Транспортирование руды от рудоспуска до бункера-накопителя в условиях «Тыретского солерудника»
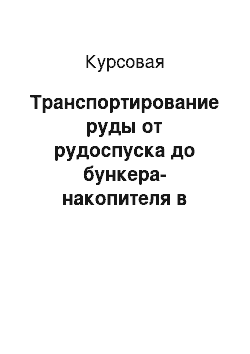
На работе по монтажу, наладке, спуску, обслуживанию и ремонту электрооборудования в подземных выработках могут назначаться только электрослесаря, прошедшие обучение и стажировку на рабочем месте, сдавшие экзамены и получившие удостоверения с указанием в нем квалификационной группы по ТБ на право производства этих работ. При необходимости остановки какой-либо подземной машины или механизма с целью… Читать ещё >
Транспортирование руды от рудоспуска до бункера-накопителя в условиях «Тыретского солерудника» (реферат, курсовая, диплом, контрольная)
МИНИСТЕРСТВО ОБРАЗОВАНИЯ И НАУКИ РОССИЙСКОЙ ФЕДЕРАЦИИ Федеральное государственное бюджетное образовательное учреждение высшего профессионального образования
Иркутский государственный технический университет
ЗАОЧНО-ВЕЧЕРНИЙ ФАКУЛЬТЕТ
Кафедра горных машин и электромеханических систем Курсовой проект По курсу Транспортные машины Тема проекта: Транспортирование руды от рудоспуска до бункера — накопителя в условиях «Тыретского солерудника»
Студент Федонина Наталья Витальевна СОДЕРЖАНИЕ ВВЕДЕНИЕ
1. ГОРНО-ГЕОЛОГИЧЕСКАЯ ХАРАКТЕРИСТИКА МЕСТОРОЖДЕНИЯ
2. ОСНОВНЫЕ СВЕДЕНИЯ
2.1 Выбор конвейера и расчёт производительности
2.2 Технико-экономическое сравнение вариантов
3. СПЕЦИАЛЬНАЯ ЧАСТЬ
3.1 Разгрузка и прием изделия получателем
3.2 Подготовка комбайна к монтажу
3.3 Спуск в шахту
3.4 Организация работ по спуску
3.5 Доставка до монтажной камеры ЗАКЛЮЧЕНИЕ СПИСОК ЛИТЕРАТУРЫ ВВЕДЕНИЕ Площадь Тыретского месторождения каменной соли административно входят в состав Заларинского района Иркутской области и расположено в 1,5 км северо-восточнее железнодорожной станции Тыреть Восточно-Сибирской железной дороги и в 240 км к северо-западу от г. Иркутска. Район месторождения электрифицирован от местной Тагнинской ГЭС Иркутской ГЭС. Площадь месторождения характеризуется выположенным рельефом, слабо расчлененным речной сетью. Абсолютные отметки в пределах контура проектируемого шахтного поля колеблются от 450 до 475 м. По южной, юго-восточной и восточной окраинами разведанной площади протекает река Унга (левый приток р. Ангары).
Климат района резко континентальный. Среднегодовая температура составляет -3єС. Распределение осадков по временам года неравномерное. Максимальное количество их выпадает в летне-осенний период. Снежный покров невелик и обычно не превышает 400 мм. Почва зимой промерзает до глубины 3,5 м. Полное оттаивание её заканчивается во второй половине июня. Вечная и островная мерзлота в районе отсутствуют. Ветры преобладают северо-западного направления. Средней скоростью 4,6м/сек.
1. ГОРНО-ГЕОЛОГИЧЕСКАЯ ХАРАКТЕРИСТИКА МЕСТОРОЖДЕНИЯ Тыретское месторождение каменной соли расположено в Заларинском районе Иркутской Области и находится в 1.5 км к Северо-востоку от железной дороги.
Границы месторождения определены контуром, утвержденным ГКЗ СССР запасом каменной соли категории С2. Площадь месторождения составляет около 25 км2 по длине 6.2 км и ширине от 3 до 5 км. В непосредственной близости к поселку Тыреть находится населенные пункты сельского типа: Мейеровка, Тыреть, Ханжиново, Веренка.
Вблизи также находится московский тракт пригодный для движения автотранспорта в любое время года. В пределах Тыретского месторождения и его окрестностях развита густая сеть грунтовых дорог. Связывающих поселок Тыреть с соседними населенными пунктами.
