Проект обогатительной фабрики по переработке медно-цинковых руд Абызского месторождения
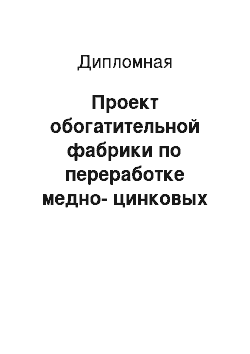
Управление оборудованием устраивают, как правило, кнопочным, расположенным на высоте 1−1,6 м над уровнем пола рабочего места при обслуживании стоя и 0,6−1,2 м — при обслуживании сидя. Посты, пульты и панели управления располагают в местах, обеспечивающих хорошую видимость обслуживаемого агрегата и прилегающих к нему участков, применяя световую и звуковую сигнализацию для извещения о пуске… Читать ещё >
Проект обогатительной фабрики по переработке медно-цинковых руд Абызского месторождения (реферат, курсовая, диплом, контрольная)
Мировое потребление цветных металлов с каждым годом возрастает. В то же время качество перерабатываемых руд и содержание в них металлов непрерывно снижается. Поэтому руды, добываемые в настоящее время, непригодны для непосредственного получения из них металла, и их дальнейшая переработка экономически не выгодна без предварительного обогащения.
Руды цветных металлов отличаются сложностью минерального состава. В большинстве своем они являются комплексными, полиметаллическими, содержащими несколько цветных и редких металлов в виде минералов, совместное присутствие которых затрудняет или исключает применение металлургических процессов без предварительного разделения их методами обогащения. Развитие техники обогащения значительно расширило сырьевую базу промышленности и позволило вовлечь в активные запасы новые месторождения цветных металлов. В настоящее время обогатительные процессы играют первостепенную роль в использовании рудного сырья и производстве цветных металлов.
В соответствии с полученным заданием необходимо разработать схему обогащения и запроектировать обогатительную фабрику по переработке медно — цинковых руд Абызского месторождения с производительностью 600 тысяч тонн в год. При проектировании за аналог взята Абызская обогатительная фабрика. В проекте так же необходимо привести технико-экономическое обоснование строительства данной фабрики, расчет рентабельности производства и себестоимости продукции. При выполнении работы использовались данные, действующей обогатительной фабрики в период прохождения преддипломной практики.
1. Общая пояснительная записка
1.1 Краткая характерисктика предприятия
Обогатительная фабрика является одним из цехов акционерного общества «КазахМыс» и расположено в Каракалинском районе Карагандинской области, в 100 км к востоку от города Каркалинск.
Годовая производительность фабрики по руде 600 000 тонн. Готовой продукцией фабрики являются медный и цинковый концентраты.
Основным потрибителем медного концентрата являются Балхашский медь зоводь, а цинковой концентрат перерабатывается на УК СЦК.
Схема дробления — трехстадиальная, схема измельчения — двухстадиальное, схема флотации предусматривает селективную медную и цинковую флотацию, доизмельчения чернового концентрата основной медной флотации.
1.2 Основные технологические и проектные решения
Принятый основной метод обогащения — флотационный. Схема флотация селективная с получением медного и цинкового концентратов. Подготовительные процессы: трехстадиальное дробление с предварительным грохочением во второй и третьей стадии. Двухстадиальное измельчение с замкнутым циклом поверочной классификации в первой и во второй стадии.
Вспомогательные процессы: доизмельчение медногоконцентрата после основной флотации, трехстадиальное обезвоживание медного и цинкового концентрата путем сгущения, фильтрования и последующей сушкой.
Все процессы осуществляются с применением стандартного технологического оборудования отечественного производства.
1.3 Состав обогатительной фабрики
В состав обогатительной фабрики входят: корпус крупного, среднего и мелкого дробления, главный корпус, фильтровальное отделение, реагентный корпус, административный корпус, бытовой корпус и вспомогательные кор-пуса. Компоновка оборудования выполнена с учетом транспортировки продуктов на наименьшие расстояния с соблюдением принципа самотечности технологических продуктов, а также компактности размещения оборудования и удобства их обслуживания.
Количество секций главного корпуса — 1. Схема компоновки оборудования уступчато-одноэтажные.
1.4 Численность и профессионально-квалификационный состав работающих
Численность трудящихся по категориям:
1) ИТР — 30 чел.;
2) МОП — 10 чел.;
3) рабочие — 306 чел.
1.5 Потребность в энерго и водоресурсах
Годовой расход электроэнергии: силовой — 287 704 569 кВт? ч;
световой — 25 770 378 кВт? ч;
общий — 257 703 789 кВт? ч;
общий — 2 034 000 м3
Годовой расход воды: свежей — 406 800 м3
оборотной — 1 627 200 м3.
2 Генеральный план, транспорт и рекультивация нарушенных земель
2.1 Генеральный план
2.1.1 Характеристика площадки для строительства
Площадка для строительства фабрики расположена в 2 км от поселка и в 1 км от хвостохранилища. Рельеф площадки колеблется в пределах абсолютных отметок 300−415 м с уклоном на север. Господствущин ветры имеет северо-восточное направление.
2.1.2 Перечень зданий и сооружений, описание планировочных решений
В состав генерального плана включены следующие здания:
1) корпус крупного дробления;
2) рудоусреднительный склад;
3) главный корпус;
4) административно-бытовой корпус;
5) реагентное отделение;
6) фильтровально-сушильное отделение;
7) склад извести и отделение приготовления известкового молока;
8) склад концентратов;
9) воздуходувно-компрессорная станция;
10) весовая;
Сооружения:
1) галерея от корпуса крупного дробления до рудосреднительного склада;
2) галерея из рудосреднительного склада в главный корпус;
3) галерея из главного корпуса в фильтровальное отделение;
4) галерея из фильтровальноотделения на склад концентратов;
5) галерея из главного корпуса в реагентное отделение;
6) галерея из реагентного отделения в склад извести;
7) галерея из реагентного отделения в фильтровальное отделение;
и эстакады;
8) пульпопроводов;
9) электрокабелей.
Общая площадь, занятая под зданиями и сооружениями, составляет 25 250 м2.
Корпус крупного дробления соединен с рудоусреднительным корпусом транспортерными галереями.
Главный корпус находится от рудоусреднительного склада на расстоянии 30 м и соединен с ним наклонными транспортерными галереями.
Отделение сгущения расположено в главном корпусе; фильтровальное отделение в здании в 40 км от главного корпуса.
2.1.3 Решения по инженерным сетям и коммуникациям
Почти все инженерные сети и коммуникации расположены под землей в проходных каналах, за исключением хвостового коллектора, который начи-нается от главного корпуса и установлен на железобетонных опорах высотой 3.5 м. Протяженность хвостового коллектора 1000 м.
2.1.4 Благоустройство и озеление
Для пешеходного движения вдоль всех автомобильных дорог, а также между отдельными зданиями и сооружениями устроены асфальтированные дорожки и тротуары. Вся свободная территория занята посадками декоративных растений.
2.1.5 Показатели генерального плана
Общая территория площадки 105 000 м2, в т. ч.;
1) под зданиями и сооружениями — 26 250 м2;
2) под надземнымными коммуникациями — 3000 м2;
3) под железными и автомобильными дорогами — 25 000 м2;
4) под тротуарами и переходами — 10 000 м2;
5) под благоустройством и озелением (без тротуаров и переходов) — 19 750 м2.
Коэффициент застройки КЗ рассчитывется по формуле:
S1
KЗ = —————,
S0
где: S1 — площадь под зданиями и сооружениями, м2;
S0 — общая площадь территории, м2.
В соответствии с формулой коэффициент застройки KЗ составит:
KЗ = ————— = 0,25
Коэффициент использования площадки КИ рассчитывается по формуле:
S2
KИ = ——,
S0
где: S2 — общая площадь, за исключением площади, занятой под благоустройством и озелением, м2.
В соответствии с формулой коэффициент застройки KИ составит:
KИ = ————— = 0,55.
2.2 Транспорт
2.2.1 Виды транспорта и грузооборот
Транспорт исходного сырья на территорию фабрики осуществляется авто-мобилями типа БелАЗ грузоподъемностью 40 и 110 т. Суточное количество транспортируемой руды составляет 1967 т. руды.
По железной дороге на фабрику поступают грузы специального назна-чения от сторонних поставщиков: дробящие тела, флотореагенты, обо-рудование. Отправка готовой продукции с территории фабрики произво-дится в полувагонах грузоподъемностью 60 т. Среднесуточное количество отправляемых концентратов составляет: медный концентрат — 110,4 т/сут; цинковый концентрат — 105,2 т/сут.
Все прочие грузы доставляются на фабрику автопоездами грузоподъемностью до 10 т. Ближайщим от месторождения населенным пунктом является поселок Абыз, расположенный в 5 км к северо-западу.
2.2.2 Железные дороги
Желездорожная сеть нормальной колеи, тупиковая, общей протяжен-ностью 2000 м, занимает площадь с учетом полосы отчуждения 24 000 м2. Имеются железодорожные тупики: в главном корпусе, в реагентном отделении, в складе концентратов.
2.3 Рекультивация нарушенных земель
2.3.1 Перечень участков, подлежащих рекультивации
В результате строительства и эксплуатации предприятия нарушаются земельные участки общей площадью 105 000 м2; снято плодородного слоя с 56 788 м2.
Итого общая площадь земель, подлежащих рекультивации, составляет 105 000 м2.
2.3.2 Метод восстановления участков
Восстановление участков, занятых сухими пляжами хвостохранилища, производится по мере их образования в процессе эксплуатации, и закан-чивается после окончания эксплуатации хвостохранилища. Восстановление участков выполняется следующими методами:
1) планировка откосов и пляжей с помощью землеройных машин;
2) выброчное нанесение культорного слоя из привозного грунта в местах посадки растительности;
3) посадка деревьев, кустарников и засухоустойчивых лиственных порд.
3. Технология производства, обеспечение энергоресурсами
3.1 Технология производства
3.1.1 Сыревая база, характеристика сырья
Сыревой базой проектируемой обогатительной фабрики является месторождение «Абыз», которое расположено в Каркалинском районе Карагандинской области, в 100 км к востоку города Каркалинск.
Район месторождения относится к низкогорному мелкосопочнику. Максимальные абсолютные отметки достигают +1172 и +1150 м, а непо-средственно на месторождении не превышают +810 м. Растительность пред-ставлена редким травяным покровом и кустарником.
В геологическом строении месторождения Абыз принимают участие отложения нижнего и среднего девона. Промышленное оруденение выявлено в двух зонах: Восточной и Западной. Рудные тела Восточной зоны имеют преимущественно линзовидную форму и залегают на глубине 30−250 м. Рудные тела Западной зоны также имеют линзовидную форму и залегают на глубине 250−300 м. По составу руд основную ценность представляет медь и цинк. Руды месторождения являются труднообогатимыми. Месторождение Абыз открыто в 1979 г. Первоначальное геологоразведочные работы проведены в 1976;1978 гг. Гидротермально измененные породы с содержанием полезных компонентов прослежены на глубину более 1,5 км. Детальная разведка проводилась с 1984 по 1992 гг.
Балансовые запасы руды по категориям С1 и С2 составили 8233 тыс.т., в том числе в них содержится 348,3 т. меди.
В таблице 1 приведен характеристика сырья месторождения «Абыз».
