Горячая объемная штамповка металлов
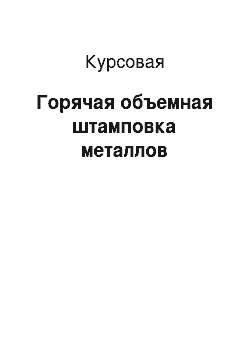
Выбор схемы штамповки и проектирование штампового инструмента, наиболее упрощенного по внешней геометрии, но максимально приближенного по форме внутренней гравюры к получаемой штампованной поковке. При этом должны быть учтены вид используемого деформирующего оборудования, конструкция штамповой оснастки и штампового блока. Важными дополнительными факторами являются условия свободного извлечения… Читать ещё >
Горячая объемная штамповка металлов (реферат, курсовая, диплом, контрольная)
Введение
В производстве металлообрабатывающей промышленности, использующих в качестве материалов алюминиевые сплавы, применяют различные заготовки полученные методом литья, ковки и штамповки. Сплавы на основе алюминия получают все более широкое применение благодаря своим технико-эксплуатационным, эргономическим и экономическим свойствам: высокой удельной плотности, коррозионной стойкости, теплопроводности и т. п., способности воспринимать отделочную обработку, покрытия, а так же — рециркуляции (утилизации и повторному использованию).
В условиях рыночной экономики важную роль приобретают время внедрения изделия в производство и его эффективность. Сокращение времени и материальных затраты на производство проектируемых объектов и повышение их качества достигается применением систем автоматизированного проектирования (САПР). Основным преимуществом САПР является идея «виртуального производства», согласно которой с помощью специализированного программного обеспечения осуществляется моделирование полного цикла изготовления изделия, включая выполнение комплекта чертежной документации, разработку трехмерной модели поковки, проектирование технологии изготовления и моделирование самого процесса изготовления (штамповки).
Представленные на рынке программные продукты, такие как FORGE 3 (Франция), DEFORM 3D (США), SuperForge (США), QFORM3D (Россия), используют метод конечных элементов. Функционирование этих систем требует наличия внешних средств трехмерного моделирования для формирования геометрии штамповочного инструмента и разработки технологии штамповки, что затрудняет внесение изменений в технологический процесс в случае выявления дефектов.
Оценка разработанной технологии и выявление возможных дефектов (зажимов, прострелов, незаполнения профиля и др.) позволяет уже на этапе проектирования технологии уменьшить вероятность серьезной корректировки разработанного технологического процесса и изготовления нескольких комплектов оснастки для проведения опытной штамповки, что дает возможность сократить время технологической подготовки производства, и расходы на внедрение технологии в производство.
Кроме того, существующие программы лишь частично охватывают процесс проектирования и не полностью реализуют открывающиеся при использовании вычислительной техники возможности. Даже если совместить на одном рабочем месте технолога программные системы, отвечающие за трехмерное геометрической моделирование, автоматизированную разработку технологического процесса и моделирование пластического формоизменения, каждая из которых имеет достаточно высокую стоимость, остаются нерешенными несколько важных задач, таких как автоматизированное конструирование поковок по чертежам или моделям деталей и оптимизация технологического процесса.
1 Методы моделирования обработки металлов давлением объемный штамповка металл В последние годы все больше внимания уделяется моделированию различных технологических процессов, в том числе и процессам обработки металлов давлением. Это объясняется тем, что мы живем в условиях рыночной экономики, и основная задача производства заключается в получении максимальной прибыли с минимальным затратами, а одними из многочисленных пунктов затрат являются опробование новой продукции, запуск нового оборудования и т. д.
Исследования и эксперименты в реальном производстве имеют свои недостатки:
— большие энергозатраты и риск получения некачественной продукции, которую скорее всего придется отдавать в переплав;
— невозможность изменения параметров процесса в широких диапазонах;
— вероятность аварии и поломки оборудования.
Поэтому совершенствование технологических процессов обработки металла давлением (ОМД), а также получение новых видов продукции ОМД требует дополнительных затрат.
Прогресс не стоит на месте, и многое сегодня может быть решено с помощью моделирования, преимущество которого состоит в том, что, прежде чем осуществлять опыты в условиях производства и тратить драгоценное время и сырье, эксперименты изначально проводят либо на лабораторном оборудовании, либо на компьютерах.
Была предложена следующая классификация методов моделирования для ОМД:
— математическое моделирование с помощью метода конечных элементов (МКЭ).
— физическое моделирование с применением пластометов;
— физическое моделирование с применением теорем подобия;
— статистические модели;
— моделирование с помощью нейросетей;
— аналоговое моделировании;
— аналитическое моделирование;
— графическое моделирование;
— численное Математическое моделирование осуществляется с помощью метода конечных элементов (МКЭ).
Метод основан на решении дифференциальных уравнений. Исследуемые области, например, деформируемое тело и элементы штампа разбиваются на конечное количество элементов (потому и метод так называется), составляется и решается система уравнений, где количество уравнений равно количеству неизвестных значений в узлах (на границах элементов). Значения функций на границах элементов — это и есть решение задачи. Более подробно о методе можно узнать из работ [1−8], а в части его применения к моделированию ОМД — из работы.
Широкое применение этого метода связано с ростом производительности компьютеров (см. рис. ниже). Понятно, что такую систему уравнений решить без вычислительной техники просто нереально, и даже сегодня решение некоторых задач может занять несколько суток даже при производительности работы компьютера несколько миллионов операций в секунду.
МКЭ позволяет решать такие задачи, как:
— моделирование течения металла внутри оснастки (при экструзии) или между матрицей и пуансоном (при штамповке) и т. п.
— позволяет установить распределение деформаций и температур по сечению.
Рис. 1. Эволюция компьютерной техники за последние двадцать лет В табл. 1 приведен список программного обеспечения, которое позволяет осуществлять расчеты с применением МКЭ.
Таблица 1. — Компьютерные программы и их разработчики
Программа | Разработчик | |
QForm | «КванторФорм» | |
Deform | Scientific Forming Technologies Corporation | |
AutoForm | Metal Forming Systems, Inc | |
AutoForm | AutoForm | |
Ansys | ANSYS, Inc | |
LS-Dyna | Livermore Software Technology Corporation (LSTC) | |
Forge | Transvalor | |
SuperForge | Superforge | |
Результат решения выводится в виде картинки, на которой цветами размечены различные области с разной деформацией или температурой:
Для моделирования в программу необходимо ввести реологические свойства материала:
кривые его пластического течения при различных температурах и скоростях деформации;
физические характеристики материала, такие как теплопроводность, температуропроводность, плотность и т. д.;
для стали — критические точки превращения при различных скоростях охлаждения (термокинетические диаграммы).
Рис. 2. Результат моделирования процесса получения клапана. Цвет показывает распределение деформации.
В качестве примера результат моделирования штамповки коленчатого вала в программе QForm:
а б Рис. 3. Поковка коленчатого вала:
а — фотография; б — модель При физическом моделировании с применением пластометров испытания проводят на специальных образцах и в особых условиях деформирования (температура, степень деформации, скорость деформации, скорости охлаждения и нагрева), используя испытаний различные схемы нагружения: сжатие, растяжение, кручение.
Результатом таких испытаний и будет серия кривых «напряжение-деформация» при различных скоростях и температурах деформации:
Рис. 4. Кривые «напряжение-деформация» [10]
Полученные кривые загружают в компьютерную программу, работающую по алгоритму МКЭ.
Получение таких кривых далеко не единственная цель. Обычно после получения кривых проводят другую серию таких же испытаний. Отличие новой серии заключается в том, что процесс прерывают по достижении определенной степени деформации, затем образцы закаляют, чтобы зафиксировать полученную микроструктуру. Такую процедуру выполняют на разных образцах (рис.5).
Рис. 5. Проведение эксперимента для изучения эволюции микроструктуры Таким образом при испытании каждого нового образца процессу позволяют идти чуть дальше, чем в предыдущем. Далее изучают микроструктуру образцов на каждом этапе деформации. Таким образом, перед глазами исследователя открывается картина эволюции микроструктуры по ходу деформации (рис. 6).
Рис. 6. Эволюция микроструктуры После обработки результатов всех опытов строят модели, которые позволяют предсказывать:
— микроструктуру конкретной стали или сплава при различных условиях деформации;
— ход самой кривой «напряжение-деформация» при любых сочетаниях параметров деформирования.
Это очень полезно, т.к. можно провести всего несколько опытов, а потом на их основе получить одно уравнение, которое описывает широкий диапазон изменения параметров.
Физическое моделирование с применением теорем подобия.
