Формообразование фасонных поверхностей при точении жаропрочных сталей и сплавов на станках с ЧПУ с использованием оперативных коррекций
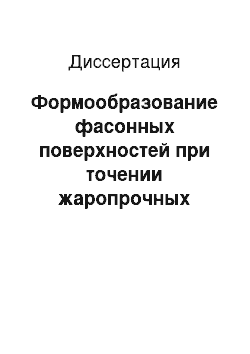
Диссертация
МЕТАЛЛООБРАБОТКИ НА 2001; 2006 г. г." внедрены на предприятиях Тюменской области, а именно: ОАО «ТЮМЕНСКИЕ АВИАДВИГАТЕЛИ», ОАО «ГРОМ», а также ООО «Сибинструментсервис». При изготовлении фасонных деталей авиадвигателей и деталей нефтегазового оборудования реализовано переоснащение токарных станков доработанными системами ЧПУ класса PCNC и диагностическими модулями. Диагностика ТС и оперативный… Читать ещё >
Содержание
- 1. ФОРМООБРАЗОВАНИЕ ФАСОННЫХ ПОВЕРХНОСТЕЙ ДЕТАЛЕЙ ТОЧЕНИЕМ НА СТАНКАХ С ЧПУ ВО ВЗАИМОСВЯЗИ С
- ИЗНАШИВАНИЕМ КРИВОЛИНЕЙНЫХ ЛЕЗВИЙ ИНСТРУМЕНТА
- СОСТОЯНИЕ ВОПРОСА И ЗАДАЧИ ИССЛЕДОВАНИЯ
- 1. 1. Проблемы обеспечения точности формообразования фасонных поверхностей деталей в процессе точения инструментом с криволинейным лезвием
- 1. 2. Системы регулирования, критерии оптимальности процесса резания и их эффективность при точении жаропрочных сталей и сплавов
- 1. 3. Управление обработкой и использование информационно-измерительных систем при точении на станках с ЧПУ
- 1. 4. Проблемы, состояние вопроса и задачи исследования
- 2. ДИАГНОСТИКА И ГЕОМЕТРИЧЕСКАЯ МОДЕЛЬ ИЗНАШИВАНИЯ КРИВОЛИНЕЙНЫХ ЛЕЗВИЙ РЕЖУЩЕГО ИНСТРУМЕНТА ПРИ ТОЧЕНИИ
- 2. 1. Специфика потери работоспособности твердосплавным инструментом при точении жаропрочных сталей и сплавов
- 2. 2. Разработка системы измерения и регистрации геометрических параметров криволинейных лезвий режущего инструмента
- 2. 3. Управление диагностикой с использованием РСМС и формирование модели криволинейного контура лезвия режущего инструмента
- 2. 4. Выводы по разделу
- 3. ДИАГНОСТИКА ПРОЦЕССОВ НАГРУЖЕНИЯ ЭЛЕМЕНТОВ ТЕХНОЛОГИЧЕСКИХ СИСТЕМ И ПРИВОДОВ СТАНКОВ С ЧПУ
- 3. 1. Определение составляющих силы резания по данным диагностики приводов станков с ЧПУ
- 3. 2. Формирование системы модулей для определения отклонений расположения элементов ТС при их нагружении
- 3. 3. Модели отклонений расположения элементов ТС и нагружения следящих приводов станков с ЧПУ
- 3. 4. Выводы по разделу
- 4. НАГРУЖЕНИЕ ИНСТРУМЕНТА И ДИАГНОСТИКА ПРОЦЕССА РЕЗАНИЯ ЖАРОПРОЧНЫХ СТАЛЕЙ И СПЛАВОВ
- 4. 1. Деформирование срезаемого слоя, нагружение и формирование отказов инструмента при точении жаропрочных сталей и сплавов
- 4. 2. Стабилизация контактных нагрузок при изнашивании инструмента и оценка ее эффективности
- 4. 3. Разработка и реализация рациональных схем, параметров нагружения и конструкций сборного инструмента повышенной работоспособности
- 4. 4. Выводы по разделу
- 5. СОВЕРШЕНСТВОВАНИЕ ФОРМООБРАЗОВАНИЯ ФАСОННЫХ ПОВЕРХНОСТЕЙ С ИСПОЛЬЗОВАНИЕМ ОПЕРАТИВНЫХ КОРРЕКЦИЙ ПРИ ТОЧЕНИИ НА СТАНКАХ С ЧПУ
- 5. 1. Формирование модели коррекций траекторий перемещений формообразующего инструмента при точении на станках с ЧПУ
- 5. 2. Синтез структуры программного обеспечения, алгоритмов и интерфейса оператора при управлении обработкой от РСЫС
- 5. 3. Повышение эффективности использования инструмента при точении фасонных деталей из жаропрочных материалов на станках с программным управлением
- 5. 4. Выводы по разделу
Список литературы
- Аваков А. А. Физические основы теории стойкости режущих инструментов Текст. / А. А. Аваков. М.: Машгиз, 1960.- 308 с.
