Энергетическая установка с реактором РБМК-1500
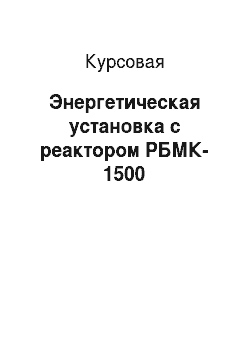
Рисунок 4.2 — Схема потока теплоносителя На Рисунке 4.2 показаны потоки двухфазной смеси, воды и пара в БС диаметром 2600 мм. Пароводяная смесь с суммарным массовым расходом Gтк из топливных каналов подается в водяной объем БС по индивидуальным трубопроводам пароводяной коммуникаций (ПВК) от каждого ТК. При номинальной мощности реактора в каждый из БС подается смесь ПВ с расходом Gтк =7900 т/ч… Читать ещё >
Энергетическая установка с реактором РБМК-1500 (реферат, курсовая, диплом, контрольная)
Федеральное агентство по образованию Государственное образовательное учреждение высшего профессионального образования Московский ордена Ленина, ордена Октябрьской Революции и ордена Трудового Красного Знамени государственный технический университет им. Н. Э. Баумана.
Пояснительная записка.
РБМК 1500.00.00 ПЗ.
Энергетическая установка с реактором РБМК-1500.
Тепловая схема контур многократной принудительной циркуляции.
Студент Манасипов Р.Я.
Группа Э 7 — 71.
Руководитель курсовой работы Дунайцев А.А.
Москва 2014.
- Введение
- 1. Общие сведения
- 1.1 Общие сведения о атомной энергетической установке
1.2 Тепловыделяющие сборки.
1.3 Каналы активной зоны.
1.4 Размещения ЯЭУ.
1.5 Охлаждения каналов АЗ.
- 2. Устройство и основные технические характеристики реактора
- 2.1 Топливо
- 2.2 Замедлитель
- 2.3 Каналы АЗ РБМК 1500
- 2.4 Системы автоматизированного управления
- 2.5 Основные технологические характеристики реактора РБМК 15
- 2.6 Эксплуатационные характеристики реактора РБМК 1500
- 3. Тепловая схема
- 3.1 КМПЦ
- 3.1.1 Технологический состав КМПЦ
- 3.1.2 ГЦН
- 3.2 Принцип работы
- 3.2.1 Узел регулирования расхода питательной воды
- 4. Сепараторы пара РБМК
- 4.1 Гравитационная сепарация пара
- 4.2 Гидродинамические процессы в БС реактора РБМК
- 4.3 Водяной и пароводяной объем сепараторов
- 5. Сепараторы пара энергоблока РБМК-1500
- 5.1 Конструкционные характеристики БС
- Заключение
- Список использованной литературыВведение
Курсовое задание:Описание реактора большой мощности канального с мощностью 1500 МВт его тепловой схемы, КМПЦ в реакторной установке РБМК 1500, с описанием основного оборудования контура, его принципа работы.
Реактор РБМК-1000 является реактором с неперегружаемыми каналами, в отличие от реакторов с перегружаемыми каналами, ТВС и технологический канал являются раздельными узлами. К установленным в реактор каналам с помощью неразъемных соединений подсоединены трубопроводы — индивидуальные тракты подвода и отвода теплоносителя. Загружаемые в каналы ТВС крепятся и уплотняются в верхней части стояка канала. Таким образом, при перегрузке топлива не требуется размыкания тракта теплоносителя, что позволяет осуществлять ее с помощью соответствующих перегрузочных устройств без остановок реактора.
При создании таких реакторов решалась задача экономичного использования нейтронов в активной зоне реактора. С этой целью оболочки твэлов и трубы канала изготовлены из слабо поглощающих нейтроны циркониевых сплавов. В период разработки РБМК температурный предел работы сплавов циркония был недостаточно высок. Это определило относительно невысокие параметры теплоносителя в РБМК. Давление в сепараторах равно 7,0 МПа, чему соответствует температура насыщенного пара 284 °C. Схема установок РБМК одноконтурная. Пароводяная смесь после активной зоны попадает по индивидуальным трубам в барабаны-сепараторы, после которых насыщенный пар направляется в турбины, а отсепарированная циркуляционная вода после ее смешения с питательной водой, поступающей в барабаны-сепараторы от турбоустановок, с помощью циркуляционных насосов подается к каналам реактора.
Разработка РБМК явилась значительным шагом в развитии атомной энергетики СССР, поскольку такие реакторы позволяют создать крупные АЭС большой мощности.
Из двух типов реакторов на тепловых нейтронах — корпусных водо-водяных и канальных водографитовых, использовавшихся в атомной энергетике, последние оказалось проще освоить и внедрить в жизнь. Это объясняется тем, что для изготовления канальных реакторов могут быть использованы общемашиностроительные заводы и не требуется такого уникального оборудования, которое необходимо для изготовления корпусов водо-водяных реакторов.
