Влияние лазерной модификации на эксплуатационные характеристики стали Р6М5
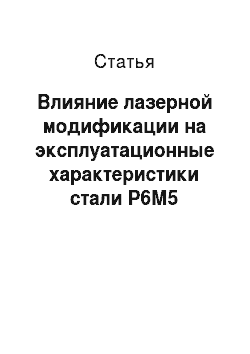
Исследования распределения остаточных напряжений, проведенные по методу Саверина М. М., на пластинчатых образцах, обработанных в соответствии с режимами таблицы, показали, что остаточные напряжения в поверхностном имеют незначительную величину. Они изменяются в диапазоне ±70МПа, рисунок 3. Их величина существенно ниже, чем в карбонитридных и карбидных слоях быстрорежущей стали Р6М5, где они… Читать ещё >
Влияние лазерной модификации на эксплуатационные характеристики стали Р6М5 (реферат, курсовая, диплом, контрольная)
УДК 620.178.4
Влияние лазерной модификации на эксплуатационные характеристики стали Р6М5
И.Н.Степанкин1, Л.С.Верещагина1, Е.П.Поздняков1,
О.Г.Девойно2, П.В.Веремей2
Учреждение образования «Гомельский государственный технический университет имени П.О.Сухого"1, г. Гомель, Беларусь Учреждение образования «Белорусский национальный технический университет"2, г. Минск, Беларусь Работа выполнена благодаря финансовой поддержке в рамках подпрограммы «Материалы в технике», задание № 4.2.02, 2014;2015 гг.
Обработка поверхностей инструментальной оснастки лазерным излучением, является одним из современных методов направленного регулирования структуры поверхностного слоя высоколегированных сталей [1, 2]. Преимущества лазерной обработки широко известны и во многом обусловлены высокой степенью локализации лазерного воздействия на модифицируемый материал. В результате нагрева с высокой скоростью, последующее охлаждение поверхности за счет теплоотвода энергии во внутренние слои металла происходит достаточно быстро. Нагрев может осуществляться с оплавлением поверхности или без него. Основной эффект обработки основан на формировании метастабильных фаз. Это приводит к приросту твердости на 3−4 единицы HRC по сравнению с максимальной твердостью, достигаемой на данной марке стали стандартными методами термообработки. В отличие от известных процессов термоупрочнения закалкой токами высокой частоты, электронагревом, закалкой из расплава и другими способами нагрев при лазерной закалке является не объемным, а локализованным поверхностным процессом. Он затрагивает весьма тонкие поверхностные слои. Однако образующаяся структура даже в слоях толщиной несколько микрометров достаточно неоднородна по структуре и свойствам. Основными структурными составляющими модифицированного слоя легированных сталей являются мелкоигольчатый мартенсит и остаточный аустенит. Присутствие остаточного аустенита оказывает неоднозначное воздействие на эксплуатационные характеристики инструмента. Во многих случаях, когда речь идет о штамповой оснастке для объемного деформирования заготовок, небольшая доля остаточного аустенита в металлической матрице ледебуритных сталей оказывает благоприятное воздействие на взаимодействие структурных составляющих, что способствует увеличению стойкости инструмента. Однако высокоэнергетическое воздействие лазерного излучения приводит к формированию модифицированных слоев, в которых за счет растворения в металлической матрице практически всех легирующих элементов аустенит становится основной и зачастую единственной фазой, которая определяет свойства поверхностного слоя детали. В этой связи, исследование влияния режимов лазерной обработки на структуру и свойства высоколегированных инструментальных сталей представляет интерес с точки зрения ресурсного проектирования технологии упрочнения оснастки. В работе представлены результаты исследования влияния параметров лазерной закалки на морфологию модифицированного слоя быстрорежущей стали Р6М5, и механизм его изнашивания в условиях контактного нагружения.
Объекты и методики исследований. Экспериментальные образцы из стали Р6М5 в качестве предварительной термообработки, подвергли закалке с температуры 1220 °C и трехкратному отпуску при температуре 550−570°С, Для полного устранения остаточного аустенита непосредственно после закалки была проведена криогенная обработка в жидком азоте. После объемной термообработки проводили поверхностную модификацию по режимам, приведенным в таблице 1.
