Технологический процесс изготовления зубчатого колеса
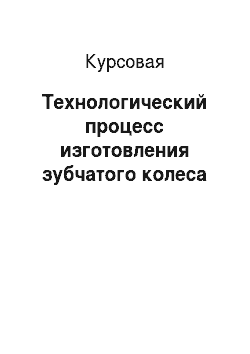
Производительность и точность станка, обусловленные его конструкцией и изготовлением, в значительной степени зависят от ухода за ним. Поэтому токарь, фрезеровщик, станочник обязан систематически очищать станок от стружек, пыли и пр. и регулярно смазывать его. Очистку станка необходимо производить, по крайней мере, один раз в смену. Тряпкой или лучше концами, смоченными в керосине, смывают… Читать ещё >
Технологический процесс изготовления зубчатого колеса (реферат, курсовая, диплом, контрольная)
Введение
Переход к новым экономическим отношениям в России существенно изменил облик нашей промышленности, коренным образом изменились условия труда: появилась безработица, увеличилась миграция кадров, а, следовательно, жизнь предъявила новые требования к квалификации и подготовке рабочих. Особо динамичными оказались изменения в металлообрабатывающей промышленности, а в ней — в машиностроении, где главная рабочая профессия — станочник.
Благодаря перестройке в промышленности организовалось большое количество небольших предприятий различных форм собственности, получили распространение рабочие — индивидуалы. На этих предприятиях, функционирующих в условиях рынка, к рабочему — станочнику предъявляются особые требования, необходимые при изготовлении конкурентоспособной продукции. Создавая только качественную продукцию малыми партиями, станочник должен часто перестраивать обслуживаемое оборудование, уметь работать на разнообразном оборудовании (токарном, фрезерном, шлифовальном и др. станках), самостоятельно контролировать качество продукции, выпускать продукцию в условиях, когда нет достаточного технического руководства (нет технолога или мастера, отсутствует техническая библиотека), отсутствует подчас квалифицированная помощь рабочего, имеющего более высокий разряд.
В этих условиях станочник должен выполнять дополнительные функции: самостоятельно налаживать оборудование, выбирать оптимальные режимы обработки, устранять отказы, контролировать качество своего труда и т. д.
При простоте станочного оборудования на многих традиционных предприятиях продолжает ощущаться общий дефицит кадров рабочих-станочников. По этой профессии создаются новые рабочие места, есть вакансии на больших и малых предприятиях различных форм собственности.
Конструкции металлорежущих станков, как любого технологического оборудования, изменяются во времени. Появляются новые механизмы, расширяются технологические возможности, повышается производительность и качество обработки. Поэтому в учебных материалах приводятся сведения о перспективах развития металлорежущих станков и о новых требованиях к профессии станочника.
1. Выбор заготовки с её физическими и химическими свойствами зубчатое колесо заготовка резание Заготовку можно получить различными способами:
Прокатом, ковкой, штамповкой, литьем.
Прежде чем выбрать род получаемой заготовки ее нужно изучить.
Необходимо сопоставить заготовку с чертежом детали, чтобы выявить, какие поверхности должны обрабатываться и с какой точностью шероховатости. После чего, учитывая необходимые требования при проектировании технологического процесса, обеспечить точное расположение обрабатываемых поверхностей.
Для изготовления детали типа зубчатое колесо, заготовка может быть выдана в виде ковкой детали.
Dзаг = 90 мм, т.к. наибольший Dзаг = 87 мм, тогда припуск = 1.5мм Химический состав стали 45 описан в таблице 1.
Таблица 1
C | Si | Mn | Cr | S | P | Cu | Ni | As | |
Не более | |||||||||
0,420,50 | 0,170,37 | 0,500,80 | 0,25 | 0,04 | 0,035 | 0,25 | 0,25 | 0,08 | |
Физические свойства стали 45 указаны в таблице 2.
Таблица 2
Марка стали | Придел прочности при растяжении увс кг/мм2 | Предел прочности кг/мм2 | Относительное удлинение в% | Ударная вязкость кг/см | Твердость по Бринелю НВ | |
2. Разработка технологического процесса обрабатываемой детали (зубчатое колесо) Рисунок 1
Технологический процесс — последовательность технологических операций, необходимых для выполнения определенного вида работ. Технологические процессы состоят из технологических (рабочих) операций, которые, в свою очередь, складываются из рабочих движений (приёмов). В зависимости от применения в производственном процессе для решения одной и той же задачи различных приёмов и оборудования различают типы техпроцессов.