Эффективность канальных реакторов типа РБМК в значительной степени зависит от мощности, снимаемой с каждого канала. Распределение мощности между каналами зависит от плотности потока нейтронов в активной зоне и выгорания топлива в каналах. При этом существует предельная мощность, которую нельзя превышать ни в одном канале. Это значение мощности определяется условиями теплосъема. Первоначально проект РБМК был разработан на электрическую мощность 1000 МВт, чему при выбранных параметрах соответствовала тепловая мощность реактора 3200 МВт. При имеющемся в реакторе количестве рабочих каналов (1693) и полученном коэффициенте неравномерности тепловыделения в активной зоне реактора максимальная мощность канала составляла около 3000кВт. В результате экспериментальных и расчетных исследований было установлено, что при максимальном массовом паросодержании на выходе из каналов около 20% и указанной мощности обеспечивается необходимый запас до кризиса теплосъема. Среднее паросодержание по реактору составляло 14,5% РБМК 1000, 28% РБМК 1500.
Энергоблоки с реакторами РБМК электрической мощностью 1000 МВт (РБМК-1000) находятся в эксплуатации на Ленинградской, Курской, Чернобыльской АЭС, Смоленской АЭС. Они зарекомендовали себя как надежные и безопасные установки с высокими технико-экономическими показателями. Если их специально не взрывать.
Для повышения эффективности реакторов РБМК были изучены возможности увеличения предельной мощности каналов. В результате конструкторских разработок и экспериментальных исследований оказалось возможным путем интенсификации теплообмена увеличить предельно допустимую мощность канала в 1,5 раза до 4500 кВт при одновременном повышении допустимого паросодержания до нескольких десятков процентов. Необходимая интенсификация теплообмена достигнута благодаря разработке ТВС, в конструкции которой предусмотрены интенсификаторы теплообмена.
При увеличении допустимой мощности канала до 4500 кВт тепловая мощность реактора РБМК повышена до 4800 МВт, чему соответствует электрическая мощность 1500 МВт. Такие реакторы РБМК-1500 работали на Игналинской АЭС. Увеличение мощности в 1,5 раза при относительно небольших изменениях конструкции с сохранением размеров реактора является примером технического решения, дающего большой эффект.
1. Общие сведения.
1.1 Общие сведения о атомной энергетической установке.
Ядерный энергетический реактор РБМК является гетерогенным канальным реактором на тепловых нейтронах, в котором в качестве замедлителя используется графит. Теплоноситель — кипящая легкая вода, которая циркулирует по вертикальным каналам, пронизывающим кладку атомной зоны. Этот тип реактора являлся продолжением развития уран-графитовых реакторов в России (СССР). Активная зона имеет форму вертикального цилиндра эквивалентным диаметром 11.8 и высотой 7 м. Она окружена боковым отражателем толщиной 1 м торцевыми отражателями по 0.5 м. В состав активной зоны входят твэлы, замедлитель, теплоноситель, технологические каналы, стержни поглотители нейтрон.
Теплоноситель подается снизу в каждый технологический канал. Экономайзерный участок, на котором вода нагревается до температуры насыщения имеет высоту около 2.5 м от низа активной зоны. На остальной ее части имеет место процесс развития кипения, причем массовое паросодержание теплоносителя по ходу потока и на выходе из активной зоны в среднем по реактору составляет 28%.
1.2 Тепловыделяющие сборки.
ТВС в РБМК состоят из двух частей-нижней и верхней, каждая из которых содержит 18 твэлов стержневого типа из таблеток спеченной двуокиси урана, заключенных в оболочку из циркониевого сплава. Высота активной части топлива в твэле 3,5 м, общая высота активной зоны в РБМК 7,0 м. Диаметр твэла 13,5 мм. Расположение твэлов в ТВС с требуемым шагом (минимальный зазор между твэлами 1,7 мм) обеспечивается с помощью дистанционирующих решеток, состоящих из 19 ячеек, из которых 18 служат для дистанционирования твэлов, а центральная ячейка — для крепления решетки к каркасной трубке ТВС. Ячейки сварены между собой точечной сваркой в единую конструкцию. В ТВС с интенсификацией теплообмена в решетках верхней части имеются устройства для турбулизации потока теплоносителя, что и обеспечивает интенсификацию теплообмена. ТВС крепятся к подвеске, в верхней части которой находится запорное устройство-пробка, предназначенная для закрепления подвески с ТВС в канале и одновременно герметизации канала. Крепление подвески осуществляется с помощью шариков, которые фиксируются в кольцевой канавке, выполненной на внутренней поверхности верха стояка канала, распорной втулкой при ее перемещении за счет вращения винта. При фиксированных шариках и дальнейшем вращении винта производится уплотнение подвески в канале путем обжатия герметизирующей прокладки. Все указанные операции производятся разгрузочно-загрузочной машиной.
