Разработка методики определения температуры поверхности деталей для совершенствования технологий электроконтактного нагрева и сварки металлов
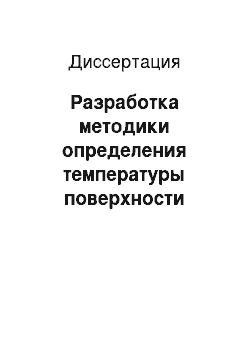
Диссертация
Разработанная методика расчета температуры поверхности деталей является эффективным инструментом, позволяющим точнее определять режимы при разработке новых технологий электроконтактного нагрева и сварки металлов, корректировать существующие и совершенствовать сварочное оборудование. Применение предлагаемой методики способствует сокращению числа бракованных деталей при их восстановлении… Читать ещё >
Содержание
- Глава 1. АНАЛИЗ СОВРЕМЕННОГО СОСТОЯНИЯ ПРОБЛЕМЫ, ПОСТАНОВКА ЦЕЛИ И ЗАДАЧ ИССЛЕДОВАНИЯ
- 1. 1. Способы электроконтактного нагрева и сварки металлов, проблемы их совершенствования
- 1. 2. Основные средства и методы определения температуры при электроконтактном нагреве и сварке, в других родственных процессах
- 1. 2. 1. Средства и методы измерения температуры
- 1. 2. 2. Расчетные методы определения температуры
- 1. 3. Предпосылки к использованию обратных задач теплопроводности для совершенствования технологий электроконтактного нагрева и сварки металлов
- Выводы по главе, постановка цели и задач исследования
- Глава 2. МОДЕЛИРОВАНИЕ И ИДЕНТИФИКАЦИЯ ТЕПЛОВЫХ ПРОЦЕССОВ ПРИ ЭЛЕКТРОКОНТАКТНОМ НАГРЕВЕ И СВАРКЕ МЕТАЛЛОВ
- 2. 1. Определение температуры поверхности детали по результатам измерений температуры на ее двух различных глубинах
- 2. 1. 1. Расчет температуры поверхности детали без учета температурной зависимости ее теплофизических характер и сти к
- 2. 1. 2. Расчет температуры поверхности детали с учетом температурной зависимости ее теплофизических характеристик
- 2. 2. Одновременное определение теплового потока и температуры поверхности медного электрода при электроконтактном нагреве и сварке металлов
- 2. 3. Теорема устойчивости алгоритма, основанного на методе квазиобращения
- 2. 1. Определение температуры поверхности детали по результатам измерений температуры на ее двух различных глубинах
- Выводы
- Глава 3. МЕТОДИКА ЭКСПЕРИМЕНТАЛЬНЫХ ИССЛЕДОВАНИЙ
- 3. 1. Общая методика
- 3. 2. Экспериментальные установки для электроконтактной 71 диффузионной сварки
- 3. 3. Выбор материала, образцов и присадочного материала для проведения исследований
- 3. 4. Методика регистрации основных параметров процесса 81 сварки
- 3. 5. Методика измерения температур
- 3. 6. Методика численных экспериментов
- 3. 7. Методика сопоставления основных качественных показателей полученных покрытий
- 3. 8. Частные методики
- 3. 8. 1. Методика определения прочности сцепления слоя с основой
- 3. 8. 2. Определение микропористости полученного слоя
- 3. 8. 3. Оценка микроструктуры и микротвердости покрытий и основы
- 4. 1. Сопоставление результатов измерения и расчета температуры поверхности при сварке на стальные 103 образцы
- 4. 1. 1. Линейный случай
- 4. 1. 2. Нелинейный случай
- 4. 2. Результаты расчета температуры поверхности медного электрода
- 4. 3. Сопоставление основных качественных показателей покрытий
- 4. 4. Анализ микроструктуры и микротвердости покрытий и основы
- 5. 1. Методика расчета температуры поверхности деталей и рекомендации по выбору режимов процессов электроконтактного нагрева и сварки металлов
- 5. 2. Предпосылки и рекомендации по совершенствованию оборудования и технологий электроконтактного нагрева и сварки металлов
- 5. 2. 1. Рекомендации по совершенствованию конструкции и повышению ресурса электрода
- 5. 2. 2. Рекомендации по уменьшению деформаций и формированию структуры восстанавливаемых деталей
- 5. 3. Оценка общего коэффициента полезного действия электроконтактной установки
- 5. 4. Оценка экономического эффекта выполненных разработок
Список литературы
- Адамар Ж. Задача Коши для линейных уравнений с частными производными гиперболического типа. М.: Наука, 1978. — 352 с.
