Очистка конвертированного газа в производстве аммиака от диоксида углерода растворами горячего поташа
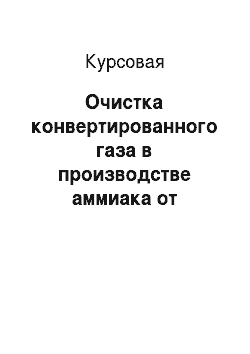
В промышленности используют следующие виды поташа: кальцинированный и полутораводный. В зависимости от физико-химических свойств поташ подразделяется также на первый, второй и третий сорт. Используется в химической и стекольной промышленности, в пожарном деле, в легкой промышленности и в других отраслях. В строительстве поташ применяют в качестве противоморозной добавки, в химической — для… Читать ещё >
Очистка конвертированного газа в производстве аммиака от диоксида углерода растворами горячего поташа (реферат, курсовая, диплом, контрольная)
Министерство образования и науки Российской Федерации Федеральное государственное бюджетное образовательное учреждение
высшего профессионального образования Пермский национальный исследовательский политехнический университет Кафедра Химические технологии КУРСОВОЙ ПРОЕКТ По дисциплине: Общая химическая технология ОЧИСТКА КОНВЕРТИРОВАННОГО ГАЗА ОТ ДИОКСИДА УГЛЕРОДА РАСТВОРОМ ГОРЯЧЕГО ПОТАША В ПРОИЗВОДСТВЕ АММИАКА
1.
Введение
Краткое изложение существа работы
2. Выбор и обоснование источников сырья, энергоресурсов, географической точки строительства
3. Выбор и обоснование способа производства
4. Обоснование оптимальных параметров технологического процесса
4.1 Термодинамический анализ
4.2 Кинетический анализ
5. Синтез и анализ ХТС
5.1 Химическая модель
5.2 Структурная схема
5.3 Операторная схема Технологическая схема
6. Выбор и основание конструкции основного аппарата Эскиз основного аппарата
7. Расчет материального и энергетического балансов. Определение расходных норм по сырью и энергии. Пути использования вторичных энергоресурсов
7.1 Материальный баланс процесса
7.2 Тепловой баланс
7.3 Расходные нормы по сырью и энергии
7.4 Пути использования вторичных ресурсов
8. Экологическая оценка производства. Отходы производства и их утилизация. ПДК Заключение Список литературы
1.
ВВЕДЕНИЕ
КРАТКОЕ ИЗЛОЖЕНИЕ СУЩЕСТВА РАБОТЫ Во всех индустриально развитых странах азотная промышленность является в настоящее время одной из основных ведущих отраслей. Бурное развитие азотной промышленности диктуется в первую очередь необходимостью удовлетворения неудержимо растущего населения земного шара продуктами земледелия. Без минеральных удобрений, и в первую очередь азотных, невозможно решить задачи интенсификации сельского хозяйства.
Производству азотных удобрений и их основы, аммиака, в нашей стране всегда уделялось первостепенное внимание. Среднегодовой прирост темпа аммиака за последние 20 лет составляет 10−19%.
Технологический газ, пригодный для синтеза аммиака, может быть получен практически из любого углеводородного сырья: природного газа, попутного газа нефтедобычи, газов переработки нефти, из нефти и ее производных: бензинов, мазутов, из каменного и бурого углей, сланцев и торфа. Основным сырьем производства аммиака (и азотных удобрений на его основе) в нашей стране является природный газ. Производство аммиака подразделяется на 6 стадий:
1. Подготовка природного газа к конверсии (сероочистка);
2. Двухступенчатая паровоздушная конверсия (риформинг) природного газа;
3. Конверсия оксида углерода водяным паром;
4. Очистка конвертированного газа от диоксида углерода;
5. Метанирование оксидов углерода;
6. Синтез аммиака Важную роль в производстве аммиака играет очистка газов[1]. Она предусматривает удаление из промышленных или природных газов вредных и балластных примесей с тем, чтобы очищеный газ был пригоден для транспортирования, дальнейшей химической переработки и непосредственного использования.
К настоящему времени на практике применяются следующие виды очистки конвертированного газа от СО2:
· Абсорбция растворами карбонатов
· Абсорбция органическими растворителями
· Водная и щелочная очистка
· Очистка водным раствором аммиака В большем количестве получил распространение метод поташной очистки (в зависимости от предприятия и технологической схемы горячие поташные растворы или растворы, активированные соединениями мышьяка).
2. ВЫБОР И ОБОСНОВАНИЕ ИСТОЧНИКОВ СЫРЬЯ, ЭНЕРГОРЕСУРСОВ, ГЕОГРАФИЧЕСКОЙ ТОЧКИ СТРОИТЕЛЬСТВА Процесс производства аммиака характеризуется большой энергоемкостью, что является главным его недостатком. Именно поэтому постоянно ведутся научные разработки, которые призваны решить проблемы экономии энергии. В частности разрабатываются способы утилизации выделенной энергии, а также совмещение, например, производства аммиака и карбамида. Все это способствует удешевлению деятельности предприятий и повышению их полезной отдачи.
Первостепенным энергоресурсом будет являться электроэнергия, расходуемая на работу оборудования: насосы, компрессоры, установок, предназначенных для нагрева (котлы, печи) посредством электрической энергии. Помимо технологического применения электричество используется для освещения производственных помещений. Основным теплоносителем и хладагентом будет являться водяной пар и вода.
Сама технологическая схема производства аммиака зависит, прежде всего, от сырья, из которого получается конечный продукт. Дело в том, что, в отличие от азота, который содержится в воздухе в больших количествах, водород в чистом виде в природе практически не присутствует, а выделять его из воды — довольно трудоемкий и энергозатратный процесс[2].
Географическое расположение подразумевает размещение завода вблизи основного сырья — месторождений газа или заводов нефтепереработки, которые могут предоставить попутный нефтяной газ или природный газ на продажу.
Начнем рассмотрение процесса с изучения сырья и получаемого целевого продукта. В качестве сырья для производства аммиака в основном используются углеводороды, содержащиеся в природном газе. По использованию окислителя и технологическому оформлению можно выделить следующие варианты процесса получения водородосодержащих газов: высокотемпературная кислородная конверсия, каталитическая парокислородная конверсия в шахтных? еакторах, каталитическая пароуглекислотная конверсия в трубчатых печах. Перед переработкой конвертированного природного газа необходимо провести процесс очистки. Очистка технологического газа направлена на снижение концентрации диоксида углерода с последующим его выводом из системы.