3.1.2 Технология обогащения
Обогащение руды месторождения «Абыз», осуществляется на Карагайлинской обогатительной фабрике по селективной схеме, которая включает в себя следующие основные процессы: дробление, измельчение, флотацию, сгущение и фильтрацию.
Таблица 1
Характеристика сырья месторождения «Абыз»
Типы руд | Содержание основных компонентов | |||||
Cu,% | Zn,% | Au, г/т | Ag, г/т | Fe,% | ||
1. Медно-цинковая руда месторождения «Абыз» | 1,24 | 3,27 | 3,90 | 43,76 | 21,0 | |
2. Планируется начать переработку медных руд месторождения «Космурын» | 5,86 | 0,20 | 2,20 | 48,40 | 33,35 | |
Руда с карьера на ОФ доставляется желездорожным транспортом в думпкарах. Исходная руда подвергается трех стадиальному дроблению до крупности 25 мм и двух стадиальному измельчению до крупности 75% класса 0,074 мм. Измельченная руда подвергается медной флотации с получением медного концентрата. Хвосты медной флотации подвергаются цинковой флотации с получением цинкого концентрата и отвальных хвостов. Медный и цинковый концентраты подвергаются двух стадиальному обезвоживанию путем сгущения и фильтрации. После обезвоживания полученные концентраты направляются на склад готовой продукции, откуда отгружаются железно-дорожным транспортом потребителю. Отвальные хвосты совместно со сливом сгустителей направляются в хвостохранилище.
В таблице 2 показана физико-механическая характеристика руды месторождения «Абыз».
Таблица 2
Физикомеханическая характеристика руды месторождения «Абыз»
Параметры | Значение | |
Максимальный кусок руды, поступающий на фабрику, мм | ||
Средневзвешанная плотность, т/м3 | 2,9 | |
Насыпная плотность, т/м3 | 1,6 | |
Коэффициент крепости по шкале М.И.Протодьяконова | 12−13 | |
Влажность,% | ||
Плановые содержание металлов в руде: Cu — 1,2%, Zn — 3,2%
3.1.3 Режим работы цехов и расчет их производительности
Заданная производительность фабрики составляет 600 000 т/ч. Корпус крупного дробления работает по режиму карьера 305 дней в году в две смены по 7 часов. Главный корпус работает 340 дней в году в три смены по 8 часов. Корпус фильтрации работает синхронно с главным корпусом. Часовая производительность корпуса крупного дробления (0 дробл.) и главного корпуса (0 изм.) рассчитывается по формуле:
Qг
Q0 = ————————————-, т/ч.
N * m * n * Kв
где: 0 дробл. часовая производительность цеха, т/ч;
г годовая производительность фабрики, т/ч;
N число рабочих дней в году;
m число рабочих смен в сутки;
n число рабочих часов в смену;
Kв коэффициент учитывающий различие в физических свойствах руды. Часовая производительность корпуса крупного дробления составит:
Q0 др. = —————————————- = 148 т/ч;
305 * 2 * 87* 0,95
Часовая производительность главного корпуса составит:
Q0 изм. = ———————————— = 77 т/ч.
340 * 3 * 8 * 0,95
3.1.4 Анализ научно-исследовательских работ
Основным источником сырья для обогатительной фабрики является поли-металлическая руда месторождения «Абыз».
В результате переработки руды получаются следующие концентраты:
1) медно-пиритный концентрат;
2) цинковый концентрат.
В конце 2004 года началось осуществление реконструкции и восстановление Карагайлинской обогатительной фабрики. Выпуск концентра-тов на обогатительной фабрике начался с янванря 2005 года.
За период 2005 года выпуск медно-пиритного концентрата составил 53,1% от плана, выпуск цинкового концентрата составил 51,3% от плана.
Основной причиной невыполнения плановых показателей по переработке руды и производству концентратов является то, что в период 2004;2005 годов осуществлялся запуск обогатительной фабрики в эксплуа-тацию и отработка технологии обогащения.
Основная производственная деятельность Карагайлинской обогати-тельной фабрики заключается в переработке руды и выпуске концентратов. Другими видами производственной деятельности и услугами обогатитель-ная фабрика не занимается.
Первоначальная проектная производительность фабрики составляла 225,0 тыс.тн. В настоящее время производительность фабрики доведена до 460,0 тыс. тн в год.
До 2004 года фабрика перерабатывала только полиметаллическую руду месторождения «В» открытой добычи. С октября 2004 г. были вовлечены в переработку медно-колчеданные руды месторождения «Сувенир». С 2005 года начата переработка полиметаллической руды месторождения «В» подземной добычи. Обогащение руды месторождения «В» ведется по разработанной рудоуправлением селективной технологии с получением медного концентрата марки ППМ, цинкового концентрата марки КЦ-4 и пиритного концентрата марки КБ-6.
3.2 Выбор и обоснование технологической схемы
В основу технологии проектируемой фабрики положена схема и режим действующей майкаинской обогатительной фабрики. Принимаются следующие технологические показатели: Cuк-т= 15%, Znк-т= 45%; извлечение: еCu= 75%, еZn= 80%;
Технологическая схема обогащения представлена на рисунке 1.
Рисунок 1
3.3 Выбор и расчёт схемы дробления
Для проектируемый фабрики принимается трехстадиальная схема дробления с предварительным грохочением в третей стадии.
Рисунок 2 Проектируемая схема дробления Трехстадиальная схема дробления выбрана по следующим основным причинам:
крепость руды по шкале Протодьяконова 12ч13;
начальная крупность 600 мм;
плотность руды 2,9 г/см3;
насыпная плотность 1,6 г/см3;
влажность5%;
конечная крупность 195 мм.
общая степень дробления 60 мм.
Расчет схемы дробления.
Общая степень дробления:
Dmax 600
Sобщ = ————— = ————— = 60;
dн 10
Средняя степень дробления:
SII = Sср = (Sобщ)1/3 = 601/3 = 3,9.
Частные степени дробления:
Sобщ. = S1* S2* S3
S1 = 3,07; S2 =3,9; S3 = 5,04.
Номинальная крупность продуктов дробления:
после I стадии d1 = Dmax / S1 =600/3,07 =195 мм;
после II стадии d2 = d1 / S2 =195/3,9 =50 мм;
после III стадии d3 = d2 / S3 =50/5,04 =10 мм.
Размер щелей дробилок:
i1=d1/ Z1 =195/ 1,5 = 130 мм;
i2=d2/ Z2 =50/ 1,7 = 29 мм.
Z крупность куска выражения в долях единицы разгрузочной щели. Величину Z принимаем по типовой характеристике крупности для первой стадии дробления и крупности дробленной руды. На рисунке 3 представлена характеристика крупности исходной руды.
Размеры отверстий грохота и эффектифность грохочения:
для III стадии а3 = d3 = 10 мм; E3 = 80%.
Рисунок 3 Ситовая характеристика исходной руды Ситовые характеристики крупности Таблица 3
Таблица типовой характеристики крупности продукта 1 (dн = 195 мм, iр = 130 мм)
Определяемый класс, в долях iр | Крупность класса, мм | Выход класса по «+»,% | Выход класса по «-»,% | |
0,2 * iр 0,4 * iр 0,8 * iр 1,2 * iр ZI * iр | ||||
Таблица 4
Расчетной характеристики крупности продукта 1
Крупность класса, мм | Расчетный выход класса по «-»,% | Выход класса по «+»,% | |
в4-26 = в0-26 + b0+130 * в3-26 = 5 + 0,77*17 = 18 в4-52 = в0-52 + b0+130 * в3-52 = 9 + 0,77*32 = 34 в4-104 = в0-104 + b0+130 * в3-104 = 16 + 0,77*60 = 62 в4-156 = в0-156 + b0+156 * в3-156 = 27 + 0,73*82 = 87 в4-195 = в0-195 + b0+195 * в3-195 = 32 + 0,68*95 = 97 | |||
По данным таблицы 4 строится характеристика крупности продукта 1, представленная на рисунке 4.
Таблица 5
Таблица типовой характеристики крупности продукта 2 (dн = 50 мм, iр = 29 мм)
Определяемый класс, в долях dн | Крупность класса, мм | Выход класса по «+»,% | Выход класса по «-»,% | |
0,2 * dн 0,4 * dн 0,6 * dн 0,8 * dн 1,0 * dн | ||||
Таблица 6
Расчетной характеристики крупности продукта 2
Крупность класса, мм | Расчетный выход класса по «-»,% | Выход класса по «+»,% | |
в8−10 = в4−10 + b4+29 * в7−10 = 6 + 0,81*37 = 36 в8−20 = в4−20 + b4+29 * в7−20 = 13 + 0,81*60 = 62 в8−30 = в4−30 + b4+30 * в7−30 = 20 + 0,80*78 = 82 в8−40 = в4−40 + b4+40 * в7−40 = 26 + 0,74*90 = 93 в8−50 = в4−50 + b4+50 * в7−50 = 32 + 0,68*95 = 97 | |||
По данным таблицы 6 строится характеристика крупности продукта 2, представленная на рисунке 5.
Рисунок 4 — Ситовая характеристика продукта 1
Рисунок 5 — Ситовая характеристика продукта 2
Расчет нагрузок на дробилки II стадии дробления Рассчитаем выход продуктов и загрузку дробилок II стадии дробления. Отсеваемый класс -50 мм. Содержание отсеваемого класса в продукте 1 в1-50 = 32%.
Q1 = Q0 * в4-50 * EII = 148 * 0,32 * 0,8 = 38 т/ч.
Загрузка дробилки составит:
Q2 = Q0 — Q1 = 148 — 38 = 110 т/ч.
Расчет нагрузок на дробилки III стадии дробления По графику расчетной характеристики продукта 2, рисунок 4 определяем:
в2 -10 = 36%
Определяем количество продукта 3:
Q3 = Q0 * в2-10 * EIII = 148 * 0,36 * 0,8 = 43 т/ч.
Загрузка дробилки составит:
Q4 = Q0 — Q3 = 148 — 43 = 105 т/ч.
3.4 Выбор и расчет схемы измельчения
В практике принимаем двухстадиальную схему измельчения с замкнутными циклами в каждой стадии.
Рисунок 6 — Проектируемая схема измельчения Научно-иследовательскими работами рекомендуемая крупность помола класса -0,074 мм должна составить 75%. Для руды средней измельчаемости, номинальной крупности 10 мм и с содержанием готового класса в исходном питании 10% можно получить в две стадии с контрольной классификацией слива второй стадии.
Расчет схемы измельчения Циркулирующая нагрузка, исходя из опыта рабты действующей фабрики, принимается равной:
для первой стадииС1 = 100%;
для второй стадии С2 = 150%;
Исходные данные:
Qч = 77 т/ч; 0 = 100%; в0 -74 = 10%; в6 -74 = 75%; d0 = 10 мм.
В6-74 — в0-74
в3-74 = в0-74 + —————————,%;
1 + k m
Определяем количество готового класса в конечном продукте I стадии измельчения по формуле.
где: k — отношение приведенного объема мельниц второй стадии к объему мельниц первой стадии k=1 так как в обеих стадиях установлены шаровые мельницы;
m — отношение удельной производительности по классу — 0,074 мм во второй стадии по этому же классу в первой стадии m — 0,7.
75 — 10
в3-74 = 10 + ————————— = 48%;
1 + 1· 0,7
При установившемся процессе С1 = г4=100%, тогда :
г1 = г0 + г4 = 100 + 100 = 200%.
