Эксплуатация и ремонт питательных насосов
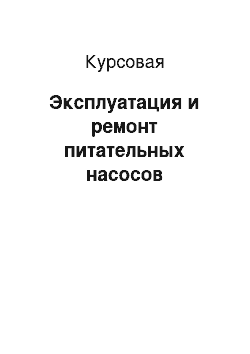
С целью достижения необходимого уровня безопасности эксплуатации и снижения трудоемкости монтажа насос ПЭ-380−185 выпускается двухкорпусным. Аналогичную конструкцию имеют питательные электронасосы ПЭ-500−180, ПЭ-500−185/200, ПЭ-720−185, ПЭ-780−185/210, ПЭ-900−185. Наружный корпус кованный обладает большой жесткостью, что обеспечивает возможность применения фланцевого присоединения подводящего… Читать ещё >
Эксплуатация и ремонт питательных насосов (реферат, курсовая, диплом, контрольная)
[Введите текст]
Министерство образования и науки Российской Федерации Федеральное государственное бюджетное образовательное учреждение высшего профессионального образования
«Южно-Уральский государственный университет» (научно-исследовательский университет) Факультет «Энергетический»
Кафедра «Промышленная теплоэнергетика»
ПОЯСНИТЕЛЬНАЯ ЗАПИСКА К КУРСОВОЙ РАБОТЕ по дисциплине «Эксплуатация теплоэнергетических систем промышленных предприятий»
Тема работы: «Эксплуатация и ремонт питательных насосов»
Челябинск 2015
АННОТАЦИЯ
Климахин В. В. Эксплуатация и ремонт питательных насосов. Челябинск: ЮУрГУ, Э, 2015, библ. список — 5 наим.
В работе осуществлен подробный анализ эксплуатации питательных насосов, главным образом питательных электронасосов. Большое внимание уделено описанию ремонтных работ питательных насосов и подготовке к ремонту персонала. Указаны основные нормы и правила безопасности при эксплуатации, ремонте и выполнения других работ, связанных с питательными электронасосами.
Для подачи воды к паровым котлам используется насосы питательные. Их применяют на тепловых электростанциях, комплектуют парогенераторные установки нефтеносных месторождений. Котлы, работающие в паре с данным оборудованием, могут быть барабанного или прямоточного типа. Перекачивают питательные насосы для паровых котлов воду с температурой от 80 до 165 градусов. В зависимости от конструктивных особенностей агрегаты могут работать с жидкостью, количество примесей в которой не превышает от 0,01 до 0,2%. Размер механических включений допустим в пределах 0,05−0,1 мм.
Основные виды питательных насосов Насосы питательные для паровых котлов производятся нескольких типов:
ПЭ — питательные электронасосыиспользуются для подачи воды с температурой до +165єС;
ПЭ, для крупных блоков скд — пускорезервный питательные насосы ЦВК — центробежно-вихревые электронасосыпитательный насос водяной с высоким напором для подачи воды с температурой до +105єС;
АН — агрегатные насосыагрегат для маломощных котлов, перекачивает воду с температурой до +80єС с возможной пиковой температурой до +105єС;
НГ — герметичные насосы — роторно-пластинчатые устройства для перекачки воды с температурой до +80єС.