- Адаптивное управление станками Текст. / Под ред. Б. С. Балакши-на.- М.: Машиностроение, 1973. 688 с.
- Адлер Ю. П. Планирование эксперимента при поиске оптимальных условий Текст. / Ю. П. Адлер, Е. В. Маркова, Ю. В. Грановский. М.: Наука, 1976. — 279 с.
- Армарего И.Д. Обработка металлов резанием Текст. / И.Д. Армаре-го, Р. Х. Браун. М.: Машиностроение, 1977. — 325 с.
- Артамонов Е.В. Сборный инструмент Текст. / Е. В. Артамонов, Ю. И. Некрасов, Н. И. Смолин // Машиностроитель.- М., 1984.- № 5.- С.32
- Артамонов Е.В. Прочность и работоспособность сменных твердосплавных пластин сборных режущих инструментов Текст. / Е. В. Артамонов.- Тюмень: ТюмГНГУ, 2003. 192 с.
- А. с. 901 844 СССР, МКИ 001 К 7/02. Устройство для измерения температуры / Ю. И. Некрасов, Е. В. Артамонов, И. А. Ефимович, В. С. Воронов (СССР). № 2 884 590/18−10- Заявл. 19.02.80- Опубл. 30.01.82, Бюл. № 4.
- Базров Б. М. Адаптивное управление станками Текст. / Б. М. Базров.- М.: Знание, 1975. 57 с.
- Безъязычный В.Ф. Оптимизация технологических условий механической обработки деталей авиационных двигателей Текст. / В.Ф. Безъ131язычный, Т. Д. Кожина, A.B. Константинов и др. М.: МАИ, 1993. -184 с.
- Бетанели А.И. Прочность и надежность режущего инструмента Текст. / А. И. Бетанели. Тбилиси: Сабчота Сакартвело, 1973. — 302с.
- Бобров В.Ф. Определение напряжений в режущей части металлорежущих инструментов Текст. / В. Ф. Бобров // Высокопроизводительное резание в машиностроении. М., 1966. — С. 233−228.
- Васин С. А. Резание материалов: термомеханический подход к системе взаимосвязей при резании Текст.: учебник для техн. вузов / С. А. Васин, A.C. Верещака, B.C. Кушнер. М.: Изд-во МГТУ им. Н. Э. Баумана, 2001. — 448 с.
- Великанов K.M. Экономичные режимы резания металлов Текст. / K.M. Великанов, В. И. Новожилов. М.: Машиностроение, 1972. — 120 с.
- Верещака A.C. Работоспособность режущего инструмента с износостойкими покрытиями Текст. / A.C. Верещака. М.: Машиностроение, 1993. — 198 с.
- Виноградов A.A. Определение оптимальной скорости резания по коэффициенту усадки стружки Текст. / A.A. Виноградов // «Станки и инструмент». 1991. — № 7. — С. 32−33.
- Грановский Г. И. О стойкости инструмента как исходном параметре для расчета режимов резания Текст. / Г. И. Грановский // «Вестник машиностроения». 1965. — № 8. — С. 59- 64.
- Гречишников В.А. Системы проектирования режущих инструментов Текст. / В. А. Гречишников. М.: ВНИИТЭМР, 1987. — № 2. — 52 с.132
- Грубый C.B. Физическое моделирование процесса изнашивания твердосплавных резцов Текст. /C.B. Грубый // «Справочник. Инженерный журнал». 2002. — № 2. — С. 37−43.
- Жуков Ю. Н. Механизм и схема стружкообразования при несвободном резании материала Текст. / Жуков Ю. Н.// «Известия вузов». -М.: Машиностроение, 1985. № 9.- С. 138 — 141.
- Зорев H.H. Вопросы механики процесса резания металлов Текст. / H.H. Зорев. М., Машгиз, 1956. — 367 с.
