Влияние качества дизельного топлива на технико-экономические показатели работы дизельного двигателя
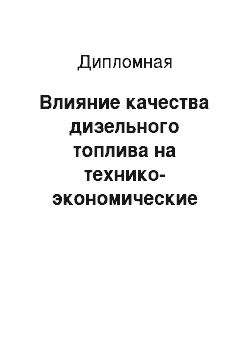
Рисунок 1.2 Зависимость вязкости дизельных топлив от температуры: 1 — летнее 2 — смешанное, 3 — зимнее, 4 — арктическое При уменьшении вязкости количество дизельного топлива, просачивающегося между плунжером и втулкой, возрастает, в результате снижается подача насоса. Перевод двигателя на топливо с меньшей плотностью и вязкостью может привести к прогару головок поршня, в связи, с чем требуется… Читать ещё >
Влияние качества дизельного топлива на технико-экономические показатели работы дизельного двигателя (реферат, курсовая, диплом, контрольная)
Содержание топливо двигатель дизельный сгорание Введение
1. Топливо и химические реакции при его сгорании
1.1 Общие сведения о смесеобразовании топливовоздушной смеси
1.2 Структура и состав дизельного топлива
1.3 Сведения о свойствах дизельного топлива
1.4 Нормативы качества дизельных топлив и тенденции их изменения
1.5 Химические реакции при сгорании топлива
1.6 Описание производственных услуг
1.7 Технические характеристики двигателя ЗМЗ 5143
2. Особенности конструкции
2.1 Конструкция основных элементов системы питания дизельного двигателя
2.2 Оценка системы питания и влияние ее на мощность двигателя
2.3 Влияние состояния ЦПГ и ГРМ на мощность двигателя
2.4 Газораспределительный механизм (ГРМ)
3. Методика проведения экспериментальных исследований по оценке состава ОГ при различных видах топлива
3.1 Анализ испытания дизельных топлив
3.2 Выбор оборудования для исследований
3.3 Методика проведения эксплуатационных испытаний
3.4 Методика построения экспериментальных зависимостей
4. Результаты экспериментальных исследований
4.1 Влияние дизельного топлива марки Л-0,5−62 на мощностные показатели двигателя
4.2 Влияние качества дизельного топлива марки З-0,2−35 на мощностные показатели двигателя
5. Конструкторская разработка прибора для проверки герметичности топливной системы
5.1 Обоснование целесообразности разработки прибора для проверки герметичности топливной системы низкого давления
5.2 Описание конструкции и принцип действия прибора для проверки герметичности топливной системы
5.3 Прочностные расчеты
6. Охрана труда
6.1 Общее положение по охране труда
6.2 Инструкции по технике безопасности при работе с прибором для проверки герметичности топливопровода низкого давления дизельного двигателя
6.3 Пожарная безопасность
7. Охрана окружающей среды
7.1 Воздействие отработавших газов на окружающую среду
7.2 Мероприятия по снижению вредного воздействия автотранспорта на окружающую среду
8. Экономическая эффективность конструкторской разработки
8.1 Затраты на изготовление прибора для проверки герметичности топливной магистрали низкого давления
8.2 Годовой экономический эффект от применения прибора для проверки герметичности топливной магистрали низкого давления
8.3 Экономическая эффективность основных показателей исследовательской работы Заключение Список использованной литературы
Введение
В соответствии с аграрной политикой нашего государства в сельскохозяйственное производство поставляется высокопроизводительная техника. Практически все мощноскоростные тракторы, самоходные уборочные машины и автомобили оснащают дизельными двигателями.
Долговечность, надежность и экономичность работы сельскохозяйственных машин во многом зависит от правильной работы топливоподающей аппаратуры автотракторных дизелей. Дизельная топливная аппаратура должна обеспечить равномерную по цилиндрам двигателя подачу топлива, величина которой зависит от загрузки двигателя. Топливо поступает в цилиндр двигателя в строго определенное время и под необходимым давлением.
Промышленность выпускает в настоящее время несколько типов топливоподающей аппаратуры. Широко применяются рядные топливные насосы, разновидностью которых являются малогабаритные унифицированные насосы распределительного типа для двух-, четырехцилиндровых дизельных двигателей, а так же многорядные насосы для двух-, четырех-, шести-, восьмицилиндровых дизельных двигателей. Одноплунжерные насосы распределительного типа по габаритам и весомым показателям значительно лучше рядных.
Практика показывает, что далеко не все предприятия и ТОО расходуют топливо и смазочные материалы в соответствии с технически обоснованными нормами. Основной причиной является технически неграмотная эксплуатация топливоподающей аппаратуры. Эксплуатационники часто не знают назначение отдельных элементов топливной аппаратуры, изменение их параметров в работе и влияние их на показатели работы дизелей. Подбор деталей в комплект и регулировку аппаратуры часто проводят не квалифицированно, в результате чего расход топлива на единицу работы возрастает на 15−30%.
Составной частью дизельной топливной аппаратуры являются прецизионные детали, которые отличаются высокой точностью изготовления. Зазоры в прецизионных парах очень малы (от 0,006 до 0,0006 мм), поэтому дизельное топливо должно очень тщательно очищаться от воды и механических примесей.
С целью повышения безотказности и более эффективного использования дизелей, снижения затрат труда и средств на техническое обслуживание и ремонт предъявляются высокие требования к качеству и своевременности диагностирования технического состояния, а так же проведения регулировок топливной аппаратуры.
1. Топливо и химические реакции при его сгорании
1.1 Общие сведения о смесеобразовании топливовоздушной смеси В двигателях внутреннего сгорания тепловая энергия, необходимая для совершения механической работы, получается в результате химических реакций между вводимым в цилиндр топливом и кислородом воздуха. Время, в течение которого протекают эти реакции в современных быстроходных двигателях, весьма ограниченно и составляет сотые и даже тысячные доли секунды. Длительность процесса подготовки смеси топлива с воздухом к химической реакции зависит от типа смесеобразования и тактности двигателя.
Способы образования топливовоздушной смеси, и протекание химических реакций обуславливают ряд требований, предъявляемых к топливам, применяемых в двигателях внутреннего сгорания. В двигателях с внутренним смесеобразованием (дизели) топливо подается непосредственно в цилиндр. Начало подачи топлива происходит в конце такта сжатия и незначительно опережает момент воспламенения, а часть топлива вводиться в процессе сгорания. В этих условиях нужно обеспечить хорошее распыливание топлива, при котором образующиеся мельчайшие капли смешиваются с находящимся в цилиндре воздухом.
Необходимо, чтобы период процесса сгорания топлива в цилиндре был небольшим.
Кроме указанных основных требований необходимо, чтобы применяемое топливо:
1 Обеспечивало быстрый и надежный запуск двигателя независимо от температуры окружающей среды;
2 Позволяло осуществить процесс сгорания без образования нагара и кокса на поверхностях камеры сгорания;
3 Способствовало уменьшению износов и коррозии зеркала цилиндра, поршневых колец и поршня;
4 Обеспечивало условия полного и своевременного сгорания и снижения количества токсических составляющих в продуктах сгорания.
Смесеобразование в дизелях осуществляется в конце такта сжатия и начале такта расширения. Процесс занимает короткий промежуток времени, соответствующий 20−60° поворота коленчатого вала. Процесс смесеобразования в дизеле имеет следующие особенности:
Смесеобразование протекает внутри цилиндра и в основном осуществляется в процессе впрыскивания топлива;
По сравнению с карбюраторным двигателем продолжительность смесеобразования в несколько раз меньше;
Горючая смесь, приготовленная в условиях ограниченного времени, характеризуется большой неоднородностью, т. е. неравномерным распределением топлива по объему камеры сгорания.
Смесеобразование, начинающееся с момента поступления топлива в цилиндр, состоит из процессов распыления топлива на мельчайшие частицы, заполнения распыленными частицами пространства камеры сгорания, испарения частиц и смешивания образующихся паров с воздухом.
В современных автомобильных и тракторных двигателях находит применение объемное, объемно-пленочное, пленочное, вихрекамерное и предкамерное смесеобразование.
1.2 Структура и состав дизельного топлива В двигателях внутреннего сгорания применяют жидкие и газообразные топлива. Главным источником для получения жидкого топлива является природная нефть. В результате ее прямой перегонки и специальной вторичной переработки получают бензин, лигроин, дизельное топливо и т. д. Жидкое топливо состоит в основном из смеси углеводородов, которые отличаются по групповому составу, определяющему содержание в нем отдельных элементов. Групповой состав характеризует содержание в топливе углеводородов различных гомологических рядов. Он определяет основные физико-химические свойства топлива и влияет на процессы испарения, воспламенения и горения топлива.
Основным составляющим нефти являются углеводороды: парафины (алканы) вида СпН2п+2, нафтены (цикланы) вида СпН2п и ароматические углеводороды вида СпН2п б и СпН2п 12. В среднем в нефти содержится 84−85% углерода и 12−14% водорода, остальное составляют азот, кислород и сера. Углеводороды, входящие в состав жидких топлив, имеют в одной молекуле 5−30 атомов углерода (в бензине 5−12, в керосине и дизельном топливе — до 30). В дизельном топливе более ценными компонентами являются Н-алканы, обладающие более низкой температурой самовоспламенения, которая, кроме того, снижается с укрупнением молекулы. Поэтому в качестве дизельного топлива применяют более тяжелые фракции нефти.
1.3 Сведения о свойствах дизельного топлива Дизельное топливо предназначено для двигателей внутреннего сгорания с воспламенением рабочей смеси от сжатия (дизелей). Представляет смесь углеводородов керосиновой, газойлевой и соляровой фракций, получаемых в результате перегонки нефти, с температурой кипения 180−360°С и плотностью 0,79−0,86 г/см3.
Качество дизельного топлива.
Важнейшими эксплуатационными показателями качества дизельных топлив являются воспламеняемость, фракционный состав, температуры помутнения и застывания, коксуемость и т. п.
Воспламеняемость. Воспламеняемость — важнейшее свойство дизельного топлива. Определяется периодом задержки самовоспламенения (ПЗС), который складывается из времени, затрачиваемого на распад топливной струи на капли, частичное их испарение и смешение паров топлива с воздухом (физическая составляющая), и времени, необходимого для завершения химических реакций и формирования очагов самовоспламенения (химическая составляющая).
Температура самовоспламенения — наименьшая температура, при которой топливо самовоспламеняется без открытого источника огня. Чем ниже температура самовоспламенения дизельного топлива, тем меньше период задержки воспламенения (ПЗВ), тем равномернее процесс сгорания и мягче работа двигателя. Процессу самовоспламенения горючей смеси в дизеле предшествует интервал времени — период задержки воспламенения, который продолжается от начала подачи топлива в камеру сгорания (КС) до момента его воспламенения. За время ПЗВ происходит целый ряд физико-химических процессов: распыление топлива, перемешивание его с воздухом, нагревание до температуры сжатого воздуха и испарение. Одновременно с этими процессами протекают сложные химические реакции многостадийного окисления углеводородов. В горючей смеси образуются неустойчивые кислородосодержащие соединения, альдегиды и т. п., которые затем распадаются. Распад сопровождается выделением части (10−15%) тепла и слабым холодным голубым свечением. В результате предпламенных реакций выделяется теплота, повышается температура горючей смеси, увеличивается скорость химических реакций, холоднопламенный процесс переходит в горючепламенный, происходят самовоспламенение и горение топлива. Дизельное топливо состоит в основном из парафиновых (П), нафтеновых (Н) и ароматических (А) углеводородов. Наиболее склонны к окислению и самовоспламенению парафиновые углеводороды. Наиболее устойчивые к окислению ароматические углеводороды.
Если ПЗВ слишком велик, то смесь воспламеняется с опозданием, при этом в цилиндре дизеля накапливается и воспламеняется большая порция топлива.
Это вызывает резкое нарастание давления, возникают стуки, т. е. дизель работает «жестко», увеличиваются износ деталей, прорыв газов в картер двигателя, расход топлива и др. На рисунке 1.1 приведена развернутая диаграмма дизельного двигателя.
Рисунок 1.1. Развернутая диаграмма дизельного двигателя.
1,2 — период задержки воспламенения; 2, 3 — фаза быстрого горения; 3, 4 — фаза медленного горения; 4 и далее — догорание на линии расширения. O — угол опережения впрыска.
Оценкой самовоспламеняемости топлива в дизеле является цетановое число (ЦЧ), зависящее главным образом от химического состава топлива. Значение ЦЧ дизельного топлива равно содержанию цетана (в процентах от объема) в смеси с альфаметилнафталином, эквивалентной по воспламеняемости испытуемому топливу. Моторный метод определения ЦЧ дизельного топлива по методу совпадения вспышек проводится на специальной дизельной одноцилиндровой установке ИТ9−3 или ИТ9-ЗМ с переменной степенью сжатия при стандартных условиях (ГОСТ 3122−67). Испытание заключается в сравнении самовоспламеняемости испытуемого дизельного топлива и эталонного. Подбирают смесь соответствующего состава до тех пор, пока воспламеняемость испытуемого топлива совпадет с известной для эталонного.