Основное положение, на котором основывается применение данного метода, состоит в том, что процессы в природе протекают одинаково в подобных системах независимо от их размера. Всего таких положения три, и называются они теоремы подобия.
Испытания проводят на миниобразцах исследуемого материала с геометрически подобными размерами. Например, при моделировании прокатки, если размеры сляба составляют 2,5×1,5×0,25 м, то уменьшенная копия будет бруском 250×150×25 мм.
Как и везде, здесь есть свои нюансы. Самый простой и легко бросающийся в глаза — маленький брусок остынет быстрее, чем большой. Более подробно о методе и его применении можно узнать из работы.
Часто такие эксперименты осуществляются с привлечением планирования эксперимента, одной из целей которого является уменьшение числа опытов без существенной потери информативности. Этому посвящены работы [12, 13]. А вот при обработке результатов такого планируемого эксперимента прибегают к статистическим методам. Так что данный вид моделирования тесно связан со следующим.
Статистические модели, можно разделить эти модели на две группы:
Модели, которые получены из запланированного или активного эксперимента.
То есть проводящий эксперимент сам влияет на параметры. На выходе исследователь получает формулы, например, зависимости временного сопротивления разрыву от параметров обработки металлов давлением, как это сделано в работе.
Модели, основанные на обработке большого массива данных, например, производственных.
Здесь исследователь имеет в своем распоряжении массив чисел и ему остается должным образом обработать этот массив и получить зависимости, например, установить влияние параметров прокатки на механические свойства.
Модели с использованием нейросетей — такие модели, которые построены по принципу нервной системы живых существ и представляют собой сеть соединённых и взаимодействующих между собой простых элементов (нейронов) (рис. 7).
Рис. 7. Схема модели нейросетей Аналоговое моделирование заключается в создании предметного образа процесса, системы или изменения каких-либо параметров, схожих по форме с реальным объектом. Это один из важнейших видов моделирования, основанный на аналогии (в более точных терминах — изоморфизме) явлений, имеющих различную физическую природу, но описываемых одинаковыми математическими (дифференциальными, алгебраическими или другими) уравнениями.
Аналоговое моделирование было основным способом «предметно-математического моделирования» многих процессов (распространение электромагнитных и звуковых волн, диффузия газов и жидкостей, кручение стержней и др.), поэтому его часто называли просто математическим моделированием. Причём для каждой конкретной задачи моделирования строилась своя модель, основными элементами которой служили соединённые в плоскую сеточную схему электрические сопротивления различных видов. Аналоговые вычислительные машины позволяли проводить моделирование целых классов однородных задач. В настоящее время значение аналогового моделирования значительно уменьшилось, заменяется компьютерным моделирование, которое имеет по сравнению с ним большие преимущества в отношении точности и универсальности. При этом для решения ряда специальных задачах оно имеет свои преимущества с точки зрения простоты и дешевизны технического выполнения. Применяется также и совместное использование методов аналогового и компьютерного моделирования.
При аналитическом моделировании процессы функционирования элементов системы записываются в виде математических соотношений (алгебраических и т. д.). Аналитическую модель можно исследовать следующими методами:
— аналитическим (получают в основном точные решения);
— численным (получают приближенные решения);
— качественным (в явном виде можно найти только некоторые свойства решения).
Ход решения задач ОМД наиболее наглядно отображают геометрические модели. Графическая интерпретация помогает проанализировать качественную картину исследуемого процесса, в тех случаях, когда не удается получить количественную оценку тех или иных параметров, что в немалой степени способствует выработке конкретных рекомендаций по улучшению технологии производства изделий либо улучшению конструкции инструмента. Кроме того, ввиду сложности формализация некоторых задач ОМД графический способ является единственным для их решения.
В работе рассматриваются графические построении, позволяющие легко получить расположение линий раздела течения металла на плоскости контакта.
Графическое моделирование в последние годы интенсивно развивается, благодаря совершенствованию компьютерной базы. В частности, задачу описания пластического течения тонкого слоя металла по жестким поверхностям, наблюдаемого в процессах ОМД, можно свести к чисто геометрической за счет упрощения математической модели. В этом случае есть возможность, как показано в работе [16], получить полный алгоритм для решения задачи формообразования штампованных поковок и реализовать его на компьютере. Разработанный алгоритм позволяет до конца решить задачу лишь для узкого класса контуров штампуемых поковок.
Много внимания вопросам графического моделирования уделено в работах А. И. Петрова. Так, в работе показана последовательность при разработке алгоритма проектирования технологии прессования профилей: предложены алгоритмы проектирования калибровок, рассмотрены вопросы анализа и кодирования чертежа профиля, а также изложены методы и последовательность разработки алгоритма автоматизированного проектирования технологических процессов. В работе описывается проектный модуль автоматического построения «скелета контура», который является эквидистантой для контура детали, т. е. геометрическим местом точек, равноудаленных от контура детали. В работе рассмотрено создание комплексной методики проектирования технологических процессов многопереходной объемной горячей объемной штамповки заготовок для деталей пространственной формы, включающей в себя: методику геометрического моделирования; проектирование геометрии заготовок по переходам штамповки с учетом технологических характеристик процессов; конструирование штампового инструмента.
Работа посвящена геометрическому моделированию процесса формообразования технологических оболочек при их поверхностном пластическом деформировании.
В последнее время при разработке технологических процессов обработки металлов давлением применяются компьютерные технологии. Компьютерное моделирование — это математическое моделирование, которое формулируется в виде алгоритма (программы для ПК), что позволяет проводить вычислительные эксперименты. В свою очередь, компьютерное моделирование делится на численное, статистическое и имитационное.
Численное моделирование предусматривает использование методов вычислительной математики (отличается от аналитического возможностью задания различных параметров модели).
Статистическое моделирование представляет собой обработку данных о системе (модели) в целях получения статистических характеристик системы.
При имитационном моделировании осуществляется воспроизведение (имитация) на компьютере процесса функционирования исследуемой системы при соблюдении логической и временной последовательностей протекания процессов, что позволяет получить данные о состоянии системы или ее отдельных элементов в определенные моменты времени.
Необходимо отметить, что классификация методов моделирования носит достаточно условный характер, поскольку при исследовании и описании того или иного процесса сегодня используются сразу несколько видов моделирования в сочетании с компьютерным.
2 Компьютерные программа, применяемые для разработки конструкторской документации и моделирования процессов ОМД Основой компьютерного моделирования в ОМД служит использование современного программного обеспечения. Для конструкторской разработки моделей технологических процессов и формирования чертежей используются следующие системы объемного проектирования: Pro/Engineer, Solid Edge, SolidWorks, «Компас 3D», AutoCAD, ZWCAD и др.
При этом непосредственно для моделирования процессов ОМД и прогнозирования поведения металла под действием деформирующих нагрузок и условий деформирования все шире распространяются специализированные программные комплексы, например, QFORM, Forge 3, DEFORM, ANSYS, PAM-STAMP, AutoForm и др.
Основными причинами создания и активного использования в ОМД этих компьютерных программ являются:
— необходимость сокращения сроков разработки технологических процессов, времени проектирования штамповок, ковочной и штамповочной оснастки и проведения опытных работ при внедрении процессов в производство;
— обязательное снижение цены ошибочных технологических и проектных решений до начала промышленных экспериментов, повышение надежности разрабатываемых технических мероприятий, в том числе технологических процессов ОМД;
— активное развитие компьютерной техники и технологии с одновременным курсом системы образования на подготовку пользователей персональными компьютерами делает допустимым привлечение программного моделирования процессов ОМД для предприятий и организаций различного уровня.
Применение современных систем САD/САМ дает возможность достичь значительной оптимизации процессов конструирования.
Для конструкторской разработки моделей технологических процессов и формирования чертежей используются следующие системы объемного проектирования:
SolidWorks — программный комплекс САПР для автоматизации работ промышленного предприятия на этапах конструкторской и технологической подготовки производства, который обеспечивает разработку изделий любой степени сложности и назначения и работает в среде Microsoft Windows. Программа появилась в 1993 году и составила конкуренцию таким продуктам, как AutoCAD и Autodesk Mechanical Desktop, SDRC I-DEAS и Pro/ENGINEER.
AutoCAD — двухи трёхмерная система автоматизированного проектирования и черчения, разработанная компанией Autodesk. Первая версия системы была выпущена в 1982 году. AutoCAD и специализированные приложения на его основе нашли широкое применение в машиностроении, строительстве, архитектуре и других отраслях промышленности.