- Использование станков с программным управлением / Под ред. В. Лесли. М.: Машиностроение, 1976. — 421 с.
- Кабалдин Ю. Г. Построение перспективных систем управления металлорежущими станками на основе самоорганизации и принципов искусственного интеллекта Текст. / Ю. Г. Кабалдин, C.B. Биленко // «Вестник машиностроения». -2002. № 6. — С. 59−65.
- Каминская В.В. Направления развития адаптивных систем управления для станков с ЧПУ Текст. / В. В. Каминская // «Станки и инструмент». 1973.- № 3. — С. 2 -4.
- Кацев П.Г. Статистические методы исследования режущего инструмента Текст. / П. Г. Кацев. М.: Машиностроение, 1974. — 231 с.
- Каширин А.И. К вопросу прочности режущей части инструмента при резании труднообрабатываемых сталей Текст. / А.И. Каширин// «Трение и износ при резании металлов». М.: Машгиз, 1955. — С. 5 -13.
- Каяшев А.И. Методы адаптации при управлении автоматизированными станочными системами Текст. / А. И. Каяшев, В. Г. Митрофанов, А. Г. Схиртладзе. М.: Машиностроение, 1995. — 240 с.
- Клушин М.И. Определение стойкости режущих инструментов, обеспечивающей получение максимально возможной прибыли и производительности общественного труда Текст. / М. И. Клушин, Г. В. Аносов // «Вестник машиностроения». 1970. — № 6. — С. 74−76.
- Кондашевский B.B. Активный контроль размеров деталей на металлорежущих станках Текст. / В. В. Кондашевский, В. Лотце: Пер. с нем. Омск: Зап.-Сиб. изд-во, 1976. — 431 с.
- Корытин A.M. Оптимизация управления металлорежущими станками Текст. / A.M. Корытин, Н. К. Шапарев. М.: Машиностроение, 1974. — 200 с.
- Красильников В.А. Методика измерения контактных нагрузок на задней грани резца Текст. / В. А. Красильников, В. Н. Козлов, А. И. Подворчан // Исследования процесса резания и режущих инструментов. Томск, 1984. — С. 130−133.
- Кривошей В.М. Экономика оптимального резания труднообрабатываемых материалов на станках с ЧПУ Текст. / В. М. Кривошей, В. Л. Юрьев // Сборник научных трудов «Вопросы оптимального резания», вып. 1. Уфа, 1976. — С. 71−79.
- Кузнецов В.Г. Приводы станков с программным управлением Текст. / В. Г. Кузнецов. М.: Машиностроение, 1983. — 248 с.
- Куклин Л.Г. Повышение прочности и износостойкости твердосплавного инструмента Текст. / Л. Г. Куклин, В. И. Сагалов, В.Б. Серебров-ский, С. П. Шабашов. М.: Машиностроение, 1968. — 140 с.
- Куфарев ГЛ. Стружкообразование и качество обработанной поверхности при несвободном резании Текст. / Г. Л. Куфарев, К. Б. Океанов, В. А. Говорухин. Фрунзе, Изд-во Мектеп, 1970. — 170 с.
- Лоладзе Т.Н. Прочность и износостойкость режущего инструмента Текст. / Т. Н. Лоладзе. -М.: Машиностроение, 1982. 317 с.
- Лошак М.Г. Прочность и долговечность твердых сплавов Текст. / М. Г. Лошак. Киев: Наукова думка, 1984. — 328 с.
- Макаров А.Д. Оптимизация процессов резания Текст. / А. Д. Макаров. М.: Машиностроение, 1976. — 276 с.
- Мартинов Г. М. Открытая система ЧПУ на базе общей магистрали Текст. / Г. М. Мартинов // «Автомобильная промышленность». -1997.-№ 4.-С. 31−34.
- Матвеев М.Г. Моделирование информационных потоков технологического объекта управления Текст. / М. Г. Матвеев // Математическое моделирование технологических систем. Воронеж: ВГТА, 1995.-С. 34−41.
- Мелихов В.В. Контактные процессы на задней поверхности режущего инструмента Текст. / В. В. Мелихов // Учебное пособие. Тюмень: ТГУ, 1989.- 112 с.
- Михайлов О.П. Современный электропривод станков с ЧПУ и промышленных роботов Текст. / О. П. Михайлов, Р. Т. Орлова, A.B. Пальцев: под ред. Б. И. Черепанова. М.: Высш. шк., 1989. — 111 с.