1.3 Каналы активной зоны.
Помимо топливных каналов в активной зоне РБМК имеется 179 каналов СУЗ. Стержни СУЗ предназначены для регулирования радиального поля энерговыделения (PC), автоматического регулирования мощности (АР), быстрой остановки реактора (A3) и регулирования высотного поля энерговыделения (УСП), причем стержни УСП длиной 3050 мм выводятся из активной зоны вниз, а все остальные длиной 5120 мм, вверх.
Для контроля за энергораспределением по высоте активной зоны предусмотрено 12 каналов с семисекционными детекторами, которые установлены равномерно в центральной части реактора вне сетки топливных каналов и каналов СУЗ. Контроль за энергораспределением по радиусу активной зоны производится с помощью детекторов, устанавливаемых в центральные трубки ТВС в 117 топливных каналах. На стыках графитовых колонн кладки реактора предусмотрено 20 вертикальных отверстий диаметром 45 мм, в которых устанавливаются трехзонные термометры для контроля за температурой графита.
1.4 Размещения ЯЭУ.
реактор сепаратор энерговыделение.
Реактор размещен в бетонной шахте размером 21,6×21,6×25,5 м. Нижняя плита толщиной 2 м и диаметром 14,5 м состоит из цилиндрической обечайки и двух листов, в которые герметично вварены трубные проходки для топливных каналов и каналов управления. Весь объем внутри плиты между проходками заполнен серпентинитом, благодаря чему она, являясь биологической защитой, обеспечивает возможность проведения работ в под реакторном пространстве во время остановки реактора.
Нижняя плита через сварную металлоконструкцию в виде креста опирается на бетонное основание шахты реактора. Реактор окружен боковой защитой в виде кольцевого бака с водой, который установлен на опорных конструкциях, крепящихся к бетонному основанию шахты реактора. Наружный диаметр бака равен 19 м, внутренний на высоте 11 м — 16,6 м. На верхнем торце бака на 16 Катковых опорах установлена верхняя плита, аналогичная по конструкции нижней. Толщина верхней плиты 3 м, диаметр 17,5 м. Вокруг верхней плиты имеется дополнительная боковая защита в виде кольцевого бака с водой высотой 3,2 м, наружным диаметром 19 м, а внутренним 17,8 м.
Нижняя и верхняя плиты соединены между собой герметичным кожухом из листового проката толщиной 16 мм. В нижней части кожуха имеются компенсаторы линейного удлинения с толщиной стенки 8 мм. Вверху и внизу кожух и бак боковой защиты соединены диафрагмами с компенсаторами, линейных удлинений. Таким образом, между кожухом и боковой защитой образуется кольцевая, также герметичная, полость.
1.5 Охлаждения каналов АЗ.
Для охлаждения каналов и стержней используется автономный водяной контур с насосно-теплообменной установкой. Вода движется в каналах сверху вниз и омывает наружную и внутреннюю поверхность оболочек поглощающих стрежней нагреваясь от 40 до 60 градусов Цельсия. При работающем реакторе внутренняя полость каналов независимо от положения стрежней заполняется водой.
2. Устройство и основные технические характеристики реактора.
2.1 Топливо.
Топливом для РБМК служит слабо обогащенная по урану-235 двуокись урана. В исходном для начала процесса состоянии каждая ее тонна содержит примерно 20 кг ядерного горючего — урана-235. А стационарная загрузка двуокиси урана в один реактор равна 180 т.
Топливо:
двуокись урана UO2 2% обогащения;
двуокись урана UO2 2.4% обогащения, содержащая эрбий;
двуокись урана UO2 2.6% обогащения, содержащая эрбий.
2.2 Замедлитель.
Замедлитель — графитовая кладка, состоящая из колонн квадратного сечения (250 мм х 250 мм). Периферийные колонны кладки образуют боковой отражатель реактора толщиной 880 мм, торцевые блоки колонн — верхний и нижний отражатели толщиною по 500 мм. В центральные сквозные отверстия колонн замедлителя установлены технологические каналы (ТК) и каналы системы управления и защиты (СУЗ) реактора, в периферийных колоннах — каналы охлаждения отражателя (КОО) и каналы СУЗ.
В ТК загружаются кассеты с топливом, предназначенные для генерации тепловой энергии. Теплосъём с топливных кассет осуществляется водой контура многократной принудительной циркуляции (КМПЦ). В каналах СУЗ размещаются исполнительные механизмы СУЗ, камеры деления (КД) и датчики контроля энерговыделения по высоте активной зоны реактора (ДКЭВ).
Номинальный температурный режим работы механизмов и датчиков СУЗ и охлаждение отражателя обеспечивается насосно-теплообменной установкой контура охлаждения СУЗ (НТУ КО СУЗ).