Технологическая операция — это часть технологического процесса, выполняемая непрерывно на одном рабочем месте, под одним или несколькими одновременно обрабатываемыми или собираемыми изделиями, одним или несколькими рабочими.
Установ — часть технологической операции, выполняемая при неизменном закреплении обрабатываемых заготовок.
Технологический переход представляет собой законченную часть технологической операции, выполняемую над одной или несколькими поверхностями заготовки, одним или несколькими одновременно работающими инструментами без изменения или при автоматическом изменении режимов работы станка.
Операция | Содержание или наименование операции | Станок, оборудование | Инструмент | Реж. резания | ||||
Режущий | Измерительный | Гл. Рез. t, мм | Подача, Sмм/об | Скорость, Vм/мин | ||||
Отрезать заготовку | Абразивно-отрезной 8Б262 | Пила | Линейка | |||||
Токарная | Токарный 1М61 | Токарный проходной резец, прямой. | ШЦ-2 | |||||
Термическая обработка | ||||||||
Подрезать торцы 6032Н7 и 87.66/66 предварительно. Сверлить, зенкеровать, развернуть отверстие 32Н7 предварительно. Расточить и точить фаски. | Токарный полуавтомат с ЧПУ КТ141 | Токарный проходной резец, прямой и с отогнутой головкой. Сверло, зенкер, развертка. | ШЦ-2, пробка для развертки | |||||
Подрезать торец 87,66/32Н7. Точить поверхность 87,66 предварительно. | Токарный полуавтомат с ЧПУ КТ141 | Токарный проходной, с отогнутой головкой | ШЦ-2 | |||||
Протянуть шпоночный паз В=10js9 окончательно. | Горизонтально-протяжной 7512 | |||||||
Опилить заусенцы на шпоночном пазе | Вибробункер | |||||||
Подрезать торец 60/32Н7 предварительно, торец 87,66/60 и точить поверхность 60, 87,66 окончательно. | Токарный полуавтомат с ЧПУ КТ141 | Токарный проходной резец, прямой и с отогнутой головкой. | ШЦ-2 | |||||
Контроль | Калибр-скоба, калибр-пробка. | |||||||
Строгать 35 зубьев (m=2,5) под шлифование | Зубострогальный 5Т23В | |||||||
Зачистить заусеницы на зубьях | Вибробункер | |||||||
Шлифовать торец 60/32Н7 окончательно и отверстие 32Н7 окончательно | Внутришлифовальный | |||||||
Шлифовать торец 87,66/32Н7 окончательно | Плоскошлифовальный 3Б740 | |||||||
Шлифовать 35 зубьев (m=2,5) окончательно | Зубошлифовальный 58П70В | |||||||
Промыть деталь | Моечная машина | |||||||
Технический контроль | ||||||||
Нанесение антикоррозионного покрытия | ||||||||
3. Расчет режимов резания. Мощности электродвигателя и основного времени Расчет режимов резания при точении.
Определяем припуск на механическую обработку:
мм Определяем глубину резания:
Учитывается, что припуск до 2 мм срезается за один проход, принимаем i = 7, где i — число проходов, то; мм Назначаем подачу для первого точения: — 0,4 мм/об Проверяем выбранную подачу с паспортной подачей станка 1 М 61:
Sпасп. = 0,368 ммоб Определяем скорость резания: V= 138
Определяем допускную скорость резания с учетом поправочных коэффициентов.
V = V * K * K * K, где
K — Коэффициент учитывающий качество обрабатываемого материала
K — Коэффициент отражающий состояние поверхности заготовки
K — Коэффициент учитывающий качество инструментального материала Определяем расчётную частоту вращения ;
где D — диаметр детали.
;
Скорректируем найденное число оборотов шпинделя по паспорту станка По паспорту станка 1М61 = 400
Определяем фактическую скорость резанья:
;
Основные режимы резания при точении:
t = 98 мин.
