большими скоростями, надежностью и безопасностью, низкой себестоимостью перевозок, меньшим воздействием на окружающую природную среду, чем другие виды транспорта.
Доля железнодорожного транспорта в общем объеме перевозок складывается с учетом экономико-географических, демографических и других факторов.
Железнодорожный транспорт связывает в единое целое многочисленные области и районы страны, обеспечивает жизнедеятельность всех отраслей экономики, реализацию социальных программ, экономическую и национальную безопасность государства, активно влияет на развитие межрегиональных и международных связей.
Железнодорожный транспорт России — сложное многоотраслевое хозяйство, в составе которого 17 железных дорог с входящими в них отделениями, станциями, локомотивными и вагонными депо, дистанциями пути, электроснабжения, сигнализации и связи и другими подразделениями. Предприятия, осуществляющие ремонт и модернизацию подвижного состава и контейнеров, производящие запасные части, оборудование и материалы, обеспечивающие средствами связи, а также сбор и обработку технологической информации, ведущие научные разработки в области техники, технологии и развитии железнодорожного транспорта, организации и учреждения по подготовке кадров, обслуживанию социальной сферы.
В целях повышения устойчивости работы железнодорожного транспорта, безопасности и качества оказываемых услуг, формирования эффективной транспортной системы страны, снижения совокупных народно — хозяйственных затрат на перевозки грузов и пассажиров железнодорожным транспортом и удовлетворения растущего спроса на услуги, оказываемые на железнодорожном транспорте, происходит реформирование отрасли.
1. Общая часть
1.1 Назначение и состав производственного участка Колесное отделение предназначено для ремонта колёсных пар с роликовыми подшипниками типа РУ1−950, РУ1Ш-950 в объеме полного и обыкновенного освидетельствования без смены элементов, поступающих из-под вагонов при плановых видах ремонта, ТО-3 и текущего ремонта.
Колесное отделение состоит из следующих участков:
а) колёсного парка, предназначенного для хранения колесных пар;
б) колесного участка, предназначенного для осмотра, обмывки, дефектоскопирования, промежуточной ревизии, обточки колесных пар по кругу катания, окраски и приемки их после ремонта на позициях:
— осмотра колесных пар, дефектации и определения вида ремонта;
— обмывки колесных пар и деталей буксового узла;
— проведения промежуточной ревизии роликовых букс;
— дефектоскопирования колёсных пар и деталей буксового узла;
— обточки колесных пар на колесно-токарном станке;
— приемки отремонтированных колесных пар;
— окраски колесных пар.
в) участка для производства полной ревизии букс, предназначенного для выполнения следующих работ: демонтаж букс, подготовка к монтажу, монтаж букс, ремонт роликовых подшипников. Отделение роликовых подшипников состоит из трёх участков: участка ремонта подшипников, комплектовочного и монтажного участка.
Участок по ремонту подшипников предназначен для протирки и хранения подшипников, поступивших после обмывки из колёсотокарного отделения, дефектоскопирования роликов, ремонта и подбора роликов, передачи промытых подшипников в комплектовочное отделение.
Комплектовочный участок предназначен для осмотра, измерения осевых зазоров подшипников, измерения диаметров внутренних колец подшипников на горячей посадке, дефектоскопии полиамидных сепараторов, смазывания блоков подшипников, хранение неснижаемого запаса подшипников.
Роликовый участок для производства полной ревизии букс предназначен для выполнения следующих работ: демонтаж букс, подготовка к монтажу, монтаж букс, ремонт роликовых подшипников. В состав участка входят следующие отделения:
— демонтажное отделение;
— ремонтно-комплектовочное отделение;
— монтажное отделение.
1.2 Определение фонда рабочего времени Фонд времени работы оборудования — это количество часов его работы в течение определенного периода времени (год, квартал, месяц). Различают номинальный и действительный годовой фонд времени работы оборудования.
Устанавливаем режим работы для роликового участка — односменный.
Номинальный фонд времени работы оборудования рассчитывается по формуле
Fноб = [(Дк — Дп) Ч tc] Ч mсм — tпр, (1)
где Дк — количество календарных дней в году, дни;
Дп — количество праздничных дней и выходных, дни;
tc — продолжительность рабочей смены, час;
mсм — количество смен, смена;
tпр — предпраздничные сокращённые дни, час (6часов).
Принимаю Дк = 365 дней, Дп = 118 дней, tc = 8 часов, mсм = 1 смены
Fноб = [(365 — 118) Ч 8] Ч 1 — 6 = 1970 часов Действительный фонд времени работы оборудования определяется по формуле
Fgоб = Fноб Ч об, (2)
где об — коэффициент, учитывающий простой оборудования по технической неисправности и в ремонте. Принимаю об = 0,95 0,98.
Fgоб = 1970 Ч 0,95 = 1871.5 часов Явочный фонд рабочего времени рассчитывается по формуле
Fяв = [(Дк — Дп) Ч tc] Ч mсм, (3)
где Дк — количество календарных дней в году, дни;
Дп — количество праздничных дней и выходных, дни;
tc — продолжительность рабочей смены, час;
mсм — количество смен, смена.
Принимаю Дк = 365 дней, Дп = 118 дней, tc = 8 часов, mсм = 1 смены
Fяв = [(365 — 118) Ч 8] Ч 1 = 1976 часов Списочный фонд рабочего времени рассчитывается по формуле
(4)
где е — коэффициент учитывающий отсутствующих рабочих, для депо = 7 — 15%.
Фонд времени работы одного рабочего определяется при условии, что среднемесячная норма часов, принятая на железнодорожном транспорте равна 165,5 часа. Тогда:
Fр = 165,5 Ч 12 = 1986 часов
1.3 Расчет производственной программы участка Основные показатели годового плана деповского ремонта это, количество вагонов выпущенных из деповского ремонта. Программа колёсного отделения определяется из следующего условия: в ремонт поступают все колёсные пары, снимаемые с вагонов деповского ремонта, а так же на пополнение не снижаемого запаса текущего отцепочного ремонта и единой технической ревизии (ТО-3).
Для нахождения годовой программы участка принимается, следующие условия:
— в участок поступают все подшипники с колёсных пар из-под вагонов деповского ремонта;
— 10−15% колёсных пар поступает в ремонт из текущего отцепочного ремонта.
Годовая программа депо по ремонту равна 955 пассажирских вагонов.
Программа колёсного отделения определяется по формуле
Nкол = Nд Ч а, (5)
где Nд — годовая программа ремонта вагонов;
а — количество узлов на вагоне.
Nкол = 955Ч4 = 3820 колёсных пар
15% колёсных пар поступивших на участок с вагонов текущего отцепочного ремонта:
Nкол = 3820Ч0,15 = 573 колёсных пар
Тогда полная годовая программа ремонта роликового отделения составит
Nкол = 3820 + 573 = 4393 колёсных пар На одну колёсную пару устанавливается 4 подшипника
Nрол = 4393 Ч 4 = 17 572 подшипника Вывод: Произведя расчет, установлена производственная программа роликового участка, которая составляет 17 572 подшипника.
1.4 Расчёт параметров производственного процесса Производственный процесс — совокупность взаимосвязанного основного, вспомогательного, естественного процесса, в результате которого, предметы труда превращаются в готовую продукцию. Основными элементами производственного процесса является предметы — ремонта вагонов и активная целенаправленная деятельность человека.
Основными параметрами производственного процесса является ритм, такт и фронт.
Ритм показывает, какое количество подшипников выходит из ремонта за определённый период времени, и определяется по формуле
(6)
где N кп — годовая программа ремонта колёсных пар, колёсных пар;
Fgоб — действительный фонд времени работы оборудования, час.
Фронтом работы называют количество одновременно ремонтируемых подшипников находящихся на позициях, и определяется по формуле
Фр = r Ч tв, (7)
где tв — норма простоя вагона в ремонте (для пассажирских вагонов 9), дней.
Фр = 10 Ч 9 = 90 подшипников Тактом называется интервал времени между последовательным выпуском подшипников. Его величина определяется по формуле
(8)
где с — количество ремонтных позиций (для пассажирских депо 4 — 8).
Сменную программу участка определяем по формуле
(9)
где Dсм — количество рабочих дней в году, день;
m — количество смен.
В депо при ремонте вагонов применяется поточный метод.
Поточный метод является передовой формой организации ремонта и характеризуется тем, что вагоны передвигаются в процессе ремонта через определённые промежутки времени с одной позиции на другую.
При этом каждая позиция оснащается механизмами и приспособлениями в соответствии с выполняемыми работами, а рабочие, находящиеся на рабочих местах, производят на каждом вагоне ремонтные операции, установленные на данной позиции.
При поточном методе с наибольшей полнотой осуществляются важнейшие принципы высокоорганизованного производства: пропорциональность, ритмичность, параллельность, прямоточность; комплексная механизация и автоматизация производственных процессов, а также широко используется передовая техника; размещение вспомогательных участков и отделений вдоль вагоносборочного участка напротив тех позиций, где детали снимаются или ставятся на вагон, что сокращает время на транспортировку их от вагона или к вагону; специализация рабочих мест на небольшом числе производственных операций, что позволяет ускорить производственный цикл ремонта вагонов.
Вместе с тем поточный метод ремонта требует постоянства объема работ в ремонтируемых вагонах и однородности их типов на каждой поточной линии. Применение этого метода в проекте возможно, так как проектируемое депо специализированно на ремонте одного типа вагонов, поэтому выбираем именно этот метод для ремонта не только вагонов, но и узлов и деталей.
2. Технологическая часть
2.1 Расчет и выбор технологического оборудования Для роликового участка потребное количество станков и оборудования определяется исходя, из их производительности и объёма работ в участке или по установленному на ремонт одного вагона времени в станко-часах и рассчитывается по формуле
(10)
где Nкол — годовая программа ремонта колёсных пар;
Hоб — норма в станко-часах на ремонт одного подшипника = 1,5 человек/час;
Fgоб — действительный годовой фонд времени работы оборудования с учетом сменности;
Коб — коэффициент времени использования оборудования (0,80,9).
