Исследование установки «Аминовой очистки» природного газа и изучение физико–химических свойств растворов
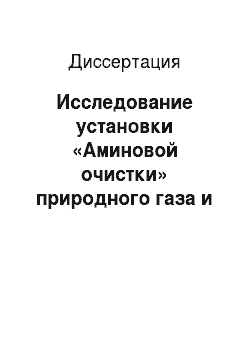
Рассматривая технологические особенности процессов очистки газов, необходимо отметить, что выбор способа очистки сводится, как правило, к выбору абсорбента, который при соответствующем конструктивном и технологическом оформлении процесса обеспечивает производство товарного газа и сопутствующих продуктов (серы и др.) при высоких технико-экономических показателях. Ниже перечислены процессы очистки… Читать ещё >
Исследование установки «Аминовой очистки» природного газа и изучение физико–химических свойств растворов (реферат, курсовая, диплом, контрольная)
[Введите текст]
МИНИСТЕРСТВО ВЫСШЕГО И СРЕДНЕГО СПЕЦИАЛЬНОГО ОБРАЗОВАНИЯ РЕСПУБЛИКИ УЗБЕКИСТАН БУХАРСКИЙ ИНЖЕНЕРНО-ТЕХНОЛОГИЧЕСКИХ ИНСТИТУТ На правах рукописи УДК 665.66
Хайдаров Латифжон Рустамович
5А522 504 — «Переработка нефти и газа и её химическая технология»
Исследование установки «Аминовой очистки» природного газа и изучение физико-химических свойств растворов.
Магистерская диссертации на соискание академической степени магистра Научный руководитель: к.т.н., Сафаров Б.Ж.
Бухара — 2013
Аннотация
Ушбу магистрлик диссертация газларни водород сульфидидан тозалашда ?ўлланиладиган алканоаминларни физик-кимёвий хоссаларига, ?амда улар ёрдамида табиий углеводород газларни тозалаш технологиясининг му? им илмий-техникавий масалаларини ечиш ва газларни дастлабки бирламчи ишлов бериш саноатидаги? урилма жи? озларини лойи? алаш масалаларига? аратилган. Бунинг учун мувозанат фаза, «табиий газметилдиэтаноламин-сув» системасида олинган моддалар бўйича мукаммал та? лил ?илинди. Аминлар ёрдамида тозалашнинг физик-кимёвий аспектлари ва регенерация жараёнига таъсир этувчи омиллар, ўт?азилган назарий изланишлар ва тад? и?отлар натижасида ўрганилди.
Аннотация
Работа посвящён, физико-химическим аспектам применения алканоаминов для очистки углеводородных газов, принципиально важным для решения научно-технических задач при эксплуатации, проектировании и реконструкции промысловых установок аминовых очистки природного газа. Проанализировано о систематизации имеющихся данных по фазовым равновесиям в системе «природный газ-алканоамин-вода». Проведена, теоретических и экспериментальных исследований различных физико-химических аспектов аминовой очистки газа, в том числе влияющие факторов процессе регенерации абсорбента.
Annatasion
Work is dedicated to, physico-chemical aspect of the using alcanoamino for peelings hydrocarbon gas, in principal important for decision of the research problems at usages, designing and reconstructions of the commercial installation aminopeelings of the natural gas. It is analysed about systematizations available given on phase balance in system «natural gasamino-water». It is organized, theoretical and experimental studies different physico-chemical aspect amino peelings of the gas, including affecting factor process to regenerations of the absorbent.
Введение
Глава 1. Литературный обзор
1.1 Общая техническая характеристика углеводородных газов
1.2 Очистка газа от сероводорода, диоксида углерода
1.3 Очистка газа алканоаминовыми растворителями
1.4 Очистка газа физическими и комбинированными растворителями Глава 2. Анализ и методика исследование
2.1 Физико-химических свойства этаноламинов и их водных растворов
2.2 Механизм поглощения H2S, CO2 и других серныстых компонентов водными растворами аминов
2.3 Растворимость H2S и CO2 в водных растворах этаноламинов
2.4 Растворимость углеводородов в водных растворах этаноламинов
2.5 Растворимость меркаптанов в водных растворах этаноламинов
2.6 Растворимость сероокиси углерода в водных растворах этаноламинов
2.7 Растворимость сероводорда, диоксида углерода, сероокиси углерода, меркаптанов и углеродов в водно-неводных растворах алканаминов Глава 3. Экспериментальная часть
3.1 Технология и изучение процесса очистки углеводородного газа на опытной установке ГПЗ Учкыр
3.2 Очиска газа высококонцентрированными растворами диэтано-ламина
3.3 Коррозионные свойства алканоаминов
3.4 Вспениваниемрастворов алканоаминов
3.5 Расчет основных узлов и параметров установок очистки газа
3.6 Выбор растворителя для очистки газа от сероводорода
3.7 Анализ газовых смесей на учебном газоадсорбционном хроматографе Заключение Список использованной литературы
Особенностью развития мирового топливно-энергитического комплекса в настоящее время является увеличение в его структуре доли природного газа. Природный газ остается самой быстро растущей составляющей в мировом потреблении энергии. По прогнозу 1ЕО 2000 в период до 2020 года потребление газа более чем удвоится.
Газовая отрасль Республики имеет четко выраженный региональный центр Мубарекском, Шуртанском Газлинский СОУ. Здесь находятся основные разведанные перспективные запасы Республики.
Газовые конденсаты Газлинском отличаются легким фракционным составом, высоким содержанием бензиновых фракций, практическим отсутствием смолисто-асфальтовых соединений и металлов, очень низким содержанием серы. Кроме того, в связи с высоким содержанием нафтеновых углеводородов они имеют низкую температуру застывания. Поэтому газовые конденсаты Газлинском, являются прекрасным нефтехимическим сырьем и сырьем для производства моторных топлив. Широкая фракция легких углеводородов, выделяемая из конденсата, имеет высокое содержание наиболее ценных для нефтехимических процессов компонентов-изобутана и изопентана. Прямогонная бензиновая фракция является прекрасным сырьем для пиролиза и для получения высокооктанового бензина. Такое уникальное по качеству углеводородное сырье требует более подробного исследования его состава, совершенствования технологии и аппаратурного оформления, направленных на повышение качества получаемых продуктов, разработки технологий, позволяющих производить новые товарные продукты.
Актуальность работы. Работа посвящён, физико-химическим аспектам аминной очистки углеводородного газа, которые принципиально важным для решения научно-технических задач при эксплуатации, проектировании и реконструкции промысловых установок абсорбционого очистки природного газа. Выполнены анализ и систематизация имеющихся данных по фазовым равновесиям в системе «природный газ-МЭА-ДЭА-МДЭА». Проанализированы причины деструкции растворителей и экспериментально изучена возможность снижения температуры регенерации поглотителей.
Цель работы. Изучение методику для термодинамических расчетов фазового равновесия при аминовой очистки газа и регенерации абсорбентов. Исследование состава и физико-химических свойств исходного сырья и его фракций как одного из важнейших факторов, влияющих на технологический процесс и на качество получаемых продуктов.
Научная новизна. Изучение процесса очистки газа с абсорбентами и при регенерации целесообразно проводить в условиях, приближенных к условиям работы промысловых установок регенерации поглотителя. При этом продукты деструкции гликоля должны определяться не только в самом МДЭА, но и в водном отгоне. С учетом этих моментов нами создана специализированная опытная установка регенерации абсорбента, которая в принципиальном отношении позволяет моделировать большинство особенностей промысловых установок регенерации абсорбентом.
Практическая ценность. Рассмотрено технологические особенности процессов очистки углеводородных газов технологическом оформлении процесса, обеспечивающего производство товарного газа и сопутствующих продуктов (серы и др.) при высоких технико-экономических показателях. В данное работе перечислены анологичные методы процессы очистки газов от сероводорода, С02, RSH и других «нежелательных» соединений, основанных на химической и физической абсорбциях.
Проведен, теоретических и экспериментальных исследований различных физико-химических аспектов аминовой очистки газа, принципиально важных для решения научно-технических задач, возникающих при эксплуатации, проектировании и реконструкции промысловых установок природного газа.
Cтруктура и объём магистерской диссертации.
Магистерская работа состоит из введения, трёх глав, списка цитированной литературы и приложений. Она изложена на 84 страницах текста, проиллюстрирована 21 рисунками и 9 таблицам.
Глава 1. Литературный обзор.
1.1 Общая техническая характеристика углеводородных газов
Нефтяные и природные газы, добываемые из недр земли, представляют собой смесь углеводородов метанового ряда-метана, этана, пропана, бутанов и других. В некоторых газах наряду с углеводородами могут содержаться гелий, азот, диоксид углерода, сероводород и другие неуглеводородные компоненты. Число и содержание их изменяются в широких пределах. В общем объеме добываемого газа большая часть приходится на метан, который используют в основном как котельно-печное топливо. Ресурсов этана, пропана, бутанов и более тяжелых углеводородов-сырьевой основы промышленности органического синтеза-значительно меньше, чем метана. Поэтому в нашей Республики и других странах большое значение придается рациональному использованию этих углеводородов.
Нефтяные и природные газы являются основными источниками получения одного из важнейших и перспективных видов химического и нефтехимического сырья — этана, из которого в Республике вырабатывают около 40% этилена, необходимого для производства пластических масс, оксида этилена, поверхностно-активных веществ и многих других химических продуктов и полупродуктов (по объему производства и структуре потребления этилена определяют уровень развития промышленности органического синтеза). В США в связи с высокой эффективностью этого сырья производство этана увеличивалось в конце 60-х годов на 24−31%. Впоследствии ежегодный прирост составлял от 5 до 25% [1−3]. В США и Канаде для транспортирования этана построены крупные трубопроводные системы. В 1977 г., например, было завершено строительство трубопровода протяженностью около 3 тыс. км, предназначенного для транспортирования этана, этилена, пропана и бутанов из западных районов Канады на восток страны и далее в США (производительность трубопровода 2,2−2,4 млн. т/г, рабочее давление 10 МПа) [4−5].
В Западной Европе после открытия крупных месторождений природного газа повысился интерес к легкому пиролизному сырью, поскольку из этана можно вырабатывать до 25% этилена. Повышенный интерес к этому сырью объясняется тем, что использование этана в химической и нефтехимической промышленности позволяет улучшить структуру пиролизного сырья и обеспечить высокую сбалансированность производства и потребления этилена с одной стороны, бутадиена и других побочных продуктов пиролиза бензина, с другой стороны.
Использование этана позволяет существенно уменьшить капитальные вложения в производство этилена и сократить сроки строительства химических и нефтехимических производств с законченным технологическим циклом (этилен — полиэтилен, этилен — этиловый спирт и т. д.), так как при пиролизе этана обеспечивается минимальный выход побочных продуктов, для утилизации которых требуются большие капитальные вложения (выход этилена из этана 70%, из бензина 27%, из вакуумного газойля 15%).
Если этиленовые производства ориентировать только на бензин, то соотношение ресурсов этилена и пропилена составит примерно 1: 0,5. А это значит, что для сбалансированного развития необходимо строго соблюдать такое же соотношение при наращивании мощностей по переработке этилена и пропилена. Такая синхронизация не всегда оказывается возможной. Особенно большие трудности в реализации сбалансированного развития возникают при строительстве этиленовых установок большой единичной мощности.
В ближайшие годы по мере углубления переработки нефти это соотношение будет уменьшаться в связи с увеличением ресурсов пропилена на нефтеперерабатывающих заводах (по содержанию пропилена составы газов пиролиза бензина и каталитического крекинга тяжелых нефтяных фракций примерно равноценны). Следовательно, в этих условиях при сохранении темпов развития этиленпотребляющих производств и отсутствии возможности (или необходимости) увеличения темпов развития пропиленпотребляющих производств пропилен каталитического крекинга будет использоваться в качестве топлива, а пиролизный пропилен, полученный из бензина, — для производства химической продукции. Такое положение вряд ли может быть признано целесообразным при дефиците прямогонных нефтяных фракций и наличии больших ресурсов этана. Поэтому в США, например, около 7 млн. т этилена получают из этана при общем объеме производства этого мономера 18 млн. т в 1980 г. (1 т этана заменяет примерно 2 т бензина).
При отсутствии этана аналогичное положение с использованием ресурсов пропилена может сложиться и при увеличении темпов прироста производства этилена, которое может быть обусловлено ускоренным развитием производства изделий из полиэтилена (труб и др.) и необходимостью организации крупнотоннажного производства кормового белка из синтетического этилового спирта методом микробиологического синтеза. В перспективе этан может превратиться в ряде случаев из альтернативного в основное углеводородное сырье ведутся разработки синтеза винилхлорида, ацетальдегида, этилового спирта и других продуктов непосредственно из этана, минуя дорогостоящую стадию производства этилена. Таким образом, этанэто весьма ценное и высокоэффективное химическое и нефтехимическое сырье.
Для рационального использования углеводородного сырья нефтяной и природный газ с повышенным содержанием этана целесообразно транспортировать в районы потребления так, чтобы по мере необходимости этот газ можно было использовать для производства этана. Транспортная схема должна обеспечивать возможность подачи этансодержащего газа до определенных пунктов в чистом виде без смешения с метановым газом. Дополнительные капитальные вложения, которые могут потребоваться при раздельном транспортировании метанового и этансодержащего газов, окупятся, так как в этом случае можно будет получить дополнительные ресурсы этана и использовать их для производства этилена вместо дорогостоящих углеводородных фракций — продуктов переработки мазута и угля (затраты на производство 3−4 млн. т в год бензиновых фракций из угля соизмеримы с капитальными затратами, необходимыми для строительства крупных газопроводов). В связи с высокой эффективностью газового сырья может оказаться целесообразным извлекать этан из природных и нефтяных газов и закачивать в одно или несколько газовых или газоконденсатных месторождений, которые в связи с истощением собственных запасов газа могут быть использованы в качестве подземных хранилищ. При наличии такой системы появятся дополнительные возможности для более гибкого использования минерально-сырьевых ресурсов нефтяных, газовых и газоконденсатных месторождений (в этансодержащих природных газах на долю этана приходится около 55% от всех потенциальных запасов углеводородов — от этана до бутанов включительно).
На ГПЗ из нефтяных и природных газов получают большое количество пропана в США около 65% пропана вырабатывают на газопере-рабатывающих заводах. В чистом виде или в смеси с бутаном пропан используют в качестве нефтехимического (пиро-лизного) сырья, коммунально-бытового и моторного топлива, для огневой культивации почвы, сушки сельскохозяйственной продукции и других целей. Кроме этана и пропана, из нефтяных и природных газов извлекают «бутан, изобутан, «-пентан и изопентан, которые используют для производства синтетического каучука, коммунально-бытового и моторного топлива.
Высокая эффективность использования этана, пропана и других гомологов метана длительное время стимулирует развитие добычи и производства этого сырья в США, Канаде и других странах. практика показывает, что при наличии больших запасов природных и нефтяных газов на базе этого сырья могут быть организованы крупнотоннажные и высокорентабельные производства этана, сжиженных газов (пропана, бутанов) и других видов углеводородного сырья и моторного топлива. Объемы производства этой продукции могут быть соизмеримы с ресурсами сырья и моторного топлива, получаемыми в результате углубления переработки нефти. Учитывая высокую эффективность газового сырья и повышенный интерес к нему на мировом рынке, многие нефтедобывающие страны осуществляют строительство, расширение и реконструкцию газоперерабатывающих заводов.
В ближайшие годы страны Ближнего Востока (Иран, Саудовская Аравия, Бахрейн и др.) предполагают завершить программу по сбору, переработке и транспортированию нефтяного газа общей стоимостью около 33 млрд долл. Считают, что это позволит экспортировать около 46 млн. т в год сжиженных нефтяных газов. Одним из элементов программы является строительство крупных мощностей по производству этилена, полиэтилена, стирола и другой нефтехимической продукции — Саудовская Аравия имеет в виду довести производство этой продукции до 8% мирового объема. В 1978 г. в капиталистических странах (без США) на строительство газоперерабатывающих заводов затрачено 3,2 млрд долл., что составляет около 50% к объему капитальных вложений в нефтеперерабатывающую промышленность.