Назначим циркулирующую нагрузку II стадии С2 = г8 = 150%, тогда:
г5 = г3 + г8 = 100 + 150 = 250%.
Количество продуктов определяем по формуле:
Qn = гn · Q0 / 100%.
Результаты расчета схемы измельчения заносим в таблицу 7.
Таблица 7
Результаты расчета схемы измельчения
№ продукта | Выход,% | Количество, т/ч | |
192,5 | |||
3.5 Расчет баланса металлов и количественной схемы обогащения
Расчет баланса металлов и количественной схемы обогащения приведен в таблице 8.
Таблица 8
Баланс металлов
Наименование продуктов | Выход,% | Содержание,% | Извлечение ,% | |||
Cu | Zn | Cu | Zn | |||
Cu концентрат | 6,0 | 15,0 | 4,0 | 75,0 | 7,5 | |
Zn концентрат | 5,69 | 3,5 | 16,60 | 80,0 | ||
Хвосты | 88,31 | 0,11 | 0,45 | 8,40 | 12,50 | |
Руда | 100,0 | 1,20 | 3,2 | 100,0 | 100,0 | |
Расчет схемы выполнен стандартным путем составления и решения уравнения баланса по твердому и основному металлу. Селективная медная флотация рассчитана по меди, селективная цинковая флотация рассчитана по цинку.
Принципиальная схема флотации приведена на рисунке 7.
Руда 0 | ||
Сu флотация 1 2 | ||
Cu к-т Zn флотация | ||
3 4 Zn к-т Хвосты | ||
Рисунок 7 — Принципиальная схема флотации Исходные данные:
г0 = 100%, в0Cu = 1,2%, в0Zn = 3,2%.
г1 = 6,0%, в1Cu = 15,0%, в1Zn = 4,0%.
г3 = 5,69%, в3Cu = 3,5%, в3Zn = 45,0%.
г4 = 88,31%, в4Cu = 0,11%, в4Zn = 0,45%.
Составим систему уравнений баланса.
г2 = г3 + г4
г2 в2 = г3в3 + г4в4
Решая систему уравнений баланса, находим:
г2 = 94,0%, в2Cu = 0,32%, в2Zn = 3,15%.
Аналогичным методом составления и решения уравнений баланса по выходам и основному металлу, выполняется расчет всей технологической схемы. Расчет медного цикла выполнен по меди, цинкового по цинку.
Результаты расчеты приведены в таблицы 9.
Таблица 9
Результаты расчета технологической схемы
Номер продукта | Наименование продуктов | Выход,% | Содержание металла,% | |
Исходная руда | Cu-1,2; Zn-3,15 | |||
Концентрат основной Cu флотации | 26,0 | 5,0 | ||
Хвосты основной Cu флотации | 127,84 | 0,5 | ||
Концентрат I Сu перечистки | 22,0 | 7,0 | ||
Хвосты I Cu перечистки | 20,0 | 2,0 | ||
Концентрат II Сu перечистки | 9,0 | 12,0 | ||
Хвосты II Cu перечистки | 6,0 | 4,0 | ||
Концентрат III Cu перечистки | 6,0 | 16,0 | ||
Хвосты III Cu перечистки | 3,0 | 6,0 | ||
Концентрат контрольной Cu флотации | 33,84 | 1,0 | ||
Хвосты контрольной Cu флотации | 94,0 | 0,32 | ||
Концентрат основной Zn флотации | 45,514 | 10,0 | ||
Хвосты основной Zn флотации | 185,45 | 1,0 | ||
Концентрат I Zn перечистки | 21,05 | 18,0 | ||
Хвосты I Zn перечистки | 39,824 | 5,0 | ||
Концентрат II Zn перечистки | 11,38 | 31,0 | ||
Хвосты II Zn перечистки | 15,36 | 8,0 | ||
Концентрат III Zn перечистки | 5,69 | 45,0 | ||
Хвосты III Zn перечистки | 5,69 | 17,0 | ||
Концентрат контрольной Zn флотации | 97,14 | 1,5 | ||
Хвосты контрольной Zn флотации | 88,31 | 0,45 | ||
3.6 Выбор схемы обезвоживания
Обезвоживанию подвергаются флотационные концентраты крупностью 85% класса -0,074 мм. В связи с транспортировкой концентратов потребителям на большие расстояния, во избежание смерзания концентрата при транспортировке, содержание влаги в нем не должно превышать 5%. Такая степень обезвоживания достигается в три стадии.
Схема обезвоживания приведена на рисунке 8.
сгущение | ||
Фильтрование | ||
Слив в оборот | ||
Рисунок 8 — Схема обезвоживания
3.7 Расчет водно-шламовой схемы
Водно-шламовая схема рассичитана на часовую производительность 77 т/ч. Выхода и количество продуктов обогащения приняты по результатам расчета качественно-количественной схемы. Также для расчета водно-шла-мовой схемы необходимо назначить содержание твердого в продуктах переработки продукты разгрузки мельниц I и II стадий, пенные продукты операций флотации, пески гидрогиклонов и рассчитать содержание твердого в сливе гидроциклонов. Содержание твердого в продуктах обогащения принято:
Исходная руда 95%
Разгрузка мельницы 75%
Слив классификатора 37%
Пески классификатора 85%
Пески гидрациклона 70%
Разгрузка мельницы II стадии 65%
Концентрат основной Cu флотации 28%
Концентрат I Cu перечистки 32%
Концентрат контрольной Cu флотации 26%
Коннцентрат II Cu перечистки 34%
Концентрат III Cu перечистки 36%
Расчет водно-шламовой схемы выполнен стандартным образом и приведен в таблице 11.
Баланс воды приведен в таблице 10
Таблица 10
Баланс воды
ПОСТУПАЕТ | ВЫХОДИТ | |||
Вода | Масса, т/ч | Вода | Масса, т/ч | |
С рудой | 4,0 | С концентратом | 8,2 | |
С водой | 33,4 | С хв. контр. фл. | 229,2 | |
В классификаторI | 93,7 | |||
В гидрациклон — II | 28,0 | |||
В измельчение — II | 12,3 | |||
В осн. Cu флотацию | 44,0 | |||
В I Cu перечистку | 10,0 | |||
В II Cu перечистку | 8,0 | |||
В III Cu перечистку | 4,0 | |||
Итого | 237,4 | Итого | 237,4 | |
Расход воды на хозбытовые нужды 10% от технологической 23,74 т/ч.
Общий расход 261,14 т/ч.
В том числе оборотной воды 50%, Wобщ. = 130,57 т/ч.
час. расход воды 261,14
Удельный расход воды = 3,39 м3/ч.
сут. переработка руды 77
Таблица 11
Результаты расчета количественной и водно-шламовой схемы
ПОСТУПАЕТ | ВЫХОДИТ | |||||||||||||
Наименование продуктов | Выход,% | Содерж. тв, % | количество, т/ч | Объём пульпы, м3/ч | Наименование продуктов | Выход,% | Содерж. тв.,% | количество, т/ч | Объём пульпы, м3/ч | |||||
тв | воды | пульпы | тв | воды | пульпы | |||||||||
ИЗМЕЛЬЧЕНИЯ — I | ||||||||||||||
Руда | 100,0 | 95,0 | 4,0 | 81,0 | 31,55 | Разгрузка мельницыI | 200,0 | 75,0 | 51,0 | 205,0 | 104,1 | |||
Пески классификатора I | 100,0 | 85,0 | 13,6 | 90,6 | 40,15 | |||||||||
Вода | ; | ; | 33,4 | 33,4 | 33,4 | |||||||||
Итого | 200,0 | 75,0 | 51,0 | 205,0 | 104,1 | Итого | 200,0 | 75,0 | 51,0 | 205,0 | 104,1 | |||
КЛАССИФИКАЦИЯ В КЛАССИФИКАТОРЕ — I | ||||||||||||||
Разгрузка мельницыI | 200,0 | 75,0 | 51,0 | 205,0 | 104,1 | Слив классификатора — I | 100,0 | 37,0 | 131,1 | 208.1 | 157,65 | |||
вода | ; | ; | ; | 93,7 | 93,7 | 93,7 | Пески классификатораI | 100,0 | 85,0 | 13,6 | 90.6 | 40,15 | ||
итого | 200,0 | 144,7 | 298,7 | 197,8 | Итого | 200,0 | 144,7 | 298.7 | 197,8 | |||||
КЛАССИФИКАЦИЯ В ГИДРОЦИКЛОНЕ — II | ||||||||||||||
Слив классификатора I | 100,0 | 37,0 | 131,1 | 208,1 | 157.65 | Слив гидрациклонаII | 100,0 | 31,0 | 171,4 | 248,4 | 197,95 | |||
Разгрузка мельницы II | 150,0 | 65,0 | 62,0 | 178,0 | 102.0 | Пески гидрациклона — II | 150,0 | 70,0 | 49,7 | 165,7 | 89,7 | |||
Вода | ; | ; | ; | 28,0 | 28,0 | 28.0 | ||||||||
Итого | 250,0 | 46,6 | 221,1 | 414,1 | 287.65 | Итого | 250,0 | 46,6 | 221,1 | 414,1 | 287,65 | |||
ИЗМЕЛЬЧЕНИЯ — II | ||||||||||||||
Пески гидроциклонаII | 150,0 | 70,0 | 49.7 | 165.7 | 89.7 | Разгрузка мельницы — II стадии | 150,0 | 65,0 | 62,0 | 178,0 | 102,0 | |||
Вода | ; | ; | ; | 12.3 | 12.3 | 12.3 | ||||||||
Итого | 150,0 | 65,0 | 62.0 | 178.0 | 102,0 | Итого | 150,0 | 65,0 | 62,0 | 178,0 | 102,0 | |||
ОСНОВНАЯ Cu ФЛОТАЦИЯ | ||||||||||||||
Слив гидроциклона — I | 100,0 | 31,0 | 171,4 | 248,4 | 197,95 | К-т основной Cu фл. | 26,0 | 28,0 | 51,4 | 71,4 | 58,29 | |||
К-т контрольной Cu фл. | 33,84 | 26,0 | 26.0 | 74,0 | 100,0 | 82,965 | Хв. основной Cu фл. | 127,84 | 98,4 | 303,2 | 401,6 | 337,13 | ||
Хвосты I Cu перечистки | 20,0 | ; | 15.4 | 65,2 | 80,6 | 70,51 | ||||||||
Вода | ; | ; | ; | 44,0 | 44,0 | 44,0 | ||||||||
Итого | 153,84 | 118,4 | 354,6 | 473,0 | 395,42 | Итого | 153,84 | 118,4 | 354,6 | 473,0 | 395,42 | |||
I Cu ПЕРЕЧИСТКА | ||||||||||||||
К — т основной Cu фл. | 26,0 | 28,0 | 51,4 | 71,4 | 58,29 | К-т I Cu перечистки | 22,0 | 32,0 | 16,9 | 35,9 | 52,8 | 41,7 | ||
Хвосты II Cu перечистки | 16,0 | ; | 12,3 | 39,7 | 52,0 | 43,9 | Хвосты I перечистки | 20,0 | ; | 15,4 | 65,2 | 80,6 | 70,51 | |
Вода | ; | ; | ; | 10,0 | 10,0 | 10,0 | ||||||||
Итого | 42,0 | 32,3 | 101,1 | 133,4 | 112,2 | Итого | 42,0 | 32,3 | 101,1 | 133,4 | 112,2 | |||
тв | воды | пульпы | тв | воды | пульпы | |||||||||
КОНТРОЛЬНАЯ Cu ФЛОТАЦИЯ | ||||||||||||||
Хв.основной Cu фл. | 127,84 | ; | 98,4 | 303,2 | 401,6 | 337,13 | К-т контрольной Cu фл. | 33,84 | 26,0 | 26,0 | 74,0 | 100,0 | 82,965 | |
Хв. контрольной Cu фл. | 94,0 | ; | 72,4 | 229,2 | 301,6 | 254,165 | ||||||||
Итого | 127,84 | 98,4 | 303,2 | 401,6 | 337,13 | Итого | 127,84 | 98,4 | 303,2 | 401,6 | 337,13 | |||
II Cu ПЕРЕЧИСТКА | ||||||||||||||
К-т I Cu перечистки | 22,0 | 32,0 | 16,9 | 35,9 | 52,8 | 41,7 | К-т II Cu перечистки | 9,0 | 34,0 | 6,9 | 13,4 | 20,3 | 15,8 | |
Хв. III Cu перечистки | 3,0 | ; | 2,3 | 9,2 | 11,5 | 10,0 | Хвосты II Cu перечистки | 16,0 | ; | 12,3 | 39,7 | 52,0 | 43,9 | |
Вода | ; | ; | ; | 8,0 | 8,0 | 8,0 | ||||||||
Итого | 25,0 | 19,2 | 53,1 | 72,3 | 59,7 | Итого | 25,0 | 19,2 | 53,1 | 72,3 | 59,7 | |||
III Cu ПЕРЕЧИСТКА | ||||||||||||||
К-т II Cu перечистки | 9,0 | 34,0 | 6,9 | 13,4 | 20,3 | 15,8 | К-т III Cu перечистки | 6,0 | 36,0 | 4,6 | 8,2 | 12,8 | 9,8 | |
Вода | ; | ; | ; | 4,0 | 4,0 | 4,0 | Хв.III Cu перечистки | 3,0 | ; | 2,3 | 9,2 | 11,5 | 10,0 | |
Итого | 9,0 | 6,9 | 17,4 | 24,3 | 19,8 | Итого | 9,0 | 6,9 | 17,4 | 24,3 | 19,8 | |||
технологический обогатительный медный цинковый
3.8 Выбор и технологической расчет основного оборудования
3.8.1 Оборудования для дробления
Часовая производительность отделения крупного дробления составляет 148 т/ч.
