Электрохимический способ осаждения
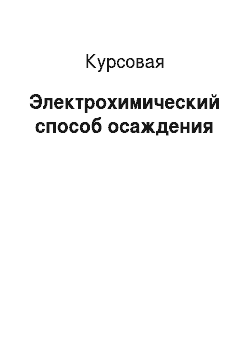
Нейтральные цианистые электролиты имеют рН = 6,5−7,5, содержание свободного цианида в них невелико (в пределах 1−2 г/л). Для получения осадков золота большой чистоты нейтральная ванна используется мало, так как при таком содержании цианистого калия возможно включение в осадок неблагородных металлов, которые могут накапливаться в электролите при работе. Нейтральные электролиты обычно широко… Читать ещё >
Электрохимический способ осаждения (реферат, курсовая, диплом, контрольная)
Гальванические покрытия широко применяются в различных отраслях промышленности для защиты изделий от коррозии, увеличения срока службы и придания им красивого декоративного вида. Один из видов нанесения гальванических покрытий — золочение.
Золото — пластичный желтый металл, его физико-химические свойства во многом зависят от состава электролита, из которого оно получено, от тех примесей металлов, которые имеются в электролите, поскольку известно, что многие металлы легко соосаждаются с золотом.
Покрытие золотом является одним из старейших методов придания декоративного вида ювелирным изделиям и различным скульптурным и архитектурным сооружениям.
Самым древним методом получения золотых покрытий является листовой способ, существующий и в настоящее время. Благодаря своей мягкости и ковкости металлическое золото может быть расплющено на лепестки толщиной 0,1−0,3 мкм. Наклеивание лепестков производится в один или несколько слоев при помощи специального лака (лак мордан), причем первый слой наносится на поверхность изделия, предварительно покрытую грунтом на основе свинцового сурика и льняной олифы и 3—5 тонкими слоями копалового лака.
Метод плакирования подобно листовому состоит в нанесении листового золота на соответствующий материал (обычно латунь или мельхиор). Для получения хорошего сцепления деталь нагревается до температуры, при которой происходит частичная взаимная диффузия одного металла в другой. Так, методом плакирования получают золоченые корпуса часов с толщиной покрытия 25—75 мкм.
Одним из старейших является также огневой метод золочения, осуществляемый путем нанесения на предметы из латуни или меди амальгамы золота с последующим нагревом, причем ртуть при этом возгоняется, а оставшееся золото плотно сцепляется с основой. Таким путем можно получить толстые слои золота, если повторять операцию несколько раз. Амальгама золота готовится смешением 1 части мелко измельченного металлического золота с 9 частями ртути. Огневой способ золочения чрезвычайно вреден и в настоящее время большого применения не имеет.
Подобным огневому является применяемый в настоящее время для золочения крупных деталей метод нанесения на поверхность изделия органических соединений золота с последующим разложением путем нагревания до 700° С, в результате чего на изделии остается чистое золото.
К новым методам нанесения золотых покрытий относится также способ распыления золота в вакууме, обычно применяемый для деталей небольшого размера.
Для восстановления истертых участков покрытия предложен метод адгезионного золочения. Он заключается в натирании поверхности изделия с помощью волосяных щеток увлажненной смесью NaCl и порошка металлического золота (4:1). Тонко измельченный порошок золота получался в результате восстановления раствора хлорного золота насыщенным раствором двухвалентного сульфата железа при комнатной температуре.
Электрохимический способ золочения начал получать распространение в начале XIX в. Золото относится к числу первых металлов, осаждаемых с применением внешнего источника тока. Вначале электролиз применялся в целях рафинирования золота, для чего использовался кислый хлоридный электролит. Почти одновременно с этим начал получать распространение метод электролитического золочения с декоративной целью.
К электрохимическим способам золочения относятся также контактный метод и метод погружения, так как золото при этих способах отлагается в результате электрохимической реакции без применения внешнего источника тока.
При контактном способе можно получать осадки большой толщины, так как осаждение ведется при помощи внутреннего источника тока — гальванического элемента, образуемого цинковым электродом и покрываемой деталью, погруженными в раствор, содержащий золото.
При методе погружения детали помещаются в раствор, содержащий золото. Как более электроположительное, золото вытесняется металлом покрываемого изделия, причем процесс останавливается, когда вся поверхность изделия будет покрыта тонким слоем золота. Поэтому при методе погружения толщина покрытия невелика.
1. Электрохимический способ осаждения
Впервые золотые покрытия электрохимическим способом были получены в 1805 г. в Италии профессором химии Луиджи Бругнателли. Осаждение золота из цианистого электролита было запатентовано в Англии братьями Элкингтон в 1840 г. С тех пор электрохимическое золочение широко применяли и применяют в настоящее время в производстве предметов быта и скульптур, в часовой и ювелирной промышленности.
Электрохимический способ позволяет получать покрытия любых оттенков и толщиной от сотых долей микрометра до десятых долей миллиметра и более. Покрытия электрохимическим способом наносят из двух групп электролитов: цианистых и нецианистых. К первым из них относят щелочные, нейтральные и кислые электролиты, в которых золото находится в виде цианистого комплексного аниона [Au (CN)2]-, весьма устойчивого как в щелочной, так и в кислой среде вплоть до рН = 3. Кислые электролиты, несмотря на наличие в них цианистого аниона, считают нетоксичными и часто относят нецианистым, так как они не содержат цианид в свободном состоянии. Разработаны сильнокислые электролиты (рН = 0−1,5), в которых золото связано в трехвалентный комплекс [Au (CN)4]-.
Для промышленного применения наибольшее распространение получили цианистые щелочные и кислые электролиты. Нецианистые электролиты практического значения не имеют, хотя синеродистый получил и практическое использование, а сульфитный находится в стадии освоения на часовых заводах и весьма перспективен.
2. Составы цианистых электролитов золочения
Щелочные электролиты работают при рН = 11−11,5 и содержат золото от 0,5 до 15 г/л; свободный цианистый калий в пределах 15−90 г/л и электропроводящую добавку от 50 до 100 г/л.
В щелочных электролитах золото находится в виде комплексного одновалентного цианида К[Аu (CN)2]. Осадки, получаемые из щелочных цианистых электролитов, обычно матовые.
