Технология алюминия
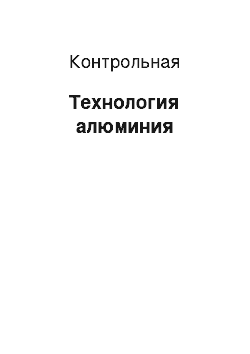
Алюминий, выделяющийся в процессе электролиза, имеет большую плотность, чем электролит, и накаливается на подине электролизёра. Извлечение жидкого алюминия из ванны осуществляется один раз в 2−3 суток. При выгрузке алюминия на дне подины оставляют слой металла, который предохраняет подину от разрушения и заполняет все неровности, что облегчает регулировку анодов. Кроме того, он способствует… Читать ещё >
Технология алюминия (реферат, курсовая, диплом, контрольная)
Контрольная работа Технология алюминия
1. Руды и минералы
2. Производство глинозёма по способу Байера
3. Получение глинозёма способом спекания
4. Переработка нефелинов
4.1 Получение криолита
4.2 Физико-химические свойства криолитноглинозёмных расплавов
4.3 Поверхностное натяжение
4.4 Напряжение разложения компонентов криолитно-глинозёмного расплава
4.5. Катодный и анодный процессы
4.6 Анодный эффект
4.7 Влияние различных факторов на выход по току
4.8 Устройство и работа электролизёра для получения алюминия
4.9 Рафинирование алюминия и разливка алюминия Литература
1. Руды и минералы Алюминий находится в рудах в виде окисленных минералов, двойных сульфатов и силикатов. Ниже приведены важнейшие рудные минералы алюминия (Таблица 1).
Таблица 1- Основные минералы алюминия
Название минерала | Формула минерала | Содержание Al2O3, % | |
Корунд Диаспор, бемит Гибсит (гидраргиллит) Нефелин Алунит Каолинит Кианит (андалузит, силлиманит) | Al2O3 AlООН Al (ОН)3 (Na, K)2О · Al2O3·2SiO2 (К, Na)2SO4· Al2(SO4)3·4Al (OH)3 Al2O3· 2SiO2·2Н2О Al2O3· SiO2 | 65,4 32−36 37−39 39,5 63,2 | |
Основной вид рудного сырья представляют собой горные породы, содержащие бемит или диаспор, гидрагиллит или гибсит и небольшие количества корунда и алюмосиликатов. Эти горные породы получили название бокситов. Пустая порода в них представлена гидратированными оксидами железа, различными водными силикатами и карбонатами кальция и магния. Крупные месторождения бокситов находятся в Северном Казахстане (тургайские). Они характеризуются следующим составом (%): Al2O3 — 40−50; SiO2 — 5−15; Fe2O3 — 14−16; TiO2 — 2−3.
Промышленное значение имеют нефелиносодержащие породы. Качество этих руд оценивается соотношением в них Na2O: Al2O3, которое по возможности должно быть близким к единице. В них также должно находиться минимальное количество железа. Иногда нефелин встечается вместе с апатитами [Са10Сl2(F2)(PO4). Апатит отделяют от нефелина флотацией и используют для получения удобрений. Полученный нефелиновый концентрат содержит порядка 30% Al2O3,20% (Na2O+Ka2O) и 44% SiO2
Алуниты содержат изоморфные смеси натриевого и калиевого алунитов и могут служить сырьём для получения глинозёма, поташа и соды и серной кислоты.
В глинах содержится каолинит. Если в глине содержится не менее 30−32% Al2O3, то она может служить сырьём для получения алюминия.
Высокоглинозёмистые силикаты имеет высокое содержание андалузита, силлиманита и кианита. Эти руды могут быть использованы для получения сплавов алюминия с кремнием — силуминов.
2. Производство глинозёма по способу Байера Производство глинозёма из алюминиевых руд является первой необходимой стадией получения алюминия. Способы получения глинозёма из разных руд различны. Так из бокситов глинозём получают по способу Байера, который основан на обратимости реакции между гидратированным оксидом алюминия и щёлочью:
Al (OH)3 + NaOH = NaAl (OH)4 (1)
или
AlOOH + NaOH + H2O = NaAl (OH)4 (2)
При нагревании боксита с концентрированной щёлочью гидраргиллит при температуре около 100оС реагирует с последней и образует моноалюминат натрия. Для подобного растворения диаспора и бемита необходима температура 160−200оС. При этом необходимо высокое давление. Поэтому процесс осуществляется в автоклавах, представляющих собой толстостенные стальные сосуды (Рисунок 1)
1-стальной толстостенный сосуд; 2- патрубок для подачи пульпы; 3-труба для загрузки автоклава или передачи пульпы в соседний аппарат Рисунок 1 Автоклав для выщелачивания боксита В бокситах присутствует кремнезём, как в чистом виде, так и в виде каолинита. Несвязанный кремнезём реагирует с едким натром и переходит в раствор в виде силиката натрия:
SiO2 + 2NaOH = Na2SiO3 + H2O (3)
Силикат натрия взаимодействует с алюминатом натрия с образованием нерастворимого гидроалюмосиликата натрияпермутита:
2Na2SiO3 + 2NaAl (OH)4 = Na2O· 2SiO2·Al2O3•2H2O +4NaOH (4)
Этот процесс приводит к очистке растворов от SiO2 — их обескремниванию, но влечёт за собой некоторые потери щёлочи и уже растворённого глинозёма с твердым нерастворимым остатком, который называется красным шламом. Для способа Байера характерно совмещение процессов выщелачивания и обескремнивания. Полнота обескремнивания алюминатного раствора характеризуется так называемым кремниевым модулем, представляющим собой отношение
? = (6)
где? — кремниевый модуль;
Al2O3 — содержание глинозёма в алюминатном растворе, %;
SiO2 — содержание кремнезёма в алюминатном растворе, %.
Чем выше кремниевый модуль, тем выше полнота обескремнивания раствора. Процесс обескремнивания в значительной степени протекает не в автоклаве, а вне его при разбавлении концентрированного алюминатного раствора и при отделении красного шлама в сгустителях. К концу выщелачивания в автоклаве кремневое отношение составляет порядка 100−150. Это недостаточно для получения глинозёма нужной чистоты. В процессе разбавления кремниевый модуль увеличивается до 200−250. Высокое содержание SiO2 в растворе нежелательно, так как оно приводит к увеличению потерь глинозёма с красным шламом. Поэтому переработка бокситов с высоким содержанием кремнезёма нецелесообразна.
Содержащиеся в боксите карбонаты кальция и магния также реагируют со щёлочью с образованием соды:
CaCO3 + 2NaOH = Ca (OH)2 + Na2CO3 (5)
MgCO3 + 2NaOH = Mg (OH)2 + Na2CO3 (6)
Сода накапливается в растворе также за счёт её взаимодействия с углекислым газом воздуха:
2NaOH + CO2 = Na2CO3 + H2O (7)
Поэтому способ Байера мало пригоден для переработки бокситов с высоким содержанием кремнезёма и карбонатов.