Площадь месторождения характеризуется слабохолмистым рельефом, слаборассеченной речной сетью. Абсолютные отметки дневной поверхности в пределах разведанной площади составляют 400−600 м.
По южной, юго-восточной и восточной окраинам разведанного рельефа протекает речка Унга (левый приток р. Ангары). Месторождение расположено в зоне с сейсмичностью 6 баллов. Район месторождения находится в пределах южной части сибирской платформы и располагается в западном крыле Ангарской антиклизы. Климат континентальный. Месторождение приурочено в Верхнебельской подсвите, характеризуется не расслаиванием пластов каменной соли мощностью от 0.6 до 17.8 м. Глубина залегания верхнего промышленного пласта каменной соли, которой является основным объектом рассмотрения данной работы, составляет 500−540 м. Пласты каменной соли прослеживаются в северо-западном и северо-восточном направлениях от разведанной площади без сколько-нибудь заметного вклинивания, а в юго-западном направлениях пласты каменной соли вклиниваются.
На площади месторождения по данным геологического отчета о его разведке буровыми работами не было зафиксировано четко выраженных структурных и текстурных нарушений. Тем не менее, породы под солевой части разреза характеризуются каверзностью.
2. ОСНОВНЫЕ СВЕДЕНИЯ конвейер месторождение шахта комбайн При разработке россыпных месторождений подземным способом ленточные конвейеры устанавливаются на сборных штреках и принимают породу, выдаваемую другими транспортами средствами из очистных забоев.
Для транспортировки горный массы крупностью кусков, породы не более 300 мм по прямолинейным горным выработкам шахт предусматривается ленточный конвейер 1Л100.
Ленточные конвейеры устанавливают горизонтально и наклонно. Наибольший угол наклона ограничивается началом ссыпания кусков по ленте под действием собственного веса и принимается при движении до 180, вниз -150. для увеличения угла наклона свыше этого предела применяют специальные ленты и ленточные конвейеры.
Горная масса может быть разгружена с ленты в конце конвейера или при установке разгрузочного устройства в средней его части.
2.1 Выбор конвейера и расчёт производительности
1Л100
Определим мощность двигателя конвейера, если заданы: производительность QСМ=500т/смену; длина конвейера L=650м; ширина ленты В=1000мм; крупность кусков дробленой соли аМАХ=300мм; плотность разрыхленной соли =2,1т/м3. Принимаем: привод однобарабанный еfa =2,72; скорость движения ленты v=1,6м/с Производительность конвейера
QЧ=
где Т — длительность рабочий смены;
kП=0,75 коэффициент учитывающий перерыв в работе конвейера по техническим причинам.
Ширина ленты:
По производительности где k=395 для лотковой поверхности ленты и соли;
V — скорость движения ленты; - посыпная плотность материала.
По крупности кусков соли В?2а/max+200=2•300+200=800мм где а/max=150 — 300 мм размеры кусков 1000?800мм Принимаем ленту с прокладками из синтетического волокна В=0,8 м, i=5, =1,2, =4мм, =1,5 мм, SP=3500H/см Нагрузка на ленту:
Вес соли
q=
Вес ленты
qЛ=11 В (11•0,8(1,2•5+4+1,5)=100Н/м где 1,1 — усредненная плотность ленты, Т/м
I — число прокладок в ленте l=5, =1,2 — 2 толщина одной прокладки,
Вес роликоопор груженой ветви.
где G/=250 — масса роликоопор, l/=1,2 м расстояния между роликоопорами груженой ветви.
Вес роликоопор холостой ветви где G//P и l// — масса плоских роликов и расстояния между роликами холостой ветви.
Сопротивление движению груженой ветви конвейера
WГ=(q+qЛ+q/P)L•w
WГ=(162+100+2041)•650•0,05=74 847Н Сопротивления движению порожней ветви контейнера
WП=(qЛ+q//P)L•w
WП=(100+877)•650•0,05=31 753Н Расчет натяжений ленты по контуру конвейера.