Текущая версия программы (AutoCAD 2014) включает в себя полный набор инструментов для комплексного трёхмерного моделирования (поддерживается твердотельное, поверхностное и полигональное моделирование). AutoCAD позволяет получить высококачественную визуализацию моделей с помощью системы рендеринга mental ray. Также в программе реализовано управление трёхмерной печатью (результат моделирования можно отправить на 3D-принтер) и поддержка облаков точек (позволяет работать с результатами 3D-сканирования). Тем не менее, следует отметить, что отсутствие трёхмерной параметризации не позволяет AutoCAD напрямую конкурировать с машиностроительными САПР среднего класса, такими как Inventor, SolidWorks и другими. В состав AutoCAD 2012 включена программа Inventor Fusion, реализующая технологию прямого моделирования.
ANSYS — универсальная программная система конечно-элементного (МКЭ) анализа, существующая и развивающаяся на протяжении последних 30 лет, является довольно популярной у специалистов в сфере автоматических инженерных расчётов (CAE, Computer-Aided Engineering) и КЭ решения линейных и нелинейных, стационарных и нестационарных пространственных задач механики деформируемого твёрдого тела и механики конструкций (включая нестационарные геометрически и физически нелинейные задачи контактного взаимодействия элементов конструкций), задач механики жидкости и газа, теплопередачи и теплообмена, электродинамики, акустики, а также механики связанных полей.
В США компанией Scientific Forming Technologies Corporation (SFTC) разработан специализированный инженерный программный комплекс DEFORM, предназначенный для анализа процессов обработки металлов давлением, термической и механической обработки, который позволяет проверить, отработать и оптимизировать технологические процессы непосредственно за компьютером, а не в ходе экспериментов на производстве методом проб и ошибок. Благодаря этому существенно сокращаются сроки выпуска продукции, повышается ее качество и снижается себестоимость.
Unigraphics NX — это лидирующая CAD/CAM/CAE система, построенная на лучших технологиях, предназначенных для создания изделий любой сложности. Основная задача системы в конечном итоге состоит в сокращении стоимости создания изделия, улучшения его качества и сокращении сроков выхода на рынок. Это дает возможность компаниям в короткий срок вернуть инвестиции, затраченные на покупку и внедрение Unigraphics. В России Unigraphics занимает прочные позиции, благодаря широким возможностям использования системы в различных областях промышленности (авиакосмическая промышленность, двигателестроение, автомобилестроение, машиностроение и т. д.) и применению современных технологий, обеспечивающих пользователя передовыми решениями в области MCAD на всех этапах создания изделия. Успех системы Unigraphics на российском рынке подтвержден обширной базой пользователей, успехами, достигнутыми ими в результате использования системы. Немаловажным преимуществом системы является то, что она является единственной CAD/CAM/CAE системой верхнего уровня на рынке, которая имеет русский интерфейс и документацию на русском языке. Компания UGS предлагает услуги по внедрению и консалтингу системы Unigraphics, что позволяет компаниям в России успешно внедрять систему и получать реальные выгоды от ее использования.
В России разработана и совершенствуются программа QForm.
QForm 7- это новый программный продукт, отвечающий самым современным требованиям в области моделирования процессов обработки металлов давлением. При создании новой версии был использован 20 летний опыт разработки программы, а так же были учтены современные требования и тенденции развития рынка. В результате новая программа собрала в себе самые прогрессивные методики моделирования, стала более удобной и приобрела гибкость, необходимую для дальнейшего развития современного программного обеспечения.
Программа приобрела новую архитектурную, структуру данных и интерфейс. Изменения позволили значительно расширить круг решаемых задач и сделать работу программы быстрее и проще.
Интерфейсная часть и расчетное ядро программы работают не зависимо. Обмен информацией между ними осуществляется с помощью файлов, в которых хранятся исходные данные и результаты моделирования.
Новая структура данных была разработана специально для управления большими массивами данных, которые характерны для моделирования методом конечных элементов. Теперь доступ к данным стал более быстрым и удобным, при этом записываются уже все шаги моделирования, а расчет большого количества дополнительных параметров осуществляется в режиме постпроцессора после окончания моделирования. Просмотр результатов стал на много быстрей и может быть осуществлен прямо во время расчета. Мастер подготовки исходных данных и редактор исходных данных имеют удобный доступ к базе данных QForm. Управление данными и просмотр результатов отделены от расчетного ядра программы. Это позволяет эффективнее использовать оперативную память компьютера, а просмотр всех результатов возможен прямо во время расчета. Расчет лангранжевых линий, трассируемых точек и других дополнительных функций осуществляется в постпроцессоре. Постпроцессор также позволяет рассчитывать некоторые функции, заданные пользователем, и обеспечивает экспорт результатов в другие программы.
2D и 3D — модели полностью объединены и теперь используют общий интерфейс, в котором возможно использовать одни и те же команды. Это значит, что обе модели имеют одинаковые возможности за исключением тех специфических возможностей, которые используются только для 2D или только для 3D — моделирования.
Новые расширенные возможности моделирования:
— связанная тепловая задача заготовки и инструментами;
— связанная механическая задача вязко-пластической заготовки с упругопластическими инструментами;
— моделирование нескольких деформируемых заготовок;
— моделирование составных 3D инструментов, предварительно напряженный инструмент;
— упруго — пластическая деформация заготовок, остаточные напряжения в заготовке;
— отсечение 3D произвольной поверхности штамповки (поковки), соответствующее механической обработке для удаления кузнечных припусков или обточке.
Новые типы оборудования:
— силовой прижим;
— пружинный прижим;
— инструмент с двумя осями вращения;
— переменное гидростатическое давление для расчета гидроштамповкм.
Расширенные методы моделирования:
— явная и неявная схемы интегрирования по времени;
— новый метод генерации конечно — элементной сетки.
3 Общая характеристика и особенности технологии и принципы моделирования процессов горячей объемной штамповки Для изготовления штампованных поковок заготовки могут быть литые, цилиндрические или плоские и предварительно деформированные прессованием, прокаткой или ковкой. Прессованные заготовки могут быть в виде полосы, профиля (круглой, прямоугольной или более сложной формы) и т. п., катаные — в виде плиты, полосы и т. п., кованые — в виде шайб, прямоугольных или фасонных поковок и т. п.
Исходную заготовку под штамповку выбирают в зависимости от формы штампованной заготовки, условий эксплуатации изготавливаемой из нее детали и имеющегося оборудования.
Для объемной штамповки заготовок под изделия ответственного назначения, как правило, применяют исходные заготовки, предварительно деформированные прессованием, прокаткой или ковкой.
Для получения мерных заготовок используют различные способы раскроя металла. Резку на мерные заготовки в зависимости от марки сплава и исходных размеров заготовок производят на ленточных или дисковых пилах, отрезных станках, пресс-ножницах. В отдельных случаях для резки используют плазменные установки.
Резку на дисковых пилах или отрезных станках выполняют со смазочно-охлаждающими веществами. Все виды заготовок, поступающие на нагрев и последующую ковку или штамповку, очищают от смазки, грязи, примесей стружки или опилок и удаляют заусенцы. На мерных заготовках в отдельных случаях заусенцы не удаляют, если они вместе с избытком металла в процессе штамповки выходят в облой.
Рекомендуемый температурный интервал штамповки заготовок из алюминиевых сплавов приведен в.
В случае нагрева металла до предельно допустимых температур его следует охладить до температуры начала деформации и далее обрабатывать в обычном порядке. Металл, нагретый выше предельно допустимых температур, дальнейшей обработке не подлежит.
Особенность нагрева заготовок из алюминиевых сплавов для штамповки заключается в необходимости точного соблюдения соответствующих температур. Ввиду этого нагрев заготовок производят только в электронагревательных устройствах, обеспечивающих высокую точность температуры нагрева.
Максимальное время нагрева заготовок под ковку и штамповку приведено в таблице 8.
Таблица 8. — Время нагрева алюминиевых заготовок перед ковкой и штамповкой
Штамповки; деформированные заготовки под штамповку | Деформированные заготовки для поковок | Литые заготовки для штамповок и поковок | |
— не более 10 часов при первом нагреве; — не более 8 часов при повторных нагревах, если температура нагрева заготовок не превышала 4200С; — не более 4 часов, если температура нагрева заготовок выше 4200С. | не более 14 часов | не ограничено | |
Допускаемая степень деформации литых и предварительно деформированных заготовок приведена в.
Штамповку алюминиевых сплавов обычно ведут на гидравлических вертикальных штамповочных прессах, которые отличаются возможностью создания высоких усилий и неударным характером работы, так как скорость рабочего хода подвижной траверсы составляет 0,01 — 0,15 м/с. Особенностью гидравлических прессов является увеличенный рабочий ход траверсы, наличие выталкивателя и выдвижного стола.