Для получения осадков большой толщины необходима повышенная концентрация золота (от 8 до 12 г/л) и свободного цианида (70−90 г/л), электролиз должен проводиться при повышенных температурах (80−90 °С) и энергичном перемешивании; при этом плотности тока достигают до 10 А/дм2. Недостаток щелочных цианистых электролитов — накопление карбонатов, которые нужно периодически удалять. Преимущество щелочных электролитов — возможность получения осадков большой чистоты, особенно в том случае, если электролит свежеприготовленный и концентрация свободного цианида достаточно высока (от 30 до 90 г/л), так как примеси неблагородных металлов при больших концентрациях цианида не соосаждаются. Щелочные электролиты могут работать с растворимыми анодами, потому что имеют высокое содержание свободного цианида.
Нейтральные цианистые электролиты имеют рН = 6,5−7,5, содержание свободного цианида в них невелико (в пределах 1−2 г/л). Для получения осадков золота большой чистоты нейтральная ванна используется мало, так как при таком содержании цианистого калия возможно включение в осадок неблагородных металлов, которые могут накапливаться в электролите при работе. Нейтральные электролиты обычно широко используются при покрытии сплавами золото — медь, для получения блестящих осадков толщиной до 20 мкм и более. Кислотность этих электролитов поддерживается добавлением фосфорной кислоты. В этих электролитах золото находится в виде одновалентного дицианаурата К[Аu (СN)2]. Работа в них проводится с нерастворимыми анодами. Эти электролиты более производительны, так как выход по току в них близок к 100, в то время, как у щелочных всего 70 -30%. В нейтральных ваннах можно получать более толстые покрытия без промежуточной крацовки. Недостаток нейтральных электролитов — их нестабильность.
Кислые электролиты работают обычно при рН = 3−6. Из этих растворов получаются блестящие осадки, особенно при добавке таких металлов как никель, кобальт, цинк, олово и др. Кислотность в них поддерживается с помощью фосфорной или органических кислот (лимонной, винной, щавелевой и др.). Свободного цианида в электролите нет. Золочение в таких ваннах возможно ввиду того, что цианистый комплекс золота очень прочный и не разрушается при этих значениях рН, особенно комплекс трехвалентного золота К[Au (CN)4]. Вероятно, большинство кислых электролитов в своей основе имеют трехвалентный комплекс золота.
Эти электролиты, как и нейтральные, работают с нерастворимыми анодами. В кислых растворах значительно более низкий выход по току (в пределах 30−40%). Это связано, в основном, с тем, что они работают при низких температурах (20 — 25 °С) и повышенных плотностях тока, что и является их основным преимуществом. Покрытия, полученные из нейтральных и кислых электролитов, менее пористы, но зато и более хрупки. Недостатками их является низкая рассеивающая способность по сравнению со щелочными (рис. 1).
Золото в цианистых электролитах, как уже говорилось выше, может находиться в виде двух комплексов: трехвалентного K[Au (CN)4] и одновалентного K[Au (CN)2]. В обычных щелочных цианистых электролитах золото находится в основном в одновалентной форме, хотя при химическом приготовлении может образовываться небольшое количество и трехвалентного комплекса, и только при анодном растворении золото переходит в раствор в виде одновалентного комплекса.
Определение катодных выходов по току при электроосаждении золота при постоянной величине потенциалов показало, что при малых плотностях тока выход по току составляет 10−60%, затем при увеличении плотности тока он достигает 100%, а когда наблюдается выделение водорода, он снова падает, что уже вполне закономерно. Так как в электролите не было трехвалентного золота, то низкий выход по току при малых плотностях тока не может быть связан с его восстановлением. По всей видимости низкий выход по току может быть обусловлен реакцией ионизации металла по уравнениям:
2Au + 4KCN + O2 + 2H2О = 2K[Au (CN)2] + H2О2 + 2KOH; (1)
2Au + 4KCN + H2О2 = 2K[Au (CN)2] + 2KOH. (2)
Опытным путем было определено, что в растворе, содержащем 30 г/л Аu и 4,3 г/л КСN (свободном) в отсутствии поляризации золотой электрод растворяется со скоростью 1,0*103 г/см2, причем концентрация цианистого калия не влияет на скорость растворения. Поляризационная кривая электроосаждения золота (рис. 2) имеет две площадки предельного тока, которые, как было выяснено, имеют диффузионный характер. Подтверждением этому служат результаты измерения стационарных потенциалов золотого электрода при различных содержаниях цианистого калия. Считая, что реакция, определяющая потенциал электрода, следующая:
[Au (CN)3]— = AuCN + CN-;
AuCN = Au+ + CN-;
произвели расчет изменения потенциала в зависимости от изменения концентрации KCN. При этом оказалось, что экспериментальные величины потенциалов тем ближе к расчетным, чем выше концентрация свободного KCN в растворе. Таким образом, на основании всех исследований катодный процесс на различных участках поляризационной кривой объясняется так: на первых двух участках кривой (см. рис. 2) при потенциале 0,4−0,6 В в элементарном разряде участвуют соединения типа AuCN или Au2(CN)2. На 3-м и 4-м участках в пределах потенциалов 0,7−0,9 В процесс осуществляется при разряде анионов [Au (CN)2]—. На 5-м участке протекает процесс выделения водорода и разряд [Au (CN)2]— на предельном токе. Под действием большого электрического поля в двойном слое у катода происходит адсорбция аниона [Au (CN)2]— положительным концом к катоду и таким образом облегчается его разряд:
[Au (CN)2]— + e = [Au (CN)2]2-;
[Au (CN)2]2— = Au + 2CN—.
Поведение трехвалентного комплекса золота при электроосаждении изучено значительно меньше, чем одновалентного.
Составы электролитов были классифицированы Е. Паркером по кислотности; они представлены в табл. 1. Ванны 1 и 2 являются типичными щелочными ваннами золочения, они могут применяться для получения подслоя под толстые покрытия или для осаждения декоративных покрытий золотом.