Рисунок 1 — Схема к детальному расчету ленточного конвейера
SHБ/SСБ?еfa f=0,3 a=10,5
S7 =S1•2,720,3•10,5 S7=1,1S1+127 662
S7=S1 20,1 20,1S1=1,1S1+127 662
S7=20,1S1 20,1S1-1,1S1=127 662
19S1=127 662
S1=127 662/19
S1=6719
Таблица 1 — Оформление расчета натяжений в ленте
№ | Общие выражения | Выражения через S1 | Численные значения | |
S1 S2=S1+W1−2 S3=S2+W2−3 S4=S3+W3−4 S5=S4+W4−5 S6=S5 S7=S6+W6−7 S8=S7 | S1=6719; S2=S1+WПОР=6719+31 753; S3=1,07(S1+WПОР)=1,07(6719+31 753); S4=1,07(S1+WПОР)+WГР=1,07(6719+ +31 753)+74 847; S5=1,07[1,07(S1+WПОР)+WГР]= =1,07[1,07(6719+31 753)+74 847]; S6=S5 S7=1,07{1,07[1,07(S1+WПОР)+WГР]}= 1,07{1,07[1,07(6719+31 753)+74 847]}; S8=S7 | |||
Наименьшее допустимое натяжения ленты груженой ветви.
Sгр min?5(q+qЛ)=5(162+100)1,2=1572Н Выбор числа накладок ленты.
Тяговое усилия на окружность приводных барабанов.
F0=S8-S1=132 822−6719=12 6103H
Мощность двигателяпривада конвейера.
Принимаем асинхронный двигатель фазным ротором ЭДКОФВ — 53/4
Мощность — 110кВт Напряжение — 1140/660 В Ток статора — 65/118А КПД — 92%
Частота вращения — 1480об/мин Маховый момент — 83Нм2
Масса — 1000 кг Расчет ленточного конвейера
1Л80
Определим мощность двигателя конвейера, если заданы: производительность QСМ=500т/смену; длина конвейера L=650м; ширина ленты В=800мм крупность кусков дробленой соли аМАХ=300мм; плотность разрыхленной соли =2,1т/м3 принимаем: привод однобарабанный еfa=3,23; скорость движения ленты V=2м/с.
Производительность конвейера
QЧ=
где Т — длительность рабочий смены. kП=0,75 коэффициент учитывающий перерыв в работе конвейера по техническим причинам.
Ширина ленты:
По производительности где k=395 для лотковой поверхности ленты и соли.
V — скорость движения ленты.
— посыпная плотность материала.
По крупности кусков соли В=2а/max+200=2•300+200=800мм где а/max=150−300мм размеры кусков 1000?800мм Принимаем ленту с прокладками из синтетического волокна В=0,8 м, l=5, =1,2, =4мм, =1,5 мм, SP=3500H/см Нагрузка на ленту:
Вес соли
q=
Вес ленты
qЛ=11 В (11•0,8(1,2•5+4+1,5)=100Н/м где 1,1 — усредненная плотность ленты, т/м
i — число прокладок в ленте l=5, =1,2 — 2 толщина одной прокладки,
Вес роликоопор груженой ветви.
где G/=85 — масса роликоопор,
l/=1,2 м расстояния между роликоопорами груженой ветви.
Вес роликоопор холостой ветви где G//P и l// — масса плоских роликов и расстояния между роликами холостой ветви.
Сопротивление движению груженой ветви конвейера
WГР=(q+qЛ+q/P)L•w
WГР=(129+100+694)•650•0,05=29 997Н Сопротивления движению порожней ветви контейнера
WПОР=(qЛ+q//P)L•w
WПОР=(100+314)650•0,05=13 455Н Расчет натяжений ленты по контуру конвейера.
SНБ/SСБ?еfa f=0,3 a=10,5
S12=S1eµa S12=1,2S1+65 353
S12 =S12,720,3•10,5 20,1S1=1,2S1+65 353
S12=20,1S1 20,1S1-1,2S1=65 353
18,82S1=65 353
S1=65 353/18,82
S1=3473
Рисунок 2 — Схема к детальному расчету ленточного конвейера Таблица 2 — Оформление расчета натяжений в ленте
№№ | Общие выражения | Выражения через S1 | Численные значения | |
S1 S2=S1+W1−2 S3=S2+W2−3 S4=S3 S5=S4+W4−5 S6=S5 S7=S6+W6−7 S8=S7+W7−8 S9=S8+W8−9 S10=S9 S11=S10+W10−11 S12=S11 | S1=3473; S2=S1+WПОР=3473+13 455; S3=1,07S2=1,07(S1+WПОР)=1,07(3473+13 455); S4=S3 S5=1,07[1.07(S1+WПОР)]=1,07[1,07(3473+13 455)] S6=S5 S7=1,07{1,07[1,07(S1+WПОР)]}= =1,07{1,07[1,07(3473+13 455)]}; S8=1,07{1,07[1,07(S1+WПОР)]}+WГР= =1,07{1,07[1,07(3473+13 455)]}+29 997; S9=1,07(1,07{1,07[1,07(S1+WПОР)]}+WГР)= =1,07(1,07{07[1,07(3473+14 490)]}+29 997); S10=S9 S11=1,07(1,07(1,07{1,07[1,07(S1+WПОР)]}+WГР))= =1,07(1,07(1,07{07[1,07(3473+14 490)]}+29 997)); S12=S11 | |||
Наименьшее допустимое натяжения ленты груженой ветви.
