Повышение износостойкости деталей гидроагрегатов трактора
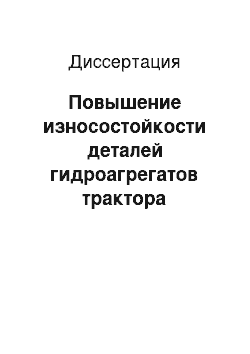
Литературный обзор публикаций показывает, что развитие процесса низкотемпературного азотирования и его разновидностей с целью поверхностного упоения изделий идет в основном по двум направлениям: создание новых нитроллоев с заданным составом, строением и свойством, а также и разработки новых газовых процессов, конкурирующих с гальваническими и химическими способами поверхностного упрочнения… Читать ещё >
Повышение износостойкости деталей гидроагрегатов трактора (реферат, курсовая, диплом, контрольная)
ДИССЕРТАЦИЯ Повышение износостойкости деталей гидроагрегатов трактора
Аннотация По мере развития техники вопросы повышения долговечности и надежности современных машин приобретают все большее значение.
В последние года получили распространение альтернативные процессы, позволяющие повысить коррозионную стойкость и износостойкость деталей, взамен гальванических способов получения покрытия. К таким процессам относится, например, совмещение процесса кратковременного газового азотирования с последующим окислением.
Тема магистерской диссертации является актуальной, т.к. повышение износостойкости шестерен масляного насоса гидроагрегатной системы является насущной проблемой инженеров и специалистов в области тракторостроения Узбекистана.
Работа посвящена исследованию и разработке комбинированного технологического процесса химико-термической обработки — азотирования с последующим парооксидированием, с целью получения диффузионных нитрид-оксидных слоев, обладающих высоким комплексом эксплуатационных свойств и способных успешно заменить гальванические покрытия для деталей, изготовленных из конструкционной стали, выявление связи между фазовым составом и строением нитрид-оксидных покрытий и их физико-механическими свойствами, создание математической модели процесса и определение рациональных режимов нитрооксидирования на деталях, работающих в условиях износа и коррозии.
В диссертации исследованы кинетика формирования диффузионных нитрид-оксидных покрытий, разработаны математические модели процессов формирования диффузионных нитрид-оксидных покрытий.
Объект исследования — шестерни масляного насоса гидроагрегатной системы.
Теоретическая ценность работы — разработана двухступенчатая технология нитрооксидирования конструкционных сталей, исследованы кинетика формирования диффузионных нитрид-оксидных покрытий, микроструктура, морфология и фазовый состав нитрид-оксидных покрытий, разработана математическая модель процесса диффузии азота при оксидировании нитридных слоев и получены аналитические зависимости перераспределения концентрации азота при нитрооксидировании.
Практическая значимость работы — разработанный технологический процесс нитрооксидирования на конструкционных сталях взамен экологически вредных гальванических способов, позволяет реализовать двухступенчатую непрерывно-последовательную схему упрочнения, заключающуюся в азотировании в аммиаке с последующим оксидированием в парах води.
Разработанная технология нитрооксидирования более экономична и экологически чистая, чем традиционные гальванические способы получения защитных покрытий.
По мере развития техники вопросы повышения долговечности и надежности современных машин приобретают все большее значение.
В настоящее время имеются разнообразные эффективные способы повышения долговечности деталей машин, в частности, для защиты поверхности от коррозии и повышения износостойкости на конструкционных сталях, широко применяются различные виды гальванических покрытий.
Гальванические способы получения покрытия обладают существенными недостатками, связанными с экологической вредностью гальванических производств, высокой стоимостью применяемых цветных металлов и необходимостью значительных дополнительных затрат на очистку отходов производства.
В последние года получили распространение альтернативные процессы, позволяющие повысить коррозионную стойкость и износостойкость деталей, взамен гальванических способов получения покрытия. К таким процессам относится, например, совмещение процесса кратковременного газового азотирования с последующим окислением.
Однако, практически во всех опубликованных работах по окислению азотированного слоя указывается на положительное влияние оксидной пленки без объяснения природы ее образования, влияния технологических параметров оксидирования на структуру и фазовый состав как нитридного, так и оксидного слоя. Отсутствие достаточных данных о кинетике формирования оксидной пленки, изменениях, происходящих в нитридном слое при его оксидировании и о влиянии технологических параметров на фазовый состав, структуру и физико-механические свойства получаемых диффузионных покрытий сдерживали применение азотирования с последующим парооксидированием в промышленности.
Целью работы является исследование и разработка комбинированного технологического процесса химико-термической обработки — азотирования с последующим парооксидированием, с целью получения диффузионных нитрид-оксидных слоев" обладающих высоким комплексом эксплуатационных свойств и способных успешно заменить гальванические покрытия для деталей, изготовленных из конструкционной стали, выявление связи между фазовым составом и строением нитрид-оксидных покрытий и их физико-механическими свойствами, создание математической модели процесса и определение рациональных режимов нитрооксидирования на деталях, работающих в условиях износа и коррозии.
Глава I. Состояние вопроса, цель и задачи исследования
1.1 Состояние вопроса
1.1.1 Основные способы повышения износостойкости и коррозионной стойкости стальных изделий Увеличение долговечности работы механизмов и их надежности является важнейшим условием повышения качества изделий машиностроительной промышленности.
Для повышения износостойкости, коррозионной стойкости и кавитационной стойкости в практике машиностроительных заводов используют различные методы получения Гальванических и химических покрытий, а также химико-термическую обработку — цементацию, низкотемпературную нитроцементацию, азотирование и его разновидности.
Гальванические и химические покрытия Гальванические и химические методы зашиты металлов применяют главным образом для повышения коррозионной стойкости и износостойкости деталей машин. В машиностроительной промышленности применяют гальванические покрытия, получаемые путем осаждения металлов из водных растворов их солей под действием постоянного электрического тока. Это процессы хромирования, никелирования, цинкования, кадмирования [l, 2]. Распространены также химические покрытия, получаемые в результате взаимодействия поверхности металла с химическими реагентами без электрического тока — никелирование, оксидирование, фосфатирование [3, 4].
Наиболее эффективно защищают стали от коррозии электролитические цинковые и кадмиевые покрытия. Сравнительно высокая стойкость цинка в атмосферных условиях делает возможным широкое применение его для защиты стальных листов, крепежных деталей и т. д. В воде при температуре более 60−70°С защитные свойства цинкового покрытия резко снижаются, а при отрицательных температурах покрытия становятся хрупкими. Для деталей, работающих в условиях трения, цинковое покрытие непригодно.
Кадмий обладает большей химической стойкостью, чем цинк. Кадмиевые покрытия более стойки в кислотах, не растворяются в щелочах, а в атмосферных условиях уступают цинковым покрытиям. В морской воде и в условиях тропического климата кадмиевые покрытия обеспечивают лучшую защиту от коррозии, чем цинковые. Электролитический слой кадмия обладает высокой пластичностью и поэтому применяется для зашиты от коррозии ответственных резьбовых и сопряженных деталей, узлы которых требуют плотной сборки. Для повышения коррозионной стойкости кадмированных деталей производят пассирование в растворе хромового ангидрида. Следует отметить, что соли кадмия и цинка ядовиты и требуют предосторожности при выполнении гальванических операций.
Электролитические хромовые покрытия обладают рядом ценных физико-механических свойств, благодаря которым они находят широкое применение в промышленности. В зависимости от плотности тока, температуры и состава электролита получают хромовые покрытия, обладающие различными свойствами.
Хромовые покрытия стойки против действия сероводорода" многих кислот и щелочей, длительное время сохраняют свой цвет и блеск. Шея более высокий нормальный потенциал, чем железо, хром не обеспечивает электрохимической защиты черных металлов. Поэтому при наличии пористости слоя хрома изделия из стали подвергаются коррозии [2,6]. На воздухе и в окислительных средах хром пассивируется, покрываясь тонкой прозрачной пленкой оксидов.
Хромовые покрытия характеризуются высокой твердостью и износостойкостью при работе деталей с умеренными ударными нагрузками и удельными давлениями до 250 МПа. Надежную защиту деталей и высокие декоративные качества изделий при одновременном действии механического износа и коррозионной среды обеспечивают комбинированные хромовые покрытия, которые состоят из осадка молочного хрома толщиной 15 мкм и блестящего хрома толщиной 35 мкм [ 2 ] .
Существенным недостатком обычных электролитических хромовых покрытий является наличие растягивающихся остаточных напряжений в поверхностных слоях, значительно снижающих усталостную прочность деталей.
Гальванически осажденный никель порист и имеет пониженную пластичность, твердость покрытия сравнительно невелика — до 3 ГПа, хорошо сопротивляется коррозии в атмосферных условиях, в растворах солей, щелочей и органических кислот. Никелирование применяют для окончательной отделки деталей в различных отраслях машиностроения, при этом в электролит добавляют специальные блескообразователи.
Наряду с гальваническим никелированием для зашиты деталей от коррозии и повышения износостойкости в последнее время используется химическое никелирование в ваннах с горячим раствором никеля и некоторых других компонентов. Химическое никелирование и никельфосфорные покрытия применяют для упрочнения деталей, изготовленных из высококачественных легированных сталей, а также для повышения коррозионной стойкости и износостойкости алюминиевых сплавов .
Оксидные пленки повышенной толщины и плотности применяют для защиты деталей" работающих в легких коррозионных условиях. Оксидные покрытия могут быть получены термическим, химическим или электрохимическим путем.
Термическое оксидирование проводится путем погружения разогретой детали в растительные масла, расплавленную селитру, щелочные растворы. В промышленности применяют щелочное и кислое химическое оксидирование. При щелочном оксидировании обработка производится в подогретом концентрированном растворе щелочи, содержащем окислители, а кислое оксидирование проводят в растворе ортофосфорной кислоты и окислителей .
Электрохимическое оксидирование в основном применяют для обработки цветных металлов для защиты от коррозии в атмосферных условиях.
Для защиты от коррозии деталей из черных металлов, алюминия, цинка, магния и др. применяют фосфотирование химическим или электрохимическим способом. Хотя фосфатные покрытия более стойки против коррозии, чем оксидные покрытия в атмосферных условиях, они хрупки и не обладают стойкостью против истирания [ 4 ] .
Гальванические и химические способы, являясь эффективными методами получения покрытий, имеют и существенные недостатки. На изделиях сложного профиля практически невозможно получить равномерной толщины покрытий. Экологическая вредность гальванических производств заставляет искать альтернативные способы получения износостойких и коррозионностойких покрытий.
Для очистки отходов гальванических производств требуется большое количество вода, а отработанные электролитные растворы, содержащие цианиты и соединения цветных металлов" особенно ядовиты и относятся к первому классу вредных веществ [ 8 ]. Кроме того, элементы, содержащиеся во вредных токсичных веществах применяемых при обработке, вызывают интенсивную коррозию основного и вспомогательного оборудования.
Химико-термическая обработка Химико-термическая обработка как метод поверхностного упрочнения металла является более эффективным способом изменения свойств поверхностного слоя вследствие изменения его состава и создания тонкого поверхностного слоя в результате диффузии атомов наносимого элемента в основной металл при высоких температурах. Для получения диффузионных износостойких и коррозионностойких слоев на сталях обычно применяют цементацию, термодиффузионную металлизацию, нитроцементацию, азотирование, оксидирование и др.
Из многочисленных методов диффузионной металлизации стальных изделий (насышения поверхностного слоя различными металлами) для повышения долговечности наибольшее практическое применение получили процессы алитирования, борирования, силицирова-ния, термодиффузионного хромирования, а также комбинированное насыщение двумя или несколькими элементами, например, хромоа-литирование, хромосилицирование, бороалитирование и т. д.. Поскольку насыщение стальных изделий металлами не является предметом исследования данной работы, поэтому они подробно не рассматриваются.
Для повышения эксплуатационных свойств конструкционных сталей применяют цементацию и нитроцементацию, основное назначение которых — обеспечить высокую твердость и износостойкость поверхности, повысить предел контактной выносливости и предел выносливости при изгибе при сохранении вязкой сердцевины. Износостойкость цементованных конструкционных деталей увеличивается в несколько раз по сравнению с нормализованными и термически обработанными сталями [10 ].
Цементация и нитроцементация повышают предел выносливости при изгибе до 1200 МПа и при контактном нагружении до 2500 МПа, при этом повышается и износостойкость поверхности [l0]. Однако цементованные и нитроцементованные детали обладают низкой коррозионной стойкостью и имеют довольно высокий коэффициент трения.
Лучшие результаты по износостойкости и коррозионной стойкости получаются после низкотемпературной химико-термической обработки — азотирования, карбонйтрирования, сульфацианирования и др.