Электролит № 2 с добавками различных металлов, таких как никель, кобальт, серебро, медь или кадмий, обычно применяются для покрытия в ювелирной промышленности. Электролит № 3 применяется для толстослойного золочения (до 1 мм): электролит № 4 обычно применяют для ванн колокольного типа. Ванна № 5 — (железистосинеродистая) применяется для скоростного золочения. Ванны № 6 и 7 — электролиты нейтрального и кислого золочения.
Основными компонентами щелочных электролитов является золото в виде цианистого одновалентного комплекса K[Au (CN)2] или Na[Au (CN)2]; свободный цианистый калий и двухзамещенные фосфаты (иногда эти электролиты содержат еще карбонат или сульфит калия). Последний добавляется для восстановления трехвалентного золота, которое может присутствовать в свежеприготовленном электролите. Карбонаты и фосфаты играют роль электропроводных и отчасти буферных добавок. Все добавки к тому же вызывают повышение поляризации при осаждении золота и, таким образом, способствуют получению мелкокристаллических осадков. Щелочные ванны работают при высоких температурах. При использовании нерастворимых анодов, можно работать и c натриевыми солями, так как при работе с растворимыми анодами: на анодах образуется пленка плохо растворимой соли Na[Au (CN)2]. Растворимость золотых комплексов понижается в присутствии свободного цианида и электропроводных добавок, поэтому применение концентрированных по золоту электролитов вызывает необходимость применения калиевых солей даже в случае работы с нерастворимыми анодами. Содержание золота в электролите в зависимости от назначения может колебаться от 0,5 до 15,0 г/л. Концентрация цианистого калия для получения гладких мелкокристаллических осадков должна соответствовать соотношению концентрации золота и свободного цианида как 1:20. Золочение в стационарных ванных во избежание больших потерь золота обычно производится в сравнительно бедных по содержанию золота электролитах. Обычно рекомендуется следующий состав, г/л: золото 2−3; калий цианистый 10−15; калий углекислый 30−50. Режим работы: плотность тока 0,13−0,14 А/дм2; температура 60−70 °С.
Для получения покрытий большой толщины рекомендуется следующий состав, г/л: дицианаурат калия 15−25; калий цианистый 8−10; калий углекислый 100; кали едкое 1. Режим работы: плотность тока 2−4 А/дм2; температура 55−60 °С.
Режимы в щелочных электролитах золочения значительно ограничены по сравнению с кислыми и нейтральными электролитами. Катодная плотность тока находится в пределах 0,1−1 А/дм2 в зависимости от концентрации золота. Температура электролита обычно поддерживается в пределах 55−70 °С, кроме того желательно механическое перемешивание. Приготовление щелочных цианистых электролитов в основном заключается в приготовлении: одновалентного комплекса золота, который может готовиться следующими методами: анодным растворением, растворением гремучего золота в цианистом калии и непосредственном растворении хлорного золота в цианистом калии.
1-й метод — анодное растворение с применением пористых керамических диафрагм для разделения катодного и анодного пространства. Диафрагма заполняется католитом (3%-ным раствором едкого калия или 6−7%-ного раствора поташа); катоды — стальные стержни завешиваются в католит. В анодное пространство заливают анолит — раствор цианистого калия концентрацией 20−30 г/л. В качестве анодов применяется чистое золото в виде пластин, завернутых в чехлы. Температура анолита 70 °C, напряжение на ванне в пределах 2−8 В в зависимости от сопротивления диафрагм. Анодная плотность тока поддерживается в пределах 1 — 1,5 А/дм2. При анодном растворении золото переходит в раствор в виде цианистого комплекса K[Au (CN)2].
2-й метод — растворение гремучего золота в цианистом калии. Гремучее золото получают осаждением из раствора хлорного золота добавлением аммиака. Хлорное золото разбавляют пятикратным количеством воды и переводят в гремучее добавлением 25% аммиака из расчета 10 мл NH3OH на 1 г Аu с последующим нагреванием раствора для удаления избытка аммиака. Осадок гремучего золота состава Аu (NH3)3(ON)3 отстаивают, промывают на фильтре горячей водой и затем с фильтра переносят в раствор цианистого калия (15−20 г/л), в котором он легко растворяется.
В случае отсутствия хлорного золота гремучее может быть получено растворением металлического золота в царской водке последующим упариванием (на водяной бане) полученного раствора.
3-й метод — непосредственное растворение хлорного золота заключается в том, что раствор хлорного золота нейтрализуют раствором поташа до прекращения выделения пузырьков СО2 и в нейтрализованный раствор добавляют цианистый калий из расчет 3−4 г на 1 г золота. Для приготовления электролитов рекомендуется использовать химически чистый цианистый калий. В случае использования технического золота его рекомендуется обработать активированным углем и если возможно прокипятить в течении 1−2 ч, после чего его отфильтровать.