ПТН — питательные турбонасосы
ПД, бустерные — предвключенные насосы
1. КОНСТРУКЦИЯ ПИТАТЕЛЬНЫХ НАСОСОВ
Рассмотрим ПЭ, их конструкцию и условия работы, примером послужит Питательный насос ПЭ-380−185
Модель насоса | Q, м3/ч | Н, м | РН, МПа | РВХ, МПа | НДОП.ВС., м | ?, % | N, кВт | М, кг | |
ПЭ-380−185 | 18,1 | 0,98 | |||||||
Рис. 1 — 1 — ведомая зубчатая полумуфта; 2 — шпонка; 3 — вал; 4 и 26 — радиальные подшипники скольжения передний и задний; 5 — водоотбойный диск; 6 и 17 — щит передний и задний; 7 — рым-болт; 8 и 15 — патрубки подводящий и напорный; 9 — кожух (термошумоограждение); 10 — канал для отвода воды в межкорпусное пространство; 11 — наружный корпус; 12 — направляющий аппарат; 13 и 38 — секции внутреннего корпуса; 14 — межкорпусное пространство; 16 — отвод на манометры; 18 — гайка, шайба плоская и пружинная; 19 — шпилька; 20 — корпус заднего концевого уплотнения; 21 — корпус задней подшипниковой опоры; 22 — упорный подшипник; 23 и 24 — ограждение и указатель осевого сдвига ротора; 25 — крышка упорного подшипника; 27 и 45 — дренаж масла; 28 — подвод масла; 29 и 43 — коллектор дренажей холодного конденсата; 30 — отвод воды от гидропяты; 31 и 32 — разгрузочный диск и подушка гидропяты; 33 — фундаментная плита; 34 — внутренний фланец наружного корпуса (фикс-пункт внутреннего корпуса); 35 — датчики контроля температуры; 36 — рабочее колесо 4-й ступени; 37 — уплотнение; 39 — рабочее колесо первой ступени; 40 — стыковая крышка; 41 — крышка кольцевой подводящей камеры; 42 — камера отвода конденсата; 44 — крышка концевого уплотнения
1.1 Работа ПЭ-380−185
Питательный электронасос ПЭ-380−185 центробежный, двухкорпусной, 11-и ступенчатый, с односторонним расположением рабочих колес рис. 2. Все колеса насоса имеют один диаметр по выходным кромкам лопаток, которые загнуты назад (в2 < 90о). Диаметр всасывающего отверстия первого колеса больше чем у всех остальных, для увеличения кавитационного запаса.
С целью достижения необходимого уровня безопасности эксплуатации и снижения трудоемкости монтажа насос ПЭ-380−185 выпускается двухкорпусным. Аналогичную конструкцию имеют питательные электронасосы ПЭ-500−180, ПЭ-500−185/200, ПЭ-720−185, ПЭ-780−185/210, ПЭ-900−185. Наружный корпус кованный обладает большой жесткостью, что обеспечивает возможность применения фланцевого присоединения подводящего и напорного трубопроводов. Механические усилия от наружного корпуса внутреннему корпусу (секционного типа) практически не передаются, а водяная рубашка между ними существенно снижает вибрацию и уровень шума при работе насоса. Оба патрубка приварены к наружному корпусу и направлены вверх. С торцов наружный корпус закрыт крышками входной и напорной. Для контроля равномерности обжатия металлической прокладки между крышкой и корпусом предусмотрен зазор в 1 мм. Крышки напорная и подводящая крепится к наружному корпусу шпильками. В верхней и нижней части корпуса установлены датчики контроля температуры.
Для заполнения пространства между корпусами питательной водой и поддерживания в нем требуемого статического давления через шесть аксиальных каналов в трех первых секциях внутреннего корпуса производится отбор воды после третей ступени. Для этого первые три секции выполняются с утолщенной наружной стенкой. Отборная вода по каналам проходит до стыковой крышки и через радиальные сверления заполняет полость между корпусами от первой до девятой ступени включительно, а оттуда по радиальному каналу в наружном корпусе поступает в трубопровод отбора. На стыке девятой и десятой ступени на внутренней поверхности наружного корпуса выполнен внутренний фланец, к которому через стальную прокладку крепится неподвижно внутренний корпус.
Этот фланец является фикс-пунктом внутреннего корпуса.
Все рабочие колеса насоса установлены на вал по скользящей посадке 2-го класса точности. Между торцом ступицы рабочего колеса последней ступени и торцом дистанционной втулки, которая с другой стороны упирается в разгрузочный диск гидропяты, предусмотрен зазор для компенсации температурных расширений деталей ротора. Исключение протечек воды по валу достигается за счет металлического контакта торцов ступиц рабочих колес под действием осевого усилия, направленного в сторону двигателя. Уплотнение первого колеса однощелевое, а всех остальных колес — двухщелевые.
Осевое усилие, передаваемое с рабочих колес на вал, воспринимает разгрузочный диск гидропяты. Он установлен неподвижно на валу за последним рабочим колесом и дистанционной втулкой. Неподвижность диска относительно вала обеспечена шпонкой и стопорной гайкой. В напорную крышку наружного корпуса запрессована калиброванная втулка, которая с дистанционной втулкой на валу образует кольцевой зазор, через который вода с давлением около 18,5Мпа поступает в рабочую полость гидропяты. Воздействуя на рабочую поверхность разгрузочного диска, вода создает осевое усилие, направленное в сторону свободного конца вала — в противоположную сторону действия осевого усилия на рабочие колеса насоса. Через радиальный кольцевой зазор между подушкой гидропяты, разгрузочным диском и напорной крышкой вода поступает в камеру отвода дренажей, где ее давление незначительно выше атмосферного.