Карбонитрирование и сульфацианирование проводят в основном в расплавах цианидных, цианид-цианитных и цианатных солей, низкотемпературное азотирование проводят в жидких средах и газовых атмосферах (частично диссоцированном аммиаке, смеси аммиака и азота, аммиака и углеродосодержаших газов, аммиака и кислородсодержащих газов).
Основными достоинствами жидкостных методов насыщения являются высокая скорость нагрева и небольшая длительность технологического процесса, однако высокая токсичность применяемых солей, сложность очистки цианистых отходов, трудность регулирования структуры и состава диффузионного слоя, а также сложность контроля состава ванны препятствуют широкому использованию этих методов.
Наиболее перспективными являются насыщения в газовых атмосферах, которые практически безвредны для окружающей среды" кроме того применение газовых атмосфер обеспечивает получение оптимального по строению и составу диффузионного слоя [П] .
В последнее время появились много сообщений и публикаций по совмещению процессов азотирования и последующего оксидирования, которые позволяют значительно повысить коррозионную стойкость и износостойкость конструкционных сталей.
1.1.2 Оксидирование сталей
Оксидированием называется процесс получения на поверхности изделий пленки оксидов, обладающей защитными свойствами. В промышленности наибольшее практическое применение получило, для защиты сталей от атмосферной коррозии и повышения износостойкости стальных и чугунных изделий, паротермическое оксидирование [12, 13 ] .
Оксидирование металлов и сплавов определяется многими факторами, к важнейшим из которых можно отнести состав газовой фазы, температуру и продолжительность воздействия окисляющей атмосферы, состав стали.
Из диаграммы состояния системы Fе-O (рис. 1.1) следует, что в технически интересной области сплавов железа с кислородом образуется три вида оксидов: закись железа Fe O (вюстит), закись-окись железа Fe3О4 (магнетит), окись железа Fe2O3 (гематит).
Закись железа имеет решетку со значительным количеством дефектов и устойчива при температуре выше 570 °C. Магнетит имеет кубическую решетку типа шпинели с параметром, а = 0,838 нм. Хотя магнетит, также как вюстит, содержит избыток кислорода, но величина этого избытка небольшая .
Рис. I. Диаграмма состояния системы «Fe-O». FeO — закись железа (вюстит); Fe3O4 — закись-окись железа (магнетит); Fe2O3 — окись железа (гематит).
Теоретические и экспериментальные данные, приведенные в работе [l5], показывают, что диффузионная проницаемость магнетита и гематита по сравнению с проницаемостью вюстита незначительна. По мнению авторов это определяет их лучшие защитные свойства против коррозии.
В работе отмечается, что при оксидировании водяным паром оксидная пленка состоит из оксида Fe3O4 который склонен к растрескиванию, что облегчает рост оксидной пленки, а в работе подтверждается, что при оксидировании железа водяным паром наружным слоем оксида является Fe3O4. Причем его кристаллы растут на открытой наружной поверхности и оттесняют друг друга только в направлениях, параллельных поверхности и поэтому склонны к растрескиванию и раскаливанию.
Более глубокому изучению свойств оксидной пленки, получаемой паротермическим оксидированием посвящены работы [12. 13.].
Сравнивая относительную коррозионную стойкость оксидных пленок различного фазового состава, авторы работ [12, 13, 15] подтверждают, что наибольшую стойкость в условиях атмосферной коррозии проявляет Fe3O4 и меньшую FeO. Получаемая тонкая пленка оксида Fe3O4 на поверхности практически мало сказывается на скорость коррозии.
Оксидные пленки, полученные паротермическим оксидированием, значительно сокращают продолжительность приработки трущихся поверхностей. Улучшение прирабатываемомости объясняется полирующим действием дисперсных частиц оксидов, отделяющихся при трении. При этом обеспечивается быстрое увеличение фактической площади контакта соприкасающихся поверхностей пар трения, равномерное их изнашивание и повышение износостойкости [I2].
Практически во всех опубликованных работах отмечаются лучшие результаты по коррозионной стойкости и износостойкости однофазных оксидных пленок из Fe3O4 при условии их достаточной сплошности и плотности.
1.1.3 Азотирование сталей
Азотирование — это процесс диффузионного насыщения поверхностного слоя сталей и сплавов азотом при нагревании в дислоцированном аммиаке, азоте, смеси аммиака с азотом, аргоном и другими газами. Азотирование чаще проводят при температурах 500−600°С (низкотемпературное азотирование).
Азотированию можно подвергать любые стали перлитного, ферритного и аустенитного классов, а также чугуны. В результате азотирования стали, и сплавы приобретают высокую поверхностную прочность; высокую износостойкость и низкую склонность к задирам; высокое сопротивление кавитации и коррозии в атмосфере, пресной воде и паре.
При азотировании металлов и сплавов образуются многослойные диффузионные покрытия, состоящие из поверхностной нитридной зоны и диффузионного подслоя — зоны внутреннего азотирования.
При насыщении стали азотом формирование слоя подчиняется общему правилу, согласно которому на поверхности образуются фазы в соответствии с диаграммой состояния «Fе-N» .
Строение поверхностного нитридного слоя зависит от потенциала насыщающей среды при азотировании, составов азотирующего газа и азотируемого сплава [19, 20] .
При азотировании железа и его сплавов в среде с высоким азотным потенциалом диффузионное нитридное покрытие состоит из последовательно расположенных слоев: Fe2N- (о фаза) > Fе2−3N (е — фаза) > Fе4N (гI— фаза). о — Фаза образуется в результате фазовой перекристаллизации при охлаждении в тех областях е — фазы, в которых концентрация азота составляет 11,0−11,35% (по массе). Слои о — и е — фазы содержат большое количество пор, стенки которых окислены (Fe2O3). Образование пор связано с метастабильностью нитридных фаз, азот из которых стремится выделиться в свободном виде. Это приводит к появлению на дислокациях, границах зерен и в развитых пустотах объемов газообразного азота, находящегося под высоким давлением сначала в атомарном, а затем в молекулярном состоянии. Вероятно, под влиянием этого давления на дислокациях (границах зерен) в нитридном покрытии образуются поры .
При азотировании стали в аммиачной атмосфере, а также при насыщении в средах, содержащих кислород и углерод, образуется карбонитрид Fe2−3 (N, С,) или оксикарбонитрид Fe2−3 (N, С, O).
При азотировании стали в аммиаке происходит интенсивная диффузия углерода из основы к поверхности и обогащение ефазы углеродом [22 ] .
Карбонитридная ефаза, полученная при одновременном диффузии в сталь и азота и углерода, менее хрупка по сравнению с чистой азотистой фазой и обладает повышенной твердостью и высокой износостойкостью.
Процесс азотирования имеет много технологических вариантов и выбор того или иного процесса определяется технологичностью, возможностью регулирования строения слоя, скоростью насыщения и т. д.
Широко применяются процессы азотирования в жидких средах. Однако, несмотря на совершенствование этих процессов, их все более 'вытесняет газовое азотирование. Это объясняется большей технологической гибкостью газовых процессов за счет широкого ассортимента оборудования, большого числа вариантов газовых сред и температур обработки, меньшей токсичностью газовых сред.
В промышленных кратковременных технологиях азотирования получили распространение регулируемые процессы на базе атмосфер аммиака, разбавленных дислоцированным аммиаком, углеродои кислородосодержащими газами, сульфоазотирование и др. [23 ].
Азотирование в аммиаке. При азотировании в аммиачной атмосфере можно осуществлять регулируемые процессы, изменяя азотный потенциал за счет разбавления аммиака азотом, инертным газом и азотоводородной смесью, полученной при предварительной диссоциации аммиака. Повышение температуры до 560−620 С позволяет проводить кратковременное газовое азотирование, являющееся конкурентоспособным процессом жидкому азотированию.
По данным авторы работы физико-механические свойства азотированного слоя на среднеуглеродистой стали после газового азотирования в среде частично диссоцированного аммиака не уступают результатам, полученным при азотировании в цианид-цианатных ваннах. Максимальной износостойкостью обладает азотированный слой, полученный после насыщения при температуре 570 °C с толщиной зоны соединения 10−20 мкм. В работе также приводятся данные о высоких физико-механических свойствах малоуглеродистой стали после кратковременного газового азотирования в среде аммиака, превышающих свойства азотированного слоя, полученного по жидкостному методу. Однако при газовом азотировании скорость насыщения ниже, чем при обработке в цианид-цианатных расплавах.
Для снижения хрупкости азотированного слоя и экономии аммиака в практике для обработки конструкционных сталей применяется азотирование в аммиаке, разбавленном азотом (аргоном) [26, 30] .
Разбавление аммиака азотом (до 70%) исследовалось А. Н. Минкевичем и Ю. В. Сорокиным [26, 27], В. Забавником [28−30], которые отмечают, что уменьшение азотного потенциала атмосферы повышает пластичность нитридного слоя и уменьшает взрывоопасность реакционной среды.
Практически во всех вышеуказанных работах отмечаются лучшие физико-механические свойства азотированного слоя по сравнению с жидким азотированием: повышенная коррозионная стойкость, износостойкость и сопротивление усталости.
Азотирование в атмосфере аммиака и углеродосодержащих газов С повышением содержания азота в высокоазотистой е — фазе одновременно повышается хрупкость нитридного слоя. С целью повышения пластичности е — фазы при газовом азотировании в качестве насыщающей атмосферы применяют аммиак с добавками углеродосодержащих газов. При этом изменяется характер образующихся фаз" предотвращается пресыщение поверхностного слоя азотом. Углерод практически не растворяется в диффузионном подслое, а участвует в формировании поверхностной карбонитридной зоны .
Азотирование в смеси аммиака и углеродосодержаших га зов было исследовано и внедрено в 1964;1966 г. г. Для азотирования использовались атмосферы аммиака в смеси с продуктами пиролиза триэтаноламина или природного газа (30−40% аммиака и 60−70% природного газа) .
В последние годы за рубежом разработаны и успешно применяются взамен обработки в цианид-цианатных расплавах кратковременные процессы азотирования, в качестве насыщающих атмосфер которых используются смеси аммиака с пропаном, экзои эндогаэами и т. д.
В США с 1970 г. применяется процесс азотирования, разработанный фирмой «Ипсен», в качестве насыщающей атмосферы используют смеси аммиака и эндогаза с соотношением 1:1. Этот процесс известен под названием «нитемпер», Аналогичный процесс, применяемый в Германии получил название пни-котрирование", в Японии — «найтемпер». Точка росы эндогаза 0 °C. Эндотермическая атмосфера не регулируется по точке росы и содержанию СО2. Фирма «Айхелин» (Германия) разработала процесс «нитрок» в смеси аммиака и экзогаза (90% N2 и 10% CO2). Успешно конкурирующие такие технологии с технологией азотирования в цианит-цианатных ваннах не только экологически чисты, но в два раза дешевле.
В работах [19, 35, 36] отмечается, что нитридные и карбонитридные слои имеют повышенную коррозионную стойкость. Подробный анализ коррозионных свойств,' проведенный в работах [37−39] показывает, что коррозионная стойкость азотированных слоев при работе в атмосферных условиях в большинстве случаев недостаточна для обеспечения долговечности деталей.
Азотирование в атмосфере аммиака и кислородосодержащих газов. При азотировании в среде аммиака с добавками кислорода, воздуха, паров воды скорость азотирования несколько возрастает по сравнению с азотированием в аммиаке. Образование оксидных пленок, оксикарбидов, оксикарбонитридов способствует повышению износостойкости и коррозионной стойкости азотируемых сталей [40, 41] .
Предложено много модификаций процесса азотирования в азотоили азотокарбоокисляющих атмосферах. Однако, следует отметить, что контролируемое введение в аммиачную атмосферу кислородосодержащих компонентов требует соблюдения строгих мер техники безопасности в связи с взрывоопасностью насыщающей атмосферы.
Для повышения триботехнических свойств азотированного слоя в аммиачную атмосферу вводят вещества, содержащие серы. Присутствие в поверхностном слое серы обеспечивает повышение эадиростойкости и износостойкости в условиях сухого трения [42, 43]. Активными составляющими в газовых смесях являются пары серы, сероводород, сернистый углерод и SO2. О происходящих при этом реакциях мало известно.
На основании вышесказанного можно заключить, что в настоящее время в практике разработаны и широко применяются целый ряд процессов газового азотирования" разнообразных по экономичности, технике безопасности и экологической чистоте.