При максимальной крупности исходной руды Dmax = 600 мм подходит стандартная дробилка ЩДП- 9×12.
Каталожная производительность дробилки при объемной массе руды 1,6 т/м3 и выбранной разгрузочной щели дробилки iр = 130 мм составляет:
qmax — qmin
VK = qmin + ————————- * (iр — imin), м3/ч;
imax — imin
230 — 130
VK = 130 + ————————- * (130 — 95) = 180 м3/ч;
165 — 95
Фактическая производительность дробилки будет:
Qр = VK * Kf * Kk * Kw * * дн, т/ч;
где: Kf коэффициент крепости, для руды крепостью 12−13 по шкале Протодьяконова Kf =1,0;
Kk коэффициент крупности, при ширине загрузочного отверстия 1200 мм и максимальной крупности Dmax = 600 мм Kk = 1,03;
Kw коэффициент влажности, при w = 5% Kw = 1,0;
дн объемная масса руды, дн = 1,6 т/ч.
Qдр. = 180 * 1,0 *1,03 * 1,0 * 1,6 = 297 т/ч.
Коэффициент загрузки дробилки составит:
Кз = Q0 /Qдр. = 148 / 297 = 0,50.
Расчет дробилок для среднего дробления и мелкого дробления выполнен тем же методом. Для среднего дробления принимаем к установ-ке дробилку КСД-1750 Гр, для мелкого дробления КИД-1750. Результа-ты расчета сведены в таблицу 12.
Таблица 12
Результаты расчета дробилок
Показатели | I стадия дробления | II стадия дробления | III стадия дробления | |
Типоразмер дробилки Размер разгрузочной щели, мм Пределы регулирования разгрузочной щели, мм Крупность питания, мм Крупность дробленого продукта, мм Количество материала, поступающего на дробление, т/ч Расчетная производительность на одну дробилку, т/ч Коэффициент загрузки Количество дробилок, шт. | ЩДП- 9×12 95 — 165 0,50 | КСД- 1750Гр 25 60 0,4 | КИД- 1750 20 — 50 0,7 | |
3.8.2 Оборудование для грохочения
Среднее и мелкое дробление.
Необходимая площадь грохочения рассчитывается по формуле :
Qр
Fр = —————————————————————-, м2.
q0 * дн * K * L * M * N * O * P
где F — площадь сита грохота, м 2 ;
q — удельная производительность на 1 м 2 поверхности сита, м 3/м 2 ч;
дн — насыпная масса, т/м3;
K — коэффициент, учитывающий влияние зерен размером меньше половины отверстия сита;
L — коэффициент, учитывающий влияние зерен размером крупнее отверстия сита;
M — коэффициент, учитывающий эффективность грохочения;
N — коэффициент, учитывающий форму зерен;
O — коэффициент, учитывающий влияние влажности;
P — коэффициент, учитывающий способ грохочения.
В данном случае для II стадии:
q = 42 м3/ м2 · ч, дн = 1,6 т/м3, К = 0,6, L = в1 +50 = 68% = 1,50,
М для Е = 80% =1,35, N =O = P = 1,0.
Необходимая площадь грохочения составляет:
Fр = ———————————————————————— = 1,81 м2.
42· 1,6· 0,6· 1,50 · 1,35 · 1,0· 1,0·1,0
К установке принимаем грохот ГИТ-31 А с общей площадью грохо-чения 3,12 м2.
В данном случае для III стадии:
q = 19 м3/ м2 · ч, дн = 1,6 т/м3, К = 0,6, L = в2 +10 = 64% = 1,50,
М для Е = 80% =1,5, N =O = P = 1,0.
Необходимая площадь грохочения составляет:
Fр = ———————————————————————— = 4.0 м2.
19· 1,6· 0,6· 1,50 · 1,35 · 1,0· 1,0·1,0
К установке принимаем грохот ГИТ-41 А с общей площадью грохо-чения 4,50 м2.
3.8.3 Оборудование для измельчения
В соответствием с принятой схемой измельчения и крупностью исходного питания dн = 10 мм принимаем к установке в первой и во второй стадии измельчения шаровые мельницы с разгрузкой через решетку.
Расчет мельниц выполнен по удельной производительности.
За эталон принимаем шаровую мельницу, установленную на Джесказганской обогатительной фабрике МШР -32×31.
Базисные условия:
1) удельная производительность — 1,15 т /м3 ч;
2) крупность питания — 35% класса -74 мкм;
3) содержание готового класса — 74 мкм в конечном продукте первой стадии 48%;
4) крепость руды по Протодьяконову — 12ч13;
5) плотность руды — 2,9 т/ м3· ч.
Необходимый ориентировочный объем принимется из соотношения:
Q0 * С 77+77
Vор. = —————— = ————- = 15,4 м3 .
10 10
Для сравнения принимаются следующие три типоразмера мельниц:
МШР — 27×21 с V = 10,0 м3;
МШР — 27×36 с V = 17,5 м3;
МШР — 33×31 с V = 22,4 м3.
Удельная производительность принятых мельниц рассчитывается по формуле:
q-74 = qЭ * KИ * KК * KТ * KD * KL * Kц * Kш, т/(м3*ч),
где q-74 — удельная производительность рассчитываемой мельницы по вновь образованному классу, т/м3· ч;
qэ — удельная производительность мельницы принятой за эталон, т/м3· ч;
Ки — коэффициент измельчаемости;
Кк — коэффициент учитывающий различие в крупности исходного питания и конечного продукта;
KD — коэффициент учитывающий различие в диаметрах рассчиты-ваемой и эталонной мельниц;
Kт — коэффициент учитывающий различие в типах рассчитываемой и эталонной мельниц;
KL — коэффициент учитывающий различие в длине барабана рассчи-тываемой и эталонной мельниц;
Kц — коэффициент учитывающий заполнение мельницы шарами;
Кш — коэффициент учитывающий различие в частоте вращения бара-бана мельниц.
Производительность мельниц по руде рассчитывается по формуле:
q-74 * V
QР = —————————, т/ч, вК-74 — вН-74
где: q-74 — удельная производительность проектируемой мельницы по вновь образованному классу -0,074 мм, т/(м3*ч);
V — объем барабана рассчитываемой мельницы, м3 ;
вК-74, вН-74 — конечное и начальное содержание класса — 74 мкм вт измельченном продукте и питании мельницы.
qЭ = 1,15 т/(м3 · ч);
KИ =1,17;
KК =m2 /m1 =1,03/ 0,85 = 1,2;
KТ =1,0;
KL = 1,0;
Kц =1,0;
Kш =1,0.
для мельницы МШР -27×21:
q-74 =1,15 * 1,17 * 1,2 * 0,91 * 1,0 * 1,0 * 1,0 * 1,0 = 1,46;
1,46 * 10
QР = ————————— = 38 т/ч;
0,48 — 0,1
N = 77 / 38 = 3 шт;
KЗ = 77 / 38 * 3 = 0,67,
для мельницы МШР -27×36:
q-74 =1,15 * 1,17 * 1,2 * 0,91 * 1,0 * 1,0 * 1,0 * 1,0 = 1,46;
1,46 * 17.5
QР = ————————— = 67 т/ч;
0,48 — 0,1
N = 77 / 67 = 2 шт;
KЗ = 77 / 67 * 2 = 1,14,
для мельницы МШР -32×31:
q-74 =1,15 * 1,17 * 1,2 * 1,0 * 1,0 * 1,0 * 1,0 * 1,0 = 1,6;
1,6 * 22,4
QР = ————————— = 94 т/ч;
0,48 — 0,1
N = 77 / 94 = 1 шт;
KЗ = 77 / 94 = 0,81.
Оптимальным вариантом в I стадии измельчения является мельница МШР-32×31 в количестве 1 шт. Выбранную мельницу проверяем на про-пускную способность:
Q0 * (1 + C) 77 * (1+ 1)
——————————————————- = 6,87 < 10.
N * V 1 * 22,4
Во II стадии измельчения установливаем такую же мельницу, т.к. отношение произведенного объема мельницы I стадии к объему мельницы II стадии равно 1.
Отношение удельной производительности мельницы I стадии ко второй равно 0,7, тогда:
q-74 II = 0,7 * 1,6 = 1,12,
1,12 * 22,4
QР = ————————— = 92,9 т/ч;
0,75 — 0,48
N = 77 / 92,9 = 1 шт;
KЗ = 77 / 92,9 = 0,82.
К установке принимаем одну мельницу МШР — 32×31 в I стадии и одну мельницу МШР — 32×31 во II стадии измельчения.
3.8.4 Оборудование для классификации
В I стадии для классификации I устанавливаем классификаторы. Содержание готового класса — 74 мкм в сливе вс -74 = 48%. Плотность руды дт = 2,9 т/м3. В первой стадии классификации I устанавливаем классифи-каторы 2КСH — 24A.