На процесс выщелачивания боксита влияет ряд факторов:
— продолжительность выщелачивания;
— концентрация щелочного раствора;
— каустическое отношение алюминатного раствора;
— давление (температура) внутри автоклава;
— добавка извести;
— тонина помола боксита.
Продолжительность выщелачивания боксита определяется опытным путём. Она должна быт таковой, чтобы извлечение глинозёма было достаточно высоким, а обескремнивание алюминатного раствора достаточно полным. Пребывание пульпы в автоклаве обычно составляет 2−2,5 часа.
С повышением концентрации щёлочи в растворе возрастает концентрация глинозёма в алюминатном растворе. Это позволяет сократить объём аппаратуры для выщелачивания и хранения растворов. Однако при повышении концентрации щёлочи ускоряется коррозия аппаратуры и затрудняется отделение красного шлама. На практике обычно используются растворы с концентрацией щёлочи, в пересчёте на Na2O, около 300г/л.
Под каустическим отношением (модулем) понимают молярное отношение концентрации щёлочи, в пересчёте на Na2O, к глинозёму:
?к = (8)
где ?ккаустическое отношение (модуль);
Na2O — число молей Na2O в 1 л раствора;
Al2O3 — число молей Al2O3 в1 л пасвора.
Скорость выщелачивания возрастает по мере увеличения каустического модуля оборотного щелочного раствора.
Важную роль играет конечное значение каустического модуля в алюминатных растворах. Снижение его приводит к уменьшению стойкости алюминатного раствора, который склонен к разложению при отстаивании красного шлама в сгустителях. На практике каустическое отношение щелочных растворов, направляемых на выщелачивание боксита, составляет 3,7−3,8, а конечного алюминатного раствора 1,7−1,8.
При прочих равных условиях с повышением давления, что идентично повышению температуры, скорость выщелачивания возрастает. При этом увеличивается также извлечение глинозёма.
Незначительная добавка извести (3−5% от массы боксита) повышает извлечение глинозёма.
С увеличением степени измельчения боксита растёт удельная поверхность его контакта с раствором, что будет приводить к повышению скорости процесса выщелачивания.
После выщелачивания пульпа из автоклава поступает на разбавление. Цель разбавления-снижение концентрации алюминатного раствора и увеличение ж: т в пульпе. Разбавление раствора в дальнейшем обеспечивает большую эффективность процесса разложения алюминатного раствора с выделением гидрооксида алюминия, более глубокое обескремнивание раствора и способствует облегчению процесса отстаивания красного шлама.
Разбавленная пульпа направляется на отстаивание, которое осуществляется в сгустителях.
Шламы отделяют от раствора, отстаиванием, фильтрованием и промывкой, а затем отправляют в отвал.
Осветлённый алюминатный раствор подвергают разложению с выделением в осадок кристаллического гидрооксида алюминия. Для этого раствор длительное время перемешивают с заранее введённой затравкой свежеосаждённого гидраргиллита. Этот процесс называют выкручиванием или декомпозицией. Схематически разложение алюминатного раствора с участием затравки можно выразить уравнением:
NaAl (OH)4 + nAl (OH)3 = (n+1)Al (OH)3 + NaOH (9)
Процесс осаждения проводится 50−70 часов.
На процесс разложения алюминатного раствора оказывают влияние следующие факторы:
— каустическое отношение алюминатного раствора;
— концентрация раствора;
— температура;
— количество и качество затравки;
— перемешивание раствора.
При уменьшении каустического модуля процесс разложения алюминатного раствора протекает более интенсивно. На практике каустическое отношение исходных алюминатных растворов поддерживают в пределах 1,6−1,8. За время операции разложения оно увеличивается до 3,8−3,9.
При повышении концентрации глинозема в растворе при одном и тот же каустическим отношением снижается скорость разложения алюминатного раствора. Однако при этом увеличивается абсолютное извлечение глинозёма. Поэтому для каждого каустического отношения существует оптимальная концентрация глинозёма. В практике в процесс выкручивания направляют алюминатные растворы с концентрацией глинозёма 120−125 г/л с каустическим отношением 1,7−1,8.
При понижении температуры до 30−40оС процесс разложения алюминатного раствора значительно увеличивается. Однако при дальнейшем понижении температуры замедляется. Это объясняется повышением вязкости раствора при низких температурах. При температуре выше 40оС процесс замедляется вследствие уменьшения пересыщения раствора. На глинозёмных заводах применяют политермический режим разложения алюминатного раствора. Процесс начинают при температуре выше 40оС и постепенно охлаждают раствор по мере его разложения. Это связано с тем, что при политермическом режиме удаётся поддерживать пресыщенное состояние раствора.
Затравка из Al (OH)3 обеспечивает готовые центры кристаллизации в алюминатном растворе и обеспечивает получение крупных кристаллов Аl (OH)3. Количество затравки характеризуется затравочным числом, которое показывает массовое отношение Al2O3, содержащееся в затравке, к Al2O3 алюминатного раствора. На практике заправочное отношение поддерживается в пределах 1,0−1,5.
Для заправки используется мелкий дисперсный свежеосаждённый из алюминатных растворов Al (OH)3. Такая затравка получила название активной. Частицы такой затравки имеют сильно развитую поверхность и обеспечивают быстрый рост кристаллов осаждаемого из алюминатного раствора Al (OH)3.
Перемешивание раствора в процессе выкручивания поизводят для поддержания затравки во взвешенном состоянии и для выравнивания концентрации алюминатного раствора.
Для разложения алюминатных растворов используют аппараты, называемые декомпозерами. Применяются декомпозеры с механическим и воздушным премешиванием.
Наибольшее распространение получили декомпозеры с воздушным перемешиванием, которые представляет собой цилиндрический сосуд диаметром 7−8 м и высотой до 30 м с коническим дном (Рисунок 2).
глинозём алюминий электролизёр расплав
1-стальной чан с коническим дном; 2-центральная труба; 3,4-трубы для подачи сжатого воздуха; 5-сливной патрубок Рисунок 2 Декомпозер с воздушным перемешиванием От 9 до 16 таких аппаратов соединяют последовательно в виде каскада. Раствор перетекает из одного в другой непрерывным потоком. Общая продолжительность пребывания раствора в этой системе составляет до 60 часов. Пульпу Al (OH)3, вытекающую из хвостового декомпозера, направляют в сгустители. Из сгущённого продукта классификацией выделяют наиболее мелкую фракцию кристаллов Al (OH)3, которая служит затравкой, а остальную часть направляют на фильтрацию и промывку. Промытый осадок гидрооксида алюминия направляют на сушку и кальцинацию.
Оборотные растворы, получаемые после процесса выкручивания, направляют на выпарку и каустификацию соды.