Sгр min?5(q+qЛ)=5(129+100)•1,2=1374Н Выбор числа накладок ленты.
Тяговое усилия на окружность приводных барабанов.
F0=S12-S1=58 086−3473=54613H
Мощность двигателя привада конвейера.
Принимаем асинхронный двигатель фазным ротором ЭДКОФ — 43/4 мощностью — 55кВт Напряжения — 1140/660 В Ток статора — 36,5/36А КПД — 90%
Частота вращения — 1475об/мин Маховый момент — 28н/м2
Масса — 580кг
2.2 Технико-экономическое сравнение вариантов Для сравнения берем два ленточных конвейера.
1Л100:
Ширина ленты В — 1000 мм Скорость ленты — 1,6
Приемная способность Qк пр — 11,2 м3/мин Максимальная производительность — 530т/ч Суммарная мощность привода — 2Ч100кВт Длина постановки — 1000 м
1Л80:
Ширина ленты — 800 мм Скорость ленты V — 1,6 — 2м/с Приемная способность QК пор — 6,5 — 8,4 м3/мин Максимальная производительность — 330 — 420т/ч Суммарная мощность привада — 1Ч40(45)кВт Длина поставки 500 м Исходные данные для экономического расчета.
Количество рабочих дней — 356
Количество смен — 2
Продолжительность смены — 14ч Отпуск — 45
Количество дней на выполнения государственных обязанностей — 2
Количество дней не работающих по болезни — 5%
Тарифная ставка — 500р Премия — 30%
Норма амортизации — 14,3
Нормативный коэффициент эффективности — 0,2
Оборудование: 1Л100 и 1Л80
Районный коэффициент — 1,5
Дополнительная зарплата — 19%
Расчет капитальных затрат на приобретения оборудования Таблица 3 — Капитальные затраты на оборудования
Наименование оборудования | Оптовая цена | Дополнительные затраты | |
Конвейер 1Л100 | 2 000 500р | Запасные части 40 010р Тара и упаковка 40 010р Доставка оборудования 408 689р Складские помещения 24 006р Балансовая стоимость 2 600 650р Монтаж 200 050р | |
Конвейер 1Л80 | 2 000 000р | Запасные части 40 000р Тара и упаковка 40 000р | |
Доставка оборудования 381 657р Складские помещения 24 000р Балансовая стоимость 2 600 000р Монтаж 200 000р | |||
Стоимость доставки оборудования Т=а•G (1+k/100)
Т — затраты на доставку, а — тариф за перевозку 1 т гр
G — вес оборудования
k — учитывающий увеличения веса за счет тары и упаковки 7%
Т1=60,15•6350(1+7/100)=408 689р Т2=60,15•5930(1+7/100)=381 657р Затраты на восстановление потенциальной 2% от балансовой стоимости
1Л100 — 52 013р
1Л80 — 52 000р Расходы на оплату труда:
Списочная численность
NCП=NЯВ•КСП
КСП — коэффициент стоимости КСП=ТРПТЭФ=365 301=1,2
Таблица 4 — Списочная численность
Показатели | Индекс форм для счета | Кол — во дней | |
Календарный фонд рабочего времени Календарное время работы Время праздничных дней Наминальный фонд времени Время отпуска Время болезни Время выполнения госуд обязанностей Эффиктивный фонд времени | ТК ТРП ТП ТРП — ТП ТО ТБ ТГО ТЭФ=ТК-ТП-ТО-ТБ-ТГО | ||
Расчет численности трудящихся и фонда заработной платы Профессия рабочих 1Л100 и 1Л80 — 2 конвейерщика Явочная численность — 2 человека Коэффициент списочности — 1,2
Списочная численность
1Л100: NСП=NЯВ•KСП=2•1,2=2,4
1Л80: NСП=NЯВ•KСП=2•1,2=2,4
Разряд конвейерщика V
Тарифная ставка — 500р/см Эффективный фонд рабочего времени 301дней Тарифный или прямой фонд заработной платы:
NСП=ТСР•ст•ТЭФ
1Л100 и 1Л80 (2.4•301•500)=361 200р Премия 30% от ФЗП
361 200•30100=108 360р Доплаты за работу в ночное время 16% от ФЗП