В перспективе актуальность комплексного подхода к использованию ресурсов нефтяных и природных газов возрастет, так как увеличение производства моторных топлив и нефтехимического сырья будет обеспечиваться в основном за счет увеличения мощностей вторичных процессов переработки нефти (каталитического крекинга и др.) и ввода мощностей по переработке угля, для стооительства которых требуются большие капитальные вложения. Для организации производства 3−4 млн. т в год моторного топлива из угля необходимы примерно такие же капитальные вложения, какие требуются для обеспечения добычи 45 млрд. м3 в год природного газа и производства из этого сырья 5,5 млн. т этана, сжиженных газов и другой продукции. Поэтому в США, например, где имеются крупные запасы различных минеральносырьевых ресурсов, нефтяной и природный газ длительное время был и остается одним из основных источников производства легкого углеводородного сырья и других сырьевых продуктов.
Многие страны мира из-за отсутствия или ограниченных ресурсов зтана и сжиженных газов (пропана и др.) стоят перед проблемой перевода пиролизных агрегатов нефтехимических производств на переработку тяжелых нефтяных фракций. Это значительно увеличит капитальные вложения и может вызвать снижение темпов развития нефтехимической промышленности.
Природный и нефтяной газ-это не только топливо и сырье для производства этана, пропана и других гомологов метана. При очистке и переработке газа получают большие количества дешевой серы, гелия и других неорганических продуктов, необходимых для развития ряда отраслей народного хозяйства. Канада благодаря наличию крупных мощностей по переработке сероводородсодержащих природных газов занимает среди капиталистических стран второе место по производству серы. По производству гелия-одного из важнейших и перспективных продуктов — первое место занимают США. Структура потребления гелия характеризуется следующими данными (в % об.) [15]: ракетно-космическая техника — 19; контролируемые атмосферы — 12; искусственные дыхательные смеси — 6; исследования — 15; сварка в атмосфере инертного газа- 18; криогенная техника-6; теплопередача-7; хроматография-4; другие области-13. В перспективе гелий предполагают широко использовать в атомной энергетике, криогенной электротехнике и других областях.
Производство гелия в США осуществляется на 12 заводах. Объем производства — около 135 млн. м3 в год. Потребление гелия: в 1980 г.-35 млн. м3; в 1999 г. прогноз — 60 млн. м3. Согласно долгосрочной правительственной программе весь избыток получаемого на заводах гелия закачивается в специальные подземные хранилища с тем, чтобы в будущем, когда запасы гелиеносных природных и нефтяных газов истощатся, этот гелий можно было использовать. Такие мероприятия оправданы, так как получение гелия из воздуха — единственного альтернативного сырьевого источника — во много раз дороже. В связи с этим при обсуждении в Конгрессе США гелиевого закона в 1980 г. были внесены предложения об увеличении государственных запасов гелия с 1,1 млрд. м3 в 1980 г. до 2,4 млрд. м3 к концу 1990;х годов.
1.2 Очистка газа от сероводорода, диоксида углерода
Нефтяные и природные газы наряду с углеводородами могут содержать кислые газы-диоксид углерода (СОа) и сероводород (H2S), а также сероорганические соединениясерооксид углерода (COS), сероуглерод (CS2), меркаптаны (RSH), тиофены и другие примеси, которые осложняют при определенных условиях транспортирование и использование газов. При наличии диоксида углерода, сероводорода и меркаптанов создаются условия для возникновения коррозии металлов, эти соединения снижают эффективность каталитических процессов и отравляют катализаторы.
Сероводород, меркаптаны, серооксид углерода-высокотоксичные вещества. Повышенное содержание в газах диоксида углерода нежелательно, а иногда недопустимо еще и потому, что в этом случае уменьшается теплота сгорания газообразного топлива, снижается эффективность использования магистральных газопроводов из-за повышенного содержания в газе балласта. Если рассматривать этот вопрос с указанных позиций, то серои кислородсодержащие соединения можно отнести к разряду нежелательных компонентов. Однако такая постановка вопроса не исчерпывает всей полноты проблемы, так как кислые газы являются в частности высокоэффективным сырьем для производства серы и серной кислоты. Поэтому при выборе процессов очистки газов учитывают возможности достижения заданной глубины извлечения «нежелательных» компонентов и использования их для производства соответствующих товарных продуктов.
В Канаде, например, сера в зависимости от содержания в газе сероводорода рассматривается как основной, сопутствующий или побочный продукт, и в зависимости от этого распределяются затраты на очистку газа и производство серы, а также регламентируются условия разработки и эксплуатации некоторых месторождений [20−22]. Известны случаи, когда сероводород-содержащий природный газ добывают с целью производства серы, очищенный газ после извлечения сероводорода закачивают обратно в пласт для поддержания пластового давления. В ряде стран мира (США, Канаде, Франции) открытие крупных месторождений природного сероводород-содержащего газа положило начало широкому развитию в 50-х годах добычи и очистки такого газа и производству серы из этого сырья. В Канаде из сероводородсодержащего газа получено около 5,3 млн. т серы (по состоянию на начало 1978 г. доказанные запасы серы составляли 105 млн. т).
В нашей стране добыча и переработка сероводородсодержащего природного газа начала широко развиваться в 60-х годах после открытия крупных газоконденсатных месторождений в Средней Азии и Оренбургской области. В связи с этим объемы переработки такого сырья увеличились с 3,4 млрд. м3 в 1970 г. до 62,5 млрд. м3 в 1980 г., а производство серы — с 3,9 до 1450 тыс. т (удельные капитальные вложения и себестоимость газовой серы значительно ниже, чем при добыче самородной). В России прогнозные запасы сероводородсодержащего газа составляют около 12% всех прогнозных запасов природного газа. Можно полагать, что объемы переработки сероводородсодержащего газа и производства серы из этого сырья в нашей стране будут увеличиваться.
Содержание сероводорода и С02 в природных газах США, Канады, Франции, России и других стран колеблется в широких пределах. Как правило, во всех сероводородсодержащих газах имеется то или иное количество СОа (соотношение С02: H2S изменяется от 1: 20 до 70: 1). В то же время довольно часто природные газы могут быть с различным содержанием С02, но без сероводорода. Максимальное содержание сероводорода в природных газах России 23% об. (Астраханское газоконденсатное месторождение), в газах Канады-75% об. (месторождение Пантер-Ривер). Во многих природных газах наряду с сероводородом и диоксидом углерода содержатся сероорганические соединения, присутствие которых даже в небольших количествах крайне осложняет добычу, транспортирование и использование минеральных ресурсов газовых и газоконденсатных месторождений.
В газе Оренбургского газоконденсатного месторождения содержание сероорганических соединений достигает 1000−2000 мг/м3 (в пересчете на серу) при содержании сероводорода около 16 000 мг/м3 (1,8−2% об.). Это привело к необходимости строительства специальных объектов для очистки газа от сероорганических соединений — до ввода этих объектов в действие при использовании газа были серьезные трудности, несмотря на очистку его от сероводорода.
При выборе способов очистки газов необходимо внимательно подходить к оценке химического состава сырья, включая примеси, которые не регламентируются в товарном газе и продуктах его переработки или не оказывают влияния на их качество из-за незначительного содержания в исходном газе. Это обусловлено в частности тем, что при взаимодействии примесей с некоторыми растворителями могут образоваться такие химические соединения, которые при нагревании их в процессе регенерации не распадаются на составные части (реакция между ними необратима в условиях процесса), в результате чего концентрация активной части растворителя постепенно уменьшается (возрастает содержание балласта в системе), растворитель дезактивируется и приходит в негодность.
Практика показывает, что наличие незначительного на первый взгляд содержания примесей может оказать принципиальное влияние на выбор растворителя или процесса очистки газа. Важное значение при рассмотрении этого вопроса имеет соотношение H2S: С02 в исходном газе — концентрация сероводорода в кислых газах может оказаться определяющей при выборе процессов и технологии очистки исходного сырья и способов утилизации «нежелательных» компонентов. Это отношение может быть настолько низким, что для переработки кислых газов в элементарную серу использовать наиболее распространенный метод термокаталитического окисления сероводорода (процесс Клауса) будет невыгодно.
Специалисты фирмы Флюор Корпорейшен (Р. Н. Теннисон и др.) считают, что по методу Клауса можно перерабатывать кислые газы с содержанием сероводорода более 15% об. На многих установках Клауса содержание сероводорода в кислых газах достигает 50% об. и более (т. е. H2S: С02). При низком соотношении сероводорода и С02 в исходном газе для получения кислых газов с высоким содержанием сероводорода используют систему селективной очистки газа, при которой на первой ступени извлекают в основном сероводород и получают при этом хорошее сырье для производства серы, а на второй ступени извлекают С02 и оставшееся количество сероводорода [29−31].
Разработаны и применяются процессы селективного извлечения сероводорода, при котором H2S вступает в реакцию с растворителем и окисляется до серы кислородом воздуха в процессе регенерации растворителя (в этом случае в составе комплекса нет установок Клауса). По первому варианту, экономически выгодно очищать газ при большом парциальном давлении сероводорода на входе на установку, по второму варианту — при низком парциальном давлении.
В кислых газах, поступающих на установки Клауса, должно не только содержаться определенное количество сероводорода, но лимитируется также содержание углеводородов, которые могут поглощаться в различных количествах на стадии очистки газа от сероводорода и С02. Считают нормальным, когда содержание углеводородов не превышает 2−4% об. (на некоторых установках за счет ряда мероприятий содержание их удается уменьшить до 0,2−1% об.). Наличие углеводородов в кислых газах приводит к увеличению расхода воздуха (кислорода) на установках Клауса, ухудшению цвета серы, обуглероживанию и снижению активности катализатора.
В 0Ф0Р и других странах к качеству природного и нефтяного газа, поступающего в магистральные газопроводы, предъявляются высокие требования по содержанию сероводорода и меркаптановой серы: в нашей стране содержание сероводорода не должно превышать 22 мг/м3, меркаптановой серы — 36 мг/м3 газа (содержание СО2 не нормируется); в США содержание сероводорода регламентируется на уровне 5,7 мг/м3, содержание С02, общей серы и меркаптанов устанавливаются обычно газотранспортными компаниями в зависимости от требований потребителей (содержание С02−1-2% об., меркаптанов-1,5−5 мг/м3, общей серы — 22−28 мг/м3 и т. д.) [33−34].
Для очистки природных и нефтяных газов от сероводорода, СО2 и других серои кислородсодержащих «нежелательных» соединений используют в основном абсорбционные процессы, которые в зависимости от особенностей взаимодействия этих соединений с растворителями — абсорбентами можно условно объединить в следующие группы.
Хемосорбционные процессы очистки газа растворителями, представляющими собой водные растворы алканоламинов: моноэтаноламина (МЭА), диэтаноламина (ДЭА), дигликольамина (ДГА) и др. Они основаны на химической реакции «нежелательных» соединений с алканоламинами, являющимися активной, реакционной частью абсорбента. К этой же группе относят процессы поташной очистки.
Аминовые процессы обеспечивают тонкую очистку газов от сероводорода и С02 при различных рабочем давлении и концентрации их в исходном сырье; растворимость углеводородов в этих абсорбентах невелика. Технологическое и аппаратурное оформление процессов отличаются простотой и надежностью.
Основные недостатки процессов: не достигается комплексная очистка газов от H2S, С02, RSH, COS и CS2; низкая глубина извлечения меркаптанов и некоторых других сероорганических соединений; при взаимодействии меркаптанов, COS и CS2 с некоторыми растворителями образуются нерегенерируемые в условиях процесса химические соединения; для реализации процессов необходимы высокая кратность циркуляции абсорбента и большие теплоэнергетические затраты (с повышением концентрации «нежелательных» соединений они увеличиваются); абсорбенты и продукты взаимодействия их с примесями, содержащимися в сыром газе, нередко обладают повышенной коррозионной активностью.
С увеличением концентрации активного вещества и степени насыщения растворителя сероводородом и другими «нежелательными» соединениями возрастает коррозионная активность алканоламиновых абсорбентов. Поэтому поглотительная их способность часто лимитируется не условиями термодинамического равновесия, а предельно допустимой степенью насыщения абсорбентов’кислыми газами.
Процессы очистки газов методом физической абсорбции «нежелательных» соединений органическими растворителями: пропиленкарбонатом, диметиловым эфиром полиэтиленгликоля (ДМЭПЭГ), N-метилпирролидоном и др. Они основаны на физической абсорбции, а не на химической реакции, как хемосорбционные процессы.
Органические растворители можно в принципе использовать для комплексной очистки газов от сероводорода, С03, RSH, COS и CS2 при высоком парциальном давлении их в условиях абсорбции; эти абсорбенты, как правило, не пенятся и не корродируют аппаратуру и оборудование, многие из них имеют низкую температуру замерзания, что важно в случае применения процессов в холодных климатических условиях.
При высоком парциальном давлении «нежелательных» соединений для реализации процессов очистки газов органическими растворителями требуются, как правило, меньшие капитальные и эксплуатационные затраты, чем для реализации аминовых хемосорбционных процессов, так как поглотительная способность органических растворителей возрастает примерно пропорционально парциальному давлению кислых газов и других «нежелательных» соединений. Регенерация физических абсорбентов протекает во многих случаях без подвода тепла за счет снижения давления в системе.
Основные недостатки процессов: применяемые растворители относительно хорошо поглощают углеводороды; тонкая очистка газов обеспечивается в ряде случаев только после дополнительной доочистки их алканоламиновыми растворителями (т. е. грубая очистка производится, например, растворителем ДМЭПЭГ, а тонкая очистка — раствором моноэтаноламина).
Процессы очистки газов от «нежелательных» соединений растворителями, представляющими собой смесь водного алканоламинового раствора с органическими растворителями — сульфоланом, метанолом и др. Они основаны на физической абсорбции «нежелательных» соединений органическими растворителями и химическом взаимодействии с алканоламинами, являющимися активной реакционной частью абсорбента. Эти процессы сочетают в себе многие достоинства химической и физической абсорбции. Их можно использовать для тонкой комплексной очистки газов от сероводорода, С02, RSH, COS и CS2. (таблица-1).
Основные недостатки процессов: применяемые растворители относительно хорошо поглощают углеводороды (особенно хорошо растворяются ароматические углеводороды); это ограничивает область применения процессов второй и третьей групп, так как для предотвращения попадания больших количеств тяжелых углеводородов в сырье установок по производству серы (типа Клаус) в состав ГПЗ необходимо включать аппаратуру и оборудование для извлечения углеводородов из сырого исходного газа или из кислых газов перед поступлением их на установку по производству серы.
Однако это не всегда сопряжено с дополнительными капитальными и эксплуатационными расходами, так как во многих случаях тяжелые углеводороды извлекают из газа по соображениям, не связанным с выбором процесса очистки газа от сероводорода и других серои кислородсодержащих «нежелательных» соединений. Процессы физической Таблица 1 — Применяемые растворители для очистки природных и нефтяных (попутных) газов процессах физических и химических абсорбциях
Химическая абсорбция | Физическая абсорбция | |||
процесс | растворитель | процесс | растворитель | |
Алканоламиновая очистка | Моноэтаноламин | Флюор | Пропиленкарбонат | |
МЭА-очистка | Диэтаноламин | Селексол | Диметиловый эфир | |
полиэтиленгликоля | ||||
ДЭА-очистка | Диизопропанол; | Пуризол | ||
Адип | Амин | (ДМЭПЭГ), N-ме; | ||
тилпирролидон (NMP) | ||||
Эконамин | ||||
Дигликольамин | Сульфинол (процесс включен | Смесь водного раствора диизопропаноламина | ||
эту группу условно) | и сульфолана | |||
Метанол (при низких температурах) | ||||
Поташная очистка | Горячий раствор | Ректизол | ||
обычная | поташа (К2С03) | |||
Горячий раствор | ||||
Бенфилд (активиро; | ||||
ванная горячая) | поташа 1,8% | |||
ДЭА (активиро | ; | ; | ||
ванная добавка) | ||||
Горячий растворителей щелочных растворителей мышьяковых со | ||||
Ветрококк | ; | ; | ||
(K3As03 и др.) | ||||
Стретфорд | Раствор натрие | |||
вых солей (2,6; | ; | |||
2,7 антрахинон; | ; | |||
сульфоновых | ||||
кислот) | ||||
абсорбции могут оказаться более экономичными также и потому, что органические растворители обеспечивают селективное извлечение сероводорода в присутствии С02 и позволяют получить хорошее сырье для производства серы при неблагоприятном соотношении H2S: С02 в исходном сырье газа и для производства товарного диоксида углерода. Эти процессы имеют при определенных условиях ряд преимуществ, которые могут быть выявлены только на основе технико-экономического анализа условий добычи, очистки и переработки газа и сопутствующих продуктов.