Удаление избыточной влаги из осадка гидрооксида алюминия осуществляется в выпарных аппаратах. (Рисунок 3)
Рисунок 3 Выпарной аппарат Выпарные аппараты соединяют в последовательную трёхчетырёхкорпусную систему работающую под разряжением. В системе осуществляется противоточное движение: пар движется навстречу раствору. Первый аппарат обогревается свежим паром, а остальные вторичным (соковым) паром. При охлаждении выпаренного раствора из него выпадают кристаллы соды Na2CO3· H2O, которая накопилась в результате взаимодействия щёлочи с углекислым газом воздуха и карбонатами, находящимися в боксите. Кристаллы соды отфильтровывают и превращают их в NaOH нагреванием в мешалках с известковым молоком.
Na2CO3 +Ca (OH)2 = 2NaOH + CaCO3 (10)
Осадок карбоната кальция отфильтровывают и направляют в отвал. Раствор щёлочи упаривают, фильтруют и направляют в голову процесса на приготовление сырой пульпы.
Завершающей операцией процесса Байера является операция кальцинации гидрооксида алюминия. Кальцинация необходима для удаления гидратной влаги из Al (OH)3 и получения безводного глинозёма Al2O3. Процесс кальцинации осуществляют при температурах 1150−1200оС. При кальцинации гидратная влага удаляется в два приёма.
При температуре 225оС из молекулы Al (OH)3 удаляется две молекулы воды:
2Al (OH)3 = 2AlOOH + 2H2O (11)
или
Al2O3· 3H2O = Al2O3· H2O + 2H2O (12)
При температуре 500 оС удаляется последняя влага:
2AlOOH = ?· Al2O3 + H2O (13)
или
Al2O3· H2O = ?· Al2O3 + 2H2O (12)
?· Al2O3 обладает большой гигроскопичностью, поэтому его нагревают до 1200 оС, при которой протекает превращение:
?· Al2O3 = ?· Al2O3 (13)
Эта температура является обычной для процесса кальцинации, так как обеспечивает не только полное удаление гидратной влаги, но и достаточную негигроскопичность продукта при его длительном хранении. Не весь глинозём превращают в ?-модификацию. В прокалённом глинозёме содержится порядка 15 — 25% ?· Al2O3, а остальное — ?· Al2O3. Это связано с тем, что глинозём ?· Al2O3 снижает скорость растворения в расплавленном электролите алюминиевой ванны.
Процесс кальцинации осуществляется во вращающихся печах диаметром 4,5 м и длиной до 110 м. Печь выложена изнутри шамотным кирпичoм. В качестве топлива для нагревания шихты могут быть использованы мазут и природный газ. Движение шихты в печи осуществляется навстречу горячим газам от горения топлива.
Выходящие из печи дымовые газы уносят до 50−60% глинозёма. Пыль улавливается системой пылеулавливания, смешивается с сырым глинозёмом и возвращается на кальцинацию. Горячий глинозём после выгрузки из печи попадает в холодильник, представляющий собой наклонную вращающуюся трубу, орошаемую снаружи водой. Готовый глинозём выгружается из холодильника и транспортируется в цех электролиза глинозёма. Упрощённая схема переработки по способу Байера приведена на рисунке 4.
Рисунок 4 Упрощённая технологическая схема производства глинозёма по способу Байера
3. Получение глинозёма способом спекания Способ спекания основан на переводе оксида алюминия из боксита в водорастворимый алюминат. В качестве реагента служит сода, которая значительно дешевле щёлочи, но менее активна. Поэтому для образования алюмината натрия требуется значительно более высокая температура, которая недостижима в водных растворах. Упрощённая схема производства глинозёма способом спекания приведена на рисунке 5.
Рисунок 5 Упрощённая технологическая схема производства глинозёма по способу спекания
Шихта для процесса спекания состоит из боксита, соды, известняка или извести. После крупного дробления боксит и известняк измельчают в шаровых мельницах в среде оборотного содового раствора. Сюда же добавляют свежую соду. Из мельниц пульпу выпускают в бассейны с мешалками, где корректируется и контролируется её состав. Шихта в печь подаётся в виде пульпы, содержащей 40% влаги. За счёт сгорания топлива в горячей зоне печи температура поддерживается в пределах 1200−1300оС.
При 900оС энергично разлагается известняк по реакции:
CaCO3 = CaO + CO2 (14)
При нагревании до 1100оС оксид кальция взаимодействует с кремнезёмом, связывая его в силикат:
СaO + SiO2 = Ca2SiO4 (15)
Основная реакция спекания — образования алюмината натрия начинается примерно при 700 оС и завершается при температуре 1200 оС:
Al2O3 + Na2CO3 = 2NaAlO2 + CO2 (17)
Одновременно сода реагирует с оксидом железа и кремнезёмом:
Na2CO3 + Fe2O3 = 2NaFeO2 + CO2 (18)
Na2CO3 + SiO2 = Na2SiO3 + CO2 (19)
Спекание бокситосодо — известковой шихты осуществляют в трубчатых вращающихся печах (Рисунок 6).
1-трубчатая печь; 2-форсунка для разбрызгивания пульпы; 3-холодильник для охлаждения спека Рисунок 6 Печь для мокрого спекания бокситов В качестве топлива могут быть использованы мазут, природный газ или каменноугольная пыль. В зависимости от температуры горячих топочных газов и физико-химических превращений, происходящих в шихте, по длине печь может быть условно разделена на четыре зоны.
Зона сушки и обезвоживания находится в верхней холодной части печного барабана. Здесь температура топочных газов составляет 200−700оС, а температура шихты 20−300оС. В этой зоне из шихты удаляется влага.
Зона кальцинации имеет температуру топочных газов от 700 до 1250оС, а шихты — 300−900оС. Здесь происходит полное разложение известняка.
Зона спекания имеет наивысшую температуру газов порядка 1600−1650оС, а шихта -1200−1250оС. В этой зоне завершается процесс спекания шихты и полностью разлагается сода Na2CO3. Эта зона находится в пределах огневого факела от сжигания топлива.
Последняя зона — зона охлаждения расположена в нижней части печи. Здесь температура газов составляет порядка 1500−1550оС, а шихты 1100оС.
Из печи спечённая шихта поступает в трубчатый холодильник, где охлаждается до 60−70оС движущимся навстречу шихте воздухом или водой, орошаемой сверху. Шихта, уносимая газами в виде пыли улавливается и возвращается на спекание в качестве оборотного материала.
После охлаждения спечённая шихта поступает на выщелачивание.
Предварительно измельчённый спек подвергается выщелачиванию горячей водой.
В процессе выщелачивания алюминат натрия хорошо растворяется в горячей воде по реакции:
Na2AlO4 + 4H2O = 2NaAl (OH)4 (20)
Феррит натрия в водной среде подвергается гидролизу с высвобождением щёлочи:
2NaFeO2 + (n+1)H2O = 2NaOH + Fe2O3· nH2O (21)
Выщелачивание осуществляется в трубчатых выщелачивателях проточным методом. (Рисунок 7)
1-вращаюаяся труба; 2 спираль; 3- устройство для загрузки спека; 4-устройство для выгрузки шлама Рисунок 7 Трубчатый выщелачиватель Трубчатый выщелчативатель представляет собой стальную трубу длиной 60 м и диаметром 3,6 м. В трубе укреплена дырчатая спираль, которая передвигает спек вверх по трубе, а через отверстия в спирали навстречу спеку сверху вниз движется вода или алюминатный раствор. При растворении алюмината натрия выделяется тепло, в результате чего раствор может сильно разогреться. Поэтому труба охлаждается водяными холодильниками и просасывемым через трубу воздухом.