Фракционный состав. Фракционный состав наряду с цетановым числом является одним из наиболее важных показателей качества дизельного топлива. Он оказывает влияние на расход топлива, дымность выпуска, легкость пуска двигателя, износ трущихся деталей, нагарообразование и закоксовывание форсунок, пригорание поршневых колец. Влияние фракционного состава топлива на рабочий процесс дизеля во многом зависит от типа смесеобразования в двигателе. Чем выше давление, температура и интенсивность вихревого движения заряда в камере сгорания двигателя, тем меньше сказывается влияние фракционного состава топлива на процесс сгорания. Для быстроходных дизелей требуется топливо более легкого фракционного состава, чем для тихоходных. О фракционном составе дизельного топлива судят по результатам перегонки топлива, осуществляемой в лабораторных условиях на стандартной аппаратуре. Наиболее важными точками фракционного состава являются значения температуры выкипания 10, 50, 90 и 96% топлива. Температура выкипания 10% топлива характеризует наличие легких фракций топлива, которые определяют его пусковые свойства. За температуру начала кипения (t H. K) принимают температуру пара, при которой в холодильник стандартного прибора падает первая капля конденсата. Для нормального запуска холодного двигателя необходимо, чтобы температура выкипания 10% топлива была не выше 140−160°С. Температура выкипания 50% топлива (средняя испаряемость) характеризует рабочие фракции топлива, которые обеспечивают прогрев, приемистость и устойчивость работы двигателя, а также плавность перехода с одного режима на другой. Для обеспечения нормальной работы двигателя эта точка должна лежать в пределах 250−280°С. Полнота испарения топлива в двигателе характеризуется температурой выкипания 90% и 96% топлива. При слишком высоких значениях этих температур хвостовые фракции не успевают испаряться, они остаются в жидкой фазе в виде капель и пленки, которые, стекая по стенкам цилиндра, приводят к повышенному нагарообразованию, разжижению масла и форсированному износу. Температура выкипания 90% для летних топлив обычно находится в пределах 320−340°С, а 96% - в пределах 340−360°С.
Температуры помутнения и застывания. Важными эксплуатационными характеристиками дизельного топлива также являются его низкотемпературные свойства, характеризующие подвижность топлива при отрицательной температуре. В дизельном топливе содержатся растворенные парафиновые углеводороды, которые при понижении температуры кристаллизуются. Низкотемпературные свойства оцениваются по значениям температуры помутнения и застывания.
Температура помутнения — это температура, при которой меняется фазовый состав топлива, так как наряду с жидкой фазой появляется твердая. При этой температуре топливо в условиях испытания начинает мутнеть. При помутнении дизельное топливо не теряет текучести. Размеры кристаллов таковы, что они проходят через элементы фильтров тонкой очистки, образуя на них тонкую парафинистую пленку. Нарушение подачи топлива из-за его помутнения возможно при пуске и прогреве дизеля. Для обеспечения нормальной эксплуатации двигателя необходимо, чтобы температура помутнения дизельного топлива была ниже температуры окружающего воздуха.
Температура застывания — это температура, при которой топливо полностью теряет подвижность. Температура застывания ниже температуры помутнения на 5−10°С. При понижении температуры растущие кристаллы парафиновых углеводородов образуют пространственную решетку, внутри ячеек, которой находятся жидкие углеводороды топлива. При температуре застывания топлива кристаллическая структура настолько упрочняется, что топливо теряет текучесть и приобретает студнеобразный вид. Для обеспечения нормальной работы дизельного двигателя необходимо, чтобы температура застывания топлива была на 8−12°С ниже температуры окружающего воздуха.
Вязкость. Определяют процессы испарения и смесеобразования в дизеле, так как от них зависит форма и строение топливного факела, размеры образующихся капель, дальность проникновения капель топлива в камеру сгорания. Более низкая плотность и вязкость обеспечивают лучшее распиливание топлива; с повышением указанных показателей качества увеличивается диаметр капель и уменьшается полное их сгорание, в результате увеличивается удельный расход топлива, растет дымность отработавших газов. Вязкость топлива влияет на наполнение насоса и на утечку топлива через зазоры плунжерных пар. С увеличением вязкости топлива возрастает сопротивление топливной системы, уменьшается наполнение насоса, что может привести к перебоям в его работе. В таблице 1.1 приведена зависимость подачи топлива насосом от температуры топлива Таблица 1.1
Зависимость подачи топлива насосом от температуры топлива
Температура топлива, °С | +10 | — 30 | — 40 | — 50 | |
Подача насоса, кг/ч | |||||
Ниже приведена зависимость вязкости дизельных топлив от температуры:
Рисунок 1.2 Зависимость вязкости дизельных топлив от температуры: 1 — летнее 2 — смешанное, 3 — зимнее, 4 — арктическое При уменьшении вязкости количество дизельного топлива, просачивающегося между плунжером и втулкой, возрастает, в результате снижается подача насоса. Перевод двигателя на топливо с меньшей плотностью и вязкостью может привести к прогару головок поршня, в связи, с чем требуется регулировка топливной аппаратуры. Коксуемость топлива Одно из важных эксплуатационных свойств дизельного топлива характеризуется чистотой двигателя и топливоподающей аппаратуры. При сгорании топлива в двигателе образуются нагар на стенках камеры сгорания и впускных клапанах, а также отложения на распылителях и иглах распылителей форсунок. На стенках камеры сгорания, днищах поршней и выпускных клапанах нагар твердый, темного цвета, а на распылителях и иглах распылителей форсунок он мягкий, смолистый, желтоватого цвета, иногда в виде лаковой светло-коричневой пленки. Отложение нагара на стенках камеры сгорания ухудшает отвод теплоты в систему охлаждения двигателя, а на выпускных клапанах приводит к их закоксовыванию и, следовательно, неправильной посадке тарелки клапана на седло. В результате такой неисправности раскаленные газы утекают, и посадочные поверхности клапана и седла обгорают; в отдельных случаях возможно зависание клапана. Нагарообразование в двигателе зависит от следующих показателей применяемого дизельного топлива: коксуемости, содержания фактических смол и серы, фракционного состава, количества непредельных и ароматических углеводородов и зольности.
Коксуемость — это свойство топлива при нагревании без доступа воздуха образовывать углистый осадок — кокс. Коксуемость определяют для 10%-ного остатка после предварительной перегонки дизельного топлива. Коксуемость 10%-ного остатка топлива зависит от его фракционного состава и содержания смолисто-асфальтовых соединений и для дизельного топлива должна быть не более 0,3%. Повышение значения этого показателя вызывает увеличение нагара в двигателе.
1.4 Нормативы качества дизельных топлив и тенденции их изменения Топлива для дизельных двигателей автомобилей вырабатываются в основном по ГОСТ 305–82 в виде трех марок: «Л» — летнее, применяемое при температуре воздуха выше 0 °C; «З» — зимнее, двух видов: для применения до -20°С и для применения до -30°С; «А» — арктическое, применяемое до -50°С. Топлива характеризуются следующими основными показателями: цетановое число — не менее 45, содержание серы — не менее 0,50 или 0,20% для разных видов, температура застывания от «не менее минус 55» для арктического до «не менее минус 10» для летнего, плотность от «не более 0,830 г/смЗ» для арктического до «не более 0,860 г/см3» для летнего топлив, содержание полиароматических соединений и смазывающая способность топлив — не нормируются. В значительно меньших количествах выпускаются дизельные топлива по различным ТУ. Зимние дизельные топлива с депрессорными присадками (ДЗП) по ТУ 38.101 889 получают на базе летнего топлива добавлением незначительного количества присадок. Данное топливо рекомендуется к применению при температуре воздуха не ниже -15°С. Обладает недостатком: склонно при охлаждении топлива ниже определенной температуры или при длительном его хранении к осаждению парафинов на дно емкости, что затрудняет его дальнейшее использование. По остальным характеристикам подобно летнему топливу по ГОСТ 305–82. Экологически чистое дизельное топливо по ТУ 38.1 011 348−2003. По данным ТУ выпускают топлива летнее марки ДЛЭЧ, зимнее марки ДЗЭЧ и арктическое марки ДАЭЧ. В сравнении с ГОСТ 305 характеризуются установлением 5 видов с более низким содержанием серы: от «не более 0,10 массовых %» до «не более 0,001 массовых %». По содержанию серы экологически чистые топлива полностью соответствуют требованиям как действующего, так и будущего европейского стандарта по содержанию серы в дизельных топливах. Городское дизельное топливо (ТУ 38.401 58−170−96). Основное отличие от экологически чистого дизтоплива — улучшенное качество благодаря использованию присадок (летом антидымной, зимой — антидымной и депрессорной), которые снижают дымность и токсичность отработавших газов на 30−50%.
Европейские требования к качеству дизельных топлив более жесткие. Так требования EN-590 1993 года отличаются от требований ГОСТ 305–82 более высокими требованиями к цетановому числу «не менее 49». Общемировая тенденция изменения требований к качеству дизельных топлив следующая: увеличение цетанового числа, уменьшение плотности и содержания серы, нормирование полиароматических соединений. С 2000 года в Европе действуют нормы Евро-3, устанавливающие требования по цетановому числу «не менее 51», по сере «не более 0,035 массовых %», плотности «не более 0,845 г/см3» при нормировании содержания полиароматических соединений «не более 11% объёма». Эти требования реализованы и в российских ТУ 38.40 158 296. В 2004;5 гг. в Европе вводятся требования Евро-4, дополнительно снижающие норматив по содержанию серы до «не более 0,005 массового %» .
Значительно различаются по свойствам и качеству отечественные дизельные топлива. В частности, по массовому содержанию серы — по ГОСТ 305–82 вырабатываются два вида: с 0,5% серы и около 90% с 0,2% серы для автомобильной техники не выше Евро-1. Остальное по ряду ТУ с содержанием серы 500 и 350 мг/кг для дизельных автомобилей Евро-2 и Евро-3. В перспективе должны вырабатываться дизтоплива по новому ГОСТ Р 52 368−2005 с содержанием серы 350, 50 и 10 мг/кг — для автомобилей, соответственно, отвечающих требованиям Евро-3, Евро-4 и Евро-5.
С таким широким диапазоном ассортимента и показателей топлива для автомобильной техники на мировом рынке уже не сталкиваются в США, Японии, странах ЕС и в ряде других развитых стран мира, которые за последние десять лет практически полностью перешли на выпуск бензиновых и дизельных автомобилей нового поколения с применением регулируемых систем нейтрализации отработавших газов, систем электронного управления двигателем и его топливной аппаратурой с бортовой компьютерной диагностикой.
Поэтому, на предстоящий период обновления и обеспечения топливами смешанного отечественного автопарка, следует обратить внимание на ряд следующих проблем.
Сложной проблемой на сегодня остается обеспечение автопарка топливами требуемых свойств и качества, где одновременно находятся в эксплуатации более половины автопарка автомобилей устаревших моделей не выше Евро-1 и растущий парк новых моделей Евро-2, Евро-3, как отечественного, так и зарубежного производства. Так, далеко не простыми являются вопросы адаптации поступающих в оборот топлив, отвечающих требованиям Евро-2, с улучшенными экологическими свойствами по содержанию серы и цетановому числу для дизельных топлив, к их применению в отечественном парке на автомобилях устаревших конструкций, не отвечающих современным экологическим требованиям.
Например, для подавляющего большинства отечественных дизелей, в том числе новых уровня Евро-2 с механической системой регулирования, рабочий процесс, конструкция и выпуск которых рассчитаны для топлива по ГОСТ 305–82 с цетановым числом 45 единиц и содержанием серы 0,2−0,5%, применение в эксплуатации топлив с ЦЧ выше 50 единиц может приводить к изменению рабочего процесса и, как следствие, к снижению мощности и экономичности, повышению дымности, т. е. под новые топлива уровня Евро-3 и выше требуется радикальная модернизация как дизельных двигателей, так и топливной аппаратуры с использованием систем электронного регулирования, что широко осуществляется сегодня зарубежными производителями техники.
1.5 Химические реакции при сгорании топлива В процессе сгорания в двигателях внутреннего сгорания образуется два вида вредных веществ: продукты частичного разложения и неполного сгорания и окислы азота.
В дизелях окись углерода, образовавшаяся при горении в зонах с богатой смесью, успевает догореть в процессе расширения, поскольку в цилиндрах дизеля всегда есть в избытке воздух, и концентрация СО в выпускных газах дизелей невысока — не более 0,2−0,3%.
Образование окиси углерода и сажи происходит в основном из-за плохого распыления топлива, вытекающего из форсунки в цилиндр после посадки иглы форсунки. Углеводороды образуются также у границы топливного факела в зонах с очень бедной смесью, где концентрация топлива выходит за нижний концентрационный предел. Концентрация углеводородов в выпускных газах дизелей невелика, и для обычных условий эксплуатации ее не нормируют.
Сажа образуется в результате пиролиза топлива при высокой температуре и давлении в среде с недостатком кислорода. Подобные условия наблюдаются в ядре топливного факела вблизи форсунки при впрыске последних порций топлива. Одновременно с сажей образуются окись углерода и углеводороды. Сажа представляет собой твердые сферические частицы с начальным диаметром около 0,45 мкм. Частицы образуют соединения размером несколько мирон.
Азот — химически инертный газ при атмосферных условиях, с кислородом реагирует при высоких температурах и давлении, образуя окись азота NO и небольшое количество двуокиси NO2. окисление азота начинается при температурах выше 1500 К, а при 2300 К и более реакция протекает достаточно быстро (время реакции равно 10″ «- 10» с). Основные вещества, являющиеся продуктами неполного сгорания топлива — окись углерода, сажа, углеводороды и альдегиды. Окись углерода является основным промежуточным продуктом сложного многостадийного процесса горения углеводородных топлив. По предложению Н. Н. Семенова принят цепной механизм образования окиси азота с двумя основными реакциями, в которых активную роль играют атомы азота и кислорода, образующие при диссоциации молекул азота и кислорода.
О + N2 — NO + N.
N + 02 — NO + О.
Скорость цепных реакций в целом определяет первая, эндотермическая, реакция, требующая значительной энергии (316,1 кДж / кмоль). Концентрация окиси азота остается на уровне равновесной концентрации при температуре 23 000К (а > 1). При работе двигателя на богатой смеси (а < 1) не большое количество окиси азота (NO) распадается на исходные продукты: азот (N2) и кислород (02).
