Электрическая контактная сварка
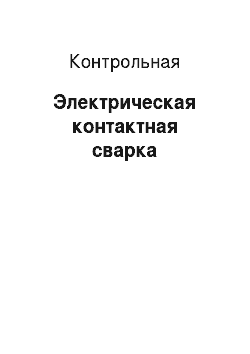
Стыковая сварка оплавлением с подогревом отличается от сварки непрерывным оплавлением тем, что перед началом процесса оплавления заготовки подогревают в зажимах машины периодическим смыканием и размыканием при постоянно включенном токе. При этом происходит процесс прерывистого оплавления и заготовки укорачиваются на заданный припуск. Выдержка при замыкании составляет около 0,5−3 с, а при… Читать ещё >
Электрическая контактная сварка (реферат, курсовая, диплом, контрольная)
Электрическая контактная сварка
Электрическая контактная сварка — это ведущий вид сварки в нашей промышленности. Она относится к видам сварки с кратковременным нагревом места соединения без оплавления или с оплавлением и осадкой разогретых заготовок. Характерная особенность этих процессов — пластическая деформация, в ходе которой формируется сварное соединение. Электрическая контактная сварка была изобретена американцем Элиху Томсоном в конце XIX в. На протяжении многих десятилетий сварку улучшали и совершенствовали, пока, наконец, она прочно не вошла в нашу промышленность.
Первоначально этот процесс был предназначен для скрепления тонких металлических листов. Благодаря целому ряду преимуществ он немедленно завоевал огромный успех, особенно потому, что момент его изобретения совпал с появлением первых автомобилей. В результате этот процесс быстро нашел себе применение в монтаже конструкции автомобильного кузова. Позднее электрическую контактную сварку начали применять изготовители подвижного состава, металлической отделки и бытовых приборов.
Важными привлекательными моментами контактной сварки являются высокая производительность и небольшой расход дополнительных материалов, а именно воды, газа, флюса и присадки, причем сварные соединения имеют высокое качество. Контактная сварка высокопроизводительна, позволяет значительно проще механизировать и автоматизировать процессы изготовления деталей, сократить расход основных и вспомогательных материалов. Эти преимущества особенно заметно проявляются в массовом и крупносерийном производстве. Эффективность контактной электросварки обусловливается большой скоростью сварочного процесса, обеспечивающей высокую производительность электросварочного оборудования, и отсутствием необходимости в присадочном материале.
К недостаткам электрической контактной сварки относится большой вес сварочных аппаратов и потребность их в больших токах, что привязывает данный вид оборудования только к стационарным условиям эксплуатации.
1. Основы электрической контактной сварки
Принцип контактной электрической сварки заключается в подаче сильного тока между двумя листами металла в строго определенной точке. Этот ток — около 6000 А для листов толщиной 1 мм — подается через медные электроды, причем свариваемые листы сильно прижимаются друг к другу с помощью рычажных сварочных клещей или ручной системы сжатия с усилением зажима. В течение около? секунды листы нагреваются до предельной температуры плавления. Усилие, прилагаемое к электродам (около 150 кг), смешивает друг с другом молекулы металла, выполняя тем самым процесс сварки. Металл не должен полностью разжижаться, так как в этом случае он будет выдавлен при внезапном расширении, что приведет к образованию низкоконсистентного, пористого или просто полого ядра сварной точки.
Фактически контактная сварка является просто современной аналогией метода, применяемого когда-то кузнецами: они нагревали два элемента докрасна, а потом ковали их молотом, чтобы прочно соединить. Сегодня электричество заменяет кузнечный горн, а усилие рычажных сварочных клещей пришло на смену молоту[2].
В базовой основе принципов электрической контактной сварки лежит давление, помноженное на тепло. Заготовки в месте соединения нагревают и сжимают определенным усилием. Нагрев осуществляют теплом, которое выделяется в заготовках и в контактах между ними при прохождении электрического тока. Для получения качественных сварных деталей металл в месте соединения нагревают до расплавления и лишь в отдельных способах (например, при стыковой контактной сварке сопротивлением) — до пластического состояния. Примыкающие к месту соединения зоны должны быть нагреты до температур, обеспечивающих требуемую пластическую деформацию заготовок. В процессе этой деформации происходит удаление окислов из места соединения, устранение раковин и уплотнение металла.
Количество тепла, выделяемого в зоне сварки, определяют по формуле Ленца-Джоуля:
Q = 0.24I2Rt
где Q — количество тепла; I — сила сварочного тока; R — общее сопротивление зоны сварки; t — время нагревания.