Потребное оборудование, приспособления и подъёмно транспортные устройства и их количество подбираем согласно технологического процесса, все данные сводим в таблицу 1
Таблица 1 — Потребное оборудование
Наименование оборудования | Количество единиц штук | Стоимость единицы, рублей | Мощность единицы, кВт | |
Установка для восстановления колец подшипников ВП-250−0-ОСБ | 14 800,00 | 1,1 | ||
Дефектоскоп УМДП-01 | 36 400,00 | 0,8 | ||
Пресс для испытания полиамидных сепараторов | 8150,55 | 0,2 | ||
Моечная машина обмывки подшипников МСП-01. | 47 400,00 | 0,8 | ||
Сверлильный станок | 24 560,00 | 1,2 | ||
Дефектоскоп ВД-211.5 для контроля роликов | 37 450,00 | 0,8 | ||
Станок для зачистки торцов роликов АЗТ-4 | 16 700,00 | 0,4 | ||
Станок для зачистки цилиндрической поверхности роликов АЗЦ-3 | 17 220,00 | 0,4 | ||
Приспособление для шлифовки роликов по кругу МИБЕ-076. | 14 750,10 | 0,2 | ||
Станок шлифовки торцов роликов МИБЕ-075. | 14 250,00 | 0,2 | ||
Всего | 231 680,65 | 6,1 | ||
Остальное оборудование также принимаю согласно технологическому процессу, в том числе и средства механизации.
2.2 Определение габаритных размеров участка Площади производственных участков и отделений определяются исходя из количества технологического оборудования и его размеров с учётом его проходов и размеров, согласно норм технологического проектирования вагонных депо.
Площадь роликового участка складывается из площадей демонтажного, ремонтно — комплектовочного и монтажного отделений. Площади этих отделений принимаются из расчёта, что на одну ремонтируемую колёсную пару в смену для демонтажного отделения необходимо 5 м2, остальных по 10 м2.
Площадь роликового отделения определяем по формуле
S = (5+10+10) ЧNсм, (11)
где Nсм — сменная программа колёсного участка (18 колёсных пар), колёсных пар.
S = (5+10+10) Ч18 =450 метров
Имея данные размеры, находим длину участка и объём по формулам
(12)
где S — площадь участка, метров;
B — длинна участка, метров.
V = S Ч h, (13)
где h — высота участка, метров.
V = 450 Ч 4,8 = 2160 метров
Данные сводим в таблицу 2
Таблица 2 — Размеры роликового отделения
Длина, м | Ширина, м | Высота, м | Площадь, м2 | Объём, м3 | |
37,5 | 4,8 | ||||
2.3 Расчёт контингента рабочей силы Расчёт численности основных производственных рабочих ведётся исходя из программы депо и трудоёмкости ремонтных работ. Явочная численность рабочих определяется по формуле
(14)
где Nкол — годовая программа ремонта, колёсная пара;
Н — трудоёмкость на техническое обслуживание роликового подшипника чел-ч/вагон, H = 4,1человек/час;
F — номинальный годовой фонд рабочего времени одного рабочего;
К — коэффициент, учитывающий снижение трудоемкости работ; вследствие внедрения средств механизации и автоматизации технического обслуживания вагонов, К = 1,14.
Списочная численность рабочих определяется по формуле
Rсп = Rсп Ч Кз (15)
где К3 — коэффициент замещения (1,1)
Rсп = 8 Ч 1,1 = 9 человек Из этого количества работников рассчитаем количество руководителей, оперативно-производственный персонал, вспомогательных рабочих.
Вспомогательных (подсобных) рабочих принимаем от 6 до 8%
Руководителей принимаем от 5 до 6%, от списочного количества рабочих и вспомогательных Специалистов принимаем от 4 до 5% от списочного состава и вспомогательных рабочих Данные расчетов заносим в таблицу 3.
Таблица 3 Численность контингента
Наименование профессии | Количество исполнителей, человек | Разряд | |
Бригадир освобождённый | |||
Слесарь | |||
Слесарь | |||
Слесарь | |||
Дефектоскопист | |||
Итого: | |||
2.4 Разработка технологического процесса
Технологический процесс роликового участка предусматривает: Изучение рабочих чертежей, технических условий и правил ремонта роликовых подшипников. И разрабатывается в соответствии со следующими основными положениями:
— соответствие применяемого оборудования правилам ремонта и техническим условиям производственных процессов;
— широкая механизация и автоматизация операций;
— поточность производства работ;
— ритмичность обеспечения рабочих мест материалами и запасными частями в соответствии с нормами неснижаемого технического запаса;
— установление технологического маршрута, содержание и последовательности операций;
— выбор технологического оборудования применяемого по каждому варианту технологического маршрута с учетом требований точности сборки, технического соответствия требованием ремонта узлов;
— установление квалификации и разряда работ по каждой операции;
— определение норм времени и расценок для производства ремонта деталей и узлов.
Общее руководство работой участка по ремонту роликовых подшипников осуществляет мастер колёсного отделения.
Мастер колесного отделения и бригадир роликового участка контролируют выполнение работниками участка правил технической эксплуатации, приказов и инструкций, данного технологического процесса, несут ответственность за обеспечение работников участка запасными частями, материалами, исправным инструментом, подъёмными механизмами, приспособлениями, обеспечение квалифицированными кадрами в соответствии с данным технологическим процессом. Контролируют правильное использование работников, а также выполнение ими правил по охране труда и технике безопасности.
Ремонт буксового узла осуществляться при полном и строгом соблюдении следующих условий:
— замены неисправных узлов и деталей заранее отремонтированными или новыми;
— механизации и автоматизации всех трудоемких работ за счет применения специальной технологической оснастки и последовательности выполнения ремонтных операций;
— проведения диагностики технического состояния узлов и деталей с составлением описи ремонтных работ.
— выполнения требований Инструктивных указаний по эксплуатации и ремонту вагонных букс с роликовыми подшипниками (3-ЦВРК);
Ремонт деталей и узлов буксового узла проводится по требованиям технологических карт настоящего технологического процесса при обеспечении исполнителей работ полным комплектом необходимого инструмента и проверочных шаблонов.
При ремонте буксового узла должны соблюдаться Правила охраны труда.
Организация ремонта буксового узла предусматривает создание неснижаемого технологического запаса основных деталей и узлов.
Все колесные пары, выкаченные из-под вагонов подают на специально выделенное место. Для их предварительного осмотра для определения ремонта, обмера элементов и оприходования.
Предварительный осмотр выполняется с целью выявления неисправностей, которые не могут быть обнаружены после очистки и обмывки колесной пары, а также для выявления бракованных элементов и определения вида ремонта.
После осмотра и дефектации колёсная пара подаётся в монтажное отделение, где производится демонтаж буксового узла.
Обыкновенное освидетельствование
На обыкновенное освидетельствование с производством промежуточной ревизией буксового узла колесная пара отправляется:
— при каждой подкатке колесных пар под вагон, кроме колесных пар, не бывших в эксплуатации после последнего полного или обыкновенного освидетельствования;
— при обточке колесных пар;
— при сроке службы осей колесных пар 15 лет и более, при условии дефектоскопирования осей.
При обыкновенном освидетельствовании колесных пар осуществляют:
— предварительный осмотр колесных пар до очистки с целью лучшего выявления ослабления или сдвига ступиц колес на оси и трещин в элементах;
— очистку от грязи и смазки;
— проверку неразрушающим контролем деталей колесной пары;
— осмотр, а также проверку соответствия размеров и износов всех элементов установленным нормам;
— промежуточную ревизию букс колесных пар.
При обточке поверхности катания колесных пар при первом предельном прокате или других неисправностях поверхности катания колес, образовавшихся после предыдущего полного освидетельствования, производится обыкновенное, освидетельствование. На бирке, установленной под болтами крепительной крышки, а также на торце левой шейки оси выбивают знак об обточке в виде буквы «О», условный номер, присвоенный ремонтному пункту, и дату.
Промежуточная ревизия букс производится:
— при обточке колесных пар;
— при обыкновенном освидетельствовании колесных пар;
— при единой технической ревизии (ТО-3);
— в качестве профилактической меры по отдельным указаниям.
Ревизию осуществляет слесарь, имеющий квалификацию не ниже 4 разряда и соответствующее удостоверение.
Перед промежуточной ревизией у выкаченных колесных пар буксы проворачивают для определения неисправностей (раковин и т. д.). При вращении буксы с толчками и ненормальным шумом производят полную ревизию.
При промежуточной ревизии слесарь с помощью гайковерта откручивает болты смотровой крышки и снимает крышку. Места прилегания крышки предварительно очищают от грязи и протирают. Снятую крышку укладывают внутренней стороной вверх в закрываемый ящик. Из передней части буксы смазку перекладывают в снятую крышку, при этом необходимо соблюдать условия, исключающие попадание в буксу и крышку различных загрязнений.
Буксы с загрязненной смазкой (стальные, латунные включения, механические и другие примеси) подлежат полной ревизии. При хорошем состоянии смазки (потемнение смазки не является браковочным признаком) производят дальнейший осмотр. Проверяют состояние переднего подшипника. При обнаружении излома сепаратора, внутреннего кольца, масла от редукторно-карданного привода, упорного приставного кольца или других дефектов буксу подвергают полной ревизии.
При единовременной технической ревизии пассажирских вагонов колесные пары, имеющие редукторно-карданный привод от торца шейки оси, выкатывают из-под вагона для тщательного осмотра и проверки круга катания колес. Профилактическая, а также единовременная техническая ревизии пассажирских вагонов производятся под вагоном без снятия стопорных планок. Надежность торцевого крепления проверяется остукиванием.
При удовлетворительном состоянии подшипника остукиванием контролируют болты стопорной планки или тарельчатой шайбы. Ослабшие болты М12 подтягивают, неисправные заменяют. Неисправную проволоку болтов стопорной планки заменяют, под болты стопорной планки ставят пружинные шайбы.