1.1.4 Комбинированные процессы азотирования Важнейшим вопросом является изучение и расширение возможностей применения азотирования с целью повышения износостойкости и коррозионной стойкости обрабатываемых деталей. Для решения этого вопроса повышенное внимание исследователей и практиков привлекают комбинированные процессы — совмещение процесса азотирования с другими процессами, не только с точки зрения обеспечения замены жидкостного азотирования, а также замены экологически вредных гальванических способов.
Фирма «Дэгусса» (Германия) предложила способ придания поверхности деталей из нелегированной или низколегированной стали и деталям из чугуна коррозионной стойкости, превышающей коррозионную стойкость покрытий, получаемых при твердом хромировании, или других гальванических покрытий. Процесс носит название Q — Р — Q, и включает следующие операции: азотирование в соляной ванне; охлаждение и оксидирование в расплаве оксидов и нитратов; полирование азотированной по верхности и повторное оксидирование [33, 44]. Хотя способ позволяет при использовании дешевых сталей обеспечить повышение износостойкости, коррозионной стойкости и адгезионной прочности, основным недостатком является использование раз личных солей, неблагоприятных по токсичности в отношении окружающей среды.
В работе приведен анализ коррозионной стойкости диффузионных слоев, полученных жидкостным азотированием и дополнительным окислением нелегированной стали по сравнению с гальваническими покрытиями. Отмечается, что азотирование с последующим оксидированием обеспечивает коррозионную стойкость, сравнимую с коррозионной стойкостью хромового покрытия.
В последние годы появилось много сообщений по новой технологии азотирования с последующим оксидированием — «Нитротек». Обработку стальных изделий при этом проводят при 550−740 °С в газовых средах на основе азота в течение 2−4 часов, затем окисляют 10−30 секунд в окисляющей среде, содержащей различные соли и наполнители. В работах [45−48] проводятся данные по коррозионной стойкости и износостойкости диффузионных покрытий после модифицированных процессов «Нитротек»: с повторным оксилением — «Нитротек-S» и с проведением этого процесса после обычной цементации — пНитротек-C" .
Несмотря на большие достоинства процесса «Нитротек», сфера применения процесса ограничена токсичностью солей, используемых при оксидировании нитридного слоя.
В связи с экологической ситуацией в мире, а также экономичностью осуществляемой технологии, разработка конкурент-носпособного и экологически чистого метода кратковременного газового азотирования и газового оксидирования, является весьма перспективным.
Регулирование фазового состава нитридного слоя азотированных сталей играет роль в случае, когда речь идет об улучшении эксплуатационных свойств азотированного слоя.
Фазовый состав и строение нитридного слоя могут быть изменены в широких границах при изменении условий азотирования. По данным различных исследователей при оксидировании азотированных слоев могут быть дополнительно улучшены коррозионные и износостойкие характеристики [49, 50, 51, 55] .
Наличие оксидных пленок на поверхности или в приповерхностных областях карбонитридного слоя, полученных оксидированием в экзогазе после карбонитрирования, предотвращает образование дефекта «глубинное шелушение» и повышает износостойкость обрабатываемого изделия.
Оксидная пленка толщиной до I мкм, полученная оксидированием в атмосфере с определенным соотношением азота и кислорода в течение до 60 секунд, позволяет улучшить трибодогические свойства и коррозионную стойкость карбонитридного слоя. По данным автора при оксилении карбонитридного слоя происходит процесс диссоциации е — фазы, образование свежевосстановленного железа и окисление последнего. На поверхности происходит перераспределение только азота, а концентрация углерода не изменяется.
В работе сделана попытка исследования нитридного слоя после оксидирования. Показана, что оксидная пленка, образующаяся на поверхности после оксидирования, имеет состав Fe3O4. По мнению авторов, в процессе окисления происходит расширение кристаллической решетки е — фазы за счет дополнительного внедрения азота или кислорода.
Результаты исследований, проведенных авторами работы [52], наводят на мысль, что атомы кислорода, проникая в решетку е — нитрида, образуют изоморфные исходному е — оксинитриды. Такое же предположение было высказано еще Б. Прженосилем [53], однако непосредственного доказательства образования таких фаз все же не было представлено.
В работе авторы утверждают, что расширение решетки е — фазы после оксидирования нитридного слоя на поверхности низкоуглеродистой стали, происходит из-за внедрения азота в. е — фазы.
Проведенными исследованиями в работе по изучению коррозионной стойкости нитридного слоя после оксидирования в парах воды, повышение наилучшей коррозионной стойкости изделий объясняется отсутствием промежуточной — фазы между оксидными и нитридными слоями, образующейся при деазотировании нитридного слоя.
Практически во всех работах подтверждается, что в результате оксидирования на поверхности нитридного (карбонитридного) слоя образуется оксидная пленка и происходит изменение структуры поверхностной зоны при оксидировании, которая влечёт за собой улучшение коррозионных и износостойких свойств.
Однако не исследованы влияния технологических параметров процесса оксидирования на фазовый состав, структуру и физико-механические свойства как поверхностного оксидного слоя, так и нитридного подслоя, что сдерживает внедрение комбинированной технологии азотирования с последующим оксидированием в промышленности.
1.2 Цель и задачи исследования
Литературный обзор публикаций показывает, что развитие процесса низкотемпературного азотирования и его разновидностей с целью поверхностного упоения изделий идет в основном по двум направлениям: создание новых нитроллоев с заданным составом, строением и свойством, а также и разработки новых газовых процессов, конкурирующих с гальваническими и химическими способами поверхностного упрочнения" обеспечивающими одновременно экологическую безопасность производства. При этом к числу наиболее эффективных методов химико-термической обработки" обеспечивших преимущественное повышение эксплуатационных свойств обрабатываемых изделий относятся газовые процессы нитрооксидирования. Это определяют, прежде всего технологические и технико-экономические преимущества процессов азотирования с последующим оксидированием:
стабильность получаемых результатов;
простота технологического процесса и возможность его автоматизации;
простота технологического оборудования для осуществления технологии и его обслуживания, большая производительность технологического оборудования (возможность использования при массовом производстве);
возможность многоцелевого использования оборудования (для упрочнения широкой номенклатуры изделий);
нетоксичность процессов, отсутствие токсичных отходов.
Хотя комбинации процессов азотирования и оксидирования дают возможность улучшения служебных свойств обрабатываемых изделий, однако широкому использованию этого метода ХТО в промышленности препятствует отсутствие научно обоснованных рекомендаций по влиянию технологических параметров процессов, строения и фазового состава как нитридного так и оксидного слоя на антифрикционные и коррозионные свойства упрочненных материалов. Между тем задача повышения эксплуатационной надежности деталей машин является одной из актуальных проблем современной технологии.
Все работы, рассматривающие низкотемпературное газовое азотирование с последующим парооксидированием, носят рекламный характер, лишь показывая положительное влияние окислительной обработки. Практически не установлены технологические параметры, позволяющие воспроизвести технологию азотирования с последующим парокосидированием в промышленных условиях. Недостаточно изучен фазовый состав и механизм формирования диффузионных нитрид-оксидных покрытий и физико-механические свойства упрочненных изделий, что сдерживает широкое промышленное применение технологии.
Это определило следующие цели и задачи настоящей работы:
Целью настоящей работы является повышение износостойкости деталей агрегатов гидросистемы трактора.
Для достижения этой цели необходимо решить следующие задачи:
использование технологии азотирования с последующим парооксидированием (нитрооксидирования) для поверхностного упрочнения для деталей агрегатов гидросистемы трактора;
изучение процессов, происходящих при оксидировании азотированного слоя в атмосфере перегретого водяного пара;
установление структурных критериев качества диффузионных нитрид-оксидных покрытий для обработки изделий;
математическое моделирование процессов, происходящих при оксидировании нитридного слоя, позволяющее прогнозировать состав, строение и свойства упрочняемых слоев и, тем самым, оптимизировать температурно-временные показатели процессов;
изучение физико-механических свойств получаемых покрытий.
Глава 2. Кинетика формирования диффузионных нитрид-оксидных покрытий
2.1 Выбор технологических параметров процесса нитрооксидирования Из анализа литературных данных можно сделать заключение, что лучшие эксплуатационные свойства нитридного слоя при азотировании конструкционных сталей достигаются при температуре ниже эвтектоидного превращения для системы «Fe-N».
При температуре азотирования выше эвтектоидной температуры (620°С) наблюдается четко выраженная столбчатость нидридной зоны. Крупные кристаллы достигают величины равной толщине е — фазы. Между кристаллами отмечается значительное количество мелких пор и трещин, границы между кристаллами широко раскрыты. При последующем оксидировании сталей при температуре 620 °C нитридная зона окисляется на большую глубину, так как кислород свободно проходит по дефектам и границам зерен вглубь е — фазы (рис. 2.1).
Нитридный слой, полученный при температурах до 550 °C отличается малой обшей толщиной с недостаточно развитой е — фазой. Однако, при последующем оксидировании при 550 С формируется тонкая, плотная пленка монооксида Fe3O4 (рис. 2.2).
Получение развитой с малым количеством пор — фазы возможно в очень узком интервале температур 570 ч 590 °C. После паротермического оксидирования такие мелкие многочисленные поры «залечиваются» слоем оксида.
Получение заданной структуры, фазового состава и свойств, наилучшим образом отвечающих требованиям характеристик нитридного слоя при азотировании ставит задачу выбора степени диссоциации аммиака.
Рис. 2.1. Микроструктура стали 45 после нитрооксидирования: Таз = 620 °C, фа = 3 часа; Ток = 620 °C, фок = 0.5 часа. А — XIOOO (РЭМ); 6 — X500 («Neaphot-21»).
Рис. 2.2. Микроструктура стали 45 после азотирования (а) и нитрооксидирования (б): Таз = 550 °C, фаз = 3 часа, TОK = 550 °C, фок = I час, Проведено исследование влияния степени диссоциации аммиака при температуре насыщения 580 С и длительности 3 часа на характер формирования нитридной зоны. Результаты рентгеноструктурного исследования представлены на рис. 2.3, показано, что яри увеличении степени диссоциации аммиака уменьшается содержание в нитридной зоне высокоазотистых нитридов (е — и еI фаз) и увеличивается содержание г' -фазы (Fe4N). Кроме того уменьшается общая толщина нитридной зоны, о чем свидетельствует рост интенсивности дифракционного максимума Feб .
На рис. 2.4 представлены микроструктуры стали 45 азотированных при температуре 580 °C продолжительностью 3 часа при различных степенях диссоциации аммиака. Образование развитой зоны высокоазотистого нитрида (ефазы) при значительной обшей толщине диффузионного слоя характерно для процессов проводимых при меньших степенях диссоциации (б? 30%), однако при этом повышается пористость нитридного слоя.
С увеличением степени диссоциации (б?50%) уменьшается количество е — фазы на поверхности и толщина нитридного слоя.
Поскольку в процессе оксидирования высокоазотистый нитрид (е — фаза) при диссоциации является источником азота, необходимо на первой 50% этот параметр в производственных условиях должен тщательно контролироваться путем установления определенного расхода газа и объема садки при постоянном давлении в муфеле печи.
Исходя из вышеуказанные была выбрана стандартная температура азотирования на первой стадии нитрооксидирования равная 580 ± 19 °C при степени диссоциации аммиака б = 35±5%.
Проведенные нами исследования, воспроизводящие данные работы [55], при осуществлении технологии азотирования с последующим парооксидированием по непрерывно-последовательной схеме при одной и той же температуре в лабораторных условиях в малом объеме печи (VM = 2,56 дм3) и при обработке единичных мелких деталей показали, что на второй стадии при подаче водяного пара происходит эндотермическая реакция, сопровождающаяся понижением температуры насыщения.
Рис. 2.3. Изменение интенсивности линий (200); Fеб(IIO); е, еI (101) при изменении степени диссоциации аммиака (б). Азотирование при температуре 580 °C в течение 3 часа.
Рис. 2.4. Микроструктура азотированного слоя при 580 °C продолжительностью 3 часа при различной степени диссоциации аммиака: а) б = 30 ч 35%; б) б = 35 ч 50%; в) б = 55 ч65%. Сталь 45.
В лабораторной печи понижение температуры составило 40 ч50°С, При этом, так как окисление происходило при температуре ниже температуры эвтектоидного превращения диаграмма «Fe-0» (570°C), на поверхности формировался слой магнетита Fe3O4 с высокими защитными характеристиками.
Экспериментальные данные по изучению понижения температуры на второй стадии (парооксидировании) показывают, что оно сильно зависит от продолжительности оксидирования (рис. 2.5). Такой эффект понижения температуры при оксидировании оказывает положительное влияние на формирование оксидного слоя на поверхности.
