Газопламенная закалка металлов
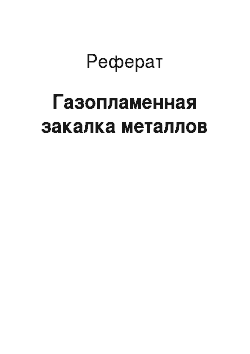
Весьма важной характеристикой режима является выбор скорости относительного перемещения горелки и закаливаемой поверхности. На рис. 132 показано изменение глубины и твердости закаленного слоя при поверхностной закалке валков из стали с содержанием углерода около 0,5% при различной линейной скорости вращения поверхности валка. Из рисунка следует, что при скорости 157 мм/мин закаленный слой… Читать ещё >
Газопламенная закалка металлов (реферат, курсовая, диплом, контрольная)
ПЕРВОЕ ВЫСШЕЕ ТЕХНИЧЕСКОЕ УЧЕБНОЕ ЗАВЕДЕНИЕ РОССИИ МИНИСТЕРСТВО ОБРАЗОВАНИЯ И НАУКИ РОССИЙСКОЙ ФЕДЕРАЦИИ Федеральное государственное бюджетное образовательное учреждение высшего профессионального образования
«НАЦИОНАЛЬНЫЙ МИНЕРАЛЬНО-СЫРЬЕВОЙ УНИВЕРСИТЕТ «ГОРНЫЙ»
Кафедра МиТХИ реферат по дисциплине «Материаловедение и ткм»
на тему «газопламенная закалка металлов»
Автор: студент гр. ПМК-12 ________ /Плотников И.Н./
Шифр: 121 154
Проверил:
преподаватель доцент _____________ /Борисова Л.Г./
Санкт-Петербург
2015г
Содержание Введение Сущность процесса поверхностной закалки Способы газопламенной закалки Закалочное оборудование Техника газопламенной поверхностной закалки Заключение Учебная литература Введение Очень часто к поверхностному слою детали предъявляются иные требования, чем для всей детали в целом. Поверхностное упрочнение детали, повышение твердости, износостойкости может быть получено не только методами наплавки, но и посредством поверхностной термической обработки — закалки.
Поверхностной закалкой улучшаются, как правило, стальные изделия. Принцип поверхностной закалки заключается в нагреве некоторого поверхностного слоя до температуры выше критической АСз с последующим охлаждением этого слоя со скоростью большей, чем критическая скорость охлаждения металла обрабатываемой детали. Для достижения необходимой глубины закаленного слоя требуется его прогрев до температуры 820−900° С, в зависимости от состава стали, с последующим быстрым охлаждением струей воды или воздуха. Такой нагрев осуществляется либо индукционным нагревом токами высокой частоты (высокочастотная поверхностная закалка), либо пламенем (газопламенная поверхностная закалка). При газопламенной закалке для получения необходимой температуры закалки на некоторой глубине (обычно 3−5 мм) сама поверхность должна быть нагрета примерно до 1000−1150° С.
Высокочастотная закалка требует применения специального оборудования и является целесообразной в основном при массовом производстве. Для газопламенной поверхностной закалки используются простейшие приспособления и аппаратура. Такая закалка является широко применяемым производственным процессом.
В качестве источника нагрева при газопламенной закалке используется в основном ацетилено-кислородное пламя, хотя могут применяться и заменители ацетилена. Степень нагрева поверхностного слоя регулируется мощностью пламени и длительностью его воздействия. Необходимое распределение температур к моменту начала охлаждения показано на рис. 129. Охлаждение производится водой при ее различной начальной температуре или различными водными растворами.
Газопламенной закалкой могут обрабатываться все углеродистые, низколегированные стали, подвергаемые обычной закалке, и, кроме того, стали с малым содержанием углерода и чугуны.
Сущность процесса поверхностной закалки Твердость поверхностного закаленного слоя при газопламенной закалке, как правило, выше твердости, получаемой при общей закалке, примерно на НВ 50 вследствие большей скорости охлаждения (сердцевина детали, будучи холодной, увеличивает скорость охлаждения). Так, например, при поверхностной закалке углеродистой стали с 0,15% С твердость достигает НВ 250; при 0,3% С — НВ до 400; с 0,4−0,45% С — НВ 550 и с 0,65% С — НВ до 650−700. В связи с характером нагрева и охлаждения твердость закаленного слоя по направлению от поверхности к внутренним частям детали обычно изменяется в достаточной степени плавно (рис. 129, в). Однако в случае закалки легированных сталей, особенно при значительном перегреве поверхности (рис. 129, б, кривая 2), большая скорость охлаждения может привести к снижению твердости на поверхности в связи с сохранением остаточного аустенита (рис. 129, в, кривая 2). Это следует рассматривать как брак, вызываемый неправильным режимом закалки.