На гидравлических штамповочных прессах изготавливают разнообразные штампованные заготовки. В связи с потребностью различных отраслей машиностроения в крупногабаритных деталях широкое распространение в металлургической промышленности получили технологические процессы изготовления крупногабаритных штампованных заготовок, в том числе плоскостных оребренных сложноконтурных деталей типа панелей, нервюр, лонжеронов, корпусов агрегатов в виде цилиндров с фланцами, отростками и т. п.
Как правило, на гидравлических прессах штампованные заготовки изготавливают в несколько операций. При изготовлении сложных заготовок в зависимости от их формы, размеров и требований к структуре металла широко применяют такие заготовительные операции, как ковка, вальцовка, набор и перераспределение части металла посредством высадки или выпрессовки и т. п., а также формоизменение в заготовительных и окончательных штампах.
При штамповке широких сложноконтурных деталей, имеющих различные по объему металла поперечные сечения, необходимо добиваться перераспределения металла не только по длине, но и по ширине. Единственным способом перераспределения металла в таких случаях является формоизменение в штампах, что при мелкосерийном производстве вызывает дополнительные трудности.
При формообразовании штампованных заготовок, имеющих различную толщину поперечных сечений, обеспечить во всех сечениях одну и ту же степень деформации практически невозможно. В результате на всех штампованных заготовках сложной формы с большим перепадом по сечениям есть участки, где степень деформации значительно больше средней. Вследствие этого имеет место увеличенный выход металла в облой, при этом возрастает неравномерность деформированного состояния, что, в конечном итоге, сказывается на качестве полуфабриката. С целью снижения неравномерности деформаций на штампованных заготовках на каждом переходе целесообразно избегать высоких степеней деформации.
Большую часть избыточного металла надо стремиться удалять в облой на переходах, при которых сечения которых имеют наиболее простую форму (круг, прямоугольник или близкую к ним) Удаление избытка металла на первых стадиях процесса формообразования всегда оправдано, даже если на сложных переходах не образуются дефекты в виде зажимов или прострелов. При этом следует иметь в виду, что формообразование волокон в зоне очага деформации должно быть как можно менее резким и большие избытки металла должны удаляться с минимальным сопротивлением его течению в облой. Так, увеличение числа переходов в формовочном ручье, вместо заготовительного, позволяет резко улучшить качество макроструктуры и получить оптимальное расположение волокон.
Известно, что при проектировании предварительных и окончательных штампов занижают высоту ребер и увеличивают радиусы таким образом, чтобы площади соответствующих поперечных сечений ручьев предварительного и окончательного штампов были одинаковы. Кроме того, в предварительном штампе иногда увеличивают толщину полотна. При использовании этих рекомендаций необходимо учитывать характер течения металла при формообразовании каждой конкретной детали. В реальных условиях штампованные заготовки имеют самую различную форму в плане, при этом ребра жесткости по полотну и контуру имеют также разнообразное расположение: от наиболее простой вафельной или лучеобразной до различного сочетания асимметрично расположенных ребер. При этом имеют место одновременно как открытые, так и закрытые сечения. В таких случаях, как правило, требуется заготовка переменной толщины. Поэтому при проектировании технологического процесса необходимо производить предварительный анализ и расчет сечений заготовок и переходов с учетом характера течения металла в полости штампа, т. е. необходимо определить расположение линий раздела течения металла.
Экспериментальные исследования и практика изготовления штампованных заготовок показали, что введение дополнительных, технологически необходимых конструктивных элементов, например, так называемого ложного полотна, позволяет компенсировать нехватку металла для оформления контура ребра и тем самым повысить эффективность процесса штамповки. В случае интенсивного течения металла в облойный мостик: имеет место удаление уже оформленного контурного элемента ребра или бобышки.
Во избежание прострелов под ребрами штамповки необходимо, чтобы сопротивление истечению в облойный мостик было несколько выше сопротивлений, металла при его течении в полость ребра. С этой целью также конструируют ложные участки полотна или ложные ребра.
Особое место при производстве крупногабаритных штампованных заготовок из легких сплавов на мощных гидравлических прессах занимают детали типа панелей, которые представляют собой сочетание тонкого полотна с ребрами жесткости различного направления и конфигурации. Установлено, что недостаток металла в заготовке ведет к незаполнению ребер, а при избытке металл трудно удалить в облой.
При недостатке металла в зоне истечения его в ребре образуется утяжина, а при резком повышении деформирующего усилия — зажим.
При проектировании деталей, изготавливаемых из штампованных заготовок, учитывают целый ряд факторов: технологические и физические свойства деформируемого материала; форма и соотношение размеров чистовой детали; вид оборудования, на котором будет изготавливаться штампованная заготовка; возможность изготовления отдельных поверхностей без последующей механической обработки; выбор линии разъема штампов.
В целях экономии металла на стадиях производства и обработки штампованных полуфабрикатов необходима разработка технологичных конструкций деталей.
Критериями, позволяющими оценить технологичность конструкции детали, запроектированной под горячую объемную штамповку, служат: коэффициент использования металла (КИМ) и коэффициент необрабатываемой поверхности (КНП), характеризующие степень приближения штампованной заготовки и готовой детали. КИМ определяется отношением массы чистовой детали к массе штампованной заготовки, КНП — отношением площади необрабатываемой поверхности к общей площади поверхности. Чем выше КИМ, тем более технологичной является деталь для изготовления ее горячей объемной штамповкой. Чем выше КНП, тем точнее штампованная заготовка.
Штампованные заготовки обычно подвергают механической обработке, объем которой зависит от степени их приближения к размерам чистовой детали. Степень точности размеров штампованных заготовок количественно определяется припусками на механическую обработку и допусками на размеры. Различают два вида припусков: технологический и припуск на механическую обработку.
Технологический припуск связан с необходимостью увеличения некоторых конструктивных элементов штампованных заготовок из-за нетехнологичности. Например, для деталей, имеющих закрытое сечение, с тонким полотном, высокими ребрами и недостаточными радиусами переходов от ребер к полотну требуется увеличить указанные конструктивные элементы для получения штампованных заготовок без дефектов, что, в конечном счете, приводит к увеличению расхода металла и объема последующей механической обработки. Такого рода припуски, величина которых определяется возможностями пластического деформирования, имеют существенное значение для технологии кузнечно-штамповочного производства и называются напусками.
Припуск на механическую обработку определяется требуемой чистотой поверхности и точностью геометрии после механической обработки, а также искажениями формы штампованной заготовки, образующимися при ее изготовлении. Величина этого припуска назначается по наибольшему габаритному размеру детали в зависимости от материала и требуемой чистоты обработки. На практике с целью увеличения точности штампованных заготовок стремятся к уменьшению припусков и ужесточению допусков на конструктивные элементы (толщину полотна, штамповочные уклоны, толщину ребер, радиусы переходов и закруглений, радиусы сопряжений и т. п.).
Возможность получения полотна минимальной толщины определяется сопротивлением деформации, скоростью остывания штамповки в процессе ее изготовления и температурой деформирования. При определении толщины полотна существенное значение имеют физические и технологические свойства материала, отношение ширины полотна к толщине, его площадь и отношение длины к ширине.
Чем больше площадь полотна при прочих равных условиях, тем больше должна быть его толщина. Чем больше отношение длины к ширине полотна при прочих равных условиях, тем меньше может быть толщина.
Существенное влияние на толщину полотна оказывают упругие деформации системы пресс-штамп. Разность упругих деформаций в различных местах полости штампа приводит к различной толщине полотна — наибольшей в середине и наименьшей по краям (так называемая чечевица).
Таким образом, предельная толщина полотна, которая может быть получена горячей штамповкой, определяется величиной необходимых удельных усилий в полости штампа.
Штамповочные уклоны служат для предотвращения застревания штампованных заготовок в ручьях штампа. При их отсутствии штампованная заготовка удаляется, преодолевая силы трения на относительно большом пути, тогда как при наличии уклонов она отрывается от стенок штампа после ничтожно малого смещения. На практике штамповочные уклоны составляют от 1 до 10°. Полости, имеющие большую площадь контакта, должны иметь большие значения штамповочных уклонов. Это объясняется повышением нормальных напряжений при штамповке в более глубокую полость штампа. При заполнении гравюры штампа выдавливанием уклон ручья повышает сопротивление течению металла, нормальные напряжения и соответствующие (удерживающие штамповку) силы трения.
В конкретных случаях, когда габариты и материал штампованных заготовок известны, величина штамповочных уклонов зависит от формы сечения и отношения высоты детали к ее ширине. В штампах с выталкивателями штамповочные уклоны выбирают такой величины, при которой исключается коробление штампованных заготовок при выталкивании.