Если осевое усилие на колеса увеличивается, то ротор смещается в сторону подводящего патрубка, зазор между подушкой и разгрузочным диском уменьшается, расход воды через камеру гидропяты уменьшается, поэтому статическое давление воды на диск увеличивается, за счет этого увеличивается и осевое усилие на разгрузочный диск — ротор занимает устойчивое положение.
Если осевое усилие на колеса уменьшается, то ротор смещается в сторону напорного патрубка, зазор между подушкой и разгрузочным диском увеличивается, расход воды через камеру гидропяты увеличивается, поэтому статическое давление воды на диск уменьшается, за счет этого уменьшается и осевое усилие на разгрузочный диск — ротор занимает устойчивое положение.
Концевые уплотнения щелевого типа выполнены с промежуточным подводом холодного и отводом отработанного конденсата. На выходе из концевых уплотнений установлены водоотбойные диски, которые исключают возможность попадания воды в подшипники при аварийном состоянии уплотнений. Корпуса уплотнений крепятся шпильками к крышкам наружного корпуса.
Ротор насоса установлен на два радиальных подшипника скольжения с принудительной смазкой, которая подается с давлением около 50кПа индивидуальной маслостанцией. Рабочие поверхности подшипников цилиндрической формы. К корпусу задней подшипниковой опоры прифланцована крышка с упорным шариковым подшипником, что повышает надежность работы насоса при неудовлетворительной работе гидропяты. Со стороны свободного конца вала предусмотрен упор ротора с визуальным указателем осевого сдвига.
Насос оборудуется системой для прогрева, которая состоит из коллектора с двумя вентилями высокого давления, трубопровода и дросселирующего устройства и используется перед запуском насоса из холодного состояния (после длительной остановки). Для этого в насос подается конденсат с давлением от 50 до 500кПа (0,5−5ата) и температурой не более 150єС.
Корпус насоса закрыт кожухом из мягкой листовой стали. Под кожух предварительно закладывается теплоизоляционный и шумопоглощающий материал — базальтовое волокно. Это позволяет иметь на поверхности кожуха температуру не более 60−70єС, а уровень шума снизить на 10−15Дбл.
Зубчатая муфта насоса имеет индивидуальный подвод масла от маслосистемы агрегата. Муфта закрыта кожухом из двух половин, в который сливается масло из муфты. Стык кожуха выполнен фланцевым и уплотнен резиновыми маслостойкими кольцами.
Смазка из подшипников и зубчатой муфты подвергается механической очистке на фильтрах, потом охлаждается и поступает в маслобак, откуда насосом опять подается на подшипники и муфту.
2. ТРЕБОВАНИЯ К ЭКСПЛУАТАЦИИ И НАРУШЕНИЯ НОРМАЛЬНОЙ РАБОТЫ ПИТАТЕЛЬНЫХ НАСОСОВ
Питательные насосы обслуживают в точном соответствии с инструкцией. Перед пуском при внешнем осмотре насоса необходимо убедиться, что ремонт и монтаж закончены, рабочая площадка освобождена от приспособлений и инструментов, установлены и. закреплены ограждения муфт, электродвигатель заземлен, положение задвижек и вентилей соответствует пусковой схеме, Обычно вентили на рециркуляционной и всасывающей линиях должны быть открыты, а на линии нагнетания — закрыты. Кроме того, проверяют исправность контрольно-измерительных приборов, наличие масла и осевое положение ротора насоса. Если насос сблокирован с другими насосами, необходимо, перед пуском отключить блокировку.
Все питательные насосы снабжены рядом защит: от понижения давления питательной воды в линии нагнетания до обратного клапана и масла перед подшипниками; от недопустимо большого осевого смещения ротора; от уменьшения расхода воды через насос. Эти защиты позволяют предотвратить повреждение самого насоса и избежать развития аварии и повреждения другого оборудования энергоблока. «Правилами технической эксплуатации» запрещается пуск питательного насоса, если неисправна хотя бы одна из защит или какое-либо средство дистанционного управления, которым обслуживающий персонал пользуется в том случае, когда не срабатывает защита.