При поверхностной закалке деформации и напряжения меньше, чем при общей закалке. Так, при общей закалке изделия длиной 1600 мм и сечением 370X 190 мм величина деформации составляет 1−1,3 мм, а при поверхностной закалке она снижается до 0,08−0,25 мм. В связи с этим удается получить поверхностную закалку чугуна без трещин, которые всегда имеют место при общей закалке.
Газопламенная закалка является средством повышения качества и срока службы таких изделий, как зубчатые колеса, шестерни, прокатные валки, шпиндели, муфты, направляющие станков, шкивы и др.
Способы газопламенной закалки В зависимости от воздействия пламенного нагрева и охлаждения существуют четыре способа газопламенной закалки (рис. 130), характеризуемые циклическими и непрерывными процессами.
Циклические процессы заключаются в нагреве сначала всего объема металла, подлежащего закалке, и последующем охлаждении при выключенном или отведенном в сторону пламени. При циклическом процессе применяются два способа: стационарный — для закалки концов рельсов, зубьев цепных колес, клапанов и подобных им деталей и быстрого вращения — для тел вращения с небольшой шириной закаливаемой части и при небольшом диаметре (цапфы валов, осей и пр.).
Циклические процессы дают равномерно закаленный слой с одинаковой твердостью, особенно при применении способа быстрого вращения, когда изделие, вращаясь со скоростью 75−150 об/мин, перед охлаждением равномерно прогревается по всей поверхности, проходящей в области воздействия пламени.
Непрерывные процессы характеризуются единовременным воздействием источника нагрева и охлаждающей струи, причем охлаждение осуществляется с некоторым запаздыванием по сравнению с нагревом.
Непрерывные процессы закалки используются в виде непрерывно-последовательного и комбинированного способов.
Непрерывно-последовательный способ характеризуется перемещением пламени и охлаждающего устройства относительно обрабатываемого изделия. При этом происходит закалка полосы по ширине примерно равной ширине закалочной горелки и зоны воздействия охлаждающих струй. Закалку широкой поверхности изделия в один проход обеспечить довольно трудно (горелка должна быть слишком широкой и большой мощности; изделие при одновременном нагреве всей поверхности получит значительные коробления). Поэтому закалку выполняют последовательными проходами по ряду полос. Однако при этом нужно учитывать, что между этими закаленными полосами будут полоски отпуска в результате вторичного нагрева при прохождении пламени по соседней зоне.
Таким же образом можно закаливать поверхность тел вращения большого диаметра (например, шкивов и пр.) при их относительно медленном вращении, неподвижном пламени и охлаждающем устройстве. Однако и в этом случае получается смягченная отпуском полоска в месте замыкания начала и конца закаливаемой поверхности.
Несмотря на некоторые недостатки закаленного слоя, закалка непрерывно-последовательным способом применяется достаточно широко в различных видоизменениях.
Комбинированный способ совмещает линейное перемещение закалочного устройства (пламени и охлаждающих струй) и вращение закаливаемой детали. Этот способ получил наибольшее применение для деталей большой длины, причем детали малого диаметра закаливают обычно в горизонтальном положении, а детали большего диаметра — в вертикальном.
При использовании в комбинированном способе быстрого вращения твердость закаленного слоя получается достаточно равномерной.
Закалочное оборудование Закалочное оборудование включает закалочные горелки, охлаждающие устройства и станки, позволяющие механизировать перемещения горелки и охлаждающего устройства относительно закаливаемой детали.
Закалочные горелки, так же как и сварочные, представляют собой инжекторные горелки обычно со сменными наконечниками, позволяющими регулировать мощность пламени в достаточно широких пределах. Сменные наконечники присоединяются к рукоятке (стволу) горелки с помощью накидной гайки.
Форма мундштуков закалочных горелок должна соответствовать профилю закаливаемой детали. На рис. 131 показаны горелки со сменными наконечниками для закалки плоских поверхностей и тел вращения, а также для закалки шестерен с различным модулем.
поверхностный закалка газопламенный деталь Мундштуки закалочных горелок могут быть многосопловыми или щелевого типа. Последние являются менее устойчивыми в работе. При многосопловых горелках для обеспечения достаточной равномерности прогрева поверхности закаливаемого изделия шаг сопел lс в зависимости от диаметра сопла dc должен быть равен 2,5dc.
Общая мощность пламени закалочного наконечника при непрерывно-последовательном способе может быть определена по формуле
Va = vbqk
где Va — расход ацетилена в м3/ч;
v — скорость относительного перемещения детали и горелки в см/мин;
b — ширина закаливаемой за один проход поверхности в см;
q — удельный расход горючего газа в л/см2 (для ацетилена 0,4−0,9);
k = 6.10−2 — коэффициент перевода размерности л/мин в м3/ч.
Общее количество ацетилено-кислородной смеси Vc, учитывая обычное при поверхностной закалке соотношение B = VK/Va = 1,2−1,3, составляет примерно 2,5Va, а суммарная площадь выходных отверстий наконечника (в см2):
где щ — скорость истечения смеси в м/сек;
m — коэффициент истечения равный 0,9−0,95.