- Михеев Ю.Е. Системы автоматического управления станками Текст. / Ю. Е. Михеев, В. Л. Сосонкин. М.: Машиностроение, 1978. — 264 с.
- Молчанов Г. Н. Повышение эффективности обработки на станках с ЧПУ Текст. / Г. Н. Молчанов. М.: Машиностроение, 1979. — 204 с.
- Моргунов А.П. Некоторые вопросы технологического обеспечения и контроля надежности неподвижных неразъемных соединений: кандидатская диссертация Текст. / А. П. Моргунов. Омск: ОМПИ, 1974.-211 с.
- Невельсон М.С. Анализ точности механической обработки с целью выбора типа корректирующей системы Текст. / М. С. Невельсон // «Передовая технология и автоматизация управления процессами обработки деталей машин». Л., 1970. — С. 309 — 317.
- Некрасов Р.Ю. Управление обработкой на станках с ЧПУ Текст. / Р. Ю. Некрасов,. С. С. Полуйков, A.A. Стулень // Официальный каталог IX Междунар. выставки «ЭКСПО Наука 2003″. — М.: ВВЦ, 2003. -С. 150.
- Некрасов Р.Ю. Модель разрушений режущих лезвий инструмента из металлокерамических твердых сплавов Текст. / Р. Ю. Некрасов // Материалы всероссийской научной конференции молодых ученых „Наука. Технологии. Инновации“. Новосибирск, 2006. — С. 26.
- Новиков Ю.В. Функциональные модули контрольно-измерительных систем на базе микро ЭВМ Текст. / Ю. В. Новиков // „Микропроцессорные средства и системы“, 1990. № 3. — С. 75−77.
- Обработка резанием высокопрочных, коррозионностойких и жаропрочных сталей /под ред. П. Г. Петрухи. М.: Машиностроение, 1980.- 167 с.
- Овчинников В.В. Техническая база интерфейсов локальных вычислительных сетей Текст. / В. В. Овчинников, И. И. Рыбкин. М.: Радио и связь, 1989.- 272 с.
- Опитц Г. Современная техника производства (состояние и тенденции) Текст. / Г. Опитц. М.: Машиностроение, 1975. — 280 с.
- Остафьев В.А. Расчет динамической прочности режущего инструмента Текст. /В.А. Остафьев. М.: Машиностроение, 1979. — 168 с.137
- Охоцимский Д.Е. Цифровая контурная следящая система для робото-технических устройств Текст. / Д. Е. Охоцимский, А. К. Платонов, Е. И. Кургушев, B.C. Ярошевский // Микропроцессорные системы для робототехники. М.: Наука, 1984. — С. 37 — 48.
- Панфилова Н.Ю. Организация использования станков с программным управлением и их эффективность Текст. / Н. Ю. Панфилова // „Повышение эффективности эксплуатации станков с ЧПУ“. Курган: НТО Машпром, 1978. — С. 7 — 12.
- Панкин A.B. Обработка металлов резанием Текст. / A.B. Панкин. -М.: Машгиз, 1961.-288 с.
- Петрушин С.И., Бобрович И. М., Корчуганова М. А. Оптимальное проектирование формы режущей части лезвийных инструментов Текст. / С. И. Петрушин, И. М. Бобрович, М. А. Корчуганова: Учебное пособие. Томск: Изд. ТПУ, 1999. — 91 с.
- Повышение эффективности эксплуатации станков с ЧПУ // Тезисы докладов зональной научно-технической конференции: Под ред. Ю. С. Шарина, Л. М. Сединкина. Курган: НТО Машпром, 1978. — 107 с.
- Подураев В.Н. Автоматически регулируемые и комбинированные процессы резания Текст. / В. Н. Подураев. М.: Машиностроение, 1977.-303 с.
- Полетика М.Ф. Контактные нагрузки на режущих поверхностях инструмента Текст. / М. Ф. Полетика. М.: Машиностроение, 1969. -150 с.
- Проников A.C. Программный метод испытания металлорежущих станков Текст. / A.C. Проников. М.: Машиностроение, 1985. — 288 с.
- Проскуряков H.A. Разработка интегрированной системы диагностики и управления процессами обработки на токарных станках с ЧПУ: кандидатская диссертация текст. / H.A. Проскуряков. Тюмень: ТюмГНГУ, 2005.-218 с.