Таблица 1.2
Концентрация веществ в выпускных газах ДВС
Тип двигателя | СН, млн -1 | СО, % | NOx. млн -1 | Сажа, г/м3 | |
Дизели с неразделенными камерами сгорания | 50−1000 | 0,05−0,3 | 200−2000 | 0,1−0,3 | |
Дизели с разделенными камерами сгорания | 50−300 | 0,03−0.05 | 200−1000 | 0.1−0,15 | |
1.6 Описание производственных услуг Легковой автомобиль для обеспечения работоспособности с момента его выпуска, до окончания срока службы, на станциях технического обслуживания сможет быть подвержен следующим техническим воздействиям:
1. диагностические работы;
2. ТО в полном объеме;
3. капитальный ремонт узлов и агрегатов;
4. текущий ремонт узлов;
5. шиномонтажные работы;
6. моечные работы;
7. ремонт электрооборудования;
8. ремонт топливных систем;
9. продажа запасных частей;
10. проведение смазочных работ;
11. регулировочные по установке углов передних колес;
12. по приборам системы питания;
13. слесарно-механические.
Распределение объема работы, %.
Диагностические — 5%, ТО в полном объеме — 25%, текущий ремонт узлов и агрегатов — 55%, капитальный ремонт узлов и агрегатов — 10%, шиномонтажные работы — 3%, моечные — 2%, итого- 100%.
Станцию планируется оснастить следующим оборудованием:
1 зона ЕО — установка для мойки автомобиля, установка для мойки двигателей.
2 зона ТО — подъемник электромеханический. Оборудование для раздачи масла для двигателей, контрольно-диагностические и измерительные приборы, гайковерты, оборудование для раздачи трансмиссионных масел, соледолонагнетатель, гайковерт для гаек колес.
3 зона ТР — подъемник электромеханический, смазочно-заправочное оборудование, гайковерт для гаек колес.
4 зона Д — стенд для проверки тормозов, тягово-экономических качеств двигателя, электрооборудовании, углов установки колес, переносные диагностические приборы.
Данное оборудование позволит качественно и в короткие сроки провести техническое обслуживание легковых автомобилей, принадлежащих как населению района, так и проезжим владельцам, которым необходима экстренная помощь.
1.7 Технические характеристики двигателя ЗМЗ 5143
Двигатель ЗМЗ 514 дизельный — является базовым вариантом семейства двигателей ЗМЗ предназначенного для установки на автомобили повышенной проходимости семейства УАЗ. Дизельный двигатель ЗМЗ 514 устанавливается на автомобиль УАЗ Хантер. Унифицирован по основным габаритам и присоединительным характеристикам с семейством бензиновых двигателей ЗМЗ-406.10.
Дизельный двигатель ЗМЗ 5143 имеет четырёх клапанную конструкцию газораспределительного механизма с рычажным приводом клапанов, двумя распределительными валами и гидроопорами в головке цилиндров, привод распределительных валов цепной с натяжными звёздочками, рабочий процесс с объёмным смесеобразованием, турбо-наддувом и системой рециркуляции отработавших газов.
Чугунный со вставными гильзами блок цилиндров, кованный из легированной стали коленчатый вал, цепной привод газораспределительного механизма и масляного насоса, отдельный привод ТНВД с зубчатым ремнём, обеспечивают надёжность. Долговечность и стабильность параметров двигателя.
Рисунок 1.3 Дизельный двигатель ЗМЗ 5143
Таблица 1.3
Технические характеристики двигатель ЗМЗ-5143
Показатель | ||
Количество цилиндров | ||
Рабочий объем, л | 2,235 | |
Степень сжатия | 19,5 | |
Максимальная мощность (брутто) при частоте вращения коленчатого вала-1, кВт (л.с.) | 72 (98) 4000 | |
Максимальный крутящий момент (брутто) по частоте вращения коленчатого вала. Нм (кгсм) | 216 (22) 2100 | |
Минимальный удельный расход топлива г/кВт (г/лсч) | 231 (170) | |
Диаметр цилиндра и ход поршня, мм | 87Ч94 | |
Масса, кг. | ||
Тип двигателя | Дизель | |
Экология | Правила ЕЭК ООН (ЕВРО 2) | |
В двигателе ЗМЗ-5143.10 применены:
4-клапанная конструкция газораспределительного механизма с двумя винтовыми впускными каналами на один цилиндр;
центральное расположение форсунки и камеры сгорания в охлаждаемом поршне;
стальная прокладка головки цилиндров;
кованный, из легированной стали, азотированный коленчатый вал;
антифрикционные, износостойкие покрытия рабочих поверхностей клапанов, поршней и поршневых колец.
Сцепление: тип диафрагменное, номинальное.
Электрооборудование: привод гидравлический, напряжение 12V
Двигатель ЗМЗ 5143.10 предназначен для установки на легковые автомобили среднего класса, легкие грузовики, микроавтобусы, внедорожники с общей массой до 3,5 тонн Дизельный, быстроходный, 4-цилиндровый двигатель с топливной аппаратурой типа VE c механическим регулятором, с регулируемой системой турбонаддува и системой рециркуляции отработанных газов.
Блок цилиндров двигателя ЗМЗ 514 отлит из специального высокопрочного чугуна, что придаёт конструкции двигателя жёсткость и прочность. Протоки для охлаждающей жидкости, образующие рубашку охлаждения. Выполнены по всей высоте блока, это улучшает охлаждение поршней и уменьшает деформацию блока от перегрева. Рубашка охлаждения открыта в верхней части в сторону головки блока. В картере блока цилиндров ЗМЗ 514 установлены форсунки, предназначенные для охлаждения поршней маслом.
Головка блока цилиндров отлита из алюминиевого сплава. В ней установлены впускные и выпускные клапаны. На каждый цилиндр приходится по четыре клапана: два впускных и два выпускных. Впускные клапаны расположены с правой стороны головки, а выпускные — с левой. В головке блока цилиндров имеются посадочные места под форсунки и свечи накаливания.
Распределительный вал изготовлены из низкоуглеродистой легированной стали. Кулачки распределительных валов разнопрофильные, расположены несимметрично относительно своих осей. На задние торцы валов нанесена маркировка клеймением: на впускном валу — «ВП» выпускном валу — «ВЫП». В двигателе у каждого вала пять опорных. Расположенных в головке блока цилиндров и закрытых крышками, расточенными за одно целое с головкой, поэтому крышки опор распределительных валов невзаимозаменяемы. У каждого вала опять опорных шеек. Валы вращаются в опорных, расположенных в головке блока цилиндров и закрытых крышками, расточенное за одно целое с головкой, поэтому крышки опор распределительных валов невзоимозаменяемы.
От осевых перемещений распределительные валы удерживаются упорными полушайбами, установленными в выточки крышек передних опор и входящими выступающими частями в проточки на первых опорных шейках распределительных валов.
Поршни отлиты из алюминиевого сплава. На днище поршня отлита маркировка размерной группы диаметра юбки поршня (буквы «A», «B», «Y») и нанесена стрелка, необходимая для правильной ориентации поршня при установке в двигатель (стрелка должна быть направлена в сторону переднего торца блока цилиндров). Внизу юбки поршня выполнена выемка, которая обеспечивает расхождение поршня с форсункой охлаждения. В головке поршня выполнены три канавки: в двух верхних установлены компрессионные кольца, в нижней — маслосъемное. Канавка под верхнее компрессионное кольцо изготовлена в упрочняющей вставке из нирезистового чугуна. На каждом поршне установлены три кольца: два компрессионных и одно маслосъемное. Компрессионные кольца отлиты из чугуна. Ось отверстия для поршневого пальца смещена на 0,5 мм в правую сторону (по направлению движения автомобиля) от средней плоскости поршня.
Коленчатый вал отлит из высокопрочного чугуна. Вал имеет восемь противовесов. От осевого перемещения его удерживают упорные полушайбы, установленные на средней шейке. К заднему концу коленчатого вала прикреплён маховик. В отверстие маховика вставлены распорная втулка и подшипник носка первичного вала коробки передач.
2. Особенности конструкции
2.1 Конструкция основных элементов системы питания дизельного двигателя Форма камеры сгорания сильно влияет на качество процесса смесеобразования, а значит и на мощность и шумность работы двигателя. Камеры сгорания дизельных двигателей разделяются на два основных типа: неразделенные и разделенные. Соответственно, моторы с камерами первого типа называются дизелями с непосредственным впрыском, а второго — с предварительным. На рисунке 2.1 представлены схемы впрыска топлива.
Рисунок 2.1 Схемы впрыска топлива дизельных двигателей До недавнего времени непосредственный впрыск использовался на тихоходных дизелях большого объема. Хотя такие двигатели экономичнее (до 20%) моторов с разделенными камерами сгорания, их применение на небольших дизелях сдерживалось трудностями организации процесса сгорания, а также повышенными шумом и вибрацией, особенно в режиме разгона.
Сейчас благодаря повсеместному внедрению электронного управления процессом дозирования топлива удалось оптимизировать процесс сгорания топливной смеси в дизеле с неразделенной камерой сгорания и снизить шумность до уровня современных требований к двигателю легкового автомобиля. В наше время уже невозможно представить себе сходящий с конвейера внедорожник с дизелем без непосредственного впрыска. При непосредственном впрыске топливо сразу поступает в камеру сгорания, расположенную в днище поршня. При этом предъявляются высокие требования к подаче топлива и воздуха. Топливо должно равномерно распределяться по объему камеры сгорания и интенсивно перемешиваться с воздухом. Для этого используют форсунки с многоструйным распылителем, а давление открытия в зависимости от системы впрыска достигает 1700 бар. Несколько лет назад на рынке легкового машиностроения доминировали дизели с разделенными камерами сгорания. Впрыск топлива в этом случае осуществляется не в надпоршневое пространство, а в специальную камеру сгорания, выполненную в головке блока цилиндров. При этом различают два процесса смесеобразования: предкамерный (его еще называют форкамерным) и вихрекамерный.
При форкамерном процессе топливо впрыскивается в специальную предварительную камеру, ударяется об ее стенки и перемешивается с воздухом. Воспламенившись, смесь поступает по специальным каналам в основную камеру сгорания, где и сгорает полностью.
Во время вихрекамерного процесса сгорание также начинается в специальной отдельной камере, только выполненной в виде полого шара. В период такта сжатия воздух по соединительному каналу поступает в предкамеру и интенсивно закручивается (образует вихрь) в ней. Впрыснутое в определенный момент топливо хорошо перемешивается с воздухом.
Таким образом, при разделенной камере сгорания происходит как бы двухступенчатое сгорание топлива. Это снижает нагрузку на поршневую группу, а также делает звук работы двигателя более мягким. Но, как мы уже упоминали, экономичность такого дизеля хуже, чем у мотора с непосредственным впрыском. Поэтому последние все чаще занимают достойное место под капотом легковых автомобилей и внедорожников, хотя предкамерные дизели все еще выпускаются. Новые же дизельные двигатели разрабатываются только с непосредственным впрыском.
Важнейшим звеном дизельного двигателя является система топливоподачи, обеспечивающая поступление необходимого количества топлива в нужный момент времени и с заданным давлением в камеру сгорания. Главными ее составляющими являются топливный насос высокого давления (ТНВД) и форсунки.
ТНВД, как это следует из названия, предназначен для создания требуемого высокого давления топлива и подачи его на всех режимах работы двигателя к форсункам, которые в свою очередь впрыскивают его в камеру сгорания. Форсунки и нагнетающие секции ТНВД являются прецизионными деталями, изготовленными с высокой точностью и имеющими микронные зазоры. Поэтому системе питания дизеля приходится уделять большое внимание в обслуживании и ремонте.
ТНВД. Данные насосы довольно сложны по конструкции, но являются самыми надежными. Состоят они из отдельных секций по числу цилиндров дизеля, каждая из которых имеет гильзу и входящий в нее плунжер, который приводится в движение кулачковым валом, получающим вращение от двигателя. Начало и окончание цикла нагнетания топлива, а соответственно и подачи в цилиндры, управляется рейкой. Секции таких механизмов расположены, как правило, в ряд, отсюда и название — рядные ТНВД. Подобные насосы, несмотря на их надежность, в настоящее время уже практически не устанавливаются на легковые автомобили, хотя их все еще можно встретить на двигателях Mercedes ОМ-606 или Nissan TD-42. К сожалению, даже использование электронного управления рейкой подачи не позволяет этим ветеранам соответствовать современным нормам по токсичности и дымности отработавших газов, предъявляемым к небольшим двигателям. Кроме того, дизели, имеющие рядные ТНВД, не отличаются тихой работой.
Форсунки. Рассмотрев системы создания высокого давления топлива, стоит сказать несколько слов о форсунках. От исправности этого элемента дизельного двигателя во многом зависит качество подготовленной для воспламенения смеси.
Обычно применяются форсунки с распылителями двух основных типов: штифтовым или многодырчатым. Первые используются в дизелях с разделенной камерой сгорания, а вторые — в моторах с непосредственным впрыском. Распылитель форсунки — очень сложный и высоконагруженный элемент. Мало того, что он должен точно впрыскивать топливо, подающееся под давлением до 2000 бар, так он еще и подвергается высокому нагреву в камере сгорания (до 900°С). Поэтому распылитель форсунки изготавливается из жаропрочных сталей с прецизионной точностью.
Турбины. Как уже было сказано выше, экономичность дизеля обусловлена тем, что он может работать на достаточно обедненных смесях. Для сгорания топлива необходим чистый воздух (идеально — кислород), который на фазе впуска поступает в цилиндр двигателя. Чем больше воздуха поместится в камере сгорания, тем больше топлива можно в ней сжечь. При этом выделится больше энергии, которая преобразуется в поступательное движение поршня — мощность на выходном валу двигателя возрастет.
Воздух в цилиндр может попадать либо путем всасывания на впуске у атмосферных дизелей, либо под давлением, создаваемым нагнетателем. Наддув воздуха давно используется на грузовых автомобилях для повышения мощности, так как давление выхлопных газов дизеля в 1,5−2 раза выше, чем у бензинового мотора, что позволяет турбокомпрессору обеспечить наддув с самых низких оборотов. Сейчас и легковой дизель нельзя представить себе без турбины.