После пуска насоса при работе на рециркуляцию необходимо контролировать температуру воды перед насосом и после него, осевое положение ротора, уровень вибрации. При нормальной работе насос подключают к питательной магистрали.
Режим пуска питательного турбонасоса имеет особенности, связанные с подготовкой и пуском приводной паровой турбины (особенности пуска турбин были рассмотрены выше). На каждой электростанции имеются резервные питательные турбонасосы, которые запускаются автоматически при недопустимом уменьшении давления питательной воды. Так как при возникновении аварийной ситуации резервный питательный турбонасос должен быть немедленно запущен в работу, он постоянно находится в готовности к пуску.
Задвижки на напорных и всасывающих трубопроводах резервных питательных насосов должны быть открыты; к стопорному клапану приводной турбины должен быть подведен пар; паропровод, арматура и турбина должны быть прогреты; через дренажи удален весь конденсат. При соблюдении этих условий быстрый пуск не вызовет повреждения турбины. При пуске резервный питательный насос медленно набирает обороты и постоянно растет давление в линии нагнетания до обратного клапана. Когда давление, развиваемое насосом, становится больше давления в магистрали питательной воды, начинается подача воды в котел от резервного насоса. Резервные насосы опробуют не реже 1 раза в месяц. Это необходимо для опробования всей системы автоматического ввода резерва, так как в работе автоматических устройств, бездействовавших длительное время, возможны отказы. Насос при этом нагружается до полной производительности и некоторое время находится в пробной эксплуатации. При этом основной питательный насос останавливают.
2.1 Особенности эксплуатации питательных насосов
Причины отказов питательных насосов Вопросы отказов питательных насосов в работе и меры по их устранению приобретают особую остроту, поскольку их остановка влечет за собой значительное понижение мощности энергоблока, а в некоторых случаях и его остановку. Опыт эксплуатации насосов показывает, что большинство их неисправностей возникает в пусковой период и при этом большая часть отказов наблюдается в период пуска насоса.
Наиболее частыми являются отказы (в порядке их частоты):
1) устройства уравновешивания осевой силы;
2) концевых уплотнений вала;
3) ротора;
4) корпуса;
5) подшипников.
Существенное влияние на работоспособность насоса и срок его службы оказывает качество питательной воды, обеспечиваемое системами водоподготовки и очистки энергетических установок. Задачей водоподготовки является обеспечение необходимого водного режима, исключающего возникновение условий, при которых вода на отдельных участках пароводяного тракта электростанций приобретает агрессивные свойства.
В ТУ к насосам обычно предъявляются только требования по механической чистоте воды и водородному показателю рН. Условие нейтральности водного раствора или воды при 25 °C определяется значением рН = 7. Значениям рН < 7 соответствует кислая среда, а рН > 7 — щелочная среда.
Значение рН питательной воды для снижения скорости эрозии деталей оборудования энергоустановок должно находиться в пределах 8,5−9,2. Одним из основных факторов, определяющих характер и интенсивность коррозии сталей, является содержание в воде растворенного кислорода. На скорость коррозии влияют также скорость движения среды, ее температура и другие факторы. Деаэрация конденсата и питательной воды существенно влияет на снижение кислородной коррозии водяных насосов.
В качестве методов консервации могут быть выбраны заполнения системы: инертным газом (обычно азотом), деаэрированной питательной водой с поддержанием в ней избыточного давления или питательной водой с присадкой гидразина, раствором аммиака с доведением рН до 10,5−11,0 (возможно сочетание гидразионной и аммиачной консервации). Стимуляторами коррозии являются взвешенные вещества, если они содержатся в воде. Допускаемое содержание в перекачиваемой жидкости взвешенных твердых включений регламентируется требованиями ГОСТ и ТУ на насосы.