Корректирование щелочных цианистых электролитов из-за растворимых анодов не составляет трудностей. Правда, в процессе работы благодаря 100%-му анодному выходу по току (катодный выход по току при этом составляет 70−90%) происходит накопление золота. Но если часть растворимых анодов можно заме нить на нерастворимые (угольные или из нержавеющей стали) подобрав соотношение площадей так, чтобы количество растворенного золота равнялось осажденному, то состав электролита будет весьма стабилен. Цианистый калий добавляется в ванну ежедневно по результатам анализа. В электролите золочения так же, как и в электролитах серебрения происходит разложение цианистого калия с образованием карбонатов. Накопление карбонатов в электролитах золочения, как отмечают многие авторы, отрицательно влияет на структуру и внешний вид покрытий. Для удаления избытка карбонатов в качестве осаждающих агентов предлагается цианид бария и кислый фосфат кальция, причем осаждение надо проводить из горячей раствора, затем с медленным охлаждением и фильтрацией. Сильное влияние на качество покрытия оказывают примеси металлов, которые в процессе работы накапливаются в электролите в таком количестве, что иногда превышают концентрацию золота. Эти примеси накапливаются в результате растворения основы, причем наличие таких металлов как свинец, мышьяк или сурьма в количестве больше, чем 1 г/л вызывает образование темных губчатых осадков. Накопление меди ведет к соосаждению ее с золотом и получению покрытия розового цвета; при покрытии серебра или посеребренных деталей в электролите накапливаются ионы серебра, которые также легко соосаждаются с золотом, при содержании его в покрытие до 5% оно становится полублестящим и твердым, при большем содержании серебра в покрытии, оно приобретает зеленоватый оттенок. Серебро легко удаляется из ванны проработкой током при ik = 0,02−0,05 А/дм2 с энергичным перемешиванием. В свежеприготовленном электролите золочения наблюдается аномалии как в катодном, так и в анодном процессах, особенно выходов по току, поэтому на практике обычно свежеприготовленный раствор разбавляют электролитом, уже работающим в течение некоторого времени. Отмеченные аномалии можно объяснить, если учесть, что при приготовлении золотого электролита, за исключением способа анодного растворения, может всегда образоваться некоторое количество трехвалентного комплекса золота; поэтому катодный выход по току будет ниже, так как часть тока будет расходоваться на его восстановление. Анодный выход по току также будет выше, так как на аноде может протекать реакция химического взаимодействия [Au (CN)4]— с металлическим золотом — растворением анода:
[Au (CN)4]— + 2Au + 2CN— = 3[Au (CN)2]— (3)
по мере работы электролита трехвалентный комплекс восстанавливается и процессы на аноде стабилизируются. Чтобы уменьшить влияние примесей неблагородных металлов, рекомендуется повысить концентрацию цианистого калия в электролите до 25 г/л тогда эти металлы не смогут соосаждаться с золотом. Кроме золочения в стационарных условиях существует способ золочения мелких деталей в колокольчике из следующего электролита, г/л: золото 4, калий цианистый (свободный) 20−25. Режим работы: начальная катодная плотность тока, А/дм2 0,25−0,4 А/дм; температура электролита 60−70 °С; среднее время золочения 1 мкм за 10 мин анод — угольная пластина. Электролиз ведут на выработку золота. Перед каждой загрузкой деталей в электролит добавляется необходимое количество золота для осаждения в виде концентрата. Добавка производится в два приема. Электролиз ведут до начала вспенивания электролита, затем плотность тока снижают до 0,03−0,05 А/дм2, что обеспечивает полноту осаждения всего золота. Эта технология практически исключает перерасход золота на детали, и отклонения от заданной толщины не выходят за пределы допустимых границ. Последующая галтовка деталей со стальными шариками в растворе мыла производит уплотнение покрытия, и оно приобретает полублестящий вид. Этот метод может применяться для регенерации и утилизации электролитов.
Кислые и нейтральные электролиты содержат кроме основного компонента — комплексной соли золотоорганические кислоты и их соли или фосфорную кислоту и ее соли, а также добавки неблагородных металлов, таких, как Ni, Co, Cd, Cu, Zn, Sn и др. Составы электролитов и режим электролиза приведены в табл. 2. Практически во всех электролитах допустимая плотность тока, позволяющая работать с высоким выходом по току, зависит от температуры и концентрации золота в электролите (рис. 3).
Чем выше температура и концентрация золота, тем выше допустимая плотность тока. Необходимо отметить, что свойства осадков, полученных из кислых электролитов, а особенно внутренние напряжения, выше, чем из щелочных электролитов, правда внутренние напряжения с повышением температуры уменьшаются.
Температура электролита по данным Напуха Э. З. при этом играет очень важную роль: исследования пористости золотых покрытий показали, что по пористости 1 мкм покрытия, полученного из электролита при 60 °C, равен 3 мкм покрытия, полученного из электролита при 20 °C. Покрытия, полученные при оптимальных условиях, толщиной 3 мкм, способны защитить основу в травильных растворах. Пористость золотых покрытий снижается с увеличением концентрации лимонной кислоты, но при этом необходимо помнить, что для нормальной работы электролита и для получения хороших, не загрязненных покрытий, электролиз следует вести при значительном снижении токовой нагрузки до 0,04−0,05 А/дм2. Такой электролит при периодической очистке активированным углем может эксплуатироваться без регенерации в течение 3−4 лет.
По данным того же автора добавки к цитратному электролиту трилона Б и сульфата калия (электролит 5 табл. 2) значительно стабилизируют работу электролита и улучшают параметры покрытия. Такой электролит может эксплуатироваться даже при комнатной температуре с той же пористостью, что и электролит без добавок, но работающий при 60 °C.
В электролите с добавками повышается выход по току, а следовательно, и скорость наращивания покрытия. Так, в электролите 5 (см. табл. 2) получают 1,5−2 мкм за 5 мин.
Лимоннокислые электролиты золочения завоевали себе широкую популярность у потребителей из-за высоких физико-химических свойств золотых покрытий, но для сварки и пайки многих элементов приборов используют Аu покрытия чистоты 99,9%, что очень трудно получить из кислого электролита. Так, по данным Юодказиса К. С. и других, покрытия из нитратного электролита содержат до 0,02% углерода, практически столько же кислорода и азота (из-за разложения лимонной кислоты или других органических соединений). Поэтому для получения необходимого качества покрытия следует использовать реактивы высокого класса чистоты (или производить их перекристаллизацию), а также не допускать пребывания деталей в ванне без тока. Необходимо также использовать ванну предварительного золочения с понижением до 0,5 г/л металла-золота. Лучше всего процесс вести в области рН ближе к нейтральным 6−7, а поддерживать рН следует с помощью фосфатов (если необходимо, можно использовать и фосфорную кислоту). Рекомендуемый этими авторами состав электролита 6 — см. в табл. 2.
Приготовление кислых и нейтральных электролитов также имеет свои особенности. Так, комплексный цианид золота, необходимый в электролите для кислых и нейтральных электролитов, готовится путем растворения гремучего золота в цианистом калии. Избыток свободного цианида в полученном комплексе не должен быть больше 0,3 г/л, так как иначе наблюдается повышенная напряженность в осадках. Отдельно готовится раствор органической кислоты и нейтрализуется 10%-ным раствором щелочи до нужного рН. Соли никеля, цинка или других металлов отдельно растворяются в воде и добавляются в нейтрализованный раствор, после этого вводится растворенный комплекс золота. Для электролите с низким значением рН обязательна нейтрализация органической кислоты перед сливанием всех растворов, так как возможно разложение одновалентного цианистого комплекса золота, поскольку последний стоек только при рН не ниже 3,0. Если получение электролит имеет рН выше требуемого, то снижение кислотности производится добавкой органической кислоты. Эти электролит работают с нерастворимыми анодами и поэтому концентрация золота падает; нормальная работа ванны возможна только до снижения содержания золота до 1,0−1,5 г/л, после чего осадки становятся матовыми. После корректировки электролита и доведения концентрации золота до 2,5−3,5 г/л электролит начинает работать нормально. При высокой концентрации золота в электролит выше 5 г/л получаются напряженные растрескивающие осадки. Содержание присадок металлов меняется мало, концентрацию органической кислоты определяют измерением рН; при его повышении добавляют органическую кислоту в виде концентрированного раствора. После корректировки ванны, качество покрытия улучшается.