Надежность крепления торцевой гайки проверяют ударами слесарного молотка по оправке, упираемой в одну из граней коронки или в шлиц гайки. Проверку производят в обе стороны вращения гайки. При ослаблении гайки торцевого крепления колесную пару выкатывают и снимают гайку. Колесная пара и гайка с поврежденной резьбой к дальнейшей эксплуатации не допускаются. При ревизии, у букс с подшипниками при торцевом креплении гайкой независимо от состояния крепления снимают стопорную планку для дефектоскопирования и клеймения, торцевую гайку и упорное кольцо — для визуального осмотра резьбы шейки оси и гайки. Колесные пары или гайки с поврежденной резьбой к дальнейшей эксплуатации не допускаются. При исправном состоянии резьбы производят затяжку гайки с последующей установкой стопорной планки в соответствии с требованиями Инструктивных указаний 3-ЦВРК.
При торцевом креплении тарельчатой шайбой болты М20 освобождают от стопорения и динамометрическим ключом проверяют их затяжку (вращением по часовой стрелке). При наличии хотя бы одного из болтов с крутящим моментом менее 5 кгс/м все болты вывертывают и проверяют визуально состояние резьбы отверстий в торце оси и болтов крепления, а также состояния места перехода стержня болта к головке. При обнаружении задиров в месте перехода стержня болта к головке радиусом менее 0,8 мм и без подголовника или других повреждений болты к дальнейшей эксплуатации в торцевом креплении не допускаются. При изломе головки или стержня болта оставшуюся часть болта вывертывают из оси без повреждения резьбы резьбового отверстия. Поврежденные болты заменяются.
При обнаружении срыва более трех ниток резьбы в резьбовых отверстиях оси или затруднений при завертывании болтов крепления допускается резьбовые отверстия исправлять метчиком. При повреждении более шести первых ниток резьбы в резьбовых отверстиях оси колесная пара не допускается к дальнейшей эксплуатации до специального указания. Болты, имеющие затяжку крутящим моментом более 5 кгс/м, подтягивают с усилием от 23 до 25 кгс/м.
Затяжка болтов должна быть равномерной. Для этого завинчивание трех болтов производят дважды по периметру, а четырех — по схеме 1−2-3−4-3−4-2−1 с последующим стопорением.
При торцевом креплении тарельчатой шайбой и болтами М20 проверку состояния такого крепления после освобождения болтов от стопорения, осмотр резьбовых отверстий в оси и болтов, а также последующую их затяжку производят в соответствии с требованиями настоящего ТП.
При промежуточной ревизии после проведения операций в буксу добавляют, свежую (не бывшую в употреблении) смазку до объема 0,2 кг. ЛЗ-ЦНИИ, которую укладывают валиком на видимую часть переднего подшипника, уплотняя ее пальцами так, чтобы смазка смогла проникнуть между сепаратором и бортом наружного кольца. Затем устанавливают смотровую крышку.
О проведенной промежуточной ревизии букс в журнале формы ВУ-92 делают соответствующие записи.
Полное освидетельствование
На полное освидетельствование с производством полной ревизии колесная пара отправляется в следующих случаях:
— колесные пары, проходившие последнее полное освидетельствование пять и более лет;
— колесные пары, срок службы оси которых 15 лет и более, при невозможности дефектоскопирования осей. Кроме колесных пар ранее проходивших последнее полное освидетельствование не более 3 месяцев;
— при капитальном ремонте вагонов;
— при неясности клейм и знаков последнего полного освидетельствования на торце шейки оси;
— при отсутствии бирки или неясности клейм на ней;
— при сварочных работах на вагоне или тележке без соблюдения правил сварочных работ на вагонах, при включении подшипников в сварочную цепь и при использовании рельс в качестве обратного провода;
— при наличии на поверхности катания колес: неравномерного проката 2 мм и более, ползуна и навара 1 мм и более, разности диаметров колес на одной оси 3 мм и более;
— при повреждении вагона от динамических ударов при падении груза;
— после схода вагона у колесных пар сошедшей тележки;
— при недопустимом нагреве буксы, повреждении буксового узла, требующего демонтажа букс, а также колесным парам, отцепленным по показаниям прибора ДИСК, КТСМ.
При полном освидетельствовании производят:
— предварительный осмотр до очистки с целью лучшего выявления ослабления или сдвига ступицы колеса на оси и трещин в элементах;
— контроль вихретоком, ультразвуком и магнитная дефектоскопия;
— демонтаж букс без снятия внутренних и лабиринтных колец при условии проверки осей специальным щупом ультразвукового дефектоскопа. Внутренние и лабиринтные кольца у букс с двумя цилиндрическими подшипниками на горячей посадке снимают при их неисправности, а также при отсутствии специального щупа ультразвукового дефектоскопа;
— очистку от грязи, смазки и краски;
— проверку магнитным дефектоскопом шеек и предподступичных частей осей колесных пар после снятия внутренних и лабиринтных колец;
— проверку магнитным дефектоскопом внутренних колец подшипников без снятия их с шейки оси;
— проверку дефектоскопом средней, части оси;
— проверку подступичных частей осей ультразвуковым дефектоскопом;
— осмотр всех элементов колесной пары, а также проверку соответствия их размеров и износов производить согласно «Инструкции по осмотру, освидетельствованию, ремонту и формированию вагонных колесных пар» ЦВ/3429, а также «Инструктивных указаний по эксплуатации и ремонту вагонных букс с роликовыми подшипниками» 3-ЦВРК.
Демонтаж буксовых узлов производится при полном освидетельствовании колесной пары.
Демонтаж букс с роликовыми подшипниками осуществляется на демонтажной площадке колесного отделения.
При демонтаже буксы не допускается сбрасывать ее с шейки оси. Категорически запрещается использовать любой ударный инструмент для удаления подшипников из корпуса. Подшипники из корпуса буксы необходимо удалять только при помощи специальных прессов или устройств.
Демонтаж выполняется в следующем порядке:
а) отвернуть пневматическим гайковертом болты крепительной крышки, а затем снять крепительную крышку вместе со смотровой;
б) удалить смазку с крышки и передней части буксы. Использованную смазку собирать в специальную емкость для отработанной смазки;
в) отвернуть и снять болты стопорной планки или тарельчатой шайбы. Планку или шайбу снять;
г) ключом отвернуть и снять торцевую гайку, а также упорное кольцо переднего подшипника;
д) перед снятием корпуса буксы с шейки оси на резьбовую часть оси навинтить предохранительный стакан.
е) вынуть из корпуса буксы блоки подшипников;
ж) снять при необходимости внутренние кольца с шейки оси.
Снятие внутренних колец с шеек оси осуществляется двумя методами:
— с помощью установки холодной выпрессовки внутренних и лабиринтных колец;
— с помощью индукционного нагревателя для внутренних и лабиринтных колец подшипников.
После демонтажа все элементы колесной пары поступают в моечную машину.
Обмывка колесных пар, корпусов букс и деталей буксового узла, кроме роликовых подшипников, болтов и стопорных планок производится в соответствии с Технологической инструкцией «ТИ 020−1 124 328−00».
Стопорные планки, болты, роликовые подшипники обмываются в автоматической моечной машине МСП-01.
Обмывка производится мыльной эмульсией, подогретой паром от 90 до 95 градусов Цельсия, и просушивают воздухом, пропускаемым через змеевик, размещенный внутри ванны моечной машины. Новые роликовые подшипники и подшипники, покрытые консервационной смазкой, также промыть в автоматической машине. В том случае, если осмотр подшипников будет производиться не ранее, чем через сутки после промывки, их необходимо смазывать смазкой ПП-95/5 (ГОСТ 4113−80).
Для предотвращения выпадания роликов из гнезд сепараторов промывку роликовых подшипников в моечных машинах производят со специальными втулками. Допускается промывка вместе с внутренними кольцами.
Для промывки новых подшипников допускается применять моющую жидкость с содержанием от 1 до 1,5 процентов смазки ЛЗ-ЦНИИ.
Корпуса букс, смотровые и крепительные крышки, лабиринтные кольца, гайки, стопорные планки, болты промываются, в моечной машине двумя моющими жидкостями при температуре не ниже 90 градусов Цельсия. Первая моющая жидкость содержит, от 2 до 5 процентов каустической соды, а вторая от 8 до 10 процентов отработанной смазки ЛЗ-ЦНИИ от объема воды в ваннах. При отсутствии в моечной машине второй ванны допускается промывка деталей вручную перед производством монтажа.
Осмотр, неразрушающий контроль, ремонт и комплектовка подшипников.
При ремонте подшипников забракованные детали наружные и внутренние кольца, сепараторы и ролики заменяют новыми или годными из числа бывших в эксплуатации, удовлетворяющих требованиям.
После обмывки детали роликовых подшипников проверяют визуально.
Осматривают внутреннее (при условии снятия с шейки оси), наружное и упорное кольца, ролики, сепаратор с помощью лупы при рассеянном свете для определения их пригодности к дальнейшему использованию. Неисправные подшипники направляют в ремонт.
Сведения о каждом осмотренном подшипнике с указанием его состояния (в том числе и упорном кольце) заносят в журнал осмотра формы ВУ-91.
После осмотра деталей роликовых подшипников производят их дефектоскопирование.
При ремонте цилиндрических подшипников забракованные детали (наружные и внутренние кольца, сепараторы и ролики) заменяются новыми или годными из числа бывших в эксплуатации. Наружные и внутренние кольца, ролики подлежат неразрушающему контролю.
В буксах, применяются роликовые подшипники: с короткими цилиндрическими роликами однорядные с однобортовым внутренним кольцом; с короткими цилиндрическими роликами однорядные с безбортовым внутренним кольцом и плоским упорным кольцом.
Геометрические размеры снятых колец проверяют прибором БВ-7492−31 (БВ-7492), размеры лабиринтного кольца прибором БВ-7492М-31 (БВ-7492М), размеры наружных колец прибором «Робокон-4161», размеры роликов прибором БВ-7606−31 (БВ-7528) и прибором «Робокон-4155».