2.3 Каналы АЗ РБМК 1500.
Общее число каналов в активной зоне реактора — 2070, из них:
— технологических — 1661.
— отбора проб газа — 1.
— СУЗ — 235.
— охлаждения отражателя — 156.
— температурных — 17.
Размеры активной зоны: Ш 11 800 мм, высота — 7000 мм. Решётка активной зоны квадратная с шагом 250 мм. Вне решетки находятся 17 температурных каналов и канал отбора проб газа.
2.4 Системы автоматизированного управления.
Реактор оснащен:
— системой управления и защиты (СУЗ);
— системой контроля распределения энерговыделения (СКРЭ);
— информационно-вычислительной и управляющей системой (УВС) «Титан» ;
— системой технологического контроля;
— системой контроля герметичности оболочек ТВЭЛов;
— системой контроля целостности технологических каналов (КЦТК);
— специальными трактами и комплектами принадлежностей и образцов-свидетелей для контроля за состоянием металла оборудования реактора.
2.5 Основные технологические характеристики реактора РБМК 15.
В Таблице 1 представлены основные технологические характеристики реактора РБМК 1500, в сравнении с реактором РБМК 1000.
Таблица 1. Технологические характеристики.
Параметр | РБМ-К 15. | РБМ-К 7. | |
Мощность тепловая. МВт. | |||
Мощность электрическая. МВт. | |||
Номинальный расход теплоносителя через реактор, т/ч. | |||
Давление теплоносителя (воды) на входе в ТК максимальной расчетной мощности, кгс/смІ. | 87,4. | 82,7. | |
Давление теплоносителя (пароводяной смеси) на выходе из ТК. кгс/смІ. | |||
Температура теплоносителя (Воды) на входе в ТК. °С. | |||
Температура теплоносителя (пароводяной смеси) на выходе из ТК, °С. | |||
Среднее массовое паросодержание на выходе из ТК. %. | 28,9. | 15,2. | |
Температура питательной воды на входе в барабан сепараторы. °С. | |||
Расход насыщенного пара, т/ч. | |||
Средняя скорость теплоносителя на выходе из ТК, м/с. | |||
2.6 Эксплуатационные характеристики реактора РБМК 1500.
Работа реактора после энергопуска и выхода на номинальную мощность характеризуется тремя эксплуатационными периодами. В начальный период загрузка реактора содержит 234 дополнительных поглотителя (ДП) для компенсации избыточной реактивности и 1427 кассет.
По мере выгорания топлива ДП извлекаются и на их место устанавливаются свежие кассеты. Полное извлечение ДП происходит приблизительно через 500 эфф.суток. После полной замены ДП начинается перегрузка кассет, основная часть которых к этому моменту имеет приблизительно одинаковое выгорание (9000 — 10 000 МВт сут/т).
В результате перегрузок в реакторе примерно через 1600 эфф. суток — это длительность переходного периода — устанавливается такое равновесное состояние, при котором вся совокупность кассет имеет постоянный спектр по выгоранию топлива. Это состояние характеризует стационарный режим или режим установившихся перегрузок.
В стационарном режиме средняя глубина выгорания топлива по реактору составляет 10 000 — 11 000 МВт сут/т.
Средняя глубина выгорания выгружаемого топлива — 21,6 МВт сут/кг.
Средний темп перегрузки — 1,94 шт/эфф.сут. (Л.42).
Расход урана при коэффициенте нагрузки ц = 0,8 (Л.42):
— обогащенного, т/год — 64,9:
— природного, т/год — 205,2.
Кампания реактора 860 суток (Л.42). Перегрузка топлива производится без останова реактора разгрузочно-загрузочной машиной (РЗМ).
3. Тепловая схема.
По отдельным стадиям технологического процесса все теплоэнергетическое оборудование АЭС одноконтурной подразделяют, на реакторную, паротурбинную и конденсационную установки и конденсаторный тракт. Взаимосвязь между этими элементами образует тепловую схему станции.
Рассмотрим упрощенную тепловую схему реакторной установки АЭС.
Реакторная установка — источник тепла, теплоноситель вода в реакторе нагревается и частично испаряется образуя пароводяную смесь. В барабане сепараторе (БС) происходит разделение пароводяной смеси на воду и пар, пар направляется на турбину. Турбина состоит из одного цилиндра высокого давления (ЦВД) и четырех цилиндров низкого давления.
Так как, пар поступает в турбину насыщенным то, расширяясь в турбине, он быстро увлажняется. Предельно допустимая влажность пара обычно не должна превышать 8−12% во избежание интенсивного эрозионного износа лопаточного аппарата каплями воды.