Основное влияние на нагрев оказывает сила сварочного тока. Например, при данном количестве тепла, расходуемом за один сварочный цикл, увеличение силы тока вдвое приведет к уменьшению времени нагревания более чем в 4 раза.
Характер нагрева заготовок, оказывающий большое влияние на качество сварного соединения, в значительной мере зависит также от величины общего сопротивления зоны сварки и соотношения между его отдельными составляющими. Общее сопротивление состоит из контактного сопротивления между заготовками, сопротивлений самих заготовок и сопротивлений между электродами и заготовками. При сварке неочищенных заготовок контактные сопротивления изменяются в широких пределах. Это приводит к изменению температур нагрева заготовок, в результате чего снижается стабильность прочностных показателей сварных соединений. Кроме того, при сварке неочищенных заготовок увеличивается износ электродов, а в сварных соединениях возникают дефекты[3].
2. Основные виды электрической контактной сварки и их применение
Наиболее широкое применение получили следующие основные виды контактной сварки: стыковая, точечная и шовная (роликовая). Каждый из этих видов сварки может осуществляться различными способами, отличающимися по технологическим признакам, роду используемой электроэнергии и способу подвода тока к свариваемым заготовкам.
2.1 Стыковая сварка
Заготовки сваривают по всей плоскости их касания. В зависимости от марки металла, площади сечения заготовок и требований к качеству соединения стыковую сварку можно выполнять следующими способами.
Стыковая сварка сопротивлением. Заготовки, установленные и закрепленные в стыковой машине, прижимают одну к другой усилием определенной величины, после чего по ним пропускают электрический ток. При нагревании металла в зоне сварки до пластического состояния происходит осадка. Ток выключают до окончания осадки. Этот способ сварки требует механической обработки и тщательной зачистки поверхностей торцов заготовок. Неравномерность нагрева и окисление металла на торцах заготовок понижают качество сварки сопротивлением, что ограничивает область ее применения. С увеличением сечения заготовок качество сварки снижается особенно заметно, главным образом из-за образования окислов в стыке.
Стыковая сварка непрерывным оплавлением состоит из двух стадий: оплавления и осадки. Заготовки устанавливают в зажимах машины, затем включают ток и медленно сближают их. При этом торцы заготовок касаются в одной или нескольких точках. В местах касания образуются перемычки, которые мгновенно испаряются и взрываются. Взрывы сопровождаются характерным выбросом из стыка мелких капель расплавленного металла. При дальнейшем сближении заготовок образование и взрыв перемычек происходят на других участках торцов. В результате заготовки прогреваются в глубину, а на торцах возникает тонкий слой расплавленного металла, облегчающий удаление окислов из стыка. В процессе оплавления заготовки укорачиваются на заданный припуск. Оплавление должно быть устойчивым (непрерывное протекание тока при отсутствии короткого замыкания заготовок), особенно перед осадкой. При осадке скорость сближения заготовок резко увеличивают, осуществляя при этом пластическую деформацию на заданный припуск. Переход от оплавления к осадке должен быть мгновенным, без малейшего перерыва. Осадку начинают при включенном токе и завершают при выключенном. Стыковая сварка непрерывным оплавлением обеспечивает равномерный прогрев заготовок по сечению и позволяет получать стабильное качество стыков. Ее существенным преимуществом является также возможность сравнительно легко автоматизировать процесс.
Стыковая сварка оплавлением с подогревом отличается от сварки непрерывным оплавлением тем, что перед началом процесса оплавления заготовки подогревают в зажимах машины периодическим смыканием и размыканием при постоянно включенном токе. При этом происходит процесс прерывистого оплавления и заготовки укорачиваются на заданный припуск. Выдержка при замыкании составляет около 0,5−3 с, а при размыкании 2−6 с. Количество замыканий может быть от одного до нескольких десятков в зависимости от размеров сечения заготовок. Применение стыковой сварки оплавлением с подогревом позволяет предупредить резкую закалку и, следовательно, получить более пластичные стыки при сварке закаливающейся стали; снизить требуемую мощность машины или на машине данной мощности сваривать заготовки с большими площадями сечения; осуществить осадку при меньшем усилии; сократить общий припуск на сварку[4].
2.2 Точечная сварка
Заготовки соединяют сваркой в отдельных местах, условно называемых точками. Размеры и структура точки, определяющие прочность соединения, зависят от формы и размеров контактной поверхности электродов, силы сварочного тока, времени его протекания через заготовки, усилия сжатия и состояния поверхностей заготовок. Качественная сварная точка характеризуется наличием общего для обеих заготовок литого ядра определенных размеров.