На некоторых заводах выщелачивание проводят в диффузорах (Рисунок 8).
1- корпус; 2 — люк для загрузки спека; 3-откидная крышка люка для разгрузки спека; 4-колосниовая решётка; 5- гидравлический привод крышки; 6- патрубок для выхода раствора Рисунок 8 Диффузор для выщелачивания спека Загрузка спека осуществляется сверху и он слоем высотой до 5 м ложится на колосниковую решётку. Снизу под решётку под некоторым давлением подают горячую воду, которая поднимается вверх по слою спека и выщелачивает его. Раствор после выщелачивания вытекает из диффузора через верхний патрубок.
На практике 12−14 диффузоров соединяют в последовательную цепь. В головной диффузор подают горячую воду, а их последнего диффузора вытекает концентрированный раствор алюмината натрия. Все диффузоры соединены трубопроводами, снабжёнными кранами, которые позволяют отключить любой из них, не нарушая процесса.
Разгрузка твёрдого остатка осуществляется через нижний люк диффузора.
Выщелачивание в диффузорах исключает необходимость отделения от раствора красного шлама.
Растворы полученные, в процессе выщелачивания содержат от 80 до 280 г/л Al2O3. Независимо от способа выщелачивания в растворах всегда присутствует силикат натрия, содержащий кремний. Загрязнённость кремнием раствора характеризуется кремниевым модулем. Кремниевый модуль после выщелачивания перемешиванием составляет порядка 35−50, а после выщелачивания в диффузорах 18−20. и нуждается в очистке до величины кремниевого отношения 450−500.
Обескремнивание заключается в связывании растворённого в алюминатном растворе кремнезёма в нерастворимые соединения и перевод их в осадок.
Удаление кремния осуществляется нагреванием алюминатного раствора до 160−170 оС в автоклавах. Процесс очистки основан на взаимодействии силиката натрия с алюминатом:
2NaAl (OН)4 + 2Na2SiO3 = Na2O· Al2O3·2SiO2·2H2O + 4NaOH (22)
Второй способ обескремнивания алюминатных растворов заключается в нагревании их с добавкой извести:
2NaAl (OН)4+2Na2SiO3+Ca (OH)2=CaO· Al2O3·2SiO2·2H2O+6NaOH (22)
Образующиеся в результате протекания реакций (22) и (23) кристаллы гидроалюмосиликатов натрия и кальция выпадают в осадок и таким образом выводят кремнезём из алюминатного раствора.
Осадок алюмосиликатов, называемый белым шламом, после сгущения и фильтрования направляют в шихту спекания.
Очищенный от кремния алюминатный раствор направляют на карбонизацию. Карбонизация — это процесс разложения алюминатных растворов под действием углекислого газа с целью получения кристаллического гидрооксида алюминия.
Для этих целей алюминатный раствор продувают предварительно очищенными от пыли дымовыми газами из печей спекания, которые содержат 10−14% СО2. Продувка осуществляется при температуре 70−80оС в течение 8−10 часов при постоянном перемешивании.
Процесс карбонизации протекает в две стадии.
Первая стадия заключается в нейтрализации присутствующей в растворе свободной едкой щёлочи с образованием соды:
2NaOH + CO2 = Na2CO3 +H2O (23)
Вторая стадия заключается в выделении гидрооксида алюминия за счёт разложения алюмината натрия в следствие сильного снижения каустического модуля, вызванного уменьшением концентрации свободной щёлочи в растворе:
NaAl (OH)4 = Al (OH)3+ NaOH (24)
Разложение алюминатного раствора осуществляют в карбонизаторах. Карбонизатор представляет собой стальной цилиндрический бак высотой до 8 м и диаметром до 6 м, снабжённый барботёром для подачи углекислого газа и цепной мешалкой (Рисунок 9).
1-стальной бак; 2-цепная мешалка; 3-дарботёр для подачи углекислого газа; 4-сливной патрубок Рисунок 9 Карбонизатор Продолжительность процесса карбонизации составляет 12−14 часов. Наиболее рациональна и удобна для эксплуатации непрерывная карбонизация, которую проводят в нескольких карбонизаторах последовательно соединённых между собой.
Выгрузку гидратной пульпы осуществляют через предусмотренное в днище отверстие. Слив содового раствора производят через патрубок в стенке карбонизатора на высоте порядка 1,3 м от днища.
Отделенный от содового раствора гидрооксид алюминия фильтруют, промывают и направляют на кальцинацию, которая осуществляется точно так же, как и в способе Байера. Оборотный содовый раствор выпаривают и и направляют на приготовление шихты для мокрого спекания.
Способ спекания является достаточно универсальным и может применяться для извлечения глинозёма из различных алюминиевых руд.
Этим способом могут быть переработаны на глинозём нефелины, глины, а также зола от сжигания каменных углей на электростанциях.
4 Переработка нефелинов В нефелинах помимо оксида алюминия содержатся щелочные металлы натрий и калий. Часто их содержания вполне хватает для образования алюмината натрия в достаточном количестве. Попутно из нефелинов получают поташ и соду.
Нефелиновый концентрат и известняк измельчают до крупности 0,1 мм и спекают во вращающихся трубчатых печах сухим способом при температуре 1250−1300оС. В основе процесса спекания лежит химическая реакция:
Na, K2ОAl2O32SiO2+4СаСО3=(Na, K)2ОAl2O3+22CaO· SiO2+4CO2(25)
Спек измельчают и выщелачивают оборотным раствором в мешалках при температуре 70−80оС. После отделения шлама раствор обескремнивают и подвергают полной карбонизации. Полученный осадок гидрооксида алюминия промывают и прокаливают. Около половина раствора от выщелачивания направляется в оборот, а остальная часть направляется на выпаривание. Из выпаренного раствора сначала кристаллизуют соду Na2CO3· H2O, а затем после дополнительного выпаривания выделяют поташ K2CO3.
4.1 Получение криолита Электролит для элекролиза алюминия состоит из трёх основных компонентов: криолита 3NaF· AlF3 или Na3AlF6, фтористого натрия NaF и фтористого алюминия AlF3.
Основной составляющей электролита является криолит. Месторождения этого минерала редки и они не в состоянии обеспечить криолитом алюминиевую промышленность. Поэтому криолит производится искусственным путём. Сырьём для получения криолита служит природный минерал флюорит (полевой шпат) CaF2. Получение криолита из полевого шпата может производиться двумя способами: кислотным и щелочным. Щелочной способ пока не получил широкого развития. Поэтому в настоящее время криолит получают в основном кислотным способом.