- Алифанов О.М. Обратные задачи теплообмена. М.: Машиностроение, 1988.-280 с.
- Алифанов О.М. Идентификация процессов теплообмена летательных аппаратов (введение в теорию обратных задач теплообмена). М.: Машиностроение, 1979.-216 с.
- Алифанов О.М., Артюхин Е. А., Румянцев С. В. Экстремальные методы решения некорректных задач. М.: Наука, 1988. — 288 с.
- Алтухов В.И. Вопросы математики и математического моделирования перспективных технологий, материалов, процессов и систем: Сб. науч. тр. // Новочеркасский государственный технический университет. Новочеркасск: НГТУ, 1997.- 124 с.
- Амелин Д.В., Рыморов Е. В. Новые способы восстановления и упрочнения деталей машин электроконтактной наваркой. М.: ВО «Агропромиздат», 1987.- 151 с.
- Андрущик Л.О., Балакшина О. Н., Ошкандеров С. П., Северянина Е. П., Швитай В. А. Особенности изменения пористости и дефектности структуры порошкового хрома при электроконтактном спекании // Порошковая металлургия. 1987. -№ 11-С. 35−38.
- Аскинази Б.М. Упрочнение и восстановление деталей машин электромеханической обработкой. -М.: Машиностроение, 1989. 197 с.
- Атанбаев С.А. Метод квазиобращения и его применение. Алматы: Изд-во «Кайнар», 1999. — 208 с.
- Бабенко Ю.И. Тепломассообмен. Метод расчета тепловых и диффузионных потоков. Л.: Химия, 1986. — 144 с.
- Бабусенко С.М., Степанов В. А. Современные способы ремонта машин. -М.: Колос, 1997.-227 с.
- Барышников С.А. Восстановление изношенных валов сельскохозяйственной техники электроконтактным напеканием металлических порошков с последующим упрочнением. Челябинск АИУ, 1997. — 129 с.
- Бахвалов Н.С., Жидков Н. П., Кобельков Г. М. Численные методы. М.: Физматлит, 2000. — 234 с.
- Бельчикова О.Г., Чижов В. Н., Шерышев В. П. Идентификация тепловых процессов при электроконтактном напекании // Пятая краевая конференция по математике: Материалы конференции. Барнаул: Изд-во АГУ, 2002. — 52 с.
- Бельчикова О.Г., Чижов В. Н., Шерышев В. П. Идентификация тепловых процессов при электроконтактном напекании // Известия АГУ: спецвыпуск. Барнаул: Изд-во АГУ, 2002. С. 92 95.
- Бельчикова О.Г., Чижов В. Н., Шерышев В. П. Совершенствование алгоритмов идентификации тепловых процессов при оптимизации режимов процессов электроконтактного нагрева // Сварочное производство. 2003. — № 4. — С. 10−14.
- Бек А. Искажающее влияние термопары на температурное поле в материалах с низкой теплопроводностью // Теплопередача. 1962. — Т. 84. — № 2. -С. 33−42.
- Богомолова Н.А. Практическая металлография. М.: Высшая школа, 1982.-272 с.
- Бодякин А.В. Разработка технологий восстановления деталей электроконтактным напеканием с одновременным термосинтезом упрочняющих частиц. Автореф. дисс. канд. техн. наук. Барнаул, 1997. — 22 с.
- Болтенков А.А. Разработка методологии прогнозирования технологических режимов электроконтактного напекания порошковых износостойких покрытий. Автореф. дисс. канд. техн. наук. Барнаул, 2002. — 18 с.
- Букмухаметова Д.Н. Нестационарные температурные поля в телах сложной геометрической формы при наличии источников (стоков) тепла, фазовых переходов в материале и теплообмена с окружающей средой // Сб. рефератов НИРИ ОКР. Сер.22, 2002, № 1.
- Бухгейм A. J1. Введение в теорию обратных задач. М.: Наука, 1988. — 215 с.