Различают наружные и внутренние штамповочные уклоны. Первые относятся к поверхностям, на которых вследствие тепловой усадки образуются зазоры, а вторые — к тем поверхностям, которые при остывании штампованной заготовки приводят к ее горячей посадке на выступ штампа. Внутренние штамповочные уклоны выбирают на 1 — 2° больше наружных.
При штамповке алюминиевых сплавов необходимо учитывать следующее:
1. На поверхности исходной заготовки не должно быть даже неглубоких трещин, плен, вмятин, пузырей. Перед штамповкой все поверхностные дефекты должны быть удалены.
2. Необходимо строго соблюдать температуру и время нагрева заготовок, выдержку при заданной температуре, а также температурные интервалы штамповки. Перед началом штамповки обязателен подогрев штампов до 250 — 300 °C; штамповка в холодных или в недостаточно нагретых штампах затрудняет заполнение ручья металлом и вызывает образование трещин на штампуемых заготовках.
3. Меньшая способность заполнения формы штампа — при осадке и большая при истечении (выдавливании), что объясняется появлением дополнительных растягивающих напряжений при осадке и значительно меньшими их величинами при выдавливании, так как деформация при выдавливании происходит при более высоких сжимающих напряжениях.
4. При изготовлении штампованных заготовок многоручьевой совмещенной штамповкой, когда в двух ручьях одновременно деформируют, например, исходную заготовку и заготовку последующего перехода, особое внимание необходимо уделять вопросам расчета размеров заготовки, соответствия объемов металла сечениям используемых ручьев и т. п.; облой в этом случае следует удалять только после окончательной штамповки.
5. Гравюра в переходных (заготовительных) штампах должна иметь плавные переходы.
6. Скорость и степень деформации должны обеспечить требуемые механические свойства и отсутствие дефектов (внутренних и внешних) у штампованной заготовки.
7. Штампованные заготовки из сплавов АМг5, АМг6, АК4, АК6, АК8, В95, в особенности сложной конфигурации, во избежание возникновения поверхностных дефектов целесообразно изготавливать в два и более перехода.
8. Заготовительные ручьи имеют ограниченное применение; подкатные ручьи совсем не применяют, а протяжной ручей используют лишь при определенной степени и скорости деформации с зачисткой дефектов после протяжки. Протяжку заготовок рекомендуется выделять в отдельную операцию и проводить ее на плоских бойках.
9. Применяемые заготовительные ручьи крупногабаритных штампов служат для формообразования, как правило, переходных форм заготовок с одновременным истечением избытка металла либо в требуемые сечения, либо в облой.
В качестве смазки рекомендуется использовать смесь графита по ГОСТ 4404–78 и масла цилиндровое 52 по ГОСТ 6411–76 в следующем соотношении, % (объемн.): 60 — 70 масло, 30 — 40 графит. При штамповке деталей с высокими тонкими ребрами, образующими замкнутый контур (закрытое сечение), диафрагму на штампе и штампуемую заготовку целесообразно смазывать тонким слоем сухого графита, а в отдельных случаях добавлять в смазку сухую алюминиевую пудру.
При штамповке сложноконтурных изделий процесс следует вести за несколько ходов пресса с нанесением смазки на отдельные участки деформированной заготовки и гравюры штампа, обеспечивая тем самым более интенсивное локальное течение металла.
Наиболее распространенными видами брака штамповок из алюминиевых сплавов являются: складки, зажимы, прострелы, расслоения, забоины, неоформление конфигурации, трещины.
Складки представляют собой наплывы отдельных слоев металла, образовавшихся при встречном течении металла.
Зажим — заштампованная складка в результате неправильного течения металла в чистовом ручье или закатывания заусенцев, полученных при неправильном выполнении первых двух переходов.
Причинами возникновения складок и зажимов служит неравномерное заполнение полостей штампа металлом при неправильной схеме штамповки, несоответствие размеров и формы заготовки, малые величины радиусов сопряжений и штампуемой заготовки, низкая температура штамповки и недостаточный предварительный нагрев штампов.
Прострелы представляют наиболее распространенный дефект при штамповке алюминиевых сплавов.
Причинами образования прострелов могут быть:
а) несоответствие предварительного и окончательного ручьев штампа;
б) избыток металла в предварительной заготовке;
в) оформление штампованной заготовки в одном окончательном штампе без применения заготовительных и предварительных штампов;
г) избыток смазки, нанесенной на гравюру штампа и, как следствие этого, различие скоростей течения металла в разных участках;
д) не технологичность штампованной заготовки.
Рисунок 8 — Недоштамповка поковки
Перекос — это смещение сверх установленного допуска одной половины поковки относительно другой половины по плоскости разъема. Причиной перекоса может быть неисправности оборудования (увеличенный зазор в направляющих, выработка плоскостей штамподержателя).
Заусенец — это несрезанный остаток облоя при плохой установке и подгонке штампов, либо при смещении поковки в обрезной матрице. Удаляется заточкой наждачным кругом.
Кривизна — отклонение осей и плоскостей поковки от их правильного геометрического положения. Возникает при обрезке заусенца у поковок со сложным контуром обрезки, с тонкими сечениями при большой длине, при использовании неправильных обрезных пуансонов или штампов неправильной конструкции.
Ослабление размера — появляется вследствие недостаточного припуска на обработку резанием или уменьшения рабочего сечения детали в необрабатываемых местах вследствие штамповки поковок с толстым слоем окалины или в изношенных штампах.
Отклонение по длине — возникает из-за разной температурной усадки по объему поковок при штамповке или нестабильности длины заготовок.
Для моделирования технологического процесса горячей объемной штамповки обычно необходимы следующие исходные данные: чертеж поковки, объем и форма заготовки, реология материала заготовки, начальная температура заготовки, температура окружающей среды, температура штампа, вид смазки и коэффициент трения, скорость деформирования.
Для обеспечения технологичности получаемых штампованных поковок необходимо правильное построение чертежа поковки, определяющего оптимальное формоизменение деформируемого металла. Важным также является задача моделирования картины течения металла по поверхности инструмента.
Компьютерное моделирование процессов ОМД в работе позволило изучить процессы формообразования, рассчитывать энергосиловые затраты, разработать меры по предотвращению образования дефектов изделии Номенклатура этих поковок, а также мелкосерийность производства могут определять высокую стоимость штамповочного производства. При этом целесообразно применение компьютерного моделирования на стадии проектирования штамповой оснастки.
Основываясь на обзоре различных методов моделирования процессов обработки металлов давлением, а также новых технологических разработок в производстве штампованных деталей можно сделать вывод о том, что классификация деталей с ребрами жесткости из алюминиевых сплавов недостаточно изучена. Актуальными на сегодняшний день остаются вопросы расчета параметров. Поковки подобного класса находят широкое применение в различных отраслях машиностроения.
В связи с этим представлена классификации поковок указанного типа.
В работе приведена классификация поковок на группы и подгруппы, которые можно штамповать с использованием различных схем формоизменения:
К группе I относятся преимущественно массивные поковки простой формы, которые получают прямым выдавливанием.
Группу II делят на две подгруппы. В подгруппу, А преимущественно включены поковки с углублениями и отверстиями, которые можно изготовлять как при прямом, так и при обратном выдавливании. Как правило, эти поковки имеют плоские торцы и полости (отверстия).
Подгруппа Б включает поковки, предназначенные для изготовления в условиях прямого выдавливания. Эти поковки имеют либо глубокие полости, либо отверстия.
В группу III входят поковки типа фланцев, крышек, панелей и тому подобные формы, которые можно изготовлять при прямом и комбинированном выдавливании или только при комбинированном выдавливании.
Группа IV включены преимущественно мелкие поковки; которые могут штамповаться по групповой технологии — несколько поковок в одном штампе одновременно.
Важным моментом является деление исследуемых параметров, которые можно использовать для характеристики поковок, по нескольким признакам, чтобы с одной стороны подчеркнуть сложность изготовления и уникальность поковок, а с другой выявить какую математическую модель целесообразно использовать для описания формоизменения; с третьей, — оценить сложность расчетов параметров процесса штамповки рассматриваемой поковки.
В работе предлагается классификация деталей на типы по признакам, которые характеризуют поковку набором параметров, присущих рассматриваемому признаку.
Первый признак оценивает уникальность поковки и сложность ее изготовления, учитывая при этом размеры поковки в плане и коэффициент использования металла (КИМ). Согласно этому признаку линейные размеры поковки характеризуют габаритные размеры детали. Производство крупногабаритных деталей уникально, т.к. требует больших усилий деформирования, а, следовательно, и применения мощных гидравлических прессов. Наряду с линейными размерами представление о размерах получаемой детали дает площадь поковки, которую указывают в конструкторской документации. КИМ характеризует рациональность формы и технологии ее изготовления. Небольшой КИМ говорит о том, что значительная часть металла идет в отходы и указывает на необходимость совершенствования технологии штамповки поковок данного класса.