По этому способу флюорит измельчают, обогащают процессом флотации и обрабатывают крепкой серной кислотой при температуре 200оС. В результате протекает химическая реакция:
CaF2 + H2SO4 = CaSO4 + 2HF (26)
При протекании реакции выделяется газообразный фтористый водород.
Присутствующий в полевом шпате кремнезём в состоянии реагировать с фтористым водородом с образованием летучего соединения SiF4:
SiO2 + 4HF = SiF4 + 2H2O (27)
Образующуюся смесь газов HF и SiF4 поглощают водой, получая в результате плавиковую кислоту, загрязнённую кремнефтористой кислотой H2SiF6, которая образуется по реакции:
SiF4 + 2HF = H2SiF6 (28)
Загрязнённая плавиковая кислота подвергается обескремниванию, путём добавления к ней соды, которая реагирует с кремнефтористой кислотой с образованием малорастворимого соединения кремнефтористого натрия Na2SiF6:
H2SiF6 + Na2CO3 = Na2SiF6 + H2O + CO2 (29)
Осадок соли Na2SiF6 отфильтровывают, а очищенный от кремния раствор обрабатывают стехиометрическим количеством гидрооксида алюминия для получения фтороалюминиевой кислоты:
6HF + Al (OH)3 = H3AlF6 + 3H2O (30)
Полученный раствор фтороалюминиевой кислоты обрабатывают содой для получения криолита:
2H3AlF6 + 3Na2CO3 = 2Na3AlF6 + 3СО2 + 3Н2О (31)
Криолит практически не растворим в воде и выпадает в осадок. Осадок криолита отфильтровывают и сушат.
Фтористый алюминий получают нейтрализацией плавиковой кислоты избыточным количеством Al (OH)3:
3HF + Al (OH)3 = AlF3 + 3H2O (32)
Действую содой на плавиковую кислоту, получают фтористый натрий:
2HF + Na2CO3 = 2NaF + CO2 + H2O (33)
4.2 Физико-химические свойства криолитноглинозёмных расплавов Для получения алюминия используется криолитноглинозёмный расплав, который должен отвечать следующим требованиям:
— он не должен содержать ионы более электроположительных металлов, чем алюминий;
— должен хорошо растворять глинозём;
— являться относительно легкоплавким ;
— его плотность должна быть меньше плотности алюминия, для исключения контакта жидкого алюминия с кислородом воздуха;
— он должен быть жидкотекучим, что благоприятствует выделению газов и выравниванию состава расплава;
— он не должен взаимодействовать с углеродистой футеровкой, анодом и катодом;
— он должен обладать достаточно высокой электропроводностью;
— он не должен быть гигроскопичен;
— он должен обладать малой летучестью при температуре процесса электролиза.
Этим требованиям отвечает расплав криолита с содержанием 3−5% СаF2, 4−5% MgF2, 1,3 -8% Al2O3.
Одной из основных характеристикой состава расплава является его криолитное отношение, характеризующее молярное отношение в расплаве. Для чистого криолита это отношение равно 3. Такой расплав считается нейтральным. Если криолитное отношение < 3, то такой расплав считается кислым, если > 3, то такой расплав называют щелочным. В промышленных электролизёрах криолитное отношение поддерживается в пределах 2,6−2,8.
Примеси N2O, H2O, CaO и SiO2 которые всегда присутствуют в криолите и глинозёме разлагают в расплаве криолит и повышают криолитное отношение:
2Na3AlF6 + 3Na2O = Al2O3 + 12NaF (34)
2Na3AlF6 + 3CaO = Al2O3 + 3CaF2 +6NaF (35)
4Na3AlF6 + 3SiO2 = Al2O3 + 12NaF + 3SiF4 (36)
2Na3AlF6 + 3H2O = Al2O3 + 6NaF + 6HF (37)
В этом случае в расплав добавляют AlF3 для снижения криолитного отношения.
В других случаях, как например, из-за впитывания угольной футеровкой ванны NaF, криолитное отношение может снижаться. Тогда для поддержания нужного криолитного отношения в расплав добавляют NaF. Таким образом, фтористые натрий и алюминий необходимы для регулирования криолитного отношения в расплаве.
Температура плавления чистого криолита составляет 1000оС. Добавление в расплав CaF2 и MgF2 снижает температуру плавления расплава. Поэтому процесс электролиза алюминия проводят при температурах 930−950оС.
Нахождение Al2O3 в расплаве в растворённом состоянии существенно облегчает процесс электролиза. Величина растворимости глинозёма в киолитно-глинозёмном расплаве в первую очередь зависит от криолитного отношения, которое сложным образом влияет на растворимость глинозёма. Увеличение криолитного отношения до 13 повышает растворимость глинозёма. Дальнейшее увеличение криолитного отношения снижает растворимость глинозёма в расплаве.
Добавление к расплаву СaF2 и MgF2 снижает растворимость глинозёма. Кроме того, они снижают скорость растворения глинозёма. Поэтому в расплаве поддерживают оптимальное содержание фторидов кальция и магния. Их суммарное содержание в расплаве обычно не превышает 10%. Это обеспечивает достаточное снижение температуры плавления расплава и достаточно высокую растворимость глинозёма. На практике содержание глинозёма в расплаве поддерживают в пределах 8%.
Из всех компонентов расплава наибольшей вязкостью обладает чистый криолит. Добавление к расплаву CaF2 и MgF2 способствуют повышению вязкости расплава. Однако определяющую роль в изменении вязкости расплава играет глинозём. Так увеличение в расплаве концентрации растворённого Al2O3 до 10% увеличивает вязкость расплава на 23%, по сравнению с вязкостью чистого криолита при 1000оС.
Вязкость промышленных электролитов при 1000оС составляет порядка 3,25−3,40 спз.
4.3 Поверхностное натяжение При электролизе глинозёмнокриолитных расплавов имеет место четыре вида пограничных поверхностей, а, следовательно, и различных поверхностных натяжения (Рисунок 10).
Рисунок 10 Виды поверхностных натяжений алюминиевом электролизёре Мерой поверхностного натяжения является краевой угол смачивания (Рисунок 11).
Рисунок 11 Краевой угол смачивания на границе твёрдая фаза-расплав-газ.
Если угол смачивания < 90о, то имеет место низкое поверхностное натяжение и твёрдая поверхность хорошо смачивается расплавом.
Если угол смачивания > 90о, то имеет место высокое поверхностное натяжение и твёрдая поверхность плохо смачивается расплавом.
Алюминий имеет высокое поверхностное натяжение и потому плохо смачивает поверхность катода и имеет выпуклый мениск.
Криолитно-глинозёмный электролит имеет низкое поверхностное натяжении и поэтому хорошо смачивает графитовую футеровку электролизёра и анод. Он способен проникать даже под слой металлического алюминия.
Добавки AlF3, MgF2 и CaF2 снижают поверхностное натяжение электролита и на границе расплавалюминий, а Al2O3 и NaF повышают.