Рассматривая технологические особенности процессов очистки газов, [38−40] необходимо отметить, что выбор способа очистки сводится, как правило, к выбору абсорбента, который при соответствующем конструктивном и технологическом оформлении процесса обеспечивает производство товарного газа и сопутствующих продуктов (серы и др.) при высоких технико-экономических показателях. Ниже перечислены процессы очистки газов от сероводорода, С02, RSH и других «нежелательных» соединений, основанных на химической и физической абсорбциях Основными критериями при выборе абсорбентов, а следовательно, и процессов являются начальное и конечное содержание извлекаемых «нежелательных» компонентов в газе и заданное рабочее давление в системе или начальное и конечное парциальное давление их в условиях очистки. Начальное давление предопределяет кратность циркуляции абсорбента (удельный его расход). Конечное парциальное давление (или глубина очистки газа) зависит в первую очередь от степени регенерации абсорбента и от равновесного давления извлекаемого газа над раствором от температуры. Капитальные и эксплуатационные затраты определяются главным образом кратностью циркуляции и условиями регенерации растворителя. Следовательно, экономика процесса предопределяется в основном парциальными давлениями извлекаемых «нежелательных» компонентов в сыром и очищенном газе. На основе этих данных можно оценить, какой из растворителей — химический или физический — наиболее приемлем для заданных условий. После этого, учитывая специфику содержащихся в газе примесей и возможные варианты взаимодействия их с растворителями данной конкретной группы, можно выбрать процесс, который целесообразно будет использовать для проведения технико-экономического исследования.
Все процессы, приведенные выше, за исключением процессов Ветрококк — H2S и Стретфорд, основаны на химической или физической абсорбции «нежелательных» серо-кислородсодержащих соединений и последующей десорбции их из абсорбента и направлении кислых сероводородсодержащих газов на установку по производству серы типа Клауса. Процессы Ветрококк — H2S и Стретфорд основаны на абсорбции сероводорода химическим растворителем и окислении его в регенераторе до серы за счет присутствия в абсорбенте соответствующих активных добавок и кислорода, который поступает в нижнюю часть регенератора вместе с воздухом (С02 в процессе Стретфорд практически не извлекается, его присутствие осложняет процесс). Процессы Ветрококк — H2S и Стретфорд чаще всего применяют для очистки газов с низким содержанием сероводорода, область применения их ограничивается парциальным давлением H2S в очищенном газе до 0,002 МПа и в исходном газе до 0,07 МПа (температура абсорбции 35−45 °С, в результате очистки обеспечивается высокая степень извлечения сероводорода). В России окислительно-восстановительные процессы Ветрококк — H2S и Стретфорд не нашли пока практического применения для очистки природных и нефтяных (попутных) газов от сероводорода. За рубежом эти процессы используют, как правило, на установках небольшой мощности. В США процесс Ветрококк не применяют из-за высокой токсичности растворителя.
1.3 Очистка газа алканоаминовыми растворителями
При низких и средних парциальных давлениях кислых газов поглотительная способность алканоламиновых абсорбентов возрастает по отношению к сероводороду и диоксиду углерода. В этой области химические абсорбенты могут конкурировать с физическими растворителями. Ниже приведены основные физико-химические свойства алканоламиновых растворителей [46−47].
Процесс взаимодействия С02 и H2S с моноэтаноламином описывается следующими суммарными реакциями:
[2RNH2 + H2S (RNH8)aS (RNH3)2 S + H2S2RNH3HS COaRNH2 + HaO (RNH3)a C03 C02 + (RNH3)a C03 + H20 +2RNHgHC03
где R — группа OHCH2CH2. При низкой температуре реакции протекают слева направо, при высокой — справа налево: в первом случае H2S и С02 «связываются» с абсорбентом, во втором — происходит регенерация абсорбента и выделение поглощенных кислых газов (H2S и С02).
Экзотермический эффект реакций составляет: при взаимодействии H2S и С02 с МЭА-раствором соответственно 1905 и 1917,6 Дж/кг, при взаимодействии H2S и С02 с ДЭА-раствором 1189 и 1515,7 Дж/кг [48−49]. Механизм поглощения С02 и H2S моноэтаноламином и основные сведения о растворимости их в водных растворах МЭА подробно описаны в литературе [50, 51,52,53].
Процесс МЭА-очистки. В работе [54,55,56] качестве растворителя используют водный раствор моноэтаноламина. Содержание МЭА в растворе не превышает, как правило, 15−20% об. при насыщении кислыми газами более концентрированных растворов увеличивается скорость коррозии металлов (чистый алканоламиновый раствор не обладает коррозионными свойствами). Наличие такой связи между концентрацией раствора и скоростью коррозии ограничивает возможность повышения эффективности хемосорбционных аминовых процессов. Однако в последние годы в связи с разработкой, ингибиторов коррозии появилась возможность увеличить концентрацию активного вещества в растворе до 30% об., что делает процесс МЭА-очистки более рентабельным и перспективным.
При проектировании установок МЭА-очистки часто принимают, что содержание кислых газов в растворе, покидающем нижнюю тарелку абсорбера, должно быть не более 65−70% от равновесной концентрации (по отношению к исходному сырому газу). При этом степень насыщения раствора должна быть не более 0,3−0,4 моль/моль МЭА. В последнее время на некоторых химических заводах при очистке синтезгаза от С02 (под давлением) степень насыщения раствора достигает 0,6−0,7 моль/моль МЭА. Это привело к необходимости использования легированных сталей для изготовления оборудования или применения ингибиторов коррозии при эксплуатации установок. Процесс МЭА-очистки рекомендуется применять для очистки газов от сероводорода и СОа при парциальном давлении их не выше 0,6−0,7 МПа.
Достоинства процесса: тонкая очистка газов от сероводорода и С02 обеспечивается в широком интервале парциальных давлений; моноэтанол амин имеет повышенную химическую стабильность, легко регенерируется, обладает высокой реакционной способностью; технологическое и конструкторское оформления процесса отличаются простотой и высокой надежностью при правильной эксплуатации установки; моноэтаноламиновый раствор относительно плохо поглощает углеводороды, что способствует повышению эффективности производства серы из кислых газов МЭА-очистки.
Недостатки процесса: низкая, как правило, степень насыщения раствора; высокие удельные расходы абсорбента и эксплуатационные затраты; некоторые примеси (С02, COS, CS2, HCN, S02 и S03), содержащиеся в сырых газах, при взаимодействии с растворителем образуют нерегенерируемые или труднорегенерируемые высокомолекулярные соединения, которые дезактивируют абсорбент, увеличивают вспениваемость и коррозионную активность растворителя; при наличии в газе COS и CS2 процесс не применяется; низкое извлечение меркаптанов и других сероорганических соединений; повышенная склонность абсорбента к вспениванию при попадании в систему жидких углеводородов, сульфида железа, тиосульфитов и других продуктов разложения моноэтанол амина, а также механических примесей и некоторых видов ингибиторов коррозии.
Поданным Кемпбела [57], скорость разложения МЭА в результате необратимого взаимодействия моноэтаноламина с С02, COS и CS2 можно принять: 3,35 кг на 1000 м8 СОа, 1 кг на 1 м³ COS; 1 кг на 1 м³ CS2 (для ДЭА она равна 3,68 кг на 1000 м³ С02; ДЭА практически не реагирует с COS и CS2 с образованием нерегенерируемых соединений). Сероорганические соединения (меркаптаны, дисульфиды, тиофены и др.), содержащиеся в природных и нефтяных газах, не реагируют с аминами. Для удаления из раствора механических примесей и продуктов необратимых реакций используют различные методы, в частности на многих промышленных установках для этих целей часть раствора (1−4% общего объема) фильтруют и перегоняют в специальном кубе. Содержание этих продуктов не должно превышать в растворителе 0,1−0,5%.
Для предотвращения вспенивания в раствор моноэтаноламина вводят противопенные добавки (0,001−0,0015% масс.). В качестве антивспени-вателей используют водные эмульсии силиконов или высококипящие спирты (олеиловый и др.). На отечественных ГПЗ используют антивспениватели КЭ-10−12 (21−2А) и КЭ-10−21. Испытание КЭ-10−12 на одной из промышленных установок показало, что применение антивспенивателей позволяет уменьшить потери растворителя, обеспечить устойчивую работу установки, а также создать условия для повышения производительности абсорбционной и ректификационной аппаратуры [65]
Рис 1 — Схема абсорбционная очистки газа с Н2S и СО2 водным растворым алканаминов: 1 — абсорбер; 2 — сепаратор; 3 — экспанзер (сепаратор); 4, 9 — водяные холодильники; 5,8 — воздушные холодильники; в — рекуперативный теплообменник: 7 — десорбер; 10 — емкость-сепаратор; 11 — ребойлер. — сырой газ; IIочищенный газ; III — насыщенный абсорбент; IV — экспанзерный газ; V — частично разгазированный абсорбент; VI — кислые газы; VII — регенерированный абсорбент На рис-1 приведена принципиальная технологическая схема абсорбционной очистки газа от H2S и С02 водным раствором алканоламина. Сырой газ с температурой 10−40 °С подают под нижнюю тарелку абсорбера 1, который орошается водным раствором МЭА или какого-либо другого алканоламина (растворитель можно подавать на одну верхнюю тарелку или на верхнюю и среднюю тарелки аппарата). С верха абсорбера выходит очищенный газ, с низа — насыщенный кислыми газами абсорбент (температура насыщенного абсорбента 55−60 °С, рабочее давление в аппарате изменяется для разных ГПЗ от 0,2 до 5,5 МПа).
Очищенный газ после сепаратора 2 направляется потребителям. Насыщенный абсорбент поступает в экспанзер (сепаратор) 3, где за счет дросселирования раствора из абсорбента выделяются поглощенные в абсорбере углеводороды (экспанзерный газ используется в качестве топлива). После сепаратора 3 насыщенный абсорбент нагревается в рекуперативном теплообменнике 6 до 95−100 °С и поступает в среднюю часть десорбера 7, где из него отпариваются кислые газы, вода и оставшиеся углеводороды. Температура в нижней кубовой части десорбера 7 поддерживается 115−130 °С за счет нагрева растворителя, стекающего с нижней тарелки десорбера, в рибойлере 11 (рабочее давление в десорбере 0,15 МПа).
Смесь кислых газов, паров воды и углеводородов выходит с верха десорбера 7, охлаждается в воздушном и водяном холодильниках 8 и 9, после чего двухфазная смесь поступает в емкостьсепаратор 10, где вода отделяется от кислых и углеводородных газов; вода из емкости 10 подается в качестве орошения на верхнюю тарелку десорбера, для предотвращения уноса моноэтаноламина с верхним продуктом, а кислые газы направляются на установку по производству серы. Регенерированный раствор алканоламина после охлаждения в рекуперативном теплообменнике 6, в воздушном и водяном холодильниках 5 и 4 подается в абсорбер 1 с температурой 35−45 °С (на схеме не показан узел очистки растворителя от механических примесей и нерегенерируемых высокомолекулярных соединений). Технологические показатели процесса приведены в табл. III.3.
Процесс ДЭА-очистки [67, 68, 69, 70, 71]. В качестве растворителя используется водный раствор диэтаноламина (ДЭА). Содержание ДЭА в растворе в зависимости от содержания кислых газов в исходном сырье и степени насыщения раствора изменяется от 20 до 30% масс; при концентрации в растворе кислых газов 0,05−0,08 м3/л ДЭА используют 20−25%-ный раствор, при 0,14−0,15 м8/л ДЭА -25−27%-ный раствор; при концентрации кислых газов 0,15−0,17 м3/л ДЭА — 25−30%-ный раствор диэтаноламина (процесс SNPA — ДЭА).
Процесс ДЭА-очистки с концентрацией диэтаноламина 25−27% применяют при парциальном давлении кислых газов 0,2 МПа и более, процесс SNPAДЭА (25−30% активного вещества) используют при парциальном давлении кислых газов 0,4 МПа и выше. Это позволяет обеспечить необходимое насыщение раствора и таким образом использовать преимущества процесса: степень насыщения раствора в процессе SNPA — ДЭА достигает 1−1,3 моль/моль ДЭА (против 0,3−0,4 для МЭА-процесса). Однако несмотря на высокую степень насыщения растворителя в SNPA — ДЭА-процессе поглотительная способность раствора ДЭА меньше, Недостатки процесса: низкая поглотительная способность растворителя, высокие удельные расходы абсорбента и эксплуатационные затраты; некоторые примеси, содержащиеся в сырых газах, частично (С02) или полностью (HCN) взаимодействуют с растворителем с образованием нерегенерируемых соединений; низкое извлечение меркаптанов и других сероорганических соединений.
Технологические схемы МЭА-и ДЭА-процессов практически не отличаются, за исключением узла очистки раствора от нерегенерируемых соединений. На установках ДЭА-очистки их удаляют путем фильтрации раствора (через фильтры пропускают до 10% циркулирующего раствора) [73, 74]. На установках МЭА-очистки для этих целей используют дистилляцию и фильтрацию (до 4% раствора циркулирует через эту систему).
Процесс Эконамин [75−76]. В качестве растворителя используются водный раствор дигликольамина (ДГА) с концентрацией активного вещества 60−65% масс, (против 20−30% в ДЭА-процессе). С помощью этого растворителя достигается тонкая очистка газа от H2S (до 5,7 мг/м3). При взаимодействии дигликольамина с С02, COS, CS2 и меркаптанами образуются легко регенерируемые соединения (активность ДГА по отношению к С02 выше, чем МЭА). В процессе очистки обеспечивается высокое извлечение С02, COS, CS2 и легких меркаптанов. Степень насыщения раствора ДГА может достигать 40−50 л кислых газов на 1 л раствора (вместо 30−35 л/л при МЭА-очистке) (таблица-2).
Процесс рекомендуется применять при содержании кислых газов в исходном сырье 1,5−8%. О растворимости углеводородов в ДГА и коррозионной активности рабочего раствора дигликольамина существуют противоречивые сведения [78, 79]. Однако, исходя из имеющихся данных, можно считать, что по этим показателям ДГА не уступает МЭАи ДЭА-растворам.
Таблица 2 — Ниже приведены некоторые технологические показатели очистки газа от сероводорода с помощью МЭА (ДЭА) и ДГА растворитель использовали на технологических установках [76]
Техническая характеристика газов | МЭА + ДЭА | ДГА | |
Производительность по сырому | |||
газу, тыс. м3/ч | 142,9 | 142,9 | |
Объем циркулирующего раство; | |||
рителя, м3/ч | |||
Поглощающая способность раство; | |||
рителя, м3/м3 | |||
Содержание в очищенном газе | |||
H2S, мг/м3 | 5,7 | 5,7 | |
С02, % об | 0,01 | 0,01 | |
Потери растворителя (разложение, | |||
унос и др.), м3/год | 77,6 | 56,9 | |
Насыщенный раствор дигликольамина рекомендуют регенерировать под вакуумом 13−17 кПа и температуре низа регенератора 160−170 °С. Технологические схемы и режимы моноэтаноламиновой и дигликольаминовой очистки примерно одинаковы.
В 1965 г. дигликольамин впервые был применен на промышленной установке для очистки сероводородсодержащего газа; в 1974 г. в США этот позволяет уменьшить удельные расходы абсорбента и теплоэнергетические затраты на 25−40%.