Оксид углерода (IV) — углекислый газ, газ без запаха и цвета, при сильном охлаждении кристаллизуется в виде белой снегообразной массы — «сухого льда». При атмосферном давлении он не плавится, а испаряется, температура сублимации ?78 °С. Углекислый газ образуется при гниении и горении органических веществ. Содержится в воздухе и минеральных источниках, выделяется при дыхании животных и растений. Растворим в воде (1 объём углекислого газа в одном объёме воды при 15 °С). Плотность при нормальных условиях 1,97 кг/мі. Концентрация углекислого газа в атмосфере Земли составляет в среднем 0,0395%. Углекислый газ легко пропускает ультрафиолетовые лучи, и лучи видимой части спектра, которые поступают на Землю от Солнца и обогревают её. В то же время он поглощает испускаемые Землёй инфракрасные лучи и является одним из парниковых газов, вследствие чего принимает участие в процессе глобального потепления. Постоянный рост уровня содержания этого газа в атмосфере наблюдается с начала индустриальной эпохи.
Диоксид углерода играет одну из главных ролей в живой природе, участвуя во многих процессах метаболизма живой клетки, получается в результате множества окислительных реакций у животных, и выделяется в атмосферу с дыханием. Углекислый газ атмосферы — основной источник углерода для растений. Однако, ошибкой будет утверждение, что животные только выделяют углекислый газ, а растения — только поглощают его. Растения поглощают углекислый газ в процессе фотосинтеза, а без освещения они тоже его выделяют.
Диоксид углерода не токсичен, но не поддерживает дыхание. Большая концентрация в воздухе вызывает гиперкапнию — состояние, связанное с избытком CO2 в крови (оно может вызываться и задержкой дыхания), когда его парциальное давление превышает 45 мм рт. ст. Однако недостаток углекислого газа в крови (гипокапния, возникающая, например, при гипервентиляции лёгких) тоже опасен.
В пищевой промышленности углекислота используется как консервант и разрыхлитель, обозначается на упаковке кодом Е290. Так же применяется для газирования лимонада и газированной воды, в качестве защитной среды при сварке проволокой. «Сухой лёд» — используется в качестве хладагента.
Очистку будем проводить поташным раствором, рассмотрим его свойства. Карбонат калия (углекислый калий, потамш) K2CO3 — средняя соль калия и угольной кислоты. Это белое кристаллическое вещество, хорошо растворимое в воде. Малотоксичен, относится к III классу опасности. Старое название соли — потамш, от лат. Potassa. Поташ — одна из солей, известных людям ещё в древности. Обычно поташ загрязнён различными примесями, поэтому не имеет такого чисто-белого цвета, как измельчённый карбонат калия. До XX века поташ был одним из важнейших промышленных химических реагентов. Его получали путём водной экстракции из растительной золы, с дальнейшей очисткой до необходимого уровня. Производство было сосредоточено в местах, богатых лесом — кое-где в Европе, но, в основном, в России и Северной Америке.
В промышленности используют следующие виды поташа: кальцинированный и полутораводный. В зависимости от физико-химических свойств поташ подразделяется также на первый, второй и третий сорт. Используется в химической и стекольной промышленности, в пожарном деле, в легкой промышленности и в других отраслях. В строительстве поташ применяют в качестве противоморозной добавки, в химической — для изготовления красок, в легкой — для выделки кож. Также поташ применяется в изготовлении моющих средств. Он служит сырьем для производства оптического стекла. В пожарном деле поташом обрабатывают деревянные строения и конструкции. В сельском хозяйстве поташ применяется в качестве удобрений, т.к. калий является жизненно важным элементом для растений. Зарегистрирован в качестве пищевой добавки E501.
3. ВЫБОР И ОБОСНОВАНИЕ СПОСОБА ПРОИЗВОДСТВА Диоксид углерода содержится в природном и коксовом газах, в конвертированном газе. В последнем содержание СО2 наибольшее и составляет в зависимости от исходного сырья и метода конверсии 20 — 30% объемных. Можно выделить физические и химические методы очистки от диоксида углерода. Физические методы основаны на повышенной растворимости его в жидкостях или на конденсации СО2 при умеренном охлаждении. Большинство химических методов основано на абсорбции этих примесей растворами химических реагентов, а в случае тонкой очистки — на каталитическом восстановлении их Н2 до СН4. Почти все способы удаления СО2 дают возможность получить его в качестве побочного продукта, используемого в производстве карбамида.
Для грубой очистки газа от двуокиси углерода применяются следующие способы:
· Водная очистка под давлением, а также физическая абсорбция органическими растворителями, имеющими низкое давление паров при обычной температуре
· Моноэтаноламиновая очистка при атмосферном давлении
· Очистка горячим раствором поташа Для тонкой очистки газа от двуокиси углерода применяются следующие способы:
· Моноэтаноламиновая очистка под давлением
· Очистка водными растворами щелочей
· Низкотемпературная очистка органическими растворителями с одновременным удалением из газа двуокиси углерода и органических сернистых соединений
· Каталитическое гидрирование, осуществляемое совместно с очисткой от окиси углерода Водная очистка газов от СО2 под давлением Способ очистки основан на различной растворимости в воде двуокиси углерода. При невысоких парциальных давлениях растворимость СО2 в воде невелика, но с увеличением давления она возрастает. При следующем снижении давления растворённая двуокись углерода выделяется из раствора. Водная очистка газа от двуокиси углерода под давлением весьма эффективна при высоком содержании СО2 в газе. Этот способ отличается простотой и позволяет многократно использовать оборотную воду. Одновременно с растворением двуокиси углерода в воде растворяются и другие компоненты конвертированного газа: водород, азот, окись углерода, сернистые соединения. По химическим свойствам СО2 является ангидридом угольной кислоты. С водой реагирует с образованием угольной кислоты, согласно уравнению:
Н2О + СО2 — Н2СО3
В технической оборотной воде, используемой для водной очистки от СО2, содержатся растворённые соли, которые понижают растворимость СО2 в технической воде по сравнению с чистой. Существенное значение для экономичности процесса водной очистки имеет расход воды на очистку и расход энергии на подачу этой воды.
Расход воды на очистку конвертированного газа от двуокиси углерода зависит от степени извлечения СО2, температуры, общего и парциального давления СО2 в газовой смеси до очистки. Если конвертированный газ в процессе конверсии углеводородов или газификации топлива получают при атмосферном давлении, то перед водной очисткой газ компримируют. Выбор давления для водной очистки от СО2 зависит от нескольких факторов.
С увеличением давления возрастает растворимость СО2 в воде и уменьшается количество воды, необходимой для промывки, почти обратно пропорционально давлению. При этом снижается расход энергии на подачу воды. С другой стороны, работа сжатия двуокиси углерода от начального низкого давления до давления абсорбции с увеличением давления возрастает. Суммарный расход энергии на водную промывку газа в пределах 1−3 МПа практически не зависит от давления. Однако с увеличением давления уменьшаются размеры абсорбера и возрастает степень очистки газа от СО2.