Оксидирование при температуре выше эвтектоидной (570°С) приводит к образованию многофазного оксидного слоя, содержащего наряду с магнетитом Fe3O4 оксиды Fe2O3 (гематит) и FeO (вюстит). При этом ухудшаются антикоррозионные свойства.
Рис. 2.5. Изменение температуры в зоне насыщения в зависимости от продолжительности оксидирования при расходе аммиака 0,3 м3/час. Начальная температура оксидирования: 1 — 580 °C; 2 — 550 °C.
Однако, с увеличением объема печи и при больших садках из-за высокой инерционности печного оборудования, понижение температуры в исследуемых интервалах продолжительности оксидирования не происходит. В этой связи необходимо было провести соответствующие исследования" позволяющие выбрать режим оксидирования для получения монофазных оксидных слоев в промышленных печах азотирования, имеющих крупные садки в которых за счет большой массы деталей не происходит снижения температуры при парооксидировании в результате эндотермичности реакций окисления. Между тем следует отметить, что оксидные слои, сформировавшиеся при доэфектоидных и заэвтектоидных температурах отличаются скоростью формирования и фазовым составом.
Основной целью работы является осуществление технологии нитрооксидирования и обеспечение стабильных технологических режимов с точки зрения получения нитрид-оксидных покрытий с заданным комплексом физико-механических свойств. Поэтому при выборе конкретных температур парооксидирования на второй стадии осуществляемой технологии в промышленных условиях был использован эффект понижения температуры искусственным путем, с учетом температуры эвтектоидного превращения в системе «Fe-O» равной 570 °C.
Комбинированный технологический процесс осуществлялся двумя способами по непрерывно-последовательной схеме:
по одноступенчатому режиму, когда температуры насыщения при азотировании и парооксидировании одинаковы и равны 580 ± 10 °C;
по двухступенчатому режиму, когда температура насыщения на второй стадии процесса искусственно! понижается до 550 ± 10 °C.
На основе литературных данных можно заключить, что оптимальное время азотирования с точки зрения получения малопористых, износостойких и коррозионностойких нитридных покрытий лежит в диапазоне 3ч5 часов при температуре 580 ± 10 °C.
2.2 Исследование процесса парооксидирования после азотирования В процессе азотирования с последующим парооксидированием получаемые упрочненные слои состоят из нитридной и оксидной зон.
Были изучены процессы получения нитрид-оксидного покрытия при различных продолжительностях каждой стадии при температуре азотирования 580 °C и оксидирования 580 °C к 550 °C.
При азотировании при 580 °C на поверхности формируется зона е — фазы с небольшим количеством пор. После парооксидирования при температурах 550 и 580 °C происходит «залечивание» пор слоем оксида. Микроструктура представляет собой нитридный слой с ровной темной пленкой оксида на поверхности.
Изменение толщины оксидного слоя при оксидировании нитридного слоя при малых объемах печи и садки (рис. 2.6) и полупромышленных печах (рис. 2.7) показывает, что эндотермическая реакция, происходящая при малых объемах печи оказывает существенное влияние на кинетику роста оксидного слоя на поверхности. Из анализа кинетических кривых следует, что во всех случаях рост эффективной толщины оксидного слоя во времени подчиняется параболической зависимости. Наиболее интенсивно оксидный слой растет в течение 0,5 часа при температуре 580 °C и до I часа при температуре 550 °C (рис. 2.7).
Кинетические кривые (рис. 2.8) свидетельствую о том, что при оксидировании нитридного слоя общая толщина нитрид-оксидного покрытия возрастает. При температуре оксидирования 580 °C до I часа и при 550 °C до 1,5 часа. Дальнейшее увеличение продолжительности оксидирования приводит к уменьшению обшей толщины нитрид-оксидного покрытия.
Сравнение микроструктур (рис. 2.9 и 2.10) образцов с нитрид-оксидными покрытиями, полученными при выполнении технологии по одноступенчатому и по двухступенчатому режимам также показывает, что при осуществлении технологии по первому варианту толщина оксидного слоя за 0,5 часа достигает б мкм, а по второму варианту за I час составляет 3 мкм. При увеличении времени оксидирования до 2-х часов, хотя и не обнаруживается значительный рост оксидного слоя, однако, толщина нитридного слоя уменьшается при увеличении толщины зоны внутреннего азотирования.
Рис. 2.6 Зависимость толщины оксидных слоев, образующихся полученных при оксидировании нитридных слоев от времени оксидирования при температурах: I — 500 °C; 2 — 550 °C; 3 — 580 °C, 3 — 620 °C в лабораторной печи с объемом муфели Vм = 2,56 м3 /час.
Анализ полученных закономерностей в изменении нитридного слоя при парооксидировании показывает (рис. 2.10), что окисление нитридного слоя сопровождается процессом азотирования, в результате которого при небольших изотермических выдержках возможно увеличение зоны соединений за счет диффузии азота в глубь матрицы и на встречу с кислородом.
Рис. 2.7. Зависимость толщины оксидных слоев, полученных при оксидировании нитридных слоев от времени оксидирования при температурах: I — 500 °C; 2 — 550 С; 3 — 580 °C, в полупромышленной печи с объемом муфели Vм = 12,31 м3 /час.
2.3 Исследование фазового состава диффузионных нитрид-оксидных покрытий
При выдержке азотированных образцов в атмосфере перегретого водяного пара наблюдаются некоторые изменения в строении и фазовом составе диффузионных слоев. Очевидно, что при парооксидировании азотированного слоя протекают процессы деазотирования и оксидирования азотированного слоя. Диффузия азота проходит в двух противоположных направлениях от концентрационного максимума азота в слое, а диффузия кислорода — от поверхности вглубь образца. Суммарная картина строения диффузионного слоя определяется кинетическими особенностями этих диффузионных процессов.
Рис. 2.8. Изменение общей толщины диффузионных нитрид-оксидных покрытий на стали 45 при азотировании 580 °C в течение 3 ч. с последующим оксидированием при температурах: I — 580 °C; 2 — 550 °C в зависимости от времени оксидирования.
Рис. 2.9. Микроструктура нитро-оксидированного слоя на стали 45. Режим обработки — азотирование: Таз = 580 °C, фаз = 3 ч; оксидирование: Ток = 580 °C; фок = 0,5 ч (а), фок = I час (б).
Рис. 2.10. Микроструктура азотированного слоя в стали 45 в течение 3 часов при температуре 580 °C (а) после различных продолжительности парооксидирования при температуре 550 °C (б — фок = 0,5ч.; фок = 1,0ч.; г — фок = 2ч.).
Оценка изменения содержания фаз в поверхностной зоне после различных режимов химико-термической обработки проводилась по изменению интенсивности отдельных дифракционных максимумов выявленных при рентгеноструктурном анализе фаз. Определялись интенсивности следующих дифракционных максимумов: г1 (200), е, е1, е (III), Fe (НО), Fe304 (311), Fe203 (112), FeO (200) и графически представлялась зависимость интенсивности линий фаз (в условных единицах), соответствующее содержанию фаз в поверхностной зоне, от изменения технологических параметров процесса.
Как известно, такая оценка изменения содержания фаз носит качественный характер и при анализе результатов необходимо учитывать также, на каком расстоянии от поверхности располагается определяемая фаза. Для уточнения расположения фаз по глубине упрочненной зоны проводился послойный рентгеновский анализ, для чего с поверхности последовательно удалялись слой материала и снимались дифрактограммы.
Фазовый состав оксидных пленок Рентгеновским методом исследовался фазовый состав полученных при различных температурах парооксидирования оксидных слоев на поверхности предварительно азотированных образцов. На дифрактограммах выявляются следующие фазы в оксидных слоях: при температуре оксидирования 550 °C — Fe3O4, Fe2O3(Рис З, 11), при 580 °C — FeO, Fe3O4, Fe2O3 (рис. 3.12), при 620 °C — FeO, Fe3O4, Fe3O4 (рис. 3.13), Основной фазой оксидных слоев при температуре оксидирования 550 °C и 580 °C является — Fe3O4. Оксид Fe2O3 вырастает на поверхности фазы Fe3O4 вероятно в процессе охлаждения, он плохо сцеплен с оксидным слоем, легко удаляется с поверхности при трении. Оксид FeO, обнаруженный в оксидных слоях, полученных при температуре 580 °C располагается тонкой пленкой на границе оксидной и нитридной зон. Такое расположение оксидов в слое подтверждается результатами послойного рентгено-структурного анализа (рис. 2.14).
При температуре оксидирования б20°С, из-за более интенсивного роста Fe2O3 и FeO, оксидный слой представляет смесь всех оксидов, отличается значительной рыхлостью и не может обеспечивать необходимую защиту материала от коррозии. Поскольку такие слои не могут иметь практического применения, они далее в работе не исследовались.
На рис. 2.15 показано, изменения интенсивности линий оксидных фаз, отражающее соотношение оксидных фаз в слое, в зависимости от времени оксидирования при температурах 580 и 550 °C, Скорость роста оксида Fe3O4 при температуре оксидирования 580 °C существенно выше, однако с увеличением длительности выдержки, скорость роста замедляется и при оксидировании более I часа интенсивность линий оксида Fe3O4 при двух температурах практически одинакова.
Следует отметить, что практическое применение могут иметь только оксиды, покрывающие поверхность сплошным слоем. Оксидная пленка, получаемая при температуре оксидирования 550 °C более плотная, с малым количеством дефектов и обладает лучшей адгезионной прочностью, что позволяет считать температуру 550 °C предпочтительной для парооксидирования.
Рис. 2.11. Дифрактограмма поверхности азотированного (580°С; 3 ч.) с последующим оксидированного (550°С; I ч.) образца из стали 45. Излучение FeK.
Рис. 2.12. Дифрактограмма поверхности азотированного (580°с; Зч.) с последующим оксидированного (580°С; I ч.) образца из стали 45. Излучение FeK
Pиc. 2.13. Дифрактограмма поверхности азотированного (580°С; 3 ч.) с последующим оксидированного (620°С; 0,5ч.) образца из стали 45. Излучение FeК.
Рис. 2.14. Изменение интенсивности линий Ге304(ЗП); Ге203(II2); FeO (200) по толщине оксидного слоя. Азотирование — 580 °C; 3 ч, оксидирование — 580 °C; 0,5 ч. Излучение СоК.
Рис. 2.15. Изменение интенсивности линий Fе304 (3II) и Fе203(II2) характеризующее изменение содержания л о соответствующей фазы в поверхностном слое в зависимости от времени оксидирования при температуре оксидирования 580 °C (—-) и 550 °C (—-) после предварительного азотирования при температуре 580 °C в течение 3 часа. Излучение СоК
Процессы, протекающие в азотированном слое при деазотировании После проведения процесса парооксидирования азотированного слоя диффузионный слой состоит из оксидной и нитридной зон. Особенности формирования оксидной зоны были рассмотрены в предыдущем разделе.
В настоящем разделе исследуются изменения фазового состава (соотношение и г'- фаз, изменение параметра решетки Ј - фазы) в нитридной зоне нитрид-оксидного покрытия, т. е. в зоне расположенной под оксидной пленкой.
Чтобы выделить из суммарной картины изменения фазового состава при парокосидировании эффекты, связанные непосредственно с процессом оксидирования (воздействием кислорода),
часть азотированных образцов выдерживалась при температурно-временных режимах, соответствующих процессу парооксидирования в инертной атмосфере (диссоциированного аммиака), что позволило исследовать процессы, протекающие при дезотировании. При изотермической выдержке азотированного слоя имеет место диссоциация нитридов (деазотирование). Выделяющийся азот диффундирует в двух направлениях от концентрационного максимума в слое, при этом изменение концентрации азота в слое приводит к изменению соотношения е и гЧ -фаз. Результаты деазотирования определяются температурой, временем выдержки и составом атмосферы.
Микроструктурные исследования показали (рис. 3.16), что при температуре до 550 °C процессы деазотирования отличаются большой инерционностью, заметных изменений в структуре нитридной зоны не наблюдается.
При температуре деазотирования 580 °C интенсифицируются процессы диссоциации нитридов, поверхностная пористая часть нитридного слоя — фазы чернеет, что свидетельствует об образовании деазотированного слоя.
При увеличении температуры до 620 °C диссоцирует не только — нитрид, но и гЧ -Фаза что приводит к образованию деазотированного слоя на большую толщину нитридной зоны и к уменьшению обшей толщины деазотированного нитридного слоя.