1.4 Очистка газа физическими и комбинированными растворителями
Применяемые абсорбенты имеют низкую теплоту растворения и характеризуются высокой поглотительной способностью по отношению к кислым газам и другим «нежелательным» компонентам, которая существенно зависит от парциального давления их в условиях абсорбции. При низких парциальных давлениях растворители имеют крайне низкую абсорбционную способность. При парциальном давлении 5 МПа и более физические растворители имеют значительные преимущества по сравнению с химическими абсорбентами, с ростом этого давления преимущества возрастают. Специалисты фирмы Флюор Корпорейшен считают, что физическая абсорбция может быть эффективной и при более низких парциальных давлениях, если процесс абсорбции проводить при низких температурах (-70 °С и ниже).
Все физические абсорбенты растворяют сероводород и С02, однако эффективность каждого из них по отношению к сероводороду и С02 неодинакова, поэтому одни абсорбенты выгодно использовать для извлечения С02, другие — для извлечения H2S, третьидля селективного (преимущественного) извлечения одного из них в присутствии другого компонента.
Процесс Флюор. В качестве абсорбента широко используют пропиленкарбонат, который имеет следующие физико-химические свойства:
Температура, кипения °С…242
Молекулярная масса. … 102
Плотность при 20 °C, давление насыщенных 1200 кг/м3, паров при 27 °C, Па 0,666.Пропиленкарбонат хорошо растворяет сероводород, С02, COS, CS2, RCH и углеводороды, он обладает слабым коррозионным действием по отношению к обычным углеродистым сталям, химически стабилен в условиях процесса, имеет низкое давление насыщенных паров. Процесс разработан фирмой Флюор. Первая промышленная установка построена в США в 1960 г. для очистки природного газа от СОа (45% об.) и H2S (70 мг/м3). Содержание кислых компонентов в очищенном газе составляло: С02 2% об., H2S-5,7 мг/м3 (мощность установки 2,3 млрд. м3/год). Процесс Флюор можно использовать для очистки природных, нефтяных и технологических сухих газов с повышенным содержанием С02 и низким отношением H2S: С02. Абсорбцию проводят в интервале от 0 до -6 °С (охлаждение обеспечивается за счет аммиачного холодильного цикла). Регенерацию абсорбента осуществляют, как правило, без подвода тепла путем ступенчатого снижения давления — для этого на установке имеется несколько сепараторов. Экспанзерный газ, выходящий после первого сепаратора, компримируют и вместе с исходным сырым газом направляют в абсорбер, так как в нем содержится значительное количество углеводородов и кислых компонентов. Такой газ не может быть использован в качестве сырья на установках по производству серы, или в качестве топлива. В процессах Флюор энергия насыщенного абсорбента, которая производится при дросселировании раствора, используется в гидротурбине для привода насоса, перекачивающего регенерированный абсорбент (потери абсорбента составляют 16 г/1000 м3 сырого газа).
Глава 2. Анализ и методика исследование
2.1 Физико-химических свойства этаноламинов и их водных растворов
Алканоламины (аминоспирты, оксиамины) можно рассматривать как производные аммиака, в котором один или несколько атомов водорода замещены на спиртовой радикал или спиртовой и углеводородный: По степени замещения центрального атома азота алкильными радикалами амины делятся на первичные, вторичные и третичные.
Первичные амины
H
N — CH2 — CH2 — ОН Моноэтаноламин (МЭА);
H
H
N — CH2 — CH2 — O — CH2 — CH2 — OH Дигликольамин (ДГА).
H
Вторичные амины он — сн2 — сн2-N — сн2 — сн2 — он Диэтаноламин (ДЭА); Третичные амины OH — CH2 — CH2 — N — CH — CH2 -OH Триэтаноламин (ТЭА);
OH — CH2 — CH2-N — CH2 — CH2 — OH Метилдиэтанол амин
| (МДЭА).
CH3
Амины содержат по крайней мере одну гидроксильную группу (- ОН) и одну аминогруппу N-присутствие гидроксильной группы снижает давление насыщенных паров и повышает растворимость амина в воде, а аминогруппа придает водным растворам щелочность, необходимую для взаимодействия с Н2S и Со2, которые в водной среде диссоциируют с образованием слабых кислот.
Физико-химические свойства безводных этаноламинов приведены в табл. 3.
Таблица 3 — Физико-химические свойства алканоламинов (массовое содержание основного вещества не менее 99%)
Показатели | МЭА | ДГА | ДЭА | ДИПА | ТЭА | МДЭА | |
Молекулярная масса | 61,1 | 105,1 | 105,1 | 133,2 | 149,2 | 119,2 | |
Плотность, г/см3 | 1,015 | 1,085 | 1,011 | 0,992 | 1,119 | 1,030 | |
(при Т, °С) | (20) | (20) | (25) | (40) | (25) | (20) | |
Кипения | 170,3 | 268,4 | 248,7 | 338,8 | |||
Застывания | 10,3 | — 9,5 | 27,5 | 32,4 | 20,4 | — 21,0 | |
Давление паров | 4,7 | 4,0 | 0,1 | ||||
при 60 °C, Па | |||||||
Динамическая вяз | 18,9 | ||||||
кость, х103 Па-с | (25) | (25) | (30) | (30) | (25) | (20) | |
(при Т, °С) | |||||||
Удельная теплоем | 2,72 | 3,4 | 2,47 | 2,51 | 2,34 | 1,71 | |
кость, кДж/(кг-°С) | (30) | (80) | (30) | (30) | (30) | (30) | |
(при Т, °С) | |||||||
Теплота реакции, | |||||||
кДж/кг: | |||||||
с H2S | |||||||
с СО2 | |||||||
Примечание. Удельная | теплоемкость воды при | 30 °С | равна | ||||
4,18 кДж/(кг-°С). | |||||||
Этаноламины — это бесцветные, вязкие, гигроскопические жидкости, смешивающиеся с водой и низшими спиртами во всех отношениях, они почти нерастворимы в неполярных растворителях.
Хемосорбенты применяют, как правило, в виде водных растворов. Концентрация амина в растворе может изменяться в широких пределах, ее выбирают на основании опыта работы и по соображениям борьбы с коррозией (см. далее). Массовая концентрация алканоламинов в воде составляет 10−60%.
Чистые амины — вязкие жидкости с высокой температурой замерзания (за исключением ДГА и МДЭА). Однако водные растворы этаноламинов менее вязкие и замерзают при низких температурах (ниже минус 10 °С), что делает возможным их применение в промышленности.
Рис 2 — Измерение рН 2н растворов аминов при нейтрализации С02: 1 — МЭА; 2 — ДЭА; 3 — МДЭА; 4 — ТЭА Рис-3.Кривые температур замерзания водных растворов аминов: 1 — МЭА; 2 — МДЭА; 3 — ДЭА Рис 4 — Кривые давления паров аминов (содержание основного вещества не менее 99%): 1 — МЭА; 2 — МДЭА; 3 — ДИПА; 4 — ДЭА; 5 — ТЭА Ср = а1 + a2T — a3C + a4CT, (1)
где Т — температура, °С; С — концентрация амина, % мас.; а — коэффициенты; показатели степени.
Значения, а и представлены в табл-3. Плотность, вязкость и теплоемкость водных растворов смеси МДЭА и ДЭА с ошибкой не более 15% могут быть рассчитаны по закону аддитивности пропорционально молярной доли каждого амина в смеси (см. Рис-6)
Зависимость давления паров воды над растворами аминов с достаточной точностью описывается законом Рауля [86]:
гдех/- мольная доля воды в растворе, р0 — давление насыщенных паров чистой воды.
Рис 5 — Зависимость вязкости (а), теплоемкости (*) и плотности (в) водных растворов МДЭА+ДЭА от температуры: о, * - доля ДЭА в смешанном абсорбенте (о — 30% мас., * - 50% мас.); 1 — общая концентрация амина в растворе 20% мас.; 2 — 30% мас.; 3 — 40% мас В пределах точности измерения наличие кислых газов в растворе мало сказывается на величине Рн2о.
2.2 Механизм поглощения H2S, CO2 и других серныстых компонентов водными растворами аминов
Механизм поглощения H2S и С02 водными растворами аминов рассмотрен в работах [90, 91]. Алканоламины, будучи щелочами, легко вступают в реакцию с кислыми газами H2S (С02), образуя водорастворимые соли. При этом протекают следующие реакции:
H2S + [Амин] Z [Амин-Н]+ + HS (мгновенно);
C02 + 2-[Амин] Г [Амин-Н]+ + [Амин-СОО]- (быстро);
С02 + H2O Н2С03 (медленно);
H2C03 Н+ + HCO3 (быстро);
НСО з Г Н+ + CO3 (быстро);
[Амин] + Н+ Z [Амин-Н]+ (быстро).
Все амины реагируют с Н одинаковым образом с образованием гидросульфида или сульфида амина, причем реакция классифицируется как мгновенная. Первичные и вторичные амины могут реагировать с С02 с образованием карбамата (соли замещенной карбаминовой кислоты — амин-С00 -Н+), которая трактуется как быстрая реакция второго порядка. Кроме того, с С02 образуются карбонаты и бикарбонаты аминов, но образованию их предшествует медленная реакция растворения С02 в воде с образованием угольной кислоты Н2С03. Считается, что при умеренных степенях карбонизации амина (до 0,5 моль С02/моль амина) преимущественно протекает реакция образования карбамата. Карбаматы аминов — нестойкие соединения и в слабощелочной среде они медленно разлагаются с образованием бикарбоната (на примере вторичного амина):
R2NCOOR2NH2 + H2O Z R2NH + R2NH2HCO3,
У третичного алканоламина нет подвижного атома Н+ в аминовой группе, поэтому становится невозможным протекание прямой и быстрой реакции с С02 по карбаматному типу, а взаимодействие осуществляется через предварительную и медленную стадию образования и диссоциации угольной кислоты:
С02 + Н20 Z Н2С03; Н2С03 Z Н+ + НС03;
[Амин] + Н+ + HCO" 3 Г [Амин-Н]+ * HCO3.
Конечными продуктами реакции являются бикарбонат и карбонат. Таким образом, разница в скоростях реакций третичных аминов с (мгновенная реакция) и Со2 (медленная реакция) гораздо значительнее, чем для первичных и вторичных аминов. Это позволяет использовать на практике третичные амины для селективного извлечения Н2О из смесей его с СО2
В соответствии с приведенными химическими реакциями н2о и Со2 с аминами концентрация активного (свободного) амина в растворе может быть рассчитана по уравнению Сж = Сж (1 — аА — naB), (2)
где Сж — концентрация свободного амина, моль/л; Сж — исходная концентрация амина, моль/л; аА, aB — насыщение амина, соответственно, H2S (А) и Со2 (В), моль/моль; n — стехиометрический коэффициент (для первичных и вторичных аминов n = 2, для третичных n = 1).
Литературные данные [121, 103] о зависимости константы скорости взаимодействия Со2 с этаноламинами от температуры обобщены в виде следующих уравнений:
для МЭА
lg rB = 11,070 — 2140/Г; (3)
для ДЭА
lg rB = 10,046 — 2050/Г; (4)
для МДЭА
lg rB = 8,932 — 2426/Г, (5)
где rB измеряется в л/(моль-с).
Реакционная способность алканоламинов изменяется в ряду: первичные > вторичные > третичные и коррелируется с их щелочностью.
Диоксид углерода образует с алканоламинами различные побочные продукты. Механизм их образования изучен не полностью. Часть из них на стадии регенерации абсорбента разрушается и снова выделяет алканоламин, другая часть-не регенерируется, вызывая потери амина. наибольшее количество нерегенерируемых соединений характерно для первичных алканоламинов.
Меркаптаны, будучи кислотами, обратимо реагируют с алканоламинами с образованием водорастворимых меркаптидов:
[Амин] + R8H Г [Амин-н]+ * RS-,
где R — углеводородный радикал (CH3; C2H5; C3H7 и т. д.).
Указанной реакции предшествует растворение меркаптанов в абсорбенте и диссоциация на ионы:
RSH Z RS- + H+.
Кислотность меркаптанов значительно ниже, чем H2S и СО2, вследствие чего последние вытесняют меркаптаны из и х соединений с аминами. Меркаптиды — нестойкие соединения, легко разрушающиеся при нагревании. Сероокись углерода в водных растворах аминов гидролизуется:
CОS + H2О Г СО2+ H2S.
Образовавшиеся H2S и С02 реагируют с аминами. 0днако, ввиду того, что в исходном газе концентрация CОS по сравнению с H2S и СО2 невелика, прямая реакция никогда не доходит до конца. Лимитирующая стадия процесса — растворение CОS в абсорбенте. Сероокись углерода может непосредственно вступать в реакции с первичными и вторичными аминами с образованием тиокарбаматов (аналогично С02). СОS способна вступать также в другие реакции с аминами, механизм которых изучен не до конца. При этом с первичными аминами образуются нерегенерируемые продукты; вторичные и третичные амины реагируют с СОS обратимо.
Аналогичным образом реагирует с алканоламинами и сероуглерод. Побочные продукты он образует и с первичными и с вторичными аминами. Сульфиды и дисульфиды с алканоламинами не взаимодействуют.
2.3 Растворимость H2S и CO2 в водных растворах этаноламинов
Многочисленные данные по растворимости H2S и С02 в водных растворах ДЭА обобщены в виде номограмм [99], которые приведены на рис. 7 и 8.
Hомограммы разработаны для определения равновесного давления кислых компонентов над системой H2S — 0,001 0,01 0,1 1 концентрация H2S в растворе, моль/моль ДЭА.
Рис 6 — Равновесное парциальное давление H2S над системой ДЭА — H2S — С02(p H2S =1,3*103 Pa)
Hзначение, полученное из номограммы; t — температура раствора; С — массовая доля ДЭА; R1, R2 — вспомогательные оси; цифры на кривых — концентрация С02 в растворе, моль/моль ДЭА. С02 — ДЭА в широком диапазоне изменения степени насыщения амина, температуры и концентрации амина в растворе.
Однако их можно использовать также для решения обратной задачи — определить емкость раствора, исходя из парциальных давлений H2S и С02 в исходном газе.
Рис 7 — Равновесная растворимость H2S в растворе МДЭА молярной концентрацией 4, 28 моль/л при различной температуре, °С: 1 — 120; 2 — 100; 3 — 70; 4 — 40; 5 — 25
Таблица 4 — Совместная растворимости H2S и С02 в 30% мас. водными растворами МДЭА при 20 °С
Парциальное давление, МПа | Содержание в растворе, моль/л | |||||||
H2S | С02 | H2S (расч.) | С02 | (расч.) | H2S (эксп.) | С02 (эксп.) | ||
физич. раствор. | химич. связан | физич. раствор | химичсвязан | общее | общее | |||
0,064 | 0,036 | 0,05 | 0,78 | 0,015 | 0,44 | 0,86 | 0,45 | |
0,340 | 0,060 | 0,09 | 1,20 | 0,110 | 0,50 | 1,32 | 0,60 | |
0,810 | 0,190 | 0,57 | 1,17 | 0,040 | 0,45 | 1,70 | 0,49 | |
0,260 | 0,290 | 0,12 | 0,80 | 0,037 | 1,92 | 0,85 | 2,10 | |
0,100 | 0,480 | 0,12 | 0,32 | 0,160 | 0,79 | 0,42 | 1,06 | |
0,012 | 0,190 | 0,05 | 0,25 | 0,150 | 1,06 | 0,35 | 1,12 | |
0,320 | 2,270 | 0,41 | 0,68 | 0,530 | 2,10 | 1,19 | 2,50 | |
0,070 | 0,980 | 0,16 | 0,37 | 0,300 | 1,70 | 0,49 | 2,00 | |
0,090 | 1,640 | 0,12 | 0,28 | 0,620 | 2,00 | 0,37 | 2,75 | |
0,280 | 3,100 | 0,57 | 0,49 | 0,720 | 2,10 | 1,17 | 2,85 | |
2.4 Растворимость углеводородов в водных растворах этаноламинов
Зависимость растворимости метана и этана в водных растворах ДЭА и МЭА при 65,6 °С приведена на рис-9. Растворимость углеводородов возрастает с увеличением концентрации амина в растворе, причем растворимость C2H6 зависит от концентрации сильнее, чем для CH4.