Измерения подшипников производят после выдержки их в комплектовочном отделении не менее 8 часов. Эталонные кольца аттестуют не реже одного раза в год.
Возможные неисправности роликовых подшипников, корпусов букс и условий их дальнейшего использования приведены в таблице 4.
Таблица 4 — Возможные неисправности подшипников и корпусов букс
Дефекты и повреждения подшипников качения | Условия дальнейшего использования | |
Подшипник в собранном виде | ||
Радиальный зазор меньше или больше установленной нормы | Необходимо перекомплектовать подшипник с заменой наружного кольца. | |
Осевой зазор меньше установленной нормы | Подшипник используют после зачистки торцевой поверхности нерабочего (маркированного) борта у наружных колец на значение до 0,03 мм. Зачистку производят шлифовальной шкуркой № 10 на тканевой основе, а затем № 6 с маслом или притиркой пастой ГОИ. Допускается перекомплектовать подшипник с заменой наружного кольца или роликов. | |
Наружное внутреннее кольца | ||
Рифление дорожки качения наружного кольца подшипника | Кольца используют с установкой рифленой поверхностью в нерабочую зону при длине рифленого участка не более половины длины дорожки качения | |
Поверхностная и точечная коррозия на дорожке качения наружного кольца | Кольца используют после зачистки пораженных коррозией поверхностей шлифовальной шкуркой № 6 с маслом. | |
Поверхностная и точечная коррозия на дорожке качения внутреннего кольца | Кольца используют после зачистки пораженных коррозией поверхностей шлифовальной шкуркой № 6 с маслом. | |
Задиры ''елочка'' и заусенцы фасок бортов наружных и внутренних колец | Кольца используют после зачистки фасок. Зачистку производят на приспособлении или шлифовальной шкуркой № 10, а затем № 6 с маслом. | |
Коррозионные повреждения на посадочных поверхностях наружного кольца | Кольца используют со следами коррозионных повреждений после зачистки шкуркой № 6 с маслом. | |
Коррозионные повреждения на посадочных поверхностях внутреннего кольца | Кольца используют со следами коррозионных повреждений после зачистки шкуркой № 6 с маслом. | |
Ролики и сепараторы | ||
Вмятины на поверхности качения | Ролики используют | |
Кольцевой след без разрушения поверхности металла | Ролики используют | |
Потемнение поверхности качения от серого до черного цвета | Ролики используют | |
Поверхностная и точечная коррозия на ролике | Ролики используют после зачистки пораженных коррозией поверхностей | |
Задиры ''елочка'' и заусенцы на торцах роликов | Ролики используют после зачистки пораженных поверхностей шкуркой № 6 с маслом. Снимать допускается с каждой стороны ролика слой не более 0,005 мм | |
Выпадение роликов из гнезд сепаратора | Сепараторы используют после восстановления чеканки | |
Корпус буксы | ||
Продольные задиры или риски на посадочной цилиндрической части | Корпуса используют после зачистки кромок, задиров или рисок. | |
Местная выработка на цилиндрической посадочной поверхности от проворачивания наружных колец. | Корпуса с выработкой, превышающей норму на овальность, ремонтируют. | |
Коррозия на внутренней цилиндрической части. | Корпуса используют со следами коррозии после зачистки. | |
Ослабление посадки отъемного лабиринта и его повреждение. | Корпус ремонтируют. | |
Ржавчина, заусенцы, забоины на лабиринтных проточках. | Корпуса используют после зачистки лабиринтных проточек. | |
Ремонт подшипников делится на два вида: первый — без переборки роликов, второй — с переборкой (измерением и подборкой роликов по диаметру и длине).
Первый вид ремонта
Подшипники ремонтируют без переборки роликов (без измерения роликов по диаметру и по длине) при замене и расточке сепаратора, зачистке (шлифовке) бортов колец, замене наружного или внутреннего колец, зачистке (шлифовке) дорожек качения колец.
Второй вид ремонта.
Ремонт подшипников с переборкой роликов (с измерением роликов по диаметру и длине) производят при замене роликов (независимо от количества сменяемых роликов), выпадении отдельных роликов из гнезд сепаратора вследствие повреждения чеканки, зачистке (шлифовке) образующих роликов и торцов роликов.
При втором виде ремонта подшипник полностью разбирают, все детали осматривают. При необходимости ролики и кольца шлифуют. При выпадении отдельных роликов из гнезд сепаратора проверяют диаметр и длину всех роликов и подшипник вновь собирают. При этом разность диаметров роликов в подшипнике должна быть не более 5 мкм, а разность длин роликов — не более 12 мкм.
У цилиндрических подшипников типа 42 726 и 232 726, не имеющих на торце роликов и сепаратора условного обозначения, необходимо наносить на одном из торцов сепаратора со стороны маркировки букву «Ж», а один из торцов роликов условно обозначать знаком «+», который ставят в лунке или в центре торца. Причем ролики, имеющие на торце лунку, маркируют механическим путем с помощью соответствующего приспособления. У роликов с плоскими торцами маркировку наносят с помощью кислоты, медного купороса или электрографом. Запрещается наносить знак «+» на рабочую часть торца ролика. Этот знак должен быть нанесен только в середине торца ролика.
Годные для комплектования подшипников ролики со скосами измеряют и сортируют по диаметрам в трех сечениях — в середине и по краям цилиндрической части вблизи скосов. При этом непостоянство диаметра, а также разность диаметров по краям цилиндрической части, конусность и выпуклость в среднем сечении ролика не должны превышать 5 мкм.
Ролики с рациональным контактом (бомбинированные) сортируют только по среднему диаметру. Бомбинированный ролик имеет разность диаметров не менее 20 мкм и не более 28 мкм. Измерение роликов после зачистки производят не ранее, чем через один час.
Устанавливается следующий порядок сортировки роликов:
— по среднему сечению одного из роликов, принятому за эталон для данной группы роликов, настраивают прибор на нулевое положение измерительной головки;
— остальные ролики измеряют и сортируют на группы по среднему сечению в пределах 5 мкм.
При комплектовании подшипников ролики в одном подшипнике должны быть одной группы по диаметру. Затем ролики проверяют и сортируют по длине.
Полиамидные сепараторы осматривают визуально на наличие трещин в зоне перехода перемычек к основаниям, разрывов, сколов и механических повреждений. Обточка сепараторов по наружному диаметру категорически запрещается. Растяжение сепараторов не производят.
Повреждения чеканки полиамидного сепаратора восстанавливают при помощи электропаяльника или нагретой металлической пластины путем вдавливания жала паяльника или пластины в тело перемычки до образования выступа, препятствующего выпадению роликов. Количество расчеканок должно быть не более трех на одной перемычке.
Механические повреждения полиамидного сепаратора в виде царапин и забоин длиной до 5 мм и глубиной до 1 мм допускаются без исправлений, длиной от 5 до 10 мм и глубиной до 2 мм зачищают острозаточенными предметами (нож, шабер). Трещины и отколы не допускаются.
При сборке необходимо следить за тем, чтобы маркировка на сепараторе была обращена в ту же сторону, что и маркировка на наружном кольце. В ту же сторону должны быть обращены торцы роликов со следующим условным обозначением: «+» или маркировкой в виде цифр, или с меньшей по диаметру выточкой сферической формы, или углублением диаметром 5 мм и глубиной 1 мм, или с выточкой с одной стороны ролика сферической формы.
В собранном состоянии подшипник должен провёртываться легко, без заедания и торможения. Не рекомендуется длительно его вращать без смазки.
У скомплектованного подшипника проверяют геометрические параметры на приборе «Робокон-4156».
Парные подшипники, устанавливаемые на одну шейку оси, подбирают по радиальным зазорам, а их внутренние кольца по внутренним диаметрам.
Учет отремонтированных подшипников ведется мастером (бригадиром) в журнале формы ВУ-93.
Осмотр деталей буксового узла.
Лабиринтные кольца после зачистки и промывки протирают и проверяют специальным шаблоном. На посадочных поверхностях и в лабиринте не допускаются трещины, вмятины, забоины, заусенцы и другие неисправности. Размеры проверяют в соответствии с нормами.
При полном освидетельствовании без снятия внутренних колец в случае выявления задиров на цилиндрической поверхности лабиринтного кольца производят зачистку шкуркой. Разрешается применять отремонтированные лабиринтные кольца, которые имеют маркировку «1р» и «2р» и т. д.
Крепительные и смотровые крышки после зачистки и промывки осматривают. Соединенные между собой крепительные и смотровые крышки разъединяют для замены уплотнения и вновь собирают. На крышках не допускаются трещины, вмятины, забоины, задиры, заусеницы, изгибы, перекосы и другие дефекты.
При всех видах ремонта вагонов разрешается заваривать отверстия, А в крепительных крышках с изношенной резьбой для болтов смотровой крышки и отверстий Б по технологии, утвержденной ЦВД ОАО «РЖД», с последующим их восстановлением по чертежным размерам.
Осмотр корпусов букс
После промывки корпусов букс производится протирка корпусов букс обтирочным материалом. После протирки производят зачистку внутренней посадочной поверхности буксы, упорного буртика и лабиринтной части шкуркой зернистостью № 6 с маслом для устранения коррозийных повреждений, заусенцев, и протирает обтирочным материалом дважды: сначала смоченным керосином, а затем сухим.
При осмотре букс, после их промывки, проверяется глубина отверстия и резьба под термодатчик с помощью 2-х шаблонов (рисунок 2):
— для проверки резьбы;
— для проверки глубины под термодатчик.
Углубление под термодатчик должно быть просверлено глубиной 14,5−0,1 мм (контролирующая часть шаблона должна входить в углубление до заплечиков, не допускается — зазор между заплечиками шаблона и корпусом буксы).
Резьба под термодатчик в углублении должна быть М 16×1,5 мм, при проверке резьбы в углублении под термодатчик должны соблюдаться следующие условия:
— шаблон не должен иметь люфт в резьбе;
— не допускается зазор между прокладкой шаблона и корпусом буксы (глубина резьбы -13 мм).