С увеличением времени выдержки при деазотировании процесс диссоциации нитридных фаз происходит более полно, вплоть до образования на поверхности Fе. Результаты рентгеновского исследования поверхности деазотированных при различных выдержках образцов стали 45 представлены на рис. 3.17. Показано, что уже при 15 мин. выдержки при температуре деаэотирования 580 °C полностью диссоцирует — фаза, а при выдержке более 30 мин. начинается диссоциация нитрида Fe4N. Образование на поверхности при диссоциации нитридов Fe подтверждается результатами послойного рентгеновского анализа (рис. 2.18)" где отмечается существенное увеличение интенсивности дифракционного максимума Fe в поверхностной зоне при увеличении времени деазотирования до I часа. При послойном анализе также выявлено существенное увеличение интенсивности рефлекса гЧ -фазы в нитридной зоне при выдержке 30 минут и увеличение толщины зоны нитридов.
После азотирования при температуре 580 °C в нитридной зоне образуются два изоморфных гексагональных нитрида, обозначаемые как и Ч— фазы. При этом на дифраитограммах наблюдается расслоение рефлексов
— фазы. Фаза рефлекса которой соответствует большим углам отражения В, обозначается как — фаза (рис. 2.19). Согласно литературным данным — фаза FexN отличается широкой областью гомогенности и в зависимости от концентрации азота X изменяется от 2 до 3,5 на границе с гЧ — фазой (около 6% по массе). Фаза ' является вероятно карбонитридной фазой, т.к. фаза с такими же параметрами решетки образуется при нитроцементации Fе-.
Рис. 2.16. Микроструктуры азотированного (а) и деазотированных (б, в, г) слоев в атмосфере диссоцированного аммиака продолжительностью 0,5 часа при температурах: б — 550 °C, в — 580 °C, г — 620 °C.
На рис. 2.20 представлены дифрактограммы образцов Fe (а) и стали 45 (б) после азотирования при 570 °C продолжительностью I час в атмосфере чистого аммиака и после нитроцементации в атмосфере с добавками пропана (C3H4) (рис. 2.21) по данным Е. Я. Тимошенко. Показано, что фаза аналогичная на Ге появляется при насыщении в атмосфере (40NH3 + 60% C3H8) (рис. 2.21, а), а на стали 45 частично выявляется при насыщении в атмосфере чистого аммиака (рис. 2.20, б) и отчетливо проявляется при насыщении в атмосфере аммиака с добавкой 10% (об.) пропана. Это позволяет сделать заключение о карбонитридном характере '- фазы, полученной при насыщении стали 45 в аммиаке при температуре 580 °C.
Рис. 2.17. Изменение интенсивности линий гЧ (200); еЧ (101) и Fe (110) при изменении продолжительности выдержки при деазотировании в атмосфере диссоцириванного аммиака при 580 °C. Предварительное азотирование при 580 °C, 3 ч. Излучение СоК.
При послойном анализе азотированных образцов стали 45 наблюдается увеличение интенсивности рефлексов — фазы в конце нитридного слоя, где отмечается повышение концентрации углерода в результате оттеснения его при диффузии азота от поверхности в глубь образца (рис. 2.22).
Рис. 2.18. Изменение интенсивности линяй: Fe (110); г1 г1 (200); е (101) по толщине нитридного слоя, характеризуещее изменение соотношения фаз в нитридном слое при времени деазотирования — 15 мин,(1), 30 мин.(2) и 60 мин.(3). Азотирование — 580 °C; Зч. Излучение СоК.
При деазотировании наблюдается диссоциация поверхностного высокоазотистого — нитрида (Fe2−3N) однако рефлексы ' - фазы стабилизированной углеродом отмечаются по всей толщине нитридной зоны вместе с — фазой (рис. 2.18).
Рис. 2.19. Дифрактограмма поверхности азотированных образцов при 580 °C в течение 3 часов. Сталь 45. Излучение СоК
Процессы протекающие в нитридной зоне при парооксидировании Отметив изменения, происходящие в азотированном слое при деазотировании, т. е. при изотермической выдержке в инертной атмосфере при температуре соответствующей парооксидированию, можно выявить те изменения которые обуславливаются диффузией кислорода при парооксидировании.
Следует отметить, что при микроструктурном исследовании азотированных, деаэотированных и парооксидированных слоев каких-либо существенных изменений в нитридной зоне, кроме некоторого увеличения ее протяженности при деазотировании и парооксидировании (причем практически одинакового для этих видов обработки) не наблюдается.
Рис. 2.20. Дифрактограмма поверхности азотированных образцов в атмосфере аммиака при 570С в течение I часа: а — техническое железо, б — сталь 45. Излучение СоК.
Рис. 2.21. Дифрактограммы поверхности азотированных при 570 С в течение I часа: а — в атмосфере (40%NН3 + 60% C3H8) на техническом железе; б — в атмосфере (90% NН3+ 10% C3H8) на стали 45. Излучение СоК.
Рис. 2.22. Изменение интенсивности линий фаз: Fe (110); гЧ — FеN (200); е, еЧ (101), отражающее изменение содержания фаз по толщине нитридного слоя. Азотирование — 580 °C; Зч, Излучение СоК.
При рентгеновском исследовании фазового состава парооксидированных нитридных слоев обнаружены некоторые особенности.
Во-первых при послойном рентгеновском анализе выявлено, что увеличение обшей толщины нитридной зоны и количества г'-фазы при деазотировании и парооксидировании при температуре 580 °C в течение 30 минут приблизительно одинаково (рис. 2.18 и 2.23). Это свидетельствует о том, что увеличение толщины зоны соединений после парооксидирования является следствием протекающего при изотермической выдержке процесса деаэотирования.
На рис. 2.24 показаны изменения соотношения ' -и г" -фаз в зоне соединения при температурах 550 и 580 °C при различных продолжительности процесса парооксидирования. Показано, что содержание в нитридной зоне ' - фазы больше, чем г' - фазы при температуре парооксидирования 550 °C и наоборот при температуре 580 °C при интенсивной диссоциации — фазы растет содержание гЧ— фазы.
Рис. 2.23. Изменение интенсивности линий Fe (110), г (200)1 е, еЧ, еЧЧ,(101) отражающее изменение содержания фаз по толщине нитридного слоя. Азотирование: 580 °C; 3 ч. + оксидирование: 580 °C; 0,5 ч. Излучение СоК.
В настоящее время имеется мало данных о влиянии количественного соотношения долей — и г' - нитридов в зоне соединения на его износостойкость и коррозионную стойкость.
Рис. 2.24. Изменение интенсивности линий г'(200) е1(101) характеризующее изменение содержания соответствующей фазы в поверхностном слое в зависимости от времени оксидирования при температуре оксидирования 550 °C (—-) и 580 °C (—-). Предварительное азотирование при 580 °C в течение 3 ч. Излучение СоК.
Рис. 2.25. Дифрактограмма поверхности азотированных яря 580 °C в течение 3 ч. и оксидированных при 580 °C в течение 0,5 часа образца из стали 45. Излучение СоК.
Однако, согласно для слоев соединений, с большей долей — нитридов можно ожидать более высокой износостойкости и коррозионной стойкости, чем для слоев с большей долей гЧ — нитридов.
При парооксидировании азотированных слоев наблюдается дальнейшее уменьшение параметров решетки — нитридов. Так, если при азотировании значения параметров решетки высокоазотистого — нитрида, а = 0,274 нм, С = 0,439 нм, при два-зотировании для ' - фазы, а = 0,269 нм, С = 0,436 нм, то после парооксидирования, а = 0,267 нм, С = 0,436 нм. При парооксидировании в зависимости от температуры и времени выдержки наблюдается смешение линий — фазы в сторону больших углов дифракции вплоть до положения указанного на рис. 3.25." Это положение рефлексов не меняется при увеличении времени парооксидирования. Полученные значения соответствуют наименьшим вычисленным значениям параметров решетки — фазы и эта фаза обозначается как н ЧЧ «.
Фаза «ЧЧ» имеет гексэгональную решетку и изоморфную и Ч — фазы, вероятно, эта фаза имеет оксикарбонитриный характер и ее следует обозначать как Fex (N, С, 0).
Присутствие кислорода в атмосфере при изотермической выдержке приводит к его внедрению в слой соединений. В работе насыщение кислородом слоя соединений рассматривается как причина повышения коррозионной стойкости.
На основании проведенных исследований можно заключить, что при оксидировании нитридного слоя в атмосфере водяного пара имеет место сложный процесс одновременного деазотирования поверхностного слоя с образованием Fе и оксилении его до оксидов железа и процесс диффузии кислорода в решетки гексогонального — нитрида, а также процесс перераспределения азота от концентрационного максимума с образованием низкоазостисых нитридных фаз. При этом надо отметить, что оптимальные свойства получаемого нитрид-оксидного покрытия могут достигаться тогда, когда диффузионный слой состоит из зоны соединений с определенным соотношением фаз (- и г'- фаз) и на поверхности которого создается оксидный слой, состоящий из Fe3O4.
2.4 Исследование режима охлаждения
При технологическом процессе нитрооксидирования конечным этапом процесса является охлаждение. При охлаждении образцов в масле или в воде с температуры насыщения фактически фиксируется структура, полученная при температуре нитро-оксидирования (рис. 2.11 — 2.13).
Оксидный слой, полученный при температуре оксидирования 580 °C состоит из оксидов FеО, Fe3O4, Fe2O3. При резком охлаждении такая оксидная пленка растрескивается и отслаивается. На рис. 2.26 видно, что хотя после нитрооксидирования поверхность более гладкая, чем поверхность азотированного образца, однако видны следы местного отслаивания оксидной пленки. Отслаивание оксидной пленки по границе раздела с нитридной зоной, по-видимому, происходит из-за образования фазы FеО на границе оксидной и нитридной зон.
При медленном охлаждении на воздухе с температуры оксидирования 580 С оксидная пленка также растрескивается" но заметного отслаивания не происходит (рис. 2.27, а). При этом обнаруживается повышение пористости увеличение шероховатости поверхности. Отчетливо видны многочисленные мелкие отростки характеризующие аназотропный рост кристаллов (рис. 2.27, б) и увеличение количества оксида Fe2O3 на поверхности (рис. 2. 28). Вероятно это связано с тем, что при охлаждении на воздухе по поверхности происходит доокисление Fe3O4 до высшего оксида Fe2O3 на поверхности, что связано с перестройкой решетки и объемными изменениями на поверхности оксидного слоя, FeOмедленном охлаждении на воздухе не был обнаружен оксид FeO, вероятно, при охлаждении FeO подвергается эвтектоидному превращению.
Рис. 2.26. Морфология поверхности азотированного (а) — Таз = 580 °C, фаэ =3часа и нитрооксидированного (б) — Таз = 580 °C, фаз — 3 часа; Tок = 580 °C, фок = 0,5 часа образцов после охлаждения в масле.(РЭМ).
Оксидная пленка, полученная при температуре вксидирования 550 С более плотная и при любом виде охлаждения не растрескивается (рис. 2.29).
Рис. 2.27. Морфология поверхности нитрооксидированных образцов (Tаз = 580 °C, фа3= - 3 часа, Ток = 58OC, фок = 0,5 часа) а — охлаждение до 450 °C на воздухе; затем в масле; б — охлаждение на воздухе.
В целом можно сделать вывод, что оксидная пленка, полученная при оксидировании нитридного слоя ниже эвтектоидной температуры практически состоит из гомогенного оксида Fe3O4 и при любом режиме охлаждения не подвергается структурным и фазовым изменениям.
Рис. 2.29. Микроструктура (х500) и дифрактограша поверхности диффузионного нитрид-оксидного покрытия, полученное при азотирования 580 °C; 3 ч. с последующим оксидированием при 580 °C; 0,25 ч. Охлаждение на воздухе.
Рис, 2.29. Морфология поверхности нитрооксидированных образцов: Таз = 580 °C, фаз = 3 ч., Ток.550°С, фок = 1ч.: а — охлаждение в масле; б — охлаждение на воздухе.
2.5 Исследование процессов формирования диффузионных нитрид-оксидных покрытий Для анализа выявленных закономерностей по перераспределению азота при получении нитрид-оксидных покрытий рассматривали математическую модель диффузии азота и кислорода в процессе оксидирования азотированного слоя.
При оксидировании — фазы нитридного слоя на поверхности возникает слой — фазы" за ним следует слой гЧфазы, за ним слой — фазы и одновременно происходит рост нитридного слоя с образованием низкоазотистых нитридных фаз" источником азота при этом служит высокоазотистая — фаза (рис. 3.1).