4.4 Напряжение разложения компонентов криолитно-глинозёмного расплава Под напряжением разложения электролита понимают напряжение между электродами, при котором с заметной скоростью начинается электролиз. Напряжение разложения определяет расход электрической энергии при электролизе.
Конечным результатом электролиза является разложение глинозёма на металлический алюминий и кислород:
Al2O3 = 2Al + 3,5O2 (38)
Величина напряжения разложения глинозёма зависит от материала анода. Если анод является инертным, когда кислород с ним не взаимодействует, то величина напряжение разложения определяется изменением энергии Гиббса реакции образования Al2O3 из элементов:
Uн.р. = - = - = 2,72 В (39)
где ?Gизменение энергии Гиббса образования A;
z = 6 — число электронов участвующих в реакции;
F = 96 500 — число Фарадея, Кл.
— 1576· 103 — изменение энергии Гиббса при температуре 298 К, Дж.
В качестве анода при электролизе алюминия используется углерод, который взаимодействует с выделяющимся на аноде кислородом по реакциям:
С + 0,5О2 = СО (40)
и С + О2 = СО2 (41)
В результате разложение глинозёма протекает по химическим реакциям, протекающим в электролизёре в процессе электролиза:
Al2O3 + 3C = 2Al + 3CO (42)
2Al2O3 + 3C = 4Al + 3CO2 (43)
Тогда напряжение разложения глинозёма будет определяться изменением энергии Гиббса реакций (5.42) и (5.43). Протекание вторичных реакций на аноде, связанных с образованием СО и СО2, связано с выделением энергии. Это служит причиной деполяризации анода, от которой снижается напряжение разложения глинозёма. По термодинамическим расчётам без учёта деполяризации зависимость напряжения разложения глинозёма от температуры выражается уравнением:
Uн.р. = 2,226 — 4,65· 10−4(Т-1000) (44)
где Uн.р. — напряжение разложения глинозёма, В.
При температуре 1000оС напряжение разложения составляет 2,131 В.
При электролизе с угольными анодами с учётом деполяризации напряжение разложения глинозёма при 1000оС составляет 0,948 В при окислении углерода анода полностью до СО и 1,048 В при окислении углерода анода полностью до СО2. Таким образом, по расчётам анодная деполяризация составляет порядка 1,083−1,183 В. Фактическая деполяризация анода в процессе электролиза примерно в два раза ниже. Это означает, что окисление углерода на аноде протекает по более сложному механизму, чем принятому при расчётах.
Величины разложения других составляющих криолитно-глинозёмного расплава при температуре 1000оС имеют следующие величины, B: NaF — 4,55, AlF3 -3,68, CaF2 — 5,28, MgF2- 4,63.
Напряхение на ванне в процессе электролиза поддерживается в пределах 4,5−5,0 В. Поэтому в условиях электролиза криолитно-глинозёмных расплавов будет разлагаться только глинозём, поскольку он обладает наименьшим напряжением разложения. Другие составляющие расплава разложению подвергаться не будут.
Часто для решения практических задач в электрохимии ионных расплавов используется понятие «тепловое напряжение разложения», которое определяется по уравнению:
Uн.р. = - (45)
4.5. Катодный и анодный процессы Криолитно-глинозёмный расплав имеет сложное строение. Изучение физико-химических свойств расплава позволило сделать определённые заключения о механизме процесса электролиза.
Составляющие криолитно-глинозёмного расплава диссоциируют по уравнениям:
Na3AlF6 = 3Na+ + AlF (46)
AlF = AlF + 2 °F (47)
Al2O3 = 2Al3+ + 3O2 (48)
Эти ионы частично взаимодействуют между собой с образованием более или менее устойчивых ионов AlO и AlO+, которые находятся в равновесии с простыми ионами:
AlO = Al3+ + 2O2 (49)
AlO+ = Al3+ + O2 (50)
Присутствующие в расплаве соли NaF, CaF2, MgF2 при диссоциации дают также ионы Na+, Ca2+ и Mg2+.
Таким образом, в криолитно-глинозёмном расплаве в переносе электричества участвуют ионы Al3+, Na+, Ca2+, Mg2+, AlF, F-, AlO, AlO+, O2-.
Однако на электродах будут разряжаться ионы, обладающие наиболее положительными (катионы) и наиболее отрицательным (анионы) потенциалами разряда. К таковым относятся ионы Al3+ и O2-.
Вследствие этого на катоде будет протекать электродная реакция:
2Al3+ + 6e = 2Al (51)
На аноде будет протекать процесс разряда ионов кислорода. Образующийся газообразный кислород будет реагировать с углеродом графитового анода с образованием оксидов СО и СО2:
2О2- - 4е +С = СО2 (52)
О2- - 2е + С = СО (53)
Тогда в электролизёре будет протекать химическая реакция:
Al2O3 + 2C = 2Al + CO + CO2 (54)
Можно считать на электродах и в электролизёре протекают параллельные реакции.
На катоде
4Аl3+ +12e = 4Al (55)
на аноде
6О2- - 12е = 3О2 (56)
3О2 + 3С = 3СО2 (57)
и в электролизёре
2Al2O3 +3C = 4Al + 3CO2 (58)
И на катоде
2Аl3+ +6e = 2Al (59)
на аноде
3О2- - 6е = 1.5О2 (60)
и в электролите
Al2O3 +3C = 2Al + 3CO (61)
Следовательно, в процессе электролиза из всех компонентов расплава будет расходоваться только глинозём. Разряд других ионов возможен только при нарушении технологии процесса электролиза.
Взаимодействие выделяющегося на угольном аноде кислорода с углеродом будет приводить к сгоранию анода и его расходу в процессе электролиза.
4.6 Анодный эффект При электролизе ионных расплавов с использованием графитовых и металлических электродов может возникнуть явление, получившее название анодного эффекта или вспышки. Это явление характеризуется следующими признаками:
1) Напряжение на ванне резко возрастает с 4,5- 5,0 В до 30−40, а иногда до 120 В.
2) Между катодом и анодом в электролите появляется световая полоса, характеризующаяся жёлтым или фиолетовым цветом и состоящая из мельчайших искр.
3) На аноде прекращается образование пузырьков газ.
4) Мениск электролита в электролизёре становится из вогнутого выпуклым.
5) На границе расплава с анодом возникает тонкая газовая плёнка, и электролит оказывается как бы оттеснённым от поверхности анода.
Появление анодного эффекта характеризуется критической плотностью тока. Выше этой плотности на аноде постоянно поддерживается состояние анодного эффекта.
Величина критической плотности тока зависит от состава криолитно-глинозёмного расплава и в первую очередь от содержания в нём глинозёма:
iкр. = А (62)
где iкр.- критическая плотность тока, А/см2;
РСодержание глинозёма в расплаве, %;
А — постоянная.
С увеличением концентрации глинозёма в электролите критическая плотность тока возрастает. Так при 1000оС эта зависимость характеризуется следующими величинами, приведёнными в таблице 1.
Таблица 1- Влияние содержания Al2O3 в расплаве на iкр.