Второй признак позволяет сделать выбор теории для моделирования процесса штамповки данного класса поковок путем оценки следующих особенностей размеров поковки.
1) По отношению характерного линейного размера к толщине полотна поковки определяют насколько слой металла по полотну штампуемой поковки можно считать тонким. В качестве характерного размера выбирают минимальный размер межреберных зон. Чем больше указанное отношение, тем более обоснованно слой можно считать тонким.
2) Отношение толщины ребра жесткости к толщине полотна поковки показывает пригодность выбранной теории моделирования данного процесса штамповки. Так, если полость под ребро жесткости имеет большую ширину по сравнению с толщиной полотна, то возможно образование «утяжин» в процессе деформирования (из-за нехватки металла перемещаемого с полотна в полость), а слишком узкая полость вызывает затрудненность затекания в нее металла. Желателен выбор рассматриваемого отношения в некотором диапазоне, обеспечивающем получение изделия без механических дефектов.
3) Высота ребер жесткости по сравнению с толщиной полотна в значительной степени определяет количество переходов, т.к. относительно высокие ребра жесткости нельзя получить за один переход.
4) Наличие наклонных ребер жесткости. Под наклоном ребер жесткости подразумевается их наклон к плоскости полотна в продольном направлении. Наклонные ребра жесткости формируются аналогично прямым на стадии свободного затекания, но для описания их формирования на стадии доштамповки математическая модель усложняется. Для ребер жесткости с небольшим наклоном (5 — 10°), можно принять ту же модель, что и для ребер жесткости, не имеющих уклона.
5) Разнотолщинность полотна. Полотно конечной поковки может иметь клиновидную форму, что значительно усложняет исходные расчетные соотношения в рамках выбранной теории.
6) Наличие бобышек. Бобышка (или, так называемый, «магазин») определяет специфические граничные условия. При этом, строго говоря, для расчета ее формообразования не совсем корректно применять тот же подход, что и для расчета формоизменения ребер жесткости.
7) Одностороннее или двухстороннее оребрение. Наличие двухсторонних ребер жесткости может не играть принципиальной роли в усложнении исходной модели [27], т.к. потоки металла распределяются в зависимости от положения ребер жесткости на полотне поковки, что и определяет граничные условия. Определяющим эти граничные условия, очевидно, является форма поперечного сечения каждого из ребер.
8) От марки сплава зависит реология исследуемого материала, а, следовательно, математическая модель, принятая для описания процесса. Как известно [28], кривые деформационного упрочнения для различных сплавов существенно отличаются друг от друга. Например, сплав АК6 практически не упрочняется в процессе деформирования.
Третий признак характеризует сложность расчетов с учетом следующих особенностей формы поковок.
1) Количество ребер жесткости, которое характеризует сложность геометрии поковки в плане.
2) Количество ячеек контура поковки, по которому оценивают многосвязность контура, а, следовательно, и сложность расчетов. При этом ячейками следует считать, как открытые (не ограниченные со всех сторон ребрами жесткости), так и закрытые (ограниченные со всех сторон ребрами жесткости) участки многосвязного контура.
3) Форма поперечного сечения ребер жесткости, которая определяет граничные давления. Чем проще форма поперечного сечения ребра жесткости, тем проще расчетные формулы. Если в одной поковке имеются ребра жесткости разной формы поперечного сечения, то схема течения металла усложняется. Существенную роль играет наличие контурного оребрения, т.к. форма контурного ребра жесткости отличается от центрального, а, следовательно, должны использоваться иные соотношения для расчета граничных давлений.
4) Наличие прямолинейных и криволинейных участков, а также их соотношение. Существенную роль играет форма криволинейных участков: если это дуги окружностей, то не требуется их аппроксимировать, т.к. они напрямую соответствуют расчетным схемам. В противном случае точность расчетов уменьшается. Наличие большего количества прямолинейных участков делает построение картины течения металла по полотну заготовки более точным, но усложняет расчет формоизменения ребер жесткости. Следует иметь в виду, что участки сопряжения прямолинейных отрезков контура (с небольшим радиусом сопряжения, не более 20% от длины прямолинейного участка) между собой можно не относить к криволинейным участкам.
5) Наличие в поковке ребер жесткости различной толщины определяет схему течения металла по полотну поковки. Варьирование толщины применяемых в технологии штамповки «ложных ребер» жесткости позволяет регулировать течение металла по полотну заготовки.
6) Ребра жесткости разной высоты существенным образом влияют на принимаемую схему течения металла, поскольку целью может быть одновременное формирование всех ребер жесткости поковки, и тогда усложняется как расчетная схема, так и технология штамповки, в зависимости от выбора технологических приемов, приводящих к достижению поставленной цели.
Четвертый признак характеризует моделирование по величине коэффициента сложности поковок.
В соответствии со сложностью расчетов Соломонов К. Н ввел понятие коэффициент сложности поковок, который дает количественную характеристику сложности расчета параметров объемной штамповки. Этот коэффициент зависит от количества ребер жесткости и ячеек контура поковки, формы поперечного сечения ребер жесткости, наличия прямолинейных и криволинейных участков поковки, а также от наличия разнотолщинности и разной высоты ребер жесткости. Каждый из этих параметров имеет количественную характеристику.
Формула для вычисления коэффициента сложности поковок выглядит так:
С = Крж +Кпс + 2Кя +3Кку+ 5Крт + 10Крв, (1.1)
где Крж — учитывает количество ребер жесткости в поковке, незначительно влияет на сложность расчетов, поэтому весовой коэффициент для него выбран равным 1;
Кпс — учитывает количество ребер жесткости с различной формой поперечного сечения, мало усложняет расчеты (известны соотношения для вычисления граничных давлений на контуре наиболее часто употребляемых конфигураций ребер жесткости);
Кя — зависит от количества ячеек контура поковки и в большей степени влияет на сложность расчетов, чем наличие ребер жесткости;
Кку — учитывает количество криволинейных участков, меняет схему расчетов по сравнению с поковками, содержащими только прямолинейные участки;
Крт — учитывает количество ребер жесткости, имеющих различную толщину, значительно усложняет расчеты, поскольку схема течения металла по полотну поковки зависит в большой степени от этого параметра;
Крв — количество ребер жесткости отличающихся по высоте друг от друга, оказывает наибольшее влияние на сложность расчетов, т.к. ведет к неравномерности формирования поковки в целом и требует применения технологических приемов, устраняющих или уменьшающих эту неравномерность.
В зависимости от величины коэффициента сложности поковки можно делить на простые, сложные и очень сложные в смысле сложности их расчетов, простые: С < 10;
сложные: 50 > С > 10;
очень сложные: С > 50.
Таким образом, из рассмотренных поковок можно считать:
простой — поковку 2;
сложными — поковки 1,3 — 5, 7, 10
очень сложными — поковки 6,8, 9
4 Моделирование горячей объемной штамповки алюминиевых сплавов
Важным моментом при компьютерном моделировании горячей объемной штамповки является интерпретация процесса течения металла при формообразовании различных изделий.
В работе предлагается подход к компьютерному моделированию, сочетающий наглядность представления о процессе и оперативную интерактивность исследования операции. Разработанная компьютерная модель в среде «Visual Basic» с интерфейсом, позволяет технологу быстро определить режимы деформирования и геометрии инструмента в соответствии с заданным чертежом изделия.
На его основе разработаны различные программные системы. В частности, система FORM-2D [32], в основном предназначенная для расчета горячей обработки давлением, которая характеризуется большими пластическими деформациями в объеме, ограниченном инструментами произвольной и часто весьма сложной формы.
Начальным этапом при моделировании объемной штамповки является подготовка исходных геометрических данных для моделирования, вид, структура и форматы которых определяют систему моделирования.
На этом этапе, авторы рекомендуют решить следующие задачи:
1. Проектирование поковки, максимально приближенной по форме и размерам к получаемой детали, которая, с одной стороны, определяет гравюру штампа, а с другой — зависит от выбранной схемы штамповки, плоскости разъема штампа, расположения поднутрений, компенсаторов и т. д. При этом для назначения допусков, припусков и напусков должны учитываться требования и рекомендации соответствующих нормативных документов (ГОСТов, ОСТов или отраслевых ТУ).