- Вабищевич П.Н. Численное моделирование. М.: Изд-во МГУ, 1993. -152 с.
- Вабищевич П.Н. Численное решение обратной задачи теплопроводности с использованием регуляризованных разностных схем // ИФЖ. 1985. — Т. 49. — № 6. — С. 963 — 965.
- Воловик E.JT. Справочник по восстановлению деталей. М.: Колос, 1981.-351 с.
- Гатапов Ф.Л. Исследование процесса электроконтактного напекания металлических порошков при восстановлении коленчатых валов двигателей. -Автореф. дис.канд. техн. наук. Челябинск, 1974. 27 с.
- Геращенко О.А. Современное состояние теплометрии в СССР // ИФЖ. 1990. — вып. 59. — № 3. — С. 516 — 522.
- Гермель В., Зигель С., Ошкандеров С. П., Андрущик Л. О., Швитай В. А. Влияние различных способов нагрева на формирование пористой структуры при спекании железа // Порошковая металлургия. 1987. — № 1. — С. 40 — 45.
- Гуляев А.И. Технология и оборудование контактной сварки. М.: Машиностроение, 1985. — 440 с.
- Гурченко П.С., Герман М. Л. Математическое моделирование температурного поля при закалке шестерен индукционным нагревом под слоем воды // ИФЖ. Т. 73. — № 2. — 2000. — С. 423 — 429.
- Давыдов А.К., Гончаров А. Е., Соловьев Г. И., Марфицын В. В. Электрошлаковая наплавка графитовым электродом // Сварочное производство. — 1997.-№ 6.-С. 47−48.
- Денисов П.В., Мирлин Г. А. Расчет температуры нагрева тонколистового металла нормально распределенным источником при точечной сварке импульсной дугой // Сварочное производство. 1974. — № 1.-С. 3 — 5.
- Дорожкин Н.Н. Упрочнение и восстановление машин металлическими порошками. Минск: Наука и техника, 1975. — 152 с.
- Есипчук A.M., Маротта А., Шараховский Л. И. О влиянии магнитного поля на теплообмен в катодном дуговом пятне // ИФЖ. Т. 73. — № 6. — 2000. -С. 1245 — 1254.
- Жук В.И., Голосов А. С. Инженерные методы определения тепловыхграничных условий по данным температурных измерений // Инженерно-технический журнал. 1975. — Т. 29. — № 1. — С. 45 — 50.
- Зайченко Ю.А., Косаревский В. В., Мамыкин С. М., Петренко Ю. М. Ин-дукционно — металлургический способ восстановления деталей // Тракторы и сельскохозяйственные машины. 2000. — № 7. — С. 14.
- Зарубин B.C. Инженерные методы решения задач теплопроводности. — М.: Энергоатомиздат, 1983. 235 с.
- Иванов А.И., Куликов А. А., Третьяков Б. С. Контрольно-измерительные приборы в сельском хозяйстве: Справочник. М.: Колос, 1984. — 352 с.
- Иванов В.К., Васин В. В., Танана В. П. Теория линейных некорректных задач и ее приложение. М.: Наука, 1978. — 121 с.
- Исаков Г. Н. Теоретические основы проектирования многослойной вспучивающейся теплозащиты с заданными свойствами // ИФЖ. Т. 73. — № 1. -2000.-С. 52−60.
- Карслоу Г., Егер Д. Теплопроводность твердых тел. М.: Наука, 1964. -487 с.
- Клименко Ю.В. Электроконтактная наплавка. М.: Металлургия, 1978. 128 с.
- Коздоба J1.A. Решение нелинейных задач теплопроводности. Киев: Наукова думка, 1976. — 136 с.
- Коздоба J1.A., Круковский П. Г. Методы решения обратных задач теп-лопереноса. Киев: Наукова думка, 1982. — 240 с.
- Кондратьев Е. Г, Кондратьев В. Е. Восстановление наплавкой деталей сельскохозяйственных машин. М.: Агропромиздат, 1989. — 95 с.
- Кочергин К.А. Контактная сварка. Л.: Машиностроение, 1987. — 240 с.