Рассчитаем его производительность по сливу по формуле:
QC = 4.56 * m * Kв * Kд * KC * Kб * D1.765, т/ч, где: m — число спиралей;
Kв — поправочный коэффициент на крупность слива;
Kд — поправочный коэффициент на плотность твердого;
KC — поправочный коэффициент на плотность слива классифи-катора;
Kб — поправочный коэффициент на угол наклона классифи-катора;
D — диаметр спирали классификатора, м.
1,96 — 1,7
Kв = 1,96 — ————————- * (48 — 41) = 1,8;
53 — 41
дТ 2.9
Kд = ———— = ——————- = 1,07;
2,7 2,7
36 — 33
Т2.7 = 36 — ——————- * (48 — 41) = 34,25%;
53 — 41
100 — Т2.7 100 — 34,25
R2.7 = ———————— = ————————- = 1,91;
Т2.7 34,25
Значение ТС принимается из расчета водно-шламовой схемы. В при-мере ТС =37%.
100 — ТС 100 — 37
RТ = —————— = ———————- = 1,7;
ТС 37
RT/R2.7 = 1,7/1,91 = 0,89;
1,07 — 0,93
КС = 0,93 + ————————— * (0,89 — 0,8) = 0,99;
1,0 — 0,8
б = 18° Kб = 1,0;
QC
D1.765 = ——————————————————, м;
4,56 * m * Kв * Kд * KC * Kб
D1.765 = ——————————————————— = 4,42 м;
4,56 * 2* 1,8* 1,07 * 0,99 * 1,0
D = 2,4 м.
Его производительность по сливу в соответствии с формулой составит:
QC = 4,56 * 2 * 1,8 * 1,07 * 0,99 * 1 * 2,41.765 = 81,5 т/ч.
Проверим классификатор по пескам по формуле :
QП = 5,45 * m * n * Kд * Kб * D3, т/ч;
где: n — частота вращения спирали, об-1.
Производительность по пескам для n = 3,6 об/мин в соответствии с формулой составит:
QП = 5,45 * 2 * 3,6 * 1,07 * 1,0 * 2,43 = 580,4 т/ч.
Таким образом, двухспиральный классификатор 2КСН-24А с заданной производительностью по сливу и пескам справляется.
Во II стадии для классификации II устанавливаем гидроциклоны диаметром 500 мм. Объем пульпы, поступающей на гидроциклониро-вание, V = 287,65 м3/ч. Номинальная крупность слива гидроциклона с со-держанием класса — 74 мкм вс = 75% в соответствии с упрощенной формулой Розина-Рамлера для R+74 = 100 — вc-74 = 100 — 75 = 25% соста-вит:
96,274 96,274
dН = ————————- = ———————- = 160 мкм.
2 — lg R+74 2 — lg 25
Граничная крупность слива состоит:
dг = dн/1,75 = 160/1,75 = 91,4 мкм.
Объемная производительность гидрациклонов рассчитывается по формуле:
V = 3 * Kб * KD * dП * dC * P00.5, м3/ч, где: VP — оъемная производительность, м3/ч ;
Kб — поправка на угол конусности;
KD — поправка на диаметр гидроциклона;
dП — эквивалентный диаметр питающего отверстия, см;
dC — диаметр сливного отверстия, см;
P0 — рабочее давление пульпы на входе в гидроциклон, МПа.
Граничная крупность слива определяется по формуле:
/ D * dC * TП
dГ = 1,5 * / ————————————————, мкм.
/ Д * KD * P00.5 * (дТ — 1)
Граничная крупность слива для диаметра песковой насадки Д = 7,5 см.
_____________
/ 50 * 16 * 46,6
dГ = 1,5 * / ——————————————————- = 136 мкм.
/ 7,5 * 1 * 0,10.5 * (2,9 — 1)
Объемная производительность гидроциклона для P0 = 0,1 МПа в соот-ветствии с формулой составит:
V = 3 * 1 * 1 * 13 * 16 * 0,10.5 = 197,3 м3/ч.
Необходимое количество гидроциклонов составит:
N = VСЕКЦ/V = 287,65 / 197,3 = 2 шт.
С учетом двух резервных гидроциклонов в каждой секции устана-вливается четыре гидроциклонов ГЦ-500.
Выбранные гидроциклоны проверяем по пескам:
QП * 4 116 * 4
q = ————————- = ————————————- = 1,31 т/(см2 * ч).
N * р * Д2 2 * 3,14 * 7,52
0,5 < 1,31< 2,5, данные гидроциклоны справляются с нагрузкой по пескам.
3.8.5 Оборудование для флотационного обогащения
Для основной и контрольной флотации во всех циклах устанавливаем пневматические машины, для перечистной операции-механические флото-машины.
Необходимое количество камер флотомашины выбранного типо-размера определяется по формуле:
V * t
n = —————————-, шт.;
60 * VK * K
где: V — объем пульпы, поступающей на операцию, м3/ч;
t — необходимое время флотации, мин.;
VK — объем одной камеры, м3;
K — отношение объема пульпы к объему камеры, (0,7ч0,8).
Основная Cu — Zn флотация.
ФПМ — 12,5. Объем одной камеры VK = 12,5 м3. Необходимое время флотации t = 15 мин. Объем пульпы, поступающей на операцию, V = 395,42 м3/ч. Принимаем К = 0,7 тогда:
395,42 * 15
n = —————————- = 12 шт.;
60 * 12,5 * 0,7
Результаты расчета сведены в таблицу 13.
Таблица 13
Сводная таблица расчета флотомашин
Наименование операций | Объем пульпы, м3/ч | Типоразмер флотомашин | Объем камеры, м3 | Время флотации, мин. | Количество камер, шт. | |
Основная Cu флотация | 395,42 | ФПМ — 12,5 | 12,5 | |||
I Cu перечистка | 112,2 | ФМ — 12,5 | 12,5 | |||
II Cu перечистка | 59,7 | ФМ — 12,5 | 12,5 | |||
III Cu перечистка | 19,8 | ФМ — 12,5 | 12,5 | |||
Контрольная Cu флотация | 337,13 | ФПМ — 12,5 | 12,5 | |||
3.8.6 Оборудование для обезвоживания
Для сгущения Часовая производительность фабрики по концентратам составляет медного — 4,6 т/ч. Потребная площадь сгущения определяется по формуле:
S = Q * Sуд ,
где: Q — производительность по концентрату, т/ч;
q — удельная площадь сгущения, т/м2· ч, для медного 20 м2/т· ч.
Площадь сгущения составит:
S = 4,6 * 20 = 92 м2
К установке принимаем: для сгущения Cu концентрата — сгуститель Ц-12А с площадью 110 м2.
Для фильтрования.
Потребная площадь фильтрации определяется по формуле:
F = Q / q, м2;
где: Q — производительность по концентрату, т/ч;
q — удельная производительность фильтров, кг/м2· ч, для медного 150 кг/ м2· ч.
Площадь фильтрации для фильтрования составит:
F = 4,6 / 0,15 = 30,6 м2
К установке принимаем: для фильтрации Cu концентрата — фильтр ДУ-34−2,5 в кол-ве 1 шт.
4. Безопасность и охрана труда
4.1 Анализ опасных производственных факторов
В производственных условиях в корпусах обогатительной фабрики возникает потенцальная опасность нежелательного воздействия на организм человека образующихся в технологическом процессе веществ, шумов, вибрации, а также опасность поражения электрическим током. Ряд этих опасностей может привести к профессиональным заболеваниям или тревматизму людей.
На проектируемой обогатительной фабрике применяется крупногаба-ритное оборудование:
дробилки — ЩДП-9×12, КСД-1750 Гр, КИД-1750;
мельницы — МШР-32×33.
Проектом предусмотрено размещение операторов вычислительной техники в отделениях дробления и в главном корпусе обогатительной фабрики.
Согласно паспорта уровень звукового давления составляет:
для дробилки ЩДП-9×12 — 90 дБ;
для дробилки КСД-1750 Гр — 105 дБ;
для дробилки КИД-1750 — 95 дБ;
для мельницы МШР-32×33 — 115 дБ.
Учитывая, что допустимый уровень шума составляет 50 дБ, а в корпу-се дробления установлен еще и грохот, дающий повышенной уровень шума и выбрации, необходимо проводить мероприятия для устранения этих нежелательных факторов. Производственные опасности и вредности создаются также:
1) неблогоприятными метеологическими условиями;
2) наличием в воздухе рабочей зоны ядовитых выделений реагентов в виде испарений ксантогената, керосина, сернистого натрия, оказывающих вредное вляние на организм человека. Поэтому необходимо обеспечить хорошую вентиляцию помещений;
3) запыленностьюпомещений в корпусах дробления, где устанавлива-ются вытяжные устройства;
4) пожароопасностью.
4.2 Организационные мероприятия
Организация работ по охране труда, а также ответственность за нее на фабрике возлагается на администрацию фабрики во главе с директором и главным инженером, на рабочем месте — на начальника цеха. Также на фабрике есть инженер по технике безопасности, который непосредствено занимается организацией мероприятий по охране труда.
При устройстве на работу предусматривается обязательной медосмотр здоровья. Каждый поступающий на работу проходит инструктаж по технике безопасности, который включает следующие этапы:
1) вводный инструктаж — знакомство с технологическими особен-ностями цеха, правилами внутреннего распорядка, требованиями правиль-ного пользования спецодеждой, правилами электробезопасности и т. д.;
2) первичный инструктаж — проводится на рабочем месте: знакомство с обязанностями и правилами по содержанию рабочего места, с устройст-вом и правилом обслуживания агрегатов, транспортных средств и с безо-пасностью использования инструментов;
3) периодический, или повторный инструктаж — проводится со всеми рабочими независимо от квалификации и стажа работы через каждые 6 месяцев;
4) внеочередной инструктаж — проводится при переводе на другое ра-бочее место, при изменении технологического процесса и при выявлении наружения техники безопасности.
Все виды инструктажа считаются законченными, если проверка подтверждает, что рабочий хорошо усвоил и овладел безопасным приемом работы. Инструктажи проводятся непосредственным наставником или исполняющим обязанности инструктора по технике безопасности.
4.3 Технические мероприятия
Для борьбы с вышеуказанными опасностями и вредными факторами предусмотрен ряд мероприятий по их предотвращению:
1) во всех корпусах фабрики предусматривается площадки для ремон-та оборудования и средства транспортировки узлов оборудования на ре-монтные площадки;
2) все площадки и переходные мостики, находящиеся на высоте 0,5 м, снабжены лестницами и перилами высотой не менее 1 м с перекладиной на уровне 0,5 и со сплошной обшивкой по низу на высоте 0,2 м. Площадки и переходные мостики, расположенные на высоте 0,5 м, обеспечиваются пандусами с уклоном не менее 100. Ширина площадок и переходных мос-тов не менее 0,8 м;
3) площадки, расположенные на высоте более 0.3 м над уровнем пола, снабжены лестницами — число ступеней в лестнице не менее 3 и не более 18. Угол наклона постоянно эксплуатируемых лестниц 450. Ширина лестниц — 0,7 м. Полы площадок, переходных мостиков и ступенек лестниц должны иметь ровную нескользкую поверхность. Проходы к чанам — 0,6 м, к машинам и механизмам — 0,8 м, между степень и обору-дованием — более 1,0 м, между машинами — более 1,2 м, магистральные проходы — 1,5 м;
4) управление оборудованием устраивают, как правило, кнопочным, расположенным на высоте 1−1,6 м над уровнем пола рабочего места при обслуживании стоя и 0,6−1,2 м — при обслуживании сидя. Посты, пульты и панели управления располагают в местах, обеспечивающих хорошую видимость обслуживаемого агрегата и прилегающих к нему участков, применяя световую и звуковую сигнализацию для извещения о пуске и остановке обслуживаемых агрегатов. Для наблюдения за работой оборудо-вания, расположенного на больших расстояниях от пункта управления и для исключения контакта рабочих с вредными веществами, применяют установки промышленного телевидения.