Присутствие H2S и СО2 в растворе в количестве 0,25 моль/ моль понижает растворимость метана примерно на 10−20%. Присутствие этана мало влияет на растворимость метана; в то же время CH4 на 10−15% понижает растворимость C2H6.
Зависимость растворимости метана в растворе амина от температуры имеет минимум (рис. 8). Для 40% мас. водного раствора ДЭА этот минимум в зависимости от парциального давления CH4 находится в пределах 70−90°С.
Рис 8 — Растворимость метана (а) и этана (б) в растворах МЭА и ДЭА при 65,6 °С: 1 — H2O; 2 — 5% ДЭА; 3 — 25% ДЭА; 4 — 40% ДЭА; 5 — 15% МДЭА; 6 — 40% МЭА Приведенные данные показывают, что растворимость CH4 и C2H6 в водных растворах ДЭА (в пределах рабочих концентраций) при парциальных давлениях их в газе, имеющих место в большинстве практических случаев, близка к растворимости их в воде. Поэтому в инженерных расчетах аминовых установок могут быть использованы данные о растворимости углеводородов в воде.
2.5 Растворимость меркаптанов в водных растворах этаноламинов
Рис 9 — Зависимость растворимости C2H5SH от концентрации ДЭА Растворимость индивидуальных меркаптанов в растворах аминов экспериментально определена Н. И. Подлегаевым. Основные результаты приведены на рис-10, 11, и табл-5. Растворимость метил-, этили изопропилмеркаптана в растворах аминов при содержании их в исходном газе в пределах от 0,5 до 15 г/м3 (в пересчете на меркаптановую Рис. 10 — Зависимость растворимости C2H5SH от концентрации ДЭА в растворе при температуре 20 °C (содержание RSH в газе — 5 г/м3)
Таблица 5 — Равновесная растворимость C2H5SH в водных растворах алканоламинов (t = 20 oC, содержание в газе — 5 г/м3)
Массовая доля амина, % | RSH в растворе, мг/л | ||||
МЭА | ДЭА | ТЭА | |||
288,1 | 80,4 | ||||
85,8 | |||||
202,4 | 92,9 | ||||
Константы растворимости меркаптанов в МДЭА приведены в табл. 5. Изотермы растворимости C2H5SH в водных растворах МДЭА даны на рис-11.
Рис 11 — Изотермы растворимости C2H5SH в водных растворах МДЭА при температуре 20 °C На растворимость меркаптанов в алканоламинах значительное влияние оказывает наличие С02 в растворе. Равновесная растворимость C2H5SH в аминах при наличии С02 в растворе в количестве 2 г/л (глубокая регенерация) снижается в 2,54 раза. С увеличением содержания С02 в растворе растворимость C2H5SH приближается к растворимости его в воде,
2.6 Растворимость сероокиси углерода в водных растворах этаноламинов
Процесс поглощения сероокиси углерода (COS) аминами определяется как физической растворимостью, так и химическим взаимодействием растворенной COS с аминами.
На рис 11 приведена зависимость растворимости COS в воде от температуры; с повышением температуры она уменьшается.
Хемосорбция COS водным раствором ДЭА сопровождается образованием тиокарбаминовой кислоты, которая диссоциирует в растворе и взаимодействует с ДЭА с образованием тиокарбамата амина. Тиокарбамат в водной среде гидролизуется, в результате чего образуется H2S и С02, которые легко связываются с ДЭА. Общая кинетика взаимодействия COS с ДЭА определяется медленной реакцией образования тиокарбаминовой кислоты.
Рис 12 — Зависимость растворимости COS в воде от температуры при давлении 101,333 кП В таблице-6 приведены значения константы скорости реакции образования тиокарбаминовой кислоты при различных температурах и значения констант фазового равновесия при физической растворимости COS в водном растворе ДЭА, экспериментально определенные К. И. Макаровым и С. П. Малютиным.
Таблица 6 — Основные константы, определяющие кинетику поглощения COS раствором ДЭА
Температура, °С | Константа фазового равновесия, кПа/мольная доля 103 | Константа скорости реакции, л/(моль-с) | |
117,5 | |||
Константа скорости образования тиокарбаминовой кислоты возрастает с увеличением температуры. Но одновременно растет константа фазового равновесия (в связи с падением физической растворимости COS в амине). Таким образом, в условиях одновременного протекания химической реакции и физической растворимости количество извлеченной COS из газа определяется скоростью поступления ее в раствор в р езультате массообмена с газовой фазой.
При создании в абсорбере аминовой очистки газа зоны гидролиза СОS, состоящей из 6−10 практических тарелок, при температуре 60−80 °С можно извлечь из газа значительную (до 80%) часть сероокиси углерода.
2.7 Растворимость сероводорда, диоксида углерода, сероокиси углерода, меркаптанов и углеродов в водно-неводных растворах алканаминов
Для комплексной очистки природных и нефтяных газов от сероводорода, диоксида углерода и сероорганических соединений применяются процессы, в которых используют водно-неводные поглотители, включающие алканоламины (для хемосорбции H2S и С02) и различные органические растворители (для физической абсорбции СОS, RSH и др.). 0сновные требования к органическим растворителям в композициях с алканоламинами: термохимическая устойчивость, низкая упругость паров, сохранение гомогенности во всем диапазоне степеней насыщения, высокая поглотительная способность и избирательность по отношению к сернистым соединениям по сравнению с углеводородами и С02 (при необходимости).
Согласно принятой модели растворимости оптимальными абсорбционными свойствами по отношению к сернистым соединениям обладают слабоассоциированные растворители основного или нейтрального характера с высокой диэлектрической постоянной (выше 23) и имеющие дипольный момент более 2 дебая. К таким растворителям относятся эфиры гликолей.
Из данных табл.-6 следует, что растворимость меркаптанов в диметиловом эфире тетраэтиленгликоля (условно-сокращенное наименование-тетраглим) почти в 30 раз выше, чем в водном растворе МДЭА. В связи с этим очевидна перспективность использования органических соединений данного класса при разработке рецептур водно-неводных поглотителей.
Установлено повышение поглотительной способности эфиров гликолей с увеличением числа гликолевых групп в молекуле (пг).Эта зависимость с коэффициентом корреляции R >> 0,9 для t = 25 oC описывается уравнениями:
H2S K = exp (10,85 — 1,078) С02 K = exp (17,34 — 0,408 пг) СОS K=exp (15,93 — 0,645)
CH3SH K = exp (9,146 — 1,276 n); (5)
C2H5SH K = exp (8,243 — 1,218 n). (6)
Растворимость парафиновых углеводородов и алифатических меркаптанов в тетраглиме с увеличением числа углеродных атомов в молекуле n возрастает согласно уравнениям:
CnHn+2 K = exp (28,7 + 393,84/(n + 6,108)); (7)
RSH K = exp (356 — 1,218 n). (8)
При наличии примесей воды поглотительная способность эфиров гликолей достаточно резко снижается, особенно по отношению к углеводородам:
K/K0 = ехр (-0,055 + 0,061 CH2O), (9)
где K0 — константа растворимости углеводорода в безводном эфире гликоля; CHO — содержание воды в поглотителе, % мол. доли.
С учетом установленных закономерностей составлен ряд композиций водно-неводных поглотителей, составы которых и константы растворимости в них компонентов природного газа представлены в табл.-6. Из этих данных следует, что водно-неводные растворы МДЭА благодаря наличию органической добавки эффективно абсорбируют сероорганические соединения, особенно меркаптаны, константа растворимости которых увеличивается Рис 13 — Зависимость парциального давления p сероводорода (1, 2) и диоксида углерода (3, 4) от степени насыщения, а для 40% мол. водного и водно-неводного раствора МДЭА при 30 °С: 1,3- водный раствор МДЭА; 2, 4 — водно-неводный раствор МДЭА, содержащий 40% мол. полиэтиленгликоля с возрастанием молекулярной массы меркаптана раствор A K = exp (17,04 — 1,17 n); (10)
раствор В K = exp (12,71 — 2,001 n). (11)
Зависимость константы растворимости углеводородов от их молекулярной массы:
раствор A ln K = 4,605 + 10,63 exp (-0,204 n); (12)
раствор В ln K = 4,605 + 9,5782 exp (-0,242 n). (13)
Влияние органической добавки на абсорбцию сероводорода и диоксида углерода проявляется главным образом в области высоких степеней насыщения алканоламинами, когда концентрации растворенного и химически связанного компонентов становятся соизмеримыми.
Глава 3. Экспериментальная часть
3.1 Технология и изучение процесса очистки углеводородного газа на опытной установке ГПЗ Учкыр
Установки очистки углеводородных попутных и природных газов предназначены для удаления из газа вредных, ядовитых, коррозионно-активных серосодержащих соединений и негорючих инертных газов, снижающих теплоту сгорания газов. Обычно в углеводородных газах содержатся следующие серосодержащие соединения: сероводород, серооксид углерода, сероуглерод, меркаптаны, а в газовом конденсате могут содержаться сульфиды и дисульфиды. В состав инертных газов входят так же диоксид углерода азот, гелий. Очистка углеводородных газов необходима в обязательном порядке сразу по нескольким причинам:
Как правило, загрязнители являются сильно ядовитыми и вредными веществами.
При контакте с металлами образуют очаги химической коррозии.
В целях промышленного извлечения содержимых веществ и их последующей переработки В зависимости от исходного состава газа, требованиям, предъявляемым к очищеному газу, ряда производственных факторов и требований компания может предложить своим заказчикам установки очистки углеводородных газов аппаратурно оформленные на базе различных разновидностей процессов абсорбции, адсорбции и при помощи молекулярных фильтрующих установок. К плюсам установок очистки газов на базе процесса абсорбции относится то, что для них абсолютно не критично любое высокие содержание вредных примесей в газе, очистка газа методом адсорбции напротив, применяется при низких начальных концентрациях загрязнителей (до 5%) но значительно глубже позволяет очистить газ.
Рис 14 — Общая вид установки АОГ Установки абсорбционной очистки газов могут быть разработаны как на основе хемосорбционных процессов с применением таких абсорбентов как: амины (моно-, ди и триэтаноламины, диизопропаноломин) и щелочи, так и на основе физических процессов с применении таких абсорбентов как диэтиленгликоли и триэтиленгликоли, метанол и др. все зависит от удобства применения для заказчика того или иного абсорбента и ряда других факторов влияющих на выбор реагента и технологии очистки газа.
Технология абсорбции, основанная на хемосорбционных процессах, заключается в химическом взаимодействии загрязнений (H2S и СO2) с абсорбентами.
При взаимодействии с загрязняющими кислыми компонентами газа они образуют химические соединения, которые впоследствии, легко распадаются на исходные компоненты при изменении процессных данных (снижении давления и увеличения температуры).
Чаще всего в установках абсорбционной очистки газа основанных на хемосорбционных процессах в качестве абсорбента применяются диэтаноламины. По сравнению с моноэтаноламинами нашедшими широкое применение в российских установках, диэтаноламины позволяют извлекать из очищаемого газа не только сероводород и диоксид углерода, но и серооксид углерода, сероуглерод и тиолы.
Но так как диэтаноламины также не лишены недостатков, выбор конкретной технологии очистки, применяемые методы и реагенты, специалисты компании на стадии подготовки предложения всегда согласовывают с заказчиком.
Технологическая схема типовой установки абсорбционной очистки газа с диэталонамином в качестве абсорбента выглядит следующим образом:
Рис. 15 — Типовая схема установки очистки газа от сероводорода Очищаемый углеводородный газ подается в абсорбер где последовательно в две ступени контактирует с абсорбентом (25%-й раствор метилдиэтаноламина) на первом этапе с потоком слаборегенерированного, а на втором с полностью регенерированным. Снизу абсорбера абсорбент поступает в десорбер растворенного газа, где происходит отделение физически растворенного в абсорбенте углеводородного газа, после чего насыщенный кислыми компонентами абсорбент через теплообменник поступает в регенерационную колонну, в которой комплексные соединения абсорбента с Н2S и CO2 разлагаются, выделяющая смесь кислых газов отводиться вверху колоны. Снизу колонны регенерированный абсорбент через ребойлер и охладительные аппараты поступает на абсорбер, далее цикл повторяется. Установки поставляются единым скидом, на месте заказчику остается только соединить трубопроводы и запитать энергоресурсы.
3.2 Очистка газа высококонцентрированными растворами диэтаноламина
Повышение концентрации амина позволяет снизить количество циркулирующего раствора при сохранении нагрузки по сырому газу, и, следовательно, сократить затраты теплоты на регенерацию насыщенных растворов, а также потребление электроэнергии на перекачку раствора амина.
Испытания проводили на одной установке III очереди ОГПЗ. Установка состоит из двух идентичных параллельно работающих ниток, каждая из которых включает один абсорбер с диаметром Dн = 3,8 м и один десорбер переменного сечения Lн = 2,7/3,7 м (верх/низ) с соответствующим теплообменным и холодильным оборудованием. Абсорбер и десорбер оснащены ситчатыми тарелками провального типа. В абсорбере установлено 25 тарелок, в десорбере — 33 тарелки (в отпарной — нижней части — 22 тарелки, в верхней — кондиционно-охладительной — 10 тарелок). Питание абсорбера — двухпоточное с одинаковой степенью регенерации раствора на 15 и 25 тарелки с соотношением потоков — 40/60% от общего количества циркулирующего раствора. Испытания проводились при соблюдении основных норм, заложенных в технологическом регламенте на эксплуатацию установок сероочистки газа.
Из полученных данных следует, что повышение концентрации ДЭА с проектного значения 25% мас. до 40% мас. позволило примерно в 1,5 раза сократить кратность циркуляции абсорбента при одновременном сокращении расхода пара на регенерацию более 10%. Кроме того, это дает возможность увеличить долю более крепкого по H2S и СО2 газа КГКМ в смеси с газом ОГКМ с 70 до 110 тыс. м3/ч при сохранении общей загрузке абсорбера сырым газом на уровне 300 тыс. м3/ч.
Технология очистки газа ДЭА повышенной концентрации (до 40% мас.) внедрена на Учкырском ГПЗ. Испытания МДЭА проводили на одной установке нитке-III. Предварительно проводился контрольный пробег установки на ДЭА. Показатели работы установки сероочистки приведены в при селективной очистке МДЭА смешанного газа ОГКМ и КГКМ. При этом доля газа КГКМ в смешанном потоке была примерно на 25% больше, чем для ДЭА. Содержание СО2 в очищенном газе было на уровне 20% от исходного при очистке от H2S не более 20 мг/м3. Вследствие этого увеличилось содержание H2S в кислых газах регене рации абсорбента на 5−10% по сравнению с ДЭА — очисткой, что привело к повышению степени конверсии H2S в серу на установках Клауса.
Из табл.7. видно что, при использовании ДЭА для получения кондиционного по H2S очищенного газа нагрузка абсорбера по сырьевому газу КГКМ составляет не более 160−165 тыс. м3/ч или 50% от номинальной производительности. В случае использования МДЭА расход газа КГКМ на абсорбер достигал 250 тыс. м3/ч (80% номинальной производительности). Сохранение проектной номинальной производительности было достигнуто В результате промышленных испытаний получены данные о влиянии удельного орошения, концентрации МДЭА в растворе, степени насыщения амина кислыми газами и температуры абсорбции на селективность процесса очистки газа. Показано, что селективность снижается с увеличением удельного орошения и возрастает при уменьшении концентрации МДЭА в растворе и при увеличении насыщения амина кислыми газами. Наибольшее влияние на селективность МДЭА оказывает температура регенерированного раствора, подаваемого в абсорбер. Повышение температуры регенерированного амина на 10−15 °С приводит к снижению в 1,3−1,5 раза селективности МДЭА.
Основные результаты испытаний приведены в табл. 7.