- Ратмиров В.А. Повышение точности и производительности станков с программным управлением Текст. / В. А. Ратмиров, И. Н. Чурин, C.JI. Шмутер. М.: Машиностроение, 1970. — 343 с.
- Решетов Д.Н. Современные направления развития станковедения Д.Н. Решетов, В. В. Каминская, А. И. Левин, В. Т. Портман // „Станки и инструмент“. 1977. — № 6. — С. 4 -9.
- Резников А.Н. Теплофизика резания Текст. / А. Н. Резников. — М.: „Машиностроение“, 1969. 287 с.
- Розенберг A.M. Элементы теории процесса резания металлов Текст. / A.M. Розенберг, А. Н. Еремин. М.: Машгиз, 1956. — 318 с.
- Розенберг Ю.А. Силы резания и методы их определения. Общие положения Текст. / Ю. А. Розенберг, С. И. Тахман: Учебное пособие, Ч I. Курган: КМИ, 1995. — 103 с.
- Свидетельство об официальной регистрации программ для ЭВМ 2 008 610 388. Российская Федерация. Программа управления компьютерным манипулятором для определения деформации срезаемого слоя при точении на станке с ЧПУ Текст. / Некрасов Р. Ю., Путилова139
- У.С., Ковенский И.М.- заявитель и патентообладатель Тюм. гос. нефте-газ. ун-т. № 2 007 614 687- заявл. 26.11.2007, опубл. 21.01.2008.- 1 с.
- Силин С.С. Автоматическое управление процессами резания Текст. / С.С. Силин//"Станки и инструмент». 1971. — № 1. — С. 13−15.
- Силич A.A. Технология обработки зубчатых колес цилиндрических передач Новикова Текст. / A.A. Силич. Тюмень: Изд-во ТюмГНГУ, 2007.- 162 с.
- Смолин Н.И. Исследование напряженно-деформированного состояния многогранных пластин применительно к вопросам прочности сборного режущего инструмента Текст. / Н. И. Смолин // Автореф. дисс. к.т.н. Омск, 1987. — 17 с.
- Солод В.И. Автоматическое управление режимами резания металлов Текст. / В. И. Солод, В. В. Глушко, Г. Г. Гегелов. М.: Машиностроение, 1979. — 157 с.
- Сосонкин В. JI. Концепция системы ЧПУ типа PCNC с открытой архитектурой. Текст. / B.JI. Сосонкин, Г. М Мартинов // «Станки и инструмент». 1998. — № 5. — С. 7−15.
- Сосонкин B.JI., Мартинов Г. М. Современные представления об архитектуре систем ЧПУ класса PCNC Текст. / B.JI. Сосонкин, Г. М Мартинов // «Автоматизация проектирования». -1998. № 3(9). — С. 35−39.
- СПМ 24 655, МПК 7 В 23 В 27/16. Сборный режущий инструмент Текст. / Р. Ю. Некрасов (РФ). № 2 002 106 044/20- заявл. 15.03.2002, опубл. 20.08.2002, Бюл. № 23. — 2 е.: ил.
- Старков В.К. Технологические методы повышения надежности отработки на станках с ЧПУ Текст. / В. К. Старков. М.: Машиностроение, 1984. — 120 с.
- Сулига В.И. Системы автоматического управления резанием Текст. / В. И. Сулига, В. В. Глушко. Донецк: Донбасс, 1973. — 128 с.
- Талантов Н.В. Физические основы процессов резания, изнашивания и разрушения инструмента Текст. / Н. В. Талантов. М.: Машиностроение, 1992. — 240 с.
- Тейлоръ Ф. Искусство ръзать металлы Текст. / Ф. Тейлор. — СПб: Издание инженера JT.A. Левенстерна «Русская Скоропечатня», 1909. -351 с.
- Утешев М.Х. Методы повышения работоспособности инструментов Текст. / М. Х. Утешев: Учебное пособие. Тюмень: ТюмГНГУ, 2001. — 112 с.
- Хает Г. Л. Прочность режущего инструмента Текст. / Г. Л. Хает. М.: Машиностроение, 1975. — 166 с.
- Хухлаев Е. Операционные системы реального времени и Windows NT Текст. / Е. Хухлаев // «Открытые системы». 1997. — № 5. — С. 48−51.