361 200•16%=57 792р Прочие доплаты (2−5%) от ФЗП
361 200•5%=18 060р Основной ФЗП складывается из прямого ФЗП, доплат за работу в ночное время и прочих доплат
361 200+108360+57 792+18060=545 412р Районный коэффициент 1,5
545 412•1,5=818 118р Доплата за работу в условиях крайнего севера 30% от ФЗП
545 412•30%=163 624р Дополнительная заработная плата 19% от ФЗП
545 412•19%=103 628р Годовой фонд заработной платы складывается из основной зарплаты с учетом Р.К. суммы доплат и дополнительной заработной платы
103 628+163624+818 118=1085370р Сумма отчислений на социальное страхование 26,2% от ФЗП с учетом Р.К.
(818 118+163624)•0,262=257 216р Затраты на энергию
1Л100: — за смену потребляет 110кВт/ч что цена потребляемой энергии составляет 277 р
WГОД=2•277•365=202 210р
1Л80: — за смену потребляет 55кВт/ч что цена потребляемой энергии составляет 138 р
WГОД=2•138•365=100 740р Амортизация Сумма амортизации
1Л100: 2 600 650•14,3=37 189 295 р
1Л80: 2 600 000•14,3=37 180 000 р Экономическое обоснование Таблица 5 — Экономическое обоснование
Наименование затрат | 1Л100 | 1Л80 | |
Вспомогательные материалы Расходы на оплату труда Отчисления в соц. страхование Затраты на энергию Амортизация Затраты на ткущий ремонт 150% от амортизации Итого: | |||
По предприятию принимаем конвейер 1Л100 в количестве 5 штук Расчет приведенных затрат
3УД=3iQ
1Л100: 3УД=9 439 070 311,2•2•356=11 836руб
1Л80: 3УД=942 659 836,5•2•356=21 354руб
3УД (1)<3УД (2)
11 836<21 354
Вывод: Принимаем первый вариант, так как из сравниваемых вариантов конвейер 1Л100 является с меньшей величиной приведенных затрат.
3. СПЕЦИАЛЬНЫЙ ВОПРОС Монтаж и демонтаж Урал — 20 КСА
3.1 Разгрузка и прием изделия получателем Комбайн отгружается с завода на открытых железнодорожных платформах частично разобранным на основные сборочные единицы без специальной упаковки. Запасные части, инструмент, техническая документация, электрический и гидравлический пульт управления, гидроцилиндры и другие малогабаритные узлы и детали, снимаемые на время транспортирования с комбайна, отгружаются упакованными в деревянные ящики.
Перед разгрузкой комбайна с платформы освободить его и основные сборочные единицы от растяжек, распорных и упорных брусков.
Разгрузку надо начинать с ящиков и демонтированных сборочных единиц. Грузоподъемность средств, используемых при разгрузке комбайна, должна быть не менее 25 т.
К месту хранения комбайн и остальной груз доставляется любым транспортом исключающим возможность повреждения грузоподъемностью не менее 25 т. со скоростью не более 20 км/час.
Получатель принимая комбайн, должен проверить комплектность поставки, подвергнуть комбайн и демонтируемые сборочные единицы внешнему осмотру с целью выявления с целью выявления возможных повреждений во время транспортировки.
В процессе проверки устанавливается соответствие договору на поставку поступившего комбайна, соответствия оборудования упаковочной ведомости, наличие предусмотренной технической документации, инструмента, запасных частей и принадлежностей.
3.2 Подготовка комбайна к монтажу Перед монтажом комбайна необходимо выполнить следующие работы:
Распаковать и освободить оборудование от тары.