4.3.1 Обеспечение электробезопасности
По электрической безопасности проектируемая обогатительная фабрика относится к особо опасным помещениям, характеризующимся наличием химически активной среды и повышенной влажностью воздуха.
С целью предотвращения несчастных случаев, связанных с электри-чеством, в проекте предусматривается защитное заземление. Заземляются корпуса электродвигателей, распределительных устройств, имеющих напряжение свыше 36 Вольт. В качестве заземляющих устройств исполь-зуются глубинные заземлители.
4.3.2 Организация приточно-вытяжной вентиляции
В дробильном отделении производится принудительный отсос пыли в точках перепада руды по рудотранспортному потоку при приеме, разгруз-ке, дроблении и грохочении, и транспортировке по конвейерам.
Пыль, образующаяся в точках перепада руды, отсасывается вентиля-тором и нагнетается в циклон, где пыль подвергается орошению водой и с дренажными сливами дробильного корпуса подается в измельчительное отделение главного корпуса.
Очищенный воздух выбрасывается в атмосферу. Уборка помещений и галерей мокрая.
Отсос пыли, аэрозолей и газов из главного корпуса производится с помощью естественной вентиляции через дефлекторы, имеющиеся в перекрытии измельчительного и флотационного отделений. Очищенный воздух выбрасывается в атмосферу через сбросные трубы, так же в отделе-нии работает приточно-вытяжная вентиляция.
4.3.3 Защита от механических травм
На проектируемой фабрике все площадки на высоте более 60 см от пола, лестничные проходы, люки, каналы ограждены перилами высотой не менее 1 м, лестницы с уклоном не более 400. Поверхность пола горизон-тальная, удобная для очистки, без порогов и выступов, прочная и не-скользкая с нарифлениями из деревянных брусков. Пол диэлектрический не пропускает искру, маслостойкий, химически устойчивый имеет стоки. Вращающиеся части агрегатов, двигатели принудительной вентиляции и вентиляторы имеют специальные закрытие кожухи. Около движущихся частей механизмов оборудования предусматривается проходы не менее 1,2 м.
Дренажные зумпфы, ямы и канавы перекрыты механическими ре-шетками. Аппаратура пылеулавливания блокирована с рабочими агрегата-ми. На мостовых кранах и кранбалках установлены сирены и светильники для освещения зоны действия кранов. Пуск и остановка механизмов со-провождается световой и звуковой сигнализацией. Во избежание несчаст-ных случаев имеется возможность блокировки и аварийной остановки ме-ханизмов в случае их неисправности.
4.3.4 Обеспечение безопасности при отравлении вредными веществами
Помещения для хранения флотационных реагентов закрытого типа находятся в отдельных изолированных зданиях на охраняемой территории. Сухие и жидкие флотореагенты хранят в разных помещениях. Во всех по-мещениях для хранения флотореагентов полы с гладким, водонепроницае-мым, кислотостойким или щелочестойким покрытием с уклонами и стока-ми в канализацию. Помещения отапливают и устраивают искуственную или естественную вентиляцию. В помещениях находятся средства механи-зации погрузочно-разгрузочных работ и операций по перемещению флотореагентов и передачи их в реагентное отделение.
Для защиты органов дыхания от вредностей используют противогазы и респираторы. Респираторы в зависимости отназначения делят на проти-вопылевые, противогазовые и универсальные.
Приготовление реагентов цианистых солей и их осветление проводят в изолированном помещении с отаплеваемым тамбуром и самостоятель-ным входом с территории фабрики. Помещение и тамбур с внутренней отделкой, обеспечивающей возможность обмывания поверхностей стен, потолка и пола. Сточные воды и мусор из флотационного отделения, склада реагентов и из реагентного отделения предварительно подвергаются обезвреживанию.
В помещениях, где хранятся флотореагенты или производится работа с ними, не принимают пищу и не курят. Не принимают пищу в спецодеж-де, в которой производились работы с реагентами.
4.4 Санитарно-гигиенические мероприятия
Целью санитарно-гигиенических мероприятий является создание бла-гоприятных условий труда, а именно:
1) обеспечение бытовыми помещениями;
2) обеспечение индивидуальными средствами защиты;
3) обеспечение спецодеждой.
В соответствии со СНиП -3−68 на обогатитльной фабрике санитарно- -бытовые соединены с отделениями обогатительной фабрики утепленны-ми переходами. Гардеробы для хранения домашней и рабочей одежды, умывальное комнаты и душевые комнаты отдельные для мужчин и женщин. Проектом предусмотрено помещение для приема пищи, прачеч-ная. Санитарно-бытовые помещения спроектированы так, чтобы обеспе-чить обслуживание трудящихся. Свободный объем здания на одного рабо-чего составляет не менее 15 м3, свободная площадь — не менее 4,5 м2. Здравпункты находятся в бытовом помещении.
4.4.1 Средства индивидуальной защиты
В соответствии с отраслевыми типовыми нормами для рабочих и слу-жащихгорной и металлургической промышленности выдается бесплатно спецодежда, спецобувь и предохранительные приборы на определенный срок. В производственных условиях спецодежда является средством инди-видуальной защиты тела человека от вредных факторов внешней среды, воздействующих через кожное покрытие и по конструкции подразделяют-ся на комбинезоны, полукомбинезоны и костюмы. Перечень выдаваемой спецодежды сведен в таблицу 14.
Спецобувь является средством защиты от вредных факторов внешней среды и механических повреждений ног человека.
Рукавицы, перчатки предназначены для защиты рук от механических повреждений, ожогов, от воздействия кислот, щелочей и других химичес-ких веществ, а также от действия вредных излучений, электрического тока, холода, воды.
Каски относятся к средствам защиты головы: к средствам защиты органов зрения и лица относятся защитные маски, очки и полумаски. К средствам защиты органов дыхания относятся: фильтрующийся противогаз и респиратор «Лепесток».
Таблица 14
Индивидуальные средства защиты
Профессия | Спецодежда | Срок годности, мес. | |
Рабочие измельчительного отделения | Спецодежда хлопчатобумажная | ||
Спецовувь | |||
Рукавицы | |||
Каска | |||
Резиновые перчатки | |||
Резиновые сапоги | |||
Флотатор | Спецодежда хлопчатобумажная | ||
Каска | |||
Резиновые перчатки | |||
Резиновые сапоги | |||
Рабочие цеха обезвоживания | Спецодежда хлопчатобумажная | ||
Рукавицы | |||
Каска | |||
Резиновые перчатки | |||
Резиновые сапоги | |||
Респиратор «Лепесток» | ежедневно | ||
4.4.2 Организация естественного и искусственного освещения
Для создания благоприятных условий труда важное значение имеет освещение. На практике применяют естественное и искусственное освеще-ние.
Естественное освещение нормируется СНиП-18−72. Электрическое освещение необходимо для проведения работ в темное суток и в местах без достаточного естественного освещения. В помещениях, где проводят относительно грубые работы, применют лампы накаливания. Естественное освещение осуществляется в виде бокового через окна в наружных стеках, в виде верхнего освещения через световые фонари в перекрытиях здания и через проемы в местах перепадов высот смежных проемов зданий из рас-чета 1 м2 площади окна на 10 м2 площади пола.
Искусственное освещение осуществлятся с помощью светильников. Наименьшая освещенность составляет на поверхности составляет 20 лк для помещений, где устанавливается вспомогательное оборудование.
Для искусственного освещения производственных помещений проек-том предусматривается система комбинированного освещения: брызгоза-щищенное и струезащищенное.
Проектом предусматривается светильники с люминесцентными лампами прямого света. При освещении подбункерного пространства используется комбинированное освещение: 30% искусственного освеще-ния достигается за счет общего освещения от отделения измельчения и отсадки, а остальные 53 лк за счет установки светильников местного осве-щения.
4.4.3 Защита от шума и вибрации
На проектируемой богатительной фабрике используется самое разно-образное оборудование, эксплуатация которых сопровождается шумом и вибрацией. Для погащения шума в проекте предусматривается ряд меро-приятий, таких, как замена металлических деталей на пластиковые, свое-временная смазка, звукоизоляция, прокладки. Для защиты органов слуха рекомендуется ношение противошумных наушников, заглушек, вклады-шей. Рабочие, непосредственно связанные с вибрирующими агрегатами и машинами, обеспечиваются специальной обувью на толстой резиновой подошве. Если параметры вибрации первосходят предельно-допустимые значения, то устанавливаются амортизаторы: в качестве виброизоляции применяются прокладки из резины, дерева и других материалов.
Вибрации делятся на три основных вида: транспортные, транспортно- -технологические, технологические. Для снижения шума в производствен-ных помещениях используются следующие способы:
1) уменьшение шума в источнике за счет снижения его звуковой мощ-ности;
2) акустическая планировка помещений;
3) акустическая обработка помещений;
4) уменьшение звуковой мощности на пути распространения шума, т. е. применение звукоизлирующих экранов или глушителей шума.
Борьба с вредными воздействиями вибрации на организм человека ведется по следующим направлениям:
1) снижение вибрации непосредственно в источнике их воздействия;
2) нанесение на вибрирующую поверхность упруго-взяких материа-лов;
3) денамические гашение вибрации путем подбора массы фундамента таким образом, чтобы амплитуда колебаний его основания не превышала 0,1 — 0,2 мм.
4.4.4 Расчет искуственного освещения главного корпуса
Для освещения главного корпуса предусмотрена система комбиниро-ванного освещения. Главный корпус проектируемой обогатительной фабрики имеет следующие размеры по пролетам.
Первый пролет: длина (А) — 108 м; ширина (В) — 12 м; высота (Н) — 5 м.
Определяем высоту подвеса светильников i под рабочей поверх-ностью по формуле:
A * B 108 * 12
i = ——————————— = ————————- = 2,15 м.
H * (A * B) 5 * (108 * 12)
Применяем светильники типа «Универсал» без уплотнения. Коэффи-циент использования К = 0,64. Принимаем коэффициент запаса в зависи-мости от условий технологического процесса. В главном корпусе коэффи-циент запаса Кз = 1,3. Находим мощность лампы по формуле:
Emin * S * КЗ
Fn = ———————————,
з где: Fn — мощность лампы, Вт;
Emin — минимальное количество освещения;
S — площадь пролета, м2;
КЗ — коэффициент запаса;
з — коэффициент использования осветительной установки.
Рассчитаем по формуле мощность лампы:
50 * 1296 * 1,3
Fn = ——————————— = 156 000 Вт.
0,54
Выбираем лампы ДРА мощностью 50 Вт. Определяем количество светильников по формуле:
Fn
n = ————, шт.
FЛ
Рассчитаем по формуле количество светильников:
n = —————- = 8 шт.