Очистка газов от СО2 растворами этаноламинов Для очистки газа от СО2 применяют растворы этаноламинов (аминоспиртов), которые обладают щелочными свойствами и при взаимодействии с кислотами образуют соли. Обычно используют водные растворы моноэтаноламина СН2ОН-СН2-NH2, диэтаноламина (СН2ОН-СН2)2NH и триэтаноламина (СН2ОН-СН2)3N. Наиболее сильным основанием среди этаноламинов является моноэтаноламин, который нашёл широкое применение в промышленности для очистки газов. При абсорбции СО2 растворами этаноламинов образуются карбонаты и бикарбонаты. Попутно может абсорбироваться сероводород, и образовываться сульфиды и бисульфиды. Эти соединения при температуре выше 100 °C диссоциируют с выделением из растворов СО2 и H2S.
В процессе этаноламиновой очистки газа от СО2 протекают побочные реакции, вызывающие необратимые изменения состава раствора, снижающие его поглотительную способность и приводящие к потерям амина. Растворы этаноламинов вызывают коррозионное разрушение оборудования в определённых условиях, особенно при высоких степенях насыщения кислыми газами. Подобно растворам аммиака, они разрушающе действуют на медь, цинк и их сплавы. Поэтому аппараты и трубы, соприкасающиеся с растворами аминов, нельзя выполнять из этих металлов.
Очистка газов от СО2 горячим раствором поташа Данный процесс основан на абсорбции кислых газов водными растворами карбонатов калия и натрия, содержащими активирующие добавки поливалентных металлов (As, Se, Te, Sb) или циклических органических соединений. В промышленности в качестве таких активирующих добавок получили соединения мышьяка, вводимые в растворы, как правило, в виде мышьяковистого ангидрида.
Реакции поглощения двуокиси углерода можно представить в виде следующих уравнений:
K2CO3 + H2O + CO2=2 KHCO3
KH2AsO3 + CO2+ H2O= KHCO3 + H3AsO3
H3AsO3 + K2CO3= KHCO3+ KH2AsO3
Эффективность абсорбции CO2 горячими растворами поташа, активированными мышьяком, зависит от температуры, парциального давления двуокиси углерода и водяного пара над раствором, концентрации активирующей добавки и щелочности раствора.
Регенерация отработанных растворов с целью выделения из них поглощенной двуокиси углерода производится путем снижения давления раствора, поступающего на регенерацию. При регенерации таких растворов воздухом возникает опасность окисления трехвалентного мышьяка в пятивалентный, обладающий сильными кислотными свойствами, что снижает эффективность абсорбента. Это нежелательное явление устраняется при частичном отборе раствора для его последующего восстановления.
Недостатками метода очистки синтез-газа моноэтаноламином являются коррозионные свойства растворителя, высокий расход электроэнергии и пара для отгонки растворителя. Промывку синтез-газа горячим раствором карбоната калия выгодно применять при давлениях 14 ат.
Щелочная очистка газа от СО2
Очистка газов от СО2 водным раствором едкого натра NaOH основана на необратимой реакции:
NaOH + СО2 = Na2СО3 + Н2О Парциальное давление СО2 над раствором едкого натра NaOH в процессе поглощения равно нулю до тех пор, пока вся щёлочь не перейдёт в карбонат. Поглощение СО2 раствором карбоната натрия протекает с образованием бикарбоната:
СО2 + Na2СО3 + Н2О = 2NaHСО3
Скорость абсорбции СО2 щёлочью возрастает с повышением температуры. Увеличение концентрации карбоната в растворе способствует снижению скорости абсорбции. В азотной промышленности очистка водным раствором едкого натра NaOH применяется в качестве последней ступени тонкой доочистки от СО2 конвертированного и коксового газа после водной очистки (когда концентрация СО2 в газе составляет не более 0,3% объёмных).
Процесс проходит в жидкой фазе при 90 — 95 °C и перемешивании. Установка регенерации щёлочи известью является громоздкой и процесс недостаточно удовлетворяет современным санитарно — гигиеническим требованиям (измельчение и гашение извести, транспортирование шлама в отвал и т. д.). Поэтому регенерацию отработанной щёлочи предусматривают только при значительном расходе щёлочи и необходимости привоза её со стороны. В остальных случаях водные растворы отработанной щёлочи стараются использовать для вспомогательных процессов нейтрализации и сбрасывают в специальные системы химически загрязнённых стоков.
Очистка газа от СО2 методом низкотемпературной абсорбции метанолом В интервале температур от -30 до -60 °С и при давлении 1 — 3 МПа метанол является эффективным абсорбентом не только двуокиси углерода, но и сероводорода, органических соединений серы и некоторых других примесей, присутствующих в газовой смеси. Растворимость СО2 в метаноле значительно выше, чем в воде, и возрастает с понижением температуры и увеличением давления. Так, при -60 °С растворимость двуокиси углерода в метаноле в 75 раз превышает её растворимость в воде при 25 °C. Поэтому при промывке газа метанолом в условиях низких температур расход абсорбента на очистку единицы объёма газа значительно меньше, чем при водной очистке от СО2.
Благодаря этому соответственно уменьшаются энергетические расходы в процессе абсорбции. Потери водорода при низкотемпературной абсорбции также снижаются по сравнению с их потерями при водной промывке газа под давлением. Это связано не только с сокращением удельного расхода абсорбента, но и с уменьшением растворимости водорода в метаноле при понижении температуры. Процесс низкотемпературной абсорбции наиболее целесообразно проводить при 1 — 3 МПа. Нижний предел давления составляет 0,5 МПа. Этот метод эффективен в случае одновременного удаления из газовой смеси нескольких примесей при их достаточно высоком начальном содержании. Несмотря на необходимость применения холодильной машины, энергетические расходы в описанном процессе не превышают расхода энергии при промывке газа водой.
Сравнение различных методов очистки При выборе процесса очистки окончательным критерием является величина приведенных затрат, зависящих в основном от энергетических и капитальных затрат.
Однако в каждом случае необходимо учитывать факторы, зависящие от конкретных условий и влияющие на экономику процесса. Эти факторы можно разбить на три группы:
· внешние технологические параметры процесса — состав, давление и температура очищаемого газа, требуемая степень очистки, параметры энергоресурсов (давление пара, наличие отбросного тепла, возможность использования вторичных энергоресурсов и т. д.);
· внутренние параметры процесса — расход тепла, электроэнергии, растворителя, отходы, тип и вес аппаратов;
· экономические факторы — цены на энергию, сырье, отходы, аппаратуру, а также дефицитность каких-либо видов сырья и энергии.
Кроме того, следует иметь в виду, что для крупнотоннажных агрегатов при сравнении методов очистки необходимо учитывать степень надежности процесса и оборудования.
Наиболее распространенный производственный вариант достаточно полной очистки — очистка горячим раствором поташа. Метод не требует больших затрат на энергию и сырье, протекание процесса позволяет повторно использовать некоторые ресурсы.