- Кривочуров Н.Т. Разработка технологии восстановления деталей электроконтактным напеканием с одновременной нитроцементацией слоя. Автор, дис.канд. техн. наук. Челябинск. 1991.-20 с.
- Кутковский С.И. Электроды контактных электросварочных машин. -Л.: Машиностроение, 1964. 112 с.
- Кутьков А.А. Износостойкие и антифрикционные покрытия. М.: Машиностроение, 1976. — 152 с.
- Лаврентьев М.М. О некоторых некорректных задачах математической физики. Новосибирск: Изд-во института математики СО АН СССР, 1962.
- Лаврентьев М.М., Романов В. Г., Шишатский С. П. Некорректные задачи математической физики и анализа. М.: Наука, 1980. — 270 с.
- Лаврентьев М.М., Савельев Л. Я. Линейные операторы и некорректные задачи. // Институт математики СО АН СССР. М.: Наука, 1991. — 331 с.
- Лагун И.М. Исследование нестационарного теплообмена методом решения обратной задачи теплопроводности // ИФЖ. 1983. — Т. 45. — № 5. — С. 797 — 802.
- Латтес Р., Лионе Ж.-Л. Метод квазиобращения и его приложения. М.: Мир, 1970.
- Лахтин Ю.М., Леонтьев В. П. Материаловедение. М.: Машиностроение, 1972.-510 с.
- Леонов А.С., Ягола А. Г. Адаптированные оптимальные алгоритмы решения некорректных задач с истокообразно представимыми решениями // Журнал вычислительной математики и математической физики. — 2001. Т. 41. — № 6. — С. 855 — 873.
- Лившиц Л.С. Металловедение для сварщиков (сварка сталей). М.: Машиностроение, 1979. -253 с.
- Линевег Ф. Измерение температур в технике. Справочник. Пер. с нем. под ред. Чариховой Л. А. М.: Металлургия. 1980. — 544 с.
- Лионе Ж.-Л. Некоторые методы решения нелинейных краевых задач. -М.: Мир, 1972.
- Лукащук С.Ю. Моделирование процессов переноса тепла и вещества в приповерхностных нанослоях твердых тел при ионном облучении // Обозрение прикладной и промышленной математики. М.: Изд-во «ТВП», 1999. С. 123 -135.
- Лушпенко С.Ф. Идентификация параметров теплопереноса методамиобратных задач теплопроводности. Автореф. дис. канд. техн. наук. Наук. Харьков, 1983.-24 с.
- Лыков А.В. Теория теплопроводности. М.: Высшая школа, 1967. -322 с.
- Лыков А.В. Тепломассообмен. Справочник. М.: Энергия, 1972. — 560с.
- Макаров В.П. Исследование и разработка технологии восстановления изношенных деталей типа «вал» электроконтактным напеканием металлических порошков. Автрореф. дис.канд. техн.наук. Челябинск, 1980. — 20 с.
- Мандрик П.А. Решение уравнения теплопроводности при смешанных граничных условиях на поверхности изотропного полупространства // Дифференциальные уравнения. 2001. — Т. 37. — № 2. — С. 238 — 241.
- Марчук Г. И. Методы вычислительной математики. М.: Наука, 1989. — 608 с.
- Мацевитый Ю.М., Лушпенко С. Ф. Идентификация теплофизических свойств твердых тел. Киев: Наукова думка, 1990. — 216 с.
- Мацевитый Ю.М., Мултановский А. В. Идентификация в задачах теплопроводности. Киев: Наукова думка, 1982. — 240 с.
- Махненко В.И., Кравцов Т. Г. Тепловые процессы при механизированной наплавке деталей типа круговых цилиндров. Киев: Наукова думка, 1976. -159 с.
- Меликов В.В., Набиев Э. С. Разработка модели численных исследований температурных полей в материале цельнокатаного вагонного колеса при автоматической многоэлектродной наплавке // Тяжелое машиностроение. -2001.-№ 8.-С. 34−35.
- Металлургические печи. / В. А. Баум и др. Под ред. М. А. Глинкова. М.: Металлургиздат, 1964.
- Металловедение и термическая обработка стали: Справ, изд. Т.1. Методы испытаний и исследования / Под ред. Бернштейна М. Л., Рахштадта А. Г. 3-е изд. перераб. и доп. — М.: Металлургия, 1983. — 325 с.