Уравнения, описывающие диффузию азота при наличии фазовых переходов, выглядят следующим образом:
(I)
(2)
(3)
где: С, СгЧ , С — концентрация азота в -, гЧ-, — фазах; D, DгЧ, D — коэффициенты диффузии азота в -, гЧ-, — фазах; tвремя; xрасстояние от поверхности. Концентрация азота на границах раздела фаз:
(4)
Рис. 3.1. Модель перераспределения азота по глубине азотированного слоя при оксидировании СгЧ = СкгЧ = …= СiгЧ = CгЧ ;
Сi? CкгЧ =…= СiгЧ = Cг ;
Поскольку при оксидировании кислород вытесняет азот с поверхности образца, поэтому концентрация азота на поверхности:
С (X = 0) = 0 (7)
Концентрация азота в глубине образца на границе Т*- и 6 — фазы С (X =) Cо (8)
Учитывая равенства (4−6) напишем условия на границах раздела фаз:
C (x=огЧ) = CгЧ= C (x=огЧ); (9)
CгЧ(x=огЧ) = CгЧ= CгЧ(x=огЧ); (10)
CгЧ(x=огЧ) = CгЧ= CгЧ(x=огЧ); (11)
C (x=огЧ) = C гЧ; (12)
где: о — координаты границ соответствующих индексам раздела между фазами;
С — концентрация азота в соответствующих индексам фазах на границе раздела.
Концентрации можно найти по диаграмме «железо-азот» Условия равенства диффузионных потоков на границах раздела фаз:
(13)
(14)
где: vгЧ — скорость движения границы, раздела — фаз;
vгЧ — скорость движения границы раздела г' и — фаз.
Решение системы уравнений (1−3) можно представить в следующем виде:
где: еrf — стандартная функция ошибок;
А, В, Аг', Вг', А, В — коэффициенты, определяются после подстановки решений (12−14) в граничные условия (7−12).
Для определения зависимости перемещения границ раздела фаз от времени подставим решения (15−17) в условия на фронтах фазовых переходов (13−14).
Система уравнений (13−17) при различных значениях коэффициента диффузии и концентраций решалась на ЭВМ с помощью стандартной программы 005 NBF из библиотеки NAG FORTRAN Р050.
В результате были получены зависимости изменения концентрации азота по глубине слоя для различных температур и времени оксидирования нитридного слоя.
На рисунке 3.2 приведено перераспределение концентрации азота после азотирования при 580 °C продолжительностью 3 часа. Изменение содержания азота в нитридных следе полученных при различных продолжительностях оксидирования при 580 °C (рис. 3.3) и при 550 °C (рис. 3.4) показывает, что процесс деазотирования происходит наиболее интенсивно при температуре оксидирования 580 °C.
На рис. 3.5 приведены зависимости времени исчезновения Ј - фазы при оксидировании азотированных образцов при 580 °C, рассчитанных по принятой модели (I) и определенные по результатам рентгеноструктурного анализа (2).
Сопоставляя результаты, полученные в главе Ш и зависимости, представленные на рис. 3.3, б и 3.5, можно прийти к выводу, что при оксидировании 580 °C нитридного слоя ко времени исчезновения — фазы на поверхности, формируется оксидная пленка толщиной 6 мкм в течение 0,5 часа. При этом надо учесть, что оксидная пленка, полученная при этой температуре состоит из смеси оксидов FeO, Fe3O4 Fe2O3.
При оксидировании образца, прошедшего предварительное азотирование, фронт оксидного слоя движется по — фазе. Расстояние между фронтами фазовых переходов — г' и г'- все время возрастает. Толщина г'- фазы постоянно растет и через некоторое время, исчезает высокоазотистая — фаза нитридного слоя.
Рис. 3.2. Перераспределение концентрации азота по глубине азотированного слоя при темпера-, туре 580 °C в течение 3 часа.
Для получения нитрид-оксидных покрытий с оптимальными свойствами необходимо обеспечить наличие низкоазотистого нитридного слоя значительной толщины под оксидной пленкой. При этом особенно важно установление времени исчезновения высокоазотистой — фазы при оксидировании нитридного слоя. Кроме того, устойчивая к окислению — фаза не должна быть разрушена полностью. На основании этих соображений, данных по кинетике и фазовому составу нитрид-оксидных покрытий, полученных в главе Ш, и анализа математической, модели формирования слоя были построены диаграммы преимущественных режимов оксидирования азотированных образцов. Пример такой диаграммы представлен на рис. 3.6 для образца, прошедшего предварительное азотирование в течение 3-х часов при температуре 580 °C.
Рис. 3.3. Перераспределение азота по глубине азотированного слоя (580°С, 3 ч.) при оксидировании 580°С: а — фок=15 мин.; б — фок=27мин.
Рис. 3.4. Перераспределение азота по глубине азотированного слоя (580°С, 3 ч.) при оксидировании 550°С: а — фок 27 мин.; б — фок=44 мин.
Рис. 3.5. Зависимость времени исчезновения высокоазотистой — фазы от продолжительности азотирования (Таз-580°С) при оксидировании 580°С: 1 — расчетные; 2- экспериментальные Верхаяя граница области на рис. 3.6 соответствует полному исчезновению — фазы нитридного слоя. Нижняя граница области соответствует области неравномерного оксидного слоя и существования высокоазотистой — фазы. Температуру и время оксидирования следует выбирать таким образом, чтобы соответствующая им точка на рис. 3.5 была расположена ближе к нижней границе области, поскольку при удалении от этой границы возрастает толщина г'- фазы, неустойчивой к окислению, между тем происходит разрыхление нитридного подслоя.
На основе разработанной модели рассичтаны оптимальные режимы нитрооксидирования при выполнении по двухступенчатому режиму, т. е. азотирование на первой стадии при 580 °C при различных продолжительности с последующим оксидированием на второй стадии при 550 °C (рис. 3.7).
Рис. 3.6. Диаграмма преимущественных режимов нитро-оксидирования: I — область существования высокоазотистой — фазы и неравномерного оксидного слоя; II — область преимущественных режимов; III — область разрыхления нитридного подслоя.
Верхняя область на рис. 3.7 соответствует полному исчезновению е — фазы (область Ш) и разрыхлению нитридного слоя, а нижняя область соответствует области существования высокоаэотистой е — фазы и неравномерного оксидного слоя (область I).
С точки зрения структурного критерия эксплуатационных свойств нитрид-оксидного покрытия необходимо проведение оксидирования нитридного слоя при продолжительностях, соответствующих области П. При этом после нитрооксидирования формируются нитрид-оксидные покрытия, состоящие из сплошного поверхностного оксидного слоя и низкоазотистого нитридного подслоя еII + гI — фаз.
Рис. 3.7. Диаграмма преимущественных режимов двухступенчатого процесса нитрооксидирования: I — область существования высокоазотистой — фазы и неравномерного оксидного слоя; II — область преимущественных режимов нитрооксидирования; III — область разрыхления нитридного подслоя.
износостойкость коррозионный насос
Глава 3. Испытание насосной установки на базе мотоблока МТЗ-05
3.1 Условия испытаний и применяемые средства измерений
Основными задачами, которые решались в процессе испытаний, были :
-определение гидравлических и технико-экономических показателей экспериментального насосного агрегата, созданного на базе мотоблока МТЗ-05;
— определение долговечности опытных образцов насосов;
— определение корррозионной стойкости опытных образцов насосов;
-анализ результатов испытаний и их оценка;
-выбор конструкции шестеренного насоса для комплектования насосного агрегата.
Испытания опытных образцов насосов проводились в три этапа:
-лабораторно-полевые испытания эксприментальной насосной установки, которая поочередно комплектовалась опытными образцами насосов;
-лабораторные ресурсные испытания опытных образцов насосов;
-эксплуатационные коррозионные испытания опышных образцов насосов.
На первом этапе испытывались:
а)шестеренный насоса НШ 32У-З-Л, прошедший коррозионные испытания в 1989 году и законсервированный после их проведения;
б) шестеренный насоса НШ-32Ш, шестерни которого изготовлены из бронзы и напрессованы на стальные валы, а в алюминиевые опоры установлены вкладыши, изготовленные из бронзового порошка ПРБр 05С5Ц5ТУ 23.4.159−88;
Рис. 1. Изменение характеристики насоса в зависимости от давлении нагнетания: 1-серийный насос; 2-насосы с азотированными шестернями; 3-насос с оксикарбонитридными Рис 1. Насос НШ 32У-3-Л Рис 2. Насос НШ 32 Ш с бронзовыми шестернями и вставками в опарах.
Рис 3. Насос НШ 32 Ш со стальными шестернями с покрытием и вставками в опарах.
Рис 4. Насос НШ 32У-З-Л со вставками в опарах.
в) шестеренный насоса НШ-32Ш, шестерни-валы которого изготовлены из стали и на них нанесено антикоррозионное покрытие, а в алюминиевые опоры установлены вкладыши, изготовленные из бронзового порошка ПРБр 05С5Ц5ТУ 23.4.159−88.
На втором этапе испытывались:
а) шестеренный насоса НШ-32Ш, шестерни которого изготовлены из бронзы и напрессованы на стальные валы, а в алюминиевые опоры установлены вкладыши, изготовленные из бронзового порошка ПРБр 05С5Ц5ТУ 23.4.159−88;
б) шестеренный насоса НШ-32Ш, шестерни-валы которого изготовлены из стали и на них нанесено антикоррозионное покрытие, а в алюминиевые опоры установлены вкладыши, изготовленные из бронзового порошка ПРБр 05С5Ц5ТУ 23.4.159−88.
в) шестеренный насоса НШ 32У-З-Л серийного исполнения;
г) шестеренный насоса НШ 32У-З-Л, шестерни-валы которого изготовлены из стали, а в алюминиевые опоры установлены вкладыши, изготовленные из бронзового порошка ПРБр 05С5Ц5ТУ 23.4.159−88.
На третьем этапе испытывались:
а) серийный шестеренный насос НШ 32У-З-Л;
б) шестеренный насоса НШ-32Ш, шестерни-валы которого изготовлены из стали и на них нанесено антикоррозионное покрытие, а в алюминиевые опоры установлены вкладыши, изготовленные из бронзового порошка ПРБр 05С5Ц5ТУ 23.4.159−88.
в) шестеренный насоса НШ-32Ш, шестерни которого изготовлены из бронзы и напрессованы на стальные валы, а в алюминиевые опоры установлены вкладыши, изготовленные из бронзового порошка ПРБр 05С5Ц5ТУ 23.4.159−88.
На рис. 1,2,3 и 4 представлены общие виды испытанных насосов, а на рис. 5 и 6 чертежи правой и левой втулок с вкладышами.
Шестерни гидранасосов
Испытания опытных и серийных насосов проводили на стенде ресурсных испытаний по методике описанной в ТУ 23.1 «Насос водяной шестеренный НШ-32Ш «, в следующих режимах:
-рабочая среда — вода и 15% -ный раствор хлорофоса в воде;
-подача жидкость — 1,8 м3/час;
-давление на выходе — 0,4 МПа;
-частота вращения ведущего вала насоса — 16 с-1;
-потребляемая мощность — 1,0 кВт;
-температура — 20−25 оС;
-длительность испытаний — 100 часов.
Также были изучены изменения технико-экономических характеристик опытных и серийных насосов при изменении давлении нагнетания от 0,05 МПа до 0,5 МПа.
Лабораторно-полевые испытания проводились на установке, общий вид которой представлен на рис. 7. В качестве рабочей жидкости использовалась вода из открытого водоема. Температура воды во время испытаний находилась в пределах от 16 С до 19 0С, а атмосферное давление — от 735 мм.рт.ст. до 747 мм.рт.ст. Высота всасывания, т. е. расстояние от оси всасывающего отверстия насоса до объема водоема, составляла 0,42 м и не изменялась при проведении испытаний. Объёмная подача испытываемого насоса в процессе испытаний изменялась регулировочным вентилем, установленным на конце нагнетатального рукава, таким образом, чтобы давление нагнетания не превыало 0,5МПа. Величина объемной подачи испытуемого насоса измерялась счетчиком жидкости 2СВШ-25. Цена деления шкалы счетчика 0,1л, класс точности — 0,5.
Слив воды из нагнетательного рукава производился в водоем на расстояние 4 м от приямка, в котором находился всасывающий рукав с фильтром и обратным клапаном.
Давление в нагнетательном рукаве измерялось образцовым манометром типа МО. Пределы измерений 0…10кгс/см2, цена давления шкалы 0,10кгс/см2.
Разряжение во всасывающем рукаве измерялось образцовым вакуумметром. Цена деления шкалы 0,01 кгс/см2. Частота вращения вала насоса определялась по специальному устройству, регистрирующему частату процесса замыкания контактов прерывателя магнето двигателя мотоблока.