Использовали иттербиевый лазер с длиной волны излучения 1070 нм. Мощность излучения при обработке всех экспериментальных образцов составляла 1,3 кВт. В поперечном направлении сканирование лазерного пучка с частотой 220 Гц, обеспечивало формирование зоны квазистационарного нагрева, размером 0,7Ч6 мм. Продольное перемещение по обрабатываемой поверхности образцов производилось машинным способом со скоростью от 600 до 1350 мм/мин. начальная, наиболее низкая скорость перемещения подбиралась опытным путем, с целью достижения эффекта частичного оплавления на боковой поверхности образцов для оценки распределения остаточных напряжений. Обработка всех последующих образцов производилась с постепенным ускорением для снижения степени нагрева поверхностного слоя.
Таблица — Режимы лазерной модификации экспериментальных образцов из стали Р6М5
№ партии | Режимы упрочнения | |||
Частота поперечного сканирования, Гц | Скорость продольного перемещения, мм/мин | Длина волны лазерного излучения, нм | ||
Для изучения структуры образцы подвергали шлифованию, полированию и травлению. В качестве травителя использовали 3% раствор HNO3. Исследование микроструктуры проводилось на металлографическом микроскопе МЕТАМ РВ22. Распределение микротвердости исследовалось с помощью прибора «ПМТ-3», при нагрузке на индентор 0,2 Н.
Исследование на контактное изнашивание проводили на установке для испытаний на контактную усталость и износ. Установка обеспечивает контактное нагружение торцовой поверхности плоской части образца за счет его прокатывания по рабочей поверхности дискового контртела. С целью моделирования контактного взаимодействия при трении без проскальзывания, контртело в виде диска крепится на шарикоподшипнике в державке штока, а образец с плоской рабочей поверхностью — в ячейке вращающейся планшайбы. Перемещение образца по круговой траектории при встрече с подпружиненным штоком, на котором закреплен диск контртела, вызывает его проворачивание, исключая проскальзывание на контактных поверхностях. Ширина дискового контртела и толщина рабочей части образца позволяет точно рассчитать площадь контактной поверхности, а схема нагружения реализует пульсирующее контактное нагружение по полоске. Подобный подход применяется при исследовании изнашивания материалов как в условиях качения, так и скольжения в зоне контакта.
Результаты исследований и их обсуждение. Изменение скорости лазерной обработки поверхностного слоя образцов оказывает влияние на глубину структурной модификации и распределение микротвердости в поверхностном слое. Наибольшая глубина упрочненного слоя формируется при минимальной скорости перемещения лазерного излучения по обрабатываемой поверхности. — 600 мм/мин. Структура модифицированного слоя при этом представлена тремя зонами. В первой — наружной зоне, где температура нагрева достигала максимальных значений, структура имеет выраженные признаки перегрева и, возможно, пережога. Это подтверждается наличием ледебуритной сетки по границам зерен и пористостью. В металле матрицы отсутствуют избыточные карбидные частицы, перешедшие в твердый раствор. Степень легирования материала матрицы имеет максимальное значение. Химическая активность металла снижена, при травлении в 5-ти % спиртовом растворе азотной кислоты сплав практически не приобретает структурного рисунка сохраняя светлую металлическую окраску (рисунок 2)
Второй зоной модифицированного слоя является зона неполного растворения первичных карбидных частиц. Она имеет максимальную микротвердость и также как, и наружная зона отличается пониженной химической активностью к травителю.
Переходная зона, в которой наблюдается текстурное строение карбидной фазы на фоне металлической матрицы отражает участок плавного снижения микротвердости. Максимальное значение микротвердости составляет 12 ГПа. Это значение зарегистрировано на некоторой глубине от поверхности образца в переходной зоне, рисунок 2. Непосредственно на поверхности микротвердость несколько снижена, из-за высокого содержания остаточного аустенита. Толщина модифицированного слоя превышает 1 мм. Увеличение скорости лазерной обработки до 1350 мм/мин сопровождается уменьшением толщины слоя до 0,5…0,6 мм. При этом зона с высоким содержанием остаточного аустенита, отличающаяся пониженной травимостью, составляет порядка 70−80% от общей толщины слоя, определенной по распределению микротвердости. Эта закономерность характеризует соотношение фазового контраста и распределения микротвердости во всех партиях исследованных образцов.