В кислых электролитах золочения, работающих при рН<4, железо может вытравливаться из основы (инвар, пермаллой) со скоростью 0,045 г/см2 и постепенно переходить в Fe3+. При этом появляется брак на золоте в виде шероховатости, рыжих пятен и точек. Освобождаться от железа рекомендуется в виде гидроксидов.
Произведения растворимости железа следующие:
ПрFe (OH)2 = 1,6*10−14; ПрFе (OH)3, = 1,1*10−36.
При рН гидратообразования трудно осадить железо в виде гидратов из-за комплексообразования в растворе, поэтому рекомендуется электролит обработать 30%-ным раствором Н2О2 затем раствор подщелачивают до рН 5−6; при этом Fe (OH)3 почти полностью выпадает в осадок, производят фильтрацию и промывку осадка и электролит после корректировки возвращают в эксплуатацию.
3. Нецианистые электролиты золочения
Из нецианистых электролитов нашел промышленное применение железистосинеродистый электролит золочения. Готовят этот электролит кипячением хлорного золота с К2Fе (СN)6 и соды. В электролите присутствует золото в виде цианистого комплекса, но вопрос о валентности золота до сих пор остается дискуссионным. Роль K4Fe (CN)6 при приготовлении заключается в том, чтобы перевести малоустойчивый железистосинеродистый комплекс в форму трехвалентного цианистого комплекса. При этом освобождается двухвалентное железо, которое постепенно образует нерастворимые соединения; и состав, и цвет осадков зависят от соотношения K4Fe (CN)6 и НАuС14 и рН раствора. В зависимости от этого соотношения осадки получаются различных цветов: желтого, коричневого, зеленого или синего. Если добавлено менее 1/3 эквимоляриого количества K4Fe (CN)6, то выпадает желтый осадок Au4[Fe (CN)6], нерастворимый в воде и кислотах
12[AuCl4]— + [Fe (CN)6]— = Au4[Fe (CN)6] + 8[AuCl4]— + 16Cl—. (4)
При добавлении щелочи желтый осадок темнеет, по-видимому, образуя окись золота
Au4[Fe (CN)6] + 12OH— = 2Au2O3 + 3[Fe (CN)6]— + 6H2O (5)
но этот же желтый осадок может растворяться в избытке цианистого калия.
Au4[Fe (CN)6] + 16CN— = 4[Au (CN)4]— + 3[Fe (CN)]4— (6)
Если же золотохлористоводородную кислоту кипятят больше, чем с эквимолярным количеством К4Fе (СN)6, то образуется синий осадок:
6[AuCl4]— + 7[Fe (CN)6]4— + 4H+ + O2 = 6[Au (CN)4]— + Fe4[Fe (CN)6]3 + 24С1— + 2Н2О. (7)
Если же к этому осадку добавить щелочь, то образуется гидроокись железа, а золото в растворе будет находиться в виде трехвалентного цианистого комплекса:
Fe4[Fe (CN)6]3 + 12KOH = 3K4[Fe (CN)6] + 4Fe (OH)3. (8)
Все эти процессы ускоряются кипячением.
В зависимости от рН раствора будет иметь место та или иная реакция, если рН<6 и при избытке K4Fe (CN)6, образовавшиеся ионы Fe3+ по реакции (7) будут образовывать берлинскую лазурь; если рН>6, то из берлинской лазури по реакции (8) будет образовываться гидрат окиси железа. Из всего вышеприведенного следует, что на каждый моль золота требуется 2/3 моля K4Fe (CN)6 и избыток его необходим только при работе с растворимым анодом и анодами и при высоких плотностях тока. При работе с нерастворимыми анодами в электролите постепенно накапливается цианистый калий, причем на каждый моль золота выделяется 4 М KCN.
При приготовлении электролита по вышеприведенным реакциям с рН<6 существование трехвалентного комплекса золота вполне обосновано, так как при этих значениях рН он устойчив даже при кипячении. Кипячение раствора после его подщелачивания может вызвать разложение трехвалентного комплекса до одновалентного.
Хейфец В.Л. предлагает другое приготовление железистосинеродистого электролита — кипячение в щелочной среде, где трехвалентный комплекс золота существовать не может. Автор предлагает следующую схему реакций:
6HAuCl4 + 18K4Fe (CN)6 = 6H[Au (CN)2] + 2Fe4[Fe (CN)6]3 + 4K3Fe (CN)6 + 24KCl + 36KCN; (9)
при добавлении соды
6H[Au (CN)2] + 2Fe4[Fe (CN)6] + 15Na2CO3 + 9H2O = 6Na[Au (CN)2] + 15CO2 + 16Na4[Fe (CN)6] + 8Fe (OH)3. (10)
Суммарная реакция
6HAuCl4 + 18K4[Fe (CN)6] + 15Na2CO3 + 9H2O = 6Na[Au (CN)2] + 4K3Fe (CN)6 + 24KCl + 36KCN + 8Fe (OH)3 + 6Na4[Fe (CN)6] + l5CO2. (11)
Из приведенной схемы ясно, что отношение K4Fe (CN)6 к НАuС14 составляет 3:1. Исходя из состава электролита предполагается протекание следующих реакций на катоде:
[Fe (CN)6]3— + e > [Fe (CN)6]4— е1 = +0,36 В; (12)
[Au (CN)2]— + e > Au + 2CN— е2 = -0,6 В; (13)
H2O + e > l/2H2 + OH— pH=14 е3 =-0,826 В. (14)
Поляризационные кривые (рис.4), снятые в этом электролите, имеют две площадки, соответствующие реакциям (12), (13). В железистосинеродистом электролите низкие выходы по току связаны с восстановлением K3Fe (CN)6 по реакциям (11), (12). Увеличение выхода по току в железисто-синеродистом электролите возможно при кипячении электролита, при этом уменьшается количество K3Fe (CN)6,так как в щелочных растворах при 70 °C происходит разложение K3Fe (CN)6 по схеме
13K3Fe (CN)6 + 6H2O + 9KOH = Fe (OH)3 + 12K4[Fe (CN)6] + 6NH3 + 6C02. (15)
Увеличить выход по току и поднять плотность тока позволяет применение реверсирования тока с соотношением катодного и анодного периодов, равным 13:1, при этом ik можно поднять до 1,6 А/дм2. Покрытия получаются светлыми, гладкими, имеют повышенную твердость и отражательную способность. Такие же результаты дает наложение асимметричного тока на постоянный. Железистосинеродистые электролиты, применяемые на практике, имеют различные составы в зависимости от содержания золота в них (см. табл. 3).