При несоответствии этих размеров или отсутствия второго углубления под термодатчик на корпусе буксы, то эта букса подается в механический цех для сверления отверстия, нарезки резьбы под термодатчик в соответствии с чертежами № М119 500.00.000−02 СБПКБ ЦЛ ОАО «РЖД».
На посадочной поверхности корпуса буксы после устранения коррозийных повреждений допускаются темные пятна, т. е. нельзя зачистку поверхности доводить до металлического блеска.
Измерение внутреннего диаметра корпуса буксы производится на приборе БВ-7588−31 (БВ-7588−21) на соответствие чертежным размерам и нормам, указанным в таблице 5.
Таблица 5 — Чертёжные размеры корпуса буксы
Наименование измерений и норм | Допускаемые размеры при ремонте, мм | Примечание | |
Диаметр внутренней цилиндрической части буксы из: стального литья | Проверяют в двух взаимно перпендикулярных направлениях индикаторным (или микрометрическим) нутромером с ценой деления 0,01 мм | ||
Овальность внутренней цилиндрической части для букс диаметром, мм: не более: из стального литья | 0,20 | Проверяют в двух взаимно перпендикулярных направлениях и в двух местах по длине корпуса индикаторным (или микрометрическим) нутромером с ценой деления 0,01 мм | |
Конусность внутренней цилиндрической части буксы, мм | 0,1 | Проверяют по всей длине корпуса индикаторным (или микрометрическим) нутромером с ценой деления 0,01 мм | |
Торцевое биение заднего упорного бортика буксы относительно оси посадочного отверстия | ; | Проверяют на заводах при изготовлении букс. | |
Ширина корпуса буксы по направляющим для боковой рамы тележки пассажирского вагона, мм | не менее 320±2 | Проверяют на заводах при изготовлении и при ремонте букс. | |
Разница в толщине стенок буксы, замеренная по направляющим, не более, мм | Проверяют на заводах при изготовлении и при ремонте. | ||
Разница в толщинах стенок корпусов букс по одной стороне колесной пары, более, мм | Проверяют на заводах при изготовлении и при ремонте. | ||
Корпуса букс, имеющие износ по посадочной поверхности (диаметру отверстия) выше допускаемой нормы, а также с повреждениями лабиринтной части, резьбовых отверстий, с оставшимися в буксе оторванными болтами повреждениями подлежат ремонту, а со сквозными отверстиями под термодатчики — бракуются.
Монтаж буксовых узлов Монтаж букс с роликовыми подшипниками производится в монтажном отделении в присутствии мастера или бригадира роликового участка. Колесные пары, требующие монтажа букс, одновременно устанавливают в ряд на рельсовый путь монтажного отделения.
Для букс вагонов с роликовыми подшипниками применяют железнодорожную смазку ЛЗ-ЦНИИ по ГОСТ 19 791–74 или ЛЗ-ЦНИИ (у) по ТУ 0254−307−148 820−95.
После установки корпуса буксы с подшипниками на шейку надевают плоское упорное кольцо переднего подшипника маркировкой, обращенной к передней части корпуса буксы, на нарезную часть оси навинчивают гайку М110×4 высотой 51 мм. Гайки предварительно подбирают по резьбе шейки оси для обеспечения наименьшего зазора в резьбовом соединении.
Затянуть гайку до соприкосновения с плоским упорным кольцом переднего подшипника и туго поджать при помощи гаечного ключа и молотка массой от 3 до 5 кг двумя-четырьмя ударами, прилагаемыми на плече 0,5 м до получения чистого металлического звука.
Затем в паз оси устанавливают стопорную планку, не вводя её хвостовик в шлиц гайки. Планку устанавливают в такое положение, чтобы при последующей затяжке гайки для ввода хвостовика планки в шлиц гайка повернулась бы
на половину до одной коронки. При применении гаечного ключа со стрелкой после установки гайки вручную до соприкосновения с плоским упорным кольцом её предварительно затягивают одним ударом молотка массой от 3 до 5 кг по рукоятке ключа. Затем, поддерживая одной рукой ключ, другой рукой на ключ устанавливают планку со стрелкой в резьбовые отверстия паза оси. Выставляя стрелку на нуль (риска на торце ключа) и ударяя по рукоятке ключа, затянуть гайку на угол 16 градусов (риска на торце ключа). Сняв планку со стрелкой, в паз оси устанавливают стопорную планку, не вводя её хвостовик в шлиц гайки. Ввернув один болт стопорной планки, произвести окончательную затяжку гайки для ввода хвостовика стопорной планки в шлиц гайки; при этом гайку затянуть на размер, равный половине коронки (примерно на угол не более 8 градусов).
Затяжку гайки производить только поворотом по часовой стрелке. Поворот гайки в обратном направлении, т. е. ослабление её затяжки, запрещается.
При затяжке гайки буксу слегка поворачивают для того, чтобы убедиться в отсутствии заклинивания подшипников. После этого устанавливают и закрепляют болты стопорной планки. Болты и отверстия под них смазывают смазкой. Под болты устанавливают пружинные шайбы. Болты связывают мягкой отожжённой) проволокой диаметром от 1,5 до 2,0 мм, проходящей через раззенкованные отверстия в их головках, независимо от установки пружинных шайб. Проволоку увязывают по форме цифры «8».
При торцевом креплении подшипников шайбой тарельчатой, переднюю после установки плоского упорного кольца переднего подшипника надевают на шейку оси. Тарельчатую шайбу прикрепляют к торцу шейки оси четырьмя или тремя болтами М20×60.4.8 с головкой, выполненной с ложной шайбой, на опорной поверхности ГОСТ 1759–70. При отсутствии таких болтов необходимо устанавливать новые болты с ложной шайбой на опорной поверхности. При монтаже торцевого крепления подшипников шайбой должны использоваться болты без следов коррозии. Особое внимание следует уделять состоянию месту перехода стержня болта к головке. При обнаружении задиров, выполнения перехода радиусом менее 0,8 мм или других повреждений болты к дальнейшей эксплуатации в торцовом креплении не допускаются. Поврежденные болты заменить.
Под болты правой и левой шеек оси устанавливают стопорные шайбы, на которые набивают клейма. При установлении новых болтов на торце головок необходимо ставить две последние цифры года монтажа букс размером 6×2,25 мм. При торцевом креплении шайбой тарельчатой болты М20 стопорят стопорной шайбой: Закрепляют болты М20 шайбы тарельчатой тарированным ключом усилием с крутящим моментом от 23 до 25 кгс/м. Затяжка болтов должна быть равномерной. Для этого завинчивание трех болтов производят дважды по периметру, а четырех по схеме в следующем порядке: 1−2-3−4-3−4-2−1.
Затем концы стопорной шайбы загибают клещами на грань головки каждого болта, и доводят до полного прилегания лепестков шайбы к граням головки болта.
После закрепления подшипников в осевом направлении производят установку буксовых крышек.
Между крепительной и смотровой крышками при их сборке ставят новую резиновую прокладку толщиной 3 мм. Внутренние поверхности крепительной и смотровой крышек, а также цилиндрическую посадочную поверхность крепительной крышки и соответствующую поверхность корпуса буксы, болты М20 и М12 и отверстия под них смазывают тонким слоем препаратом модификатором эМПи-1. Крышки скрепляют между собой четырьмя болтами М12, под которые устанавливают пружинные шайбы, при этом запрещается устанавливать болты с различными размерами головок. Болты затягивать с применением гаечного ключа, а болты М20 с применением динамометрического ключа с крутящим моментом от 19 до 21 кгс по схеме в следующем порядке: 1−2-3−4-3−4-2−1.
Смазку массой 0,2 кг уложить на внешнюю поверхность гайки по всему периметру и на переднюю видимую часть подшипника и уплотняют пальцами так, чтобы смазка проникла между сепаратором и бортом наружного кольца. Общее количество смазки, закладываемой в буксы, должно быть 0,8 кг, при этом смазку можно дозировать мерной емкостью вместо взвешивания.
Между торцом корпуса и фланцем крышки устанавливают новое резиновое кольцо, имеющее сечение диаметром 4 мм, фланцевую поверхность крышки смазывают смазкой из расчета заполнения всего зазора между этой поверхностью и торцом корпуса буксы после затяжки болтов. После этого буксу закрывают крышками, прикрепляемыми к корпусу болтами М20, под которые также устанавливают пружинные шайбы. Под два болта (или один болт, если это предусмотрено конструкцией) крепительной крышки буксы правой шейки оси с левой стороны устанавливают бирку.
Резиновые прокладки или резиновые кольца, бывшие в эксплуатации независимо от их состояния заменить на новые, имеющие клейма и дату изготовления.
Правильность сборки буксы контролируют по легкости ее вращения на шейке оси, которое должно быть совершенно свободным (букса вращается вручную). Допускается неравномерный зазор по всей окружности, при этом минимально допускаемый зазор 0,3 мм должен находиться в зоне расположения ушков крепительных крышек. Причинами затруднительного вращения может быть чрезмерное заполнение буксы смазкой, случайное попадание в буксу посторонних тел (металлическая стружка, тряпки и т. д.), особенно опасно отсутствие осевого разбега буксы, трение сепаратора о борт внутреннего кольца заднего подшипника или о плоское упорное кольцо переднего. Эти причины должны быть немедленно выяснены и устранены.
Вручную проверяют осевое смещение буксы. Букса должна свободно перемещаться вдоль шейки оси в пределах осевого разбега. Не допускается защемление роликов в осевом направлении.
После производства полной ревизии буксовых узлов проводить обкатку колесных пар на стенде ревизии или ремонта редукторов с частотой вращения от 250 до 270 об/мин в течение 5 минут под собственным весом колесной пары. Дату обкатки фиксировать в журнале формы ВУ-90 в графе примечание.
Буксы после монтажа окрасить серой краской. Тщательно должны быть окрашены места соединения лабиринтного кольца с предподступичной частью оси, а также предподступичная часть между лабиринтным кольцом и ступицей колеса во избежание коррозионных повреждений.