Исследования распределения остаточных напряжений, проведенные по методу Саверина М. М. [8], на пластинчатых образцах, обработанных в соответствии с режимами таблицы, показали, что остаточные напряжения в поверхностном имеют незначительную величину. Они изменяются в диапазоне ±70МПа, рисунок 3. Их величина существенно ниже, чем в карбонитридных и карбидных слоях быстрорежущей стали Р6М5, где они достигают 330 и 670 МПа соответственно [9, 10]. В первом случае основной причиной возникновения остаточных напряжений, является легирование металлической матрицы сплава азотом. Во втором, при имплантации азота и углерода структурные изменения затрагивают и металлическую матрицу, и карбидную фазу. При этом высокие напряжения в карбидном слое возникают, лишь при максимальной степени легирования аустенита углеродом, который впоследствии на стадии дисперсионного твердения, выделялся из материала матрицы, в виде вторичных мелкодисперсных карбидов вызывая возникновение фазовых напряжений. В обоих рассмотренных случаях основной структурной составляющей металлической матрицы является мартенсит, с незначительным присутствием остаточного аустенита в науглероженных слоях.
инструментальный лазерный поверхность легированный
Как видно из рисунка 1, структура слоя, модифицированного лазерным излучением, состоит преимущественно из аустенита. Подобное явление обусловлено высокой температурой нагрева сплава, что обеспечивает интенсивное растворение легирующих элементов в металлической матрице. Пластичность аустенита, а также его способность к динамическому старению, по видимому, являются причинами релаксации термических и фазовых напряжений в материале, обработанном высококонцентрированным источником лазерного излучения.
Отмеченные особенности, а именно отсутствие высоких остаточных напряжений и преимущественно аустенитное строение поверхностного слоя, отражаются на способности материала сопротивляться контактному изнашиванию. Как видно из рисунка 4, изнашивание экспериментальных образцов описывается монотонно возрастающими кривыми, на которых отмечается участок приработки, с увеличенной интенсивностью износа и последующая стадия замедленного разрушения поверхностного слоя.
Рисунок 4 — Кривые контактного износа образцов из стали Р6М5 с поверхностным слоем модифицированным лазерным излучением: ¦ - 1 партия, ¦ - 2 партия, ^ -3 партия, ?- 14 партия,? — 15 партия, Д — 16 партия Характер разрушения контактной поверхности на начальной стадии испытания образцов, отличается появлением подповерхностных трещин, которые возникают вследствие микропластических деформаций под действием касательных напряжений (рисунок 5). Как отмечается в работах [11, 12], максимальные по величине касательные напряжения, возникающие на глубине 0,3…0,5 мм, создают условия для увеличения напряжений вблизи структурных концентраторов напряжений. Как видно из рисунка 5, зарождение микротрещин происходит на глубине 0,1…0,2 мм, несколько ближе зоны концентрации максимальных касательных напряжений. Локальными концентраторами напряжений служат границы крупных зерен. Вследствие перегрева и окисления они являются наименее прочной фазой материала. Распространение трещин по границам зерен, вызывает их выкрашивание и образование достаточно внутренних полостей. Подобный механизм разрушения подповерхностного слоя металла, не зависит от наличия в сплаве избыточных фаз, и может реализоваться в однородном материале [12, 13].
а
б
Ч300 Ч1500
Рисунок 5 — Повреждения рабочей поверхности образцов партии 1 после 200 циклов приложения контактного напряжения 1300
Изнашивание контактной поверхности образца происходит по классическому механизму, сочетающему углубление трещинообразного дефекта и его выход на поверхность. В большинстве исследованных случаев отмечено расположение начального дефекта под углом 45 градусов к контактной поверхности материала. Отличительной особенностью разрушения поверхностного слоя упрочненного посредством лазерной гомогенизации является распространение первичных дефектов параллельно контактной поверхности, несмотря на то, что некоторые участки границ зерен, безусловно, располагаются под углом близким к 45 градусам к контактной поверхности. Высокая хрупкость межзеренных границ определяет индивидуальный механизм распространения трещин контактной усталости. Выявленные морфологические признаки отражают механизм усталостного разрушения, в условиях развития межкристаллитной коррозии [15], что является очевидным для наружного слоя сплава, который имеет признаки перегрева в виде оплавленных границ зерен.