Добавки в электролит № 3 роданистого калия и сегнетовой соли применяются для осаждения с растворимыми анодами и с применением реверса. Корректировка электролитов, работающих с нерастворимыми анодами заключается в добавлении концентрата приготовленного так же, как и обычный электролит. Четвертый электролит применяют для получения толстых осадков. Ванна № 5 является этилендиаминовым электролитом, в который золото вводится в виде сульфитного комплекса, причем покрытия получаются зеркально блестящие, но более пористые, чем из цианистого электролита. На практике этот электролит из-за этилендиамина не может быть применен.
Попытки получить новые нецианистые комплексы золота продолжаются. Найдено, что золото образует комплексы смешанного типа на основе сульфита золота с этилендиаминтетрауксусной кислотой ЭДТА, с нитрилтриуксусной кислотой NTA и с оксиэтиленинодиуксусной кислотой. Получающиеся комплексы имеют структуру хелатного типа. Наибольшая стойкость отмечена для комплекса золота с ЭДТА К4 ?10−23. K6[Au (SO3)2 ЭДТА].
На основе его и создан электролит, состав которого представлен в табл. 3 под номером 6.
Электролит устойчив, отличается высокой катодной поляризацией, скорость осаждения в нем 7−14 мкм/ч.
4. Возможные нарушения здоровья при воздействии химических веществ
электролит золото калий Производственная среда в цехах гальванопокрытий может оказывать неблагоприятное воздействие на работающих вследствие наличия вредных химических и физических факторов. Как показывают исследования в гальванических цехах число работающих, имеющих постоянный контакт с химически вредными веществами, составляет 2/з от общего числа работающих и является одинаковым как для мужчин, так и дли женщин. Химические вещества при любом пути поступления в организм человека могут вызывать острые или хронические отравления, профессиональные заболевания, заболевания с временной потерей трудоспособности. В результате воздействия химических веществ могут поражаться слизистые оболочки носа, глотки, зева, органы дыхания бронхи, легкие, пищеварительная система и др.
К вредным веществам относятся кислоты, щелочи, растворители (ароматические, хлорированные и другие «углеводороды), соли тяжелых металлов и сами металлы, цианистые соединения и др. Кислоты (серная, соляная, азотная и др.) и их растворы представляют опасность как при вдыхании паров, так и при попадании на кожу. В первом случае отмечаются поражения слизистой оболочки носоглотки и гортани, приводящие к появлению хронических заболеваний (ринит, бронхит), иногда к разрушению зубной эмали. Попадание на кожу приводит к ожогам или к раздражению. Примерно такая же клиническая картина наблюдается при воздействии на организм щелочей. Ожоги щелочами протекают значительно тяжелее.
Важно отметить, что почти все кислоты, щелочи и органические растворители обладают выраженным обезжиривающим действием на кожу. Это приводит к нарушению ее защитных функций и способствует развитию заболеваний в результате одновременного или последующего контакта с хромом, никелем и другими сенсибилизаторами.
В токсиколого-клинической характеристике действия отдельных кислот имеется ряд специфических особенностей.
Соляная кислота НСl оказывает раздражающее воздействие на дыхательную систему, вызывает ожоги кожи. Наиболее опасны выделения хлористого водорода и его соединений с водяными парами, что приводит к образованию тумана в воздухе рабочей зоны.
Серная кислота H2SO4 при попадании на кожу вызывает более выраженные ожоги, чем соляная. Для обеих кислот характерна возможность наличия в них мышьяка в виде примеси (в технической соляной кислоте содержится до 0,01% мышьяка), что может привести к образованию мышьяковистого водорода — чрезвычайно опасного вещества. Мышьяк как источник возможного выделения мышьяковистого водорода AsH3 может находиться и в металле, подвергаемом воздействию кислот.
Азотная кислота HNO3 поражает дыхательные пути, зубы, вызывает ожоги кожи с возможным развитием экземы.
Уксусная кислота СН3СООН является сильным раздражителем. Основные симптомы поражения: ожоги кожи, хронический ринит, фарингит, бронхит, конъюнктивит.
Щелочи NaOH и КОН получили наиболее широкое распространение в гальванотехнике. Это очень сильные щелочи, воздействие которых проявляется в основном при контакте с незащищенной кожей. В результате резкого прижигающего действия на коже возникают язвы, струпья, экзематозные поражения. Очень большую опасность представляет попадание щелочей в глаза, что может вызвать в них необратимые процессы, поэтому в таком случае нужно срочно принимать решительные меры.
Ароматические углеводороды, применяемые в качестве растворителей, — это бензол и его гомологи: толуол и ксилол. Они при длительном воздействии в концентрациях выше ПДК вызывают хронические отравления с изменениями кроветворной системы (костного мозга), нервной системы (полиневриты, астенические симптомы), поражения печени и других внутренних органов. В начальном периоде острых отравлений появляются жалобы на быструю утомляемость, слабость, головные боли. При продолжении контакта с веществами начинает появляться кровоточивость. Все указанные явления могут возникать при вдыхании паров растворителей и при их контакте с кожей, через которую они легко проникают. Наиболее токсичным является бензол, в меньшей степени токсичны толуол и ксилол.