4. ОБОСНОВАНИЕ ОПТИМАЛЬНЫХ ПАРАМЕТРОВ ТЕХНОЛОГИЧЕСКОГО ПРОЦЕССА Очистка конвертированного газа от CO2 — процесс, протекающий в несколько стадий. Во-первых, происходит физическая абсорбция газа (растворение), во-вторых — химическая реакция, результатом которой является связывание растворенного (абсорбированного) газа. Протекание абсорбционных процессов характеризуется их статикой и кинетикой:
Статика абсорбции, т. е. равновесие между жидкой и газовой фазами, определяет состояние, которое устанавливается при весьма продолжительном соприкосновении фаз. Равновесие между фазами определяется термодинамическими свойствами компонента и поглотителя и зависит от состава одной из фаз, температуры и давления.
Кинетика абсорбции, т. е. скорость процесса массообмена определяется движущей силой процесса (т. е. степенью отклонения системы от равновесного состояния), свойствами поглотителя, компонента и инертного газа, а также способом соприкосновения фаз (устройством абсорбционного аппарата и гидродинамическим режимом его работы). В абсорбционных аппаратах движущая сила, как правило, изменяется по их длине и зависит от характера взаимного движения фаз (противоток, прямоток, перекрестный ток и т. д.).
Различают физическую абсорбцию и хемосорбцию.
При физической абсорбции растворение газа не сопровождается химической реакцией (или, по крайней мере, эта реакция не оказывает заметного влияния на процесс). В данном случае над раствором существует более или менее значительное равновесное давление компонента и поглощение последнего происходит лишь до тех пор, пока его парциальное давление в газовой фазе выше равновесного давления над раствором. Полное извлечение компонента из газа при этом возможно только при противотоке и подаче в абсорбер чистого поглотителя, не содержащего компонента.
При хемосорбции (абсорбция, сопровождаемая химической реакцией) абсорбируемый компонент связывается в жидкой фазе в виде химического соединения. При необратимой реакции равновесное давление компонента над раствором ничтожно мало и возможно полное его поглощение. При обратимой реакции над раствором существует заметное давление компонента, хотя и меньшее, чем при физической абсорбции. Уравнение реакции, лежащей в основе хемосорбции рассматриваемого процесса при очистке конвертированного газа:
K2CO3 + H2O + CO2=2 KHCO3
Бикарбонат калия взаимодействует с растворенным углекислым газом, связывая его, что влияет на изменение парциального давления над раствором. С помощью термодинамического анализа определим термодинамические условия протекания процесса, температуру, давление, концентрацию компонентов; определим тепловой эффект реакции и температуру начала реакции. Так же найдем условия протекания побочных реакций и условия максимального выхода целевого продукта (в случае очистки подразумеваем максимальное связывание примесей в ходе протекающей реакции).
4.1 ТЕРМОДИНАМИЧЕСКИЙ АНАЛИЗ Воспользуемся энтропийным методом для расчета энергии Гиббса:
Термодинамические константы исходных веществ и продуктов реакции взяты из справочной литературы[3] и представлены в таблице 3.1.
Проводим расчет и по формулам:
89,48 кДж/моль
89,48 кДж/моль Таблица 4.1.1
Термодинамические константы участников основной реакции
Термодинамическая величина | Вещество | ||||
K2CO3 | H2O | CO2 | KHCO3 | ||
кДж/моль | — 1150,18 | — 285,83 | — 393,51 | — 959,5 | |
Дж/моль· К | 155,52 | 68,95 | 213,66 | 128,7 | |
Реакция идет с небольшим выделением тепла (экзотермична), для смещения равновесия к продуктам необходимо отводить тепло от системы. За счет последующего применения отведенного тепла к другим процессам можем снизить затраты на энергию (вторичный энергоресурс).
Дж/моль· K
Процесс трудно осуществить при атмосферном давлении, так как энтропия отрицательна. Определим температуру начала реакции, используя следующее условие:
На основе температуры начала реакции выберем температурный интервал расчета энергии Гиббса: 300 600 К. С помощью энтропийного метода проведем расчет при различных температурах:
= 89 480 300· (182,13) = 34 841 Дж/моль
= 89 480 400· (182,13) = 16 628 Дж/моль
= 89 480 430· (182,13) = 11 164 Дж/моль
= 89 480 460· (182,13) = 5700,2 Дж/моль
= 89 480 500· (182,13) = 1585 Дж/моль
= 89 480 600· (182,13) = 19 798 Дж/моль Отобразим полученные данные на графике (рис. 4.1) в координатах. Сделаем вывод о влиянии температуры на протекание реакции. Термодинамическая вероятность протекания основной реакции с увеличением температуры уменьшается, необходимость отведения тепла от системы подтверждается.
Рис. 4.1.1 График зависимости энергии Гиббса от температуры аммиак двуокись углерод абсорбция Зависимость константы равновесия от температуры может быть представлена в виде уравнения:
Рассчитаем значения констант равновесия в указанном интервале температур, результаты представим в виде таблицы 4.2. Построим график зависимости константы равновесия от температуры протекания процесса.
Таблица 4.1.2
Значения константы равновесия основной реакции при различных температурах
Температура, К | K2CO3 + H2O + CO2=2 KHCO3 | ||
lgKp | Kp | ||
6,073 | 9,3 1013 | ||
2,174 | 149,250 | ||
1,358 | 22,790 | ||
0,648 | 4,447 | ||
— 0,166 | 0,683 | ||
— 1,726 | 0,019 | ||
Рис. 4.1.2 График зависимости константы равновесия от температуры Термодинамический анализ процесса очистки конвертированного газа от диоксида углерода раствором поташа позволил сделать следующие выводы:
1. В рассматриваемом интервале температур (300−600 К) термодинамическая вероятность самопроизвольного протекания процесса уменьшается, о чем свидетельствует значение энергии Гиббса.
2. Согласно принципу Ле-Шателье увеличение давления способствует смещению равновесия в сторону продуктов реакции (Растворимость СО2 в горячем растворе поташа в значительной степени зависит от парциального давления двуокиси углерода над раствором)
3. Увеличение концентрации раствора поташа по сравнению со стехиометрическим ведет к смещению равновесия в сторону продуктов реакции (предельная концентрация соли в горячем растворе 40%, т.к. дальше наблюдается выпадение осадка); горячие растворы поташа вызывают коррозионное разрушение углеродистой стали, поэтому в растворы добавляют ингибиторы коррозии.
4.2 КИНЕТИЧЕСКИЙ АНАЛИЗ В качестве побочной реакции рассмотрим процесс, который применяют для выделения поглощенного газа (абсорбтива) из абсорбента и получения его в чистом виде, а также для повторного использования абсорбента в процессе абсорбции. Для проведения десорбции газа из жидкости необходимо, чтобы концентрация этого газа в газовой фазе была ниже концентрации, соответствующей равновесной в системе газ — жидкость. На практике для проведения процесса десорбции используют три следующих метода:
· отгонку в токе инертного газа или водяного пара;
· отгонку под действием подводимой к абсорбенту теплоты;
· отгонку при снижении давления над абсорбентом Учитывая термодинамическую вероятность самопроизвольного протекания основной реакции, заключаем, что в интервале температур 300−600 К возможно протекание обратной реакции (десорбции газа), при подведением тепла к системе.