Первостепенные значения этих требований определяются опытным путем, показывающим, что наиболее частыми причинами повреждений насосов являются попадания в проточную часть инородных металлических частиц из питательной воды и конденсата, вызывающие преждевременный износ уплотнений рабочего колеса, концевых уплотнений вала и других элементов насоса. Это приводит к увеличению протечек в уплотнениях и тем самым к снижению экономичности насоса, а также к увеличению величины осевой силы, действующей на ротор. Наличие инородных частиц в воде может косвенно влиять и на режим работы энергоблока. Так, например, при пусках блока мощностью 300 МВт после монтажа вследствие большого количества инородных частиц на одном из трех установленных предвключенных насосов обычно производится чистка защитных сеток на стороне входа (наличие резерва по предвключенным насосам позволяет не останавливать и не разгружать этот блок).
На энергоблоках мощностью 500, 800 и 1200 МВт, где предвключенные насосы входят в состав агрегатов, засорение защитных сеток предвключенных насосов может привести к необходимости снижения нагрузки блока, а возможно и к его остановке. На чистку сеток расходуется значительное время, в некоторых случаях до 25−30 ч. Все это время энергоблок работает на пониженной нагрузке. Таким образом, металлические частицы, находящиеся в воде (например, сварочный грат, окалина и др.), могут оказать влияние как на надежность, так и на экономичность энергоблока и могут повлечь за собой аварию насоса (заклинивание проточной части, разрушение гидравлической пяты, концевых уплотнений вала и др.).
Для предотвращения попадания инородных частиц в насос рекомендуется: на входе в насоса устанавливать защитные сетки из нержавеющей стали (проходное сечение сетки должно в три-четыре раза превышать площадь сечения трубопровода, диаметр отверстий в каркасе сетки 5−10 мм — в зависимости от значения величины подачи насоса); на период пусков после монтажа или ремонта на каркас сетки устанавливать мелкую плетеную сетку (сечение мелкой сетки принимается 0,3−0,4 мм). Перед вводом насоса в работу после ремонта и монтажа необходимо производить тщательно очистку всех подводящих и отводящих трубопроводов.
Однако установка сеток и фильтров не может предотвратить полностью попадание в насос мельчайших твердых частиц, которые способны причинить большой вред при попадании в уплотнения рабочего колеса или вала. Поэтому перед пуском насоса в эксплуатацию в некоторых установках производят не только промывку трубопроводов водой, но и продувку их паром при больших скоростях или щелочение, а в ряде случаев устанавливают временные уплотнения с расширенными зазорами и др.
3. ДЕРЕВО ОЦЕНКИ СИТУАЦИИ
Рассмотрим одну из важных проблем, с которой можно столкнуться при эксплуатации питательного электронасоса — кавитацию, а также причины её возникновения и способы их устранения.
4. ЦЕНТРОВКА РОТОРОВ ПО ПОЛУМУФТАМ
Центровка валов — это процесс определения относительного положения осей роторов машин, регулировка их положения в пространстве так, чтобы центры вращения их валов были соосны.
Несоосность приводит: к возрастанию нагрузки на подшипники, сальники, посадочные места подшипников; увеличение потерь энергии; возрастание вибрации; снижение объёма выпуска продукции; снижение качества продукции. Исследования показывают, что до 50% всех выходов из строя роторных машин и оборудования напрямую связан с плохой центровкой. Кроме того, более 90% роторов машин работают за пределами рекомендованных допусков. Поэтому особо остро стоит проблема обучения специалистов ремонтных служб навыков центровки.
Если оси вращения валов находятся под углом к друг другу, такую несоосность называют угловой, если оси вращения валов расположены на равном расстоянии друг от друга по всей длине, то такое явление называется смещением или параллельной несоосностью. В большинстве случаев эти несоосности присутствуют одновременно (рис. 1).
А Б Рис. 1 — Виды несоосности: а — параллельная несоосность б — угловая несоосность Существует много методов центровки и в последнее время набирают популярность всевозможные автоматические системы (оптические лазерные ультразвуковые и др.), но для приобретения принципиального понятия, как снизить влияние расцентровки на работу механизмов в целом, важно научится центровать валы роторных машин механическими методами. Особую популярность из-за простоты и наглядности получили механические методы с использованием линейки и щупов, радиально-осевой метод; метод обратных индикаторов (рис. 2).