а
б
Рисунок 6 — Характер повреждений в области дна лунки износа образцов 1-й партии после17 200 (а) 18 280 (б) циклов приложения контактного напряжения 1300 МПа (Ч50)
После стадии приработки механизм разрушения поверхностного слоя характеризуется формированием полукруглых трещин, которые охватывают зону пластической деформации в окрестности полоски контакта. Как видно из рисунков 6 а и 7, внутри контура трещины контактной усталости текстурное строение сплава изменяется. Расположение карбидных включений характеризуется эквидистантным расположением строчек включений по отношению к линии трещины. За пределами контура металла, структурные изменения выражены в меньшей степени.
Момент отделения упрочненного фрагмента металла на кривых износа отражается ступенчатым приростом. После чего начинается наклеп более глубоких слоев металла, рисунок 6 б.
Рисунок 7 — Структурные изменения в области распространения трещины контактной усталости в образцах 1-й партии после 17 200 циклов нагружения контактным напряжением 1300 МПа (Ч250)
Изнашивание образцов других партий, несмотря на различия в толщинах модифицированных слоев, не имеет существенных отличий. Во всех случаях формирование питтингов происходит, как правило, в результате зарождения и роста одной трещины. Эта особенность присуща процессу контактного изнашивания, протекающему без скольжения. Данное требование при испытании образцов реализовано с целью приближения испытаний к эксплуатационным условиям работы штамповой оснастки на операциях холодной высадки и чеканки прецизионных поковок. Интенсивность износа всех партий образцов, имеющих толщину модифицированного слоя от 0,7 до 1,2 мм, отражается схожими зависимостями.
Выводы Лазерная обработка, проведенная в качестве финишной операции термического упрочнения быстрорежущей стали Р6М5, позволяет существенно изменить структуру и свойства сплава. За счет высокоэнергетического воздействия поверхность модифицированного слоя приобретает аустенитную структуру, с признаками перегрева. Изменение толщины слоя в сторону уменьшения, При снижении интенсивности нагрева поверхности позволяют избавиться от структурных дефектов в виде оплавленных границ зерен и сохранить на поверхности тонкую аустенитизированную прослойку сплава.
Износ модифицированных слоев описывается монотонно возрастающими зависимостями. На первом этапе изнашивания, в процессе приработки, трещины контактной усталости зарождаются в области межзеренных границ, которые сформированы ледебуритной сеткой в результате перегрева наружного поверхности модифицированного слоя. Уменьшение толщины модифицированного слоя и устранение признаков перегрева наружной прослойки практически не изменяют скорости и механизма контактного изнашивания. Во всех исследованных случаях этапу разрушения очага контактной нагрузки предшествуют структурные изменения в поверхностном слое металла. Они заключаются в изменении ориентации скоплений карбидных включений в очаге действия максимальных касательных напряжений. Полученные зависимости контактного изнашивания показывают, что глубокая модификация поверхностного слоя быстрорежущей стали Р6М5 не оказывает существенного влияния на изменение скорости контактного изнашивания по сравнению с более тонкими слоями. Данный результат позволяет прогнозировать ресурс контактной выносливости большого числа деталей инструментальной оснастки не предъявляя высоких требований к условиям автозакалки поверхностного слоя, которые зависят не только от режимов лазерной обработки, но и массивности деталей.
1. Григорьянц, А. Г. Основы Лазерной обработки / А. Г. Григорьянц. М.: Машиностроение, 1989. — 300 с.
2. Упрочнение деталей лучем лазера / В. С. Коваленко [и др.]; под ред. В. С. Коваленко. — Киев: Техника, 1981. — 131 с.
3. Бровер, А. В. Особенности лазерной упрочняющей обработки деталей машин и инструмента / А. В. Бровер // Упрочняющие технологии и покрытия. 2008. № 6. С.12−16.