4.5 Противопожарные мероприятия
Проектируемое предприятие относится по пожароопасности к кате-гории D. На обогатительной фабрике маслостанция и склады с горючими веществами выделены отдельно. На территории фабрики предусмотрен по-жарный трубопровод, предсталенный кольцевой сетью. Для забора воды при пожаре из водопровода на территории фабрики установлены гидранты. Пожарные гидранты расположены вдоль дорог и проездов на расстоянии не более 5 м от стен зданий. Источником водоснабжения является река Бе-резовка. Насосной станцией комбината вода подается в водонапорный ре-зервуар технологической воды, откуда осуществляется снабжение водой предприятия.
Внутренний противопожарный водопровод расположен в администра-тивно-бытовом корпусе. Внутренние пожарные краны установлены на лестницах, у входах, в коридорах. При каждом внутреннем пожарном кра-не имеется откидной рукав длиной не менее 10 м. Во всех производствен-ных помещениях для пожаротушения можно использовать воду, предназ-наченную для уборки рабочих мест.
Помимо всего этого предусматривается установление в цехах первич-ных средств тушения пожара: ручные пенные огнетушители ОХП-10, руч-ные углекислотные огнетушители ОУ-5, в складах устанавливаются дрей-перные установки. Нормами предусматривается:
на 600−800 м2 — огнетушитель ОУ-5 в количестве 1 шт. для производ-ственных зданий;
на 200 м2 — огнетушитель ОУ-5 в количестве 1 шт. для служебно-бытовых зданий;
на 900 м2 — ОУ-5 в количестве 2 шт. для складских помещений.
На фабрике предусмотрены эвакуационные выходы для безопасного вывода людей из зданий и помещений фабрики в случае пожара. Длина пу-тей эвакуации — 40−75 м. Ширина выходов и путей эвакуации принята из плотности массы людских потоков и принята 1,5−2,5 м, а также предусмат-риваются стальные наружные лестницы по периметру здания шириной 0,7 м с углом наклона 600. Оповещение людей производится по селектору, а также звуковой сигнализацией. Для лучшей организации пожарной безопасности организуется пожарно-техническая комиссия, возглавляемая главным инженером, который разрабатывает мероприятия по пожарной безопасности и добровольную пожарную дружину (ДПД). Руководство ДПД возлагаетсяна начальника обогатительной фабрики.
5. Технико-экономическое обоснование
5.1 Главный корпус
Стоительный объем главного корпуса составляет 160 400 м3 по цене 60 000 тенге за 1 м3.
1) Стоимость корпуса составит:
160 400 * 60 000 = 9 624 000 000 тенге.
2) Стоимость строительных металлоконструкций составит при цене 70 000 тенге за 1 тонну металлоконструкций:
(160 400 * 2 / 1000) * 70 000 = 22 456 000 тенге.
3) Стоимость технологических металлоконструкций составит:
(160 400 * 1 / 1000) * 70 000 = 11 228 000 тенге.
4) Общая стоимость корпуса составит: 9 657 684 000 тенге.
5) Накладные расходы на строительство составляют 18% и равны:
9 657 684 000 * 0,18 = 1 738 383 120 тенге.
6) Плановые накопления составляют 2,5% и равны: 241 442 100 тенге.
7) Монтаж электроосвещения по цене 30,0 тенге за 1 кВт устано-вочной мощности равен:
226 112 * 0,385 * 30,0 = 2 611 594 тенге.
8) Стоимость сантехнических работ составляет 15% от стоимости зда-ния и равна 1 448 652 600 тенге.
Всего стоимость строительных работ по главному корпусу составит 22 746 457 414 тенге.
5.2 Расчет стоимости основного и вспомогательного оборудования
Таблица 15
Стоимость основного и вспомогательного оборудования корпуса крупного, среднего и мелкого дробления и главного корпуса
Наименование | Типоразмер | Кол-во | Цена за единицу, тг | Общая стоимость, тенге | Амортизационные отчисления | ||
% | тенге | ||||||
Дробилки | ЩДП — 9×12 | ||||||
КСД — 1750 Гр | |||||||
КИД — 1750 Гр | |||||||
Грохота | ГИТ — 31 | ||||||
ГИТ — 41 | |||||||
Мельница | МШР — 32×31 | ||||||
Спиральный классификатор | 2KCH — 24 A | ||||||
Гидроциклон | ГЦ — 500 | ||||||
Флотационные машины | ФПМ | ; | ; | ; | |||
Сгуститель | СЦ — 12 А | ||||||
Вентилятор | ; | ||||||
Всего | ; | ; | ; | ; | |||
Средства амортизации | ; | ; | ; | ||||
Транспортные и накладные расходы | ; | ; | ; | ||||
Монтаж технологического оборудования | ; | ; | ; | ||||
Неучетное оборудование | ; | ; | ; | ||||
Всего | ; | ; | ; | ; | |||
Общее капиталожение на оборудование | ; | ; | ; | ; | |||
5.3 Расчет стоимости вспомагательных материалов
Таблица 16
Расчет стоимости вспомогательных материалов
Наименование материалов | Годовой расход | |||
Кол-во | Цена, тг | Сумма, тг | ||
Цинковый купорос, кг | ||||
Ксантогенат бутиловый, кг | ||||
Сернистый натрий, кг | ||||
Известь, кг | ||||
Медный купорос, кг | ||||
Фильтроткань, м2 | ||||
Лента транспортерная, м | ||||
Футеровка, кг | ||||
Итого | ||||
Таблица17
Определение энергетических нагрузок
Наименование | Количество | Общая установочная мощность | Коэф-т исп. мощности | Часов работы | Годовой расход э/энергии, кВт-ч | ||||
Рабочих | Резерв-ных | Рабочих, кВт | Резерв-ных, кВт | В сутки | В год | ||||
ЩДП — 9×12 | ; | ; | 0,65 | ||||||
КСД — 1750 Гр | ; | ; | 0,65 | ||||||
КИД — 1750 Гр | ; | ; | 0,65 | ||||||
ГИТ — 31 | ; | ; | 0,65 | ||||||
ГИТ — 41 | ; | ; | 0,65 | ||||||
МШР -32×31 | ; | ; | 0,65 | ||||||
2KCH — 24 A | ; | ; | 0,65 | ||||||
ГЦ — 500 | ; | ; | ; | ; | ; | ; | |||
ФПМ | ; | 0,65 | |||||||
Венилятор | 30,35 | ; | 0,65 | ||||||
Ремонтная нагрузка 7−9% | ; | ; | ; | ; | ; | ; | 6,9 | ||
Потери сетях 0.5% | ; | ; | ; | ; | ; | ; | 0,5 | ||
Всего по объекту | ; | ; | ; | ; | ; | ; | ; | ||
5.4 Стоимость энергозатрат
Годовой расход электроэнергии составляет 287 704 569 кВт по цене 9 тенге за 1 кВт. Стоимость электроэнергии составит:
287 704 569 * 9,0 = 2 589 341 121 тенге.
Годовой расход воды составляет 2 034 000 м3, из нее свежей воды 406 800 м3 по цене 4 тенге за 1 м3, и оборотной воды 1 627 200 м3 по цене 1,8 тенге за 1 м3. Стоимость расходуемой воды составит:
Свежей — 406 800 * 4 = 1 627 200 тенге.
Оборотной — 1 627 200 * 1,8 = 2 928 960 тенге.
Всего — 4 556 160 тенге.
5.5 Заработная плата
Принятая система заработной платы — повременно-премиальная. Премирование производится за перевыполнение плана по переработке руды и качественным показателям: содержание металлов в концентратах и извлечение металлов в концентраты. Шкала и условия премирования разрабатываются отделом труда и заработной платы предприятия, согласуются с профсоюзной организацией и утверждаются соответствующими главными управлениями Министерства металлургии Республики Казахстан. Для примера рассчитаем заработную плату одного рабочего дробильщика крупного дробления. Исходные данные для расчета:
1) разряд — 3;
2) количество смен в сутки — 2;
3) явочная численность в сутки — 2;
4) коэффициент списочности — 1,43;
5) списочная численность — 3;
6) действительной фонд рабочего времени — 189 дней;
7) отработано человек смен — 189 * 3 = 567;
8) сменная тарифная ставка — 560 тенге.
Рассчитаем основной фонд заработной платы:
1) тарифный фонд = Тэф * Nсп * Тт.ст. = 189*3 * 560 = 317 520 тг;
2) приработок сдельщика при перевыполнении плана на 2% = 327 520 * 0,02 = 6350 тг;
3) премии =(тарифный фонд + приработок) * 0,2 = (317 520 + 6350) *0,2 = 64 774 тг;
4) доплата за ночные часы = (8/24) * (0/7) * тарифный фонд = 0 тг;
5) доплата за праздники = Nпр * Nяв * Тт.ст. = 8 * 2 * 560 = 8960 тг.
Итого основного фонда заработной платы = 317 520 + 6350 + 64 774 +8960 = 397 604 тг.
С учетом районного коэффициента К = 1,3 основной фонд заработной платы = 397 604 * 1,3 = 516 885.2 тг.
Рассчитаем дополнительный фонд заработной платы:
1) оплата отпусков = (дни отпуска / Тэф) * 516 885,2 = (36 / 189) * 517 197,2 = 98 454 тг;
2) оплата гособязанностей = 2 / 189 * 516 885,2 = 5470;
Итого доплаты = 98 454 + 5470 = 103 924 тг.
Всего годовой фонд = 516 885,2 + 103 924 = 620 809,2 тг.
Среднемесячная заработная плата = годовой фонд / (Nсп*12) = 620 809,2/(3*12) = 17 245 тг.
Определение численного профессионального состава трудящихся. Расстановчные основных производственных рабочих, ремонтной службы, руководителей, специалистов и служащих приняты по аналогии с дей-ствующей ОФ. Численность трудящихся по категриям:
1) ИТР — 30 чел.;
2) Служащие — 1 чел.;
3) МОП — 10 чел.;
4) Рабочие -306 чел.;
В таблице приведена штатная ведомость ИТР, служащих и МОП.
Таблица 18
Штатная ведомость ИТР, служащих и МОП
Должность, профессия | Явочная численность.чел. | Списочная числен., чел. | Месячная ставка | Годовой фонд зарпл., тенге | ||
Основная, тенге | С учетом районного коэффициента, тенге | |||||
ИТР | ||||||
Начальник фабрики | ||||||
Главный инженер | ||||||
Главный механик | ||||||
Главный энергетик | ||||||
Энергетик | ||||||
Механик | ||||||
Механик кранового хозяйства | ||||||
Начальник главного корпуса | ||||||
Начальник ФСО | ||||||
Начальник реагентного отдел. | ||||||
Начальник хвостового хоз-ва | ||||||
Электромеханик хвост. хоз-ва | ||||||
Мастер основного пр-ва | ||||||
Мастер основного пр-ва | ||||||
Мастер хозслужбы | ||||||
Старший мастер рем.отдел. | ||||||
Начальник участка автоматиз. | ||||||
Мастер участка автоматизации | ||||||
Инженер-электроник | ||||||
Инженер-программист | ||||||
Старший экономист | ||||||
Начальник исслед. лаборатории | ||||||
Инженер-исследователь | ||||||
Начальник экспресс-лаборат. | ||||||
Секретарьмашинистка | ||||||
Итого | ||||||
5.6 Расчет расходов на содержание и эксплуатацию оборудования
Эксплуатация оборудования составляет 0,5% от стоимости всего оборудования без монтажа:
199 602 000 * 0,005 = 998 010 тенге.