В общем случае метод хемосорбционной очистки обладает рядом особенностей оп сравнению с физической абсорбцией:
· Возможность абсорбции при низком парциальном давлении вследствие более высокой поглотительной абсорбции раствора;
· Относительно малая циркуляция раствора и соответственно небольшой расход энергии на перекачку сорбента;
· Регенерацию осуществляют, как правило, путем нагревания в сочетании со сбросом давления, при этом расход тепла на десорбцию относительно невелик;
· Регенерацию проводят часто при кипении абсорбента, его пары могут играть роль десорбирующего агента;
· Возможность проведения весьма тонкой очистки;
· Увеличение коррозии и протекание побочных реакций, обусловленных применением повышенных температур и щелочных агентом — сильных и слабых электролитов Метод поташной очистки основан на применении относительно дешевого абсорбента, но имеет ряд недостатков: малая растворимость карбоната в воде (особенно бикарбоната) при обычной температуре, низкая скорость абсорбции, что приводит к необходимости значительной циркуляции раствора и обуславливает увеличение габаритов аппаратов. Кроме того, равновесное парциальное давление СО2 над растворами поташа относительно велико, и не удается достичь тонкой очистки газа (0,08 -0,15% СО2 в газе после очистки). Преимущество метода — сравнительно низкий расход тепла на регенерацию.
Скорость процесса абсорбции может быть рассмотрена через применение основного уравнения массопередачи[4]. Если выразить движущую силу процесса в концентрациях газовой фазы (парциальные давления), то оно принимает следующий вид:
Где — средняя движущая сила процесса, выраженная в единицах давления;
— коэффициент массопередачи, отнесенный к единице движущей силы, выраженной через парциальные давления поглощаемого газа;
Химическая реакция, сопровождающая процесс абсорбции, оказывает существенное влияние на кинетику процесса, т.к. скорость определяется не только интенсивностью массопереноса, но и скоростью протекания химической реакции. Благодаря химической реакции растворенный CO2 переходит в связанной состояние (KHCO3). Концентрация свободного газа в жидкости уменьшается, а процесс абсорбции ускоряется (рост величины), в сравнении с абсорбцией без химического взаимодействия фаз[1]. Скорость хемосорбция зависит как от скорости химической реакции, так и от скорости массопереноса между фазами. В зависимости от лимитирующего процесса различаются кинетическую и диффузионную области процесса хемосорбции.
Кинетическая область определяется как протекание процесса, при котором скорость химического взаимодействия меньше скорости массопереноса. В диффузионной области лимитирующая стадия — скорость диффузии компонента в зоне реакции, которая зависит от гидродинамических условий в системе и физических свойств.
Абсорбция, как и другие процессы, протекает на границе раздела фаз. Как следствие — абсорбционные аппараты (далее — абсорберы) должна иметь развитую поверхность контакта между жидкой и газовой фазами. Абсорберы по своим конструктивным особенностям делят на следующие основные группы: пленочные, насадочные, тарельчатые, распыливающие. На практике очистка конвертированного газа от CO2 проводится в насадочных колоннах. Варьирование площади поверхности раздела фаз происходит за счет смены насадки. Основные применяемые виды — кольца Рашига и седловидная насадка Берля.
Значения коэффициентов абсорбции CO2 растворами карбонатов могут быть вычисленные по уравнениям[4]:
Где — объемный коэффициент абсорбции, отнесенный к газовой пленке, кмоль/(м3· ч·атм)
L — расход жидкости, кг/(м3· ч)
— удельная поверхность несмоченной насадки, м2/м3
C', n — константы, зависящие от типа насадки Где — объемный коэффициент абсорбции, отнесенный к газовой пленке, кмоль/(м3· ч·атм)
— удельная поверхность насадки, м2/м3
a — 0,288 + 0,00316u, (u — плотность орошения), м3/(м2ч)
b = 0,0059
— вязкость раствора Таблица 4.2
Насадка | n | |||
Кольца Рашига d=9,5 мм d=25 мм | 1,53 0,81 | 0,56 0,36 | ||
Седловидная (насадка Берля), l = 25 мм | 1,00 | 0,42 | ||
Выводы теоретического анализа:
1. По условиям равновесия абсорбция происходит тем полнее, чем ниже температура. Однако, скорость абсорбции тем выше, чем выше температура. На основании сопоставления термодинамических и кинетических факторов выбираем оптимальную температуру абсорбции 35−100оС. Реакции, протекающие при очистке, являются экзотермическими и обратимыми, при повышении температуры раствора химическое соединение разлагается с выделением исходных компонентов, регенерация раствора протекает при 120−135оС.
2. Согласно принципу Ле-Шателье увеличение давления способствует смещению равновесия в сторону продуктов реакции. На производстве применяется абсорбционный метод с давлением 2,5 — 2,8 мПа, с последующей тонкой очисткой растворами моноэтаноламина или едкого натра.
3. При десорбции применяется дросселирование поглотительного раствора, при котором раствор вскипает и CO2 выдувается образующимся водяным паром.
4. На основании справочных данных о влиянии степени карбонизации на температуру выпадения твердой фазы в водных растворах K2CO3, выбираем оптимальную концентрацию раствора 30 — 40%.
5. СИНТЕЗ И АНАЛИЗ ХТС
5.1 ХИМИЧЕСКАЯ МОДЕЛЬ Абсорбционная очистка газа — циклический процесс, на стадии абсорбции диоксид углерода поглощается растворителем, очищенный газ отправляется на последующую переработку, а насыщенный раствор регенерируют, что требует дополнительного расхода энергии. Процесс абсорбции проводим в массообменном аппарате типа насадочной колонны (насадка — кольца Рашига или седловидная насадка Берля).
Первоначально происходит физическая абсорбция CO2 раствором, после чего поглощенный диоксид углерода вступает в реакцию с карбонатом калия. Благодаря химической реакции растворенный CO2 переходит в связанной состояние (KHCO3). Концентрация свободного газа в жидкости уменьшается, а процесс абсорбции ускоряется. Особую важность представляет десорбция компонента и вторичное использование поташного раствора в целях экономии сырья. При десорбции применяется дросселирование поглотительного раствора, при котором раствор вскипает и CO2 выдувается образующимся водяным паром.
Очистка газа поташным раствором основана на взаимодействии диоксида углерода с карбонатом калия по суммарному уравнению
K2CO3 + H2O + CO2 = 2 KHCO3
Скорость реакции практически полностью лимитируется скоростью медленно протекающей реакции в жидкой фазе СO2 + ОН- = HCO3;
5.2 СТРУКТУРНАЯ СХЕМА
Схема 4.2.1 Структурная схема очистки конвертированного газа от СО2 раствором горячего поташа Метод основан на применении относительно дешевого абсорбента, но имеет ряд недостатков: малая растворимость карбоната в воде (особенно бикарбоната), низкая скорость абсорбции, что приводит к необходимости значительной циркуляции раствора и обуславливает увеличение габаритов аппаратов. Кроме того, равновесное парциальное давление СО2 над растворами поташа достаточно велико, и не удается достичь тонкой очистки газа (0,08 — 0,15% СО2 в газ после очистки). Преимущество метода — сравнительно низкий расход тепла на регенерацию.