Таблица 7 — Результаты промышленных испытаний процесса очистки природного газа растворами ДЭА и МДЭА
Расход очищаемого газа, м3/ч | Объем циркулирующего абсорбента, м3/ч | Концентрация амина в растворе, % мас. | Содержание кислых компонентов в газе, % мол. | Селективность очистки, % | Степень насыщения амина, кислыми газами моль/моль | Состав кислых газов регенерации, % мол. | Расход пара на регенерацию, кг/м3 кислотного газа | ||||||
До очистки | После очистки | ||||||||||||
H2S | СО2 | СО2 | H2S | СО2 | Общая | H2S | СО2 | ||||||
Диэтаноламин | |||||||||||||
3,9 | 5,1 | 0,02 | 0,4 | 0,22 | 0,30 | 0,52 | 40,2 | 51,8 | 3,2 | ||||
3,8 | 5,0 | 0,03 | 0,6 | 0,23 | 0,31 | 0,54 | 39,6 | 3,3 | |||||
2,0 | 1,3 | 0,03 | 2,3 | 0,30 | 0,22 | 0,52 | 55,7 | 36.0 | 3,7 | ||||
2,1 | 1,6 | 0,03 | 1,3 | 0,31 | 0,24 | 0,55 | 53,2 | 39,4 | 3,5 | ||||
2,3 | 2,0 | 0,03 | 1,5 | 0,28 | 0,26 | 0,54 | 49,5 | 42,3 | 3,4 | ||||
Метилдиэтанололамин | |||||||||||||
36,4 | 4,0 | 5,2 | 1,08 | 20,8 | 0,27 | 0,33 | 0,60 | 45,2 | 47,0 | 2,5 | |||
40,4 | 4,0 | 5,1 | 1,05 | 20,6 | 0,26 | 0,3 | 0,56 | 45,7 | 45,8 | 2,4 | |||
41,8 | 3,7 | 4,2 | 0,88 | 20,9 | 0,26 | 0,28 | 0,54 | 47,3 | 45,2 | 2,3 | |||
31,0 | 2,1 | 1,6 | 0,33 | 20,6 | 0,30 | 0,20 | 0,50 | 57,8 | 34,8 | 3,2 | |||
32,0 | 2,3 | 1,9 | 0,40 | 21,0 | 0,30 | 0,22 | 0,52 | 55,3 | 37,3 | 3,1 | |||
36,0 | 2,2 | 3,0 | 0,41 | 20,5 | 0,27 | 0,21 | 0,48 | 53,4 | 41,9 | 3,0 | |||
40,0 | 2,4 | 2,3 | 0,47 | 20,4 | 0,26 | 0,21 | 0,47 | 56,7 | 43,3 | 2,9 | |||
3.3 Коррозионные свойства алканоаминов
Проблема, с которой сталкиваются при эксплуатации аминовых установок очистки газа, — это коррозия технологического оборудования. Механизм коррозии на установках аминовой очистки весьма сложен и недостаточно изучен. Коррозия зависит от многих факторов: от концентрации H2S и CO2 в очищенном газе, степени насыщения амина кислыми газами, температуры и концентрации амина, качества поглотительного раствора и т. д.
0сновными агрессивными веществами являются сами кислые газы. Сероводород действует на сталь как кислота и ведет к образованию нерастворимого сернистого железа. Диоксид углерода в присутствии воды вступает в реакцию с металлическим железом с образованием бикарбоната железа, который при нагревании раствора переходит в нерастворимый карбонат железа, который осаждается на стенках аппаратов и трубопроводов. Коррозия ускоряется под действием продуктов деградации амина, которые взаимодействуют с металлом.
Коррозии оборудования также способствует накопление в растворе твердых частиц, которые разрушают защитные пленки, вызывают эрозию металла. Такими твердыми частицами являются сульфид железа, окись железа, пыль, песок, прокатная окалина, которые попадают в абсорбер вместе с потоком газа.
Интенсивность коррозии возрастает в ряду: первичные алканоламины > вторичные > третичные, так как более реакционноспособные первичные и вторичные амины требуют более высоких температур для десорбции кислых газов; остаточное содержание кислых газов в регенерированных растворах таких аминов также выше.
Оборудование установок аминовой очистки газов помимо общей коррозии подвергается и другому виду разрушения — коррозионному растрескиванию. Зарегистрированы случаи появления коррозионных трещин в абсорберах, десорберах, теплообменниках, трубопроводах.
В литературе неоднозначно оценивается влияние на коррозионную агрессивность аминовых растворов, увеличение и х концентрации. В основном проводятся данные по усилению коррозии с увеличением концентрации растворов первичных аминов.
Специалисты ГПЗ месторождения Лак (Франция) утверждают, что возможно использование ДЭА концентрации до 40% мас. без ингибитора коррозии с приемлемой степенью коррозии оборудования.
Исследования, проведенные в институте ВНИИНефтемаш, показали, что при увеличении концентрации ДЭА с 20 до 50% мас. при степени насыщения амина кислыми газами 0,5 моль/моль (H2S /СО2 — 1/1) скорость коррозии углеродистой стали снижается. Для 50% мас. раствора ДЭА она составляет 0,1 мм/год, что дает возможность при прибавке на коррозию 3 мм (стандарт) прогнозировать длительный срок эксплуатации оборудования. Было также установлено, что при увеличении концентрации ДЭА в растворе, склонность сталей к коррозионному растрескиванию уменьшается.
Оценка коррозионной агрессивности различных абсорбентов, насыщенных H2S и СО2, проведенная в автоклавах под давлением на Опытном заводе ВНИИГАЗа в условиях, близких к промышленным, показала (табл. 4.38), что скорость коррозии (сталь 20) в водных растворах МДЭА и смеси МДЭА+ДЭА (соотношение МДЭА/ДЭА = 50/50%) не намного превышает значения для одного стандартного ДЭА одинаковой концентрации. Коррозионная агрессивность абсорбентов физико-химического действия — «Укарсол-702» ниже, чем для ДЭА. Скорость коррозии стали 20 для всех испытываемых растворов в данных условиях не превышает 0,1 мм/год, что ниже допустимой — 0,3 мм/год.
При очистке газа водными растворами аминов коррозия происходит по всему тракту поглотительного раствора. Наиболее интенсивная коррозия наблюдается в зонах с максимальной концентрацией кислых газов и максимальной температурой, поэтому в промышленных условиях наиболее интенсивной коррозии обычно подвержены теплообменники, кипятильники, конденсаторы, десорберы.
Обычно основное оборудование установок очистки газа изготавливается из углеродистой стали и лишь наиболее подверженные коррозии узлы Скорость коррозии стали 20 в различных абсорбентах (р = 50 МПа, t = 90 °C, Еа = 0,5 моль/моль, H2S/C02 = 2:1)
Абсорбент, % мас. | Скорость коррозии, мм/ год | |
ДЭА (40%) | 0,06 | |
МДЭА (40%) | 0,074 | |
МДЭА + ДЭА (40%) | 0,09 | |
Укарсол-702 (70%) | 0,05 | |
(трубные пучки теплообменников, кипятильников, холодильников) из нержавеющей стали, скорость коррозии которой в 10−100 раз ниже, чем углеродистой стали. Абсорберы обычно не корродируют, хотя бывают случаи коррозионного растрескивания при определенных условиях. Одним из средств борьбы с растрескиванием является отжиг сварных швов.
Термообработке подвергаются и сами колонны. Срок службы абсорберов и десорберов поддерживается увеличением толщины стенок при их изготовлении.
В теплообменниках трубные пучки корродируют как со стороны насыщенного, так и регенерированного раствора, что объясняется высоким содержанием кислых газов в растворе и неполной их отпаркой из раствора. При этом особенно интенсивная коррозия происходит в высокотемпературной секции теплообменников, в которых раствор перегревается выше температуры кипения и происходит десорбция кислых газов. Кожухи из углеродистой стали обычно корродируют значительно слабее.
Особенно агрессивны условия работы кипятильников (рибойлеров), что связано с тем, что в них зачастую происходит отпарка значительного количества СО2 при температуре около 130 °C, и образуются застойные зоны, содержащие СО2 и продукты деструкции амина.
Подвержены коррозии и конденсаторы-холодильники парогазовой смеси, выходящей из десорбера. Добавление этаноламина (до 1%) в газообразную систему Н2О — H2S — СО2 приводит к значительному ослаблению коррозии углеродистой стали. Поэтому, в последнее время охлаждение парогазовой смеси проводится в верхней части десорбера путем непосредственного контакта с флегмой, циркулирующей в замкнутом контуре.
Ниже приведены мероприятия по борьбе с коррозией на аминовых установках очистки газа.
На стадии эксплуатации:
поддержание низких скоростей в теплообменниках амин /амин;
циркуляция насыщенного раствора амина по трубам теплообменника, а регенерированного раствора — в межтрубном пространстве;
поддержание повышенного давления в теплообменниках с целью предотвращения выделения из раствора кислых газов при снижении давления и повышении температуры насыщенного раствора;
применение ингибиторов коррозии, особенно при высокой степени насыщения амина кислыми газами (>0,5 моль /моль).
На стадии проектирования и изготовления:
правильный выбор рабочего раствора и конструкции оборудования;
правильный выбор металла для изготовления оборудования и трубопроводов;
термообработка сварных соединений.
Главным требованием для ослабления коррозии является хорошее качество поглотительного раствора (снижение содержания в растворе продуктов побочных реакций — не более 0,2%, а также солей жесткости и механических примесей) — это достигается путем непрерывного вывода примесей из раствора на фильтрацию.
3.4 Вспениванием растворов алканоаминов
Вспенивание растворов аминов — одна из серьезных проблем при эксплуатации установок очистки газа. Вспенивание приводит к нарушению режима работы установок, ухудшению качества очищенного газа и, как следствие этого, к необходимости снижения производительности установок по газу. При вспенивании возрастают потери дорогостоящих аминов в результате уноса с газом.
Вспенивание возникает, как правило, в абсорберах. Но бывают случаи, когда начавшееся вспенивание раствора переносится в десорбер. Вспенивание чаще возникает в аппаратах с высокими нагрузками по газу и раствору. Признаком вспенивания является увеличение объема пены на контактных тарелках, резкое увеличение перепада давления в аппарате, появление значительного уровня жидкости в сепараторах очищенного (абсорбер) и кислого (десорбер) газов.
Основная причина вспенивания — это примеси, поступающие вместе с сырым газом и попадающие в абсорбент (жидкие углеводороды, пластовая вода, механические примеси, ингибиторы коррозии, различные ПАВ, смолистые вещества и др.). Пенообразователями являются также сульфид железа, смазочные масла, продукты коррозии и деградации амина. Указанные продукты накапливаются в растворе до определенной концентрации, при которой начинается его вспенивание.
На рис 16 приведены результаты испытаний по вспениванию 25%-ного мас. ДЭА при 20 °C в присутствии различных примесей. Эти данные показывают, что практически все вещества, присутствующие в поступающем с промысла газе, способны вызывать вспенивание аминовых растворов.
Рис 16 — График влияния различных добавок на пенообразующую способность 25%-ного раствора ДЭА: Iпарафины; II — нафтены; III — фракции конденсата; IV — спирты; 1 — пентаны; 2 — октан; 3 — нонан; 4 — ундекан; 5 — циклогексан; 6 — циклопентан; 7 — конденсат, фракция 150 °C; 8 — конденсат ОГКМ НК-КК; 9 — метанол (технический); 10 — остаток (10%) от перегонки технического метанола Кипения выше 100 °C (конденсат, нефть), ПАВ, некоторые ингибиторы коррозии.
Для предотвращения вспенивания необходима реализация следующих основных мероприятий:
Сведение к допустимому минимуму содержания в поступающем на очистку газе примесей, вызывающих или способствующих вспениванию. Это достигается эффективной работой входных сепараторов и промывкой газа каким-либо абсорбентом, например, водой или углеводородной фракцией стабильного конденсата.
Подача регенерированного амина на 2−5 °С выше температуры уходящего из абсорбера газа для предупреждения конденсации углеводородов.
Периодическая промывка и очистка аппаратов от шлама.
Наиболее эффективное средство — вывод примесей из системы путем непрерывной фильтрации раствора амина. На фильтрацию направляют небольшую часть циркулирующего раствора (от 5 до 20%). Как правило, фильтрации подвергается регенерированный раствор амина.
Вначале раствор прокачивается через листовой фильтр для вывода из раствора механических и взвешенных частиц. На листовой фильтр предварительно наносится фильтрующая смесь. На отечественных установках сероочистки в качестве фильтрующей смеси используется порошок «Перлит», древесный осветляющий уголь и фильтр-волокно.
Отфильтрированный от механических примесей раствор подается в адсорбер с активированным углем для улавливания углеводородов, продуктов деградации амина и других примесей. После угольного фильтра устанавливается патронный фильтр для улавливания частиц угля, уносимых раствором из адсорбера. Рекомендуется на угольный фильтр подавать 520% раствора, а на механический — максимальное количество, вплоть до 100%.
При фильтрации рекомендуется поддерживать скорость раствора около 10 л/(мин-м2), хотя в ряде случаев может достигать величины 20−60 л/(мин-м2). Высота фильтрующего слоя в одном адсорбере составляет 3−4 м.
По практическим данным для нормального ведения технологического процесса содержание примесей в растворе не должно превышать 2 г/л.
Эффективное средство против вспенивания — применение антивспенивателей (пеногасителей). В качестве антипенных добавок используются различные силиконовые вещества и высококипящие спирты при концентрации их в растворе 0,001−0,01% мас.
Пеногасители используют в виде 2−5%-ных растворов в амине или воде и подают в систему либо постоянно небольшими порциями, либо осуществляют кратковременную быструю подачу их в момент вспенивания раствора. Второй путь является более предпочтительным, так как иногда чрезмерное количество антивспенивателя может привести к обратному явлению — к стабилизации пены.
ПОТЕРИ АБСОРБЕНТОВ: Расход аминов — один из важных показателей работы установок очистки газов, поскольку стоимость абсорбентов высока и затраты на абсорбент составляют существенную часть эксплуатационных затрат.
Основные составляющие потерь аминов на установках: унос с газом, термохимическая деструкция аминов, механические потери.
Унос с газом. 0бщий унос амина с газом определяется уносом в паровой фазе и в капельном виде. Величина первого определяется давлением паров амина над водными растворами и зависит от температуры, типа и концентрации амина в растворе. Хотя давление паров аминов относительно невелико, потери их из-за испарения значительны, вследствие больших объемов очищаемого газа.
Потери амина за счет уноса в капельном состоянии зависят от нагрузок по газу и раствору, от эффективности работы сепарирующих устройств на газовых потоках, от вида применяемых контактных элементов в колонных аппаратах. Капельный унос резко возрастает при вспенивании поглотительного раствора. Эта величина потерь амина при нормальной работе заводских установок составляет 20−30 мг/м3 газа и возрастает до 100 мг/м3 при вспенивании раствора.
Термическое разложение аминов без углекислоты протекает в малой степени и усиливается с повышением температуры и степени насыщения аминов С02. Потери ДЭА под действием С02 незначительны при температуре 100 °C и давлении 1,2 МПа и достигают более 90% при температуре 175 °C и давлении 4,1 МПа. Hасыщенный С02 водный 20%-ный раствор ДЭА в течение 8 ч при давлении 1,7 МПа и температуре 125 °C разлагается на 22%. При нагревании раствора ДЭА без С02 в атмосфере азота в течение 8 ч при давлении 4,1 МПа и температуре 205 °C не наблюдается значительных изменений концентрации ДЭА или образования продуктов деструкции амина.
Механизм взаимодействия С02 с аминами с образованием побочных нерегенерируемых или труднорегенерируемых соединений изучен не полностью. Считают [39], что на первой стадии карбонаты или карбаматы, образовавшиеся в результате взаимодействия С02 с аминами, превращаются в оксазолидон-2, который затем образует оксиэтилимидазолидон-2. Замещенный имидазолидон гидролизуется до оксиэтилэтилендиамина. В растворах ДЭА оксазолидон при повышенных температурах может превратиться в другое термически стойкое соединение — оксиэтилпиперазин. 0ксазолидон-2 может образовываться и при обычных температурах, если в газе имеется сероокись углерода. В растворах амина были обнаружены и другие содержащие азот и имеющие сложную структуру не идентифицированные продукты разложения.