А Б В
Рис. 2 — Механические методы центровки: а — с использованием линейки и щупов; б — радиально-осевой метод; в — метод обратных индикаторов
1. Метод с использованием линейки и щупов. Для проверки параллельного смещения валов, край линейки прикладывается к образующим одной из полумуфт. При этом сопрягаемые валы должны совместно проворачиваться. Зазор между линейкой и другой полумуфтой измеряется набором щупов. Замеры производятся в противоположных горизонтальных и вертикальных точках. Угловую несоосность измеряют конусными калибрами, штангенциркулем, набором щупов и т. д.
Измерения производят в диаметрально противоположных точках. Разница в зазорах используется для определения относительного наклона валов. Преимущество данного метода: простота, непосредственное измерение, при ограниченном доступе может быть использован для тонких муфт.
2. Радиально-осевой метод. Два индикатора крепятся на валу стационарной машины, одним индикатором проводят измерения по ободу полумуфты подвижной машины для определения смещения вала, другим проводят измерения на фланце полумуфты в осевом направлении, чтобы определить угловое положение вала. Основные ограничения для использования метода: прогиб выносных элементов, что ограничивает расстояние для измерений и ограничения доступа к фланцу муфты из-за конструкции муфтового соединения, при этом процесс корректировки — многоступенчатый, а осевые перемещения вала напрямую влияют на результат измерения, и для оценки результата необходимо повторное измерение. Основным преимуществом является то, что в ограниченном пространстве только этим методом можно выполнить центровку.
3. Метод обратных индикаторов. Центровка валов этим методом предполагает измерения по окружности муфтового соединения в двух точках, что позволяет определить смещение валов. Угловое положение вала определяется наклоном между измеренными смещениями валов в двух точках. Главным преимуществом метода является получение информации о смещении и об угловом положении валов, что обеспечивает простой расчёт и графическое построение положения валов при центровке. Увеличение расстояния между точками измерения приводит к увеличению точности углового положения валов. На коротком расстоянии, этот метод уступает радиально-осевому методу.
Для отработки навыков центровки валов роторных машин популярными механическими методами, разработан специализированный стенд (рис. 3).
Основа стенда — станина (1) на которую крепится редуктор (2) и электродвигатель (4) установленный на специальную регулируемую подставку (3). Этот элемент позволяет задавать начальную несоосность валов. Вал двигателя и входного вала соединены муфтой (5). Центровку можно осуществлять с помощью набора щупов или индикаторных головок (6). Конструкция стенда позволяет центрировать как с помощью радиально-осевого метода так и методом обратных индикаторов. При центровке роторных машин в реальных условиях часто возникает проблема ограниченого пространства. Для отработки навыка центрирования в таких условиях в конструкцию стенда добавлен подвижный кожух (7).
Рис. 3 — Принципиальная схема стенда центровки
4.1 Проверка состояния центровки валопровода по муфтам
1.Определение расчетным путем радиальных и осевых зазоров
По правилу
Возьмем зазоры равные:
2. Непараллельность торцов муфты
Расчет производится в вертикальной и горизонтальной плоскостях, определяется по отношению к диаметру муфты (диаметр муфты возьмем из стандартного диапазона 40−80 мм):
3. Радиальное смещение осей роторов Вывод: При непараллельностях и смещениях проводят расчет перемещения роторов для устранения расцентровки по полумуфтам. В результате строится специальная номограмма, по которой определяют варианты центровки валопровода исходя из перемещений подшипников.
5. ПОДГОТОВКА ПИТАТЕЛЬНОГО НАСОСА К РЕМОНТУ
Нормы и правила:
1.Перед началом разборки следует предусмотреть меры против случайного включения агрегата;
2.Запорная арматура на всасывающем и напорном трубопроводах должны быть закрыты.
3.При разборке необходимо помечать положение деталей.
4.Запрещается менять детали местами, следить за состоянием посадочных и уплотнительных поверхностей и оберегать их от забоин, царапин и других повреждений.
5.Перед разборкой и ремонтом насоса необходимо:
— проверить надежность работы запорной арматуры;
— проверить отсутствие напряжения питания электродвигателя;
— отсоединить все контрольно-измерительные приборы;
— рассоединить муфту;
— отсоединить насос от магистралей (отвода, подвода, разгрузки и подачи охлаждающей жидкости). Отверстия патрубков насоса закрыть заглушками.
— опорожнить насос;
— снять насос с фундамента и доставить его к месту разборки;
— начать мероприятия по устранению неполадок в работе насоса.