Устроен этот непременный атрибут современных дизельных моторов следующим образом. Поток горячих выхлопных газов из двигателя направляется на лопатки турбинной части компрессора, раскручивая их до сотен тысяч оборотов, и проходит дальше в выпускной тракт. Турбинная часть жестко закреплена на валу компрессорной части нагнетателя, которая имеет лопатки обратного направления. Раскручиваясь, они создают давление чистого воздуха во впускном коллекторе, а значит и в камере сгорания. Для того чтобы избыточное давление нагнетаемого в цилиндры воздуха не превышало расчетных величин (порядка 1000−1500 бар), нагнетатели оборудуют специальным клапаном, перепускающим выхлопные газы мимо турбинной части, тем самым, снижая ее обороты. Небольшим недостатком турбокомпрессоров этого типа является провал по мощности. Пока двигатель не наберет 2200−2500 об/мин, достаточных для раскручивания нагнетателя, наддув воздуха в цилиндры происходит не слишком эффективно. Чтобы избежать этого, на современных дизелях устанавливаются нагнетатели с изменяемой геометрией турбины. Ее подвижные направляющие лопатки преобразуют сечение каналов, по которым движутся отработавшие газы, что обеспечивает ускорение турбины при малых оборотах двигателя. Но применение данного нагнетателя стало возможным только после внедрения электронного управления дизельным двигателем. У такого турбокомпрессора, несмотря на его высокую эффективность по сравнению с простым, есть и существенный недостаток. В процессе работы мотора постепенно происходит закоксовывание лопаток турбины изменяемой геометрии, что неизбежно ведет к постепенному выходу механизма из строя.
Рисунок 2.2 Схема турбокомпрессора с изменяемой геометрией турбины:
Компрессорная часть нагнетателя.
Лопатки турбинной части нагнетателя.
3. Лопатки изменяемой геометрии.
Мембранный клапан управления лопатками изменяемой геометрии.
Вакуумная магистраль.
Охладители надувочного воздуха (INTERCOOLER).
Кажется, что охладитель надувочного воздуха существует уже целую вечность и каждый знает, для чего он предназначен. Однако опыт показывает, что многие владельцы дизельных автомобилей всерьез считают, что это радиатор охлаждения турбокомпрессора. Внесем ясность. При нагнетании воздуха в цилиндры двигателя при помощи турбокомпрессора он сжимается и, соответственно, нагревается. Как известно, горячий воздух имеет меньшую плотность, чем холодный. Значит, в камере сгорания его поместится меньше. Кроме того, повышение температуры негативно сказывается на наполнении цилиндров в целом. Установленный после турбокомпрессора радиатор охлаждения надувочного воздуха, который и называется intercooler, позволяет устранить эти негативные эффекты. Масса воздуха для приготовления рабочей смеси увеличивается, за счет чего могут быть достигнуты более высокие мощностные характеристики, а также меньший расход топлива и дымление.
Современный дизельный автомобиль невозможно представить себе без электронного управления всеми системами. Основными задачами электронного управления двигателем являются регулирование подачи топлива и угла впрыска во всем диапазоне нагрузок и частот вращения коленчатого вала, а также управление турбокомпрессором. Электроника дизеля состоит из трех основных блоков: датчики и устройства для сбора информации, микропроцессорный блок для ее обработки и исполнительные механизмы. В общих чертах работает эта тройка следующим образом. Блок управления считывает и оценивает сигналы с датчиков сбора информации (датчик оборотов двигателя, температурный, подъема иглы форсунки и прочее). Исходя из полученных данных, микропроцессор рассчитывает количество топлива для впрыскивания и момент начала впрыска. После этого расчетные величины преобразуются в сигналы для исполнительных механизмов (в основном — электромагнитных клапанов).
В отличие от механических дизелей, в которых от педали «газа» к ТНВД подходит трос, в моторах с электронным управлением педаль акселератора — это всего лишь задающее устройство, показывающее блоку управления степень ее нажатия. Электронная система управления способна к самодиагностике. Микропроцессор постоянно сравнивает уровни сигналов от датчиков с нормативными, заложенными в память, и в случае несоответствия немедленно сигнализирует об этом. Естественно, применение таких систем значительно облегчает поиск неисправностей.
Описание системы питания COMMON RAIL.
Постоянно возрастающие требования к системам впрыска дизельных двигателей привели к появлению системы, опережающей предшественников по большинству показателей и имеющей значительные возможности для дальнейшего развития. Главными ее отличиями от конкурентов являются способность изменения момента впрыска топлива и высокого давления в широком диапазоне, а также применение многоступенчатого впрыска. В результате повышается мощность двигателя при сокращении расхода топлива, падают шум и вибрации силового агрегата.
Принцип действия этой системы следующий. Топливоподкачивающий насос низкого давления (электрический или механический) подает топливо в ТНВД. Последний постоянно нагнетает топливо в магистраль, называемую рампой. Имея значительный объем, рампа является аккумулятором высокого давления. Его величина чутко отслеживается датчиками, передающими сигнал на электронный блок, который управляет работой электромагнитных клапанов, сбрасывающих давление в системе или, наоборот, запирающих ее в зависимости от режима работы двигателя.
По коротким магистралям топливо из рампы поступает к форсункам, которые впрыскивают его в камеру сгорания.
Рисунок 2.3 Схема размещения элементов системы Common Rail на двигателе:
Датчик массового расхода воздуха.
Электронный блок управления двигателем.
ТНВД Рампа (аккумулятор давления).
Форсунка.
Датчик оборотов двигателя.
Датчик давления масла.
Топливный фильтр, Датчик положения педали акселератора.
Рисунок 2.4 Принципиальная схема системы Common Rail:
1. ТНВД.
2. Клапан отключения плунжерной секции.
3. Редукционный клапан.
4. Магистраль высокого давления.
5. Рампа (аккумулятор давления).
6. Датчик давления.
7. Клапан ограничения давления.
8. Ограничитель пропускной способности.
9. Форсунка.
10. Электронный блок управления двигателем.
В этой системе наиболее сложным элементом является форсунка с электромагнитным клапаном. Зато постоянно подведенное к форсункам высокое давление дает возможность им многократно приоткрываться перед основным впрыском, делая процесс сгорания оптимальным. Многие крупные автопроизводители считают такую систему топливоподачи наиболее перспективной. Видимо, она будет находить все большее применение. Сейчас ее можно встретить на автомобилях BMW Х5 3.0, Toyota LC Prado с двигателем 1KD, Mercedes G400.
2.2 Оценка системы питания и влияние ее на мощность двигателя Уменьшение подачи топлива и снижение давления при впрыске — основные неисправности системы питания дизельного двигателя.
Признаки неисправности следующие: невозможность пуска или затрудненный пуск двигателя, падение мощности, задымление, стуки, неустойчивая работа или «разнос» его (двигатель трудно остановить).
Причинами уменьшения подачи топлива, снижения давления при впрыске и невозможности вследствие этого запустить двигатель могут быть засорение топливопроводов, заборника в топливном баке или фильтрующих элементов топливных фильтров, замерзание воды или загустение топлива в топливопроводах, наличие воздуха в топливной системе, нарушение угла опережения впрыска топлива, неисправности топливных насосов низкого и высокого давления. Уменьшение подачи топлива и снижение давления при впрыске, приводящие к падению мощности, задымлению и стукам двигателя, возникают при засорении системы выпуска газов; неисправности привода рычага регулятора (при полном нажатии на педаль подачи топлива частота вращения коленчатого вала двигателя не увеличивается); наличии воздуха в топливной системе; нарушении угла опережения впрыска топлива (стуки или задымление); попадании воды в топливную систему (дым белого цвета); избытке топлива, подаваемого в цилиндры (дым черного или серого цвета); нарушении регулировки или засорении форсунок; износе плунжерной пары и отверстий распылителя форсунки; загрязнении воздушного фильтра.
Равномерность работы двигателя нарушается при ослаблении крепления или лопнувшей трубке высокого давления, неудовлетворительной работе отдельных форсунок, нарушении равномерности подачи топлива секциями ТНВД, неисправном регуляторе частоты вращения. Двигатель начинает работать «вразнос» при заедании рейки ТНВД, поломке пружины рычага ее привода, при попадании лишнего количества масла в камеру сгорания из-за износа цилиндропоршневой группы.
Нарушение герметичности магистрали низкого давления возникает как, правило, из-за неплотности в соединениях. Если такие неплотности возникнут в магистрали между топливным баком и насосом низкого давления, то подача топлива резко уменьшиться, двигатель работает неустойчиво на малой частоте вращения коленчатого вала и останавливается при увеличении нагрузки. При сборке магистрали добиваются полной герметичности, особенно у соединений с топливным баком, фильтром грубой очистки и насосом низкого давления.
Засорение топливопроводов и фильтров в магистрали низкого давления. О степени засорения судят по снижению давления топлива на входе в насос высокого давления. Определяют величину давления по контрольному манометру, который подсоединяют к отверстию под пробку для выпуска воздуха на фильтре тонкой очистки. Если давление ниже допустимого предела при герметичных соединениях, то заменяют фильтрующие элементы и проверяют работу подкачивающего насоса низкого давления.
Неисправности насоса низкого давления. Неисправности насоса низкого давления вызывают падение его производительности и сказываются на пуске и работе двигателя. Прежде всего, затрудняется запуск двигателя, так как на малой частоте вращения коленчатого вала насос будет подавать меньше топлива и при более низком давлении. В случае возрастания нагрузки и при малой подаче топлива насосом наблюдается перебои в работе двигателя, и он не сможет воспринимать нагрузку. Основными причинами неисправностей и нарушений в работе насосов низкого давления являются: попадание под клапаны соринок, износ стержня толкателя. При повышенном износе основных рабочих поверхностей насоса (поршня и цилиндра) снижается его производительность и падает давление в магистрали. Снижение производительности может произойти также при уменьшении упругости рабочей пружины.
Неисправности насоса высокого давления и форсунок. Неисправности насоса высокого давления и форсунок при эксплуатации можно обнаружить лишь частично, большинство их определяют только при проверке с помощью специального оборудования. Ниже приведены основные признаки и характер неисправности насосов высокого давления и форсунок.
Затрудненный пуск двигателя происходит вследствие износа плунжеров, гильз и нагнетательных секций насоса, поломки пружин плунжеров, нагнетательных клапанов, понижения давления впрыска форсунками в результате потери упругости пружин штоков, работки сопловых отверстий форсунок и нарушения оптимальной регулировки насоса. Перебои и неравномерность в работе цилиндров двигателя связаны с нарушением равномерности подачи нагнетательными секциями насоса, отклонениями в регулировке форсунок, зависанием нагнетательных клапанов, ослаблением соединений трубопроводов высокого давления, неисправностями всережимного регулятора частоты вращения коленчатого вала. Потеря мощности двигателя зависит от величины подачи топлива в цилиндры двигателя и протекания процессов воспламенения и сгорания. Недостаточная подача вызывается неисправностями приборов магистрали низкого давления, а также неправильной регулировкой насоса высокого давления и регулятора. Повышенная дымность наблюдается при излишней подаче топлива секциями насоса высокого давления, нарушении угла опережения впрыска, снижении давления открытия форсунок, заедании иглы и увеличении отверстий распылителя форсунок. При этих неисправностях отработавшие газы имеют черный цвет. Угол опережения впрыска влияет на начало подачи топлива в цилиндры двигателя и на состав смеси. Изменение угла опережения впрыска в сторону опережения или запаздывания от оптимального положения приводит к увеличению дымления двигателя. Как видно из кривой 1, изменение угла на 4 — 6° вызывает увеличение дымности на 25 — 30%. Такое изменение угла опережения впрыска наблюдается практически у 50% дизельных автомобилей находящихся в эксплуатации.
Начало впрыска форсункой, определяемое степенью затяжки пружины, влияет на распыление топлива и на момент воспламенения. С уменьшением затяжки пружины форсунки, а, следовательно, и изменением давления впрыска (кривая 2) ухудшается качество распыливания и возрастает дымление двигателя и падение мощности на 20%.
Зависимость изменения дымления двигателя от нагрузки (кривая 3) показывает, что даже при нормальном техническом состоянии приборов системы питания дымление двигателя возрастает в 4 — 5 раз при увеличении нагрузки двигателя от 25 до 100%.
2.3 Влияние состояния ЦПГ и ГРМ на мощность двигателя Как известно износ цилиндропоршневой группы вызывает снижение величины компрессии до 20−25%. Предельный износ ЦПГ у восьмицилиндровых двигателей ухудшает их мощностные качества на 8−10% и увеличивает на 3−5% угар моторного масла, а также приводит к увеличению выброса с продуктами сгорания канцерогенных веществ. Предельная величина износа цилиндров достигает 400 мкм. При этом доля пусковых взносов составляет около 25%.Угар моторного масла и дымление двигателя являются определяющим фактором для сдачи его на капитальный ремонт. При износе цилиндров, поршней и колец зазоры между ними увеличиваются. Ухудшается компрессия, воздух и отработавшие газы прорываются из цилиндра в картер, а масло из картера проникает в камеру сгорания. Такие ненормальные явления, в свою очередь, вызывают снижение мощности, увеличение дымности, повышенный расход масла и топлива, интенсивное нагарообразование в камере сгорания, а иногда пригорание поршневых колец.