Данные монтажа заносятся в журнал формы ВУ-90.
3. Экономическая часть
3.1 Прямые расходы, связанные с производством и реализацией по вагонному хозяйству По экономическому содержанию, расходы классифицируются: на основные, общие для всех отраслей хозяйства и общие. К основным расходам относятся затраты непосредственно связанные с производственным процессом. По вагонному хозяйству они планируются по статье 6607. По этой статье, кроме заработной платы, планируются расходы на материалы, запчасти и прочее. Их учитывают с 6757 по 6765 статьи, общехозяйственные расходы связаны с организацией и управлением производства, их планируют с 6797 по 6833 статьи.
Основные расходы Статья 6607 «Деповской ремонт вагонов»
Заработная плата основных производственных рабочих. Оплата труда рабочих связанных с ремонтом и эксплуатацией вагонов, производится по повременно — премиальной и сдельно — премиальной системам. В состав среднемесячной заработной платы входят:
— тарифная ставка;
— среднемесячный приработок (при сдельной оплате труда);
— премии и доплаты.
Тарифные ставки работников железнодорожного транспорта берутся в перечне единых тарифных сеток по оплате труда работников ОАО «РЖД» (с учётом индексации, среднемесячной нормы часов). Расчёт премий выплачиваемых из фонда заработной платы, устанавливают в виде среднего процента к заработку. Расчёт годового фонда заработной платы сводят в таблицу 6.
Таблица 6 — Заработная плата
Профессия | Разряд | Человек, штук | Часовая тарифная ставка, рублей | Норма времени, час | Должностной или тарифный оклад, рублей | Доплаты | Зарплата одного рабочего в месяц, рублей. | Годовой фонд зарплаты всех работников в год, рублей | |||
За вредные условия труда, (%) | Размер премии, (%) | Сумма премии, рублей | |||||||||
Бригадир | 103,36 | 165,5 | 17 106,08 | 3421,21 | 21 895,77 | 262 749,31 | |||||
Слесарь | 89,89 | 165,5 | 14 876,79 | 2975,35 | 19 637,35 | 942 593,03 | |||||
Слесарь | 85,45 | 165,5 | 14 141,97 | 2828,39 | 18 667,39 | 672 026,27 | |||||
Слесарь | 82,58 | 165,5 | 13 666,99 | 2733,39 | 18 040,41 | 432 970,05 | |||||
Дефектоскопист | 82,36 | 165,5 | 13 630,58 | 2726,11 | 17 447,13 | 418 731,27 | |||||
Итого ОПР | 2 729 069,93 | ||||||||||
Потребность в материалах и запчастях определяется на основании норм расходов материалов и запасных частей на плановые виды и текущий ремонты пассажирских вагонов с учётом годовой программы. Полученные данные заносим в таблицу 7.
Таблица 7 Расход материалов и запасных частей по роликовому участку
Наименование материалов и запасных частей | Количество на годовую программу | Стоимость единицы, руб. | Общая стоимость, руб. | |
Болт М12×40 | 20,75 | 10 997,50 | ||
Подшипник 32 314 | 2510,50 | 502 100,00 | ||
Крышка крепительная | 1235,15 | 185 272,50 | ||
Крышка смотровая | 621,14 | 158 390,70 | ||
Сепаратор полиамидный | 115,00 | 69 000,00 | ||
Болт М 12×35 | 17,09 | 5981,50 | ||
Болт М 12×60 | 23,50 | 4700,00 | ||
Шайба граверная Ш20 | 8,50 | 2550,00 | ||
Шайба граверная Ш12 | 8,20 | 1476,00 | ||
Планка стопорная | 90,97 | 5458,20 | ||
Кольцо резиновое Ш250 | 4,18 | 3344,00 | ||
Прокладка буксовая Ш250 | 7,79 | 6232,00 | ||
Наждачная бумага № 6 | 123,87 | 12 387,00 | ||
Наждачная бумага № 10 | 173,74 | 17 374,00 | ||
Лак БТ | 60,65 | 9097,50 | ||
Эмаль серая | 75,20 | 48 880,00 | ||
Керосин | 12,58 | 1383,80 | ||
Корпус буксы | 14 368,5 | 143 685,00 | ||
Смазка ЛЗ ЦНИИ | 8,8 | 27 250,15 | 239 801,32 | |
Модификатор ЭМПИ-1 | 54,07 | 7029,10 | ||
Салфетка техническая | 38,12 | 8005,20 | ||
Итого: | 1 443 145,32 | |||
Неучтённые запасные части, и материалы принимаются в размере 2% от заработной платы основных производственных рабочих и учитываются как прочие расходы.
Сложив количество расходов на запасные части и материалы, и неучтённые материалы и запчасти получим сумму необходимую для выполнения плана годового ремонта роликового участка.
1 443 145,32 + 49 326,41 = 1 492 471,73 рублей Сложив выплаты на заработную плату и приобретение необходимых материалов, получим сумму прямых расходов связанных с выполнением плана годового ремонта по роликовому участку.
2 729 069,93+ 1 492 471,73 = 4 221 541,66 рублей Вывод: произведя расчёты и сложив выплаты по заработной плате и на приобретение запасных частей и материалов, получили сумму прямых расходов, связанных с производством и реализацией по вагонному хозяйству, которая составила — 4 221 541,66 рублей
3.2 Расходы, общие для всех мест возникновения затрат и видов работ Статья 6757 «Дополнительная заработная плата и отчисления на социальное страхование рабочих»
По этой статье учитываем заработную плату за время, не проработанное на производстве, неоплачиваемое им и другие выплаты по производственному персоналу (оплата очередных отпусков, компенсаций за неиспользованный отпуск, льготных часов подросткам, перерыв в работе кормящим матерям). Составляет 7% от заработной платы основных производственных рабочих.
Расходы на оплату прочих невыходов, на работу по уважительным причинам 3% от заработной платы основных производственных рабочих с учетом доплат на отпуск Отчисления на социальное страхование рабочих составляет 5,4% от заработной платы основных производственных рабочих и всех доплат.
Сложив все отчисления, получим сумму необходимую на дополнительную заработную плату и социальное страхование.
172 642,44 + 79 168,89 + 146 779,12= 398 590,45 рублей Статья 6759 «Отчисления на социальные нужды производственного персонала»
Составляют (страховые взносы): пенсионный фонд 26%, фонд социального страхования 5,4% + 1,4% на увечье. Медицинское страхование 3,6%, фонд занятости населения 1,5%.
Общая сумма отчислений на социальные нужды составляет 37,9% от годового фонда заработной платы основных производственных рабочих.
Статья 6758 «Расходы по форменной одежде»
Расходы по форменной одежде определяются в зависимости от числа работников получающих ее со скидкой. Размеры скидки, срока носки и стоимости. Работникам старшего и среднего состава должностные оклады, которых не превышают 4тысяч рублей в месяц, фирменная одежда выдается со скидкой в размере 20% от ее стоимости, младшему и рядовому составу, получающему бесплатную спецодежду форменная одежда выдается со скидкой 40%, а не получающим бесплатной одежды со скидкой 50%.
Статья 6761 «Расходы по технике безопасности и производственной санитарии»
По этой статье планируются расходы по содержанию дезинфекционных камер, умывальников, душевых на производстве, сушильных шкафов для спецодежды и другие, связанные с охранной труда и составляет 5% от фонда заработной платы.
Таблица 8. Расходы на спецодежду
Спецодежда | Списочное количество получающих спецодежду, человек | Стоимость спецодежды, рублей | Срок носки, месяцы | Сумма износа спецодежды в год, рублей | ||
единица | общая | |||||
Костюм х/б | 1150,46 | 13 805,52 | 13 805,52 | |||
Каска защитная | 286,12 | 1144,48 | до износа | 1144,48 | ||
Ботинки рабочие | 480,21 | 5762,52 | 5762,52 | |||
Очки защитные | 177,95 | 2135,40 | до износа | 2135,40 | ||
Рукавицы х/б | 11,50 | 138,00 | 1656,00 | |||
ИТОГО | 24 509,92 | |||||
Рассчитанную сумму учитывают по элементу затрат «Материалов», прочие расходы не капитального характера связанные с охраной труда, определяют в размере 3% от заработной платы основных производственных рабочих Статья 6768 «Обслуживание производственных зданий и сооружений»
Расходы по этой статье состоят из затрат на электроэнергию, на освещение, топливо, материалы на содержание здании и сооружений и прочих расходов.
Стоимость электроэнергии на освещение подсчитывается исходя и площади производственного участка или отделения, по формуле
(16)
где S — площадь производственного участка, метров;
Тr — годовое число часов осветительной нагрузки (для депо 2250), часов;
Ксп — коэффициент спроса = 0,8;
Кэкс — коэффициент экономии электроэнергии = 0,85−0,9;
Сэ — цена 1кВт электроэнергии, рублей;
h — часовая норма расхода электроэнергии на м2 = 11Вт.
Стоимость топлива, для отопления помещения рассчитывается по формуле Этоп = б Ч Тотп Ч gотп ЧVзд Ч (tв-tн) Ч КэксЧ КсмЧ Ст Ч 10-6, (17)
где б — коэффициент, учитывающий вид топлива = 0,23;
Тотп — число часов отопительного сезона = 3980, часов;
gотп — часовой расход тепла на м3 = 0,8 Вт/м3;
Vзд — объём здания, метров;
tв, tн — внутренняя и наружная температура воздуха (tв= 16°С, tн = -16°С), градус;
Кэкс — эксплуатационный коэффициент = 1,25;
Ксм — коэффициент сменности = 0,85;
Ст — цена 1 тонны топлива, рублей.
Этоп = 0,23Ч3980Ч0,8Ч2160Ч (16 — (-16))Ч1,25Ч0,85Ч14 500Ч10-6 = 24 369,77рублей Расходы на «материалы по содержанию зданий и сооружений» можно принять в размере 10% суммы расходов на топливо и электроэнергию.