6. СЕТЕВОЙ ГРАФИК ВЫПОЛНЕНИЯ РАБОТ
Рис. 4
7. ОБЕСПЕЧЕНИЕ БЕЗОПАСНОСТИ ЭКСПЛУАТАЦИИ ИЛИ ПРОВЕДЕНИЯ РЕМОНТА
питательный насос ремонт центровка Правила обеспечения безопасности:
1.Запрещается поднимать насос (агрегат) за места, не предусмотренные схемой строповки.
2.Категорически запрещается эксплуатация электронасосного агрегата без проведения проверки и подцентровки валов электродвигателя и насоса
3.От точности центровки в значительной степени зависят вибрационная характеристика агрегата, надежность и долговечность подшипников, уплотнений, соединительной муфты, валов и агрегатов в целом.
4.Ограждение муфты насоса должно обеспечивать гарантированный зазор между муфтой и кожухом
5.Запрещается исправлять перекос фланцев подтяжкой болтов или путем постановки косых прокладок.
6.Передача нагрузок от трубопроводов на фланцы насоса недопустима.
7.Категорически запрещается:
— Эксплуатация насосов (агрегатов) за пределами рабочего интервала характеристики;
— Работа насоса при закрытой задвижке на нагнетании допускается не более 5 минут при температуре жидкости до 353к (80єс).
— Запуск агрегата без заполнения насоса перекачиваемой жидкостью;
— Эксплуатация агрегата без подсоединения двигателя, насоса и рамы к заземляющему устройству;
— Эксплуатация агрегата без установки защитного ограждения муфты;
— Последовательная работа насосов;
— Эксплуатация насосов без установленных во всасывающей и напорной линии приборов контроля давления (разрежения);
8.При работающем агрегате запрещается:
— производить ремонт;
— подтягивать болты, винты и гайки, сальниковое уплотнение.
— остерегаться случайного соприкосновения с вращающимися и нагретыми свыше 323к (50ос) частями оборудования.
8. ПОДГОТОВКА ПЕРСОНАЛА И КОМПЛЕКТОВАНИЕ ВАХТ И БРИГАД
1.Эксплуатация тепловых энергоустановок осуществляется подготовленным персоналом. Специалисты должны иметь соответствующее их должности образование, а рабочие — подготовку в объеме требований квалификационных характеристик.
С целью предупреждения аварийности и травматизма в организации следует систематически проводить работу с персоналом, направленную на повышение его производственной квалификации.
2. В соответствии с принятой структурой в организации персонал, эксплуатирующий тепловые энергоустановки, подразделяется на:
— руководящих работников;
— руководителей структурного подразделения;
— управленческий персонал и специалистов;
— оперативных руководителей, оперативный и оперативно-ремонтный;
— ремонтный.
3. Персонал организации до допуска к самостоятельной работе или при переходе на другую работу (должность), связанную с эксплуатацией тепловых энергоустановок, а также при перерыве в работе по специальности свыше 6 месяцев, проходит подготовку по новой должности.
4. Для подготовки по новой должности работнику предоставляется срок, достаточный для ознакомления с оборудованием, аппаратурой, схемами и т. п. организации в соответствии с программой, утвержденной руководителем организации.
5. Программа производственного обучения по новой должности предусматривает:
— изучение настоящих Правил и нормативно-технических документов по эксплуатации тепловых энергоустановок;
— изучение правил безопасности и других специальных правил, если это требуется при выполнении работы;
— изучение должностных, эксплуатационных инструкций и инструкций по охране труда, планов (инструкций) ликвидации аварий, аварийных режимов;
— изучение устройства и принципов действия технических средств безопасности, средств противоаварийной защиты;
— изучение устройства и принципов действия оборудования, контрольно-измерительных приборов и средств управления;
— изучение технологических схем и процессов;
— приобретение практических навыков пользования средствами защиты, средствами пожаротушения и оказания первой помощи пострадавшим при несчастном случае;
— приобретение практических навыков управления тепловыми энергоустановками (на тренажерах и других технических средствах обучения).
6. Необходимый уровень квалификации персонала организации определяет ее руководитель, что отражается в утвержденных положениях о структурных подразделениях и службах организации и (или) должностных инструкциях работников.