%Al2O3 | 1,0 | 2.0 | 3.0 | 5.0 | 7.0 | |||
iкр, А/см2 | 0,43 | 2,02 | 3,08 | 4,44 | 7,5 | 8,9 | 10,5 | |
Критическая плотность тока зависит также от природы расплавленных солей, температуры и природы материала электродов.
Для расплавленных хлоридов критическая плотность тока выше, чем для фторидов. Для расплавов щелочных металлов она также выше, чем для расплавов щёлочно-земельных металлов.
С повышением температуры критическая плотность тока возрастает.
Для угольных электродов критическая плотность тока меньше, чем для металлических электродов.
Причиной возникновения анодного эффекта плохая смачиваемость анода расплавом. При плохой смачиваемости выделяющиеся на аноде пузырьки газа сливаются в сплошную плёнку, которая оттесняет расплав от поверхности электрода (Рисунок 10).
1- выделение пузырьков газа на аноде при нормальном ходе электролиза; 2-образование газовой пленки, вызывающей анодный эффект Рисунок 10 Образование газовой плёнки на угольном аноде при анодном эффекте В свою очередь, смачиваемость анода электролитом определяется величиной поверхностного натяжения. Чем больше поверхностное натяжение электролита, тем больше угол смачивания, тем хуже поверхность электрода смачивается электролитом, тем ниже критическая плотность тока. Поэтому все факторы, снижающие поверхностное натяжение электролита, способствуют хорошему смачиванию поверхности электрода и повышению критической плотности тока.
Анодный эффект является нежелательным явлением, как повышает расход энергии из-за скачка потенциала, снижает производительность электролизёра из-за понижения силы тока, вызывает перегрев ванны, и способствует снижению выхода по току для алюминия.
Для ликвидации анодного эффекта наиболее эффективным является повышение концентрации глинозёма в расплаве, что достигается загрузкой новой порции глинозёма в электролит.
4.7 Влияние различных факторов на выход по току Выход по току при электролитическом получении алюминия колеблется в пределах 80−90%. На выход по току влияет ряд факторов.
С повышением температуры выход по току сначала увеличивается и по достижения максимального значения уменьшается. Максимальное значение выхода по току достигается при оптимальной температуре, которая составляет порядка 950оС. Снижение температуры от этого значения приводит к возрастанию вязкости расплава, вследствие чего корольки металла запутываются в электролите и не успевают опуститься на дно ванны до выгрузки металла. Повышение температуры сверх 950оС приводит к интенсивному взаимодействию алюминия с расплавом сообразованием субсоединения AlF:
2Al + AlF3 = 3AlF (63)
Кроме того, увеличивается скорость взаимодействия металлического алюминия с кислородом и углекислым газом воздуха:
4Al + 3O2 = 2Al2O3 (64)
2Al + CO2 = Al2O3 + CO (65)
Протекание этих реакций приводят к потере алюминия, что снижает выход по току.
На выход по току влияет плотность тока. В алюминиевой ванне различают анодную iа, катодную iк и среднюю iср плотности тока, связь между которыми определяется уравнением:
icр. = (66)
С увеличением средней плотности тока выход по току алюминия увеличивается. Повышение плотности тока сопровождается увеличением напряжения на ванне. Чрезмерное увеличение плотности тока может привести к разряду ионов натрия на катоде, что будет приводить к снижению выхода по току.
На выход по току оказывает влияние расстояние между электродамимежполюсное расстояние. Увеличение межполюсного расстояния с одной стороны способствует увеличению выхода поток, так в этом случае затрудняется перенос металлического алюминия к аноду, где он снова может окислитсья. С другой стороны увеличение межполюсного расстояния приводит к увеличению оммического падения напряжения в электролите, что связано с дополнительным расходом энергии. Поэтому при конструкции электролизёра выбирается оптимальное межполюсное расстояние, которое обычно составляет 7- 9 см.
На выход по току влияет криолитное отношение в расплаве. При увеличении криолитного отношения выход по току сначала увеличивается и по достижении некоторого максимального значения начинает уменьшаться. Максимальный выход по току наблюдается при значениях криолитного отношения в пределах 2,5−2,7. Снижение криолитного одношения ниже этого предела приводит к снижению электропроводности расплава, а, следовательно, к непроизводительным потерям электрической энергии и к снижению выхода по току. Увеличение криолитного отношения может привести к разряду на катоде ионов натрия совместно с ионами алюминия. Это также приведёт к снижению выхода по току.
4.8 Устройство и работа электролизёра для получения алюминия Ванны, применяемые для электролитического получения алюминия, бывают двух типов: с прессованными обожжёнными анодами и с непрерывными самообжигающимися анодами. В настоящее время получение алюминия осуществляется в основном в ваннах с непрерывными самообжигающимися анодами. Устройство ванны с верхним подводом токаи самообжигающимися анодами приведено на рисунке 12.
1-токоподводящие шины; 2-анод; 3-токоподводы к электродам; 4-глинлзём; 5-корка застывшего электролита; 6-кожух; 7-шамоьная футеровка; 8-боковые угольные плиты; 9-катодные угольные блоки Рисунок 12 Устройство ванны с верхним подводом тока Для изготовления электролизёров используются угольные прямоугольные блоки и плиты. Катодом служит подина, которую выкладывают из угольных блоков. В качестве анодов используется угольные электроды, которые изготовляются из анодной массы. Приготовление анодной массы осуществляется по особой технологии. Стены электролизёра выкладываются из угольных плит. Снаружи стены укреплены кирпичной кладкой и шамотной засыпкой и для прочности заключены в стальной кожух с рёбрами жёсткости. В катодных блоках сделаны канавки, в которые закладывают стальные стержни и заливают чугуном. К этим стержням крепятся шины, подводящие электрический ток.
Над ванной на конструкции из стальных балок подвешен анод в кожухе из листового алюминия. В кожух загружают анодную массу. По мере опускания электрода в электролизёр анодная масса нагревается, плавится, затем густеет и затвердевает. Нижние слои массы, погружённые в электролит, спекаются и образуют «твёрдый конус спекания». По мере сгорания анод постепенно опускают с помощью специального механизма. Алюминиевый кожух в электролите расплавляется. Сверху в кожух периодически загружают свежую анодную массу. Алюминиевый кожух можно заменить неподвижным стальным, в котором спечённая часть анода опускается, скользя по стенкам стального кожуха. Ток к аноду подводится вбитыми в анод стальными штырями, концы которых образуют по высоте в анодной массе четыре ряда. По мере сгорания анода, штыри, образующие нижний ряд выдёргивают из анода и снова забивают выше следующего ряда.
Ванна имеет раздвижные или подъёмные боковые железные шторки, позволяющие отсасывать вредные анодные газы.