2.4 Газораспределительный механизм (ГРМ) Эксплуатационные дефекты ГРМ связаны преимущественно с не плотностью прилегания клапанов и нарушением регулировочных зазоров в клапанном механизме. Увеличение зазора у впускных клапанов на 0,1 мм (между штангой и коромыслом) вызывает нарушение фаз газораспределения. Нарушение (сдвиг) фаз газораспределения приводит к уменьшению коэффициента наполнения и увеличению коэффициента остаточных газов. Отмеченные явления вызывают ухудшение мощности двигателя до 3—4% и увеличение расхода топлива на 5—7%. Характерными дефектами деталей ГРМ являются: износ и выгорание фасок клапана и его седла, износ стержня клапана по диаметру, износ бойка коромысла, потеря упругости и уменьшение длины пружины клапана, износ кулачков и шеек распределительного вала и т. д. Перечисленные дефекты сопровождаются уменьшением мощности и экономичности двигателя, подсасыванием воздуха и обеднением смеси, прорывом отработанных газов.
Все характерные неисправности дизельного двигателя, а так же методы их устранения приведены в таблице.
Таблица 2.1
Возможные причины неисправностей дизельного двигателя
Признак неисправности | Возможная причина | Способ устранения | ||
Проверка 1 | Черный или серый дым под нагрузкой, более заметный на высоких оборотах | Забивание системы подачи воздуха | Удалите забивание | |
Проверка 2 | Черный или серый дым под нагрузкой, более заметный при высоких и средних оборотах. Двигатель может терять мощность | Загрязнены, изношены или несоответствующие форсунки | Очистите или замените форсунки | |
Проверка3 | Черный или серый дым под нагрузкой, более заметный при низких и средних оборотах. Двигатель работает тише обычного. | Запаздывает момент впрыска ТНВД | Установите момент впрыска. Отремонтируйте или замените ТНВД, если его состояние вызывает сомнения | |
Проверка 4 | Черный или серый дым под нагрузкой, более заметный при низких и средних оборотах. Двигатель работает шумнее обычного | Слишком ранний момент впрыска ТНВД | Установите момент впрыска. Отремонтируйте или замените ТНВД, если его состояние вызывает сомнения | |
Проверка 5 | Черные или серый дым под нагрузкой, более заметный при низких и средних оборотах. Затруднен запуск | Низкая компрессия в цилиндрах | Отремонтируйте двигатель | |
Проверка6 | Случайные выбросы белого или серого дыма. Может сопровождаться пропусками «зажигания» или детонацией | Заедает форсунка | Отремонтируйте или замените форсунку | |
Проверка 7 | Черный или серый дым на всех оборотах. Заметная потеря мощности | Низкое давление наддува (двигатели с турбонаддувом) | Отремонтируйте систему управления наддувом | |
Проверка 8 | Черный или серый дым, более заметный на низких и средних оборотах. Двигатель может пропускать «зажигание» | Неправильные клапанные зазоры | Отрегулируйте клапанные зазоры | |
Проверка 9 | Черный или серый дым на всех оборотах. Двигатель также может пропускать «зажигание» или детонировать | Неправильный тип или качество топлива | Слейте топливо и залейте новое | |
Проверка 10 | Черный или серый дым на всех оборотах на теплом двигателе. Более заметен на низких и средних оборотах | Неисправно пусковое устройство (работающее на топливе) | Отремонтируйте или замените пусковое устройство | |
Проверка 11 | Беловатый дым при высоких оборотах двигателя и при небольших нагрузках. Возможен необычный запах выхлопных газов | Двигатель работает непрогретым | Устраните или замените неисправный термостат | |
Проверка 12 | Беловатый дым при высоких оборотах двигателя и при небольших нагрузках. Более заметен на холодном двигателе. Цвет дыма изменяется на черный при повышении температуры. | Поздний момент впрыска ТНВД | Установите момент впрыска. Отремонтируйте или замените ТНВД, если его состояние вызывает сомнения | |
Проверка 13 | Беловатый дым при небольших нагрузках и нормальной температуре двигателя. Может сопровождаться детонацией | Утечка в одной или нескольких форсунках | Отремонтируйте или замените подозреваемые форсунки | |
Проверка 14 | Голубой дым при разгоне или работе двигателя на холостом ходу | Утечка в сальниках клапанов или износ направляющих втулок или стержней клапанов | Замените сальники или отремонтируйте головку блока цилиндров | |
Проверка 15 | Голубой дым при всех оборотах, нагрузках и температурах | Изношены поршневые кольца или отверстия цилиндров | Отремонтируй те двигатель | |
Проверка 16 | Голубой дым при высоких оборотах, снижается при средних оборотах при всех нагрузках | Утечка в сальниках турбокомпрессора | Отремонтируйте турбокомпрессор | |
Проверка 17 | Голубой дым при высоких температурах и при всех оборотах и нагрузках | Моторное масло слишком жидкое | Слейте старое масло и залейте масло нужного сорта | |
Проверка 18 | Голубой или серо-голубой дым из выхлопного отверстия системы вентиляции картера | Изношены поршневые кольца или отверстия цилиндров | Отремонтируйте двигатель | |
Проверка 19 | Избыточные масляные пары или капельки из выходного отверстия системы вентиляции картера | Неисправен вакуумный насос (если он установлен) | Отремонтируйте вакуумную систему | |
Как было сказано в данной главе неисправности системы питания и неудовлетворительное состояние ЦПГ и ГРМ ведут к снижению мощности двигателя, увеличению расхода топлива и масел.
3. Методика проведения экспериментальных исследований по оценке состава ОГ при различных видах топлива
3.1 Анализ испытания дизельных топлив На сегодняшний день согласно техническим условиям выпускается дизельное топливо трех марок. В зависимости от условий применения утверждены следующие марки дизельного топлива: Л — летнее предназначенное для применения от 0 °C и выше, 3 — зимнее применяемое от -20°С до 0 °C, и, А — арктическое применяемое от -50°С до -20°С. Принято следующее условное обозначение дизельного топлива. Например: Л-0,2−40 — здесь Л — летнее, 0,2 — содержание серы 0,2%, 40 — температура вспышки °С; З-0,2−35 — здесь З — зимнее, 0,2 — содержание серы 0,2%, 35 -температура застывания -35°С; у арктического топлива отражается только содержание серы А-0,4 — А — арктическое, 0,4 — содержание серы в %.
Таблица 3.1
Результаты проверки дизельного топлива марки Л-0.5−65
Показатели | Требования ГОСТ 305–73 | Результат анализа | |
Цетановое число | 45 (не менее) | ; | |
Фракционный состав: перегоняется при t, С0: 50% | 280 (не выше) | ||
90% | |||
Вязкость при 20 С", сСт | 3,0−6.0 | 4,2 | |
Температура, Си: | |||
помутнения | — 5 (не выше) | — 7 | |
Застывания | — 10 | — 11 | |
Вспышки | 65 (не ниже) | ||
Содержание серы, % | 0,5 (не более) | 0,47 | |
Содержание фактических смол мг/100 мл (не более) | |||
Кислотность, мг/100 мл | 4,0 | ||
Коксуемость 10%-ного остатка, % | 0,3 | 0,29 | |
Испытание на медной пластинке | Выдерживает | ||
Содержание водорастворимых кислот и щелочей | Отсутствуют | ||
Содержание воды | Отсутствует | 0,040 | |
Содержание механических примесей, % | Отсутствует | 0,065 | |
В процессе проведения лабораторных исследований был проведен анализ дизельных топлив марок Л-0,2−40 и 3−0,2−35.
Таблица 3.2
Результаты проверки дизельного топлива марки 3−0,2−25
Показатели | Требования ГОСТ 305–73 | Результат анализа | |
Цетановое число | 45 (не менее) | ; | |
Фракционный состав: перегоняется при t, С°: 50% | 250 (не выше) | ||
90% | |||
Вязкость при 20 Си, сСт | 2,0 | 2,3 | |
Температура, Си: | |||
помутнения | — 20 (не выше) | — 18 | |
Застывания | — 25 | — 21 | |
Вспышки | 35 (не ниже) | ||
Содержание серы, % | 0,3 (не более) | 0.33 | |
Содержание фактических смол мг/100 мл (не более) | |||
Кислотность, мг/100 мл | |||
Коксуемость 10%-ного остатка, % | 0,3 | 0.29 | |
Испытание на медной пластинке | Выдерживает | ||
Содержание водорастворимых кислот и щелочей | Отсутствуют | ||
Содержание воды | Отсутствует | 0,040 | |
Содержание механических примесей, % | Отсутствует | 0.065 | |
Механические примеси в дизельных топливах недопустимы, а согласно проведенному анализу они присутствуют.
Механические примеси в дизельных топливах появляются в результате небрежной транспортировке.
Для улучшения качества дизельных топлив на нефтеперерабатывающих заводах применяют присадки: изопропилнитрат и циклогексилнитрат — для повышения цетанового числа, присадка ПДП — для улучшения низкотемпературных свойств. Товарные топлива для быстроходных дизелей получают путем смешения керосиногазойлевых фракций прямой перегонки нефти до гидроочистки, и после гидроочистки в таком соотношении, чтобы обеспечить требования ГОСТ 305–82 по содержанию серы.
3.2 Выбор оборудования для исследований Лабораторные исследования включали в себя стендовые испытания топливной системы с помощью тормозного стенда двигателей. Для проведения этих исследований и оценки диагностических параметров на основе теоретического анализа качества смесеобразования и литературных источников был разработан исследовательский комплекс, который включал в себя дизельный компрессометр с пределом измерения 10−60 кг/см', стенд для проверки дизельных форсунок КИ 15 706 — производства ОАО «Мопаз» (г. Малоярославец), стенд для регулировки топливных насосов высокого давления КИ-921 МТ, мотортестер М2−2 белорусского производства (г. Минск). Этот прибор позволяет помимо частоты вращения и угла опережения впрыска контролировать еще 9 параметров двигателя, включая мощностные, а также наблюдать осциллограммы впрыска по цилиндрам на встроенном осциллоскопе. Для измерения давления здесь используется устанавливаемый в разрыв топливопровода датчик, очень точный и никогда не дающий сбоев. Он универсален и позволяет, в отличие от накладных импортных тензодатчиков, работать с любыми топливопроводами от 4,5 мм (Merceries) до 10 мм (тяжелая техника). Недостатком этого датчика являются большие габариты и необходимость разъединения топливопровода. При проведении экспериментальных исследований для получения достоверной оценки технического состояния ЦПГ, ГРМ и СЗ использовались дополнительные диагностические средства и приборы. Для оценки ЦПГ и ГРМ использовались пневмотестер К-272, вакууманализатор КИ-5315, индикатор расхода газов КИ-13 671 и прибор для измерения давления в конце такта сжатия отдельных цилиндров двигателя КИ-861. Кроме указанных приборов и диагностических средств, использовался мерительный инструмент (нутромер, микрометр, набор щупов и индикатор часового типа ИЧ-10), с помощью которого измерялись геометрические размеры элементов ЦПГ и ГРМ на разобранном двигателе.
Определение состава ОГ проводилось дымомером «Мета-01 МП» .
3.3 Методика проведения эксплуатационных испытаний В процессе эксперимента проводилось измерение мощностных параметров. Испытание метода проводилось на автомобилях, пришедших на пост диагностики в связи с неисправностями, которые водители не смогли выявить своими силами.
Неисправности испытуемых автомобилей выявлялись с помощью стандартных средств диагностики, остальная часть — с использованием мотортестер М2−2.
Достоверность полученных результатов диагностирования проверялась всей совокупностью стандартных средств, имеющихся на посту диагностики, а также частичной и полной разборкой составных частей двигателя (ЦПГ, ГРМ и т. д.).
Технологические воздействия по устранению и обнаружению неисправностей осуществлялись по предложенному нами алгоритму. При проведении испытаний не выявленное количество неисправностей, возникших в СК и двигателя, составило около 7%, причем около 5% из них не выявлено из-за ошибок оператора-диагноста.
Для получения достоверной и точной информации в процессе экспериментальных исследований нами было найдено количество автомобилей, необходимых для проведения испытаний, которое определялось исходя из принятой в практике доверительной вероятности Р = 95% с погрешностью измерений 5%.
Для расчета необходимого количества испытуемых объектов достаточно использовать шесть измерений. Результаты проведенных измерений представлены в табл. 3.3.
Таблица 3.3
Значение параметра СО на различных режимах работы двигателя
№ автомобиля | Режимы проверки и значение параметра сажи, в % | ||
n = об/мин | Свободное ускорение | ||
14,2 | 39,6 | ||
15,5 | 38,5 | ||
39,2 | |||
14,3 | |||
Затем находим интервалы варьирования W, определяемые как положительная разность между соседними значениями для указанных в табл.3.7 режимов:
W1 = 15−14,2=0,8;
W2= 15,5−14=1,5;
W3 = 15−14,3=0,7;
W4 = 40−39,6=0,4;
W5 =41−38,5=2,5;
W6 = 40−39,2=0,8.
Разбив шесть значений полученных интервалов варьирования на 3 группы по 2 объекта (автомобиля), получим:
W1, W2 — 1 -ая группа;
W3, W4 — 2-ая группа;
W5, W6 — 3-ая группа.
По указанным выше данным определяем размах варьирования Wn:
Wn = У Wn /f,
где fчисло степеней свободы,
f = 1 (n-1),
где 1 — количество повторных определений, проведенных в одинаковых условиях;
n — число автомобилей при проверке.
(3.1.)
Тогда зная Wn, можно определить максимальное допустимое отклонение среднего значения от истинного Jp:
где — ошибка среднего значения;
tp (n-1) — значение коэффициента Стьюдента для вероятности р при числе измерений n;
dn — постоянный коэффициент, который равен dn = 1,693; для принятой вероятности 95% коэффициент Стьюдента
tp95=2,45 · 1=0,9.
Зная найденные показатели, определяем необходимое количество испытуемых автомобилей:
(3.2.)
После выполнения необходимых расчетов n = 30,2, т. е. при заданной доверительной вероятности 95% и погрешности измерений 5% для испытаний требуется 30 автомобилей.
Принятые диагностические параметры — частота вращения коленчатого вала двигателя, содержание сажи в отработавших газах — оценивались по стабильности и информативности с помощью следующих формул:
(3.3)
где — среднеквадратическое отклонение — стабильность параметра;
X — среднеарифметическое значение диагностического параметра;
X — текущее значение диагностического параметра;
n — число проверок.