- Морозов В.А. Некоторые аспекты восстановления сигналов методом регуляризации // Вычислительные методы и программирование. 2001. — Т. 2. -№ 1.-С. 31 — 37.
- Морозов В.А. Регулярные методы решения некорректно поставленных задач. М.: Наука, 1987. — 240 с.
- Мошенский Ю.А., Воронов И. Н. Расчет температуры нагрева металла при контактно-шлаковой сварке // Сварочное производство. 1975. — № 9. — С. 5 — 7.
- Музылев Н.В. О единственности одновременного определения коэффициента теплопроводности и объемной теплоемкости // Журнал вычислительной математики и математической физики. 1983. — Т. 23. — № 1. — С. 102 — 108.
- Мусияченко В.Ф., Миходуй Л. И. Дуговая сварка высокопрочных легированных сталей. М.: Машиностроение, 1987. — 80 с.
- Никитенко Н.И. Сопряженные и обратные задачи теплопереноса. Киев: Наукова думка, 1988. — 240 с.
- Николаев А.К., Розенберг В. М. Сплавы для электродов контактной сварки. М.: Металлургия, 1978. — 96 с.
- Осовец С.В., Торопов Е. В., Прохоров А. В., Кириллов В. Л. Расчет нестационарного теплового состояния плиты при ее нагреве перемещающимся источником // ИФЖ. Т. 73. — № 4. — 2000. — С. 757 — 760.
- Патон Б.Е., Лебедев В. К. Электрооборудование для электроконтактной сварки. М.: Машиностроение, 1969. — 440 с.
- Пермяков П.П., Михайлов Н. Е., Макаров В. В. Восстановление тепловых потоков на поверхности мерзлых фунтов / Сб. Идентификация динамических систем и обратные задачи. Санкт-Петербург, 1994. С. 143 152.
- Петров Г. П., Тумарев А. С. Теория сварочных процессов. М.: Высшая школа, 1967. — 508 с.
- Поверка приборов для температурных и тепловых измерений. Сб. инструкций. — М.: Стандартгиз, 1963. 586 с.
- Поляченко А.В. Современные методы восстановления и повышениядолговечности деталей при ремонте. М.: Машиностроение, 1985. — 42 с.
- Поляченко А.В. Увеличение долговечности восстановленных деталей контактной приваркой износостойких покрытий в условиях сельскохозяйственных ремонтных предприятий. Автореф. дис.докт. техн. наук. Москва, 1984. -44 с.
- Попов Ю.П., Самарский А. А. Вычислительный эксперимент. М.: Знание, 1984. -64 с.
- Пытьев Ю.П. Математические методы интерпретации эксперимента. -М.: Высшая школа, 1989. 240 с.
- Рабинович С.Г. Погрешности измерений. Л.: Энергия, 1978. — 262 с.
- Райченко А. И Основы процесса спекания порошков пропусканием электрического тока. М.: Металлургия, 1987. — 128 с.
- Ремонт и совершенствование конструкций тракторов, автомобилей и двигателей. Науч. тр. / Челябинский институт механизмов и электрификации сельского хозяйства. 1965. Вып. 24. С. 219 — 222.
- Романов В.Г. Обратные задачи математической физики. М.: Наука, 1984.-260 с.
- Романов Д.И. Электроконтактный нагрев металлов М.: Машиностроение, 1965. — 255 с.
- Рустем С.Л. Оборудование и проектирование термических цехов. -М.: Машгиз, 1962. 588 с.
- Рыкалин Н.Н. Расчеты тепловых процессов при сварке. — Машгиз, 1951.-296 с.
- Рыкалин Н.Н. Тепловые процессы при контактной сварке. М.: Изд-во АН СССР, 1959. — 275 с.
- Самарский А.А. Вычислительный эксперимент в задачах технологии //Вестник АН СССР. 1984. — № 11.-С.17−29.
- Самарский А.А. Современная прикладная математика и вычислительный эксперимент // Коммунист. 1983. — № 18. — С.31.
- Самарский А.А., Гулин А. В. Численные методы. М.: Наука, 1989. -432 с.
- Самарский А.А., Михайлов А. Г. Математическое моделирование. -М.: Физматлит, 2001.-320 с.