Снять защитные шишки, пробки и т. д. с редукторов, трубопроводов, шлангов и мест их подсоединения.
Очистить все сборочные единицы и детали от пыли и грязи.
Произвести расконсервацию сборочных единиц и деталей, для чего снять консервационную смазку, промыть и протереть.
Внутренние поверхности редукторов и деталей гидросистемы расконсервации не подлежат.
Осмотреть трубопроводы гидросистемы и при необходимости произвести их промывку.
Тщательно осмотреть все электрооборудование на предмет выявления механических повреждений, обратив особое внимание на состояние кабелей и механической защиты, блокировок и взрывозащищенных поверхностей.
Проверить соединение обмоток двигателей.
Проверить сопротивление изоляции в течении 1 минуты электрических цепей относительно корпуса мегаометром на 1000 В, при этом сопротивления должно быть не менее 0,5 Мом, при сопротивлении изоляции двигателей ниже допустимого, их необходимо просушить.
После всех выше перечисленных проверок комбайн сначала собирается на поверхности, для точной готовности комбайна для работы в шахте после чего комбайн снова разбирается для спуска в шахту.
Инструкция по ТБ для подземного электрослесаря.
Данная инструкция распространяется на подземных электрослесарей, обслуживающих действующие подземное электрооборудование рудников, производящих оперативное переключение, выполняющих ремонтные, монтажные и наладочные или ремонтные работы.
Электрослесарь всегда должен помнить, что от правильности выполняемых им методов обслуживания, ремонта и монтажа в значительной степени зависит безопасность использования рудничного электрооборудования в рудниках.
Электрооборудование перед спуском должно быть осмотрено и проверено электрослесарем, и, по возможности, опробовано при работе в холостую или даже под нагрузкой в присутствии лица надзора.
3.3 Спуск в шахту Спуск комбайна в шахту производится в клети или под клетью по частям:
На работе по монтажу, наладке, спуску, обслуживанию и ремонту электрооборудования в подземных выработках могут назначаться только электрослесаря, прошедшие обучение и стажировку на рабочем месте, сдавшие экзамены и получившие удостоверения с указанием в нем квалификационной группы по ТБ на право производства этих работ. При необходимости остановки какой-либо подземной машины или механизма с целью их осмотра электрослесарь должен получить на это разрешение лица надзора участка, в технологическом цикле которого они используются. Если же машины или механизмы используются в общерудничной технологической цепи, то на их остановку электрослесарь должен получить разрешение горного диспетчера (дежурного по шахте).
О всех замеченных неисправностях электрооборудования электрослесарь должен сообщить дежурному надзору участка. А в экстренных случаях — горному диспетчеру.
Особенно ответственным, выполнением с предельной внимательностью, является спуск негабаритного оборудования по стволу под клетью. Предварительно составляют проект организации работ по спуску, утверждаемый главным инженером рудника.
Проект состоит из пяти частей: общей; подготовительных работ; организации работ; объема работ; техники безопасности.
Одним из основных и опасных моментов являются ввод груза в клетевое отделение ствола и его вывод, так как при этом возможны динамические нагрузки на подвесные устройства и даже внезапный обрыв оттяжного троса, а также сопровождение негабаритного груза при спуске, так как возможно перекашивание, а следовательно, и заклинивание в стволе.
С целью четкой организации работ каждый участник должен твердо знать свое местоположений и круг обязанностей.
Начальник участка должен: согласовать с диспетчером работу клетьевого и скипового подъема в период начала и окончания спуска; письменно извещать механика подъема о дате и времени начала и окончания спуска; выдавать наряд напроизводство работ, который должен быть утвержден старшим лицом технического надзора шахты; сообщать диспетчеру рудника об окончании работ по спуску.
Механик подъема обязан выдавать наряд машинисту клетьевого подъема на производство работ по спуску и производить инструктаж по безопасным методам проведения спуска.
Лицо технического надзора смены должно: осуществлять непосредственное руководство работы по спуску; определять местонахождение и обязанности каждого рабочего, участвующего в процессе спуска; предупреждать машиниста клетьевого подъема о характере спускаемого груза.
Машинист клетьевого подъема должен остановить клеть и поставить в известность механика подъема о нарушениях при спуске груза и возобновить работу по спуску только после указания главного механика шахты.