- Шаламов В.Г. Исследование операции цилиндрического фрезерования узких поверхностей деталей, изготовленных из высокопрочной стали, подвергнутой ТМО Текст. / В. Г. Шаламов: Автореф. дисс. к.т.н. Челябинск. — 1978. — 20 с.
- Шарин Ю.С. Обработка деталей на станках с ЧПУ Текст. / Ю. С. Шарин. М.: Машиностроение, 1983. — 117 с.
- Экономическая эффективность станков с числовым управлением / Под ред. П. С. Мирошникова. Киев: Наукова думка, 1976. — 174 с.
- Archibald F. R. Analysis of the Stresses in a Cutting Edge. «Trans, of the ASME», 1956, vol. 78, N 6, p. 1149 1154.
- Boothroyd G. Temperatures in Ortogonal Metal Cutting. — «Proc. Inst. Mech. Eng.», London, v. 177, 1963, p. 144 — 152.
- Centner R.M., Idelsohn I.M.- Adaptive Controller for a Metal Cutting Process.- «IEEE Transaction on Application and Industry», 1964, vol. 83, № 72, p. 154- 161.
- Chao B.T., Trigger K.I. Cutting temperatures and metalcutting of the ASME. — «Iornal of Enginieerung for Industry», 1959, v.81, Ser.B., № 2, p. 861 — 866.
- Eberle I. Voraussetzungen, Stand und Ausblick beim Werkzeug fur NC — Werkzeugmachinen — «Machinenmarkt», 1973,79, № 68, 1477−1480.
- Feiten K. Entwicklung einer numerisch gesteuerten NC — Drehfertigungszelle — «Technisches Zentralblatt fur praktische Metalbearbeitung». Ig. 71, № 10, p. 8−11.
- Poch H., Hecher N.- Technologische und okonomische Betrachtungen zum Einsats der DFS 400 NC mit ACEMA- «Fertigungstechnik und Betrieb», 1973,23, № 1, 13 18.
- Pekelharing A. J. The Exit Failure in Interrupted Cutting. — Annals of the CIRP. Manufacturing Technology, 1978, vol. 27/1, p. 5 10.
- Tanaka Voschinobu, Ikawa Naoga, Vasugi Kuniharu Stress analysis in cutting edge Fundamental study of Cutting edge chipping. 1st. Report. Сеймицу Кикай, I. Jap. Soc. Precis. Eng., 1973, 39, № 10, 1055 1061.
- Trent E. M. Metal Cutting. Butterworths & Ltd. London Boston, 1977, p. 203.
- Въчков С.Г. Производительност, точност на обработка и надежност на металлорежещите машин. София: Държавно издательство «Тех-шка», 1980. — 244 с.
- Wiebach H.G.- Einfuhrung in die Scnitt weroptimierung- «VDI-Z», 1978, 120, № 18, 825−829.
- Zorev N. N., Uteschev M. Ch., Senjukov W. A., Institut Zniitmasch, Moskau. Untersuchung der Kontaktspannungen auf den Arbeitsflachen des Werkzeugs mit einer Schneidenabrundung. Annals of the CIRP vol. 20/1
- ФЕДЕРАЛ Ь-Н-О Е АГЕНТСТВО ПО ОБРАЗОВАНИЮ
- ГОСУДАРСТВЕННОЕ ОБРАЗОВАТЕЛЬНОЕ УЧРЕЖДЕНИЕ ВЫСШЕГО ПРОФЕССИОНАЛЬНОГО ОБРАЗОВАНИЯ
- ТЮМЕНСКИЙ ГОСУДАРСТВЕННЫЙ НЕФТЕГАЗОВЫЙ УНИВЕРСИТЕТ"1. ОЧЛооувЬЖ1. На правах рукописи1. НЕКРАСОВ Роман Юрьевич
- ФОРМООБРАЗОВАНИЕ ФАСОННЫХ ПОВЕРХНОСТЕЙ ПРИ ТОЧЕНИИ ЖАРОПРОЧНЫХ СТАЛЕЙ И СПЛАВОВ НА СТАНКАХ С ЧПУ С ИСПОЛЬЗОВАНИЕМ ОПЕРАТИВНЫХ КОРРЕКЦИЙ
- Специальность 05.03.01 Технологии и оборудование механической и физико-технической обработки
- Диссертация на соискание ученой степени кандидата технических наук
- Научный руководитель-заслуженный деятель науки РФ, доктор технических наук, профессор КОВЕНСКИЙ Илья Моисеевич1. Тюмень 2008