Скорости побочных реакций обычно низки. 0днако при длительной циркуляции поглотительного раствора происходит накопление труднорегенерируемых продуктов в системе. Это приводит к снижению концентрации активного амина, повышению вязкости раствора и в целом к уменьшению эффективности процесса абсорбции. Кроме того, наличие продуктов деградации аминов вызывает вспенивание и усиливает коррозионную агрессивность раствора.
Установлено, что продукты превращения ДЭА несколько тормозят реакции его разложения; сероводород тормозит деструкцию ДЭА под воздействием СО2.
Сложность происходящих в растворе процессов деструкции аминов и отсутствие в литературе представительных данных по кинетике и механизму побочных реакций СО2 с ДЭА и МДЭА затрудняют количественную оценку этой статьи потерь аминов.
В связи с этим в работе было проведено экспериментальное исследование термохимической деструкции ДЭА и МДЭА под действием СО2 в автоклавах при температуре до 250 °C и парциальном давлении СО2 до 5 МПа.
Было установлено, что процесс деградации аминов подчиняется кинетическому уравнению первого порядка:
d [A]/dx = -K[A]. (14)
Зависимость константы K скорости деструкции аминов под действием СО2 от температуры приведена на рис 17.
Представленные данные свидетельствуют о значительно более высокой термохимической стабильности МДЭА по сравнению с ДЭА, причем это различие с ростом температуры проявляется все сильнее. Экспериментальные данные по зависимости константы скорости процесса деструкции аминов (K, моль/(л-ч) от парциального давления CO2 (pCO2, МПа) и температуры (°С) описываются следующими критериальными.
Рис 17 — Зависимость константы скорости процесса термохимической деструкции алканоламинов от температуры при PCOl > > 0,1 МПа уравнениями: Для МДЭА при pCO > 4 МПа:
K = -0,0846 + 0,169-lnpCO2,
t = 185 °C; (15) K = exp (-15,1335 + 0,0749-t),
100 oC < t < 165 oC; (16) K = -0,8505 + 5,5−10−3 — 3t,
165 oC < t < 205 oC. (17) Для МДЭА (при рСОг > 2 МПа):
205 oC < t <255 oC. (18) K = exp (-12,05 + 0,3 856-t).
По уравнениям (15−18) можно рассчитать примерный расход аминов с учетом технологических режимов работы установок сероочистки газа и состава перерабатываемого сырья.
Следует отметить, что в промышленных условиях наибольшую деструкцию амина следует ожидать в зонах с повышенной температурой и степенью насыщения CO2. Такой зоной, по-видимому, является линия насыщенного раствора в интервале температур 80−110 °С.
Основным способом снижения потерь аминов в результате термохимического разложения является вывод продуктов деструкции из системы путем фильтрации и сорбционной очистки (активные угли, цеолиты и др.) раствора.
Добавление к амину небольшого количества водного раствора соды или щелочи ускоряет гидролиз первичного продукта деструкции аминов — оксазолидона-2, что приводит к снижению количества продуктов разложения в растворе.
Немаловажное значение имеет также поддержание температуры регенерации насыщенного амина — не выше 130 °C.
Механические потери происходят от разливов и утечек через неплотности аппаратуры в системе хранения и перекачки раствора. Эти потери характеризуют культуру производства и не должны превышать 10% от общих потерь аминов.
Прочие потери вызываются химическим взаимодействием амина с другими компонентами газа (COS, CS2, RSH и др.), кислородом воздуха.
Продукт взаимодействия ДЭА с COS при регенерации легко диссоциируется, выделяя амин. Содержание CS2 в природных газах, как правило, незначительно — до 20 мг/м3 и продукты реакции CS2 с ДЭА при нагревании регенерируются на 80% и более. МДЭА с COS и CS2 не реагирует. Меркаптаны, дисульфиды и тиофены не вступают в реакцию с аминами и поэтому не вызывают потерь поглотителей.
Этаноламины подвержены окислительному разложению. В присутствии кислорода сероводород реагирует с аминами с образованием устойчивых соединений (тиосульфат, соли дитиокарбаминовой кислоты, тиомочевина и другие продукты), которые не удается разложить при нагревании. Для предотвращения потерь амина от окислительного разложения необходимо исключить контакт амина с воздухом (инертная «подушка» в емкостях с амином).
Прочие потери амина с примесями газа и раствора рассчитать практически невозможно, так как очень много веществ может участвовать в этом процессе. Указанные потери принимаются в размере 5−10 мг/м3 сырьевого газа.
3.5 Расчет основных узлов и параметров установок очистки газа
Для осуществления комплексной интенсификации процесса аминовой очистки необходима разработка общей математической модели, на базе которой на ЭВМ выполняются расчеты в целях поиска оптимальных решений на стадии проектирования и управления. Оптимальным следует считать режим, при котором обеспечиваются минимальные эксплуатационные затраты на проведение процесса очистки газа.
К настоящему времени проведены исследования, позволяющие разработать обобщенную модель процесса абсорбции — десорбции Н и СО2 водными растворами этаноламинов.
Кратность циркуляции абсорбента является одним из самых важных показателей работы установок очистки газа, так как на ее долю приходится примерно 60% энергетических затрат на процесс очистки.
Расход абсорбента должен быть таким, чтобы обеспечить требуемую степень очистки газа от кислых компонентов при минимальных затратах на процесс. Более высокий расход поглотителя по сравнению с требуемым приведет к увеличению себестоимости очистки, а более низкий — не обеспечит заданную степень очистки газа. В свою очередь, требуемый расход абсорбента определяется рабочей степенью насыщения раствора кислыми компонентами, которая принимается на основании данных о предельной равновесной степени насыщения амина.
Общая емкость равняется сумме химической и физической емкости:
a-i = aix + айф. (3.1)
Предельная химическая емкость в соответствии с приведенными уравнениями реакций H2S и СО2 с аминами равна:
1 — аах — n * aBX = 0, (3.2)
где аах, aBX — химическая емкость по H2S и СО2, моль/моль.
В интервале температур 10−100 °С и парциальных давлений до 2 МПа физическая емкость амина может быть определена по данным о растворимости H2S и СО2 в воде:
ааф = У, а * К/та * С ж0; (3.3)
а, ф = У, * К/т, * Сжо, (3.4)
где у — молярная доля компонента в газе; Сжо — концентрация амина в растворе, моль/л; та, тв — константа фазового равновесия H2S и СО2 в воде, (кмоль/м3)/(кмоль/м3):
т H2S = 0,257 + 0,716 * t; (3.5)
т CO2= 0,6 + 0,028 * t, (3.6)
где К — коэффициент перевода к нормальным условиям К = 10 * p * 273/22,4 * (273 + t), (3.7)
где p — общее давление абсорбции, МПа; t — температура раствора, °С.
Совместное решение этих уравнений позволяет найти выражение для определения минимального удельного расхода поглотителя :
0, 0446 * [Ун 2S +С *[1 + К/С.ж (у H2S/ m H2S ++(1 -ф) * Я * yH2S] (3.9)
+ [(1 -ф) * n * Усо2]/mCO2) — (ан2Sр — n * aCO2) р) где ф — селективность абсорбции H2S из смесей его с С02 ф = (Cyxсо2 /CBX Со2). Для ДЭА — n = 2, для МДЭА — n = 1.
Приведенное уравнение справедливо только при одновременной абсорбции H2S и С02 водными растворами аминов при высоком давлении газа (более 2 МПа) и высоком содержании кислых компонентов.
3.6 Выбор растворителя для очистки газа от сероводорода
В результате обобщения опыта работы промышленных установок фирмы Флюор Корпорейшен мы разработали диаграммы для выбора процессов очистки газа от H2S и (или) С02 (рис.-19). Рабочие площади на этих рисунках очерчивают области применения процессов очистки газа при различных парциальных давлениях H2S и (или) С02 в сыром и очищенном газах. Все диаграммы составлены применительно к условиям очистки газа, в составе которого имеется только H2S и (или) СОа, т. е. они отражают наиболее простые варианты, встречающиеся в практике. Однако, зная характер других примесей и возможные последствия от взаимодействия их с растворителями, эти диаграммы можно использовать и для ориентировочного выбора процесса очистки газа более сложного химического состава (выбранный таким образом вариант может быть положен в основу детального технико-экономического анализа). Ниже изложены рекомендации по выбору процесса.
Рис 18 — Диаграмма для выбора процесса очистки гaзa от СО, в отсутствие H2S: I — физические растворители плюс амины; II — физические растворители или физические растворители плюс амины или горячий поташ; /// - физические растворители; IV — физические растворители или активированный поташ; V — активированный горячий поташ или ингиоированные концентрированные амины; VI — активированный горячий поташ или амины; VII — амины Рис 19 — Диаграмма для выбора процесса очистки газа от H2S в отсутствие С02: I — процессы Эконамин, Селексол, Сульфинол или диэтаноламин высокой степени насыщения; II — физические растворители; III — физические растворители или процесс Сульфинол; IV — диизопропаноламин, процессы Эконамин, Сульфинол или диэтаноламин высокой степени насыщения; V — амины; процессы Стретфорд, Сульфинол или Ветрококк — H2S; VI — процессы Стретфорд или Ветрококк-H8S
1. Очистка газа от С02 в отсутствие H2S (рис.20). Такой случай может быть при переработке природного и других газов. Из диаграммы следует в частности, что при низких парциальных давлениях диоксида углерода в сыром газе (до 0,07 МПа) целесообразно использовать алканоламиновые растворители; при парциальных давлениях от 0,07 до 0,7 МПа — алканоламиновые абсорбенты, горячий поташ или физические растворители; при парциальном давлении более 0,7 МПа — физические растворители, комбинации их с аминами или горячим поташем. Из рис. 19 следует в частности, что при низких парциальных давлениях С02 и H2S в сыром газе (до 0,065 МПа) рекомендуется использовать алканоламиновые растворители или процесс Сульфинол. Начиная от 0,065 до 0,55 МПа для очистки газов целесообразно использовать также активированный горячий поташ, физические растворители и процесс Эконамин. При парциальном давлении H2S и С02 в сыром газе более 0,55 МПа рекомендуются процессы Эконамин и Селексол, а также процессы, в которых используются диэтанодамин и физические растворители.
4. Селективное извлечение из газа H2S в присутствии С02 (см. рис. 20). Такой случай встречается довольно часто — при тонкой очистке газа от сероводорода с низким соотношением H2S: С02 и необходимости получения кислых газов с высоким соотношением H2S: С02 на первой ступени и низким соотношением этих компонентов на второй ступени очистки (в этом случае кислые газы первой ступени предназначаются для производства серы, а кислые газы второй ступени — для производства товарного диоксида углерода). Из рис. 20 следует в частности, что при низких парциальных давлениях кислых газов в исходном сырье процессы Стретфорд и Ветрококк обеспечивают тонкую очистку газа. Однако в связи с известными их недостатками более рационально использовать для этих целей процесс Адип (растворитель диизопропаноламин), область применения которого распространяется от низких до средних парциальных давлений (до 0,04 МПа) — при более высоких парциальных давлениях рекомендуется использовать процессы Ректизол и Селексол.
углеводородный газ очистка этаноламин
3.7 Анализ газовых смесей на учебном газоадсорбционном хроматографе
На газоадсорбционном учебном хромотографе наглядно и достаточно легко можно провести разделение газовой смеси, состоящей из водорода, оксида углерода, метана и воздуха.
Адсорбция этой смеси осуществляется на активированном угле марки АГ, а в качестве газа — носителя применяется углекислый газ, получаемый в аппарате Киппа. Газ носитель вытесняет из колонки компоненты анализируемой смеси в следующем порядке Водород, воздух, оксид углерода, метан. В приемной газовой бюретке, наполненной раствором щелочи, углекислый газ поглащается, что дает возможность замерять объёмы газов, выходящих последовательно из колонки. Зная объём каждого компонента, порядок и время его выделения, строят ступенчатую хромотограмму, по которой и устанавливают количественный состав анализируемой газовой смеси в % (об).
Рис 20 — Схема учебного газадсорбционного хромотографа:
моши углекислого газа анализируемый газ предавливают в колонку. Из колонки газовые компоненты в виде бинарных смесей с углекислым газом направляются в газовую бюретку со щелочью.
Таблица 9
Заключение
1. Изучено физико-химический аспекты аминной очистки углеводородного газа, которые принципиально важным для решения научно-технических задач при эксплуатации, проектировании и реконструкции промысловых установок абсорбционого очистки природного газа.
2. Изучено методику для термодинамических расчетов фазового равновесия при аминовой очистки газа и регенерации абсорбентов.
3. Исследовалось состав и физико-химических свойств исходного сырья и его фракций как одного из важнейших факторов, влияющих на технологический процесс и на качество получаемых продуктов.
4. Определялось состав продукты деструкции гликоля не только в самом МДЭА, но и в водном отгоне. С учетом этих моментов нами создана специализированная опытная установка регенерации абсорбента, которая в принципиальном отношении позволяет моделировать большинство особенностей промысловых установок регенерации абсорбентом.
5. Рассмотрено технологические особенности процессов очистки углеводородных газов технологическом оформлении процесса, обеспечивающего производство товарного газа и сопутствующих продуктов (серы и др.) при высоких технико-экономических показателях.
6. Проведен, теоретических и экспериментальных исследований различных физико-химических аспектов аминовой очистки газа, принципиально важных для решения научно-технических задач, возникающих при эксплуатации, проектировании и реконструкции промысловых установок природного газа.
7. В работе было проведено экспериментальное исследование термохимической деструкции ДЭА и МДЭА под действием СО2 в автоклавах при температуре до 250 °C и парциальном давлении СО2 до 5 МПа.
8. Проведены исследования, позволяющие разработать обобщенную модель процесса абсорбции — десорбции Н и СО2 водными растворами этаноламинов.
Список использованной литературы
1. Каримов И. А. Биздан озод ва обод Ватан? олсин.Т.2.-Т.: Ўзбекистон, 1996.
2. Каримов И. А. Ўзбекистон и? тисодий сиёсатининг устувор йўналишлари. — Т.: Ўзбекистон, 1993.
3. Каримов И. А. «Ўзбекистон демократик ўзгаришларни янада чу? урлаш-тириш ва фу? аролик жамият асосларини шакллантиришнинг асосий йўналишлари». Иккинчи ча? ири? Ўзбекистон Республикаси Олий Мажлисининг тў??изинчи сессиясидаги маъруза. «Адолат» 2002 й. 30 августь.
4. Каримов И. А. Озод ва обод Ватан, эркин ва фаровон? аёт пировард ма? садимиз. Т. 8. Т.: Ўзбекистон, 2000.
5. Хужакулов А. Ф. Хайдаров Л.Р. Влияние деэмульгаторов и магнитного поля на глубину обессоливания узбекистанских нефтей. Ж, «Молодой учёный» Т-7, М., 2013,
6. Маннопов Ш. Н. Хайдаров Л.Р., Сафаров Б. Ж. Термодинамические аспекты применения гликолей системах абсорбционной осушки газа. Бух.ИТИВТ. конф. тезисы докл. магистров. Бухара-2012. 189−191 стр.
7. Киченко Б. В., Пинчук П. Н., В.И., Елистратов В. И. и др. Дополнительные результаты коррозионного контроля в линии регенерации диэтиленгликоля на УКПГ-7 месторождения Медвежье // НТИС. Защита от коррозии и охрана окружающей среды. — М.: ВНИИОЭНГ, 1997. — № 6.
8. Бабиков Ю. М., Рассказов Д. С. Органические и кремнийорганические теплоносители. — М.: Энергия, 1997. — 272 с.
9. Шленский О. Ф., Афанасьев Н. В., Шашков А. Г. Терморазрушение материалов. Полимеры и композиты при интенсивном нагреве. — М.: Энергоатомиздат, 1996. — 288 с.
10. Маслов В. М. Концепции анализа и совершенствования техники и технологии промысловых подготовки и транспорта газа. — Ташкент: Изд-во ФАН Академии Наук Республики Узбекистан, 1997. — 662 с.