При достижении предельной влажности весь пар выводится из цилиндра высокого давления и пропускается через сепаратор — пароподогреватель (СПП), где он осушается и нагревается. Для подогрева основного пара до температуры насыщения используется пар первого обора турбины, для перегрева используется острый пар, дренаж греющего пара сливается в деаэратор (Рисунок 3.1): БС — барабан сепаратор; ГЦН — главный циркуляционный насос; ДА — деаэраторы; ПН — питательный насос; ЦНД — цилиндр низкого давления турбины; СПП — сепаратор пароперегреватель; ЦВД — цилиндр высокого давления; К — конденсатор; КН1 — конденсатные насосы первой ступени; КН2 — конденсатные насосы второй ступени; ОД — охладитель дренажа; ПНД — подогреватель низкого давления; БОУ — блочная очистная установка.
Рисунок 3.1- Принципиальная тепловая схема.
После сепаратора — пароподогревателя пар поступает в цилиндр низкого давления. Здесь пар в процессе расширения снова увлажняется до предельно допустимой влажности и поступает в конденсатор (К). Стремление получить от каждого килограмма пара возможно большую работу и тем самым повысить к.п.д. заставляет поддерживать в конденсаторе возможно более глубокий вакуум. В связи с этим конденсатор и большая часть цилиндра низкого давления турбины находятся под разрежением. Тепло, передаваемое в конденсаторе охлаждающей воде, безвозвратно теряется. Величину потерь можно снизить путем уменьшения пропуска пара в конденсатор, что достигается направлением части пара в систему регенеративных подогревателей воды.
Турбина имеет семь отборов пара, второй отбор используется для подогрева воды в деаэраторе, а отборы 3 — 7 используются для подогрева основного потока конденсата в, соответственно, ПНД-5 — ПНД-1 (подогреватели низкого давления). Так как цикл рабочего тела замкнут, то весь турбинный конденсат должен быть подан в барабан сепаратор. За счет работы насосов давление повышается от величины, характерной для конденсатора, до давления в барабане сепараторе, с учетом необходимости преодоления сопротивления тракта от конденсатора до барабана сепаратора. Этот тракт делят на две части. Конденсатные насосы первой ступени (КН 1) забирают конденсат из водяного объема конденсатора и прокачивают его через блочную очистную установку (БОУ), после чего, конденсатные насосы второй ступени (КН 2) прокачивают основной конденсат через охладитель дренажа (ОД) и регенеративные подогреватели, называемые подогревателями низкого давления, до деаэратора (ДА) назначение которого в схеме будет объяснено позже. В деаэраторном баке, давление в котором выше атмосферного, создается определенный запас воды. Питательным насосом (ПН), обеспечивающим последующее повышение давления вплоть до рабочего в барабане сепараторе, вода из деаэраторного бака подается в барабан сепаратор. Где происходит ее смешение с водой контура многократной принудительной циркуляции.
Главными циркуляционными насосами (ГЦН), вода из барабана сепаратора подается в активную зону. Весь тракт от конденсатора до барабана сепаратора называют конденсатно-питательным, а его части до и после деаэратора — конденсатным и питательным трактами соответственно. В регенеративных подогревателях конденсат подогревается отборным паром турбин, конденсат которого возвращается в систему (в конденсатор).
Так как цилиндр низкого давления турбины работает в области вакуума, то трубопроводы отборного пара к ПНД, сами эти подогреватели по стороне греющего пара и линии конденсата греющего пара находятся под разрежением. Из цилиндра высокого давления отбор пара производится также и для подогрева воды в сетевом подогревателе для отопления, вентиляции и горячего водоснабжения.
Таким образом, по конденсатно-питательному тракту происходит увеличение давления и энтальпии рабочего тела. В реакторе установке энтальпия пара увеличивается при постоянном давлении до максимальной величины для данного цикла. Далее в паровой турбине энтальпия и давление пара непрерывно уменьшаются до давления в конденсаторе, где в связи с конденсацией пара при постоянном давлении энтальпия уменьшается до минимального значения для данного цикла, цикл замыкается.
3.1 КМПЦ.
3.1.1 Технологический состав КМПЦ.
Контур МПЦ предназначен для подачи воды в технологические каналы реактора в целях отвода тепла от ТВС. Он состоит из двух аналогичных автономных петель: каждая отводит тепло от половины тепловыделяющих кассет реактора. В каждую петлю входят:
— два сепаратора пара;
— соединительные перемычки между двумя сепараторами по пару и воде;
— опускные трубопроводы;
— четыре ГЦН;
— всасывающий коллектор ГЦН;
— всасывающие трубопроводы ГЦН с арматурой;
— напорный коллектор ГЦН;
— байпас между всасывающими и напорными коллекторами ГЦН;
— раздаточные групповые коллекторы с запорно-регулирующими клапанами;
— трубы водяных коммуникаций;
— технологические каналы;
— трубы пароводяных коммуникаций.
3.1.2 ГЦН.