- Сварка и проблемы вязкохрупкого перехода / Ларионов В. П. С78 и др.- Новосибирск: Изд-во СО РАН, 1998. 593 с.
- Сварные конструкции: достижения и перспективы нового тысячелетия: Металлургическая конференция МИС, Флоренция, Италия, 13 июля 2000 / «АО Спецэлектрод». М., 2000. — 204с.
- Сергеев Н.П. Справочник молодого сварщика на контактных машинах. М.: Высшая школа, 1979. — 205 с.
- Слиозберг С.К., Чулошников П. Л. Электроды для контактной сварки.- Л.: Машиностроение, 1972. 96 с.
- Смирнягин Г. Ф. Исследование процесса электроконтактного напека-ния порошков при восстановлении изношенных деталей ремонтируемых машин. Автореф. дис.канд. техн. наук. Челябинск, 1972. — 21 с.
- Стрелков С.М. Исследование и управление характеристиками износостойкости напеченных слоев при ремонте деталей ЭКН МП. — Автореф. Дис.канд. техн. наук. Челябинск, 1974 32 с.
- Суденков Е.Г., Румянцев С. И. Восстановление деталей плазменной металлизацией. М.: Высшая школа, 1980. — 38 с.
- Султангазин У.М., Мацевитый Ю. М., Шерышев В. П. Об одной псевдообратной задаче теплопроводности // Труды 2-ой Международной конференции: Идентификация динамических систем и обратные задачи. Санкт-Петербург, 22−25 августа 1994. Т.2.
- Султангазин У.М., Шерышев В. П. Решение задачи индукционного нагрева методом квазилинеаризации / Дифференциальные уравнения и их приложения. Алматы, 1981. 234 с.
- Таран В.Д., Гачен Ю. Г. К вопросу расчета нагрева электрода при сварке // Сварочное производство. 1972. — № 2. — С. 1 — 2.
- Тарасов Ю.С. Расчет толщины слоя при восстановлении внутренних цилиндрических поверхностей деталей ЭКН МП //Совершенствование организации и технологии восстановления изношенных деталей. Челябинск. 1984. -С. 53 -58.
- Тарасов Ю.С. Исследование электроконтактного напекания металлических порошков, как возможного способа восстановления деталей. Автореф. дис.канд. техн. наук. Челябинск, 1979. — 24 с.
- Теория сварочных процессов / Под ред. В. В. Фролова. М.: Высшая школа, 1988. — 552 с.
- Теплофизические измерения и приборы / Под ред. B.C. Платунова. -Л.: Машиностроение, 1986. 256 с.
- Технология и оборудование контактной сварки: Учебник для машиностроительных вузов / Б. Д. Орлов, А. А. Чакалев, Ю. В. Дмитриев и др.- Под общ. Ред. Б. Д. Орлова 2-е изд. перераб. и доп. — М.: Машиностроение, 1986. — 352 с.
- Тимошенко В.П. Разработка технологии индукционной наплавки с регулируемым тепловложением. Автореф. дис. на соиск. учен, степени канд. техн. наук / Урал, политехи, ин-т им. С. М. Кирова. Барнаул. 1989. — 20 с.
- Тихонов А.Н., Арсенин В. Я. Методы решения некорректных задач. -М.: Наука, 1986.-288 с.
- Тихонов А.Н., Гласко В. Б. К вопросу о методах определения температуры поверхности тела // ЖВМ И МФ. 1967. — Т. 7. — № 4. — С. 910 — 914.
- Тихонов А.Н., Кальнер В. Д., Гласко В. Б. Математическое моделирование технологических процессов и метод обратных задач в машиностроении. -М.: Машиностроение, 1990. 264 с.
- Ульман И.Е., Тарасов Ю. С., Чижов В. Н. Определение прочности сцепления слоя, напеченного на чугунные цилиндрические детали. / Эксплуатация и ремонт машинно-тракторного парка. Новосибирск: АСХИ, 1981. С. 54 — 58.
- Уманский В.Б., Маняк JI.K. Новые способы упрочнения деталей машин. Донецк: Донбасс, 1990. — 144 с.
- Федоренко Р.Г. Введение в вычислительную физику. М.: Изд-во МФТИ, 1994.-528 с.