Лабораторные ресурсные испытания насосов проводились в ЕИБ гидравлики ГСКБ МТЗ на специальном стенде. Гидравлическая схема стенда и его общий вид показаны на рис. 8 и 9. В качестве рабочей жидкости использовалась вода.
Испытания насосов проводились при постоянном давлении на выходе из насоса. Величина давления устанавливалась дросселем. Частота вращения ведущей шестерни насоса составляла 20 1/с.
Перед началом испытаний и через каждые 5 часов работы проводился замер объемной подачи насоса. Объемная подача насоса замерялась счетчиком жидкостей типа 2СВШС-25 при температуре воды 20…24оС. Цена деления шкалы счетчика — 0,1л. класс точности — 0,5. Температура воды замерялись спиртовым термометром с ценой деления 2 оС.
Емкость гидробака составляла 30л.
Замер давления производился манометром класса 2,5 со шкалой 0…10 кгс/см2, и ценой деления 0,2 кгс/см2.
Уровень воды в гидробаке относительно всасывающего отверстия в корпусе насоса устанавливался путем перемещения гидробака.
Эксплуатационные коррозионные испытания насосов проводились на стационарной установке, работающей по замкнутому контуру.
Установка состаяла из насосного агрегата (мотоблок МТЗ-05, насос НШ 32) и дополнительной емкости, в которую были опущены всасывающий и напорный рукава.
В качестве рабочей жидкости использовался 10…15% раствор хлорофоса, который наиболее широко применяется при химической защите картофельных посадок.
В процессе испытаний опытные насосы эксплуатировались по два часа в течение 3 суток и после этого хранились в течение одного месяца. Далее насосы подвергались разборке и дефектовке.
а) Экспериментальный насосно-транспортный агрегат.
б)Экспериментальный насоный агрегат.
Рис. 7. Экспериментальный насоный агрегат на базе мотоблока МТЗ-05 и шестеренного насоса НШ 32Ш.
Рис. 8. Принципиальная гидравлическая схема испытаний насосов. 1. Гидробак; 2. Испытываемый насос; 3. Электродвигатель; 4. Манометр; 5. Гидродроссель; 6. Счетчик жидкостей; 7. Термометр; 8. Всасывающий рукав; 9. Сливной рукав.
Рис. 9. общий вид стенда для испытаний насосов.
3.2 Результаты испытаний и их анализ
3.2.1 Критерии оценки параметрических, ресурсных и коррозионных показателей опытных насосов.
Для объективной комплексной оценки результатов испытаний необходимо было выработать перечень критеров и их величины.
При оценки результатов лабораторно-полевых испытаний эксприментальной насосной установки, созданной на базе мотоблока и шестеренных насосов типа НШ 32, нами были приняты показатели технической характерестики насосов, указанные в Паспорте НШ 32.00.000 ПС «Насос водяной шестеренный НШ 32Ш», утвержденном Главным инженером завода «Мосгидропривод» 4 мая 1990 г. и проекте ТУ 23.1 «Насос водяной шестеренный НШ 32Ш». Они приведены в таблице I.
Таблица I.
№ | Наименование показателя | Единица измерения показателя | Величина показателя | |
Подача | м3/ч | 1,8 | ||
Напор | МПа | 0,4 | ||
Частота вращения вала насоса | с-1 | |||
КПД | 0,25 | |||
Потребляемая мощность | кВт | 1,0 | ||
Кроме указанные в таблице для оценки результатов испытаний использовались также величины коэффициента подачи и его стабильности.
Оценка результатов русурсных испытаний опытных и серийных насосов производились по величине набора часов работы под нагрузкой, сохранение величин объемной подачи и коэффициента подачи в процессе возрастания наработки, величинам износа пар трения «зубъев шестерен, опор и т. д.», определяемых микрометражом деталей. Программой испытаний предусматривалось, что объем наработки опытных насосов не должен быть менее 100 м. часов работы под нагрузкой.
Объем наработки насоса в 100 моточасов выбран исходя из того, что насосный агрегат эксплуатируется в течение 5% времени работы мотоблока до капитального ремонта, которые составляет 2000мч.
Считаем, что при указанном объме наработки, сохранении величин объемной подачи и коэффициента подачи на первоначальном уровне, износа пар трения в технически допустимых пределах насос обладает необходимой долговечностью и пригоден для комплектования насосного агрегата .
Коррозионную стойкость насосов оценивались по величине очагов коррозии деталей насосов и пригодности насосов к дальнейшей эксплуатации, т. е. сохранении насосами работоспособности.
3.2.2 Гидравлические и технико-экономические показатели насосов при работе в агрегате с мотоблоком МТЗ-05
Гидравлические и технико-экономические показатели серийного насоса НШ 32У-З-Л, прошедшего коррозионные испытания в 1989 году и законсервированного на год.
Было установлено, что при изменении давления нагнетания с 0,04МПа до 0,5МПа объемная подача насоса уменьшается с 1,84 м3/ч до 1,5 м3/ч. Уменьшение объемной подачи насоса объясняется несколькими причинами — ухудшением гермитичности рабочей полости вследствие коррозионных резрушений деталей, уменьшением частоты вращения коленчатого вала двигателя, работающего на регляторной ветви характирестики, вследствие возросшей мощности на привод насоса. Величина коэффициента подачи уменьшается с 0,92 до 0,75, а величина общего КПД постепенно возрастает и достигает своей максимальной величины 0,12. Мощность необходимая на привод насоса, резко увеличивается, достигая 1,2кВт при объемной подаче 1,58 м3/ч и давлении 0,4МПа. Протекание кривых показано на рис. 10.
Таким образом, технические показатели насоса НШ32У-З-Л, прошедшего коррозионные испытания в 1989 году и находившегося в течение года на консервации, значительно ухудшились по сравнению с исходными. По состоянию на момент испытаний насос НШ 32У-З-Л не соответствовал паспортным показателям. Основной причиной ухудшения технической характеристики насоса НШ 32У-З-Л, по нашему мнению, явилось продолжающееся и в период консервации коррозионное разрушение деталей насоса. Техничекая экспертиза насоса, проведенная после испытаний, полностью подтвердила это предположение — интенсивному разрушению подвергались алюминиевыеопоры, посадочные места опор валов, валов и зубья шестерен.
Гидравлические и технико-экономические показатели шестеренного насоса НШ 32Ш, имеющего бронзовые шестерни и вставки в опорах.
Было установлено, что при изменении давления нагнетания с 0,04МПа до 0,5МПа величина объемной подача насоса уменьшается с 1,92 м3/ч до 1,75 м3/ч. При этом коэффициент подачи насоса падает с 0,96 до 0,88, а общий коэффициент эффиктивности возрастает с 0,04 до 0,22. мощность, затрачиваемая на привод насоса, возрастает с 0,83кВт до 0,92кВт. Протекание кривых характирестики насоса показано на рис. 11. Уменьшение объемнойподачи насоса на 9% не может быть объяснено только падением частоты вращения коленчатого вала двигателя мотоблока (2%). В процессе испытаний нами отбирались пробы воды из нагнетательного рукава насоса для выявления в ней продуктов износа его деталей (шестерен, всавок). Начиная со второго часа с начала испытаний насоса в пробах воды были обнаружены частички бронзы, что свидетельствовало об интенсивном износе шестерен. Позднее это было подтверждено и результатами ресурсных испытаний. Таким образом, уменьшение величины коэффициента подачи объясняется интенсивным износом рабочих поверхностей шестерен. Максимальная величина общего КПД 0,22 также ниже, чем можно было ожидать. Это можно объяснить только тем, что уменьшается коэффициента подачи в связи с интенсивным износом рабочих поверхностей шестерен насоса.
По своим техническим показателям новый насос НШ 32Ш с бронзовыми шестернями и бронзовыми вставками не соответствует нормативам приведенным в паспорте, и проекту ТУ 23.1 по величине объемной подачи и общего КПД.
Рис. 10. Характеристика насоса НШ 32У-З-Л после годичной консервации.
Гидравлические и технико-экономические показатели насоса НШ 32Ш, имеющего стальные шестерни с антикоррозионным покрытием и бронзовые вставки в опорах.
Было установлено, что при изменении давления нагнетания с 0,12МПа до 0,5МПа объемной подача насоса НШ 32Ш, оснащенного стальными валами — шестернями с антикоррозионным покрытием и бронзовыми вставками в алюминиевых опорах, находилась в пределах от 1,92 м3/ч до 1,9 м3/ч. При этом коэффициент подачи насоса во всем диапазоне давлений составлял 0,95 и оставался постоянным. Общий коэффициент полезного действия насоса возрастает от 0,2 до 0,43. Это свидетельствует о высоком механическом коэффициенте полезного действия насоса — он находится в пределах 0,21…0,45. высокое значение Юо и Ю обусловило (по сравнению с другими образцами насосов НШ32У-З-Л и НШ 32Ш с бронзовыми шестернями) минимальные затраты мощности на привод и самую высокую частату вращения коленчатого вала двигателя мотоблока. Протекание характеристик насоса показано на рис. 12. По всем показательям данный насос полностью соответствует или же превышает нормативные показатели, преведенные в техническом паспорте насоса и проекте ТУ 23.1. Из всех испытанных образцов насосов данный является оптимальным для комплектования насосного агрегата, созданного на базе мотоблока МТЗ — 05 и шестеренного насоса.
Рис. 11. Характеристика насоса НШ 32Ш с брозовыми шестернями и втулками при работе на воде в агрегате с мотоблокам МТЗ-05.
Рис. 12. Характеристика насоса НШ 32Ш со стальными с антикоррозионным покрытием и брозовыми втулками при работетна воде в агрегате с мотоблокам МТЗ-05.
3.2.3 Ресурс опытных и серийных насосов Ресурс серийного насоса НШ 32У-З-Л.
Испытания насоса НШ 32У-З-Л серийного исполнения (шестерни насоса, выполненные заодно с валом — стальные, опоры — алюминиевые) проводились при давлении на выходе из насоса 5кгс/см2 при уровне воды на 70 мм выше оси всасывающего отверстия насоса.
При испытаниях отмечено, что вода в гидробаке становится темной с бронзовыми блестками за счет выноса продуктов износа.
Объемная подача насоса при давлении 5кгс/см2 и температуре воды 20…24 оС при уровне воды на 70 мм выше оси всасывающего отверстия насоса в процессе испытаний составляла:
Таблица 2.
№ | Количество часов работы | Объемная подача насоса, л/мин | Ориентировочный коэффициент подачи насоса | |
39,1 | 1,0 | |||
38,6 | 1,0 | |||
37,8 | 0,98 | |||
29,3 | 0,76 | |||
19,4 | 0,51 | |||
13,8 | 0,36 | |||
После 25 часов работы насоса испытания были прекращены из-за малой объемной подачи насоса, а насос был разобран для техэкспертизы и микрометража деталей.
При разборке насоса выявлена односторонняя выработка со стороны ведомой шестерни насоса опор, компенсаторов и корпуса насоса (см. рис.13,14,15).
Ресурс насоса НШ 32Ш с бронзовыми шестернями и бронзовыми вставками в алюминиевых опорах.
Испытания насоса проводились при давлении на выходе из насоса 5кгс/см2 при уровне воды на 400 мм ниже оси всасывающего отверстия насоса.
Рис. 13. Насос НШ 32У-З-Л после 25 часов работы с односторонней выработкой опоры шестерен.
После 2-х часов работы в воде появились бронзовые продукты износа.
После 17 часов работы насос перестал качать воду. Для дальнейших испытаний уровень воды был установлен по оси всасывающего отверстия насоса.
Рис. 14.Односторонная выработка корпуса насоса, компенсатора и опоры шестерен насоса после 25 часов работы.
Рис. 15.Односторонная выработка компенсатора после 25 часов работы насоса.
Микрометражом деталей насоса (карта обмера деталей) выявлено:
— односторонняя выработка обоих опор шестерен на ведомой шестерне, корпуса насоса по месту контакта с ведомой шестерней и компенсаторов составила 6,6…6,8 мм;
— износ обоих опор ведущей шестерни по размеру 026+0,013 составил 0,12…0,35 мм;
Объемная подача насоса при давлении 5кгс/см2 и температуре воды 20…24 оС в процессе испытаний составляла:
Таблица 3.
Количество часов работы | Объемная подача насоса, л/мин | Ориентировочный коэффициент подачи насоса | Уровень воды | |
37,0 | 0,96 | На 400 мм ниже оси всасывающего отверстия насоса. По оси всасывающего отверстия | ||
33,6 | 0,88 | |||
31,4 | 0,82 | |||
28,7 | 0,75 | |||
27,9 | 0,73 | |||
23,8 | 0,62 | |||
После 20 часов работы насоса испытаний были прекращены из-за повы шенного шума при работе насоса и интенсивного выноса бронзовых продуктов износа, а насос был разобран для техэкспертизы и микрометража деталей.