Хром — наиболее опасный и вредный из металлов в практике гальванопокрытий. Вредны и его соединения. В промышленности применяются окись хрома Сr2Оз, хромовый ангидрид СrО3, бихромат калия К2Сг2О7. Все эти вещества оказывают вредное воздействие на печень, почки, пищеварительную, сердечно-сосудистую систему, кожу и слизистые оболочки. В развитии интоксикации возможны приступы бронхиальной астмы и хромовые экземы, являющиеся результатом сенсибилизации к хрому.
Соединения никеля (сернокислый никель NiSO4, солянокислый никель NiCl2) по своему действию на организм человека в общем сходны с соединениями хрома. Характерным является воспалительное поражение слизистой оболочки носа, иногда сопровождаемое носовыми кровотечениями. Возможно появление бронхиальной астмы у лиц с повышенной чувствительностью к никелю. Никелевые дерматиты составляют до 15% всех профессиональных заболеваний кожи в промышленности. Весьма неблагоприятно сочетание воздействия солей никеля и серной кислоты на верхние дыхательные пути.
Соединения цинка ZnSO4 в условиях гальванического цеха выбывают поражения носа, языка, десен. Отмечаются повышенная заболеваемость органов дыхания, изъязвления кожи, которые возникают при воздействии сухого порошка сернокислого цинка и его растворов.
Соли кадмия CdSO4 воздействуют на функции обоняния, появляется золотисто-желтая кайма зубов, носовые кровотечения. Жалобы неспецифичны.
Медь и ее соли CuSO4 могут поражать зубы, слизистую оболочку рта, приводить к появлению язвы желудка, раздражению кожи, слизистых.
Цианистые соединения широко применяются в практике гальванопокрытий. Соли (KCN и NaCN) синильной кислоты (НCN) часто используются в гальванических цехах. Соли легко разлагаются на воздухе в условиях повышенной влажности и присутствия углекислоты воздуха с образованием цианистого водорода.
Вдыхание синильной кислоты в виде паров или цианистого водорода приводит к поражениям различной тяжести, но всегда весьма опасным для здоровья и даже жизни. Причинный механизм отравления состоит в образовании циангемоглобина с блокадой и прекращением функций гемоглобина — основного транспортного физиологического механизма доставки кислорода в ткани. В результате происходит прекращение тканевого дыхания.
В тяжелых случаях при вдыхании HCN наступает быстрая потеря сознания. В более легких случаях отмечается металлический жгучий вкус во рту, слюнотечение, покраснение глаз, боль и чувство сдавления в груди, тошнота, рвота, одышка, пульсация височных артерий, судороги вплоть до паралича.
При постоянном контакте с цианистыми солями, их растворами и при приготовлении электролитов возникают поражения кожи, сопровождающиеся зудом, изъязвлениями, хронической экземой. Установлена возможность всасывания цианидов через слизистую полости рта. Заглатывание цианидов в результате небрежности или других причин может очень быстро привести к непоправимым последствиям. Следует отметить, что судороги, одышка, потеря сознания отмечаются в очень тяжелых случаях.
Из приведенных токсиколого-клинических признаков воздействия химических веществ на организм следует, что в условиях большого числа опасных факторов решающее значение имеет внедрение системы эффективных мероприятий по устранению малейших возможностей контакта с вредными веществами. Тогда потенциальная опасность их воздействия будет предотвращена.
Заключение
До середины этого столетия золотые покрытия применились в основном с декоративной целью в ювелирной промышленности или с целью защиты от коррозии лабораторного оборудования (калориметрические бомбы, аналитические разновесы и т. п.). Для ювелирных целей пользуются осадками золота, окрашенными в различные тона, которые получаются при добавке в золотой электролит небольших количеств различных металлов, например, Ni, Co, Ag, Cd, Cu, Zn и Sn. При этом окраска изменяется, варьирует от очень желтой до зеленой и почти белой, соответствующей окраске никеля. Такие покрытия очень тонкие и почти все без исключения являются сплавами золота с соответствующим металлом.
Золочение широко используют в электротехнике, радиотехнике и электронике для покрытия ответственных контактов (главным образом разрывных и скользящих), работающих при малых токах (от 5 мкА до 100 мА) и малых контактных давлениях (0,01 — 0,1 МПа), плат печатного монтажа, локальных объемных микроэлементов, интегральных схем и волноводов, в производстве полупроводниковых приборов, в реактивной технике и ядерной энергетике. Применяют его и при изготовлении точных измерительных приборов (детали аналитических весов, разновесы, колориметрические бомбы и т. д.), различных отражателей (особенно для инфракрасной части спектра и радиоволн), селективных светофильтров и других изделий, а также в качестве твердой смазки вместо органических смазочных материалов, которые в условиях космоса быстро испаряются или разрушаются под воздействием радиации.
Однако, несмотря на разнообразие применения, основной расход золота приходится на покрытие электроконтактных поверхностей, где важны не только длительное сохранение малого переходного сопротивления, но и такие характеристики золота, как эрозионная стойкость, низкая термоэлектродвижущая сила, способность выдерживать смену низких и высоких температур.
В области низкочастотных коммутирующих устройств нашли применение золото-никелевые сплавы, содержащие 0,5−2% никеля. Добавка никеля способствует уменьшению величины зерна, вследствие чего золотое покрытие становится менее пористым и более коррозионностойким. Присутствие никеля в золотых покрытиях делает их более стойкими к эрозии. Добавка никеля к золоту также рекомендуется при защите серебряных покрытий от потемнения, так как присутствие никеля в решетке золота уменьшает диффузию серебра к поверхности через слой золота.
В производстве печатных схем также находят применение золото-серебряные сплавы 1691, содержащие 1—3% Ag. Такие покрытия получаются из холодного электролита, причем это устраняет отслаивание — дефект, часто наблюдающийся при покрытии печатных схем.
Для коммутирующих устройств сейчас получает распространение термодиффузионное золочение контактов из пермаллоя или ковара в целях получения твердого поверхностного слоя золота, хорошо сопротивляющегося эрозии. При этом к золотому покрытию, предназначенному к термодиффузии, предъявляются особые требования. Оно должно быть мелкокристаллическим и не должно содержать примесей, которые могут попасть из электролита.