Последовательность операций точечной сварки следующая. Заготовки устанавливают и затем плотно сжимают между электродами контактной машины. Включают ток, и заготовки быстро нагреваются; особенно быстро нагреваются участки металла, прилегающие к контакту между заготовками, так как эти участки имеют повышенное электрическое сопротивление. Кроме того, они менее подвержены охлаждающему действию электродов. В момент образования в зоне сварки расплавленного ядра заданных размеров ток выключают. После выключения тока заготовки кратковременно выдерживают между электродами под действием усилия сжатия, в результате чего происходит охлаждение зоны сварки, кристаллизация расплавленного металла и уменьшение усадочной раковины в ядре сварной точки. Силу тока и усилие сжатия заготовок устанавливают постоянными или меняют по определенному графику в течение цикла сварки одной точки. Характер их изменения определяется толщиной и материалом свариваемых заготовок. Точечной сваркой можно сваривать листовые заготовки одинаковой или разной толщины, пересекающиеся стержни, листовые заготовки со стержнями или профильными заготовками (уголками, швеллерами, таврами и т. п.).
Точечную сварку применяют для соединения заготовок из сталей различных марок (углеродистой, легированной, нержавеющей, жаростойкой и др.), а также из цветных металлов и их сплавов. Точечной сваркой можно соединять заготовки из разнородных металлов. Толщина каждой из заготовок, соединяемых точечной сваркой, может быть от сотых долей миллиметра до 35 мм. В зависимости от количества свариваемых точек, способа подвода тока к заготовкам и других факторов применяют различные способы точечной сварки.
2.3 Роликовая сварка
Роликовая (шовная сварка) — разновидность контактной сварки, при которой между свариваемыми частями заготовки образуется прочное и плотное соединение. Электроды выполняют в виде плоских роликов, между которыми пропускают свариваемые заготовки.
Заготовки соединяют непрерывным прочно-плотным сварным швом, состоящим из ряда точек, в котором каждая последующая точка частично перекрывает предыдущую. В отличие от точечной сварки здесь заготовки устанавливают между вращающимися роликами (или между роликами и оправкой), на которые действует усилие механизма давления и к которым подведен электрический ток. Толщина каждой из заготовок обычно не превышает 2−3 мм.
В тех случаях, когда невозможно подвести ролики к свариваемому изделию с двух сторон, применяют одностороннюю роликовую сварку (приварка облицовки к каркасам больших размеров, приварка кровли и т. п.).
Шовную сварку применяют в массовом производстве при изготовлении различных сосудов. Толщина свариваемых листов составляет 0, 3−3 мм. Шовной сваркой выполняют те же типы сварных соединений, что и точечной, но используют для получения герметичного шва.
Шовная сварка отличается от предыдущих двух такими моментами: свариваемые детали закрепляют внахлёст, и электродами служат ролики, сделанные из медного сплава. Подача большого тока происходит точно так же, посредством подачи напряжения на плечи автомата через гибкие шины от вторичной обмотки трансформатора. [3]
3. Технология электрической контактной сварки. Подготовка заготовок к сварке
Перед сваркой производят правку и взаимную подгонку заготовок, а также очистку их поверхностей от окалины, ржавчины, смазки, пыли и других загрязнений. При сварке неочищенных заготовок заметно снижается качество соединений и увеличивается износ электродов контактных машин. Способ очистки выбирают в зависимости от размеров и материала заготовок, характера загрязнений и типа производства. Мелкие детали с окалиной и ржавчиной в условиях массового производства очищают в галтовочных барабанах или травлением в растворах кислот с последующей нейтрализацией в щелочной ванне, промывкой проточной водой и сушкой горячим воздухом. Окалину и ржавчину с крупных заготовок удаляют абразивными кругами или дисковыми металлическими щетками. Применяют также гидропескоструйную или дробеструйную обработку. Жиры и масло удаляют бензином, ацетоном или другими растворителями.
сварка контактный стыковой электрический
3.1 Стыковая сварка
Для получения качественного стыкового соединения необходимо равномерно нагреть заготовки по всему сечению в прилегающих к стыку зонах; обеспечить возможность одинаковой пластической деформации обеих заготовок; предотвратить или свести до минимума окисление металла на торцах в процессе нагрева; обеспечить условия для свободного удаления окислов из стыка. Выполнение этих требований возможно при надлежащей подготовке деталей к сварке и правильно выбранных способе и режиме сварки.