Вода из нижней части сепаратора по 12 опускным трубам поступает во всасывающий коллектор и в четыре всасывающих трубопровода ГЦН. На всасывающих трубопроводах установлены запорные задвижки с дистанционным приводом. В период пуска, нормальной работы и начальной период расхолаживания циркуляция осуществляется насосами марки ЦВН — 7, из которых три работающие и один резервный. Насос ЦВН — 7 — центробежный вертикальный, одноступенчатый с уплотнением вала, исключающим выход теплоносителя в помещение. Производительность — 8000 мі/ч, напор — 203 м. вод. Ст. (2 Мпа), абсолютное давление на вс. 72 кгс/смІ.
Насос состоит (Рисунок 3.2) из корпуса, выемной части и электродвигателя тип ВДА — 173 199 — 6 мощностью 5500 кВт, и располагает маховым моментом 15 т/мІ. При обесточивании всех ГЦН в случае аварии благодаря такому маховому моменту увеличивается время выбега ГЦН, чем и улучшаются условия расхолаживания реактора в первые секунды после остановки. На уплотнение вала насоса подается запирающая вода с давлением 2.6 кгс/смІ (0.25) выше давления на всосе. ГЦН. Для четырех ГЦН, входящих в состав одной насосной, предусмотрены индивидуальные узлы регулирования уплотняющей воды. Последняя из баков чистого конденсата подается насосами [типа ЦН — 900 производительностью 100 мі/ ч напором 930 м вод. ст.] в мультигидроциклон, который служит для очистки уплотняющей воды от мех. примесей. Очищенная вода из последнего поступает в узел регулирования, который поддерживает давления на входе в ГЦН. Расход на уплотнение каждого ГЦН 22 мі/ч. Подпитка контура уплотнения ведется конденсатными насосами. Вода в подшипник ГЦН поступает из напорного коллектора через мультигидроциклон и дроссельную шайбу.
Рисунок 3.2 — ГЦН: 1 — диск прижимной; 2- рабочее колесо;3 — направляющий аппарат; 4- бак насоса; 5 — промежуточная плита; 6 — прокладка;7- крышка; 8 — выемная часть; 9 -корпус; 10 — уплотнение вала; 11, 15 — слив масла из подшипников; 12 — корпус подшипника;13 — радиально осевой подшипник; 14 — подача масла в радиально осевой подшипник; 16,19 — вода из уплотнения;17- слив вода-масляной эмульсии; 18 -вода в уплотнении В случае полного обесточивания АЭС до момента включения дизель-генераторов уплотняющая вода подается давлением от аварийной газовой системы, состоящей из гидравлических баллонов, заполненных конденсатом, и газовых баллонов подключенных к системе сжатого воздуха ВД. Система обеспечивает питание уплотнений ГЦН в течении 10 мин.
Для надежной работы насосов предусмотрена индивидуальная система маслохозяйства, обеспечивающая смазку и охлаждение верхнего радиально — упорного подшипника ГЦН и подшипников ЭД .
3.2 Принцип работы.
К технологическим каналам вода поступает с температурой 270 °C. Омывая твэлы, вода нагревается до температуры насыщения, частично испаряется и пароводяная смесь с температурой 285 °C и давлением 72 кгс/смІ (приблизительно 7 МПа) по индивидуальным трубопроводам пароводяных коммуникаций поступает в сепараторы пара. В сепараторах смесь разделяется на пар и воду. Кроме того, в сепараторах содержится запас воды, который расходуется на заполнение пароводяного тракта контура МПЦ при резких снижениях мощности реактора (при отключении одной или двух турбин, при обесточивании собственных нужд блока). В целях обеспечения минимальной разности уровней воды в двух соседних сепараторах последние соединяются по водяному объему двумя и по паровому объему — пятью перемычками.
Уровень воды в сепараторах регулируется автоматически трехимпульсной системой, работающей по сигналам изменения уровня воды в сепараторах, по сигналам от расходомеров, установленных на паропроводах сепаратора, и по сигналам от расходомеров на линиях подвода питательной воды..
От одной из водяных перемычек каждой пары сепараторов имеется отбор воды контура МПЦ в систему расхолаживания. Другая водяная перемычка каждой пары сепараторов нижней частью через трубу связана с одной из опускных труб, что обеспечивает опорожнение перемычки при опорожнении опускных труб в период ремонта.
Вода из сепаратора поступает в опускные трубопроводы, на входе смешиваясь в специальных смесителях с питательной водой, которая подается питательными насосами в сепаратор. Трубопроводы питательной воды имеют наружный диаметр 426 и толщину стенки 22 мм. Смесители и коллектор питательной воды входят в конструкцию сепаратора.
Насыщенный пар отводится из верхней части сепаратора по 14 паропроводам. Семь отводов объединяются в паровой коллектор, пар из которого направляется к одной турбине, от семи других к другой. Это обеспечивает равномерную нагрузку сепараторов при работе блока как с двумя, так и с одной турбиной.