S = S12 = 368 мм/об
= 110 м/мин
= 400 об/мин Проверяем выбранный режим по мощности, потребляемой на резание:
где Кр — поправочный коэффициент
где
— поправочный коэффициент на обрабатываемый материал
= 89 (в = 61 кг-с/мм2)
— поправочный коэффициент на главный угол в плане резца
= 0; (= 450);
То Кр = = 89 0 = 89;
Значения находим по таблице 8
Определяем эффективную мощность на резании Nэф;
Nэф==кВт Определяем требуемую мощность электродвигателя.
КПД станка = 75
Определяем технологическое (машинное) время
где L — расчётная длина обрабатываемой поверхности.
L = l + у +, где у = t ctg = 98 ctg450 = 98 мм;
= (12); Sпасп = 2 37 = 74 мм;
i = 7 (количество проходов)
L = l + у + = 12 + 98 + 74 = 172 мм;
минут.
Расчёт режима резания при сверлении. Деталь — заготовка конического зубчатого колеса. Материал — сталь 45: в = 61 кг-с/мм2;
Станок вертикально сверлильный модели 2Н135; Сверло — спиральное из быстрорежущей стали Р18; 30
Определяем глубину резания:
15 мм Назначаем подачу для первого точения:
S = 02 = 02 30 = 6 мм/об;
Корректируем подачу по паспорту станка 2Н135;
Sпас = 1 6 мм/об; Z =9;
S = 6, т. е. 1 < S < 6
Проверяем выбранную подачу с паспортной подачей станка 2H135:
Sпасп = S6 = 577 мм/об Определяем допускную скорость резания с учетом поправочных коэффициентов.
где
Кv = KLv KMv KHv
поправочный коэффициент.
KLv — коэффициент, учитывающий глубину отверстия в зависимости от диаметра сверла. По таблице 9 находим KLv = 0;
KMv — коэффициент, учитывающий влияние материала.
Для стали; где = 9 (таб. 10)
в = 61; ;
KMv — коэффициент, учитывающий материал сверла.
Для сверла из быстрорежущей стали KMv = 0;
Кv = KLv KMv KMv = 0 14 0 = 14;
По табл. 11 находим для S > 2;
Cv = 8; bv = 4; Xv = 0; Yv = 7; m = 2;
м/мин;
Определяем расчётную частоту вращения ;
Скорректируем найденное число оборотов шпинделя по паспорту станка Nпасп = 245 об/мин Определяем фактическую скорость резанья:
Основные режимы резанья при сверлении:
S = 6 мм/об;
V = 231 м/мин;
n = 245 об/мин;
Определяем эффективную мощность на резании Nэф;
= 8 (КПД станка по паспорту)
4. Определяем технологическое (машинное) время где L — расчётная длина обрабатываемой поверхности.
;
lдействительная длина (чертёжный размер) l = 33 мм;
У — величина врезания;
— выход инструмента;
У+ = 0.4 D = 0.4 30 = 12 мм
5. Выбор станка, уход за ним Станок надо выбирать с учетом наибольшего диаметра обрабатываемой заготовки и требуемой мощности. Станок должен быть таким, чтобы мощность его электродвигателя была ближайшей большей требуемой мощности, и максимальный диаметр детали, который можно обрабатывать на данном станке, был бы ближайшим большим наибольшего диаметра обрабатываемой детали. Для обработки зубчатого колеса чаще применяют станок модели 1К62 (Рисунок 2).