11. Lloyd W.G. The Temperature Autoxidation of Dietilene Glycol // J. Amer. Chem. Soc", 1999, V.78, p. 72−73,75.
12. Гликоли и опыт их применения в нефтяной и газовой промышленности (Обзор зарубежной литературы) // Сер. Газовое дело-М.: ВНИИОЭНГ, 1998. — 151 с.
13. Дымент О. Н., Казанский К. С, Мирошников A.M. Гликоли и другие производные окиси этилена и пропилена. — М.: Химия, 1999. — 376 с.
14. Гордиенок Н. И., Фрейдин Б. Г., Проскурина Л. С. Автоокисление диэтиленгликоля // Журнал прикладной химии, 1996. — № 7. — С. 1549- 1554.
15. Гордиенок Н. И., Фрейдин Б. Г. Кинетические данные для прогнозирования допустимых сроков хранения диэтиленгликоля // Журнал прикладной химии, 1996. — № 1. — С. 132−135.
16. Алиева Р. Б., Алиев P.P., Джафаров Ш. Б. Газовые конденсаты сырьё для получения реактивных топлив. Тр. конференции «Эксплуатационные свойства авиационных топлив». 1997, вып. З, ч. II, с. 131−136.
17. Гордиенок Н. И., Фрейдин Б. Г, Гущина Е. А., Хапилова О. М. О реакционной способности низших олигомеров этиленгликоля в реакциях окисления в жидкой фазе // Кинетика и катализ, 2004. — Т. XXYII. — Вып. 6. — С. 1462−1465.
18. Гордиенок Н. И., Фрейдин Б. Г. Относительно связи реакционной способности диэтиленгликоля при автоокислении с прочностью водородных связей // Кинетика и катализ, 1998. — Т. XXIX. — Вып. 5. — С. 1242- 1245.
19. Барков И. И., Шаронов К. Г., Рожнов A.M. и др. К вопросу о смолообразовании и ухудшении массообмена в экстракторе при извлечении ароматических углеводородов диэтиленгликолем // Химия и технология топлив и масел, 1999. — № 12. — С. 25−27.
20. Коуль А. Л., Ризенфельд Ф. С. Очистка газа. — М.: Недра, 1968. — 392 с.
21. Pears R.L., Protr J.E., Lyon G.W. Dry gas to low dew points // International Hydrocarbon Processing, 1998, v. 51, № 12, p. 79−81.
22. Д. Л. Катц, Д. Корнелл, P. Кобояши и др. Руководство по добыче, транспорту и переработке природного газа. — М.: Недра, 1965. — 676 с.
23. Gas Conditioning Fact Book. — Midland, Michigan: The Dow Chemical Company, 2008, 394 p.
24. Жданова H.B., Халиф А. Л. Осушка углеводородных газов. — М.: Химия, 1997. — 192 с.
25. Халиф А. Л., Зиновьева A.M. Регенерация диэтиленгликоля при повы-шенной температуре // Газовая промышленность, 1978. — № 2, — С. 21−22
26. Ланчаков Г. А., Кульков А. Н., Зиберт Г. К. Технологические процессы подготовки природного газа и методы расчета оборудования. — М.: Недра-Бизнесцентр, 2000. — 279 с.
27. Чуракаев A.M. Газоперерабатывающие заводы. Технологические процессы и установки. — М.: Химия, 2001. — 240 с.
28. Анисонян А. А. Очистка диэтиленгликоля и промстоков методом адсорбции. Диссертация на соискание ученой степени кандидата технических наук. — М.: ВНИИГАЗ, 2001. 132 с.
29. Forster R. Extending glycol life in natural gas dehydration systems // Proceedings of the 1998 International Gas Research Conference, San Diego, USA, p. 113−125.
30. Рыбак Б. М. Анализ нефти и нефтепродуктов. — М.: Гостоптехиздат, 1998. — 888 с.
31. Бородина И. И. Интенсификация процесса осушки конденсат-содержащего газа гликолями (на примере головных сооружений газопровода Ставрополь-Москва). Диссертация на соискание ученой степени кандидата технических наук. — Ставрополь: СевКавНИПИгаз, 1999. — 198 с.
32. Жила Н. П., Ключева Э. С. Методы очистки гликолей от тяжелых углеводородов и продуктов деструкции // Обз. информ. Сер. Подготовка и переработка газа и газового конденсата.-М.: ВНИИЭ газпром, 2002. — 40 с.
33. Разработать технологию комплексной очистки гликолевых абсорбентов // Отчет о НИР, филиал ВНИПИгазпереработка, Нижневартовск, 2003. — 72 с.
34. Барков И. И., Шаронов К. Г., Рожнов A.M. и др. Влияние примесей на смолообразование и термическую стабильность диэтиленгликоля // Химия и технология топлив и масел, 1976. — № 9. — С. 35−36.
35. Кэслер X. Осушка природного газа // Газовая промышленность, 2001. — № 7. — С. 48−50.
36. Форстер Р., Гризе К., Кэслер X. Современная технология осушки природного газа на базе ингибиторов старения и путем фильтрации по точке помутнения // Новые высокие технологии, 2001. — Т. 10. — Кн. 2. — С. 231−239.
37. Барков И. И., Шаронов К. Г., Рожнов A.M. и др. Адсорбционная очистка диэтиленгликолей от легких примесей // Химия и технология топлив и масел, 2003. — № 3. — С. 11−13.
38. Киченко Б. В., Пинчук И. Н., Минигулов P.M. и др. К вопросу о коррозии и способах ее ослабления в линиях регенерации диэтиленгликоля на установках осушки газа // НТИС. Защита от коррозии и охрана окружающей среды. — М.: ВНИИОЭНГ, 1997. — № 3.
39. Елистратов А. В., Борисов А. В., Глазунова Л. В., Рудаков В. А. Изменение свойств и окраски растворов гликолей в процессе эксплуатации // Сборник научных трудов «Вопросы эксплуатации северных газовых и газоконденсатных месторождений». — М.: ВНИИГАЗ, 2001. — С. 70−78.
40. Елистратов А. В., Истомин В. А. Оборудование для регенерации гликолей // Газовая промышленность, 2003. — № 3. — С. 58−59.
41. Дю Пар М. С., Руни П. С., Бэкон Т. Р. Сопоставление лабораторных и промышленных данных о химической стойкости смесей МДЭА и ДЭА // Нефтегазовые технологии, 1999. — № 4. — С. 57−58.
42. Дубина Н. И., Ефимов Ю. Н. Технологические и экономические аспекты утилизации вторичного ДЭГА на Уренгойском ГНКМ // Обз. информ. Сер. Подготовка и переработка газа и газового конденсата. — М.: ИРЦ Газпром, 1999. — 55 с.
43. Дубина Н. И., Ефимов Ю. Н. Очистка абсорбента на УКПГ Уренгойского ГНКМ // Обз. информ. Сер. Подготовка и переработка газа и газового конденсата. — М.: ИРЦ Газпром, 2003. — 39 с.
44. Дудов А. Н., Дубина Н. И., Ставицкий В. А., Ефимов Ю. Н., Гузов В. Ф. Влияние изменения основных свойств и характеристик гликоля в процессе осушки газа на эффективность работы основного технологического оборудования УКПГ сеноманской залежи. — В кн. Проблемы освоения месторождений уренгойского комплекса. — М.: Недра, 1998. — С. 88- 100.
45. Чуракаев A.M. Низкотемпературная ректификация нефтяного газа. — М.: Недра, 1989. — 150 с.
46. Гриценко А. И., Истомин В. А., Кульков А. Н. и др. Сбор и промысловая подготовка газа на северных месторождениях России. — М.: Недра, 1999. — 473 с.
47. Елистратов А. В. Результаты экспериментального изучения термостойкости гликолей на опытной установке // Сборник научных трудов «Вопросы эксплуатации северных газовых и газоконденсатных месторождений». — М.: ВНИИГАЗ, 2001. — С. 58−69.
48. Лисовский В. Ф., Виленский Л. М., Гибкин В. И. и др. Перевод на триэтиленгликоль установки осушки газа // Газовая промышленность, 1997. — № 11. — С. 48 — 49.
49. Маннинг В. Р., Вуд Х. С. Основные положения конструирования аппаратов для осушки газа гликолями // Нефть, газ и нефтехимия за рубежом, 1993. — № 9 — С. 46 — 56.
50. Осушка газа под высоким давлением // БТИ ВНИИГАЗ, перевод № 585. — 1998. — 75 с.
51. Гордиенок Н. И., Фрейдин Б. Г. Кинетические данные для прогнозирования допустимых сроков хранения диэтиленгликоля // Журнал прикладной химии, 1999. — № 1. — С. 132−135.
52. Газовая промышленность. Серия: Экономика, организация и управление в газовой промышленности. Обзорная информация. Выпуск 10. М., 1999.
53. Газовые и газоконденсатные месторождения. Справочник. М.: Недра, 1998.
54. Сергиенко С. Р. Углеводородный состав конденсатов газовых месторождений Средней Азии. «Нефтехимия», 1999, т. IX, № 6, с.909−913.
55. Сводные данные по запасам и изменению содержания стабильного конденсата и пропан-бутановых фракций в газе и товарных характеристик конденсатов крупных газоконденсатных месторождений. М.: ВНИИТЦ, 1971.
56. Коротаев Ю. П., Гвоздев Б. П., Каган Я. М. и др. Подготовка газа к транспорту. М.: Недра, 1997.
57. Талдай В. А. Внедрение установок подготовки газа с высокопроизводительным оборудованием. Газовая промышленность, № 7, М., 1998.
58. Абрамович В. Н., Вышеславцев Ю. Ф. Технико-экономические показатели Оренбургского газохимического комплекса в первые годы эксплуатации. М.: ВНИИЭГазпром, 1976.
59. Казаков В. М. Состояние и пути совершенствования технологии добычи и подготовки газа на Оренбургском месторождении. Экспресс-информация. М.: ВНИИЭГазпром, № 11, 1998
60. Берго Б. Г., Гаджиев Н. Г., Фишман Л. Л. Повышение производительности установки получения широкой фракции лёгких углеводородов. М.: ВНИИЭГазпром, № 11, 2005.
61. Рекомендации по обустройству газоконденсатных месторождений на примере Вуктыльского промысла. М.: ВНИИГаз, 2005.
62. Бурных B.C., Ткаченко М. Ф. Повышение гидравлической эффективности магистральных газопроводов Харьковского и Донецкого УМГ. В кн. Развитие газовой промышленности Украинской ССР. М.: Недра, 1970, с. 294.
63. Тихненко Н. Ф. Меры снижения потерь конденсата на газоконденсатных промыслах Кубани. Безопасность труда в промышленности, № 7, 2004.
64. Берго Б. Г., Твердохлебов В. И., Гаджиев Н. Г. и др. Интенсификация промысловой подготовки конденсатсодержащих газов к транспорту. М.: ВНИИЭГазпром, 1985, с. 41.
65. Столяров A.A. Подготовка и переработка газа и газового конденсата. М.: ВНИИЭГазпром, № 2, 2004, с. 12.
66. Гнусова С. П., Берго Б. Г., Фишман Л. Л. Технический прогресс в технологии сбора и стабилизации газового конденсата. М.: ВНИИЭГазпром, 2004, с. 57.
67. Бекиров Т. М. Первичная переработка природных газов. М. Химия, 2004.
68. Власюк А. И. Исследование процесса абсорбции углеводородов в потоке природного газа. Нефтяная и газовая промышленность. Киев, № 5, 1972, с. 45.
69. Грищенко А. И., Коротаев Ю. П., Гвоздёв В. П. и др. Вопросы подготовки газа на промыслах. М.: ВНИИЭГазпром, 2006, с. 95.
70. Патент США № 3 210 949, кл. 62−17, опубл. 12.10. 2007.
71. Euring R.C. New refinery for Delta marshland. «Oil and Gas J.» 2004.65, № 32, p.127.
72. Aalund Leo R. Big heartland refinery ready. «70» S «Oil and Gas J.», 2009, № 17, p.45.
73. Dissimilar streams accommodated. «Oilweek», 2004, 19, № 48, p.40.
74. Martin I.E. Rimby gas plant shows 5-year on-stream factor of 99%. «Oil and Gas J.», 2004. 64, № 3, p.63.
75. Kaybob 3 plant Features unique equipment design. «Oilweek», 2002. 21, № 48, p.50.
76. Strachan gas plant stresses instrumentation monitoring. «Oil and Gas J.» 1971.69, № 45, p.76.
77. Ram River boasts unique design. «Oilweek», 1972, № 49, p.60.
78. Chemical Eng., 2007, № 21, p.160/
79. Новый нефтеперерабатывающий завод в Канаде. Газовое дело, 1969, № 9, с. 29.
80. Lindsey Oil Refinery. «Petroleum Times», 2004, 72, № 1839.
81. Cranfield John. North Sea condensate could become major petrochemical feedstock. «Petrol, and Petrochem. Int.», 2008.13, № 4, p.34.
82. U.K. ponders use North Sea gas liquids. «Oil and Gas J.», 2007. 73, № 43, p.45.
83. Алиев Р. Б., Штейншнайдер M.M., Миргагирова Э. П. Исследование конденсатов Валанжинской залежи Уренгойского месторождения. В кн. «Переработка газа и газового конденсата. Вып. 6. М.: ВНИИЭГазпром, 2004.
84. Кульджаев Б. А., Сергиенко С. Д. Газоконденсаты (состав, направления переработки и использования). Ашхабад.: Ылым, 1999.
85. Возможные варианты переработки газоконденсатов Уренгойского месторождения. В кн. «Переработка газа и газового конденсата». М.: ВНИИЭГазпром, 1996, № 5, с. 16.
86. Гуревич М. Г., Колесникова Л. П., Самозванцева М. С. и др. Исследование индивидуального углеводородного состава конденсатов месторождения Сакар. Изв. АН Туркменской ССР. Серия физико-технических и геологических наук. 1998, № 5, с. 27.
87. Бобылёва A.A., Гуревич М. Г. Ароматические углеводороды в газовых конденсатах. Нефтехимия. 1998, 8, № 4, с. 622.
88. Гаджиев Г. Г., Аббасова H.A., Гамбарова С. А. Каталитическое и термическое превращение узкой фракции 100−125 °С газоконденсата Карадагского месторождения. Ученые записки Азербайджанского государственного университета. Серия «Химия», 1995, № 2, с. 35.
89. Белов К. А. Пиролиз углеводородного Шебеменского конденсата на коксе. «Вестник Харьковского политехнического института». 1996, № 6, с. 71.
90. Каталитический пиролиз газового конденсата Вуктыльского месторождения. Газовая промышленность, 1999, № 11, с. 46.
91. Бадретдинова С. С., Новосёлов C.B., Ломакин С. П. Исследование процесса переработки конденсата нефтяного газа на промысле с получением бензина А-94. Нефтепромысловое дело. 1998, № 2, с. 38.
92. Кессель И. Б., Майоров Б. И., Пак Д. П. Определение качества газовых конденсатов. Газовая промышленность, 1998, № 2, с.22−24.
93. Степанов В. Г., Сытникова Г. П., Агестелян Л. Г. и др. Автобензины из фракций газового конденсата. «Газовая промышленность», 1989, № 1, с.54−57.
94. Разработка предложений по замещению нефтяного сырья в химическом и нефтехимическом производстве газовым углеводородным сырьём из добываемого природного газа. М., 1996.
95. Пескаролло Е., Тротта Ф., Сарати П. Р. и др. Этерификация лёгких бензинов. Нефть, газ и нефтехимия за рубежом. 1997, № 12, с. 46.
96. S. Shelly, К. Foundy. The driver for cleaner burning fuel. Chem. Eng. 1997.101, №l, p.61.
97. Салимов М. К. Производство экологически чистых топлив. Нефтепереработка и нефтехимия. 1998, № 7, с. 61.
98. Томас Дж. X. МТБЭ: его влияние на нефтеперерабатывающую промышленность и перспективы. // Нефтегазовые технологии, 1995, № 1, с. 52.