По элементу затрат «Прочие» планируют стоимость воды на бытовые нужды, учитывая расходы на 1 работающего по формуле
(18)
где б — удельный расход воды на одного работающего = 65, литров;
Rяв — явочное число работников, человек;
Dр — число рабочих дней в году, дней;
Свод — цена 1 м3 воды, рублей.
Статья 6766 «Ремонт зданий и инвентаря»
Расходы на текущий ремонт зданий принимается в размере 1,5% от их стоимости, которая определяется по формуле Сзд = а Ч Vзд, (19)
где, а — стоимость 1 м3 здания;
Vзд — объем здания.
Сзд = 220 Ч 2160 = 475 200,00 рублей Расходы на текущий ремонт инвентаря принимаются в размере 5% от его стоимости.
Статья 6771 «Амортизация производственных основных средств»
По этой статье учитывают амортизационные отчисления на капитальный ремонт и полное восстановление основных средств непосредственно участвующих в процессе производства (здания и оборудование).
Годовая сумма амортизационных отчислений на полное восстановление и капитальные ремонт здания и оборудования, определяется по формуле
(20)
где Сзд, Соб — балансовая стоимость здания и оборудования, рублей;
Нзд, Ноб — норма амортизации в процентах (зданий — 2,6%; оборудования — 12,5%).
Статья 6765 «Содержание и ремонт оборудования»
При этой статье учитывают стоимость силовой электроэнергии для производственных целей, а также расходы на обмывку вагонов и деталей перед постановкой в ремонт. Стоимость электросиловой энергии определяют по мощности выбранного и установленного оборудования по формуле Эсил = Сэл Ч 1,2 Ч Кспэл Ч Руст Ч Fоб Ч mcm Ч з, (21)
где Сэл — стоимость 1 кВт/ч, рублей;
1,2 — коэффициент, учитывающий потери электроэнергии сети;
Кспэл — средний коэффициент спроса = 0,35;
Руст — установленная мощность оборудования, кВт;
Fоб — годовой фонд времени работы оборудования в одну смену, часов;
mcm — число смен работы оборудования, смен;
з — коэффициент загрузки оборудования = 0,75.
Эсил = 3,40 Ч 1,2 Ч 0,35 Ч 6,1 Ч1871,5 Ч 1 Ч 0,75 = 12 226,69 рублей Расходы на воду для обмывки деталей и узлов для участков, где есть моечные машины, рассчитываются по формуле
(22)
где ?Q — расход воды на обмывку колёсной пары = 0,025 м3/час;
Kсп — коэффициент спроса воды = 0,75;
Fоб — действительный годовой фонд времени работы оборудования;
j — коэффициент учитывающий утечку воды = 1,1;
Свод — стоимость 1 м3 воды, рублей.
Полученную сумму умножаем на годовую программу колёсного отделения и получаем расходы на воду для обмывки деталей.
4393Ч0,72 = 3162,96 рублей Расходы на сжатый воздух пневмогайковёртов
Qвоз = (60Ч Fоб Ч 1.5 Чn Ч Ксп Ч qсв + V Ч Nкол) Ч Своз, (23)
где 60 — минут в 1 часе;
Fоб — действительный годовой фонд времени работы оборудования;
1,5 — коэффициент учитывающий потери воздуха;
n — количество потребителей;
Ксп — коэффициент спроса для пневмоинструмента = 0,2−0,4;
qсв — количество сжатого воздуха потребляемого единицей оборудования = 0,8−1,2;
V — расход сжатого воздуха на полный цикл работ = 0,8;
Nкол — годовая программа колёсного отделения;
Своз — стоимость 1 м3 сжатого воздуха, рублей.
Qвоз = (60Ч 1871,5 Ч 1.5 Ч2 Ч 0,2 Ч 0,8 + 0,8 Ч 4393) Ч 0,35 = 20 094,76 рублей
3.3 Общехозяйственные расходы Статья 6797 «Изобретательство и рационализация»
По этой статье учитываются вознаграждения авторам изобретений и рационализаторских предложений. Принимаются в размере 1% от общей заработной платы работников участка Статья 6798 «Подготовка кадров»
Расходы принимаются в размере 0,1% от общего фонда заработной платы Статья 6809 «Отчисления от фонда оплаты труда»
Расходы по этой статье рассчитываются от общего фонда оплаты труда работников на социальное страхование 4%, пенсионный фонд 26%, медицинское страхование 3,6%. На расчеты по средствам обязательного страхования от несчастного случая на производстве и профессиональных заболеваний 2%
Статья 6830 «Зарплата аппарата управления»
По этой статье учитывается основная месячная заработная плата и годовой фонд основной заработной платы мастера.
Дополнительная заработная плата аппарата управления составляет 2% от основной заработной платы мастера Статья 6831 «Командировки аппарата управления»
Расходы по этой статье принимаются в размере 2,5% от фонда заработной платы мастера Статья 6833 «Прочие расходы по содержанию аппарата управления»
Расходы по этой статье принимаются в размере 0,5% от суммы основных расходов В плане эксплуатационных расходов спланируем сумму денежных средств, необходимую для выполнения производственной программы колёсного отделения.
Все рассчитанные выше затраты сводим в таблицу 9 плана эксплуатации по статьям расходов и соответствующим элементам затрат.
3.4 Расчет себестоимости Основные расходы депо относятся к определенному виду продукции непосредственно. Основные расходы общие для всех отраслей хозяйства и оборота распределяются по измерителям работы пропорционально заработной плате, учтенной по этим измерителям в основных расходах.
После этого все виды расходов суммируются по каждому измерителю работы.
Плановая себестоимость продукции определяется по формуле
(24)
где Э — общая стоимость расходов по плану депо, рублей;
Nрол — величина измерителя продукции, подшипник.
Таблица 9 — Эксплуатационные расходы
№ статьи | Наименование статьи | Контингент, человек | Зарплата, рублей | Расходы в рублях | |||||
Материалы и запасные части | Топливо | Электроэнергия | Прочие | Всего | |||||
Основные расходы | |||||||||
Деповской ремонт пассажирских вагонов | 2 729 069,93 | 1 443 145,32 | 49 326,41 | 4 221 541,66 | |||||
Итого | 2 729 069,93 | 1 443 145,32 | 49 326,41 | 4 221 541,66 | |||||
Расходы, общие для всех отраслей хозяйства | |||||||||
Дополнительная зарплата и отчисления на социальные нужды | 398 590,45 | 398 590,45 | |||||||
Отчисления на социальные нужды производственного персонала | 934 735,51 | 934 735,51 | |||||||
Расходы по форменной одежде | 24 509,92 | 24 509,92 | |||||||
Расходы по технике безопасности и производственной санитарии | 136 453,49 | 73 989,10 | 210 442,59 | ||||||
Обслуживание производственных зданий и сооружений | 5011,96 | 24 396,77 | 25 749,90 | 3612,37 | 58 711,00 | ||||
Ремонт зданий и инвентаря | 18 712,03 | 18 712,03 | |||||||
Амортизация основных производственных средств | 41 315,27 | 41 315,27 | |||||||
Таблица 10 — Калькуляция себестоимости единицы продукции
Измеритель | Показатель | |
Объём работы, подшипник | ||
Основные расходы, рублей | 4 221 541,66 | |
Расходы, общие для всех мест возникновения затрат и видов работ, рублей | 1 722 501,18 | |
Общехозяйственные расходы, рублей | 1 033 350,52 | |
Всего расходов, рублей | 6 977 393,36 | |
Плановая себестоимость, рублей | 397,07 | |
4. Охрана труда
4.1 Требования безопасности к технологическому процессу
При ремонте должны выполняться требования ГОСТ 12.3.002.
Запасные части, и материалы доставляются на производственный участок в производственной таре, отвечающей требованиям ГОСТ 12.3.010. Перемещения грузов должны соответствовать требованиям ГОСТ 12.3.020.
Проходы и транспортные проезды должны быть свободными и иметь габаритные полосы безопасности.
Освидетельствование и эксплуатация грузоподъемных механизмов и вспомогательных приспособлений должны удовлетворять:
— правилам устройства и безопасности эксплуатации грузоподъемных кранов ГОСТ 12.2.071;
— инструкции по безопасному ведению работ для стропальщиков, обслуживающих грузоподъемные краны ГОСТ 12.3.009.
Все производственное оборудование должно отвечать требованиям ГОСТ 12.2.003, ГОСТ 12.2.022.
Состояние воздушной среды на производственных участках должно соответствовать требованиям ГОСТ 12.1.005.
Коллективные и индивидуальные средства защиты работающих должны отвечать требованиям ГОСТ 12.4.011.
Мероприятия по ограничению шума должны отвечать требованиям ГОСТ 12.1.003.
При погрузке и разгрузке материалов, запасных частей и изделий должны соблюдаться требования ГОСТ 12.3.009.
На производственных участках, в отделениях и на рабочих местах имеются местные инструкции по охране труда (ИОТ) и технике безопасности.
На рабочих местах действуют местные инструкции по охране труда.
Общие требования безопасности
Местная инструкция токарей, прессовщиков, маляров, устанавливает основные требования безопасности при ремонте колёсных пар.
К работе по ремонту колёсных пар допускаются мужчины не моложе 18 лет, прошедшие при поступлении на работу предварительный медицинский осмотр, вводный и первичный инструктаж на рабочем месте, обучение, стажировку и проверку знаний.
В процессе работы работники должны проходить повторный инструктаж не реже 1 раза в 3 месяца, и внеплановый согласно поступления телеграммных указаний. Работники, занятые на работах во вредных и опасных условиях труда периодический медицинский осмотр.
Данные работники должны знать:
— действие на человека опасных и вредных факторов, возникающих во время работы;
— правила оказания первой (доврачебной) помощи;
— требования техники безопасности, производственной санитарии и пожарной безопасности.
Работники должны:
— выполнить работу, входящую в его обязанности или поручение мастера;
— владеть безопасными приёмами труда;
— содержать в исправном состоянии и чистоте инструмент, приспособления, инвентарь, средства индивидуальной защиты;
— внимательно следить за сигналами машиниста крана и мастера;
— быть предельно внимательными, следовать только по установленным маршрутам, проходам и переходам;
— соблюдать требования правил внутреннего трудового распорядка.