Рисунок 2
Техническая характеристика универсального токарно-винторезного станка 1К62 Класс точности по ГОСТ 8–82 H
Наибольший диаметр обрабатываемой заготовки, мм над станиной 400
над суппортом 220
Наибольшая длина обрабатываемой заготовки, мм 1000
Размер внутреннего конуса в шпинделе, М Морзе 6 М80*
Конец шпинделя по ГОСТ 12 593–72 6К, 6М*
Диаметр сквозного отверстия в шпинделе, мм 55, 62*
Наибольшая масса устанавливаемой заготовки, кг закрепленного в патроне 300
закрепленного в центрах 1300
Число ступеней частот вращения шпинделя прямого 23
обратного 12
Пределы частот вращения шпинделя, мин прямого 12,5 — 2000
обратного 19 — 2420
Число ступеней рабочих подач:
— продольных 42, 56*
— поперечных 42, 56*
Пределы рабочих подач, мм/об продольных 0,07 — 4,16
поперечных 0,035 — 2,08
Количество нарезаемых резьб, единиц:
метрических 45, 53*
дюймовых 28, 57*
модульных 38
архимедовой спирали 5
Пределы шагов нарезаемых резьб дюймовых, число ниток на дюйм 24 — 1,625
метрических, мм 0,5 — 192
модульных, модуль 0,5 — 48
архимедовой спирали, дюйм 3/8″, 7/16″
архимедовой спирали, мм 8, 10, 12
Наибольший крутящий момент, кНм 2
Наибольшее перемещение пиноли, мм 200
Поперечное смещение корпуса, мм ±15
Наибольшее сечение резца, мм 25
Габаритные размеры станка, мм Длина 2812
ширина 1166
высота 1324
Масса станка, кг 2140
Привод станка Мощность электродвигателя привода главного движения, кВт 10
Мощность электродвигателя привода быстрых перемещений суппорта, кВт 0,75 или 1,1
Мощность насоса охлаждения, кВт 0,12
Производительность и точность станка, обусловленные его конструкцией и изготовлением, в значительной степени зависят от ухода за ним. Поэтому токарь, фрезеровщик, станочник обязан систематически очищать станок от стружек, пыли и пр. и регулярно смазывать его. Очистку станка необходимо производить, по крайней мере, один раз в смену. Тряпкой или лучше концами, смоченными в керосине, смывают со станка грязь и засохшее масло. Если на станке обрабатывались чугунные детали, нужно щеткой всюду смести стружку. После очистки все обработанные поверхности станка следует слегка смазать маслом, чтобы защитить их от коррозии.
Особо важное значение имеет своевременное смазывание всех трущихся частей станка. Необходимо изучить карту смазки станка той модели, на которой токарю предстоит работать. В корпус коробки скоростей должно быть налито в достаточном количестве масло индустриальное 30. Коробки скоростей многих станков имеют указатели высшего уровня масла, что облегчает наблюдение за количеством последнего. Смазка механизмов коробки скоростей осуществляется во время работы станка разбрызгиванием масла зубчатыми колесами. Смену масла в коробке скоростей рекомендуется производить не реже, чем один раз в месяц. Если станок запускается в работу впервые, то масло, залитое в коробку при пуске станка, необходимо сменить в первый раз через 10 дней его работы, во второй — после 20 дней и лишь после этого перейти на регулярную смену масла. После спуска отработанного масла коробку следует промыть чистым керосином. Заливаемое масло рекомендуется фильтровать через сетку.
Очень тщательно следует смазывать подшипники шпинделя станка. У многих современных станков, в том числе и у рассмотренного выше станка модели 1К62, смазка переднего подшипника шпинделя и фрикционной муфты производится посредством специального электронасоса. Необходимо постоянно наблюдать за его исправностью. Если смазка подшипников фитильная, надо при заполнении проверить исправность фитилей. Для этого необходимо, заполнив каждую масленку маслом, вынуть фитили и посмотреть, проходит ли масло к месту смазывания. Коробка подач смазывается так же, как и коробка скоростей, разбрызгиванием. Кроме того, иногда для дополнительной фитильной смазки подшипников коробки подач в верхней ее части имеется резервуар для масла. Через фитили и особые трубки масло из этого резервуара поступает к местам смазки. Все прочие трущиеся поверхности деталей фартука получают фитильную смазку из общих резервуаров, расположенных в верхней части фартука, или через отверстия, закрытые шариком. На станке модели 1К62 механизм фартука смазывается от плунжерного насоса.
Через отверстия смазываются один раз в смену все скользящие поверхности частей суппорта. Не меньше чем один раз в смену необходимо смазывать чистым маслом направляющие станины и частей суппортов, поверхность ходового винта и ходового валика и их подшипники. Направляющие станины и поперечного суппорта станка модели 1К62 обеспечиваются периодической смазкой струей масла из фартука через специальный краник.
Необходимо также один раз в смену смазывать пиноль и винт задней бабки.
Смазывание некоторых частей станка производится техническим вазелином, которым наполняется масленка, имеющаяся вблизи от смазываемых поверхностей.
6. Описание режущего инструмента Сущность технологии изготовления деталей машин состоит в последовательном использовании различных технологических способов воздействия на обрабатываемую заготовку с целью придать ей заданную форму и размеры указанной точности.