Сварка сопротивлением. Целесообразно осуществлять сварку на повышенных плотностях тока, так как при этом повышается качество соединения и снижается расход электроэнергии. Величину усилия осадки Р подсчитывают как произведение удельного давления на площадь заготовок. Силу сварочного тока подсчитывают как произведение плотности тока на площадь сечения заготовок. Необходимая плотность тока возрастает с уменьшением сечения заготовок, с уменьшением времени сварки, с превышением теплопроводности и снижением удельного сопротивления металла.
Установочная длина — величина выступающих из губок концов деталей в начале сварки. При заниженной установочной длине детали прогреваются недостаточно, так как тепло интенсивно отводится в губки. Завышение ее сопровождается перегревом деталей и увеличением длины деформируемого участка. Кроме того, возможны перекосы торцов вследствие потери устойчивости. Если осадка недостаточна, в стыке остаются окислы и раковины, наблюдаются непроваренные участки. При завышении величины осадки качество стыков также понижается вследствие искривления волокон и перегрева металла.
Время нагрева tСв — время прохождения тока через заготовки. При сварке на машинах, у которых выключение тока осуществляется в определенный момент осадки регулируемым конечным выключателем, время нагрева зависит в основном от плотности тока. Кроме того, оно зависит от давления и величины осадки под током.
Сварка оплавлением. Припуск на оплавление Соп должен быть таким, чтобы осуществить равномерный и достаточный нагрев деталей, выровнять зазоры между торцами и получить на торцах тонкий слой жидкого металла. Для создания защитной среды, препятствующей окислению металла в зоне сварки, оплавление должно быть устойчивым. Припуск на оплавление возрастает с увеличением диаметра или толщины деталей. Силу сварочного тока подсчитывают так же, как и при сварке сопротивлением. Плотность тока для стальных заготовок при сварке непрерывным оплавлением 3−50 А/мм2, при сварке с подогревом 3−15 А/мм2 (нижние пределы соответствуют сварке заготовок большого сечения). В момент осадки и коротких замыканий плотность тока в 2−3,5 раза выше, чем при устойчивом оплавлении. Необходимая мощность машины при стыковой сварке зависит от производительности процесса и типа свариваемых заготовок.
Скорость оплавления V>оп в начале процесса незначительна, возрастает до своего максимального значения перед осадкой. Низкая начальная скорость оплавления увеличивает глубину прогрева деталей, а высокая конечная скорость оплавления предупреждает окисление металла на торцах.
Скорость осадки иос должна быть не ниже определенного предела, который растет с увеличением теплопроводности и склонности металла к окислению. Высокая скорость осадки (особенно в начальный момент, когда закрывается зазор между оплавленными торцами) затрудняет образование окислов и способствует более полному удалению окислов из стыка.
Усилие осадки Рос возрастает с повышением жаропрочности свариваемого материала. Оно также возрастает с уменьшением температуры металла в околостыковых зонах, за счет которых происходит пластическая деформация. [5]
3.2 Точечная сварка
Конструкция узлов для точечной сварки должна позволять: применять нормальные электроды, интенсивное охлаждение которых повышает их стойкость; выполнять сварку без введения больших участков стальных заготовок в сварочный контур машины; сваривать точки в необходимой последовательности, обеспечивающей наименьшую деформацию деталей.
С увеличением количества одновременно свариваемых заготовок снижается качество сварного соединения. В связи с этим в ответственных конструкциях рекомендуется одновременно сваривать не более двух заготовок. Толщины двух заготовок из листового материала не должны различаться более чем в 3 раза. При большей разности для получения качественного соединения рекомендуется применять конденсаторную или рельефно-точечную сварку. Точки на деталях необходимо размещать с учетом шунтирования тока. Чем меньше расстояние между точками, а также чем больше толщина и выше электропроводность материала заготовок, тем большая часть общего тока шунтируется через ранее сваренную точку.
Порядок сварки. Участки вблизи ребер жесткости, углы и другие труднодеформируемые места должны быть сварены в первую очередь; участки больших размеров должны свариваться от середины к концам; точки должны свариваться подряд, так как это препятствует образованию гофр и уменьшает шунтирование тока.
Режим сварки определяется следующими основными показателями: величиной силы тока, временем включения тока, усилием сжатия заготовок, формой и диаметром контактной поверхности электродов. Величины этих показателей зависят от свариваемого материала и его толщины. При сварке двух заготовок различной толщины режим в основном определяется более тонкой заготовкой с некоторым увеличением тока. [4]
3.3 Роликовая сварка
Типы соединений для роликовой сварки выбирают с учетом толщины и материала заготовок, а также условий работы изделия. При изготовлении сосудов предпочтительнее соединение с отбортовкой.