4. Костюк, Г. И. Лазерное упрочнение легированных сталей / Г. И. Костюк, Н. В. Руденко // Авиационно-космическая техника и технология. 2012. № 2 (89). С.23−27.
5. Степанкин, И. Н. Стойкость холодновысадочной оснастки и методы её повешения / И. Н. Степанкин, В. М. Кенько. Гомель.: УО «ГГТУ им. П.О.Сухого», 2014. — 197 с.
6. Пат. Республ. Беларусь на полезную модель № 8260 МПК (2009) G 01 N 3/00 Устройство испытания материалов на контактную усталость и износ / И. Н. Степанкин, Е. П. Поздняков, В. М. Кенько, И. А. Панкратов, Л. В. Степанкина; заявитель Гомельск. гос. техн. ун-т им. П. О. Сухого. — № u20110940, заявл. 23.11.2011. опубл. // Афiцыйны бюлетэнь / Нац. цэнтр iнтэлектуал. уласнасцi. — 2012. — № 3. — С. 260.
7. Beheshti, Ali On the prediction of fatigue crack initiation in rolling/sliding contacts with provision for loading sequence effect / Ali Beheshti, M.M.Khonsari // Tribology International. 2011. vol. 44. p. 1620−1628.
8. Саверин, М. М. Дробеструйный наклеп // М. М. Саверин.- М.: Машгиз, 1955. 312 с.
9. Степанкин, И. Н. Учет свойств диффузионно-упрочненных карбонитридных слоев при проектировании тяжелонагруженной технологической оснастки из инструментальных сталей ледебуритного класса / И. Н. Степанкин // Кузнечно-штамповочное производство.- 2012. № 4. C.24−28.
10. Степанкин, И. Н. Влияние науглероживания и температуры закалки на стойкость штампового инструмента из стали Р6М5 / И. Н. Степанкин, В. М. Кенько, А. А. Бойко // Металловедение и термическая обработка металлов. 2013. № 3. С.19−23.
11. Рыжов, Н. М. Технологическое обеспечение сопротивления контактной усталости цементуемых зубчатых колес из теплостойких сталей / Н. М. Рыжов // Металловедение и термическая обработка металлов. 2010. № 7. С.39−45.
12. Nelias, D Role of inclusions, surface roughness and operating conditions on rolling contact fatigue / D. Nelias, M.L. Dumont, F. Champiot, A. Vincent, D. Girodin. // Journal of Tribology, ASME. 1999. V.121(2). Р.240−251.
13. Chen, L. Study on initiation and propagation angles of subsurface cracks in GCr15 bearing steel under rollingcontact / L. Chen, Q. Chen, E. Shao. // Wear. 1989. V.133(2). P.205−218.
14. Glodez, S. Evaluation of the service life of gears in regard to surface pitting / S. Glodez, B. Abersek, J. Flasker, Z. Ren. // Engineering Fracture Mechanics. 2004. V.71. P. 429−438.
15. Raje, N. A discrete damage mechanics model for high cycle fatigue in polycrystalline materials subject to rolling contact / N. Raje, T. Slack, F. Sadeghi // International Journal of Fatigue. 2009. V.31(2). P.346−360,.
16. Alfredsson, B. A Study on Contact Fatigue Mechanisms: Doctoral Thesis no. 44, 2000 / Alfredsson Bo. Department of Solid Mechanics Royal Institute of Technology, Stockholm, 2000. 27 р.
Аннотация В работе исследовано влияние лазерной обработки поверхностного слоя быстрорежущей стали Р6М5 на характер и интенсивность её контактного изнашивания. Показано, что механизм износа поверхностного слоя состоит из двух фаз. На первой происходит накопления внутренних повреждений, сопровождающееся деструктуризацией металла в области полоски контакта и зарождение преимущественно межкристаллитных микротрещин. На втором этапе в результате распространения трещины контактной усталости поверхностный слой, претерпевший наклеп отделяется от основного материала. Полученные зависимости контактного изнашивания показывают, что глубокая модификация поверхностного слоя быстрорежущей стали Р6М5 не оказывает существенного влияния на изменение скорости контактного изнашивания по сравнению с более тонкими слоями.