7. На время подготовки по новой должности обучаемый персонал распоряжением по организации (для управленческого персонала и специалистов) или по подразделению (для рабочих) прикрепляется к опытному работнику из теплоэнергетического персонала.
8. Обязательные формы работы с различными категориями работников:
8.1. С руководящими работниками организации:
— вводный инструктаж по безопасности труда;
— проверка органами госэнергонадзора знаний правил, норм по охране труда, правил технической эксплуатации, пожарной безопасности.
8.2. С руководителем структурного подразделения:
— вводный и целевой инструктаж по безопасности труда;
— проверка органами госэнергонадзора знаний правил, норм по охране труда, правил технической эксплуатации, пожарной безопасности.
8.3. С управленческим персоналом и специалистами:
— вводный и целевой инструктаж по безопасности труда;
— проверка знаний правил, норм по охране труда, правил технической эксплуатации, пожарной безопасности.
— пожарно-технический минимум.
8.4. С оперативными руководителями, оперативным и оперативно-ремонтным персоналом:
— вводный, первичный на рабочем месте, повторный, внеплановый и целевой инструктажи по безопасности труда, а также инструктаж по пожарной эксплуатации;
— подготовка по новой должности или профессии с обучением на рабочем месте (стажировка);
— проверка знаний правил, норм по охране труда, правил технической эксплуатации, пожарной безопасности;
— дублирование;
— специальная подготовка;
— контрольные противоаварийные и противопожарные тренировки.
8.5. С ремонтным персоналом:
— вводный, первичный на рабочем месте, повторный, внеплановый и целевой инструктажи по безопасности труда, а также инструктаж по пожарной эксплуатации;
— подготовка по новой должности или профессии с обучением на рабочем месте (стажировка);
— проверка знаний правил, норм по охране труда, правил технической эксплуатации.
Стажировка
1. Стажировку проходит ремонтный, оперативный, оперативно-ремонтный персонал и оперативные руководители перед первичной проверкой знаний при поступлении на работу, а также при назначении на новую должность или при переводе на другое рабочее место. Стажировка проводится под руководством опытного обучающего работника.
2. Стажировка осуществляется по программам, разработанным для каждой должности и рабочего места и утвержденным руководителем организации. Продолжительность стажировки составляет 2 — 14 смен.
Руководитель организации или подразделения может освобождать от стажировки работника, имеющего стаж по специальности не менее 3 лет, переходящего из одного структурного подразделения в другое, если характер его работы и тип оборудования, на котором он работал ранее, не меняются.
3. Допуск к стажировке оформляется распорядительным документом руководителя организации или структурного подразделения. В документе указываются календарные сроки стажировки и фамилии лиц, ответственных за ее проведение.
4. Продолжительность стажировки устанавливается индивидуально в зависимости от уровня профессионального образования, опыта работы, профессии (должности) обучаемого.
5. В процессе стажировки работнику необходимо:
— усвоить настоящие Правила и другие нормативно-технические документы, их практическое применение на рабочем месте;
— изучить схемы, инструкции по эксплуатации и инструкции по охране труда, знание которых обязательно для работы в данной должности (профессии);
— отработать четкое ориентирование на своем рабочем месте;
— приобрести необходимые практические навыки в выполнении производственных операций;
— изучить приемы и условия безаварийной, безопасной и экономичной эксплуатации обслуживаемого оборудования.
9. РЕМОНТ ПИТАТЕЛЬНЫХ НАСОСОВ
Бригада:
Слесарь — 4разряд -2 чел Сварщик — 6 разряд-1 чел Бригадир -1 чел Мастер механик -1человек Мастер по регулированию -1чел Кладовщик -1чел Мастер по арматуре -1 чел Мастер по вспомогательному оборудованию-1чел Токарь 4 разряд -1 чел Шлифовшик-4 разряд-1чел Крановщик -6 разряд-1чел
БИБЛИОГРАФИЧЕСКИЙ СПИСОК
1. http://www.cntd.ru/ Профессиональные справочные системы
2. http://www.ehms.ru/ Сварочное оборудование
3. http://atomac.ru/ Эксплуатация энергооборудования
4. http://www.hms-livgidromash.ru/ «ГМС Ливгидромаш»
5. http://edu.dvgups.ru/ Организация производственного процесса