3.2.1 Узел регулирования расхода питательной воды.
Питательная вода с расходом 2800 т/ч подается к каждой паре сепараторов от напорного коллектора питательных насосов через узел регулирования расхода питательной воды (Рисунок 3.3).
Рисунок 3.3. Узел регулирование расхода питательной воды.
Питательная вода в смесителях 2 смешивается с водой, прошедшей байпасную очистку и имеющей температуру 255°С. Температура питательной воды на входе в сепараторы приблизительно 168 °C. Узел регулирования расхода питательной воды, один на два сепаратора, состоит из четырех параллельных ниток трубопроводов: трех основных и одной байпасной. В номинальном режиме работы блока две основные нитки являются рабочими, одна — резервная.
В каждой основной нитке последовательно установлены: запорная задвижка, механический фильтр 1, клапан автоматического регулирования, обратный клапан, запорная задвижка. Последняя предназначена для отключения нитки при выходе из строя любого из установленного там оборудования. В механических фильтрах улавливаются частицы размером не менее 0,1 мм..
На байпасной нитке последовательно установлены: расходомер, механический фильтр, запорная задвижка с сельсином, обратный клапан, запорная задвижка. Эта нитка предназначена для заполнения контура МПЦ питательной водой после планово-предупредительного ремонта (расход по нитке при заполнении 100 — 150 т/ч) и для подачи питательной воды в сепараторы в период пуска или стоянки реактора, а также при работе реактора на малой мощности, когда паропроизводительность реактора не превышает 200−300 т/ч (уровень воды в сепараторах в это время поддерживается с помощью задвижек).
4. Сепараторы пара РБМК.
4.1 Гравитационная сепарация пара.
Для получения пара требуемого качества на РУ РБМК применяется гравитационная сепарация. Гравитационная (осадительная) сепарация — наиболее простой и поэтому широко применяющийся в промышленной энергетике. Отделение пара от воды происходит в восходящем дисперсном потоке пароводяной смеси, т. е. смеси пара и водяных капель широкого спектра размеров.
4.2 Гидродинамические процессы в БС реактора РБМК.
В каждой из двух циркуляционных петель КМПЦ реактора РБМК установлено по два барабан-сепаратора, которые предназначаются для разделения пароводяной смеси, поступающей из топливных каналов, на пар и воду и для размещения запаса воды, который используется для заполнения «паровых пустот» при снижении мощности или заглушении реактора, так называемый оперативный запас воды. В барабан-сепараторе так же происходит смешивание питательной воды с отсепарированной насыщенной водой для создания необходимого недогрева на входе в топливные каналы. Смесители питательной и насыщенной воды в входных патрубках опускных трубопроводах.
Для получения пара требуемого качества т. е. влажностью менее 0,1% используется гравитационная сепарация (Рисунок 4.1). Основным преимуществом этого типа сепарации является исключительная простота конструкции сепарационных устройств.
Рисунок 4.1 — Схема движения пара в сепараторе.
Недостатки — гравитационная сепарация эффективна только при низких скоростях пара, уходящего с «зеркала испарения». Для большинства паропроизводительностей, характерных для большинства современных энергоустановок, это означает необходимость больших габаритов сепараторов пара. Для давления 7 МПа получим значение средней скорости пара на «зеркале» испарения 0.2 м /c. При паропроизводительности РУ 1500 кг/с потребная площадь испарения составит 210 метров квадратных. Для РУ РБМК это задача решена размещением площади испарения в четырех горизонтальных барабанах, по два на каждую ЦП.
На реакторах РБМК-1500 используются барабаны сепараторы диаметром 2,6 м со своими ВКУ.
4.3 Водяной и пароводяной объем сепараторов.
Барабаны сепараторы внутренним диаметром 2600 мм, спроектированные ОКБ «Гидропресс» и изготовленные компанией «Энергоинвест» (СФРЮ, Сараево), установлены на всех энергоблоках Смоленской АЭС, и на 3-м 4-м энергоблоках КуАЭС.
Рисунок 4.2 — Схема потока теплоносителя На Рисунке 4.2 показаны потоки двухфазной смеси, воды и пара в БС диаметром 2600 мм. Пароводяная смесь с суммарным массовым расходом Gтк из топливных каналов подается в водяной объем БС по индивидуальным трубопроводам пароводяной коммуникаций (ПВК) от каждого ТК. При номинальной мощности реактора в каждый из БС подается смесь ПВ с расходом Gтк =7900 т/ч, который распределяется по бортам БС на две равные части. Это ПВ смесь со средним массовым паросодержанием 28% поступает в короба, которые образованы наклонными сплошными (отбойными) и перфорированные (в верхней части) стенками. Таким образом, водяной объем БС разделен на три части: отбойные короба в которых происходит первичное гашение кинетической энергии струй; межкоробовое пространство, где отделяется пар, попавший в него через наклонные дырчатые листы, а отсепарированная вода опускается к водоотводящим патрубкам. В последних установлены ВВ смесители; питательная вода, поступающая из коллектора смешивается с отсепарированной водой. Третья часть — двухфазный слой над погруженным дырчатым листом ПДЛ где идет подготовка среды к окончательному разделению фаз.