Работы по спуску обычно проводит бригада в составе шести человек, представленная двумя звеньями. Первое звено под руководством лица технического надзора занято на спуске, а второе — под руководством бригадира осуществляет прием груза площадке.
Состав и обязанности звена:
1-й рабочий — бригадир (звеньевой) непосредственно руководит работой звена и выполняет работы по строповке и креплению груза, производит подачу груза в ствол и извлечение его из ствола; обязан иметь удостоверение и опыт работы машиниста тяговой лебедки и стропальщика;
2-й рабочий выполняет работы по строповке груза и извлечению оттяжной стороны, подает сигнал первому рабочему при оттяжке груза от ствола по выработок; обязан иметь удостоверение стропальщика;
3-й рабочий выполняет вспомогательные работы.
В период подготовки к спуску ответственное лицо технического надзора совместно с бригадиром обязаны: произвести осмотр площадок — погрузочной на поверхности и приемной на горизонте — с выдачей соответствующих указаний по удалению не нужного оборудования, приспособлений и др.: произвести осмотр и проверку вспомогательных механизмов и приспособлений (лебедок, блоков, грузозахватных средств, подвесных устройств, стопоров, оттягивающих тросов и прицепных устройств) на исправность обращая внимание при этом на тормозные устройства, заземление и целостность тросов; удостовериться в наличии и исправности рабочего инструмента, вспомогательных материалов (ломы, крючья, жимки, ключи, молотки и т. д.) и предохранительных поясов; проверить частоту пола клети, под которую будет подвешен спускаемый груз; в соответствии с нарядом каждому рабочему указать его рабочее место, объем работы и возложенные на него обязанности.
Менее тяжелые составные части комбайна
1. редуктор раздаточный правый с двумя редукторами и режущими дисками (4840 кг)
2. редуктор раздаточный левый с двумя редукторами и режущими дисками (4840 кг)
3. редуктор исполнительного органа с двигателями левый (6720 кг)
4. редуктор исполнительного органа с двигателями правый (6720 кг)
5. барабан отбойного устройства (1028 кг)
6. редуктор привода отбойного устройства верхний 2 штуки (1260 кг)
7. редуктор привода отбойного устройства нижний 2 штуки (932 кг)
8. редуктор бермовых фрез 2 штуки (2860 кг)
9. шнеки (средняя часть бермового органа 853 кг)
10. кронштейн бермового со шнеком 2 штуки (475 кг)
11. кронштейн (полубланка) правый (1960 кг)
12. кронштейн (полубланка) левый (1960 кг)
13. элементы системы пылеотсоса (1320 кг)
14. рама грузчика передняя (2745 кг)
15. рама грузчика задняя (2650 кг)
16. баки системы смазки редукторов (295 кг)
17. насосная станция (890 кг)
18. кабина машиниста (с гидропультом и электропультом управления 1036 кг)
19. станция управления (1310 кг)
20. бурильная установка (903 кг)
21. конвейер скребковый (2859 кг)
22. рама гусеничного хода (4000 кг)
23. гусеничная цепь 2 штуки (1965 кг)
24. редуктор гусеничного хода 2 штуки (1965 кг)
25. тележка гусеничная 2 штуки (1265 кг)
26. буфер (1770 кг)
27. цепь скребковая (568 кг)
28. секция щита верхняя 2 штуки (163 кг)
29. секция щита нижняя 2 штуки (292 кг)
30. проставка исполнительного органа 2 штуки (785 кг) Наиболее тяжелые составные части комбайна
31. конвейер скребковый
32. рама передняя
33. рама задняя
34. рама гусеничного хода
35. тележка гусеничная
36. редуктор раздаточный с двумя редукторами резцовых дисков
37. редуктор исполнительного органа
38. кронштейн правый Перед клетью, под которой спускаю груз перекрывают ствол стволовой решеткой. Рабочие, выполняющие эту работу, должны быть оснащены предохранительными поясами.
Работу по подготовке комбайна ведет бригада слесарей под руководством механика внутришахтного транспорта. С целью уменьшения массы комбайн разбирают и каждая его составная часть не должна превышать 1 т.
Руководитель спуска обязан проконтролировать подготовку комбайна и принять его у механика ВШТ.
3.4 Организация работ по спуску На подготовительной площадке В клети на пол укладывают трубу размером 168Х8 мм и приваривают её к полу клети.