2. Выбор схемы штамповки и проектирование штампового инструмента, наиболее упрощенного по внешней геометрии, но максимально приближенного по форме внутренней гравюры к получаемой штампованной поковке. При этом должны быть учтены вид используемого деформирующего оборудования, конструкция штамповой оснастки и штампового блока. Важными дополнительными факторами являются условия свободного извлечения поковки из штампа, а также благоприятная схема течения металла для предотвращения образования дефектов (зажимов, прострелов, незаполнений и др.) и формирования благоприятной макроструктуры. Имеют значение предварительные оценки допустимых степеней местных деформаций, которые не должны превышать значений максимальной пластичности для предотвращения локальной повреждаемости металла (нарушения сплошности, образования трещин, макродефектов) поковки или ее разрушения.
3. Расчет объема поковки с компенсаторами или другими неизбежными технологическими напусками на удаляемые отходы и определение формы и размеров заготовки соответствующего объема. Как правило, верхняя поверхность заготовки — плоская, а форма боковой и нижней части заготовки может быть достаточно сложной, так как она должна полностью повторять часть боковой и всю нижнюю часть гравюры матрицы.
4. Согласование совмещения геометрических форм и взаимного расположения заготовки, верхней (пуансона) и нижней штамповых вставок, сопряжений их контактных поверхностей и задание расчетной величины хода штампа.
В работе было рассмотрено моделирования течения металла в процессах объемной штамповки оребренных поковок. Разработанный программный комплекс позволил провести анализ формообразования поковок с тонким полотном, а также были предложены параметры технологических вырезов.
Характер заполнения полости штампа при моделировании технологического процесса можно разделить на три стадии: первая стадия, соприкосновение пуансона с металлом, осадка переходит в объемную штамповку; вторая стадия, соприкосновение металла со стенками штампа, при этом начинает расти усилие штамповки; третья стадия, заполнение облойной канавки, усилие максимальное.
Важным фактором является равномерность нагрева заготовки, так как есть вероятность возникновения трещин внутри поковки. Максимальная температура в большинстве случаев наблюдается на последних стадиях, в области перехода металла в облойную канавку.
Одним из наиболее эффективных считается математическое моделирование, основанное на построении модели физического процесса с помощью математического аппарата.
При постановке краевых задач технологической пластичности в качестве модели деформируемого материала наиболее часто используют изотропную идеальную жесткопластическую среду и определяющие уравнения теории пластического течения.
С помощью данной системы, разработанной в нашей стране, которая также применяется и за рубежом, были проведены моделирования и анализ процессов объемной штамповки, ковки и прессования.
Программа дает возможность двухмерного и осесимметричного моделирования течения материала и указывает на дефекты, вызванные неравномерностью формообразования. Она базируется на модели, в соответствии с которой материал рассматривается как жесткопластичный. С помощью компьютерного моделирования по системе FORM-2D на основе анализа кинематики течения металла и распределения внутренних напряжений в работе произведена оптимизация выбора переходов штамповки.
Авторами работы была разработана методика расчета формоизменения заготовки и энергосиловых параметров процесса штамповки с кручением, позволяющая определить неоднородное напряженно-деформированное состояние заготовки при штамповке с учетом графика изменения угловой скорости вращения инструмента и свойств материала заготовки.
В работе описаны результаты анализа многооперационных процессов объемной штамповки с использованием жестко-пластичной модели на основе МКЭ, проведенного с помощью программы SPID, которая позволяет решать двухмерные и осесимметричные задачи, и открывает новые возможности: учета трения между материалом и инструментом; оценки усилий пуансона; графического представления необходимых количественных величин и т. п.
В настоящее время существует множество коммерческих пакетов программ для математического моделирования процессов штамповки, базирующихся на МКЭ. Такие виды моделирования дают точные результаты, которыми часто трудно воспользоваться. Кроме того, время расчетов для моделирования очень велико.
Наиболее серьезными проблемами моделирования процессов горячей формовки металлов с использованием МКЭ являются термомеханические условия, большие пластические деформации и резкие изменения сетки. Для устранения этих проблем предложен специальный код МКЭ и представлены результаты моделирования горячего выдавливания одной из деталей.
В работе показано исследование на основе МКЭ геометрических и механических параметров горячей штамповки осесимметричных деталей. Моделирование осуществляется по программе для упругопластической среды в трехмерном пространстве. Сетка конечных элементов моделируемой заготовки в поперечном сечения состояла из 380 элементов и 852 узлов.
При моделировании процессов объемной штамповки считается, что металл в штампе течет в направлении наименьшего сопротивления. Усилие деформирования определяется в зависимости от размеров заготовки, ее формы, трения и формы инструмента. Кроме того с помощью моделирования можно определить такие важные параметры заготовки, как накопленная деформация, распределение напряжений и температуры в ее объеме, направление волокна, предсказать опасность разрушения и оценить степень износа инструмента.
Общие вопросы и взаимосвязи решения проблем по оптимизации параметров достаточно подробно рассмотрены в книге. Показаны подходы по оптимизации в горячештамповочном производстве. В зависимости от сложности формы детали рассматривается проектирование технологических процессов и штампов, также представлено решения задач по выбору оптимального варианта загрузки штамповочного оборудования и оптимальных вариантов технологических процессов штамповки.
Из-за ограниченных возможностей получения общего решения задач, возникают трудности на этапе применения методов оптимизации к решению практических задач, поэтому возникает подмена оптимизации простым подбором параметров по каким либо критериям. Выбор чаще всего осуществляется вручную.
Методы оптимизации при решении задач ОМД применяются к выбору оптимальных параметров штампов и заготовок, технологии получения изделия, а также оптимального управления процессом.
Работа посвящена вопросам оптимизации параметров штампов, рассмотрены оптимизации формы и размеров заготовительных ручьев для поковок, изготовляемых объёмной штамповкой, на основе применения компактно описываемых форм рациональных заготовок, где неравномерность деформации по сечению поковок оценивается комплексом критериев качества. Авторами работы представлена оптимизация геометрических параметров многослойных матриц с твердослойной вставкой. Традиционно используемая теория наибольших касательных напряжений приводит к значительно заниженным значениям расчетного разрушающего внутреннего давления. Отсутствие на рабочей поверхности матриц окружных растягивающих напряжений приводит к повышению износостойкости инструмента, но при этом снижается расход дорогостоящего твердого сплава.
Не менее важным способом, обеспечивающим экономию металла, является оптимизация размеров исходной заготовки. В работе рассмотрена методика выбора оптимальных параметров формы штампов для кольцевых заготовок. На основе компьютерного было получено решение, которое позволяет устранить причины возникновения дефектов в изделии.
При однопереходной штамповке авторами работы были получены результаты оптимизации первоначальной формы заготовки и штампа, в том числе и предварительного штампа при штамповке в два перехода. Была рассмотрена задача по оптимизации первоначальной формы заготовки при осадке в плоских штампах.
В статье рассмотрены задачи оптимального управления непрерывными и дискретными технологическими процессами, а также дано описание основных методов решения таких задач. Приведены постановки еще не решенных задач кузнечно-штамповочного производства: определения оптимального режима трения при осадке, оптимизации управления многопереходной штамповки корпусных деталей.
Интерес представляет опыт использования экспертных систем для решения задач оптимизации. При решении многих задач проектирования разработчик приходит к приемлемому решению путем последовательного многократного анализа математической модели проектируемого объекта. При этом метод подбора, может оказаться достаточно сложным и громоздким при его реализации в экспертной системе. Использование численной оптимизации для отыскания наилучшего решения позволяет существенно сократить объем базы правил проектирования и упростить работу в ней. В статье представлен пример экспертной системы, которая заключается в постановке задачи оптимизации и анализе полученного решения. Благодаря возможности обращения к алгоритмам оптимизации экспертная система смогла показать лучшие результаты, чем специалист.
Выводы
Проведенный обзор источников литературы показал актуальность применения компьютерного моделированию для процессов горячей объемной штамповки алюминиевых сплавов. При этом наиболее перспективно применение для этих целей таких программных комплексов, как QFORM и DEFORM, хорошо зарекомендовавших себя при решении подобных задач. Но при этом в большинстве рассмотренных примеров показаны только отдельные фрагменты технологических процессов горячей объемной штамповки и практически отсутствуют сведения о компьютерном моделировании реальных процессов штамповки в полном объеме, от начала и до конца с их подробным анализом. Что позволило бы внести определенные коррективы в эти процессы и послужить ориентиром при последующей разработке технологических процессов для подобных поковок.
Особенно важна задача оптимизации технологического процесса. Одним из основных показателей эффективности производства при штамповке является коэффициент использования металла (отношение массы детали к массе материала поступившего в обработку). Относительно большие потери металла требуют тщательного подбора многих параметров технологического процесса (например, размеров заусенечной канавки) для их минимизации. Применение систем анализа пластического формоизменения для решения подобной задачи приводит к перебору большого числа вариантов технологического процесса, основанных на применении численных методов, которые отличаются длительным временем расчета, что значительно увеличивает срок разработки технологии.