В последнее время в электронной технике особое значение придается получению покрытий чистым золотом и золотом с добавкой кобальта в связи с производством оборудовании с большим сроком службы, подвергающегося высокотемпературным изменениям. Электролитические покрытия золотом находят также применение для защиты оболочек космических аппаратов, для покрытия подшипников в качестве смазывающего слоя при работе на трение, а также в других областях техники, как, например, для покрытия таких материалов, как молибден, кремний и др. При этом, конечно, требуется технология, обеспечивающая прочность сцепления с основой.
1. Буркат Г. К. Серебрение, золочение, палладирование и родирование. — Л.: Машиностроение Лен. отд-ние, 1984 г., 86 с.
2. Буркат Г. К. Электролитическое осаждение драгоценных металлов. — М., «Металлические и другие неорганические покрытия», 1993 г., 100 с.
3. Вячеславов П. М. Гальванотехника благородных и редких металлов. — Л.: Машиностроение, 1970 г., 248 с.
4. Мелащенко Н. Ф. Гальванические покрытия благородными металлами. — М.: Машиностроение, 1993 г., 239 с.
5. Серебряный Л. А. Безопасность труда при нанесении гальванических покрытий. — М.: Машиностроение, 1980 г., 70 с.
Приложение 1
Рис. 1 — Распределение золота на различно удаленных от анода катодах: 1 — в кислом электролите; 2, 3, 4 — в щелочном электролите при плотности тока 0,4; 0,2; 0,1 А/дм2
Рис. 2 — Поляризационные кривые золота в щелочном цианистом электролите при концентрации (г/л): 1 — 17; 2 — 30
Рис. 3 — Влияние плотности тока на выход по току при различной температуре и различной концентрации золота, г/л: 1 — 13,7; 2 — 6,8; 3 — 3,4; 4 — 1,7
Рис. 4 — Поляризационные кривые золота в синеродистых электролитах золочения при различной концентрации K4Fe (CN)6 (г/л): 1- 15,0; 2 — 5,0; 3 — 1,7.
Приложение 2
Основные электролиты золочения
Компоненты электролита | Концентрация, г/л, для номеров ванн золочения | |||||||
Золото (металл) | 2,0 | 1,0 | 8,0 | 4,0 | 22,0 | 8,0 | 15−30 | |
Калий цианистый (свободный) | 15,0 | 0,1−15 | 20,0 | 30,0 | -; | -; | -; | |
Двухзамещенный фосфат калия | 15,0 | 15,0 | 20,0 | 30,0 | -; | 30,0 | -; | |
Калий углекислый | -; | -; | 20,0 | 30,0 | -; | -; | -; | |
Калий железистосинеродистый | -; | -; | -; | -; | -; | -; | ||
Цитрат аммония | -; | -; | -; | -; | -; | -; | 25−50 | |
рН | 11−11,5 | 10,0−11,5 | 11,0−11,5 | 11,0−11,5 | -; | 6,5−7,5 | 5,0−7,0 | |
Составы кислых и нейтральных электролитов золочения.
Компоненты электролита, г/л, режим электролиза. | Номера электролитов. | ||||||
Дицианаурат калия | 1−100 | 8,0 | 16,0 | 2,5−3,5 | 14−15 | 7−9 | |
Вторичный фосфат аммония | 5−500 | -; | -; | -; | -; | -; | |
Вторичный фосфат калия | 5−500 | -; | -; | -; | -; | 35−40 | |
Цитрат натрия | -; | 135,0 | -; | -; | 150−170 | ||
Лимонная кислота | -; | -; | 55,0 | 80−100 | 60−80 | 20−25 | |
Диметилгидразин | -; | -; | 5,0 | -; | -; | -; | |
Никель (металлический) | -; | -; | -; | 3,0−3,5 | -; | -; | |
Цинк (металлический) | -; | -; | -; | 0,2−0,3 | -; | -; | |
Сульфат калия | -; | -; | -; | -; | 35−40 | -; | |
Трилон Б | -; | -; | -; | -; | 25−30 | -; | |
рН электролита | 5,2−5,8 | 3,6 | 4,2 | 4,0−5,0 | 5,0 | 6,0−7,0 | |
Температура, °С | 70−75 | 30−40 | |||||
Плотность тока, А/дм2 | 0,5−1,5 | 0,2 | 0,3−0,4 | 0,5−0,6 | 0,2−0,5 | ||
Состав нецианистых электролитов золочения.
Компоненты электролита, г/л, режим электролиза | Номера электролитов | ||||||
Хлорное золото | 2,6 | -; | -; | -; | -; | ||
Золото (в пересчете на металл) | -; | -; | 4,0 | 25−40 | 3−5 | 5−7 | |
Железистосинеродистый калий | 15,0 | -; | -; | -; | |||
Углекислый натрий | 15,0 | -; | -; | -; | |||
Роданистый калий | -; | -; | -; | -; | -; | ||
Сегнетова соль | -; | -; | 60−70 | -; | -; | -; | |
Двухзамещенный фосфат калия | -; | -; | -; | -; | -; | 20−30 | |
Хлористый натрий | -; | -; | -; | 10−30 | 10−30 | -; | |
Серная кислота | -; | -; | -; | 10−20 | -; | -; | |
Соляная кислота | -; | -; | -; | 20−50 | -; | -; | |
Компоненты электролита, г/л, режим электролиза. | Номера электролитов | ||||||
Этилендиамеин | -; | -; | -; | -; | 30−90 | -; | |
Калий этилендиаминтетрауксусной кислоты | -; | -; | -; | -; | -; | 20−40 | |
Аммоний сернокислый | -; | -; | -; | -; | -; | ||
Натрий (калий) сернокислый | -; | -; | -; | -; | 20−25 | ||
Температура, °С | 18−25 | 50−60 | 65−70 | ||||
Плотность тока, А/дм2 | 0,1 | 4−6 | 0,2−0,3 | до 10 | 0,8 | 0,2−0,4 | |
рН электролита | -; | -; | -; | -; | -; | 8,2−8,5 | |