При таком соединении деталь во время сварки не вводится в сварочный контур машины, следовательно, сохранится постоянной величина силы сварочного тока.
Введение
в сварочный контур машины магнитных материалов, например, заготовок из низкоуглеродистой стали, вызывает рост индуктивного сопротивления машины, в результате чего уменьшается сила сварочного тока. Ширина отбортовки для стальных заготовок толщиной 1−2 мм находится в пределах 12−18 мм.
Широко применяют соединение внахлестку, которые при роликовой сварке обеспечивают высокую прочность и плотность швов. Величину нахлестки берут 10−18 мм. Другие соединения, показанные на рис. применяют значительно реже, так как они не обеспечивают достаточной прочности.
Длинные швы при роликовой сварке заготовок из магнитных материалов, вводимых в контур машины, рекомендуется разбивать на два или более участка. При разбивке на два участка швы сваривают от середины к концам. При большем количестве одинаково расположенные участки выделяют в отдельные группы, которые затем сваривают на разных ступенях трансформатора. Это позволяет предупредить непровар шва вследствие уменьшения силы тока при введении в контур машины магнитных материалов. [6]
Заключение
Электрическая контактная сварка на сегодняшний день занимает значительную производственную нишу. Будучи изобретённой почти сто лет тому назад, электрическая контактная сварка не только не потеряла своих приоритетов в сварочном деле, но в эпоху развития компьютерных технологий приумножила и развила новые, более совершенные технологии, активно внедряясь в массовое и серийное производство разнообразных изделий однотипного формата. Она применяется как в строительстве для производства крупногабаритных изделий и конструкций, так и при изготовлении самых крохотных полупроводниковых микросхем и устройств. Например, контактная рельефная сварка востребована при креплении кронштейнов к деталям листообразной формы — скобы к капоту автомобиля, сварка проволоки и тонких деталей в радиоэлектронике. Шовная сварка используется при производстве разнообразных герметичных емкостей, например, летательных аппаратов и топливных баков автомобилей, емкостей и камер бытовой техники. Потенциальные возможности электрической контактной сварки весьма значительны. На сегодняшний день множество конструкций самолетов, вертолетов, ракет, морских судов, железнодорожных вагонов, автобусов и автомобилей, как в нашей стране, так и за рубежом изготовляются контактной точечной и шовной сваркой.
В настоящее время очень широко используется применение промышленных роботов. Их применение для автоматизации контактной сварки открывает возможности не только повысить экономическую эффективность производства, но и значительно улучшить качество готовой продукции. На сегодняшний день, автоматизация контактной сварки является одним из основных направлений в робототехнике. Важнейшая задача, которую решает промышленный робот, выполняющий точечную сварку, это полное освобождение человека от монотонного и очень тяжелого труда. Поэтому, я считаю, следует как можно активнее внедрять применение роботов для автоматизации контактной сварки. Это позволит нам избавиться от производственного брака, полностью исключив человеческий фактор. Роботы для контактной сварки обеспечивают высокую производительность, при этом, нет необходимости в использовании специализированных технологических материалов.
Однако, несмотря на достигнутые успехи в области внедрения электрической контактной и в первую очередь точечной сварки, дальнейшее расширение области ее применения сдерживается рядом факторов, например низкими циклическими характеристиками соединений, выполненных контактной сваркой, а также сложностью антикоррозионной защиты. Для повышения эффективности антикоррозионной защиты при борьбе с коррозией с целью обеспечения безопасного ведения технологических процессов следует:
· снизить в несколько раз затраты и количество ремонтов;
· снизить потери продукции от брака и сквозной коррозии;
· снизить уровень загрязнения и ущерба от загрязнения окружающей среды.
1. Пути повышения эффективности контактной сварки: Тез. докл. На всесоюз. науч. — техн. конф. (Окт. 1980) / [Науч. Редакторы В. И. Снежко, Г. А. Липович] 82 с. ил. 20 см., Таганрог Б. и. 1980
2. Банов М. Д., Казаков Ю. В., Козулин М. Г. Сварка и резка материалов. — М.
3. Кабанов Н. Г., Слепак Э. Ш. Технология стыковой контактной сварки. М., «Машиностроение», 1969.
4. Гуляев А. И. Технология точечной и рельефной сварки сталей. М., «Машиностроение», 1969.
5. Гельман А. С. Технология и оборудование контактной электросварки. М., Машгиз, 1960.
6. Орлов Б. Д., Чулошников П. Л. Контактная электросварка лёгких сплавов. М., Машгиз, 1963.
7. Слиозберг С. К. Медные сплавы и электроды контактных сварочных машин. М., «Машиностроение», 1970.