Спускаемую деталь (на примере показана рама конвейера) с помощью кары подают к стволу на расстояние не более 5 м от клети и укладывают её на ствольную решетку.
Два несущих каната диаметром 31 мм заводят за трубу, а свободные концы через монтажные люки в полу клети выводят из клети и закрепляют за раму конвейера.
По указанию ответственного лица машинист поднимает клеть с грузом, и рама конвейера находится в висячем положении.
По указанию ответственного лица двое рабочих закрепляют два троса с одного и другого бока клети, а другие концы за бока рамы конвейера (это нужно, для того чтобы рама при спуске не раскачивалась).
После того как ответственное лицо убедилось, что груз надежно закреплен, подает команду убрать стволовую решетку.
Связь с участниками спуска осуществляют по телефону.
Машинисту клетьевого подъема подается команда о проведении спуска.
Скорость спуска не должна превышать 0,5 м/c.
Сигнал «стоп» свидетельствующий об окончании спуска, подают тогда, когда уже возможно захватить крючком лебедки раму.
На приемной площадке.
Рабочий, застрахованный предохранительным поясом, подцепляет раму крючком лебедки и отцепляет боковые поддерживающие канаты.
По соответствующему сигналу машинист подъема опускает, рабочий с помощью каната тяговой лебедки вытягивает раму из ствола, устанавливает на приемную площадку Ненесущий канат отсоединяют от рамы конвейера и убирают из клети. Опускаемую раму конвейера с помощью машины ВОМ с крановой установкой (до 1 т) грузят на несущую тележку (до 3,5 т) этой же машины, перевозят в монтажную камеру.
3.5 Доставка до монтажной камеры При доставке должны быть приняты все меры, исключающие повреждение сборочных единиц и деталей. При этом необходимо, чтобы трубы гидросистемы, подсоединительные штуцера, а также открытые полости редукторов были заглушены как во время транспортирования, так и при монтаже.
На месте сборки комбайна необходимо подготовить монтажную камеру, которая должна иметь размеры не менее: по ширине 10 м, по высоте 5 м, по длине не менее 20 м. Кровля камеры должна быть закреплена в соответствии с утвержденным паспортом.
Монтаж комбайна производиться лебедками с тяговыми усилиями не менее 10 т через блоки, подвешенные к кровле выработки, в нашем случае имеется мостовой кран. На месте сборки должен находиться необходимый слесарный инструмент, ветошь, ванна с соляровым маслом. Камера должна быть хорошо освещена, оборудована противопожарными средствами.
На месте монтажа комбайна должен быть обеспечен безопасный проход персонала, производящего монтаж.
Перед началом монтажа необходимо проверить исправность подъемных средств, безопасность ведения работ и правильность расстановки людей.
ЗАКЛЮЧЕНИЕ
В курсовом проекте была рассмотрена горно-геологическая характеристика Тыретского солерудника.
В данном проекте было произведено технико-экономическое сравнение двух конвейеров: 1Л100 и 1Л80. На основании технико-экономического сравнения двух вариантов принят конвейер 1Л100. Данный конвейер характеризуется большей производительностью труда, меньшими удельными затратами. Удельные капитальные и удельные эксплуатационные затраты данного конвейера имеют на много меньшие затраты, чем конвейер 1Л80.
На основании технико-экономического сравнения вариантов механизации транспорта на очистных работах принят конвейер 1Л100. Приведен детальный расчет данного конвейера.
В специальной части рассмотрены монтаж и демонтаж комбайна Урал — 20 КСА.
1 Методические указания и программа для курсового проектирования по транспортным машинам и комплексам для специальности 17.01 Составители Я. Н. Долгун, Д. Е. Махно. — Иркутск: Изд-во ИрГТУ, 2002, — 15 с.
2 Н. В. Тихонов Транспортные машины горнорудных предприятий. Учебник для вузов. 2-е изд., перераб. И доп. М.: Недра. 1985, 336 с.
3 Ю. М. Коледин, Я. Н. Долгун. Транспортные машины при разработке месторождений полезных ископаемых подземным способом Часть 1: Учебное пособие. — Иркутск: Изд-во ИрГТУ, 2004. — 123 с.
4 Ю. М. Коледин, Я. Н. Долгун. Транспортные машины при разработке месторождений полезных ископаемых подземным способом Часть 2: Учебное пособие. — Иркутск: Изд-во ИрГТУ, 2006. — 195 с.