- Федоренко И. Я. Методология компьютерного эксперимента в инженерных задачах // Вестник АГАУ. 2002. -№ 2.-С.4−7.
- Физические основы электротермического упрочнения стали / В. Н. Гриднев, Ю. Я. Мешков, С. П. Ошкадеров и др. Киев: Наук, думка, 1973. — 335 с.
- Фундаментальные проблемы теории точности / Под ред. В. П. Булатова, И. Г. Фридлендера. СПб.: Наука, 2001. — 504 с.
- Хольм Р. Электрические контакты. Изд-во иностр. лит., 1961.
- Черноиванов В.И., Андреев В. П. Восстановление деталей сельскохозяйственных машин. М.: Колос, 1983. — 288 с.
- Чернышев В.П. Наплавка деталей ходовой части гусеничных тракторов // Техника в сельском хозяйстве. 2000. — № 4. — С. 12 — 14.
- Чижов В.И. Исследование и разработка технологии чугунных коленчатых валов электроконтактным напеканием. Автор. дисс.канд. техн. наук. -Челябинск, 1982.-21 с.
- Чижов В.Н., Борисенко В. А. Определение микропористости слоя, напеченного на высокопрочный чугун // Труды ЧИМЭСХ. Челябинск, 1980. вып. 166.-С. 59−63.
- Чижов В.Н. К определению параметров процесса электроконтактногонапекания металлических порошков с использованием теорий подобия и размерностей // Труды Алтайского с.-х. ин-та. Барнаул, 1979. — Вып.36. С. 43 -48.
- Чижов В.Н. Фактическая площадь механического холодного контакта // Проблемы агропромышленного комплекса. Т. 2. Вестник алтайской науки. Вып. 1. Барнаул: Изд-во Алт. гос. ун-та. 2001. — С. 159 — 161.
- Чижов В.Н., Болтенков А. А. Прогнозирование режимов электроконтактного напекания металлических порошков / Стратегическое направление регионального развития Российской Федерации: Материалы всерос. науч.-практ. конф.: Омск, 1999. С. 218 219.
- Чижов В.Н., Электроконтактный нагрев как перспективный инструмент для создания технологий в ремонтном производстве / Повышение устойчивости АПК Алтайского края: Материалы региональной науч.-практ. конф. -Барнаул: Изд-во АГАУ, 2000. С. 154 155.
- Чулошников П.Л. Контактная сварка. — М.: Машиностроение, 1977. — 143 с.
- Щелканов В.В. Проблемы и перспективы метрологического обеспечения в области измерения температуры // Энергетик. 2002. — № 5. — С. 10 — 12.
- Шерышев В.П. Моделирование и идентификация процессов теплопе-реносов с использованием концепции сосредоточенной емкости. Автореф. дисс. .док. техн. наук. Харьков: ИПМаш АН Украины, 1996. — 24 с.
- Шишатский С.П. Об одном методе приближенного решения некорректной задачи Коши для эволюционного уравнения. В кн.: Математические проблемы геофизики. — Новосибирск: ВЦ СО АН СССР, 1972, вып. 3, С. 216 -228.
- Шорников Е.А. Электронные приборы для контроля и автоматического регулирования температуры. М. JL: Энергия, 1964. — 48 с.
- Шубин Д.П. Технология восстановления внутренних цилиндрических поверхностей стальных деталей электроконтактным напеканием. Автореф. дисс.канд. техн. наук. Барнаул, 1989. 23 с.
- Ярышев Н.А. Теоретические основы измерения нестационарных температур. J1.: Энергия, 1967. — 299 с.
- Beck J.V., Blackwell В., St. Clair C.R. Jr. Inverse Heat Conduction: 111 -posed Problems. A Wiley — Interscience Publication. New York, 1985, 308 p.
- Gross M., Moscardini A.O. Lerning the Art of Mathematical Modelling. -Wiley, 1985, № 4.- 154 p.
- Hensel E. Inverse Theory and Applications for Engineers. Englewood Cliffs, New Jersey: Prentice Hall, 1991.
- Sharakhovsky L.I., Marotta A., Borisyuk V.N. // J. Phys. D: Appl. Phys. 1997. Vol. 30. P. 2421 -2430.