где J (П) — информативность диагностического параметра;
П1, П2 — среднее арифметическое значение диагностический параметров, соответствующие исправному и неисправному состоянию рассматриваемого объекта (ЦПГ, ГРМ);
уl, у2 — среднеквадратические отклонения параметров распределений, соответствующих исправному и неисправному состоянию рассматриваемого объекта.
Таким образом, диагностическими параметрами является содержание сажи в %, обороты коленчатого вала двигателя — n об/мин.
3.4 Методика построения экспериментальных зависимостей Построение зависимостей проводилось по полученным экспериментальным точкам.
Так при построении мощностных характеристик устанавливались заданные обороты двигателя, на которых измерялся мощность двигателя. Затем обороты увеличивались на 500 об/мин-1 и вновь после стабилизации показаний мотортестера, измерялась мощность двигателя. После проведения данной операции в отдельную тару (бутылку) заливалось дизельное топливо другой марки, и вновь измерялся мощность двигателя, по вышеуказанной методике. Полученные кривые обрабатывались с помощью ЭВМ по методу наименьших квадратов. Для получения более точных данных дизельное топливо проверяемой марки использовалось до конца. Следует указать, что неисправности в системах и механизмах двигателя в частности ЦПГ, ГРМ отсутствовали, что позволило получить более точные и достоверные результаты.
При проведении эксплуатационных испытаний, дизельное топливо, аналогично вышеуказанному случаю, дожигалось до конца и заливалось испытуемое.
При достижении определенной скорости движении, на бутылке ставилась метка, и после определенного пробега определялся расход топлива. Затем оставшееся топливо дожигалось, вновь заливалось другое топливо, и при определенной скорости замерялся расход топлива.
Предложенная выше методика построения полученных зависимостей и проведения эксплуатационных испытаний дает погрешность измерения не более 5−7%.
Вывод.
На основании выше изложенного можно заключить, что для получения точных и достоверных результатов необходимо использовать количество автомобилей равных 30.
4. Результаты экспериментальных исследований
4.1 Влияние дизельного топлива марки Л-0,5−62 на мощностные показатели двигателя Анализ проведенных экспериментальных исследований на тормозном стенде, по определению мощности и удельного расхода топлива показал, что при использовании эталонного топлива мощность двигателя ЗМЗ-5143.10 автомобиля УАЗ «Патриот», составляет 72 кВт при 3500 об/мин, а удельный расход топлива составляет 245 г/кВт*час.
Ниже приведены диаграммы испытания образцов топлива взятых на АЗС г. Костанай.
Рисунок 4.1 Результаты испытания на топливе марки Л-0,5−65 где:
линия 1 -результаты испытания на эталонном топливе линия 2-резульгаты испытания на образце топлива № 1
линия 3-результаты испытания на образце топлива № 2
При использовании образца № 1 мощность двигателя снизилась на 7%, удельный расход топлива повысился на 9%. При использовании образца № 2 мощность снизилась на 10%, удельный расход топлива повысился на 12%. Это происходит из-за механических и прочих примесей присутствующих в топливе, которые повышают вязкость топлива. Эти примеси появляются в результате небрежной транспортировке и хранении топлива. Так, например в одном из образцов топлива были явные следы моторного масла и воды. Из-за этого ухудшается качество распыла, качество сгорания топлива, вследствие чего растет удельный расход топлива и падает мощность двигателя.
4.2 Влияние качества дизельного топлива марки З-0,2−35 на мощностные показатели двигателя Ниже приведены диаграммы испытания образцов топлива взятых на АЗС г. Костанай.
Рисунок 4.2 Диаграмма испытания на топливе З-0,2−35
где: линия 1 -результаты испытания на эталонном топливе линия 2-результаты испытания на образце топлива № 1
линия 3-результаты испытания на образце топлива № 2
При использовании образца № 1 мощность двигателя увеличилась на 5%, удельный расход топлива снизился на 2%.
При использовании образца № 2 мощность повысилась на 5%, удельный расход топлива снизился на 3%.
Увеличение мощности и снижение удельного расхода топлива происходит за счет того, что дизельное топливо марки 3−0,2−25 имеет меньшую вязкость, а следовательно улучшается качество распыла и сгорания топлива.
Вывод При работе дизельного двигателя на форсунках и в камере сгорания образуются отложения, нарушающие подачу топлива и нормальное протекание рабочего процесса. В результате снижается мощность и экономичность двигателя, увеличиваются дымность и токсичность отработавших газов.
Применение дизельных топлив не соответствующего качества негативно сказывается на работе двигателя и его эксплуатационных и топливо — экономических характеристиках. В связи с этим появляется необходимость в частом проведении ТО топливной аппаратуры, частой смене топливных фильтрующих элементов.
Применение дизельных топлив соответствующего качества позволяет экономить на затратах на топливе, т.к. идет снижение расхода топлива, позволяет реже проводить ТО и замену фильтрующих элементов.
5. Конструкторская разработка прибора для проверки герметичности топливной системы
5.1 Обоснование целесообразности разработки прибора для проверки герметичности топливной системы низкого давления Как было сказано выше неудовлетворительное состояние топливной магистрали низкого давления сильно влияет на работу двигателя, его мощность, расход топлива и дымность отработавших газов. Из-за нарушения герметичности магистрали низкого давления подача топлива уменьшиться, двигатель работает неустойчиво на малой частоте вращения коленчатого вала и останавливается при увеличении нагрузки. При сборке магистрали добиваются полной герметичности, особенно у соединений с топливным баком, фильтром грубой очистки и насосом низкого давления.
В настоящее время данная процедура проводиться водителями. Данная операция очень трудоемка и не редко водители сами не могут выявить неисправность или выявляют ее с ошибкой, а это неизбежно ведет к дополнительным потерям топлива, увеличивает простои на автомобиля на ремонте.
Ниже приведены способы проверки магистрали без применения прибора: пускают двигатель и на малой частоте вращения коленчатого вала двигателя отвертывают сливную пробку фильтра тонкой очистки топлива и осматривают струю. При наличии в топливе неоднородностей, пузырьков воздуха можно заключить, что магистраль негерметична. При этом проверяют все соединения на участке от бака до насоса низкого давления и устраняют неплотности подтяжкой резьбы, заменой негодных прокладок, муфт, штуцеров или трубопроводов. Данный способ дает общую оценку состояния топливной магистрали низкого давления, т. е. механик (водитель) не может конкретно знать место разгерметизации т.к. нет явных следов подтекания топлива. При использовании этого метода увеличивается время простоя автомобиля в ремонте, растет себестоимость ремонта.
С целью снижения времени простоя автомобиля, увеличения производительности в данном дипломном проекте предлагается приспособление для проверки герметичности магистрали низкого давления. Данное приспособление способно непосредственно указать место подтекеания топлива, что резко увеличит производительность труда.
5.2 Описание конструкции и принцип действия прибора для проверки герметичности топливной системы Прибор позволяет выявлять места разгерметизации системы питания по появлению пузырьков воздуха или подтеканию топлива. Кроме того, прибор позволяет быстро заполнить фильтры предварительной очистки при замене элементов фильтров. Устройство прибора показано на рисунке 5.1.
Рисунок 5.1 Прибор для проверки герметичности топливной системы дизельных двигателей.
1- упор; 2- насос; 3- хомут; 4- манометр; 5- кран подачи топлива из бака в магистраль автомобиля; 6- штуцер нагнетательного шланга; 7- плавающий клапан; 8- бак; 9- воздушный кран: 10- глазок для контроля уровня топлива; 11- трубка; 12- заливная горловина; 13- зацепы для укладки шланга; 14- обратный клапан.
Прибор состоит из бака 8, на верхней крышке которого смонтированы: обратный клапан 14 для пропуска воздуха в одном направлении из насоса в бак; манометр 4; заливная горловина 12 с трубой 11, определяющая верхний уровень топлива в баке и обеспечивающая воздушную подушку меду крышкой бака и топливом.
Сжатый воздух обеспечивает подачу топлива под давлением по мере его расходования.
В крышке бака расположен воздушный кран 9 для сброса давления из бака.
На обечайке бака имеются два глазка 10 для контроля уровня топлива, хомут 3 и упор 1 для крепления ручного автомобильного насоса 2. В днище бака вмонтирован запорный клапан 7.
При нормальном уровне топлива плавающий клапан 7 находится в верхнем положении, и топливо проходит через отверстие в седле клапана.
При понижении уровня топлива плавающий клапан перекрывает выходное отверстие, тем самым прекращается поступление топлива в шланг, а топливная магистраль предохраняется от попадания воздуха.
При положении уровня топлива до ¼ емкости бака, равной 6 л, следует долить топливо через горловину бака.
Перед проверкой необходимо испытать сам прибор. Для этого закрывают двухходовой кран 5 и заливают в бак чистое профильтрованное топливо (5−6 литров). Затем закрывают кран 9, и насосом накачивают в бак воздух до давления 0,3 МПа. Давление контролируют по манометру 4. если давление не снижается в течение 1 мин, то прибор считают годным для работы.
Проверку герметичности магистра низкого давления проводят в следующем порядке. Отсоединяют отводящий топливо провод от топливного бака и устанавливают на него заглушку. Подводящий топливопровод также отсоединяют от бака и соединяют с резиновым шлангом прибора. Затем открывают кран 5, и топливо под давлением воздуха в баке прибора заполняет магистраль низкого давления. Неплотности и места нарушения герметичности обнаруживают по появлению течи топлива или пузырьков воздуха. После устранения неисправностей вновь проверяют герметичность прибором.
5.3 Прочностные расчеты Произведем проверочный расчет сварного соединения крепления упора к баку.
Упор служит для установки насоса и воспринимает усилие от воздействия рук на рукоятку насоса, для наших расчетов примем значение этой силы F=500 Н. Место установки упора показано на рисунке 5.2. По рисунку видно, что линия действия силы расположена эксцентрично к сварному шву, поэтому расчет произведем на совместное действие среза и изгиба.
Рисунок 5.2 Установка упора на баке прибора.
где — уравнение прочности на срез.
S-площадь среза шва, для бокового шва
b-длина бокового шва у нас конструктивно l=36мм.
— толщина свариваемых деталей =4мм.
где — уравнение прочности на срез.
S-площадь среза шва, для бокового шва
— допускаемое напряжение на срез материала шва:
б1-коэффициент, учитывающий тип сварки, для ручной сварки б1= 0,6
[фСР]=0,6 · 160=96МПа, уи-напряжение изгиба, возникающее в материале шва:
где Н-Расстояние от основания шва до направления действия силы. Конструктивно у нас получилось Н=58мм Подставим значения в (5.1) и вычислим
МПа
39МПа<[тСР]
Из расчета следует, что прочность сварочного шва обеспечена.
Запас прочности соединения
МПа
6. Охрана труда
6.1 Общее положение по охране труда Важнейшей целью казахстанского общества является превращение труда в первейшую жизненную потребность человека. Это возможно только в том случае, если труд человека протекает в благоприятных условиях, способствующих развитию всех его способностей и обеспечивающих высокую производительность труда. Кроме того, в процессе труда человек не должен заболеть или получить травму. В то же время ежегодно в мире происходит 50 млн. несчастных случаев (в среднем 160 тыс. случаев в день).
Проблемами, связанными с обеспечением здоровых и безопасных условий труда занимается охрана труда. Сложность стоящих перед охраной труда задач требует использование достижений и выводов многих научных дисциплин, прямо или косвенно связанных с задачами создания здоровых и безопасных условий труда. Прежде всего, это относится к социально-правовым наукам, которые рассматривают правовые гарантии трудящихся, а так же к исследованиям в области научной организации труда, технической эстетики, эргономики, социальной и инженерной психологии.
Охрана труда является органическим элементом процесса производства. Поэтому она имеет как организационно-технические, так и социальные аспекты. Охрана Труда призвана ограждать работников от воздействия опасных и вредных производственных факторов, обеспечивать наиболее благоприятные условия труда, что предотвращает бесполезную затрату сил, содействует повышению производительности труда, всестороннему развитию личности.
Благоприятные условия труда на производстве способствуют активному участию людей в общественно-политической жизни, позволяют шире удовлетворять их культурные запросы.
Современный научно-технический прогресс вносит принципиальные новшества во все сферы материального производства. Атомная энергия, автоматизация и электроника, полимеры и физика твердого тела с ее воздействием на структуру вещества, химизация и микробиология, оптимизация процессов, кибернетика и ЭВМ — все это в корне преобразовывает энергетику, орудия и предметы труда, технологию, методы обработки информации и управления, меняет условия труда.
В большинстве отраслей промышленности научно-технический процесс сопровождается улучшением труда, ликвидацией на многих производствах тяжелого ручного труда, широким внедрением новых эффективных средств обеспечения безопасности. Происходит значительное развитие научно-исследовательских и конструкторских работ в области охраны труда.
Значительный прогресс достигнут в машиностроении. На вновь создаваемых станках механизированы загрузка заготовок и выгрузка деталей, автоматизированы смена режущего инструмента и удаление стружки. Это значительно облегчает обслуживание станков. Полностью освобождает рабочих от тяжелых, вредных и монотонных работ внедрение автоматических механизаторов с программным управлением промышленных роботов. Использование промышленных роботов придает принципиально новые качества комплексно-механизированным и автоматизированным системам как в основных, так и во вспомогательных производствах.
Огромные перемены происходят в сельском хозяйстве, где ручной труд во все большей степени заменяется машинным.
В то же время недостаточное использование возможностей научно-технического прогресса, отсутствие рационального им управления приводят в ряде случаев к ухудшению условий труда.
Рост количества одновременно управляемых объектов влечет за собой увеличение объема информации, значительно усложняет анализ и оценку производственной обстановки, приводит к повышению нервно-психических нагрузок.