Алюминий, выделяющийся в процессе электролиза, имеет большую плотность, чем электролит, и накаливается на подине электролизёра. Извлечение жидкого алюминия из ванны осуществляется один раз в 2−3 суток. При выгрузке алюминия на дне подины оставляют слой металла, который предохраняет подину от разрушения и заполняет все неровности, что облегчает регулировку анодов. Кроме того, он способствует выравниванию температуры расплава. Извлечение алюминия осуществляется вакуумным ковшом. Вакуумный ковш представляет собой литейный ковш, снабжённый плотно пригнанной крышкой, через которую пропущена коленчатая труба. Другой конец трубы опускают в расплавленный алюминий на подине ванны. В ковше создают разрежение, и металл по трубе засасывается внутрь ковша.
4.9 Рафинирование алюминия и разливка алюминия Извлекаемый из ванн алюминий содержит ряд примесей, которые ухудшают его качество. Примеси, содержащиеся в элетролитическом алюминии можно разбить на три группы: неметалличесие (элeктролит, глинозём, карбид алюминия, угольные частицы); металлические (Fe, Ti, Si, Na и Ca); газообразные — в основном водород. Поэтому алюминий подвергается рафинированию. От неметаллических и газообразных примесей, а также от натрия и кальция алюминий рафинируют либо продувкой расплавленного металла хлором, либо переплавкой. Хлорирование проводят в особом ковше, выложенном внутри огнеупорным кирпичом.
В ковш заливают жидкий алюминий, ставят под колпак, опускают в него графитовую трубу, через которую вдувают в расплавленный металл газообразный хлор. Во время хлорирования в ковше поддерживается температура порядка 750оС. По степени убывания сродства к хлору металлы могут быть выстроены в ряд: Ca, Na, Mg, Al, Mn, Zn, Si, Fe, Ni. Cu. Поэтому в присутствии алюминия хлорированию подвергаются только Ca, Mg и Na. Поэтому из металлических примесей хлорированием удаляются только Ca и Na. Хлориды этих металлов всплывают на поверхность. Остальные металлы остаются в расплаве. При продувке хлором хлорируется небольшое количество алюминия:
2Al + 3Cl2 = 2AlCl3 (67)
Температура кипения хлорида алюминия составляет 180 оС, поэтому он образуется в газообразном состоянии. Пузырьки хлорида всплывают в металле и выносят за собой неметалличесие включения и растворённые газы. Очищенные таким образом несколько выпусков металла заливают в электрическую печь, где происходит отстаивание и усреднение состава металлов различных выпусков. В электрической печи металл нагревается до температуры 670- 730оС. Чрез 7−10 суток отстаивания металл разливают, а ванну тщательно очищают от шлака и оксидов. В печи происходит некоторая дополнительная очистка металла. Угар металла в печи составляет 1,5−2,0%.
Очищенный металл разливается конвейерными разливочными машинами длиной 9−10м. Чтобы металл быстрее застывал в изложницах, их обдувают воздухом. Чушки алюминия отправляются потребителю.
Металл разливают также в слитки особой формы, которые называют вайербарсами. Вайербарсы используются для изготовления алюминиевой проволоки. Рафинированный алюминий содержит 99,0- 99,85% Al.
1. Григорьев В. М. Повышение качества сплавов при использовании рудного сырья Дальнего Востока / Монография. — Хабаровск: Изд-во ДВГУПС, 2009. — 347 с.
2. Буряк В. А. Новый геолого-промышленный тип циркониевого оруденения (условия образования, перспективные использования) / В. А. Буряк, В. Я. Беспалов, В. Н. Гагаев, Б. А. Зарубин, В. Б. Троян. — Хабаровск: Изд-во ДВИМС, 1999. — 216 с.
3. Пат. 2 201 991 РФ, ПМК7 С 22 С33/04, 35/00. Способ получения циркониевой лигатуры / В. М. Григорьев, Т. В. Белаус; заявитель и патентообладатель Хабаровский государственный технический университет. 2 001 104 262/02; заявл. 13.02.2001; опубл. 10.04.2003. — Бюл. № 10. — 4 с.
4. Пат. 2 184 791 РФ, ПМК7 С 22, С 35/00. Лигатура / В. М. Григорьев, Т. В. Белаус; заявитель и патентообладатель Хабаровский государственный технический университет. — 2 001 103 397/02; заявл. 05.02.2001; опубл. 10.07.2002. — Бюл. № 19. — 5 с.
5. Григорьев В. М. Особенности формирования структуры кокильных отливок при обработке чугуна цирконийсодержащими присадками / В. М. Григорьев, Т. В. Белоус, Е. М. Баранов // Литейное производство. 2004. № 2. С. 9−13.
6. Давыдов С. В., Панов А. Г. Тенденции развития модификаторов для чугуна и стали // Заготовительные производства в машиностроении. -2007. № 1. — С. 3−11.
7. Чугун: Справочник / Под ред. А. Д. Шермана и А. А. Жукова. — М.: Металлургия, 1991. — 576 с.
8. Панов А. Г., Корниенко А. Э., Корниенко А. Э., Совершенствование технологии модифицирования чугунов с шаровидным графитом Mg-Ni-Fe лигатурой // М: Литейщик России, 2009, № 3. — с. 27−30.
9. Панов А. Г., Давыдов С. В. Исследование влияния микроструктуры литых Ni-Mg-Fe лигатур на их ударную вязкость // Заготовительные производства в машиностроении. 2010. — № 2. — С. 3−8.
10. Панов А. Г., Конашков В. В., Цепелев В. С., Гуртовой Д. А., Корниенко А. Э. Исследование структурообразования расплавов чугунов // М: Литейщик России, 2010, № 3. — С. 32−38.
11. Б. А. Баум, Г. А. Хасин, Г. В. Тягунов и др. Жидкая сталь. — М.: Металлургия, 1984. — 208 с.
12. Афанасьев В. К. О воздействии термоциклической деформации и последующей термообработки на свойства малоуглеродистой стали / В. К. Афанасьев, А. А. Столбов, А. А. Золотовский и др. // Известия ВУЗов. Черная металлургия. — № 2. — 1994. — С. 37−39.
13. Афанасьев В. К. Влияние обработки расплава на линейное расширение чугуна / В. К. Афанасьев, О. В. Исаенко, М. М. Сагалакова и др. // Литейное производство. — 2001. — № 9. — С. 8−9.
14. А.с. 1 470 780 МПК С21Д 5/02. Способ термической обработки конструкционной стали / В. К. Афанасьев, И. А Сушкова, М. В. Афанасьева и др.
15. Афанасьев В. К. Об аномалии теплового расширения железа и стали / В. К. Афанасьев, С. В. Долгова, А. А. Копытько и др. // Металлургия машиностроения. — № 5. — 2009. — С. 15−18.
16. Курочкин К. Т. Влияние водорода и азота на электротехнические свойства трансформаторной стали / К. Т. Курочкин, П. В. Умрихин, Б. А. Баум // Известия ВУЗов. Черная металлургия. — 1958. — № 2. — С. 143−150.
17. Афанасьев В. К. Особенности влияния нагрева на газосодержание и механические свойства высокочистого железа / В. К. Афанасьев, С. В. Долгова, Н. Б. Лаврова и др. // Металлургия машиностроения. — № 6. — 2009. — С. 12−15.
.ur