Диаметры отверстий, расход газов и скорости истечения, обычно применяемые в закалочных горелках, представлены в табл. 28.
Устройства для охлаждения обычно многоструйные и называются разбрызгивателями. Они изготовляются либо отдельно от горелки, либо конструктивно представляют одно целое с мундштуком. В последнем случае закалочная жидкость одновременно служит и для охлаждения мундштука горелки. При обычных режимах закалки расход воды через разбрызгиватели составляет примерно 0,65−0,9 л/см2.
Станки для относительного перемещения закалочного устройства и закаливаемой детали должны поддерживать установленный режим.
Станки для закалки могут быть универсальными и специализированными. Универсальные станки рационально использовать при индивидуальном и мелкосерийном изготовлении различных деталей, проходящих поверхностную закалку, а также при выполнении ремонтных работ. Специализированные станки являются наиболее рациональными при большом объеме выполнения однотипных работ в массовом и крупносерийном производстве.
В ряде случаев предприятия сами изготовляют такие станки, используя для этого станины и другие узлы различных металлообрабатывающих станков, в частности токарных.
Техника газопламенной поверхностной закалки Техника выполнения газопламенной поверхностной закалки определяется выбором способа закалки, оборудования и режима закалки, зависящего от состава закаливаемой стали, формы и размеров обрабатываемого изделия.
Выбор режима закалки, в свою очередь, включает:
1) выбор мощности пламени;
2) выбор расстояния между мундштуком горелки и закаливаемой поверхностью;
3) выбор скорости относительного перемещения горелки и закаливаемой детали (или продолжительности нагрева при циклических процессах закалки);
4) выбор расстояния между средней зоной пламени и охлаждающей струей (или времени между прекращением нагрева и пуском охлаждающей струи при циклических процессах); подбор необходимой температуры и состава охлаждающей среды.
Выбор мощности пламени описан в разделе сварки. Расстояние от сопел горелки до закаливаемой поверхности устанавливается так, чтобы ядро пламени отстояло от нагреваемой поверхности примерно на 2−3 мм.
Весьма важной характеристикой режима является выбор скорости относительного перемещения горелки и закаливаемой поверхности. На рис. 132 показано изменение глубины и твердости закаленного слоя при поверхностной закалке валков из стали с содержанием углерода около 0,5% при различной линейной скорости вращения поверхности валка. Из рисунка следует, что при скорости 157 мм/мин закаленный слой получается глубиной меньше 1 мм, а местами повышения твердости вообще не получается (штриховая линия). Меньшие скорости дали в этом случае более устойчивые результаты. В зависимости от технических требований к величине слоя закалки в приведенном примере могут быть приняты линейные скорости вращения от 45 до 25 мм/мин.
Расстояние от средней зоны пламени до струи охлаждающей жидкости берется в зависимости от состава закаливаемого материала и составляет обычно 12−25 мм.
При циклических процессах закалки время между концом нагрева и началом охлаждения жидкостью обычно составляет 5−10 сек. Степень необходимого нагрева устанавливается экспериментально, и уточненный режим поддерживается либо визуально, либо по времени нагрева.
Выбор охлаждающей жидкости и ее удельного расхода зависит от химического состава закаливаемого материала. В большинстве случаев для этих целей применяется вода при температуре 18−35° С и удельном расходе до 1 л/см2.
Для высокого качества закаливаемых деталей перед закалкой необходима тщательная очистка поверхности щетками, пескоструйным или химическим способом. При этом на деталях не допускаются поверхностные дефекты, наличие окислов и краски. Острые углы на деталях во избежание подплавления или образования трещин должны предварительно заваливаться в виде фасок. Контроль качества закалки сводится к наружному осмотру закаленной поверхности, выявлению трещин и определению ее твердости. При подборе режимов также проверяется и глубина закаленного слоя.
При правильном выполнении поверхностной закалки эксплуатационная стойкость деталей значительно повышается. Например, по данным сопоставления закаленных и незакаленных узлов и деталей металлургического оборудования стойкость закаленных повышается в два-пять раз.
Заключение
Газовая закалка приводит к значительным выигрышам в качестве, которые могут свободно превратиться такие экономии, как снижению процентного содержания брака или уменьшению количества операций после обработки. Однако применение газопламенной закалки поверхности ограничено отсутствием уверенности в получении равномерной твердости по всей длине поверхности, а из-за отпуска закаленной зоны при перекрытии ее во время закаливания следующей зоны.
Учебная литература
1. http://mash-xxl.info/info/768 882/
2. http://osvarke.info/gazobrabotka/apparatura.html
3. http://metallicheckiy-portal.ru/articles/obrabotka/termo/poverxnostnaa_gazoplamennaa_zakalka