Одним из таких способов является механическая обработка заготовок резанием. Она осуществляется металлорежущим инструментом и ведётся на металлорежущих станках.
Все способы и виды обработки металлов основаны на срезании припуска и преобразования его в стружку, составляют разновидности, определяемые термином резание металлов.
Наивыгоднейшим режимом резания называется такой, при котором обеспечиваются наибольшая производительность и наименьшая себестоимость обработки при этом, не нарушая качества изделия.
При назначении элементов режима резания необходимо наиболее полно использовать режущие свойства инструмента, а также кинематические и динамические данные станка. При этом должно быть обеспечено заданное качество обработанной детали. Назначение режима резания — это выбор скорости, подачи и глубины резания, обеспечивающий требуемый период стойкости инструмента.
Выбор метода расчёта диктуется конкретными условиями.
В основном это затраченное время и качество обработки. Для этого выпущено достаточное количество литературы, которое с изменением технологии и новыми требованиями всё больше пополняется. Единственное, что требуется правильно в них ориентироваться и более точно использовать их по назначению.
Обработка металлов резанием — это процесс снятия режущим инструментом с поверхности заготовки слоя металла для получения необходимой геометрической формы, точности размеров и шероховатости поверхности детали.
При работе на токарных станках наиболее часто используют проходные прямые, проходные отогнутые, проходные упорные и отрезные резцы. Для обработки детали типа зубчатое колесо, в процессе токарной обработки, чаще всего используется резец проходной отогнутый.
Размеры и обозначение проходных отогнутых резцов с пластинками из твердого сплава (ГОСТ 18 866−73, ГОСТ 18 877–73) (Рис.3)
Рисунок 3
Различают следующие элементы режущей части резца: передняя поверхность, по которой сходит стружка. Главная задняя поверхность, обращённая к поверхности резания заготовки. Вспомогательная задняя поверхность, обращённая к обработанной поверхности заготовки. Главная режущая кромка — линия пересечения передней и главной задней поверхностей. Вспомогательная режущая кромка — линия пересечения передней и вспомогательной задней поверхностей. Вершина резца — точка пересечения главной и вспомогательной режущих кромок. Для увеличения износостойкости резца и повышения чистоты обработанной поверхности вершину иногда закругляют или срезают прямолинейной переходной кромкой (Рис.4).
Рисунок 4
Для выполнения работы резания рабочей части резца необходимо придать форму клина. С этой целью резец затачивают по передней и задней поверхностям. Для определения углов, под которыми располагаются относительно друг друга поверхности рабочей части инструмента, вводят координатные плоскости:
Основная плоскость — плоскость, параллельная направлениям продольной и поперечной подач. У токарных резцов за основную плоскость принимают нижнюю опорную поверхность резца. Плоскость резания — плоскость, проходящая через главную режущую кромку резца касательно к поверхности резания заготовки. Главная секущая плоскость — плоскость, перпендикулярная к проекции главной режущей кромки на основную плоскость.
Все три плоскости взаимно перпендикулярны.
Важными характеристиками токарного резца являются углы его заточки:
Главный задний угол б (альфа) — угол между главной задней поверхностью резца и плоскостью резания. Увеличение данного угла уменьшает трение задней грани резца о поверхность заготовки.
Передний угол г (гамма) — оказывает влияние на процесс резания, на легкость схода стружки, качество обработанной поверхности.
Угол заострения в (бета) — угол между передней и главной задней поверхностями. Чем меньше угол заострения, тем легче резец входит в металл и отделяет стружку с меньшим усилием. Однако при уменьшении угла заострения снижается прочность резца, и он быстрей затупляется и ломается.
Рисунок 5
Угол резания д (дельта) — угол между передней поверхностью резца и плоскостью резания (д=б+в). (Рисунок 5)
Токарные резцы подразделяют:
— По направлению подачи (правые и левые)
— По конструкции головки (прямые и отогнутые)
— По способу изготовления (цельные и составные)
— По сечению стержня (прямоугольные, круглые и квадратные)
— По виду обработки (проходные, подрезные, отрезные, прорезные, расточные, фасонные, резьбонарезные).
Следует помнить, что токарные резцы являются дорогостоящим инструментом. Их нельзя использовать не по назначению, бросать, хранить «навалом». Необходимо не допускать значительного затупления инструмента.