5.3 ТЕХНОЛОГИЧЕСКАЯ СХЕМА Проведен анализ различных технологических схем, представленных в литературе[1] [5] [9]. Выделены следующие виды схем: с разделенным потоком, схема поташной очистки с активатором, схема поташной очистки без активатора.
Описание технологической схемы Газ под давлением 12,5 — 15 атм при температуре 155оС, которая развивается при сжатии его в компрессоре, поступает в теплообменник 1, куда подводится отработанный раствор после абсорбции. Часть тепла газ передает раствору, охлаждаясь при этом до температуры 125−130 оС, затем проходит водяной холодильник 2, где охлаждается до 122оС, и через влагоотделитель 3 поступает в абсорбер 4.
В абсорбере имеется несколько слоев насадки из колец Палля. Сюда подается регенерированный раствор поташа, 2/3 которого из регенератора 5 поступает в нижнюю часть абсорбера при температуре 102 °C. Примерно 1/3 раствора охлаждается в водяном холодильнике до 80 °C и затем подается в верхнюю часть абсорбера. Такая схема циркуляции раствора способствует снижению остаточного содержания СО2 в газе.
В абсорбере 4 газ очищается с 18 — 19% начальной концентрации СО2 до остаточного содержания 0,3 — 1,5% и при температуре 80 °C выходит из абсорбера. Далее очищенный газ охлаждается в водяных холодильниках и, пройдя влагоотделитель, поступает на сжатие в газовые компрессоры.
Отработанный поташный раствор удаляется из абсорбера через автоматический клапан регулятора уровня, проходит теплообменник 1 и дросселируется в верхнюю часть регенератора 5, где поддерживается избыточное давление порядка 0,06 — 0,07 атм. При этом из раствора выделяется двуокись углерода, концентрация которой достигает 99,5 — 99,8% СО2.
Регенератор представляет собой вертикальный колонный аппарат с двумя слоями насадки из колец Палля. Раствор стекает сверху вниз по насадке; при нагревании его парам из раствора выделяется двуокись углерода. К низу регенератора подключен выносной подогреватель, в котором раствор нагревается глухим паром до 104 — 105 °C.
Горячий регенерированный раствор перекачивается из регенератора насосом 8 на орошение абсорбера 4. Уровень раствора в регенераторе регулируется изменением подачи свежего конденсата в куб этого аппарата.
Операторная и технологическая схема поташной очистки конвертированного газа от СО2 приведены в приложениях 1 и 2 соответсвенно.
6. ВЫБОР И ОСНОВАНИЕ КОНСТРУКЦИЯ ОСНОВНОГО АППАРАТА Основными аппаратами на стадии очистки являются абсорберы[7] и регенераторы, в которых осуществляются массообменные процессы поглощения и выделения диоксида углерода.
К массообменной температуре очистки предъявляют следующие требования:
· Большая пропускная способность по газу и жидкости, что позволяет создать малогабаритные аппараты и делает возможным их транспортирование по железной дороге с завода изготовителя
· Высокая степень насыщения хемосорбента, а абсорбере, что обеспечивает высокие технико-экономические показатели процесса
· Глубокая степень извлечения СО2 из газа, остаточное содержание не должно превышать 0,03 — 0,15% об.
· Минимальный расход тепла в регенераторе
· Стабильность в работе и легкость регулирования работы аппарата Для очистки технологического газа от СО2 в крупнотоннажных агрегатах производства аммиака используют насадочные колонны (для случая не активированного поташного раствора). Массообменные аппараты с нерегулярной насадкой обеспечивают высокую надежность эксплуатации в широком диапазоне нагрузок по газу и жидкости, что важно для агрегатов большой единичной мощности. В качестве насадки в абсорберах и регенераторах применяют кольца Рашига, насадку Берля, металлические кольца Палля, керамические седла Инталлокс.
Абсорбер представляет собой двухсекционный аппарат, верхняя секция имеет диаметр 3,9, нижняя — 4,2 м. Аппараты изготовляют из конструкционной низколегированной стали 09Г2С с термообработкой сварных швов. Рабочий диапазон температур для стали от -70оС до +450оС.
Общий вид абсорбера поташной очистки из справочной литературы и показан в приложении 3 Технологические и некоторые конструктивные данные, характеризующие абсорбер приведены в таблице 5.1., проведен сравнительный анализ представленных данных на основе расчетов из литературы[6].
Таблица 5.1
Технологические и конструктивные характеристики абсорбера поташной очистки
Показатель | Значение | ||
Диаметр аппарата, м | 4,242/2,740 | ||
Высота аппарата, м | 58,5 | ||
Характеристика насадки, м | |||
нижняя секция, 3 слоя колец Палля, м | 0,05 | ||
верхняя секция, 2 слоя колец Палля, м | 0,04 | ||
Скорость газа на входе в аппарат, м/с | 0,24 | ||
Давление в абсорбере, МПа | 2,7 | ||
Температура раствора, оС | |||
вход, I поток | |||
вход, II поток | |||
выход | |||
Концентрация СО2 в газе, % | |||
вход | 18 — 19% | ||
выход | 0,3 — 1,5 | ||
Сопротивление аппарата, МПа | 0,05 | ||
Помимо основных аппаратов — абсорберов и регенераторов, на стадии очистки применяют теплообменные аппараты — газовые и паровые кипятильники, воздушные холодильники, конденсатор-холодильник. Для подачи в абсорбер регенерированного раствора используют насосы с приводом от паровых турбин или с электроприводом.
7. РАСЧЕТ МАТЕРИАЛЬНОГО И ЭНЕРГЕТИЧЕСКОГО БАЛАНСОВ. ОПРЕДЕЛЕНИЕ РАСХОДНЫХ НОРМ ПО СЫРЬЮ И ЭНЕРГИИ. ПУТИ ИСОЛЬЗОВАНИЯ ВТОРИЧНЫХ ЭНЕРГОРЕСУРСОВ
7.1 МАТЕРИАЛЬНЫЙ БАЛАНС Используя данные из литературы[4][5] по входящему и выходящему из абсорбера потоков, рассчитаем материальный баланс в программе Microsoft Office Excel 2007. Исходные данные потоков представлены в таблице 6.1.