На основании изложенного в работе были поставлены следующие задачи.
1. Сделать анализ действующего технологического процесса горячей объемной штамповки поковки из алюминиевого сплава.
2. Провести компьютерное моделирование выбранного технологического процесса.
3. Подготовить рекомендации по корректировке действующего технологического процесса.
Список использованных источников
1. Бреббия К. Методы граничных элементов. / Бреббия К., Теллес Ж., Вроубел Jl. -М.: Мир, 1987. — 524 с.
2. Сегерлинд Л. Применение метода конечных элементов — М.: Мир, 1979. — 392 С.
3. Галлагер Р. Метод конечных элементов. Основы: Пер. с англ. — М.: Мир, 1984
4. Зенкевич О. Метод конечных элементов в технике — М.: Мир, 1975.
5. Зенкевич О., Морган К. Конечные элементы и аппроксимация: Пер. с англ. — М.: Мир, 1986
6. Деклу Ж. Метод конечных элементов: Пер. с франц. — М.: Мир, 1976
7. Галлагер Р. Метод конечных элементов. Основы. М.: Мир, 1984. — 428 с.
8. Ю. И. Рыбин, А. И. Рудской, А. М. Золотов. Математеическое моделирование и проектирование технологических процессов обработки металлов давлением. СПб, Изд-во СПбГПУ: 2004
9. ASM Hanbook. Vol. 22B. Metals Process Simulation, ASM International, 2010.
10. J.M. Cabrera, A. Al Omar, J.M. Prado. Simulation de la fluencies en client de un aero microaleado con un contenido medio de carbono. II parte. Recristalizacin dinmica: inicio y cintica. Rev. Metal Madrid, 33 (3), 1997, pp. 143−152
11. Ю. М. Чижиков — Моделирование процесса прокатки, М: Металлургиздат, 1963
12. Адлер Ю. П., Маркова Е. В., Грановский Ю. В. Планирование эксперимента при поиске оптимальных условий. 2-е изд., перераб. и доп. — М.: Наука, 1976. — 280 с.
13. Лунев В. А. Математическое моделирование и планирование эксперимента[Электронный ресурс] .
14. Григорьев А. К., Коджаспиров Г. Е. Термомеханическое упрочнение стали в заготовительном производстве. Л.: Машиностроение, 1985. — 143 с.
15. Mynors D.J., Tildesley J.C.A., Bonnavand F. Forging simulation: ForgeRond: A fast numerical simulation package // Metallurgia. — 1999. — 66, № 2. — P. 4.
16. Hans Raj K., Chenot J.L., Fourment L. Finite element modelling of hot metal forming // J. Eng. and Mater. Sci. — 1996. — 3, № 6. — P. 234−238.
17. Janjic M., Vukccevic M., Domazetovic V. // J. Technol. Plast. —1997. — 22, № 1−2. — C. 40−48.
18. Кононов B.B., Егорова Л. И. Новые возможности в области моделирования процессов штамповки // Кузнечно-штамповочное производство. — 2000. — № 7. — С. 35−38.
19. Макаров А. Н. Исследование процесса формообразования ребристых деталей. Дисс. канд. техн. наук: 05.16.05. — М., 1975.
20. Костарев И. В. Разработка методов проектирования технологических процессов и штампов для изготовления качественных ребристых штампованных поковок из алюминиевых сплавов с тонким полотном. Дисс. докт. техн. наук: 05.03.05. — М., 1986.
21. Татарников И. 3D шагает в массы с AutoCAD 2011 // САПР и Графика. — М.: КомпьютерПресс, 2010, № 5, с. 14—18.
22. Ушаков Д. «Бесплатный» Inventor Fusion в составе AutoCAD 2012 кардинально меняет расклад на рынке трехмерных САПР. Isicad, 2011.
23. Справочник кузнеца / под ред. В. Ф. Безъязычного. М.: Машиностроение, 2011.360с.:ил.
24. Лисунец Н. Л., Соломонов К. Н., Цепин М. А. Объемная штамповка алюминиевых заготовок. — М.: Машиностроение, 2009, с.84−87.
25. Ильюшин А. А., Полная пластичность в процессах течения между жесткими поверхностями, аналогия с песчаной насыпью и некоторые приложения// Прикладная математика и механика 1955, Т.XIX. № 6, с. 693−713
26. Диссертация Соломонова, можно ли ссылаться?
27. Костарев И. В. Определение усилий осаживания тонких поковок // Пластическая деформация металлов и сплавов. — М., 1969. — С. 232−234.
28. Охрименко Я. М. Технология кузнечно-штамповочного производства. — М.: Машиностроение, 1976. — 560 с.
29. Костарев И. В., Казьмин А. В. Исследование процесса формообразования деталей с однои двухсторонними ребрами жесткости // Изв. вузов. Машиностроение. — 1980. — № 1. — С. 106−109.
30. СПРАВОЧНИК
31. Yang D.Y., Han C.H. A New Formulation of Generalized Velocity Field for Axisymmetric Forward Extrusion Through Arbitrarily Curved Dies // J. of Eng. for Indust. — 1987. — № 2. — P. 161.
32. Беккер П. В., Евдокимов А. К. Компьютерное моделирование при исследовании процессов многоканального выдавливания // Кузнечно-штамповочное производство. — 1999. — № 12. — С. 25−27.
33. Соломонов К. Н., Моделирование течения металла в процессах объемной штамповки оребрённых деталей//Технология легких сплавов 2005, № 1−4, с. 142−149
34. Полищук Е. Г., Жиров Д. С., Вайсбурд Р. А. // Система расчета пластического деформирования РАПИД // Кузнечно-штамповочное производство. — 1997. — № 8. — С. 16−18.
35. Голонков В. А., Радченко С. Ю., Тюков В. М. ППП для моделирования процессов обработки металлов давлением // Новые материалы и технологии. — М., 1994. — С. 123.
36. Автоматизированная система ФОРМ-2Д для расчета формоизменения в процессе штамповки на основе МКЭ / Г. Я. Гун, Н. В. Биба,
37. О. В. Садыков и др. // Кузнечно-штамповочное производство. — 1992. — № 9-ю. — С. 4−7.
38. Manabu G., Gang S. Z.,. Masaki К // Trans. Jap. Soc. Mech. Eng. C. — 1996. — 62, № 602. — P. 4099−4106.
39. Joun M.S., Moon H.K., Shivpuri R. Automatic simulation of a sequence of hot-former forging processes by a rigid-thermoviscoplastic finite element method // J. Eng. Mater, and Technol. — 1998. — 120, № 4. — P. 291−296.
40. Петров А. И., Корольков В. И. Моделирование геометрического преобразования контура заготовки в процессе обработки // Кузнечно-штамповочное производство. — 2000. — № 11. — С. 40−42.
41. Автоматизированная подготовка технологической документации для производства штампованных деталей / Г. И. Тимофеев, Ю.А. Ар-замаскин, О. И. Леушин и др. // Кузнечно-штамповочное производство. — 1998. —№ 5. —С. 31−32.
42. Осадчий В. А. Информационно-обучающая система в области обработки металлов давлением // Изв. вузов. Черная металлургия. — 2000. — № 3. — С. 45−47.
43. Добровольская М. К., Исаевич JI.A., Полойко О. О. Автоматизированное проектирование штампов в системе «КОМПАС-ШТАМП 5» // Кузнечно-штамповочное производство. — 1999. — № 11. — С. 6−8.
44. Резников Ю. Н., Калинин Г. Г. Оптимизация заготовительных ручьев для поковок, изготовляемых объемной штамповкой // Кузнечно-штамповочное производство. — 1998. — № 10. — С. 8−10.
45. Белоновская И. Д., Глинская Н. Ю., Осадчий Ю. С. Автоматизация выбора оптимальной исходной заготовки // Машиностроитель. —1999. —№ 12. —С. 22.
46. Fourment L., Balan Т., Chenot J.L. Optimal design for поп-steady—state metal forming processes. II. Application of shape optimization in forging // Int. J. Numer. Meth. Eng. — 1996. — 39, № 1. — P. 51−65.
47. Воронов С. М. Процессы упрочнения сплавов AL-Mg-Si и их новые промышленные композиции. М.: Оборонгиз, 1946
48. ПИ 1.2.085−78 (ВИЛС) Ковка и штамповка деформируемых алюминиевых и магниевых сплавов. Типы технологических процессов, 1978