Известное положение о том, что механизация и автоматизация трудовых процессов облегчает физическую тяжесть труда, сейчас нуждается в некотором уточнении. Безусловно, если оценивать тяжесть труда только по величине энергозатрат, то труд человека, обслуживающего современные машины, сложные технические комплексы, конвейерные линии, различные виды транспорта, можно считать легким. Но высокомеханизированный труд совершается в условиях ограниченной подвижности, связан с длительным мышечным статическим напряжением, а это является самой утомительной формой мышечной деятельности. Труд человека, протекающий в условиях чрезмерного нервного напряжения и длительной статической нагрузки с ограниченной подвижностью, приводит к возникновению неврозов, нервно-психических и сердечнососудистых заболеваний.
С другой стороны, развитие автоматизации, механизации, дистанционного управления, применение наиболее совершенного оборудования привели к резкому снижению содержания в воздухе рабочих зон химических, металлургических и других цехов вредных веществ. В этих условиях опасность отравления значительно уменьшилась, и на первый план выдвинулись проблемы, связанные с длительным воздействием небольших концентраций вредных веществ, их комбинированным воздействием и влиянием на возможные последствия в отдельные сроки, а также влиянием на общую сопротивляемость организма и его работоспособность.
Увеличение мощностей и скоростей работы оборудования, замена традиционных технологических процессов новыми (электрофизическими, электрохимическими, ультразвуковыми) приводит к возрастанию воздействия на работающих такие неблагоприятные факторы, как шум, вибрация, ультразвук.
Дальнейшее совершенствование охраны труда в условиях научно-технического прогресса требует глубокого и комплексного изучения последствий внедрения его достижений с психофизиологической, экономической, социальной и других точек зрения.
Создание здоровых и безопасных условий труда начинается с правильного выбора территории для размещения предприятия и рационального расположения на ней производственных и вспомогательных зданий и сооружений.
При размещении производственных, вспомогательных зданий и других сооружений на территории предприятия помимо технологических и технико-экономических показателей необходимо учитывать и санитарно-гигиенические требования.
6.2 Инструкции по технике безопасности при работе с прибором для проверки герметичности топливопровода низкого давления дизельного двигателя Требования производственной санитарии. Культура производства начинается с чистоты и аккуратности рабочего. Беспорядок, грязь на рабочем месте, неаккуратная, плохо подогнанная спецодежда могут привести к травме или заболеванию.
Во избежание простудных заболеваний одежда и обувь должны быть хорошо просушены; следует избегать сквозняков и принимать меры к их устранению.
Рабочее место должно быть хорошо освещено. Необходимо следить за чистотой окон, ламп и плафонов местного освещения.
Для защиты органов дыхания от паров и газов, следует применять респираторы соответствующих марок, фильтрующие или шланговые противогазы.
Для защиты кожи рук, лица, шеи от оставшихся нефтепродуктов на топливопроводах следует применять пасты ХИОТ, ИЭР, биологические перчатки, биокремы, силиконовый крем и другие.
Для защиты от шума следует применять, в зависимости от интенсивности, наушники, шлемы или беруши.
Важной мерой профилактики профессиональных заболеваний являются ежегодные врачебные осмотры и флюорография, которые позволяют своевременно обнаружить ранние формы заболеваний, легко поддающиеся лечению.
Требования электробезопасности. Воздействие электрического тока на организм человека опасно для жизни. Опасным является напряжение свыше 42 В, а в сырых помещениях и помещениях с токопроводящими полами — свыше 12 В. Прохождение через тело человека электрического тока свыше 0.1 ампера может привести к смертельному исходу. Исход воздействия электрического тока зависит от электрического сопротивления тела человека. Усталость организма, болезненное состояние, потливость, алкогольное опьянение значительно уменьшают сопротивление электротоку.
Прикасаться к оголенным токоведущим частям, открывать электрошкафы электрооборудования запрещается.
В случае обнаружения нарушения изоляции проводов или нарушения заземления следует немедленно прекратить работу и сообщить об этом своему непосредственному начальнику для устранения неисправности. Производить самостоятельно какой-либо ремонт электрооборудования запрещается. Эту работу может выполнять только электрик, имеющий допуск к обслуживанию электрооборудования.
При перерыве в подаче электроэнергии необходимо выключить пресс.
6.3 Пожарная безопасность Руководители и инженерно-технические работники заводов и управлений объединения обязаны руководствоваться инструкцией и не снижать требований специальных правил по обеспечению пожарной безопасности. В соответствии с действующим законодательством ответственность за обеспечение пожарной безопасности заводов и управлений несут руководители этих подразделений. Ответственность за пожарную безопасность отдельных цехов, лаборатории, отделов, складов, мастерских и других участков несут руководители или лица, исполняющие их обязанности.
Начальники цехов, лабораторий, отделов, заведующие складами, мастерскими и другие должностные лица, ответственные за пожарную безопасность, обязаны:
— обеспечить соблюдение на вверенных им участках работы установленного противопожарного режима;
— следить за исправностью приборов отопления, вентиляции, электроустановок, технологического оборудования и принимать немедленные меры к устранению обнаруженных неисправностей, могущих привести к пожару;
следить за тем, чтобы после окончания работы проводилась уборка рабочих мест и помещений, отключалась электросеть, за исключением дежурного освещения и электроустановок, которые по условиям технологического процесса производства работ должны работать круглосуточно. При необходимости помещения запирать на замок:
обеспечить исправное состояние и постоянную готовность к действию имеющихся средств пожаротушения, связи и сигнализации.
Инструкции вывешиваются на планшетах уголков пожарной безопасности или иных видных местах. На пожароопасных участках вывешиваются выписки из инструкций.
Каждый работающий с установкой обязан четко знать и строго выполнять установленные правила пожарной безопасности, не допускать действий, могущих привести к пожару или загоранию. Лица, виновные в нарушении правил пожарной безопасности, в зависимости от характера нарушений и их последствий несут ответственность в дисциплинарном, административном или судебном порядке в соответствии с правилами внутреннего распорядка и действующим законодательством.
При обработке трубок топливопровода металлическую стружку, обтирочный материал необходимо убирать в металлические ящики с закрывающимися крышками и по окончании смены удалять.
Спецодежда должна своевременно стираться и храниться в шкафах. Запрещается стирка ее в ЛВЖ и ГЖ.
Не допускается складировать спецодежду, промасленную ветошь, горючие материалы на нагревательные приборы и трубопроводы отопления.
Для указания местонахождения средств пожаротушения должны применяться указательные знаки по ГОСТ 12.4.020−76., которые размещаются на видных местах на высоте 2−2,5 м как внутри, так и вне помещений.
7. Охрана окружающей среды Общее ухудшение экологической обстановки, связанное с комплексным влиянием негативных факторов, сопровождающих интенсивное развитие автомобильной промышленности, ежегодно прогрессирующее увеличение численности мирового автомобильного парка, носит в городах катастрофический характер. Это обусловлено высокой плотностью населения, обеспечение жизнедеятельности которого, в свою очередь, требует сосредоточения большого количества транспортных средств (автомобилей) на ограниченной площади, а так же микроклиматических условий техносферы, т. е. характера изменения параметров атмосферного воздуха: температуры, влажности, давления, подвижности (способность воздушных масс к перемещению в условиях городской застройки).
Техносферой принято считать территорию города или промышленной зоны, т. е. окружающую среду человека, созданную преобразованием биосферы в результате техногенной деятельности (с помощью прямого или косвенного воздействия технических средств). В настоящее время в техносфере проживает 75% жителей нашей планеты. Так же существуют тенденции:
— к непрерывному увеличению городского населения, связанному с высокими темпами роста численности населения на Земле и процесса его урбанизации, имеющего во многом объективный характер;
— к увеличению потребности населения в индивидуальных транспортных средствах, обусловленной как экологическими, гак и социальными причинами, приводящей к росту объема годового выпуска автомобилей.
Так, автомобильный парк нашей области, республики и всего мира постоянно увеличивается, соответственно, увеличивается, и объём вредных веществ, выделяющихся при работе автомобилей. Значит поиск путей снижения этих выбросов — актуальнейшая на сегодня проблема.
В процессе работы автомобили с двигателями внутреннего сгорания выбрасывают в окружающую среду отработанные газы, содержащие вредные для здоровья людей, животных, растений компоненты, в том числе угарный газ, чрезмерное содержание которого в атмосфере особенно вредно для всего живого. Кроме того, автомобили в процессе работы создают шум, вибрацию, что вызывает утомляемость людей, ускоренный износ и разрушения самого подвижного состава, а также сооружений, расположенных на дороге и вблизи неё.
7.1 Воздействие отработавших газов на окружающую среду Загрязнение окружающей среды токсичными компонентами отработавших газов приводит к большим экономическим потерям в хозяйстве, так как токсичные вещества вызывают нарушения в росте растений, что в свою очередь способствует снижению урожаев и потерям в животноводстве. Вредному воздействию особенно подвержено хозяйства, расположенные вблизи крупных городов и транспортных магистралей, кроме того, отработавшие газы способствую ускорению процессов разрушения изделий из пластмассы и резины, а также облицовки и конструкции зданий.
В число токсичных компонентов отработавших газов, оказывающих непосредственное воздействие на окружающую среду, относятся: окись углерода, углеводороды, окислы азота, сажа и соединения свинца.
Воздействие окислов азота нельзя ослабить никакими нейтрализующими средствами. Окислы азота в соединение с водяными парами образуют азотную кислоту, которая разрушает лёгочную ткань, что приводит к хроническим заболеваниям, а также раздражает слизистую оболочку глаз.
Не полностью сгоревшие углеводороды, выбрасываемые с отработавшими газами, представляют собой смесь нескольких сотен химических соединений. Эта смесь, имеющая неприятный запах, является причиной многих хронических заболеваний. Наиболее опасным является бензапирен, который имеет и канцерогенные свойства.
Некоторые ароматические углеводороды обладают сильными отравляющими свойствами. Они воздействуют на процессы кроветворения, центральную нервную систему и мышечную систему. Двуокись серы также оказывает вредное влияние на органы человека, действует раздражающе на кроветворение, костный мозг и селезёнку.
Основная причина загрязнения воздуха заключается в неполном и неравномерном сгорании топлива. В цилиндрах двигателей сгорает топливовоздушная смесь, для приготовления которой применяют весьма сложную аппаратуру.
7.2 Мероприятия по снижению вредного воздействия автотранспорта на окружающую среду Среди мероприятий по экономии топлива важнейшим являются:
рациональная организация дорожного движения;
повышение коэффициента использования грузоподъемности и коэффициента использования пробега автомобиля.
Следует избегать непроизводительной работы двигателя. В холодный период года при безгаражном хранении автомобилей необходимо предусмотреть обогрев автомобилей (двигателя, коробки передач и других агрегатов) от внешнего источника тепла.
Снижению загрязнения атмосферы способствует перевод автомобилей с бензинового (карбюраторного) двигателя на дизельный, в отработавших газах которого содержится значительно меньше окиси углерода и углеводородов. Все больше на дорогах страны появляется газобаллонных автомобилей, в которых используются в качестве топлива сжиженный нефтяной газ (бутан-пропановая смесь) или сжатый природный газ (в основном метан). В отработавших газах газобаллонных автомобилей по сравнению с бензиновыми содержится меньше окиси углерода в 2−4 раза, окислов азота в 1,2−2,0 раза и углеводородов в 1,1−1,5 раза. Новые возможности по повышению экологичности автомобилей открывает внедрение и других видов моторного топлива с менее токсичным составом отработавших газов (синтетические спирты, аммиак, водород и прочие).
Для обезвреживания отработавших газов находят применение различные типы нейтрализаторов. Ведутся работы по усовершенствованию конструкции двигателей (системы питания, зажигания). Идет поиск новых типов силовых установок для автомобилей и их конструктивная доработка (электродвигатели с автономным питанием, роторные двигатели, газовые турбины, инерционные двигатели, двигатели «внешнего» сгорания Стерлинга и др.).
Токсичность отработавших газов двигателей можно уменьшить путем предупреждения образования токсичных компонентов или посредством их нейтрализации.
Устанавливать на двигателе дополнительные устройства для уменьшения токсичности отработавших газов следует при крайней необходимости и только в случае, если исчерпаны все возможности достижения удовлетворительного состава газов путем конструктивных доработок и регулировки двигателя. В настоящее время в большинстве автомобилей применяют различные способы уменьшения концентрации токсичных компонентов перед выбросом отработавших газов из камеры сгорания. С этой целью изменяют конструкцию и регулировку двигателей, что позволяет создать условия, необходимые для полного сгорания смеси в широком диапазоне режимов работы двигателя. Это достигается совершенствованием процессов смесеобразования в системе питания и камере сгорания. Обычно с этой целью для питания двигателей применяют бедные смеси. При этом наблюдается увеличение окислов азота, которое, однако, можно избежать уменьшением угла опережения впрыска. При работе автомобиля на неустановившихся режимах, во время замедления и в период прогрева двигателя после пуска на богатой смеси можно значительно уменьшить выделение углеводородов, применяя дополнительный прогрев всасываемого воздуха горячей охлаждающей жидкостью или отработавшими газами.
Уменьшение содержания окиси азота в отработавших газах достигается путем ограничения максимальных температур сгорания и уменьшения количества подаваемого топлива или одновременным использованием двух этих способов. Подобные результаты можно получить установкой более позднего зажигания, обогащения или значительного обеднения смеси, а также посредством направления части отработавших газов обратно в цилиндр двигателя. Выделение токсичных соединений серы, как отмечалось выше, можно уменьшить только путем ограничения их содержания в топливе или полного их исключения из него.
Чтобы устранить или свести к допустимым пределам все вредные воздействия подвижного состава на окружающую среду, конструкция различных узлов автомобилей, их двигателей должна обеспечивать такой режим работы, который позволял бы не превышать нормы вредных воздействий на окружающую среду, устанавливаемые санитарной службой и правилами охраны труда.