Таблица 6.1
Исходные данные по входному и выходному потоку абсорбционного аппарата в методе поташной очистки конвертированного газа от диоксида углерода в производстве аммиака
КОНВЕРТИРОВАННЫЙ ГАЗ | ||||||||||||||
Вход в абсорбер | Выход из абсорбера | |||||||||||||
Статья | % об. | Статья | % об. | Разница | ||||||||||
Газ | Сухой газ | |||||||||||||
N2 | 19,59 | N2 | 23,86 | |||||||||||
Ar | 0,25 | Ar | 0,30 | |||||||||||
H2 | 60,56 | H2 | 73,75 | |||||||||||
CO | 0,49 | CO | 0,60 | |||||||||||
CO2 | 17,06 | CO2 | 0,10 | |||||||||||
CH4 | 0,30 | CH4 | 0,37 | |||||||||||
Вода | 1,75 | Вода | 1,03 | |||||||||||
В систему приходит | Выходит из системы | |||||||||||||
Начальное содержание СО2 в газе | 17,06 | % | ||||||||||||
Остаточное содержание СО2 в газе | 0,099 | % | ||||||||||||
Степень очистки от СО2 | 99,421 | % | |||
На хемосорбцию расходуется СО2 | нм3/ч | ||||
Конденсируется воды | нм3/ч | ||||
Таблица 6.2
Сводная таблица материального баланса для абсорбера поташной очистки от диоксида углерода в производстве аммиака
Вход в абсорбер | Выход из абсорбера | |||||||||||
Статья | Об. | Масс. | Статья | Об. | Масс. | |||||||
Конвертированный газ | 113 489,20 | Сухой газ | 43 193,30 | |||||||||
N2 | 25 811,25 | N2 | 25 811,25 | |||||||||
Ar | 930,36 | Ar | 930,36 | |||||||||
H2 | 11 399,20 | H2 | 11 399,20 | |||||||||
CO | 1295,00 | CO | 1295,00 | |||||||||
CO2 | 70 631,79 | CO2 | 335,89 | |||||||||
CH4 | 456,43 | CH4 | 456,43 | |||||||||
H2O | 2965,18 | H2O | 1427,95 | |||||||||
Вода, конденсат | ||||||||||||
H2O конд | 1537,23 | |||||||||||
Раствор поташа | 734 911,61 | Раствор поташа | ||||||||||
K2CO3 | 220 473,48 | H2O | 485 680,71 | |||||||||
H2O | 514 438,13 | На десорбцию | ||||||||||
KHCO3 | 319 526,786 | |||||||||||
В систему приходит | 848 400,80 | Выходит из системы | 848 400,80 | |||||||||
кг/ч | кг/ч | |||||||||||
Вывод: Согласно материальному балансу для данного аппарата за час абсорбируется 35 787 нм3, а на десорбцию уходит 848 400,8 кг абсорбента. Используя последний показатель можно рассчитать материальный баланс для десорбции.
7.2 ТЕПЛОВОЙ БАЛАНС
Вход | K | Выход | K | ||||
Cp= a + b· T + c· T2 | |||||||
a | b | c' | Cp= a + b· T + c'· T-2 | ||||
N2 | 27,88 | 0,427 | 29,567 | Дж/моль· К | |||
Ar | 27,88 | 0,427 | 29,567 | ||||
H2 | 27,28 | 0,326 | 0,5 | 28,568 | |||
CO | 28,41 | 0,0041 | — 4,6E-05 | 30,029 | |||
CO2 | 44,14 | 0,904 | — 0,85 | 47,711 | |||
CH4 | 14,32 | 0,7 466 | — 0,17 | 16,616 | |||
H2O | 39,02 | 0,7 664 | 0,1 196 | 69,293 | |||
K2CO3 | 80,29 | 0,10 904 | 123,361 | ||||
Используя данные из литературы[3] по коэффициентами теплоемкости рассчитаем теплоемкость веществ на входе и количество теплоты приносимое веществами в систему.
ПРИХОД ТЕПЛА В СИСТЕМУ | |||||||
Тепло, приносимое конвертированным газом | 1 672 565,221 | кДж/ч | |||||
Теплота химической реакции | 39 710,06076 | кДж/ч | |||||
Тепло, подводимое | 2 310 792,774 | кДж/ч | |||||
Итого | 4 023 068,055 | кДж/ч | |||||
РАСХОД ТЕПЛА СИСТЕМОЙ | |||||||
Теплота конденсации воды | 3 549 469,018 | кДж/ч | |||||
Тепло, уносимое очищенным газом | 451 046,7019 | кДж/ч | |||||
Потери тепла | 22 552,3351 | кДж/ч | |||||
Итого | 4 023 068,055 кДж/ч | ||||||
Расчет теплового баланса показал, что необходимо подводить к абсорберу количество теплоты, равное 4 023 060 кДж. Подача такого количества энергии возможна через нагрев раствора поташа.
7.3 ВТОРИЧНОЕ ИСПОЛЬЗОВАНИЕ ЭНЕРГОРЕСУРСОВ Технологическая схема, описанная ранее, подразумевает циклическое использование раствора поташа и переносимого им тепла. На примере теплообменника 01 можем наблюдать охлаждение газа за счет частичной передачи теплоты охлажденному отработанному раствору. Далее отработанный раствор переходит в десорбер 05, где претерпевает дросселирование и обработку водяным паром, за счет чего происходит регенерация поташного раствора, в результате которой горячий раствор идет на дальнейшую абсорбцию, а пар, частично сконденсировавшаяся вода и СО2 выходят из системы. Данная технология позволяет существенно экономить энергию на нагрев и поддержание температуры газа и поташного раствора.
Так же возможно замыкание обмена воды между теплообменниками 02, 03, подачей водяного пара и скруббером-промывателем, что так же существенно снизит затраты на использование энергии и ресурса технической воды.
Тонкая очистка от СО2 позволяет получить два готовых к синтезу или транспортировке и последующей продаже следующие продукты: конвертированный газ (производство аммиака) и СО2 (производство карбамида)
8. ЭКОЛОГИЧЕСКАЯ ОЦЕНКА ПРОИЗВОДСТВА. ОТХОДЫ ПРОИЗВОДСТВА, ИХ УТИЛИЗАЦИЯ. ПДК Экологические проблемы отрасли производства аммиака непосредственно связаны с ее экономическими проблемами. Устаревшие технологии и оборудование не способствуют решению проблем загрязнения среды. Поэтому вложения в модернизацию промышленности напрямую связаны с улучшением экологической ситуации в отрасли. Недостаток таких вложений ведет к снижению спроса на продукцию и объема производства. Неэффективность производства и относительно большое количество отходов на единицу продукции уменьшают доходы, необходимые для инвестирования в природоохранные объекты В производстве аммиака имеются выбросы газов в атмосферу, сточные воды и твёрдые отходы.
Выбросы в атмосферу Выбросы газов в атмосферу разделяются на:
· постоянные выбросы газов, обусловленные ведением постоянного технологического процесса;
· периодические выбросы газов в период пуска и остановки производства;
· периодические выбросы газов, обусловленные нарушением технологического режима;
В производстве аммиака имеются постоянные выбросы газов, содержащие вредные компоненты: дымовые газы после подогревателя природного газа, дымовые газы после трубчатой печи и вспомогательной печи, «грязная фракция» СО2 или «чистая фракция» СО2 вместе с «грязной», вентвыбросы из аккумуляторной и кислотной. Вредными веществами в выбрасываемых дымовых газах огневого подогревателя сероочистки и первичного риформинга является сернистый ангидрид, окислы азота, окись углерода. Вредными веществами, выбрасываемыми в атмосферу с углекислым газом, является угарный газ, моноэтаноламин и сероводород.