Стоимость текущего ремонта составляет 3,5% от стоимости всего оборудования:
199 602 000 * 0,035 = 6 986 070 тенге.
Съемные части и быстроизнашивающийся инвентарь составляет 3% от стоимости всего оборудования:
199 602 000 * 0,03 = 5 988 060 тенге.
Амортизационные отчисления составляют 25% от стоимости всего оборудования:
199 602 000 * 0,25 = 49 900 500 тенге.
Сменные части и быстроизнашивающееся оборудование и инвентарь из расчета 10 000 тенге в год на одного рабочего составляет:
56 * 10 000 = 560 000 тенге.
5.7 Расчет цеховых расходов
1) содержание аппарата и МОП — 8 156 490 тг;
2) амортизация зданий и сооружений из расчета 7% от стоимости всех зданий и сооружений составляет:
1 399 661 470 * 7% = 97 976 303 тг;
3) текущий ремонт зданий и сооружений из расчета 3,5% от стои-мости зданий и сооружений :
1 399 661 470 * 3,5% = 48 988 112 тг;
4) исследования и испытания из расчета 1% от годового фонда зара-ботаной платы :
96 613 206 * 1% = 966 132 тг;
5) охрана труда из расчета 5% от годового фонда заработной платы:
96 613 206 * 5% = 4 830 660 тг;
6) износ малоценного и быстро изнашивающегося инвентаря из расчета 0,2% от стоимости зданий и сооружений :
1 399 661 470 * 0,2% = 1 799 323 тг .
5.7.1 Калькуляция себестоимости переработки руды
Калькуляция себестоимости переработки одной тонны руды приведена в таблице 19.
Таблица 19
Калькуляция переработки одной тонны руды
Наименование статей | Цена за единицу, тенге | Количество в год | Сумма в год, тенге | |
Исходная руда | ||||
Итого | ; | ; | ||
Транспортировка | ||||
Итого | ; | ; | ||
Цинковый купорос, кг | ||||
Ксантогенат бутиловый, кг | ||||
Сернистый натрий, кг | ||||
Известь, кг | ||||
Медный купорос, кг | ||||
Наименование статей | Количество в год | Сумма в год, тенге | ||
Фильтроткань, м2 | ||||
Лента транспортерная, м | ||||
Футеровка, кг | ||||
Итого | ; | ; | ||
Электроэнергия | ||||
Вода свежая | ||||
Вода оборотная | 1,8 | |||
Итого | ; | ; | ||
Зарплата ИТР и МОП | ; | ; | ||
Расходы на содержание иэксплуатацию оборудования | ; | ; | ; | |
Эксплуатация оборудования | ; | ; | ||
Текущий ремонт | ; | ; | ||
Износ малоценного и быстроизнашивающегося оборудования | ; | ; | ||
Амортизация оборудования | ; | ; | ||
Прочие расходы | ; | ; | ||
Итого | ; | ; | ||
Цеховые расходы | ; | ; | ; | |
Содержание аппарата и МОП | ; | ; | ||
Амортизация зданий и сооружений | ; | ; | ||
Текущий ремонт | ; | ; | ||
Исследования и испытания | ; | ; | ||
Охрана труда | ; | ; | ||
Износ малоценного и быстроизнашивающегося инвентаря | ; | ; | ||
Итого | ; | ; | ||
Всего по калькуляции | ; | ; | ||
5.8 Расчет себестоимости концентратов
Таблиц 20
Оптовая стоимость концентратов
Наименование | Выпуск концентрата, т/г | Содержание металла,% | Цена за 1 т концентрата, тг | Сумма, тг | |
Медный концентрат | |||||
Цинковый концентрат | |||||
Итого | |||||
1) Затраты на 1 тонну готовой продукции: (готовой расход по калькуляции) / (оптовая цена всей продукции) = 620 200,3406 тыс. тг / 1 668 100 тыс. тг = 0,37 тыс. тг;
2) Себестоимость 1 тонны продукции: (годовой расход всей калькуляции) / (количество продукции) = 620 200,3406 / 11 107 = 55,83 тыс. тг;
Расчет основных технико-экономических показателей Производительность труда в натуральном выражении на одного трудящегося: (годовая производительность по руде) / (списочный состав трудящихся) = 600 000 / 347 = 1729 т/год;
Производительность труда в денежном выражении на одного трудящегося: (оптовая стоимость всей продукции) / (списочный состав трудящихся) = 1 668 100 тыс. тг / 347 = 4807,20 тыс. тг;
3) Прибыль = (оптовая стоимость годовой продукции) — (себестоимость годовой продукции) = 1 668 100 тыс. тг — 620 200,3406 тыс. тг = 104 789,96 тыс. тг;
4) Рентабельность = (прибыль) · 100 / (себестоимость годовой продукции) = 1 047 899,6 тыс. тг · 100 / 620 200,3406 тыс. тг = 16%;
5) Срок окупаемости = (общая сумма капиталовложений) / (прибыль) = 2 274 645,414 тыс. тг / 1 047 899,6 тыс. тг = 2,1 года.
В таблице 21 приведены основные технико-экономические показтели.
Таблица 21
Технико-экономические показатели проектируемого предприятия
Наименование показателей | Количество | ||
Производительность по руде | т | ||
Содержание в руде основного металла | Cu% Zn% | ||
Содержание металлов в концентратах | Cu% Mo% | ||
Извлечение металлов в концентраты | Cu% Zn% | ||
Численный состав трудящихся в том числе рабочих | чел. чел. | ||
Производительность труда на 1-го трудящегося по руде | т тыс. тг. | 4807.20 | |
Общие капиталовложения | тыс. тг. | 2 274 645,414 | |
Себестоимость переработки 1 т руды | тг. | 2,16 | |
Стоимость годовой продукции | тыс. тг. | ||
Годовая прибыль | тыс. тг. | 104 789.96 | |
Рентабельность | % | ||
Срок окупаемости | г | 2.1 | |
ЗАКЛЮЧЕНИЕ
В соответствии с полученным заданием разработан проект обогатительной фабрики с производительностью 600 тысяч тонн руды в год по переработке медно цинковых руд Абызского месторождения.
Проектом предусмотрено:
— трехстадиальное дробление исходной руды с предварительным грохочением во второй и третьей стадии;
— двухстадиальное измельчение с контрольной классификацией в замкнутом цикле первой и второй стадии;
— схема селективной флотации минералов меди и цинка;
— трехстадиальное обезвоживание, включающее сгущение, фильтрование и сушку.
На проектируемой фабрике приняты следующие основные технологические показатели:
1) содержание металла в одноименных концентратах: Cu — 15%;
Zn — 45%;
2) извлечение металла в одноименные концентраты: Cu — 75%;
Zn — 80%;
В результате выполненных расчетов получены следующие технико-экономические показатели:
— количества получаемых концентратов: Cu — 4241 т/г;
Zn — 6866 т/г;
1. Полькин С. И., Адамов Э. В. Обогащение руд цветных и редких металлов. — М.: Недра, 1975 г.
2. Флотационное обогащение. О факторах влияющих на флотацию медно-свинцово-цинково-пиритных руд и на выбор реагентов. //Экспресс — информация, ВИНИТИ, № 35, — М.: 1977 г.
3. Ревазашвилли Б. И., Сажин Ю. Г. Расчеты схем рудоподготовки и выбор дробильно-измельчительного оборудования. Измельчение — А.: Каз ПТИ, 1985 г.
4. Сажин Ю. Г. Расчеты схем рудоподготовки и выбор оборудования для дробления, грохочения, измельчения и классификации — А.: Каз НТУ, 1999 г.
5. Справочник по обогащению руд. Под редакцией Богданова О. С., Олевского В. А. — М.: Недра, том I, II, III, 1982 г.
6. Разумов К. А., Перов В. А. Проектирование обогатительных фабрик. — М.: Недра, 1982 г.
7. Троп А. Е., Козин В. З., Прокофьев Е. В. Автоматическое управление технологическими процессами обогатительной фабрики. — М.: Недра, 1986 г.
8. Моршинин В. М. Охрана труда на обогатительных фабриках. — М.: Недра, 1986 г.
9. Малинова Р. Д., Граценштейн И. М. Организация, планирование и управление на предприятиях цветной металлургии — М.: Металлургия, 1987 г.
10. Милованов Л.и. — М.: Металлургия, 1971 г.
11. Сажин Ю. Г. Расчеты схем рудоподготовки и выбор оборудова-ния для дробления, грохочения, измельчения и классификации: Учеб.пособие. Алматы: КазНТУ, 2005 г. — 177 с.
12. Справочник по обогащению руд. Подготовительные процессы. Изд. 2-е, переработанное и дополненное — М.: Недра, 1982 г.
13. Справочник по обогащению руд. Основные процессы. Изд. 2-е, переработанное и дополненное — М.: Недра, 1984 г.
14. Егоров В. Л. Обогащение полезных ископаемых. — М.: Недра, 1986 г.
15. Технический регламент РК «Общие требования к пожарной безопасности» от 16 января 2009 года № 14.
16. СН № 1.02.013−94 «Вибрация рабочих мест»
17. Закон РК о пожарной безопасности от 22 ноября 1996 г.
18. Шокобаев Т. Ш. Микроэкономика промышленности, 1999 г.-237 с.
19. Злобинский Б. М. Охрана труда в металлургии, М.: Металлургия, 1975 г.-251с.
20. Жарспаев М. Т. Охрана труда и аэрология карьеров: Учеб. Пособие. — Алматы: КазНТУ, 2010 г.
22 Сажин Ю. Г. Выбор и технологический расчет оборудования для классификации и перекачки пульп. Методические указания. — Алматы, 1997 г.
21. Сажин Ю. Г. Расчет хвостового хозяйства обогатительных и золотоизвлекательных фабрик. Методические указания. — Алматы, 1989 г.
ПРИЛОЖЕНИЕ А
ДУ — 34 — 2.5 | Фильтр | ||||||||||
СЦ — 12А | Сгуститель | ||||||||||
ФПМ — 12.5 | Флотомашины | ||||||||||
ФПМ — 12,5 | Флотомашины | ||||||||||
МШЦ 3200×3100 | Мельница | ||||||||||
МШР 2700×3600 | Мельница | ||||||||||
ГЦ — 500 | Гидроциклон | ||||||||||
2КСН-24 А | Классификатор | ||||||||||
Распределительный бункер | |||||||||||
Транспортер с тялежкой | |||||||||||
КИД — 1750 | Дробилка | ||||||||||
ГИТ — 31 | Грохот | ||||||||||
КСД — 1750Гр | Дробилка | ||||||||||
Ленточный конвейер | |||||||||||
ЩДП — 9Ч12 | Дробилка | ||||||||||
Пластинчитый питатель | |||||||||||
Бункер | |||||||||||
№ поз | Тип, марка | Наименование | Кол. | Примечание | |||||||
СПЕЦИФИКАЦИЯ 5В73 700-ОПИ | |||||||||||
Схема цепи аппаратов | Лит. | Масса | Масшт | ||||||||
Изм | Лист | № докум. | Подп. | Дата | у | ||||||
Разработал | Рнашева | ||||||||||
Руководит. | Телков | ||||||||||
Проверил | Телков | Лист | Листов | ||||||||
Проект обогатительной фабрики месторождения Абыз | КазНТУ кафедра МБМ и ОПИ | ||||||||||