Рис. 16.Ведомый шестерня При разборке насоса выявлен значительный износ зубьев обоих бронзовых шестерен (см. рис.16).
Микрометражом деталей насоса (карта обмера деталей) выявлено:
— износ зубьев шестерен составил 0,7…1,6 мм у ведомой шестерни и 1,8…2,4 мм у ведущей;
— износ корпуса насоса по размеру 055+0,04+0,01 состовил 0,03…0,06 мм;
— износ втулок по размеру 026+0,013 составил 0,03…0,08 мм;
— износ компенсаторов по размеру 12-0,08 составил 0,5…0,8 мм;
— износ валов обоих шестерен (размер 026-0,080-0,95) практически отсутствует.
Таблица 4 Обмера деталей насосов НШ 32Ш и НШ 32У-З-Л
Наименование и № деталей | Размер по чертижу | Фактический размер | ||
Насос с бронзовыми шестернями | Насос серийного исполнения | |||
Корпус насоса НШ32.03.00.022 | 055+0,04+0,01 | 55,07…55,7* | 55,05…55,6* | |
под ведущую шестерню | 55,10…55,12 | 55,42…55,47 | ||
под ведомую | 55,12…55,13 | 61,65…61,72 | ||
шестерню | 100,10* | 100,02* | ||
0100+0,04 | 100,22 | 100,24 | ||
Шестерня ведущая НШ32.03.00.023 | 026−0,080−0,95 | 25,90…25,92 | 25,90…25,92 | |
24,833−0,16 | 22,4…23,0 | 24,84…24,84 | ||
Шестерня ведомая НШ32.03.00.024 | 026−0,080−0,95 | 25,89…25,92 | 25,90…25,92 | |
24,833−0,16 | 23,2…24,1 | 24,84…24,84 | ||
Втулка НШ32.03.00.025 | 026+0,013 | 26,03…26,03 | 26,03…26,03 | |
26,07…26,08 | 26,07…26,08 | |||
26,03…26,04 | 26,03…26,04 | |||
НШ32.03.00.026 | 26,03…26,04 | 26,03…26,04 | ||
Компенсатор НШ32.03.00.003 | 12−0,08 | 11,20…11,45 | 11,45…11,52 | |
11,42…11,46 | 11,62…11,77 | |||
*Размер по месту установки втулок.
Ресурс насоса НШ 32Ш со стальными шестернями с антикоррозионным покрытием и бронзовые вставки в алюминиевых опорах.
Испытания насоса НШ 32Ш серийной конструкции, у каторого установлены бронзовые вставки в алюминиевые опоры валов — шестерен, и шестерни имеют антикоррозионное покрытие проводились при давлении на выходе из насоса 4кгс/см2 при уровне воды на 70 мм выше оси всасывающего отверстия насоса.
За время испытаний насоса в объема 100 часов отказов в работе насоса не наблюдалось.
Объемная подача насоса при давлении 4кгс/см2 и температуре воды 22…26 оС при уровне воды на 70 мм выше оси всасывающего отверстия насоса в процессе испытаний составляла:
После 100 часов работы насоса был разобран для техэкспертизы и микрометража деталей.
При внешнем осмотре отмечено, что антикоррозионное покрытие на цапфах шестерен сохранились, на зубьях шестерен имеются потертости, следы приработки, антикоррозионное покрытие сохранилось лишь частично. На других деталях видимых износов не обнаружено.
Таблица 5.
Кол-во часов работы | Объемная подача насоса, л/мин | Ориентировочный коэффициент подачи насоса | Кол-во часов работы | Объемная подача насоса, л/мин | Ориентировочный коэффициент подачи насоса | Кол-во часов работы | Объемная подача насоса, л/мин | Ориентировочный коэффициент подачи насоса | |
36,6 | 0,95 | 38,3 | 1,0 | 3,78 | 0,98 | ||||
38,0 | 0,99 | 38,3 | 1,0 | 3,78 | 0,98 | ||||
38,0 | 0,99 | 38,3 | 1,0 | 3,78 | 0,98 | ||||
38,0 | 0,99 | 3,78 | 0,98 | 3,78 | 0,98 | ||||
38,3 | 1,0 | 3,78 | 0,98 | 3,78 | 0,98 | ||||
38,3 | 1,0 | 3,78 | 0,98 | 3,78 | 0,98 | ||||
38,3 | 1,0 | 3,78 | 0,98 | 3,78 | 0,98 | ||||
Микрометражом деталей насоса (карта обмера деталей насосов НШ 32Ш после 100 часов работы) выявлено:
— износ корпуса насоса по размеру 055+0,04+0,01 состовил 0,01…0,06 мм;
— износ втулок по размеру 026+0,013 составил 0,03…0,08 мм;
— износ компенсаторов по размеру 12-0,08 составил 0,16…0,29 мм;
— износ шестерен по размеру 026-0,080-0,95) практически отсутствует.
Ресурс насоса НШ 32У-З-Л с бронзовыми вставками в алюминиевых опорах.
Испытания насоса НШ 32У-З-Л серийного исполнения, у которого алюминиевые опоры валов шестерен были заменены на алюминиевые опоры с бронзовыми от насоса, прошедшего испытания в объеме 20 часов, проводились придавлении на выходе из насоса 4кгс/см2 при уровне воды на 70 мм выше оси всасывающего отверстия насоса.
За время испытаний насоса в объеме 100 часов отказов в работе насоса не наблюдалось.
Объемная подача насоса при давлении 4кгс/см2 и температуре воды 22…28 оС при уровне воды на 70 мм выше оси всасывающего отверстия насоса в процессе испытаний составляла:
Таблица 6
Кол-во часов работы | Объемная подача насоса, л/мин | Ориентировочный коэффициент подачи насоса | Кол-во часов работы | Объемная подача насоса, л/мин | Ориентировочный коэффициент подачи насоса | Кол-во часов работы | Объемная подача насоса, л/мин | Ориентировочный коэффициент подачи насоса | |
36,9 | 0,96 | 34,9 | 0,91 | 33,5 | 0,87 | ||||
38,6 | 1,0 | 34,8 | 0,91 | 32,6 | 0,85 | ||||
38,3 | 1,0 | 34,6 | 0,90 | 32,0 | 0,83 | ||||
38,0 | 0,99 | 33,0 | 0,86 | 33,7 | 0,88 | ||||
36,0 | 0,94 | 33,2 | 0,86 | 33,7 | 0,88 | ||||
35,1 | 0,91 | 32,9 | 0,86 | 32,4 | 0,84 | ||||
36,0 | 0,94 | 32,6 | 0,85 | 32,3 | 0,84 | ||||
После 100 часов работы насоса был разобран для техэкспертизы и микрометража деталей.
При внешнем осмотре на деталях насоса имеется коррозия, видимых износов не обнаружено.
Микрометражом деталей насоса (карта обмера деталей насосов НШ 32У-З-Л с бронзовыми вставками после 100 часов работы) выявлено:
— износ корпуса насоса по размеру 055+0,04+0,01 состовил 0,10…0,15 мм;
— износ втулок по размеру 026+0,013 составил 0,01…0,05 мм;
— износ компенсаторов по размеру 12-0,08 не превышает 0,29…0,33 мм;
— износ шестерен по размеру 026-0,080-0,95) практически отсутствует.
Таблица 7
Наименование и № деталей | Размер по чертежу | Фактический размер | ||
С антикоррозионым покрытиям | Серийного исполнения | |||
Корпус насоса Ш32.03.00.022 | 055+0,04+0,01 под ведущую | 55,06…55,07* | 55,00…55,01* | |
шестерню | 55,08…55,11 | 55,12…55,15 | ||
под ведомую | 55,09…55,12 | 55,11…55,14 | ||
шестерню | 100,05* | ; | ||
0100+0,04 | 100,08 | |||
Шестерня ведущая НШ32.03.00.023 | 026−0,080−0,95 | 25,91…25,93 | 25,90…25,95 | |
24,833−0,16 | 24,72…24,80 | 24,74…24,76 | ||
Шестерня ведомая НШ32.03.00.024 | 026−0,080−0,95 | 25,93…25,96 | 25,89…25,97 | |
24,833−0,16 | 24,74…24,82 | 24,84…24,84 | ||
Втулка НШ32.03.00.025 | 026+0,013 | 26,05…26,06 | 26,04…26,07 | |
25,05…26,05 | 26,07…26,10 | |||
26,03…26,08 | 26,04…26,08 | |||
НШ32.03.00.026 | 26,04…26,08 | 26,04…26,09 | ||
Компенсатор НШ32.03.00.003 | 12−0,08 | 11,71 | 11,71 | |
11,86 | 11,67 | |||
*Размер по месту установки втулок.
Карта Обмера деталей насосов НШ 32У-З-Л с бронзовыми вставками и НШ 32Ш с стальными шестернями с антикоррозионным покрытием и бронзовые вставками после 100 часов работы
3.2.4 Коррозионная стойкость опытных насосов
Результаты испытаний коррозионной стойкости серийных и опытных образцов насослв приведены в таблице 6. Там же указаны режимы испытание состояния насосов после испытаний. На рис. 17,18, и 19 данны фотографии объектов испытаний в разобранном виде, которые характеризуют состояние деталей после завершения испытаний
Рис. 17. Общий вид насоса НШ 32У-З-Л Рис. 18.Общий вид насоса НШ 32 с бронзовыми шестернями на стальных валах и бронзовыми втулками на опорах валов шестерен.
Рис. 19. Насос НШ 32Ш с антикоррозионным покрытием.
Выводы Разработана и исследована двухступенчатая технология нитрооксидирования конструкционных сталей, заключающаяся в азотировании при температуре 570ч590°С с последующим оксидированием в парах воды при температуре 540ч560°С. Разработанный комбинированный технологический процесс химико-термической обработки предназначен для поверхностного упрочнения деталей, работающих на износ при малых контактных нагрузках и одновременно подвергающихся атмосферной коррозии, и рекомендован для замены традиционных экологически вредных гальванических способов получения покрытий.
Исследована кинетика формирования диффузионных нитрид-оксидных покрытий. Показано, что при оксидировании нитридного слоя ниже эвтектоидной температуры для системы «Fe-0» (570°С) достигается стабильность процесса и лучшие свойства изделий при формировании на поверхности азотированного слоя сплошной оксидной пленки состоящий из Fe3О4, толщиной до 3мкм и низкоазотистого нитридного подслоя состоящей из еII и гIфаз.
Исследована микроструктура, морфология и фазовый состав нитрид-оксидных покрытий, полученных при однои двухступенчатых режимах нитридоксидирования.
Установлено, что при оксидировании нитридного слоя происходит процесс диссоциации поверхностной высокоазотистой ефазы с образованием на поверхности б-фазы, на которой образуются оксиды железа.
При оксидировании нитридных слоев в атмосфере водяного пара ниже эвтектоидной температуре 570 °C на поверхности образуются оксидная пленка, состоящая из магнетита Fe3О4, выше 570 °C в составе оксидной пленки появляются оксид FеО и Fe2O3.
Установлено, что наличие в составе оксидной пленки оксида FеО приводит к растрескиванию и отслаиванию оксидной пленки с поверхности нитрид-оксидного покрытия.
На основании данных рентгеноструктурного анализа получены сведения о новой низкоазотистой фазе, условно обозначенный е", образующихся при оксидировании’нитридного слоя. Показано, что е" - фаза имеет оксикарбонитридный характер и при одновременном диффузии кислорода из насыщающей атмосферы и углерода из матрицы.
Разработана математическая модель процесса диффузии азота при оксидировании нитридных слоев и получены аналитические зависимости перераспределения концентрации азота при нитрооксидировании, которые хорошо коррелируют с результатами эксперимента. На основании полученных данных по кинетике, фазовому составу нитрид-оксидных покрытий и анализа математической модели формирования слоя построены диаграммы преимущественных режимов нитрооксидирования Исследованы физико-механические свойства диффузионных нитрид-оксидных покрытий:
Установлено, что оксидирование нитридного слоя приводит к повышению микротвердости, так как в результате диссоциации е — фазы в присутствии кислорода в зоне соединений образуется е" - фаза, имеющая оксикарбонитридный характер и значительно увеличивается содержание твердого гIфазы.
Изучение влияния температуры оксидирования на микропластичность показало, что наибольшая пластичность достигается при получении на поверхности плотной, гомогенной оксидной пленки, состоящей из Fe3O4.