Поток паровой смеси в коробах разделяется на две части. Одна часть выбрасывается вверх ПДЛ образуя на нем динамический двухфазный слой, на верхней границе которого начинается процесс осушения пара. Другая часть двухфазной смеси попадает в межкоробовое пространство через отверстия НДЛ, предварительно смешавшись с потоком Gгз сливающимся с ПДЛ через каналы гидрозатворов. Низкая опускная скорость воды в МКП позволяет пузырям всплывать. Далее этот пар отводится вверх по «дыхательным трубам» .
Одной из важнейших характеристик БС, точнее его водяного объема, является величина уровня воды, которой начинается захват пара в опускные трубопроводы. Попадания пара в опускные трубопроводы и далее во всасывающий коллектор создает угрозу срыва подачи ГЦН и нарушения циркуляции теплоносителя. Уровень воды над ПДЛ при нулевом значении равен 150 мм может изменяться в пределах 100…200 мм. Он контролируется при заполнении контура теплоносителем и при эксплуатации уровнемерами, которые подключаются к штуцерам, расположенным в средине на концах цилиндрической части, а также на днище корпуса БС.
5. Сепараторы пара энергоблока РБМК-1500.
5.1 Конструкционные характеристики БС.
Размеры барабана — сепаратора при проектировании реакторной установки РБМК определялись под влиянием технологических и транспортных ограничений. В результате площадь «зеркала испарения» и объем воды, необходимые для каждой половины КМПЦ, были образованы двумя БС, которые связали между собой с помощью ВУТ и параперепускных трубопроводов. Эти трубопроводы приблизили характеристики пары БС к характеристике единого объема.
Корпус БС представляет собой горизонтальный цилиндрический сосуд с двумя эллиптическими днищами. В центре каждого днища имеются люки диаметром около 400 мм, закрытые самоуплотняющимися крышками. Вдоль верхней образующей цилиндрической части расположены патрубки отвода пара и для присоединения ППТ. Отвод воды из БС осуществляется снизу через 12 патрубков внутренним диаметром 29 мм, в которых размещены ВВС. Так же на нижней образующей расположены патрубки для ВУТ, шесть штук.
Для подвода пароводяной смеси на боковых поверхностях БС диаметром 2,6 м имеют четырехрядное расположение патрубков Ду 100 (попарно в шахматном порядке. У всех БС подвод питательной осуществляется через патрубок, приваренный в средней части корпуса под углом 45 градусов к вертикальной оси симметрии БС.
Таблица 1 -Основные характеристики БС РБМК-1500.
Параметр | Значение. | |
Внутренний диаметр корпуса, м. | 2,6. | |
Паровая нагрузка, т/ч. | ||
Расход ПВ смеси, т/ч. | ||
Среднее паросодержание на входе в БС, %. | 26 — 30. | |
Рабочее давление, Мпа. | 6,85. | |
Расход питательной воды. | ||
Температура питательной воды, °С. | ||
Номинальный массовый уровень над нагруженным дырчатым щитом, мм. | +200 ± 50. | |
Допустимый захват пара в опускную систему в долях расхода отсепарированной воды, масс %. | 0,4. | |
Оперативный запас воды при номинальном уровне, мі. | ||
Приведенная средняя скорость на зеркале испарения, м/с. | 0,248. | |
Длина сепаратора, м. | 33,880. | |
Число патрубков подвода пароводяной смеси. | ||
Число патрубков отвода пароводяной смеси. | ||
Число патрубков отвода воды. | ||
Внутренний диаметр патрубков отвода пара, мм. | ||
Масса сепаратора, т в сухом состоянии в рабочем состоянии. | ||
Заключение.
В ходе выполнения курсовой работы была рассмотрена и изучена тепловая схема ядерной установки РБМК 2500, входящих в нее оборудования, изучены основные принципы работы.
Таким образом:
— Рассмотрена тепловая схема, контур многократной принудительной циркуляции (КМПЦ).
— Изучены основные принципы работы оборудования КМПЦ
— Рассмотрен механизм сепарации пара.
1. Канальный ядерный энергетический реактор/Н.А, Доллежаль.
2. Сепараторы пара РБМК/О.Ю. Новосельский, В. К. Сафонов, А. В. Шишов и др.: ГУП НИКИЭТ, 2005.
3. Сепарационные устройства ядерных энергетических установок/В.Г. Крапивцев.: МГТУ им Н. Э. Баумана 2009.