Наиболее перспективными путями по борьбе с вредным воздействием автомобилей на окружающую среду являются создание и широкое применение на подвижном составе электродвигателей (электромобили); производство и установка на подвижном составе так называемых чистых двигателей внутреннего сгорания, обеспечивающих полное сгорание топлива в камере двигателя и тем самым устраняющих выброс в атмосферу вредных остатков процесса сгорания топлива; увеличение парка газобаллонных автомобилей.
Установка на подвижном составе эффективных амортизаторов, надёжных экранов для электрооборудования позволяет снизить шумы, вибрацию и устраняет возникновение радиопомех.
8. Экономическая эффективность конструкторской разработки Как было отмечено выше, в конструкторской части работы, предлагается прибор для проверки герметичности топливной магистрали низкого давления. Внедрение, которого позволяет сократить затраты труда и время на обслуживание и поиск неисправностей. С целью внедрения его на предприятия необходимо просчитать стоимость изготовления, годовой экономический эффект приносимый приспособлением основываясь на экспериментальных данных, и просчитать срок окупаемости. На основе данных расчетов сделаем необходимые выводы о целесообразности внедрения данного приспособления на предприятия.
8.1 Затраты на изготовление прибора для проверки герметичности топливной магистрали низкого давления Для того, что бы определить величину экономического эффекта, определяем изготовления прибора по формуле:
СИЗГ = СКД + СПД + СЗ. СБ + СОН (8.1)
где СКД — стоимость материалов корпусных деталей, тг.
СПД — стоимость покупных деталей, тг.
СЗ.СБ — заработная плата рабочих занятых на изготовлении и сборке, тг.
СОН — общенакладные расходы, тг.
Определяем стоимость покупных деталей, основываясь на средние цены магазинов автозапчастей города Костанай.
Перечень покупных деталей и их стоимость приведена в таблице 8.1.
Таблица 8.1
Перечень покупных деталей
Наименование | Примечание | Цена, тг | |
Насос шинный | 1 шт | ||
Шланг резиновый | 1 метр | ||
Кран двухходовой | 1 шт | ||
Манометр | 1 шт | ||
Метизы | |||
Итого | |||
Определяем стоимость корпусных деталей:
С =Q*СД (8.2)
где: Q — масса материала (по чертежам) (4 кг), кг Сд — стоимость материала (1200 тг), тг.
С =5*1200=6000 тг Определяем заработную плату производственных рабочих:
СПР.Н. = СПР+СД+ССОЦ+СПЕН (8.3)
где: СПР — заработная плата производственных рабочих, тг СД — дополнительная заработная плата, тг ССОЦ — отчисления на социальные нужды, тг СПЕН — отчисления в пенсионный фонд, тг Определяем заработную плату производственных рабочих занятых на изготовлении:
СПР.ИЗГ. =tСР *СЧ *КД (8.4)
где: tcp — средняя трудоемкость изготовления, чел-час.
Трудоемкость была принята на основании фотографии рабочего дня и составляет 20 чел-час.
Сч — часовая тарифная ставка производственного рабочего (300 тг — для рабочего 4-го разряда), тг.
Кдкоэффициент учитывающий доплаты (Кд= 1,025… 1,030)
СПР.ИЗГ. =20* 300* 1,03 = 6180 тг Определяем заработную плату производственных рабочих занятых на сборке:
СПР.СБ = tCP СЧ КД (8.5)
где: tCP — средняя трудоемкость изготовления, чел-час.
Трудоемкость была принята на основании фотографии рабочего дня и составляет 3 чел-час.
Сч — часовая тарифная ставка производственного рабочего (300 тг — для рабочего 4-го разряда), тг.
Кд — коэффициент учитывающий доплаты (К= 1,025… 1,030)
СПРСБ =3*300*1,03=927 тг Определяем общую заработную плату производственных рабочих:
СПР = СПР. ИЗГ + СПР. СБ (8.6)
где:
СПР.ИЗГ — заработная плата производственных рабочих занятых на изготовлении, тг СПР. СБ — заработная плата производственных рабочих занятых на сборке, тг СПР =6180+927=7107 тг Определяем отчисления на социальные налог, который составляет 21% от заработной платы:
-, тг (8.7)
где: RCCОЦ — отчисления на социальное страхование (21%)
тг Определяем отчисления в пенсионный фонд, который составляет 10% от заработной платы:
(8.8)
тг Определяем заработную плату производственных рабочих:
С ПР.Н.= СПР+ССОЦ+СПЕН (8.9)
С ПР. Н =7107+1642+710,7=9459,7 тг Определяем накладные расходы:
(8.10)
=5675,6 тг Стоимость изготовления приспособления:
СИЗГ = СК. Д+СПД+С3.СБ +СО.Н (8.11)
СИЗГ=6000+7100+9459,7+5675,6 =28 235,3 тг.
8.2 Годовой экономический эффект от применения прибора для проверки герметичности топливной магистрали низкого давления
1. Экономия топлива
(8.12)
где АСП — списочное количество автомобилей (20 шт), шт
LГ — годовой пробег автомобиля (20 тыс км), км
QФ — средний фактический расход топлива одного автомобиля (10л/100км)
?Q — процент экономии топлива, (2%)
СTстоимость 1 литра топлива (85 тг за литр, принято по ценам АЗС города Костанай), тг тг
2. Экономия от исключения ненужных работ при ТО и TP с среднем на 2%
(8.12)
где: СТО, ТР — годовая заработная плата ремонтных рабочих проводящих ТО и TP, отнесенная к 1000 км пробега.
(8.14)
где: АСП — списочное количество автомобилей (20 шт), шт
LГ — годовой пробег автомобиля (20 тыс км), км УСI — общая заработная плата рабочих проводящих ТО и TP, тг УСI = СТО1.+С ТО2+СТР (8.15)
C ТО1 =NTО1 · G TО1 (8.16)
C ТО2 =NТО2· G TО2 (8.17)
где: N — количество обслуживаний в год
G — стоимость одного обслуживания, тг (принято что стоимость одного обслуживания ТО — 1 составляет 1500 тг, а ТО — 2 — 3000 тг, TP — 5000 тг).
C ТО1 =80*1500=120 000 тг
C ТО2 =50*3000=150 000 тг
2 000 000 тг УС1=120 000+150000+2 000 000=2270000 тг
тг
45 400 тг
3. Экономия от сокращения простоев во время ТО в среднем на 2%
(8.19)
где: СМC — стоимость машиносмены, тг (принято 3000 тг)
?СМС — процент экономии средств за счет сокращения простоев, %
LTO2 — периодичность ТО — 2, км (принято для а/м УАЗ 8000 км)
=3000 тг Суммарная годовая экономия ЭГ=ЭТ+ЭТО, ТР + (8.20)
ЭГ =68 000+45400+3000=116 400 тг Срок окупаемости дополнительных капиталовложений определяется по формуле:
(8.21)
где: ?К — дополнительные капиталовложения на изготовление приспособления.
= 0,24 года
В итоге получаем, что данное приспособление целесообразно внедрять на предприятия, т.к. уменьшаются простои на ТО, экономится время и топливо на диагностику и данное приспособление быстро окупается.
8.3 Экономическая эффективность основных показателей исследовательской работы Расчет расхода топлива на 100 000 км пробега где S — пробег автомобиля, км
V — расход топлива на 100 км, л
=9000л Затраты на топливо З1 = G*C T (8.23)
где: СТ — стоимость 1 литра топлива, тг (принято 85 тг) З1 =9000*85= 765 000 тг Затраты на топливо базового автомобиля рассчитываем аналогично. Базовым принимаем автомобиль «УАЗ Патриот», фактический расход топлива которого 10 литров на 100 км.
З2= 850 000 тг Расчет экономии затрат на топливо ЗЭ= З1-З2 (8.24)
ЗЭ = 850 000 — 765 000 = 85 000 тг Расчет затрат на замену фильтров.
По стандартам топливные фильтры меняются через 10 000 км пробега. Что будет составлять 10 штук на 100 000 км пробега, если использовать машину на рекомендуемых режимах. Замену фильтров можно снизить до 7 штук на 100 000 км пробега.
Ф = КФ*ЦФ (8.25)
Ф= 7*2000 = 14 000 тг Ф1 = Кф*Цф (8.26)
Ф1= 10*2000=20 000 тг где Ф, Ф, — затраты на замену фильтров (предлагаемый, базовый), тенге;
Кф — количество фильтров;
Цф — цена одного фильтра.
Расчет экономии затрат на замену фильтров ФЭ = Ф-Ф1 (8.27)
ФЭ = 20 000−14 000=6000 тг Расчет суммарной годовой экономии ЗЭ + ФЭ = 85 000 + 6000 = 91 000 тг
Заключение
В процессе выполнения эксплуатационного, технического, организационно-экономического и других расчетов мы пришли к следующим выводам и предложениям.
Практика показывает, что далеко не все предприятия и ТОО расходуют топливо и смазочные материалы в соответствии с технически обоснованными нормами. Основной причиной является технически неграмотная эксплуатация топливоподающей аппаратуры. Эксплуатационники часто не знают назначение отдельных элементов топливной аппаратуры, изменение их параметров в работе и влияние их на показатели работы дизелей.
С целью повышения безотказности и более эффективного использования дизелей, снижения затрат труда и средств на техническое обслуживание и ремонт предъявляются высокие требования к качеству и своевременности диагностирования технического состояния, а так же проведения регулировок топливной аппаратуры.
В работе рассмотрен вариант использования российских автомобилей семейства «УАЗ» в качестве транспорта для диагностики на СТО.
Для снижения затрат по обслуживанию и технической эксплуатации предлагается построить станцию технического обслуживания для диагностики системы питания дизельных двигателей.
В процессе работы над дипломной работой нами были предложены мероприятия (эксплуатационного, технологического, конструктивного характера), способные повысить эффективность диагностики системы питания дизельных двигателей и как следствие снизить их себестоимость, что является важной задачей в условиях рыночных отношений. Использование предложенного в конструкторской части устройства позволит улучшить и облегчит условия труда при ремонте транспорта. Это и являлось конечной целью моей дипломной работы.
Также в дипломной работе рассмотрены вопросы охраны труда, техники безопасности и экологической безопасности проекта.
Также произведен технико-экономический расчет внедрения конструкторской разработки.
1. Афанасьев Л. Л., Островский Н. Б., Цукерберг С. М. «Единая транспортная система и автомобильные перевозки». М., Транспорт 1984 г.
2. Фастовцев В. Г. «Единая транспортная система и автомобильные перевозки». Методические указания М., Транспорт 1986 г.
3. «Положение о ТО и ТР подвижного состава автомобильного транспорта» М., Транспорт 1988 г.
4. Крамаренко Г. В. и др. «Техническая эксплуатация автомобилей». М., Транспорт 1988 г.
5. МИИАТ Краткий автомобильный (транспортный) справочник. М., Транспорт 1987 г.
6. «Прейскурант № 07−02 от 24.12.01. Оптовые цены на нефтепродукты», ТНК, 2 стр.
7. Иворев С. А. «Экономические вопросы при организации работы АТП», М., Высшая школа, 1991 г., 132 стр.
8. Долик П. А. «Справочник по технике безопасности», М., Энергосетьиздат, 1984 г.
9. ГОСТ 12.0.003 — 80 ССБТ. «Опасные и вредные производственные факторы» .
10. ГОСТ 12.4.011−75 «Средства защиты рабочих» .
11. Серов И. П. «Методики определения оптовых цен на продукцию машиностроительного комплекса», М., Экономиздат, 1993 г.
12. «Экономические вопросы в дипломном проекте». Методические указания, Рязанская ГСХА, Рязань 1999 г.
13. Решетов Д. Н. «Детали машин». Издание 4-ое. М., Машиностроение, 1989 г.
14. «Нормы амортизационных отчислений и методы определения оптовых цен на продукцию машиностроения», под редакцией Симонева А. А. М., Экономика, 1992 г.
15. ГОСТ 12.0.003−86 ССБТ «Опасные и вредные производственные факторы» .
16. Демин П. А. «Справочник по технике безопасности». М., 1988 г.
17. Напольский Г. М. «Технологическое проектирование автотранспортных предприятий и станций ТО». Учебник для ВУЗов, М., Транспорт 1985 г.
18. «Краткий справочник НИИАТ». М., Транспорт 1982 г.
19. ГОСТ 12.1.004−76 ССБТ «Пожарная безопасность. Общие требования» .
20. «Охрана труда». Методические указания по дипломному проектированию, Рязанская ГСХА, Рязань 1998 г.
21. ГОСТ 12.1.005−76 ССБТ «Воздух в рабочей зоне. Общие санитарно-технические требования» .
22. ГОСТ 12.1.003−80 ССБТ «Шум. Общие требования безопосности» .
23. ГОСТ 12.01.02−88 ССБТ «Вибрация. Общие требования безопасности» .
24. СНиП II — 4 — 79 «Естественное и искусственное освещение» .
25. Новак В. М. и др. «Справочник технолога машиностроителя». М., Машиностроение 1983 г.
26. Великанов К. М. и др. «Производительность, экономика и организация труда токаря». М., Машиностроение 1984 г.
27. Александров Л. А. «Техническое нормирование на автомобильном транспорте». М., Транспорт 1978 г.
28. Аршинов В. А., Алексеев Т. Р. «Резание металлов и режущие инструменты». М., Машиностроение 1983 г.
29. Черпаков С. С. «Техническое обслуживание и ремонт автобусов». М., Колос 1978 г.
30. Боков В. Н. «Детали машин». М., Высшая школа 1960 г.
31. Кузнецов Е. С. «Техническая эксплуатация автомобилей». Учебник для ВУЗов 3-е издание. М., Транспорт 1991 г., 413 стр.