Запрещается:
— находиться под поднятым грузом и перемещаться под грузом;
— наступать на электропровода и кабели, прикасаться к оборванным проводам;
— находиться на территории депо в тех местах, на которых имеется знак «Осторожно негабаритное место», а также находиться ближе 2 м от пути, на которых производится установка или уборка вагонов при маневровой работе;
— работать в порванной, неисправной, замазученной спецодежде и спецобуви и средств индивидуальной защиты;
— приступать к работе на неисправном оборудовании, неисправном инструментом.
При работе на станке необходимо соблюдать следующие требования:
— тщательно проверять крепление обрабатываемой заготовки;
— перед уборкой и чисткой станок отключать от электросети;
— не убирать стружку от станка во время его работы;
— замеры обрабатываемой заготовки производить только при остановленной планшайбе;
— не работать на станке с неисправным электрооборудованием и не производить никакого ремонта на подключенном к сети станке;
— не оставлять на планшайбе посторонние предметы;
— запрещается работать на станке, у которого отсутствует заземление, не установлены ограждающие устройства;
— во время работы станка не брать и не производить через работающий станок какие — либо предметы, не подтягивать болты, гайки и производить другие работы.
Не прикасаться к кислородным баллонам руками, загрязнёнными маслом.
Знать и использовать средства для пожаротушения;
Своевременно убирать в специальную тару ветошь, замасленную и замазученную.
Требования гигиены и производственной санитарии.
Культура производства — это точное соблюдение технологических режимов и регламентов, выполнение всех санитарных требований и правил, поддержание в исправности технологического оборудования.
Для плодотворного, без аварийного труда, наряду с применением исправной спецодежды и средств индивидуальной защиты, содержания в чистоте рабочего места и инструмента, необходимо соблюдать рациональный режим труда и отдыха, правильную организацию отдыха во время работы, соблюдение рационального питьевого режима и режима питания.
Содержание рабочего места
Рабочие места и проходы к ним следует содержать в чистоте, не допуская загромождения их запасными частями (оси и колёса) и постоянными предметами;
Обтирочный материал необходимо складывать в металлические ящики с плотно, закрывающимися крышками;
Детали и инструмент размещать так, чтобы работать с ними не вызывала лишних движений. Детали и инструмент укладывать в местах, исключающих их падение.
Перед использованием приставных лестниц или лестниц стремянок проверить наличие на них тетивах инвентарного номера, дата следующего испытания, принадлежность цеху (участку), на тетивах — наличие резиновых наконечников (шипов) и стяжек, на ступеньках и тетивах — отсутствие сколов и трещин.
У стремянок проверить исправность устройства от самопроизвольного сдвига.
Запрещается применять лестницы с истекшим сроком испытания, сбитые гвоздями, без скрепления тетивы стяжками и врезками ступенек в тетивы.
При работе на приставной лестнице, внизу должен находиться второй работник в защитной каске, страхующего на лестнице.
4.2 Требования пожарной безопасности
На основании требований Правил пожарной безопасности на железнодорожном транспорте (ЦУО / 112), Правил пожарной безопасности в Российской Федерации (ППБ 01 — 03) и устанавливает общие требования пожарной безопасности на территории, в зданиях и сооружениях принадлежащих предприятию и являются обязательной для исполнения всеми работниками предприятия. Лица, виновные в нарушении Инструкции о мерах пожарной безопасности несут уголовную, административную, дисциплинарную или иную ответственность в соответствии с действующим законодательством.
Во всех производственных и вспомогательных помещениях на видных местах должны быть вывешены таблички с указанием номера телефона вызова пожарной охраны «01», план эвакуации на случай пожара:
— определены и оборудованы места для курения;
— определены места и допустимое количество хранения запасных частей и готовой продукции;
— установлен порядок уборки горючих отходов, хранение промасленной одежды;
— определен порядок обесточивания электрооборудования в случае пожара и по окончании рабочего дня;
— порядок осмотра и закрытия помещений после окончания работы;
— действия работников при обнаружении пожара;
— определен порядок и сроки прохождения противопожарного инструктажа и занятий по пожарно-техническому минимуму, а также назначенные ответственные за их проведение.
В помещениях зданий и сооружений запрещается:
— хранение и применение баллонов с газами и других взрывопожарных веществ и материалов;
— устраивать склады горючих материалов;
— проводить отогревание замерзших труб паяльными лампами и другими способами с применением открытого огня;
— оставлять неубранным промасленный обтирочный инвентарь и материалы по окончании работ.
Для сбора использованных обтирочных материалов необходимо устанавливать металлические ящики с плотно закрывающимися крышками.
Все двери эвакуационных выходов должны свободно открываться в сторону выхода из помещений.
Все работники должны допускаться к работе только после прохождения противопожарного инструктажа, а при изменении специфики работы проходить дополнительное обучение, по предупреждению к тушению возможных пожаров.
4.3 Экологическая безопасность
Под охраной окружающей среды понимается система мер, направленных на поддержание взаимодействия человека с окружающей средой. Обеспечивающее сохранение и восстановление природных богатств, рациональное использование природных ресурсов, прямого и косвенного влияния результатов деятельности общества на природу и здоровье человека.
Важнейшим мероприятием по борьбе с загрязнением атмосферного воздуха вредными веществами является уменьшение их выделения в источниках образования. Этому служат механизация и автоматизация производственных процессов, уплотнение, герметизация и вакуумитизация оборудования, создание поточных и непрерывных технологических линий, замена вредных летучих веществ менее вредными не летучими, а твердого топлива — газообразными и т. д.
На железнодорожном транспорте наибольшую опасность в отношении загрязнения поверхностных источников питьевого назначения представляют локомотивные, вагонные депо и вагоноремонтные заводы, шпалопропиточные заводы, промыво — пропарочные и дезинфекционно-промывочные станции, рельсосварочные поезда, литейно-механические, электрические и другие производства.
Обезвреживание сточных вод — важная санитарно-техническая проблема, от решения которой зависят безопасное водопользование населения и развитие живого мира, рек, озёр, водохранилищ. Поэтому при осуществлении санитарного контроля исследуют сточные воды и воды водоемов на содержание многочисленных химических веществ, оценивают их запахи, прозрачность или щелостность.
В зависимости от степени и качества загрязнений применяют разные способы очистки сточных вод.
Объектами санитарной охраны почвы являются балластная призма железнодорожного полотна, территория станций, промышленных объектов и железнодорожных посёлков.
Почва загрязняется промышленными и бытовыми отходами, причем интенсивность загрязнения зависит от интенсивности образования и степени обезвреживания этих отходов. Большой урон почве наносят ядохимикаты.
Организация и руководство работой по вопросам охраны природы и рационального использования природных ресурсов в РЖД возложены на специальный отдел, который является структурным подразделением главного управления по безопасности движения и экологии. Отдел контролирует проводимую управлениями РЖД работу по охране природы. В своей деятельности отдел руководствуется действующим законодательством, приказами и указаниями РДЖ, главного управления по безопасности движения и экологии.
Разработка и внедрение новых технологических процессов на железнодорожном транспорте и в транспортном строительстве связаны с необходимостью повышения скорости движения поездов.
Увеличения пропускной способности на железных дорогах, улучшения условий труда работающих, повышения комфортных условий проезда пассажиров. При этом должны быть созданы также условия, при которых решение вышеуказанных задач не будет отрицательно влиять на природную среду. Вместе с тем при строительстве и ремонте пути возникает опасность загрязнения окружающей среды, особенно при ремонте пути.
При работе щебнеочистительных машин возникает высокая запыленность, причем пыль содержит не только силиций, но и загрязнена бактериями, пестицидами, гербицидами, которые сбрасываются на путь со сточными канализационными водами пассажирских и грузовых поездов, интенсивность движения которых на сети железных дорог весьма высока.
Заключение
Дипломный проект выполнен в соответствии с заданной темой: «Организация работы роликового участка пассажирского вагоноремонтного депо по проведению полной ревизии», и состоит из пояснительной записки и графической части.
Пояснительная записка содержит данные по трем разделам: техническому, индивидуальному и экономическому.
В технической части представлены пояснения и расчет по работе роликового участка: фронт работ, ритм, такт, производственная мощность.
В индивидуальной части рассмотрены вопросы по организации работы в роликовом участке: программа ремонта, площадь участка, штат работников, мероприятия по охране труда и технике безопасности.
В экономической части представлены расчеты штатной ведомости и плана эксплуатационных расходов.
В период выполнения дипломного проекта я посещал вагонное депо и ознакомился с типовыми технологическими процессами работы депо и отделения по ремонту колесных пар. Эти сведения были использованы при выполнении дипломного проекта, мною были сделаны расчеты и составлен план эксплуатационных расходов.
транспортный вагоноремонтный оборудование
Список использованных источников
1. Быков Б. В. Технология ремонта вагонов / Б.В., В. Е. Пигарев — М.: Желдориздат, 2001. — 559с.
2. Стрекалина, Р. П. Экономика и организация вагонного хозяйства / Р. П. Стрекалина — М.: Маршрут, 2003. — 436с.
3. Организация, планирование и управление на вагоноремонтных предприятиях / под редакцией Меланина В. Н. — М.: ГОУ «УМЦ ЖДТ», 2008. — 383с.
4. Клочкова Е. А. Охрана труда на железнодорожном транспорте / Е. А. Клочкова — М.: Маршрут, 2004, — 413с.
5. Лукин В. В. Вагоны. Общий курс/ В. В. Лукин, П. С. Анисимов, Ю. П. Мотовилов — М.: Маршрут, 2004. — 424с.
6. Мотовилов К. В. Технология производства и ремонта вагонов/ К. В. Мотовилов — М.: Маршрут, 2003. — 382с.
7. Инструктивные указания по эксплуатации и ремонту вагонных букс с роликовыми подшипниками 3-ЦВРК — М.: 2001. — 101с.