Диаметры и высоты труб выбросов выбраны таким образом, чтобы количество вредных веществ, выбрасываемых в атмосферу, не создавали в приземном слое концентраций вредных веществ, превышающие санитарные нормы (после их рассеивания).
Периодически при пуске агрегата в атмосферу выбрасываются:
· дымовые газы из огневого подогревателя синтеза
· парогазовая смесь из отпарной колонны Периодически при пуске, остановке, нарушении технологического режима предусмотрено сжигание газов в факельной установке для предотвращения загрязнения атмосферы при выбросах газа. Кроме того, периодически в аварийных случаях в атмосферу сбрасываются выбросы от предохранительных клапанов и перед ремонтом оборудования.
Сточные воды Для обеспечения надёжности охраны водных ресурсов при аварийных ситуациях и остановках на ремонт агрегата предусмотрено наличие аварийных и дренажных ёмкостей. Все вредные стоки направляются на очистные сооружения и на биологическую очистку. Сбросы после химической очистки (промывки) системы парообразования перекачиваются в накопительные ёмкости и далее на очистные сооружения.
Стоков, содержащих аммиак, из блоков синтеза не имеется. Аммиачная вода, образующаяся в период восстановления катализатора синтеза, а также опорожнения аппаратов от остаточного количества аммиака перед ремонтом направляются в дренажную ёмкость, размещённую на складе жидкого аммиака.
Твёрдые и жидкие отходы Отработанные катализаторы процессов сероочистки, конверсии метана, конверсии диоксида углерода, метанирования и синтеза аммиака отправляются в отвал, на металлолом или на переработку.
Продувочные газы Продувочные газы разделяются на фракции в зависимости от температуры. Разделение происходит на аммиачную воду; водород, который поступает обратно на компрессор сжатия газа; метан, который используется в качестве топлива и аргон, который является готовой продукцией.
Рассмотрим предельно допустимые концентрации вредных веществ в воздухе рабочей зоны. Данные представлены в документе ГН 2.2.5.2100−06 «Предельно допустимые концентрации (ПДК) вредных веществ в воздухе рабочей зоны» и Дополнению N 2 к ГН 2.2.5.1313−03.
При концентрации углерода диоксида в воздухе 0,25−1% у человека изменяется функция дыхания и кровообращения, при 2,5−5% наблюдается головная боль, раздражение верх, дыхательных путей и др., при 7% учащается сердцебиение, появляются рвота, головокружение и другие симптомы. При высоких концентрациях углерода диоксида в воздухе наступает смерть от остановки дыхания (при 20% через несколько секунд).
Окись углерода образует с гемоглобином крови стойкие соединения, кровь теряет способность поглощать кислород воздуха, наступает кислородное голодание. Лёгкое отравление угарным газом сопровождается головной болью, шумом в ушах, мельканием и туманом в глазах, слабостью и сильным головокружением, рвотой. При остром отравлении наступает отдышка, потеря сознания, судороги, удушье. Систематическое отравление небольшими дозами угарного газа сопровождается быстрой утомляемостью, раздражительностью, головными болями. ПДК газа в воздухе рабочей зоны составляет 20 мг/м3. Окись углерода — горючий газ, в смеси с воздухом или кислородом образует взрывоопасные смеси.
Водород (Н2) — физиологически инертный газ без запаха и цвета. Может вызывать удушье вследствие снижения концентрации кислорода в воздухе. Легко воспламеняется, пламя бледно-голубого цвета. В смеси с воздухом и кислородом образует взрывоопасные смеси.
Аммиак (NH3) — сильно токсичное, огнеи взрывоопасное вещество. В нормальных условиях — газ, хорошо растворим в воде, имеет резкий характерный запах нашатырного спирта. При нарушении герметичности оборудования и трубопроводов высокого давления мгновенно образует облако большой концентрации. В зоне выделения аммиака у человека могут возникнуть спазмы органов дыхания: из-за сильного слезотечения и рези в глазах происходит потеря ориентации. ПДК аммиака 20 мг/м3.
Моноэтаноламин (МЭА) — и его растворы имеют запах аммиака, токсичны и огнеопасны, вызывают ожоги, опасно попадание их в глаза.
ЗАКЛЮЧЕНИЕ
В ходе курсовой работы была рассмотрена технологическая схема поташной очистки конвертированного газа раствором горячего поташа. В современной технологии переработки природного газа очистка от диоксида углерода с использованием растворов поташа занимает первое место в общем числе промышленных способов.
Как уже было отмечено выше, эффективность процесса абсорбции СО2 карбонатными растворами зависит от температуры, парциального давления диоксида углерода и водяного пара над раствором, состава и концентрации активирующих добавок, а также от основности раствора. Повышение температуры абсорбции, хотя и приводит к уменьшению поглотительной способности раствора, однако увеличивает растворимость карбонатных солей в воде и скорость абсорбции. В промышленности существуют различные модификации этого процесса, основными отличиями которых являются различные активаторы, температура и концентрация растворов Дальнейшие научные и технические разработки для данного процесса необходимо направить на повышение степени очистки конвертированного газа и повышение степени десорбции поташного раствора для снижения количества используемого сырья и частичного решения проблем экологического характера.
[1] Семенова, Т. А. Очистка технологических газов / Семенова Т. А., Лейтес И. Л., Аксельрод Ю. В., [и др.] М, Химия 1977, — 488с.
[2] Степанов, А. В. Получение водорода и водородосодержащих газов /Степанов А. В, Киев: Наукова думка 1982, — 312 с.
[3] Равдель, А. А. Краткий справочник физико-химических величин / Равдель, А.А., Пономарева А. М., Спб:. Иван Федоров 2003, — 240 с.
[4] Справочник азотчика: Физико-химические свойства газов и жидкостей. Производство технологических газов. Очистка технологических газов. Синтез аммиака. — 2-е изд., перераб / Под редакцией Е. Я. Мельников, М.: Химия 1986, — 512 с.
[5] Семенов, В. П. Производство аммиака / Семенов В. П., Киселев Г. Ф., Орлов А. А., Семенова Т. А., М:. Химия, 1985, — 368 с.
[6] Александров, И. А. Ректификационные и абсорбционные аппараты: Методы расчета и основы конструирования / Александров И. А., М:. Химия, — 296 с.
[7] Андреев Ф. А. Технология связанного азота/ Андреев Ф. А., Каргин С. И., Козлов Л. И., Приставко В. Ф., М:. Химия 1966, — 500 с.
[8] Ведерников М. И. Производство аммиака из природного газа / Ведерников М. И., Киев: Технiка 1970, — 232 с.